CHEVROLET PLYMOUTH ACCLAIM 1993 Service Manual
Manufacturer: CHEVROLET, Model Year: 1993, Model line: PLYMOUTH ACCLAIM, Model: CHEVROLET PLYMOUTH ACCLAIM 1993Pages: 2438, PDF Size: 74.98 MB
Page 461 of 2438
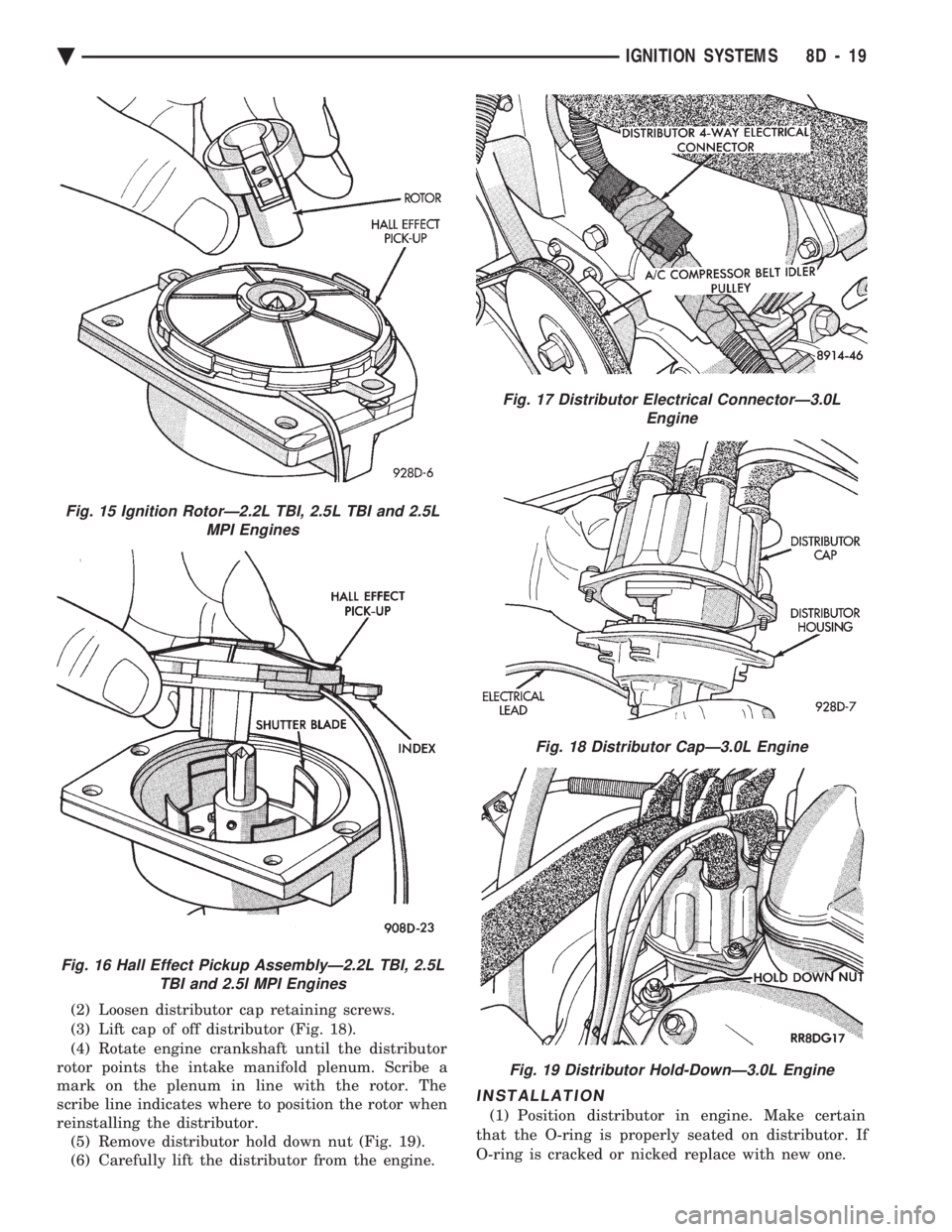
(2) Loosen distributor cap retaining screws.
(3) Lift cap of off distributor (Fig. 18).
(4) Rotate engine crankshaft until the distributor
rotor points the intake manifold plenum. Scribe a
mark on the plenum in line with the rotor. The
scribe line indicates where to position the rotor when
reinstalling the distributor. (5) Remove distributor hold down nut (Fig. 19).
(6) Carefully lift the distributor from the engine.
INSTALLATION
(1) Position distributor in engine. Make certain
that the O-ring is properly seated on distributor. If
O-ring is cracked or nicked replace with new one.
Fig. 15 Ignition RotorÐ2.2L TBI, 2.5L TBI and 2.5L MPI Engines
Fig. 16 Hall Effect Pickup AssemblyÐ2.2L TBI, 2.5LTBI and 2.5l MPI Engines
Fig. 17 Distributor Electrical ConnectorÐ3.0L Engine
Fig. 18 Distributor CapÐ3.0L Engine
Fig. 19 Distributor Hold-DownÐ3.0L Engine
Ä IGNITION SYSTEMS 8D - 19
Page 462 of 2438
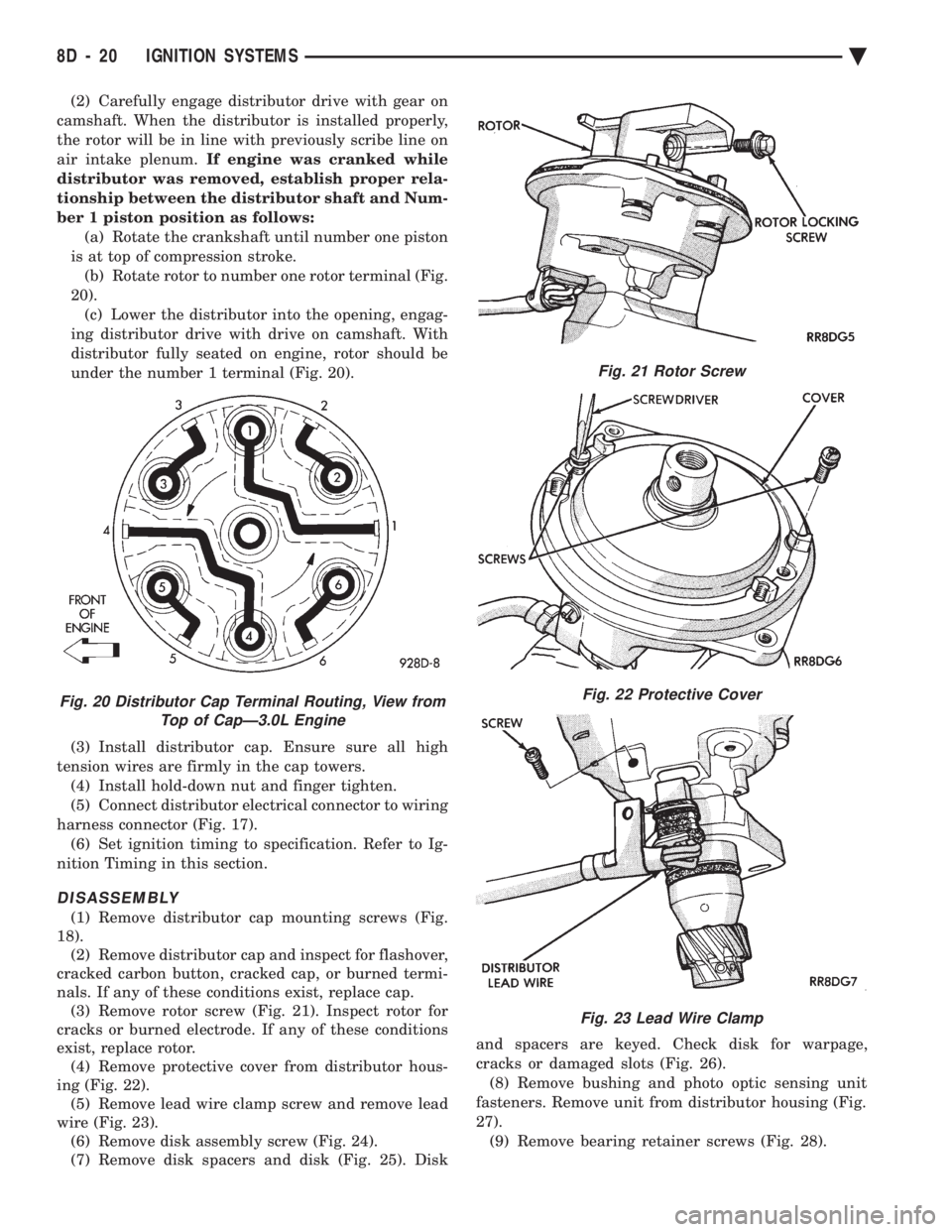
(2) Carefully engage distributor drive with gear on
camshaft. When the distributor is installed properly,
the rotor will be in line with previously scribe line on
air intake plenum. If engine was cranked while
distributor was removed, establish proper rela-
tionship between the distributor shaft and Num-
ber 1 piston position as follows: (a) Rotate the crankshaft until number one piston
is at top of compression stroke. (b) Rotate rotor to number one rotor terminal (Fig.
20). (c) Lower the distributor into the opening, engag-
ing distributor drive with drive on camshaft. With
