CHEVROLET CAMARO 1967 1.G Chassis Workshop Manual
Manufacturer: CHEVROLET, Model Year: 1967, Model line: CAMARO, Model: CHEVROLET CAMARO 1967 1.GPages: 659, PDF Size: 114.24 MB
Page 271 of 659
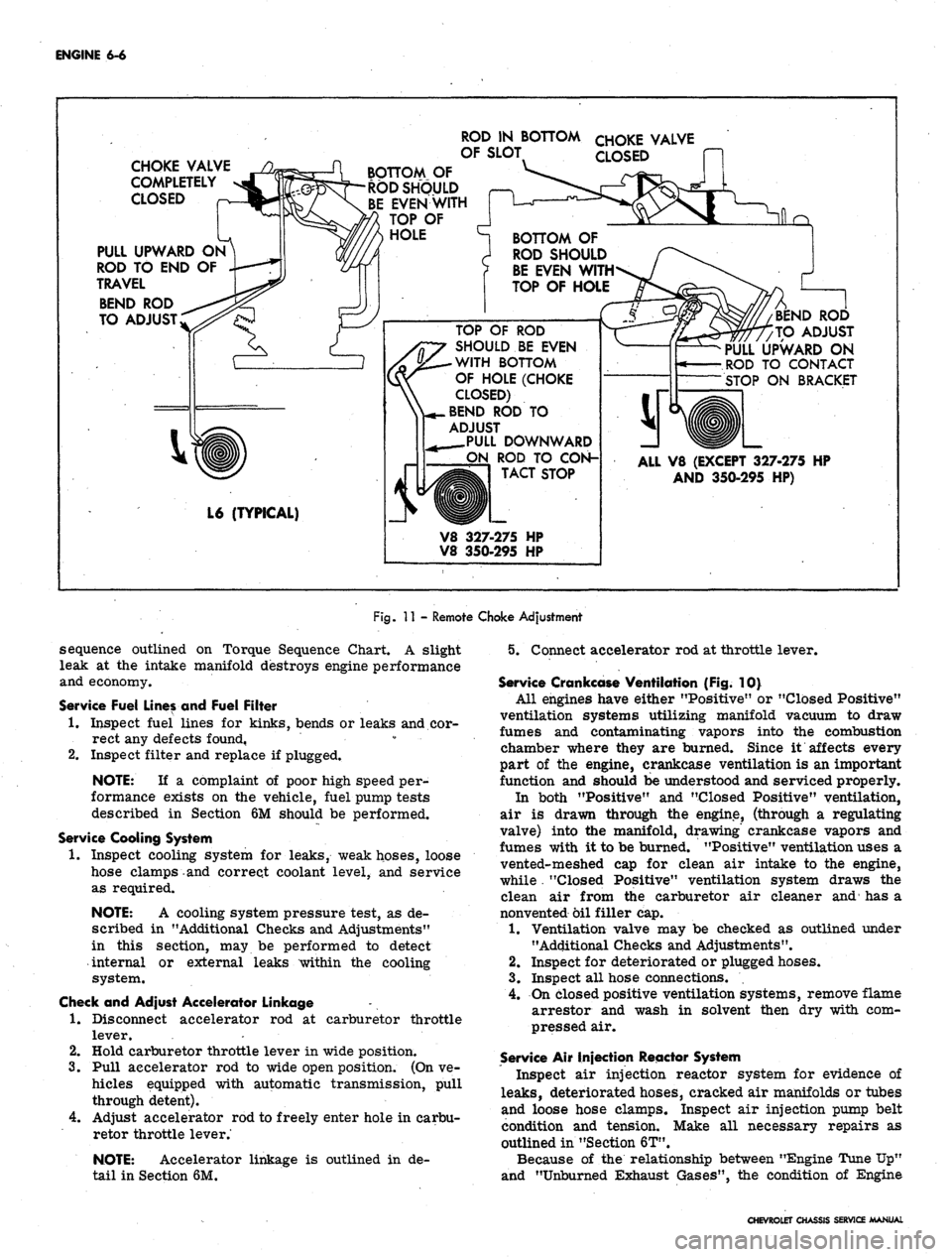
ENGINE 6-6
CHOKE VALVE
COMPLETELY
CLOSED
PULL UPWARD ON
ROD TO END OF
TRAVEL
BEND ROD
TO ADJUST
ROD IN BOTTOM
OF SLOT
BOTTOM OF
ROD SHOULD
EVENWITH
TOP OF
HOLE
CHOKE VALVE
CLOSED
BOTTOM OF
ROD SHOULD
BE EVEN WITH
TOP OF HOLE
TOP OF ROD
SHOULD BE EVEN
WITH BOTTOM
OF HOLE (CHOKE
CLOSED)
^..BEND ROD TO
ADJUST
_PULL DOWNWARD
ON ROD TO CON-
TACT STOP
L6 (TYPICAL)
V8 327-275 HP
V8 350-295 HP
BEND ROI
TO ADJUST
PULL UPWARD ON
ROD TO CONTACT
STOP ON BRACKET
ALL V8 (EXCEPT 327-275 HP
AND 350-295 HP)
Fig.
11 - Remote Choke Adjustment
sequence outlined on Torque Sequence Chart. A slight
leak at the intake manifold destroys engine performance
and economy.
Service Fuel Lines and Fuel Filter
1.
Inspect fuel lines for kinks, bends or leaks and cor-
rect any defects found, • • •
2.
Inspect filter and replace if plugged.
NOTE:
If a complaint of poor high speed per-
formance exists on the vehicle, fuel pump tests
described in Section 6M should be performed.
Service Cooling System
1.
Inspect cooling system for leaks, weak hoses, loose
hose clamps and correct coolant level, and service
as required.
NOTE:
A cooling system pressure test, as de-
scribed in "Additional Checks and Adjustments"
in this section, may be performed to detect
internal or external leaks within the cooling
system.
Check and Adjust Accelerator Linkage
1.
Disconnect accelerator rod at carburetor throttle
lever.
2.
Hold carburetor throttle lever in wide position.
3.
Pull accelerator rod to wide open position. (On ve-
hicles equipped with automatic transmission, pull
through detent).
4.
Adjust accelerator rod to freely enter hole in carbu-
retor throttle lever.'
NOTE:
Accelerator linkage is outlined in de-
tail in Section 6M.
5. Connect accelerator rod at throttle lever.
Service Crankcase Ventilation (Fig. 10}
All engines have either "Positive" or "Closed Positive"
ventilation systems utilizing manifold vacuum to draw
fumes and contaminating vapors into the combustion
chamber where they are burned. Since it affects every
part of the engine, crankcase ventilation is an important
function and should be understood and serviced properly.
In both "Positive" and "Closed Positive" ventilation,
air is drawn through the engine, (through a regulating
valve) into the manifold, drawing' crankcase vapors and
fumes with it to be burned. "Positive" ventilation uses a
vented-meshed cap for clean air intake to the engine,
while . "Closed Positive" ventilation system draws the
clean air from the carburetor air cleaner and has a
nonvented oil filler cap.
1.
Ventilation valve may be checked as outlined under
"Additional Checks and Adjustments".
2.
Inspect for deteriorated or plugged hoses.
3.
Inspect all hose connections.
4.
On closed positive ventilation systems, remove flame
arrestor and wash in solvent then dry with com-
pressed air.
Service Air Injection Reactor System
Inspect air injection reactor system for evidence of
leaks,
deteriorated hoses, cracked air manifolds or tubes
and loose hose clamps. Inspect air injection pump belt
condition and tension. Make all necessary repairs as
outlined in "Section 6T".
