ECO mode DATSUN 210 1979 Service Manual
[x] Cancel search | Manufacturer: DATSUN, Model Year: 1979, Model line: 210, Model: DATSUN 210 1979Pages: 548, PDF Size: 28.66 MB
Page 4 of 548
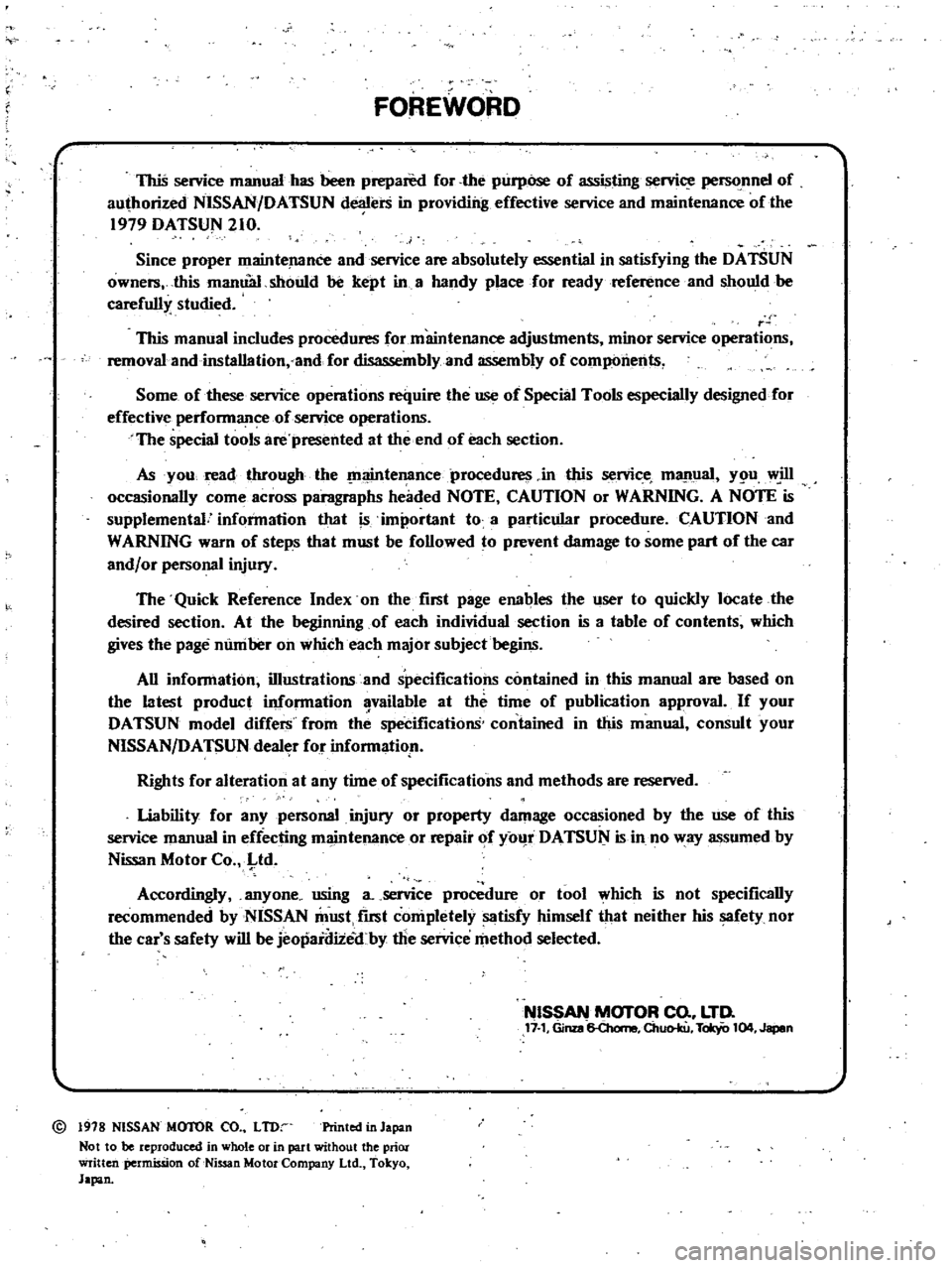
FO
REWO
RD
TJili
service
manual
has
been
prepared
for
the
purpose
of
assisting
service
personnel
of
authorized
NISSAN
DATSUN
dealerS
in
providing
effective
service
and
maintenance
of
the
1979
DATSU
II210
Since
proper
maintenance
and
service
are
absolutely
essential
in
satisfying
the
DATSUN
owners
this
manu31
should
be
kept
in
a
handy
place
for
ready
reference
and
should
be
carefully
studied
t
This
manual
includes
procedures
for
maintenance
adjustments
minor
service
operations
removal
and
instaUation
and
for
rli
mblyand
assembly
of
components
Some
of
these
service
opemtions
require
the
of
Special
Tools
especially
designed
for
effective
performance
of
service
operations
The
special
tools
are
presented
at
the
end
of
each
section
As
you
read
through
the
l
lIintenance
procedures
inthis
service
m3
lual
y
lu
w
ll
occasionally
come
across
paragraphs
headed
NOTE
CAUTION
or
WARNING
A
NOTE
is
supplemental
information
that
is
important
to
a
particular
procedure
CAUTION
and
WARNING
warn
of
steps
that
must
be
fonowed
to
prevent
damage
to
some
part
of
the
car
and
or
personal
injury
The
Quick
Reference
Index
on
the
first
page
enables
the
user
to
quickly
locate
the
desired
section
At
the
beginning
of
each
individual
section
is
a
table
of
contents
which
gives
the
page
mimber
on
which
each
major
subject
begins
An
information
illustrations
and
specifications
contained
in
this
manual
are
based
on
the
latest
product
information
available
at
the
time
of
publication
approval
If
your
DATSUN
model
differs
from
the
specificationS
contained
in
this
manual
consult
your
NISSAN
DA
TSUN
dealer
for
information
Rights
for
alteration
at
any
time
of
specifications
and
methods
are
reserved
liability
for
any
personal
injury
or
property
damage
occasioned
by
the
use
of
this
service
manual
in
effecting
maintenance
or
repair
of
Y
1
r
DATSUN
is
in
no
way
assumed
by
Nissan
Motor
Co
td
Accordingly
anyone
using
a
service
procedure
or
tool
which
is
not
specifically
recommended
by
NISSAN
must
first
completely
satisfy
himself
that
neither
his
safety
nor
the
car
s
safety
will
be
jeopaiiliiedby
the
service
method
selected
NISSAN
MOTOR
Co
lTD
17
1
G11ZlI6
chomo
chuD
kil
TokyO
l04
J
n
@
1978
N1SSAN
MOTOR
CO
LTD
Printed
in
Japan
Not
to
be
reproduced
in
whole
or
in
part
without
the
prior
writtenpermisUon
of
Nissan
Motor
Company
Ltd
Tokyo
Japan
Page 5 of 548
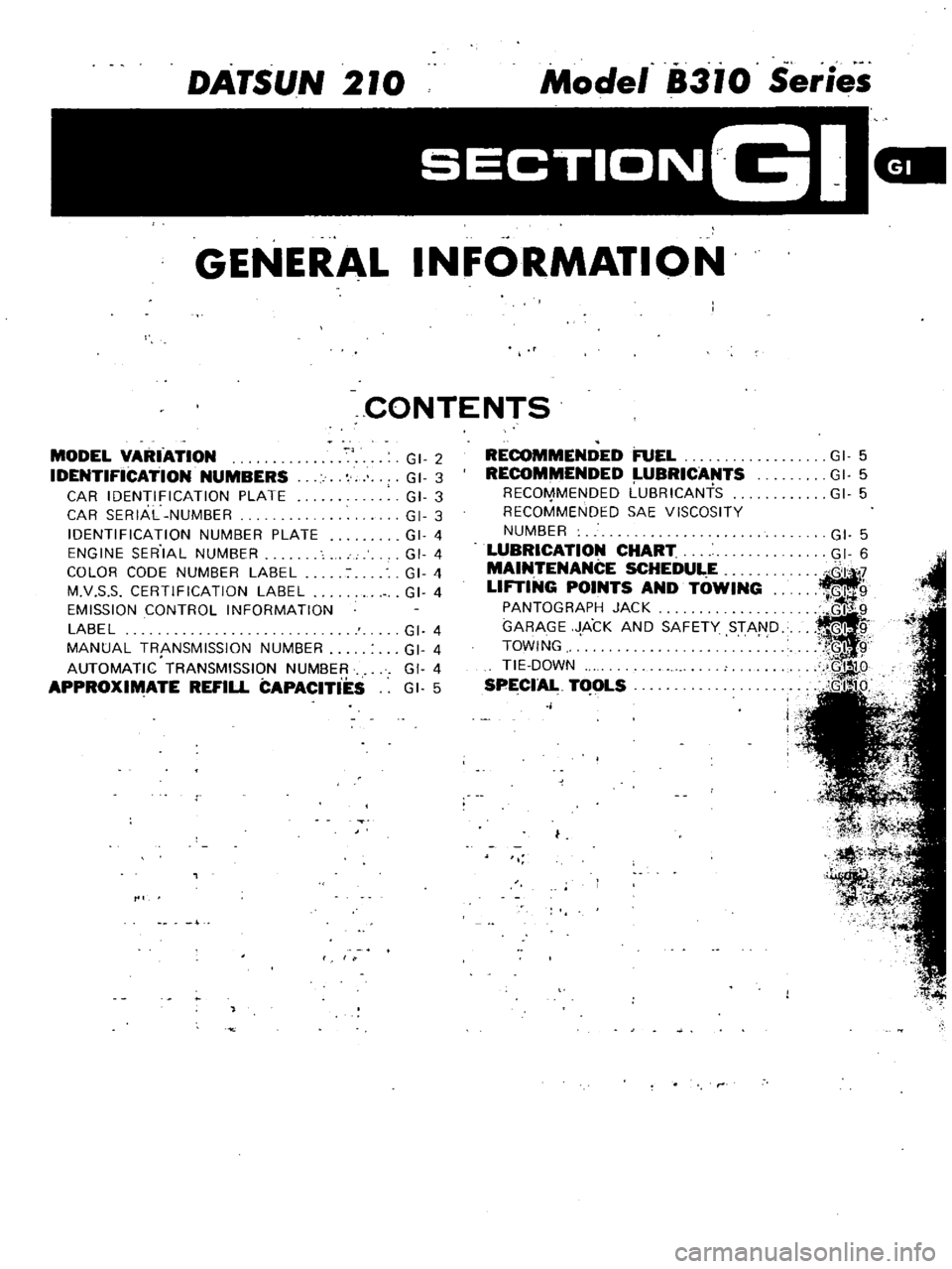
DATSUN
210
Model
8310
Series
SECTIONGI
GENERAL
INFORMATION
CONTENTS
MODEL
VARIATION
IDENTIFICATION
NUMBERS
CAR
IDENTIFICATION
PLATE
CAR
SERIAL
NUMBER
IDENTIFICATION
NUMBER
PLATE
ENGINE
SERIAL
NUMBER
COLOR
CODE
NUMBER
LABEL
M
V
S
S
CERTIFICATION
LABEL
EMISSION
CONTROL
INFORMATION
LABE
L
MANUAL
TRf
NSMISSION
NUMBER
AUTOMATIC
TRANSMISSION
NUMBER
APPROXIMATE
REFILL
CAPACITIES
GI
2
GI
3
GI
3
GI
3
GI
4
GI
4
GI
4
GI
4
GI
4
GI
4
GI
4
GI
5
RECOMMENDED
FuEL
RECOMMENDED
LUBRICANTS
RECOf
