SUZUKI SWIFT 2000 1.G RG413 Service Workshop Manual
[x] Cancel search | Manufacturer: SUZUKI, Model Year: 2000, Model line: SWIFT, Model: SUZUKI SWIFT 2000 1.GPages: 698, PDF Size: 16.01 MB
Page 251 of 698
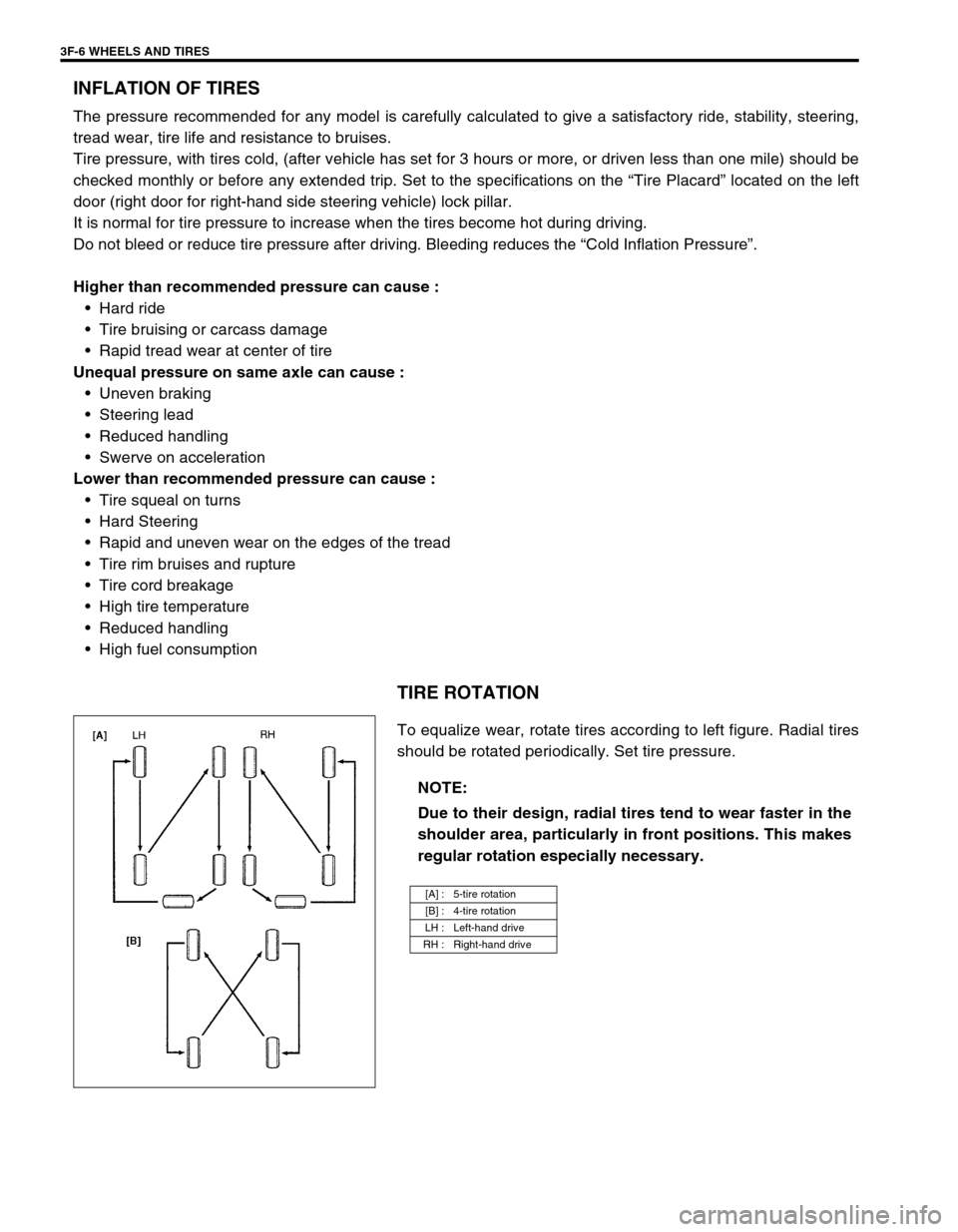
3F-6 WHEELS AND TIRES
INFLATION OF TIRES
The pressure recommended for any model is carefully calculated to give a satisfactory ride, stability, steering,
tread wear, tire life and resistance to bruises.
Tire pressure, with tires cold, (after vehicle has set for 3 hours or more, or driven less than one mile) should be
checked monthly or before any extended trip. Set to the specifications on the “Tire Placard” located on the left
door (right door for right-hand side steering vehicle) lock pillar.
It is normal for tire pressure to increase when the tires become hot during driving.
Do not bleed or reduce tire pressure after driving. Bleeding reduces the “Cold Inflation Pressure”.
Higher than recommended pressure can cause :
Hard ride
Tire bruising or carcass damage
Rapid tread wear at center of tire
Unequal pressure on same axle can cause :
Uneven braking
Steering lead
Reduced handling
Swerve on acceleration
Lower than recommended pressure can cause :
Tire squeal on turns
Hard Steering
Rapid and uneven wear on the edges of the tread
Tire rim bruises and rupture
Tire cord breakage
High tire temperature
Reduced handling
High fuel consumption
TIRE ROTATION
To equalize wear, rotate tires according to left figure. Radial tires
should be rotated periodically. Set tire pressure.
NOTE:
Due to their design, radial tires tend to wear faster in the
shoulder area, particularly in front positions. This makes
regular rotation especially necessary.