Because of the relationship between "Engine Tune Up"
and "Unburned Exhaust Gases", the condition of Engine
CHEVROLET CHASSIS SERVICE MANUAL
Page 272 of 659
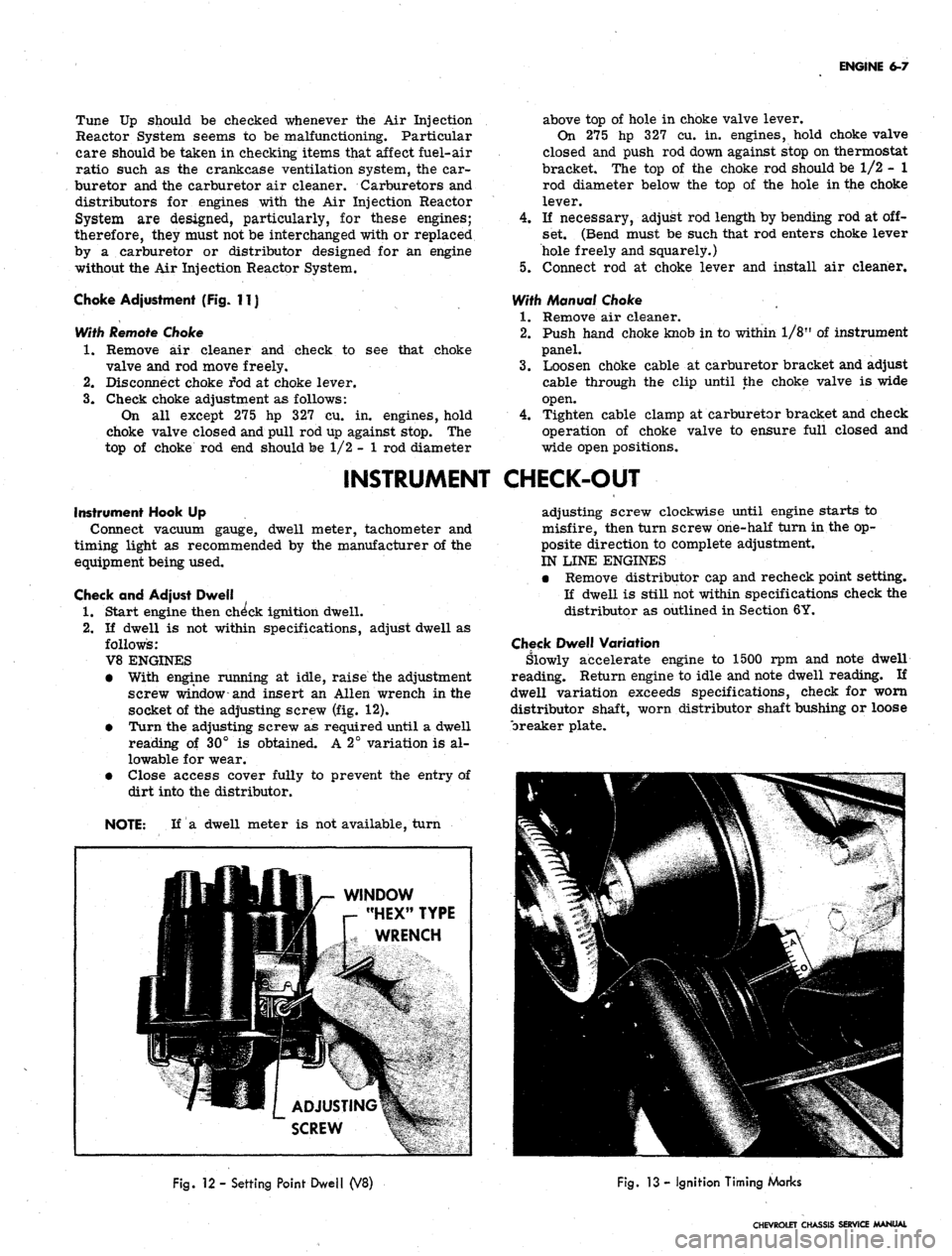
ENGINE 6-7
Tune Up should be checked whenever the Air Injection
Reactor System seems to be malfunctioning. Particular
care should be taken in checking items that affect fuel-air
ratio such as the crankcase ventilation system, the car-
buretor and the carburetor air cleaner. Carburetors and
distributors for engines with the Air Injection Reactor
System are designed, particularly, for these engines;
therefore, they must not be interchanged with or replaced
by a carburetor or distributor designed for an engine
without the Air Injection Reactor System.
Choke Adjustment (Fig. 11)
With Remote Choke
1.
Remove air cleaner and check to see that choke
valve and rod move freely.
2.
Disconnect choke r*od at choke lever.
Check choke adjustment as follows:
On all except 275 hp 327 cu. in. engines, hold
choke valve closed and pull rod up against stop. The
top of choke rod end should be 1/2 - 1 rod diameter
4.
5.
above top of hole in choke valve lever.
On 275 hp 327 cu. in. engines, hold choke valve
closed and push rod down against stop on thermostat
bracket. The top of the choke rod should be 1/2 - 1
rod diameter below the top of the hole in the choke
lever.
If necessary, adjust rod length by bending rod at off-
set. (Bend must be such that rod enters choke lever
hole freely and squarely.)
Connect rod at choke lever and install air cleaner.
3.
With Manual
Choke
1.
Remove air cleaner.
2.
Push hand choke knob in to within 1/8" of instrument
panel.
3.
Loosen choke cable at carburetor bracket and adjust
cable through the clip until the choke valve is wide
open.
4.
Tighten cable clamp at carburetor bracket and check
operation of choke valve to ensure full closed and
wide open positions.
INSTRUMENT CHECK-OUT
Instrument Hook Up
Connect vacuum gauge, dwell meter, tachometer and
timing light as recommended by the manufacturer of the
equipment being used.
Check and Adjust Dwell
1.
Start engine then ch^ck ignition dwell.
.2.
If dwell is not within specifications, adjust dwell as
follows:
V8 ENGINES
• With engine running at idle, raise the adjustment
screw window-and insert an Allen wrench in the
socket of the adjusting screw (fig. 12).
• Turn the adjusting screw as required until a dwell
reading of 30° is obtained. A 2° variation is al-
lowable for wear.
• Close access cover fully to prevent the entry of
dirt into the distributor.
NOTE: If a dwell meter is not available, turn
adjusting screw clockwise until engine starts to
misfire, then turn screw one-half turn in the op-
posite direction to complete adjustment.
IN LINE ENGINES
• Remove distributor cap and recheck point setting.
If dwell is still not within specifications check the
distributor as outlined in Section 6Y.
Check Dwell Variation
Slowly accelerate engine to 1500 rpm and note dwell
reading. Return engine to idle and note dwell reading. If
dwell variation exceeds specifications, check for worn
distributor shaft, worn distributor shaft bushing or loose
breaker plate.
WINDOW
"HEX" TYPE
WRENCH
Fig.
12 - Setting Point Dwell (V8)
Fig.
13 - Ignition Timing Marks
CHEVROLET CHASSIS SERVICE MANUAL
Page 273 of 659
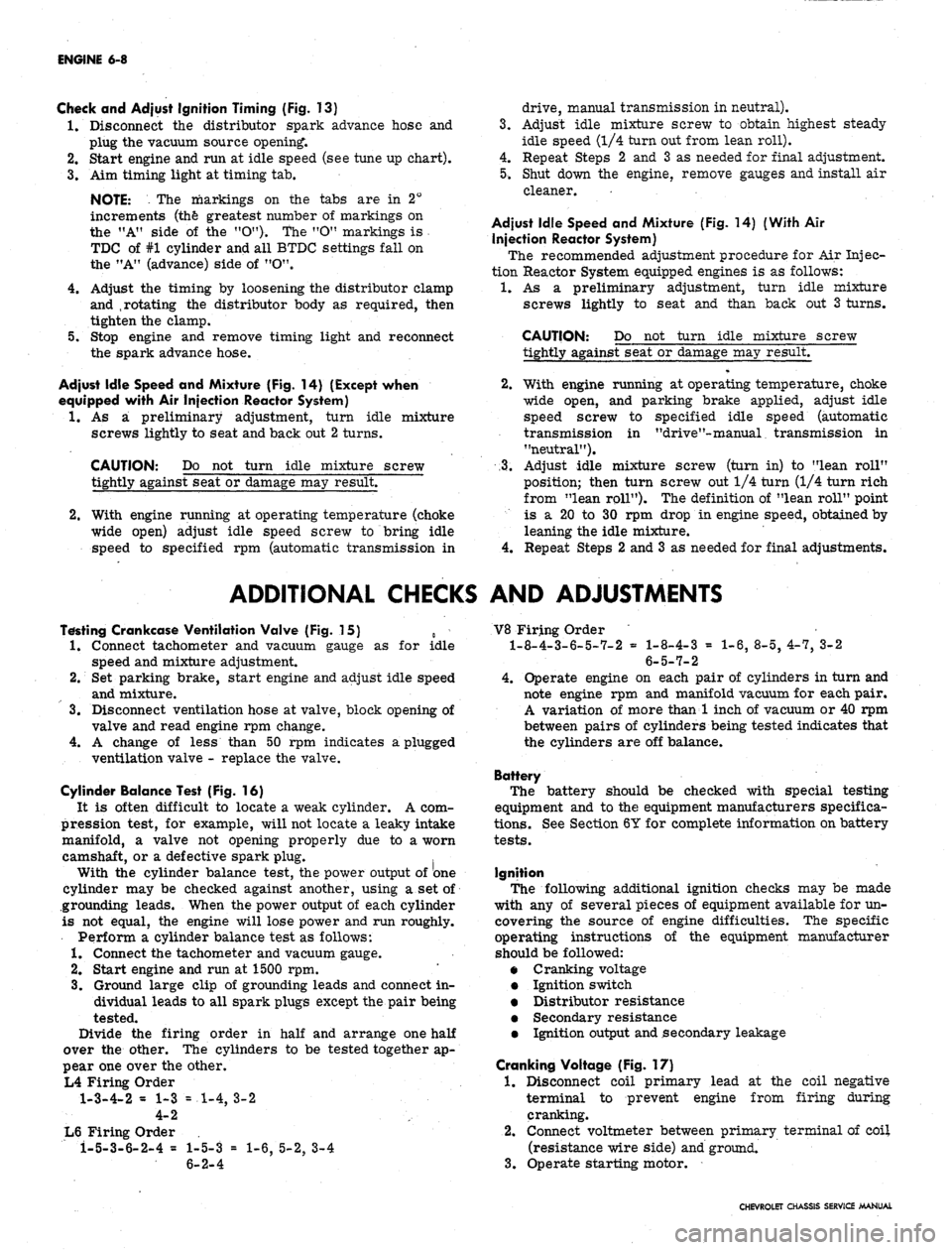
ENGINE
6-8
Check
and
Adjust Ignition Timing
(Fig. 13)
1.
