CHEVROLET PLYMOUTH ACCLAIM 1993 Service Manual
Manufacturer: CHEVROLET, Model Year: 1993, Model line: PLYMOUTH ACCLAIM, Model: CHEVROLET PLYMOUTH ACCLAIM 1993Pages: 2438, PDF Size: 74.98 MB
Page 451 of 2438
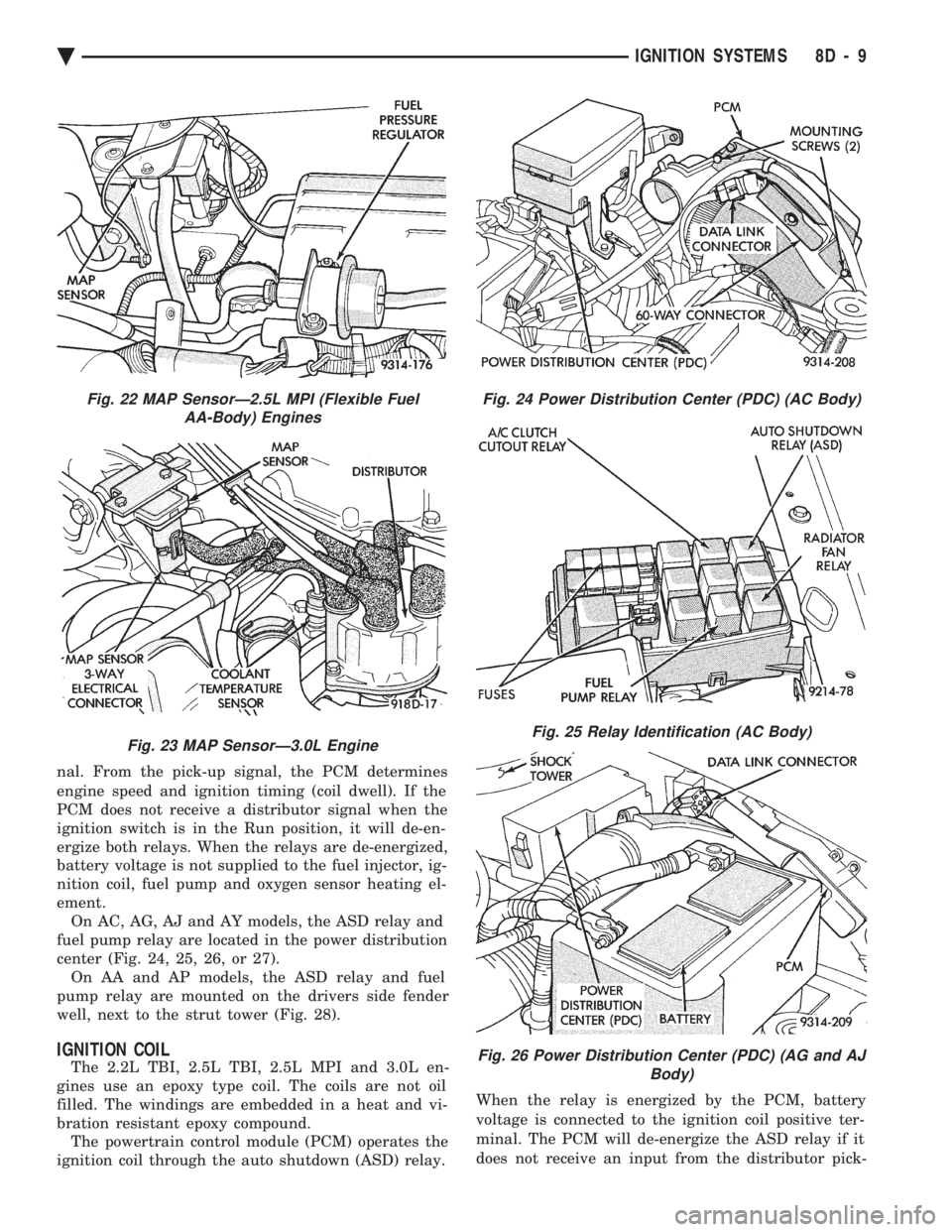
nal. From the pick-up signal, the PCM determines
engine speed and ignition timing (coil dwell). If the
PCM does not receive a distributor signal when the
ignition switch is in the Run position, it will de-en-
ergize both relays. When the relays are de-energized,
battery voltage is not supplied to the fuel injector, ig-
nition coil, fuel pump and oxygen sensor heating el-
ement. On AC, AG, AJ and AY models, the ASD relay and
fuel pump relay are located in the power distribution
center (Fig. 24, 25, 26, or 27). On AA and AP models, the ASD relay and fuel
pump relay are mounted on the drivers side fender
well, next to the strut tower (Fig. 28).
IGNITION COIL
The 2.2L TBI, 2.5L TBI, 2.5L MPI and 3.0L en-
gines use an epoxy type coil. The coils are not oil
filled. The windings are embedded in a heat and vi-
bration resistant epoxy compound. The powertrain control module (PCM) operates the
ignition coil through the auto shutdown (ASD) relay. When the relay is energized by the PCM, battery
voltage is connected to the ignition coil positive ter-
minal. The PCM will de-energize the ASD relay if it
does not receive an input from the distributor pick-
Fig. 22 MAP SensorÐ2.5L MPI (Flexible Fuel AA-Body) Engines
Fig. 23 MAP SensorÐ3.0L Engine
Fig. 24 Power Distribution Center (PDC) (AC Body)
Fig. 25 Relay Identification (AC Body)
Fig. 26 Power Distribution Center (PDC) (AG and AJ Body)
Ä IGNITION SYSTEMS 8D - 9
Page 452 of 2438

up. Refer to Auto Shutdown (ASD) Relay and Fuel
Pump Relay in this section.On 2.2L TBI, 2.5L TBI and 2.5L MPI engines, the
ignition coil is mounted to the thermostat housing
(Fig. 29). On 3.0L engines the coil is mounted on the
rear of the intake manifold next to the air cleaner
(Fig. 30).
