lock DATSUN PICK-UP 1977 Manual PDF
[x] Cancel search | Manufacturer: DATSUN, Model Year: 1977, Model line: PICK-UP, Model: DATSUN PICK-UP 1977Pages: 537, PDF Size: 35.48 MB
Page 243 of 537
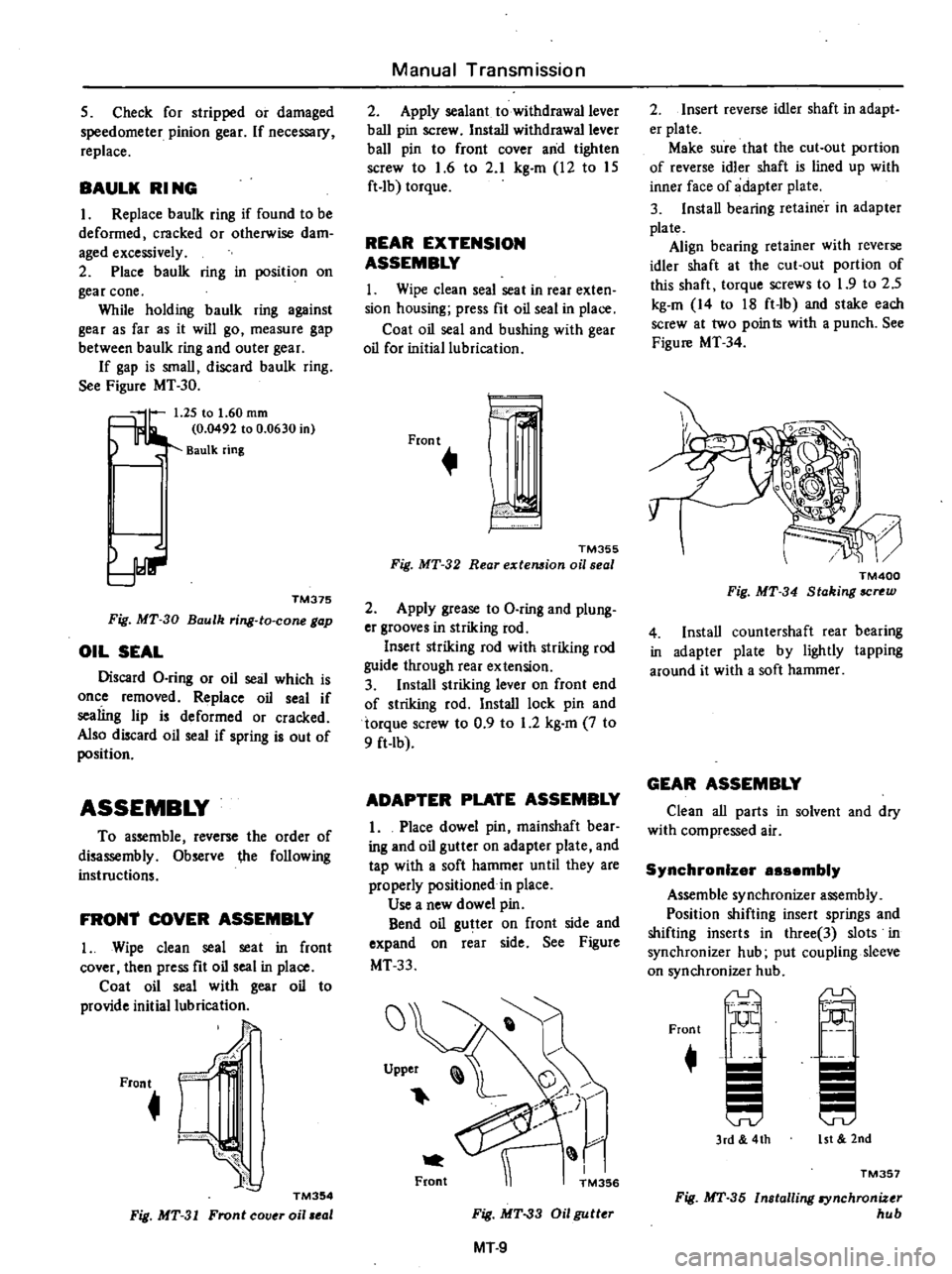
5
Check
for
stripped
or
damaged
speedometer
pinion
gear
If
necessary
replace
BAULK
RI
NG
I
Replace
baulk
ring
if
found
to
be
deformed
cracked
or
otherwise
dam
aged
excessively
2
Place
baulk
ring
in
position
on
gear
cone
While
holding
baulk
ring
against
gear
as
far
as
it
will
go
measure
gap
between
baulk
ring
and
outer
gear
If
gap
is
small
discard
baulk
ring
See
Figure
MT
30
5
lr
1
25
to
1
60
rom
0
0492
to
0
0630
in
Baulk
ring
TM375
Fig
MT
30
Baulk
ring
to
cone
gap
OIL
SEAL
Discard
O
ring
or
oil
seal
which
is
once
removed
Replace
oil
seal
if
sealing
lip
is
deformed
or
cracked
Also
discard
oil
seal
if
spring
is
out
of
position
ASSEMBLY
To
assemble
reverse
the
order
of
disassembly
Observe
ihe
following
instructions
FRON1
COVER
ASSEMBLY
I
Wipe
clean
seal
seat
in
front
cover
then
press
fit
oil
seal
in
place
Coat
oil
seal
with
gear
oil
to
provide
initial
lubrication
Front
J
f
C
J
TM354
Fig
MT
31
Front
cov
oil
eol
Manual
Transmission
2
Apply
sealant
to
withdrawal
lever
ball
pin
screw
Install
withdrawal
lever
ball
pin
to
front
cover
and
tighten
screw
to
1
6
to
2
1
kg
m
12
to
15
ft
lb
torque
REAR
EXTENSION
ASSEMBLY
1
Wipe
clean
seal
seat
in
rear
exten
sion
housing
press
fit
oil
seal
in
place
Coat
oil
seal
and
bushing
with
gear
oil
for
initial
lubrication
Front
h
TM355
Fig
MT
32
Rear
extemion
oil
seal
2
Apply
grease
to
O
ring
and
plung
er
grooves
in
striking
rod
Insert
striking
rod
with
striking
rod
guide
through
rear
extension
3
Install
striking
lever
on
front
end
of
striking
rod
Install
lock
pin
and
torque
screw
to
0
9
to
1
2
kg
m
7
to
9
ft
Ib
ADAPTER
PLATE
ASSEMBLY
1
Place
dowel
pin
mainshaft
bear
ing
and
oil
gutter
on
adapter
plate
and
tap
with
a
soft
hammer
until
they
are
properly
positioned
in
place
Use
a
new
dowel
pin
Bend
oil
gutter
on
front
side
and
expand
on
rear
side
See
Figure
MT33
J
7
r
M356
Upper
Front
Fig
MT
33
Oil
gutter
MT
9
2
Insert
reverse
idler
shaft
in
adapt
er
plate
Make
sure
that
the
cut
out
portion
of
reverse
idler
shaft
is
lined
up
with
inner
face
of
adapter
plate
3
Install
bearing
retainer
in
adapter
plate
Align
bearing
retainer
with
reverse
idler
shaft
at
the
cut
out
portion
of
this
shaft
torque
screws
to
1
9
to
2
5
kg
m
14
to
18
ft
lb
and
stake
each
screw
at
two
poin
Is
with
a
punch
See
Figure
MT
34
TM400
Fig
MT
34
Staking
SCN
