TOYOTA RAV4 2006 Service Repair Manual
Manufacturer: TOYOTA, Model Year: 2006, Model line: RAV4, Model: TOYOTA RAV4 2006Pages: 2000, PDF Size: 45.84 MB
Page 1251 of 2000
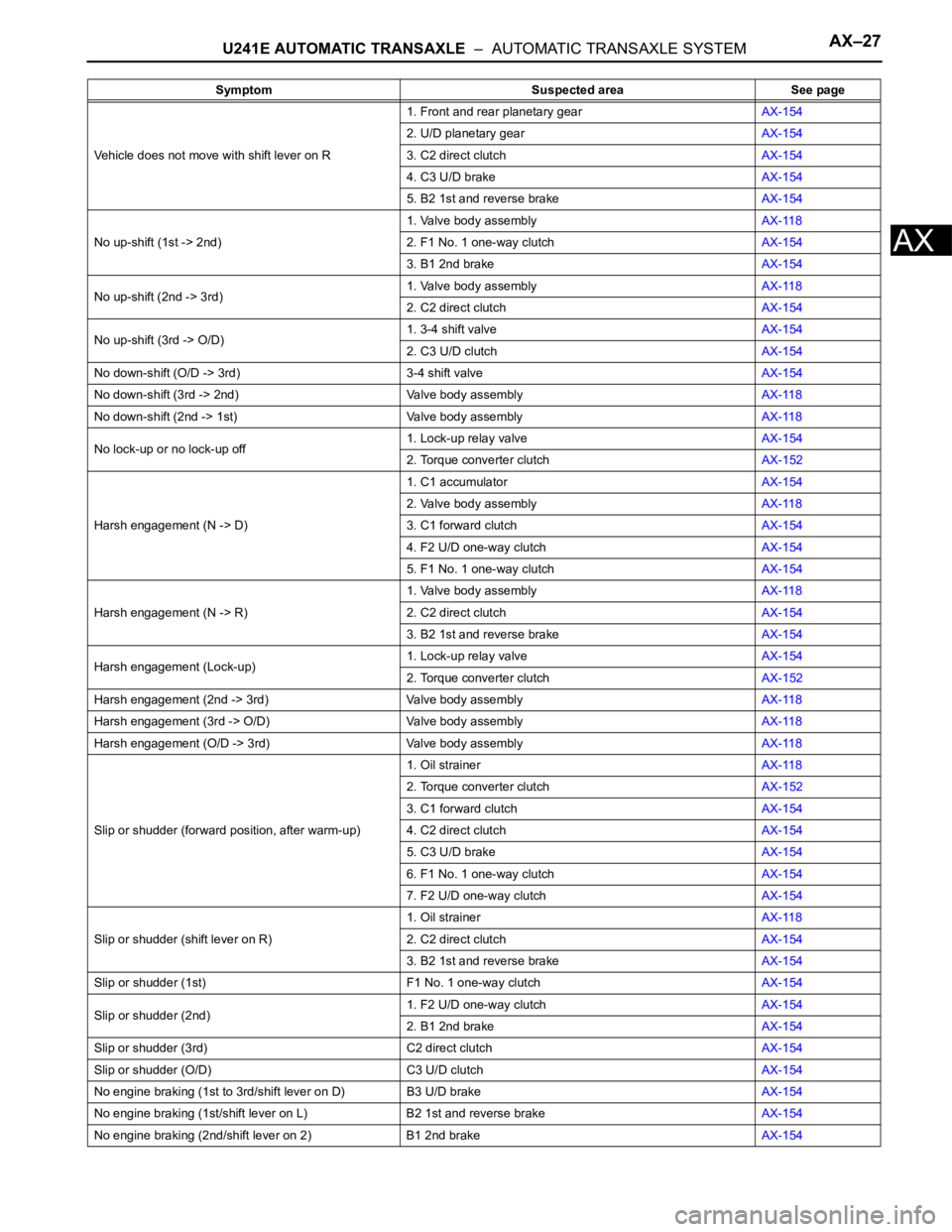
U241E AUTOMATIC TRANSAXLE – AUTOMATIC TRANSAXLE SYSTEMAX–27
AX
Vehicle does not move with shift lever on R1. Front and rear planetary gearAX-154
2. U/D planetary gearAX-154
3. C2 direct clutchAX-154
4. C3 U/D brakeAX-154
5. B2 1st and reverse brakeAX-154
No up-shift (1st -> 2nd)1. Valve body assemblyAX-118
2. F1 No. 1 one-way clutchAX-154
3. B1 2nd brakeAX-154
No up-shift (2nd -> 3rd)1. Valve body assemblyAX-118
2. C2 direct clutchAX-154
No up-shift (3rd -> O/D)1. 3-4 shift valveAX-154
2. C3 U/D clutchAX-154
No down-shift (O/D -> 3rd) 3-4 shift valveAX-154
No down-shift (3rd -> 2nd) Valve body assemblyAX-118
No down-shift (2nd -> 1st) Valve body assemblyAX-118
No lock-up or no lock-up off1. Lock-up relay valveAX-154
2. Torque converter clutchAX-152
Harsh engagement (N -> D)1. C1 accumulatorAX-154
2. Valve body assemblyAX-118
3. C1 forward clutchAX-154
4. F2 U/D one-way clutchAX-154
5. F1 No. 1 one-way clutchAX-154
Harsh engagement (N -> R)1. Valve body assemblyAX-118
2. C2 direct clutchAX-154
3. B2 1st and reverse brakeAX-154
Harsh engagement (Lock-up)1. Lock-up relay valveAX-154
2. Torque converter clutchAX-152
Harsh engagement (2nd -> 3rd) Valve body assemblyAX-118
Harsh engagement (3rd -> O/D) Valve body assemblyAX-118
Harsh engagement (O/D -> 3rd) Valve body assemblyAX-118