Disconnect
the
distributor spark advance hose
and
plug
the
vacuum source opening.
2.
Start engine
and run at
idle speed
(see
tune
up
chart).
3.
Aim
timing light
at
timing
tab.
NOTE:
- The
markings
on the
tabs
are in 2°
increments
(the
greatest number
of
markings
on
the
"A"
side
of the "O"). the "O"
markings
is
TDC
of
#1 cylinder
and all
BTDC settings fall
on
the
"A"
(advance) side
of "O".
4.
Adjust
the
timing
by
loosening
the
distributor clamp
and
,
rotating
the
distributor body
as
required, then
tighten
the
clamp.
5.
Stop engine
and
remove timing light
and
reconnect
the spark advance hose.
Adjust Idle Speed
and
Mixture
(Fig. 14)
(Except when
equipped with
Air
Injection Reactor System)
1.
As a
preliminary adjustment, turn idle mixture
screws lightly
to
seat
and
back
out 2
turns.
CAUTION:
Do not
turn idle mixture screw
tightly against seat
or
damage
may
result.
2.
With engine running
at
operating temperature (choke
wide open) adjust idle speed screw
to
bring idle
speed
to
specified
rpm
(automatic transmission
in
drive, manual transmission
in
neutral).
3.
Adjust idle mixture screw
to
obtain highest steady
idle speed
(1/4
turn
out
from lean roll).
4.
Repeat Steps
2 and 3 as
needed
for
final adjustment.
5.
Shut down
the
engine, remove gauges
and
install
air
cleaner.
Adjust Idle Speed
and
Mixture
(Fig. 14)
(With
Air
Injection Reactor System)
The recommended adjustment procedure
for Air
Injec-
tion Reactor System equipped engines
is as
follows:
1.
As a
preliminary adjustment, turn idle mixture
screws lightly
to
seat
and
than back
out 3
turns.
CAUTION:
Do not
turn idle mixture screw
tightly against seat
or
damage
may
result.
2.
With engine running
at
operating temperature, choke
wide open,
and
parking brake applied, adjust idle
specified idle speed (automatic
"drive"-manual transmission
in
to
in
screw
transmission
"neutral").
;3.
Adjust idle mixture screw (turn
in) to
"lean roll"
position; then turn screw
out 1/4
turn
(1/4
turn rich
from "lean roll").
The
definition
of
"lean roll" point
is
a 20 to 30 rpm
drop
in
engine speed, obtained
by
leaning
the
idle mixture.
4.
Repeat Steps
2 and 3 as
needed
for
final adjustments.
ADDITIONAL CHECKS
AND
ADJUSTMENTS
Testing Crankcase Ventilation Valve
(Fig. 15) 0
1.
Connect tachometer
and
vacuum gauge
as for
idle
speed
and
mixture adjustment.
2.
Set
parking brake, start engine
and
adjust idle speed
and mixture.
3.
Disconnect ventilation hose
at
valve, block opening
of
valve
and
read engine
rpm
change.
4.
A
change
of
less than
50 rpm
indicates
a
plugged
ventilation valve
-
replace
the
valve.
Cylinder Balance Test
(Fig. 16)
It
is
often difficult
to
locate
a
weak cylinder.
A com-
pression test,
for
example, will
not
locate
a
leaky intake
manifold,
a
valve
not
opening properly
due to a
worn
camshaft,
or a
defective spark plug.
With
the
cylinder balance test,
the
power output
of one
cylinder
may be
checked against another, using
a set of
grounding leads. When
the
power output
of
each cylinder
is
not
equal,
the
engine will lose power
and run
roughly.
Perform
a
cylinder balance test
as
follows:
1.
Connect
the
tachometer
and
vacuum gauge.
2.
Start engine
and run at 1500 rpm.
3.
Ground large clip
of
grounding leads
and
connect
in-
dividual leads
to all
spark plugs except
the
pair being
tested.
Divide
the
firing order
in
half
and
arrange
one
half
over
the
other.
The
cylinders
to be
tested together
ap-
pear
one
over
the
other.
L4 Firing Order
V8 Firing Order
1-8-4-3-6-5-7-2
1-6, 8-5, 4-7, 3-2
1-3-4-2
= 1-3
4-2
L6 Firing Order
1-5-3-6-2-4
=
=
1-4. 3-2
1-5-3
6-2-4
1-6, 5-2, 3-4
1-8-4-3
6-5-7-2
4.
Operate engine
on
each pair
of
cylinders
in
turn
and
note engine
rpm and
manifold vacuum
for
each pair.
A variation
of
more than
1
inch
of
vacuum
or 40 rpm
between pairs
of
cylinders being tested indicates that
the cylinders
are off
balance.
Battery
The battery should
be
checked with special testing
equipment
and to the
equipment manufacturers specifica-
tions.
See
Section 6Y
for
complete information
on
battery
tests.
Ignition
The following additional ignition checks
may be
made
with
any of
several pieces
of
equipment available
for un-
covering
the
source
of
engine difficulties.
The
specific
operating instructions
of the
equipment manufacturer
should
be
followed:
Cranking voltage
Ignition switch
Distributor resistance
Secondary resistance
Ignition output
and
secondary leakage
Cranking Voltage
(Fig. 17)
1.
Disconnect coil primary lead
at the
coil negative
terminal
to
prevent engine from firing during
cranking.
2.
Connect voltmeter between primary terminal
of coi|
(resistance wire side)
and
ground.
3.
Operate starting motor.
CHEVROLET CHASSIS SERVICE MANUAL
Page 274 of 659
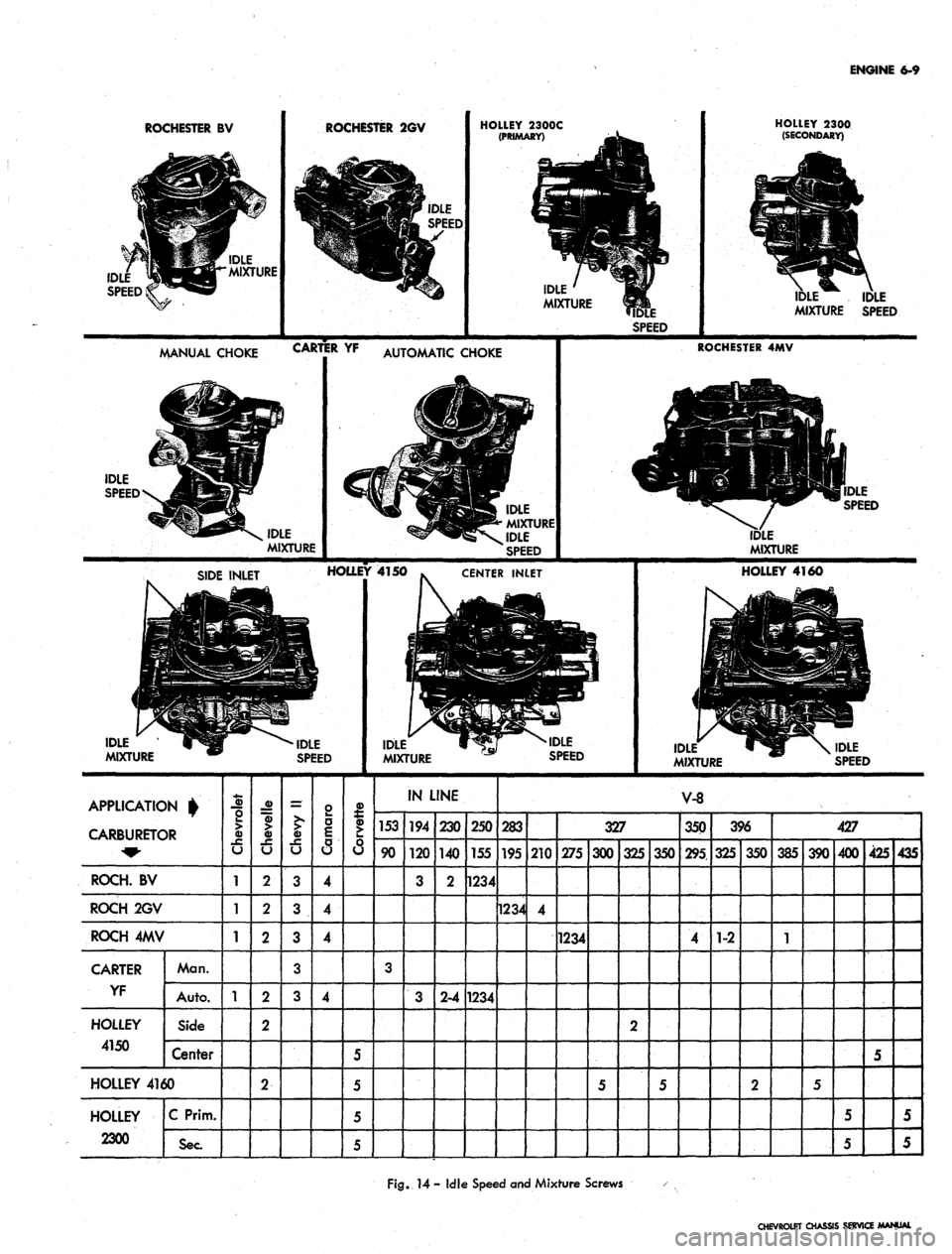
ENGINE
6-9
ROCHESTER
BV
IDLE
MIXTURE
ROCHESTER
2GV
HOLLEY 2300C
(PRIMARY)
IDLE
MIXTURE
SPEED
HOLLEY 2300
(SECONDARY)
LE IDLE
MIXTURE SPEED
MANUAL CHOKE
CARTER
YF
IDLE
MIXTURE
AUTOMATIC CHOKE
IDLE
MIXTURE
IDLE
SPEED
ROCHESTER
4MV
IDLE
MIXTURE
SIDE INLET
HOLLEY 4150
CENTER INLET
IDLE
MIXTURE
IDLE
MIXTURE
HOLLEY 4160
IDLE
MIXTURE
APPLICATION |
CARBURETOR
IN LINE
153
90
194
120
230
140
250
155
V-8
283
195
210
327
275 300 325 350
350
295
396
325 350
427
385 390 400 425 435
ROCH.
