CHERY TIGGO 2009 Service Repair Manual
Manufacturer: CHERY, Model Year: 2009, Model line: TIGGO, Model: CHERY TIGGO 2009Pages: 1903, PDF Size: 33.38 MB
Page 1271 of 1903
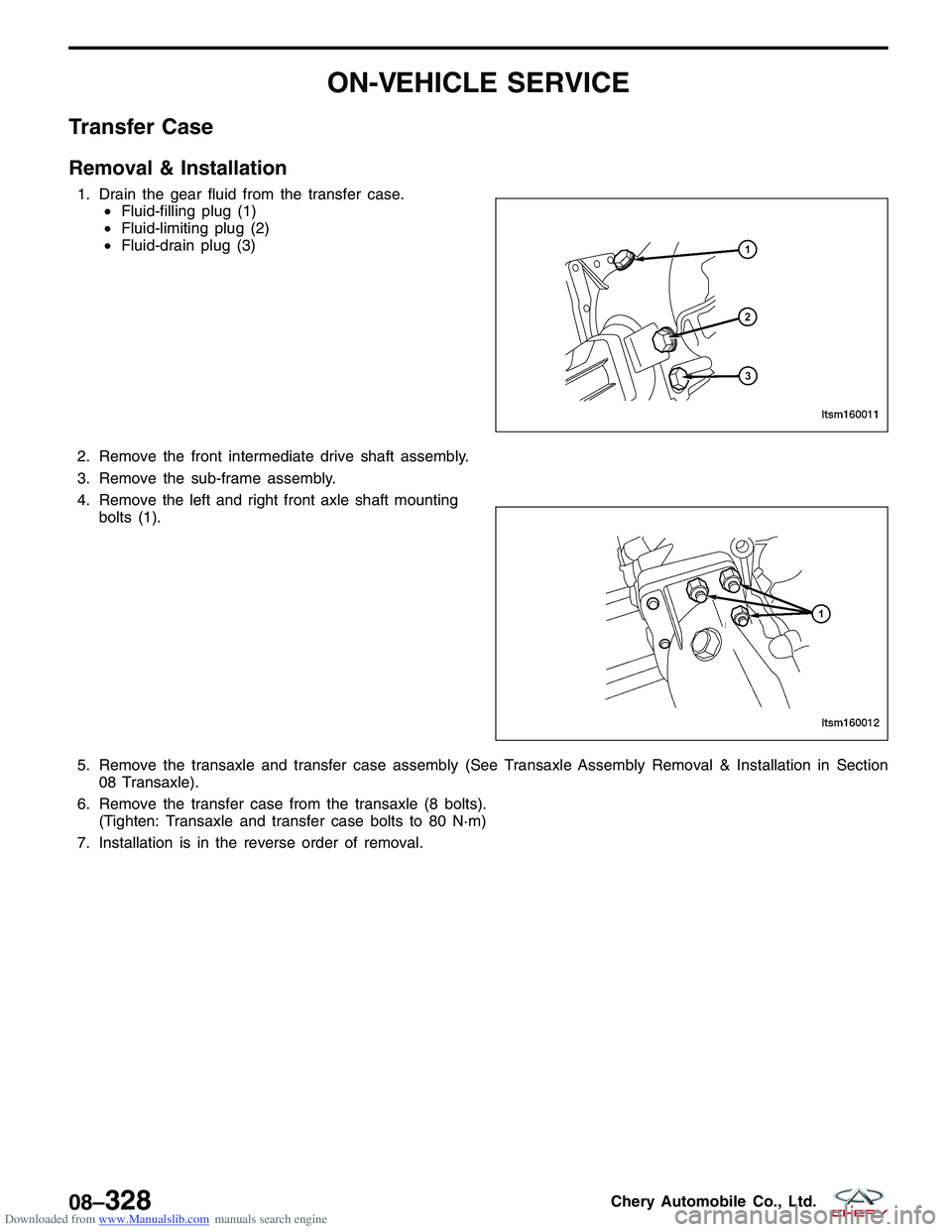
Downloaded from www.Manualslib.com manuals search engine ON-VEHICLE SERVICE
Transfer Case
Removal & Installation
1. Drain the gear fluid from the transfer case.•Fluid-filling plug (1)
• Fluid-limiting plug (2)
• Fluid-drain plug (3)
2. Remove the front intermediate drive shaft assembly.
3. Remove the sub-frame assembly.
4. Remove the left and right front axle shaft mounting bolts (1).
5. Remove the transaxle and transfer case assembly (See Transaxle Assembly Removal & Installation in Section 08 Transaxle).
6. Remove the transfer case from the transaxle (8 bolts). (Tighten: Transaxle and transfer case bolts to 80 N·m)
7. Installation is in the reverse order of removal.
LTSM160011
LTSM160012
08–328Chery Automobile Co., Ltd.