W
4
Install
countershaft
rear
bearing
in
adapter
plate
by
lightly
tapping
around
it
with
a
soft
hammer
GEAR
ASSEMBLY
Clean
all
parts
in
solvent
and
dry
with
compressed
air
Synchronizer
888embly
Assemble
synchronizer
assembly
Position
shifting
insert
springs
and
shifting
inserts
in
three
3
slots
in
synchronizer
hub
put
coupling
sleeve
on
synchronizer
hub
r
Front
3rd
4th
15t
2nd
TM351
Fig
MT
35
Installing
synchronizer
hub
Page 246 of 537
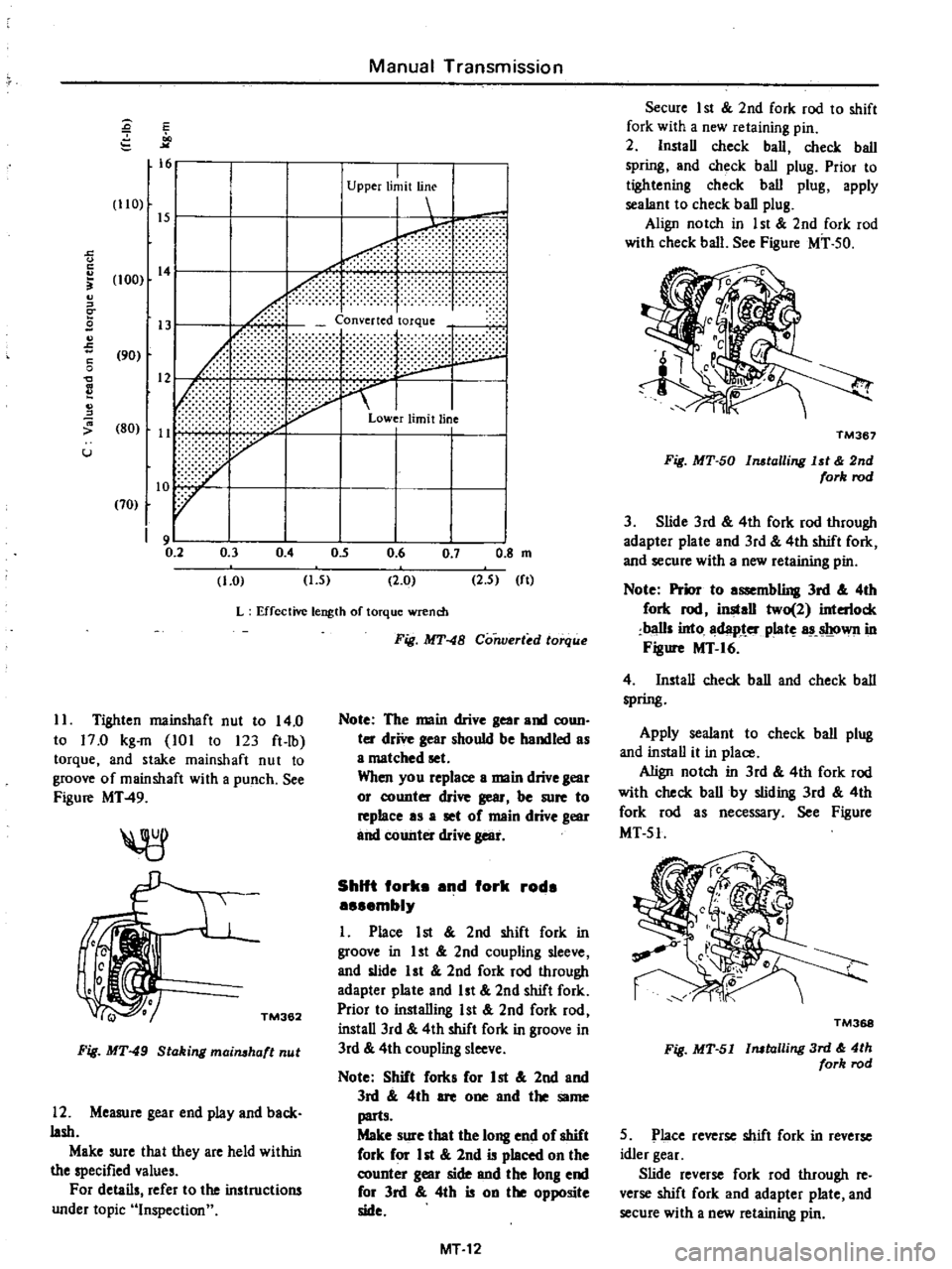
I
Upper
limit
line
I
r
6
1
f
fdl
13
Converted
torque
90
I
Lower
limit
line
80
11
70
10
V
S
s
15
110
15
c
u
c
c
9
S
c
o
C
U
100
14
9
0
2
0
3
1
0
0
4
Manual
Transmission
0
5
0
6
2
0
0
7
0
8
m
2
5
It
1
5
L
Effective
length
of
torque
wrench
Fig
MT
48
CO
1Vert
d
torque
11
Tighten
mainshaft
nut
to
14
0
to
17
0
kg
m
101
to
123
ft
lb
torque
and
stake
mainshaft
nut
to
groove
of
main
shaft
with
a
punch
See
Figure
MT49
TM362
Fig
MT
49
Staking
mai
haft
nut
12
Measure
gear
end
play
and
back
lash
Make
sure
that
they
are
held
within
the
specified
values
For
details
refer
to
the
instructions
under
topic
Inspection
Note
The
main
drive
gear
and
coun
ter
driVe
gear
should
be
handled
as
a
matched
set
When
you
replace
a
main
drive
gear
or
counter
drive
gear
be
sure
to
replace
as
a
set
of
main
drive
gear
and
counter
drive
gear
ShUt
fork
nd
fork
rod
mbly
I
Place
1st
2nd
shift
fork
in
groove
in
1st
2nd
coupling
sleeve
and
slide
1st
2nd
fork
rod
through
adapter
plate
and
1st
2nd
shift
fork
Prior
to
installing
1st
2nd
fork
rod
install
3rd
4th
shift
fork
in
groove
in
3rd
4th
coupling
sleeve
Note
Shift
forks
for
1st
2nd
and
3rd
4th
are
one
and
the
same
parts
Make
sure
that
the
long
end
of
shift
fork
for
lot
2nd
is
placed
on
the
counter
gear
side
and
the
long
end
for
3rd
4th
is
on
the
e
side
MT12
Secure
1st
2nd
fork
rod
to
shift
fork
with
a
new
retaining
pin
2
Install
check
ball
check
ball
spring
and
check
ball
plug
Prior
to
tightening
check
ball
plug
apply
sealant
to
check
ball
plug
Align
notch
in
1st
2nd
fork
rod
with
check
ball
See
Figure
MT
50
TM367
Fig
MT
50
l
talling
1st
2nd
fork
rod
3
Slide
3rd
4th
fork
rod
through
adapter
plate
and
3rd
4th
shift
fork
and
secure
with
a
new
retaining
pin
Note
Prior
to
a
mbling
3rd
4th
fork
rod
install
two
2
interlock
balls
into
dap
er
plat
own
in
Figure
MT
16
4
Install
check
ball
and
check
ball
spring
Apply
sealant
to
check
ball
plug
and
install
it
in
place
Align
notch
in
3rd
4th
fork
rod
with
check
ball
by
sliding
3rd
4th
fork
rod
as
necessary
See
Figure
MT51
TM368
Fig
MT
51
Installing
3rd
