CHEVROLET PLYMOUTH ACCLAIM 1993 Service Manual
Manufacturer: CHEVROLET, Model Year: 1993, Model line: PLYMOUTH ACCLAIM, Model: CHEVROLET PLYMOUTH ACCLAIM 1993Pages: 2438, PDF Size: 74.98 MB
Page 481 of 2438
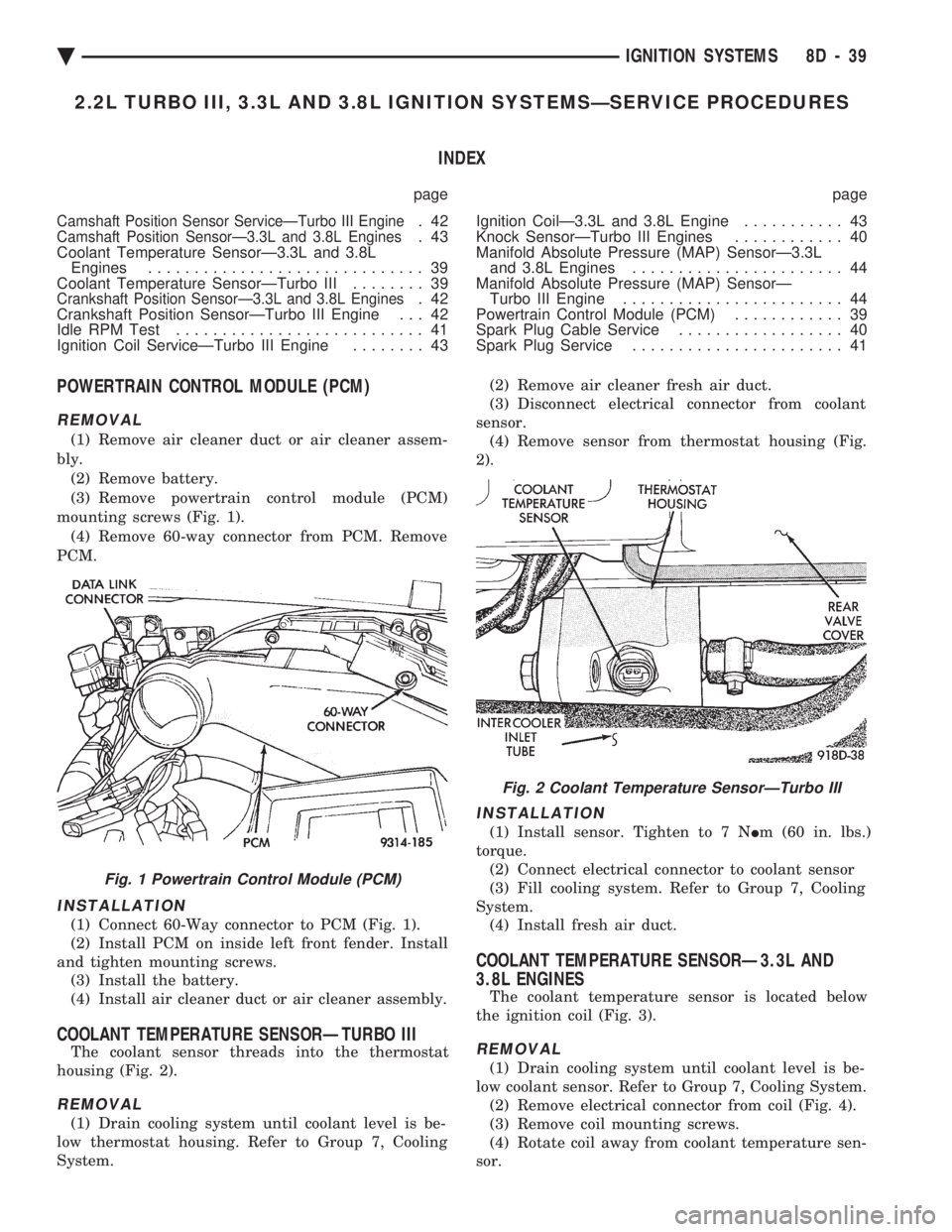
2.2L TURBO III, 3.3L AND 3.8L IGNITION SYSTEMSÐSERVICE PROCEDURES INDEX
page page
Camshaft Position Sensor ServiceÐTurbo III Engine.42Camshaft Position SensorÐ3.3L and 3.8L Engines.43
Coolant Temperature SensorÐ3.3L and 3.8L Engines .............................. 39
Coolant Temperature SensorÐTurbo III ........ 39
Crankshaft Position SensorÐ3.3L and 3.8L Engines.42
Crankshaft Position SensorÐTurbo III Engine . . . 42
Idle RPM Test ........................... 41
Ignition Coil ServiceÐTurbo III Engine ........ 43 Ignition CoilÐ3.3L and 3.8L Engine
........... 43
Knock SensorÐTurbo III Engines ............ 40
Manifold Absolute Pressure (MAP) SensorÐ3.3L and 3.8L Engines ....................... 44
Manifold Absolute Pressure (MAP) SensorÐ Turbo III Engine ........................ 44
Powertrain Control Module (PCM) ............ 39
Spark Plug Cable Service .................. 40
Spark Plug Service ....................... 41
POWERTRAIN CONTROL MODULE (PCM)
REMOVAL
(1) Remove air cleaner duct or air cleaner assem-
bly. (2) Remove battery.
(3) Remove powertrain control module (PCM)
mounting screws (Fig. 1). (4) Remove 60-way connector from PCM. Remove
PCM.
INSTALLATION
(1) Connect 60-Way connector to PCM (Fig. 1).
(2) Install PCM on inside left front fender. Install
and tighten mounting screws. (3) Install the battery.
(4) Install air cleaner duct or air cleaner assembly.
COOLANT TEMPERATURE SENSORÐTURBO III
The coolant sensor threads into the thermostat
housing (Fig. 2).
REMOVAL
(1) Drain cooling system until coolant level is be-
low thermostat housing. Refer to Group 7, Cooling
System. (2) Remove air cleaner fresh air duct.
(3) Disconnect electrical connector from coolant
sensor. (4) Remove sensor from thermostat housing (Fig.
2).
INSTALLATION
(1) Install sensor. Tighten to 7 N Im (60 in. lbs.)
torque. (2) Connect electrical connector to coolant sensor
(3) Fill cooling system. Refer to Group 7, Cooling
System. (4) Install fresh air duct.
COOLANT TEMPERATURE SENSORÐ3.3L AND
3.8L ENGINES
The coolant temperature sensor is located below
the ignition coil (Fig. 3).
REMOVAL
(1) Drain cooling system until coolant level is be-
low coolant sensor. Refer to Group 7, Cooling System. (2) Remove electrical connector from coil (Fig. 4).
(3) Remove coil mounting screws.
(4) Rotate coil away from coolant temperature sen-
sor.