Page 1272 of 1903
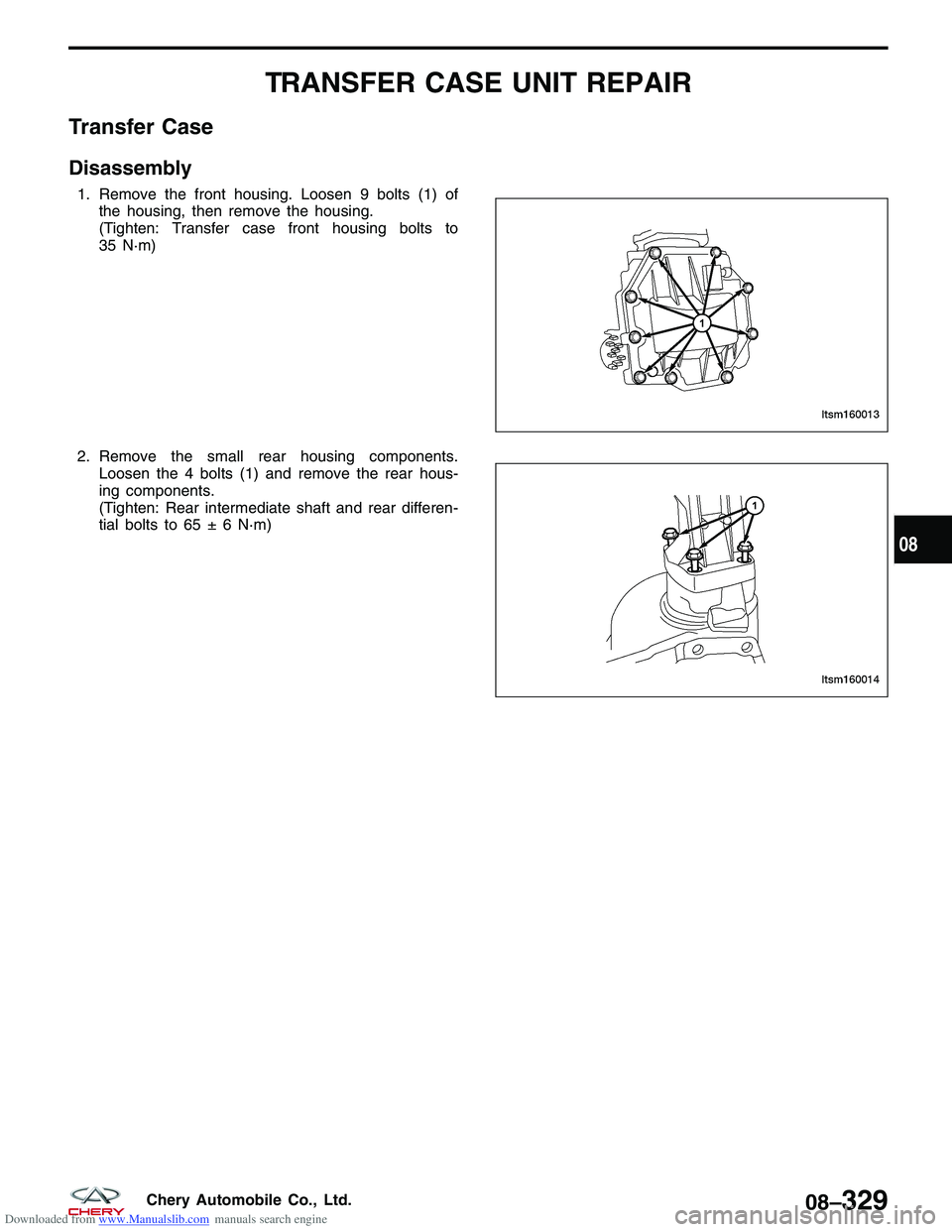
Downloaded from www.Manualslib.com manuals search engine TRANSFER CASE UNIT REPAIR
Transfer Case
Disassembly
1. Remove the front housing. Loosen 9 bolts (1) ofthe housing, then remove the housing.
(Tighten: Transfer case front housing bolts to
35 N·m)
2. Remove the small rear housing components. Loosen the 4 bolts (1) and remove the rear hous-
ing components.
(Tighten: Rear intermediate shaft and rear differen-
tial bolts to 65 ± 6 N·m)
LTSM160013
LTSM160014
08
08–329Chery Automobile Co., Ltd.
Page 1273 of 1903
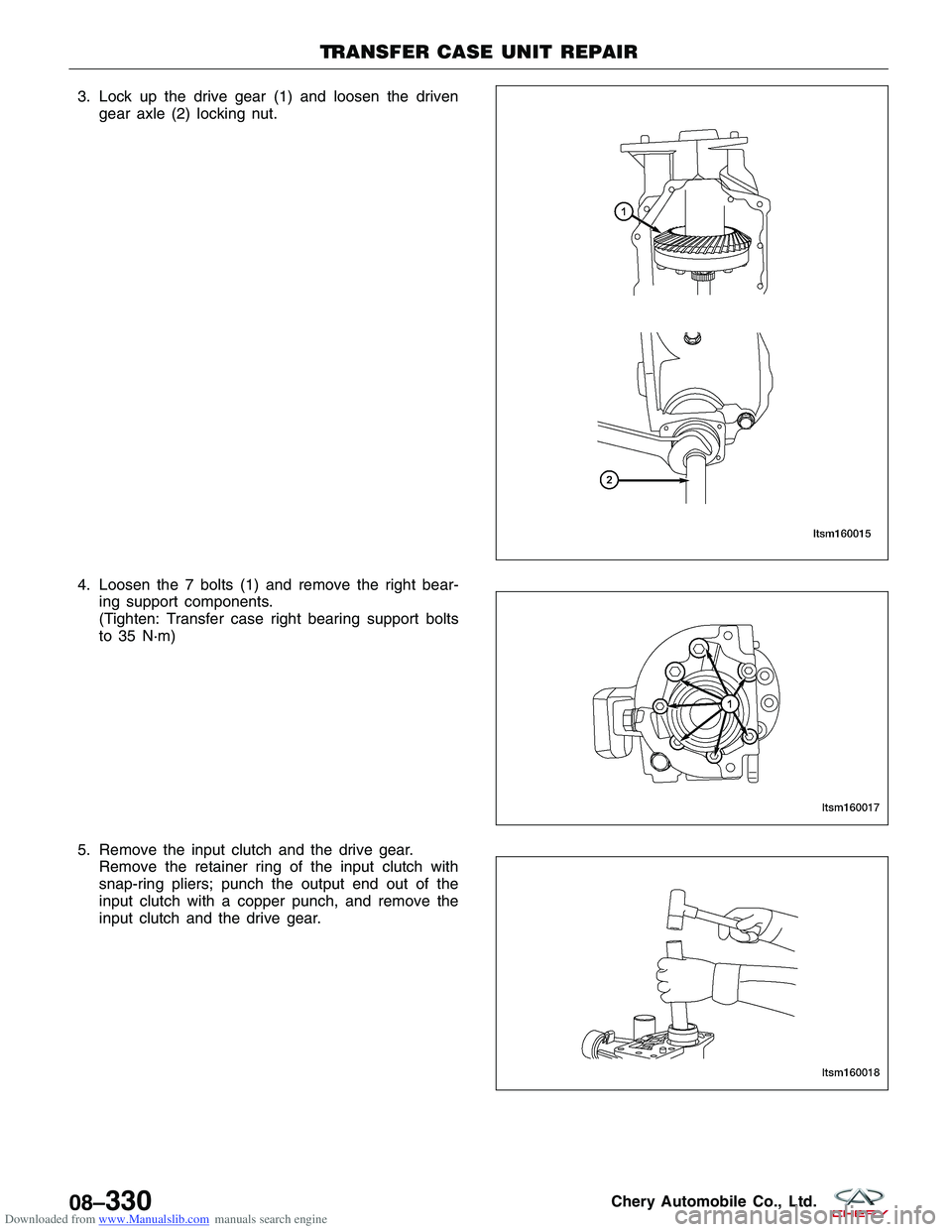
Downloaded from www.Manualslib.com manuals search engine 3. Lock up the drive gear (1) and loosen the drivengear axle (2) locking nut.