lMENDED
LUBRICANTS
RECOMMENDED
SAE
VISCOSITY
NUMBER
LUBRICATION
CHART
MAINTENANCE
SCHEDULE
LIFTING
POINTS
AND
TOWING
PANTOGRAPH
JACK
GARAGE
JA
CK
AND
SAFETY
STAND
TOWING
TIE
DOWN
SPECIAL
TOOLS
j
GI
5
GI
5
GI
5
GI
5
GI
6
Gill
j
9
GI
9
GI
eGI
9
p
G
I
O
Page 21 of 548
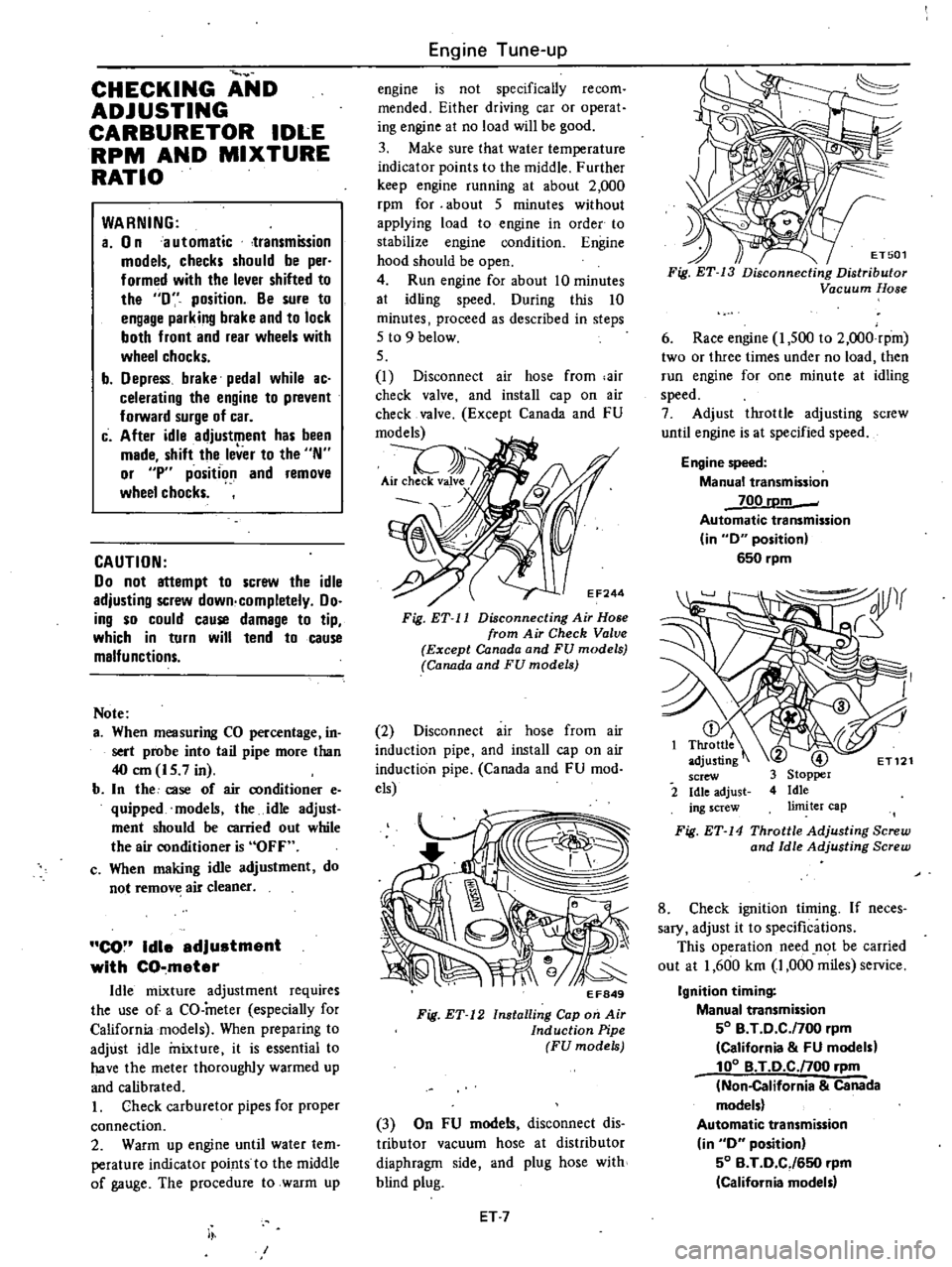
CHECKING
AND
ADJUSTING
CARBURETOR
IDLE
RPM
AND
MIXTURE
RATIO
WARNING
a
0
n
a
utomatic
transmission
models
checks
should
be
per
formed
with
the
lever
shifted
to
the
0
position
Be
sure
to
engage
parking
brake
and
to
lock
both
front
and
rear
wheels
with
wheel
chocks
b
Oepress
brake
pedal
while
ac
celerating
the
engine
to
prevent
forward
surge
of
car
c
After
idle
adjustment
has
been
made
shift
the
lever
to
the
N
or
P
positfon
and
remove
wheel
chocks
CAUTION
00
not
attempt
to
screw
the
idle
adjusting
screw
down
completely
00
ing
so
could
cause
damage
to
tip
which
in
turn
will
tend
to
cause
malfunctions
Note
a
When
measuring
CO
percentage
in
sert
probe
into
tail
pipe
more
than
40
cm
15
7
in
b
In
thee
case
of
air
conditioner
e
quipped
models
the
idle
adjust
ment
should
be
carried
out
while
the
air
conditioner
is
OFF
c
When
making
idle
adjustment
do
not
removt
air
cleaner
CO
Idle
adJustment
with
CO
meter
Idle
mixture
adjustment
requires
the
use
of
a
CO
meter
especially
for
California
models
When
preparing
to
adjust
idle
mixture
it
is
essential
to
have
the
meter
thoroughly
warmed
up
and
calibrated
1
Check
carburetor
pipes
for
proper
connection
2
Warm
up
engine
until
water
tern
perature
indicator
points
to
the
middle
of
gauge
The
procedure
to
warm
up
J
Engine
Tune
up
engine
is
not
specifically
recom
mended
Either
driving
car
or
operat
ing
engine
at
no
load
will
be
good
3
Make
sure
that
water
temperature
indicator
points
to
the
middle
Further
keep
engine
running
at
about
2
000
rpm
for
about
5
minutes
without
applying
load
to
engine
in
order
to
stabilize
engine
condition
Engine
hood
should
be
open
4
Run
engine
for
about
10
minutes
at
idling
speed
During
this
10
minutes
proceed
as
described
in
steps
5
to
9
below
5
I
Disconnect
air
hose
from
air
check
valve
and
install
cap
on
air
check
valve
Except
Canada
and
FU
models
EF244
Fig
ET
11
Disconnecting
Air
Hose
from
Air
Check
Valve
Except
Canada
and
FU
models
Canada
and
FU
models
2
Disconnect
air
hose
from
air
induction
pipe
and
install
cap
on
air
induction
pipe
Canada
and
FU
mod
els
EF849
Fig
ET
12
Installing
Cap
on
Air
Induction
Pipe
FU
models
3
On
FU
models
disconnect
dis
tributor
vacuum
hose
at
distributor
diaphragm
side
and
plug
hose
with
blind
plug
ET
7
ET501
Fig
ET
13
Disconnecting
Distributor
Vacuum
Hose
6
Race
engine
I
500
to
2
OOO
rpm
two
or
three
times
under
no
load
then
run
engine
for
one
minute
at
idling
speed
7
Adjust
throttle
adjusting
screw
until
engine
is
at
specified
speed
Engine
speed
Manual
transmission
700
rDm
Automatic
transmission
in
0
position
650
rpm
2
Fig
ET
14
Throttle
Adjusting
Screw
and
Idle
Adjusting
Screw
8
Check
ignition
timing
If
neces
sary
adjust
it
to
specifications
This
operation
need
n
t
be
carried
out
at
1
600
km
1
000
miles
service
Ignition
timing
Manual
transmission
