YAMAHA WR 250F 2009 Owners Manual
Manufacturer: YAMAHA, Model Year: 2009, Model line: WR 250F, Model: YAMAHA WR 250F 2009Pages: 224, PDF Size: 13.93 MB
Page 91 of 224
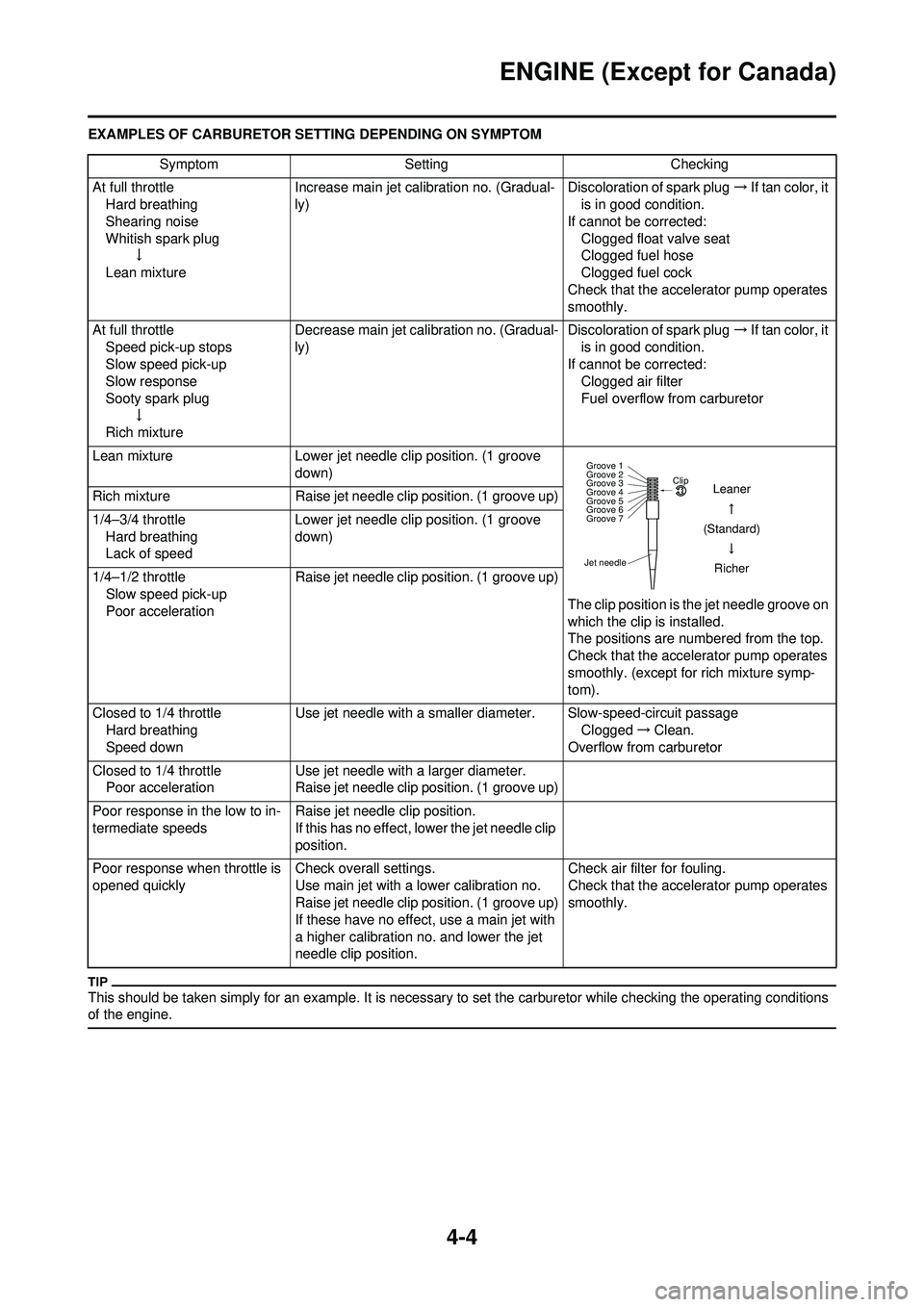
4-4
ENGINE (Except for Canada)
EXAMPLES OF CARBURETOR SETTING DEPENDING ON SYMPTOM
This should be taken simply for an example. It is necessary to set the carburetor while checking the operating conditions
of the engine.
SymptomSetting Checking
At full throttle Hard breathing
Shearing noise
Whitish spark plug ↓
Lean mixture Increase main jet calibration no. (Gradual-
ly)
Discoloration of spark plug
→If tan color, it
is in good condition.
If cannot be corrected: Clogged float valve seat
Clogged fuel hose
Clogged fuel cock
Check that the accelerator pump operates
smoothly.
At full throttle Speed pick-up stops
Slow speed pick-up
Slow response
Sooty spark plug ↓
Rich mixture Decrease main jet calibration no. (Gradual-
ly)
Discoloration of spark plug
→If tan color, it
is in good condition.
If cannot be corrected: Clogged air filter
Fuel overflow from carburetor
Lean mixture Lower jet needle clip position. (1 groove
down)
The clip position is the jet needle groove on
which the clip is installed.
The positions are numbered from the top.
Check that the accelerator pump operates
smoothly. (except for rich mixture symp-
tom).
Rich mixture
Raise jet needle clip position. (1 groove up)
1/4–3/4 throttle Hard breathing
Lack of speed Lower jet needle clip position. (1 groove
down)
1/4–1/2 throttle Slow speed pick-up
Poor acceleration Raise jet needle clip position. (1 groove up)
Closed to 1/4 throttle Hard breathing
Speed down Use jet needle with a smaller diameter. Slow-speed-circuit passage
Clogged→Clean.
Overflow from carburetor
Closed to 1/4 throttle Poor acceleration Use jet needle with a larger diameter.
Raise jet needle clip position. (1 groove up)
Poor response in the low to in-
termediate speeds Raise jet needle clip position.
If this has no effect, lower the jet needle clip
position.
Poor response when throttle is
opened quickly Check overall settings.
Use main jet with a lower calibration no.
Raise jet needle clip position. (1 groove up)
If these have no effect, use a main jet with
a higher calibration no. and lower the jet
needle clip position. Check air filter for fouling.
Check that the accelerator pump operates
smoothly.
