ASTON MARTIN V8 VANTAGE 2010 Workshop Manual
Manufacturer: ASTON MARTIN, Model Year: 2010, Model line: V8 VANTAGE, Model: ASTON MARTIN V8 VANTAGE 2010Pages: 947, PDF Size: 43.21 MB
Page 461 of 947
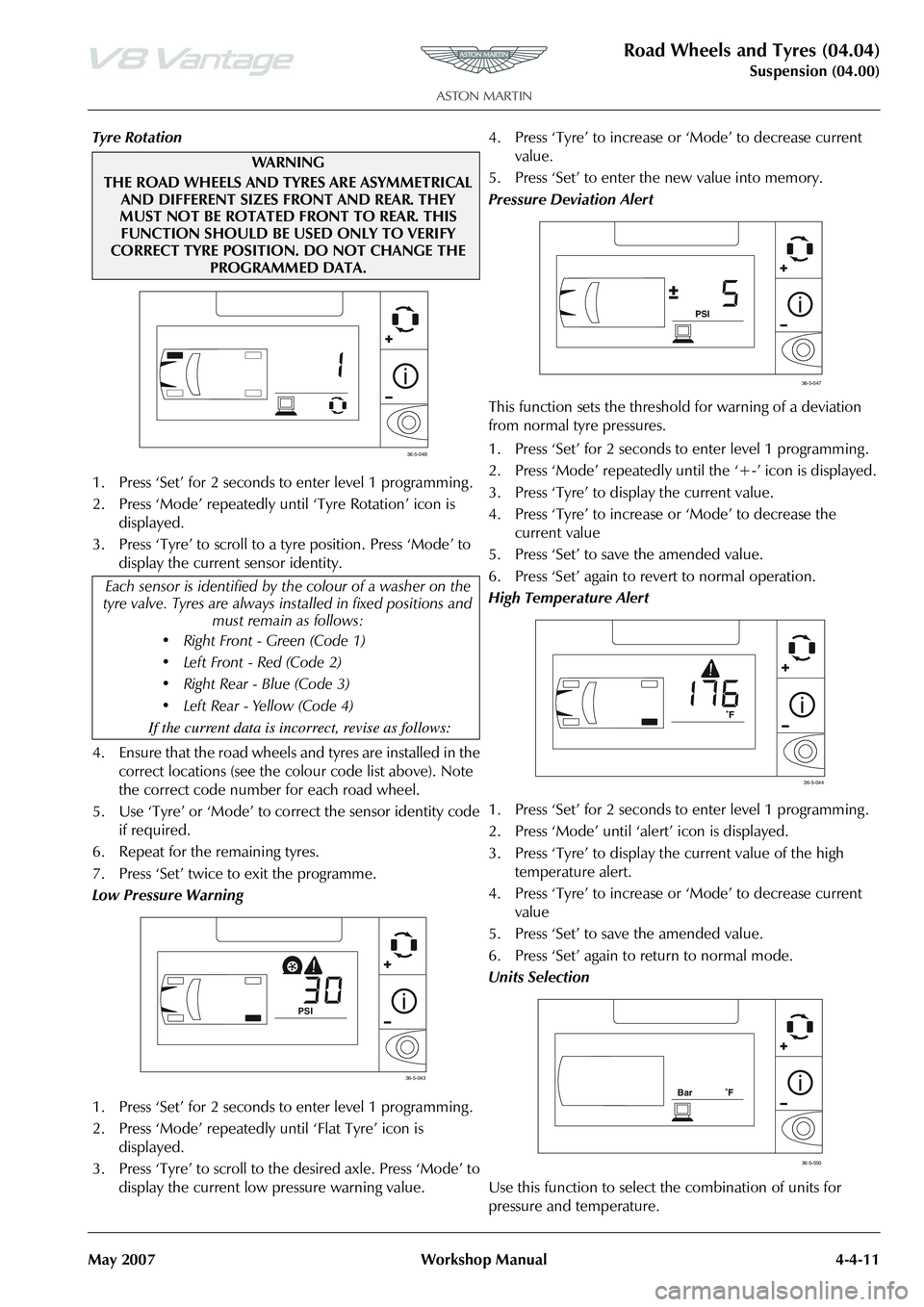
Road Wheels and Tyres (04.04)
Suspension (04.00)
May 2007 Workshop Manual 4-4-11
Tyre Rotation
1. Press ‘Set’ for 2 seconds to enter level 1 programming .
2. Press ‘Mode’ repeatedly until ‘Tyre Rotation’ icon is displayed.
3. Press ‘Tyre’ to scroll to a tyre position. Press ‘Mode’ to display the current sensor identity.
4. Ensure that the road wheels and tyres are installed in the correct locations (see the colour code list above). Note
the correct code number for each road wheel.
5. Use ‘Tyre’ or ‘Mode’ to co rrect the sensor identity code
if required.
6. Repeat for the remaining tyres.
7. Press ‘Set’ twice to exit the programme.
Low Pressure Warning
1. Press ‘Set’ for 2 seconds to enter level 1 programming .
2. Press ‘Mode’ repeatedly until ‘Flat Tyre’ icon is displayed.
3. Press ‘Tyre’ to scroll to th e desired axle. Press ‘Mode’ to
display the current low pressure warning value. 4. Press ‘Tyre’ to increase or
‘Mode’ to decrease current
value.
5. Press ‘Set’ to enter the new value into memory.
Pressure Deviation Alert
This function sets the threshold for warning of a deviation
from normal tyre pressures.
1. Press ‘Set’ for 2 seconds to enter level 1 programming .
2. Press ‘Mode’ repeatedly until the ‘+-’ icon is displayed.
3. Press ‘Tyre’ to display the current value.
4. Press ‘Tyre’ to increase or ‘Mode’ to decrease the
current value
5. Press ‘Set’ to save the amended value.
6. Press ‘Set’ again to revert to normal operation.
High Temperature Alert
1. Press ‘Set’ for 2 seconds to enter level 1 programming .
2. Press ‘Mode’ until ‘ale rt’ icon is displayed.
3. Press ‘Tyre’ to display the current value of the high temperature alert.
4. Press ‘Tyre’ to increase or ‘Mode’ to decrease current
value
5. Press ‘Set’ to save the amended value.
6. Press ‘Set’ again to return to normal mode.
Units Selection
Use this function to select the combination of units for
pressure and temperature.
WAR NI N G
THE ROAD WHEELS AND TYRES ARE ASYMMETRICAL AND DIFFERENT SIZES FRONT AND REAR. THEY
MUST NOT BE ROTATED FRONT TO REAR. THIS FUNCTION SHOULD BE USED ONLY TO VERIFY
CORRECT TYRE POSITION. DO NOT CHANGE THE PROGRAMMED DATA.