[A] : 5-tire rotation
[B] : 4-tire rotation
LH : Left-hand drive
RH : Right-hand drive
Page 252 of 698
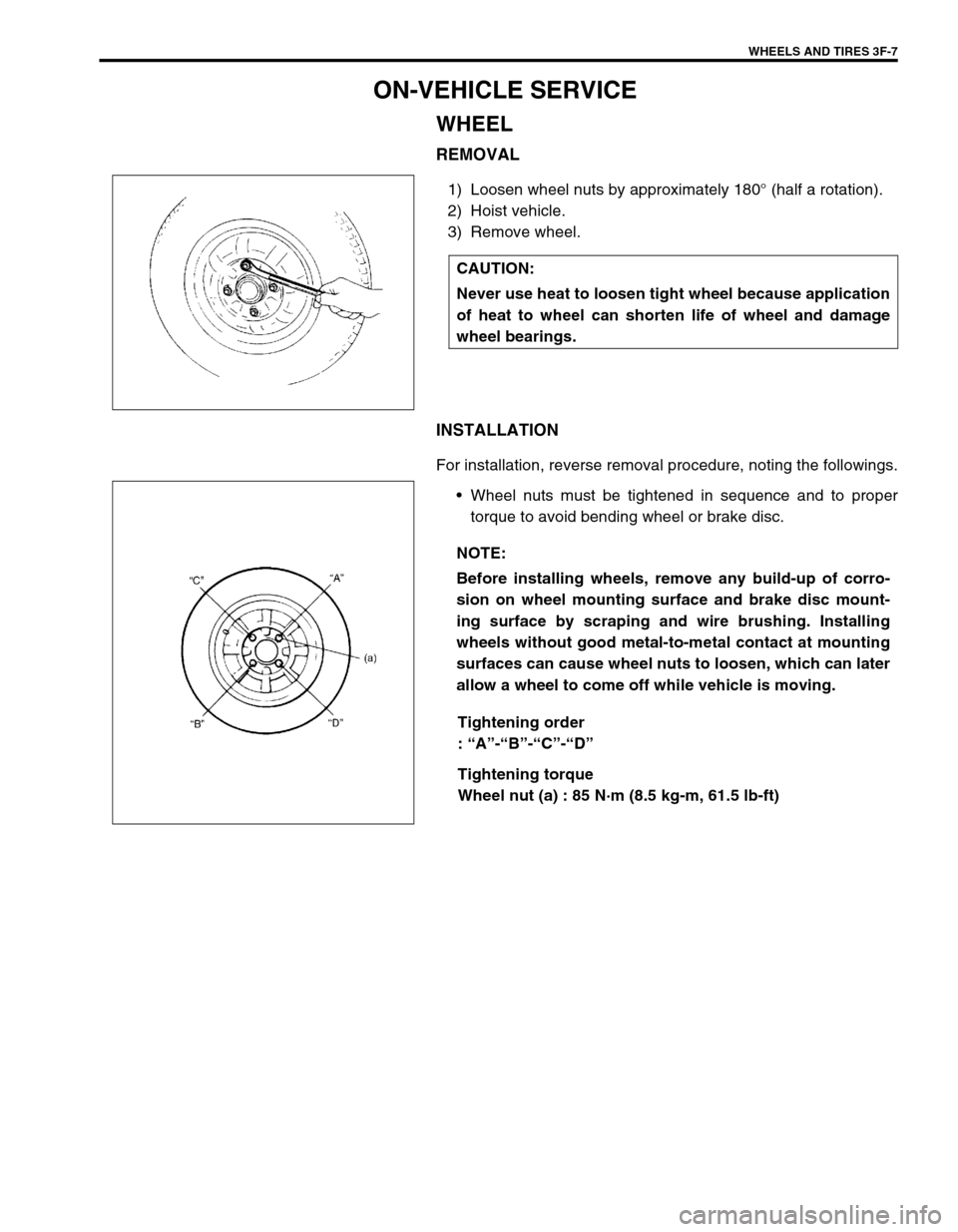
WHEELS AND TIRES 3F-7
ON-VEHICLE SERVICE
WHEEL
REMOVAL
1) Loosen wheel nuts by approximately 180° (half a rotation).
2) Hoist vehicle.
3) Remove wheel.
INSTALLATION
For installation, reverse removal procedure, noting the followings.
Wheel nuts must be tightened in sequence and to proper
torque to avoid bending wheel or brake disc.
Tightening order
: “A”-“B”-“C”-“D”
Tightening torque
Wheel nut (a) : 85 N·m (8.5 kg-m, 61.5 lb-ft) CAUTION:
Never use heat to loosen tight wheel because application
of heat to wheel can shorten life of wheel and damage
wheel bearings.
NOTE:
Before installing wheels, remove any build-up of corro-
sion on wheel mounting surface and brake disc mount-
ing surface by scraping and wire brushing. Installing
wheels without good metal-to-metal contact at mounting
surfaces can cause wheel nuts to loosen, which can later
allow a wheel to come off while vehicle is moving.
