CHEVROLET PLYMOUTH ACCLAIM 1993 Service Manual
Manufacturer: CHEVROLET, Model Year: 1993, Model line: PLYMOUTH ACCLAIM, Model: CHEVROLET PLYMOUTH ACCLAIM 1993Pages: 2438, PDF Size: 74.98 MB
Page 2331 of 2438
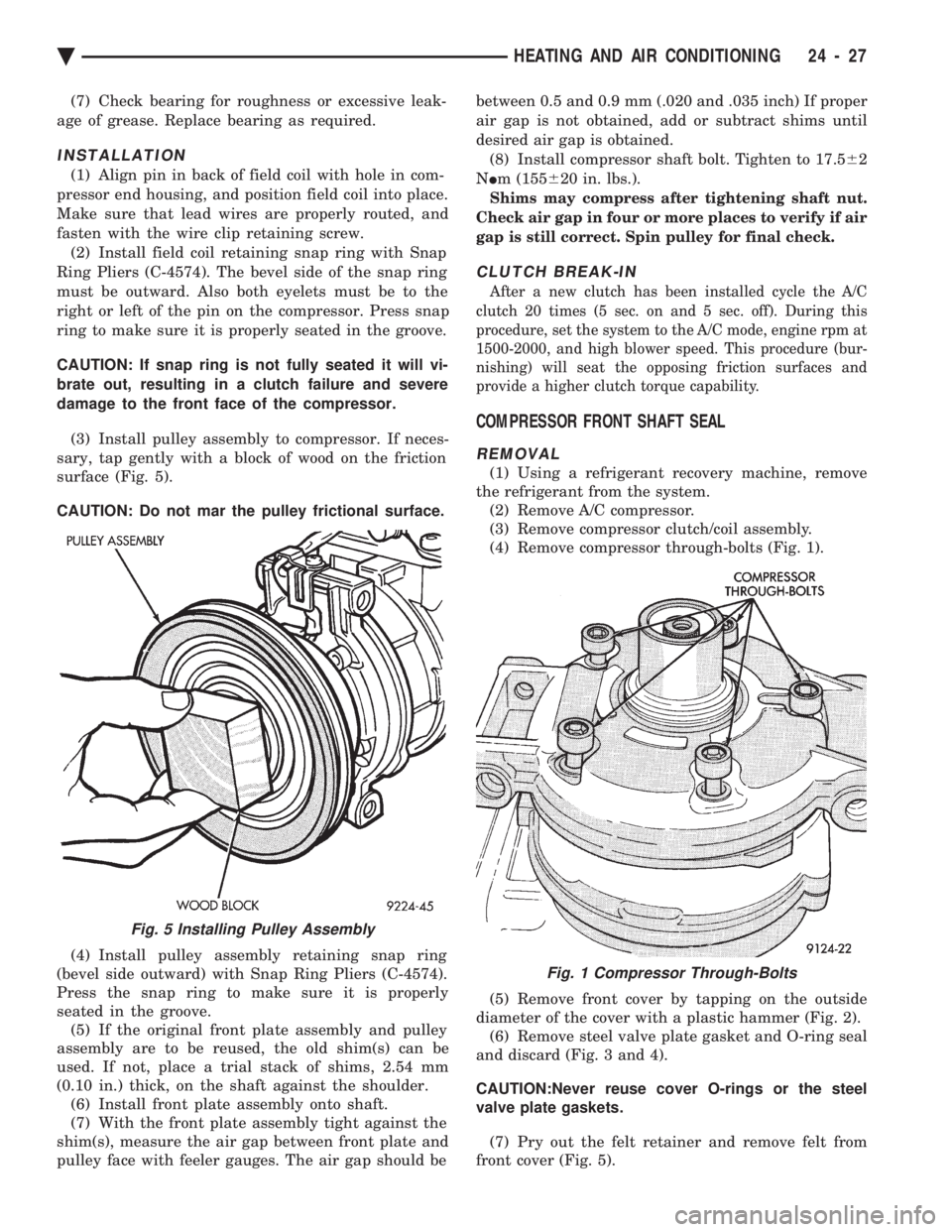
(7) Check bearing for roughness or excessive leak-
age of grease. Replace bearing as required.
INSTALLATION
(1) Align pin in back of field coil with hole in com-
pressor end housing, and position field coil into place.
Make sure that lead wires are properly routed, and
fasten with the wire clip retaining screw. (2) Install field coil retaining snap ring with Snap
Ring Pliers (C-4574). The bevel side of the snap ring
must be outward. Also both eyelets must be to the
right or left of the pin on the compressor. Press snap
ring to make sure it is properly seated in the groove.
CAUTION: If snap ring is not fully seated it will vi-
brate out, resulting in a clutch failure and severe
damage to the front face of the compressor.
(3) Install pulley assembly to compressor. If neces-
sary, tap gently with a block of wood on the friction
surface (Fig. 5).
CAUTION: Do not mar the pulley frictional surface.
(4) Install pulley assembly retaining snap ring
(bevel side outward) with Snap Ring Pliers (C-4574).
Press the snap ring to make sure it is properly
seated in the groove. (5) If the original front plate assembly and pulley
assembly are to be reused, the old shim(s) can be
used. If not, place a trial stack of shims, 2.54 mm
(0.10 in.) thick, on the shaft against the shoulder. (6) Install front plate assembly onto shaft.
(7) With the front plate assembly tight against the
shim(s), measure the air gap between front plate and
pulley face with feeler gauges. The air gap should be between 0.5 and 0.9 mm (.020 and .035 inch) If proper
air gap is not obtained, add or subtract shims until
desired air gap is obtained.
(8) Install compressor shaft bolt. Tighten to 17.5 62
N Im (155 620 in. lbs.).
Shims may compress after tightening shaft nut.
Check air gap in four or more places to verify if air
gap is still correct. Spin pulley for final check.
CLUTCH BREAK-IN
After a new clutch has been installed cycle the A/C
clutch 20 times (5 sec. on and 5 sec. off). During this
procedure, set the system to the A/C mode, engine rpm at
1500-2000, and high blower speed. This procedure (bur-
nishing) will seat the opposing friction surfaces and
provide a higher clutch torque capability.
COMPRESSOR FRONT SHAFT SEAL
REMOVAL
(1) Using a refrigerant recovery machine, remove
the refrigerant from the system. (2) Remove A/C compressor.
(3) Remove compressor clutch/coil assembly.
(4) Remove compressor through-bolts (Fig. 1).
(5) Remove front cover by tapping on the outside
diameter of the cover with a plastic hammer (Fig. 2). (6) Remove steel valve plate gasket and O-ring seal
and discard (Fig. 3 and 4).