BV
1234
ROCH 2GV
1234
ROCH
4MV
1234
1-2
CARTER
YF
Man.
Auto.
2-4
1234
HOLLEY
4150
Side
Center
HOLLEY
4160
HOLLEY
2300
C Prim.
Sec.
Fig.
14 - Idle Speed and Mixture Screws
CHEVROLET CHASSIS SERVICE MANUAL
Page 275 of 659
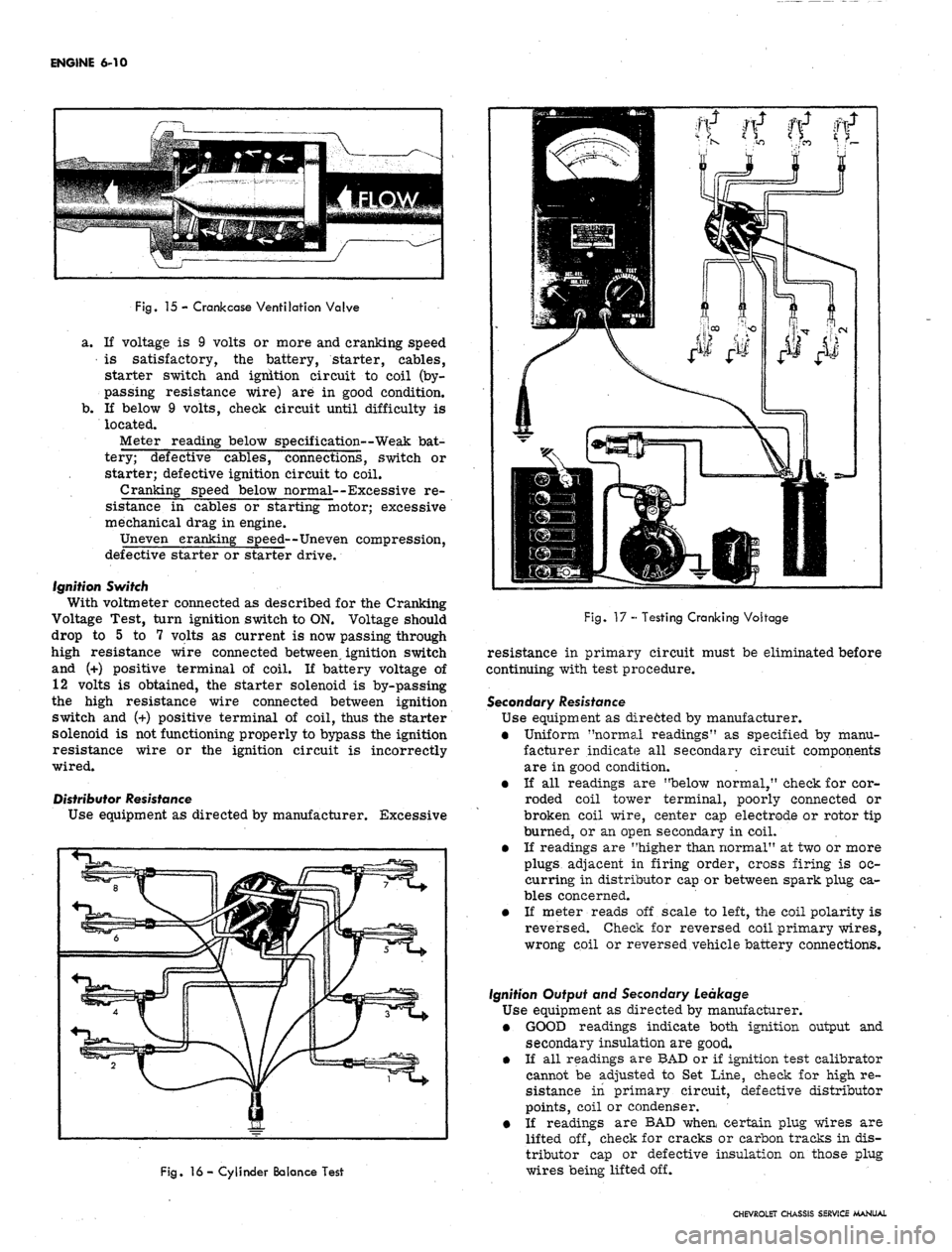
ENGINE 6-10
Fig.
15 - Crank case Ventilation Valve
a. If voltage is 9 volts or more and cranking speed
is satisfactory, the battery, starter, cables,
starter switch and ignition circuit to coil (by-
passing resistance wire) are in good condition.
b.
If below 9 volts, check circuit until difficulty is
located.
Meter reading below specification—Weak bat-
tery; defective cables, connections, switch or
starter; defective ignition circuit to coil.
Cranking speed below normal--Excessive re-
sistance in cables or starting motor; excessive
mechanical drag in engine.
Uneven cranking speed—Uneven compression,
defective starter or starter drive.
Ignition Switch
With voltmeter connected as described for the Cranking
Voltage Test, turn ignition switch to ON. Voltage should
drop to 5 to 7 volts as current is now passing through
high resistance wire connected between ignition switch
and (+) positive terminal of coil. If battery voltage of
12 volts is obtained, the starter solenoid is by-passing
the high resistance wire connected between ignition
switch and (+) positive terminal of coil, thus the starter
solenoid is not functioning properly to bypass the ignition
resistance wire or the ignition circuit is incorrectly
wired.
Distributor Resistance
Use equipment as directed by manufacturer.
Excessive
(t n ti ft
Fig.
16 - Cylinder Balance Test
Fig.
17 - Testing Cranking Voltage
resistance in primary circuit must be eliminated before
continuing with test procedure.
Secondary Resistance
Use equipment as dire6ted by manufacturer.
• Uniform "normal readings" as specified by manu-
facturer indicate all secondary circuit components
are in good condition.
• If all readings are "below normal," check for cor-
roded coil tower terminal, poorly connected or
broken coil wire, center cap electrode or rotor tip
burned, or an open secondary in coil.
• If readings are "higher than normal" at two or more
plugs adjacent in firing order, cross firing is oc-
curring in distributor cap or between spark plug ca-
bles concerned.
• If meter reads off scale to left, the coil polarity is
reversed. Check for reversed coil primary wires,
wrong coil or reversed vehicle battery connections.
Ignition Output and Secondary Leakage
Use equipment as directed by manufacturer.
• GOOD readings indicate both ignition output and
secondary insulation are good.
• If all readings are BAD or if ignition test calibrator
cannot be adjusted to Set Line, check for high re-
sistance in primary circuit, defective distributor
points, coil or condenser.
e If readings are BAD when certain plug wires are
lifted off, check for cracks or carbon tracks in dis-
tributor cap or defective insulation on those plug
wires being lifted off.
