ECO DATSUN PICK-UP 1977 Owner's Manual
[x] Cancel search | Manufacturer: DATSUN, Model Year: 1977, Model line: PICK-UP, Model: DATSUN PICK-UP 1977Pages: 537, PDF Size: 35.48 MB
Page 75 of 537
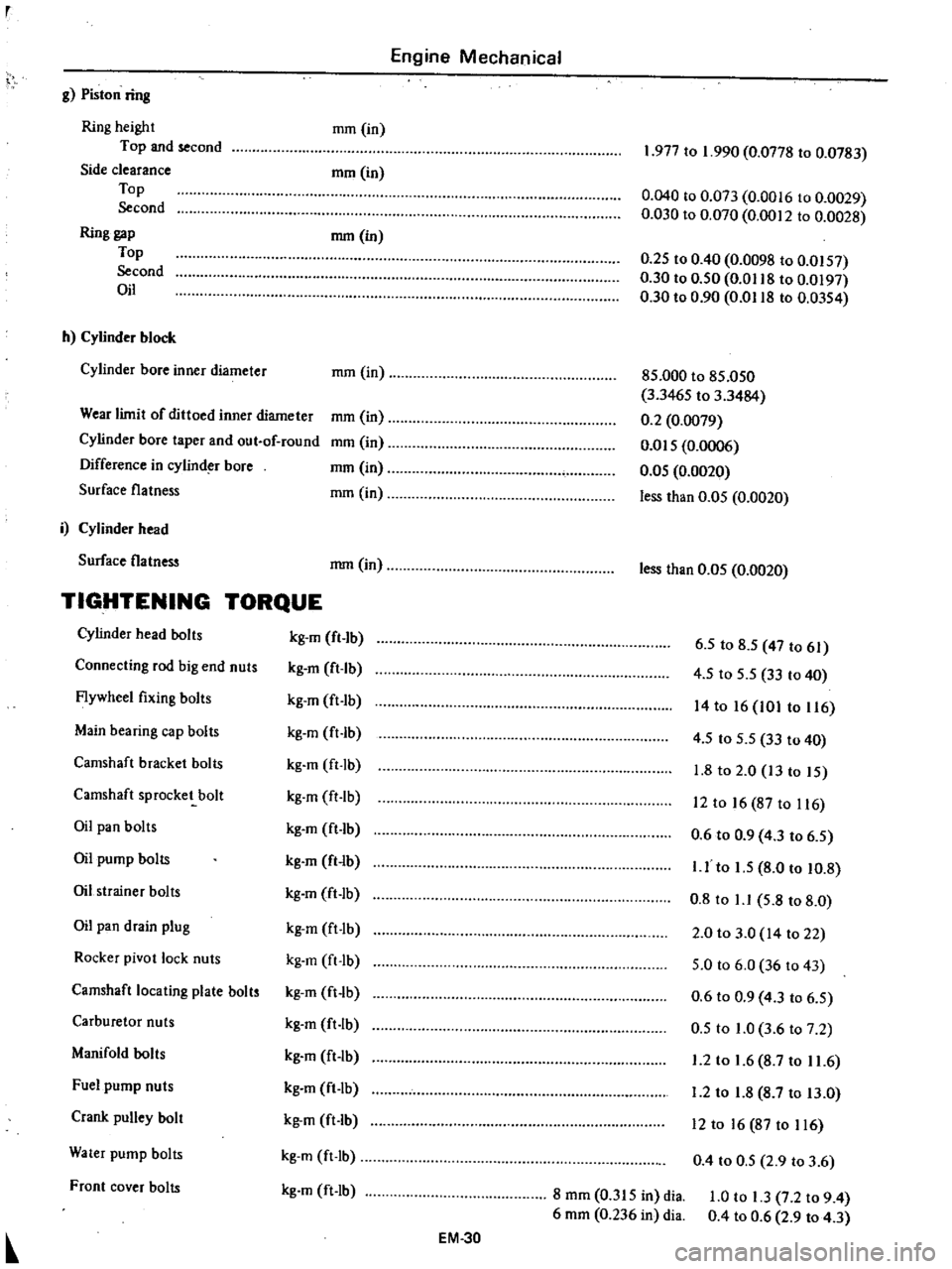
Engine
Mechanical
g
Piston
ring
Ring
height
Top
and
second
Side
clearance
Top
Second
Ring
gap
Top
Second
Oil
mm
in
mrn
in
mm
in
h
Cylinder
block
Cylinder
bore
inner
diameter
mm
in
Wear
limit
of
dittoed
inner
diameter
Cylinder
bore
taper
and
out
of
round
Difference
in
cylind
bore
Surface
flatness
mm
in
mm
in
mm
in
mm
in
i
Cylinder
head
Surface
flatness
mm
in
TIGHTENING
TORQUE
Cylinder
head
bolts
kg
m
fl
lb
Connecting
rod
big
end
nuts
kg
m
ft
Ib
Flywheel
fixing
bolts
kg
m
ft
Ib
Main
bearing
cap
bolts
kg
m
ft
lb
Camshaft
bracket
bolts
kg
m
ft
lb
Camshaft
sprocket
bolt
kg
m
ft
lb
Oil
pan
bolts
kg
m
ft
1b
Oil
pump
bolts
kg
m
ft
lb
Oil
strainer
bolts
kg
m
ft
lb
Oil
pan
drain
plug
kg
m
ft
lb
Rocker
pivot
lock
nuts
kg
m
ft
Ib
Camshaft
locating
plate
bolts
kg
m
ft
lb
Carburetor
nuts
kg
m
ft
lb
Manifold
bolts
kg
m
ft
lb
Fuel
pump
nuts
kg
m
ft
lb
Crank
pulley
bolt
kg
m
ft
lb
Water
pump
bolts
kg
m
ft
Ib
Front
cover
bolts
kg
m
ft
lb
EM
30
1
977
to
1
990
0
0778
to
0
0783
0
040
to
0
073
0
0016
to
0
0029
0
030
to
0
070
0
0012
