lock DATSUN PICK-UP 1977 Repair Manual
[x] Cancel search | Manufacturer: DATSUN, Model Year: 1977, Model line: PICK-UP, Model: DATSUN PICK-UP 1977Pages: 537, PDF Size: 35.48 MB
Page 211 of 537
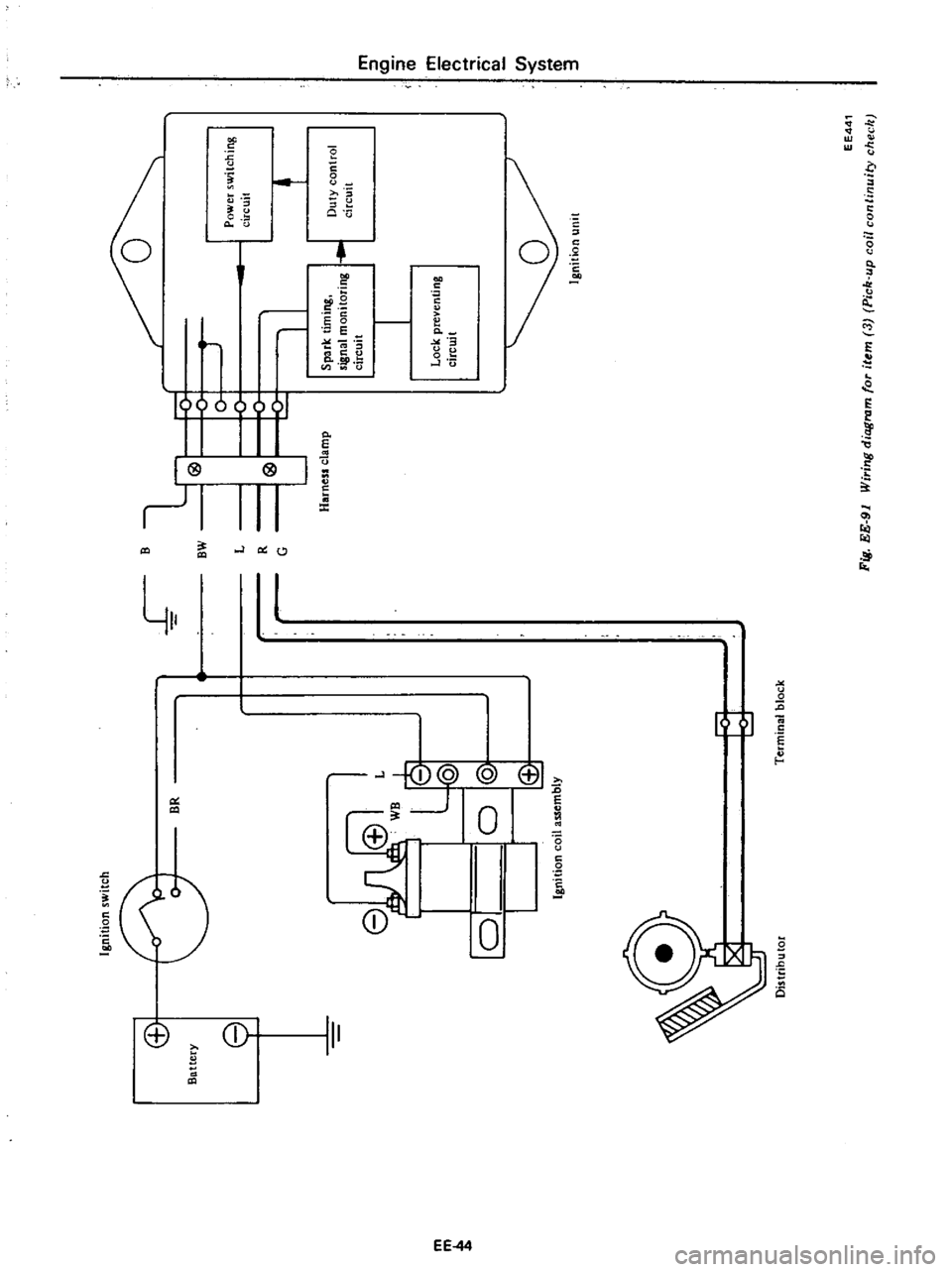
W
t
gni
on
s
Witch
ll
l
I
o
f1
t
Of
CO
a
rntM
OliU
bUlot
r
Terrn
oa
blocK
o
B
powet
swilchln
CltCU1l
BW
I
l
G
@
DUtY
cof
lTO
C
tCU
l
I
I
u
5
l
l
l
l
0
1Il
St
l
titrllt
t
signa
tl
onitotifl
circuit
Ratt
e
cump
LOCK
preyen
tn
circuit
f
l
o1
unl
l
EE44
f
o
o
Page 220 of 537
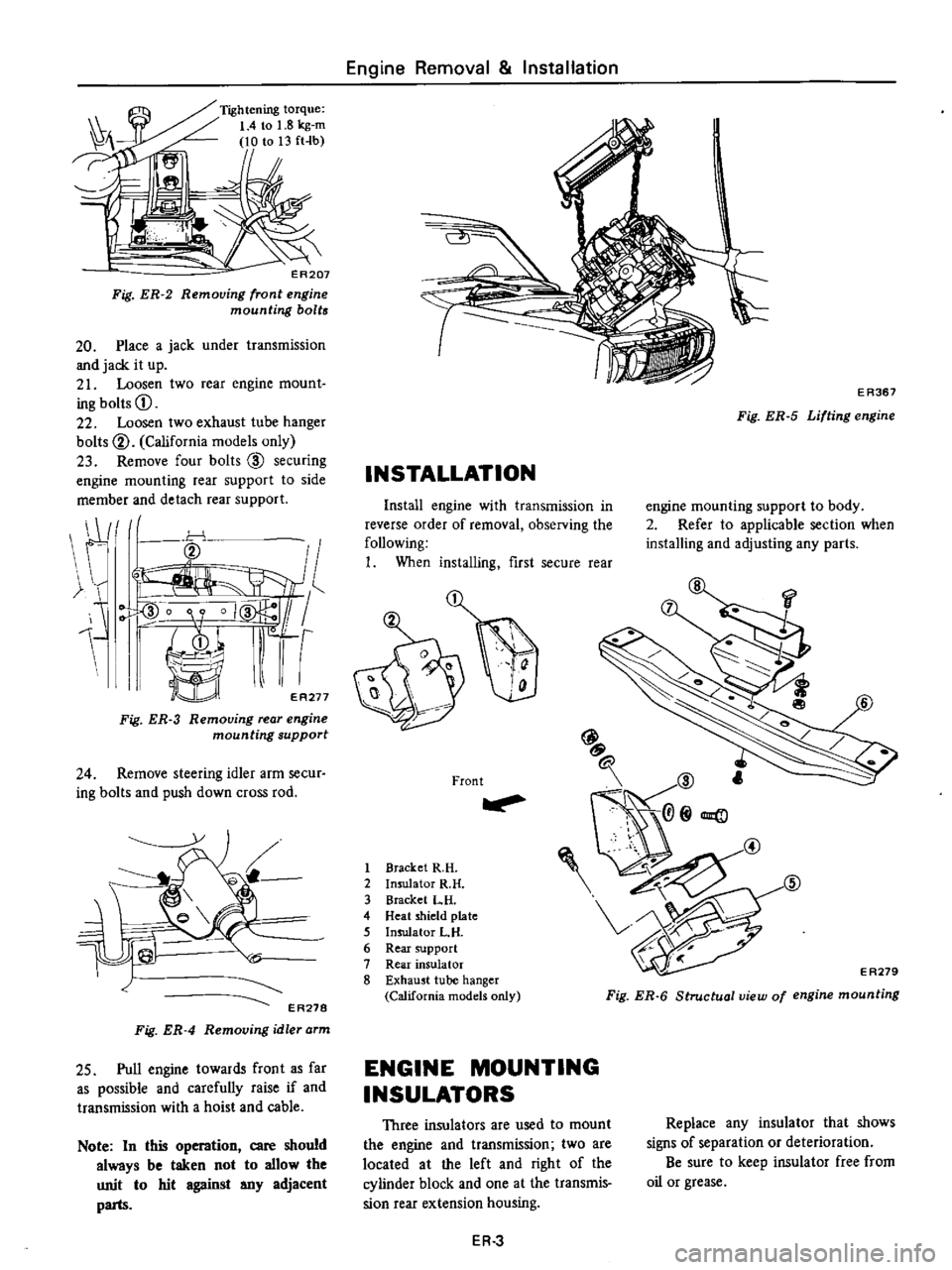
Fig
ER
2
ER207
Removing
front
engine
mounting
bolts
20
Place
a
jack
under
transmission
and
jack
it
up
21
Loosen
two
rear
engine
mount
ing
bolts
CD
22
Loosen
two
exhaust
tube
hanger
bolts
V
California
models
only
23
Remove
four
bolts
CID
securing
engine
mounting
rear
support
to
side
member
and
detach
rear
support
j
r
O
1
ER271
Fig
ER
3
Removing
rear
engine
mounting
support
24
Remove
steering
idler
arm
secur
ing
bolts
and
push
down
cross
rod
iC
EA278
Fig
ER
4
Removing
idler
arm
25
Pull
engine
towards
front
as
far
as
possible
and
carefully
raise
if
and
transmission
with
a
hoist
and
cable
Note
In
this
r
an
care
should
always
be
taken
not
to
allow
the
unit
to
hit
against
any
adjacent
parts
Engine
Removal
Installation
INSTALLATION
E
R367
Fig
ER
5
Lifting
engine
Install
engine
with
transmission
in
reverse
order
of
removal
observing
the
following
I
When
installing
first
secure
rear
2
Front
1
Bracket
R
H
2
Insulator
R
H
3
Bracket
LH
4
Heat
shield
plate
5
Insulator
L
H
6
Rear
support
7
Rear
insulator
8
Exhaust
tube
hanger
California
models
only
engine
mounting
support
to
body
2
Refer
to
applicable
section
when
installing
and
adjusting
any
parts
@
E
A279
Fig
ER
6
Structual
view
of
engine
mounting
ENGINE
MOUNTING
INSULATORS
Three
insulators
are
used
to
mount
the
engine
and
transmission
two
are
located
at
the
left
and
right
of
the
cylinder
block
and
one
at
the
transmis
sion
rear
extension
housing
Replace
any
insulator
that
shows
signs
of
separation
or
deterioration
Be
sure
to
keep
insulator
free
from
oil
or
grease
ER
3
Page 221 of 537
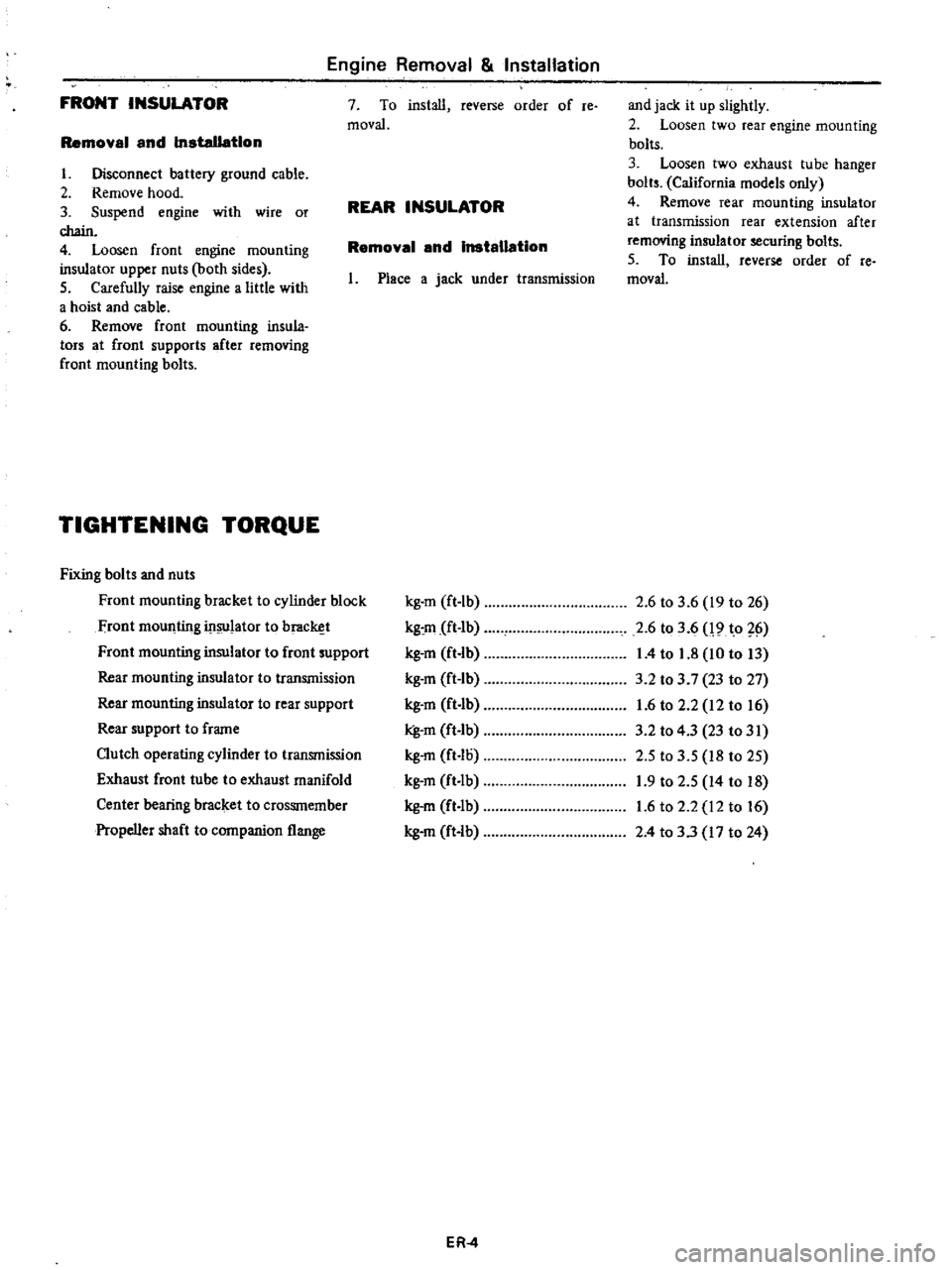
Engine
Removal
Installation
FRONT
INSULATOR