CHEVROLET CHASSIS SERVICE MANUAL
Page 276 of 659
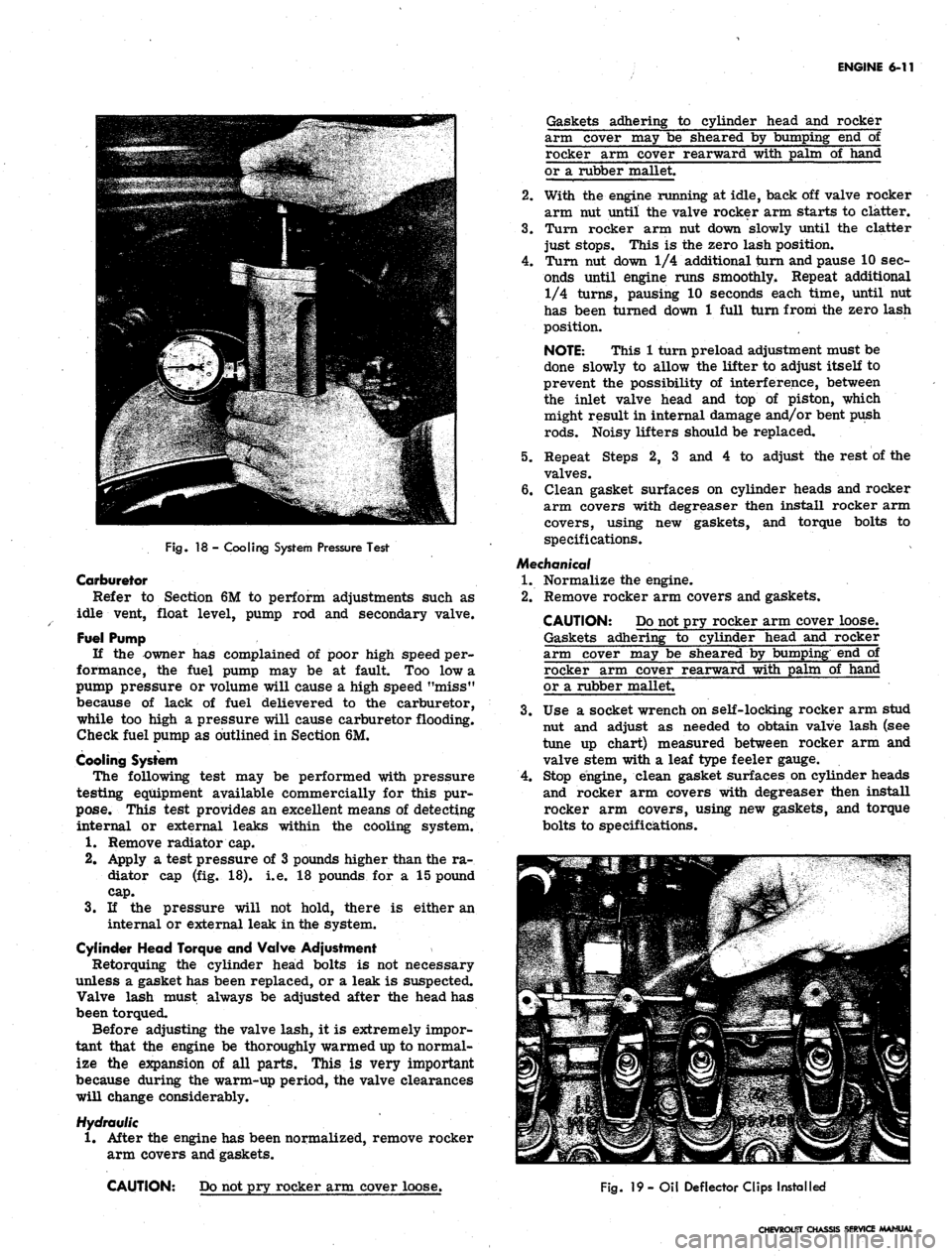
ENGINE 6-11
Fig.
18 - Cooling System Pressure Test
Carburetor
Refer to Section 6M to perform adjustments such as
idle vent, float level, pump rod and secondary valve.
Fuel Pump
If the owner has complained of poor high speed per-
formance, the fuel pump may be at fault. Too low a
pump pressure or volume will cause a high speed "miss"
because of lack of fuel delievered to the carburetor,
while too high a pressure will cause carburetor flooding.
Check fuel pump as outlined in Section 6M.
Cooling System
The following test may be performed with pressure
testing equipment available commercially for this pur-
pose.
This test provides an excellent means of detecting
internal or external leaks within the cooling system.
1.
Remove radiator cap.
2.
Apply a test pressure of 3 pounds higher than the ra-
diator cap (fig. 18). i.e. 18 pounds for a 15 pound
cap.
3.
If the pressure will not hold, there is either an
internal or external leak in the system.
Cylinder Head Torque and Valve Adjustment
Retorquing the cylinder head bolts is not necessary
unless a gasket has been replaced, or a leak is suspected.
Valve lash must always be adjusted after the head has
been torqued.
Before adjusting the valve lash, it is extremely impor-
tant that the engine be thoroughly warmed up to normal-
ize the expansion of all parts. This is very important
because during the warm-up period, the valve clearances
will change considerably.
Hydraulic
1.
After the engine has been normalized, remove rocker
arm covers and gaskets.
CAUTION: Do not pry rocker arm cover loose.
Gaskets adhering to cylinder head and rocker
arm cover may be sheared by bumping end of
rocker arm cover rearward with palm of hand
or a rubber mallet.
2.
With the engine running at idle, back off valve rocker
arm nut until the valve rocker arm starts to clatter.
3.
Turn rocker arm nut down slowly until the clatter
just stops. This is the zero lash position.
4.
Turn nut down 1/4 additional turn and pause 10 sec-
onds until engine runs smoothly* Repeat additional
1/4 turns, pausing 10 seconds each time, until nut
has been turned down 1 full turn from the zero lash
position.
NOTE: This 1 turn preload adjustment must be
done slowly to allow the lifter to adjust itself to
prevent the possibility of interference, between
the inlet valve head and top of piston, which
might result in internal damage and/or bent push
rods.
Noisy lifters should be replaced.
5.
Repeat Steps 2, 3 and 4 to adjust the rest of the
valves.
6. Clean gasket surfaces on cylinder heads and rocker
arm covers with degreaser then install rocker arm
covers, using new gaskets, and torque bolts to
specifications.
Mechanical
1.
Normalize the engine.
2.
Remove rocker arm covers and gaskets.
CAUTION: Do not pry rocker arm cover loose.
Gaskets adhering to cylinder head and rocker
arm cover may be sheared by bumping end of
rocker arm cover rearward with palm of hand
or a rubber mallet.
3.
Use a socket wrench on self-locking rocker arm stud
nut and adjust as needed to obtain valve lash (see
tune up chart) measured between rocker arm and
valve stem with a leaf type feeler gauge.
4.
Stop engine, clean gasket surfaces on cylinder heads
and rocker arm covers with degreaser then install
rocker arm covers, using new gaskets, and torque
bolts to specifications.
Fig.
19
- Oil Deflector Clips Installed
CHEVROLET CHASSIS SERVICE MANUAL
Page 277 of 659
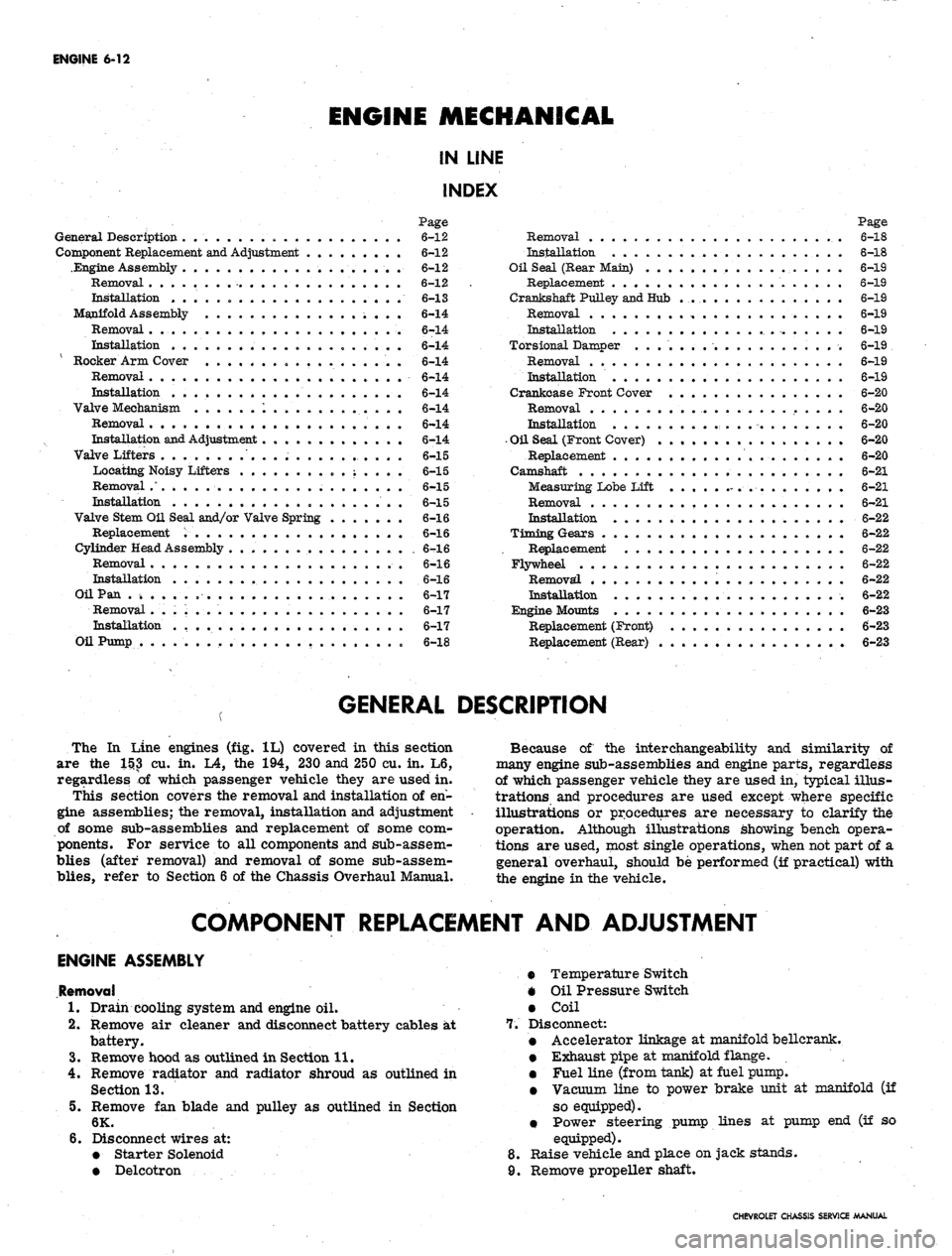
ENGINE
6-12
ENGINE
MECHANICAL
IN LINE
INDEX
Page
General Description . „ 6-12
Component Replacement and Adjustment 6-12
.Engine Assembly 6-12
Removal 6-12
Installation 6-13
Manifold Assembly 6-14
Removal . 6-14
Installation 6-14
Rocker Arm Cover . 6-14
Removal 6-14
mstallation . . . 6-14
Valve Mechanism
......
