CHEVROLET CAMARO 1967 1.G Chassis Workshop Manual
Manufacturer: CHEVROLET, Model Year: 1967, Model line: CAMARO, Model: CHEVROLET CAMARO 1967 1.GPages: 659, PDF Size: 114.24 MB
Page 261 of 659
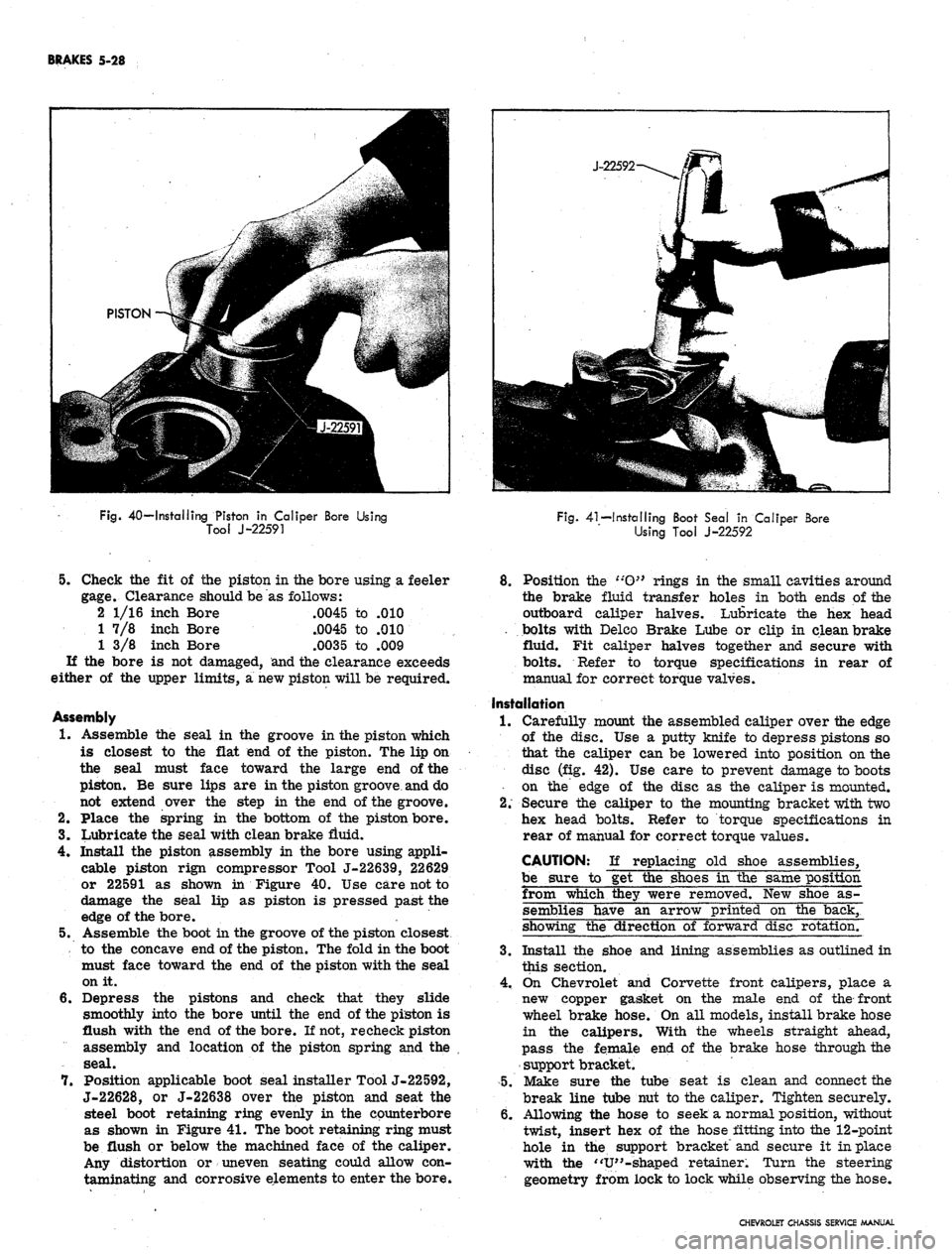
BRAKES 5-28
Fig.
40—Installing Piston in Caliper Bore Using
Tool J-22591
Fig.
41—Installing Boot Seal in Caliper Bore
Using Tool J-22592
5.
Check the fit of the piston in the bore using a feeler
gage.
Clearance should be as follows:
2 1/16 inch Bore .0045 to .010
1 7/8 inch Bore .0045 to .010
1 3/8 inch Bore .0035 to .009
If the bore is not damaged, and the clearance exceeds
either of the upper limits, a new piston will be required.
Assembly
1.
Assemble the seal in the groove in the piston which
is closest to the flat end of the piston. The lip on
the seal must face toward the large end of the
piston. Be sure lips are in the piston groove and do
not extend over the step in the end of the groove.
2.
Place the spring in the bottom of the piston bore.
3.
Lubricate the seal with dean brake fluid.
4.
Install the piston assembly in the bore using appli-
cable piston rign compressor Tool J-22639, 22629
or 22591 as shown in Figure 40. Use care not to
damage the seal lip as piston is pressed past the
edge of the bore. .
5.
Assemble the boot in the groove of the piston closest
to the concave end of the piston. The fold in the boot
must face toward the end of the piston with the seal
on it.
6. Depress the pistons and check that they slide
smoothly into the bore until the end of the piston is
flush with the end of the bore. If not, re check piston
assembly and location of the piston spring and the
seal.
7.
Position applicable boot seal installer Tool J-22592,
J-22628, or J-22638 over the piston and seat the
steel boot retaining ring evenly in the counterbore
as shown in Figure 41. The boot retaining ring must
be flush or below the machined face of the caliper.
Any distortion or uneven seating could allow con-
taminating and corrosive elements to enter the bore.
8. Position the t:O}> rings in the small cavities around
the brake fluid transfer holes in both ends of the
outboard caliper halves. Lubricate the hex head
. bolts with Delco Brake Lube or clip in clean brake
fluid. Fit caliper halves together and secure with
bolts.
Refer to torque specifications in rear of
manual for correct torque valves.
Installation
1.
Carefully mount the assembled caliper over the edge
of the disc. Use a putty knife to depress pistons so
that the caliper can be lowered into position on the
disc (fig. 42). Use care to prevent damage to boots
• on the edge of the disc as the caliper is mounted.
2.
Secure the caliper to the mounting bracket with two
hex head bolts. Refer to torque specifications in
rear of manual for correct torque values.
CAUTION: If replacing old shoe assemblies,
be sure to get the shoes in the same position
from which they were removed. New shoe as-
semblies have an arrow printed on the back,
showing the direction of forward disc rotation.
3.
Install the shoe and lining assemblies as outlined in
this section.
4.
On Chevrolet and Corvette front calipers, place a
new copper gasket on the male end of the front
wheel brake hose. On all models, install brake hose
in the calipers. With the wheels straight ahead,
pass the female end of the brake hose through the
support bracket.
5.
Make sure the tube seat is clean and connect the
break line tube nut to the caliper. Tighten securely.
6. Allowing the hose to seek a normal position, without
twist, insert hex of the hose fitting into the 12-point
hole in the support bracket and secure it in place
with the "V"-shaped retainer. Turn the steering
geometry from lock to lock while observing the hose.