Fig. 28 Relay Identification (AA and AP Bodies)
Fig. 29 Ignition CoilÐ2.2L TBI, 2.5L TBI and 2.5L MPI Engines
Fig. 30 Ignition CoilÐ3.0L Engine
Fig. 27 Relay Identification (AG and AJ Body)
8D - 10 IGNITION SYSTEMS Ä
Page 453 of 2438
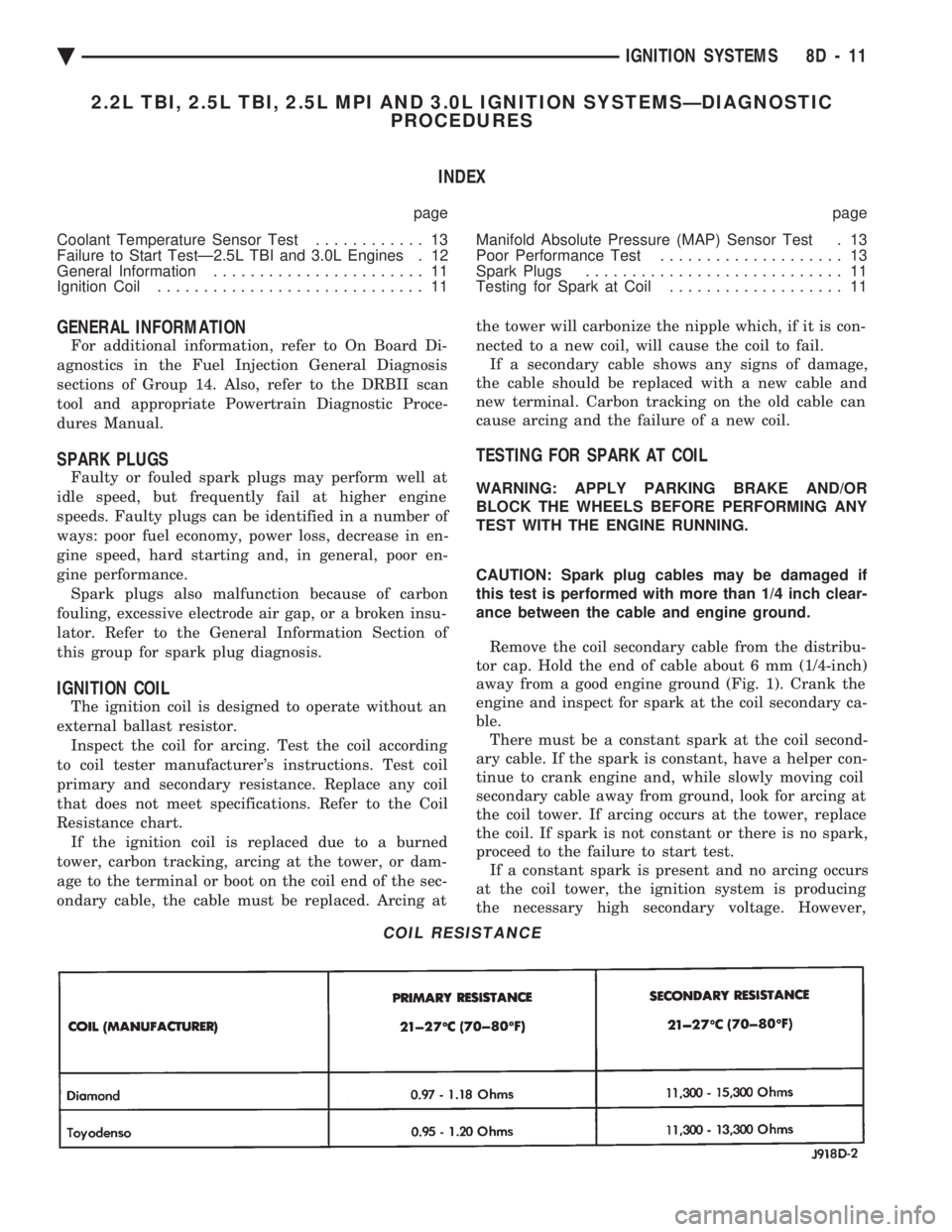
2.2L TBI, 2.5L TBI, 2.5L MPI AND 3.0L IGNITION SYSTEMSÐDIAGNOSTIC PROCEDURES
INDEX
page page
Coolant Temperature Sensor Test ............ 13
Failure to Start TestÐ2.5L TBI and 3.0L Engines . 12
General Information ....................... 11
Ignition Coil ............................. 11 Manifold Absolute Pressure (MAP) Sensor Test . 13
Poor Performance Test .................... 13
Spark Plugs ............................ 11
Testing for Spark at Coil ................... 11
GENERAL INFORMATION
For additional information, refer to On Board Di-
agnostics in the Fuel Injection General Diagnosis
sections of Group 14. Also, refer to the DRBII scan
tool and appropriate Powertrain Diagnostic Proce-
dures Manual.
SPARK PLUGS
Faulty or fouled spark plugs may perform well at
idle speed, but frequently fail at higher engine
speeds. Faulty plugs can be identified in a number of
ways: poor fuel economy, power loss, decrease in en-
gine speed, hard starting and, in general, poor en-
gine performance. Spark plugs also malfunction because of carbon
fouling, excessive electrode air gap, or a broken insu-
lator. Refer to the General Information Section of
this group for spark plug diagnosis.
IGNITION COIL
The ignition coil is designed to operate without an
external ballast resistor. Inspect the coil for arcing. Test the coil according
to coil tester manufacturer's instructions. Test coil
primary and secondary resistance. Replace any coil
that does not meet specifications. Refer to the Coil
Resistance chart. If the ignition coil is replaced due to a burned
tower, carbon tracking, arcing at the tower, or dam-
age to the terminal or boot on the coil end of the sec-
ondary cable, the cable must be replaced. Arcing at the tower will carbonize the nipple which, if it is con-
nected to a new coil, will cause the coil to fail. If a secondary cable shows any signs of damage,
the cable should be replaced with a new cable and
new terminal. Carbon tracking on the old cable can
cause arcing and the failure of a new coil.
TESTING FOR SPARK AT COIL
WARNING: APPLY PARKING BRAKE AND/OR
BLOCK THE WHEELS BEFORE PERFORMING ANY
TEST WITH THE ENGINE RUNNING.
CAUTION: Spark plug cables may be damaged if
this test is performed with more than 1/4 inch clear-
ance between the cable and engine ground.