to
0
0028
0
25
to
0
40
0
0098
to
0
0157
0
30
to
0
50
0
0118
to
0
0197
0
30
to
0
90
0
0118
to
0
0354
85
000
to
85
050
3
3465
to
3
3484
0
2
0
0079
om
5
0
0006
0
05
0
0020
less
than
0
05
0
0020
less
than
0
05
0
0020
6
5
to
8
5
47
to
61
4
5
to
5
5
33
to
40
14
to
16
101
to
116
4
5
to
5
5
33
to
40
1
8
to
2
0
13
to
15
12
to
16
87
to
116
0
6
to
0
9
4
3
to
6
5
I
J
to
1
5
8
0
to
10
8
0
8
to
1
1
5
8
to
8
0
2
0
to
3
0
14
to
22
5
0
to
6
0
36
to
43
0
6
to
0
9
4
3
to
6
5
0
5
to
1
0
3
6
to
7
2
1
2
to
1
6
8
7
to
11
6
1
2
to
1
8
8
7
to
13
0
12
to
16
87
to
116
0
4
to
0
5
2
9
to
3
6
8
mm
0
315
in
dia
6
mm
0
236
in
dia
1
0
to
1
3
7
2
to
9
4
0
4
to
0
6
2
9
to
4
3
Page 76 of 537
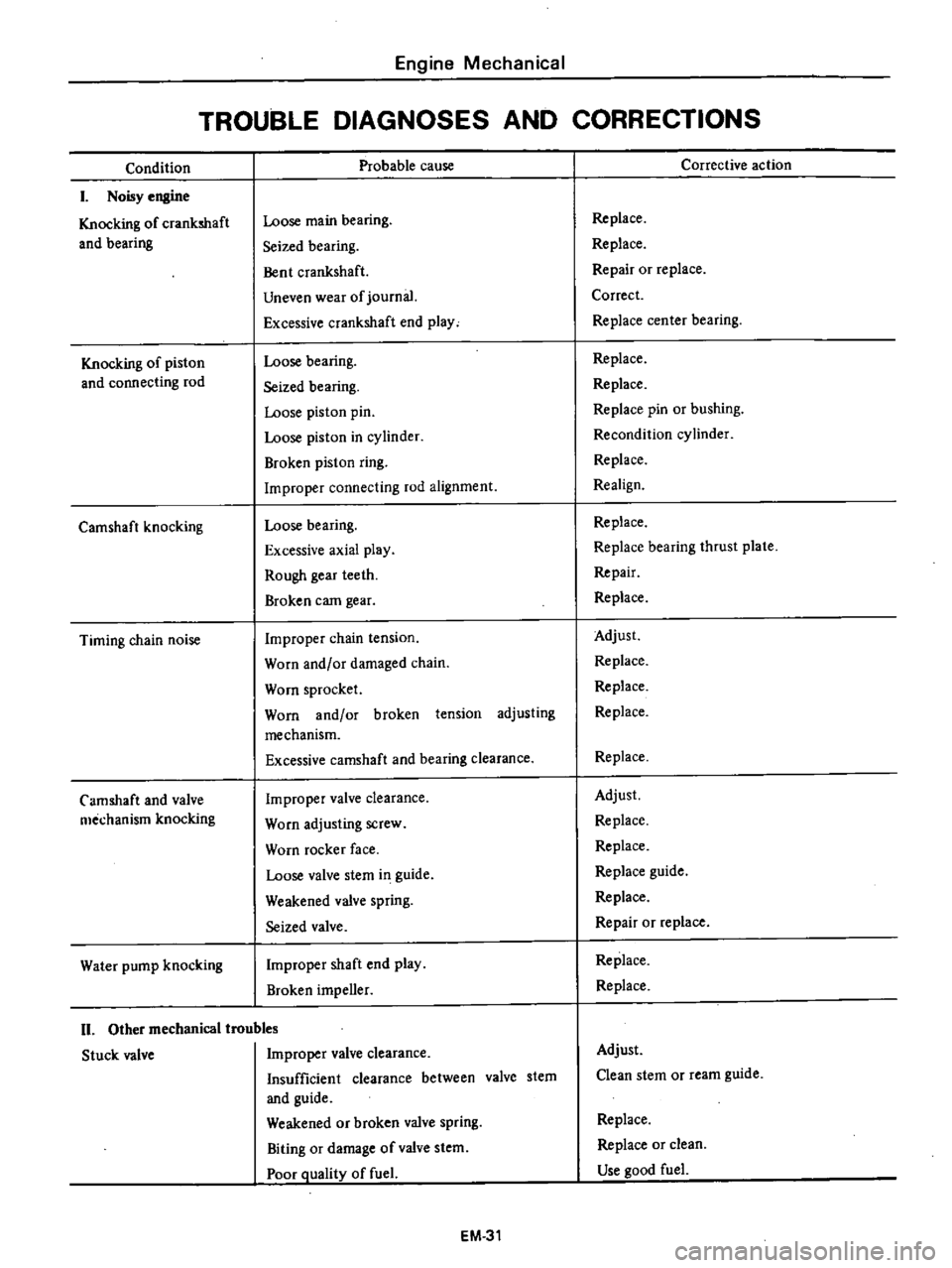
Engine
Mechanical
TROUBLE
DIAGNOSES
AND
CORRECTIONS
Condition
I
Noisy
engine
Knocking
of
crankshaft
and
bearing
Knocking
of
piston
and
connecting
rod
Camshaft
knocking
Timing
chain
noise
Camshaft
and
valve
mechanism
knocking
Water
pump
knocking
Probable
cause
Loose
main
bearing
Seized
bearing
Bent
crankshaft
Uneven
wear
of
journal
Excessive
crankshaft
end
play
Loose
bearing
Seized
bearing
Loose
piston
pin
Loose
piston
in
cylinder
Broken
piston
ring
Improper
connecting
rod
alignment
Loose
bearing
Excessive
axial
play
Rough
gear
teeth
Broken
eam
gear