1 6-14
Removal 6-14
Installation and Adjustment . 6-14
Valve Lifters
..............
6-15
Locating Noisy Lifters
„.;....
6-15
Removal
.'.*...•
6-15
Installation . 6-15
Valve Stem Oil Seal and/or Valve Spring . 6-16
Replacement . 6-16
Cylinder Head Assembly . 6-16
Removal 6-16
Installation . 6-16
Oil Pan . » 6-17
Removal . . . ; . . 6-17
Installation
.........
. 6-17
Oil Pump . 6-18
Page
Removal . 6-18
Installation . 6-18
Oil Seal (Rear Main) . 6-19
Replacement 6-19
Crankshaft Pulley and Hub 6-19
Removal 6-19
Installation 6-19
Torsional Damper 6-19
Removal 6-19
Installation 6-19
Crankcase Front Cover . 6-20
Removal . 6-20
Installation 6-20
•
Oil Seal (Front Cover) 6-20
Replacement 6-20
Camshaft 6-21
Measuring Lobe Lift . ... .
.-.••.-.
6-21
Removal 6-21
Installation 6-22
Timing Gears
..••••.............••• 6—22
Replacement
6-22
Flywheel
6-22
Removal
* 6-22
Installation
6-22
Engine
Mounts
6-23
Replacement
(Front)
6-23
Replacement
(Rear)
. 6-23
GENERAL DESCRIPTION
The
In
Line engines
(fig. 1L)
covered
in
this section
are
the 1H3 cu. in. L4, the 194,
230
and
250
cu. in. L6,
regardless
of
which passenger vehicle they
are
used
in.
This section covers
the
removal
and
installation
of en-
gine assemblies;
the
removal, installation
and
adjustment
of some sub-assemblies
and
replacement
of
some
com-
ponents.
For
service
to all
components
and
sub-assem-
blies (after removal)
and
removal
of
some sub-assem-
blies,
refer
to
Section
6 of the
Chassis Overhaul Manual.
Because
of the
interchangeability
and
similarity
of
many engine sub-assemblies
and
engine parts, regardless
of which passenger vehicle they
are
used
in,
typical illus-
trations
and
procedures
are
used except where specific
illustrations
or
procedures
are
necessary
to
clarify
the
operation. Although illustrations showing bench opera-
tions
are
used, most single operations, when
not
part
of a
general overhaul, should
be
performed
(if
practical) with
the engine
in the
vehicle.
COMPONENT REPLACEMENT
AND
ADJUSTMENT
ENGINE ASSEMBLY
Removal
1.
Drain cooling system
and
engine
oil.
2.
Remove
air
cleaner
and
disconnect battery cables
at 7.
battery.
3.
Remove hood
as
outlined
in
Section 11.
4.
Remove radiator
and
radiator shroud
as
outlined
in
Section 13.
5.
Remove
fan
blade
and
pulley
as
outlined
in
Section
6K.
6. Disconnect wires
at:
• Starter Solenoid
8.
• Delcotron
9.
Temperature Switch
Oil Pressure Switch
Coil
Disconnect:
Accelerator linkage
at
manifold bellerank.
Exhaust pipe
at
manifold flange.
.
Fuel line (from tank)
at
fuel pump.
Vacuum line
to
power brake unit
at
manifold
(if
so equipped).
• Power steering pump lines
at
pump
end (if so
equipped).
Raise vehicle
and
place
on
jack stands.
Remove propeller shaft.
CHEVROLET CHASSIS SERVICE MANUAL
Page 278 of 659
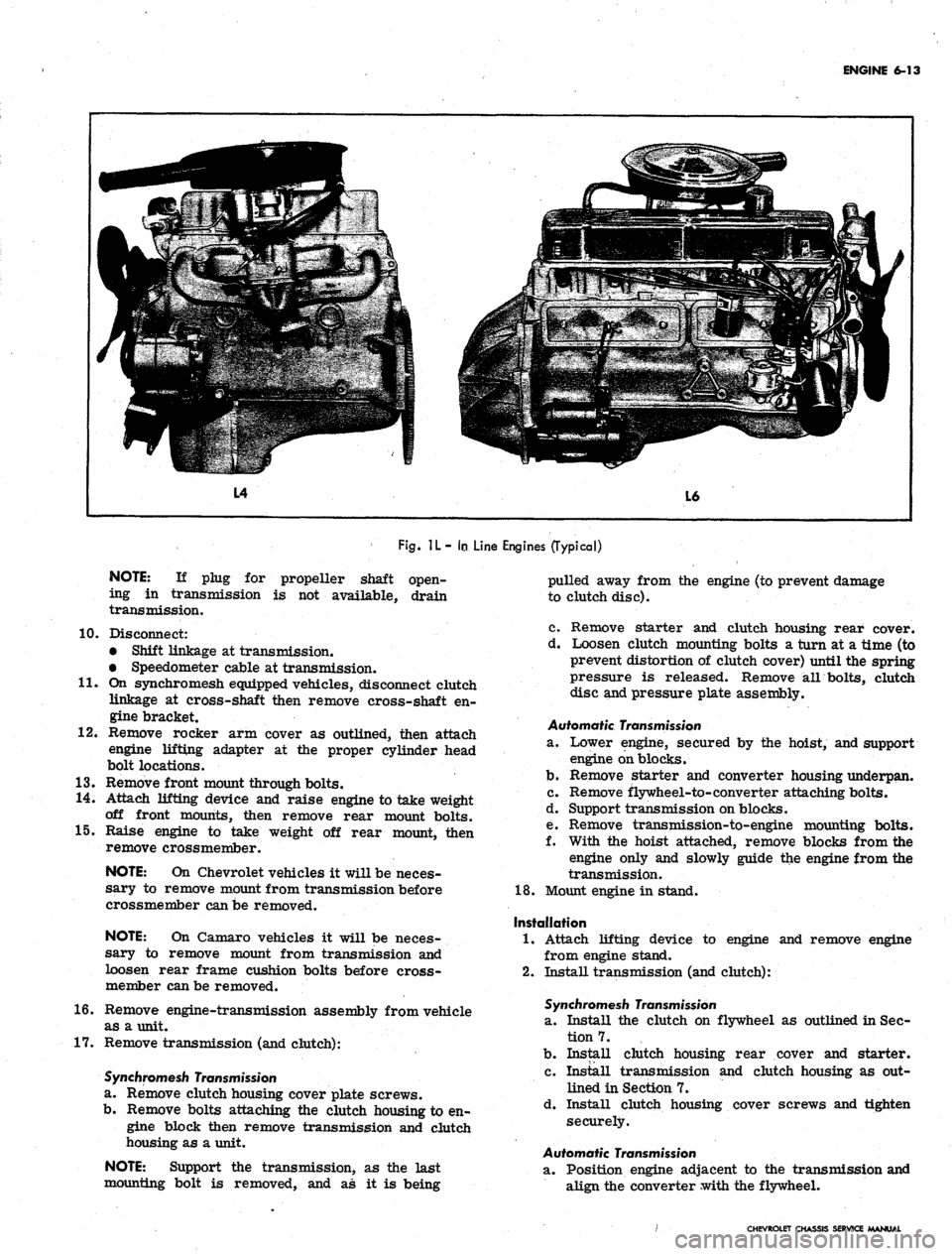
ENGINE 6-13
Fig.
1L- In
Line Engines (Typical)
NOTE:
If plug for propeller shaft open-
ing in transmission is not available, drain
transmission.
10.
11.
12.
Disconnect:
• Shift linkage at transmission.
• Speedometer cable at transmission.
On synchromesh equipped vehicles, disconnect clutch
linkage at cross-shaft then remove cross-shaft en-
gine bracket.
Remove rocker arm cover as outlined, then attach
engine lifting adapter at the proper cylinder head
bolt locations.
13.
Remove front mount through bolts.