Jet needleClip
Groove 7 Groove 6
Groove 5
Groove 4
Groove 3
Groove 2
Groove 1
Leaner
(Standard) Richer
Page 92 of 224
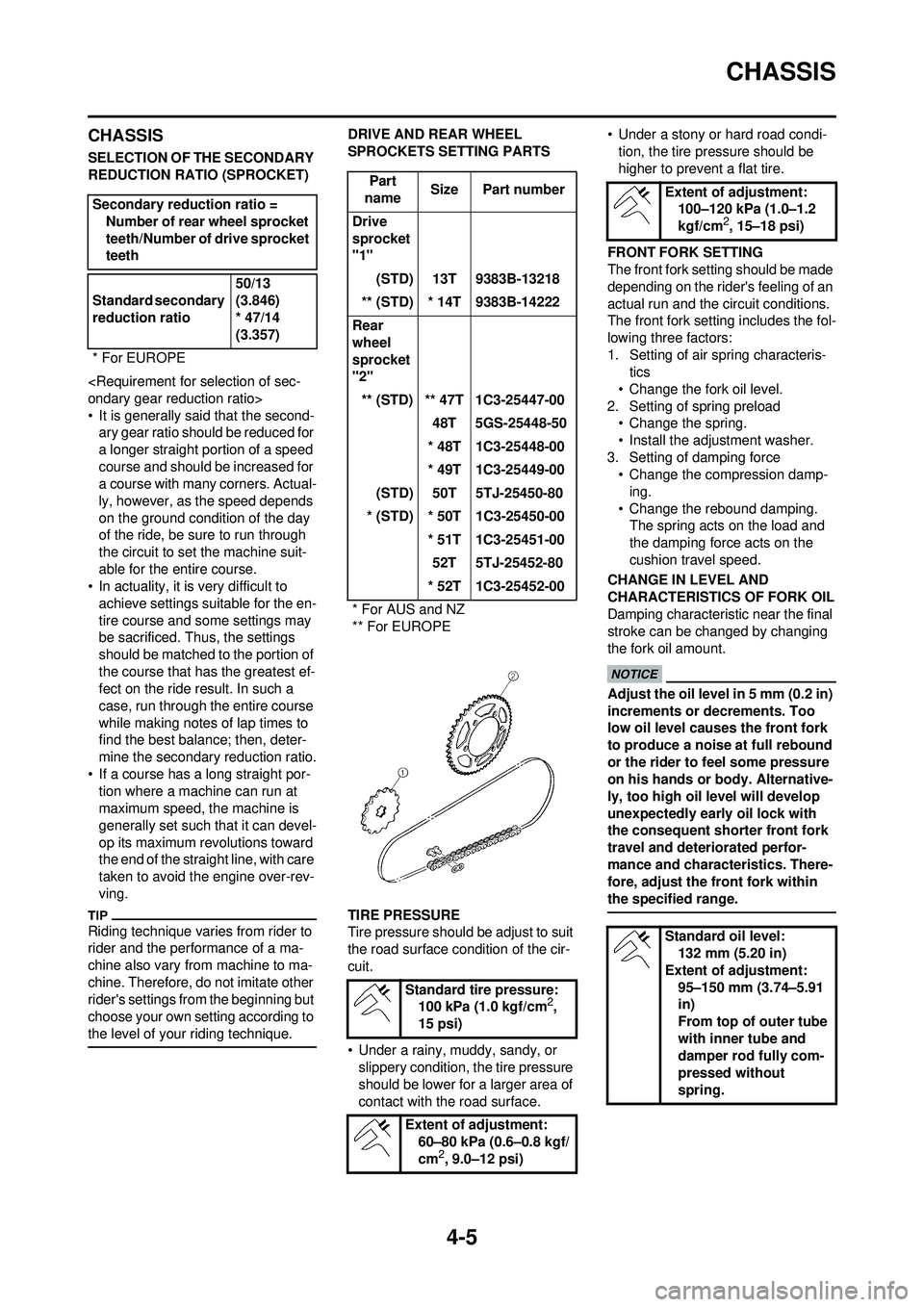
4-5
CHASSIS
CHASSIS
SELECTION OF THE SECONDARY
REDUCTION RATIO (SPROCKET)
• It is generally said that the second-ary gear ratio should be reduced for
a longer straight portion of a speed
course and should be increased for
a course with many corners. Actual-
ly, however, as the speed depends
on the ground condition of the day
of the ride, be sure to run through
the circuit to set the machine suit-
able for the entire course.
• In actuality, it is very difficult to
achieve settings suitable for the en-
tire course and some settings may
be sacrificed. Thus, the settings
should be matched to the portion of
the course that has the greatest ef-
fect on the ride result. In such a
case, run through the entire course
while making notes of lap times to
find the best balance; then, deter-
mine the secondary reduction ratio.
• If a course has a long straight por- tion where a machine can run at
maximum speed, the machine is
generally set such that it can devel-
op its maximum revolutions toward
the end of the straight line, with care
taken to avoid the engine over-rev-
ving.
Riding technique varies from rider to
rider and the performance of a ma-
chine also vary from machine to ma-
chine. Therefore, do not imitate other
rider's settings from the beginning but
choose your own setting according to
the level of your riding technique.
DRIVE AND REAR WHEEL
SPROCKETS SETTING PARTS
TIRE PRESSURE
Tire pressure should be adjust to suit
the road surface condition of the cir-
cuit.
• Under a rainy, muddy, sandy, or slippery condition, the tire pressure
should be lower for a larger area of
contact with the road surface. • Under a stony or hard road condi-
tion, the tire pressure should be
higher to prevent a flat tire.
FRONT FORK SETTING
The front fork setting should be made
depending on the rider's feeling of an
actual run and the circuit conditions.
The front fork setting includes the fol-
lowing three factors:
1. Setting of air spring characteris- tics
• Change the fork oil level.
2. Setting of spring preload • Change the spring.
• Install the adjustment washer.
3. Setting of damping force • Change the compression damp-
ing.
• Change the rebound damping. The spring acts on the load and
the damping force acts on the
cushion travel speed.
CHANGE IN LEVEL AND
CHARACTERISTICS OF FORK OIL
Damping characteristic near the final
stroke can be changed by changing
the fork oil amount.
Adjust the oil level in 5 mm (0.2 in)
increments or decrements. Too
low oil level causes the front fork
to produce a noise at full rebound
or the rider to feel some pressure
on his hands or body. Alternative-
ly, too high oil level will develop
unexpectedly early oil lock with
the consequent shorter front fork
travel and deteriorated perfor-
mance and characteristics. There-
fore, adjust the front fork within
the specified range.
Secondary reduction ratio = Number of rear wheel sprocket
teeth/Number of drive sprocket
teeth
Standard secondary
reduction ratio 50/13
(3.846)
* 47/14
(3.357)
* For EUROPE
Part
name Size Part number
Drive
sprocket
"1" (STD) 13T 9383B-13218
** (STD) * 14T 9383B-14222
Rear
wheel
sprocket
"2" ** (STD) ** 47T 1C3-25447-00 48T 5GS-25448-50
* 48T 1C3-25448-00
* 49T 1C3-25449-00
(STD) 50T 5TJ-25450-80
* (STD) * 50T 1C3-25450-00 * 51T 1C3-25451-0052T 5TJ-25452-80
* 52T 1C3-25452-00
* For AUS and NZ
** For EUROPE
Standard tire pressure:100 kPa (1.0 kgf/cm
2,
15 psi)
Extent of adjustment: 60–80 kPa (0.6–0.8 kgf/
cm
2, 9.0–12 psi)
Extent of adjustment:100–120 kPa (1.0–1.2
kgf/cm
2, 15–18 psi)
Standard oil level: 132 mm (5.20 in)
Extent of adjustment: 95–150 mm (3.74–5.91
in)
From top of outer tube
with inner tube and
damper rod fully com-
pressed without
spring.