Each sensor is identified by th e colour of a washer on the
tyre valve. Tyres are always in stalled in fixed positions and
must remain as follows:
• Right Front - Green (Code 1)
• Left Front - Red (Code 2)
Page 462 of 947
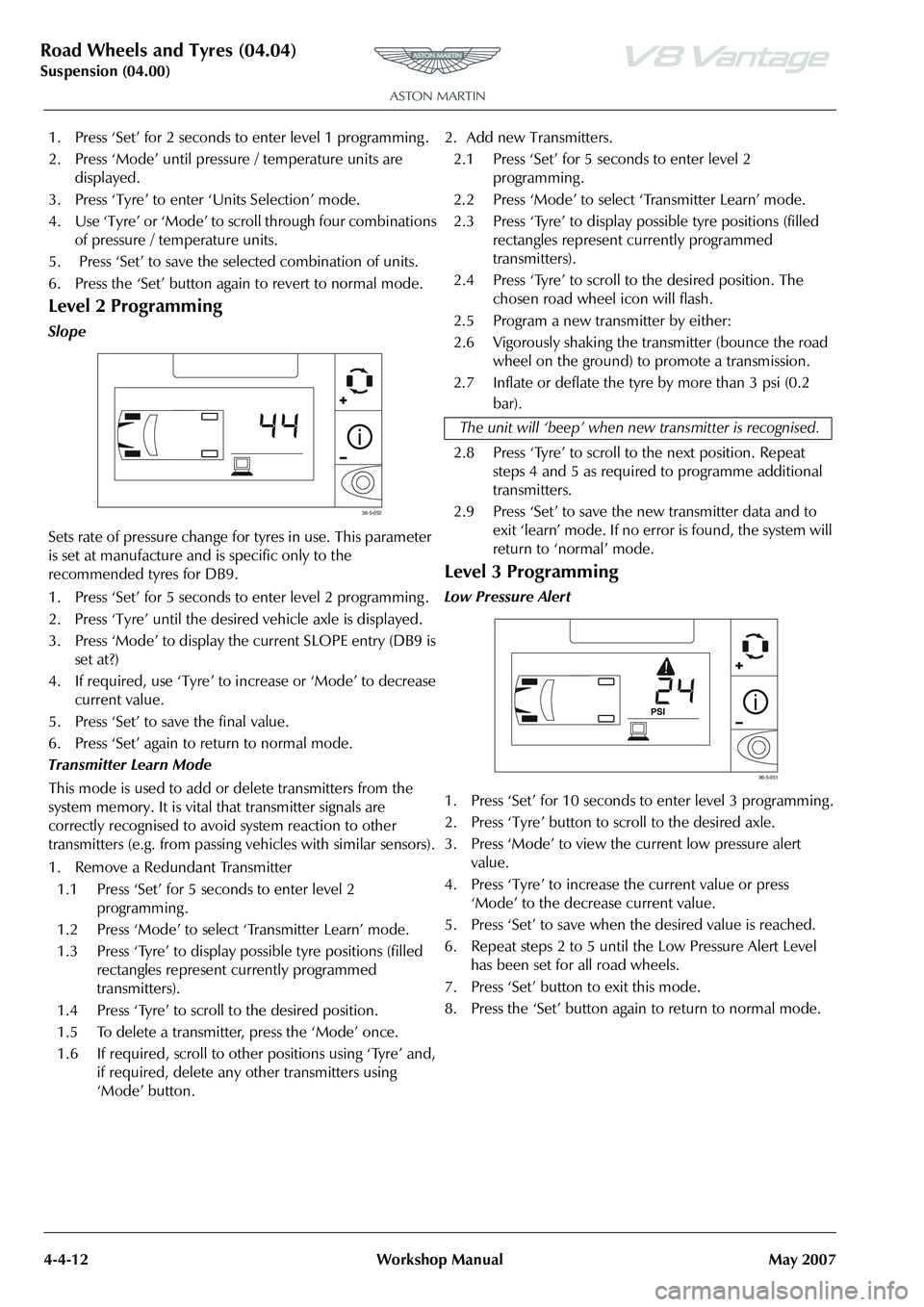
Road Wheels and Tyres (04.04)
Suspension (04.00)4-4-12 Workshop Manual May 2007
1. Press ‘Set’ for 2 seconds to enter level 1 programming .
2. Press ‘Mode’ until pressure / temperature units are displayed.
3. Press ‘Tyre’ to enter ‘Units Selection’ mode.
4. Use ‘Tyre’ or ‘Mode’ to scroll through four combinations of pressure / temperature units.
5. Press ‘Set’ to save the selected combination of units.
6. Press the ‘Set’ button again to revert to normal mode.
Level 2 Programming
Slope
Sets rate of pressure change for tyres in use. This parameter
is set at manufacture and is specific only to the
recommended tyres for DB9.
1. Press ‘Set’ for 5 seconds to enter level 2 programming .
2. Press ‘Tyre’ until the desired vehicle axle is displayed.
3. Press ‘Mode’ to display the current SLOPE entry (DB9 is set at?)
4. If required, use ‘Tyre’ to increase or ‘Mode’ to decrease current value.
5. Press ‘Set’ to save the final value.
6. Press ‘Set’ again to return to normal mode.
Transmitter Learn Mode
This mode is used to add or delete transmitters from the
system memory. It is vital that transmitter signals are
correctly recognised to avoid system reaction to other
transmitters (e.g. from passing vehicles with similar sensors).
1. Remove a Redundant Transmitter 1.1 Press ‘Set’ for 5 seconds to enter level 2 programming .
1.2 Press ‘Mode’ to select ‘Transmitter Learn’ mode.
1.3 Press ‘Tyre’ to display possible tyre positions (filled rectangles represent currently programmed
transmitters).
1.4 Press ‘Tyre’ to scroll to the desired position.
1.5 To delete a transmitter, press the ‘Mode’ once.
1.6 If required, scroll to other positions using ‘Tyre’ and, if required, delete any other transmitters using
‘Mode’ button. 2. Add new Transmitters.
2.1 Press ‘Set’ for 5 seconds to enter level 2 programming .
2.2 Press ‘Mode’ to select ‘Transmitter Learn’ mode.
2.3 Press ‘Tyre’ to display possible tyre positions (filled rectangles represent currently programmed
transmitters).
2.4 Press ‘Tyre’ to scroll to the desired position. The chosen road wheel icon will flash.
2.5 Program a new transmitter by either:
2.6 Vigorously shaking the transmitter (bounce the road wheel on the ground) to promote a transmission.
2.7 Inflate or deflate the tyre by more than 3 psi (0.2 bar).
2.8 Press ‘Tyre’ to scroll to the next position. Repeat steps 4 and 5 as required to programme additional
transmitters.
2.9 Press ‘Set’ to save the new transmitter data and to exit ‘learn’ mode. If no error is found, the system will
return to ‘normal’ mode.
Level 3 Programming
Low Pressure Alert
1. Press ‘Set’ for 10 seconds to enter level 3 programming .
2. Press ‘Tyre’ button to scroll to the desired axle.
3. Press ‘Mode’ to view the current low pressure alert value.
4. Press ‘Tyre’ to increase the current value or press ‘Mode’ to the decrease current value.
5. Press ‘Set’ to save when the desired value is reached.
6. Repeat steps 2 to 5 until the Low Pressure Alert Level has been set for all road wheels.
7. Press ‘Set’ button to exit this mode.
8. Press the ‘Set’ button again to return to normal mode.
36-5-052
The unit will ‘beep’ when ne w transmitter is recognised.