Page 253 of 698
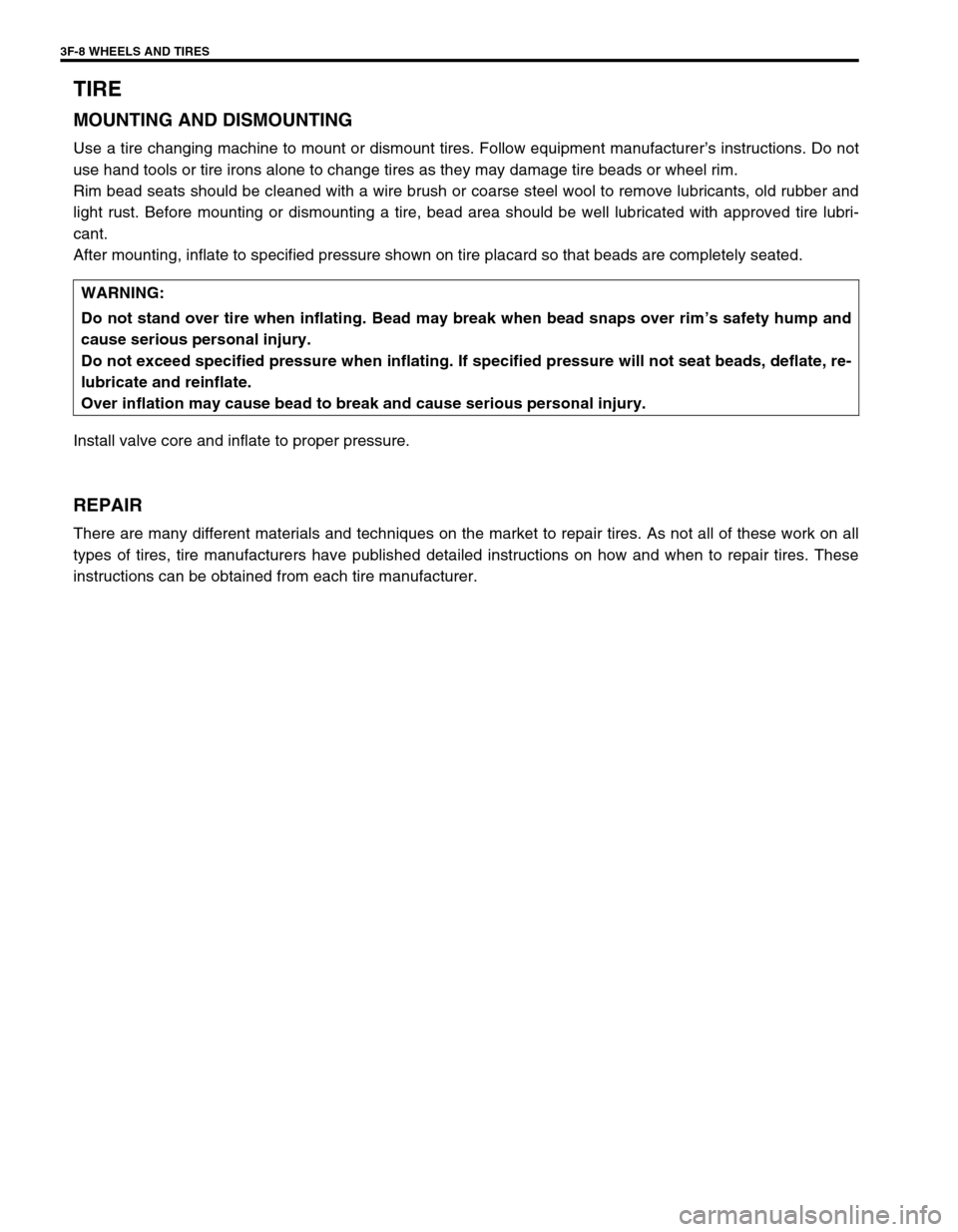
3F-8 WHEELS AND TIRES
TIRE
MOUNTING AND DISMOUNTING
Use a tire changing machine to mount or dismount tires. Follow equipment manufacturer’s instructions. Do not
use hand tools or tire irons alone to change tires as they may damage tire beads or wheel rim.
Rim bead seats should be cleaned with a wire brush or coarse steel wool to remove lubricants, old rubber and
light rust. Before mounting or dismounting a tire, bead area should be well lubricated with approved tire lubri-
cant.
After mounting, inflate to specified pressure shown on tire placard so that beads are completely seated.
Install valve core and inflate to proper pressure.
REPAIR
There are many different materials and techniques on the market to repair tires. As not all of these work on all
types of tires, tire manufacturers have published detailed instructions on how and when to repair tires. These
instructions can be obtained from each tire manufacturer.WARNING:
Do not stand over tire when inflating. Bead may break when bead snaps over rim’s safety hump and
cause serious personal injury.
Do not exceed specified pressure when inflating. If specified pressure will not seat beads, deflate, re-
lubricate and reinflate.
Over inflation may cause bead to break and cause serious personal injury.