Slip or shudder (forward position, after warm-up)1. Oil strainerAX-118
2. Torque converter clutchAX-152
3. C1 forward clutchAX-154
4. C2 direct clutchAX-154
5. C3 U/D brakeAX-154
6. F1 No. 1 one-way clutchAX-154
7. F2 U/D one-way clutchAX-154
Slip or shudder (shift lever on R)1. Oil strainerAX-118
2. C2 direct clutchAX-154
3. B2 1st and reverse brakeAX-154
Slip or shudder (1st) F1 No. 1 one-way clutchAX-154
Slip or shudder (2nd)1. F2 U/D one-way clutchAX-154
2. B1 2nd brakeAX-154
Slip or shudder (3rd) C2 direct clutchAX-154
Slip or shudder (O/D) C3 U/D clutchAX-154
No engine braking (1st to 3rd/shift lever on D) B3 U/D brakeAX-154
No engine braking (1st/shift lever on L) B2 1st and reverse brakeAX-154
No engine braking (2nd/shift lever on 2) B1 2nd brakeAX-154 Symptom Suspected area See page
Page 1252 of 2000
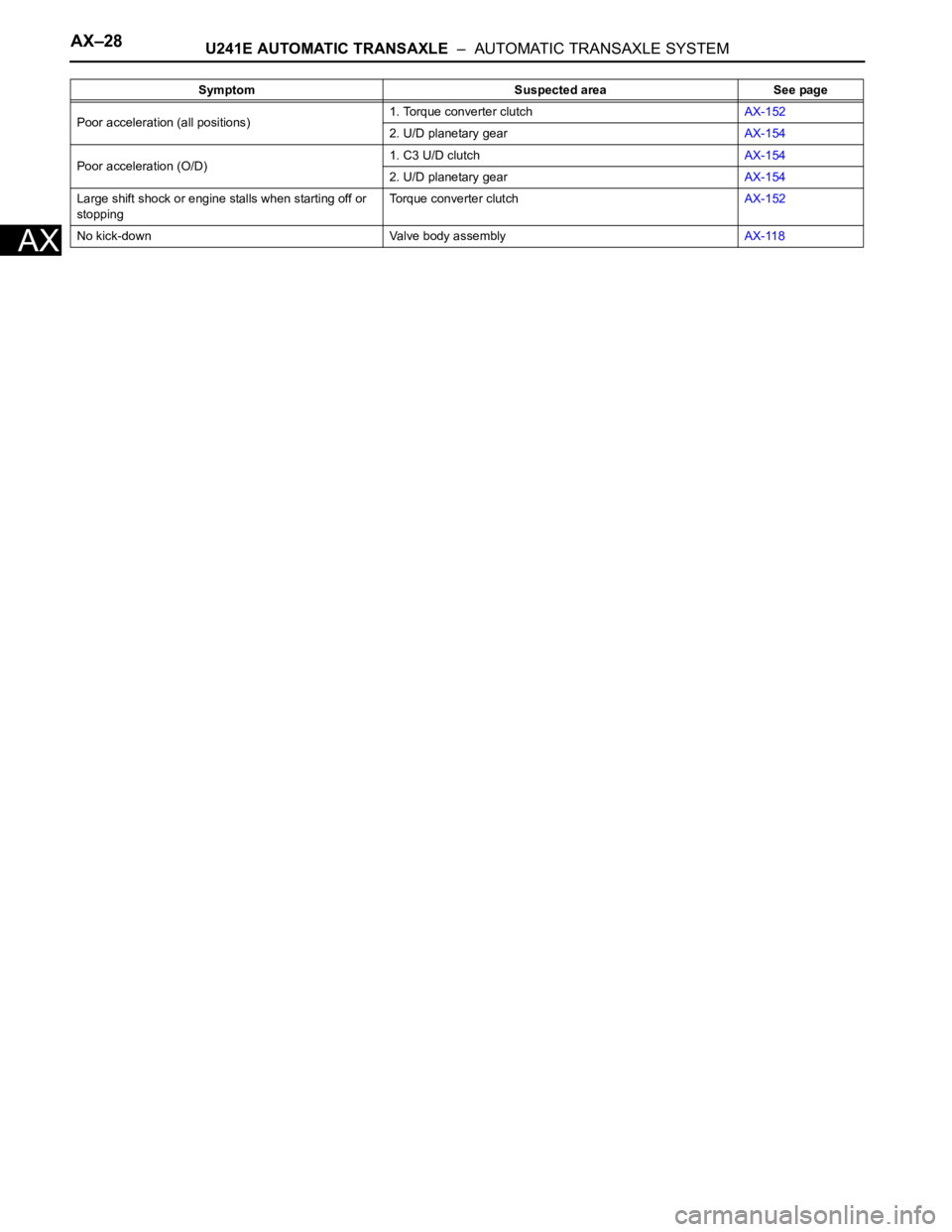
AX–28U241E AUTOMATIC TRANSAXLE – AUTOMATIC TRANSAXLE SYSTEM
AX
Poor acceleration (all positions)1. Torque converter clutchAX-152
2. U/D planetary gearAX-154
Poor acceleration (O/D)1. C3 U/D clutchAX-154
2. U/D planetary gearAX-154
Large shift shock or engine stalls when starting off or
stoppingTorque converter clutchAX-152
No kick-down Valve body assemblyAX-118 Symptom Suspected area See page
Page 1253 of 2000
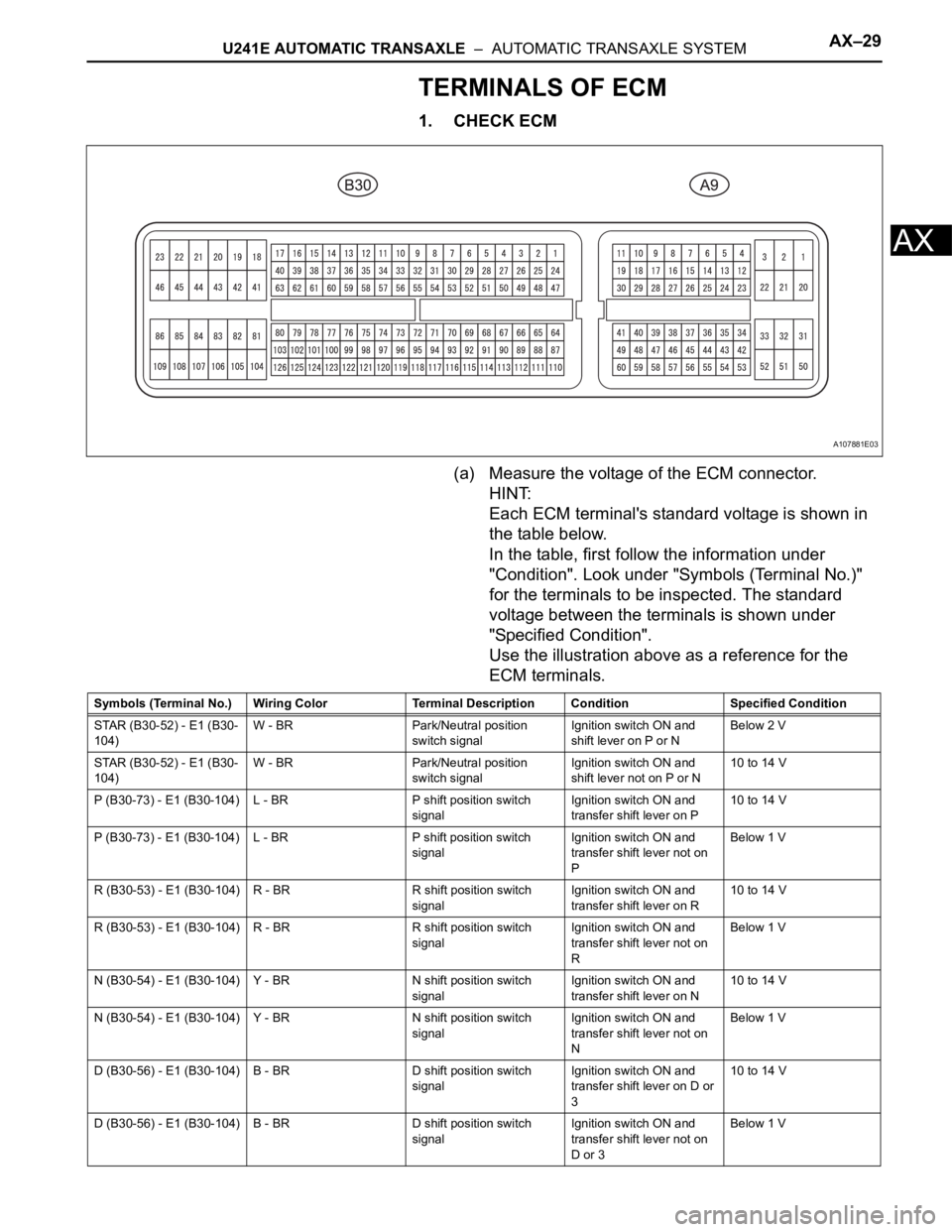
U241E AUTOMATIC TRANSAXLE – AUTOMATIC TRANSAXLE SYSTEMAX–29
AX
TERMINALS OF ECM
1. CHECK ECM
(a) Measure the voltage of the ECM connector.