CHEVROLET CHASSIS SERVICE MANUAL
Page 262 of 659
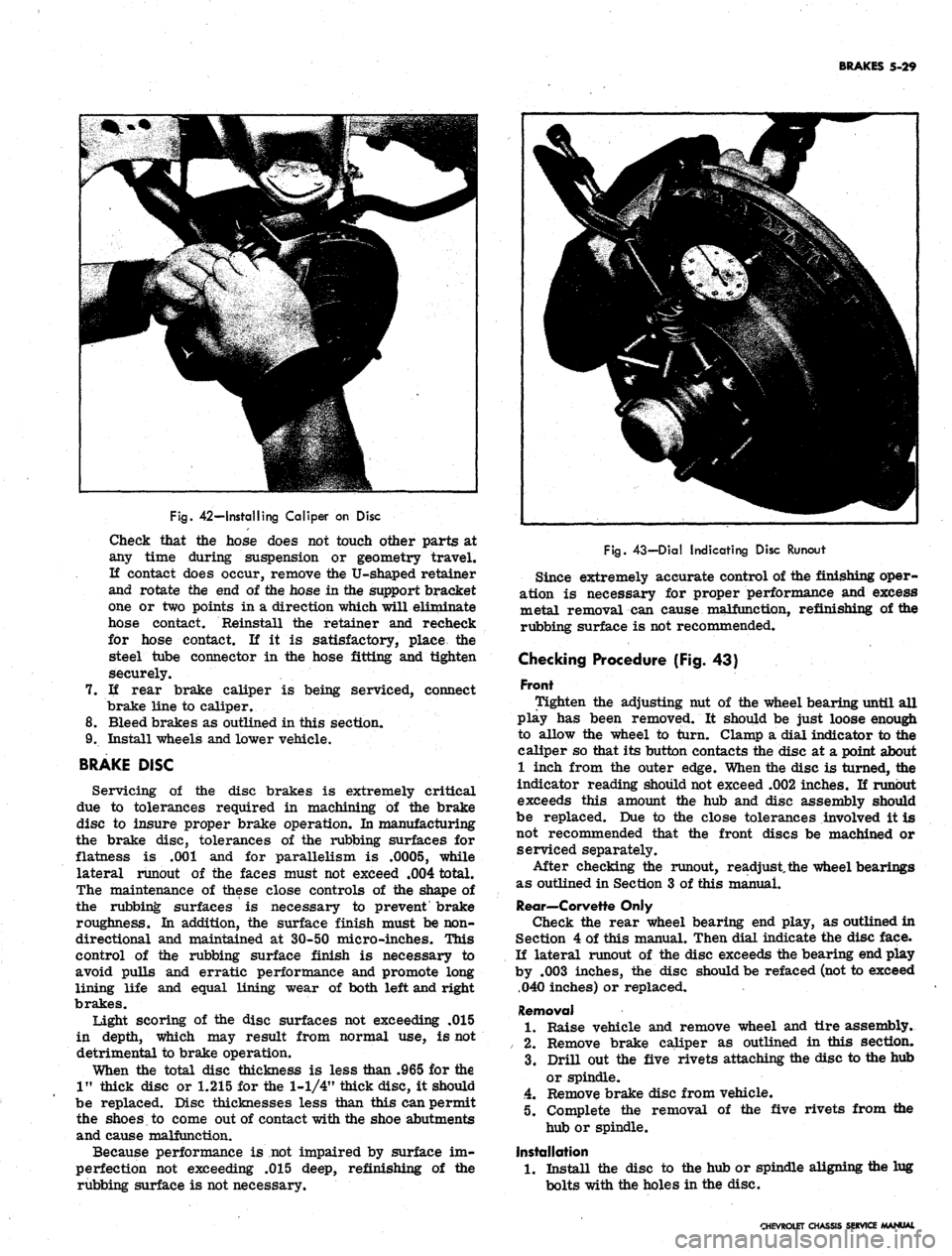
BRAKES 5-29
Fig.
42—Installing Caliper on Disc
Check that the hose does not touch other parts at
any time during suspension or geometry travel.
If contact does occur, remove the U-shaped retainer
and rotate the end of the hose in the support bracket
one or two points in a direction which will eliminate
hose contact. Reinstall the retainer and recheck
for hose contact. If it is satisfactory, place the
steel tube connector in the hose fitting and tighten
securely.
If rear brake caliper is being serviced, connect
brake line to caliper.
Bleed brakes as outlined in this section.
Install wheels and lower vehicle.
BRAKE DISC
Servicing of the disc brakes is extremely critical
due to tolerances required in machining of the brake
disc to insure proper brake operation. In manufacturing
the brake disc, tolerances of the rubbing surfaces for
flatness is .001 and for parallelism is .0005, while
lateral runout of the faces must not exceed .004 total.
The maintenance of these close controls of the shape of
the rubbing surfaces is necessary to prevent brake
roughness. In addition, the surface finish must be non-
directional and maintained at 30-50 micro-inches. This
control of the rubbing surface finish is necessary to
avoid pulls and erratic performance and promote long
lining life and equal lining wear of both left and right
brakes.
tight scoring of the disc surfaces not exceeding .015
in depth, which may result from normal use, is not
detrimental to brake operation.
When the total disc thickness is less than .965 for the
1"
thick disc or 1.215 for the 1-1/4" thick disc, it should
be replaced. Disc thicknesses less than this can permit
the shoes to come out of contact with the shoe abutments
and cause malfunction.
Because performance is not impaired by surface im-
perfection not exceeding .015 deep, refinishing of the
rubbing surface is not necessary.
Fig.
43—Dial Indicating Disc Runout
Since extremely accurate control of the finishing oper-
ation is necessary for proper performance and excess
metal removal can cause malfunction, refinishing of the
rubbing surface is not recommended.
Checking Procedure (Fig. 43)
Front
Tighten the adjusting nut of the wheel bearing until all
play has been removed. It should be just loose enough
to allow the wheel to turn. Clamp a dial indicator to the
caliper so that its button contacts the disc at a point about
1 inch from the outer edge. When the disc is turned, the
indicator reading should not exceed .002 inches. If runout
exceeds this amount the hub and disc assembly should
be replaced. Due to the close tolerances involved it is
not recommended that the front discs be machined or
serviced separately.
After checking the runout, readjust, the wheel bearings
as outlined in Section 3 of this manual.
Rear—Corvette Only
Check the rear wheel bearing end play, as outlined in
Section 4 of this manual. Then dial indicate the disc face.
If lateral runout of the disc exceeds the bearing end play
by .003 inches, the disc should be refaced (not to exceed
.040 inches) or replaced.
Removal
1.
Raise vehicle and remove wheel and tire assembly.
/ 2. Remove brake caliper as outlined in this section.
3.
Drill out the five rivets attaching the disc to the hub
or spindle.
4.
Remove brake disc from vehicle.
5. Complete the removal of the five rivets from the
hub or spindle.
Installation
1.
Install the disc to the hub or spindle aligning the lug
bolts with the holes in the disc.
CHEVROLET CHASSIS SERVICE MANUAL
Page 263 of 659
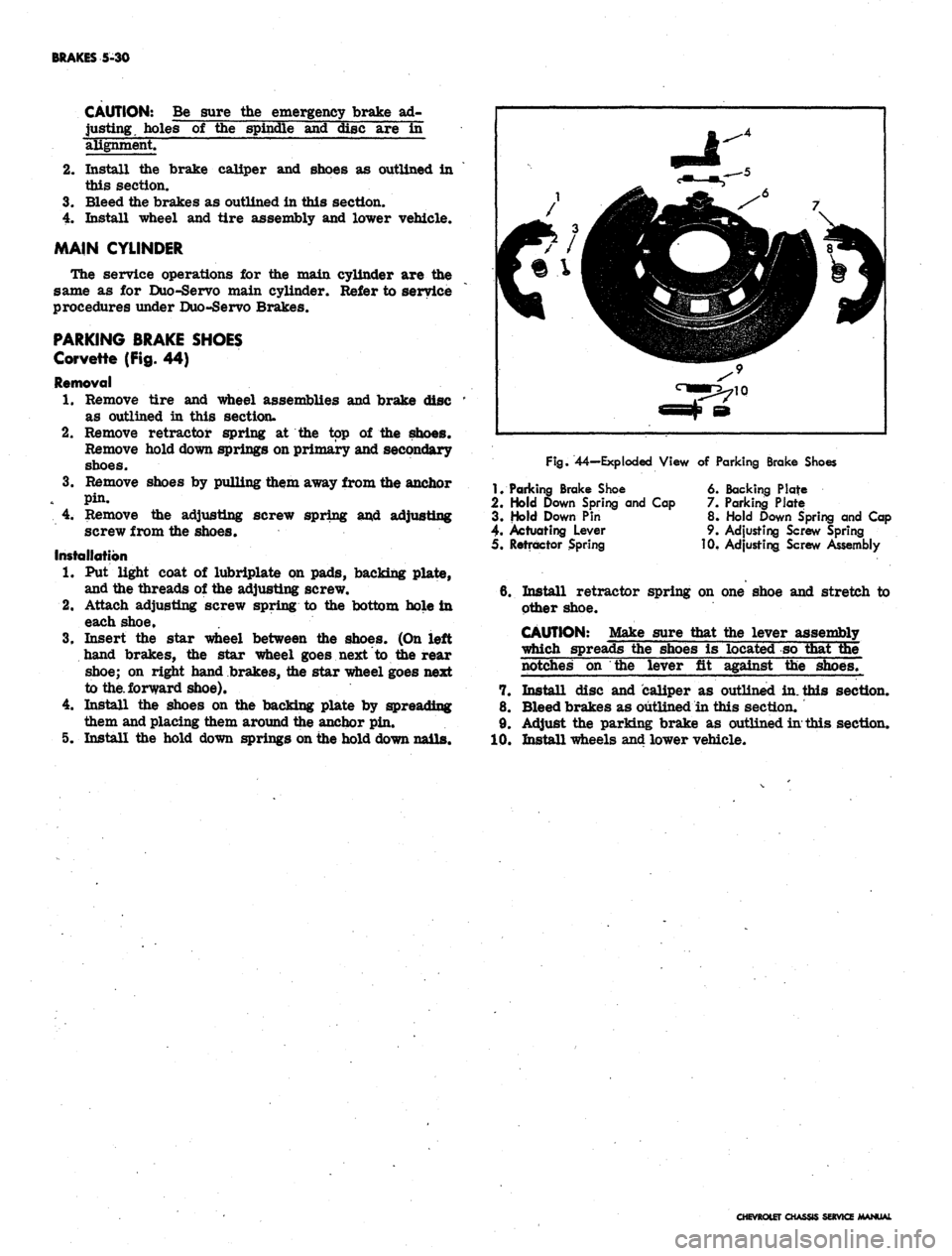
BRAKES 5-30
CAUTION: Be sure the emergency brake ad-
justing, holes of the spindle and disc are in
alignment.