Fig. 1 Powertrain Control Module (PCM)
Fig. 2 Coolant Temperature SensorÐTurbo III
Ä IGNITION SYSTEMS 8D - 39
Page 482 of 2438
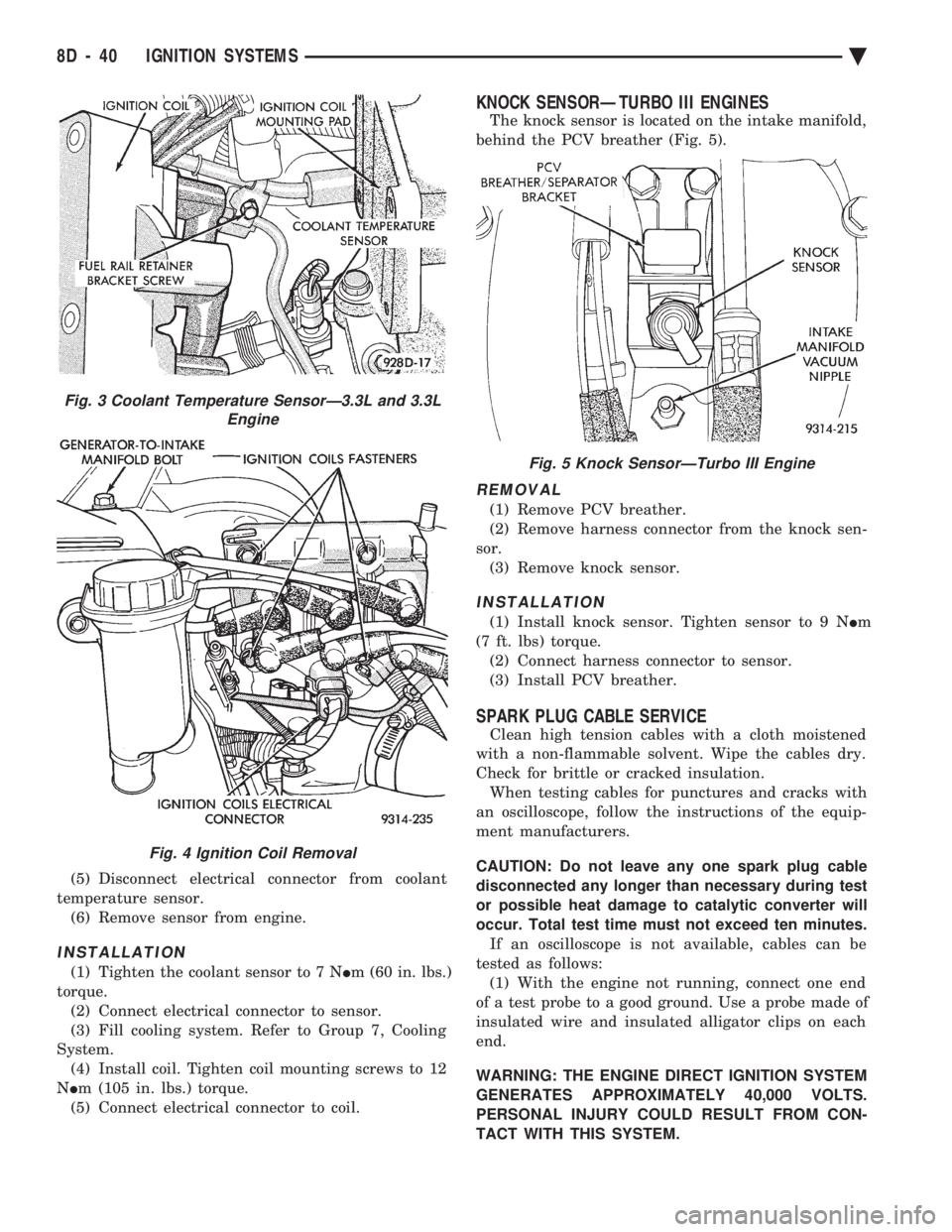
(5) Disconnect electrical connector from coolant
temperature sensor. (6) Remove sensor from engine.
INSTALLATION
(1) Tighten the coolant sensor to 7 N Im (60 in. lbs.)
torque. (2) Connect electrical connector to sensor.
(3) Fill cooling system. Refer to Group 7, Cooling
System. (4) Install coil. Tighten coil mounting screws to 12
N Im (105 in. lbs.) torque.
(5) Connect electrical connector to coil.
KNOCK SENSORÐTURBO III ENGINES
The knock sensor is located on the intake manifold,
behind the PCV breather (Fig. 5).
REMOVAL
(1) Remove PCV breather.
(2) Remove harness connector from the knock sen-
sor. (3) Remove knock sensor.
INSTALLATION
(1) Install knock sensor. Tighten sensor to 9 N Im
(7 ft. lbs) torque. (2) Connect harness connector to sensor.
(3) Install PCV breather.
SPARK PLUG CABLE SERVICE
Clean high tension cables with a cloth moistened
with a non-flammable solvent. Wipe the cables dry.
Check for brittle or cracked insulation. When testing cables for punctures and cracks with
an oscilloscope, follow the instructions of the equip-
ment manufacturers.
CAUTION: Do not leave any one spark plug cable
disconnected any longer than necessary during test
or possible heat damage to catalytic converter will
occur. Total test time must not exceed ten minutes. If an oscilloscope is not available, cables can be
tested as follows: (1) With the engine not running, connect one end
of a test probe to a good ground. Use a probe made of
insulated wire and insulated alligator clips on each
end.
WARNING: THE ENGINE DIRECT IGNITION SYSTEM
GENERATES APPROXIMATELY 40,000 VOLTS.
PERSONAL INJURY COULD RESULT FROM CON-
TACT WITH THIS SYSTEM.