CAUTION:Never reuse cover O-rings or the steel
valve plate gaskets.
(7) Pry out the felt retainer and remove felt from
front cover (Fig. 5).
Fig. 5 Installing Pulley Assembly
Fig. 1 Compressor Through-Bolts
Ä HEATING AND AIR CONDITIONING 24 - 27
Page 2332 of 2438
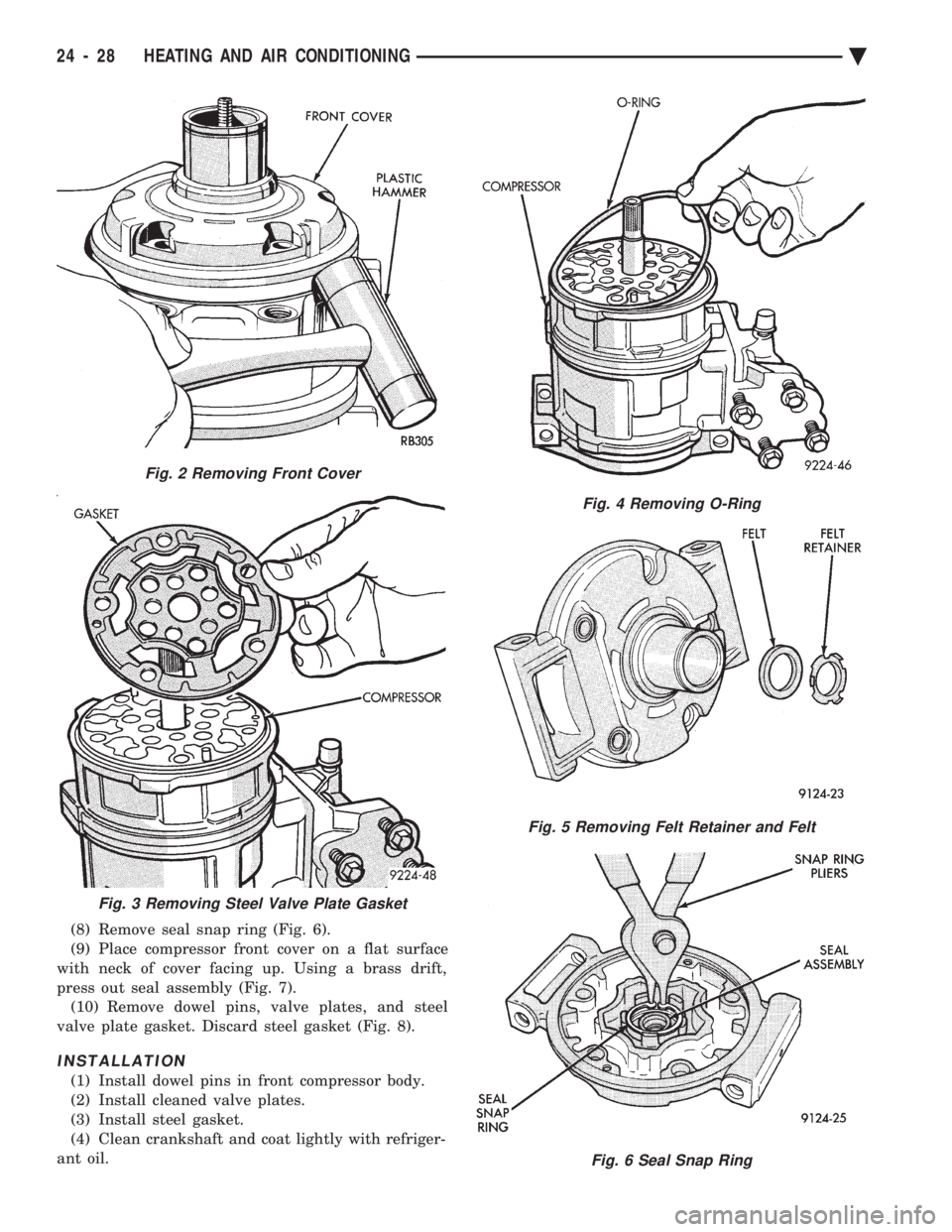
(8) Remove seal snap ring (Fig. 6).
(9) Place compressor front cover on a flat surface
with neck of cover facing up. Using a brass drift,
press out seal assembly (Fig. 7). (10) Remove dowel pins, valve plates, and steel
valve plate gasket. Discard steel gasket (Fig. 8).
INSTALLATION
(1) Install dowel pins in front compressor body.
(2) Install cleaned valve plates.
(3) Install steel gasket.
(4) Clean crankshaft and coat lightly with refriger-
ant oil.
Fig. 2 Removing Front Cover
Fig. 4 Removing O-Ring
Fig. 5 Removing Felt Retainer and Felt
Fig. 6 Seal Snap Ring
Fig. 3 Removing Steel Valve Plate Gasket
24 - 28 HEATING AND AIR CONDITIONING Ä
Page 2333 of 2438
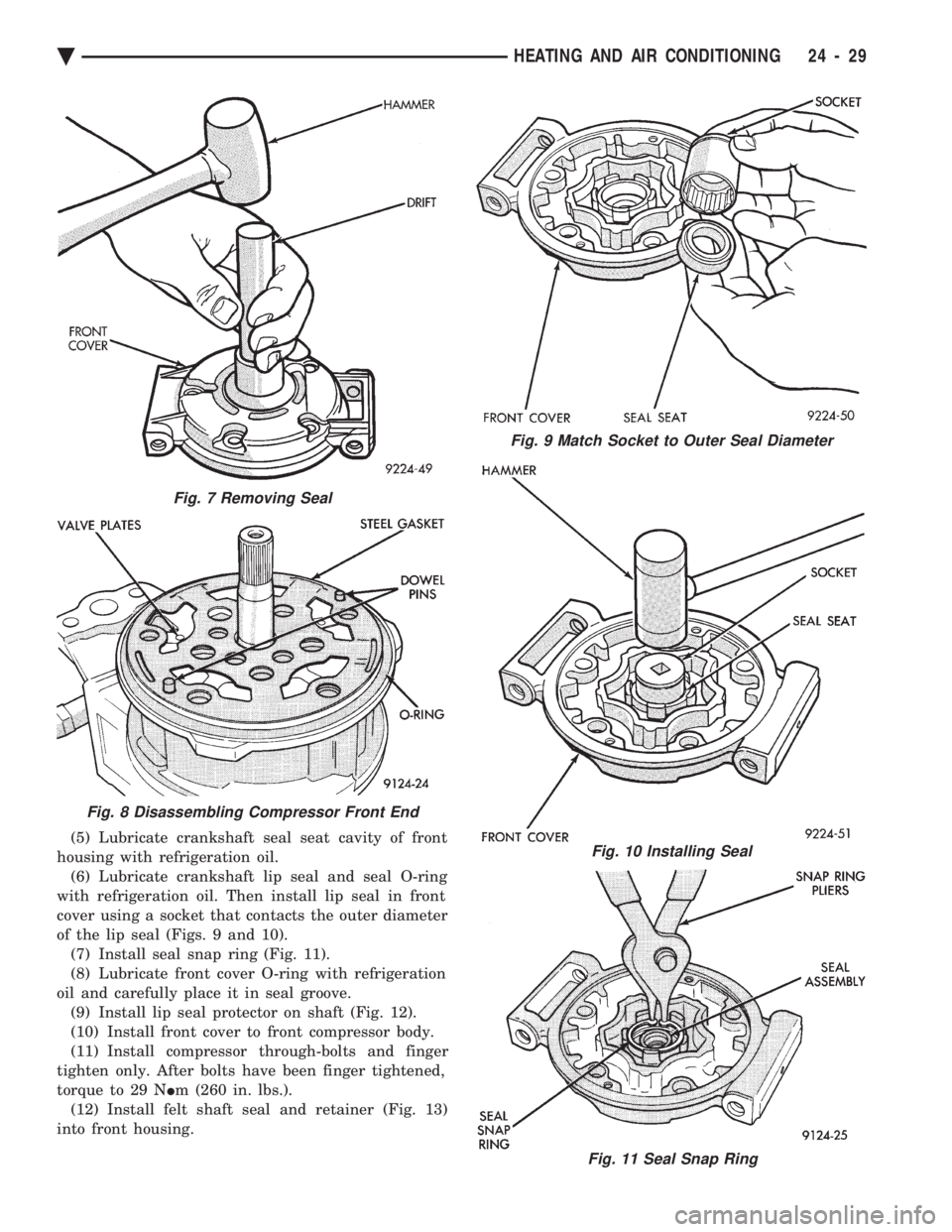
(5) Lubricate crankshaft seal seat cavity of front
housing with refrigeration oil. (6) Lubricate crankshaft lip seal and seal O-ring
with refrigeration oil. Then install lip seal in front