Removal
and
installation
7
To
install
reverse
order
of
re
moval
1
Disconnect
battery
ground
cable
2
Remove
hood
3
Suspend
engine
with
wire
or
chain
4
Loosen
front
engine
mounting
insulator
upper
nuts
both
sides
5
Carefully
raise
engine
a
little
with
a
hoist
and
cable
6
Remove
front
mounting
insula
tors
at
front
supports
after
removing
front
mounting
bolts
REAR
INSULATOR
Ramoval
and
Installation
1
Place
a
jack
under
transmission
TIGHTENING
TORQUE
Fixing
bolts
and
nuts
Front
mounting
bracket
to
cylinder
block
Front
mounting
in
lator
to
brac
t
Front
mounting
insulator
to
front
support
Rear
mounting
insulator
to
transmission
Rear
mounting
insulator
to
rear
support
Rear
support
to
frame
Clutch
operating
cylinder
to
transmission
Exhaust
front
tube
to
exhaust
manifold
Center
bearing
bracket
to
crossrnember
Propeller
shaft
to
companion
flange
kg
m
ft
lb
kg
m
ft
Ib
kg
m
ft
lb
kg
m
ft
lb
kg
m
ft
Ib
kg
m
ft
lb
kg
m
ft
Io
kg
m
ft
lb
kg
m
ft
lb
kg
m
ft
lb
ER
4
and
jack
it
up
slightly
2
Loosen
two
rear
engine
mounting
bolts
3
Loosen
two
exhaust
tube
hanger
bolts
California
models
only
4
Remove
rear
mounting
insulator
at
transmission
rear
extension
after
removing
insulator
securing
bolts
5
To
install
reverse
order
of
Ie
moval
2
6
to
3
6
19
to
26
2
6
to
3
6
19
t
o
76
1
4
to
1
8
10
to
13
3
2
to
3
7
23
to
27
1
6
to
2
2
12
to
16
3
2
to
4
3
23
to
31
2
5
to
3
5
18
to
25
1
9
to
2
5
14
to
18
1
6
to
2
2
12
to
16
2
4
to
3
3
17
to
24
Page 227 of 537
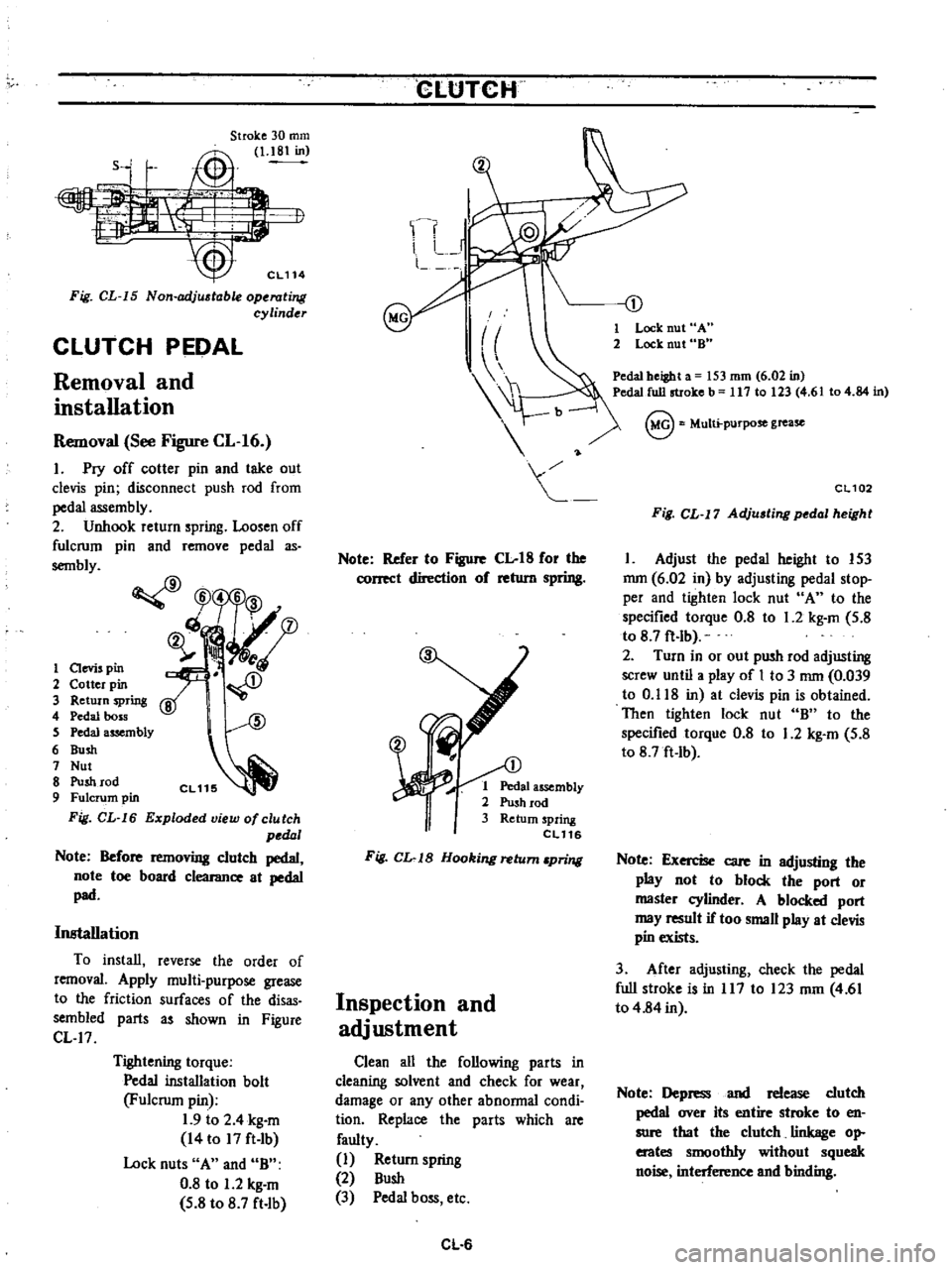
Stroke
30
mm
Jt
i
I
1
18
in
Sj
1
i
J
o
Fig
CL
15
Non
adj
table
operating
cylinder
CLUTCH
PEDAL
Removal
and
installation
Removal
See
Figure
CL
16
1
Pry
off
cotter
pin
and
take
out
clevis
pin
disconnect
push
rod
from
pedal
assembly
2
Unhook
return
spring
Loosen
off
fulcrum
pin
and
remove
pedal
as
sembly
CfJ
W5
6
3
ch
fD
ij
ll
i
A
1
aevis
pin
2
Cotter
pin
3
Return
spring
4
Pedal
boss
S
Pedal
assembly
6
Bush
7
Nut
8
Push
rod
9
Fulcrum
pin
Fig
CL
16
Exploded
view
of
clutch
pedal
Note
Before
removing
clutch
pedal
note
toe
board
clearance
at
pedal
pad
Installation
To
install
reverse
the
order
of
removal
Apply
multi
purpose
grease
to
the
friction
surfaces
of
the
disas
sembled
parts
as
shown