Fig. 3 Coolant Temperature SensorÐ3.3L and 3.3L Engine
Fig. 4 Ignition Coil Removal
Fig. 5 Knock SensorÐTurbo III Engine
8D - 40 IGNITION SYSTEMS Ä
Page 483 of 2438
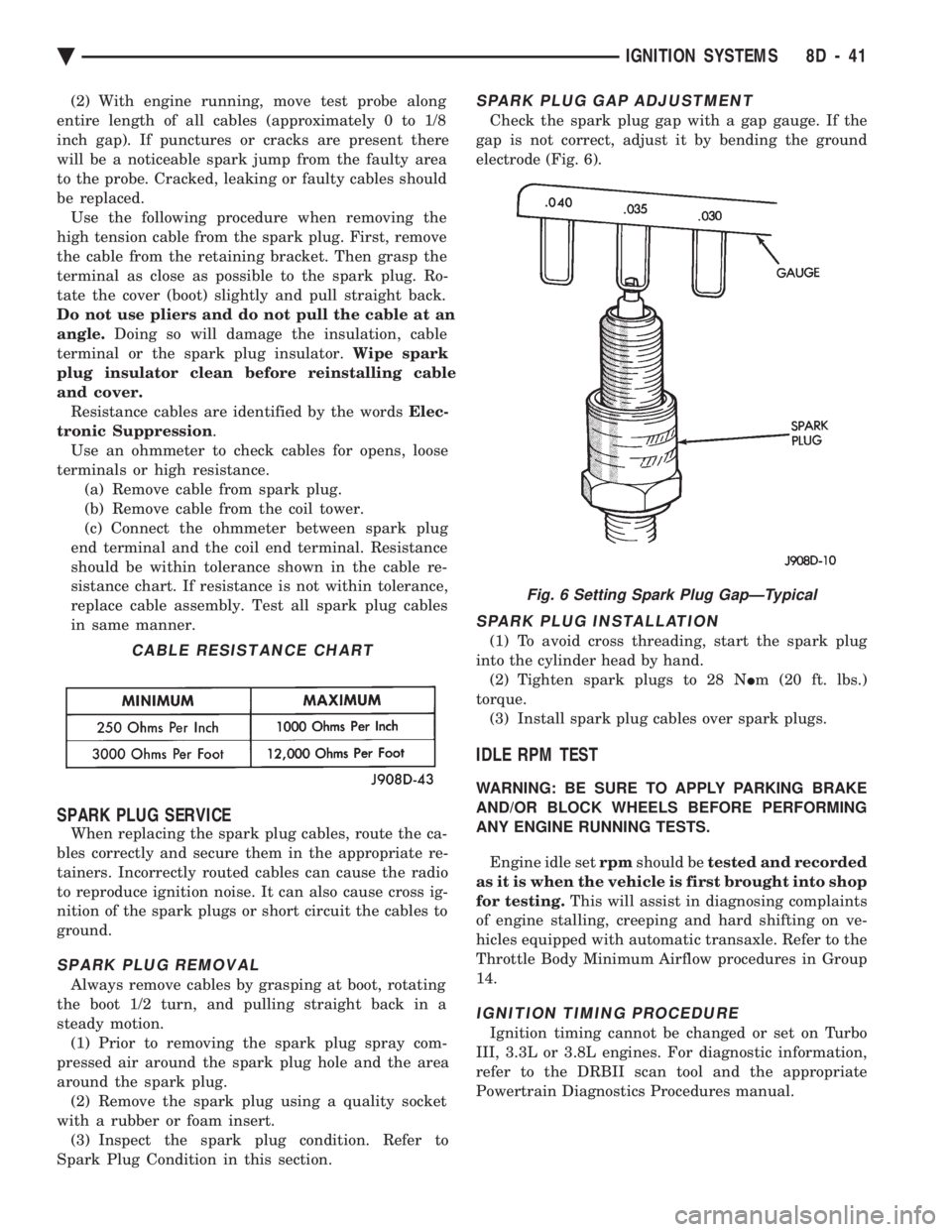
(2) With engine running, move test probe along
entire length of all cables (approximately 0 to 1/8
inch gap). If punctures or cracks are present there
will be a noticeable spark jump from the faulty area
to the probe. Cracked, leaking or faulty cables should
be replaced. Use the following procedure when removing the
high tension cable from the spark plug. First, remove
the cable from the retaining bracket. Then grasp the
terminal as close as possible to the spark plug. Ro-
tate the cover (boot) slightly and pull straight back.
Do not use pliers and do not pull the cable at an
angle. Doing so will damage the insulation, cable
terminal or the spark plug insulator. Wipe spark
plug insulator clean before reinstalling cable
and cover. Resistance cables are identified by the words Elec-
tronic Suppression .
Use an ohmmeter to check cables for opens, loose
terminals or high resistance. (a) Remove cable from spark plug.
(b) Remove cable from the coil tower.
(c) Connect the ohmmeter between spark plug
end terminal and the coil end terminal. Resistance
should be within tolerance shown in the cable re-
sistance chart. If resistance is not within tolerance,
replace cable assembly. Test all spark plug cables
in same manner.
SPARK PLUG SERVICE
When replacing the spark plug cables, route the ca-
bles correctly and secure them in the appropriate re-
tainers. Incorrectly routed cables can cause the radio
to reproduce ignition noise. It can also cause cross ig-
nition of the spark plugs or short circuit the cables to
ground.
SPARK PLUG REMOVAL
Always remove cables by grasping at boot, rotating
the boot 1/2 turn, and pulling straight back in a
steady motion. (1) Prior to removing the spark plug spray com-
pressed air around the spark plug hole and the area
around the spark plug. (2) Remove the spark plug using a quality socket
with a rubber or foam insert. (3) Inspect the spark plug condition. Refer to
Spark Plug Condition in this section.
SPARK PLUG GAP ADJUSTMENT
Check the spark plug gap with a gap gauge. If the
gap is not correct, adjust it by bending the ground
electrode (Fig. 6).
SPARK PLUG INSTALLATION
(1) To avoid cross threading, start the spark plug
into the cylinder head by hand. (2) Tighten spark plugs to 28 N Im (20 ft. lbs.)
torque. (3) Install spark plug cables over spark plugs.
IDLE RPM TEST
WARNING: BE SURE TO APPLY PARKING BRAKE
AND/OR BLOCK WHEELS BEFORE PERFORMING
ANY ENGINE RUNNING TESTS.
Engine idle set rpmshould be tested and recorded
as it is when the vehicle is first brought into shop
for testing. This will assist in diagnosing complaints
of engine stalling, creeping and hard shifting on ve-
hicles equipped with automatic transaxle. Refer to the
Throttle Body Minimum Airflow procedures in Group
14.
IGNITION TIMING PROCEDURE
Ignition timing cannot be changed or set on Turbo
III, 3.3L or 3.8L engines. For diagnostic information,
refer to the DRBII scan tool and the appropriate
Powertrain Diagnostics Procedures manual.