4th
fork
rod
5
Place
reverse
shift
fork
in
reverse
idler
gear
Slide
reverse
fork
rod
through
re
verse
shift
fork
and
adapter
plate
and
secure
with
a
new
retaining
pin
Page 247 of 537
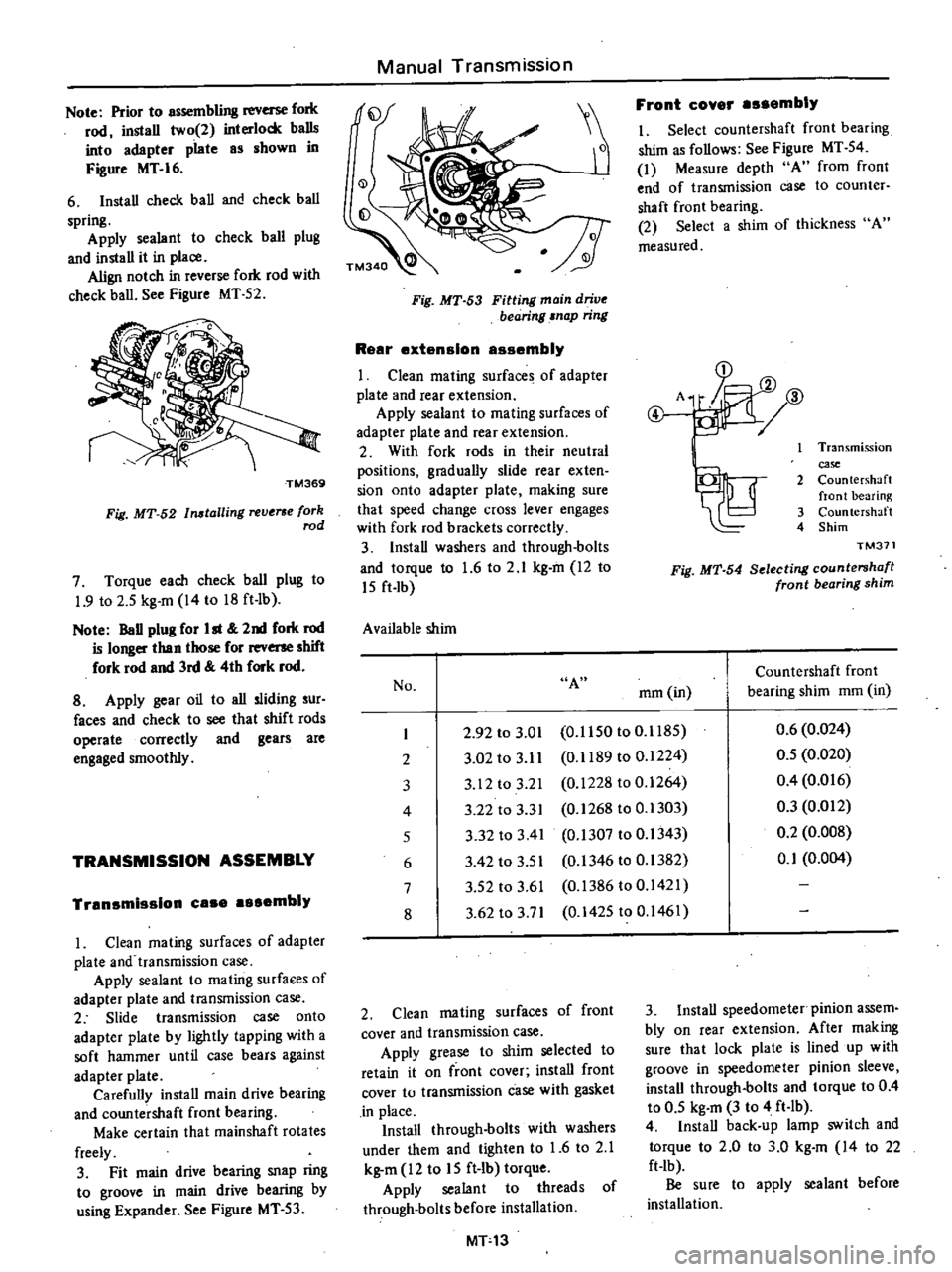
Note
Prior
to
assembling
reverse
fork
rod
instaU
two
2
interlock
balls
into
adapter
piate
as
shown
in
Figure
MT
I6
6
Install
check
ball
and
check
ball
spring
Apply
sealant
to
check
ball
plug
and
install
it
in
place
Align
notch
in
reverse
fork
rod
with
check
ball
See
Figure
MT
52
TM369
Fig
MT
52
Installing
reverse
fork
rod
7
Torque
each
check
ball
plug
to
1
9
to
2
5
kg
m
14
to
18
ft
Ib
Note
BaD
plug
for
ht
2nd
fork
rod
is
longer
than
those
for
rev
shift
fork
rod
and
3rd
4th
fork
rod
8
Apply
gear
oil
to
all
sliding
sur
faces
and
check
to
see
that
shift
rods
operate
correctly
and
gears
are
engaged
smoothly
TRANSMISSION
ASSEMBLY
Tran
mis
lon
ea
mbly
1
Clean
mating
surfaces
of
adapter
plate
and
transmission
case
Apply
sealant
to
mating
surfaces
of
adapter
plate
and
transmission
case
2
Slide
transmission
case
onto
adapter
plate
by
lightly
tapping
with
a
soft
hammer
until
case
bears
against
adapter
plate
Carefully
install
main
drive
bearing
and
countershaft
front
bearing
Make
certain
that
mainshaft
rotates
freely
3
Fit
main
drive
bearing
snap
ring
to
groove
in
main
drive
bearing
by
using
Expander
See
Figure
MT
53
Manual
Transmission
Fig
MT
53
Fitting
main
drive
bearing
snap
ring
R
ar
xt
nslon
ass
mbly
I
Clean
mating
surfaces
of
adapter
plate
and
fear
extension
Apply
sealant
to
mating
surfaces
of
adapter
plate
and
rear
extension
2
With
fork
rods
in
their
neutral
positions
graduaUy
slide
rear
exten
sion
onto
adapter
plate
making
sure
that
speed
change
cross
lever
engages
with
fork
rod
brackets
correctly
3
Install
washers
and
through
bolts
and
torque
to
1
6
to
2
1
kg
m
12
to
15
ft
lb
Available
shim
Front
eov
r
s
mbly
I
Select
countershaft
front
bearing
shim
as
follows
See
Figure
MT
54
1
Measure
depth
A
from
front
end
of
transmission
case
to
counter
shaft
front
bearing
2
Select
a
shim
of
thickness
A
measured
D
A
JJ
ID
@
2J1
I
Transmission
case
2
Countershaft
front
bearing
3
Countershaft
4
Shim
TM371
Fig
MT
54
Selecting
countershafl
front
bearing
shim
No
A
Countershaft
front
rnm
in
bearing
shim
mm
in
I
2
92
to
3
01
0
1150
to
0
1185
0
6
0
024
2
3
02
to
3
11
0
1189
to
0
1224
0
5
0
020
3
3
12
to
3
21
0
1228
to
0
1264
0
4
0
016
4
3
22
to
3
3
I
0
1268
to
0
1303
0
3
0
012
5
3
32
to
3
41
0
1307
to
0
1343
0
2
0
008
6
3
42
to
3
5
I
0
1346
to
0
1382
0
1
0
004
7
3
52
to
3
61