distributor fully seated on engine, rotor should be
under the number 1 terminal (Fig. 20).
(3) Install distributor cap. Ensure sure all high
tension wires are firmly in the cap towers. (4) Install hold-down nut and finger tighten.
(5) Connect distributor electrical connector to wiring
harness connector (Fig. 17). (6) Set ignition timing to specification. Refer to Ig-
nition Timing in this section.
DISASSEMBLY
(1) Remove distributor cap mounting screws (Fig.
18). (2) Remove distributor cap and inspect for flashover,
cracked carbon button, cracked cap, or burned termi-
nals. If any of these conditions exist, replace cap. (3) Remove rotor screw (Fig. 21). Inspect rotor for
cracks or burned electrode. If any of these conditions
exist, replace rotor. (4) Remove protective cover from distributor hous-
ing (Fig. 22). (5) Remove lead wire clamp screw and remove lead
wire (Fig. 23). (6) Remove disk assembly screw (Fig. 24).
(7) Remove disk spacers and disk (Fig. 25). Disk and spacers are keyed. Check disk for warpage,
cracks or damaged slots (Fig. 26). (8) Remove bushing and photo optic sensing unit
fasteners. Remove unit from distributor housing (Fig.
27). (9) Remove bearing retainer screws (Fig. 28).
Fig. 21 Rotor Screw
Fig. 22 Protective Cover
Fig. 23 Lead Wire Clamp
Fig. 20 Distributor Cap Terminal Routing, View from Top of CapÐ3.0L Engine
8D - 20 IGNITION SYSTEMS Ä
Page 463 of 2438
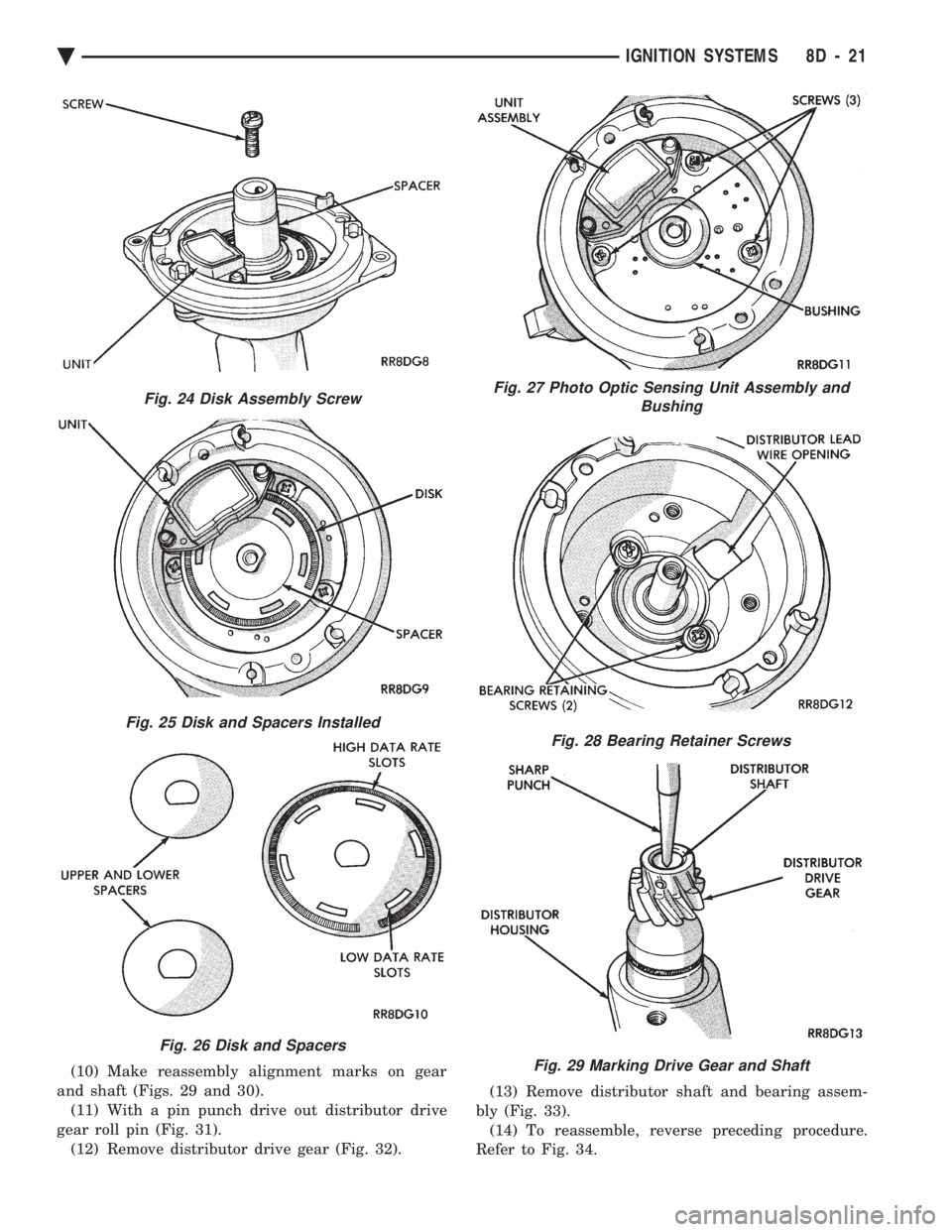
(10) Make reassembly alignment marks on gear
and shaft (Figs. 29 and 30). (11) With a pin punch drive out distributor drive
gear roll pin (Fig. 31). (12) Remove distributor drive gear (Fig. 32). (13) Remove distributor shaft and bearing assem-
bly (Fig. 33). (14) To reassemble, reverse preceding procedure.