cover using a socket that contacts the outer diameter
of the lip seal (Figs. 9 and 10). (7) Install seal snap ring (Fig. 11).
(8) Lubricate front cover O-ring with refrigeration
oil and carefully place it in seal groove. (9) Install lip seal protector on shaft (Fig. 12).
(10) Install front cover to front compressor body.
(11) Install compressor through-bolts and finger
tighten only. After bolts have been finger tightened,
torque to 29 N Im (260 in. lbs.).
(12) Install felt shaft seal and retainer (Fig. 13)
into front housing.
Fig. 9 Match Socket to Outer Seal Diameter
Fig. 10 Installing Seal
Fig. 11 Seal Snap Ring
Fig. 7 Removing Seal
Fig. 8 Disassembling Compressor Front End
Ä HEATING AND AIR CONDITIONING 24 - 29
Page 2334 of 2438
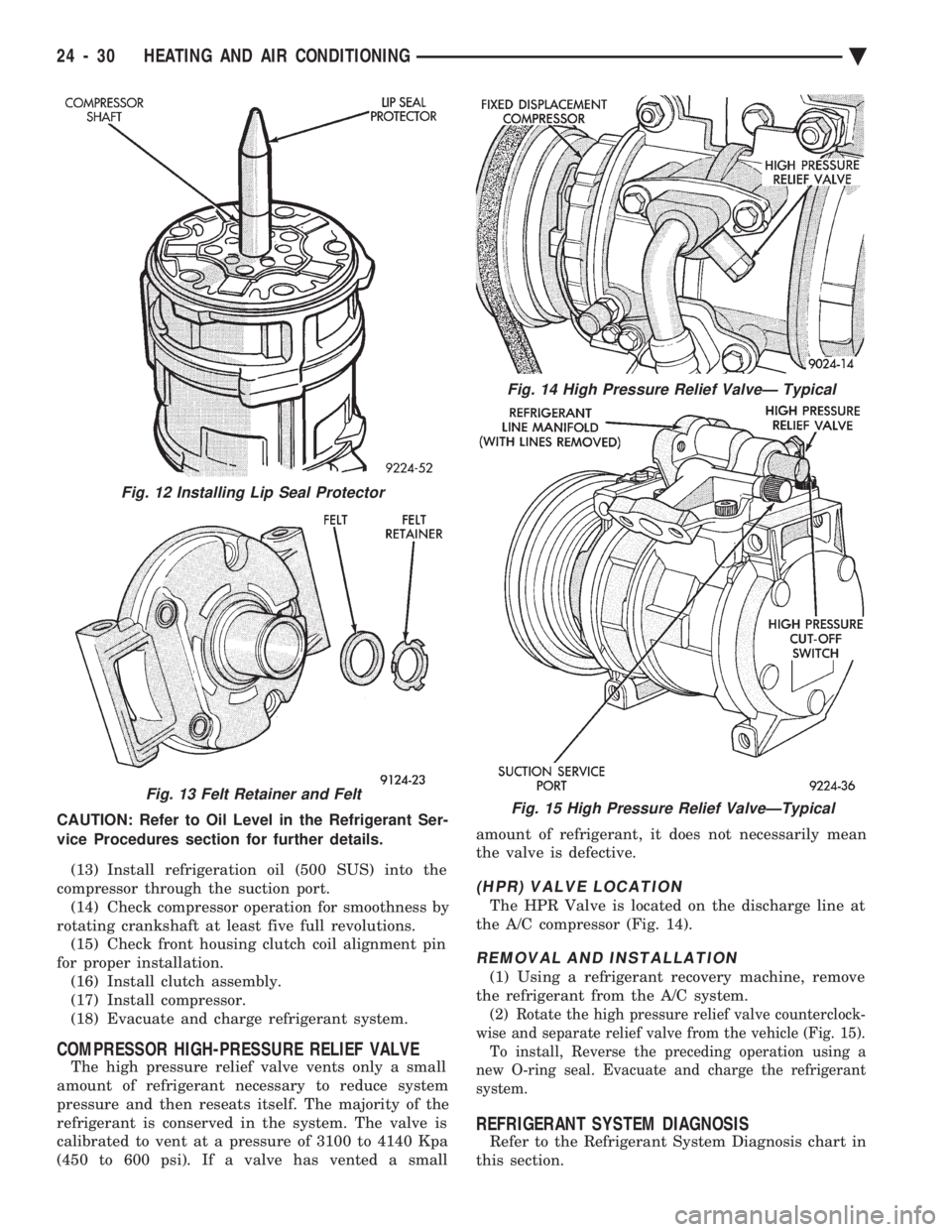
CAUTION: Refer to Oil Level in the Refrigerant Ser-
vice Procedures section for further details. (13) Install refrigeration oil (500 SUS) into the
compressor through the suction port. (14) Check compressor operation for smoothness by
rotating crankshaft at least five full revolutions. (15) Check front housing clutch coil alignment pin
for proper installation. (16) Install clutch assembly.