2.
Install the brake caliper and shoes as outlined in
this section.
3.
Bleed the brakes as outlined in this section.
4.
Install wheel and tire assembly and lower vehicle.
MAIN CYLINDER
The service operations for the main cylinder are the
same as for Duo-Servo main cylinder. Refer to service
procedures under Duo-Servo Brakes.
PARKING BRAKE SHOES
Corvette (Fig. 44)
Removal
1.
Remove tire and wheel assemblies and brake disc
as outlined in this section.
2.
Remove retractor spring at the top of the shoes.
Remove hold down springs on primary and secondary
shoes.
3.
Remove shoes by pulling them away from the anchor
pin.
4.
Remove the adjusting screw spring and adjusting
screw from the shoes.
Installation
1.
Put light coat of lubriplate on pads, backing plate,
and the threads of the adjusting screw.
2.
Attach adjusting screw spring to the bottom hole in
each shoe.
3.
Insert the star wheel between the shoes. (On left
hand brakes, the star wheel goes next to the rear
shoe; on right hand brakes, the star wheel goes next
to
the.
forward shoe).
4.
Install the shoes on the backing plate by spreading
them and placing them around the anchor pin.
5. Install the hold down springs on the hold down nails.
Fig.
44-Exploded View of Parking Brake Shoes
1.
Parking Brake Shoe
2.
Hold Down Spring and Cap
3. Hold Down Pin
4. Actuating Lever
5. Retractor Spring
6. Backing Plate
7. Parking Plate
8. Hold Down Spring and Cap
9. Adjusting Screw Spring
0, Adjusting Screw Assembly
6. Install retractor spring on one shoe and stretch to
other shoe.
CAUTION: Make sure that the lever assembly
which spreads the shoes is located so that the
notches on the lever fit against the shoes.
7. Install disc and caliper as outlined in. this section.
8. Bleed brakes as outlined in this section.
9. Adjust the parking brake as outlined in this section.
10.
Install wheels and lower vehicle.
CHEVROLET CHASSIS SERVICE MANUAL
Page 264 of 659
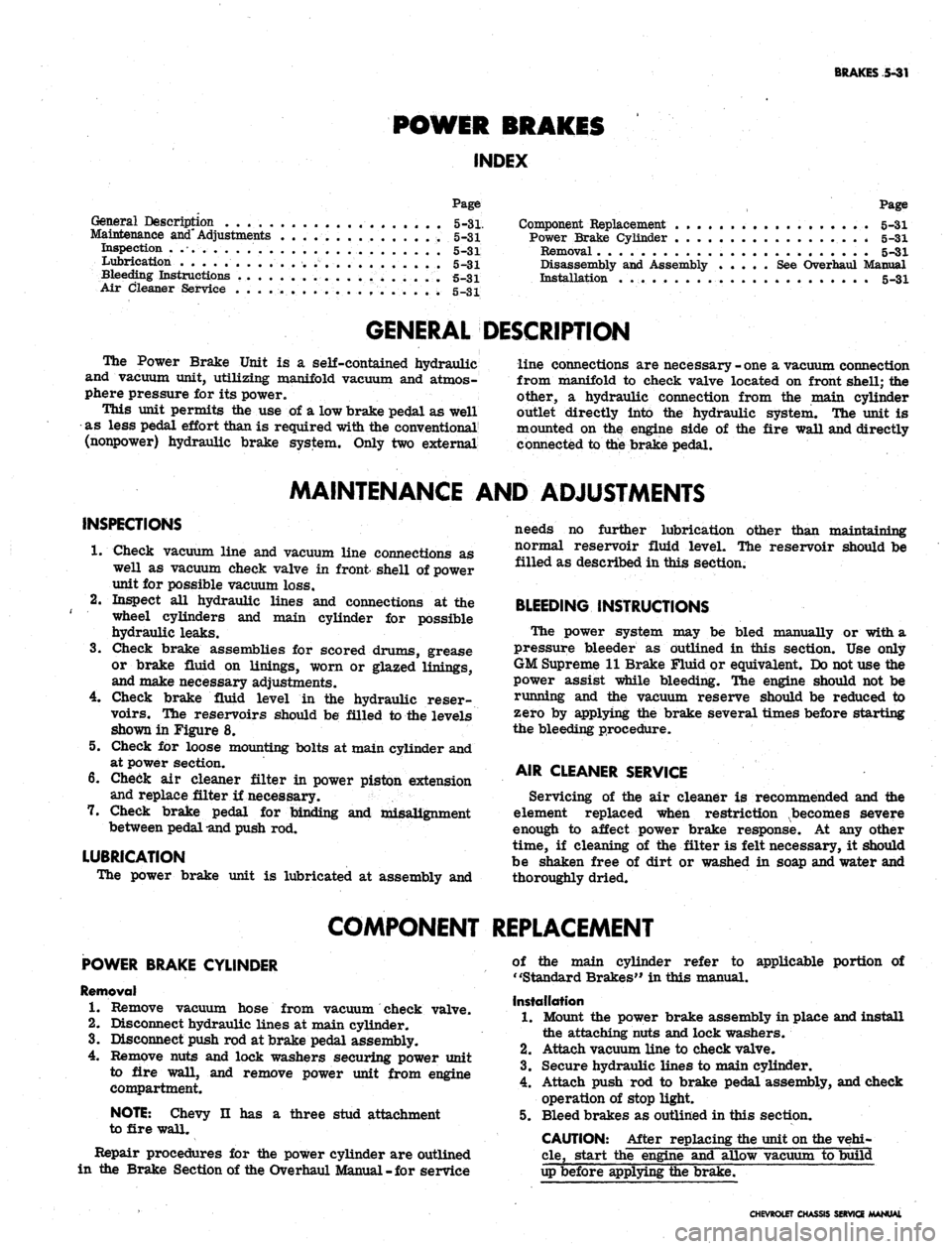
BRAKES
5-31
POWER BRAKES
INDEX
General Description 5-31
Maintenance
and"
Adjustments 5-31
Inspection . ... 5_31
Lubrication 5-31
Bleeding Instructions . . . 5.31
Air Cleaner Service . . . , 5.31
Page
Component Replacement 5-31
Power Brake Cylinder ......* 5-31
Removal . . 5-31
Disassembly and Assembly See Overhaul Manual
Installation . . . . 5-31
GENERAL DESCRIPTION
The Power Brake Unit is a self-contained hydraulic
and vacuum unit, utilizing manifold vacuum and atmos-
phere pressure for its power.