Page 93 of 224
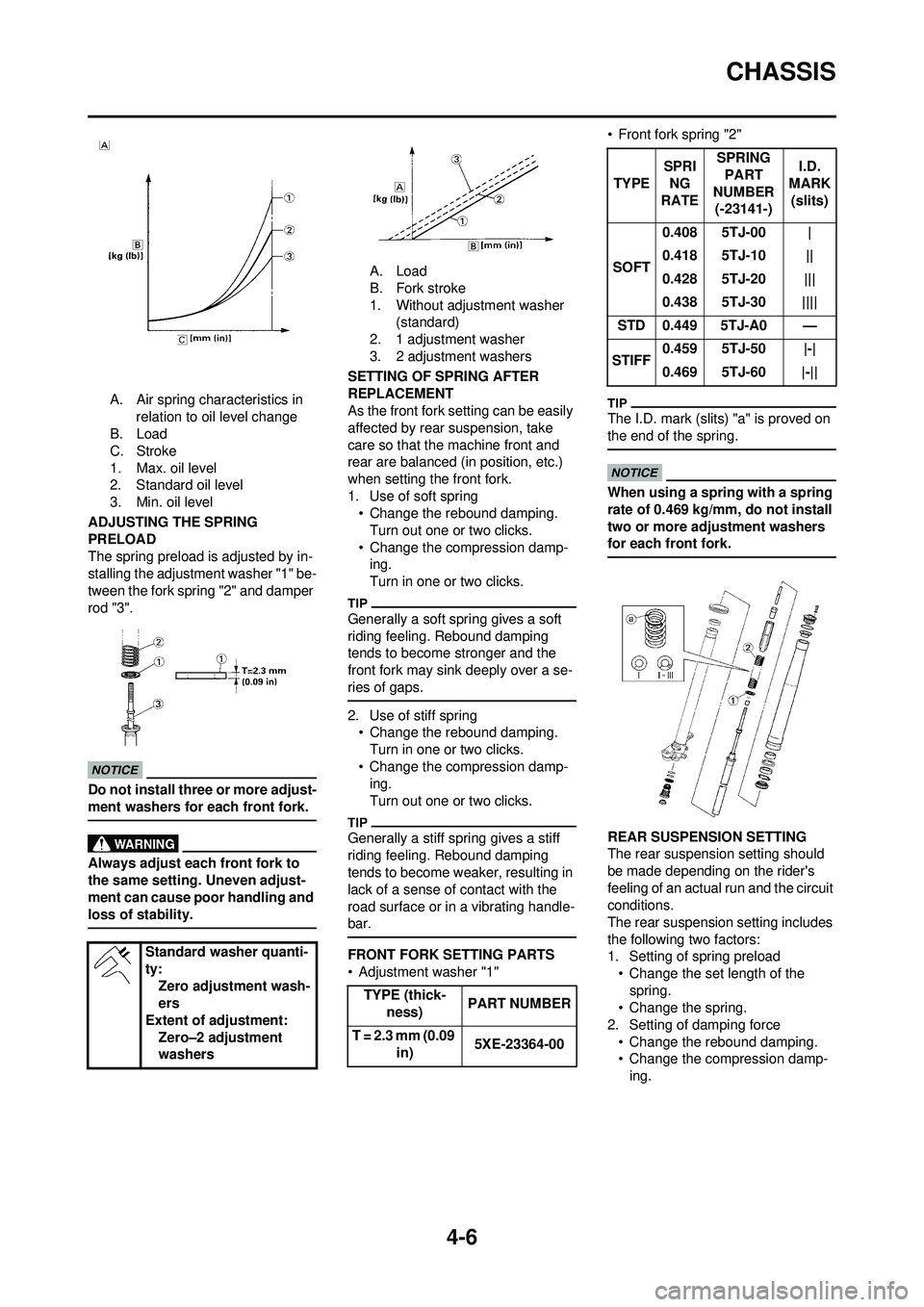
4-6
CHASSIS
A. Air spring characteristics in relation to oil level change
B. Load
C. Stroke
1. Max. oil level
2. Standard oil level
3. Min. oil level
ADJUSTING THE SPRING
PRELOAD
The spring preload is adjusted by in-
stalling the adjustment washer "1" be-
tween the fork spring "2" and damper
rod "3".
Do not install three or more adjust-
ment washers for each front fork.
Always adjust each front fork to
the same setting. Uneven adjust-
ment can cause poor handling and
loss of stability.
A. Load
B. Fork stroke
1. Without adjustment washer (standard)
2. 1 adjustment washer
3. 2 adjustment washers
SETTING OF SPRING AFTER
REPLACEMENT
As the front fork setting can be easily
affected by rear suspension, take
care so that the machine front and
rear are balanced (in position, etc.)
when setting the front fork.
1. Use of soft spring • Change the rebound damping.
Turn out one or two clicks.
• Change the compression damp- ing.
Turn in one or two clicks.
Generally a soft spring gives a soft
riding feeling. Rebound damping
tends to become stronger and the
front fork may sink deeply over a se-
ries of gaps.
2. Use of stiff spring• Change the rebound damping.
Turn in one or two clicks.
• Change the compression damp- ing.
Turn out one or two clicks.
Generally a stiff spring gives a stiff
riding feeling. Rebound damping
tends to become weaker, resulting in
lack of a sense of contact with the
road surface or in a vibrating handle-
bar.
FRONT FORK SETTING PARTS
• Adjustment washer "1" • Front fork spring "2"
The I.D. mark (slits) "a" is proved on
the end of the spring.
When using a spring with a spring
rate of 0.469 kg/mm, do not install
two or more adjustment washers
for each front fork.
REAR SUSPENSION SETTING
The rear suspension setting should
be made depending on the rider's
feeling of an actual run and the circuit
conditions.
The rear suspension setting includes
the following two factors:
1. Setting of spring preload
• Change the set length of the spring.
• Change the spring.
2. Setting of damping force • Change the rebound damping.
• Change the compression damp-ing.
Standard washer quanti-
ty:
Zero adjustment wash-
ers
Extent of adjustment: Zero–2 adjustment
washers
TYPE (thick- ness) PART NUMBER
T = 2.3 mm (0.09 in) 5XE-23364-00
TYPESPRI
NG
RATE SPRING
PART
NUMBER (-23141-) I.D.