Remove the coil secondary cable from the distribu-
tor cap. Hold the end of cable about 6 mm (1/4-inch)
away from a good engine ground (Fig. 1). Crank the
engine and inspect for spark at the coil secondary ca-
ble. There must be a constant spark at the coil second-
ary cable. If the spark is constant, have a helper con-
tinue to crank engine and, while slowly moving coil
secondary cable away from ground, look for arcing at
the coil tower. If arcing occurs at the tower, replace
the coil. If spark is not constant or there is no spark,
proceed to the failure to start test. If a constant spark is present and no arcing occurs
at the coil tower, the ignition system is producing
the necessary high secondary voltage. However,
COIL RESISTANCE
Ä IGNITION SYSTEMS 8D - 11
Page 454 of 2438
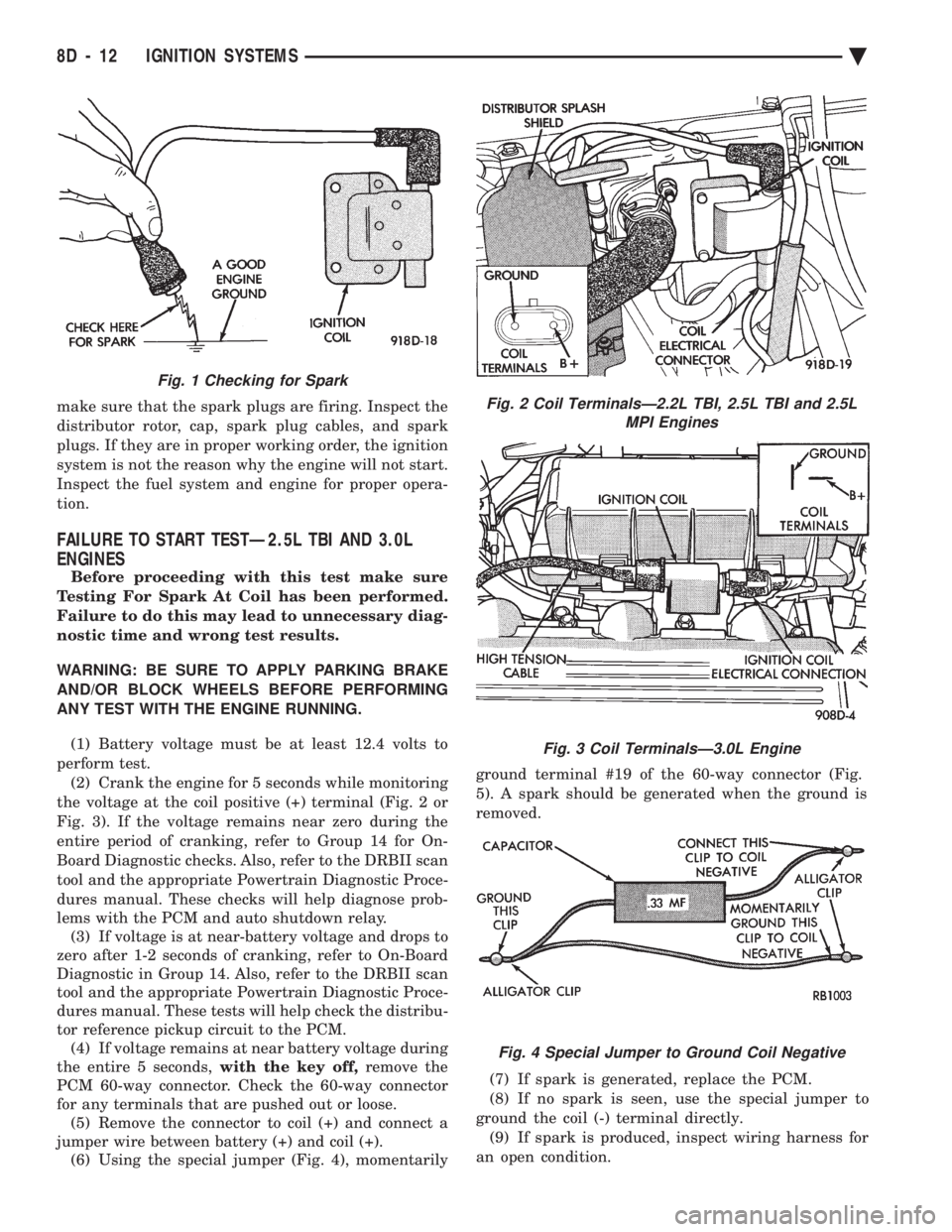
make sure that the spark plugs are firing. Inspect the
distributor rotor, cap, spark plug cables, and spark
plugs. If they are in proper working order, the ignition
system is not the reason why the engine will not start.
Inspect the fuel system and engine for proper opera-
tion.
FAILURE TO START TESTÐ2.5L TBI AND 3.0L
ENGINES
Before proceeding with this test make sure
Testing For Spark At Coil has been performed.
Failure to do this may lead to unnecessary diag-
nostic time and wrong test results.
WARNING: BE SURE TO APPLY PARKING BRAKE
AND/OR BLOCK WHEELS BEFORE PERFORMING
ANY TEST WITH THE ENGINE RUNNING.
(1) Battery voltage must be at least 12.4 volts to
perform test. (2) Crank the engine for 5 seconds while monitoring
the voltage at the coil positive (+) terminal (Fig. 2 or
Fig. 3). If the voltage remains near zero during the
entire period of cranking, refer to Group 14 for On-
Board Diagnostic checks. Also, refer to the DRBII scan
tool and the appropriate Powertrain Diagnostic Proce-
dures manual. These checks will help diagnose prob-
lems with the PCM and auto shutdown relay. (3) If voltage is at near-battery voltage and drops to
zero after 1-2 seconds of cranking, refer to On-Board
Diagnostic in Group 14. Also, refer to the DRBII scan
tool and the appropriate Powertrain Diagnostic Proce-
dures manual. These tests will help check the distribu-
tor reference pickup circuit to the PCM. (4) If voltage remains at near battery voltage during
the entire 5 seconds, with the key off,remove the
PCM 60-way connector. Check the 60-way connector
for any terminals that are pushed out or loose. (5) Remove the connector to coil (+) and connect a
jumper wire between battery (+) and coil (+). (6) Using the special jumper (Fig. 4), momentarily ground terminal #19 of the 60-way connector (Fig.
5). A spark should be generated when the ground is
removed.
(7) If spark is generated, replace the PCM.
(8) If no spark is seen, use the special jumper to
ground the coil (-) terminal directly. (9) If spark is produced, inspect wiring harness for
an open condition.