0
1386
to
0
1421
8
3
62
to
3
71
0
1425
to
0
1461
2
Clean
mating
surfaces
of
front
cover
and
transmission
case
Apply
grease
to
shim
selected
to
retain
it
on
front
cover
install
front
cover
to
transmission
case
with
gasket
in
place
Install
through
bolts
with
washers
under
them
and
tighten
to
1
6
to
2
1
kg
m
12
to
15
ft
lb
torque
Apply
sealant
to
threads
of
through
bolts
before
installation
MT13
3
Install
speedometer
pinion
assem
bly
on
rear
extension
After
making
Sure
that
lock
plate
is
lined
up
with
groove
in
speedometer
pinion
sleeve
install
through
bolts
and
torque
to
0
4
to
0
5
kg
m
3
to
4
ft
lb
4
Install
back
up
lamp
switch
and
torque
to
2
0
to
3
0
kg
m
14
to
22
ft
lb
Be
sure
to
apply
sealant
before
installation
Page 250 of 537
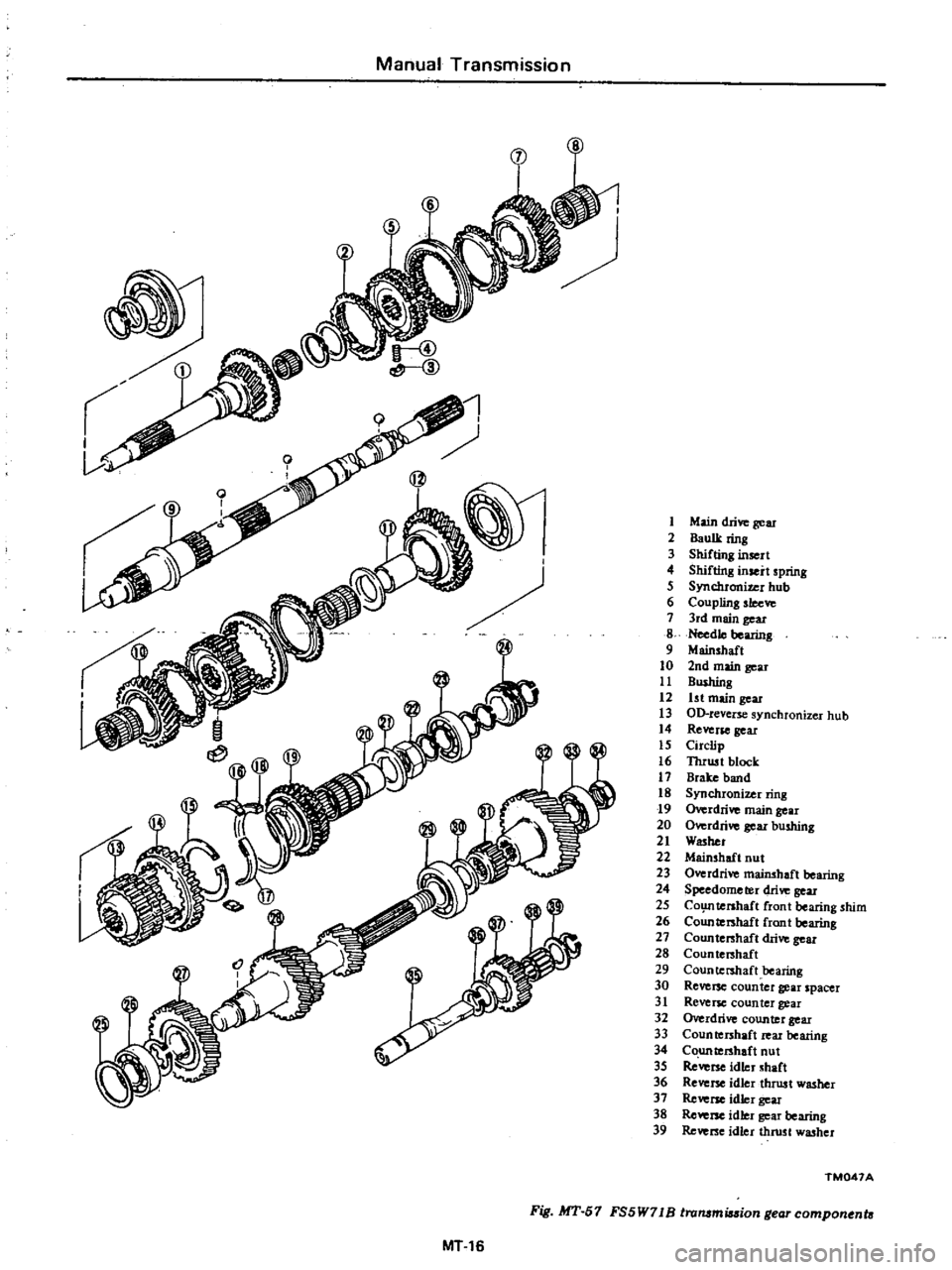
Manual
Transmission
j
W
h
I
l
1
Main
drive
gear
2
Baulk
ring
3
Shifting
insert
4
Shifting
insert
spring
5
Synchronir
c
r
hub
6
Coupling
slee
7
3rd
main
gear
g
Needle
bearing
9
Mainshaft
10
2nd
main
gear
11
Bushing
12
1st
main
gear
13
O
revcrse
synchronizer
hub
14
Rever
gear
15
Circlip
16
Thrwt
block
t
7
Brake
band
18
Synchronizer
ring
19
Overdrive
main
gear
20
Overdrive
gear
bushing
21
Washer
22
Mainshaft
nut
13
Overdrive
mainshaft
bearing
24
Speedometer
drive
gear
25
COlplteBhaft
fr
mt
bearing
shim
26
Countershaft
front
bearing
27
Countershaft
drive
gear
28
Coontcrshaft
29
Countershaft
bearing
30
Reverse
counter
gear
spacer
31
Rever
C
counter
gear
32
rdrive
counter
gear
33
Countershaft
zear
bearing
34
C
untershaft
nut
3S
Reverse
idler
lIhaCt
36
Reverse
idlcrthrust
washer
37
Reverse
idler
gear
38
Reye
nc
idler
gear
bearing
39
Reverse
idler
thrust
w8
her
TM041A
MT
16
Fig
MT
51
FS5W11B
tru
miasion
gear
componenta
Page 251 of 537
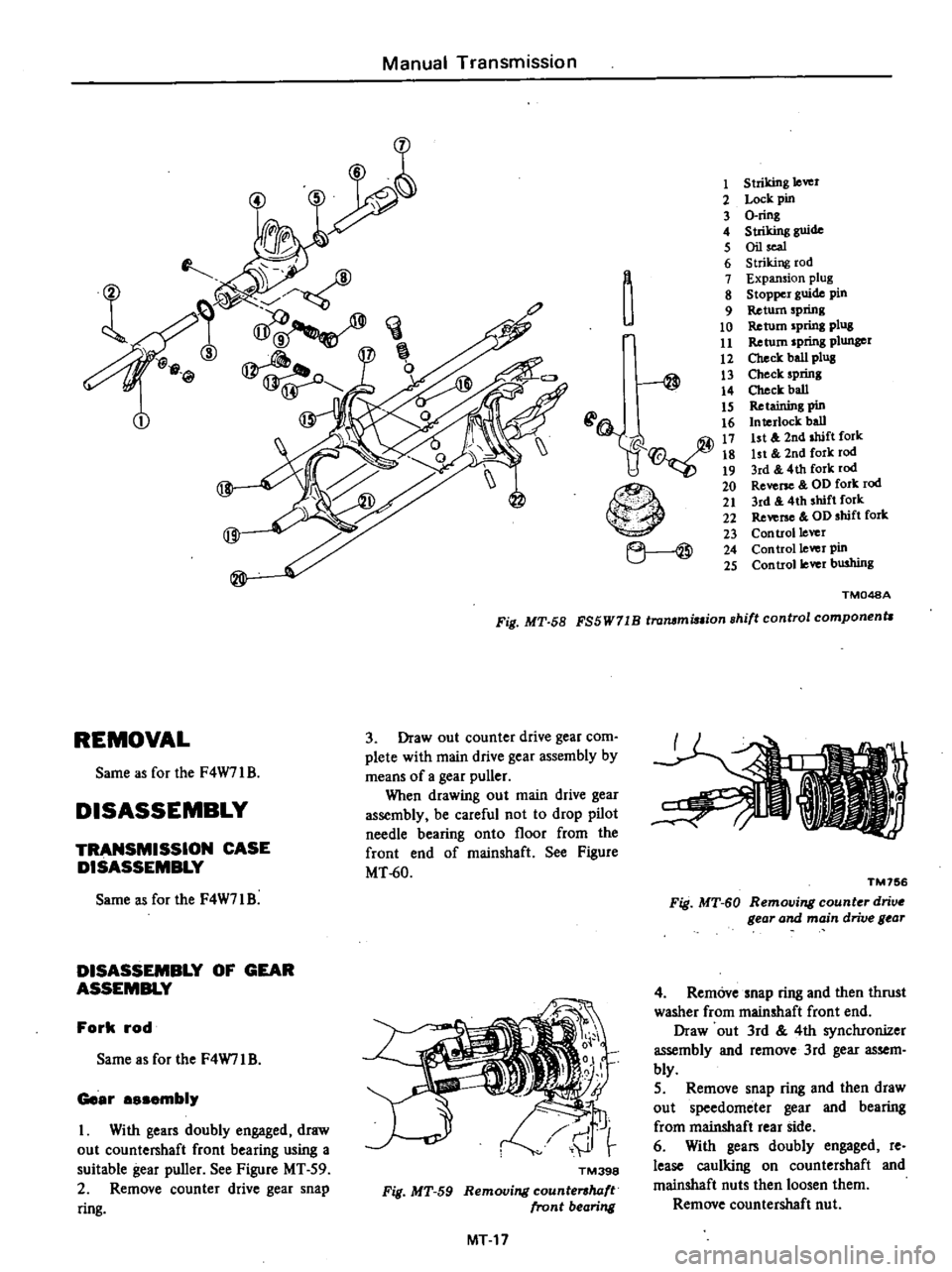
Manual
Transmission
CD
t
e
I
2
3
4
5
6
7
8
9
10
11
12
13
14
17
18
19
O
20
o
21
24
25
j
@
Striking
lever
Lock
pin
Q
ring
Striking
guide
Oil
seal
Striking
rod
Expansion
plug
Stopper
guide
pin
Return
spring
Return
spring
plug
Return
spring
plunger
Check
ball
plUS
Check
spring
Check
ball
Retaining
pin
Interlock
ball
ist
2nd
shift
fork
1st
2nd
fork
rod
3rd
4th
fork
rod
Reverse
OD
fork
rod
3rd
4th
shift
fork
Revene
OD
shift
fork
Con
trol1ever
Con
trol1cver
pin
Con
trollever
bushing
TM048A
Fig
MT
58
FS5W71B
trammi
ion
shift
control
component
3
Draw
out
counter
drive
gear
com
plete
with
main
drive
gear
assembly
by
means
of
a
gear
puller
When
drawing
out
main
drive
gear
assembly
be
careful
not
to
drop
pilot
needle
bearing
onto
floor
from
the
front
end