Page 254 of 698
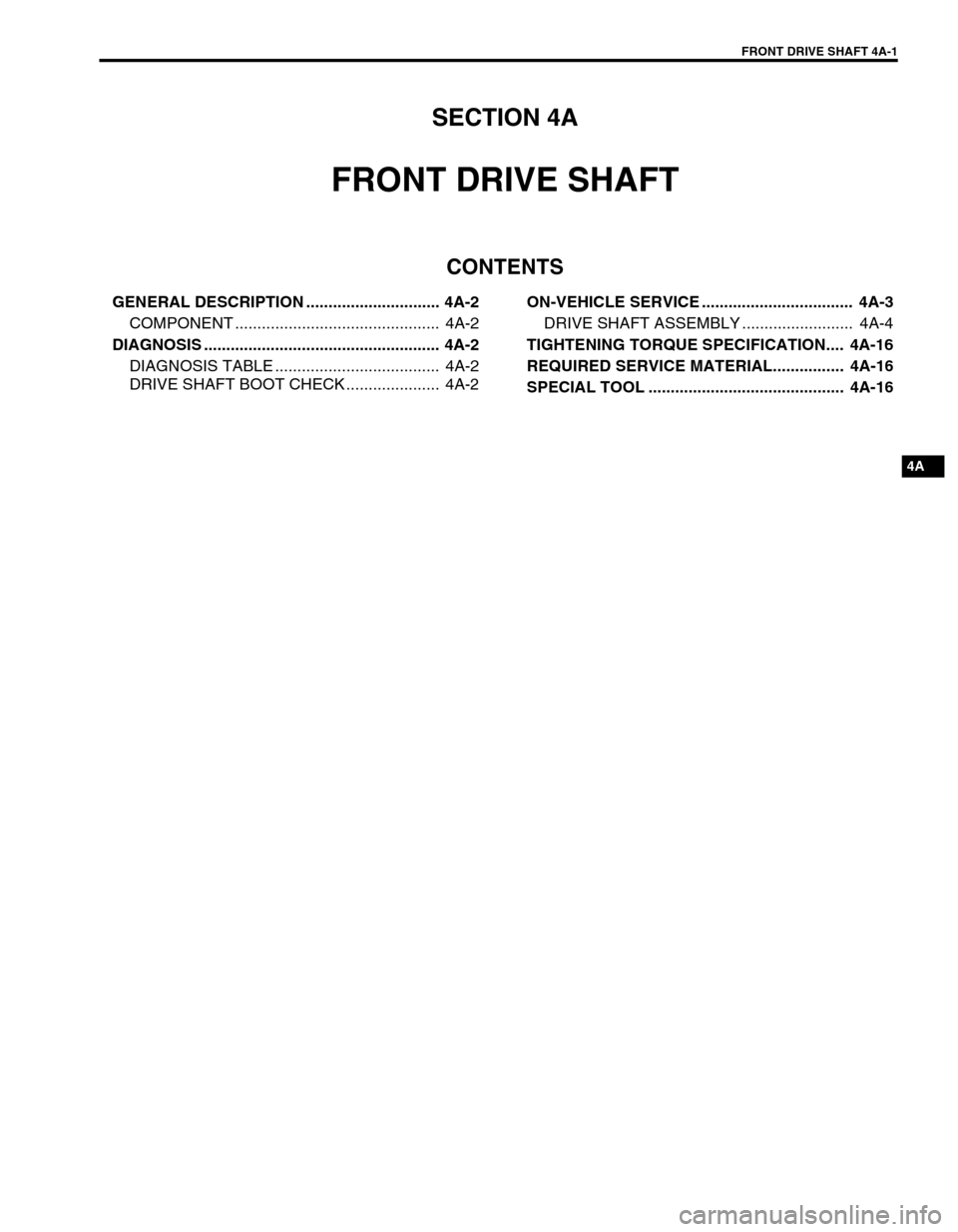
FRONT DRIVE SHAFT 4A-1
6F1
6F2
6G
6H
6K
7A
7A1
7B1
7C1
7D
7E
7F
4A
8C
8D
8E
9
10
10A
10B
SECTION 4A
FRONT DRIVE SHAFT
CONTENTS
GENERAL DESCRIPTION .............................. 4A-2
COMPONENT .............................................. 4A-2
DIAGNOSIS ..................................................... 4A-2
DIAGNOSIS TABLE ..................................... 4A-2
DRIVE SHAFT BOOT CHECK ..................... 4A-2ON-VEHICLE SERVICE .................................. 4A-3
DRIVE SHAFT ASSEMBLY ......................... 4A-4
TIGHTENING TORQUE SPECIFICATION.... 4A-16
REQUIRED SERVICE MATERIAL................ 4A-16
SPECIAL TOOL ............................................ 4A-16
Page 255 of 698
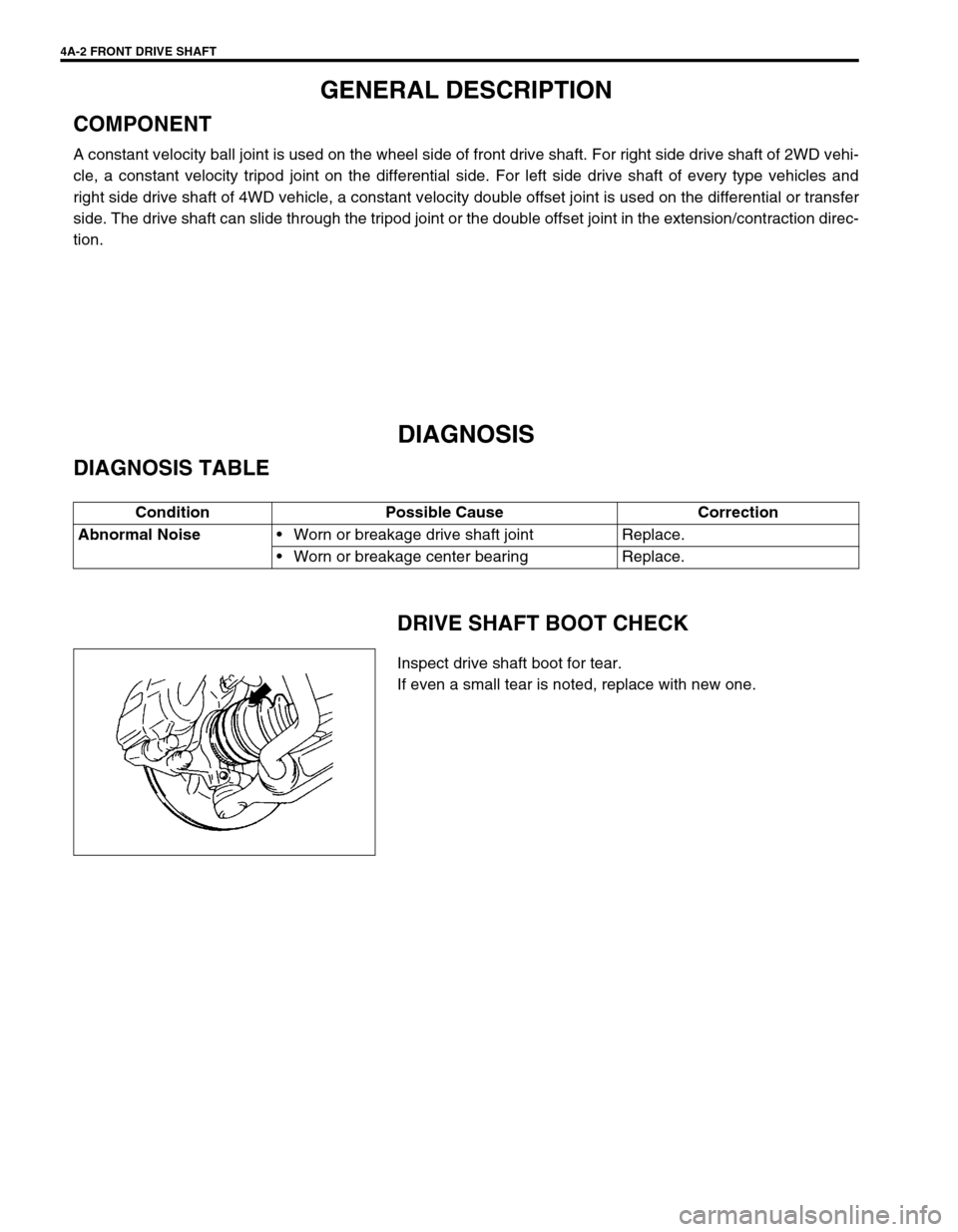
4A-2 FRONT DRIVE SHAFT
GENERAL DESCRIPTION
COMPONENT
A constant velocity ball joint is used on the wheel side of front drive shaft. For right side drive shaft of 2WD vehi-
cle, a constant velocity tripod joint on the differential side. For left side drive shaft of every type vehicles and
right side drive shaft of 4WD vehicle, a constant velocity double offset joint is used on the differential or transfer
side. The drive shaft can slide through the tripod joint or the double offset joint in the extension/contraction direc-
tion.