This unit permits the use of a low brake pedal as well
as less pedal effort than is required with the conventional
(nonpower) hydraulic brake system. Only two external
line connections are necessary -
one
a vacuum connection
from manifold to check valve located on front shell; the
other, a hydraulic connection from the main cylinder
outlet directly into the hydraulic system. The unit is
mounted on the engine side of the fire wall and directly
connected to the brake pedal.
MAINTENANCE AND ADJUSTMENTS
INSPECTIONS
1.
Check vacuum line and vacuum line connections as
well as vacuum check valve in front shell of power
unit for possible vacuum loss.
2.
Inspect all hydraulic lines and connections at the
wheel cylinders and main cylinder for possible
hydraulic leaks.
3.
Check brake assemblies for scored drums, grease
or brake fluid on linings, worn or glazed linings,
and make necessary adjustments.
4.
Check brake fluid level in the hydraulic reser-
voirs.
The reservoirs should be filled to the levels
shown in Figure 8.
5. Check for loose mounting bolts at main cylinder and
at power section.
6. Check air cleaner filter in power piston extension
and replace filter if necessary.
7. Check brake pedal for binding and misalignment
between pedal
-and
push rod.
LUBRICATION
The power brake unit is lubricated at assembly and
needs no further lubrication other than maintaining
normal reservoir fluid level. The reservoir should be
filled as described in this section.
BLEEDING INSTRUCTIONS
The power system may be bled manually or with a
pressure bleeder as outlined in this section. Use only
GM
Supreme 11 Brake Fluid or equivalent. Do not use the
power assist while bleeding. The engine should not be
running and the vacuum reserve should be reduced to
zero by applying the brake several times before starting
the bleeding procedure.
AIR CLEANER SERVICE
Servicing of the air cleaner is recommended and the
element replaced when restriction becomes severe
enough to affect power brake response. At any other
time, if cleaning of the filter is felt necessary, it should
be shaken free of dirt or washed in soap and water and
thoroughly dried.
COMPONENT REPLACEMENT
POWER BRAKE CYLINDER
Removal
1.
Remove vacuum hose from vacuum check valve.
2.
Disconnect hydraulic lines at main cylinder.
Disconnect push rod at brake pedal assembly.
Remove nuts and lock washers securing power unit
to fire wall, and remove power unit from engine
compartment.
3.
4.
NOTE:
Chevy
to fire wall.
has a three stud attachment
Repair procedures for the power cylinder are outlined
in the Brake Section of the Overhaul Manual-for service
of the main cylinder refer to applicable portion of
"Standard Brakes" in this manual.
Installation
1.
Mount the power brake assembly in place and install
the attaching nuts and lock washers.
2.
Attach vacuum line to check valve.
3.
Secure hydraulic lines to main cylinder.
4.
Attach push rod to brake pedal assembly, and check
operation of stop light.
5. Bleed brakes as outlined in this section.
CAUTION: After replacing the unit on the vehi-
cle,
start the engine and allow vacuum to build
up before applying the brake.
CHEVROLET CHASSIS SERVICE
Page 265 of 659
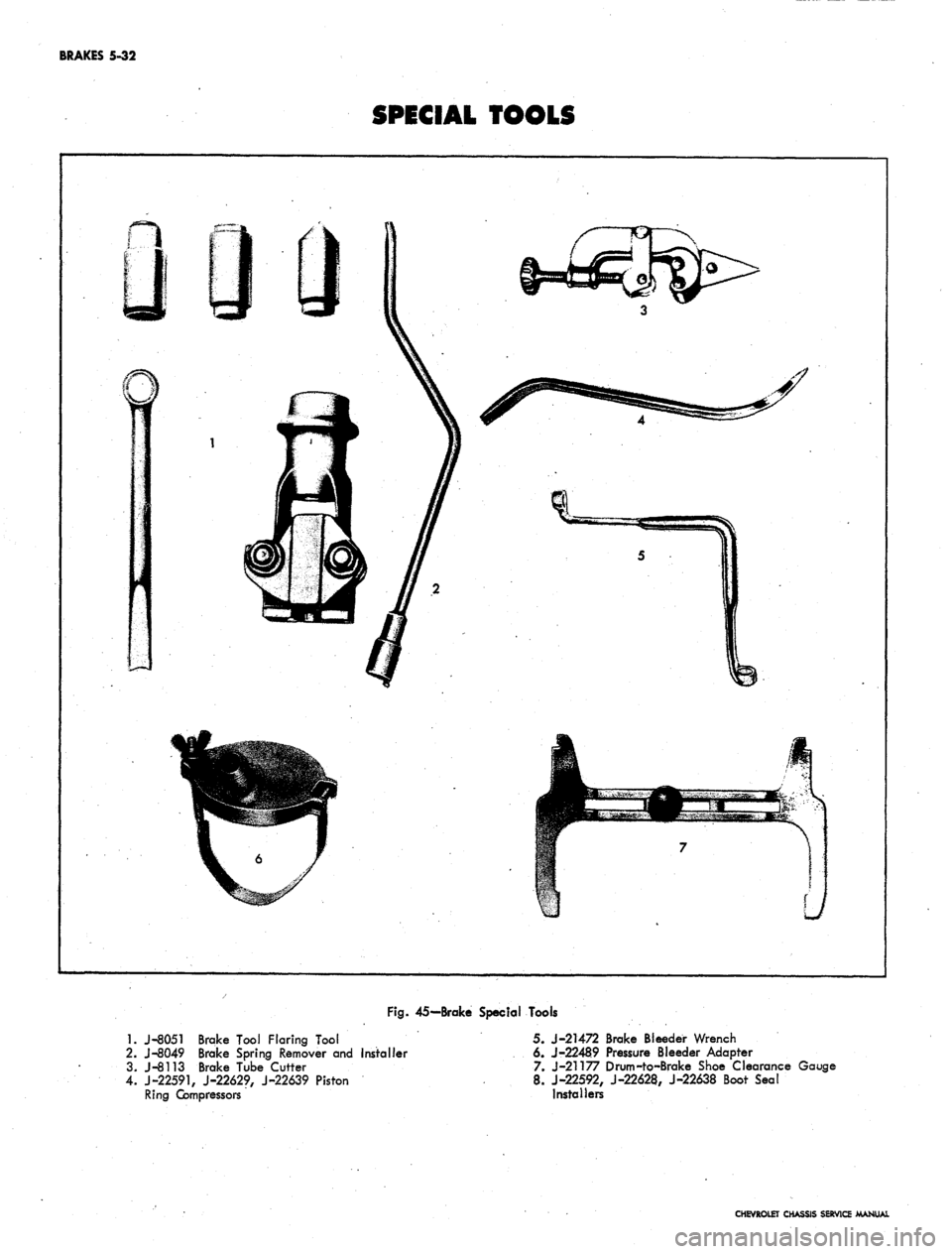
BRAKES 5-32
SPECIAL TOOLS
Fig.
45-Brake Special Tools
1.
J-8051 Brake Tool Flaring Tool
2.
J-8049 Brake Spring Remover and Installer
3. J-8113 Brake Tube Cutter
4.