in
Figure
CL
17
Tightening
torque
Pedal
installation
bolt
Fulcrum
pin
1
9
to
2
4
kg
m
14
to
17
ft
Ib
Lock
nuts
A
and
B
0
8
to
1
2
kg
m
5
8
to
8
7
ft
lb
CLtJTCH
Note
Refer
to
Figure
Clot8
for
the
correct
direction
of
return
spring
1
Pedal
assembly
2
Push
rod
3
Return
spring
eL116
Fig
CL
1B
Hooking
return
pring
Inspection
and
adjustment
Clean
all
the
following
parts
in
cleaning
solvent
and
check
for
wear
damage
or
any
other
abnormal
condi
tion
Replace
the
parts
which
are
faulty
1
Return
spring
2
Bush
3
Pedal
boss
etc
CL
6
1
Lock
nut
A
2
Lock
nut
8
Pedal
beiBht
a
53
mm
6
02
in
Pedal
full
stroke
b
117
10
23
4
6
104
84
in
@
Multi
purpose
grease
CL102
Fig
CL
17
Adju
ting
pedal
height
1
Adjust
the
pedal
height
to
153
mm
6
02
in
by
adjusting
pedal
stop
per
and
tighten
lock
nut
A
to
the
specified
torque
0
8
to
1
2
kg
m
5
8
to
8
7
ft
lb
2
Turn
in
or
out
push
rod
adjusting
screw
until
a
play
of
I
to
3
mm
0
039
to
0
118
in
at
clevis
pin
is
obtained
Then
tighten
lock
nut
B
to
the
specified
torque
0
8
to
1
2
kg
m
5
8
to
8
7ft
Ib
Note
Exercise
care
in
adjusting
the
play
not
to
block
the
port
or
master
cylinder
A
blocked
port
may
result
if
too
small
play
at
clevis
pin
exists
3
After
adjusting
check
the
pedal
full
stroke
is
in
117
to
123
mm
4
61
to
4
84
in
Note
Depress
and
release
clutch
pedal
over
its
entire
stroke
to
en
sure
that
the
clutch
linkage
op
erates
smoothly
without
squeak
noise
interference
and
binding
Page 228 of 537
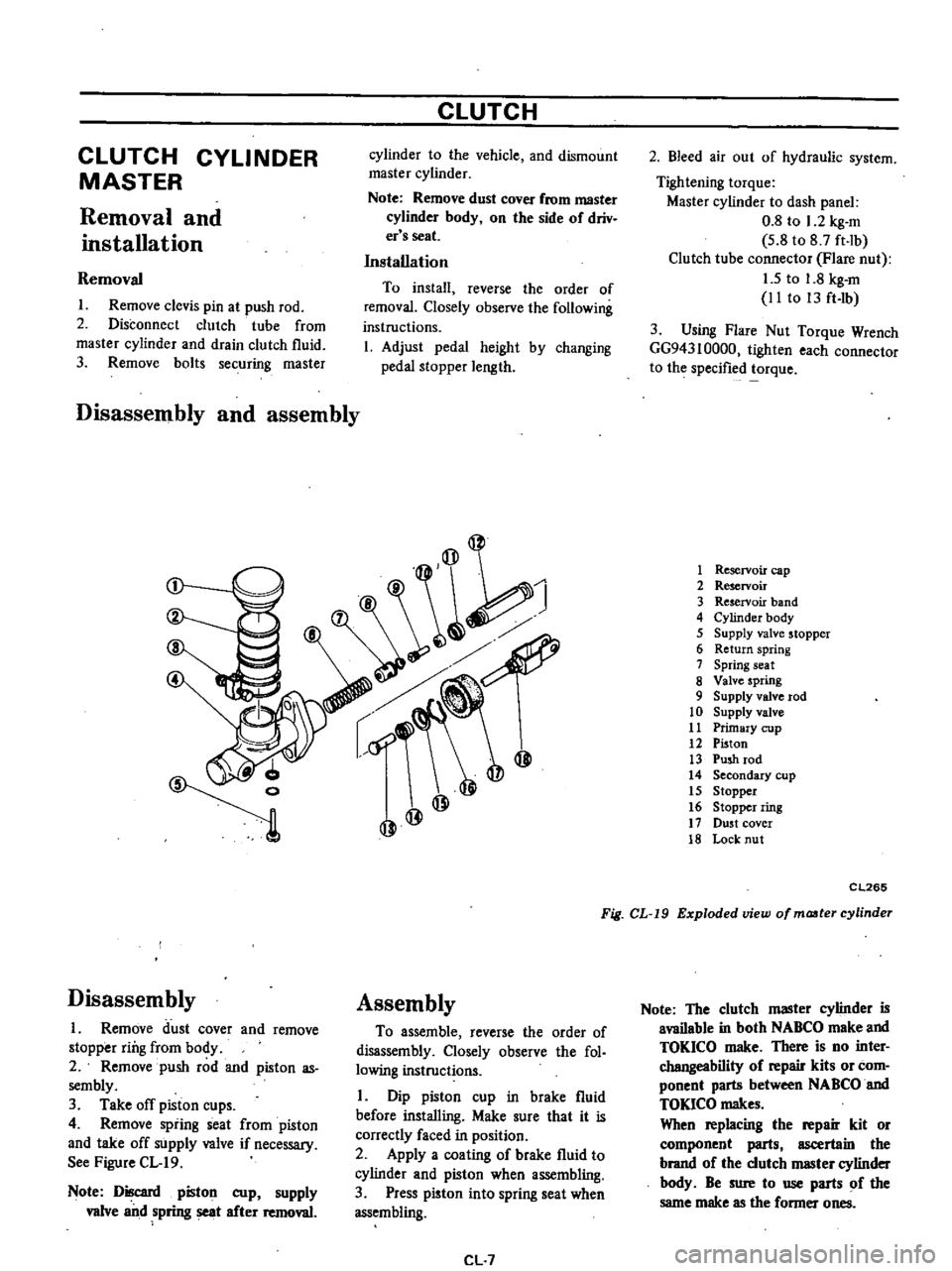
CLUTCH
CYLINDER
MASTER
Removal
and
installation
Removal
I
Remove
clcvis
pin
at
push
rod
2
Disconnect
clutch
tube
from
master
cylinder
and
drain
clutch
fluid
3
Remove
bolts
securing
master
Disassembly
and
assembly
CLUTCH
cylinder
to
the
vehicle
and
dismount
master
cylinder
Note
Remove
dust
cover
from
master
cylinder
body
on
the
side
of
driv
er
s
seat
Installation
To
install
reverse
the
order
of
removal
Closely
observe
the
following
instructions
1
Adjust
pedal
height
by
changing
pedal
stopper
length
Disassembly
1
Remove
dust
cover
and
remove
stopper
ring
from
body
2
Remove
push
rod
and
piston
as
sembly
3
Take
off
piston
cups
4
Remove
spiing
seat
from
piston
and
take
off
supply
valve
if
necessary
