CHEVROLET PLYMOUTH ACCLAIM 1993 Service Manual
Manufacturer: CHEVROLET, Model Year: 1993, Model line: PLYMOUTH ACCLAIM, Model: CHEVROLET PLYMOUTH ACCLAIM 1993Pages: 2438, PDF Size: 74.98 MB
Page 1991 of 2438
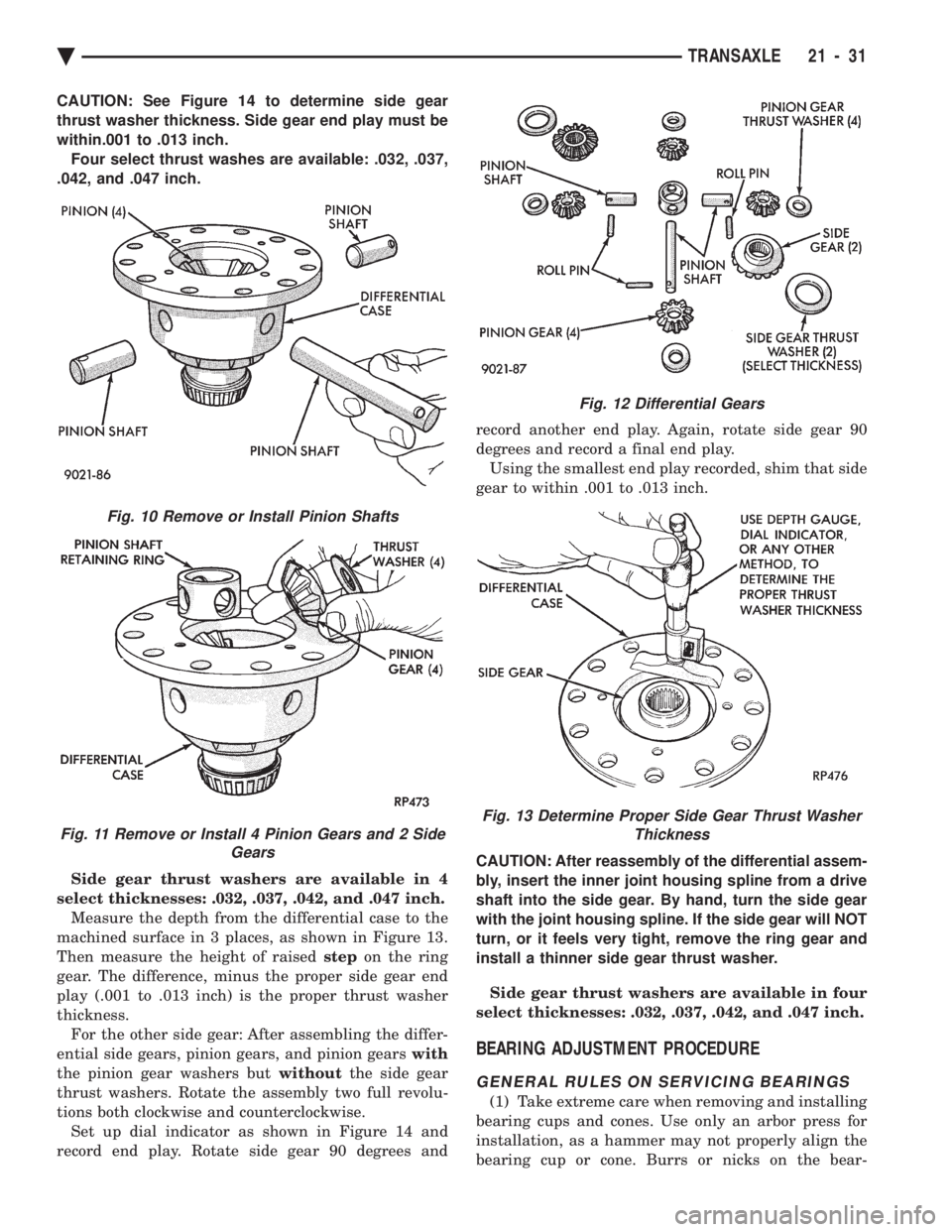
CAUTION: See Figure 14 to determine side gear
thrust washer thickness. Side gear end play must be
within.001 to .013 inch.Four select thrust washes are available: .032, .037,
.042, and .047 inch.
Side gear thrust washers are available in 4
select thicknesses: .032, .037, .042, and .047 inch. Measure the depth from the differential case to the
machined surface in 3 places, as shown in Figure 13.
Then measure the height of raised stepon the ring
gear. The difference, minus the proper side gear end
play (.001 to .013 inch) is the proper thrust washer
thickness. For the other side gear: After assembling the differ-
ential side gears, pinion gears, and pinion gears with
the pinion gear washers but withoutthe side gear
thrust washers. Rotate the assembly two full revolu-
tions both clockwise and counterclockwise. Set up dial indicator as shown in Figure 14 and
record end play. Rotate side gear 90 degrees and record another end play. Again, rotate side gear 90
degrees and record a final end play.
Using the smallest end play recorded, shim that side
gear to within .001 to .013 inch.
CAUTION: After reassembly of the differential assem-
bly, insert the inner joint housing spline from a drive
shaft into the side gear. By hand, turn the side gear
with the joint housing spline. If the side gear will NOT
turn, or it feels very tight, remove the ring gear and
install a thinner side gear thrust washer.
Side gear thrust washers are available in four
select thicknesses: .032, .037, .042, and .047 inch.