Fig. 2 Coil TerminalsÐ2.2L TBI, 2.5L TBI and 2.5L MPI Engines
Fig. 3 Coil TerminalsÐ3.0L Engine
Fig. 4 Special Jumper to Ground Coil Negative
Fig. 1 Checking for Spark
8D - 12 IGNITION SYSTEMS Ä
Page 455 of 2438
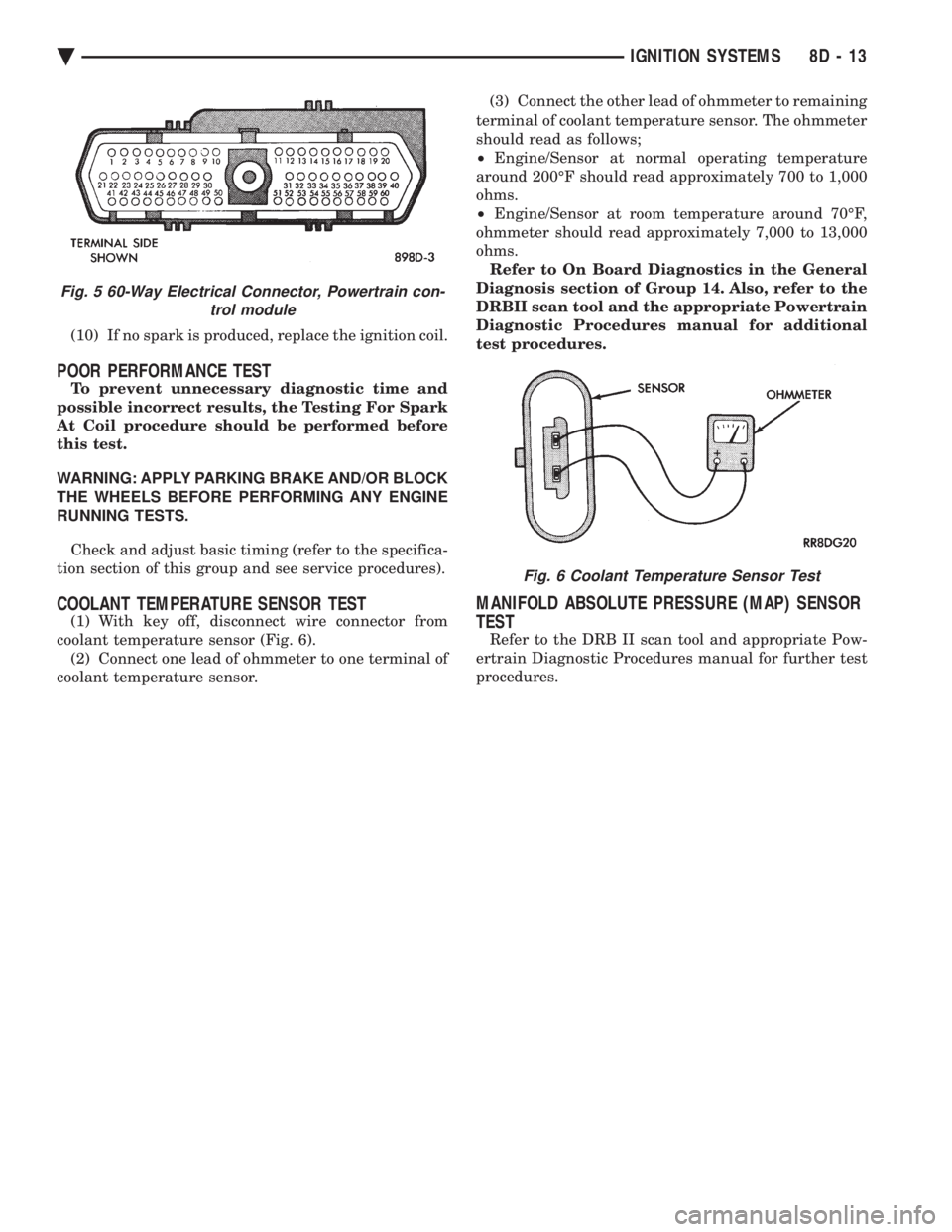
(10) If no spark is produced, replace the ignition coil.
POOR PERFORMANCE TEST
To prevent unnecessary diagnostic time and
possible incorrect results, the Testing For Spark
At Coil procedure should be performed before
this test.
WARNING: APPLY PARKING BRAKE AND/OR BLOCK
THE WHEELS BEFORE PERFORMING ANY ENGINE
RUNNING TESTS.
Check and adjust basic timing (refer to the specifica-
tion section of this group and see service procedures).
COOLANT TEMPERATURE SENSOR TEST
(1) With key off, disconnect wire connector from
coolant temperature sensor (Fig. 6). (2) Connect one lead of ohmmeter to one terminal of
coolant temperature sensor. (3) Connect the other lead of ohmmeter to remaining
terminal of coolant temperature sensor. The ohmmeter
should read as follows;
² Engine/Sensor at normal operating temperature
around 200ÉF should read approximately 700 to 1,000
ohms.
² Engine/Sensor at room temperature around 70ÉF,
ohmmeter should read approximately 7,000 to 13,000
ohms. Refer to On Board Diagnostics in the General
Diagnosis section of Group 14. Also, refer to the
DRBII scan tool and the appropriate Powertrain
Diagnostic Procedures manual for additional
test procedures.
MANIFOLD ABSOLUTE PRESSURE (MAP) SENSOR
TEST
Refer to the DRB II scan tool and appropriate Pow-
ertrain Diagnostic Procedures manual for further test
procedures.
Fig. 5 60-Way Electrical Connector, Powertrain con- trol module
Fig. 6 Coolant Temperature Sensor Test
Ä IGNITION SYSTEMS 8D - 13
Page 456 of 2438
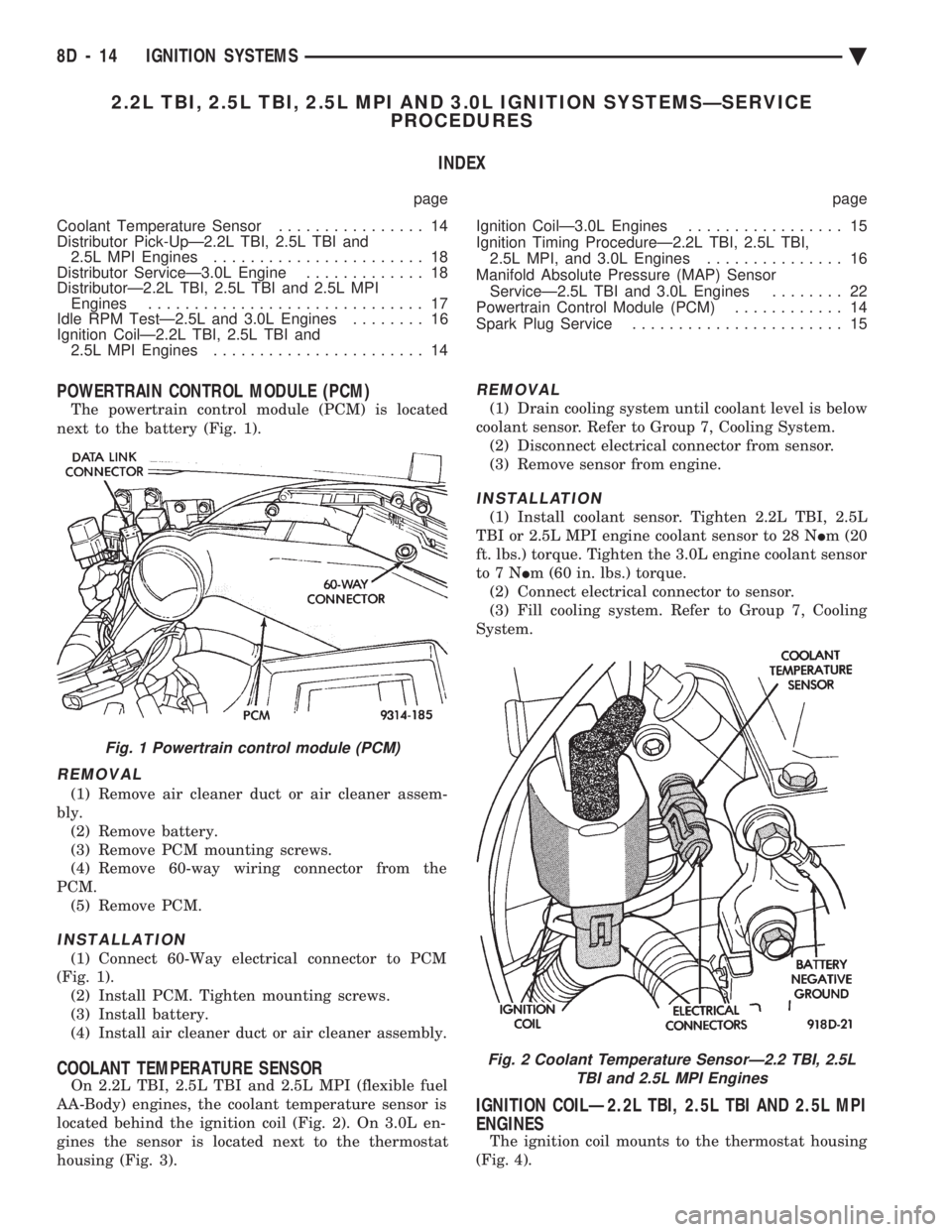
2.2L TBI, 2.5L TBI, 2.5L MPI AND 3.0L IGNITION SYSTEMSÐSERVICE PROCEDURES
INDEX
page page
Coolant Temperature Sensor ................ 14
Distributor Pick-UpÐ2.2L TBI, 2.5L TBI and 2.5L MPI Engines ....................... 18
Distributor ServiceÐ3.0L Engine ............. 18
DistributorÐ2.2L TBI, 2.5L TBI and 2.5L MPI Engines .............................. 17
Idle RPM TestÐ2.5L and 3.0L Engines ........ 16
Ignition CoilÐ2.2L TBI, 2.5L TBI and 2.5L MPI Engines ....................... 14 Ignition CoilÐ3.0L Engines
................. 15
Ignition Timing ProcedureÐ2.2L TBI, 2.5L TBI, 2.5L MPI, and 3.0L Engines ............... 16
Manifold Absolute Pressure (MAP) Sensor ServiceÐ2.5L TBI and 3.0L Engines ........ 22
Powertrain Control Module (PCM) ............ 14
Spark Plug Service ....................... 15
POWERTRAIN CONTROL MODULE (PCM)
The powertrain control module (PCM) is located
next to the battery (Fig. 1).