36-5-051
Page 463 of 947
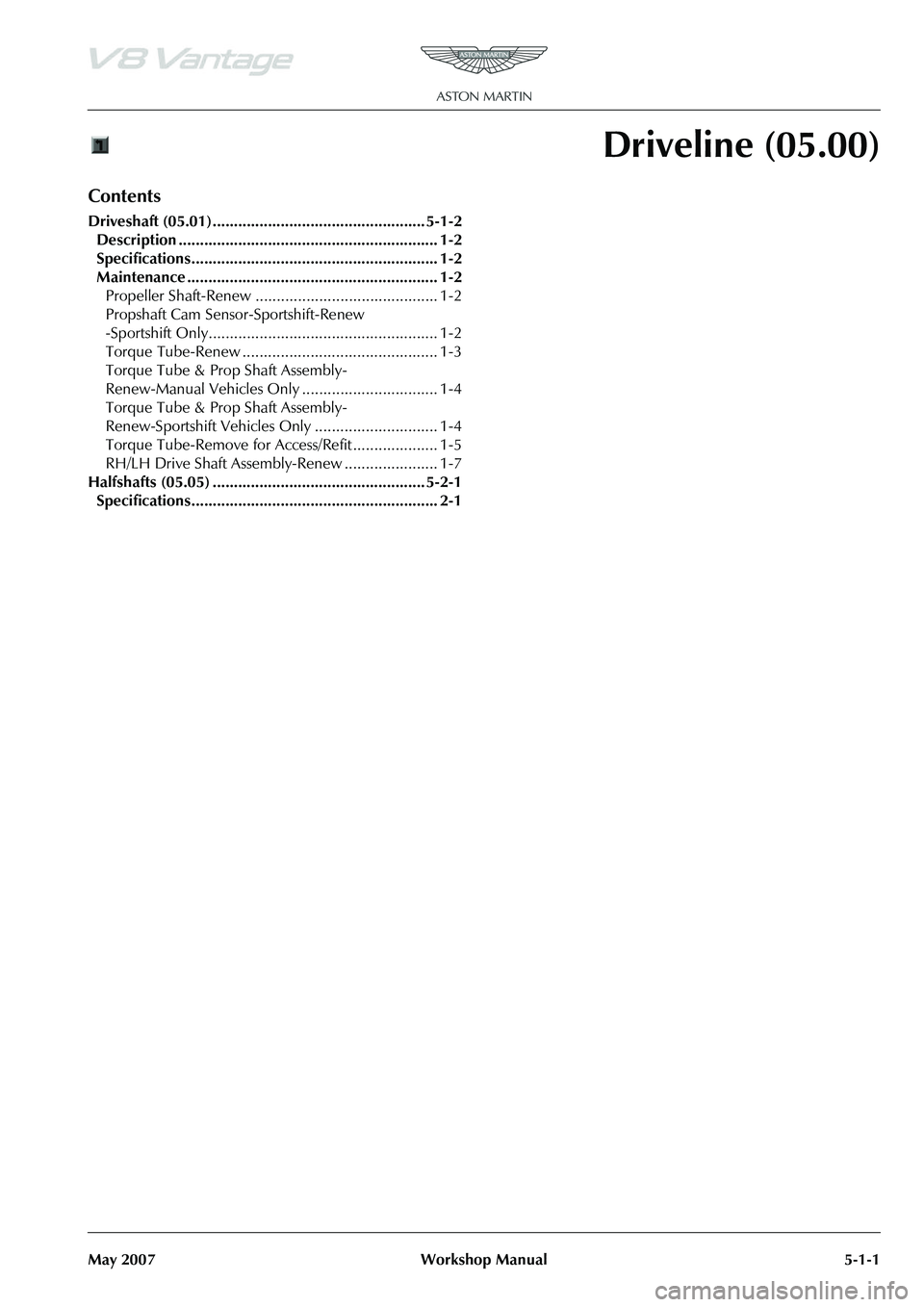
May 2007 Workshop Manual 5-1-1
Driveline (05.00)
Contents
Driveshaft (05.01) .................................................. 5-1-2Description ............................................................. 1-2
Specifications.......................................................... 1-2
Maintenance ........................................................... 1-2 Propeller Shaft-Renew ........................................... 1-2
Propshaft Cam Sensor-Sportshift-Renew
-Sportshift Only...................................................... 1-2
Torque Tube-Renew .............................................. 1-3
Torque Tube & Prop Shaft Assembly-
Renew-Manual Vehicles Only ................................ 1-4
Torque Tube & Prop Shaft Assembly-
Renew-Sportshift Vehicles Only ............................. 1-4
Torque Tube-Remove for Access/Refit .................... 1-5
RH/LH Drive Shaft Assembly-Renew ...................... 1-7
Halfshafts (05.05) .................................................. 5-2-1 Specifications.......................................................... 2-1
Page 464 of 947
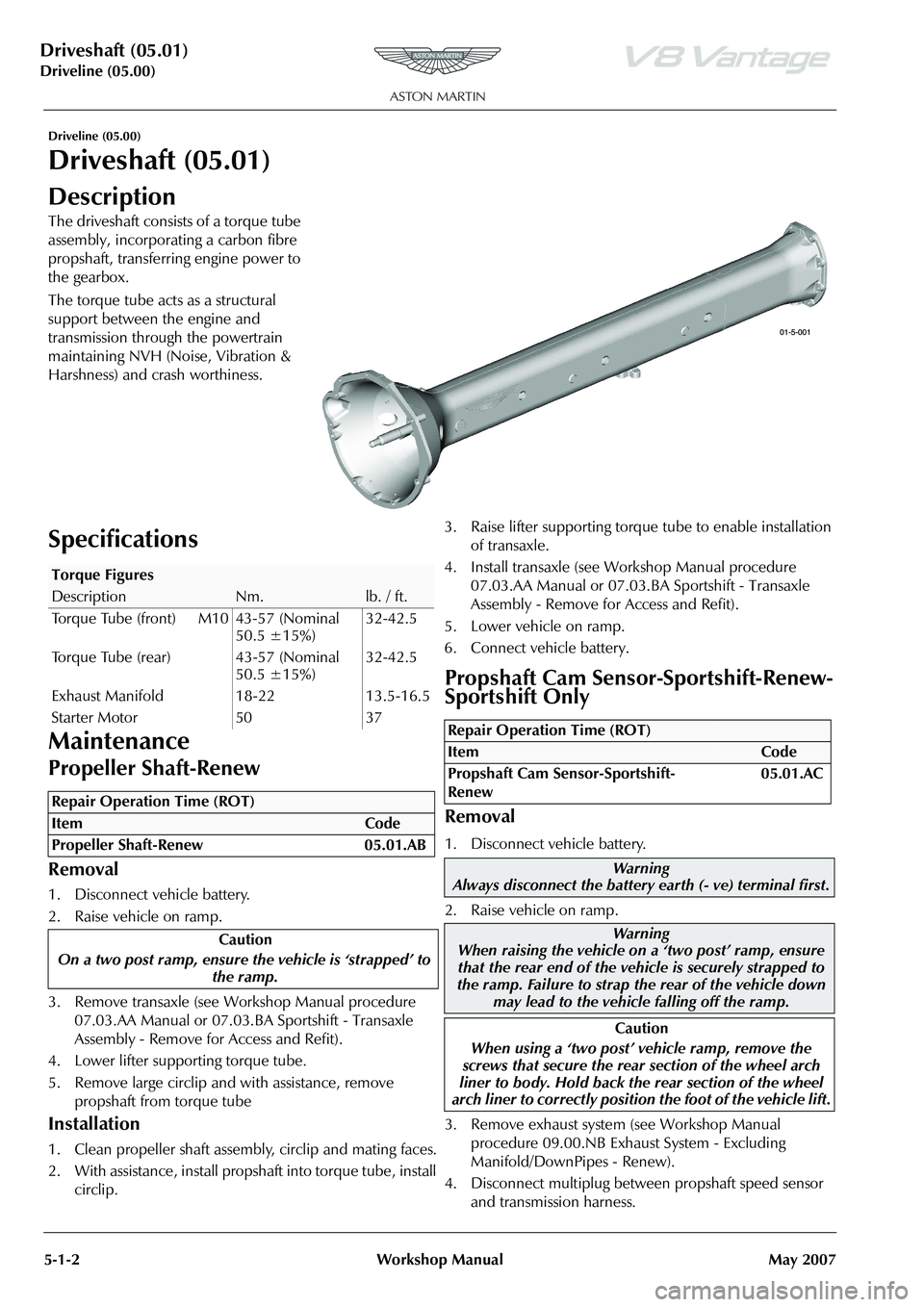
Driveshaft (05.01)
Driveline (05.00)5-1-2 Workshop Manual May 2007
Driveline (05.00)
Driveshaft (05.01)
Description
The driveshaft consists of a torque tube
assembly, incorporating a carbon fibre
propshaft, transferring engine power to
the gearbox.