CABLE RESISTANCE CHART
Fig. 6 Setting Spark Plug GapÐTypical
Ä IGNITION SYSTEMS 8D - 41
Page 484 of 2438
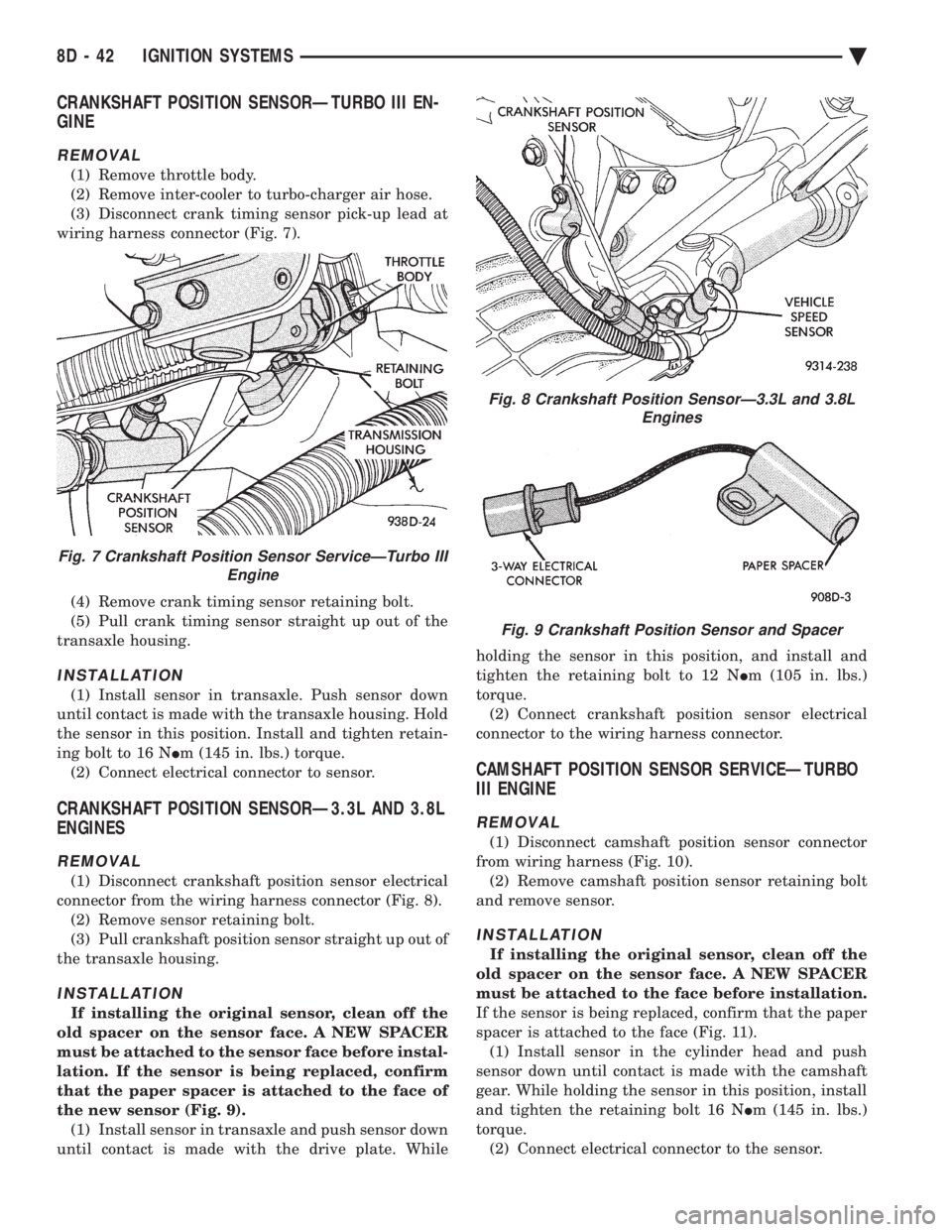
CRANKSHAFT POSITION SENSORÐTURBO III EN-
GINE
REMOVAL
(1) Remove throttle body.
(2) Remove inter-cooler to turbo-charger air hose.
(3) Disconnect crank timing sensor pick-up lead at
wiring harness connector (Fig. 7).
(4) Remove crank timing sensor retaining bolt.
(5) Pull crank timing sensor straight up out of the
transaxle housing.
INSTALLATION
(1) Install sensor in transaxle. Push sensor down
until contact is made with the transaxle housing. Hold
the sensor in this position. Install and tighten retain-
ing bolt to 16 N Im (145 in. lbs.) torque.
(2) Connect electrical connector to sensor.
CRANKSHAFT POSITION SENSORÐ3.3L AND 3.8L
ENGINES
REMOVAL
(1) Disconnect crankshaft position sensor electrical
connector from the wiring harness connector (Fig. 8). (2) Remove sensor retaining bolt.
(3) Pull crankshaft position sensor straight up out of
the transaxle housing.
INSTALLATION
If installing the original sensor, clean off the
old spacer on the sensor face. A NEW SPACER
must be attached to the sensor face before instal-
lation. If the sensor is being replaced, confirm
that the paper spacer is attached to the face of
the new sensor (Fig. 9). (1) Install sensor in transaxle and push sensor down
until contact is made with the drive plate. While holding the sensor in this position, and install and
tighten the retaining bolt to 12 N
Im (105 in. lbs.)
torque. (2) Connect crankshaft position sensor electrical
connector to the wiring harness connector.
CAMSHAFT POSITION SENSOR SERVICEÐTURBO
III ENGINE
REMOVAL
(1) Disconnect camshaft position sensor connector
from wiring harness (Fig. 10). (2) Remove camshaft position sensor retaining bolt
and remove sensor.
INSTALLATION
If installing the original sensor, clean off the
old spacer on the sensor face. A NEW SPACER
must be attached to the face before installation.
If the sensor is being replaced, confirm that the paper
spacer is attached to the face (Fig. 11). (1) Install sensor in the cylinder head and push
sensor down until contact is made with the camshaft
gear. While holding the sensor in this position, install
and tighten the retaining bolt 16 N Im (145 in. lbs.)
torque. (2) Connect electrical connector to the sensor.
Fig. 7 Crankshaft Position Sensor ServiceÐTurbo III Engine
Fig. 8 Crankshaft Position SensorÐ3.3L and 3.8LEngines
Fig. 9 Crankshaft Position Sensor and Spacer
8D - 42 IGNITION SYSTEMS Ä
Page 485 of 2438
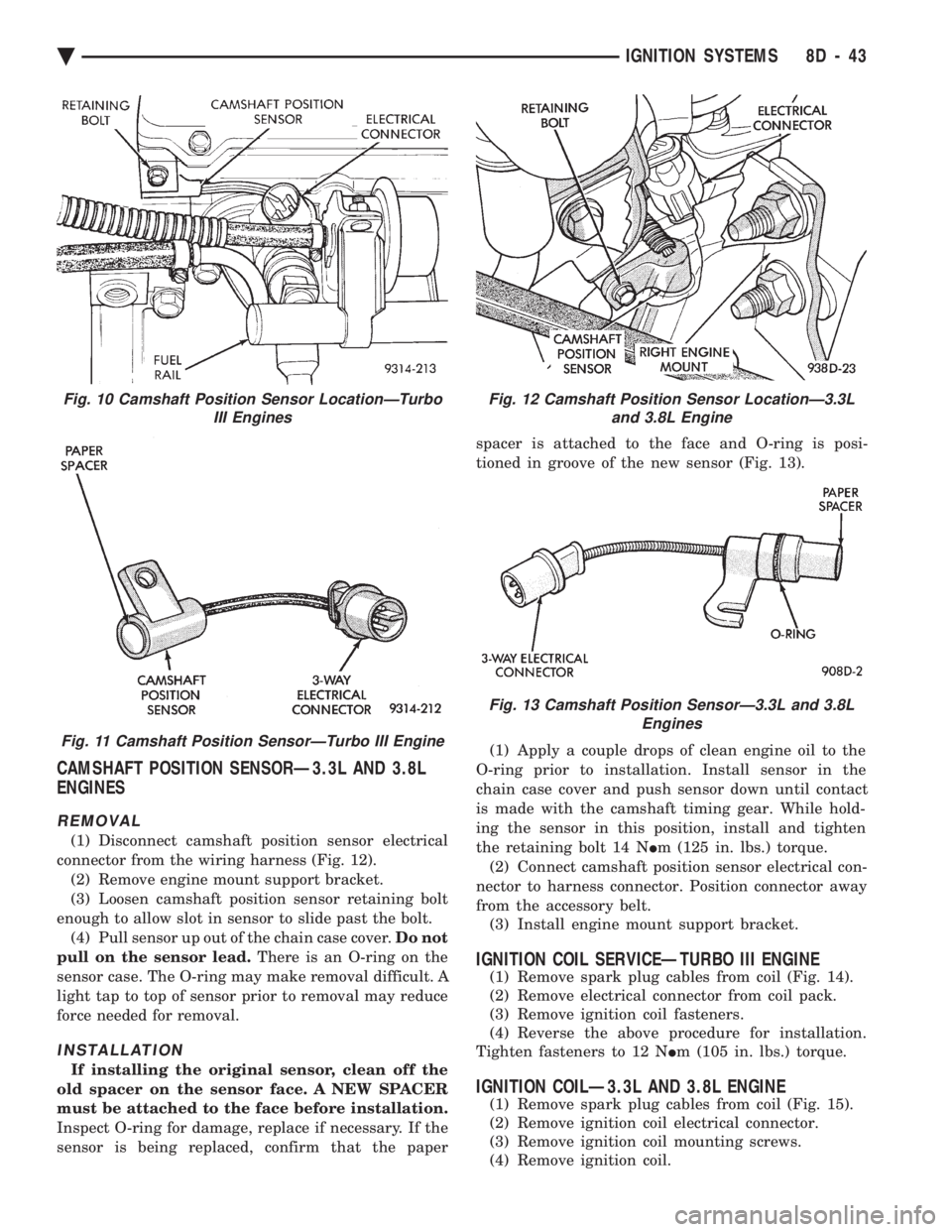
CAMSHAFT POSITION SENSORÐ3.3L AND 3.8L
ENGINES
REMOVAL
(1) Disconnect camshaft position sensor electrical
connector from the wiring harness (Fig. 12). (2) Remove engine mount support bracket.