Refer to Fig. 34.
Fig. 24 Disk Assembly Screw
Fig. 25 Disk and Spacers Installed
Fig. 26 Disk and Spacers
Fig. 27 Photo Optic Sensing Unit Assembly and Bushing
Fig. 28 Bearing Retainer Screws
Fig. 29 Marking Drive Gear and Shaft
Ä IGNITION SYSTEMS 8D - 21
Page 464 of 2438
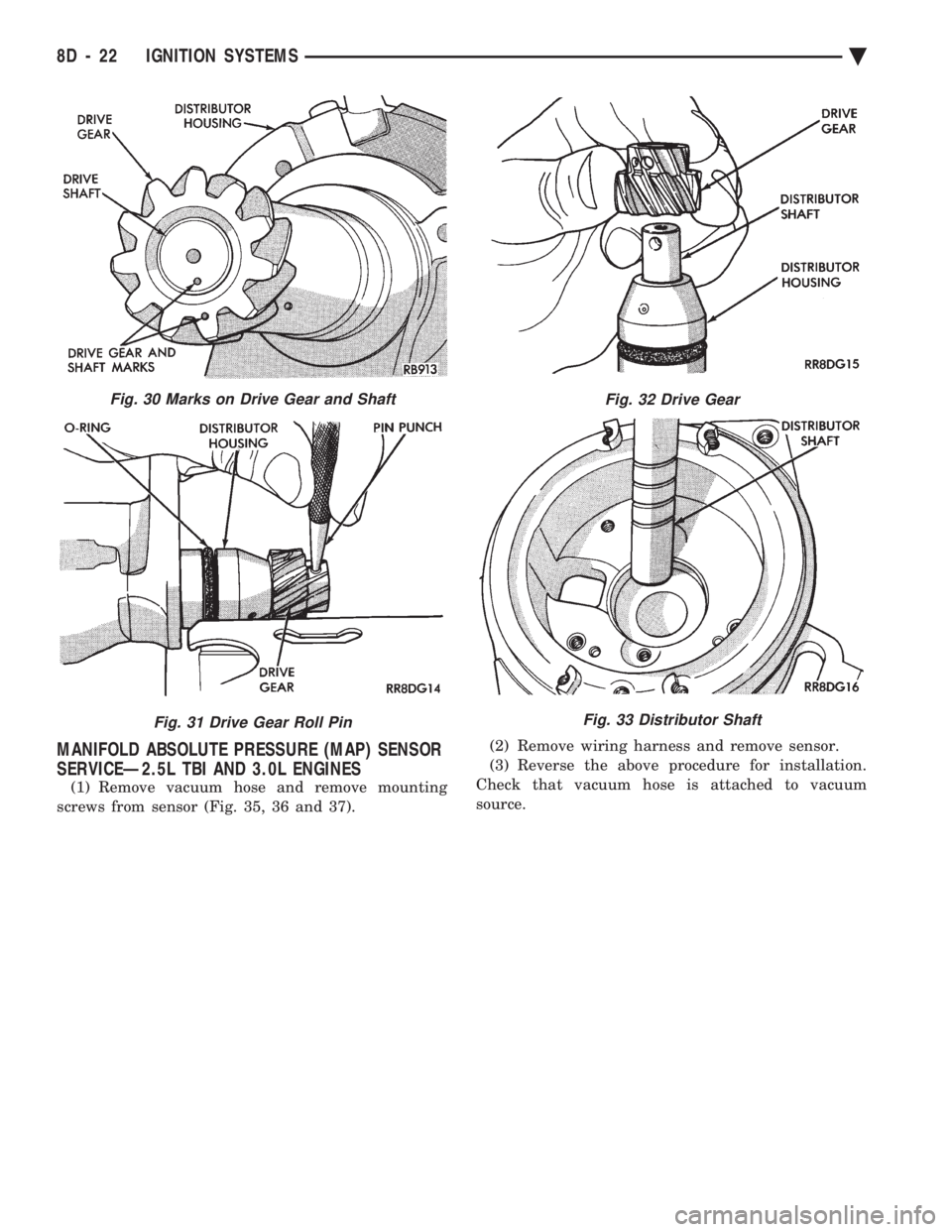
MANIFOLD ABSOLUTE PRESSURE (MAP) SENSOR
SERVICEÐ2.5L TBI AND 3.0L ENGINES
(1) Remove vacuum hose and remove mounting
screws from sensor (Fig. 35, 36 and 37). (2) Remove wiring harness and remove sensor.
(3) Reverse the above procedure for installation.
Check that vacuum hose is attached to vacuum
source.