MARK (slits)
SOFT 0.408 5TJ-00 |
0.418 5TJ-10 ||
0.428 5TJ-20 |||
0.438 5TJ-30 ||||
STD 0.449 5TJ-A0 —
STIFF 0.459 5TJ-50 |-|
0.469 5TJ-60 |-||
Page 94 of 224
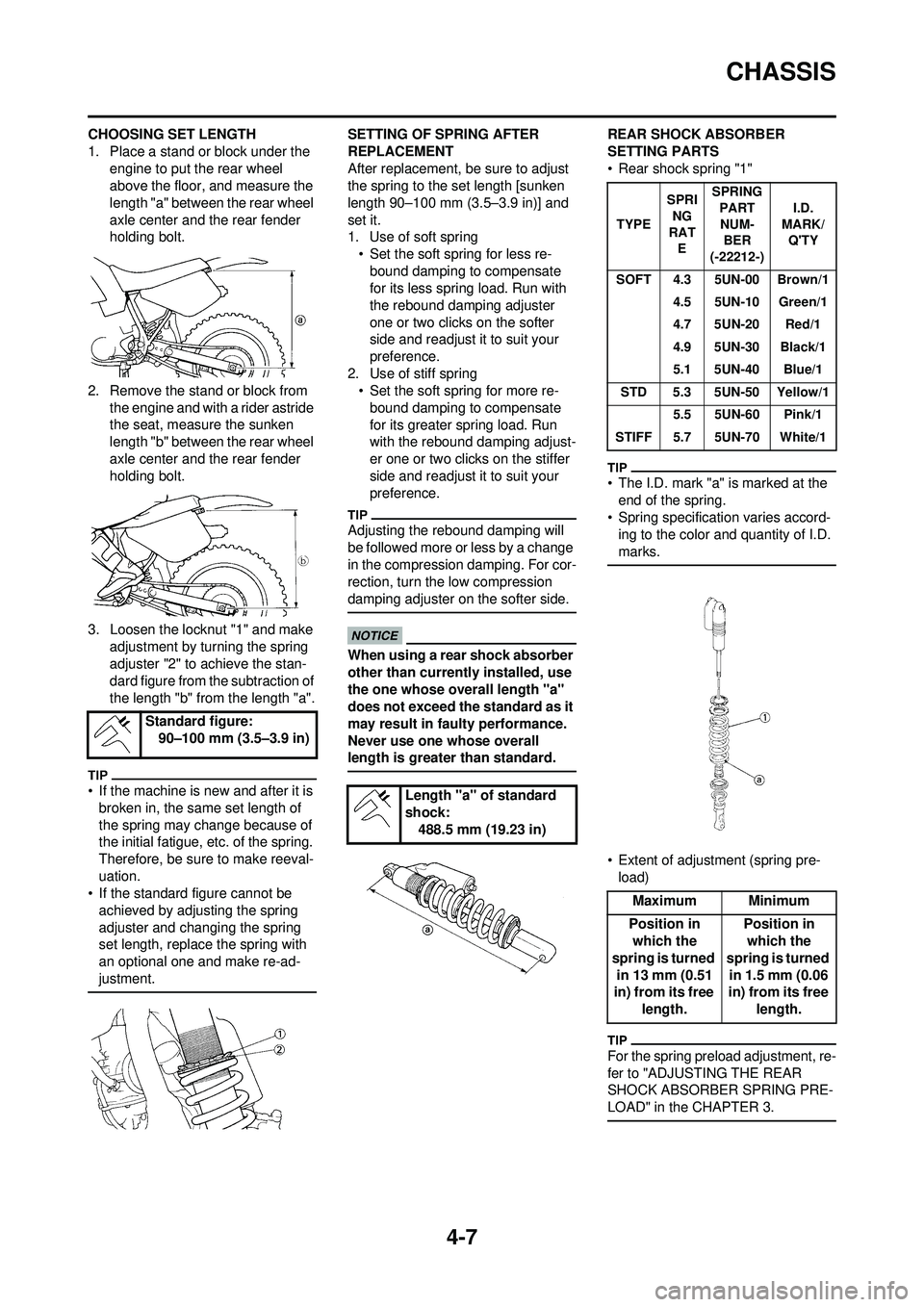
4-7
CHASSIS
CHOOSING SET LENGTH
1. Place a stand or block under the engine to put the rear wheel
above the floor, and measure the
length "a" between the rear wheel
axle center and the rear fender
holding bolt.
2. Remove the stand or block from the engine and with a rider astride
the seat, measure the sunken
length "b" between the rear wheel
axle center and the rear fender
holding bolt.
3. Loosen the locknut "1" and make adjustment by turning the spring
adjuster "2" to achieve the stan-
dard figure from the subtraction of
the length "b" from the length "a".
• If the machine is new and after it is broken in, the same set length of
the spring may change because of
the initial fatigue, etc. of the spring.
Therefore, be sure to make reeval-
uation.
• If the standard figure cannot be
achieved by adjusting the spring
adjuster and changing the spring
set length, replace the spring with
an optional one and make re-ad-
justment.
SETTING OF SPRING AFTER
REPLACEMENT
After replacement, be sure to adjust
the spring to the set length [sunken
length 90–100 mm (3.5–3.9 in)] and
set it.
1. Use of soft spring• Set the soft spring for less re-bound damping to compensate
for its less spring load. Run with
the rebound damping adjuster
one or two clicks on the softer
side and readjust it to suit your
preference.
2. Use of stiff spring • Set the soft spring for more re-
bound damping to compensate
for its greater spring load. Run
with the rebound damping adjust-
er one or two clicks on the stiffer
side and readjust it to suit your
preference.
Adjusting the rebound damping will
be followed more or less by a change
in the compression damping. For cor-
rection, turn the low compression
damping adjuster on the softer side.
When using a rear shock absorber
other than currently installed, use
the one whose overall length "a"
does not exceed the standard as it
may result in faulty performance.
Never use one whose overall
length is greater than standard.
REAR SHOCK ABSORBER
SETTING PARTS
• Rear shock spring "1"
• The I.D. mark "a" is marked at the end of the spring.
• Spring specification varies accord- ing to the color and quantity of I.D.
marks.
• Extent of adjustment (spring pre-
load)
For the spring preload adjustment, re-
fer to "ADJUSTING THE REAR
SHOCK ABSORBER SPRING PRE-
LOAD" in the CHAPTER 3.
Standard figure: 90–100 mm (3.5–3.9 in)
Length "a" of standard
shock:
488.5 mm (19.23 in)
TYPE SPRI
NG
RAT E SPRING
PART
NUM- BER
(-22212-) I.D.
MARK/ Q'TY
SOFT 4.3 5UN-00 Brown/1 4.5 5UN-10 Green/1
4.7 5UN-20 Red/1
4.9 5UN-30 Black/1
5.1 5UN-40 Blue/1
STD 5.3 5UN-50 Yellow/1 5.5 5UN-60 Pink/1
STIFF 5.7 5UN-70 White/1
Maximum Minimum
Position in which the
spring is turned in 13 mm (0.51
in) from its free
length. Position in
which the
spring is turned in 1.5 mm (0.06
in) from its free
length.