(3) Loosen camshaft position sensor retaining bolt
enough to allow slot in sensor to slide past the bolt. (4) Pull sensor up out of the chain case cover. Do not
pull on the sensor lead. There is an O-ring on the
sensor case. The O-ring may make removal difficult. A
light tap to top of sensor prior to removal may reduce
force needed for removal.
INSTALLATION
If installing the original sensor, clean off the
old spacer on the sensor face. A NEW SPACER
must be attached to the face before installation.
Inspect O-ring for damage, replace if necessary. If the
sensor is being replaced, confirm that the paper spacer is attached to the face and O-ring is posi-
tioned in groove of the new sensor (Fig. 13).
(1) Apply a couple drops of clean engine oil to the
O-ring prior to installation. Install sensor in the
chain case cover and push sensor down until contact
is made with the camshaft timing gear. While hold-
ing the sensor in this position, install and tighten
the retaining bolt 14 N Im (125 in. lbs.) torque.
(2) Connect camshaft position sensor electrical con-
nector to harness connector. Position connector away
from the accessory belt. (3) Install engine mount support bracket.
IGNITION COIL SERVICEÐTURBO III ENGINE
(1) Remove spark plug cables from coil (Fig. 14).
(2) Remove electrical connector from coil pack.
(3) Remove ignition coil fasteners.
(4) Reverse the above procedure for installation.
Tighten fasteners to 12 N Im (105 in. lbs.) torque.
IGNITION COILÐ3.3L AND 3.8L ENGINE
(1) Remove spark plug cables from coil (Fig. 15).
(2) Remove ignition coil electrical connector.
(3) Remove ignition coil mounting screws.
(4) Remove ignition coil.
Fig. 12 Camshaft Position Sensor LocationÐ3.3L and 3.8L Engine
Fig. 13 Camshaft Position SensorÐ3.3L and 3.8L Engines
Fig. 10 Camshaft Position Sensor LocationÐTurboIII Engines
Fig. 11 Camshaft Position SensorÐTurbo III Engine
Ä IGNITION SYSTEMS 8D - 43
Page 486 of 2438
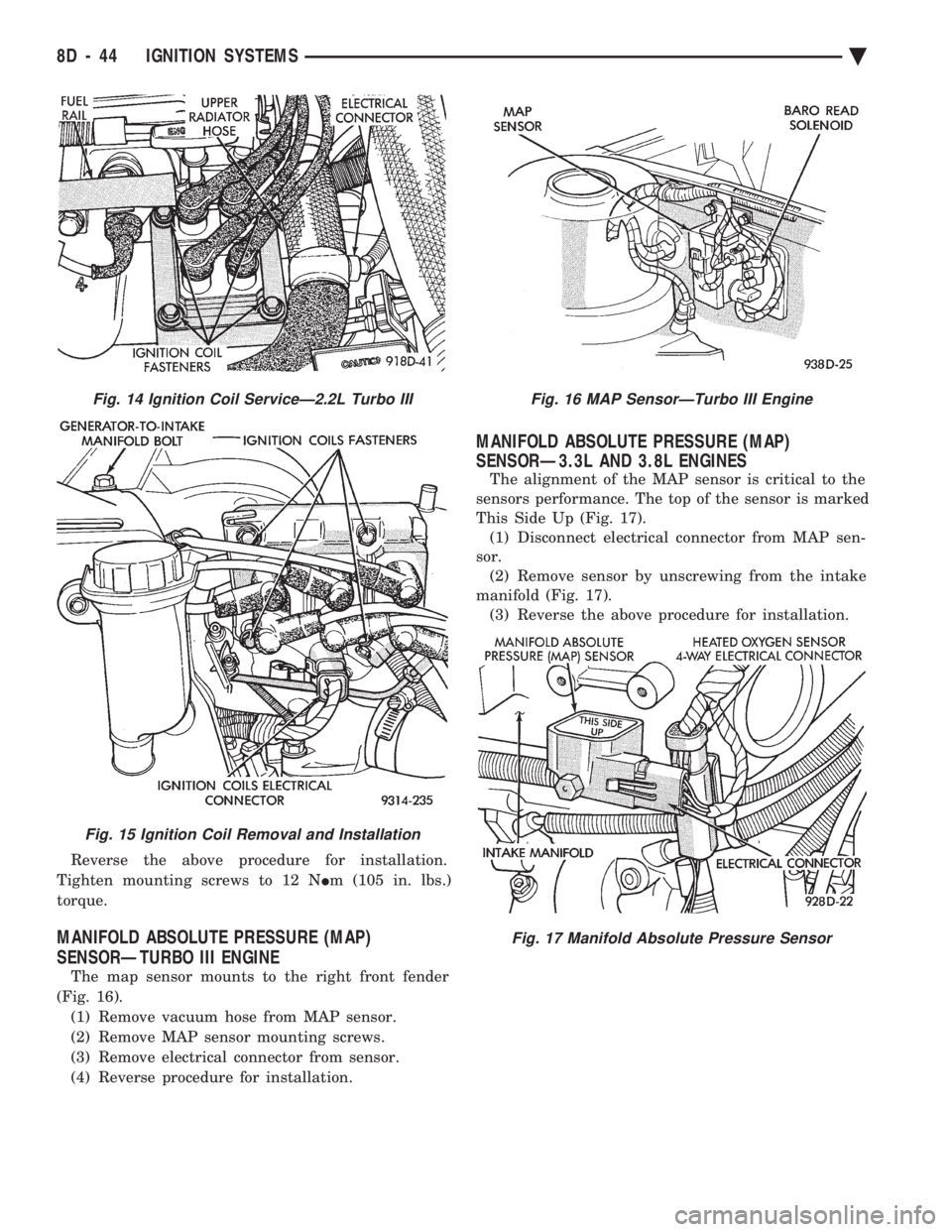
Reverse the above procedure for installation.