50
B
T
0
C
f700
rpm
California
FU
models
100
B
T
O
C
noo
rpm
Non
California
Canada
models
Automatic
transmission
in
0
position
50
B
T
0
CJ650
rpm
California
model
Page 22 of 548
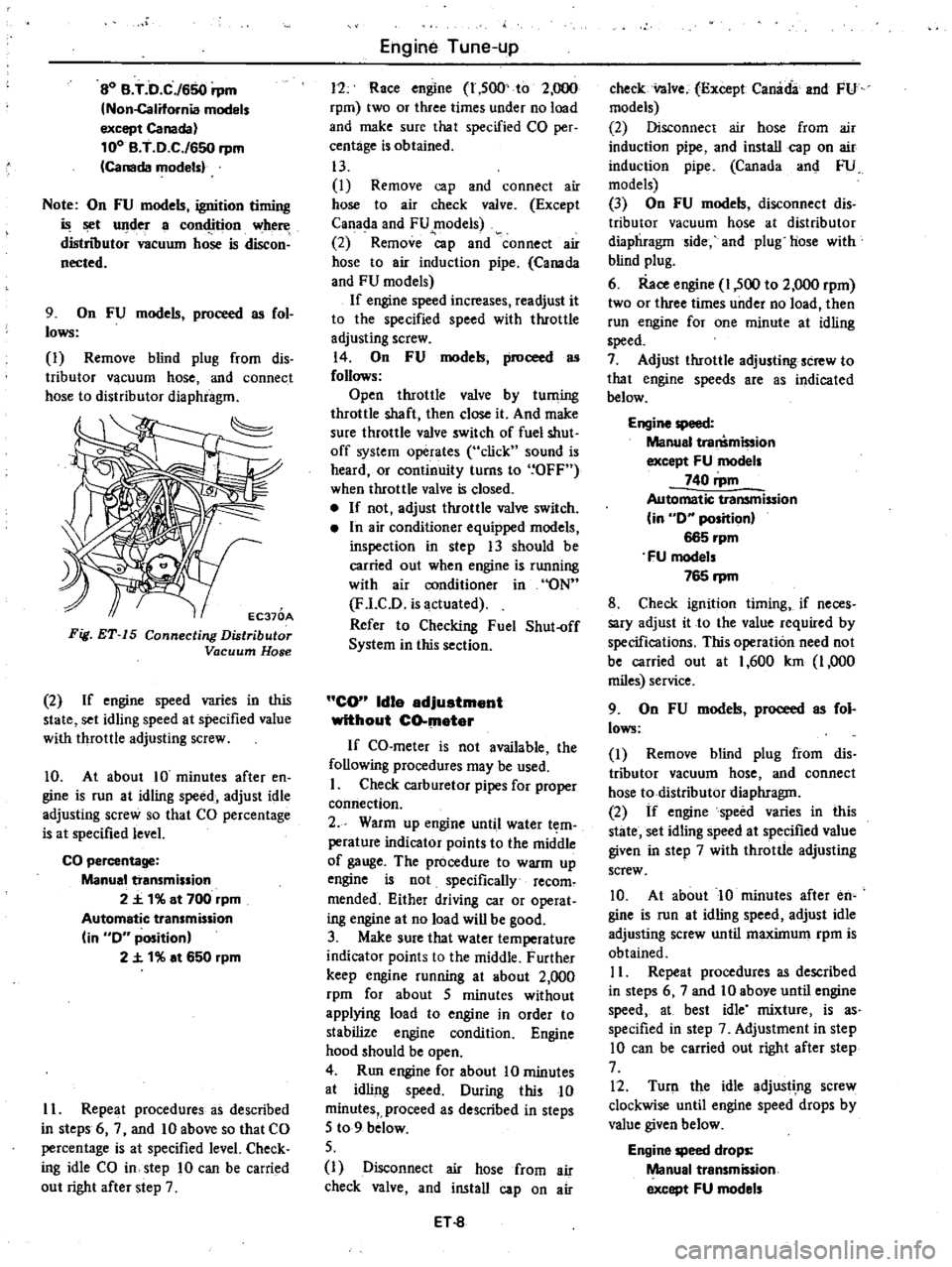
SO
B
T
D
C
650
rpm
Non
California
models
except
Canada
100
B
T
0
C
650
rpm
Canada
models
Note
On
FU
models
ignition
timing
t
under
a
con4ition
where
distnoutor
vacuum
hose
is
discon
nected
9
On
FU
models
proceed
as
fol
lows
I
Remove
blind
plug
from
dis
tributor
vacuum
hose
and
connect
hose
to
distributor
diaphragm
EC370A
Fig
ET
15
Connecting
Distributor
Vacuum
Hose
2
If
engine
speed
varies
in
this
state
set
idling
speed
at
specified
value
with
throttle
adjusting
screw
10
At
about
10
minutes
after
en
gine
is
run
at
idling
speed
adjust
idle
adjusting
screw
so
that
CO
percentage
is
at
specified
level
CO
percentage
Manual
transmission
2
t
1
at
700
rpm
Automatic
transmission
in
0
position
2
t
1
at
650
rpm
II
Repeat
procedures
as
described
in
steps
6
7
and
10
above
so
that
CO
percentage
is
at
specified
level
Check
ing
idle
CO
in
step
10
can
be
carried
out
right
after
step
7
Engine
Tune
up
11
Race
engine
1
500
to
2
000
rpm
two
or
three
times
under
no
load
and
make
sure
that
specified
CO
per
centage
is
obtained
13
I
Remove
cap
and
connect
air
hose
to
air
check
valve
Except
Canada
and
FU
models
2
Remove
p
and
connect
air
hose
to
air
induction
pipe
Canada
and
FU
models
If
engine
speed
increases
readjust
it
to
the
specified
speed
with
throttle
adjusting
screw
14
On
FU
models
proceed
as
follows
Open
throttle
valve
by
tuming
throttle
shaft
then
close
it
And
make
sure
throttle
valve
switch
of
fuel
shut
off
system
operates
click
sound
is
heard
or
continuity
turns
to
OFF
when
throttle
valve
is
closed
If
not
adjust
throttle
valve
switch
In
air
conditioner
equipped
models
inspection
in
step
13
should
be
carried
out
when
engine
is
running
with
air
conditioner
in
ON
F
l
CD
is
actuated
Refer
to
Checking
Fuel
Shut
off
System
in
this
section
CO
Idle
adjuatment
without
CO
mater
If
CO
meter
is
not
available
the
following
procedures
may
be
used
I
Check
carburetor
pipes
for
proper
comiection
2
Warm
up
engine
until
water
t
m
perature
indicator
points
to
the
middle
of
gauge
The
procedure
to
warm
up
engine
is
not
specifically
recom
mended
Either
driving
car
or
operat
ing
engine
at
no
load
will
be
good
3
Make
sure
that
water
temperature
indicator
points
to
the
middle
Further
keep
engine
running
at
about
2
000
rpm
for
about
5
minutes
without
applying
load
to
engine
in
order
to
stabilize
engine
condition
Engine
hood
should
be
open
4
Run
engine
for
about
10
minutes
at
idling
speed
During
this
10
minutes
proceed
as
described
in
steps
5
to
9
below
5
I
Disconnect
air
hose
from
air
check
valve
and
install
cap
on
air
ET
8
check
nlve
Except
Canada
and
FU
models
2
Disconnect
air
hose
from
air
induction
pipe
and
install
cap
on
air
induction
pipe
Canada
an
FU
models
3
On
FU
models
disconnect
dis
tributor
vacuum
hose
at
distributor
diaphragm
ide
and
plug
hose
with
blind
plug
6
Race
engine
1
500
to
2
000
rpm
two
or
three
times
under
no
load
then
run
engine
for
one