REMOVAL
(1) Remove air cleaner duct or air cleaner assem-
bly. (2) Remove battery.
(3) Remove PCM mounting screws.
(4) Remove 60-way wiring connector from the
PCM. (5) Remove PCM.
INSTALLATION
(1) Connect 60-Way electrical connector to PCM
(Fig. 1). (2) Install PCM. Tighten mounting screws.
(3) Install battery.
(4) Install air cleaner duct or air cleaner assembly.
COOLANT TEMPERATURE SENSOR
On 2.2L TBI, 2.5L TBI and 2.5L MPI (flexible fuel
AA-Body) engines, the coolant temperature sensor is
located behind the ignition coil (Fig. 2). On 3.0L en-
gines the sensor is located next to the thermostat
housing (Fig. 3).
REMOVAL
(1) Drain cooling system until coolant level is below
coolant sensor. Refer to Group 7, Cooling System. (2) Disconnect electrical connector from sensor.
(3) Remove sensor from engine.
INSTALLATION
(1) Install coolant sensor. Tighten 2.2L TBI, 2.5L
TBI or 2.5L MPI engine coolant sensor to 28 N Im (20
ft. lbs.) torque. Tighten the 3.0L engine coolant sensor
to7N Im (60 in. lbs.) torque.
(2) Connect electrical connector to sensor.
(3) Fill cooling system. Refer to Group 7, Cooling
System.
IGNITION COILÐ2.2L TBI, 2.5L TBI AND 2.5L MPI
ENGINES
The ignition coil mounts to the thermostat housing
(Fig. 4).
Fig. 1 Powertrain control module (PCM)
Fig. 2 Coolant Temperature SensorÐ2.2 TBI, 2.5L TBI and 2.5L MPI Engines
8D - 14 IGNITION SYSTEMS Ä
Page 457 of 2438
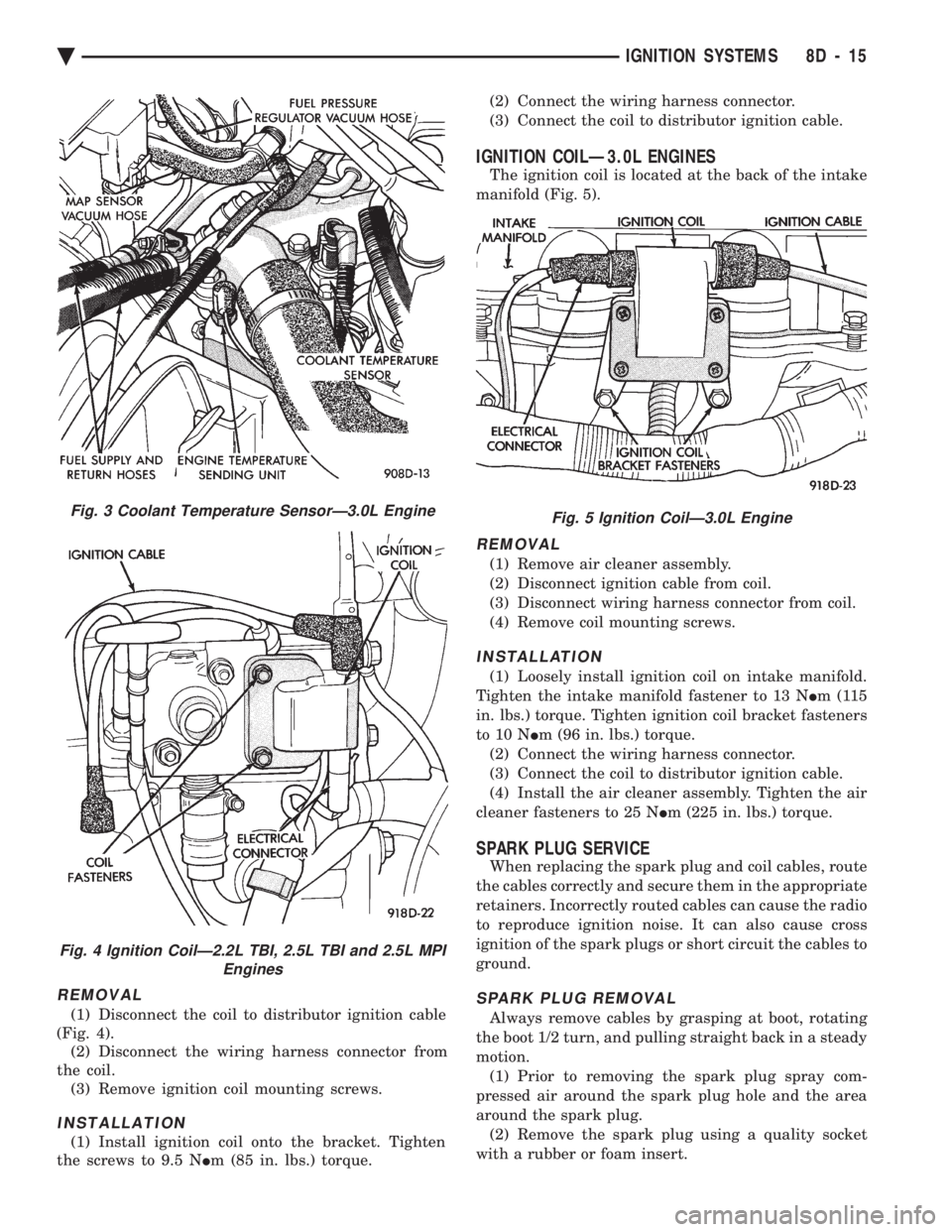
REMOVAL
(1) Disconnect the coil to distributor ignition cable
(Fig. 4). (2) Disconnect the wiring harness connector from
the coil. (3) Remove ignition coil mounting screws.