J-22591,
J-22629, J-22639 Piston
Ring Compressors
5. J-21472 Brake Bleeder Wrench
6. J-22489 Pressure Bleeder Adapter
7. J-21177 Drum-ro-Brake Shoe Clearance
8. J-22592, J-22628, J-22638 Boot Seal
Installers
Gauge
CHEVROLET CHASSIS SERVICE MANUAL
Page 266 of 659
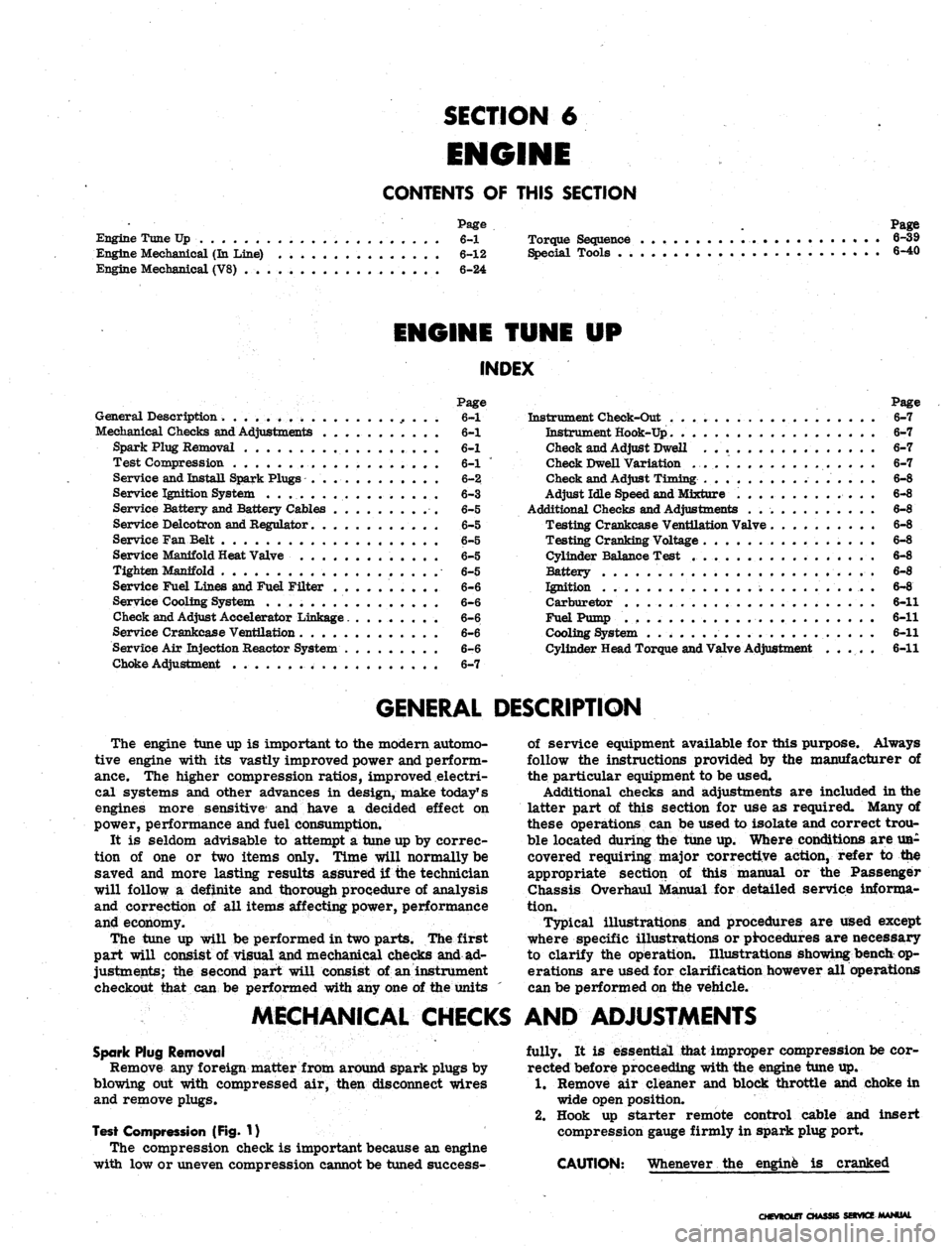
SECTION 6
ENGINE
CONTENTS
OF
THIS SECTION
Page
Engine Tune Up
6-1
Torque Sequence
Engine Mechanical
(In
Line)
6-12
Special Tools
. .
Engine Mechanical (V8)
6-24
Page
6-39
6-40
ENGINE TUNE UP
INDEX
Page
General Description
. 6-1
Mechanical Checks and Adjustments
6-1
Spark Plug Removal
6-1
Test Compression
6-1
Service and Install Spark Plugs
6-2
Service Ignition System
6-3
Service Battery
and
Battery Cables
6-5
Service Delcotron
and
Regulator
6-5
Service
Fan
Belt
6-5
Service Manifold Heat Valve
6-5
Tighten Manifold
6-5
Service Fuel Lines
and
Fuel Filter ..........
6-6
Service Cooling System
6-6
Check and Adjust Accelerator Linkage
6-6
Service Crankcase Ventilation
6-6
Service
Air
Injection Reactor System
6-6
Choke Adjustment
6-7
Page
Instrument Cheek-Out
6-7
Instrument Hook-Up.
. 6*7
Check and Adjust Dwell
6-7
Check Dwell Variation
6-7
Check and Adjust Timing
6-8
Adjust Idle Speed
and
Mixture
6-8
Additional Checks and Adjustments
. 6-8
Testing Crankcase Ventilation Valve
. 6-8
Testing Cranking Voltage
6-8
Cylinder Balance Test
. 6-8
Battery
6-8
Ignition
; 6-8
Carburetor
6-11
Fuel Pump
6-11
Cooling System
. 6-11
Cylinder Head Torque and Valve Adjustment
..... 6-11
GENERAL DESCRIPTION
The engine tune up
is
important
to the
modern automo-
tive engine with
its
vastly improved power and perform-
ance.
The
higher compression ratios, improved electri-
cal systems
and
other advances
in
design, make today1 s
engines more sensitive
and
have
a
decided effect
on
power, performance and fuel consumption.
It
is
seldom advisable
to
attempt
a
tune up
by
correc-
tion
of one or two
items only. Time will normally
be
saved
and
more lasting results assured
if the
technician
will follow
a
definite
and
thorough procedure
of
analysis
and correction
of all
items affecting power, performance
and economy.
The tune
up
will
be
performed
in
two parts.
The
first
part will consist
of
visual and mechanical checks and
ad-
justments;
the
second part will consist
of
an instrument
checkout that
can be
performed with
any one of the
units
of service equipment available
for
this purpose. Always
follow
the
instructions provided
by the
manufacturer
of
the particular equipment
to be
used.
Additional checks
and
adjustments
are
included
in the
latter part
of
this section
for use as
required. Many
of
these operations
can be
used
to
isolate and correct trou-
ble located during
the
tune up. Where conditions
are
UB-
covered requiring major corrective action, refer
to the
appropriate section
of
this manual
or the
Passenger
Chassis Overhaul Manual
for
detailed service informa-
tion.
Typical illustrations
and
procedures
are
used except
where specific illustrations
or
procedures
are
necessary
to clarify
the
operation. Illustrations showing bench
op-
erations
are
used
for
clarification however
all
operations
can
be
performed
on the
vehicle.
MECHANICAL CHECKS
AND
ADJUSTMENTS
Spark Plug Removal
Remove any foreign matter from around spark plugs
by
blowing
out
with compressed
air,
then disconnect wires
and remove plugs.
Test Compression
(Fig. 1)
The compression check
is
important because
an
engine
with
low or
uneven compression cannot
be
tuned success-
fully.
It is
essential that improper compression
be cor-
rected before proceeding with
the
engine tune
up.
1.
Remove
air
cleaner
and
block throttle
and
choke
in
wide open position.
2.
Hook
up
starter remote control cable
and
insert
compression gauge firmly
in
spark plug port.