DIAGNOSIS
DIAGNOSIS TABLE
DRIVE SHAFT BOOT CHECK
Inspect drive shaft boot for tear.
If even a small tear is noted, replace with new one. Condition Possible Cause Correction
Abnormal Noise
Worn or breakage drive shaft joint Replace.
Worn or breakage center bearing Replace.
Page 256 of 698
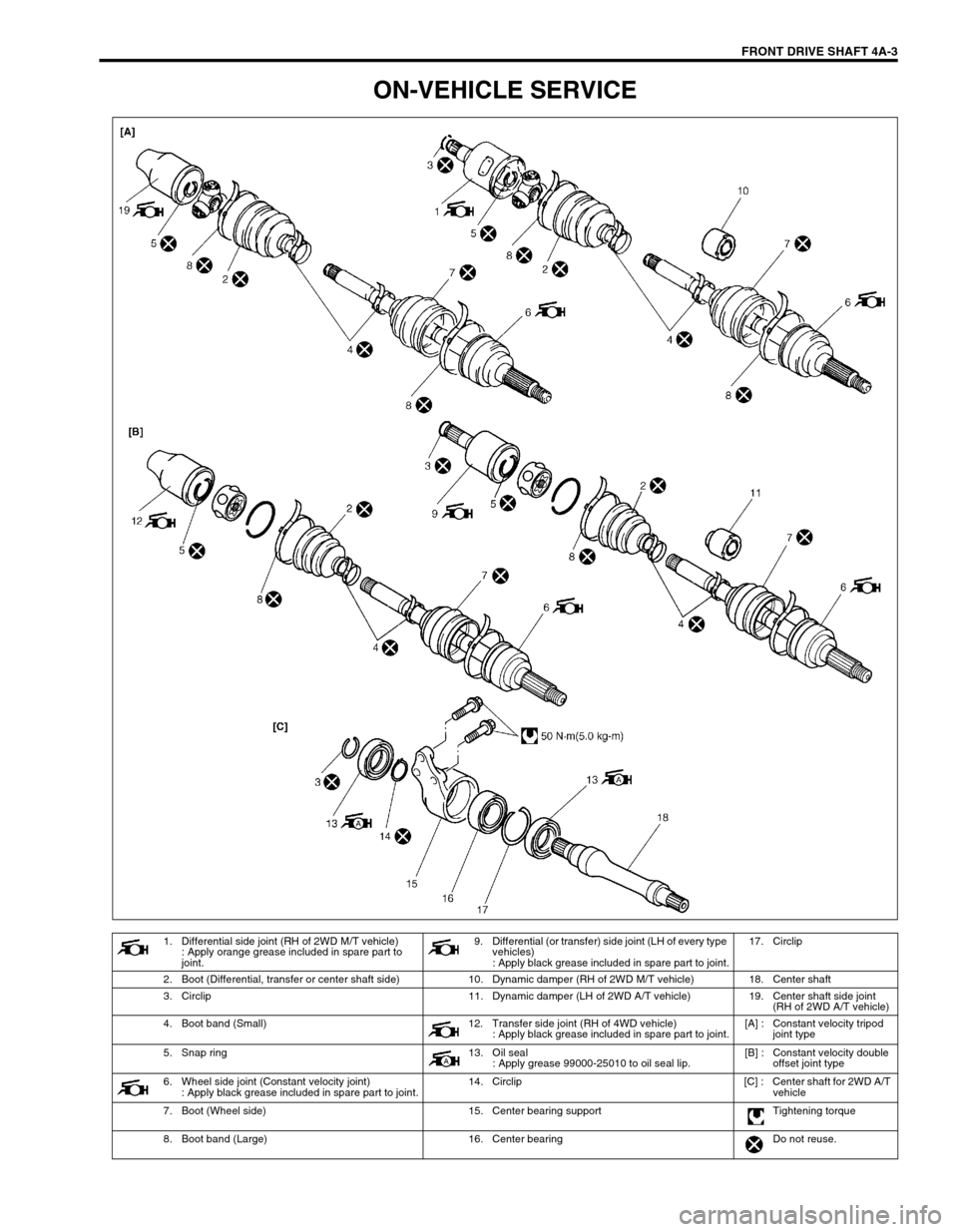
FRONT DRIVE SHAFT 4A-3
ON-VEHICLE SERVICE
1. Differential side joint (RH of 2WD M/T vehicle)
: Apply orange grease included in spare part to
joint.9. Differential (or transfer) side joint (LH of every type
vehicles)
: Apply black grease included in spare part to joint.17. Circlip
2. Boot (Differential, transfer or center shaft side) 10. Dynamic damper (RH of 2WD M/T vehicle) 18. Center shaft
3. Circlip 11. Dynamic damper (LH of 2WD A/T vehicle) 19. Center shaft side joint
(RH of 2WD A/T vehicle)
4. Boot band (Small) 12. Transfer side joint (RH of 4WD vehicle)
: Apply black grease included in spare part to joint.[A] : Constant velocity tripod
joint type
5. Snap ring 13. Oil seal
: Apply grease 99000-25010 to oil seal lip.[B] : Constant velocity double
offset joint type
6. Wheel side joint (Constant velocity joint)
: Apply black grease included in spare part to joint.14. Circlip [C] : Center shaft for 2WD A/T