INSTALLATION
(1) Install ignition coil onto the bracket. Tighten
the screws to 9.5 N Im (85 in. lbs.) torque. (2) Connect the wiring harness connector.
(3) Connect the coil to distributor ignition cable.
IGNITION COILÐ3.0L ENGINES
The ignition coil is located at the back of the intake
manifold (Fig. 5).
REMOVAL
(1) Remove air cleaner assembly.
(2) Disconnect ignition cable from coil.
(3) Disconnect wiring harness connector from coil.
(4) Remove coil mounting screws.
INSTALLATION
(1) Loosely install ignition coil on intake manifold.
Tighten the intake manifold fastener to 13 N Im(115
in. lbs.) torque. Tighten ignition coil bracket fasteners
to 10 N Im (96 in. lbs.) torque.
(2) Connect the wiring harness connector.
(3) Connect the coil to distributor ignition cable.
(4) Install the air cleaner assembly. Tighten the air
cleaner fasteners to 25 N Im (225 in. lbs.) torque.
SPARK PLUG SERVICE
When replacing the spark plug and coil cables, route
the cables correctly and secure them in the appropriate
retainers. Incorrectly routed cables can cause the radio
to reproduce ignition noise. It can also cause cross
ignition of the spark plugs or short circuit the cables to
ground.
SPARK PLUG REMOVAL
Always remove cables by grasping at boot, rotating
the boot 1/2 turn, and pulling straight back in a steady
motion. (1) Prior to removing the spark plug spray com-
pressed air around the spark plug hole and the area
around the spark plug. (2) Remove the spark plug using a quality socket
with a rubber or foam insert.
Fig. 3 Coolant Temperature SensorÐ3.0L Engine
Fig. 4 Ignition CoilÐ2.2L TBI, 2.5L TBI and 2.5L MPI Engines
Fig. 5 Ignition CoilÐ3.0L Engine
Ä IGNITION SYSTEMS 8D - 15
Page 458 of 2438
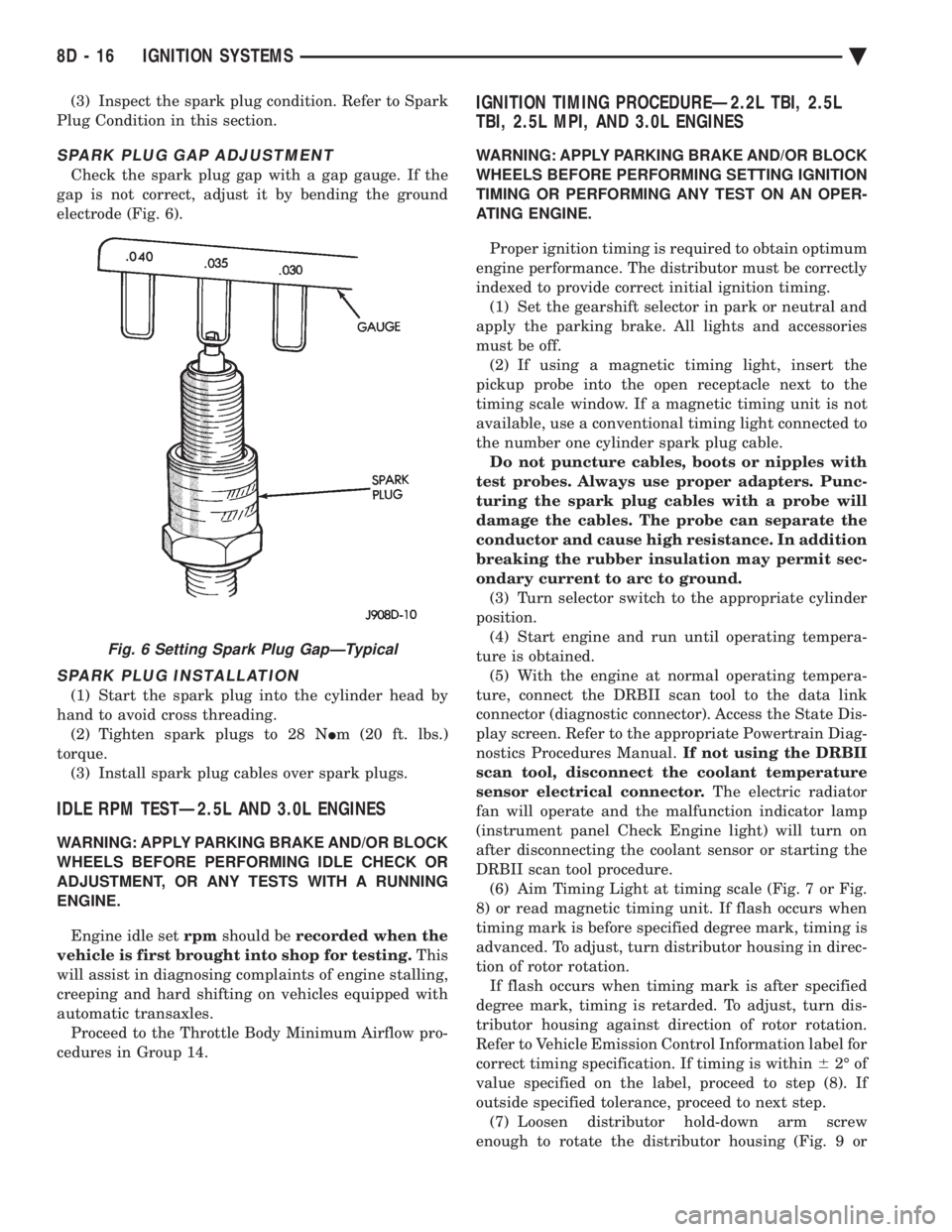
(3) Inspect the spark plug condition. Refer to Spark
Plug Condition in this section.
SPARK PLUG GAP ADJUSTMENT
Check the spark plug gap with a gap gauge. If the
gap is not correct, adjust it by bending the ground
electrode (Fig. 6).
SPARK PLUG INSTALLATION
(1) Start the spark plug into the cylinder head by
hand to avoid cross threading. (2) Tighten spark plugs to 28 N Im (20 ft. lbs.)
torque. (3) Install spark plug cables over spark plugs.
IDLE RPM TESTÐ2.5L AND 3.0L ENGINES
WARNING: APPLY PARKING BRAKE AND/OR BLOCK
WHEELS BEFORE PERFORMING IDLE CHECK OR
ADJUSTMENT, OR ANY TESTS WITH A RUNNING
ENGINE.