Fig. 30 Marks on Drive Gear and Shaft
Fig. 31 Drive Gear Roll Pin
Fig. 32 Drive Gear
Fig. 33 Distributor Shaft
8D - 22 IGNITION SYSTEMS Ä
Page 465 of 2438
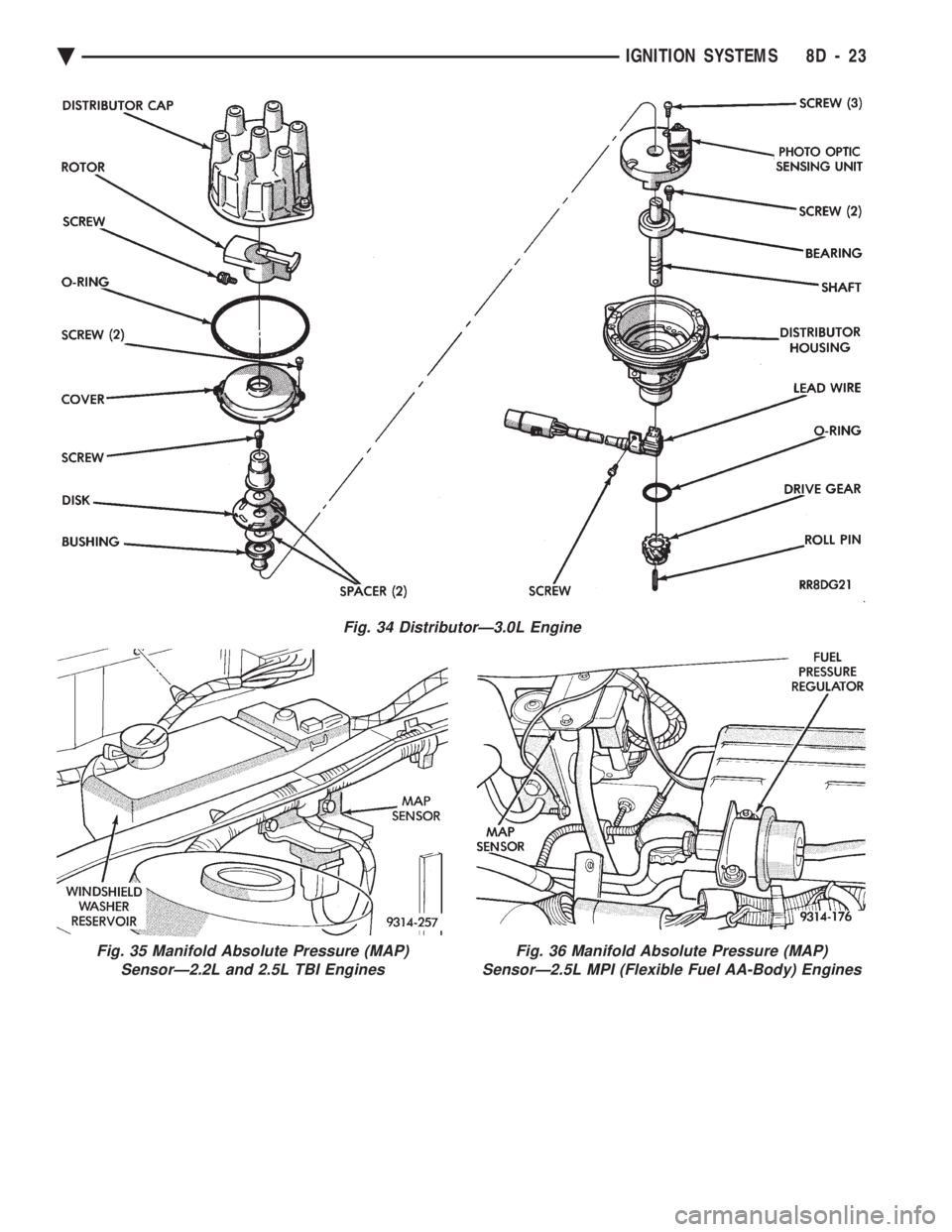
Fig. 35 Manifold Absolute Pressure (MAP) SensorÐ2.2L and 2.5L TBI EnginesFig. 36 Manifold Absolute Pressure (MAP)
SensorÐ2.5L MPI (Flexible Fuel AA-Body) Engines
Fig. 34 DistributorÐ3.0L Engine
Ä IGNITION SYSTEMS 8D - 23
Page 466 of 2438
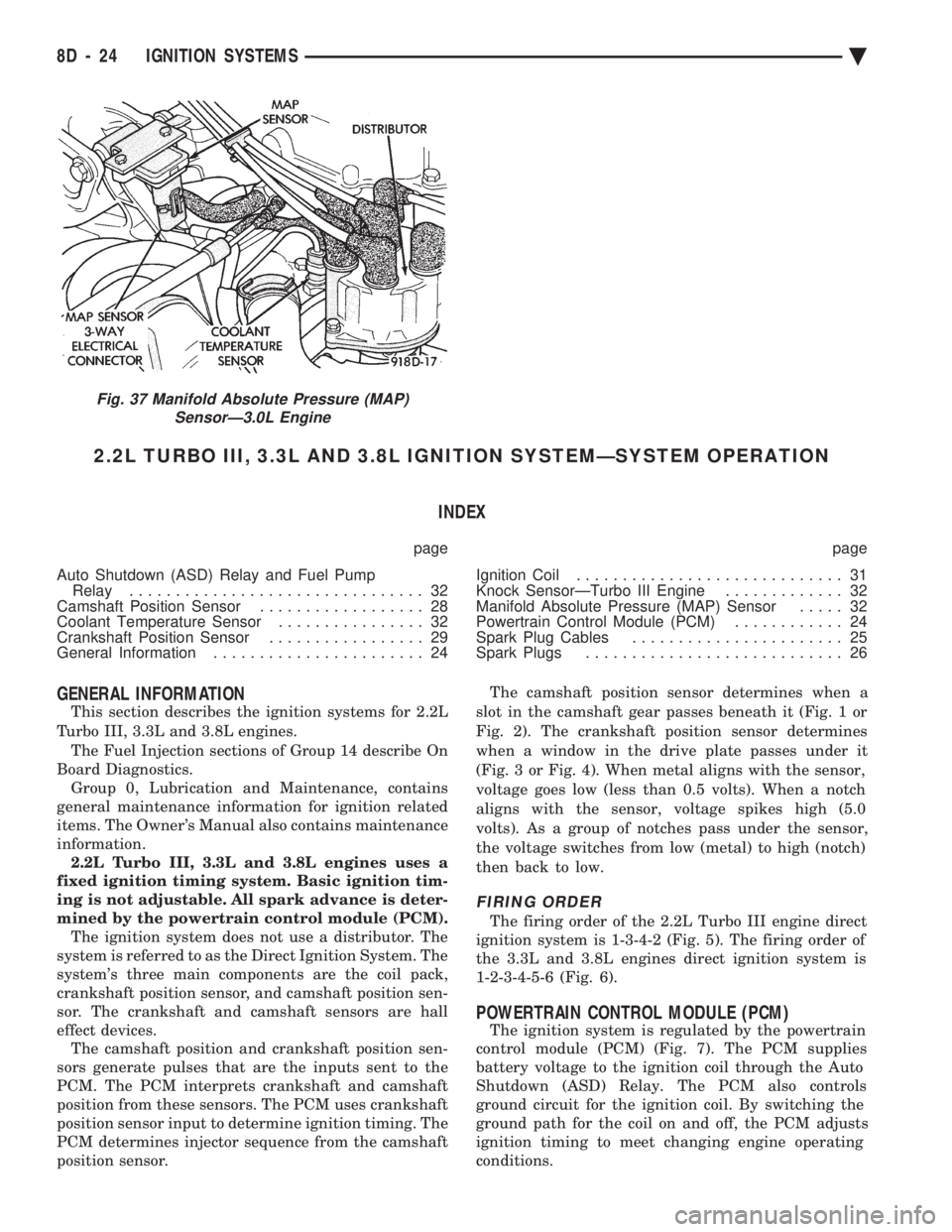
2.2L TURBO III, 3.3L AND 3.8L IGNITION SYSTEMÐSYSTEM OPERATION INDEX
page page
Auto Shutdown (ASD) Relay and Fuel Pump Relay ................................ 32
Camshaft Position Sensor .................. 28
Coolant Temperature Sensor ................ 32
Crankshaft Position Sensor ................. 29
General Information ....................... 24 Ignition Coil
............................. 31
Knock SensorÐTurbo III Engine ............. 32
Manifold Absolute Pressure (MAP) Sensor ..... 32
Powertrain Control Module (PCM) ............ 24
Spark Plug Cables ....................... 25
Spark Plugs ............................ 26
GENERAL INFORMATION
This section describes the ignition systems for 2.2L
Turbo III, 3.3L and 3.8L engines. The Fuel Injection sections of Group 14 describe On
Board Diagnostics. Group 0, Lubrication and Maintenance, contains
general maintenance information for ignition related
items. The Owner's Manual also contains maintenance
information. 2.2L Turbo III, 3.3L and 3.8L engines uses a
fixed ignition timing system. Basic ignition tim-
ing is not adjustable. All spark advance is deter-
mined by the powertrain control module (PCM). The ignition system does not use a distributor. The
system is referred to as the Direct Ignition System. The
system's three main components are the coil pack,
crankshaft position sensor, and camshaft position sen-
sor. The crankshaft and camshaft sensors are hall