Improper
chain
tension
Worn
and
or
damaged
chain
Worn
sprocket
Worn
and
or
broken
tension
adjusting
mechanism
Excessive
camshaft
and
bearing
clearance
Improper
valve
clearance
Worn
adjusting
screw
Worn
rocker
face
Loose
valve
stem
i1
1
guide
Weakened
valve
spring
Seized
valve
Improper
shaft
end
play
Broken
impeller
II
Other
mechanical
troubles
Stuck
valve
Improper
valve
clearance
Insufficient
clearance
between
valve
stem
and
guide
Weakened
or
broken
valve
spring
Biting
or
damage
of
valve
stem
Poor
Quality
of
fuel
EM
31
Corrective
action
Replace
Replace
Repair
or
replace
Correct
Replace
cen
ter
bearing
Replace
Replace
Replace
pin
or
bushing
Recondition
cylinder
Replace
Realign
Replace
Replace
bearing
thrust
plate
Repair
Replace
Adjust
Replace
Replace
Replace
Replace
Adjust
Replace
Replace
Replace
guide
Replace
Repair
or
replace
Replace
Replace
Adjust
Clean
stem
or
ream
guide
Replace
Replace
or
clean
Use
ood
fuel
Page 96 of 537
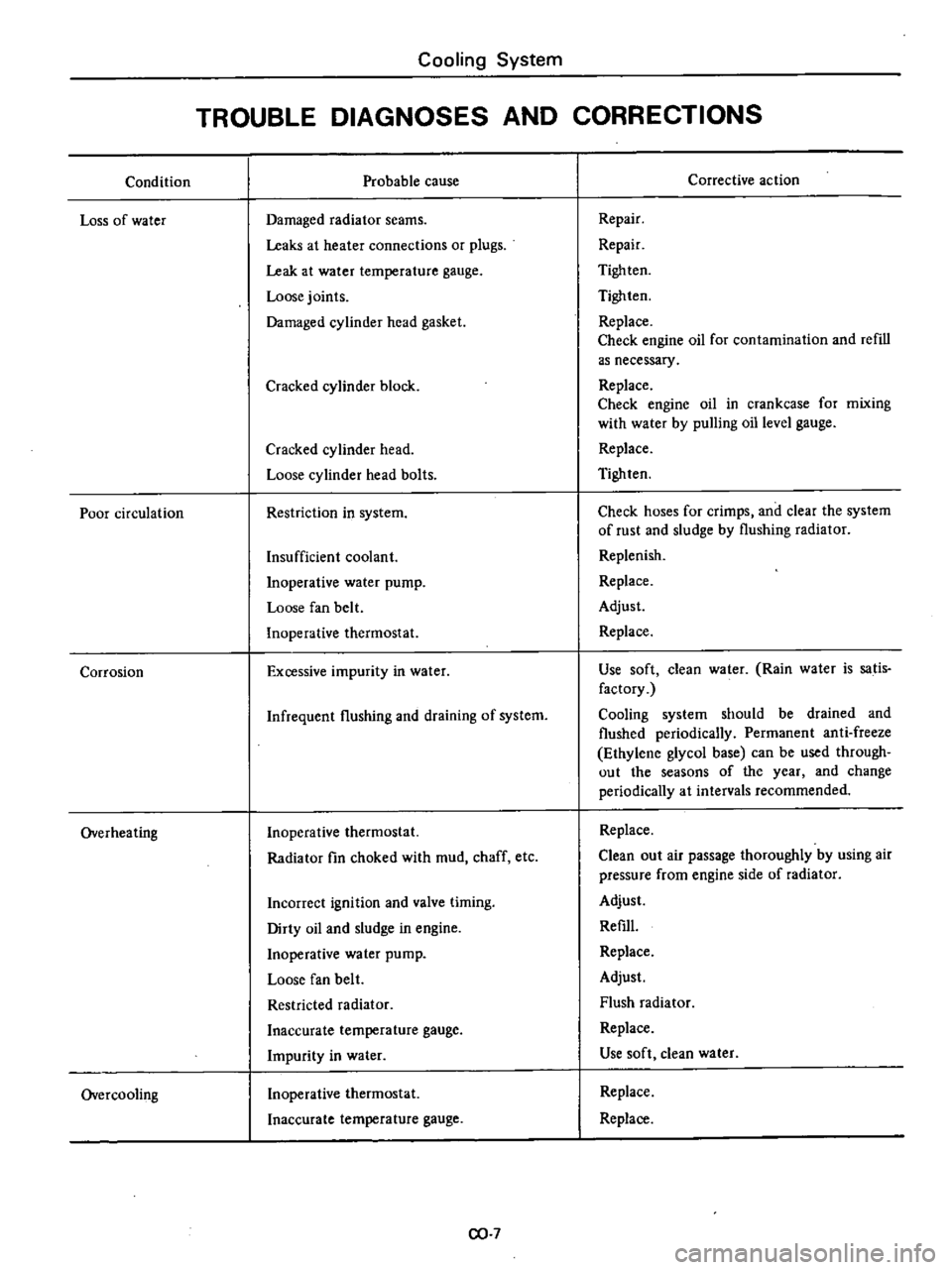
Condition
Loss
of
water
Poor
circulation
Corrosion
Overheating
Overcooling
Cooling
System
TROUBLE
DIAGNOSES
AND
CORRECTIONS
Probable
cause
Damaged
radiator
seams
Leaks
at
heater
connections
or
plugs
Leak
at
water
temperature
gauge
Loose
joints
Damaged
cylinder
head
gasket