HINT:
Each ECM terminal's standard voltage is shown in
the table below.
In the table, first follow the information under
"Condition". Look under "Symbols (Terminal No.)"
for the terminals to be inspected. The standard
voltage between the terminals is shown under
"Specified Condition".
Use the illustration above as a reference for the
ECM terminals.
A107881E03
Symbols (Terminal No.) Wiring Color Terminal Description ConditionSpecified Condition
STAR (B30-52) - E1 (B30-
104)W - BR Park/Neutral position
switch signalIgnition switch ON and
shift lever on P or NBelow 2 V
STAR (B30-52) - E1 (B30-
104)W - BR Park/Neutral position
switch signalIgnition switch ON and
shift lever not on P or N10 to 14 V
P (B30-73) - E1 (B30-104) L - BR P shift position switch
signalIgnition switch ON and
transfer shift lever on P10 to 14 V
P (B30-73) - E1 (B30-104) L - BR P shift position switch
signalIgnition switch ON and
transfer shift lever not on
PBelow 1 V
R (B30-53) - E1 (B30-104) R - BR R shift position switch
signalIgnition switch ON and
transfer shift lever on R10 to 14 V
R (B30-53) - E1 (B30-104) R - BR R shift position switch
signalIgnition switch ON and
transfer shift lever not on
RBelow 1 V
N (B30-54) - E1 (B30-104) Y - BR N shift position switch
signalIgnition switch ON and
transfer shift lever on N10 to 14 V
N (B30-54) - E1 (B30-104) Y - BR N shift position switch
signalIgnition switch ON and
transfer shift lever not on
NBelow 1 V
D (B30-56) - E1 (B30-104) B - BR D shift position switch
signalIgnition switch ON and
transfer shift lever on D or
310 to 14 V
D (B30-56) - E1 (B30-104) B - BR D shift position switch
signalIgnition switch ON and
transfer shift lever not on
D or 3Below 1 V
Page 1254 of 2000
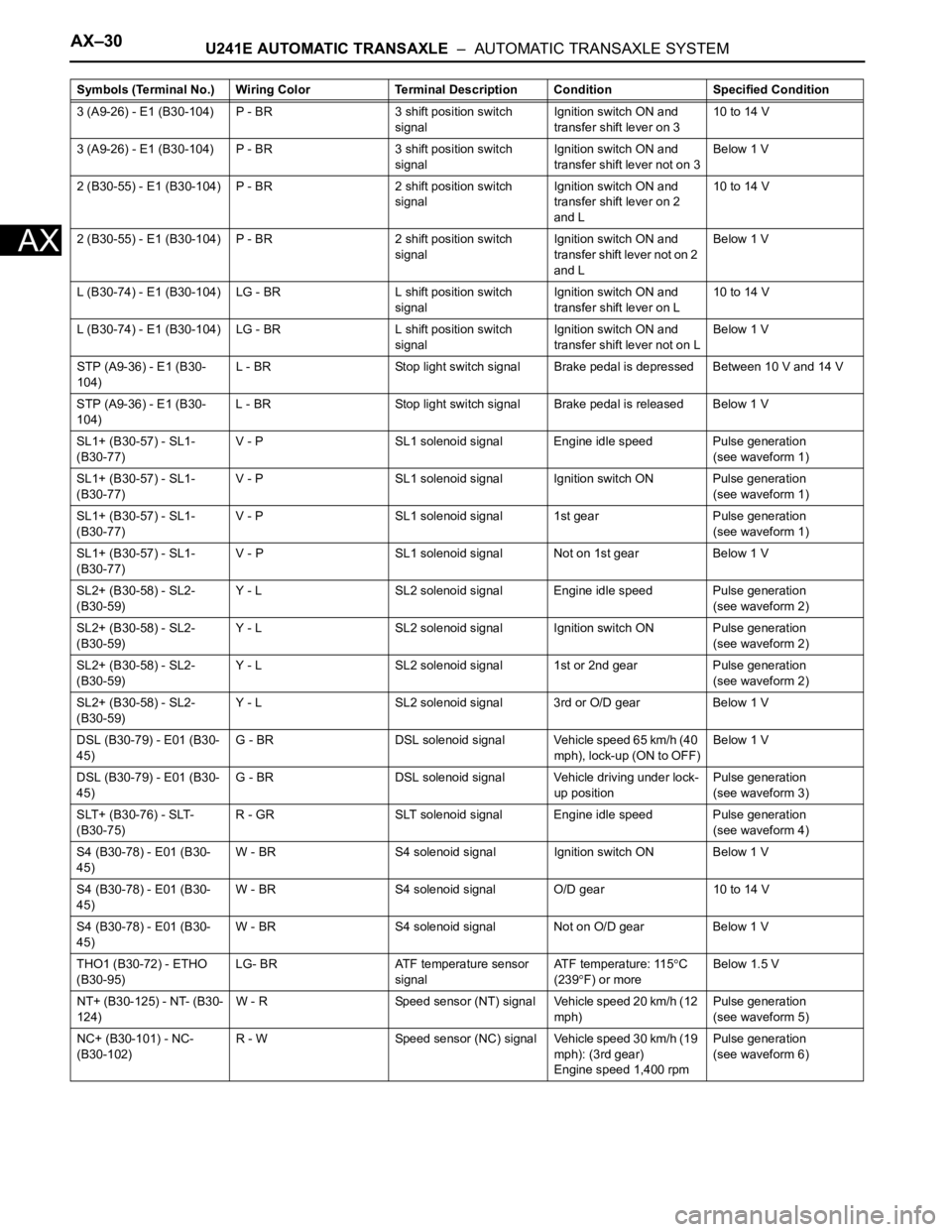
AX–30U241E AUTOMATIC TRANSAXLE – AUTOMATIC TRANSAXLE SYSTEM
AX
3 (A9-26) - E1 (B30-104) P - BR 3 shift position switch
signalIgnition switch ON and
transfer shift lever on 310 to 14 V
3 (A9-26) - E1 (B30-104) P - BR 3 shift position switch
signalIgnition switch ON and
transfer shift lever not on 3Below 1 V
2 (B30-55) - E1 (B30-104) P - BR 2 shift position switch
signalIgnition switch ON and
transfer shift lever on 2
and L10 to 14 V
2 (B30-55) - E1 (B30-104) P - BR 2 shift position switch
signalIgnition switch ON and
transfer shift lever not on 2
and LBelow 1 V
L (B30-74) - E1 (B30-104) LG - BR L shift position switch
signalIgnition switch ON and