effect devices. The camshaft position and crankshaft position sen-
sors generate pulses that are the inputs sent to the
PCM. The PCM interprets crankshaft and camshaft
position from these sensors. The PCM uses crankshaft
position sensor input to determine ignition timing. The
PCM determines injector sequence from the camshaft
position sensor. The camshaft position sensor determines when a
slot in the camshaft gear passes beneath it (Fig. 1 or
Fig. 2). The crankshaft position sensor determines
when a window in the drive plate passes under it
(Fig. 3 or Fig. 4). When metal aligns with the sensor,
voltage goes low (less than 0.5 volts). When a notch
aligns with the sensor, voltage spikes high (5.0
volts). As a group of notches pass under the sensor,
the voltage switches from low (metal) to high (notch)
then back to low.
FIRING ORDER
The firing order of the 2.2L Turbo III engine direct
ignition system is 1-3-4-2 (Fig. 5). The firing order of
the 3.3L and 3.8L engines direct ignition system is
1-2-3-4-5-6 (Fig. 6).
POWERTRAIN CONTROL MODULE (PCM)
The ignition system is regulated by the powertrain
control module (PCM) (Fig. 7). The PCM supplies
battery voltage to the ignition coil through the Auto
Shutdown (ASD) Relay. The PCM also controls
ground circuit for the ignition coil. By switching the
ground path for the coil on and off, the PCM adjusts
ignition timing to meet changing engine operating
conditions.
Fig. 37 Manifold Absolute Pressure (MAP) SensorÐ3.0L Engine
8D - 24 IGNITION SYSTEMS Ä
Page 467 of 2438
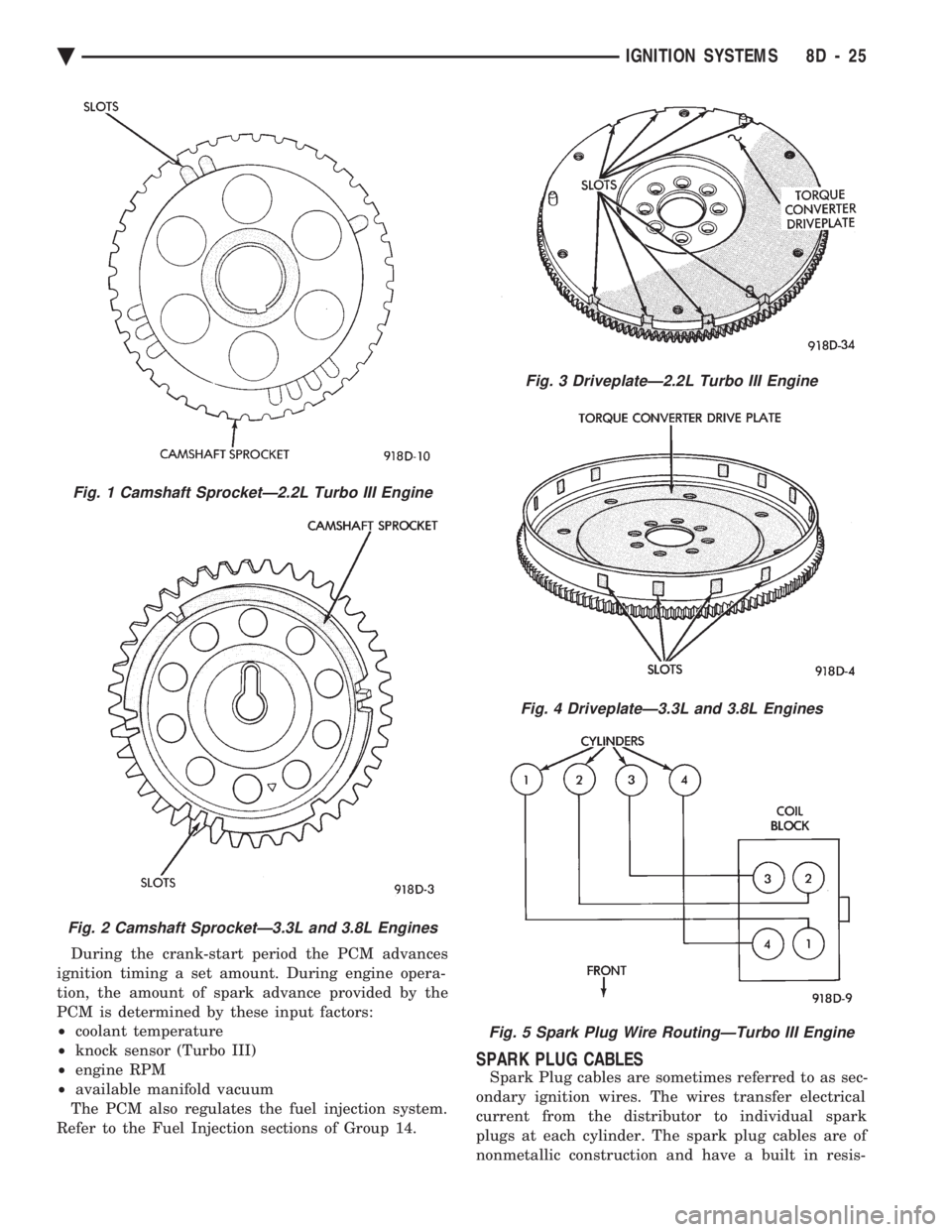
During the crank-start period the PCM advances
ignition timing a set amount. During engine opera-
tion, the amount of spark advance provided by the
PCM is determined by these input factors:
² coolant temperature
² knock sensor (Turbo III)
² engine RPM
² available manifold vacuum
The PCM also regulates the fuel injection system.