14.
Attach lifting device and raise engine to take weight
off front mounts, then remove rear mount bolts.
15.
Raise engine to take weight off rear mount, then
remove crossmember.
NOTE:
On Chevrolet vehicles it will be neces-
sary to remove mount from transmission before
crossmember can be removed.
NOTE:
On Camaro vehicles it will be neces-
sary to remove mount from transmission and
loosen rear frame cushion bolts before cross-
member can be removed.
16.
Remove engine-transmission assembly from vehicle
as a unit.
17.
Remove transmission (and clutch):
Synchromesh Transmission
a. Remove clutch housing cover plate screws.
b.
Remove bolts attaching the clutch housing to en-
gine block then remove transmission and clutch
housing as a unit.
NOTE:
Support the transmission, as the last
mounting bolt is removed, and as it is being
pulled away from the engine (to prevent damage
to clutch disc).
c. Remove starter and clutch housing rear cover.
d. Loosen clutch mounting bolts a turn at a time (to
prevent distortion of clutch cover) until the spring
pressure is released. Remove all bolts, clutch
disc and pressure plate assembly.
Automatic Transmission
SL.
Lower engine, secured by the hoist, and support
engine on blocks.
b.
Remove starter and converter housing underpan.
c. Remove flywheel-to-converter attaching bolts.
d. Support transmission on blocks.
e. Remove transmission-to-engine mounting bolts.
f. With the hoist attached, remove blocks from the
engine only and slowly guide the engine from the
transmission.
18.
Mount engine in stand.
Installation
1.
Attach lifting device to engine and remove engine
from engine stand.
2.
Install transmission (and clutch):
Synchromesh Transmission
a. Install the clutch on flywheel as outlined in Sec-
tion 7.
b.
Install clutch housing rear cover and starter.
c. Install transmission and clutch housing as out-
lined in Section 7.
d. Install clutch housing cover screws and tighten
securely.
Automatic Transmission
a. Position engine adjacent to the transmission and
align the converter with the flywheel.
CHEVROLET CHASSIS SERVICE MANUAL
Page 279 of 659
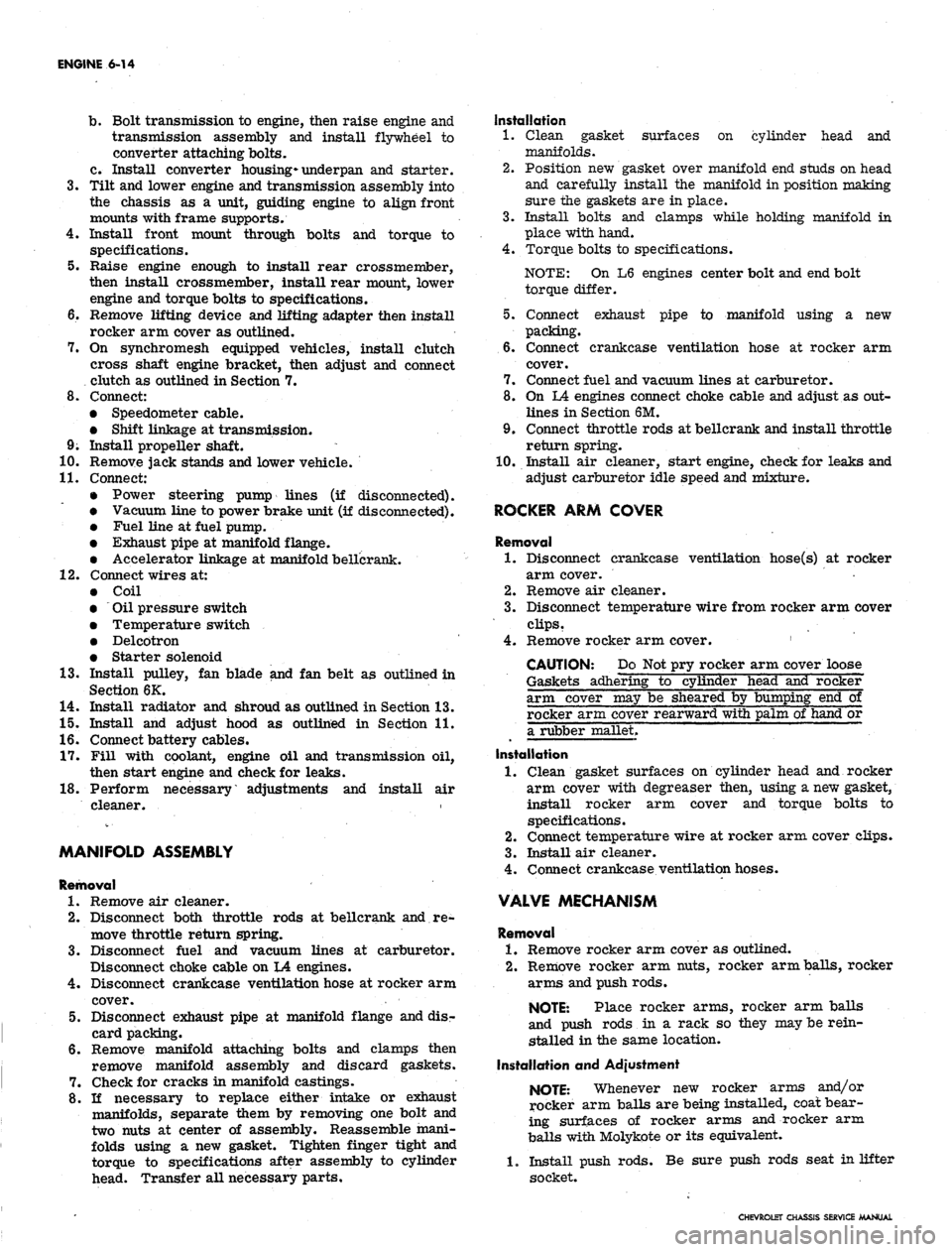
ENGINE 6-14
b.
Bolt transmission to engine, then raise engine and
transmission assembly and install flywheel to
converter attaching bolts.
c. Install converter
housing*
underpan and starter.
3.
Tilt and lower engine and transmission assembly into
the chassis as a unit, guiding engine to align front
mounts with frame supports.
4.
Install front mount through bolts and torque to
specifications.
5.
Raise engine enough to install rear crossmember,
then install crossmember, install rear mount, lower
engine and torque bolts to specifications.
6. Remove lifting device and lifting adapter then install
rocker arm cover as outlined.
7.
On synchromesh equipped vehicles, install clutch
cross shaft engine bracket, then adjust and connect
clutch as outlined in Section 7.
8. Connect:
• Speedometer cable.
• Shift linkage at transmission.
9; Install propeller shaft.
10.
Remove jack stands and lower vehicle.
11.
Connect:
Power steering pump lines (if disconnected).
Vacuum line to power brake unit (if disconnected).
Fuel line at fuel pump.
Exhaust pipe at manifold flange.
Accelerator linkage at manifold bellcrank.
12.
Connect wires at:
Coil
Oil pressure switch
Temperature switch
Delcotron
Starter solenoid
13.
Install pulley, fan blade and fan belt as outlined in
Section 6K.
14.
Install radiator and shroud as outlined in Section 13.
15.
Install and adjust hood as outlined in Section 11.
16.
Connect battery cables.
17.
Fill with coolant, engine oil and transmission oil,
then start engine and check for leaks.
18.
Perform necessary adjustments and install air
cleaner.
MANIFOLD ASSEMBLY
Removal
1.
Remove air cleaner.
2.
Disconnect both throttle rods at bellcrank and re-
move throttle return spring.
3.
Disconnect fuel and vacuum lines at carburetor.
Disconnect choke cable on \A engines.
4.
Disconnect crankcase ventilation hose at rocker arm
cover.
5.
Disconnect exhaust pipe at manifold flange and dis-
card packing.
6. Remove manifold attaching bolts and clamps then
remove manifold assembly and discard gaskets.
7.
Check for cracks in manifold castings.
8. If necessary to replace either intake or exhaust
manifolds, separate them by removing one bolt and
two nuts at center of assembly. Reassemble mani-
folds using a new gasket. Tighten finger tight and
torque to specifications after assembly to cylinder
head. Transfer all necessary parts.
Installation
1.
Clean gasket surfaces on cylinder head and
manifolds*
2.
Position new gasket over manifold end studs on head
and carefully install the manifold in position making
sure the gaskets are in place.
3.
Install bolts and clamps while holding manifold in
place with hand.
4.
Torque bolts to specifications.
NOTE: On L6 engines center bolt and end bolt
torque differ.
5.
Connect exhaust pipe to manifold using a new
packing.
6. Connect crankcase ventilation hose at rocker arm
cover.
7.
Connect fuel and vacuum lines at carburetor.
8. On L4 engines connect choke cable and adjust as out-
lines in Section 6M.
9. Connect throttle rods at bellcrank and install throttle
return spring.
10.
Install air cleaner, start engine, check for leaks and
adjust carburetor idle speed and mixture.
ROCKER ARM COVER
Removal
1.
Disconnect crankcase ventilation hose(s) at rocker
arm cover.