The torque tube acts as a structural
support between the engine and
transmission through the powertrain
maintaining NVH (Noise, Vibration &
Harshness) and crash worthiness.
Specifications
Maintenance
Propeller Shaft-Renew
Removal
1. Disconnect vehicle battery.
2. Raise vehicle on ramp.
3. Remove transaxle (see Workshop Manual procedure 07.03.AA Manual or 07.03.BA Sportshift - Transaxle
Assembly - Remove for Access and Refit).
4. Lower lifter supporting torque tube.
5. Remove large circlip and with assistance, remove propshaft from torque tube
Installation
1. Clean propeller shaft assembly, circlip and mating faces.
2. With assistance, install propshaft into torque tube, install circlip. 3. Raise lifter supporting torque tube to enable installation
of transaxle.
4. Install transaxle (see Workshop Manual procedure 07.03.AA Manual or 07.03.BA Sportshift - Transaxle
Assembly - Remove for Access and Refit).
5. Lower vehicle on ramp.
6. Connect vehicle battery.
Propshaft Cam Sensor-Sportshift-Renew-
Sportshift Only
Removal
1. Disconnect vehicle battery.
2. Raise vehicle on ramp.
3. Remove exhaust system (see Workshop Manual procedure 09.00.NB Exhaust System - Excluding
Manifold/DownPipes - Renew).
4. Disconnect multiplug between propshaft speed sensor and transmission harness.
Torque Figures
DescriptionNm.lb. / ft.
Torque Tube (front) M10 43-57 (Nominal 50.5 ±15%)32-42.5
Torque Tube (rear) 43-57 (Nominal 50.5 ±15%)32-42.5
Exhaust Manifold 18-22 13.5-16.5
Starter Motor 50 37
Repair Operation Time (ROT)
Repair Operation Time (ROT)
ItemCode
Propshaft Cam Sensor-Sportshift-
Renew 05.01.AC
Warning
Always disconnect the battery earth (- ve) terminal first.
Warning
When raising the vehicle on a ‘two post’ ramp, ensure
that the rear end of the vehi cle is securely strapped to
the ramp. Failure to strap th e rear of the vehicle down
may lead to the vehicl e falling off the ramp.
Caution
When using a ‘two post’ vehicle ramp, remove the
screws that secure the rear section of the wheel arch
liner to body. Hold back the rear section of the wheel
arch liner to correctly position the foot of the vehicle lift.
Page 465 of 947
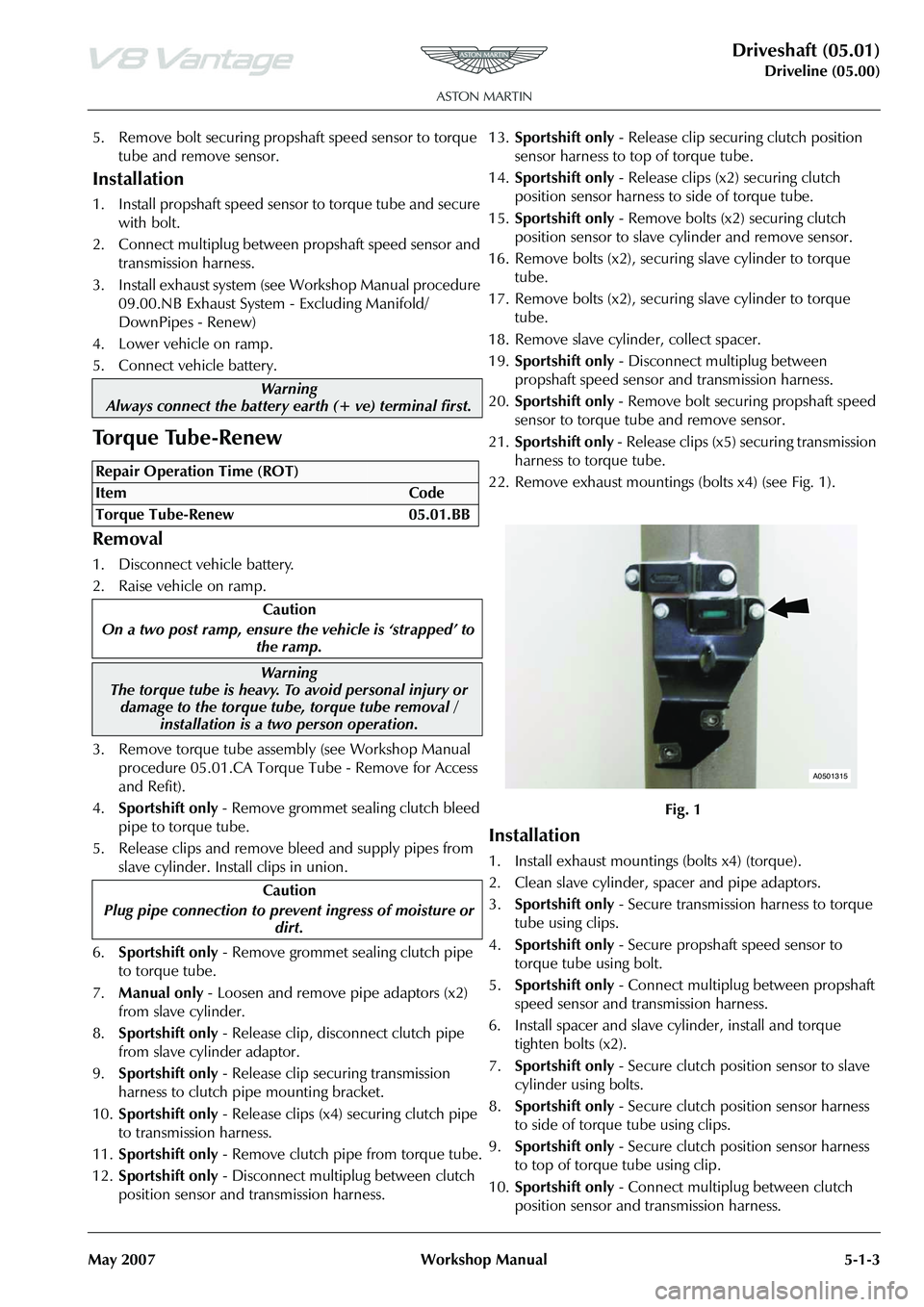
Driveshaft (05.01)
Driveline (05.00)
May 2007 Workshop Manual 5-1-3
5. Remove bolt securing propshaft speed sensor to torque tube and remove sensor.
Installation
1. Install propshaft speed sensor to torque tube and secure with bolt.
2. Connect multiplug between propshaft speed sensor and transmission harness.
3. Install exhaust system (see Workshop Manual procedure 09.00.NB Exhaust System - Excluding Manifold/
DownPipes - Renew)
4. Lower vehicle on ramp.
5. Connect vehicle battery.
To r q u e Tu b e - R e n e w
Removal
1. Disconnect vehicle battery.
2. Raise vehicle on ramp.
3. Remove torque tube assemb ly (see Workshop Manual
procedure 05.01.CA Torque Tube - Remove for Access
and Refit).
4. Sportshift only - Remove grommet sealing clutch bleed
pipe to torque tube.
5. Release clips and remove bleed and supply pipes from slave cylinder. Install clips in union.
6. Sportshift only - Remove grommet sealing clutch pipe
to torque tube.
7. Manual only - Loosen and remove pipe adaptors (x2)
from slave cylinder.
8. Sportshift only - Release clip, disconnect clutch pipe
from slave cylinder adaptor.
9. Sportshift only - Release clip securing transmission
harness to clutch pipe mounting bracket.
10. Sportshift only - Release clips (x4) securing clutch pipe
to transmission harness.