Page 95 of 224
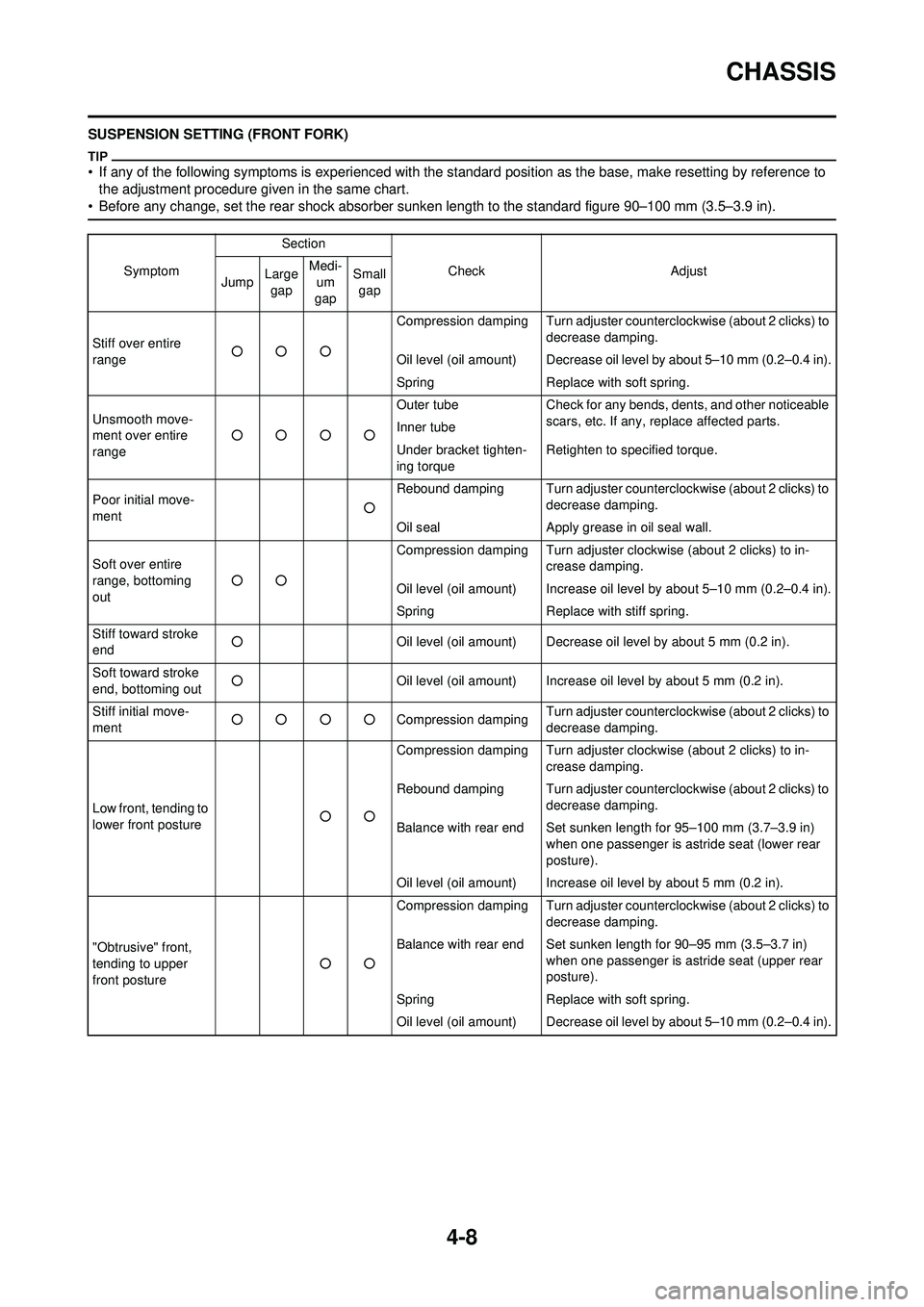
4-8
CHASSIS
SUSPENSION SETTING (FRONT FORK)
• If any of the following symptoms is experienced with the standard position as the base, make resetting by reference to the adjustment procedure given in the same chart.
• Before any change, set the rear shock absorber sunken length to the standard figure 90–100 mm (3.5–3.9 in).
Symptom Section
Check Adjust
Jump Large
gap Medi-
um
gap Small
gap
Stiff over entire
range ○○○ Compression damping Turn adjuster counterclockwise (about 2 clicks) to
decrease damping.
Oil level (oil amount) Decrease oil level by about 5–10 mm (0.2–0.4 in).
Spring Replace with soft spring.
Unsmooth move-
ment over entire
range ○○○○ Outer tube
Check for any bends, dents, and other noticeable
scars, etc. If any, replace affected parts.
Inner tube
Under bracket tighten-
ing torque Retighten to specified torque.
Poor initial move-
ment ○Rebound damping Turn adjuster counterclockwise (about 2 clicks) to
decrease damping.
Oil seal Apply grease in oil seal wall.
Soft over entire
range, bottoming
out ○○ Compression damping Turn adjuster clockwise (about 2 clicks) to in-
crease damping.
Oil level (oil amount) Increase oil level by about 5–10 mm (0.2–0.4 in).
Spring Replace with stiff spring.
Stiff toward stroke
end ○
Oil level (oil amount) Decrease oil level by about 5 mm (0.2 in).
Soft toward stroke
end, bottoming out ○
Oil level (oil amount) Increase oil level by about 5 mm (0.2 in).
Stiff initial move-
ment ○○○○
Compression dampingTurn adjuster counterclockwise (about 2 clicks) to
decrease damping.
Low front, tending to
lower front posture ○○Compression damping Turn adjuster clockwise (about 2 clicks) to in-
crease damping.
Rebound damping Turn adjuster counterclockwise (about 2 clicks) to decrease damping.
Balance with rear end Set sunken length for 95–100 mm (3.7–3.9 in) when one passenger is astride seat (lower rear
posture).
Oil level (oil amount) Increase oil level by about 5 mm (0.2 in).
"Obtrusive" front,
tending to upper
front posture ○○Compression damping Turn adjuster counterclockwise (about 2 clicks) to
decrease damping.
Balance with rear end Set sunken length for 90–95 mm (3.5–3.7 in) when one passenger is astride seat (upper rear
posture).
Spring Replace with soft spring.
Oil level (oil amount) Decrease oil level by about 5–10 mm (0.2–0.4 in).