BEARING ADJUSTMENT PROCEDURE
GENERAL RULES ON SERVICING BEARINGS
(1) Take extreme care when removing and installing
bearing cups and cones. Use only an arbor press for
installation, as a hammer may not properly align the
bearing cup or cone. Burrs or nicks on the bear-
Fig. 12 Differential Gears
Fig. 13 Determine Proper Side Gear Thrust Washer Thickness
Fig. 10 Remove or Install Pinion Shafts
Fig. 11 Remove or Install 4 Pinion Gears and 2 Side Gears
Ä TRANSAXLE 21 - 31
Page 1992 of 2438
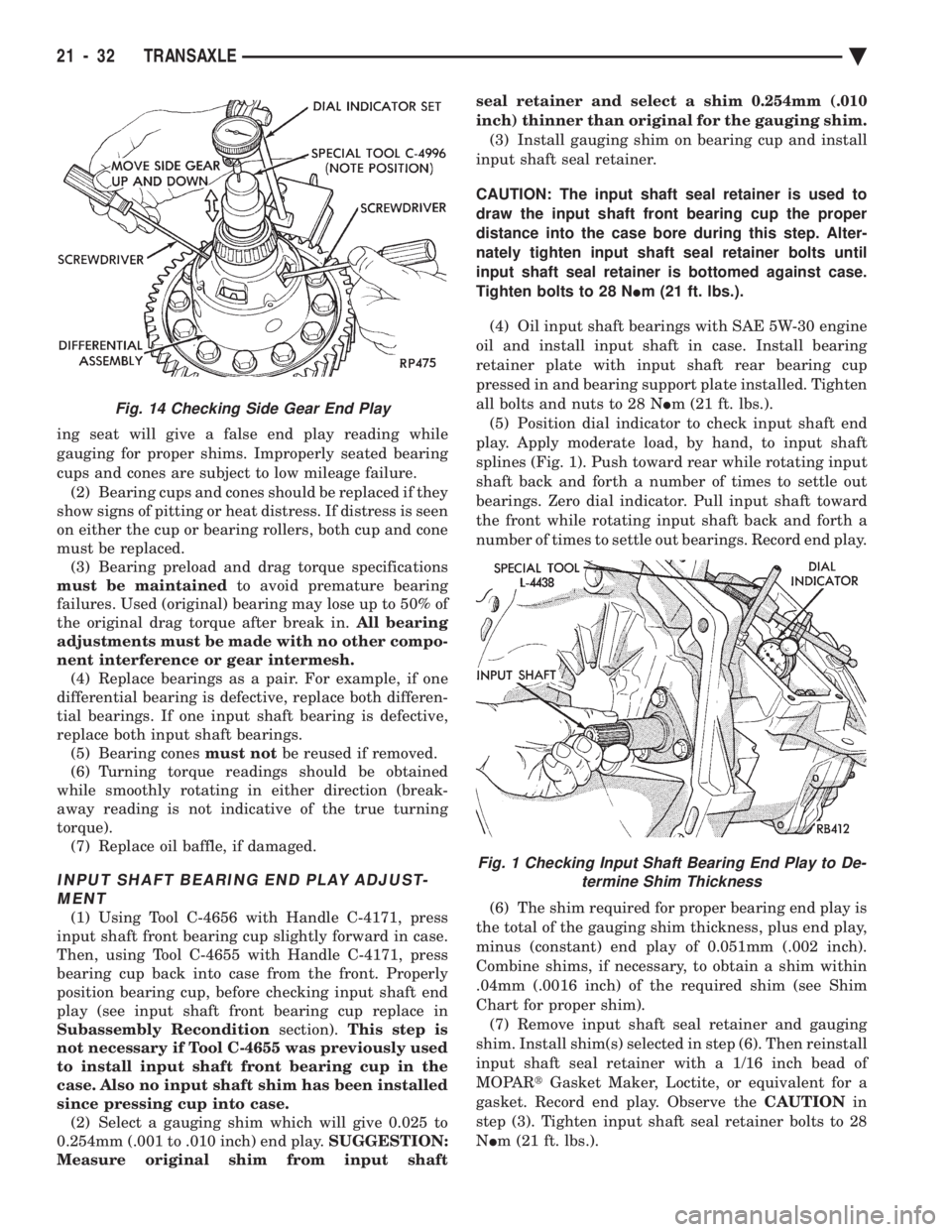
ing seat will give a false end play reading while
gauging for proper shims. Improperly seated bearing
cups and cones are subject to low mileage failure.(2) Bearing cups and cones should be replaced if they
show signs of pitting or heat distress. If distress is seen
on either the cup or bearing rollers, both cup and cone
must be replaced. (3) Bearing preload and drag torque specifications
must be maintained to avoid premature bearing
failures. Used (original) bearing may lose up to 50% of
the original drag torque after break in. All bearing
adjustments must be made with no other compo-
nent interference or gear intermesh. (4) Replace bearings as a pair. For example, if one
differential bearing is defective, replace both differen-
tial bearings. If one input shaft bearing is defective,
replace both input shaft bearings. (5) Bearing cones must notbe reused if removed.
(6) Turning torque readings should be obtained
while smoothly rotating in either direction (break-
away reading is not indicative of the true turning
torque). (7) Replace oil baffle, if damaged.
INPUT SHAFT BEARING END PLAY ADJUST-MENT
(1) Using Tool C-4656 with Handle C-4171, press
input shaft front bearing cup slightly forward in case.
Then, using Tool C-4655 with Handle C-4171, press
bearing cup back into case from the front. Properly
position bearing cup, before checking input shaft end
play (see input shaft front bearing cup replace in
Subassembly Recondition section).This step is
not necessary if Tool C-4655 was previously used
to install input shaft front bearing cup in the
case. Also no input shaft shim has been installed
since pressing cup into case. (2) Select a gauging shim which will give 0.025 to
0.254mm (.001 to .010 inch) end play. SUGGESTION:
Measure original shim from input shaft seal retainer and select a shim 0.254mm (.010
inch) thinner than original for the gauging shim.
(3) Install gauging shim on bearing cup and install
input shaft seal retainer.
CAUTION: The input shaft seal retainer is used to
draw the input shaft front bearing cup the proper
distance into the case bore during this step. Alter-
nately tighten input shaft seal retainer bolts until
input shaft seal retainer is bottomed against case.
Tighten bolts to 28 N Im (21 ft. lbs.).
(4) Oil input shaft bearings with SAE 5W-30 engine
oil and install input shaft in case. Install bearing
retainer plate with input shaft rear bearing cup
pressed in and bearing support plate installed. Tighten
all bolts and nuts to 28 N Im (21 ft. lbs.).
(5) Position dial indicator to check input shaft end
play. Apply moderate load, by hand, to input shaft
splines (Fig. 1). Push toward rear while rotating input
shaft back and forth a number of times to settle out
bearings. Zero dial indicator. Pull input shaft toward
the front while rotating input shaft back and forth a
number of times to settle out bearings. Record end play.
(6) The shim required for proper bearing end play is
the total of the gauging shim thickness, plus end play,
minus (constant) end play of 0.051mm (.002 inch).
Combine shims, if necessary, to obtain a shim within
.04mm (.0016 inch) of the required shim (see Shim
Chart for proper shim). (7) Remove input shaft seal retainer and gauging
shim. Install shim(s) selected in step (6). Then reinstall
input shaft seal retainer with a 1/16 inch bead of
MOPAR tGasket Maker, Loctite, or equivalent for a
gasket. Record end play. Observe the CAUTIONin
step (3). Tighten input shaft seal retainer bolts to 28
N Im (21 ft. lbs.).
Fig. 14 Checking Side Gear End Play
Fig. 1 Checking Input Shaft Bearing End Play to De-
termine Shim Thickness
21 - 32 TRANSAXLE Ä
Page 1993 of 2438
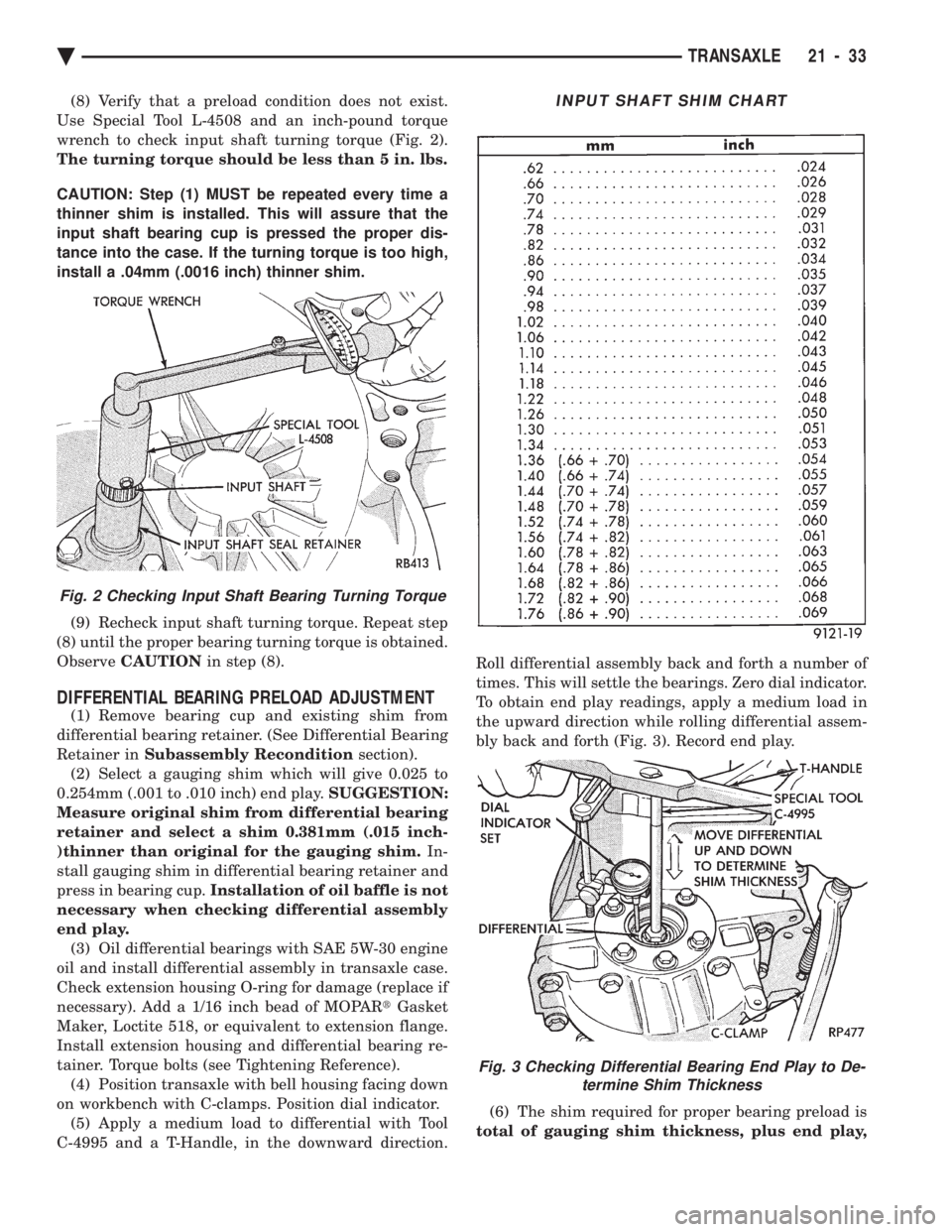
(8) Verify that a preload condition does not exist.