Engine idle set rpmshould be recorded when the
vehicle is first brought into shop for testing. This
will assist in diagnosing complaints of engine stalling,
creeping and hard shifting on vehicles equipped with
automatic transaxles. Proceed to the Throttle Body Minimum Airflow pro-
cedures in Group 14.
IGNITION TIMING PROCEDUREÐ2.2L TBI, 2.5L
TBI, 2.5L MPI, AND 3.0L ENGINES
WARNING: APPLY PARKING BRAKE AND/OR BLOCK
WHEELS BEFORE PERFORMING SETTING IGNITION
TIMING OR PERFORMING ANY TEST ON AN OPER-
ATING ENGINE.
Proper ignition timing is required to obtain optimum
engine performance. The distributor must be correctly
indexed to provide correct initial ignition timing. (1) Set the gearshift selector in park or neutral and
apply the parking brake. All lights and accessories
must be off. (2) If using a magnetic timing light, insert the
pickup probe into the open receptacle next to the
timing scale window. If a magnetic timing unit is not
available, use a conventional timing light connected to
the number one cylinder spark plug cable. Do not puncture cables, boots or nipples with
test probes. Always use proper adapters. Punc-
turing the spark plug cables with a probe will
damage the cables. The probe can separate the
conductor and cause high resistance. In addition
breaking the rubber insulation may permit sec-
ondary current to arc to ground. (3) Turn selector switch to the appropriate cylinder
position. (4) Start engine and run until operating tempera-
ture is obtained. (5) With the engine at normal operating tempera-
ture, connect the DRBII scan tool to the data link
connector (diagnostic connector). Access the State Dis-
play screen. Refer to the appropriate Powertrain Diag-
nostics Procedures Manual. If not using the DRBII
scan tool, disconnect the coolant temperature
sensor electrical connector. The electric radiator
fan will operate and the malfunction indicator lamp
(instrument panel Check Engine light) will turn on
after disconnecting the coolant sensor or starting the
DRBII scan tool procedure. (6) Aim Timing Light at timing scale (Fig. 7 or Fig.
8) or read magnetic timing unit. If flash occurs when
timing mark is before specified degree mark, timing is
advanced. To adjust, turn distributor housing in direc-
tion of rotor rotation. If flash occurs when timing mark is after specified
degree mark, timing is retarded. To adjust, turn dis-
tributor housing against direction of rotor rotation.
Refer to Vehicle Emission Control Information label for
correct timing specification. If timing is within 62É of
value specified on the label, proceed to step (8). If
outside specified tolerance, proceed to next step. (7) Loosen distributor hold-down arm screw
enough to rotate the distributor housing (Fig. 9 or
Fig. 6 Setting Spark Plug GapÐTypical
8D - 16 IGNITION SYSTEMS Ä
Page 459 of 2438
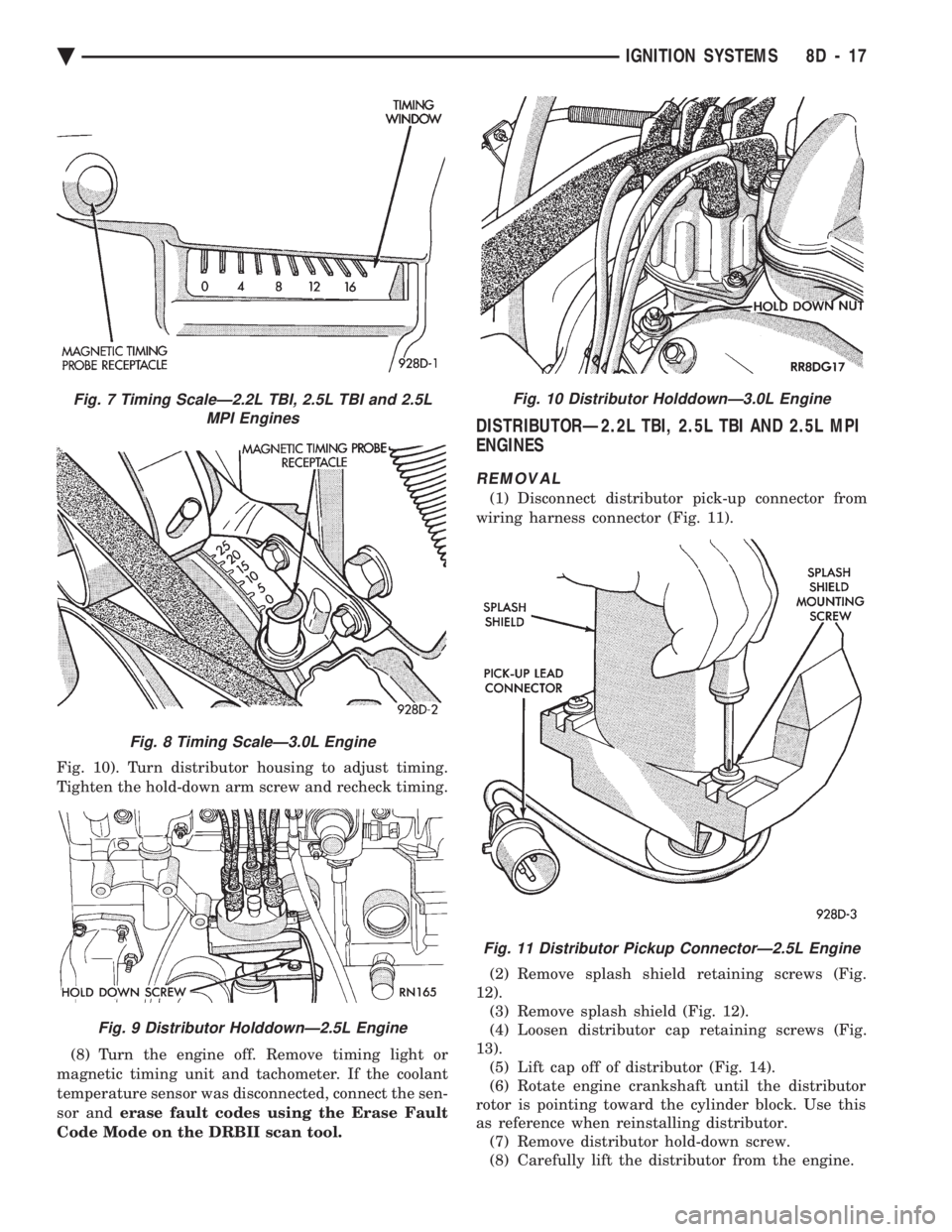
Fig. 10). Turn distributor housing to adjust timing.
Tighten the hold-down arm screw and recheck timing.
(8) Turn the engine off. Remove timing light or
magnetic timing unit and tachometer. If the coolant
temperature sensor was disconnected, connect the sen-
sor and erase fault codes using the Erase Fault
Code Mode on the DRBII scan tool.