Page 96 of 224
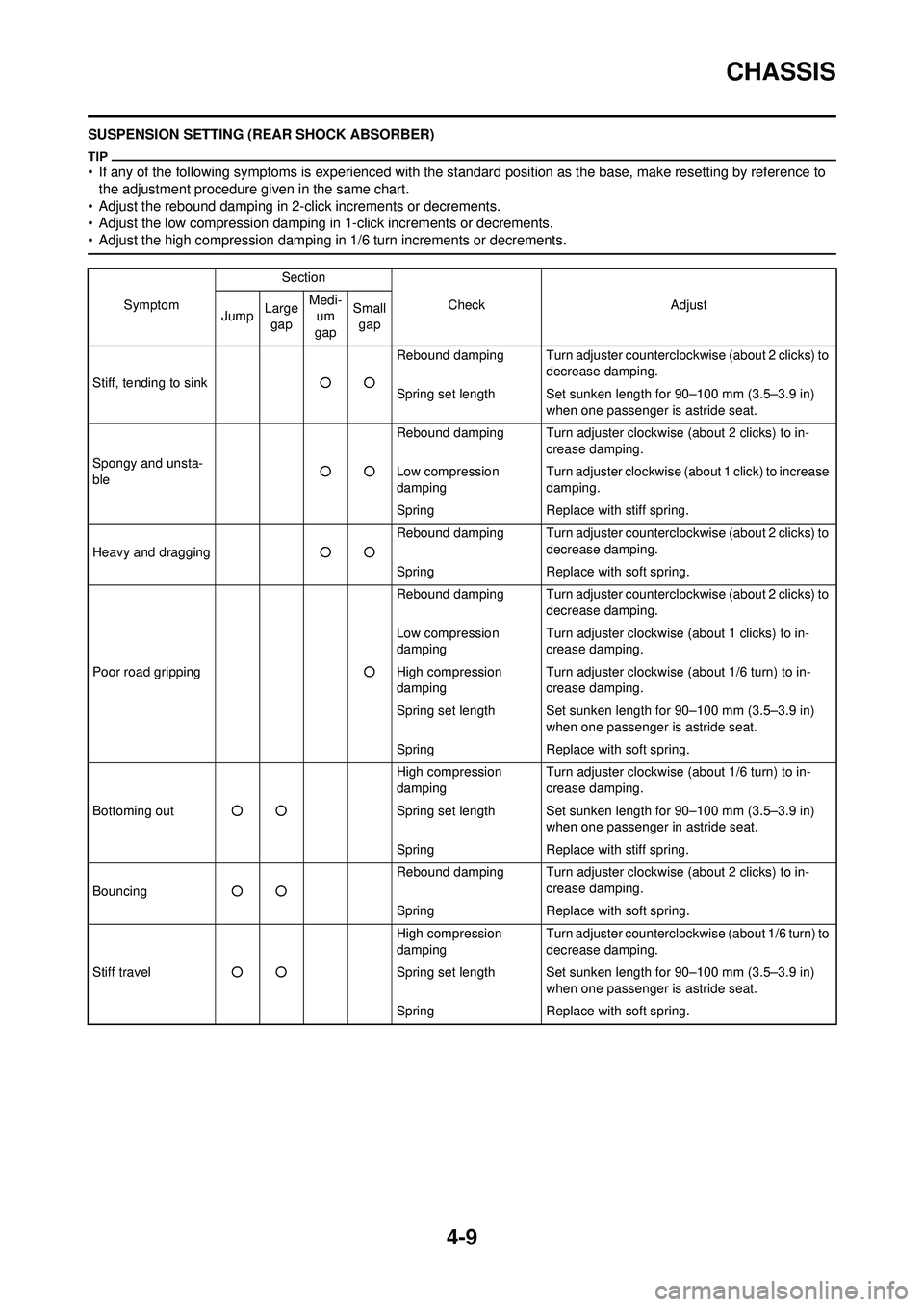
4-9
CHASSIS
SUSPENSION SETTING (REAR SHOCK ABSORBER)
• If any of the following symptoms is experienced with the standard position as the base, make resetting by reference to the adjustment procedure given in the same chart.
• Adjust the rebound damping in 2-click increments or decrements.
• Adjust the low compression damping in 1-click increments or decrements.
• Adjust the high compression damping in 1/6 turn increments or decrements.
Symptom Section
Check Adjust
Jump Large
gap Medi-
um
gap Small
gap
Stiff, tending to sink ○○Rebound damping Turn adjuster counterclockwise (about 2 clicks) to
decrease damping.
Spring set length Set sunken length for 90–100 mm (3.5–3.9 in) when one passenger is astride seat.
Spongy and unsta-
ble ○○Rebound damping Turn adjuster clockwise (about 2 clicks) to in-
crease damping.
Low compression
damping Turn adjuster clockwise (about 1 click) to increase
damping.
Spring Replace with stiff spring.
Heavy and dragging ○○Rebound damping Turn adjuster counterclockwise (about 2 clicks) to
decrease damping.
Spring Replace with soft spring.
Poor road gripping ○Rebound damping Turn adjuster counterclockwise (about 2 clicks) to
decrease damping.
Low compression
damping Turn adjuster clockwise (about 1 clicks) to in-
crease damping.
High compression
damping Turn adjuster clockwise (about 1/6 turn) to in-
crease damping.
Spring set length Set sunken length for 90–100 mm (3.5–3.9 in) when one passenger is astride seat.
Spring Replace with soft spring.
Bottoming out ○○ High compression
damping
Turn adjuster clockwise (about 1/6 turn) to in-
crease damping.
Spring set length Set sunken length for 90–100 mm (3.5–3.9 in) when one passenger in astride seat.
Spring Replace with stiff spring.
Bouncing ○○ Rebound damping Turn adjuster clockwise (about 2 clicks) to in-
crease damping.
Spring Replace with soft spring.
Stiff travel ○○ High compression
damping
Turn adjuster counterclockwise (about 1/6 turn) to
decrease damping.
Spring set length Set sunken length for 90–100 mm (3.5–3.9 in) when one passenger is astride seat.
Spring Replace with soft spring.
Page 97 of 224
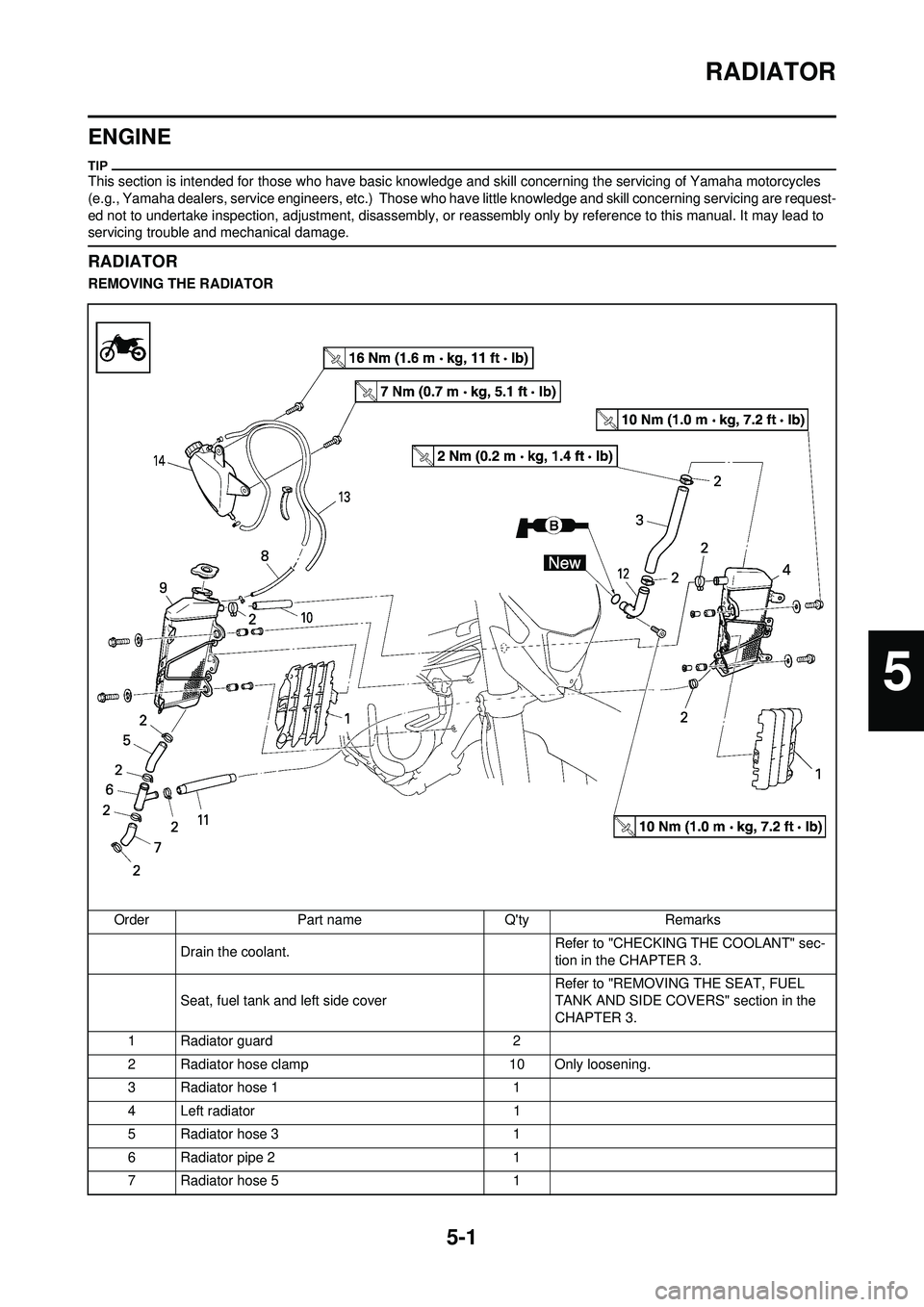
5-1
RADIATOR
ENGINE
This section is intended for those who have basic knowledge and skill concerning the servicing of Yamaha motorcycles
(e.g., Yamaha dealers, service engineers, etc.) Those who have little knowledge and skill concerning servicing are request-
ed not to undertake inspection, adjustment, disassembly, or reassembly only by reference to this manual. It may lead to
servicing trouble and mechanical damage.