See
Figure
CL
19
Note
Discard
piston
cup
supply
valve
and
spring
seat
after
removal
Assembly
To
assemble
reverse
the
order
of
disassembly
Closely
observe
the
fol
lowing
instructions
I
Dip
piston
cup
in
brake
fluid
before
installing
Make
sure
that
it
is
correctly
faced
in
position
2
Apply
a
coating
of
brake
fluid
to
cylinder
and
piston
when
assembling
3
Press
piston
into
spring
seat
when
assembling
CL
7
2
Bleed
air
out
of
hydraulic
system
Tightening
torque
Master
cylinder
to
dash
panel
0
8
to
1
2
kg
m
5
8
to
8
7
ft
lb
Clutch
tube
connector
Flare
nut
1
5
to
1
8
kg
m
II
to
13
ft
lb
3
Using
Flare
Nut
Torque
Wrench
GG94310000
tighten
each
connector
to
the
specified
torque
1
Reservoir
cap
2
Reservoir
3
Reservoir
band
4
Cylinder
body
5
Supply
valve
stopper
6
Return
spring
7
Spring
seat
8
Valve
spring
9
Supply
valve
rod
10
Supply
valve
11
Primary
cup
12
Piston
13
Push
rod
14
Secondary
cup
15
Stopper
16
Stopper
ring
17
DU5t
cover
18
Lock
nut
CL265
Fig
CL
19
Exploded
view
of
maater
cylinder
Note
The
clutch
master
cylinder
is
available
in
both
NABCO
make
and
TOKICO
make
There
is
no
inter
changeability
of
repair
kits
or
com
ponent
parts
between
NABCO
and
TOKlCO
makes
When
replacing
the
repair
kit
or
component
parts
ascertain
the
brand
of
the
clutch
IIIBSter
cylinder
body
Be
sure
to
use
parts
of
the
same
make
as
the
former
ones
Page 230 of 537
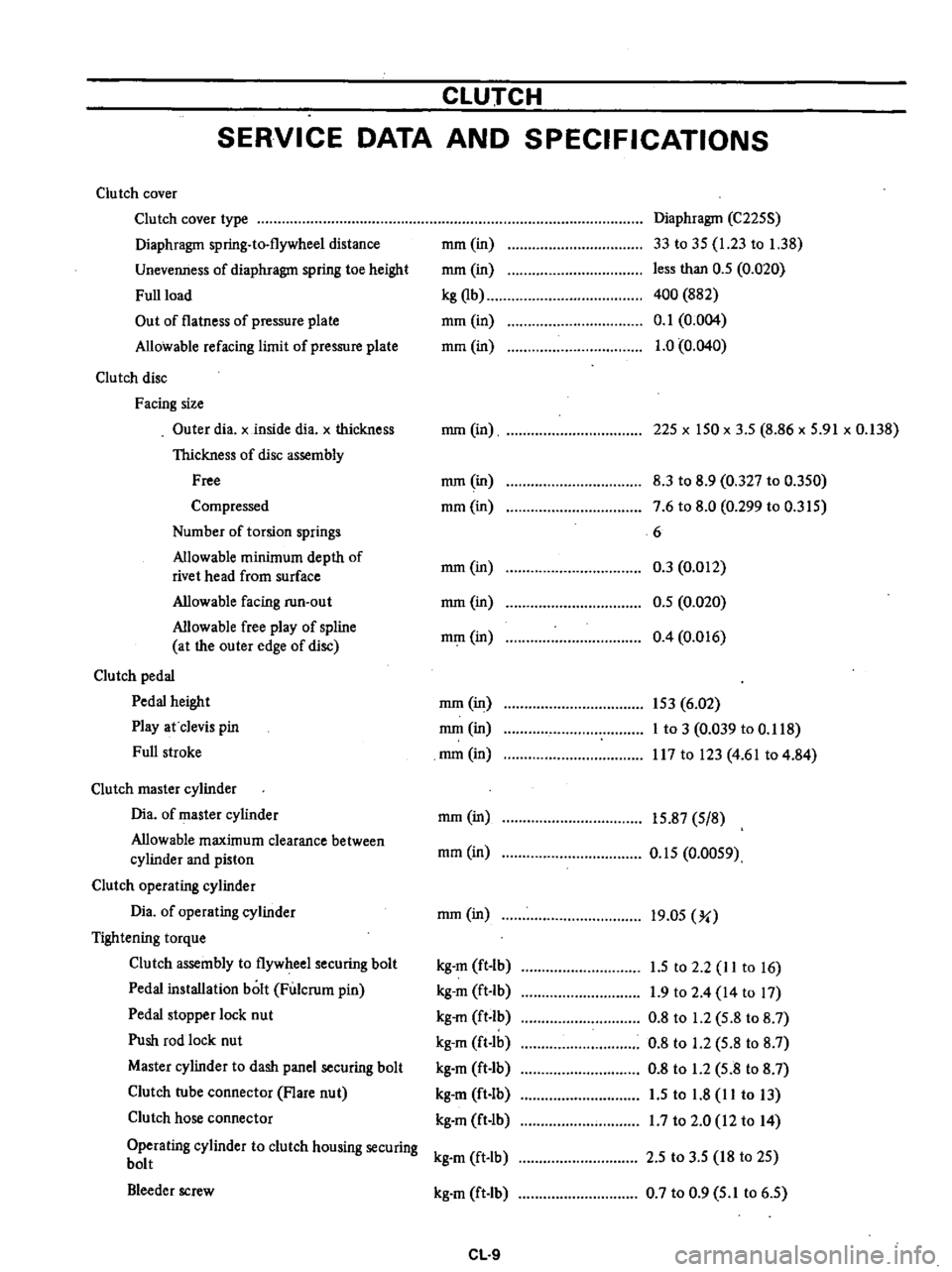
CLUTCH
SERVICE
DATA
AND
SPECIFICATIONS
Clutch
cover
Clu
tch
cover
type
Diaphragm
spring
to
flywheel
distance
Unevenness
of
diaphragm
spring
toe
height
Full
load
Out
of
flatness
of
pressure
plate
Allowable
refacing
limit
of
pressure
plate
Clutch
disc
Facing
size
Outer
dia
x
inside
dia
x
thickness
Thickness
of
disc
assembly
Free
Compressed
Number
of
torsion
springs
Allowable
minimum
depth
of
rivet
head
from
surface
Allowable
facing
run
out
Allowable
free
play
of
spline
at
the
outer
edge
of
disc
Clutch
pedal
Pedal
height
Play
at
clevis
pin
Full
stroke
Clutch
master
cylinder
Dia
of
master
cylinder
Allowable
maximum
clearance
between
cylinder
and
piston
Clutch
operating
cylinder
Dia
of
operating
cylinder
Tightening
torque
Clutch
assembly
to
flywheel
securing
bolt
Pedal