(17) Install compressor.
(18) Evacuate and charge refrigerant system.
COMPRESSOR HIGH-PRESSURE RELIEF VALVE
The high pressure relief valve vents only a small
amount of refrigerant necessary to reduce system
pressure and then reseats itself. The majority of the
refrigerant is conserved in the system. The valve is
calibrated to vent at a pressure of 3100 to 4140 Kpa
(450 to 600 psi). If a valve has vented a small amount of refrigerant, it does not necessarily mean
the valve is defective.
(HPR) VALVE LOCATION
The HPR Valve is located on the discharge line at
the A/C compressor (Fig. 14).
REMOVAL AND INSTALLATION
(1) Using a refrigerant recovery machine, remove
the refrigerant from the A/C system.
(2) Rotate the high pressure relief valve counterclock-
wise and separate relief valve from the vehicle (Fig. 15). To install, Reverse the preceding operation using a
new O-ring seal. Evacuate and charge the refrigerant
system.
REFRIGERANT SYSTEM DIAGNOSIS
Refer to the Refrigerant System Diagnosis chart in
this section.
Fig. 13 Felt Retainer and Felt
Fig. 14 High Pressure Relief ValveÐ Typical
Fig. 15 High Pressure Relief ValveÐTypical
Fig. 12 Installing Lip Seal Protector
24 - 30 HEATING AND AIR CONDITIONING Ä
Page 2335 of 2438
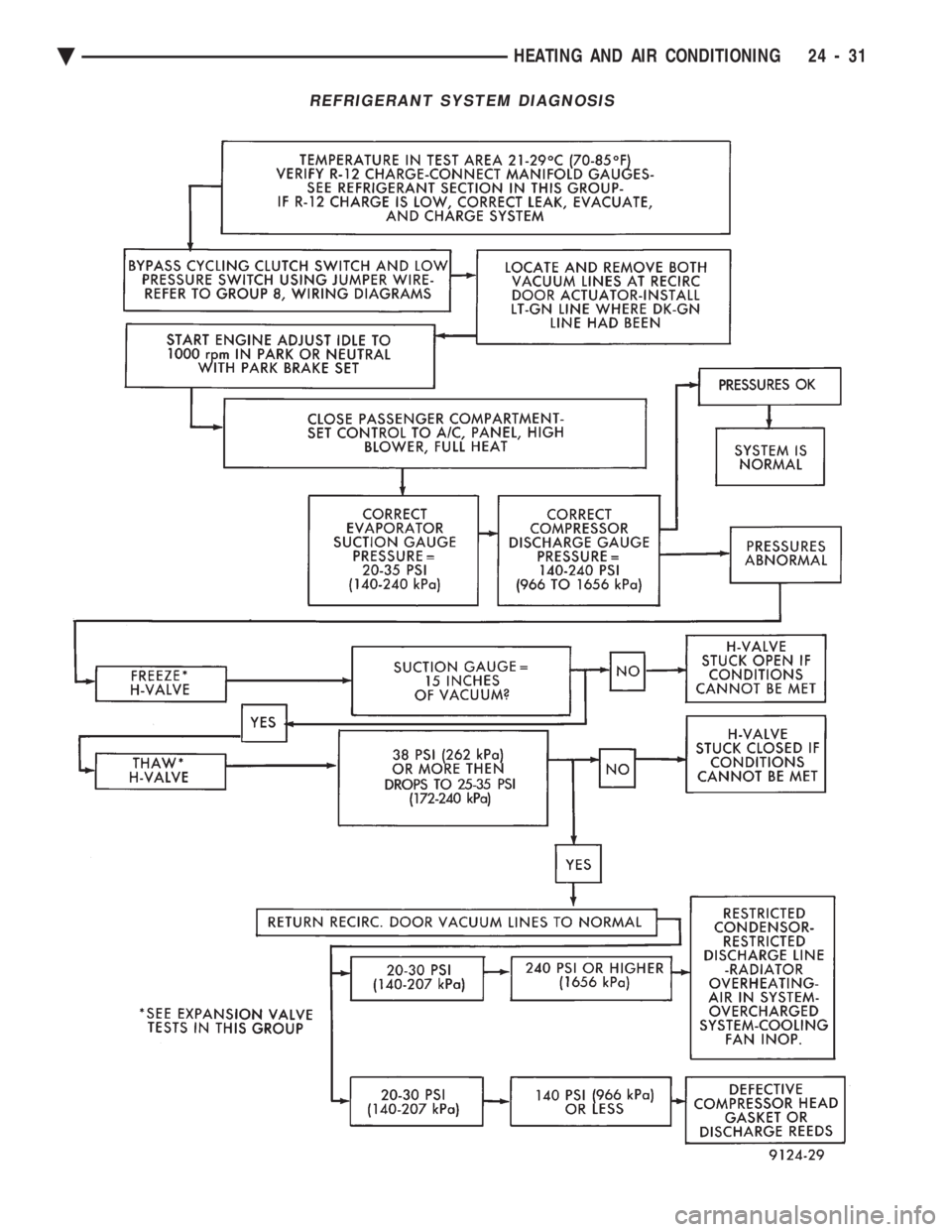
REFRIGERANT SYSTEM DIAGNOSIS
Ä HEATING AND AIR CONDITIONING 24 - 31
Page 2336 of 2438
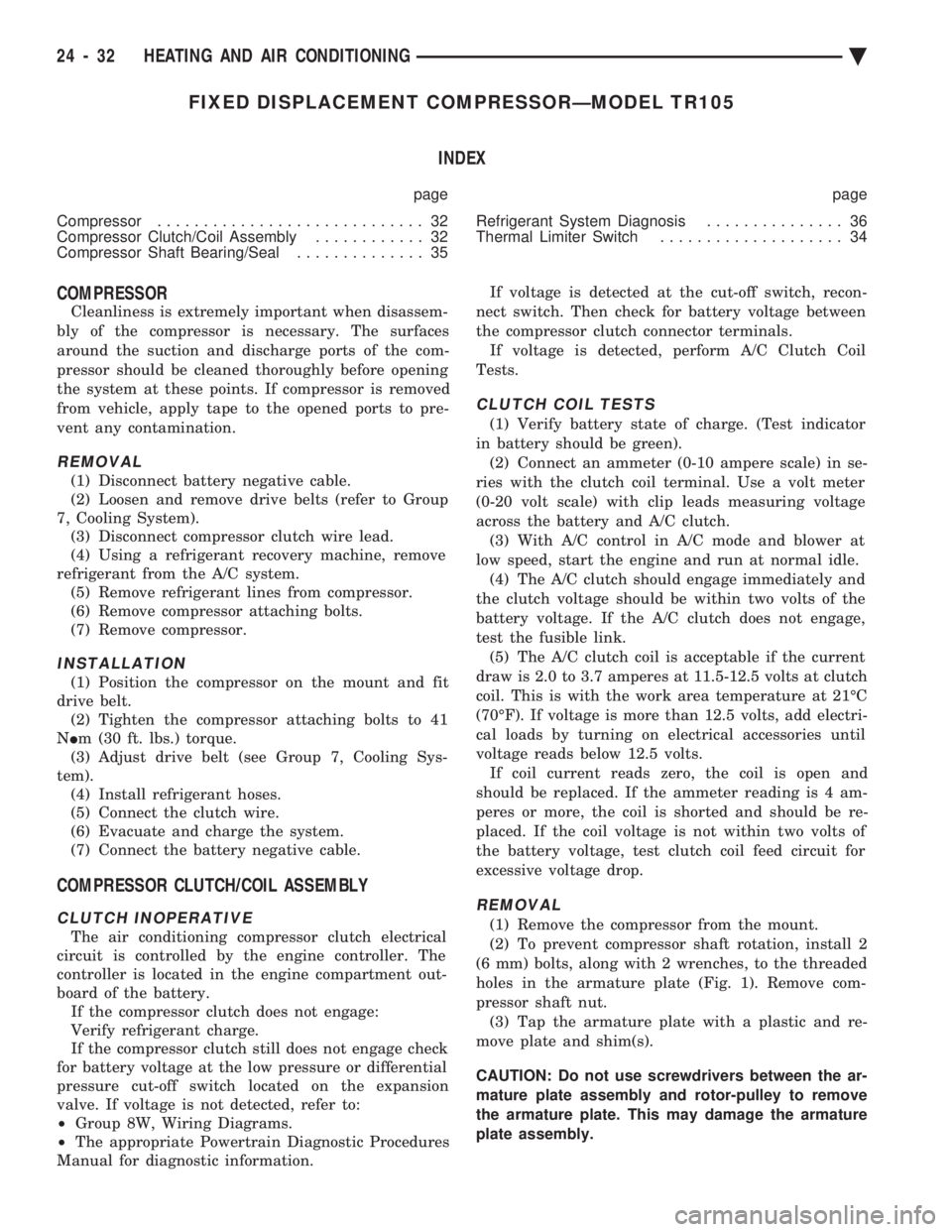
FIXED DISPLACEMENT COMPRESSORÐMODEL TR105 INDEX
page page
Compressor ............................. 32
Compressor Clutch/Coil Assembly ............ 32
Compressor Shaft Bearing/Seal .............. 35 Refrigerant System Diagnosis
............... 36
Thermal Limiter Switch .................... 34
COMPRESSOR
Cleanliness is extremely important when disassem-
bly of the compressor is necessary. The surfaces
around the suction and discharge ports of the com-
pressor should be cleaned thoroughly before opening
the system at these points. If compressor is removed
from vehicle, apply tape to the opened ports to pre-
vent any contamination.
REMOVAL
(1) Disconnect battery negative cable.
(2) Loosen and remove drive belts (refer to Group
7, Cooling System). (3) Disconnect compressor clutch wire lead.
(4) Using a refrigerant recovery machine, remove
refrigerant from the A/C system. (5) Remove refrigerant lines from compressor.
(6) Remove compressor attaching bolts.
(7) Remove compressor.
INSTALLATION
(1) Position the compressor on the mount and fit
drive belt. (2) Tighten the compressor attaching bolts to 41
N Im (30 ft. lbs.) torque.
(3) Adjust drive belt (see Group 7, Cooling Sys-