vehicle
7. Boot (Wheel side) 15. Center bearing support Tightening torque
8. Boot band (Large) 16. Center bearing Do not reuse.
Page 257 of 698
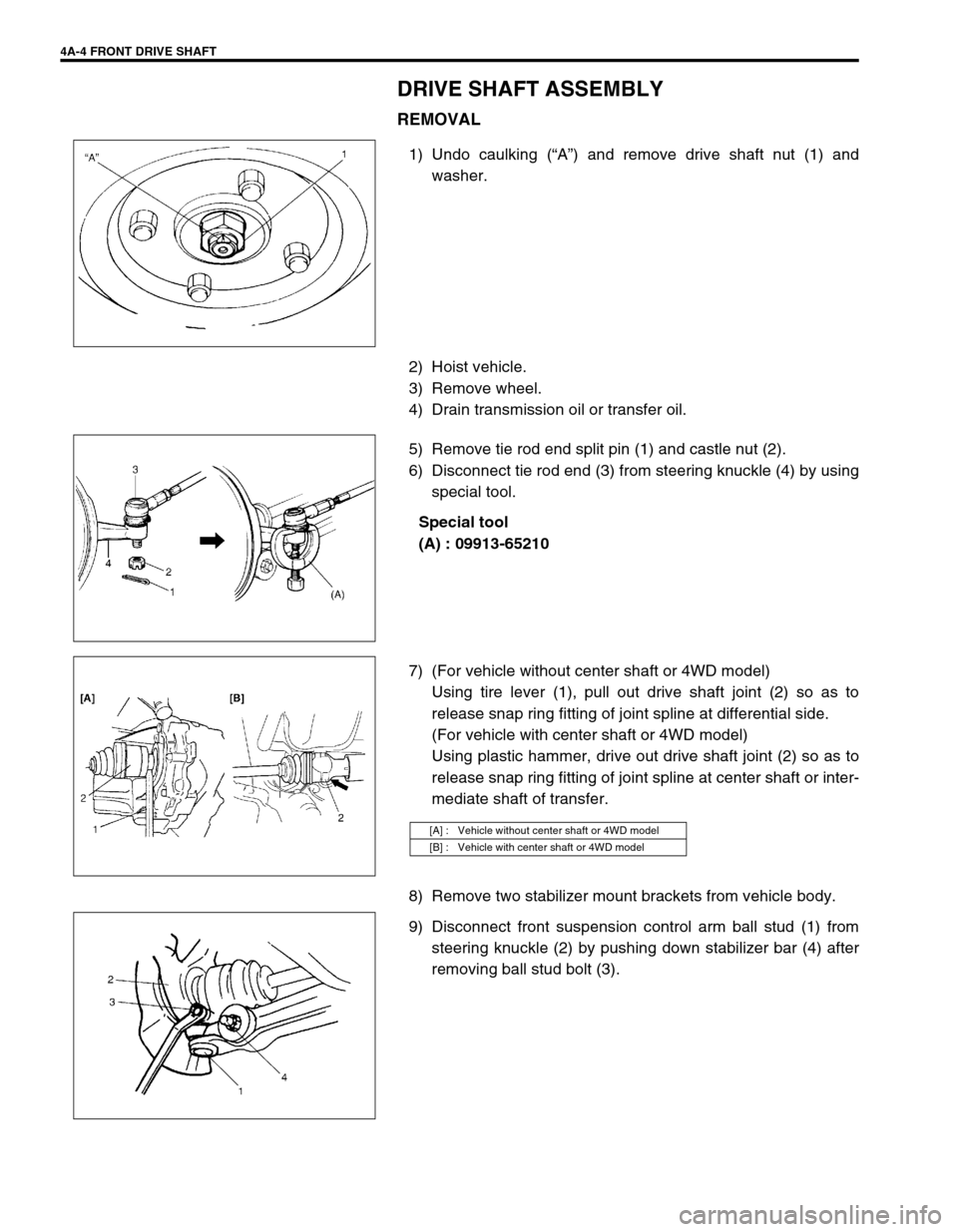
4A-4 FRONT DRIVE SHAFT
DRIVE SHAFT ASSEMBLY
REMOVAL
1) Undo caulking (“A”) and remove drive shaft nut (1) and
washer.
2) Hoist vehicle.
3) Remove wheel.
4) Drain transmission oil or transfer oil.
5) Remove tie rod end split pin (1) and castle nut (2).
6) Disconnect tie rod end (3) from steering knuckle (4) by using
special tool.
Special tool
(A) : 09913-65210
7) (For vehicle without center shaft or 4WD model)
Using tire lever (1), pull out drive shaft joint (2) so as to
release snap ring fitting of joint spline at differential side.
(For vehicle with center shaft or 4WD model)
Using plastic hammer, drive out drive shaft joint (2) so as to
release snap ring fitting of joint spline at center shaft or inter-
mediate shaft of transfer.
8) Remove two stabilizer mount brackets from vehicle body.
9) Disconnect front suspension control arm ball stud (1) from
steering knuckle (2) by pushing down stabilizer bar (4) after
removing ball stud bolt (3).