Tighten mounting screws to 12 N Im (105 in. lbs.)
torque.
MANIFOLD ABSOLUTE PRESSURE (MAP)
SENSORÐTURBO III ENGINE
The map sensor mounts to the right front fender
(Fig. 16). (1) Remove vacuum hose from MAP sensor.
(2) Remove MAP sensor mounting screws.
(3) Remove electrical connector from sensor.
(4) Reverse procedure for installation.
MANIFOLD ABSOLUTE PRESSURE (MAP)
SENSORÐ3.3L AND 3.8L ENGINES
The alignment of the MAP sensor is critical to the
sensors performance. The top of the sensor is marked
This Side Up (Fig. 17). (1) Disconnect electrical connector from MAP sen-
sor. (2) Remove sensor by unscrewing from the intake
manifold (Fig. 17). (3) Reverse the above procedure for installation.
Fig. 14 Ignition Coil ServiceÐ2.2L Turbo III
Fig. 15 Ignition Coil Removal and Installation
Fig. 16 MAP SensorÐTurbo III Engine
Fig. 17 Manifold Absolute Pressure Sensor
8D - 44 IGNITION SYSTEMS Ä
Page 487 of 2438
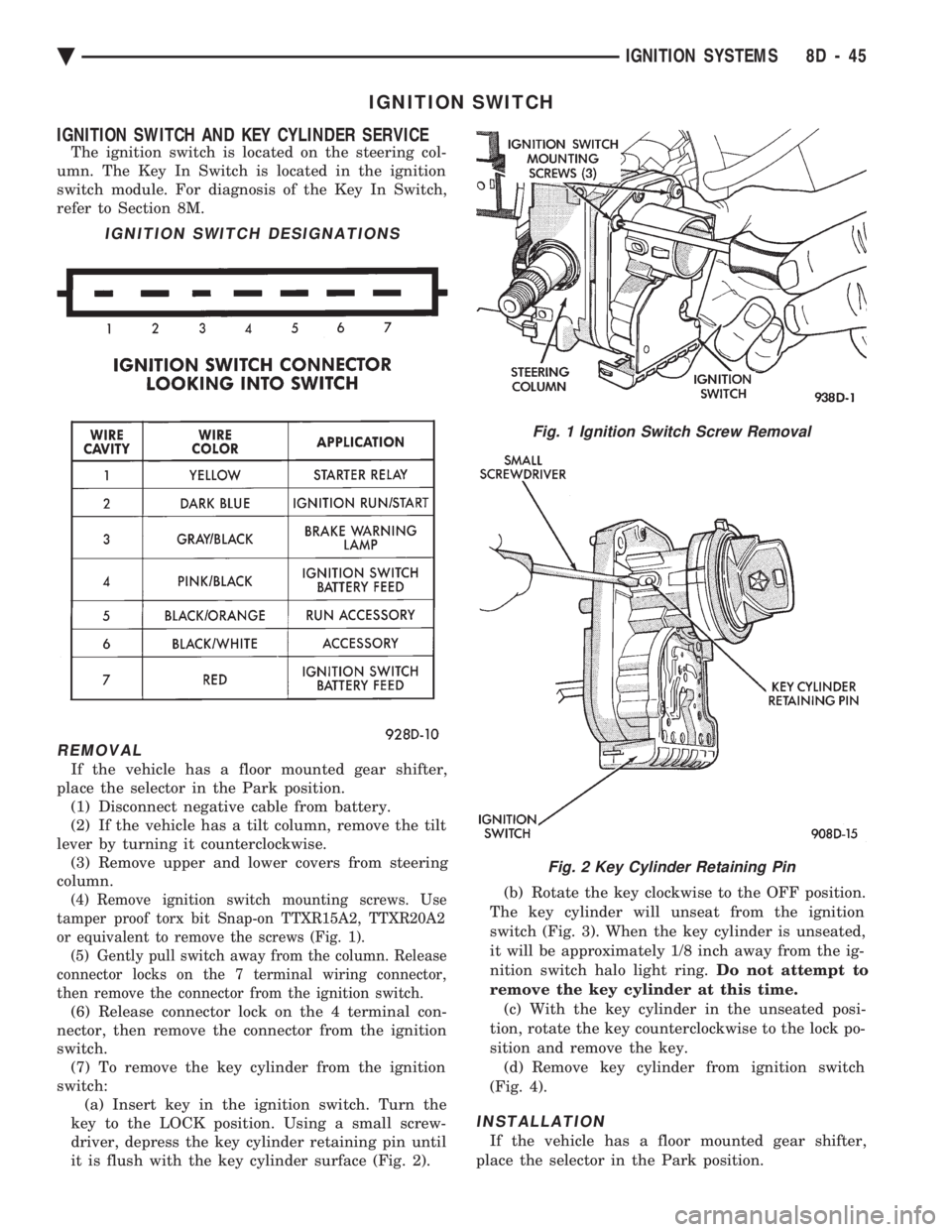
IGNITION SWITCH
IGNITION SWITCH AND KEY CYLINDER SERVICE
The ignition switch is located on the steering col-
umn. The Key In Switch is located in the ignition
switch module. For diagnosis of the Key In Switch,
refer to Section 8M.
REMOVAL
If the vehicle has a floor mounted gear shifter,
place the selector in the Park position. (1) Disconnect negative cable from battery.
(2) If the vehicle has a tilt column, remove the tilt
lever by turning it counterclockwise. (3) Remove upper and lower covers from steering
column.
(4) Remove ignition switch mounting screws. Use
tamper proof torx bit Snap-on TTXR15A2, TTXR20A2
or equivalent to remove the screws (Fig. 1). (5) Gently pull switch away from the column. Release
connector locks on the 7 terminal wiring connector,
then remove the connector from the ignition switch.
(6) Release connector lock on the 4 terminal con-
nector, then remove the connector from the ignition
switch. (7) To remove the key cylinder from the ignition
switch: (a) Insert key in the ignition switch. Turn the
key to the LOCK position. Using a small screw-
driver, depress the key cylinder retaining pin until
it is flush with the key cylinder surface (Fig. 2). (b) Rotate the key clockwise to the OFF position.
The key cylinder will unseat from the ignition
switch (Fig. 3). When the key cylinder is unseated,
it will be approximately 1/8 inch away from the ig-
nition switch halo light ring. Do not attempt to
remove the key cylinder at this time. (c) With the key cylinder in the unseated posi-
tion, rotate the key counterclockwise to the lock po-
sition and remove the key. (d) Remove key cylinder from ignition switch
(Fig. 4).
INSTALLATION
If the vehicle has a floor mounted gear shifter,
place the selector in the Park position.