of
mainshaft
See
Figure
MT
60
REMOVAL
Same
as
for
the
F4W71B
DISASSEMBLY
TRANSMISSION
CASE
DISASSEMBLY
Same
as
for
the
F4W71
B
DISASSEMBLY
OF
GEAR
ASSEMBLY
Fork
rod
Same
as
for
the
F4W71
B
Geer
sembi
I
With
gears
doubly
engaged
draw
out
counte
haft
front
bearing
using
a
suitable
gear
puller
See
Figure
MT
59
2
Remove
counter
drive
gear
snap
ring
TM398
Fig
MT
59
Removing
countershaft
front
bearing
MT
17
TM756
Fig
MT
60
Removing
counter
drive
gear
and
main
drive
gear
4
Rem6vesnap
ring
and
then
thrust
washer
from
mainshaft
front
end
Draw
out
3rd
4th
synchronizer
assembly
and
remove
3rd
gear
assem
bly
5
Remove
snap
ring
and
then
draw
out
speedometer
gear
and
bearing
from
mainshaft
rear
side
6
With
gea
doubly
engaged
re
lease
caulking
on
countershaft
and
mainshaft
nuts
then
loosen
them
Remove
countershaft
nut
Page 252 of 537
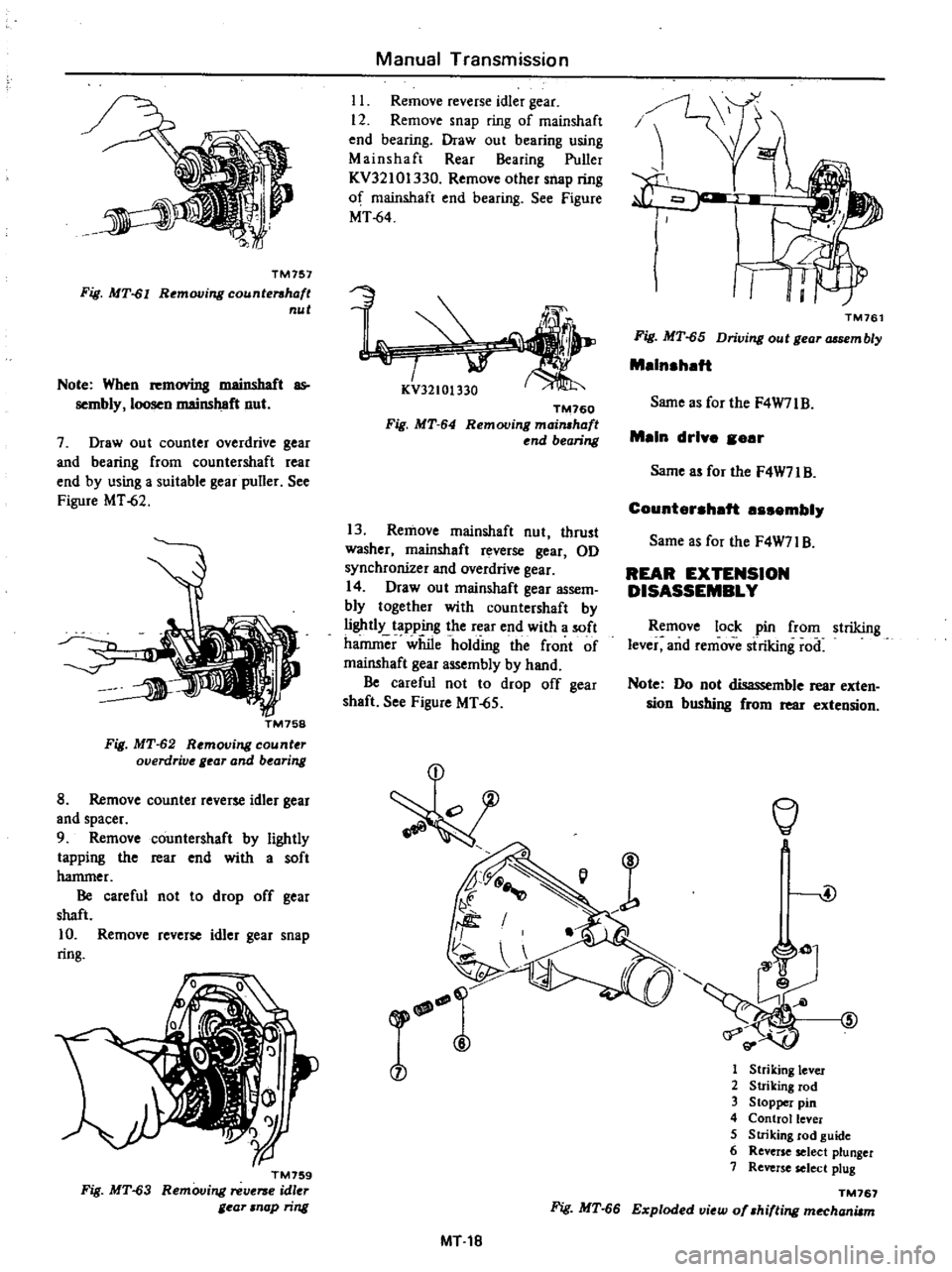
TM757
Fig
MT
61
Removing
counterahaft
nut
Note
When
removing
mainshaft
as
sembly
loosen
mainshaft
nut
7
Draw
out
counter
overdrive
gear
and
bearing
from
countershaft
rear
end
by
using
a
suitable
gear
puller
See
Figure
MT
62
TM758
Fig
MT
62
Removing
count
r
overdriv
gear
and
bearing
8
Remove
counter
reverse
idler
gear
and
spacer
9
Remove
countershaft
by
lightly
tapping
the
rear
end
with
a
soft
hammer
Be
careful
not
to
drop
off
gear
shaft
10
Remove
reverse
idler
gear
snap
ring
TM759
Fig
MT
63
Removing
reverse
idler
gear
nap
ring
Manual
Transmission
II
Remove
reverse
idler
gear
12
Remove
snap
ring
of
mainshaft
end
bearing
Draw
out
bearing
using
Mainshaft
Rear
Bearing
Puller
KV32101330
Remove
other
snap
ring
of
mainshafl
end
bearing
See
Figure
MT
64
tw
KV32101330
TM160
Fig
MT
64
Removing
mai
haft
nd
bearing
13
Remove
mainshaft
nut
thrust
washer
mainshaft
reverse
gear
OD
synchronizer
and
overdrive
gear
14
Draw
out
mainshaft
gear
assem
bly
together
with
countershaft
by
lightly
tapping
the
rear
end
with
a
soft
hainmer
Me
holding
the
front
of
mainshaft
gear
assembly
by
hand
Be
careful
not
to
drop
off
gear
shaft
See
Figure
MT
65
k
r
IT
TM761
Fig
MT
65
Driving
out
gear
sembly
Malnahaft
Same
as
for
the
F4W7IB
Main
drive
ear
Same
as
for
the
F4W71
B
Counterahaft
aaaembly
Same
as
for
the
F4W7l
B
REAR
EXTENSION
DISASSEMBLY
Remove
lock
pin
from
striking
lever
and
remove
siriking
rod
Note
Do
not
disassemble
rear
exten
sion
bushing
from
rear
extension
J
l
J
@
1
Striking
lever
2
Striking
rod
3
Stopper
pin
4
Control
lever
5
Striking
rod
guide
6
Reverse
select
plunger
7
Reverse
select
plug
TM767
Fig
MT
66
Exploded
view
of
shifting
mechanilm