4. Loosen the 7 bolts (1) and remove the right bear- ing support components.
(Tighten: Transfer case right bearing support bolts
to 35 N·m)
5. Remove the input clutch and the drive gear. Remove the retainer ring of the input clutch with
snap-ring pliers; punch the output end out of the
input clutch with a copper punch, and remove the
input clutch and the drive gear.
TRANSFER CASE UNIT REPAIR
LTSM160015
LTSM160017
LTSM160018
08–330Chery Automobile Co., Ltd.
Page 1274 of 1903
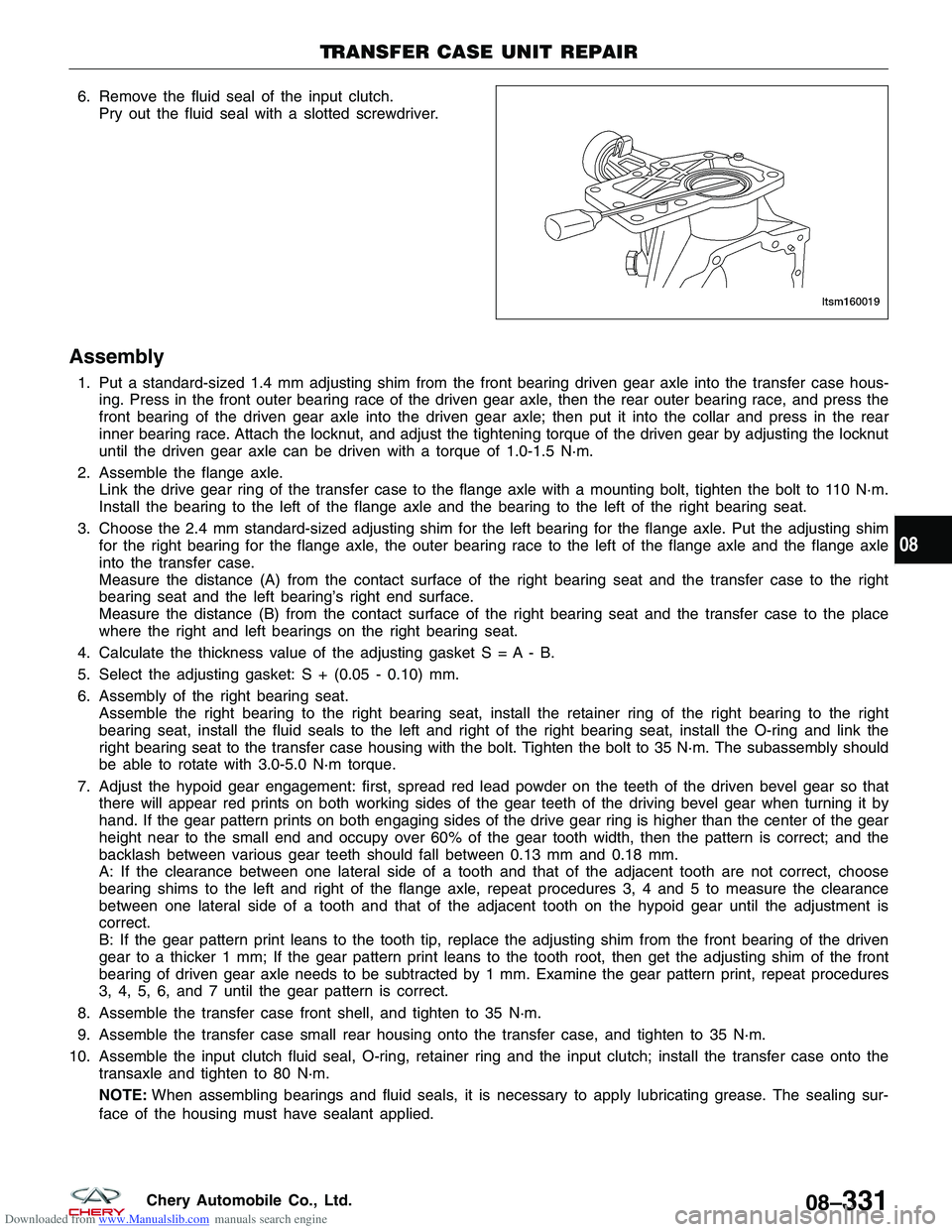
Downloaded from www.Manualslib.com manuals search engine 6. Remove the fluid seal of the input clutch.Pry out the fluid seal with a slotted screwdriver.
Assembly
1. Put a standard-sized 1.4 mm adjusting shim from the front bearing driven gear axle into the transfer case hous-ing. Press in the front outer bearing race of the driven gear axle, then the rear outer bearing race, and press the
front bearing of the driven gear axle into the driven gear axle; then put it into the collar and press in the rear
inner bearing race. Attach the locknut, and adjust the tightening torque of the driven gear by adjusting the locknut
until the driven gear axle can be driven with a torque of 1.0-1.5 N·m.
2. Assemble the flange axle. Link the drive gear ring of the transfer case to the flange axle with a mounting bolt, tighten the bolt to 110 N·m.
Install the bearing to the left of the flange axle and the bearing to the left of the right bearing seat.
3. Choose the 2.4 mm standard-sized adjusting shim for the left bearing for the flange axle. Put the adjusting shim for the right bearing for the flange axle, the outer bearing race to the left of the flange axle and the flange axle
into the transfer case.
Measure the distance (A) from the contact surface of the right bearing seat and the transfer case to the right
bearing seat and the left bearing’s right end surface.
Measure the distance (B) from the contact surface of the right bearing seat and the transfer case to the place
where the right and left bearings on the right bearing seat.
4. Calculate the thickness value of the adjusting gasket S = A - B.
5. Select the adjusting gasket: S + (0.05 - 0.10) mm.
6. Assembly of the right bearing seat. Assemble the right bearing to the right bearing seat, install the retainer ring of the right bearing to the right
bearing seat, install the fluid seals to the left and right of the right bearing seat, install the O-ring and link the
right bearing seat to the transfer case housing with the bolt. Tighten the bolt to 35 N·m. The subassembly should
be able to rotate with 3.0-5.0 N·m torque.