Use Special Tool L-4508 and an inch-pound torque
wrench to check input shaft turning torque (Fig. 2).
The turning torque should be less than 5 in. lbs.
CAUTION: Step (1) MUST be repeated every time a
thinner shim is installed. This will assure that the
input shaft bearing cup is pressed the proper dis-
tance into the case. If the turning torque is too high,
install a .04mm (.0016 inch) thinner shim.
(9) Recheck input shaft turning torque. Repeat step
(8) until the proper bearing turning torque is obtained.
Observe CAUTION in step (8).
DIFFERENTIAL BEARING PRELOAD ADJUSTMENT
(1) Remove bearing cup and existing shim from
differential bearing retainer. (See Differential Bearing
Retainer in Subassembly Recondition section).
(2) Select a gauging shim which will give 0.025 to
0.254mm (.001 to .010 inch) end play. SUGGESTION:
Measure original shim from differential bearing
retainer and select a shim 0.381mm (.015 inch-
)thinner than original for the gauging shim. In-
stall gauging shim in differential bearing retainer and
press in bearing cup. Installation of oil baffle is not
necessary when checking differential assembly
end play. (3) Oil differential bearings with SAE 5W-30 engine
oil and install differential assembly in transaxle case.
Check extension housing O-ring for damage (replace if
necessary). Add a 1/16 inch bead of MOPAR tGasket
Maker, Loctite 518, or equivalent to extension flange.
Install extension housing and differential bearing re-
tainer. Torque bolts (see Tightening Reference). (4) Position transaxle with bell housing facing down
on workbench with C-clamps. Position dial indicator. (5) Apply a medium load to differential with Tool
C-4995 and a T-Handle, in the downward direction. Roll differential assembly back and forth a number of
times. This will settle the bearings. Zero dial indicator.
To obtain end play readings, apply a medium load in
the upward direction while rolling differential assem-
bly back and forth (Fig. 3). Record end play.
(6) The shim required for proper bearing preload is
total of gauging shim thickness, plus end play,
Fig. 2 Checking Input Shaft Bearing Turning Torque
INPUT SHAFT SHIM CHART
Fig. 3 Checking Differential Bearing End Play to De- termine Shim Thickness
Ä TRANSAXLE 21 - 33
Page 1994 of 2438
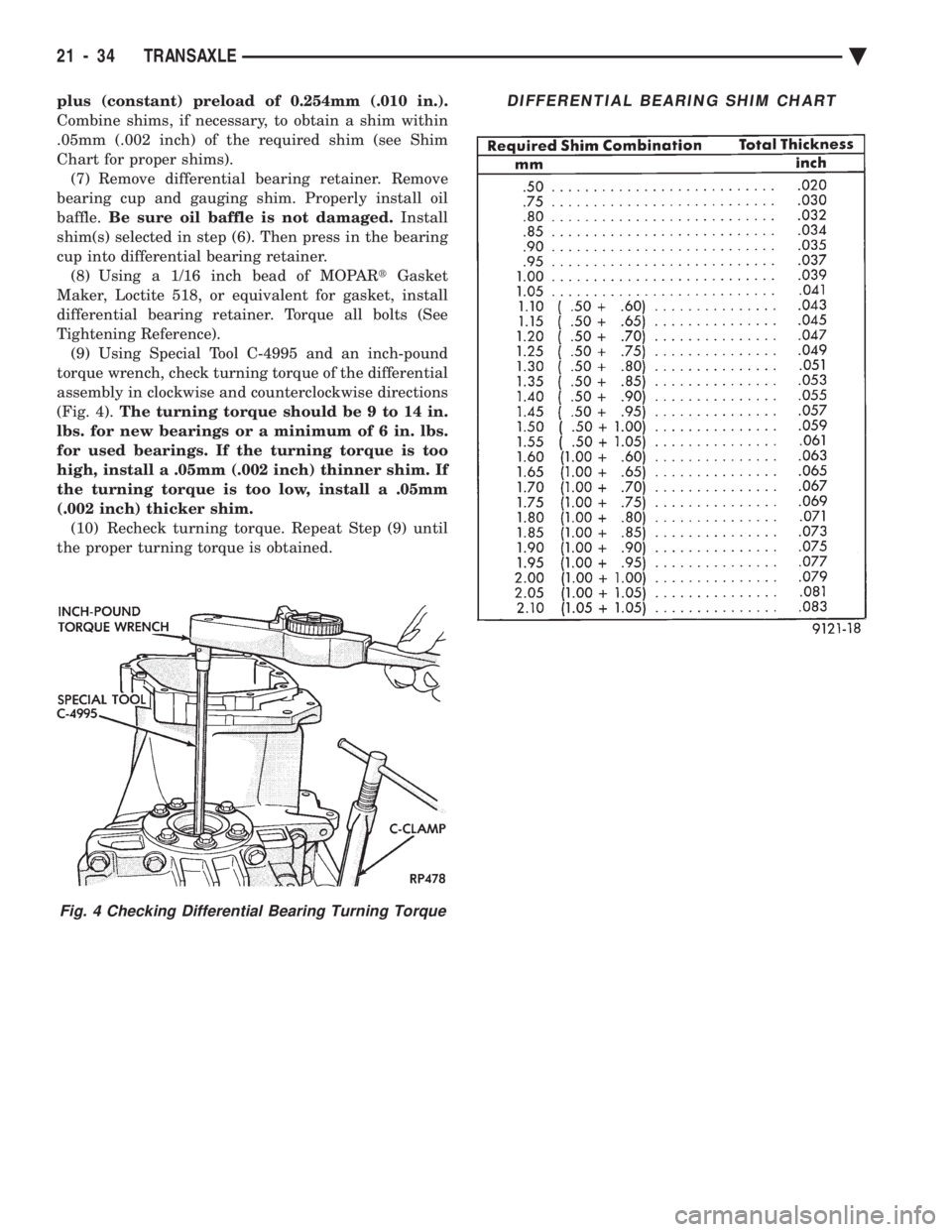
plus (constant) preload of 0.254mm (.010 in.).