CAUTION: Whenever
the
engine
is
cranked
CHEVROLET
C*
IS SERVICE MANUAL
Page 267 of 659
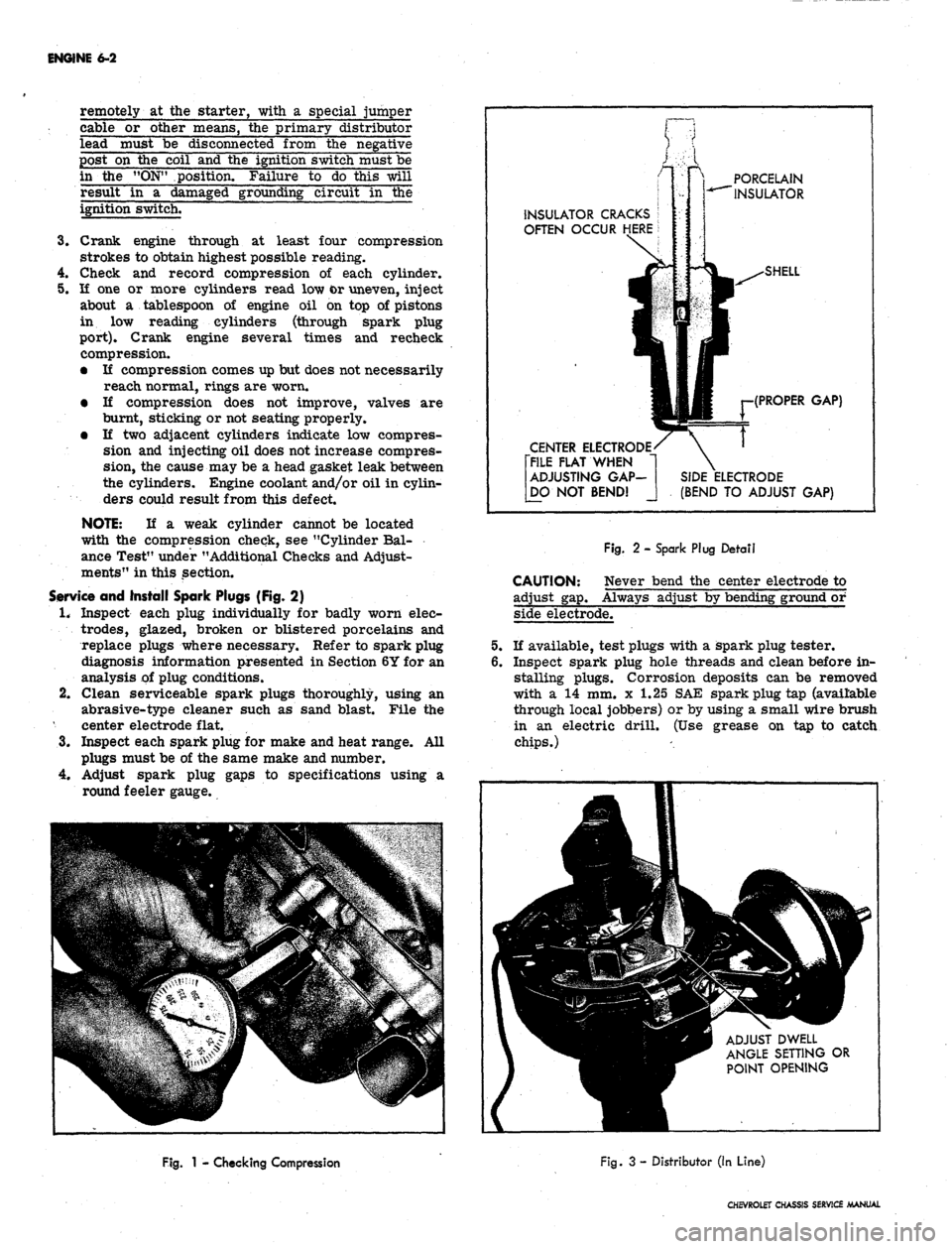
ENGINE 6-2
remotely at the starter, with a special jumper
cable or other means, the primary distributor
lead must be disconnected from the negative
post on the coil and the ignition switch must be
in the "ON" position. Failure to do this will
result in a damaged grounding circuit in the
ignition switch.
3.
Crank engine through at least four compression
strokes to obtain highest possible reading.
4.
Check and record compression of each cylinder.
5.
If one or more cylinders read low tor uneven, inject
about a tablespoon of engine oil on top of pistons
in low reading cylinders (through spark plug
port).
Crank engine several times and recheck
compression.
• If compression comes up but does not necessarily
reach normal, rings are worn.
• If compression does not improve, valves are
burnt, sticking or not seating properly.
• If two adjacent cylinders indicate low compres-
sion and injecting oil does not increase compres-
sion, the cause may be a head gasket leak between
the cylinders. Engine coolant and/or oil in cylin-
ders could result from this defect.
NOTE: If a weak cylinder cannot be located
with the compression check, see "Cylinder Bal-
ance Test" under "Additional Checks and Adjust-
ments" in this section.
Service and Install Spark Plugs (Fig. 2)
1.
Inspect each plug individually for badly worn elec-
trodes,
glazed, broken or blistered porcelains and
replace plugs where necessary. Refer to spark plug
diagnosis information presented in Section 6Y for an
analysis of plug conditions.
2.
Clean serviceable spark plugs thoroughly, using an
abrasive-type cleaner such as sand blast. File the
center electrode flat.
3.
Inspect each spark plug for make and heat range. All
plugs must be of the same make and number.
4.
Adjust spark plug gaps to specifications using a
round feeler gauge.
PORCELAIN
INSULATOR
INSULATOR CRACKS
OFTEN OCCUR HERE
CENTER ELECTRODE
[FILE FLAT WHEN
ADJUSTING GAP-
[DO NOT BEND!
(PROPER GAP)
(BEND TO ADJUST GAP)
CAUTION:
adjust gap.
Fig.
2 - Spark Plug Detail
Never bend the center electrode to
Always adjust by bending ground or
side electrode.
If available, test plugs with a spark plug tester.
Inspect spark plug hole threads and clean before in-
stalling plugs. Corrosion deposits can be removed
with a 14 mm. x 1.25 SAE spark plug tap (available
through local jobbers) or by using a small wire brush
in an electric drill. (Use grease on tap to catch
chips.)
ADJUST DWELL
ANGLE SETTING OR
POINT OPENING
Fig.
1 - Checking Compression
Fig.
3 - Distributor (In Line)
CHEVROLET CHASSIS SERVICE MANUAL
Page 268 of 659
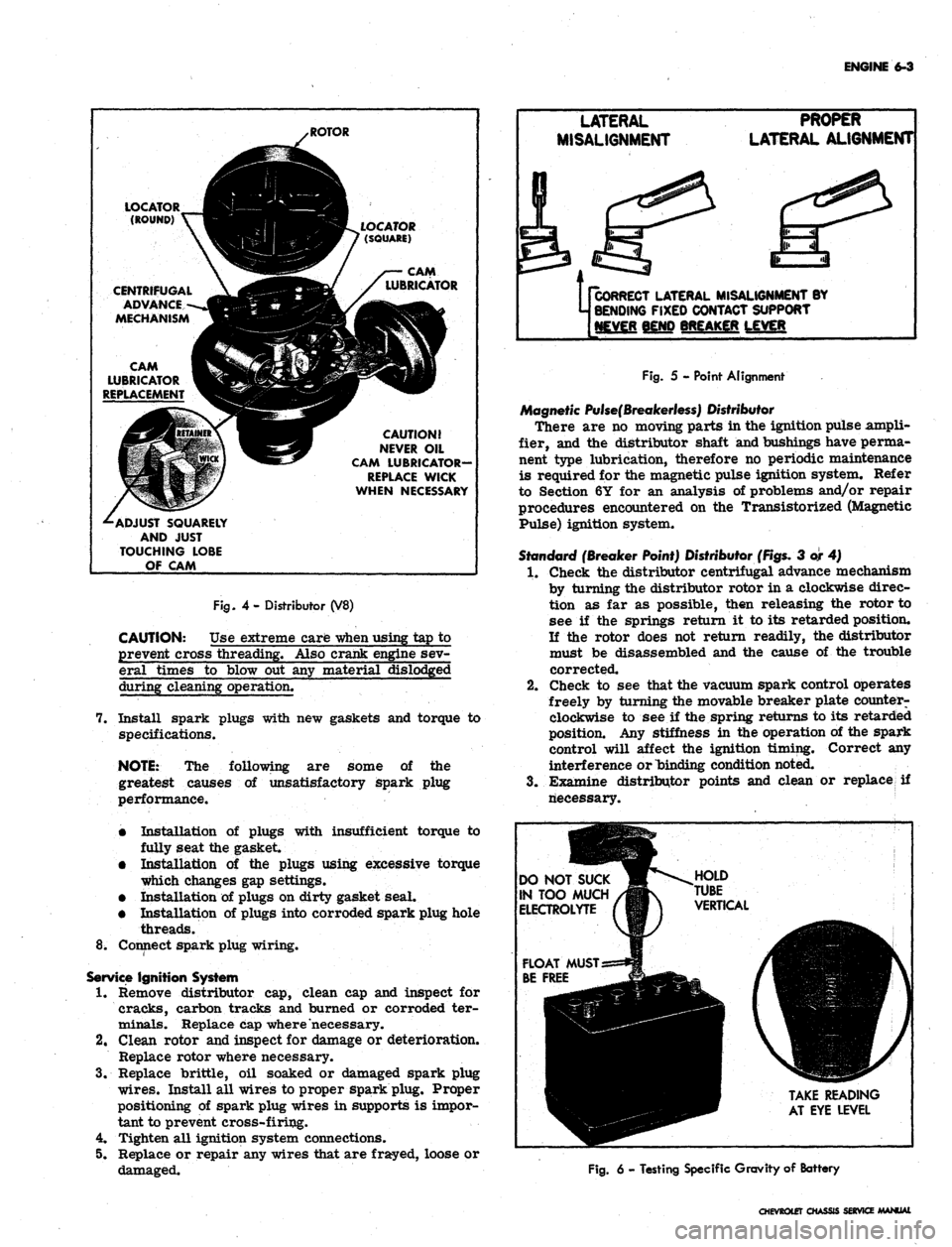
ENGINE
6-3
(ROUND) Y~~fll^H
CENTRIFUGAL
A ^k
ADVANCE--jflgKpl
MECHANISM
UB|
CAM
KSK^2
LUBRICATOR
VlSMi
REPLACEMENT
^BK
-^ADJUST
SQUARELY
AND
JUST
TOUCHING
LOBE
OF
CAM
/ROTOR
HBB
__
I^BH^F
?