[A] : Vehicle without center shaft or 4WD model
[B] : Vehicle with center shaft or 4WD model
Page 258 of 698
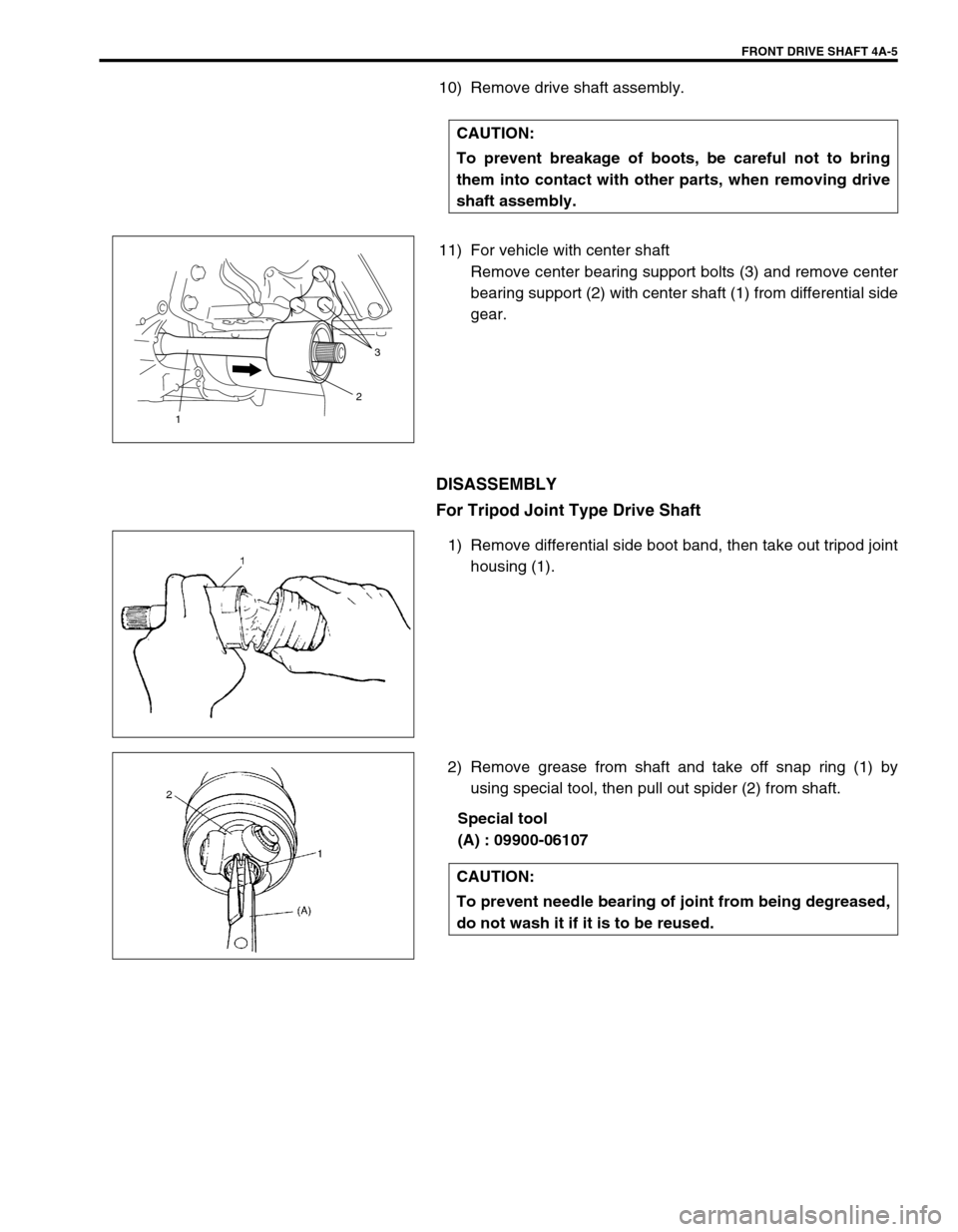
FRONT DRIVE SHAFT 4A-5
10) Remove drive shaft assembly.
11) For vehicle with center shaft
Remove center bearing support bolts (3) and remove center
bearing support (2) with center shaft (1) from differential side
gear.
DISASSEMBLY
For Tripod Joint Type Drive Shaft
1) Remove differential side boot band, then take out tripod joint
housing (1).
2) Remove grease from shaft and take off snap ring (1) by
using special tool, then pull out spider (2) from shaft.
Special tool
(A) : 09900-06107 CAUTION:
To prevent breakage of boots, be careful not to bring
them into contact with other parts, when removing drive
shaft assembly.
3
2
1
CAUTION:
To prevent needle bearing of joint from being degreased,
do not wash it if it is to be reused.
Page 259 of 698
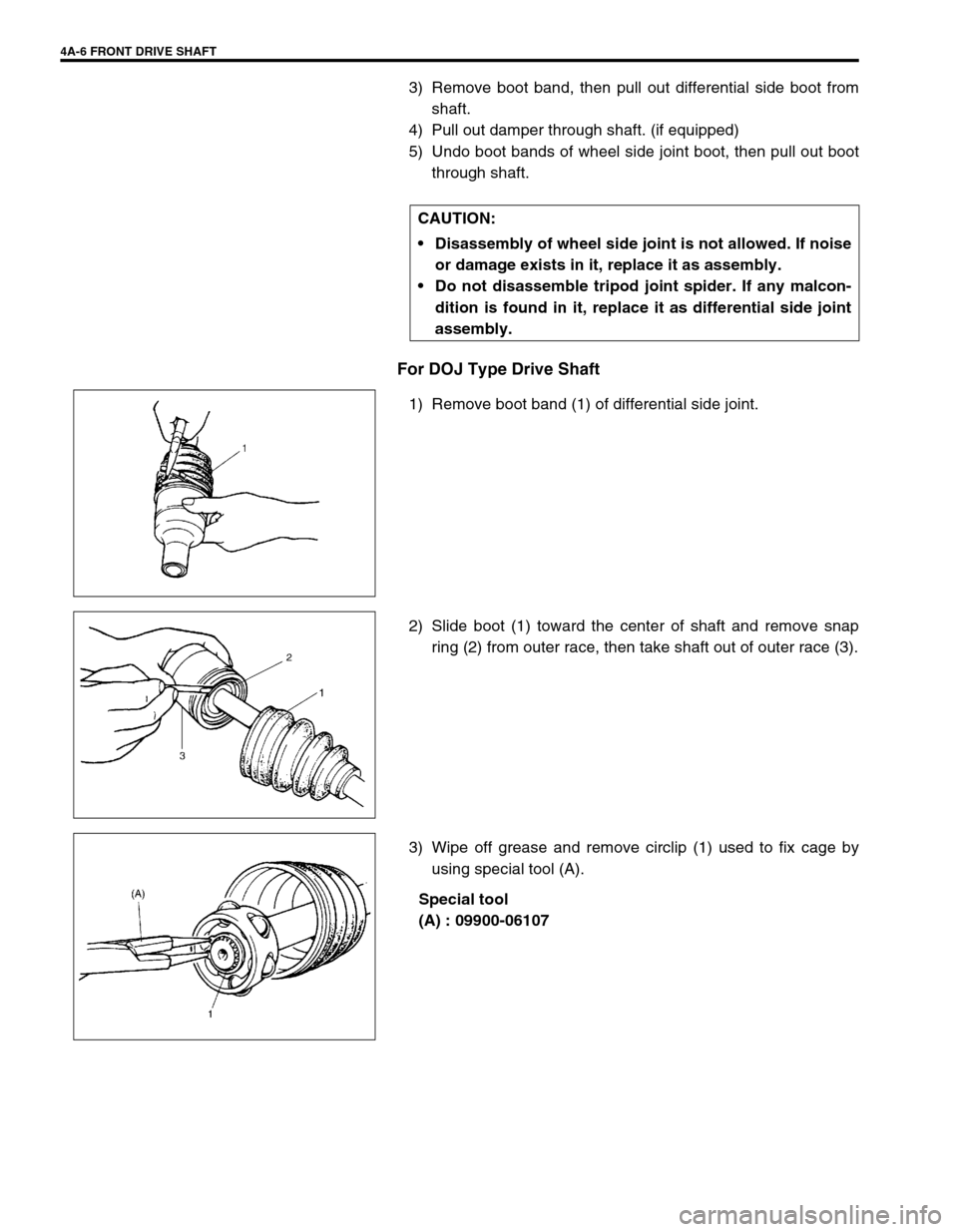
4A-6 FRONT DRIVE SHAFT
3) Remove boot band, then pull out differential side boot from
shaft.