installation
bolt
Fulcrum
pin
Pedal
stopper
lock
nut
Push
rod
lock
nut
Master
cylinder
to
dash
panel
securing
bolt
Clutch
tube
connector
Flare
nut
Clutch
hose
connector
Operating
cylinder
to
clutch
housing
securing
bolt
Bleeder
screw
mm
in
mm
in
kg
Qb
mm
in
mm
in
Diaphragm
C225S
33
to
35
1
23
to
1
38
less
than
0
5
0
020
400
882
0
1
0
004
1
0
0
040
mm
in
225
x
150
x
3
5
8
86
x
5
91
x
0
138
mm
in
mm
in
8
3
to
8
9
0
327
to
0
350
7
6
to
8
0
0
299
to
0
315
6
0
3
0
012
0
5
0
020
0
4
0
016
mm
in
mm
in
mm
in
mm
in
153
6
02
mm
in
I
to
3
0
039
to
0
118
mm
in
117
to
123
4
61
to
4
84
mm
in
15
87
5
8
mm
in
0
15
0
0059
mm
in
19
05
Yo
kg
m
ft
lb
1
5
to
2
2
lito
16
kg
m
ft
Ib
1
9
to
2
4
14
to
17
kg
m
ft
b
0
8
to
1
2
5
8
to
8
7
kg
m
ft
lb
0
8
to
1
2
5
8
to
8
7
kg
m
ft
Ib
0
8
to
1
2
5
8
to
8
7
kg
m
ft
lb
1
5
to
1
8
11
to
13
kg
m
ft
lb
1
7
to
2
0
12
to
14
kg
m
ft
lb
2
5
to
3
5
18
to
25
kg
m
ft
Ib
0
7
to
0
9
5
1
to
6
5
CL
9
Page 237 of 537
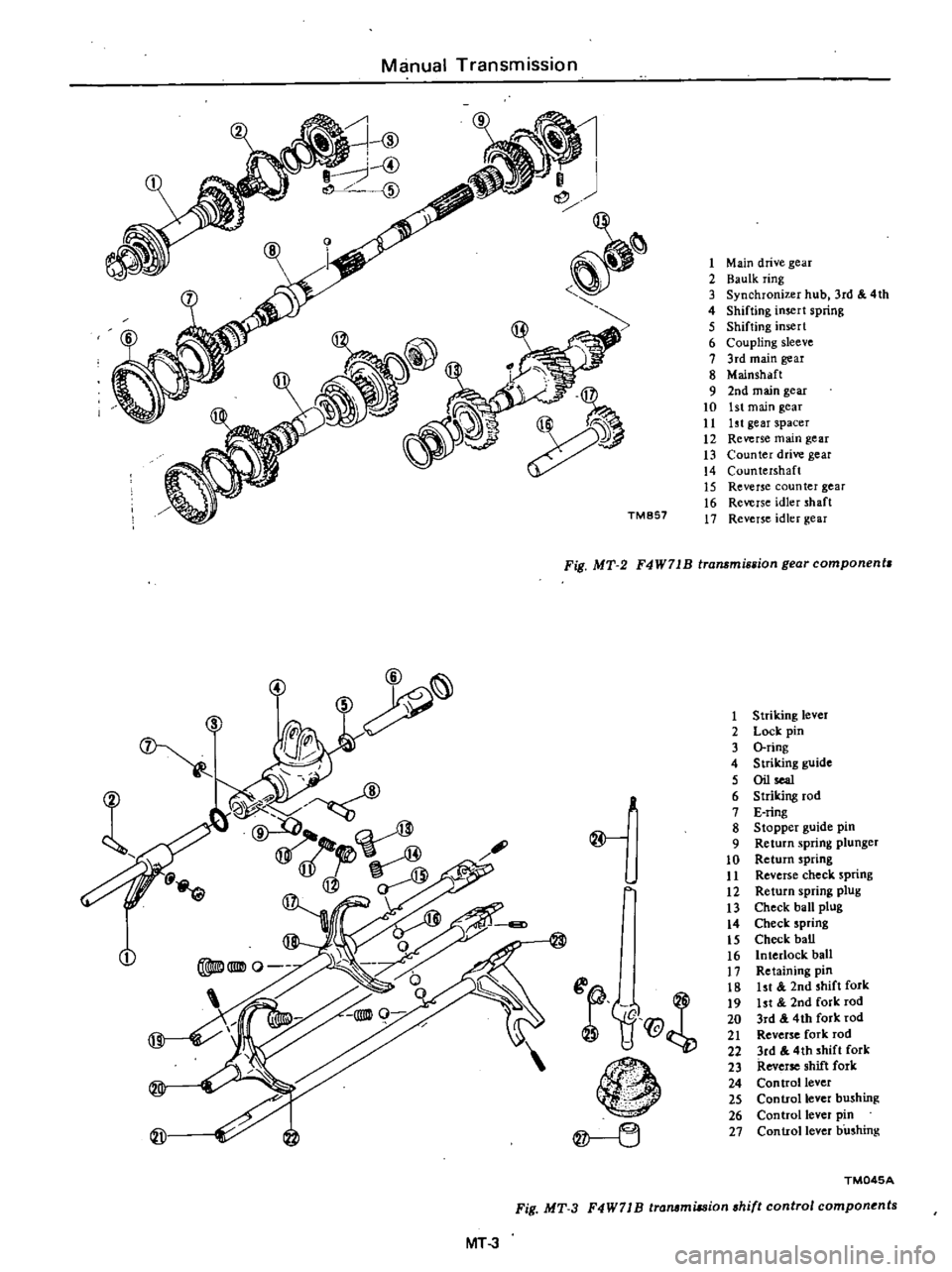
Manual
Transmission
o
cCl
4
@
@
fl
t
o
@
Fig
MT
3
MT
3
TM857
1
Main
drive
gear
2
Baulk
ring
3
d
4th
3
Synchronizer
hub
r
4
Shifting
insert
spnng
5
Shifting
insert
6
Coupling
sleeve
7
3rd
main
gear
8
Mainshaft
9
2nd
main
gear
10
1st
main
gear
11
ht
gear
spacer
12
Reverse
main
gear
13
Counter
drive
gear
14
Countershaft
15
Reverse
counter
gear
16
Reverse
idler
shaft
17
Reverse
idler
gear
Fig
MT
2
n
ear
component
F4W71B
transmlsBIO
g
@
f1f@
n
1
2
3
4
5
6
7
8
9
10
11
12
13
14
15
16
17
18
19
20
21
22
23
24
25
26
27
Striking
lever
Lock
pin
O
ring
Striking
guide
Oil
sea1
Striking
rod
E
ring
Stopper
guide
pm
Return
spring
plunger
Return
spring
Reverse
check
spnng
Return
spring
plug
Check
ball
plug
Check
spring
Check
baD
Interlock
ball
Retaining
pin
k
1st
2nd
shift
or
ht
2nd
fork
rod
3rd
4th
fork
rod
Reverse
fork
rod
3rd
4th
shift
fork
Reverse
shift
fork
Con
trollever
Control
lever
b
shmg
Control
lever
p
n
Control
lever
bushmg
TM045A
I
ponents
shift
contro
com
F4W71
B
transmuswn
Page 238 of 537
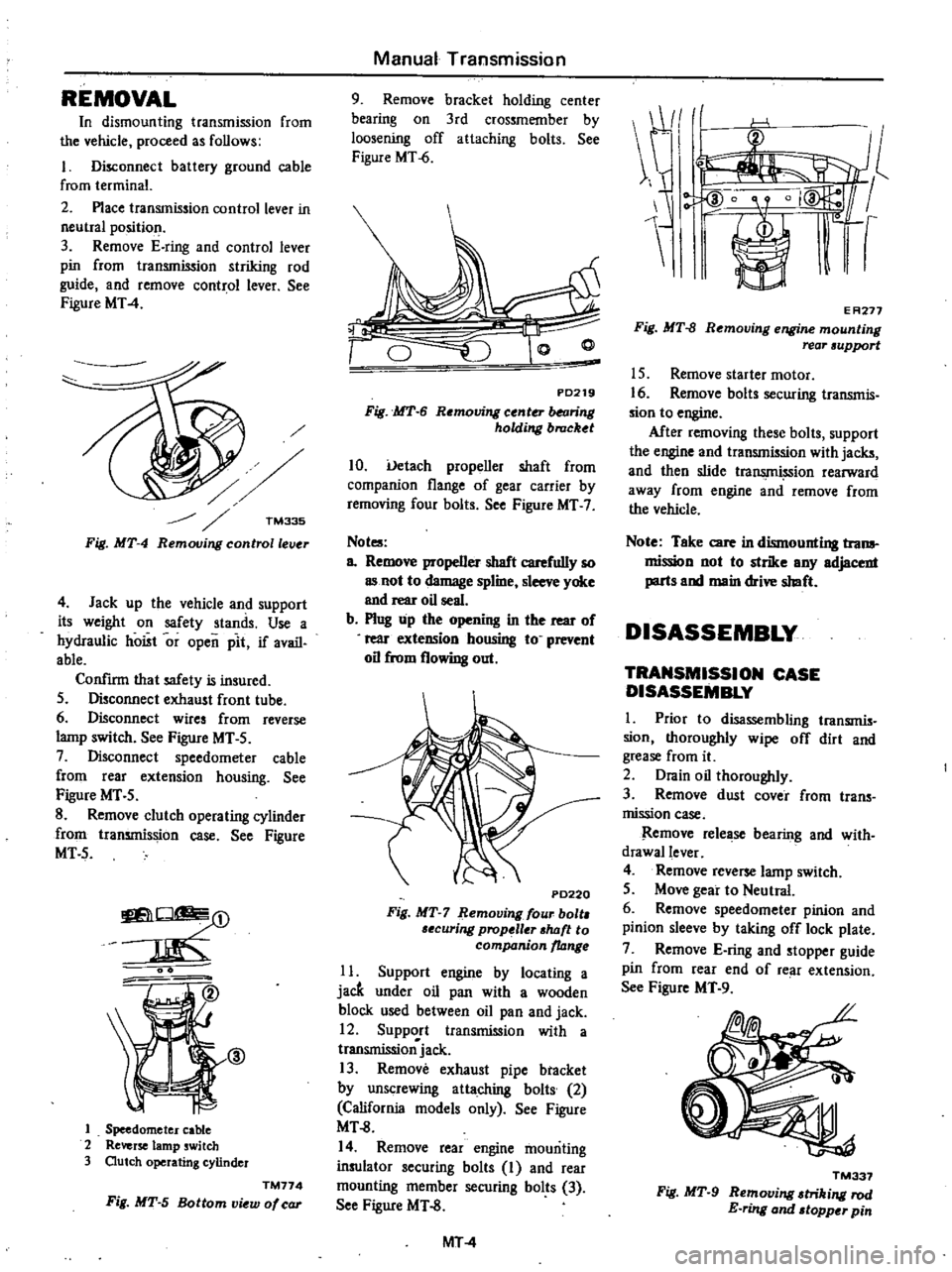
REMOVAL
In
dismounting
transmission
from
the
vehicle
proceed
as
follows
I
Disconnect
battery
ground
cable
from
terminal
2
Place
transmission
control
lever
in
neutIal