RADIATOR
REMOVING THE RADIATOROrder Part name Q'ty Remarks Drain the coolant. Refer to "CHECKING THE COOLANT" sec-
tion in the CHAPTER 3.
Seat, fuel tank and left side cover Refer to "REMOVING THE SEAT, FUEL
TANK AND SIDE COVERS" section in the
CHAPTER 3.
1 Radiator guard 2
2 Radiator hose clamp 10 Only loosening.
3 Radiator hose 1 1
4 Left radiator 1
5 Radiator hose 3 1
6 Radiator pipe 2 1
7 Radiator hose 5 1
5
Page 98 of 224
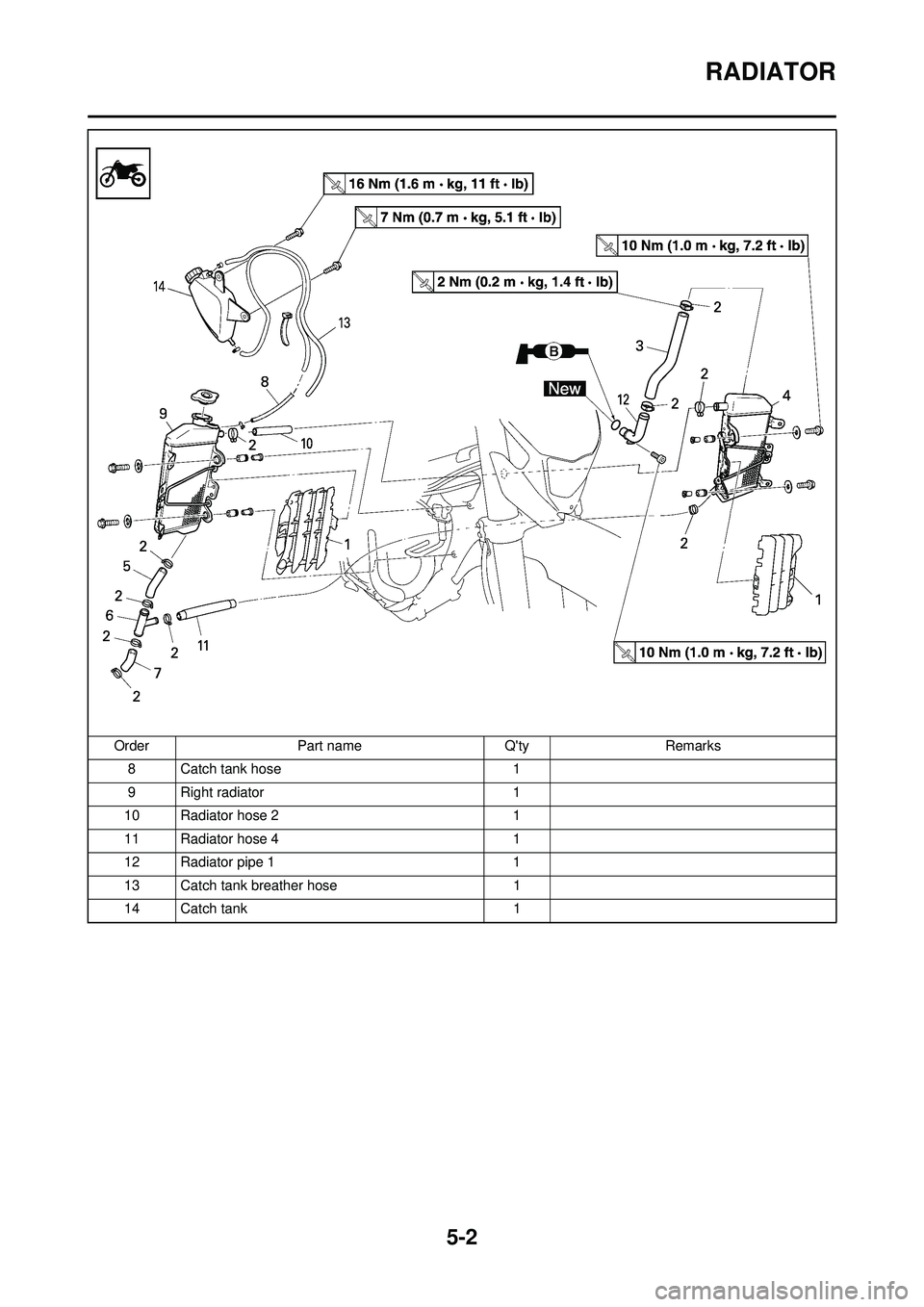
5-2
RADIATOR
8 Catch tank hose1
9 Right radiator 1
10 Radiator hose 2 1
11 Radiator hose 4 1
12 Radiator pipe 1 1
13 Catch tank breather hose 1
14 Catch tank 1
Order
Part name Q'tyRemarks
Page 99 of 224

5-3
RADIATOR
HANDLING NOTE
Do not remove the radiator cap
when the engine and radiator are
hot. Scalding hot fluid and steam
may be blown out under pressure,
which could cause serious injury.
When the engine has cooled, open
the radiator cap by the following
procedure:
Place a thick rag, like a towel, over
the radiator cap, slowly rotate the
cap counterclockwise to the de-
tent. This procedure allows any re-
sidual pressure to escape. When
the hissing sound has stopped,
press down on the cap while turn-
ing counterclockwise and remove
it.
CHECKING THE RADIATOR
1. Inspect:• Radiator core "1"Obstruction →Blow out with com-
pressed air through rear of the ra-
diator.