(SOUARE)
^K^ I /—
CAM
jKft^J / LUBRICATOR
H^T^
CAUTION!
QV NEVER
OIL
•L-^
CAM LUBRICATOR-
REPLACE
WICK
WHEN
NECESSARY
LATERAL
MISALIGNMENT
PROPER
LATERAL ALIGNMENT
Fig.
4- Distributor (V8)
CAUTION: Use extreme care
-when
using tap to
prevent cross threading. Also crank engine sev-
eral times to blow out any material dislodged
during cleaning operation.
7. Install spark plugs with new gaskets and torque to
specifications.
NOTE:
The following are some of the
greatest causes of unsatisfactory spark plug
performance.
•
Installation of plugs with insufficient torque to
fully seat the gasket.
•
Installation of the plugs using excessive torque
which changes gap settings.
•
Installation of plugs on dirty gasket seal.
•
Installation of plugs into corroded spark plug hole
threads.
8^ Connect spark plug wiring.
Service
Ignition System
1.
Remove distributor cap, clean cap and inspect for
cracks, carbon tracks and burned or corroded ter-
minals. Replace cap where necessary.
2.
Clean rotor and inspect for damage or deterioration.
Replace rotor where necessary.
3.
Replace brittle, oil soaked or damaged spark plug
wires.
Install all wires to proper spark plug. Proper
positioning of spark plug wires in supports is impor-
tant to prevent cross-firing.
4.
Tighten all ignition system connections.
5. Replace or repair any wires that are frayed, loose or
damaged.
Us
CORRECT
LATERAL MISALIGNMENT BY
j BENDING
FIXED CONTACT SUPPORT
[NEVER
BEND BREAKER LEVER
Fig.
5 - Point Alignment
Magnetic
Pulse(Breakerless)
Distributor
There are no moving parts in the ignition pulse ampli-
fier, and the distributor shaft and bushings have perma-
nent type lubrication, therefore no periodic maintenance
is required for the magnetic pulse ignition system. Refer
to Section 6Y for an analysis of problems and/or repair
procedures encountered on the Transistorized (Magnetic
Pulse) ignition system.
Standard
(Breaker Point) Distributor
(Figs.
3 or 4)
1.
Check the distributor centrifugal advance mechanism
by turning the distributor rotor in a clockwise direc-
tion as far as possible, then releasing the rotor to
see if the springs return it to its retarded position.
If the rotor does not return readily, the distributor
must be disassembled and the cause of the trouble
corrected.
2.
Check to see that the vacuum spark control operates
freely by turning the movable breaker plate counter-
clockwise to see if the spring returns to its retarded
position. Any stiffness in the operation of the spark
control will affect the ignition timing. Correct any
interference or binding condition noted.
3.
Examine distributor points and clean or replace if
riecessary.
DO
NOT SUCK
IN
TOO MUCH
ELECTROLYTE
TAKE
READING
AT
EYE LEVEL
Fig.
6 - Testing Specific Gravity of Battery
CHEVROtET
CHASSIS SERVICE MANUAL
Page 269 of 659
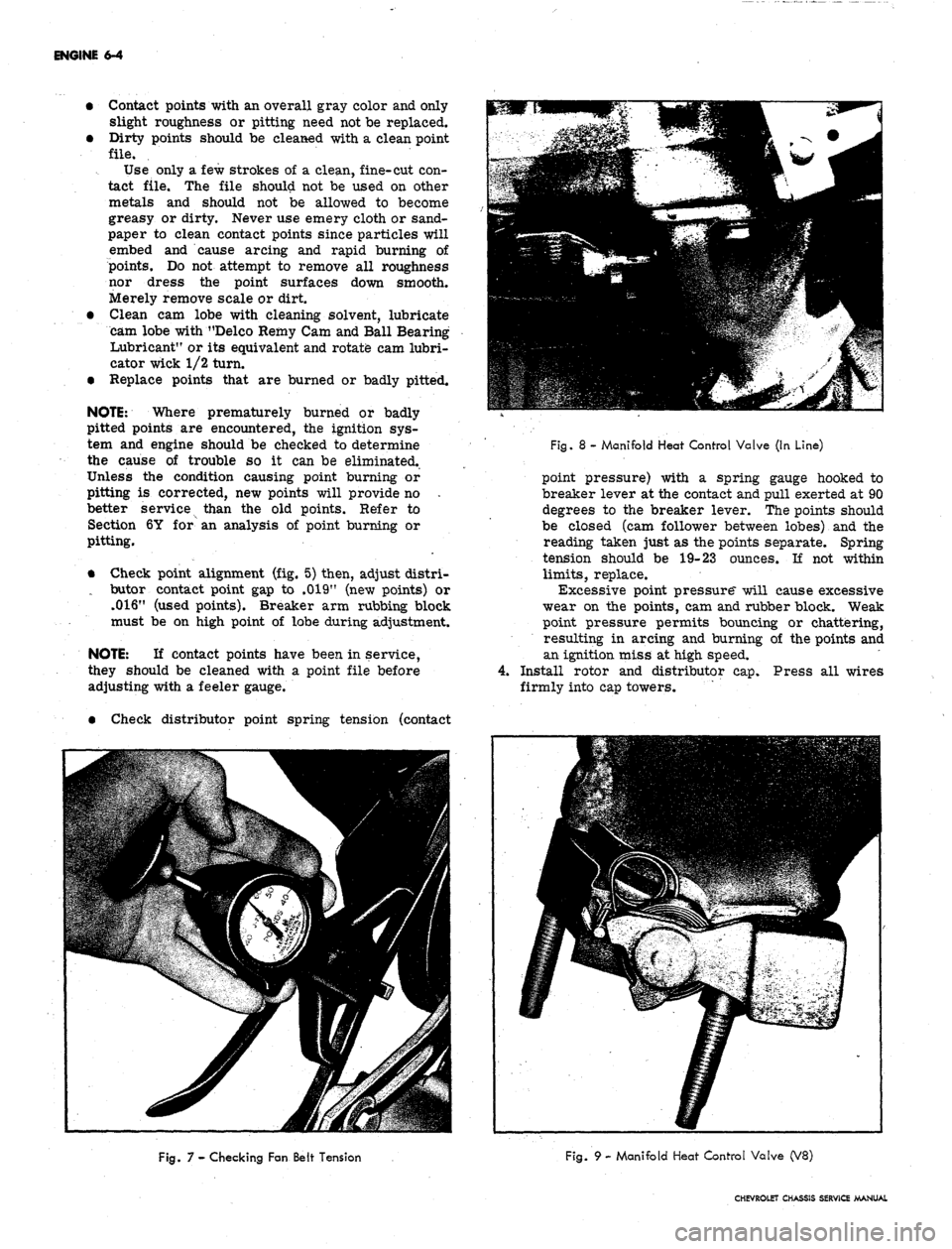
ENGINE 6-4
• Contact points with an overall gray color and only
slight roughness or pitting need not be replaced.
• Dirty points should be cleaned with a clean point
file.
Use only a few strokes of a clean, fine-cut con-
tact file. The file should not be used on other
metals and should not be allowed to become
greasy or dirty. Never use emery cloth or sand-
paper to clean contact points since particles will
embed and cause arcing and rapid burning of
points. Do not attempt to remove all roughness
nor dress the point surfaces down smooth.
Merely remove scale or dirt.
• Clean cam lobe with cleaning solvent, lubricate
cam lobe with "Delco Remy Cam and Ball Bearing
Lubricant" or its equivalent and rotate cam lubri-
cator wick 1/2 turn.
• Replace points that are burned or badly pitted.