2.
Remove air cleaner.
3.
Disconnect temperature wire from rocker arm cover
clips.
4.
Remove rocker arm cover. '
CAUTION: Do Not pry rocker arm cover loose
Gaskets adhering to cylinder head and rocker
arm cover may be sheared by bumping end of
rocker arm cover rearward with palm of hand or
a rubber mallet.
Installation
1.
Clean gasket surfaces on cylinder head and rocker
arm cover with degreaser then, using anew gasket,
install rocker arm cover and torque bolts to
specifications.
2.
Connect temperature wire at rocker arm cover clips.
3.
Install air cleaner.
4.
Connect crankcase ventilation hoses.
VALVE MECHANISM
Removal
1.
Remove rocker arm cover as outlined.
2.
Remove rocker arm nuts, rocker arm
balls,
rocker
arms and push rods.
NOTE:
Place rocker arms, rocker arm balls
and push rods in a rack so they may be rein-
stalled in the same location.
Installation and Adjustment
NOTE:
Whenever new rocker arms and/or
rocker arm balls are being installed, coat bear-
ing surfaces of rocker arms and rocker arm
balls with Molykote or its equivalent.
1.
Install push rods,
socket.
Be sure push rods seat in lifter
CHEVROLET CHASSIS SERVICE MANUAL
Page 280 of 659
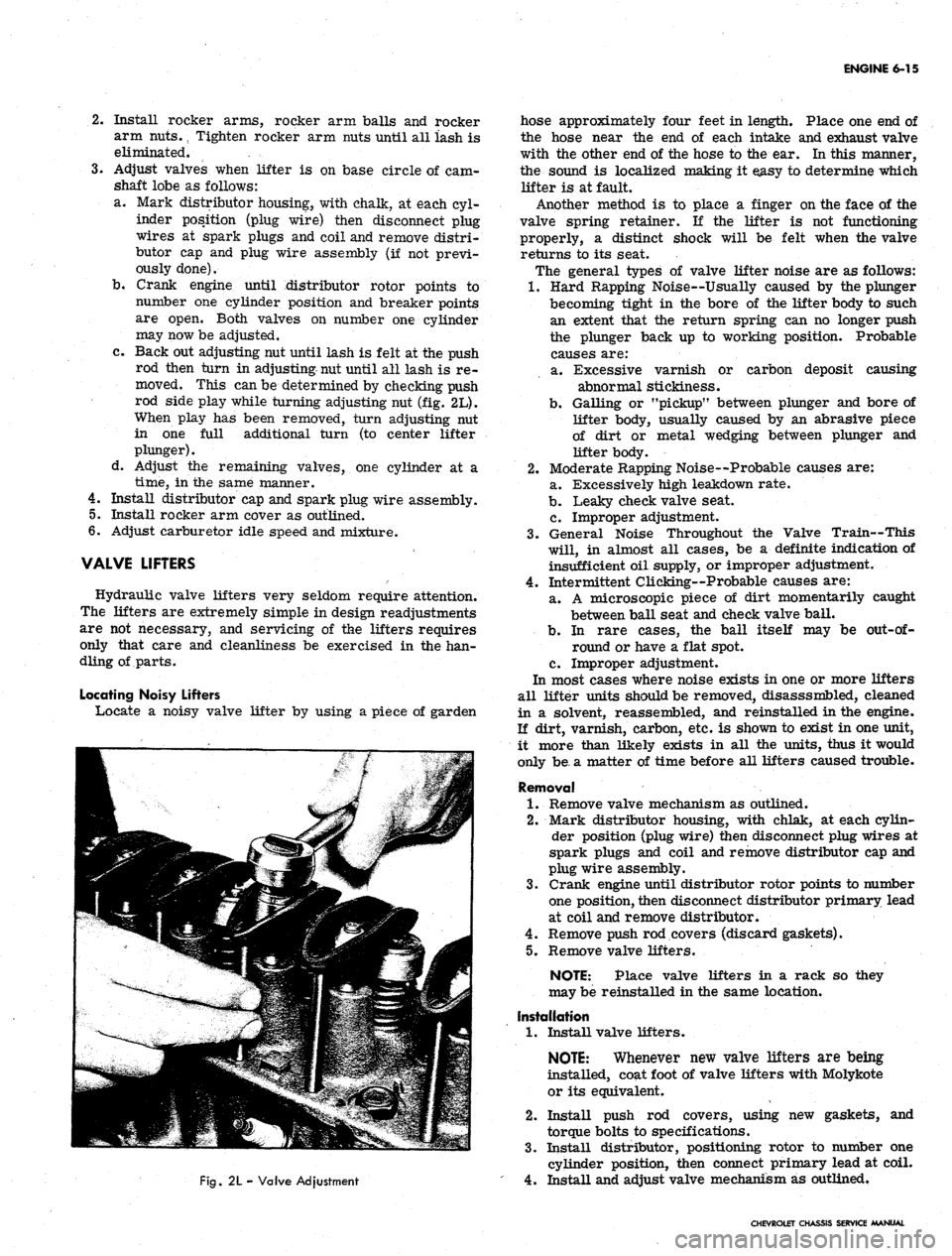
ENGINE 6-15
2.
Install rocker arms, rocker arm balls and rocker
arm
nuts.
\
Tighten rocker arm nuts until all lash is
eliminated. .
3.
Adjust valves when lifter is on base circle of cam-
shaft lobe as follows:
a. Mark distributor housing, with chalk, at each cyl-
inder position (plug wire) then disconnect plug
wires at spark plugs and coil and remove distri-
butor cap and plug wire assembly (if not previ-
ously done).
b.
Crank engine until distributor rotor points to
number one cylinder position and breaker points
are open. Both valves on number one cylinder
may now be adjusted.
c. Back out adjusting nut until lash is felt at the push
rod then turn in adjusting nut until all lash is re-
moved. This can be determined by checking push
rod side play while turning adjusting nut (fig. 2L).
When play has been removed, turn adjusting nut
in one full additional turn (to center lifter
plunger).
d. Adjust the remaining valves, one cylinder at a
time,
in the same manner.
4.
Install distributor cap and spark plug wire assembly.
5.
Install rocker arm cover as outlined.
6. Adjust carburetor idle speed and mixture.
VALVE LIFTERS
Hydraulic valve lifters very seldom require attention.
The lifters are extremely simple in design readjustments
are not necessary, and servicing of the lifters requires
only that care and cleanliness be exercised in the han-
dling of parts.
Locating Noisy Lifters
Locate a noisy valve lifter by using a piece of garden
Fig.
2L - Valve Adjustment
hose approximately four feet in length. Place one end of
the hose near the end of each intake and exhaust valve
with the other end of the hose to the ear. In this manner,
the sound is localized making it easy to determine which
lifter is at fault.
Another method is to place a finger on the face of the
valve spring retainer. If the lifter is not functioning
properly, a distinct shock will be felt when the valve
returns to its seat.
The general types of valve lifter noise are as follows:
1.
Hard Rapping Noise--Usually caused by the plunger
becoming tight in the bore of the lifter body to such
an extent that the return spring can no longer push
the plunger back up to working position. Probable
causes are:
a. Excessive varnish or carbon deposit causing
abnormal stickiness.
b.
Galling or "pickup" between plunger and bore of
lifter body, usually caused by an abrasive piece
of dirt or metal wedging between plunger and
lifter body.
2.
Moderate Rapping Noise--Probable causes are:
a. Excessively high leakdown rate.
b.
Leaky check valve seat.
c. Improper adjustment.
3.
General Noise Throughout the Valve Train—This
will, in almost all cases, be a definite indication of
insufficient oil supply, or improper adjustment.
4.
Intermittent Clicking—Probable causes are:
a. A microscopic piece of dirt momentarily caught
between ball seat and check valve ball.
b.
In rare cases, the ball itself may be
out-of-
round or have a flat spot.
c. Improper adjustment.
In most cases where noise exists in one or more lifters
all lifter units should be removed, disasssmbled, cleaned
in a solvent, reassembled, and reinstalled in the engine.
If dirt, varnish, carbon, etc. is shown to exist in one unit,
it more than likely exists in all the units, thus it would
only be, a matter of time before all lifters caused trouble.
Removal
1.
Remove valve mechanism as outlined.
2.
Mark distributor housing, with chlak, at each cylin-
der position (plug wire) then disconnect plug wires at
spark plugs and coil and remove distributor cap and
plug wire assembly.
3.
Crank engine until distributor rotor points to number
one position, then disconnect distributor primary lead
at coil and remove distributor.
4.
Remove push rod covers (discard gaskets).
5.
Remove valve lifters.
NOTE: Place valve lifters in a rack so they
may be reinstalled in the same location.
Installation
1.
Install valve lifters.
NOTE:
Whenever new valve lifters are being
installed, coat foot of valve lifters with Molykote
or its equivalent.
2.
Install push rod covers, using new gaskets, and
torque bolts to specifications.
3.
Install distributor, positioning rotor to number one
cylinder position, then connect primary lead at coil.
4.
Install and adjust valve mechanism as outlined.
CHEVROLET CHASSIS SERVICE MANUAL