Combine shims, if necessary, to obtain a shim within
.05mm (.002 inch) of the required shim (see Shim
Chart for proper shims).(7) Remove differential bearing retainer. Remove
bearing cup and gauging shim. Properly install oil
baffle. Be sure oil baffle is not damaged. Install
shim(s) selected in step (6). Then press in the bearing
cup into differential bearing retainer. (8) Using a 1/16 inch bead of MOPAR tGasket
Maker, Loctite 518, or equivalent for gasket, install
differential bearing retainer. Torque all bolts (See
Tightening Reference). (9) Using Special Tool C-4995 and an inch-pound
torque wrench, check turning torque of the differential
assembly in clockwise and counterclockwise directions
(Fig. 4). The turning torque should be 9 to 14 in.
lbs. for new bearings or a minimum of 6 in. lbs.
for used bearings. If the turning torque is too
high, install a .05mm (.002 inch) thinner shim. If
the turning torque is too low, install a .05mm
(.002 inch) thicker shim. (10) Recheck turning torque. Repeat Step (9) until
the proper turning torque is obtained.
Fig. 4 Checking Differential Bearing Turning Torque
DIFFERENTIAL BEARING SHIM CHART
21 - 34 TRANSAXLE Ä
Page 1995 of 2438
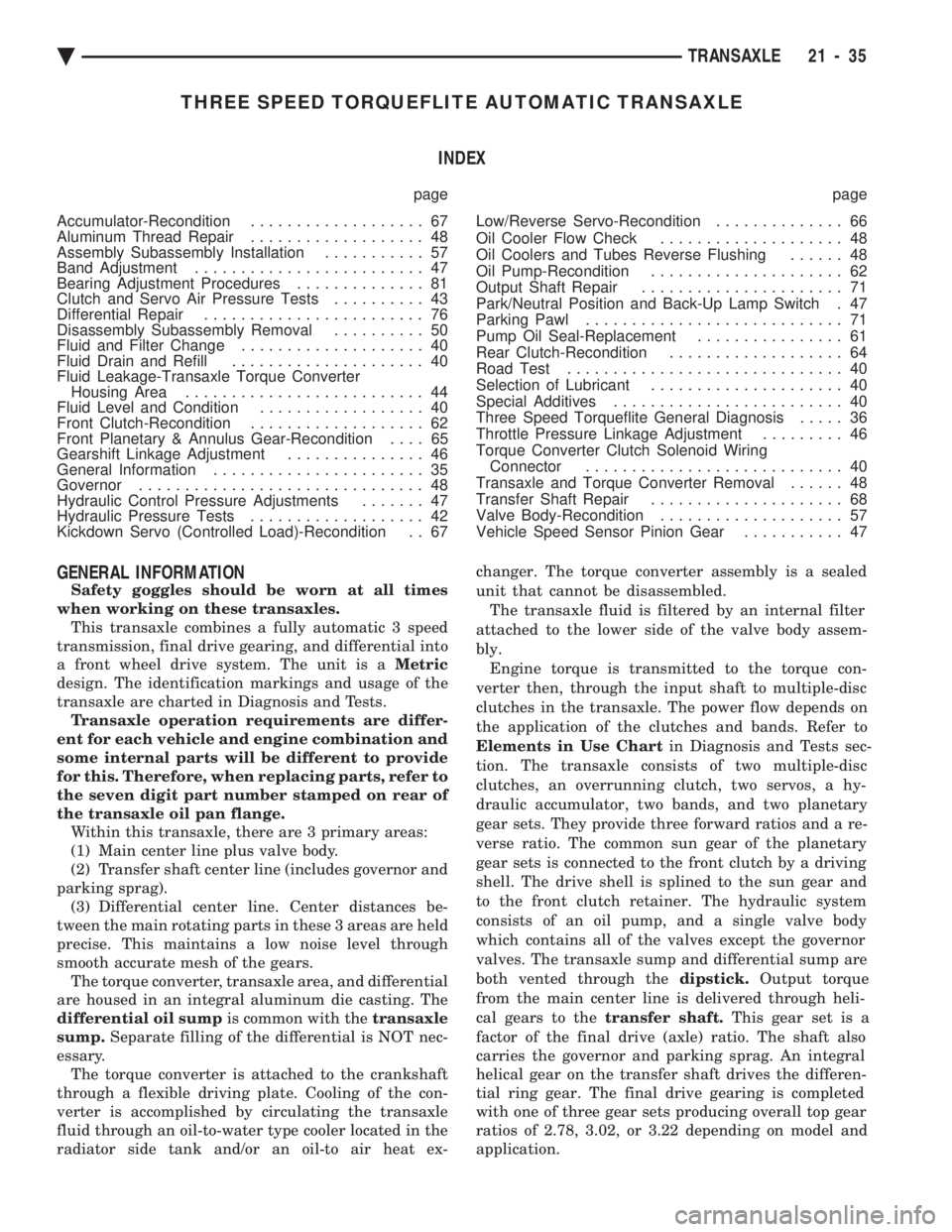
THREE SPEED TORQUEFLITE AUTOMATIC TRANSAXLE INDEX
page page
Accumulator-Recondition ................... 67
Aluminum Thread Repair ................... 48
Assembly Subassembly Installation ........... 57
Band Adjustment ......................... 47
Bearing Adjustment Procedures .............. 81
Clutch and Servo Air Pressure Tests .......... 43
Differential Repair ........................ 76
Disassembly Subassembly Removal .......... 50
Fluid and Filter Change .................... 40
Fluid Drain and Refill ..................... 40
Fluid Leakage-Transaxle Torque Converter Housing Area .......................... 44
Fluid Level and Condition .................. 40
Front Clutch-Recondition ................... 62
Front Planetary & Annulus Gear-Recondition .... 65
Gearshift Linkage Adjustment ............... 46
General Information ....................... 35
Governor ............................... 48
Hydraulic Control Pressure Adjustments ....... 47
Hydraulic Pressure Tests ................... 42
Kickdown Servo (Controlled Load)-Recondition . . 67 Low/Reverse Servo-Recondition
.............. 66
Oil Cooler Flow Check .................... 48
Oil Coolers and Tubes Reverse Flushing ...... 48
Oil Pump-Recondition ..................... 62
Output Shaft Repair ...................... 71
Park/Neutral Position and Back-Up Lamp Switch . 47
Parking Pawl ............................ 71
Pump Oil Seal-Replacement ................ 61
Rear Clutch-Recondition ................... 64
Road Test .............................. 40
Selection of Lubricant ..................... 40
Special Additives ......................... 40
Three Speed Torqueflite General Diagnosis ..... 36
Throttle Pressure Linkage Adjustment ......... 46
Torque Converter Clutch Solenoid Wiring Connector ............................ 40
Transaxle and Torque Converter Removal ...... 48
Transfer Shaft Repair ..................... 68
Valve Body-Recondition .................... 57
Vehicle Speed Sensor Pinion Gear ........... 47
GENERAL INFORMATION
Safety goggles should be worn at all times
when working on these transaxles. This transaxle combines a fully automatic 3 speed
transmission, final drive gearing, and differential into
a front wheel drive system. The unit is a Metric
design. The identification markings and usage of the
transaxle are charted in Diagnosis and Tests. Transaxle operation requirements are differ-
ent for each vehicle and engine combination and
some internal parts will be different to provide
for this. Therefore, when replacing parts, refer to
the seven digit part number stamped on rear of
the transaxle oil pan flange. Within this transaxle, there are 3 primary areas:
(1) Main center line plus valve body.