minute
at
idling
speed
7
Adjust
throttle
adjusting
screw
to
that
engine
speeds
are
as
indicated
below
Engine
speed
Manual
tra
mi
ion
except
FU
models
740
rpm
Automatic
transmission
in
0
position
665
rpm
FU
models
765
rpm
8
Check
ignition
timing
if
neces
sary
adjust
it
to
the
value
required
by
specifications
This
operation
need
not
be
carried
out
at
1
600
km
1
000
miles
service
9
On
FU
models
proceed
as
fol
lows
I
Remove
blind
plug
from
dis
tributor
vacuum
hose
and
connect
hose
to
distributor
diaphragm
2
If
engine
speed
varies
in
this
state
set
idling
speed
at
specified
value
given
in
step
7
with
throttle
adjusting
screw
10
At
about
10
minutes
after
en
gine
is
run
at
idling
speed
adjust
idle
adjusting
screw
until
maximum
rpm
is
obtained
II
Repeat
procedures
as
described
in
steps
6
7
and
10
above
until
engine
speed
at
best
idle
mixture
is
as
specified
in
step
7
Adjustment
in
step
10
can
be
carried
out
right
after
step
7
12
Turn
the
idle
adjustIng
screw
clockwise
until
engine
speed
drops
by
value
given
below
Engine
speed
drops
Manual
transmission
except
FU
models
Page 26 of 548
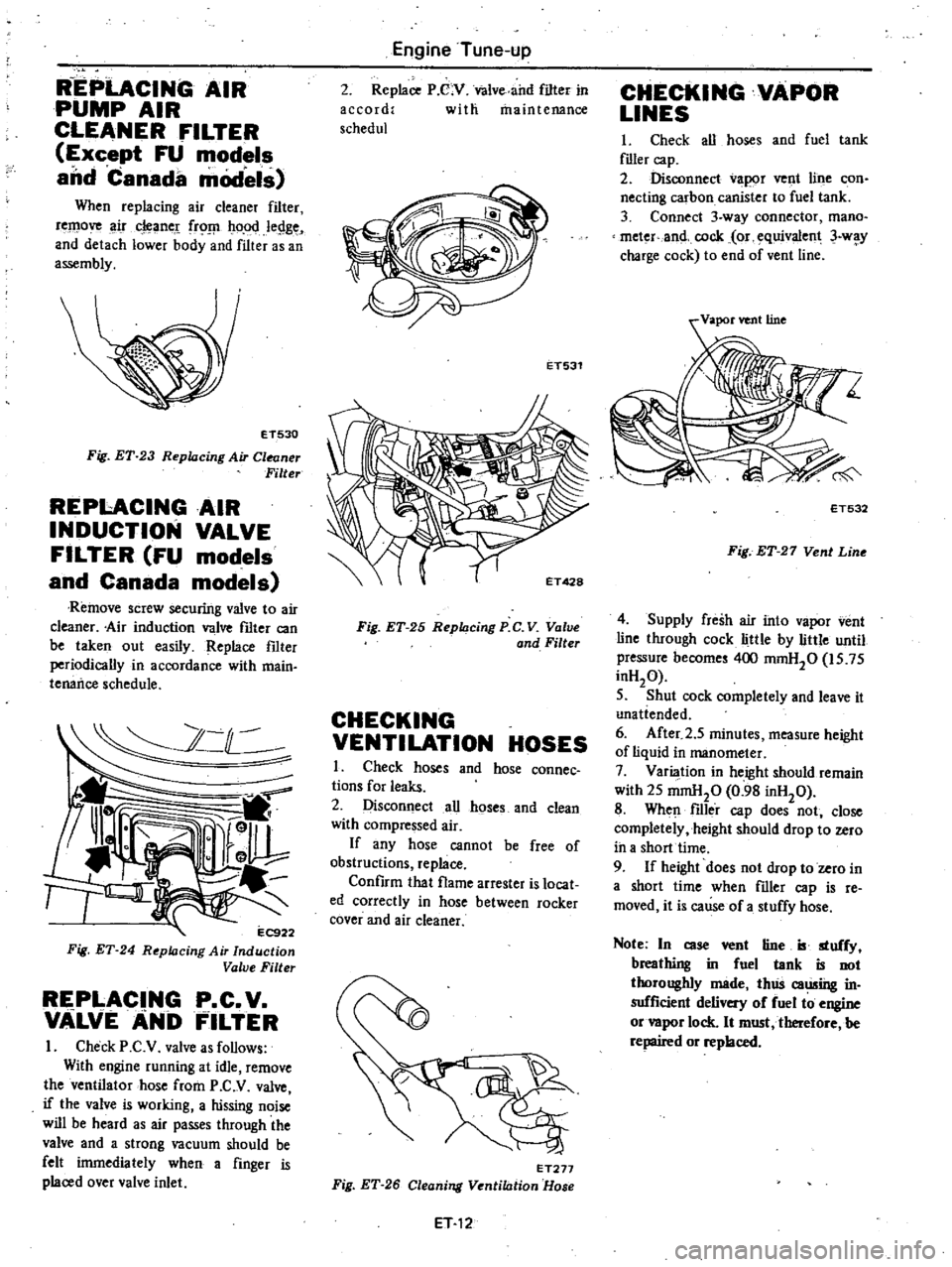
R
EPIACING
AIR
PUMP
AIR
CLEANER
FILTER
Except
FU
models
and
Canada
models
When
replacing
air
cleaner
filter
remove
ir
cleane
frO
ho
od
legge
and
detach
lower
body
and
filter
as
an
assembly
ET530
Fig
ET
23
Replacing
Air
Cleaner
Filter
REPI
ACINGAIR
INDUCTION
VALVE
FILTER
FU
models
and
Canada
models
Remove
screw
securirtg
valve
to
air
cleaner
Air
induction
valve
fIlter
can
be
taken
out
easily
Replace
fIlter
periodically
in
accordance
with
main
tenance
schedule
2
C
l
11
l
r
r
EC9
Fig
ET
24
R
pklcing
Air
Induction
Value
Filter
REPLACING
P
C
V
VALVEANb
FILTER
I
Check
P
C
V
valve
as
follows
With
engine
running
at
idle
remove
the
ventilator
hose
from
P
C
V
valve
if
the
valve
is
working
a
hissing
noise
will
be
heard
as
air
passes
through
the
valve
and
a
strong
vacuum
should
be
felt
inunediately
when
a
finger
is
placed
over
valve
inlet
Engine
Tune
up
2
Replace
P
C
V
Valve
and
filter
in
accord
with
maintenance
schedul
ET531
Fig
ET
25
Replacing
P
C
V
Value
and
Filter
CHECKING
VENTILATION
HOSES
I
Check
hoses
and
hose
connec
tions
for
leaks
2
Disconnect
all
hoses
and
clean
with
compressed
air
If
any
hose
cannot
be
free
of
obstructions
replace
Confirm
that
flame
arrester
is
locat
ed
correctly
in
hose
between
rocker
cover
and
air
cleaner
ET277
Fig
ET
26
Cleaning
Ventilation
Hose
ET
12
CHECKING
VAPOR
LINES
I
Check
all
hoses
and
fuel
tank
flller
cap
2
Disconnect
vapor
vent
line
con
necting
carbon
canister
to
fuel
tank
3
Connect
3
way
connector
mana
meter
and
cock
or
equivalent
3
w
y
charge
cock
to
end
of
vent
line
ET532
Fig
ET
27
Vent
Line
4
Supply
fresh
air
into
vapor
vent
line
through
cock
little
by
little
until
pressure
become
400
mmH20
is
75
inH20
5
Shut
cock
completely
and
leave
it
unatiended
6
After
2
5
minutes
measure
height
of
liquid
in
manometer
7
Varilllion
in
height
should
remain
with
25
mmHp
0
98
inH20
8
When
filler
cap
does
not
close
completely
height
should
drop
to
zero
ih
a
short
time
9
If
height
does
not
drop
to
zero
in
a