position
3
Remove
E
ring
and
control
lever
pin
from
transmission
striking
rod
guide
and
remove
control
lever
See
Figure
MT
4
TM335
Fig
MT
4
Remouing
controllelJ
r
4
Jack
up
the
vehicle
and
support
its
weight
on
safety
stands
Use
a
hydraulic
hoist
or
open
pit
if
avail
able
Confirm
that
safety
is
insured
5
Disconnect
exhaust
front
tube
6
Disconnect
wires
from
reverse
lamp
switch
See
Figure
MT
5
7
Disconnect
speedometer
cable
from
rear
extension
housing
See
Figure
MT
5
8
Remove
clutch
operating
cylinder
from
transmission
case
See
Figure
MT5
O
m
J
@
1
Speedometer
cable
2
Reverse
lamp
switch
3
Outch
operating
cylinder
TM774
Fig
MT
5
Bottom
view
of
car
Manual
Transmission
9
Remove
bracket
holding
center
bearing
on
3rd
crossmember
by
loosening
off
attaching
bolts
See
Figure
MT
6
PD219
Fig
MT
6
Removing
center
balring
holding
brucket
10
Uetach
propeller
shaft
from
companion
flange
of
gear
carrier
by
removing
four
bolts
See
Figure
MT
7
Not
a
Remove
propeller
shaft
carefully
so
as
not
to
damage
spline
sleeve
yoke
and
rear
oil
seal
b
Plug
up
the
opening
in
the
rear
of
rear
exteDSion
housing
to
prevent
oil
from
flowing
out
P0220
Fig
MT
7
Remouing
four
bolt
6ecuring
prop
ller
shtJft
to
companion
ltJnge
11
Support
engine
by
locating
a
jacft
under
oil
pan
with
a
wooden
block
used
between
oil
pan
and
jack
12
Support
transmission
with
a
transmissionjack
13
Remove
exhaust
pipe
btacket
by
unscrewing
attaching
bolts
2
California
models
only
See
Figure
MT
8
14
Remove
rear
engine
mounting
insulator
securing
bolts
I
and
rear
mounting
member
securing
bolts
3
See
Figure
MT
8
MT
4
E
A277
Fig
MT
8
Removing
engine
mounting
rear
support
15
Remove
starter
motor
16
Remove
bolt
securing
transmis
sion
to
engine
After
removing
these
bolts
support
the
engine
and
transmission
with
jacks
and
then
slide
tra
ion
rearward
away
from
engine
and
remove
from
the
vehicle
Note
Take
care
in
dismounting
trona
mission
not
to
strike
any
adjacent
parts
and
main
drive
shaft
DISASSEMBLY
TRANSMISSION
CASE
DISASSEMBLY
I
Prior
to
disassembling
transmis
sion
thoroughly
wipe
off
dirt
and
grease
from
it
2
Drain
oil
thoroughly
3
Remove
dust
cover
from
trans
mission
case
Remove
release
bearing
and
with