(2) Transfer shaft center line (includes governor and
parking sprag). (3) Differential center line. Center distances be-
tween the main rotating parts in these 3 areas are held
precise. This maintains a low noise level through
smooth accurate mesh of the gears. The torque converter, transaxle area, and differential
are housed in an integral aluminum die casting. The
differential oil sump is common with thetransaxle
sump. Separate filling of the differential is NOT nec-
essary. The torque converter is attached to the crankshaft
through a flexible driving plate. Cooling of the con-
verter is accomplished by circulating the transaxle
fluid through an oil-to-water type cooler located in the
radiator side tank and/or an oil-to air heat ex- changer. The torque converter assembly is a sealed
unit that cannot be disassembled.
The transaxle fluid is filtered by an internal filter
attached to the lower side of the valve body assem-
bly. Engine torque is transmitted to the torque con-
verter then, through the input shaft to multiple-disc
clutches in the transaxle. The power flow depends on
the application of the clutches and bands. Refer to
Elements in Use Chart in Diagnosis and Tests sec-
tion. The transaxle consists of two multiple-disc
clutches, an overrunning clutch, two servos, a hy-
draulic accumulator, two bands, and two planetary
gear sets. They provide three forward ratios and a re-
verse ratio. The common sun gear of the planetary
gear sets is connected to the front clutch by a driving
shell. The drive shell is splined to the sun gear and
to the front clutch retainer. The hydraulic system
consists of an oil pump, and a single valve body
which contains all of the valves except the governor
valves. The transaxle sump and differential sump are
both vented through the dipstick.Output torque
from the main center line is delivered through heli-
cal gears to the transfer shaft.This gear set is a
factor of the final drive (axle) ratio. The shaft also
carries the governor and parking sprag. An integral
helical gear on the transfer shaft drives the differen-
tial ring gear. The final drive gearing is completed
with one of three gear sets producing overall top gear
ratios of 2.78, 3.02, or 3.22 depending on model and
application.
Ä TRANSAXLE 21 - 35
Page 1996 of 2438
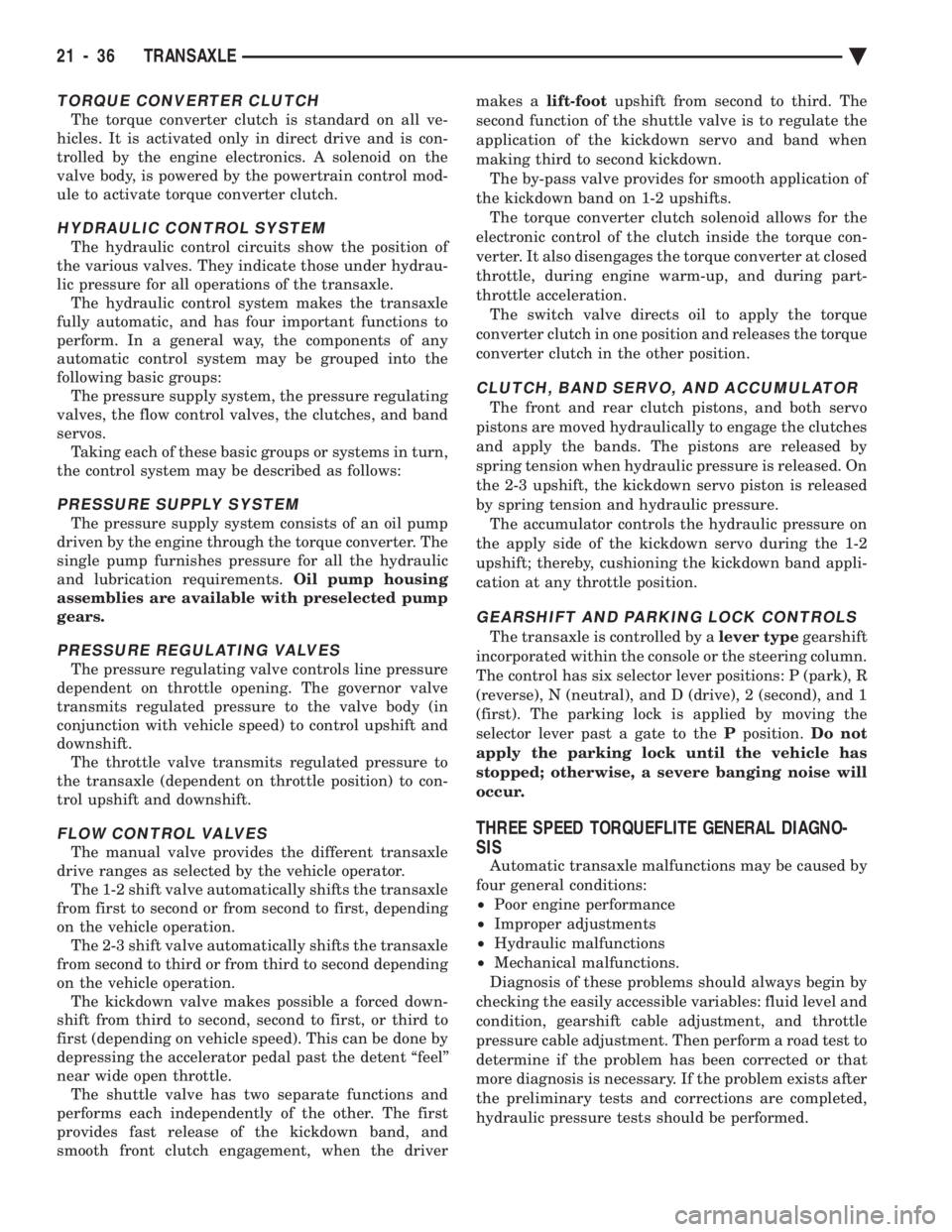
TORQUE CONVERTER CLUTCH
The torque converter clutch is standard on all ve-
hicles. It is activated only in direct drive and is con-
trolled by the engine electronics. A solenoid on the
valve body, is powered by the powertrain control mod-
ule to activate torque converter clutch.
HYDRAULIC CONTROL SYSTEM
The hydraulic control circuits show the position of
the various valves. They indicate those under hydrau-
lic pressure for all operations of the transaxle. The hydraulic control system makes the transaxle
fully automatic, and has four important functions to
perform. In a general way, the components of any
automatic control system may be grouped into the
following basic groups: The pressure supply system, the pressure regulating
valves, the flow control valves, the clutches, and band
servos. Taking each of these basic groups or systems in turn,
the control system may be described as follows:
PRESSURE SUPPLY SYSTEM
The pressure supply system consists of an oil pump
driven by the engine through the torque converter. The
single pump furnishes pressure for all the hydraulic
and lubrication requirements. Oil pump housing
assemblies are available with preselected pump
gears.
PRESSURE REGULATING VALVES
The pressure regulating valve controls line pressure
dependent on throttle opening. The governor valve
transmits regulated pressure to the valve body (in
conjunction with vehicle speed) to control upshift and
downshift. The throttle valve transmits regulated pressure to
the transaxle (dependent on throttle position) to con-
trol upshift and downshift.