short
time
when
filler
cap
is
re
moved
it
is
cause
of
a
stuffy
hose
Note
In
case
vent
tine
B
stuffy
breathing
in
fuel
tank
is
not
thoroughly
made
thlis
caming
in
sufficient
delivery
of
fuel
to
engine
or
vapor
lock
It
must
tberefore
be
repaired
or
replaced
Page 93 of 548

DESCRIPTION
The
carburetors
are
of
downdraft
two
barrel
type
designed
to
increase
ppwe
r
a
fu
l
eC
l
Il
Y
t
3
ell
a
to
reduce
exhaust
gas
emissions
These
carburetors
present
several
distinct
features
of
importance
to
car
owner
A
summary
of
features
is
as
fol
lows
1
Secondary
throttle
valve
is
oper
ated
by
throttle
lever
High
power
and
good
acceleration
are
gained
with
com
bination
of
the
auxiliary
valve
2
Accelerating
pump
provide
ex
cellent
acceleration
3
Power
valve
mechanism
is
a
vacuo
urn
actuated
boost
type
and
improves
high
speed
driving
4
The
throttle
opener
control
sys
tem
Except
FU
model
incorporates
a
servo
diaphragm
which
helps
open
the
throttle
valve
at
a
decreasing
speed
so
as
to
reduce
hydrocarbon
emissions
to
a
minimum
5
An
anti
d
eseling
solenoid
valve
is
installed
to
prevent
dieseling
When
ignition
key
is
turned
off
the
fuel
passage
involved
in
the
ow
system
is
closed
and
the
fuel
supply
is
shut
down
completely
The
solenoid
valve
also
serves
as
an
actuator
of
the
fuel
shut
off
system
on
the
FU
model
6
In
the
choke
mechanism
an
elec
trie
automatic
choke
is
used
to
auto
maticaDy
control
chok
valve
opera
tion
during
engin
war
up
7
The
carburetor
comes
equipped
with
dash
pot
which
ensures
smooth
deceleration
without
engine
stall
under
aU
operating
conditions
STRUCTURE
AND
OPERATION
These
carburetors
consist
of
a
main
system
for
normal
running
a
slow
system
for
idling
and
an
accelerating
and
power
mechanisIll
Some
emission
control
devices
are
added
E
ngine
Fuel
CARBURETOR
I
J
1
Primary
main
jet
2
Idle
adjust
screw
3
hUe
nozzle
4
By
pass
hole
5
Primary
throttle
valve
6
Primary
slow
jet
7
ptug
8
Primary
5l
w
air
bleed
9
Primary
main
air
bleed
10
Primary
air
vent
pipe
11
Primuy
main
nozzle
12
Choke
valve
13
Primary
small
venturi
14
Secondary
small
venturi
15
Secondary
air
vent
pipe
16
Secondary
main
nozzle
17
Secondary
main
air
bleed
18
Secondary
slow
air
bleed
1
Oloke
valve
2
Primary
air
vent
pipe
3
Prima
y
main
nozzle
4
Primary
slow
jet
19
Plug
20
Secondary
slow
jet
21
Needte
22
Fuel
fLlter
23
Secondary
tIuottle
valve
24
Auxiliary
valve
25
Secondary
main
jet
Note
Do
not
remo
the
parts
inarbd
with
anuteriak
EF416A
Fig
EF
17
Carburetor
PRIMARY
SYSTEM
PrlinarJ
main
sJstam
The
fUel
flowing
out
of
the
passages
at
bottom
of
float
chamber
passes
through
the
primary
main
jet
and
is
mixed
with
air
coming
from
main
air
bleed
The
gas
mixture
is
pulled
out
into
the
venturi
through
the
main
nozzle
When
throttle
valve
is
wide
open
and
engine
require
dense
mixture
gas
power
valve
opens
and
fuel
also
flows
into
main
system
EF044A
Fig
EF
18
PtJrlially
Loading
EF
8
Page 95 of 548
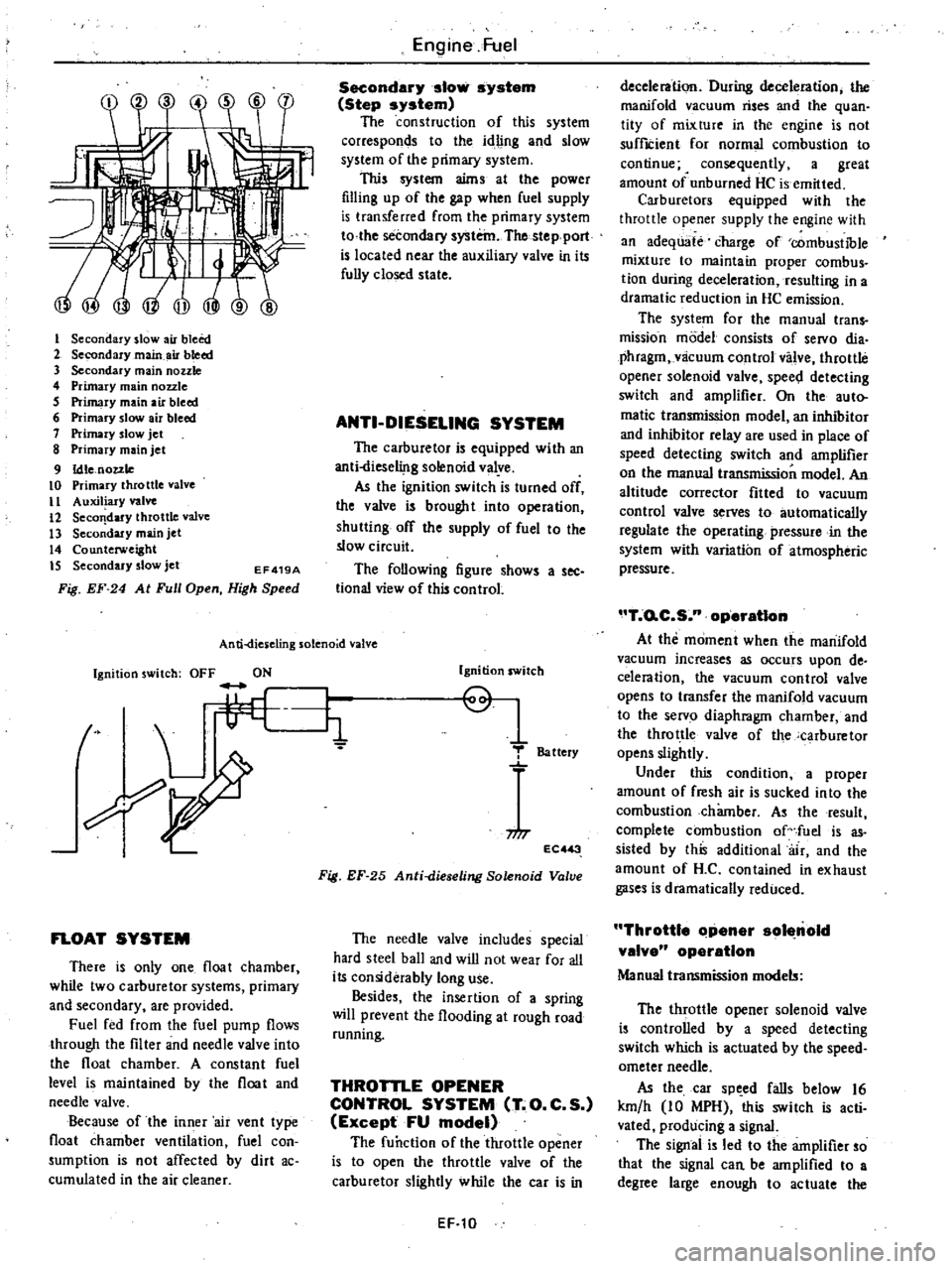
I
Secondary
slow
air
bleed
2
Secondary
main
air
bleed
3
Secondary
main
nozzle
4
Primary
main
nozzle
5
Primary
main
air
bleed
6
Primary
slow
air
bleed
7
Primary