Cracked
cylinder
block
Cracked
cylinder
head
Loose
cylinder
head
bolts
Restriction
in
system
Insufficient
coolant
Inoperative
water
pump
Loose
fan
belt
Inoperative
thermostat
Excessive
impurity
in
water
Infrequent
flushing
and
draining
of
system
Inoperative
thermostat
Radiator
fin
choked
with
mud
chaff
etc
Incorrect
ignition
and
valve
timing
Dirty
oil
and
sludge
in
engine
Inoperative
water
pump
Loose
fan
belt
Restricted
radiator
Inaccurate
temperature
gauge
Impurity
in
water
Inoperative
thermostat
Inaccurate
temperature
gauge
CO
7
Corrective
action
Repair
Repair
Tigh
ten
Tighten
Replace
Check
engine
oil
for
contamination
and
refill
as
necessary
Replace
Check
engine
oil
in
crankcase
for
mixing
with
water
by
pulling
oil
level
gauge
Replace
Tighten
Check
hoses
for
crimps
and
clear
the
system
of
rust
and
sludge
by
flushing
radiator
Replenish
Replace
Adjust
Replace
Use
soft
clean
water
Rain
water
is
satis
factory
Cooling
system
should
be
drained
and
flushed
periodically
Permanent
anti
freeze
Ethylene
glycol
base
can
be
used
through
out
the
seasons
of
the
year
and
change
periodically
at
intervals
recommended
Replace
Clean
out
air
passage
thoroughly
by
using
air
pressure
from
engine
side
of
radiator
Adjust
Refill
Replace
Adjust
Flush
radiator
Replace