transfer shift lever on L10 to 14 V
L (B30-74) - E1 (B30-104) LG - BR L shift position switch
signalIgnition switch ON and
transfer shift lever not on LBelow 1 V
STP (A9-36) - E1 (B30-
104)L - BR Stop light switch signal Brake pedal is depressed Between 10 V and 14 V
STP (A9-36) - E1 (B30-
104)L - BR Stop light switch signal Brake pedal is released Below 1 V
SL1+ (B30-57) - SL1-
(B30-77)V - P SL1 solenoid signal Engine idle speed Pulse generation
(see waveform 1)
SL1+ (B30-57) - SL1-
(B30-77)V - P SL1 solenoid signal Ignition switch ON Pulse generation
(see waveform 1)
SL1+ (B30-57) - SL1-
(B30-77)V - P SL1 solenoid signal 1st gear Pulse generation
(see waveform 1)
SL1+ (B30-57) - SL1-
(B30-77)V - P SL1 solenoid signal Not on 1st gear Below 1 V
SL2+ (B30-58) - SL2-
(B30-59)Y - L SL2 solenoid signal Engine idle speed Pulse generation
(see waveform 2)
SL2+ (B30-58) - SL2-
(B30-59)Y - L SL2 solenoid signal Ignition switch ON Pulse generation
(see waveform 2)
SL2+ (B30-58) - SL2-
(B30-59)Y - L SL2 solenoid signal 1st or 2nd gear Pulse generation
(see waveform 2)
SL2+ (B30-58) - SL2-
(B30-59)Y - L SL2 solenoid signal 3rd or O/D gear Below 1 V
DSL (B30-79) - E01 (B30-
45)G - BR DSL solenoid signal Vehicle speed 65 km/h (40
mph), lock-up (ON to OFF)Below 1 V
DSL (B30-79) - E01 (B30-
45)G - BR DSL solenoid signal Vehicle driving under lock-
up positionPulse generation
(see waveform 3)
SLT+ (B30-76) - SLT-
(B30-75)R - GR SLT solenoid signal Engine idle speed Pulse generation
(see waveform 4)
S4 (B30-78) - E01 (B30-
45)W - BR S4 solenoid signal Ignition switch ON Below 1 V
S4 (B30-78) - E01 (B30-
45)W - BR S4 solenoid signal O/D gear 10 to 14 V
S4 (B30-78) - E01 (B30-
45)W - BR S4 solenoid signal Not on O/D gear Below 1 V
THO1 (B30-72) - ETHO
(B30-95)LG- BR ATF temperature sensor
signalATF temperature: 115
C
(239F) or moreBelow 1.5 V
NT+ (B30-125) - NT- (B30-
124)W - R Speed sensor (NT) signal Vehicle speed 20 km/h (12
mph)Pulse generation
(see waveform 5)
NC+ (B30-101) - NC-
(B30-102)R - W Speed sensor (NC) signal Vehicle speed 30 km/h (19
mph): (3rd gear)
Engine speed 1,400 rpmPulse generation
(see waveform 6) Symbols (Terminal No.) Wiring Color Terminal Description ConditionSpecified Condition
Page 1255 of 2000
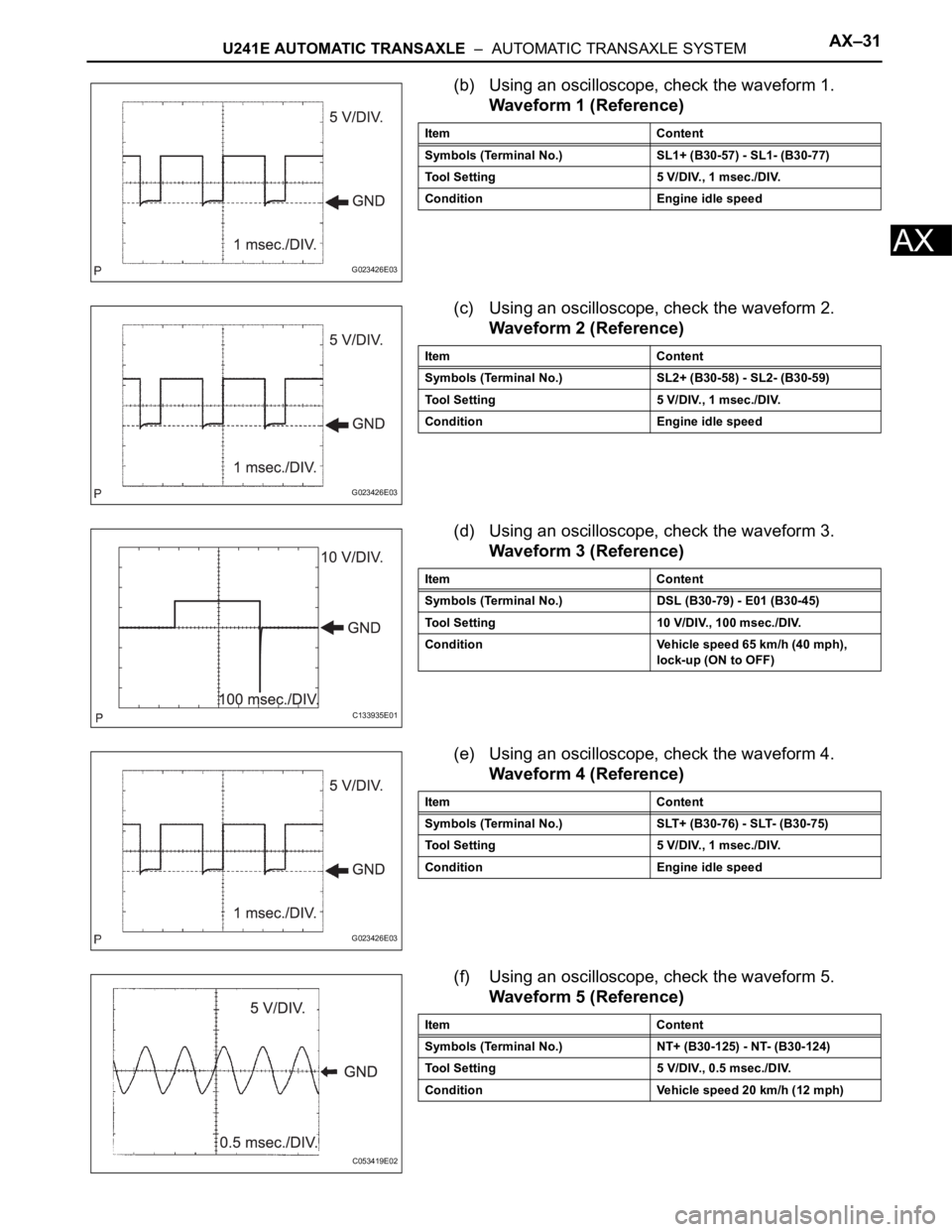
U241E AUTOMATIC TRANSAXLE – AUTOMATIC TRANSAXLE SYSTEMAX–31
AX
(b) Using an oscilloscope, check the waveform 1.