4) Pull out damper through shaft. (if equipped)
5) Undo boot bands of wheel side joint boot, then pull out boot
through shaft.
For DOJ Type Drive Shaft
1) Remove boot band (1) of differential side joint.
2) Slide boot (1) toward the center of shaft and remove snap
ring (2) from outer race, then take shaft out of outer race (3).
3) Wipe off grease and remove circlip (1) used to fix cage by
using special tool (A).
Special tool
(A) : 09900-06107 CAUTION:
Disassembly of wheel side joint is not allowed. If noise
or damage exists in it, replace it as assembly.
Do not disassemble tripod joint spider. If any malcon-
dition is found in it, replace it as differential side joint
assembly.
Page 260 of 698
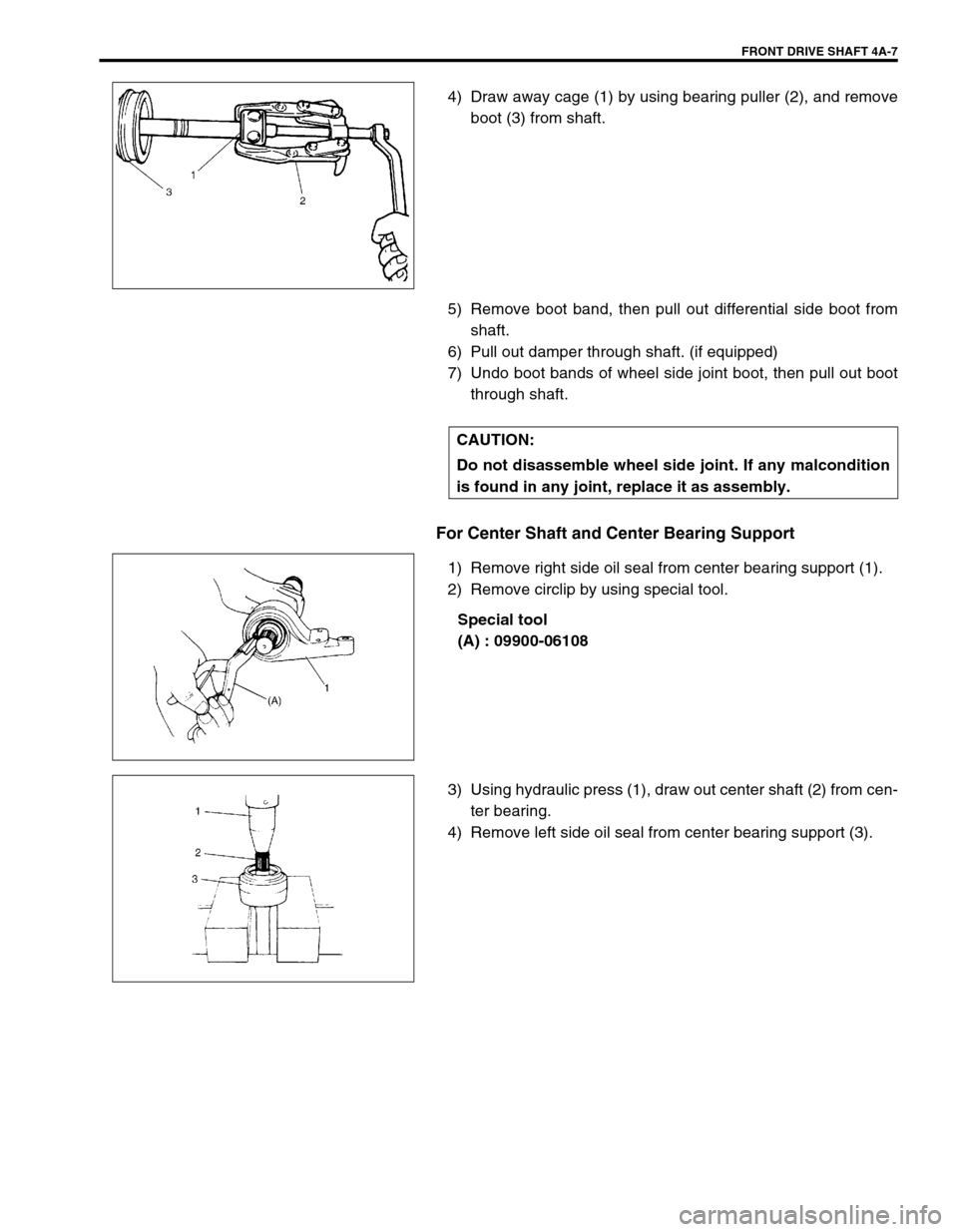
FRONT DRIVE SHAFT 4A-7
4) Draw away cage (1) by using bearing puller (2), and remove
boot (3) from shaft.
5) Remove boot band, then pull out differential side boot from
shaft.
6) Pull out damper through shaft. (if equipped)
7) Undo boot bands of wheel side joint boot, then pull out boot
through shaft.
For Center Shaft and Center Bearing Support
1) Remove right side oil seal from center bearing support (1).
2) Remove circlip by using special tool.
Special tool
(A) : 09900-06108
3) Using hydraulic press (1), draw out center shaft (2) from cen-
ter bearing.
4) Remove left side oil seal from center bearing support (3).
CAUTION:
Do not disassemble wheel side joint. If any malcondition
is found in any joint, replace it as assembly.