MT1B
Page 253 of 537
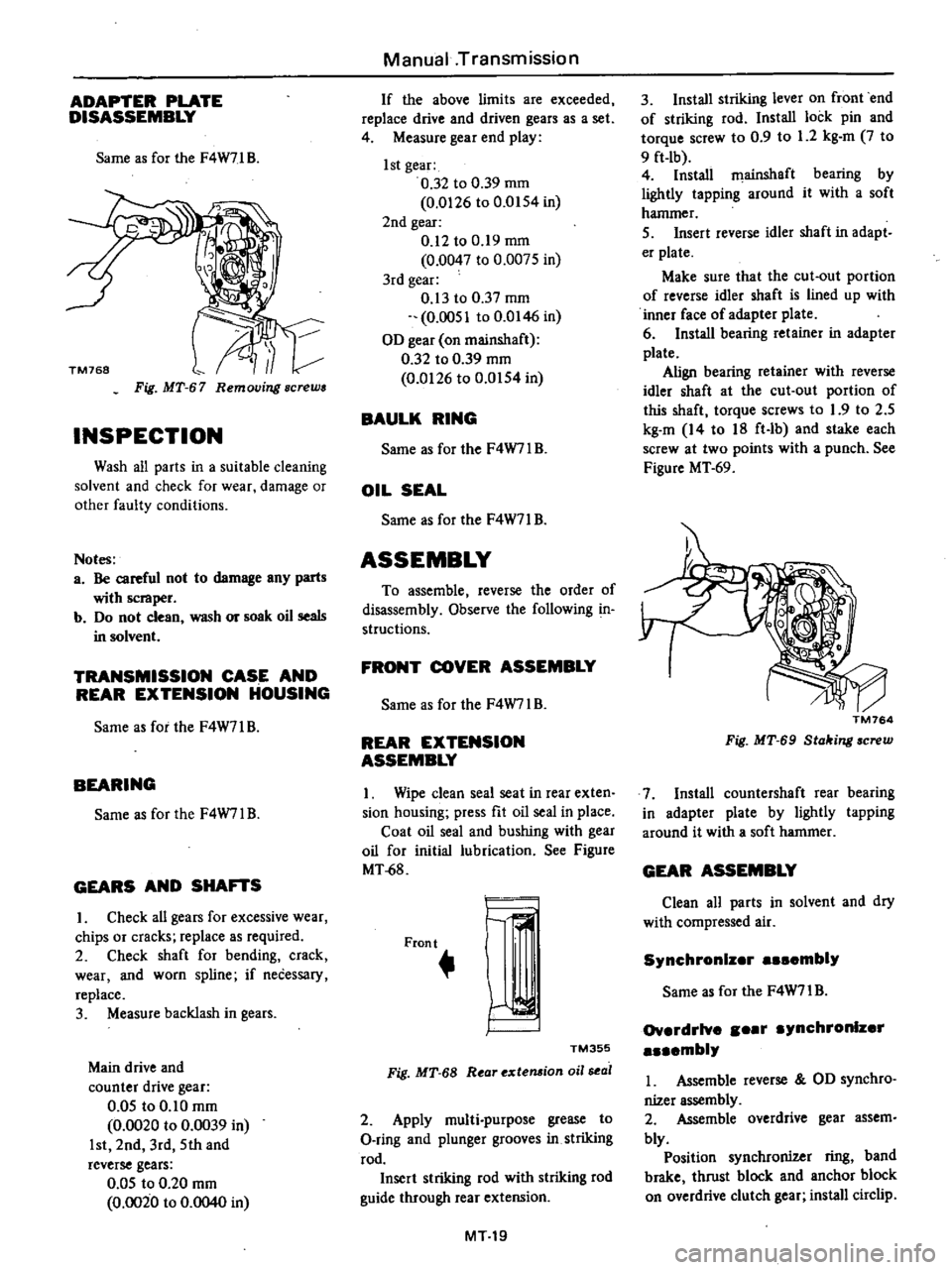
ADAPTER
PLATE
DISASSEMBLY
Same
as
for
the
F4W71
B
Fig
MT
67
Removing
screws
INSPECTION
Wash
all
parts
in
a
suitable
cleaning
solvent
and
check
for
wear
damage
or
other
faulty
conditions
Notes
a
Be
careful
not
to
damage
any
parts
with
scraper
b
Do
not
clean
wash
or
soak
oil
seals
in
solvent
TRANSMISSION
CASE
AND
REAR
EXTENSION
HOUSING
Same
as
for
the
F4W71
B
BEARING
Same
as
for
the
F4W7l
B
GEARS
AND
SHA
S
I
Check
all
gears
for
excessive
wear
chips
or
cracks
replace
as
required
2
Check
shaft
for
bending
crack
wear
and
worn
spline
if
necessary
replace
3
Measure
backlash
in
gears
Main
drive
and
counter
drive
gear
0
05
to
0
10
mm
0
0020
to
0
0039
in
1st
2nd
3rd
5th
and
reverse
gears
0
05
to
0
20
mm
0
0020
to
0
0040
in
Manual
Transmission
If
the
above
limits
are
exceeded
replace
drive
and
driven
gears
as
a
set
4
Measure
gear
end
play
1st
gear
0
32
to
0
39
mm
0
0126
to
0
0154
in
2nd
gear
0
12
to
0
19
mm
0
0047
to
0
0075
in
3rd
gear
0
13
to
0
37
mm
0
0051
to
0
0146
in
OD
gear
on
mainshaft
0
32
to
0
39
mm
0
0126
to
0
0154
in
BAULK
RING
Same
as
for
the
F4W7IB
OIL
SEAL
Same
as
for
the
F4W71
B
ASSEMBLY
To
assemble
reverse
the
order
of
disassembly
Observe
the
following
in
structions
FRONT
COVER
ASSEMBLY
Same
as
for
the
F4W7l
B
REAR
EXTENSION
ASSEMBLY
I
Wipe
clean
seal
seat
in
rear
exten
sion
housing
press
fit
oil
seal
in
place
Coat
oil
seal
and
bushing
with
gear
oil
for
initial
lubrication
See
Figure
MT
68
Front
r
I
TM355
Fig
MT
68
R
ar
extemion
oil
sea
2
Apply
multi
purpose
grease
to
O
ring
and
plunger
grooves
in
striking
rod
Insert
striking
rod
with
striking
rod
guide
through
rear
extension
MT19
3
Install
striking
lever
on
front
end
of
striking
rod
Install
lock
pin
and
torque
screw
to
0
9
to
1
2
kg
m
7
to
9
ft
lb
4
Install
filainshaft
bearing
by
lightly
tapping
around
it
with
a
soft
hammer
5
Insert
reverse
idler
shaft
in
adapt
er
plate
Make
sure
that
the
cut
out
portion
of
reverse
idler
shaft
is
lined
up
with
inner
face
of
adapter
plate
6
Install
bearing
retainer
in
adapter
plate
Align
bearing
retainer
with
reverse
idler
shaft
at
the
cut
out
portion
of
this
shaft
torque
screws
to
1
9
to
2
5
kg
m
14
to
18
ft
lb
and
stake
each
screw
at
two
points
with
a
punch
See
Figure
MT
69
TM764
Fig
MT
69
Stahing
screw
7
Install
countershaft
rear
bearing
in
adapter
plate
by
lightly
tapping
around
it
with
a
soft
hammer
GEAR
ASSEMBLY
Clean
all
parts
in
solvent
and
dry
with
compressed
air
Synchronlz
r
embly
Same
as
for
the
F4W71
B
Ov