Bent fin →Repair/replace.
INSTALLING THE RADIATOR
1. Install: • O-ring "1"
• Radiator pipe 1 "2"
• Bolt (radiator pipe) "3"
Apply the lithium soap base grease
on the O-ring.
2. Install:• Catch tank hose "1"
• Radiator hose 2 "2"
• Radiator hose 3 "3"
• Radiator pipe 2 "4"
• Radiator hose 5 "5"
• Radiator hose 4 "6"To right radiator "7".
3. Install: • Right radiator "1"
• Bolt (right radiator) "2"
• Radiator hose 5 "3"
Refer to "CABLE ROUTING DIA-
GRAM" section in the CHAPTER
2.
4. Install: • Left radiator "1"
• Bolt (left radiator) "2"
• Radiator hose 1 "3"
Refer to "CABLE ROUTING DIA-
GRAM" section in the CHAPTER
2. 5. Tighten:
• Radiator hose clamp "4"
6. Install: • Radiator guard "1"
First fit the inner hook portion "a" and
then the outer one "b" onto the radia-
tor.
7. Install:• Catch tank "1"
• Bolt (catch tank) "2"
• Bolt (catch tank) "3"
• Catch tank hose "4"
• Catch tank breather hose "5"Refer to "CABLE ROUTING DIA-
GRAM" section in the CHAPTER
2.
Bolt (radiator pipe):
10 Nm (1.0 m•kg, 7.2
ft•lb)
Bolt (right radiator):10 Nm (1.0 m•kg, 7.2
ft•lb)
Bolt (left radiator): 10 Nm (1.0 m•kg, 7.2
ft•lb)
Radiator hose 1: 2 Nm (0.2 m•kg, 1.4
ft•lb)
Radiator hose clamp:2 Nm (0.2 m•kg, 1.4
ft•lb)
Bolt (catch tank): 7 Nm (0.7 m•kg, 5.1
ft•lb)
Bolt (catch tank): 16 Nm (1.6 m•kg, 11
ft•lb)
Page 100 of 224
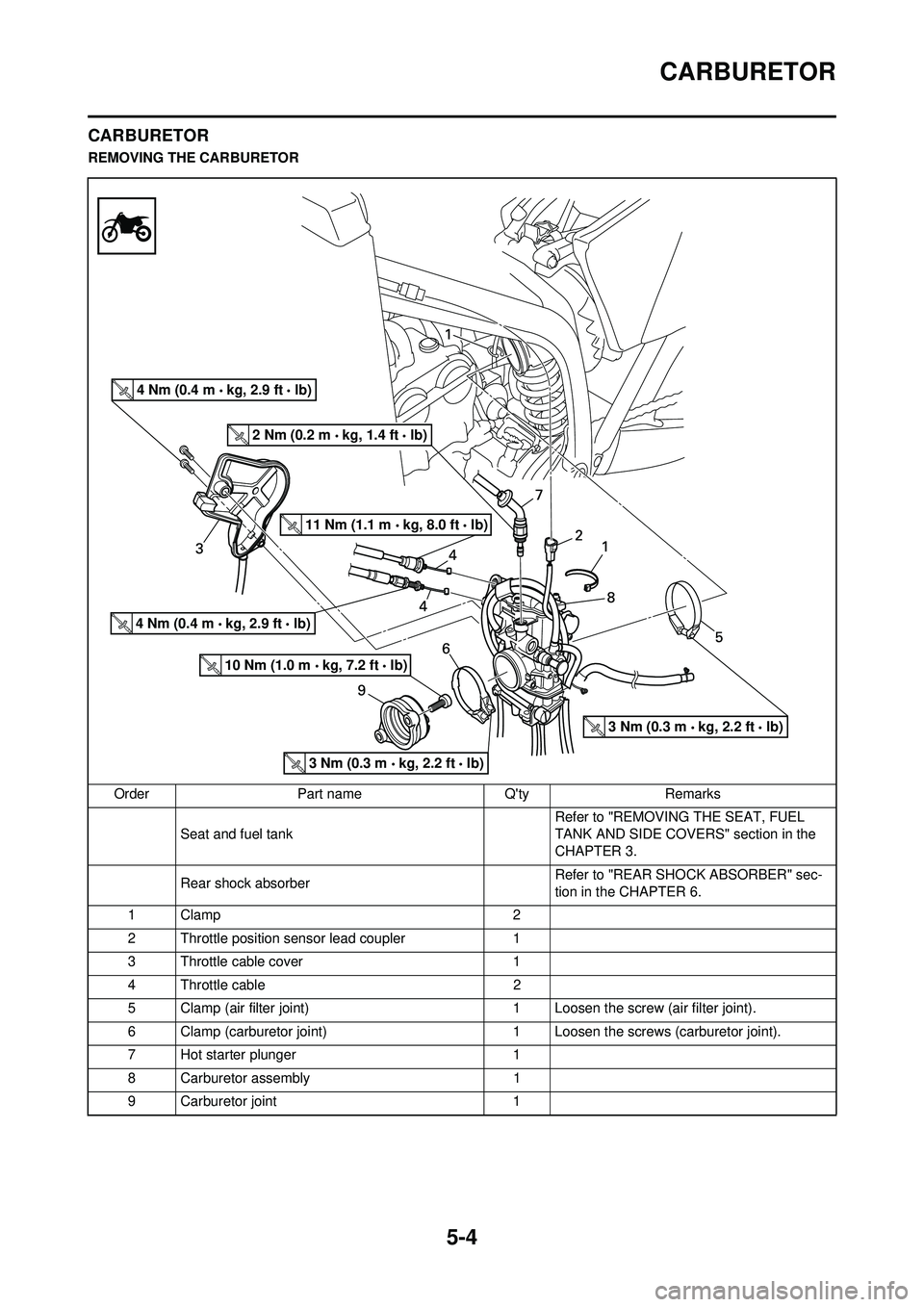
5-4
CARBURETOR
CARBURETOR
REMOVING THE CARBURETOROrder Part name Q'ty Remarks Seat and fuel tank Refer to "REMOVING THE SEAT, FUEL
TANK AND SIDE COVERS" section in the
CHAPTER 3.
Rear shock absorber Refer to "REAR SHOCK ABSORBER" sec-
tion in the CHAPTER 6.
1Clamp 2
2 Throttle position sensor lead coupler 1
3 Throttle cable cover 1
4 Throttle cable 2
5 Clamp (air filter joint) 1 Loosen the screw (air filter joint).
6 Clamp (carburetor joint) 1 Loosen the screws (carburetor joint).
7 Hot starter plunger 1
8 Carburetor assembly 1
9 Carburetor joint 1
4 Nm (0.4 m kg, 2.9 ft lb)
2 Nm (0.2 m kg, 1.4 ft lb)
11 Nm (1.1 m kg, 8.0 ft lb)
4 Nm (0.4 m kg, 2.9 ft lb)
10 Nm (1.0 m kg, 7.2 ft lb)
3 Nm (0.3 m kg, 2.2 ft lb)
3 Nm (0.3 m kg, 2.2 ft lb)