Use
soft
clean
water
Replace
Replace
Page 102 of 537
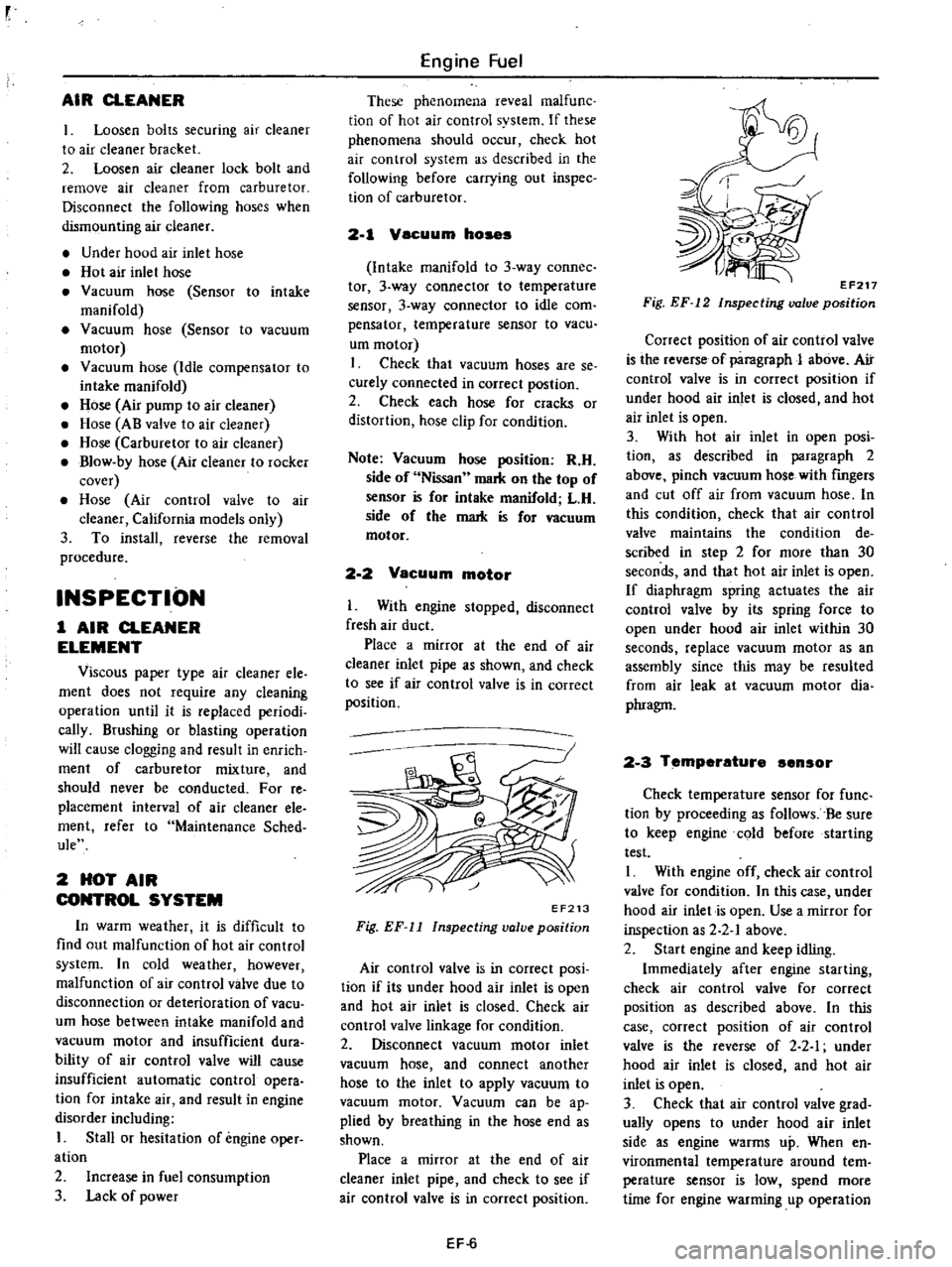
r
AIR
CLEANER
1
Loosen
bolts
securing
air
cleaner
to
air
cleaner
bracket
2
Loosen
air
cleaner
lock
bolt
and
remove
air
cleaner
from
carburetor
Disconnect
the
following
hoses
when
dismounting
air
cleaner
Under
hood
air
inlet
hose
Hot
air
inlet
hose
Vacuum
hose
Sensor
to
intake
manifold
Vacuum
hose
Sensor
to
vacuum
motor
Vacuum
hose
Idle
compensator
to
intake
manifold
Hose
Air
pump
to
air
cleaner
Hose
AB
valve
to
air
cleaner
Hose
Carburetor
to
air
cleaner
Blow
by
hose
Air
cleaner
to
rocker
cover
Hose
Air
control
vaive
to
air
cleaner
California
models
only
3
To
install
reverse
the
removal
procedure
INSPECTION
1
AIR
CLEANER
ELEMENT
Viscous
paper
type
air
cleaner
ele
ment
does
not
require
any
cleaning
operation
until
it
is
replaced
periodi
cally
Brushing
or
blasting
operation
will
cause
clogging
and
result
in
enrich
ment
of
carburetor
mixture
and
should
never
be
conducted
For
reo
placement
interval
of
air
cleaner
ele
ment
refer
to
Maintenance
Sched
ule
2
HOT
AIR
CONTROL
SYSTEM
In
warm
weather
it
is
difficult
to
find
out
malfunction
of
hot
air
control
system
In
cold
wea
thee
however
malfunction
of
air
control
valve
due
to
disconnection
or
deterioration