FLOW CONTROL VALVES
The manual valve provides the different transaxle
drive ranges as selected by the vehicle operator. The 1-2 shift valve automatically shifts the transaxle
from first to second or from second to first, depending
on the vehicle operation. The 2-3 shift valve automatically shifts the transaxle
from second to third or from third to second depending
on the vehicle operation. The kickdown valve makes possible a forced down-
shift from third to second, second to first, or third to
first (depending on vehicle speed). This can be done by
depressing the accelerator pedal past the detent ``feel''
near wide open throttle. The shuttle valve has two separate functions and
performs each independently of the other. The first
provides fast release of the kickdown band, and
smooth front clutch engagement, when the driver makes a
lift-footupshift from second to third. The
second function of the shuttle valve is to regulate the
application of the kickdown servo and band when
making third to second kickdown. The by-pass valve provides for smooth application of
the kickdown band on 1-2 upshifts. The torque converter clutch solenoid allows for the
electronic control of the clutch inside the torque con-
verter. It also disengages the torque converter at closed
throttle, during engine warm-up, and during part-
throttle acceleration. The switch valve directs oil to apply the torque
converter clutch in one position and releases the torque
converter clutch in the other position.
CLUTCH, BAND SERVO, AND ACCUMULATOR
The front and rear clutch pistons, and both servo
pistons are moved hydraulically to engage the clutches
and apply the bands. The pistons are released by
spring tension when hydraulic pressure is released. On
the 2-3 upshift, the kickdown servo piston is released
by spring tension and hydraulic pressure. The accumulator controls the hydraulic pressure on
the apply side of the kickdown servo during the 1-2
upshift; thereby, cushioning the kickdown band appli-
cation at any throttle position.
GEARSHIFT AND PARKING LOCK CONTROLS
The transaxle is controlled by a lever typegearshift
incorporated within the console or the steering column.
The control has six selector lever positions: P (park), R
(reverse), N (neutral), and D (drive), 2 (second), and 1
(first). The parking lock is applied by moving the
selector lever past a gate to the Pposition. Do not
apply the parking lock until the vehicle has
stopped; otherwise, a severe banging noise will
occur.
THREE SPEED TORQUEFLITE GENERAL DIAGNO-
SIS
Automatic transaxle malfunctions may be caused by
four general conditions:
² Poor engine performance
² Improper adjustments
² Hydraulic malfunctions
² Mechanical malfunctions.
Diagnosis of these problems should always begin by