drawallever
4
Remove
reverse
lamp
switch
5
Move
gear
to
Neutral
6
Remove
speedometer
pinion
and
pinion
sleeve
by
taking
off
lock
plate
7
Remove
E
ring
and
stopper
guide
pin
from
rear
end
of
re
ll
extension
See
Figure
MT
9
TM337
Fig
MT
9
Removing
triking
rod
E
ring
and
topper
pin
Page 239 of 537
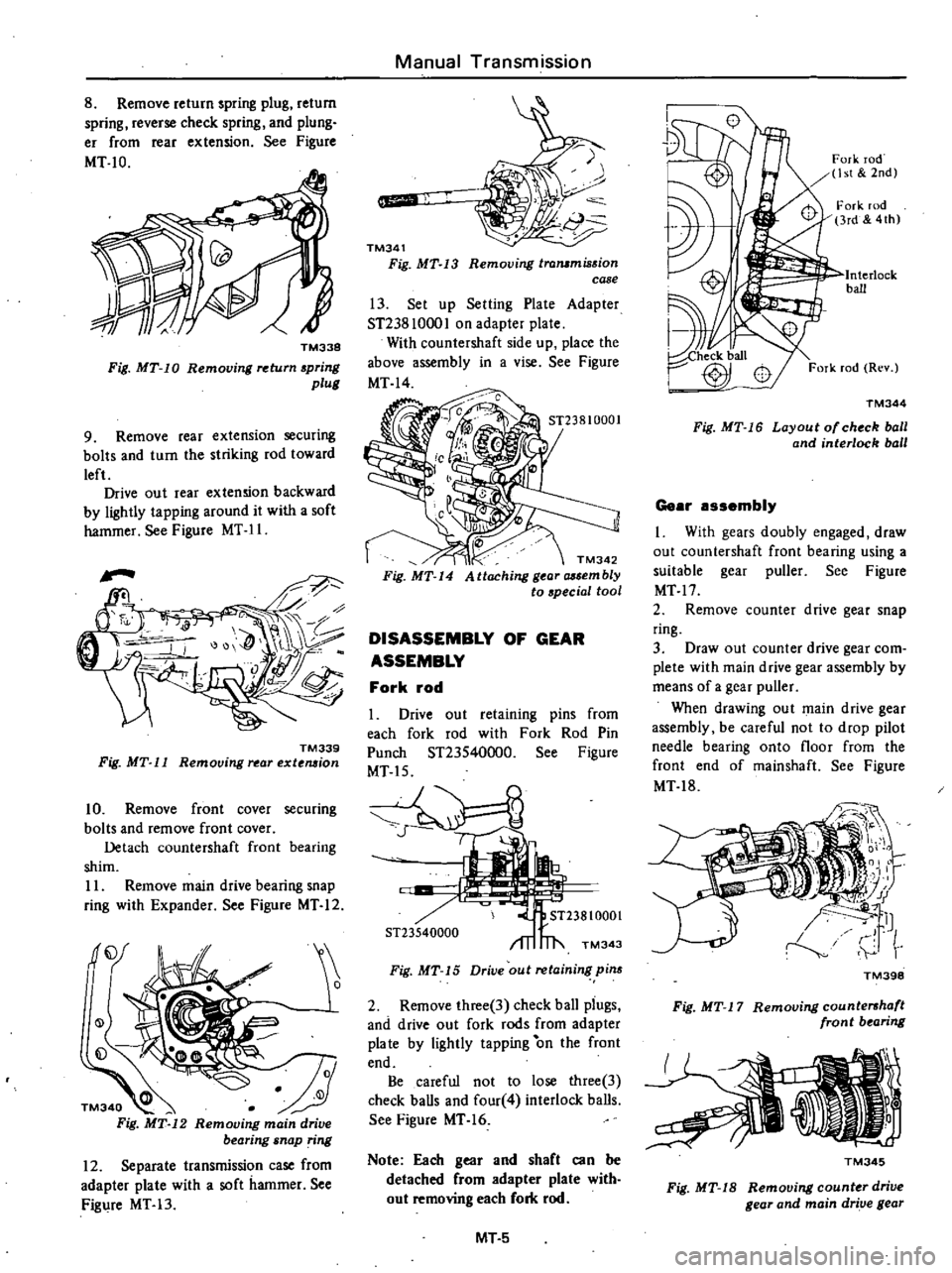
8
Remove
return
spring
plug
return
spring
reverse
check
spring
and
plung
er
from
rear
extension
See
Figure
MT
10
TM338
Fig
MT
10
Removing
return
spring
plull
9
Remove
rear
extension
securing
bolts
and
turn
the
striking
rod
toward
left
Drive
out
rear
extension
backward
by
lightly
tapping
around
it
with
a
soft
hammer
See
Figure
MT
11
TM339
Fig
MT
11
Removing
rear
extension
10
Remove
front
cover
securing
bolts
and
remove
front
cover
Detach
countershaft
front
bearing
shim
II
Remove
main
drive
bearing
snap
ring
with
Expander
See
Figure
MT
12
j
12
Separate
transmission
case
from
adapter
plate
with
a
soft
hammer
See
Figure
MT
13
Manual
Transmission
qJiiiiiI
TM341
Fig
MT
13
Removing
trammission
case
13
Set
up
Setting
Plate
Adapter
ST238
1000
I
on
adapter
plate
With
countershaft
side
up
place
the
above
assembly
in
a
vise
See
Figure
MT
14
TM342
Fig
MT
14
Attaching
l
or
mbly
to
special
tool
DISASSEMBLY
OF
GEAR
ASSEMBLY
Fork
rod
Drive
out
retaining
pins
from
each
fork
rod
with
Fork
Rod
Pin
Punch
ST23540000
See
Figure
MT
15
S
ST23540000
TM343
Fig
MT
15
Drive
out
retaining
pim
2
Remove
three
3
check
ball
piugs
and
drive
out
fork
rods
from
adapter
pia
te
by
lightly
tapping
on
the
front
end
Be
careful
not
to
lose
three
3
check
balls
and
four
4
interlock
balls
See
Figure
MT
16
Note
Each
gear
and
shaft
can
be
detached
from
adapter
plate
with
out
removing
each
fork
rod
MT
5
Fork
rod
ht
2nd
Interlock
ball
TM344
Fig
MT
16
Layout
o
ch
ck
boll
and
interlock
ball
Gear
assembly
I
With
gears
doubly
engaged
draw
out
countershaft
front
bearing
using
a
suitable
gear
puller
See
Figure
MT
17
2
Remove
counter
drive
gear
snap
ring
3
Draw
out
counter
drive
gear
com
plete
with
main
drive
gear
assembly
by
means
of
a
gear
puller
When
drawing
out
main
drive
gear
assembly
be
careful
not
to
drop
pilot
needle
bearing
onto
floor
from
the
front
end
of