of
vacu
um
hose
between
intake
manifold
and
vacuum
motor
and
insufficient
dura
bility
of
air
control
valve
will
cause
insufficient
automatic
control
opera
tion
for
intake
air
and
result
in
engine
disorder
including
I
Stall
or
hesitation
of
engine
oper
ation
2
Increase
in
fuel
consumption
3
uck
of
power
Engine
Fuel
These
phenomena
reveal
malfunc
tion
of
hot
air
control
system
If
these
phenomena
should
occur
check
hot
air
control
system
as
described
in
the
following
before
carrying
out
inspec
tion
of
carburetor
2
1
Vacuum
hose
Intake
manifold
to
3
way
connec
tor
3
way
connector
to
temperature
sensor
3
way
connector
to
idle
com
pensator
temperature
sensor
to
vacu
um
motor
I
Check
that
vacuum
hoses
are
se
curely
connected
in
correct
postion
2
Check
each
hose
for
cracks
or
distortion
hose
clip
for
condition
Note
Vacuum
hose
position
R
H
side
of
Nissan
mark
on
the
top
of
sensor
is
for
intake
manifold
L
U
side
of
the
mark
is
for
vacuum
motor
2
2
Vacuum
motor
I
With
engine
stopped
disconnect
fresh
air
duct
Place
a
mirror
at
the
end
of
air
cleaner
inlet
pipe
as
shown
and
check
to
see
if
air
con
trol
valve
is
in
correct
position
EF213
Fig
EF
11
Inspecting
valve
position
Air
control
valve
is
in
correct
posi
tion
if
its
under
hood
air
inlet
is
open