slow
jet
8
Primary
main
jet
9
Idle
nozzle
10
Primary
throttle
valve
II
Auxiliary
valve
12
Seco
dary
throttle
valve
13
Secondary
main
jet
14
Counterweight
IS
Secondary
slow
jet
EF419A
Fig
EF
24
At
Full
Open
High
Speed
Engine
Fuel
Secondary
slow
system
Step
system
The
construction
of
this
system
corresponds
to
the
idling
and
slow
system
of
the
primary
system
This
system
aims
at
the
power
filling
up
of
the
gap
when
fuel
supply
is
transferred
from
the
primary
system
to
the
secondary
system
The
stepport
is
located
near
the
auxiliary
valve
in
its
fully
closed
state
ANTI
DIESELING
SYSTEM
The
carburetor
is
equipped
with
an
anti
liese1i
lg
solenoid
valye
As
the
ignition
switch
is
turned
off
the
valve
is
brought
into
operation
shutting
off
the
supply
of
fuel
to
the
slow
circuit
The
following
figure
shows
a
see
tional
view
of
this
control
An
ti
dies
eling
solenoid
valve
Ignition
switch
OFF
ON
t
L
li
FLOAT
SYSTEM
There
is
only
one
float
chamber
while
two
carburetor
systems
primary
and
secondary
are
provided
Fuel
fed
from
the
fuel
pump
flows
through
the
filter
and
needle
valve
into
the
float
chamber
A
constant
fuel
level
is
maintained
by
the
float
and
needle
valve
Because
of
the
inner
air
vent
type
float
chamber
ventilation
fuel
con
sumption
is
not
affected
by
dirt
ac
cumulated
in
the
air
cleaner
Ignition
switch
Q
1
T
Battery
niT
EC
3
Fig
EF
25
Anti
dieseling
Solenoid
Valve
The
needle
valve
includes
special
hard
steel
ball
and
wiD
not
wear
for
all
its
considerably
long
use
Besides
the
insertion
of
a
spring
will
prevent
the
flooding
at
rough
road
running
THROTTLE
OPENER
CONTROL
SYSTEM
T
O
C
S
Except
FU
model
The
function
of
the
throttle
opener
is
to
open
the
throttle
valve
of
the
carburetor
slightly
while
the
car
is
in
EF
10
deceleration
During
deceleration
the
manifold
vacuum
rises
and
the
quan
tity
of
mixture
in
the
engine
is
not
suffICient
for
normal
combustion
to
continue
4
consequently
a
great
amount
of
unburned
HC
is
emitted
Carburetors
equipped
with
the
throttle
opener
supply
the
engine
with
an
adequate
charge
of
combustible
mixture
to
maintain
proper
combus
tion
during
deceleration
resulting
in
a
dramatic
reduction
in
HC
emission
The
system
for
the
manual
trans
mission
model
consists
of
servo
dia
phragm
vlicuum
control
valve
throttle
opener
solenoid
valve
spee
l
detecting
switch
and
amplifier
On
the
auto
matic
transmission
model
an
inhibitor
and
inhibitor
relay
are
used
in
place
of
speed
detecting
switch
and
amplifier
on
the
manual
transmission
model
An
altitude
corrector
fitted
to
vacuum
control
valve
serves
to
automatically
regulate
the
operating
pressure
in
the
system
with
variation
of
atmospheric
pressure
T
o
C
S
n
operatIon
At
the
moment
when
the
manifold
vacuum
increases
as
occurs
upon
de
celeration
the
vacuum
control
valve
opens
to
transfer
the
manifold
vacuum
to
the
servo
diaphragm
chamber
and
the
throttle
valve
of
the
carburetor
opens
slightly
Under
this
condition
a
proper
amount
of
fresh
air
is
sucked
into
the
combustion
chamber
As
the
result
complete
combustion
of
fuel
is
as
sisted
by
this
additional
air
and
the
amount
of
H
C
contained