DISTRIBUTORÐ2.2L TBI, 2.5L TBI AND 2.5L MPI
ENGINES
REMOVAL
(1) Disconnect distributor pick-up connector from
wiring harness connector (Fig. 11).
(2) Remove splash shield retaining screws (Fig.
12). (3) Remove splash shield (Fig. 12).
(4) Loosen distributor cap retaining screws (Fig.
13). (5) Lift cap off of distributor (Fig. 14).
(6) Rotate engine crankshaft until the distributor
rotor is pointing toward the cylinder block. Use this
as reference when reinstalling distributor. (7) Remove distributor hold-down screw.
(8) Carefully lift the distributor from the engine.
Fig. 10 Distributor HolddownÐ3.0L Engine
Fig. 11 Distributor Pickup ConnectorÐ2.5L Engine
Fig. 7 Timing ScaleÐ2.2L TBI, 2.5L TBI and 2.5L MPI Engines
Fig. 8 Timing ScaleÐ3.0L Engine
Fig. 9 Distributor HolddownÐ2.5L Engine
Ä IGNITION SYSTEMS 8D - 17
Page 460 of 2438
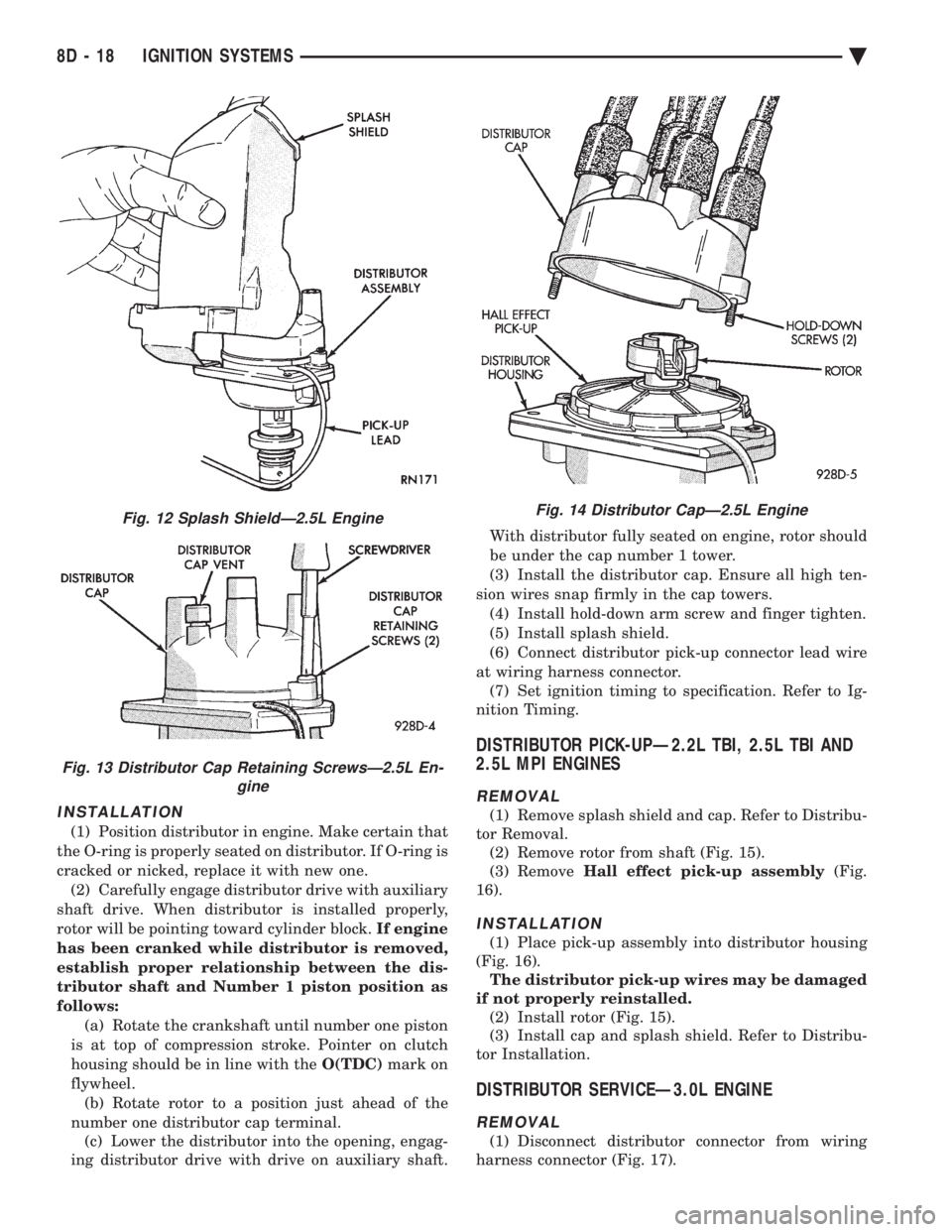
INSTALLATION
(1) Position distributor in engine. Make certain that
the O-ring is properly seated on distributor. If O-ring is
cracked or nicked, replace it with new one. (2) Carefully engage distributor drive with auxiliary
shaft drive. When distributor is installed properly,
rotor will be pointing toward cylinder block. If engine
has been cranked while distributor is removed,
establish proper relationship between the dis-
tributor shaft and Number 1 piston position as
follows: (a) Rotate the crankshaft until number one piston
is at top of compression stroke. Pointer on clutch
housing should be in line with the O(TDC)mark on
flywheel. (b) Rotate rotor to a position just ahead of the
number one distributor cap terminal. (c) Lower the distributor into the opening, engag-
ing distributor drive with drive on auxiliary shaft. With distributor fully seated on engine, rotor should
be under the cap number 1 tower.
(3) Install the distributor cap. Ensure all high ten-
sion wires snap firmly in the cap towers. (4) Install hold-down arm screw and finger tighten.
(5) Install splash shield.
(6) Connect distributor pick-up connector lead wire
at wiring harness connector. (7) Set ignition timing to specification. Refer to Ig-
nition Timing.
DISTRIBUTOR PICK-UPÐ2.2L TBI, 2.5L TBI AND
2.5L MPI ENGINES
REMOVAL
(1) Remove splash shield and cap. Refer to Distribu-
tor Removal. (2) Remove rotor from shaft (Fig. 15).
(3) Remove Hall effect pick-up assembly (Fig.
16).
INSTALLATION
(1) Place pick-up assembly into distributor housing
(Fig. 16). The distributor pick-up wires may be damaged
if not properly reinstalled. (2) Install rotor (Fig. 15).
(3) Install cap and splash shield. Refer to Distribu-
tor Installation.
DISTRIBUTOR SERVICEÐ3.0L ENGINE
REMOVAL
(1) Disconnect distributor connector from wiring
harness connector (Fig. 17).
Fig. 12 Splash ShieldÐ2.5L Engine
Fig. 13 Distributor Cap Retaining ScrewsÐ2.5L En- gine
Fig. 14 Distributor CapÐ2.5L Engine
8D - 18 IGNITION SYSTEMS Ä