checking the easily accessible variables: fluid level and
condition, gearshift cable adjustment, and throttle
pressure cable adjustment. Then perform a road test to
determine if the problem has been corrected or that
more diagnosis is necessary. If the problem exists after
the preliminary tests and corrections are completed,
hydraulic pressure tests should be performed.
21 - 36 TRANSAXLE Ä
Page 1997 of 2438
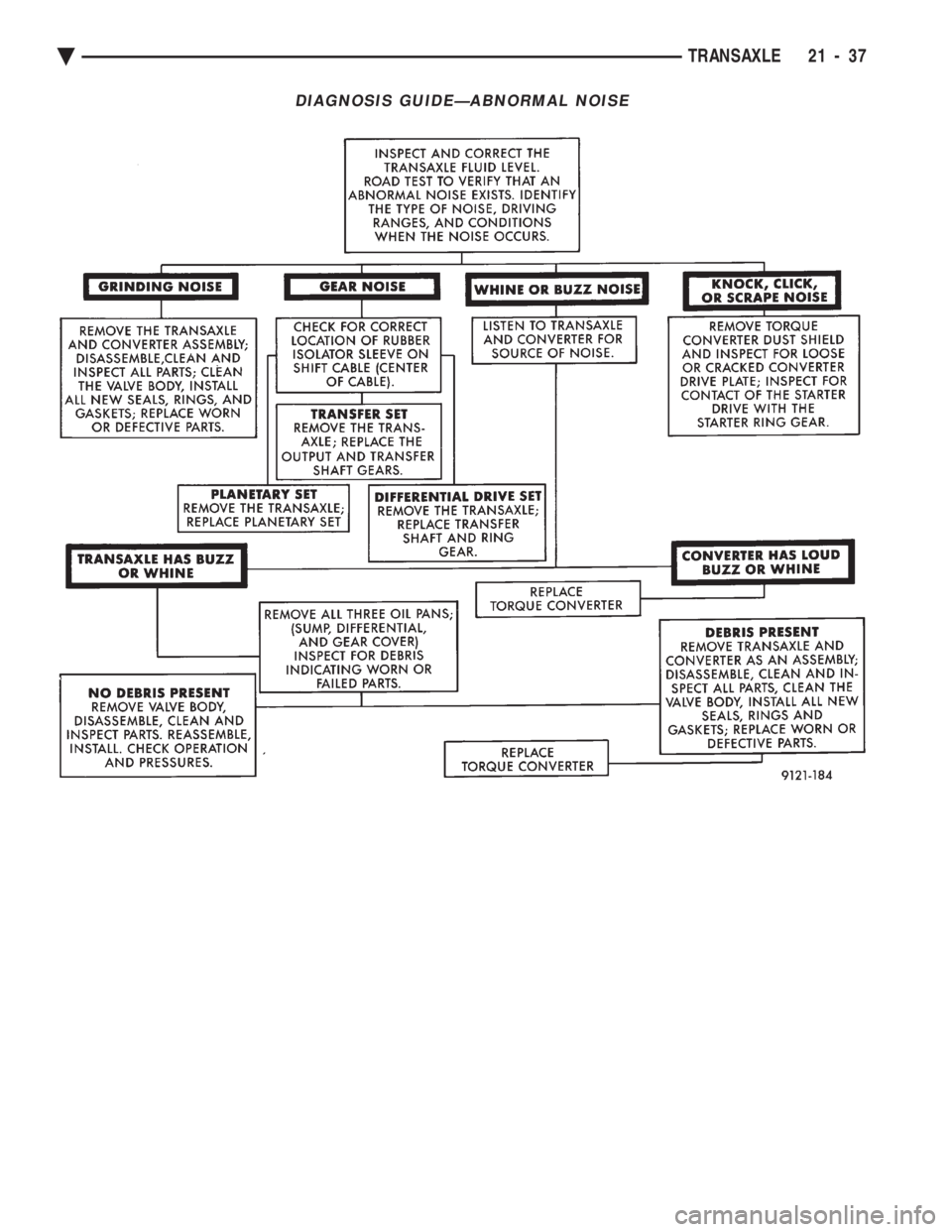
DIAGNOSIS GUIDEÐABNORMAL NOISE
Ä TRANSAXLE 21 - 37
Page 1998 of 2438
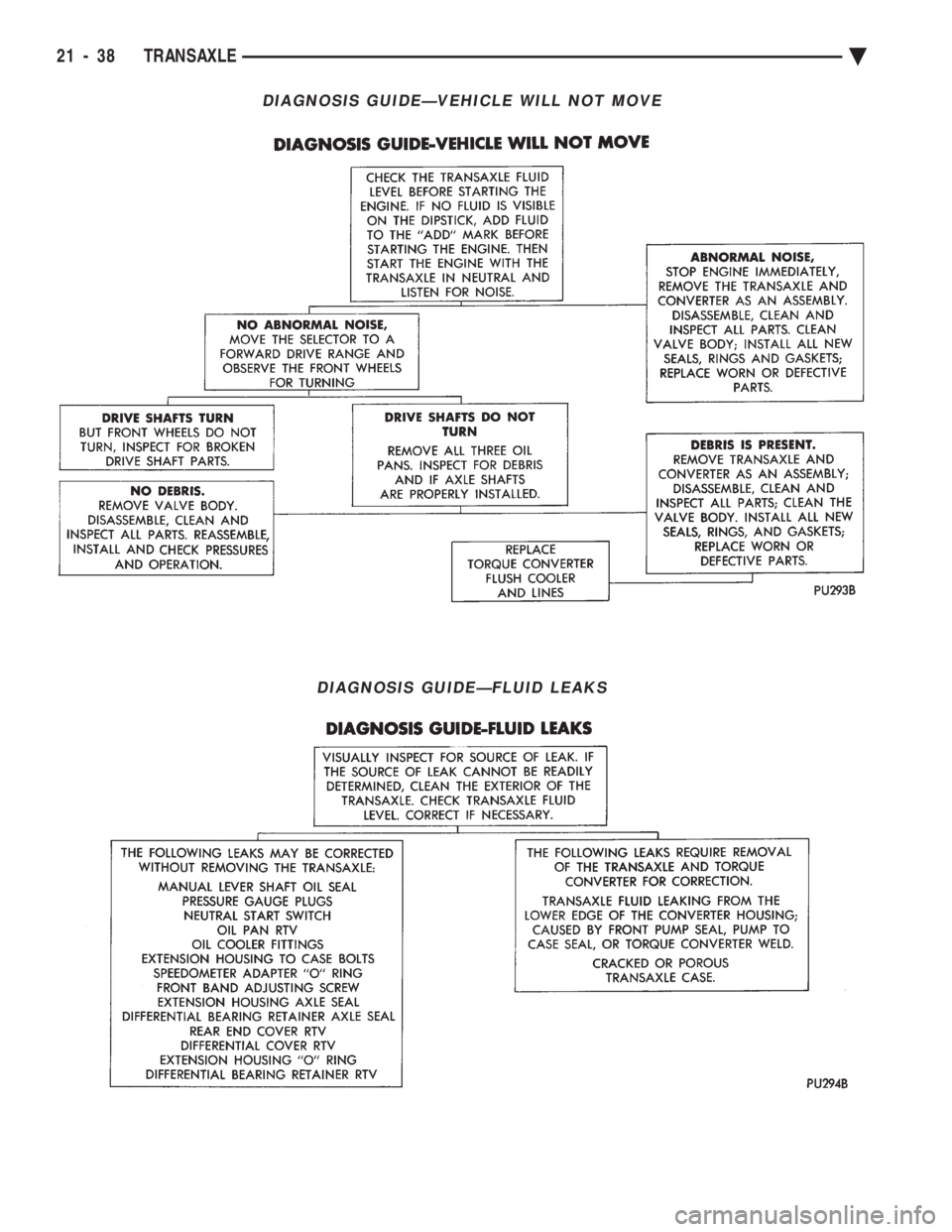
DIAGNOSIS GUIDEÐVEHICLE WILL NOT MOVE
DIAGNOSIS GUIDEÐFLUID LEAKS
21 - 38 TRANSAXLE Ä
Page 1999 of 2438
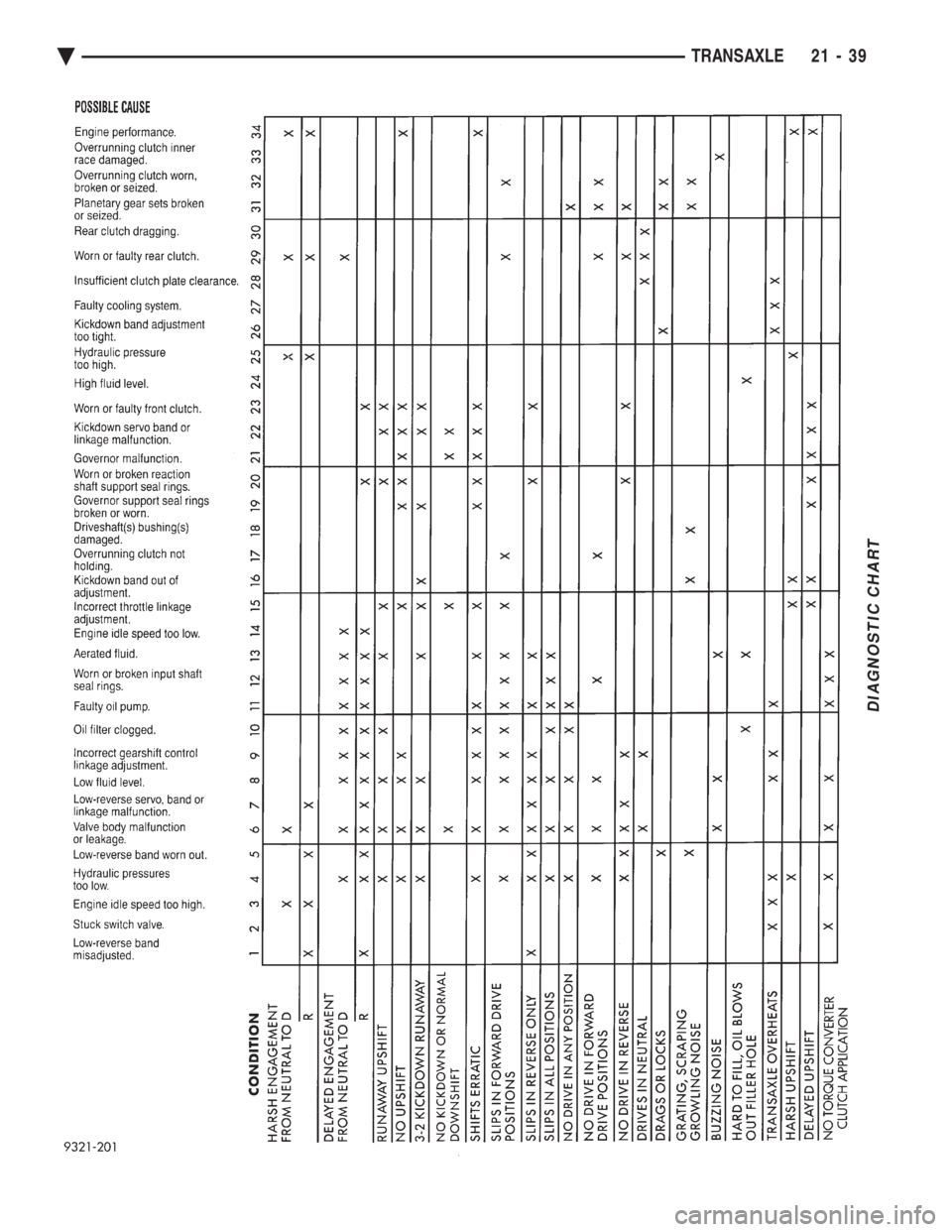
DIAGNOSTIC CHART
Ä TRANSAXLE 21 - 39
Page 2000 of 2438
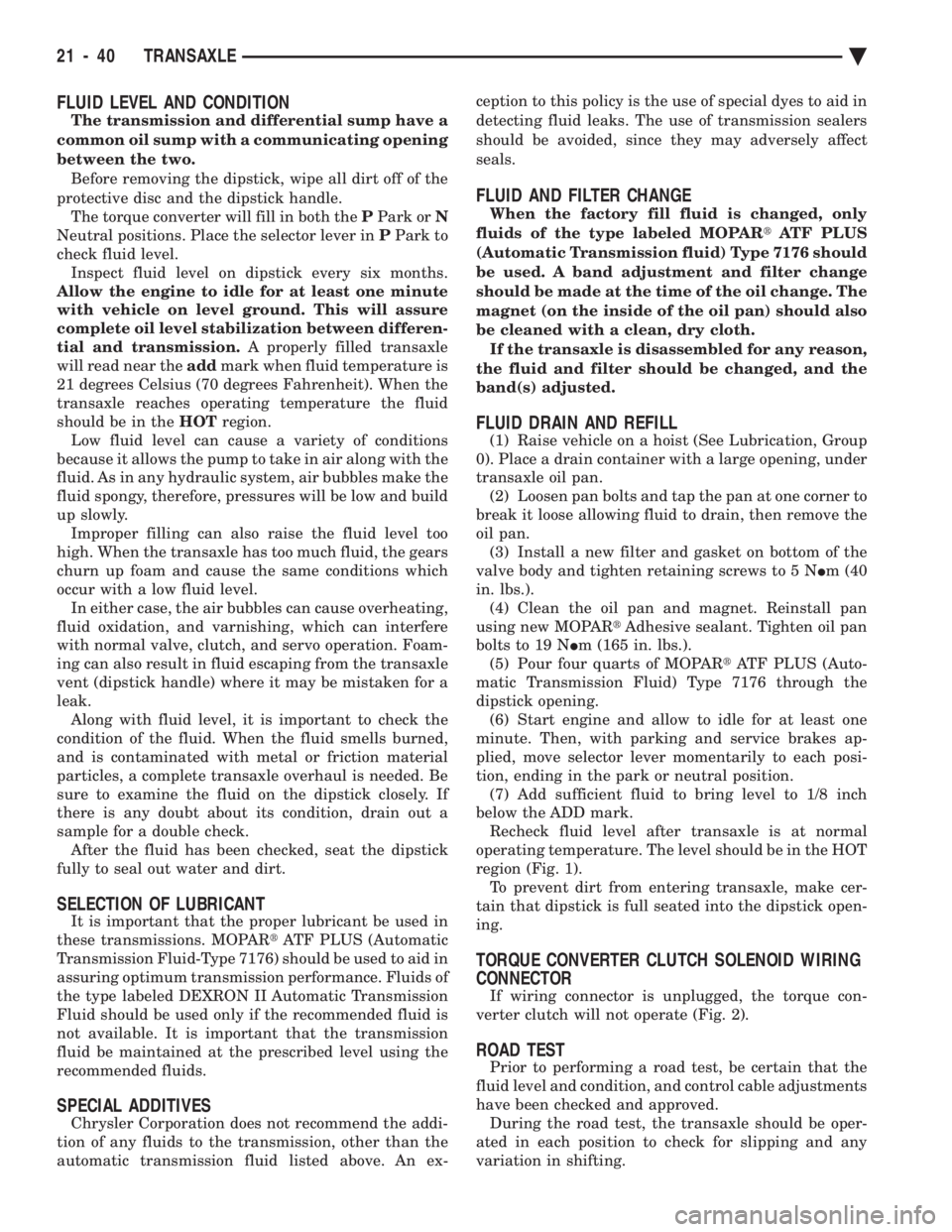
FLUID LEVEL AND CONDITION
The transmission and differential sump have a
common oil sump with a communicating opening
between the two. Before removing the dipstick, wipe all dirt off of the
protective disc and the dipstick handle. The torque converter will fill in both the PPark or N
Neutral positions. Place the selector lever in PPark to
check fluid level. Inspect fluid level on dipstick every six months.
Allow the engine to idle for at least one minute
with vehicle on level ground. This will assure
complete oil level stabilization between differen-
tial and transmission. A properly filled transaxle
will read near the addmark when fluid temperature is
21 degrees Celsius (70 degrees Fahrenheit). When the
transaxle reaches operating temperature the fluid
should be in the HOTregion.
Low fluid level can cause a variety of conditions
because it allows the pump to take in air along with the
fluid. As in any hydraulic system, air bubbles make the
fluid spongy, therefore, pressures will be low and build
up slowly. Improper filling can also raise the fluid level too
high. When the transaxle has too much fluid, the gears
churn up foam and cause the same conditions which
occur with a low fluid level. In either case, the air bubbles can cause overheating,
fluid oxidation, and varnishing, which can interfere
with normal valve, clutch, and servo operation. Foam-
ing can also result in fluid escaping from the transaxle
vent (dipstick handle) where it may be mistaken for a
leak. Along with fluid level, it is important to check the
condition of the fluid. When the fluid smells burned,
and is contaminated with metal or friction material
particles, a complete transaxle overhaul is needed. Be
sure to examine the fluid on the dipstick closely. If
there is any doubt about its condition, drain out a
sample for a double check. After the fluid has been checked, seat the dipstick
fully to seal out water and dirt.
SELECTION OF LUBRICANT
It is important that the proper lubricant be used in