tem). (4) Install refrigerant hoses.
(5) Connect the clutch wire.
(6) Evacuate and charge the system.
(7) Connect the battery negative cable.
COMPRESSOR CLUTCH/COIL ASSEMBLY
CLUTCH INOPERATIVE
The air conditioning compressor clutch electrical
circuit is controlled by the engine controller. The
controller is located in the engine compartment out-
board of the battery. If the compressor clutch does not engage:
Verify refrigerant charge.
If the compressor clutch still does not engage check
for battery voltage at the low pressure or differential
pressure cut-off switch located on the expansion
valve. If voltage is not detected, refer to:
² Group 8W, Wiring Diagrams.
² The appropriate Powertrain Diagnostic Procedures
Manual for diagnostic information. If voltage is detected at the cut-off switch, recon-
nect switch. Then check for battery voltage between
the compressor clutch connector terminals. If voltage is detected, perform A/C Clutch Coil
Tests.
CLUTCH COIL TESTS
(1) Verify battery state of charge. (Test indicator
in battery should be green). (2) Connect an ammeter (0-10 ampere scale) in se-
ries with the clutch coil terminal. Use a volt meter
(0-20 volt scale) with clip leads measuring voltage
across the battery and A/C clutch. (3) With A/C control in A/C mode and blower at
low speed, start the engine and run at normal idle. (4) The A/C clutch should engage immediately and
the clutch voltage should be within two volts of the
battery voltage. If the A/C clutch does not engage,
test the fusible link. (5) The A/C clutch coil is acceptable if the current
draw is 2.0 to 3.7 amperes at 11.5-12.5 volts at clutch
coil. This is with the work area temperature at 21ÉC
(70ÉF). If voltage is more than 12.5 volts, add electri-
cal loads by turning on electrical accessories until
voltage reads below 12.5 volts. If coil current reads zero, the coil is open and
should be replaced. If the ammeter reading is 4 am-
peres or more, the coil is shorted and should be re-
placed. If the coil voltage is not within two volts of
the battery voltage, test clutch coil feed circuit for
excessive voltage drop.
REMOVAL
(1) Remove the compressor from the mount.
(2) To prevent compressor shaft rotation, install 2
(6 mm) bolts, along with 2 wrenches, to the threaded
holes in the armature plate (Fig. 1). Remove com-
pressor shaft nut. (3) Tap the armature plate with a plastic and re-
move plate and shim(s).
CAUTION: Do not use screwdrivers between the ar-
mature plate assembly and rotor-pulley to remove
the armature plate. This may damage the armature
plate assembly.