rdrlve
r
ynchronlz
r
mbly
I
Assemble
reverse
OD
synchro
nizer
assembly
2
Assemble
overdrive
gear
assem
bly
Position
synchronizer
ring
band
brake
thrust
block
and
anchor
block
on
overdrive
clutch
gear
install
circlip
Page 254 of 537
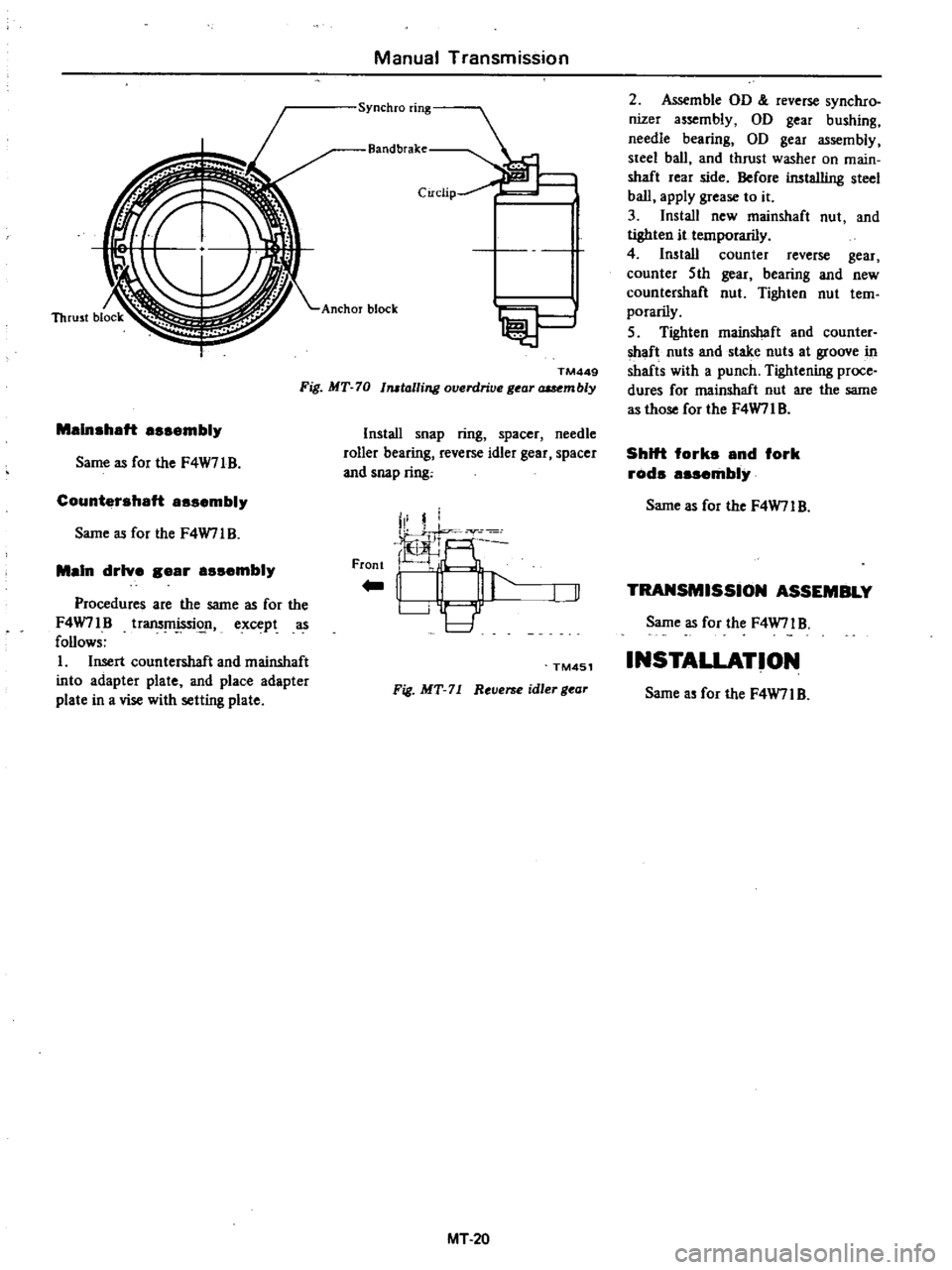
Malnshaft
assembly
Same
as
for
the
F4W7IB
Countershaft
assembly
Same
as
for
the
F4W71
B
Main
drive
gear
assembly
Procedures
are
the
same
as
for
the
F4W7IB
trans
i
n
except
as
follows
I
Insert
countershaft
and
mainshaft
into
adapter
plate
and
place
adapter
plate
in
a
vise
with
setting
plate
Manual
Transmission
Synchro
ring
8andbrake
Circlip
Anchor
block
TM449
Fig
MT
70
Imtalling
overdrive
gear
assembly
Install
snap
ring
spacer
needle
roller
bearing
reverse
idler
gear
spacer
and
snap
ring
h
I
L
TM4S1
Fig
MT
71
R
lJerse
idler
gear
MT
20
2
Assemble
OD
reverse
synchro
nizer
assembly
OD
gear
bushing
needle
bearing
OD
gear
assembly
sreel
ball
and
thrust
washer
on
main
shaft
rear
side
Before
installing
steel
ball
apply
grease
to
it
3
Install
new
mainshaft
nut
and
tighten
it
temporarily
4
Install
counter
reverse
gear
counter
5
th
gear
bearing
and
new
countershaft
nut
Tighten
nut
tem
porarily
5
Tighten
mainshafl
and
counter
shaft
nuts
and
stake
nuts
at
groove
in
shafts
with
a
punch
Tightening
proce
dures
for
mainshaft
nut
are
the
same
as
those
for
the
F4W7IB
Shift
forks
and
fork
rods
assembly
Same
as
for
the
F4W71
B
u
TRANSMISSION
ASSEMBLY
Same
as
for
the
F4W71
B
INSTALLATION
Same
as
for
the
F4W71
B
Page 256 of 537
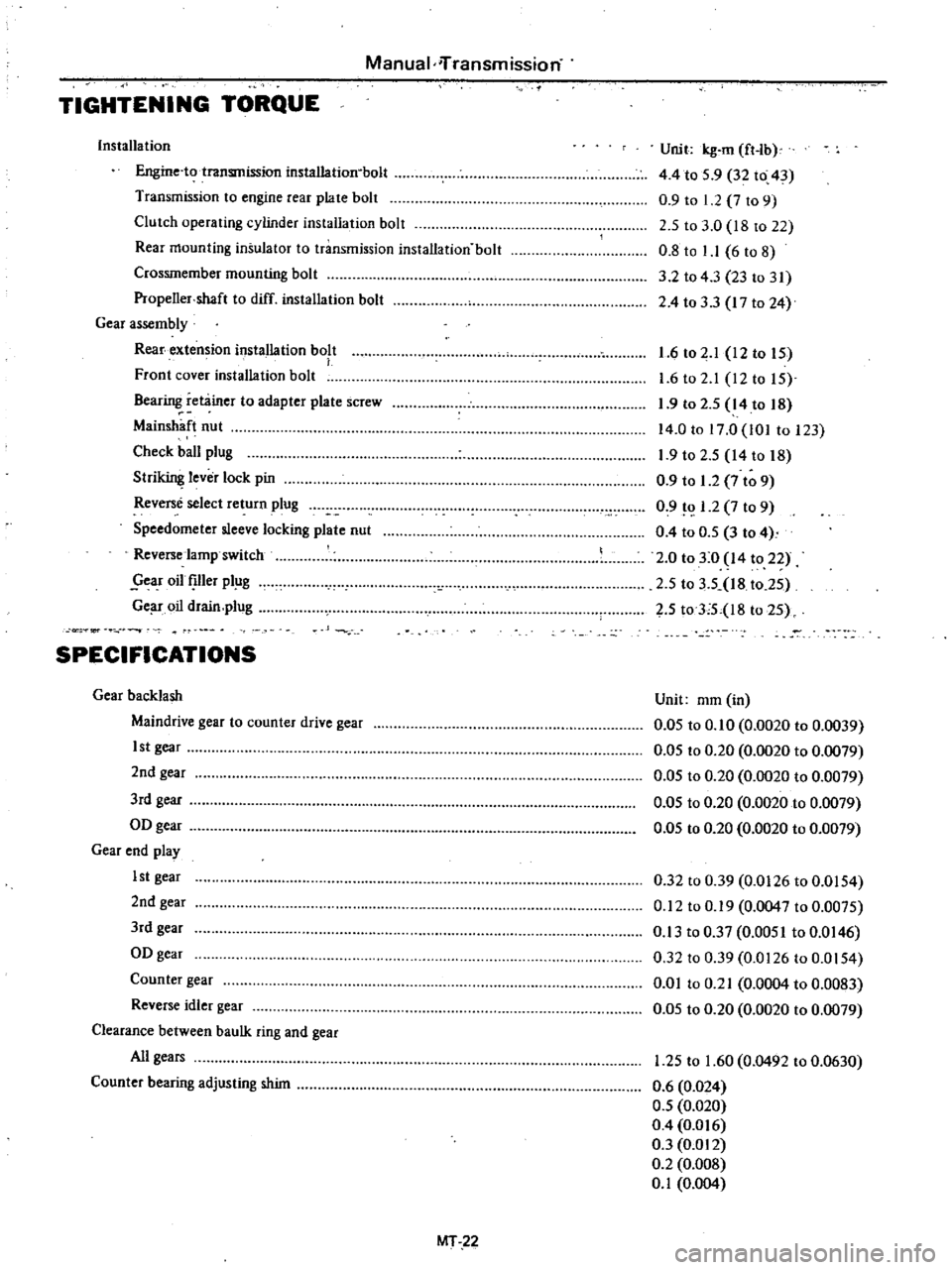
Manual
iTransmission
TIGHTENING
TORQUE
Installa
tion
Engine
to
transmission
installation
bolt
Transmission
to
engine
rear
plate
bolt
Clutch
operating
cylinder
installation
bolt
Rear
mounting
insulator
to
transmission
installation
bolt
Crossmember
mounting
bolt
Propeller
shaft
to
diff
installation
bolt
Gear
assembly
Rear
extension
installation
bolt
Front
cover
installation
bolt
Bearing
retainer
to
adapter
plate
screw
Main
haft
nut
Check
ball
plug
Stri
lever
lock
pin
Reverse
select
return
plug
Speedometer
sleeve
locking
plate
nut
Reverse
lamp
switch
year
oil
Ier
pl
g
Ge
r
oil
drain
plug
Unit
kg
m
ft
lb
4
4
to
5
9
32
to
43
0
9
to
1
2
7
to
9
2
5
to
3
0
18
to
22
0
8
to
1
1
6
to
8
3
2
to
43
23
to
31
2
4
to
33
17
to
24
1
6
to
2
1
12
to
IS
1
6
to
2
1
12to
IS
1
9
to
2
S
14
to
18
14
0
to
17
0
101
to
123
1
9
to
2
S
14
to
18
0
9
to
1
2
7
to
9
0
9
1
2
7
to
9
0
4
to
O
S
3
to
4
2
0
to
3
0
14
to
22
2
S
to
3
5
18
t02S
2
S
toTS
l8
to
2S
or
SPECIFICATIONS
Gear
backlash
Maindrive
gear