7. Adjust the hypoid gear engagement: first, spread red lead powder on the teeth of the driven bevel gear so that there will appear red prints on both working sides of the gear teeth of the driving bevel gear when turning it by
hand. If the gear pattern prints on both engaging sides of the drive gear ring is higher than the center of the gear
height near to the small end and occupy over 60% of the gear tooth width, then the pattern is correct; and the
backlash between various gear teeth should fall between 0.13 mm and 0.18 mm.
A: If the clearance between one lateral side of a tooth and that of the adjacent tooth are not correct, choose
bearing shims to the left and right of the flange axle, repeat procedures 3, 4 and 5 to measure the clearance
between one lateral side of a tooth and that of the adjacent tooth on the hypoid gear until the adjustment is
correct.
B: If the gear pattern print leans to the tooth tip, replace the adjusting shim from the front bearing of the driven
gear to a thicker 1 mm; If the gear pattern print leans to the tooth root, then get the adjusting shim of the front
bearing of driven gear axle needs to be subtracted by 1 mm. Examine the gear pattern print, repeat procedures
3, 4, 5, 6, and 7 until the gear pattern is correct.
8. Assemble the transfer case front shell, and tighten to 35 N·m.
9. Assemble the transfer case small rear housing onto the transfer case, and tighten to 35 N·m.
10. Assemble the input clutch fluid seal, O-ring, retainer ring and the input clutch; install the transfer case onto the transaxle and tighten to 80 N·m.
NOTE: When assembling bearings and fluid seals, it is necessary to apply lubricating grease. The sealing sur-
face of the housing must have sealant applied.
TRANSFER CASE UNIT REPAIR
LTSM160019
08
08–331Chery Automobile Co., Ltd.
Page 1275 of 1903
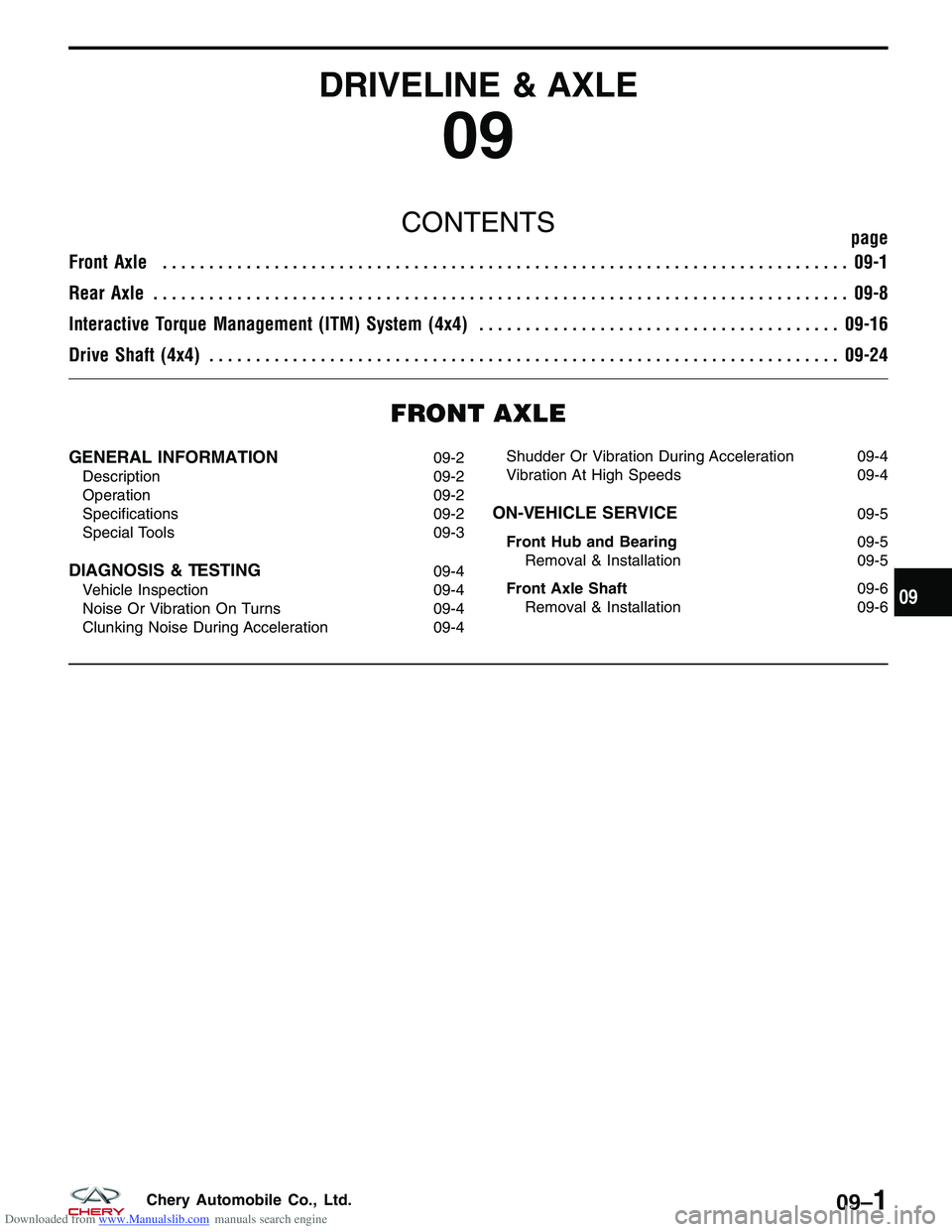
Downloaded from www.Manualslib.com manuals search engine DRIVELINE & AXLE
09
CONTENTSpage
Front Axle ........................................................................\
.. 09-1
Rear Axle ........................................................................\
... 09-8
Interactive Torque Management (ITM) System (4x4) .......................................09-16
Drive Shaft (4x4) .................................................................... 09-24
FRONT AXLE
GENERAL INFORMATION09-2
Description 09-2
Operation 09-2
Specifications 09-2
Special Tools 09-3
DIAGNOSIS & TESTING09-4
Vehicle Inspection 09-4
Noise Or Vibration On Turns 09-4
Clunking Noise During Acceleration 09-4 Shudder Or Vibration During Acceleration 09-4
Vibration At High Speeds 09-4
ON-VEHICLE SERVICE09-5
Front Hub and Bearing 09-5
Removal & Installation 09-5
Front Axle Shaft 09-6
Removal & Installation 09-6
09
09–1Chery Automobile Co., Ltd.