24 - 32 HEATING AND AIR CONDITIONING Ä
Page 2337 of 2438

(4) Remove rotor-pulley retaining snap ring with
Snap Ring Pliers C-4574. Slide rotor-pulley assembly
from compressor. Use a plastic hammer, if necessary. (5) Loosen the lead wire retaining clamps and re-
move lead wire from the compressor front end plate.
Disconnect the lead wire from the thermal limiter
switch. (6) Remove the snap ring which secures the field
coil-core assembly to the front boss (Fig. 2). Note the
alignment of field coil-core assembly when removing.
WARNING: TAKE CARE THAT THE SNAP RING
DOES NOT FLY OUT FROM THE GROOVE.
INSPECTION
Examine frictional faces of the rotor-pulley and ar-
mature plate for wear. The pulley and plate should
be replaced if there is excessive wear or scoring. If
the friction surfaces are oily, inspect the shaft nose
area of the compressor for excess oil. If excess oil is
present, the shaft seal is leaking and will have to be
replaced. Check rotor-pulley bearing for roughness or exces-
sive grease leakage. Check for bearing grease con-
tamination on armature plate faces. The rotor-pulley and armature plate should be re-
placed as a matched set.
INSTALLATION
(1) Position the back of the field coil-core over the
compressor front boss. This will allow the locating
nipple on the back of the coil to line up with the lo-
cating indentation on the front boss. This ensures
correct angular position of the clutch coil and lead
wire. (2) Fasten lead wire to the compressor front plate
with the retaining clip. Connect the lead wire to the
thermal limiter switch. (3) Install field coil-core retaining snap ring (bevel
side outward) with Snap Ring Pliers C-4574. Press
snap ring to make sure it is properly seated in the
groove.
CAUTION: If snap rings on field coil-core and rotor-
pulley are not fully seated, they will vibrate out. A
clutch failure and possible severe damage to the
compressor could result.
(4) Slide pulley assembly onto compressor.
CAUTION: Do not mar the pulley frictional surface. (5) Install rotor-pulley assembly retaining snap
ring (bevel side outward) with Snap Ring Pliers
C-4574. Press the snap ring to make sure it is prop-
erly seated in the groove. (6) If the original armature plate assembly and ro-
tor-pulley assembly are to be reused, the old shim(s)
can be used. If not, place a trial stack of shims, 2.54
mm (0.10 in.) thick, on the compressor shaft against
the shoulder of the armature plate. (7) Install armature plate to the compressor shaft.
Note the machined mating splines (Fig. 3).
Fig. 1 Compressor Shaft Nut Removal/Installation
Fig. 2 Armature Plate/Rotor-Pulley/Field Coil-Core
Fig. 3 Aligning Clutch Plate Splines
Ä HEATING AND AIR CONDITIONING 24 - 33
Page 2338 of 2438
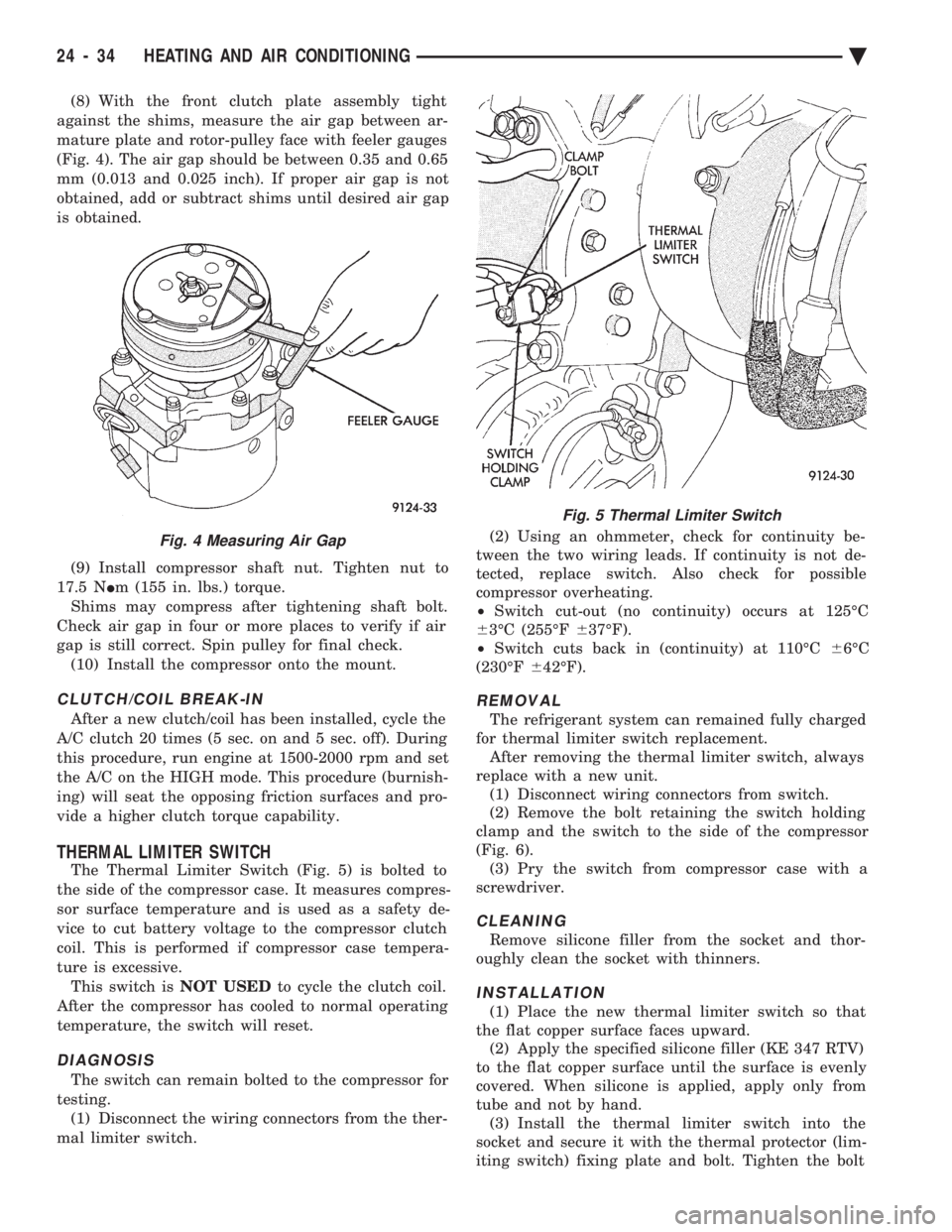
(8) With the front clutch plate assembly tight
against the shims, measure the air gap between ar-
mature plate and rotor-pulley face with feeler gauges
(Fig. 4). The air gap should be between 0.35 and 0.65
mm (0.013 and 0.025 inch). If proper air gap is not
obtained, add or subtract shims until desired air gap
is obtained.