in
exhaust
gases
is
dramatically
reduced
Throttle
Clpener
sol
nold
valve
operation
Manual
transmission
models
The
throttle
opener
solenoid
valve
is
controlled
by
a
speed
detecting
switch
which
is
actuated
by
the
speed
ometer
needle
As
the
car
sp
ed
falls
below
16
km
h
10
MPH
this
switch
is
acti
vated
producing
a
signal
The
signal
is
led
to
the
amplifier
so
that
the
signal
can
be
amplified
to
a
degree
large
enough
to
actuate
the
Page 100 of 548
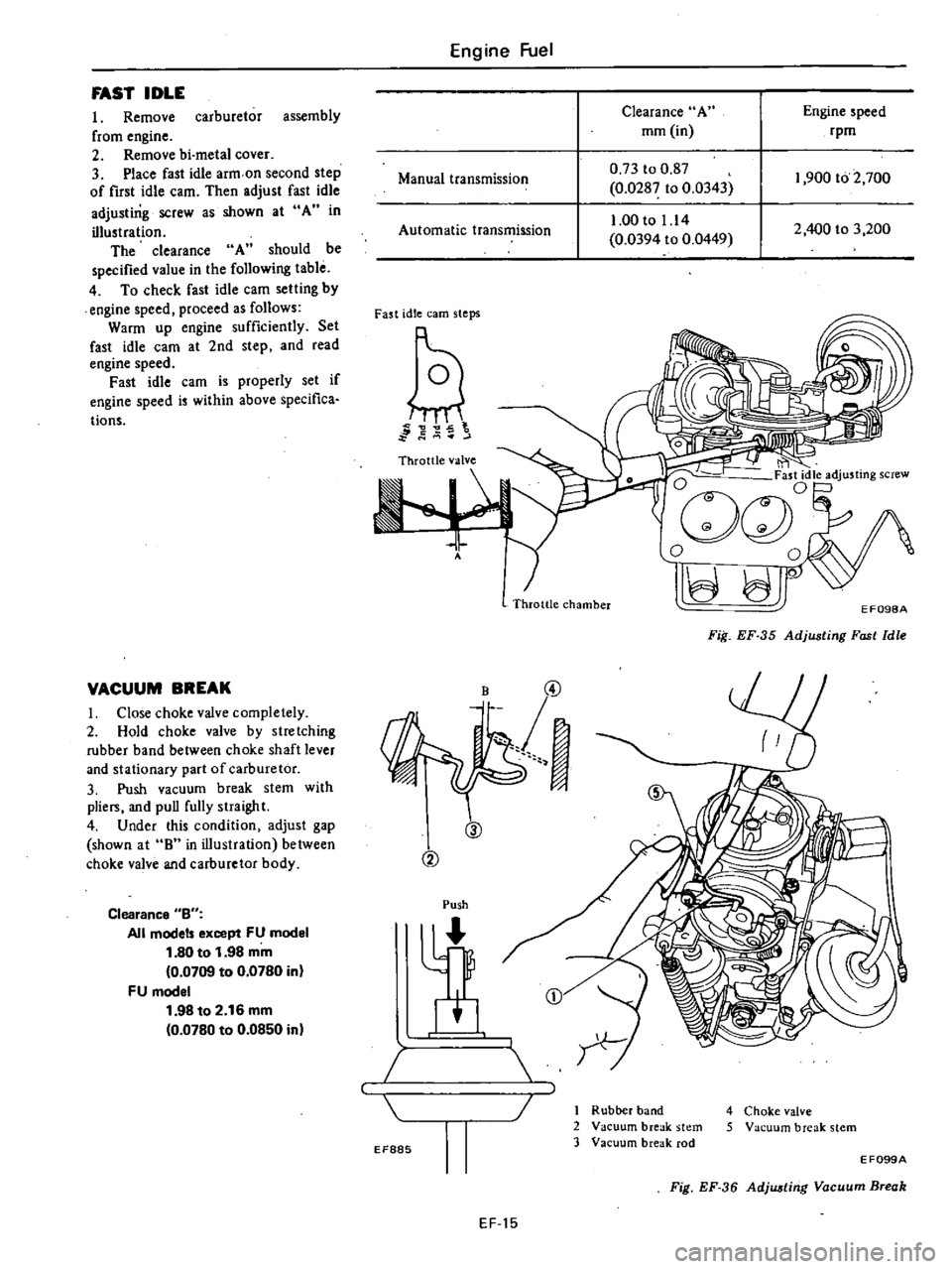
FAST
IDLE
I
Remove
carburetor
assembly
from
engine
2
Remove
bi
metal
cover
3
Place
fast
idle
arm
on
second
step
of
first
idle
cam
Then
adjust
fast
idle
adjusting
screw
as
shown
at
A
in
illustration
The
clearance
A
should
be
specified
value
in
the
following
table
4
To
check
fast
idle
cam
setting
by
engine
speed
proceed
as
follows
Warm
up
engine
sufficiently
Set
fast
idle
cam
at
2nd
step
and
read
engine
speed
Fast
idle
cam
is
properly
set
if
engine
speed
is
within
above
specifica
Hons
VACUUM
BREAK
I
Close
choke
valve
completely
2
Hold
choke
valve
by
stretching
rubber
band
between
choke
shaft
lever
and
stationary
part
of
carburetor
3
Push
vacuum
break
stem
with
plie
and
puD
fully
straight
4
Under
this
condition
adjust
gap
shown
at
8
in
illustration
between
choke
valve
and
carburetor
body
Clearance
Bu
All
model
except
FU
model
1
80
to
1
98
mm
0
0709
to
0
0780
in
FU
model
1
98
to
2
16
mm
0
0780
to
0
0850
in
Engine
Fuel
Clearance
A
mm
in
Engine
speed
rpm
Manual
transmission
0
73
to
0
87
0
0287
to
0
0343
1
00
to
1
14
0
0394
to
0
0449
2
400
to
3
200
1
900
to
2
700
Automatic
transmission
Fast
idle
earn
steps
g
g
2
5
t
to
J
A
ti
Ogc
j
jdle
adjusting
screw
o
0
II
r
Throttle
chamber
EF098A
Fiil
EF
35
Adjusting
Fast
Idle
@
B
@
cv
Push
I
4
Choke
valve
5
Vacuum
break
stem
EF885
1
Rubber
band
2
Vacuum
break
stem
3
Vacuum
break
rod
E
F099A
Fig
EF
36
Adjwtirig
Vacuum
Break
EF
15
Page 101 of 548
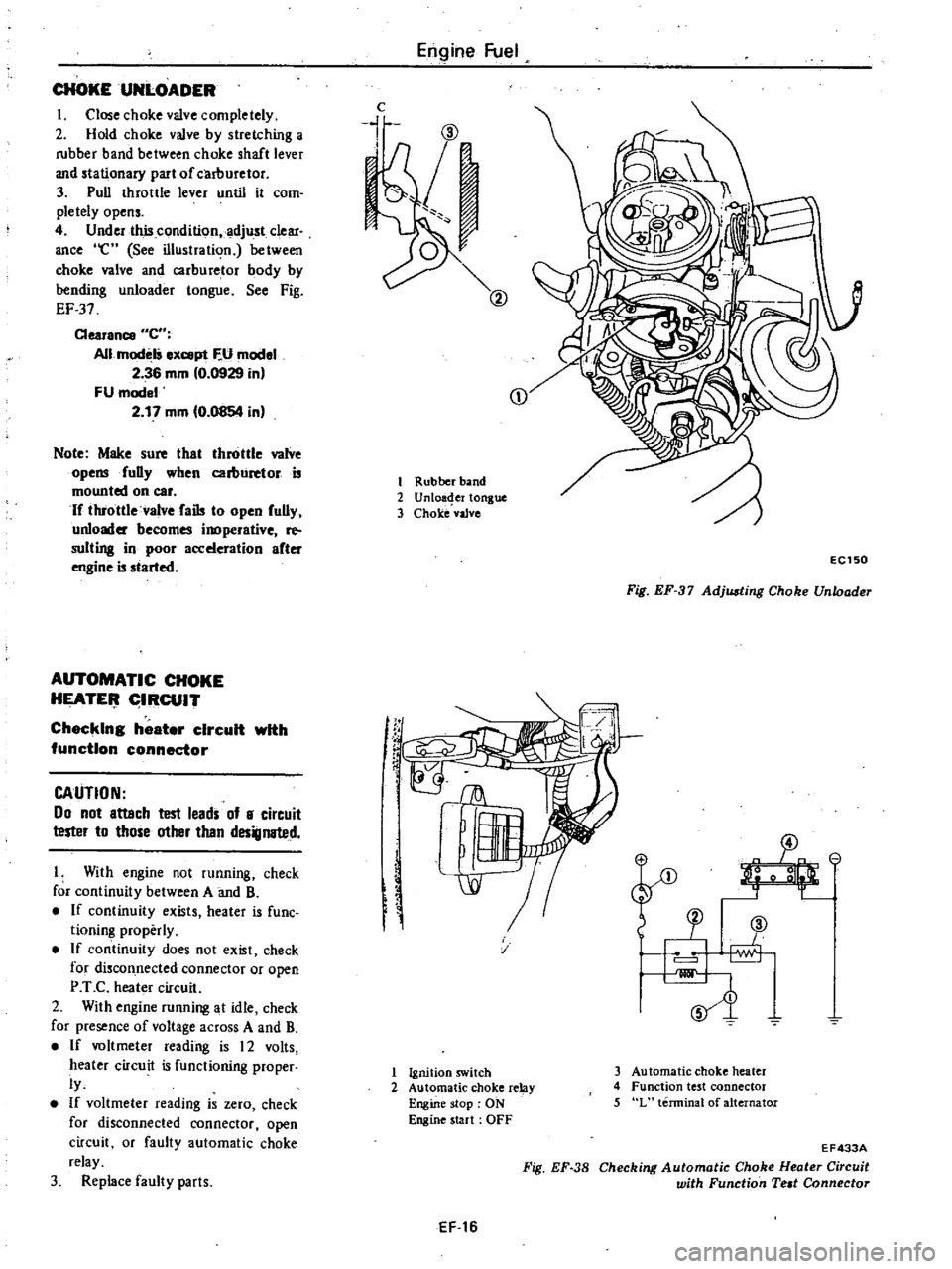
CHOKEUNLOADER
I
Close
choke
valve
completely
2
Hold
choke
valve
by
stretching
a
rubber
band
between
choke
shaft
lever
and
stationary
part
of
carllUretor
3
Pull
throttle
lever
until
it
com
pletely
opens
4
Under
this
condition
adjust
clear
ance
e
See
illustration
between
choke
valve
and
carburetor
body
by
bending
unloader
tongue
See
Fig
EF
37
Clearance
C
All
modelS
ex
pt
F
U
model
2
36
mm
0
0929
in
FU
model
2
17
mm
0
0854
in
Note
Make
sure
that
throttle
valve
opensfuDy
when
carburetor
is
mounted
on
car
If
throttle
valve
fails
to
open
fully
unloader
becomes
inoperative
re
suiting
in
poor
acceleration
after
engine
is
started
AUTOMATIC
CHOKE
HEATE
IRCUIT
Checking
heater
circuit
with
function
connector
CAUTION
00
not
attach
test
leads
of
8
circuit
tester
to
those
other
than
designated
I
With
engine
not
running
check
for
continuity
between
A
and
B
If
continuity
exists
heater
is
fune
tioning
properly
If
continuity
does
not
exist
check
for
discon
nected
connector
or
open
P
T
C
heater
circuit
2
With
engine
running
at
idle
check
for
presence
of
voltage
across
A
and
B
If
voltmeter
reading
is
12
volts
heater
circuit
is
functioning
proper
ly
If
voltmeter