11. Sportshift only - Remove clutch pipe from torque tube.
12. Sportshift only - Disconnect multiplug between clutch
position sensor and transmission harness. 13.
Sportshift only - Release clip securing clutch position
sensor harness to top of torque tube.
14. Sportshift only - Release clips (x2) securing clutch
position sensor harness to side of torque tube.
15. Sportshift only - Remove bolts (x2) securing clutch
position sensor to slave cylinder and remove sensor.
16. Remove bolts (x2), securing slave cylinder to torque tube.
17. Remove bolts (x2), securing slave cylinder to torque tube.
18. Remove slave cylinder, collect spacer.
19. Sportshift only - Disconnect multiplug between
propshaft speed sensor and transmission harness.
20. Sportshift only - Remove bolt securing propshaft speed
sensor to torque tube and remove sensor.
21. Sportshift only - Release clips (x5) securing transmission
harness to torque tube.
22. Remove exhaust mountings (bolts x4) (see Fig. 1).
Installation
1. Install exhaust mounting s (bolts x4) (torque).
2. Clean slave cylinder, spacer and pipe adaptors.
3. Sportshift only - Secure transmission harness to torque
tube using clips.
4. Sportshift only - Secure propshaft speed sensor to
torque tube using bolt.
5. Sportshift only - Connect multiplug between propshaft
speed sensor and transmission harness.
6. Install spacer and slave cylinder, install and torque tighten bolts (x2).
7. Sportshift only - Secure clutch position sensor to slave
cylinder using bolts.
8. Sportshift only - Secure clutch position sensor harness
to side of torque tube using clips.
9. Sportshift only - Secure clutch position sensor harness
to top of torque tube using clip.
10. Sportshift only - Connect multiplug between clutch
position sensor and transmission harness.
Warning
Always connect the battery ea rth (+ ve) terminal first.
Repair Operation Time (ROT)
Warning
The torque tube is heavy. To avoid personal injury or damage to the torque tube, torque tube removal / installation is a two person operation.
Caution
Plug pipe connection to prevent ingress of moisture or dirt.
Fig. 1
$
Page 466 of 947
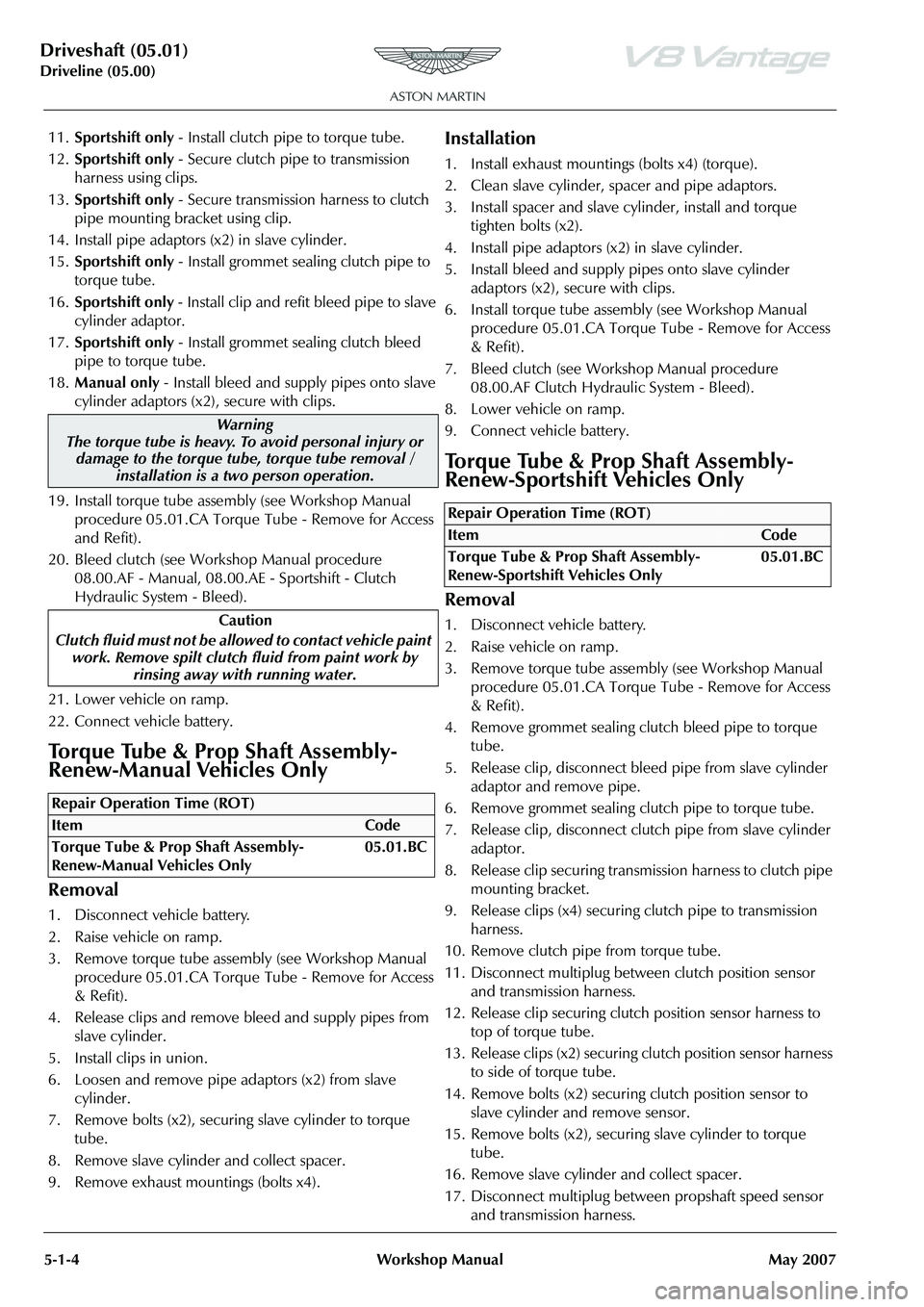
Driveshaft (05.01)
Driveline (05.00)5-1-4 Workshop Manual May 2007
11. Sportshift only - Install clutch pipe to torque tube.
12. Sportshift only - Secure clutch pipe to transmission
harness using clips.
13. Sportshift only - Secure transmission harness to clutch
pipe mounting bracket using clip.
14. Install pipe adaptors (x2) in slave cylinder.
15. Sportshift only - Install grommet sealing clutch pipe to
torque tube.
16. Sportshift only - Install clip and refit bleed pipe to slave
cylinder adaptor.
17. Sportshift only - Install grommet sealing clutch bleed
pipe to torque tube.
18. Manual only - Install bleed and supply pipes onto slave
cylinder adaptors (x2), secure with clips.
19. Install torque tube assembly (see Workshop Manual procedure 05.01.CA Torque Tube - Remove for Access
and Refit).
20. Bleed clutch (see Workshop Manual procedure 08.00.AF - Manual, 08.00.AE - Sportshift - Clutch
Hydraulic System - Bleed).
21. Lower vehicle on ramp.
22. Connect vehicle battery.
Torque Tube & Prop Shaft Assembly-
Renew
-Manual Vehicles Only
Removal
1. Disconnect vehicle battery.
2. Raise vehicle on ramp.
3. Remove torque tube assembly (see Workshop Manual procedure 05.01.CA Torque Tube - Remove for Access
& Refit).
4. Release clips and remove bleed and supply pipes from slave cylinder.
5. Install clips in union.
6. Loosen and remove pipe adaptors (x2) from slave cylinder.
7. Remove bolts (x2), securing slave cylinder to torque
tube.