these transmissions. MOPAR tATF PLUS (Automatic
Transmission Fluid-Type 7176) should be used to aid in
assuring optimum transmission performance. Fluids of
the type labeled DEXRON II Automatic Transmission
Fluid should be used only if the recommended fluid is
not available. It is important that the transmission
fluid be maintained at the prescribed level using the
recommended fluids.
SPECIAL ADDITIVES
Chrysler Corporation does not recommend the addi-
tion of any fluids to the transmission, other than the
automatic transmission fluid listed above. An ex- ception to this policy is the use of special dyes to aid in
detecting fluid leaks. The use of transmission sealers
should be avoided, since they may adversely affect
seals.
FLUID AND FILTER CHANGE
When the factory fill fluid is changed, only
fluids of the type labeled MOPAR tATF PLUS
(Automatic Transmission fluid) Type 7176 should
be used. A band adjustment and filter change
should be made at the time of the oil change. The
magnet (on the inside of the oil pan) should also
be cleaned with a clean, dry cloth. If the transaxle is disassembled for any reason,
the fluid and filter should be changed, and the
band(s) adjusted.
FLUID DRAIN AND REFILL
(1) Raise vehicle on a hoist (See Lubrication, Group
0). Place a drain container with a large opening, under
transaxle oil pan. (2) Loosen pan bolts and tap the pan at one corner to
break it loose allowing fluid to drain, then remove the
oil pan. (3) Install a new filter and gasket on bottom of the
valve body and tighten retaining screws to 5 N Im (40
in. lbs.). (4) Clean the oil pan and magnet. Reinstall pan
using new MOPAR tAdhesive sealant. Tighten oil pan
bolts to 19 N Im (165 in. lbs.).
(5) Pour four quarts of MOPAR tATF PLUS (Auto-
matic Transmission Fluid) Type 7176 through the
dipstick opening. (6) Start engine and allow to idle for at least one
minute. Then, with parking and service brakes ap-
plied, move selector lever momentarily to each posi-
tion, ending in the park or neutral position. (7) Add sufficient fluid to bring level to 1/8 inch
below the ADD mark. Recheck fluid level after transaxle is at normal
operating temperature. The level should be in the HOT
region (Fig. 1). To prevent dirt from entering transaxle, make cer-
tain that dipstick is full seated into the dipstick open-
ing.
TORQUE CONVERTER CLUTCH SOLENOID WIRING
CONNECTOR
If wiring connector is unplugged, the torque con-
verter clutch will not operate (Fig. 2).
ROAD TEST
Prior to performing a road test, be certain that the
fluid level and condition, and control cable adjustments
have been checked and approved. During the road test, the transaxle should be oper-
ated in each position to check for slipping and any
variation in shifting.
21 - 40 TRANSAXLE Ä