NOTE: Where prematurely burned or badly
pitted points are encountered, the ignition sys-
tem and engine should be checked to determine
the cause of trouble so it can be eliminated.
Unless the condition causing point burning or
pitting is corrected, new points will provide no .
better service than the old points. Refer to
Section 6Y for an analysis of point burning or
pitting.
• Check point alignment (fig. 5) then, adjust distri-
. butor contact point gap to .019" (new points) or
.016"
(used points). Breaker arm rubbing block
must be on high point of lobe during adjustment.
NOTE: If contact points have been in service,
they should be cleaned with a point file before
adjusting with a feeler gauge.
• Check distributor point spring tension (contact
Fig. 8 - Manifold Heat Control Valve (In Line)
point pressure) with a spring gauge hooked to
breaker lever at the contact and pull exerted at 90
degrees to the breaker lever. The points should
be closed (cam follower between lobes) and the
reading taken just as the points separate. Spring
tension should be 19-23 ounces. If not within
limits,
replace.
Excessive point pressure" will cause excessive
wear on the points, cam and rubber block. Weak
point pressure permits bouncing or chattering,
resulting in arcing and burning of the points and
an ignition miss at high speed.
4.
Install rotor and distributor cap. Press all wires
firmly into cap towers.
Fig. 7 - Checking Fan Belt Tension
Fig. 9 - Manifold Heat Control Valve (V8)
CHEVROLET CHASSIS SERVICE MANUAL
Page 270 of 659
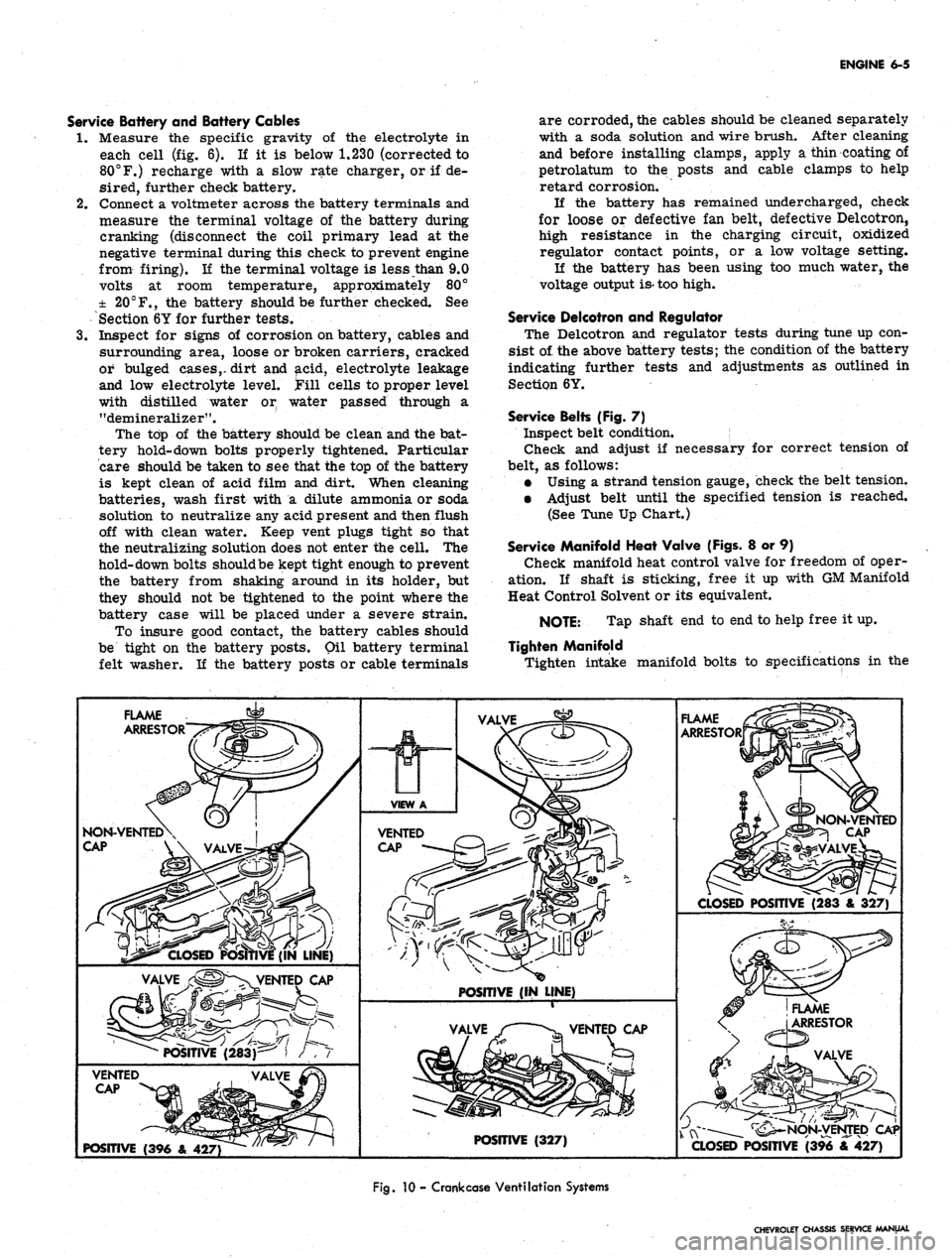
ENGINE
6-5
Service Battery and Battery Cables
1.
Measure the specific gravity of the electrolyte in
each cell (fig. 6). If it is below 1.230 (corrected to
80°F.) recharge with a slow rate charger, or if de-
sired, further check battery.
2.
Connect a voltmeter across the battery terminals and
measure the terminal voltage of the battery during
cranking (disconnect the coil primary lead at the
negative terminal during this check to prevent engine
from firing). If the terminal voltage is less than 9.0
volts at room temperature, approximately 80°
±
20°
F.,
the battery should be further checked. See
Section 6Y for further tests.
3.
Inspect for signs of corrosion on battery, cables and
surrounding area, loose or broken carriers, cracked
or bulged cases,- dirt and acid, electrolyte leakage
and low electrolyte level. !Fill cells to proper level
with distilled water or water passed through a
"demineralizer".
The top of the battery should be clean and the bat-
tery hold-down bolts properly tightened. Particular
care should be taken to see that the top of the battery
is kept clean of acid film and dirt. When cleaning
batteries, wash first with a dilute ammonia or soda
solution to neutralize any acid present and then flush
off with clean water. Keep vent plugs tight so that
the neutralizing solution does not enter the cell. The
hold-down bolts should be kept tight enough to prevent
the battery from shaking around in its holder, but
they should not be tightened to the point where the
battery case will be placed under a severe strain.
To insure good contact, the battery cables should
be tight on the battery posts. Oil battery terminal
felt washer. If the battery posts or cable terminals
are corroded, the cables should be cleaned separately
with a soda solution and wire brush. After cleaning
and before installing clamps, apply a thin coating of
petrolatum to the posts and cable clamps to help
retard corrosion.
If the battery has remained undercharged, check
for loose or defective fan belt, defective Delcotron,
high resistance in the charging circuit, oxidized
regulator contact points, or a low voltage setting.
If the battery has been using too much water, the
voltage output
is-
too high.
Service Deicotron and Regulator
The Delcotron and regulator tests during tune up con-
sist of the above battery tests; the condition of the battery
indicating further tests and adjustments as outlined in
Section 6Y.
Service Belts (Fig. 7)
Inspect belt condition.
Check and adjust if necessary for correct tension of
belt, as follows:
• Using a strand tension gauge, check the belt tension.
• Adjust belt until the specified tension is reached.
(See Tune Up Chart.)
Service Manifold Heat Valve (Figs. 8 or 9)
Check manifold heat control valve for freedom of oper-
ation. If shaft is sticking, free it up with GM Manifold
Heat Control Solvent or its equivalent.
NOTE: Tap shaft end to end to help free it up.
Tighten Manifold
Tighten intake manifold bolts to specifications in the
FLAME
ARRESTOR
FLAME
ARRESTOR
NON-VENTED\
CAP
V\ VALVE
CLOSED
POSITIVE (283 & 327)
POSITIVE
(IN LINE)
POSITIVE
(327)
POSITIVE
(396 & 427)
Fig.
10 -
Crank case
Ventilation Systems
CHEVROLET CHASSIS SERVICE MANUAL