8. Remove slave cylinder and collect spacer.
9. Remove exhaust mountings (bolts x4).
Installation
1. Install exhaust mountings (bolts x4) (torque).
2. Clean slave cylinder, spacer and pipe adaptors.
3. Install spacer and slave cylinder, install and torque tighten bolts (x2).
4. Install pipe adaptors (x2) in slave cylinder.
5. Install bleed and supply pipes onto slave cylinder adaptors (x2), secure with clips.
6. Install torque tube assembly (see Workshop Manual procedure 05.01.CA Torque Tube - Remove for Access
& Refit).
7. Bleed clutch (see Workshop Manual procedure 08.00.AF Clutch Hydraulic System - Bleed).
8. Lower vehicle on ramp.
9. Connect vehicle battery.
Torque Tube & Prop Shaft Assembly-
Renew
-Sportshift Vehicles Only
Removal
1. Disconnect vehicle battery.
2. Raise vehicle on ramp.
3. Remove torque tube assembly (see Workshop Manual procedure 05.01.CA Torque Tube - Remove for Access
& Refit).
4. Remove grommet sealing clutch bleed pipe to torque tube.
5. Release clip, disconnect bleed pipe from slave cylinder adaptor and remove pipe.
6. Remove grommet sealing clutch pipe to torque tube.
7. Release clip, disconnect clutch pipe from slave cylinder adaptor.
8. Release clip securing transmission harness to clutch pipe mounting bracket.
9. Release clips (x4) securing clutch pipe to transmission harness.
10. Remove clutch pipe from torque tube.
11. Disconnect multiplug betwee n clutch position sensor
and transmission harness.
12. Release clip securing clutch position sensor harness to
top of torque tube.
13. Release clips (x2) securing clutch position sensor harness to side of torque tube.
14. Remove bolts (x2) securing clutch position sensor to slave cylinder and remove sensor.
15. Remove bolts (x2), securing slave cylinder to torque tube.
16. Remove slave cylinder and collect spacer.
17. Disconnect multiplug between propshaft speed sensor and transmission harness.
Warning
The torque tube is heavy. To avoid personal injury or damage to the torque tube, torque tube removal / installation is a two person operation.
Caution
Clutch fluid must not be allowed to contact vehicle paint work. Remove spilt clutch fluid from paint work by
rinsing away with running water.
Repair Operation Time (ROT)
Repair Operation Time (ROT)
ItemCode
Torque Tube & Prop Shaft Assembly-
Renew-Sportshift Vehicles Only 05.01.BC
Page 467 of 947
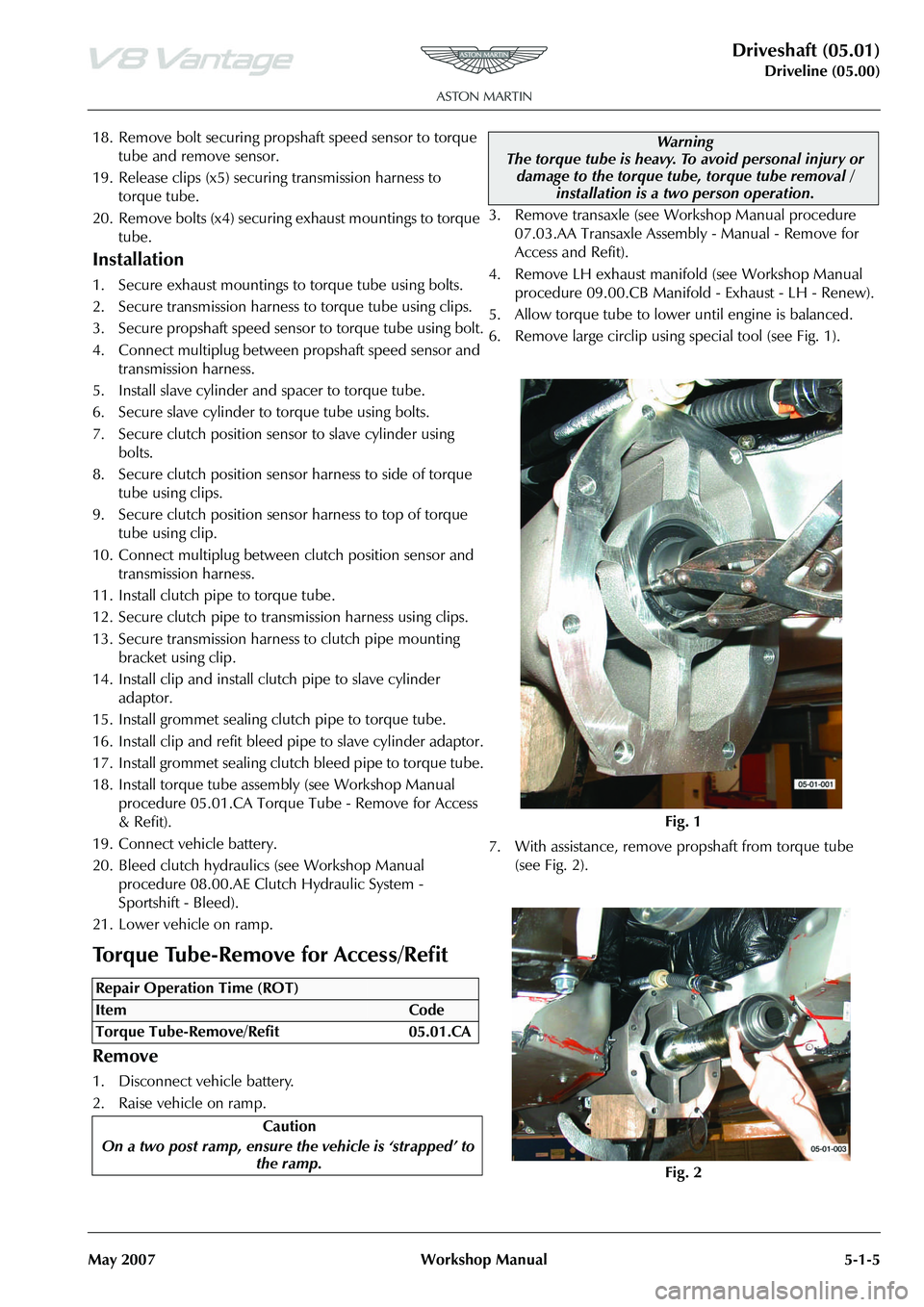
Driveshaft (05.01)
Driveline (05.00)
May 2007 Workshop Manual 5-1-5
18. Remove bolt securing propshaft speed sensor to torque tube and remove sensor.
19. Release clips (x5) securing transmission harness to torque tube.
20. Remove bolts (x4) securing exhaust mountings to torque tube.
Installation
1. Secure exhaust mountings to torque tube using bolts.
2. Secure transmission harness to torque tube using clips.
3. Secure propshaft speed sensor to torque tube using bolt.
4. Connect multiplug between propshaft speed sensor and transmission harness.
5. Install slave cylinder and spacer to torque tube.
6. Secure slave cylinder to torque tube using bolts.
7. Secure clutch position sensor to slave cylinder using bolts.
8. Secure clutch position sensor harness to side of torque
tube using clips.
9. Secure clutch position sensor harness to top of torque tube using clip.
10. Connect multiplug between clutch position sensor and transmission harness.
11. Install clutch pipe to torque tube.
12. Secure clutch pipe to transmission harness using clips.
13. Secure transmission harness to clutch pipe mounting bracket using clip.
14. Install clip and install clutch pipe to slave cylinder adaptor.
15. Install grommet sealing clutch pipe to torque tube.
16. Install clip and refit bleed pi pe to slave cylinder adaptor.
17. Install grommet sealing clutch bleed pipe to torque tube.
18. Install torque tube assembly (see Workshop Manual procedure 05.01.CA Torque Tube - Remove for Access
& Refit).
19. Connect vehicle battery.
20. Bleed clutch hy draulics (see Workshop Manual
procedure 08.00.AE Clutch Hydraulic System -
Sportshift - Bleed).