Refer to the Fuel Injection sections of Group 14.
SPARK PLUG CABLES
Spark Plug cables are sometimes referred to as sec-
ondary ignition wires. The wires transfer electrical
current from the distributor to individual spark
plugs at each cylinder. The spark plug cables are of
nonmetallic construction and have a built in resis-
Fig. 1 Camshaft SprocketÐ2.2L Turbo III Engine
Fig. 2 Camshaft SprocketÐ3.3L and 3.8L Engines
Fig. 3 DriveplateÐ2.2L Turbo III Engine
Fig. 4 DriveplateÐ3.3L and 3.8L Engines
Fig. 5 Spark Plug Wire RoutingÐTurbo III Engine
Ä IGNITION SYSTEMS 8D - 25
Page 468 of 2438
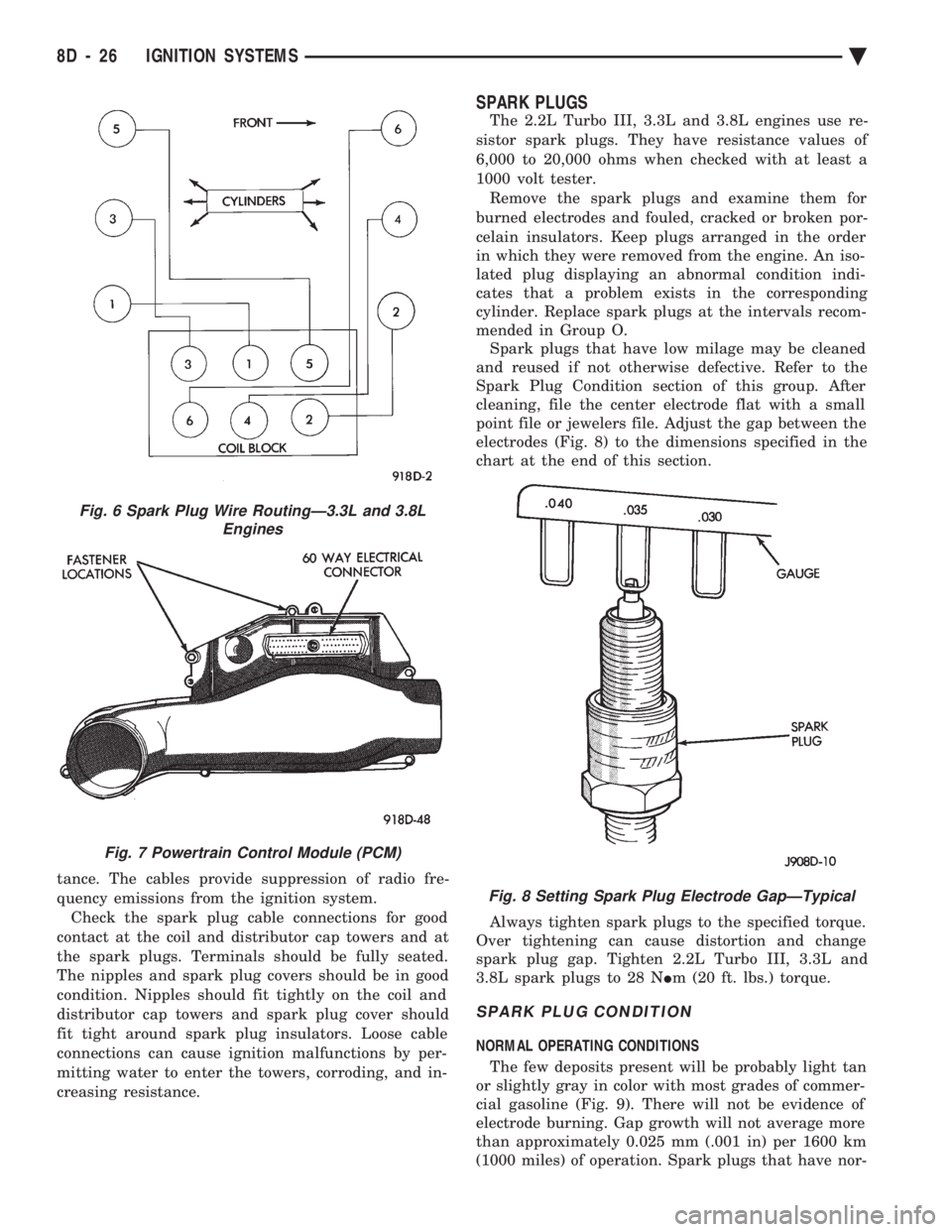
tance. The cables provide suppression of radio fre-
quency emissions from the ignition system.Check the spark plug cable connections for good
contact at the coil and distributor cap towers and at
the spark plugs. Terminals should be fully seated.
The nipples and spark plug covers should be in good
condition. Nipples should fit tightly on the coil and
distributor cap towers and spark plug cover should
fit tight around spark plug insulators. Loose cable
connections can cause ignition malfunctions by per-
mitting water to enter the towers, corroding, and in-
creasing resistance.