(9) Install compressor shaft nut. Tighten nut to
17.5 N Im (155 in. lbs.) torque.
Shims may compress after tightening shaft bolt.
Check air gap in four or more places to verify if air
gap is still correct. Spin pulley for final check. (10) Install the compressor onto the mount.
CLUTCH/COIL BREAK-IN
After a new clutch/coil has been installed, cycle the
A/C clutch 20 times (5 sec. on and 5 sec. off). During
this procedure, run engine at 1500-2000 rpm and set
the A/C on the HIGH mode. This procedure (burnish-
ing) will seat the opposing friction surfaces and pro-
vide a higher clutch torque capability.
THERMAL LIMITER SWITCH
The Thermal Limiter Switch (Fig. 5) is bolted to
the side of the compressor case. It measures compres-
sor surface temperature and is used as a safety de-
vice to cut battery voltage to the compressor clutch
coil. This is performed if compressor case tempera-
ture is excessive. This switch is NOT USEDto cycle the clutch coil.
After the compressor has cooled to normal operating
temperature, the switch will reset.
DIAGNOSIS
The switch can remain bolted to the compressor for
testing. (1) Disconnect the wiring connectors from the ther-
mal limiter switch. (2) Using an ohmmeter, check for continuity be-
tween the two wiring leads. If continuity is not de-
tected, replace switch. Also check for possible
compressor overheating.
² Switch cut-out (no continuity) occurs at 125ÉC
6 3ÉC (255ÉF 637ÉF).
² Switch cuts back in (continuity) at 110ÉC 66ÉC
(230ÉF 642ÉF).
REMOVAL
The refrigerant system can remained fully charged
for thermal limiter switch replacement. After removing the thermal limiter switch, always
replace with a new unit. (1) Disconnect wiring connectors from switch.
(2) Remove the bolt retaining the switch holding
clamp and the switch to the side of the compressor
(Fig. 6). (3) Pry the switch from compressor case with a
screwdriver.
CLEANING
Remove silicone filler from the socket and thor-
oughly clean the socket with thinners.
INSTALLATION
(1) Place the new thermal limiter switch so that
the flat copper surface faces upward. (2) Apply the specified silicone filler (KE 347 RTV)
to the flat copper surface until the surface is evenly
covered. When silicone is applied, apply only from
tube and not by hand. (3) Install the thermal limiter switch into the
socket and secure it with the thermal protector (lim-
iting switch) fixing plate and bolt. Tighten the bolt
Fig. 4 Measuring Air Gap
Fig. 5 Thermal Limiter Switch
24 - 34 HEATING AND AIR CONDITIONING Ä
Page 2339 of 2438
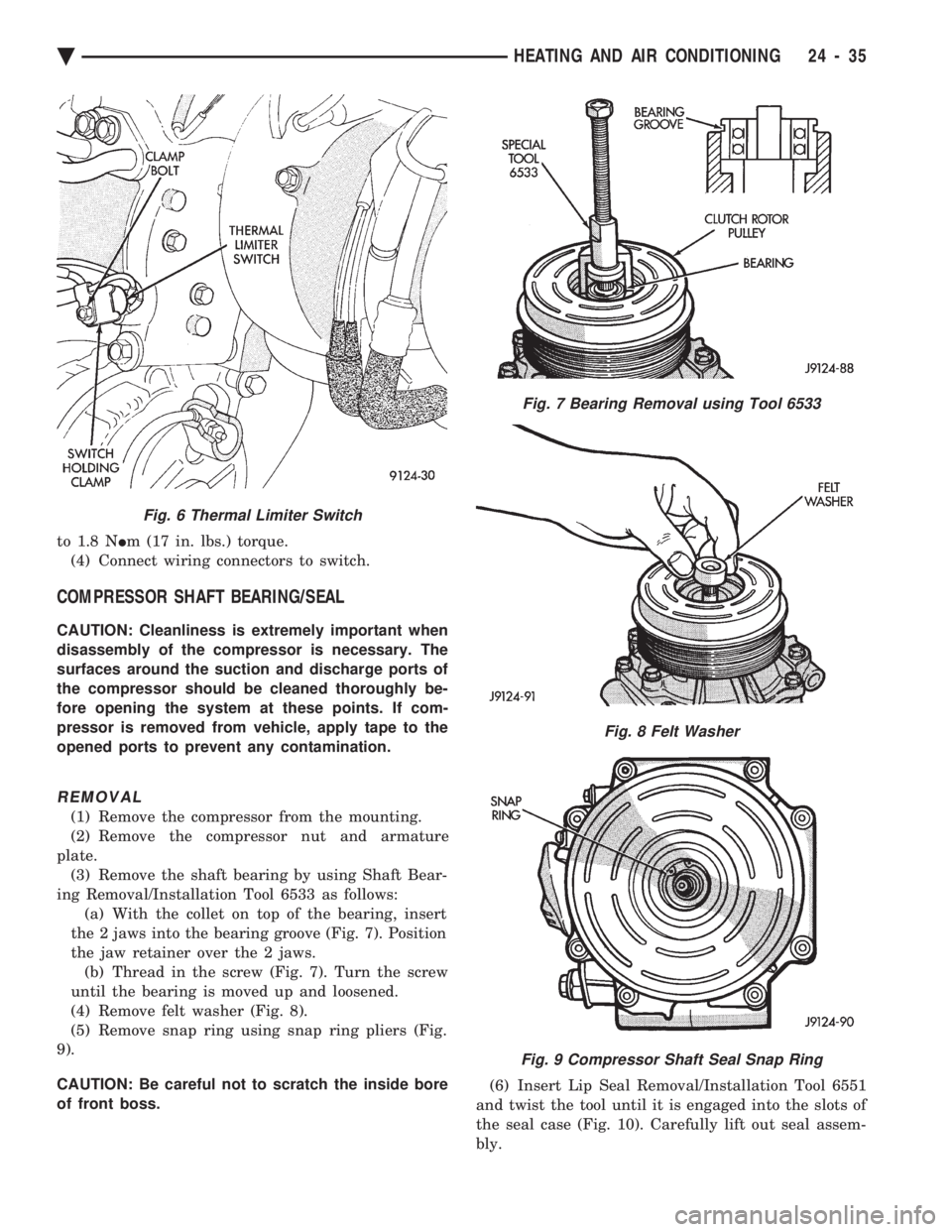
to 1.8 N Im (17 in. lbs.) torque.
(4) Connect wiring connectors to switch.
COMPRESSOR SHAFT BEARING/SEAL
CAUTION: Cleanliness is extremely important when
disassembly of the compressor is necessary. The
surfaces around the suction and discharge ports of
the compressor should be cleaned thoroughly be-
fore opening the system at these points. If com-
pressor is removed from vehicle, apply tape to the
opened ports to prevent any contamination.