Page 1276 of 1903
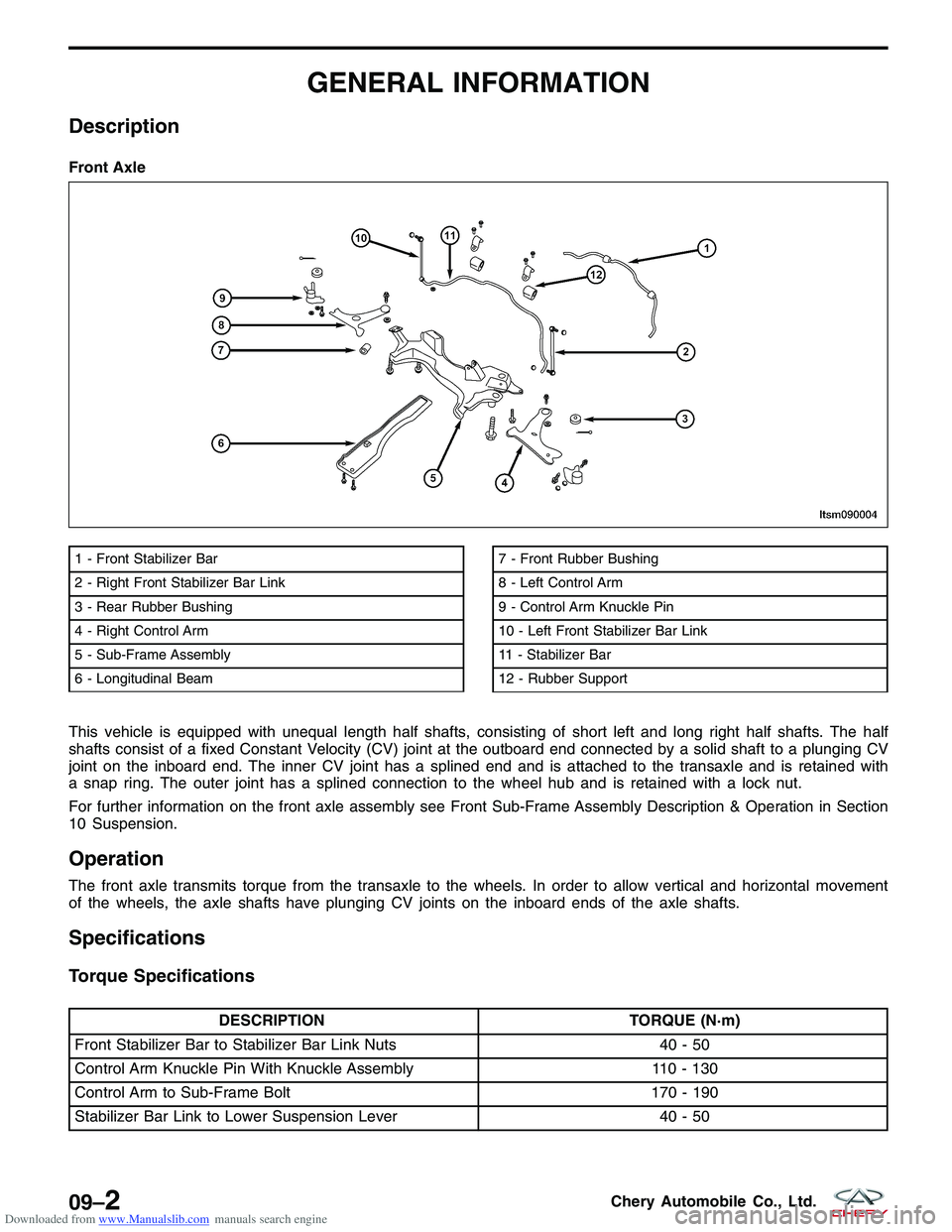
Downloaded from www.Manualslib.com manuals search engine GENERAL INFORMATION
Description
This vehicle is equipped with unequal length half shafts, consisting of short left and long right half shafts. The half
shafts consist of a fixed Constant Velocity (CV) joint at the outboard end connected by a solid shaft to a plunging CV
joint on the inboard end. The inner CV joint has a splined end and is attached to the transaxle and is retained with
a snap ring. The outer joint has a splined connection to the wheel hub and is retained with a lock nut.
For further information on the front axle assembly see Front Sub-Frame Assembly Description & Operation in Section
10 Suspension.
Operation
The front axle transmits torque from the transaxle to the wheels. In order to allow vertical and horizontal movement
of the wheels, the axle shafts have plunging CV joints on the inboard ends of the axle shafts.
Specifications
Torque Specifications
DESCRIPTIONTORQUE (N·m)
Front Stabilizer Bar to Stabilizer Bar Link Nuts 40 - 50
Control Arm Knuckle Pin With Knuckle Assembly 110 - 130
Control Arm to Sub-Frame Bolt 170 - 190
Stabilizer Bar Link to Lower Suspension Lever 40 - 50
Front Axle
1 - Front Stabilizer Bar
2 - Right Front Stabilizer Bar Link
3 - Rear Rubber Bushing
4 - Right Control Arm
5 - Sub-Frame Assembly
6 - Longitudinal Beam7 - Front Rubber Bushing
8 - Left Control Arm
9 - Control Arm Knuckle Pin
10 - Left Front Stabilizer Bar Link
11 - Stabilizer Bar
12 - Rubber Support
LTSM090004
09–2Chery Automobile Co., Ltd.