SPARK PLUGS
The 2.2L Turbo III, 3.3L and 3.8L engines use re-
sistor spark plugs. They have resistance values of
6,000 to 20,000 ohms when checked with at least a
1000 volt tester. Remove the spark plugs and examine them for
burned electrodes and fouled, cracked or broken por-
celain insulators. Keep plugs arranged in the order
in which they were removed from the engine. An iso-
lated plug displaying an abnormal condition indi-
cates that a problem exists in the corresponding
cylinder. Replace spark plugs at the intervals recom-
mended in Group O. Spark plugs that have low milage may be cleaned
and reused if not otherwise defective. Refer to the
Spark Plug Condition section of this group. After
cleaning, file the center electrode flat with a small
point file or jewelers file. Adjust the gap between the
electrodes (Fig. 8) to the dimensions specified in the
chart at the end of this section.
Always tighten spark plugs to the specified torque.
Over tightening can cause distortion and change
spark plug gap. Tighten 2.2L Turbo III, 3.3L and
3.8L spark plugs to 28 N Im (20 ft. lbs.) torque.
SPARK PLUG CONDITION
NORMAL OPERATING CONDITIONS
The few deposits present will be probably light tan
or slightly gray in color with most grades of commer-
cial gasoline (Fig. 9). There will not be evidence of
electrode burning. Gap growth will not average more
than approximately 0.025 mm (.001 in) per 1600 km
(1000 miles) of operation. Spark plugs that have nor-
Fig. 6 Spark Plug Wire RoutingÐ3.3L and 3.8L Engines
Fig. 7 Powertrain Control Module (PCM)
Fig. 8 Setting Spark Plug Electrode GapÐTypical
8D - 26 IGNITION SYSTEMS Ä
Page 469 of 2438
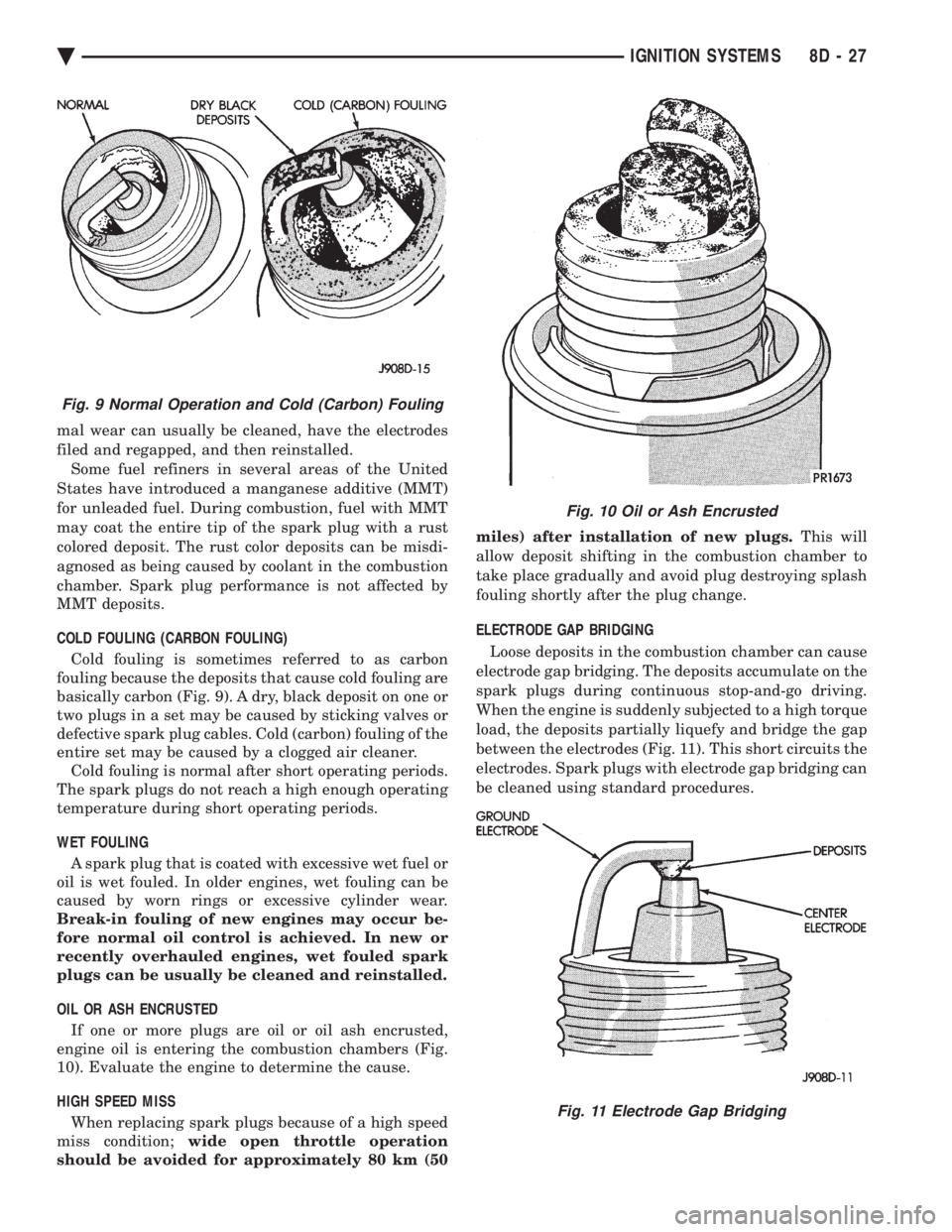
mal wear can usually be cleaned, have the electrodes
filed and regapped, and then reinstalled. Some fuel refiners in several areas of the United
States have introduced a manganese additive (MMT)
for unleaded fuel. During combustion, fuel with MMT
may coat the entire tip of the spark plug with a rust
colored deposit. The rust color deposits can be misdi-
agnosed as being caused by coolant in the combustion
chamber. Spark plug performance is not affected by
MMT deposits.
COLD FOULING (CARBON FOULING) Cold fouling is sometimes referred to as carbon
fouling because the deposits that cause cold fouling are
basically carbon (Fig. 9). A dry, black deposit on one or
two plugs in a set may be caused by sticking valves or
defective spark plug cables. Cold (carbon) fouling of the
entire set may be caused by a clogged air cleaner. Cold fouling is normal after short operating periods.
The spark plugs do not reach a high enough operating
temperature during short operating periods.
WET FOULING A spark plug that is coated with excessive wet fuel or
oil is wet fouled. In older engines, wet fouling can be
caused by worn rings or excessive cylinder wear.
Break-in fouling of new engines may occur be-
fore normal oil control is achieved. In new or
recently overhauled engines, wet fouled spark
plugs can be usually be cleaned and reinstalled.
OIL OR ASH ENCRUSTED If one or more plugs are oil or oil ash encrusted,
engine oil is entering the combustion chambers (Fig.
10). Evaluate the engine to determine the cause.
HIGH SPEED MISS When replacing spark plugs because of a high speed
miss condition; wide open throttle operation
should be avoided for approximately 80 km (50 miles) after installation of new plugs.