IGNITION SWITCH DESIGNATIONS
Fig. 1 Ignition Switch Screw Removal
Fig. 2 Key Cylinder Retaining Pin
Ä IGNITION SYSTEMS 8D - 45
Page 488 of 2438
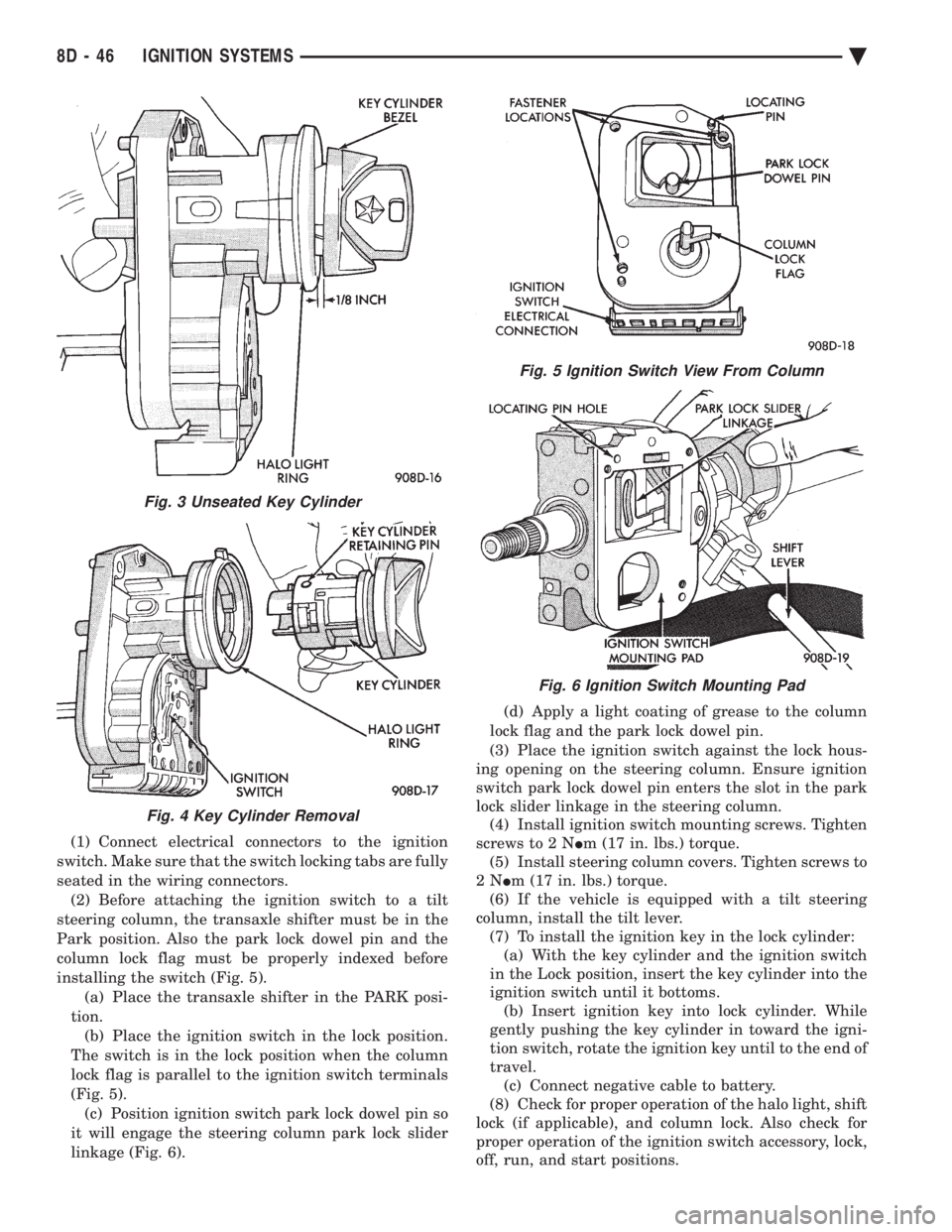
(1) Connect electrical connectors to the ignition
switch. Make sure that the switch locking tabs are fully
seated in the wiring connectors. (2) Before attaching the ignition switch to a tilt
steering column, the transaxle shifter must be in the
Park position. Also the park lock dowel pin and the
column lock flag must be properly indexed before
installing the switch (Fig. 5). (a) Place the transaxle shifter in the PARK posi-
tion. (b) Place the ignition switch in the lock position.
The switch is in the lock position when the column
lock flag is parallel to the ignition switch terminals
(Fig. 5). (c) Position ignition switch park lock dowel pin so
it will engage the steering column park lock slider
linkage (Fig. 6). (d) Apply a light coating of grease to the column
lock flag and the park lock dowel pin.
(3) Place the ignition switch against the lock hous-
ing opening on the steering column. Ensure ignition
switch park lock dowel pin enters the slot in the park
lock slider linkage in the steering column. (4) Install ignition switch mounting screws. Tighten
screws to 2 N Im (17 in. lbs.) torque.
(5) Install steering column covers. Tighten screws to
2N Im (17 in. lbs.) torque.
(6) If the vehicle is equipped with a tilt steering
column, install the tilt lever. (7) To install the ignition key in the lock cylinder:(a) With the key cylinder and the ignition switch
in the Lock position, insert the key cylinder into the
ignition switch until it bottoms. (b) Insert ignition key into lock cylinder. While
gently pushing the key cylinder in toward the igni-
tion switch, rotate the ignition key until to the end of
travel. (c) Connect negative cable to battery.
(8) Check for proper operation of the halo light, shift
lock (if applicable), and column lock. Also check for
proper operation of the ignition switch accessory, lock,
off, run, and start positions.