Page 1277 of 1903
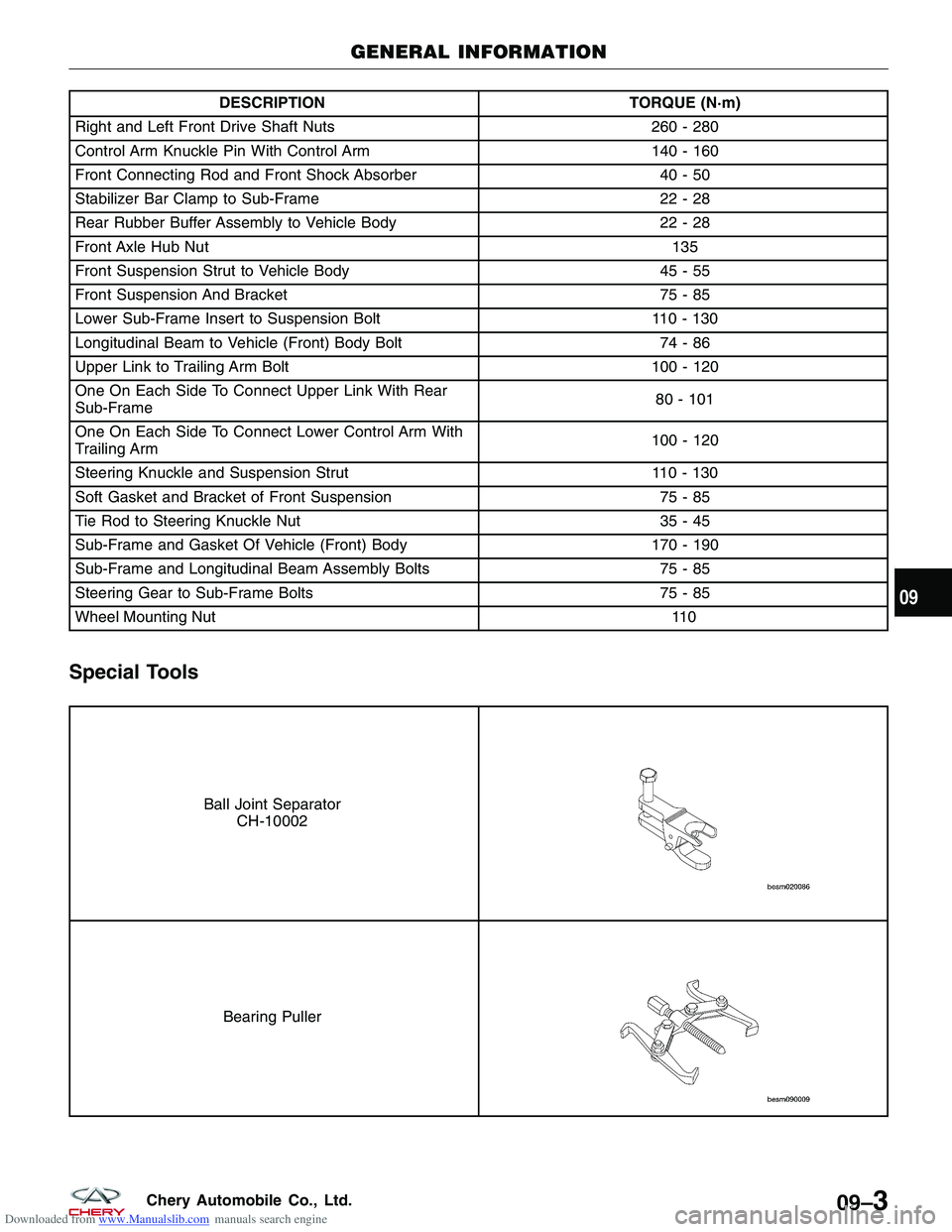
Downloaded from www.Manualslib.com manuals search engine DESCRIPTIONTORQUE (N·m)
Right and Left Front Drive Shaft Nuts 260 - 280
Control Arm Knuckle Pin With Control Arm 140 - 160
Front Connecting Rod and Front Shock Absorber 40 - 50
Stabilizer Bar Clamp to Sub-Frame 22 - 28
Rear Rubber Buffer Assembly to Vehicle Body 22 - 28
Front Axle Hub Nut 135
Front Suspension Strut to Vehicle Body 45 - 55
Front Suspension And Bracket 75 - 85
Lower Sub-Frame Insert to Suspension Bolt 110 - 130
Longitudinal Beam to Vehicle (Front) Body Bolt 74 - 86
Upper Link to Trailing Arm Bolt 100 - 120
One On Each Side To Connect Upper Link With Rear
Sub-Frame 80 - 101
One On Each Side To Connect Lower Control Arm With
Trailing Arm 100 - 120
Steering Knuckle and Suspension Strut 110 - 130
Soft Gasket and Bracket of Front Suspension 75 - 85
Tie Rod to Steering Knuckle Nut 35 - 45
Sub-Frame and Gasket Of Vehicle (Front) Body 170 - 190
Sub-Frame and Longitudinal Beam Assembly Bolts 75 - 85
Steering Gear to Sub-Frame Bolts 75 - 85
Wheel Mounting Nut \
\
11 0
Special Tools
Ball Joint Separator CH-10002
Bearing Puller
GENERAL INFORMATION
09
09–3Chery Automobile Co., Ltd.