mainshaft
See
Figure
MT
18
TM398
Fig
MT
17
Removing
countershaft
front
b
aring
TM345
Fig
MT
18
Removing
count
r
drive
gear
and
main
drive
gear
Page 242 of 537
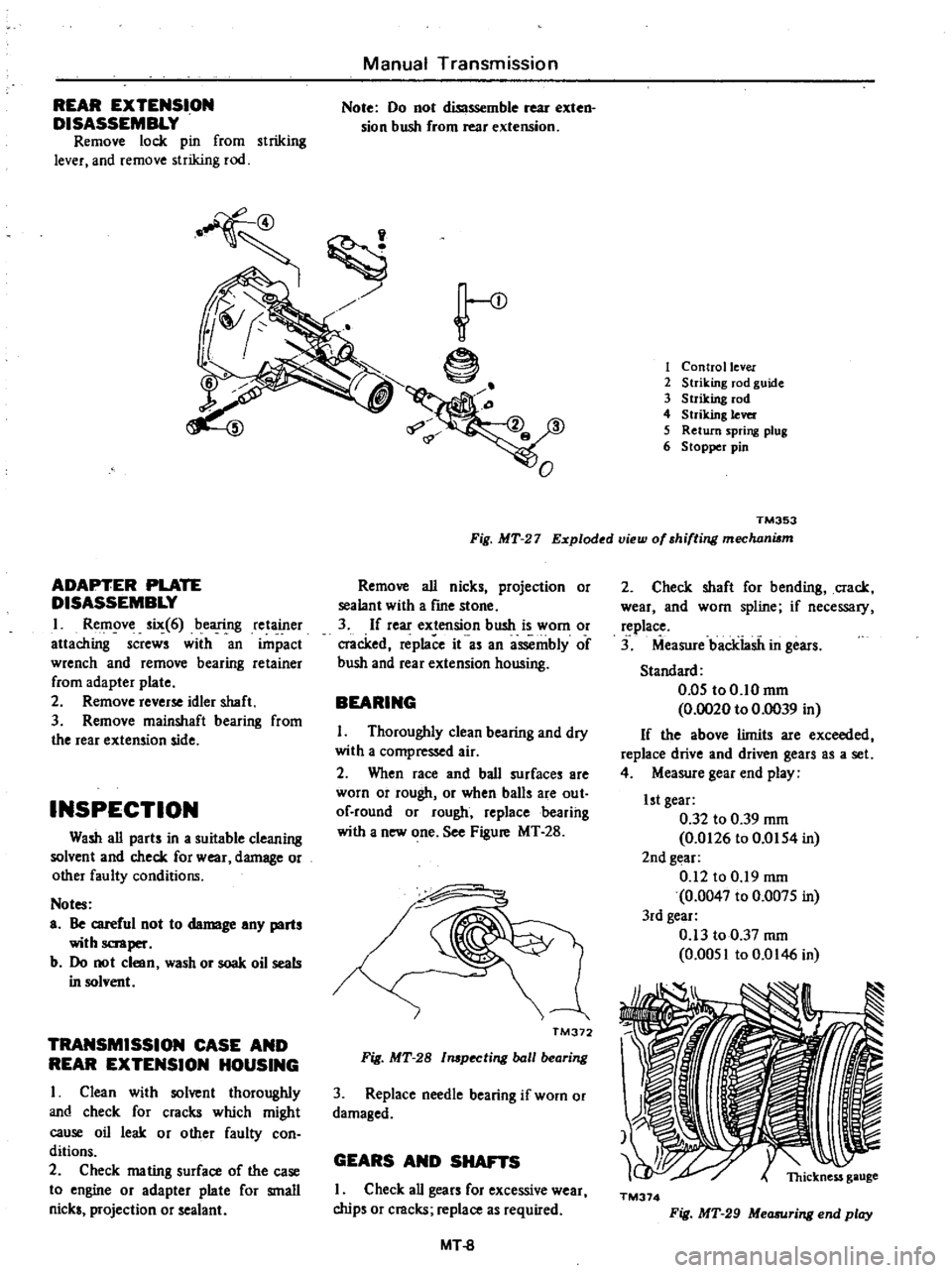
REAR
EXTENSION
DISASSEMBLY
Remove
lock
pin
from
striking
lever
and
remove
striking
rod
Manual
Transmission
Note
00
not
diSlssemble
rear
exten
sion
bush
from
rear
extension
ADAPTER
PLATE
DISASSEMBLY
I
Remove
six
6
bearing
retainer
attaching
screws
with
an
impact
wrench
and
remove
bearing
retainer
from
adapter
plate
2
Remove
reverse
idler
shaft
3
Remove
mainshaft
bearing
from
the
rear
extension
side
INSPECTION
Wash
all
parts
in
a
suitable
cleaning
solvent
and
check
for
wear
damage
or
other
faulty
conditions
Notes
a
Be
careful
not
to
damage
any
parts
with
scraper
b
00
not
clean
wash
or
soak
oil
seals
in
solvent
TRANSMISSION
CASE
AND
REAR
EXTENSION
HOUSING
I
Clean
with
solvent
thoroughly
and
check
for
cracks
which
might
cause
oil
leak
or
other
faulty
con
ditions
2
Check
mating
surface
of
the
case
to
engine
or
adapter
plate
for
small
nicks
projection
or
sealant
e
1
Control
lever
2
Striking
rod
guide
3
Striking
rod
4
Striking
lever
5
Return
spring
plug
6
Stopper
pin
TM353
Fig
MT
27
Exploded
view
of
shifting
mechani6m
Remove
all
nicks
projection
or
sealant
with
a
frne
stone
3
If
rear
extension
bush
is
worn
or
cracked
replace
it
as
an
assembly
of
bush
and
rear
extension
housing
BEARING
I
Thoroughly
clean
bearing
and
dry
with
a
compressed
air
2
When
race
and
ball
surfaces
are
worn
or
rough
or
when
balls
are
out
of
round
or
rough
replacebearihg
with
a
new
one
See
Figure
MT
28
I
TM372
Fig
MT
28
l
pecting
ball
bearing
3
Replace
needle
bearing
if
worn
or
damaged
GEARS
AND
SHAFTS
I
Check
all
gears
for
excessive
wear
chips
or
cracks
replace
as
required
MT
8
2
Check
shaft
for
bending
crack
wear
and
worn
spline
if
necessary
replace
3
Measure
backiasii
in
gears
Standard
0
05
to0
10mm
0
0020
to
0
0039
in
If
the
above
limits
are
exceeded
replace
drive
and
driven
gears
as
a
set
4
Measure
gear
end
play
1st
gear
0
32
to
0
39
mm
0
0126
to
0
0154
in
2nd
gear
0
12
to
0
19
mm
0
0047
to
0
0075
in
3rd
gear
0
13
to
0
37
mm
0
0051
to
0
0146
in
TM374
Fig
MT
29
Measuring
end
play