reading
is
zero
check
for
disconnected
connector
open
circuit
or
faulty
automatic
choke
relay
3
Replace
faulty
parts
Engine
Fuel
c
i
CD
1
Rubber
band
2
Unloa
er
tongue
3
Choke
vaJve
f
rC
EC150
Fig
EF
37
Adjusting
Choke
Unloader
SJ
v
1
Ignition
switch
2
Automatic
choke
relay
Engine
stop
ON
Engine
start
OFF
3
Automatic
choke
heater
4
Function
test
connector
5
L
terminal
of
alternator
EF
16
Fig
EF
38
EF433A
Checking
Automatic
Choke
Heater
Circuit
with
Function
Teat
Connector
Page 103 of 548
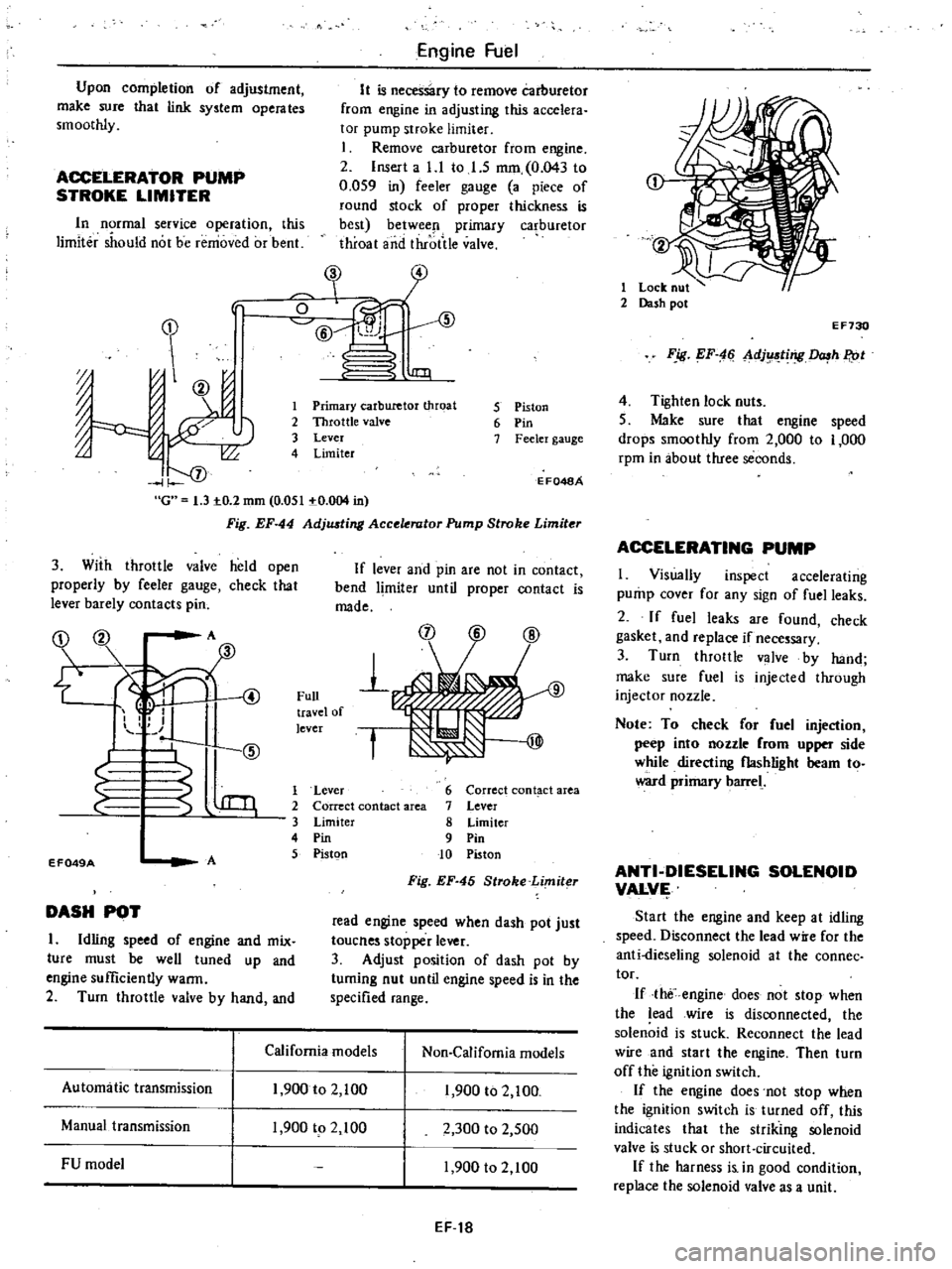
Engine
Fuel
Upon
completion
of
adjustment
make
sure
that
link
system
opera
tes
smoothly
It
is
necessary
to
remove
Carburetor
from
engine
in
adjusting
this
accelera
tor
pump
stroke
limiter
1
Remove
carburetor
from
engine
2
Insert
a
l
l
to
I
S
mm
0
043
to
0
059
in
feeler
gauge
a
piece
of
round
stock
of
proper
thickness
is
best
betwee
l
primary
ca
buretor
throat
and
throtile
valve
ACCELERATOR
PUMP
STROKE
LIMITER
In
rmal
service
operation
this
limiter
should
not
be
removed
or
bent
In
J
0
ID
@
l
1IJl
J
J
00
I
f
oj
G
1
3
IO
2
mm
0
051
IO
004
in
Fig
EF
44
AdjlUting
Acce
rator
Pump
Stroke
Limiter
1
Primary
carburetor
throat
2
Throttle
valve
3
Lever
4
Limiter
5
Piston
6
Pin
7
Feeler
gauge
E
F048A
3
With
throttle
valve
held
open
properly
by
feeler
gauge
check
that
lever
barely
contacts
pin
If
lever
and
pin
are
not
in
contact
bend
limiter
until
proper
contact
is
made
OZ
00
A
fID
1
S
@
4
1
Full
travel
of
lever
f
EF049A
A
1
Lever
2
Correct
contact
area
3
Limiter
4
Pin
5
Pistgn
6
Correct
cont
ct
area
7
Lever
8
Limiter
9
Pin
10
Piston
Fig
EF
45
Stroke
Limiter
DASH
POT
I
Idling
speed
of
engine
and
mix
ture
must
be
well
tuned
up
and
engine
sufficiently
warm
2
Turn
throttle
valve
by
hand
and
read
engine
speed
when
dash
pot
just
toucnes
stopper
lever
3
Adjust
position
of
dash
pot
by
tuming
nut
until
engine
speed
is
in
the
specified
range
California
models
Non
Califomia
models
Automatic
transmission
1
900
to
2
100
1
900
to
2
100
Manual
transmission
1
900
tp
2
100
2
300
to
2
500
FU
model
1
900
to
2
100
EF
t8
1
Lock
nut
2
Dash
pot
E
F730
F
ig
EF
4
Ll
dj
ting
h
P
ot
4
Tighten
lock
nuts
5
Make
sure
that
engine
speed
drops
smoothly
from
2
000
to
1
000
rpm
in
about
three
seconds
ACCELERATING
PUMP
I
Visually
inspect
accelerating
pump
cover
for
any
sign
of
fuel
leaks
2
If
fuel
leaks
are
found
check
gasket
and
replace
if
necessary
3
Turn
throttle
valve
by
hand
make
sure
fuel
is
injected
through
injector
nozzle
Note
To
check
or
fuel
injection
peep
into
nozzle
rom
upper
side
while
directing
flashlight
beam
to
ward
primary
barrel
ANTI
DIESELING
SOLENOID
VALVI
Start
the
engine
and
keep
at
idling
speed
Disconnect
the
lead
w
e
for
the
anti
dieseling
solenoid
at
the
connec
tor
If
the
engine
does
not
stop
when
the
lead
wire
is
disconnected
the
solenoid
is
stuck
Reconnect
the
lead
wire
and
start
the
engine
Then
turn
off
the
ignition
switch
If
the
engine
does
not
stop
when
the
ignition
switch
is
turned
off
this
indicates
that
the
striking
solenoid
valve
is
stuck
or
short
circuited
If
the
harness
i
in
good
condition
replace
the
solenoid
valve
as
a
unit