Page 1278 of 1903
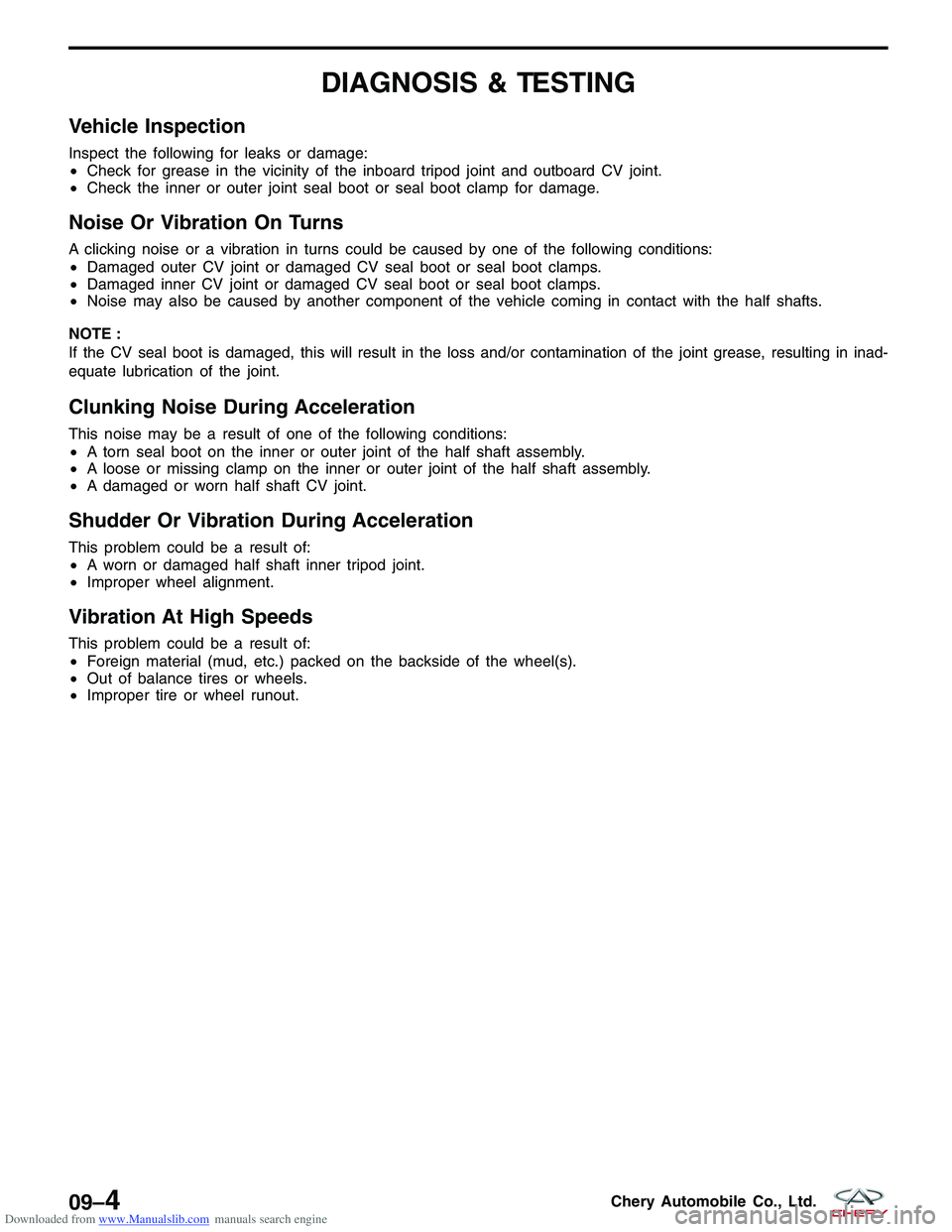
Downloaded from www.Manualslib.com manuals search engine DIAGNOSIS & TESTING
Vehicle Inspection
Inspect the following for leaks or damage:
•Check for grease in the vicinity of the inboard tripod joint and outboard CV joint.
• Check the inner or outer joint seal boot or seal boot clamp for damage.
Noise Or Vibration On Turns
A clicking noise or a vibration in turns could be caused by one of the following conditions:
•Damaged outer CV joint or damaged CV seal boot or seal boot clamps.
• Damaged inner CV joint or damaged CV seal boot or seal boot clamps.
• Noise may also be caused by another component of the vehicle coming in contact with the half shafts.
NOTE :
If the CV seal boot is damaged, this will result in the loss and/or contamination of the joint grease, resulting in inad-
equate lubrication of the joint.
Clunking Noise During Acceleration
This noise may be a result of one of the following conditions:
• A torn seal boot on the inner or outer joint of the half shaft assembly.
• A loose or missing clamp on the inner or outer joint of the half shaft assembly.
• A damaged or worn half shaft CV joint.
Shudder Or Vibration During Acceleration
This problem could be a result of:
•A worn or damaged half shaft inner tripod joint.
• Improper wheel alignment.
Vibration At High Speeds
This problem could be a result of:
•Foreign material (mud, etc.) packed on the backside of the wheel(s).
• Out of balance tires or wheels.
• Improper tire or wheel runout.
09–4Chery Automobile Co., Ltd.
Page 1279 of 1903
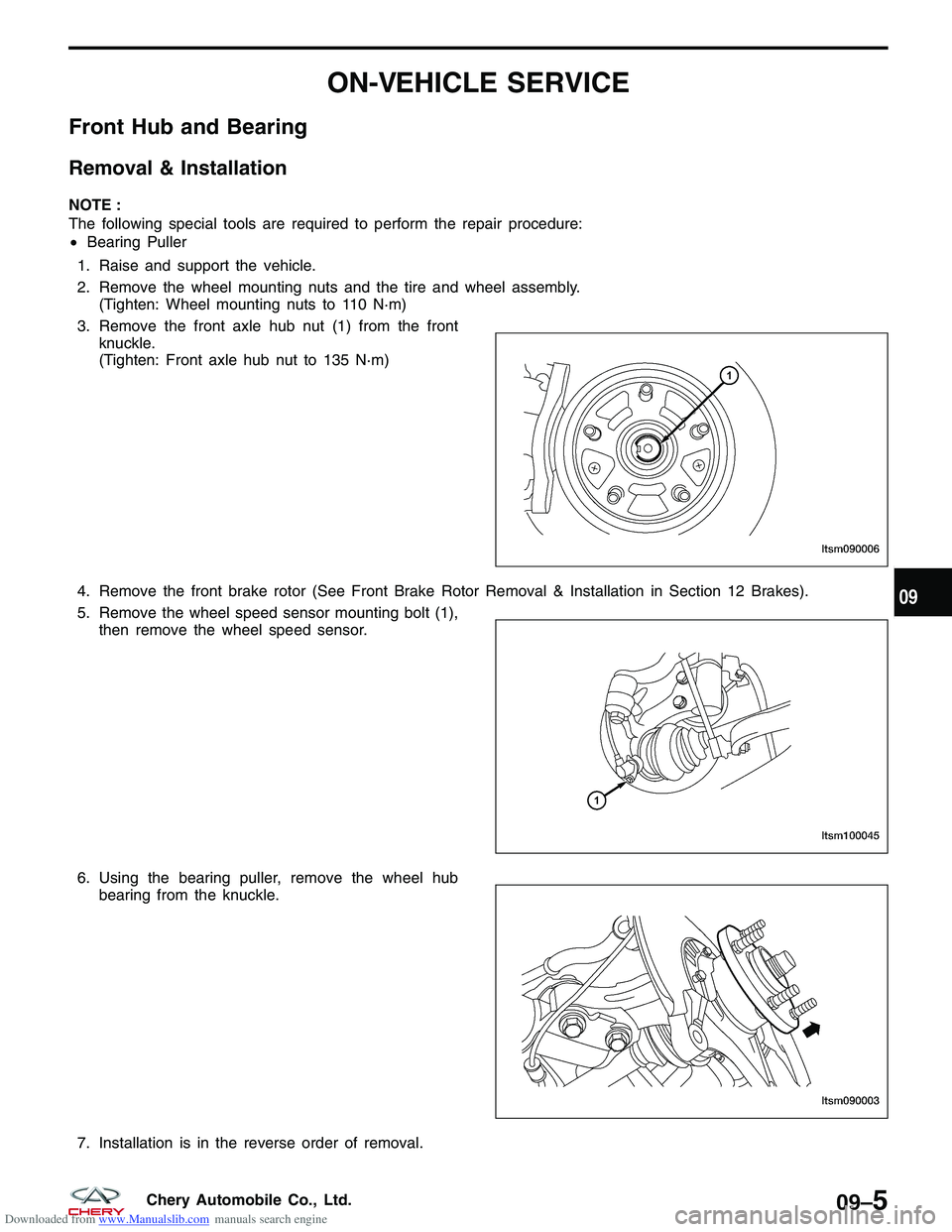
Downloaded from www.Manualslib.com manuals search engine ON-VEHICLE SERVICE
Front Hub and Bearing
Removal & Installation
NOTE :
The following special tools are required to perform the repair procedure:
•Bearing Puller
1. Raise and support the vehicle.
2. Remove the wheel mounting nuts and the tire and wheel assembly. (Tighten: Wheel mounting nuts to 110 N·m)
3. Remove the front axle hub nut (1) from the front knuckle.
(Tighten: Front axle hub nut to 135 N·m)
4. Remove the front brake rotor (See Front Brake Rotor Removal & Installation in Section 12 Brakes).
5. Remove the wheel speed sensor mounting bolt (1), then remove the wheel speed sensor.
6. Using the bearing puller, remove the wheel hub bearing from the knuckle.
7. Installation is in the reverse order of removal.
LTSM090006
LTSM100045
LTSM090003
09
09–5Chery Automobile Co., Ltd.
Page 1280 of 1903
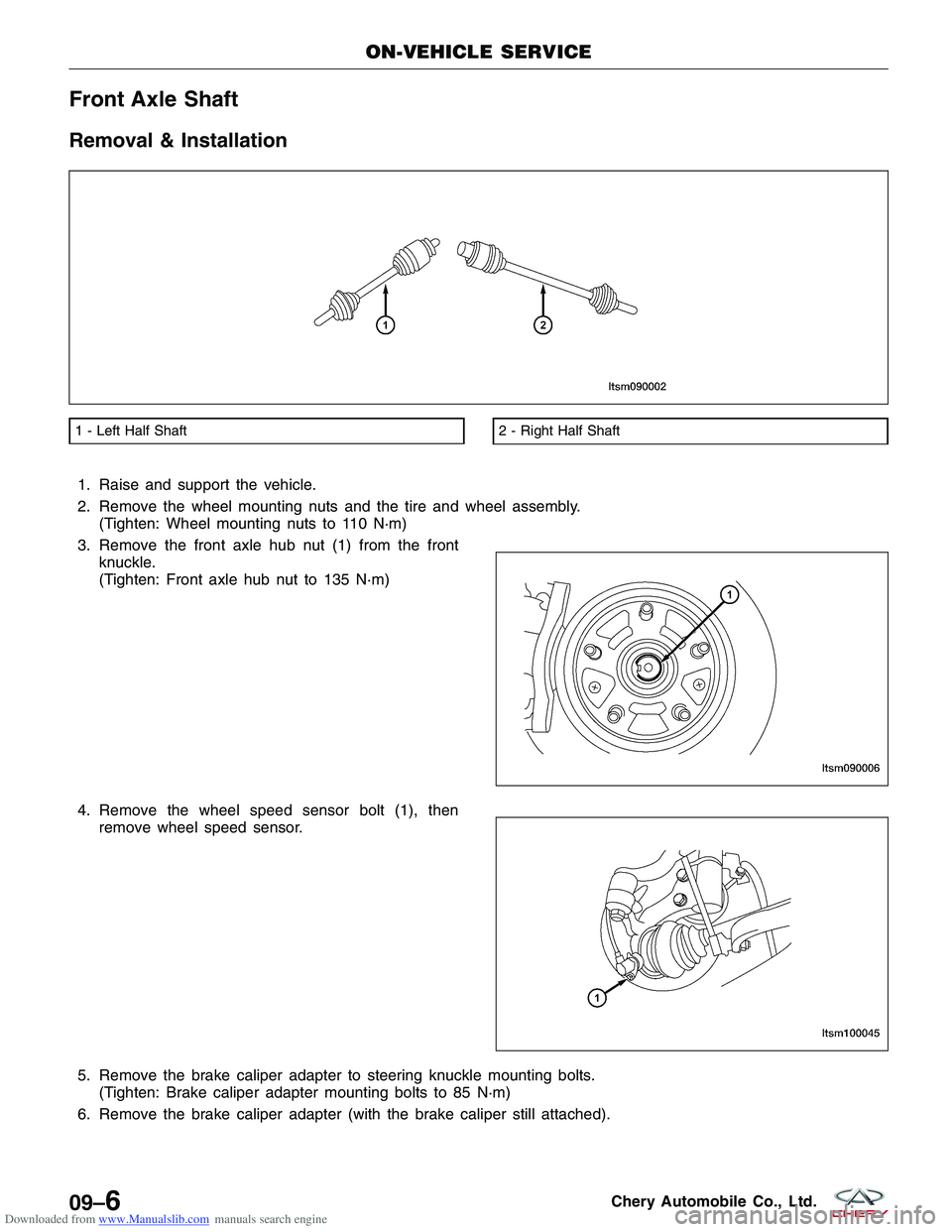
Downloaded from www.Manualslib.com manuals search engine Front Axle Shaft
Removal & Installation
1. Raise and support the vehicle.
2. Remove the wheel mounting nuts and the tire and wheel assembly.(Tighten: Wheel mounting nuts to 110 N·m)
3. Remove the front axle hub nut (1) from the front knuckle.
(Tighten: Front axle hub nut to 135 N·m)
4. Remove the wheel speed sensor bolt (1), then remove wheel speed sensor.
5. Remove the brake caliper adapter to steering knuckle mounting bolts. (Tighten: Brake caliper adapter mounting bolts to 85 N·m)
6. Remove the brake caliper adapter (with the brake caliper still attached).
1 - Left Half Shaft2 - Right Half Shaft
ON-VEHICLE SERVICE
LTSM090002
LTSM090006
LTSM100045
09–6Chery Automobile Co., Ltd.