Waveform 1 (Reference)
(c) Using an oscilloscope, check the waveform 2.
Waveform 2 (Reference)
(d) Using an oscilloscope, check the waveform 3.
Waveform 3 (Reference)
(e) Using an oscilloscope, check the waveform 4.
Waveform 4 (Reference)
(f) Using an oscilloscope, check the waveform 5.
Waveform 5 (Reference)
G023426E03
Item Content
Symbols (Terminal No.) SL1+ (B30-57) - SL1- (B30-77)
Tool Setting 5 V/DIV., 1 msec./DIV.
Condition Engine idle speed
G023426E03
Item Content
Symbols (Terminal No.) SL2+ (B30-58) - SL2- (B30-59)
Tool Setting 5 V/DIV., 1 msec./DIV.
Condition Engine idle speed
C133935E01
Item Content
Symbols (Terminal No.) DSL (B30-79) - E01 (B30-45)
Tool Setting 10 V/DIV., 100 msec./DIV.
Condition Vehicle speed 65 km/h (40 mph),
lock-up (ON to OFF)
G023426E03
Item Content
Symbols (Terminal No.) SLT+ (B30-76) - SLT- (B30-75)
Tool Setting 5 V/DIV., 1 msec./DIV.
Condition Engine idle speed
C053419E02
Item Content
Symbols (Terminal No.) NT+ (B30-125) - NT- (B30-124)
Tool Setting 5 V/DIV., 0.5 msec./DIV.
Condition Vehicle speed 20 km/h (12 mph)
Page 1256 of 2000
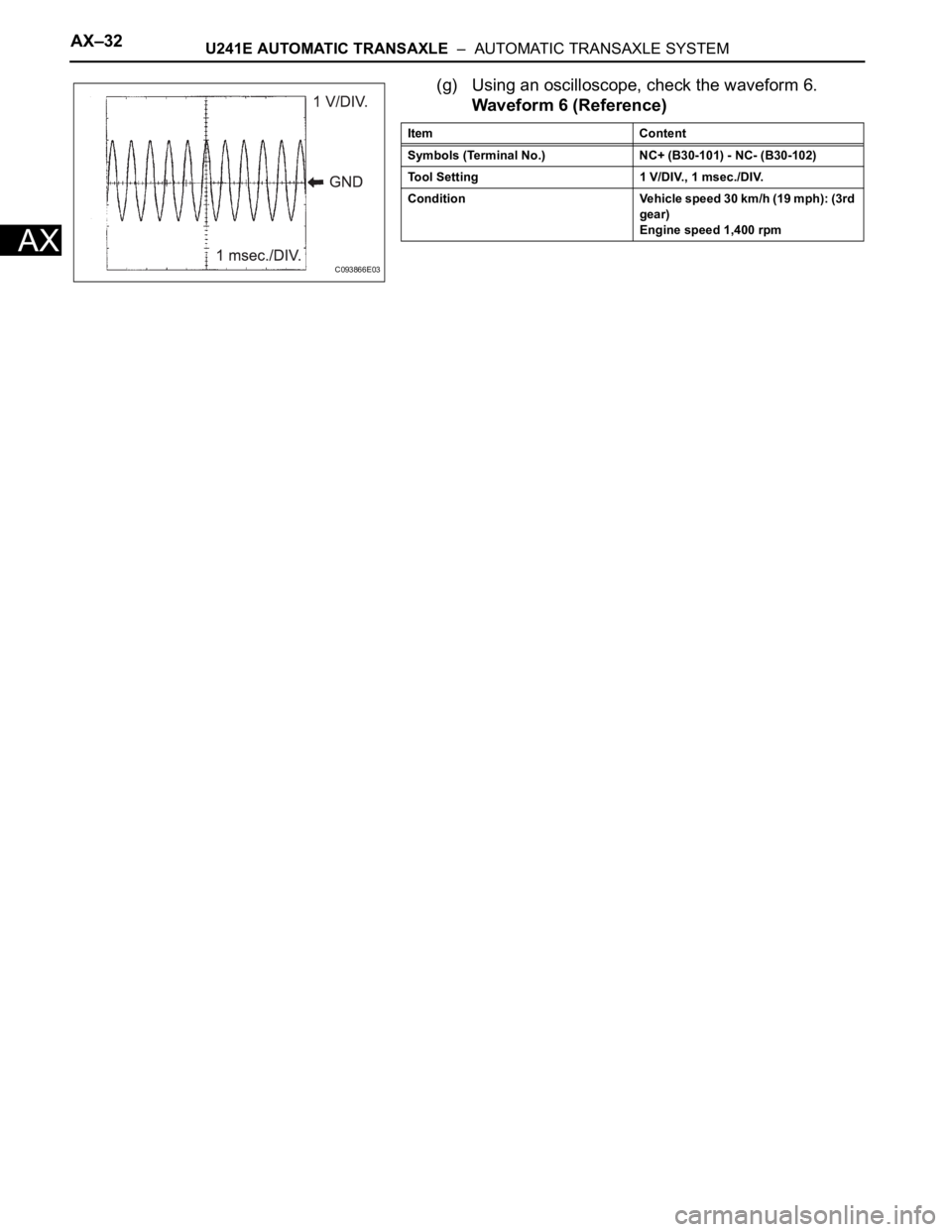
AX–32U241E AUTOMATIC TRANSAXLE – AUTOMATIC TRANSAXLE SYSTEM
AX
(g) Using an oscilloscope, check the waveform 6.
Waveform 6 (Reference)
C093866E03
Item Content
Symbols (Terminal No.) NC+ (B30-101) - NC- (B30-102)
Tool Setting 1 V/DIV., 1 msec./DIV.