REMOVAL
(1) Remove the compressor from the mounting.
(2) Remove the compressor nut and armature
plate. (3) Remove the shaft bearing by using Shaft Bear-
ing Removal/Installation Tool 6533 as follows: (a) With the collet on top of the bearing, insert
the 2 jaws into the bearing groove (Fig. 7). Position
the jaw retainer over the 2 jaws. (b) Thread in the screw (Fig. 7). Turn the screw
until the bearing is moved up and loosened.
(4) Remove felt washer (Fig. 8).
(5) Remove snap ring using snap ring pliers (Fig.
9).
CAUTION: Be careful not to scratch the inside bore
of front boss. (6) Insert Lip Seal Removal/Installation Tool 6551
and twist the tool until it is engaged into the slots of
the seal case (Fig. 10). Carefully lift out seal assem-
bly.
Fig. 6 Thermal Limiter Switch
Fig. 7 Bearing Removal using Tool 6533
Fig. 8 Felt Washer
Fig. 9 Compressor Shaft Seal Snap Ring
Ä HEATING AND AIR CONDITIONING 24 - 35
Page 2340 of 2438
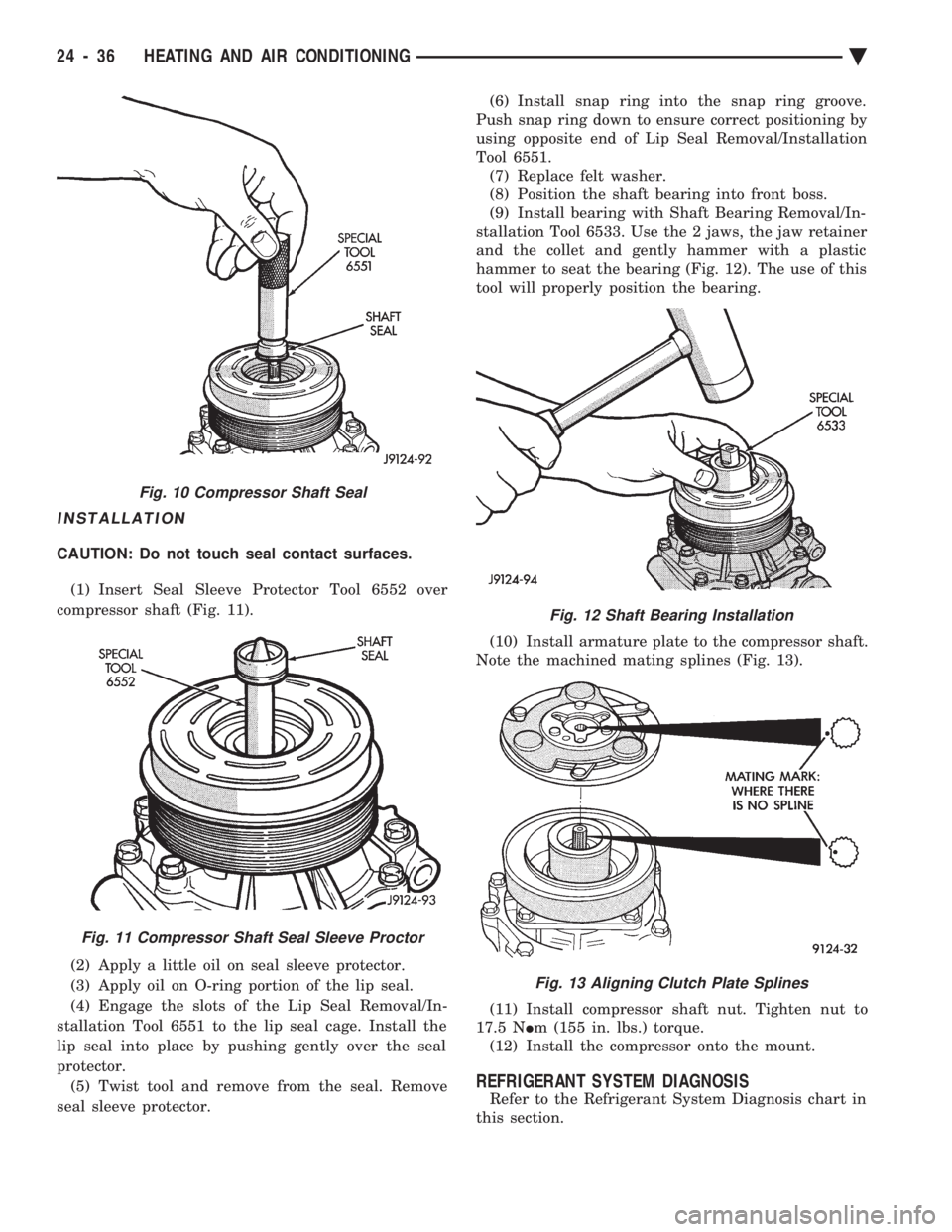
INSTALLATION
CAUTION: Do not touch seal contact surfaces. (1) Insert Seal Sleeve Protector Tool 6552 over
compressor shaft (Fig. 11).
(2) Apply a little oil on seal sleeve protector.
(3) Apply oil on O-ring portion of the lip seal.
(4) Engage the slots of the Lip Seal Removal/In-
stallation Tool 6551 to the lip seal cage. Install the
lip seal into place by pushing gently over the seal
protector. (5) Twist tool and remove from the seal. Remove
seal sleeve protector. (6) Install snap ring into the snap ring groove.
Push snap ring down to ensure correct positioning by
using opposite end of Lip Seal Removal/Installation
Tool 6551. (7) Replace felt washer.
(8) Position the shaft bearing into front boss.
(9) Install bearing with Shaft Bearing Removal/In-
stallation Tool 6533. Use the 2 jaws, the jaw retainer
and the collet and gently hammer with a plastic
hammer to seat the bearing (Fig. 12). The use of this
tool will properly position the bearing.
(10) Install armature plate to the compressor shaft.
Note the machined mating splines (Fig. 13).
(11) Install compressor shaft nut. Tighten nut to
17.5 N Im (155 in. lbs.) torque.
(12) Install the compressor onto the mount.
REFRIGERANT SYSTEM DIAGNOSIS
Refer to the Refrigerant System Diagnosis chart in
this section.
Fig. 10 Compressor Shaft Seal
Fig. 11 Compressor Shaft Seal Sleeve Proctor
Fig. 12 Shaft Bearing Installation
Fig. 13 Aligning Clutch Plate Splines
24 - 36 HEATING AND AIR CONDITIONING Ä