to
counter
drive
gear
1st
gear
2nd
gear
3rd
gear
OD
gear
Gear
end
play
1st
gear
2nd
gear
3rd
gear
OD
gear
Counter
gear
Reverse
idler
gear
Clearance
between
baulk
ring
and
gear
All
gears
Counter
bearing
adjusting
shim
Unit
mm
in
0
05
to
0
10
0
0020
to
0
0039
0
05
to
0
20
0
0020
to
0
0079
O
OS
to
0
20
0
0020
to
0
0079
0
05
to
0
20
0
0020
to
0
0079
0
05
to
0
20
0
0020
to
0
0079
0
32
to
0
39
0
0126
to
0
0154
0
12
to
0
19
0
0047
to
0
0075
0
13
to
0
37
0
0051
to
0
0146
0
32
to
0
39
0
0126
to
0
0154
0
01
to
0
21
0
0004
to
0
0083
0
05
to
0
20
0
0020
to
0
0079
1
25
to
1
60
0
0492
to
0
0630
0
6
0
024
0
5
0
020
0
4
0
016
0
3
0
012
0
2
0
008
0
1
0
004
MT
22
Page 257 of 537
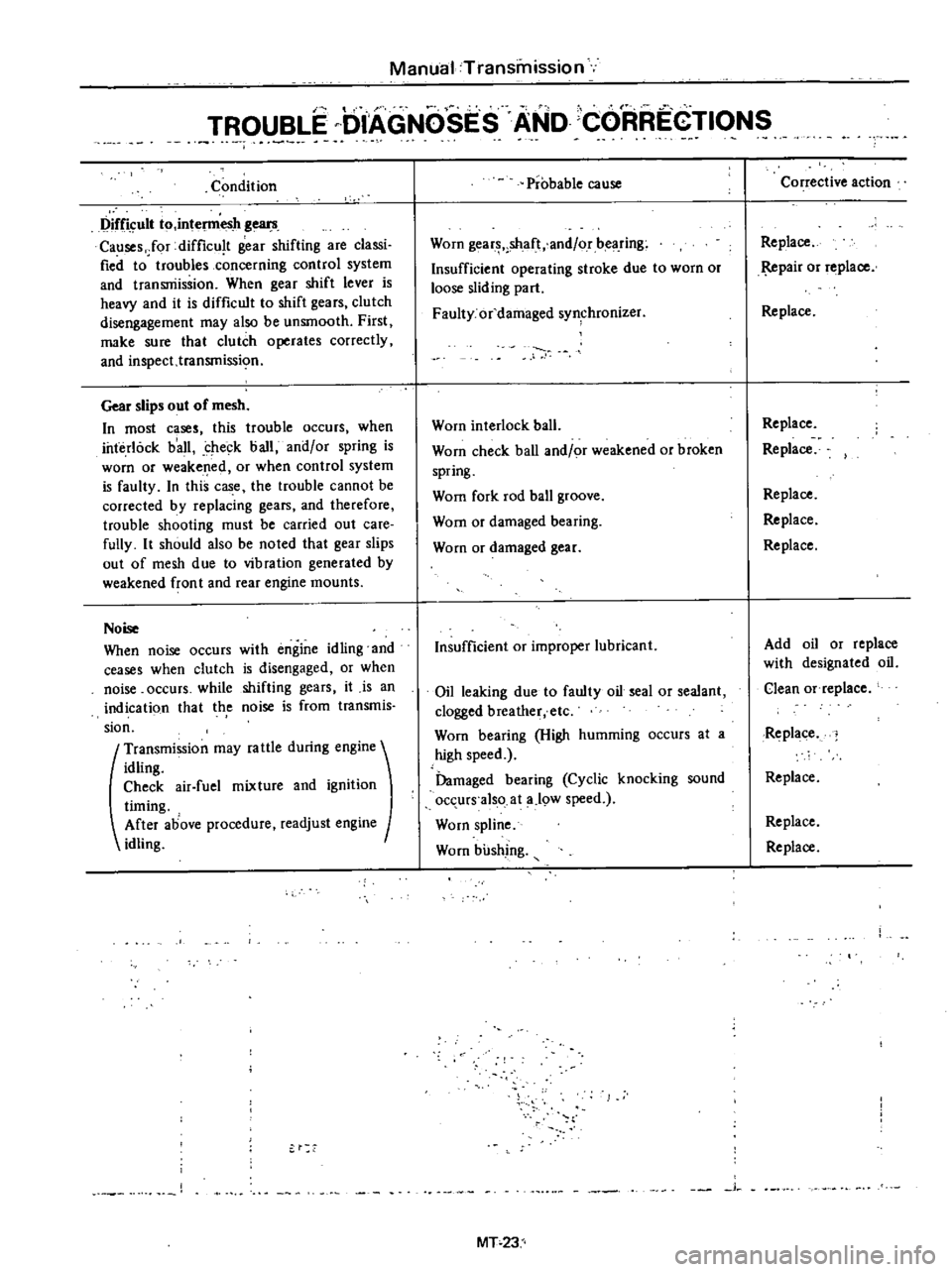
Manual
Transmission
I
TROUBLE
DIAGNOSES
AND
CORREGTIONS
Condition
Difficult
to
intel11lesh
gears
Causes
Jor
difficu
t
gear
shifting
are
classi
fied
to
troubles
concerning
control
system
and
transniissioo
When
gear
shift
lever
is
heavy
and
it
is
difficult
to
shift
gears
clutch
disengagement
may
also
be
unsmooth
First
make
sure
that
clutch
operates
correctly
and
inspect
transmissi
o
Gear
slips
out
of
mesh
In
most
cases
this
trouble
occurs
when
interlock
b
all
check
ball
and
or
spring
is
worn
or
weakened
or
when
control
system
is
faulty
In
this
case
the
trouble
cannot
be
corrected
by
replacing
gears
and
therefore
trouble
shooting
must
be
carried
out
care
fully
It
should
also
be
noted
that
gear
slips
out
of
mesh
due
to
vibration
generated
by
weakened
fron
t
and
rear
engine
mounts
Noise
When
noise
occurs
with
engine
idling
and
ceases
when
clutch
is
disengaged
or
when
noise
occurs
while
shifting
gears
it
is
an
indicati90
that
th
e
noise
is
from
transmis
sion
t
Transmission
may
fa
ule
during
engine
idling
Check
air
fuel
mixture
and
ignition
timing
After
above
procedure
readjust
engine
idling
Probable
cause
Worn
gear
shaft
and
or
bearing
Insufficient
operating
stroke
due
to
worn
or
loose
sliding
part
Faulty
or
damaged
synchronizer
Worn
interlock
ball
Worn
check
ball
and
or
weakened
or
broken
spring
Wom
fork
rod
ball
groove
Wom
or
damaged
bearing
Worn
or
damaged
gear
Insufficient
or
improper
lubricant
Oil
leaking
due
to
faulty
oil
seal
or
sealant
clogged
breather
etc
Worn
bearing
High
humming
occurs
at
a
high
speed
Damaged
bearing
Cyclic
knocking
sound
occurs
also
at
a
19W
speed
Worn
spline
Worn
bushing
j
MT
23
Corrective
action
Replace
pair
or
replace
Replace
Replace
Replace
Replace
Replace
Replace
Add
oil
or
replace
with
designated
oil
Clean
Of
replace
Replace
Replace
Replace
Replace