Condition Vehicle speed 30 km/h (19 mph): (3rd
gear)
Engine speed 1,400 rpm
Page 1257 of 2000
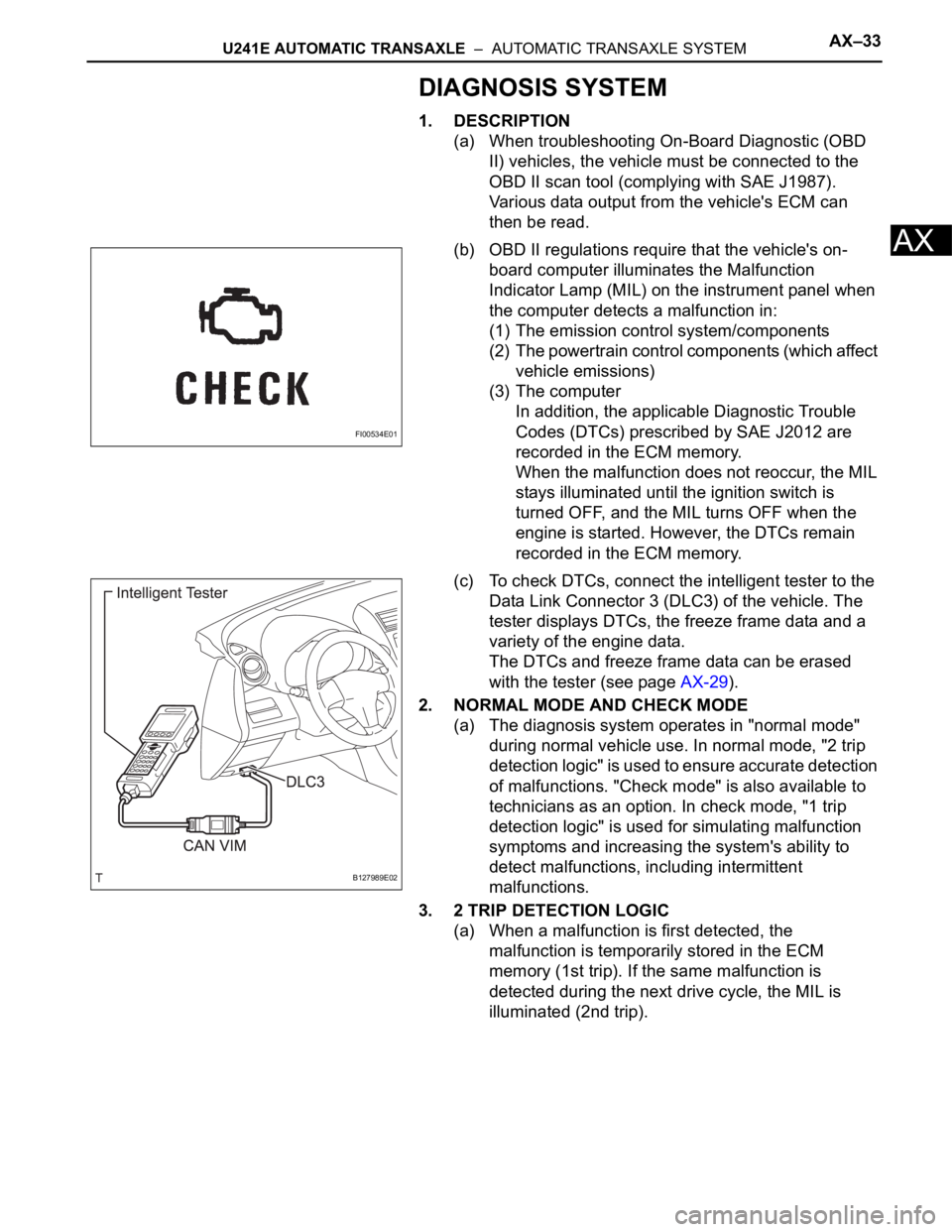
U241E AUTOMATIC TRANSAXLE – AUTOMATIC TRANSAXLE SYSTEMAX–33
AX
DIAGNOSIS SYSTEM
1. DESCRIPTION
(a) When troubleshooting On-Board Diagnostic (OBD
II) vehicles, the vehicle must be connected to the
OBD II scan tool (complying with SAE J1987).
Various data output from the vehicle's ECM can
then be read.
(b) OBD II regulations require that the vehicle's on-
board computer illuminates the Malfunction
Indicator Lamp (MIL) on the instrument panel when
the computer detects a malfunction in:
(1) The emission control system/components
(2) The powertrain control components (which affect
vehicle emissions)
(3) The computer
In addition, the applicable Diagnostic Trouble
Codes (DTCs) prescribed by SAE J2012 are
recorded in the ECM memory.
When the malfunction does not reoccur, the MIL
stays illuminated until the ignition switch is
turned OFF, and the MIL turns OFF when the
engine is started. However, the DTCs remain
recorded in the ECM memory.
(c) To check DTCs, connect the intelligent tester to the
Data Link Connector 3 (DLC3) of the vehicle. The
tester displays DTCs, the freeze frame data and a
variety of the engine data.
The DTCs and freeze frame data can be erased
with the tester (see page AX-29).
2. NORMAL MODE AND CHECK MODE
(a) The diagnosis system operates in "normal mode"
during normal vehicle use. In normal mode, "2 trip
detection logic" is used to ensure accurate detection
of malfunctions. "Check mode" is also available to
technicians as an option. In check mode, "1 trip
detection logic" is used for simulating malfunction
symptoms and increasing the system's ability to
detect malfunctions, including intermittent
malfunctions.
3. 2 TRIP DETECTION LOGIC
(a) When a malfunction is first detected, the
malfunction is temporarily stored in the ECM
memory (1st trip). If the same malfunction is
detected during the next drive cycle, the MIL is
illuminated (2nd trip).
FI00534E01
B127989E02
Page 1258 of 2000
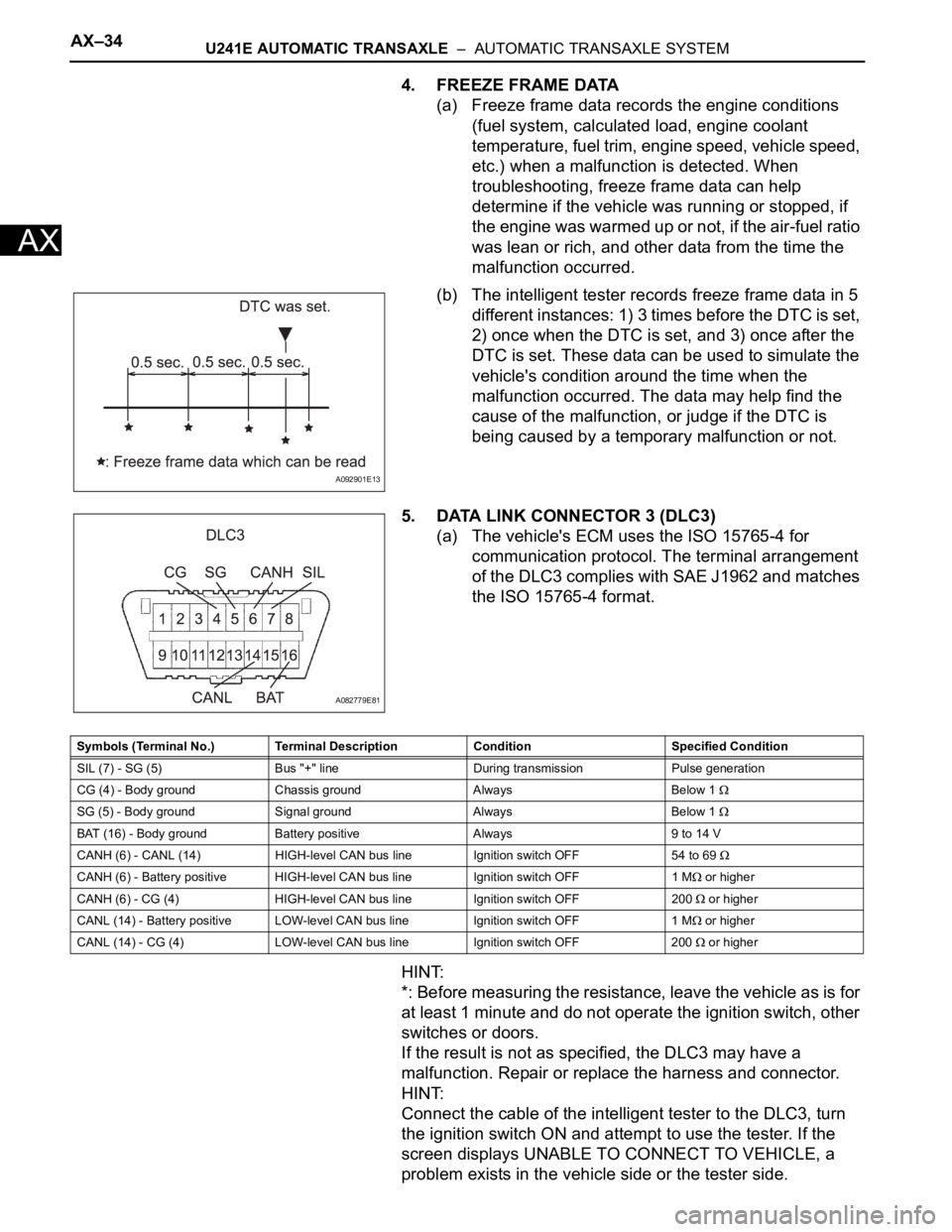
AX–34U241E AUTOMATIC TRANSAXLE – AUTOMATIC TRANSAXLE SYSTEM
AX
4. FREEZE FRAME DATA
(a) Freeze frame data records the engine conditions
(fuel system, calculated load, engine coolant
temperature, fuel trim, engine speed, vehicle speed,
etc.) when a malfunction is detected. When
troubleshooting, freeze frame data can help
determine if the vehicle was running or stopped, if
the engine was warmed up or not, if the air-fuel ratio
was lean or rich, and other data from the time the
malfunction occurred.