21. Lower vehicle on ramp.
Torque Tube-Remove for Access/Refit
Remove
1. Disconnect vehicle battery.
2. Raise vehicle on ramp. 3. Remove transaxle (see Workshop Manual procedure
07.03.AA Transaxle Assembly - Manual - Remove for
Access and Refit).
4. Remove LH exhaust manifo ld (see Workshop Manual
procedure 09.00.CB Manifold - Exhaust - LH - Renew).
5. Allow torque tube to lower until engine is balanced.
6. Remove large circlip using special tool (see Fig. 1).
7. With assistance, remove propshaft from torque tube (see Fig. 2).
Repair Operation Time (ROT)
Warning
The torque tube is heavy. To avoid personal injury or
damage to the torque tube, torque tube removal / installation is a two person operation.
Fig. 1
Fig. 2
Page 468 of 947
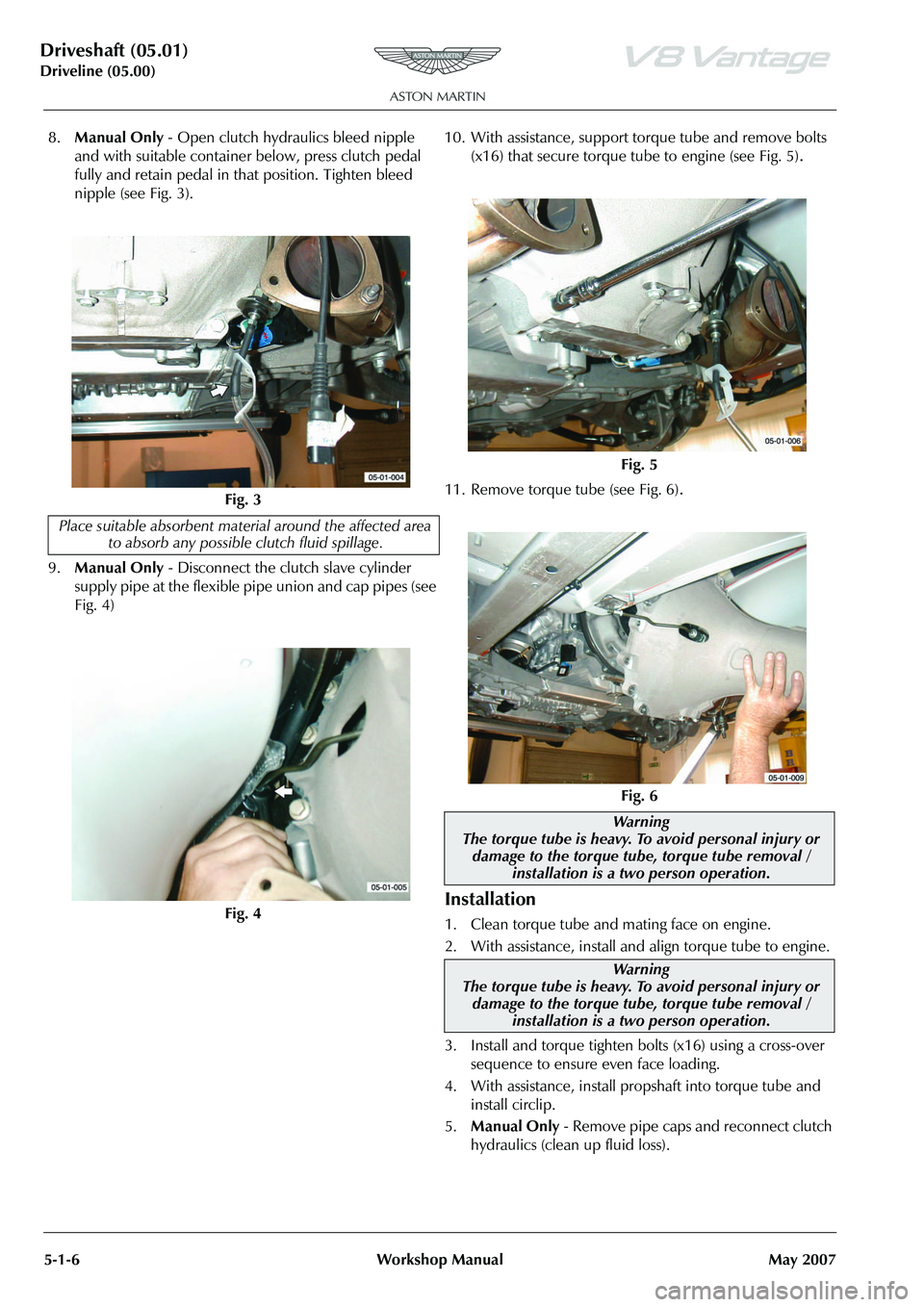
Driveshaft (05.01)
Driveline (05.00)5-1-6 Workshop Manual May 2007
8. Manual Only - Open clutch hydraulics bleed nipple
and with suitable container below, press clutch pedal
fully and retain pedal in that position. Tighten bleed
nipple (see Fig. 3).
9. Manual Only - Disconnect the clutch slave cylinder
supply pipe at the flexible pipe union and cap pipes (see
Fig. 4) 10. With assistance, support torque tube and remove bolts
(x16) that secure torque tube to engine (see Fig. 5)
.
11. Remove torque tube (see Fig. 6).
Installation
1. Clean torque tube and mating face on engine.
2. With assistance, install and align torque tube to engine.
3. Install and torque tighten bolts (x16) using a cross-over sequence to ensure even face loading.
4. With assistance, install propshaft into torque tube and install circlip.
5. Manual Only - Remove pipe caps and reconnect clutch
hydraulics (clean up fluid loss).
Fig. 3
Place suitable absorbent material around the affected area to absorb any possible clutch fluid spillage.
Fig. 4
Fig. 5
Fig. 6
Warning
The torque tube is heavy. To avoid personal injury or damage to the torque tube, torque tube removal / installation is a two person operation.
Warning
The torque tube is heavy. To avoid personal injury or damage to the torque tube, torque tube removal /
installation is a two person operation.