Fig. 3 Unseated Key Cylinder
Fig. 4 Key Cylinder Removal
Fig. 5 Ignition Switch View From Column
Fig. 6 Ignition Switch Mounting Pad
8D - 46 IGNITION SYSTEMS Ä
Page 489 of 2438
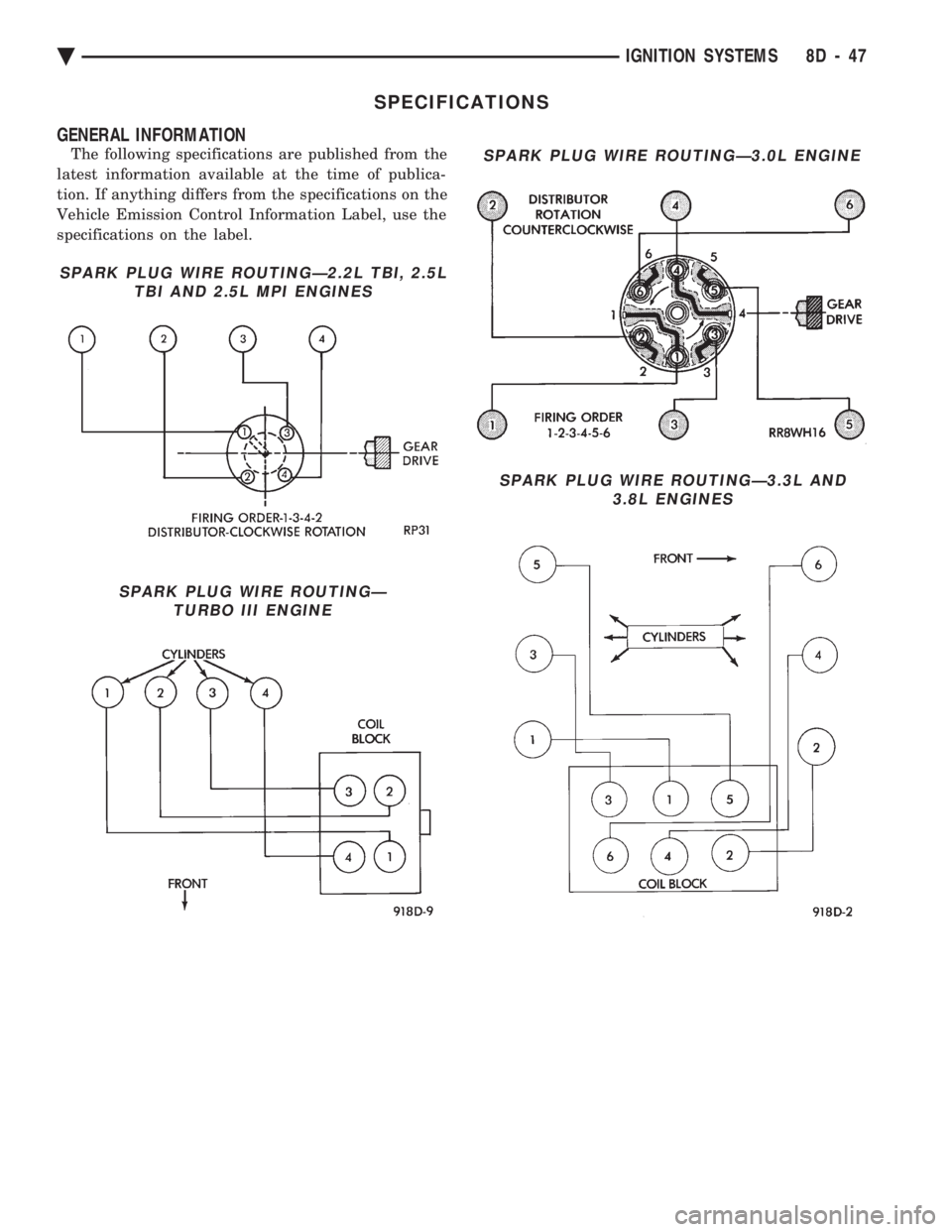
SPECIFICATIONS
GENERAL INFORMATION
The following specifications are published from the
latest information available at the time of publica-
tion. If anything differs from the specifications on the
Vehicle Emission Control Information Label, use the
specifications on the label.
SPARK PLUG WIRE ROUTINGÐ2.2L TBI, 2.5L TBI AND 2.5L MPI ENGINES
SPARK PLUG WIRE ROUTINGÐTURBO III ENGINE
SPARK PLUG WIRE ROUTINGÐ3.0L ENGINE
SPARK PLUG WIRE ROUTINGÐ3.3L AND 3.8L ENGINES
Ä IGNITION SYSTEMS 8D - 47
Page 490 of 2438
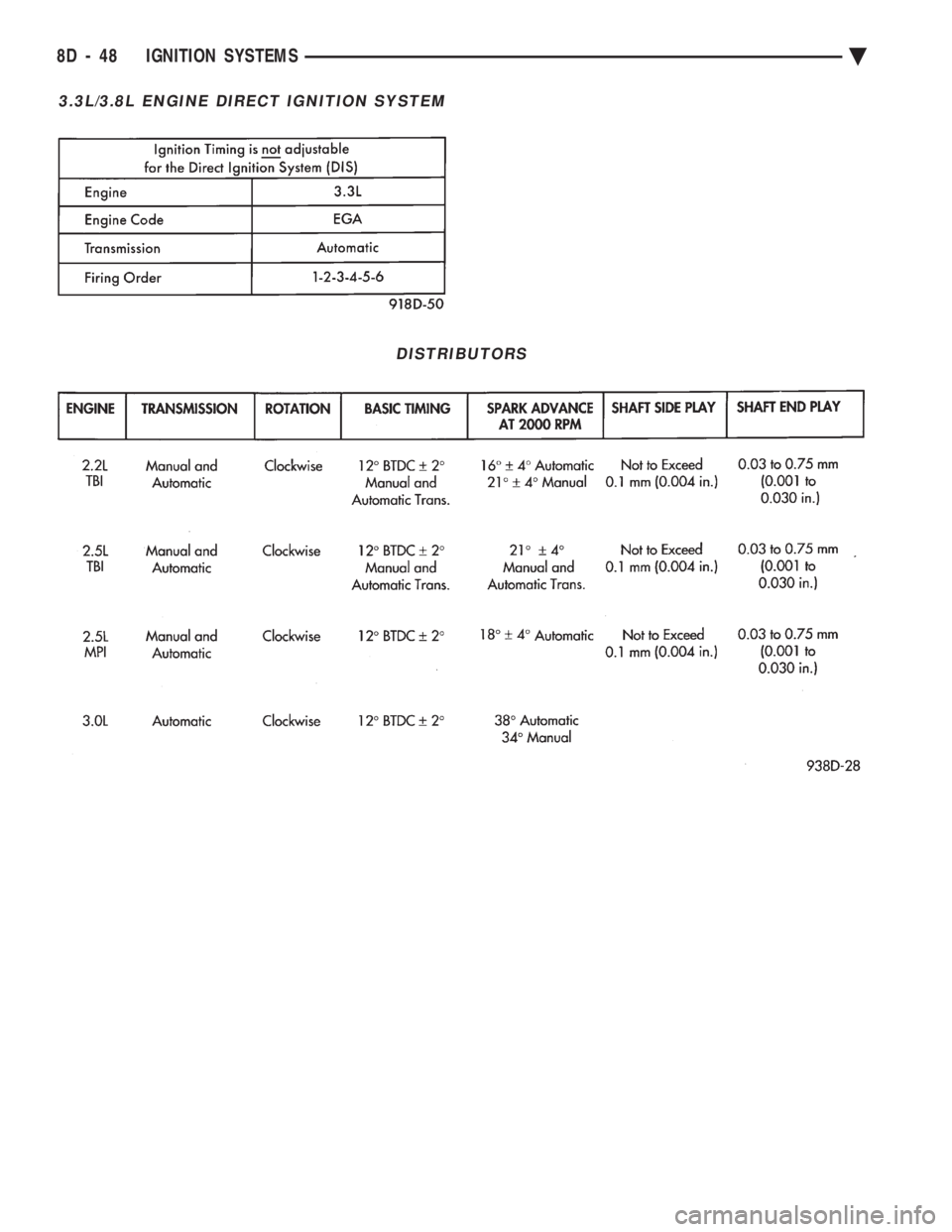
3.3L/3.8L ENGINE DIRECT IGNITION SYSTEM
DISTRIBUTORS
8D - 48 IGNITION SYSTEMS Ä