(b) The intelligent tester records freeze frame data in 5
different instances: 1) 3 times before the DTC is set,
2) once when the DTC is set, and 3) once after the
DTC is set. These data can be used to simulate the
vehicle's condition around the time when the
malfunction occurred. The data may help find the
cause of the malfunction, or judge if the DTC is
being caused by a temporary malfunction or not.
5. DATA LINK CONNECTOR 3 (DLC3)
(a) The vehicle's ECM uses the ISO 15765-4 for
communication protocol. The terminal arrangement
of the DLC3 complies with SAE J1962 and matches
the ISO 15765-4 format.
HINT:
*: Before measuring the resistance, leave the vehicle as is for
at least 1 minute and do not operate the ignition switch, other
switches or doors.
If the result is not as specified, the DLC3 may have a
malfunction. Repair or replace the harness and connector.
HINT:
Connect the cable of the intelligent tester to the DLC3, turn
the ignition switch ON and attempt to use the tester. If the
screen displays UNABLE TO CONNECT TO VEHICLE, a
problem exists in the vehicle side or the tester side.
A092901E13
A082779E81
Symbols (Terminal No.) Terminal Description Condition Specified Condition
SIL (7) - SG (5) Bus "+" line During transmission Pulse generation
CG (4) - Body ground Chassis ground Always Below 1
SG (5) - Body ground Signal ground Always Below 1
BAT (16) - Body ground Battery positive Always 9 to 14 V
CANH (6) - CANL (14) HIGH-level CAN bus line Ignition switch OFF 54 to 69
CANH (6) - Battery positive HIGH-level CAN bus line Ignition switch OFF 1 M or higher
CANH (6) - CG (4) HIGH-level CAN bus line Ignition switch OFF 200
or higher
CANL (14) - Battery positive LOW-level CAN bus line Ignition switch OFF 1 M
or higher
CANL (14) - CG (4) LOW-level CAN bus line Ignition switch OFF 200
or higher
Page 1259 of 2000
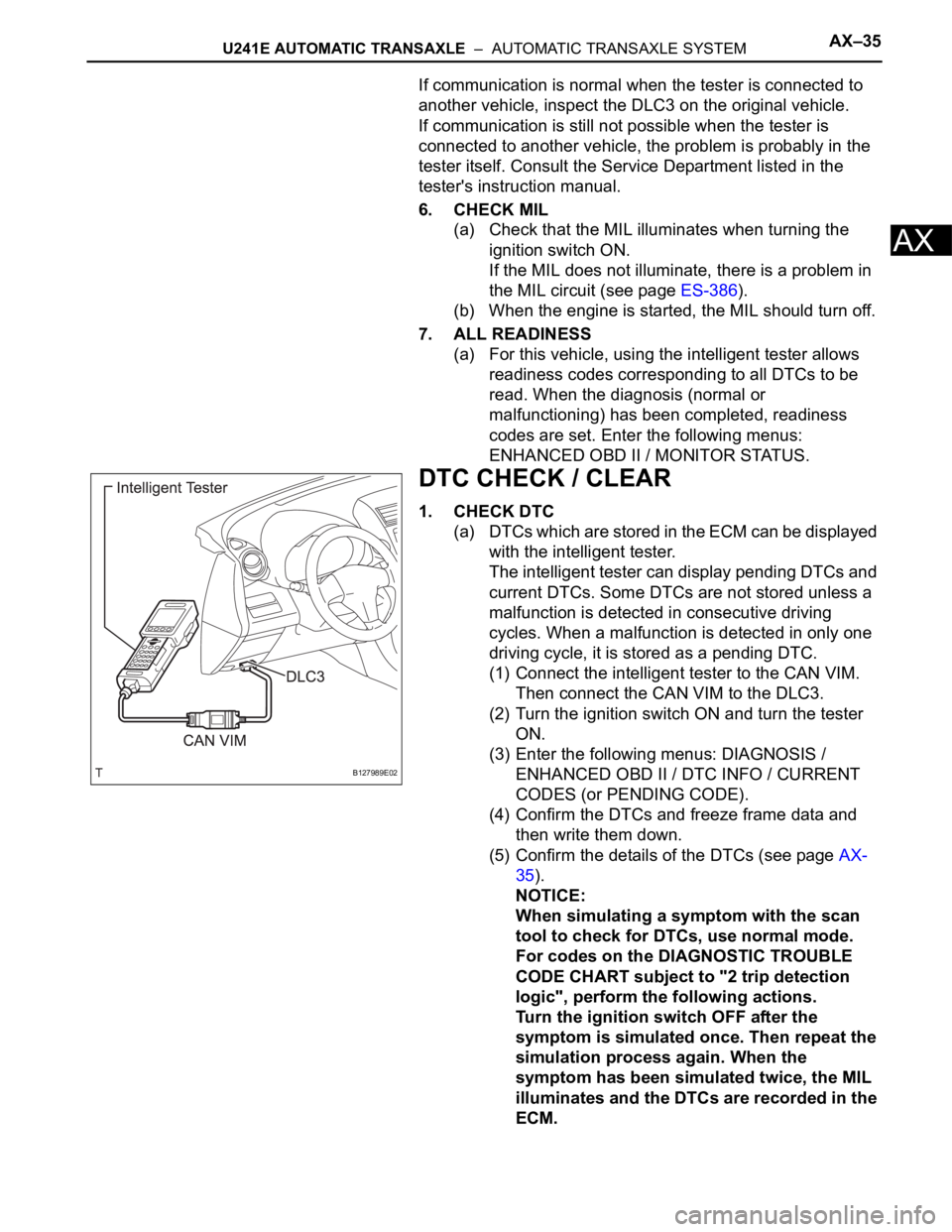
U241E AUTOMATIC TRANSAXLE – AUTOMATIC TRANSAXLE SYSTEMAX–35
AX
If communication is normal when the tester is connected to
another vehicle, inspect the DLC3 on the original vehicle.