Page 469 of 947
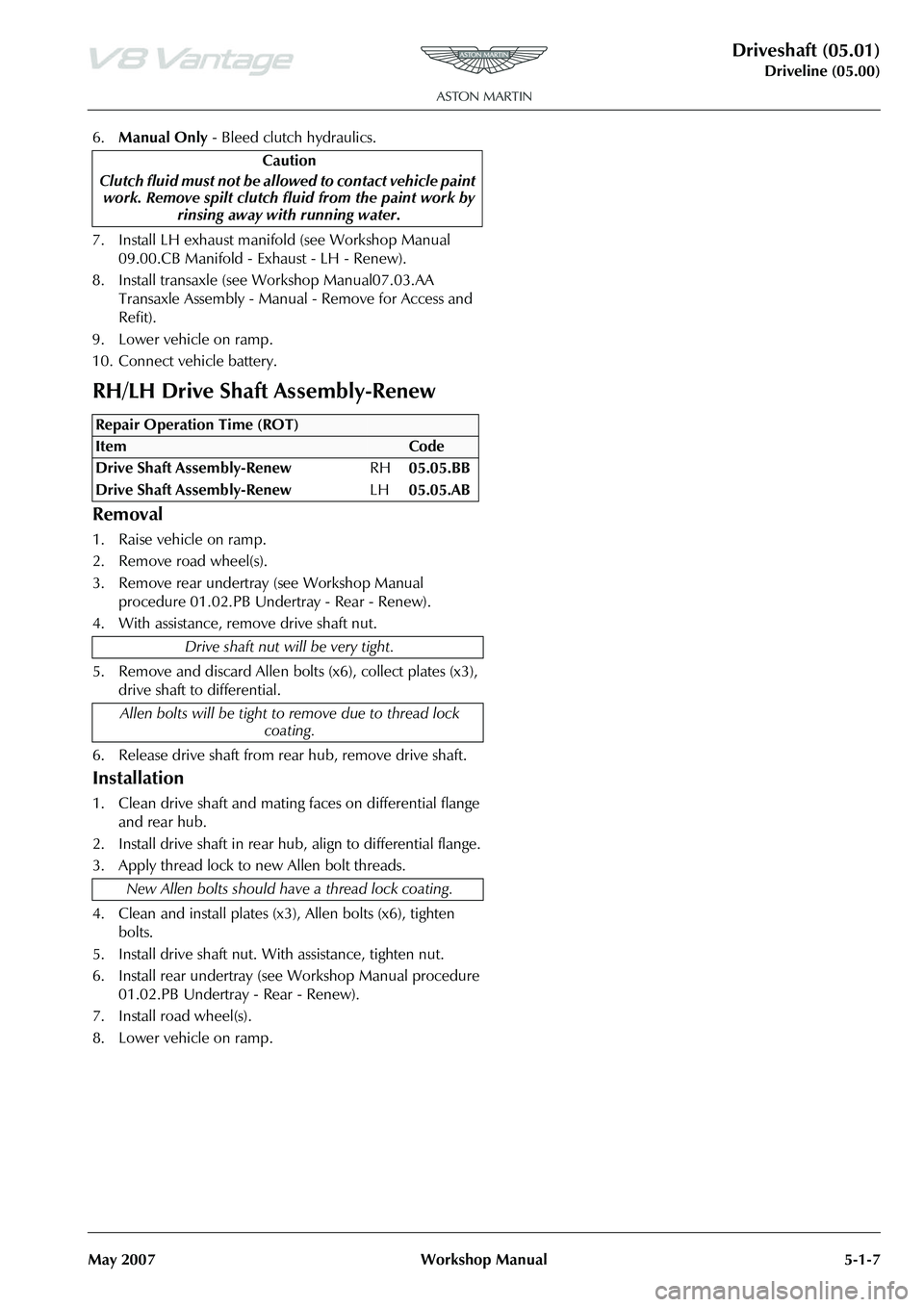
Driveshaft (05.01)
Driveline (05.00)
May 2007 Workshop Manual 5-1-7
6. Manual Only - Bleed clutch hydraulics.
7. Install LH exhaust manifold (see Workshop Manual 09.00.CB Manifold - Exhaust - LH - Renew).
8. Install transaxle (see Workshop Manual07.03.AA Transaxle Assembly - Manual - Remove for Access and
Refit).
9. Lower vehicle on ramp.
10. Connect vehicle battery.
RH/LH Drive Shaft Assembly-Renew
Removal
1. Raise vehicle on ramp.
2. Remove road wheel(s).
3. Remove rear undertray (see Workshop Manual procedure 01.02.PB Undertray - Rear - Renew).
4. With assistance, remove drive shaft nut.
5. Remove and discard Allen bolt s (x6), collect plates (x3),
drive shaft to differential.
6. Release drive shaft from rear hub, remove drive shaft.
Installation
1. Clean drive shaft and mating faces on differential flange and rear hub.
2. Install drive shaft in rear hub, align to differential flange.
3. Apply thread lock to new Allen bolt threads.
4. Clean and install plates (x3), Allen bolts (x6), tighten bolts.
5. Install drive shaft nut. With assistance, tighten nut.
6. Install rear undertray (see Workshop Manual procedure 01.02.PB Undertray - Rear - Renew).
7. Install road wheel(s).
8. Lower vehicle on ramp. Caution
Clutch fluid must not be allowed to contact vehicle paint work. Remove spilt clutch fl uid from the paint work by
rinsing away with running water.
Repair Operation Time (ROT)
Page 470 of 947
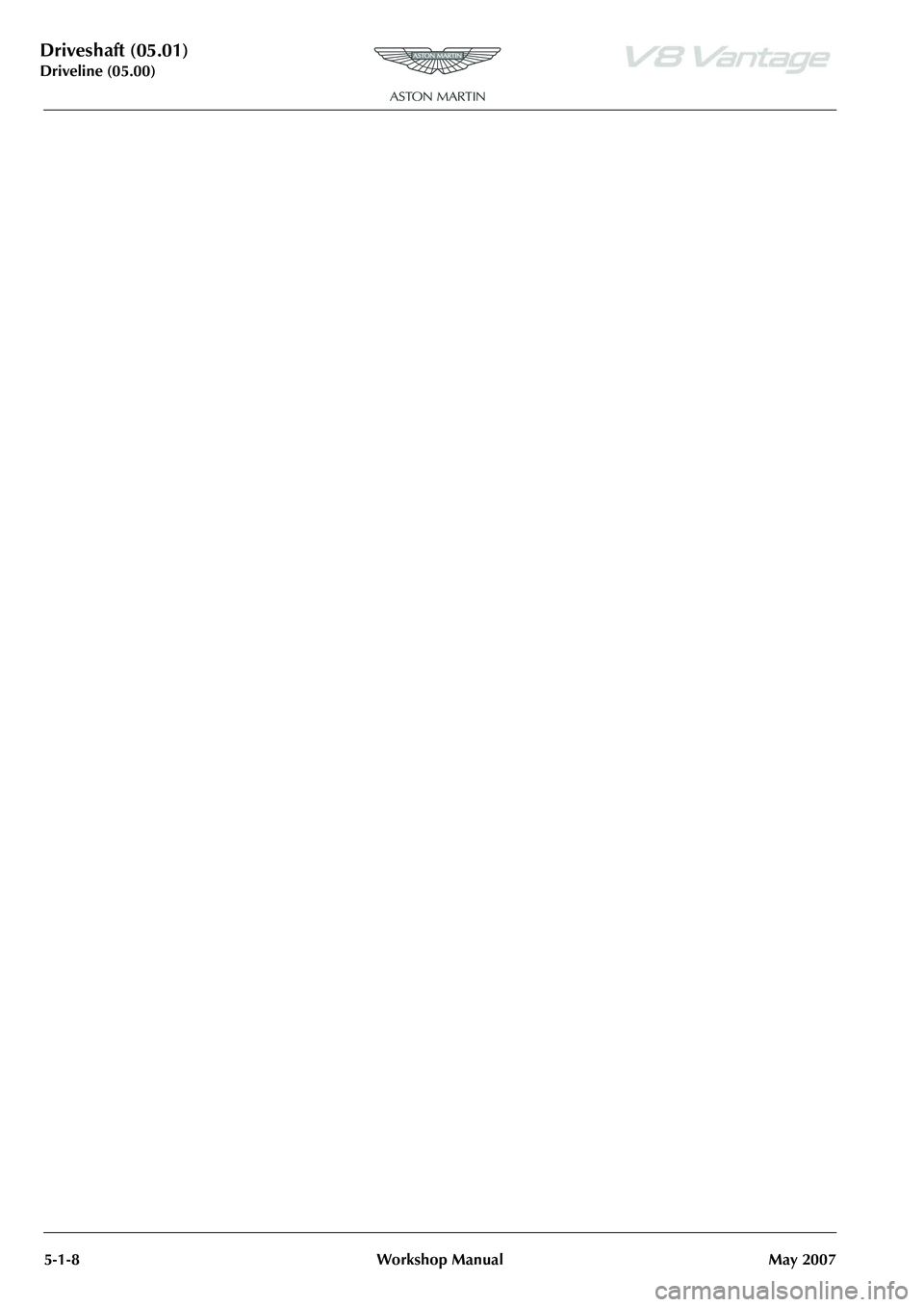
Driveshaft (05.01)
Driveline (05.00)5-1-8 Workshop Manual May 2007