and
hot
air
inlet
is
closed
Check
air
control
valve
linkage
for
condition
2
Disconnect
vacuum
motor
inlet
vacuum
hose
and
connect
another
hose
to
the
inlet
to
apply
vacuum
to
vacuum
motor
Vacuum
can
be
ap
plied
by
breathing
in
the
hose
end
as
shown
Place
a
mirror
at
the
end
of
air
cleaner
inlet
pipe
and
check
to
see
if
air
control
valve
is
in
correct
position
EF
6
EF217
Fig
EF
12
Inspecting
valve
position
Correct
position
of
air
control
valve
is
the
reverse
of
paragraph
J
above
Air
control
valve
is
in
correct
position
if
under
hood
air
inlet
is
closed
and
hot
air
inlet
is
open
3
With
hot
air
inlet
in
open
posi
tion
as
described
in
paragraph
2
above
pinch
vacuum
hose
with
fingers
and
cut
off
air
from
vacuum
hose
In
this
condition
check
that
air
control
valve
maintains
the
condition
de
scribed
in
step
2
for
more
than
30
seconds
and
that
hot
air
inlet
is
open
If
diaphragm
spring
actuates
the
air
control
valve
by
its
spring
force
to
open
under
hood
air
inlet
within
30
seconds
replace
vacuum
motor
as
an
assembly
since
this
may
be
resulted
from
air
leak
at
vacuum
motor
dia
phragm
2
3
Temperature
ensor
Check
temperature
sensor
for
func
tion
by
proceeding
as
follows
Be
sure
to
keep
engine
cold
before
starting
test
I
With
engine
off
check
air
control