If communication is still not possible when the tester is
connected to another vehicle, the problem is probably in the
tester itself. Consult the Service Department listed in the
tester's instruction manual.
6. CHECK MIL
(a) Check that the MIL illuminates when turning the
ignition switch ON.
If the MIL does not illuminate, there is a problem in
the MIL circuit (see page ES-386).
(b) When the engine is started, the MIL should turn off.
7. ALL READINESS
(a) For this vehicle, using the intelligent tester allows
readiness codes corresponding to all DTCs to be
read. When the diagnosis (normal or
malfunctioning) has been completed, readiness
codes are set. Enter the following menus:
ENHANCED OBD II / MONITOR STATUS.
DTC CHECK / CLEAR
1. CHECK DTC
(a) DTCs which are stored in the ECM can be displayed
with the intelligent tester.
The intelligent tester can display pending DTCs and
current DTCs. Some DTCs are not stored unless a
malfunction is detected in consecutive driving
cycles. When a malfunction is detected in only one
driving cycle, it is stored as a pending DTC.
(1) Connect the intelligent tester to the CAN VIM.
Then connect the CAN VIM to the DLC3.
(2) Turn the ignition switch ON and turn the tester
ON.
(3) Enter the following menus: DIAGNOSIS /
ENHANCED OBD II / DTC INFO / CURRENT
CODES (or PENDING CODE).
(4) Confirm the DTCs and freeze frame data and
then write them down.
(5) Confirm the details of the DTCs (see page AX-
35).
NOTICE:
When simulating a symptom with the scan
tool to check for DTCs, use normal mode.
For codes on the DIAGNOSTIC TROUBLE
CODE CHART subject to "2 trip detection
logic", perform the following actions.
Turn the ignition switch OFF after the
symptom is simulated once. Then repeat the
simulation process again. When the
symptom has been simulated twice, the MIL
illuminates and the DTCs are recorded in the
ECM.
B127989E02
Page 1260 of 2000
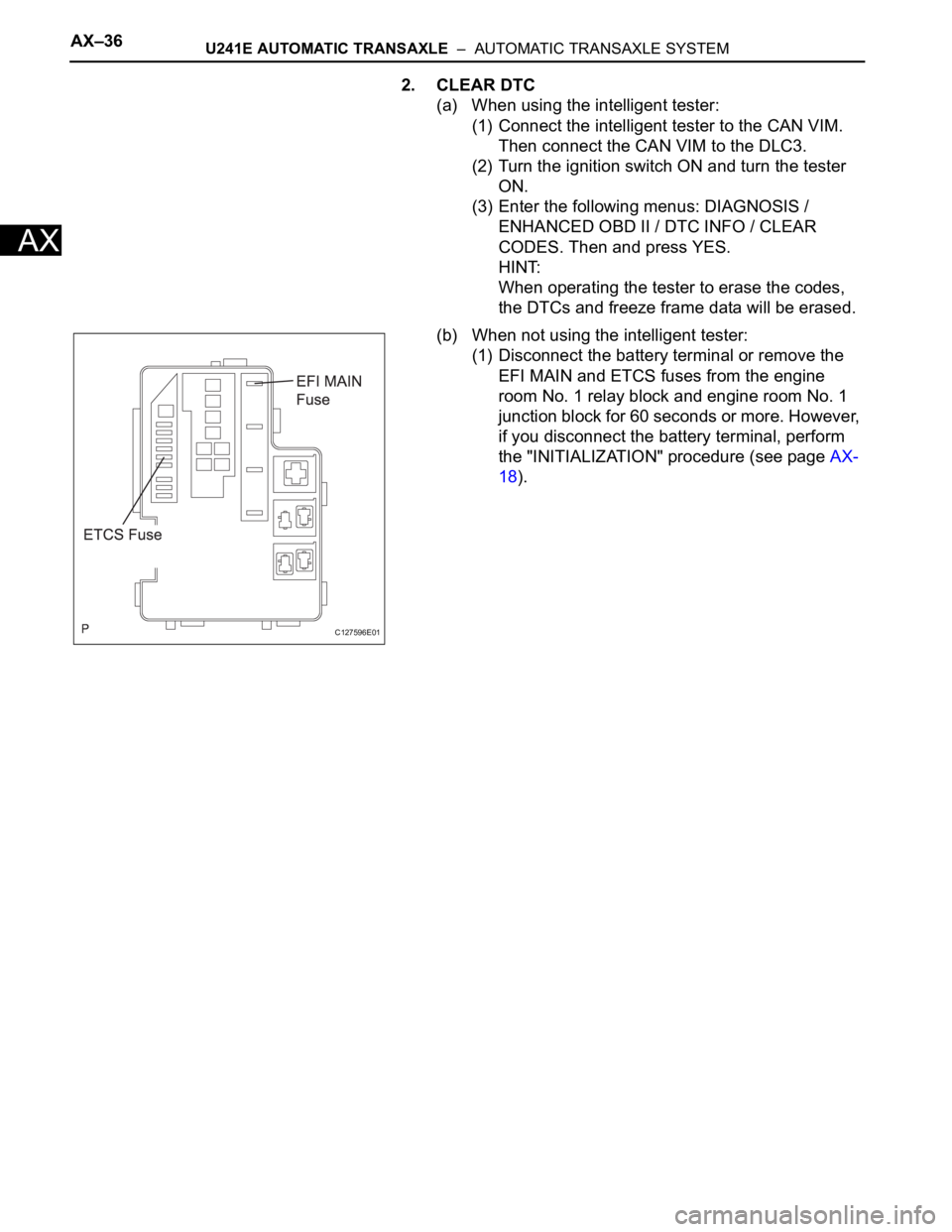
AX–36U241E AUTOMATIC TRANSAXLE – AUTOMATIC TRANSAXLE SYSTEM
AX
2. CLEAR DTC
(a) When using the intelligent tester:
(1) Connect the intelligent tester to the CAN VIM.
Then connect the CAN VIM to the DLC3.
(2) Turn the ignition switch ON and turn the tester
ON.
(3) Enter the following menus: DIAGNOSIS /
ENHANCED OBD II / DTC INFO / CLEAR
CODES. Then and press YES.
HINT:
When operating the tester to erase the codes,
the DTCs and freeze frame data will be erased.
(b) When not using the intelligent tester:
(1) Disconnect the battery terminal or remove the
EFI MAIN and ETCS fuses from the engine
room No. 1 relay block and engine room No. 1
junction block for 60 seconds or more. However,
if you disconnect the battery terminal, perform
the "INITIALIZATION" procedure (see page AX-
18).
C127596E01