This will
allow deposit shifting in the combustion chamber to
take place gradually and avoid plug destroying splash
fouling shortly after the plug change.
ELECTRODE GAP BRIDGING
Loose deposits in the combustion chamber can cause
electrode gap bridging. The deposits accumulate on the
spark plugs during continuous stop-and-go driving.
When the engine is suddenly subjected to a high torque
load, the deposits partially liquefy and bridge the gap
between the electrodes (Fig. 11). This short circuits the
electrodes. Spark plugs with electrode gap bridging can
be cleaned using standard procedures.
Fig. 9 Normal Operation and Cold (Carbon) Fouling
Fig. 10 Oil or Ash Encrusted
Fig. 11 Electrode Gap Bridging
Ä IGNITION SYSTEMS 8D - 27
Page 470 of 2438
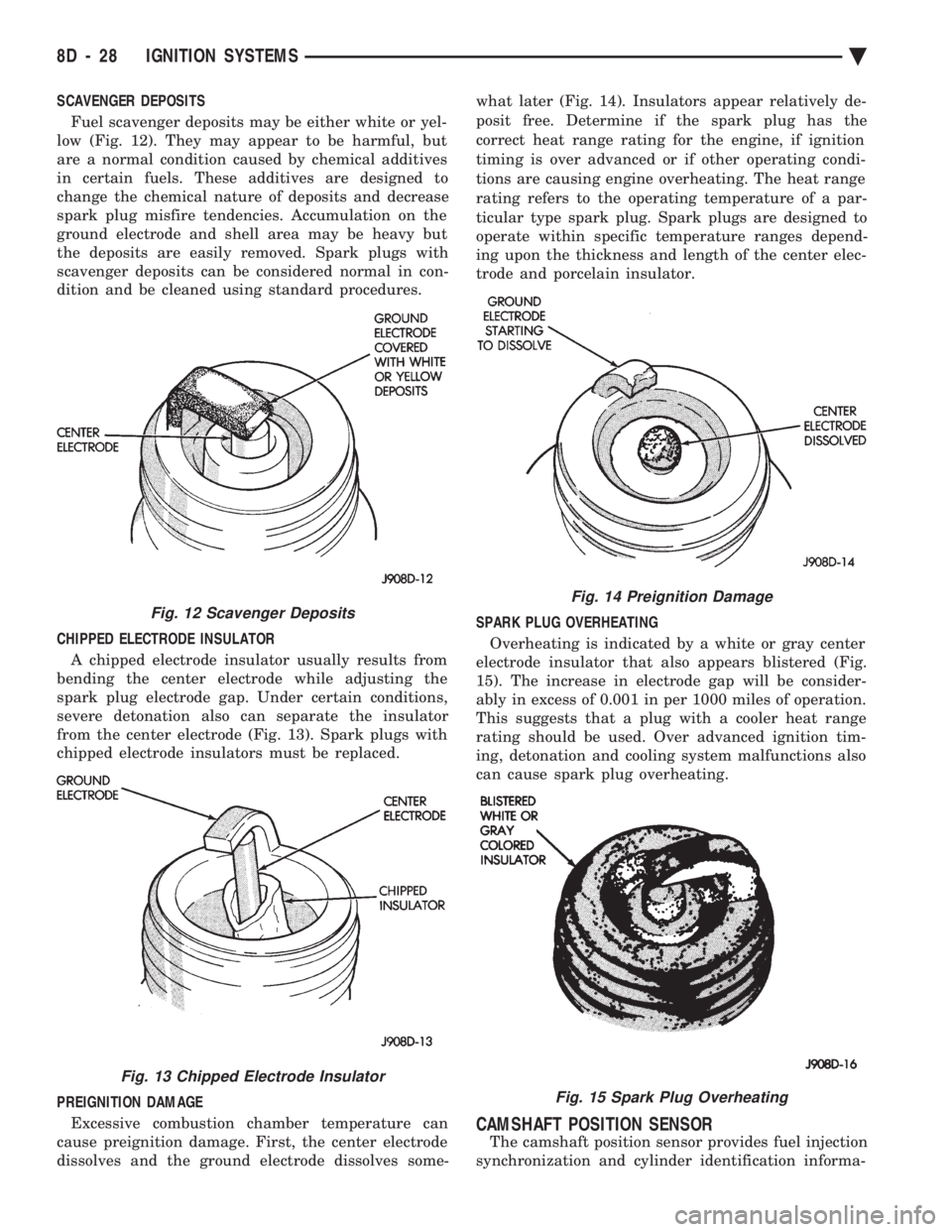
SCAVENGER DEPOSITS Fuel scavenger deposits may be either white or yel-
low (Fig. 12). They may appear to be harmful, but
are a normal condition caused by chemical additives
in certain fuels. These additives are designed to
change the chemical nature of deposits and decrease
spark plug misfire tendencies. Accumulation on the
ground electrode and shell area may be heavy but
the deposits are easily removed. Spark plugs with
scavenger deposits can be considered normal in con-
dition and be cleaned using standard procedures.
CHIPPED ELECTRODE INSULATOR A chipped electrode insulator usually results from
bending the center electrode while adjusting the
spark plug electrode gap. Under certain conditions,
severe detonation also can separate the insulator
from the center electrode (Fig. 13). Spark plugs with
chipped electrode insulators must be replaced.
PREIGNITION DAMAGE
Excessive combustion chamber temperature can
cause preignition damage. First, the center electrode
dissolves and the ground electrode dissolves some- what later (Fig. 14). Insulators appear relatively de-
posit free. Determine if the spark plug has the
correct heat range rating for the engine, if ignition
timing is over advanced or if other operating condi-
tions are causing engine overheating. The heat range
rating refers to the operating temperature of a par-
ticular type spark plug. Spark plugs are designed to
operate within specific temperature ranges depend-
ing upon the thickness and length of the center elec-
trode and porcelain insulator.
SPARK PLUG OVERHEATING
Overheating is indicated by a white or gray center
electrode insulator that also appears blistered (Fig.
15). The increase in electrode gap will be consider-
ably in excess of 0.001 in per 1000 miles of operation.
This suggests that a plug with a cooler heat range
rating should be used. Over advanced ignition tim-
ing, detonation and cooling system malfunctions also
can cause spark plug overheating.
CAMSHAFT POSITION SENSOR
The camshaft position sensor provides fuel injection
synchronization and cylinder identification informa-
Fig. 12 Scavenger Deposits
Fig. 13 Chipped Electrode Insulator
Fig. 14 Preignition Damage
Fig. 15 Spark Plug Overheating
8D - 28 IGNITION SYSTEMS Ä