valve
for
condition
In
this
case
under
hood
air
inlet
is
open
Use
a
mirror
for
inspection
as
2
2
1
above
2
Start
engine
and
keep
idling
Immediately
after
engine
starting
check
air
control
valve
for
correct
position
as
described
above
In
this
case
correct
position
of
air
control
valve
is
the
reverse
of
2
2
I
under
hood
air
inlet
is
closed
and
hot
air
inlet
is
open
3
Check
that
air
control
valve
grad
ually
opens
to
under
hood
air
inlet
side
as
engine
warms
up
When
en
vironmental
temperature
around
tern
perature
sensor
is
low
spend
more
time
for
engine
warming
up
operation
Page 107 of 537
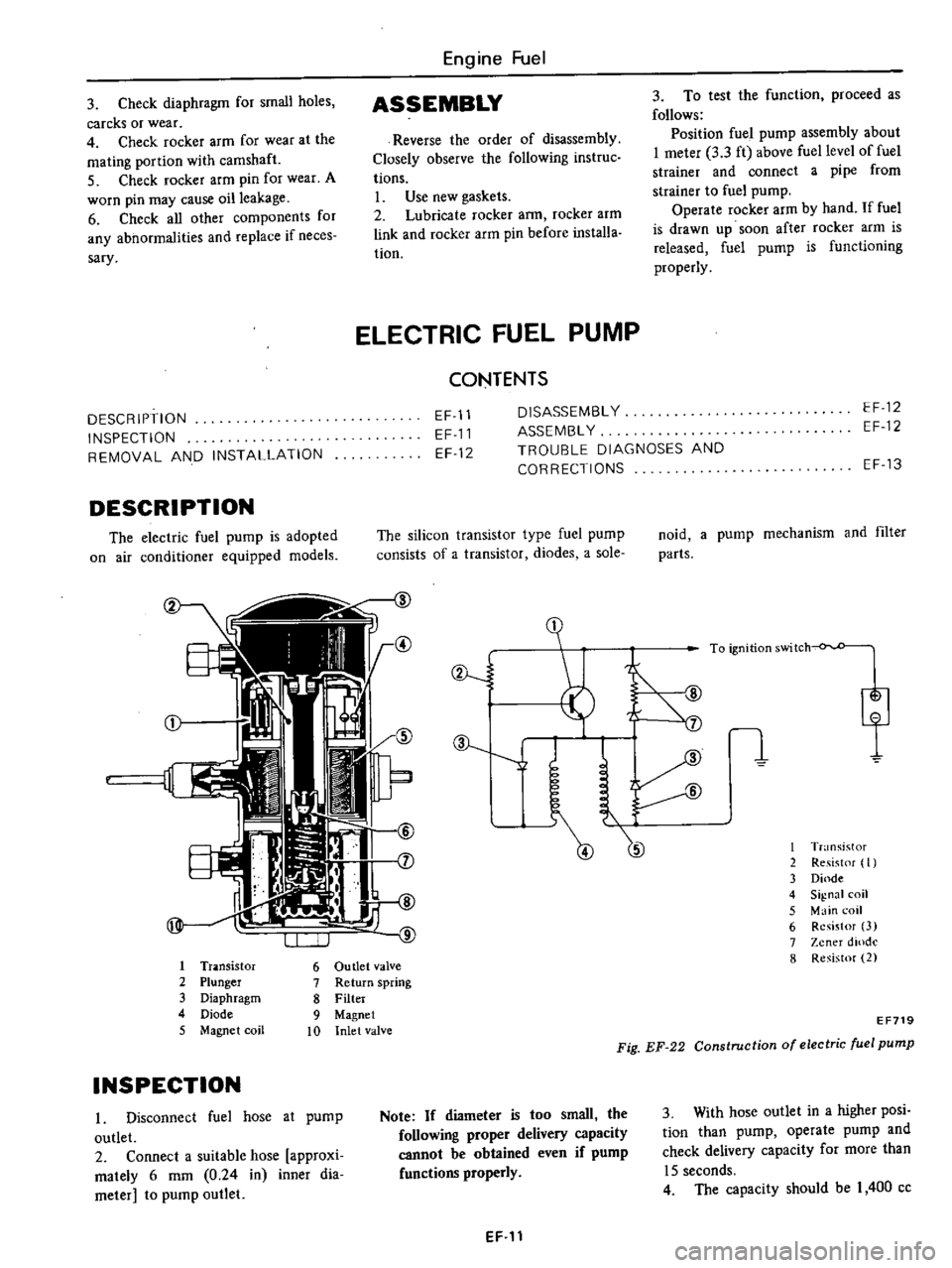
3
Check
diaphragm
for
small
holes
carcks
or
wear
4
Check
rocker
arm
for
wear
at
the
mating
portion
with
camshaft
5
Check
rocker
arm
pin
for
wear
A
worn
pin
may
cause
oil
leakage
6
Check
all
other
components
for
any
abnormalities
and
replace
if
neces
sary
DESCRIPTION
INSPECTION
REMOVAL
AND
INSTALLATION
DESCRIPTION
The
electric
fuel
pump
is
adopted
on
air
conditioner
equipped
models
Engine
Fuel
ASSEMBLY
Reverse
the
order
of
disassembly
Closely
observe
the
following
instruc
tions
L
Use
new
gaskets
2
Lubricate
rocker
ann
rocker
arm
link
and
rocker
arm
pin
before
installa
tion
3
To
test
the
function
proceed
as
follows
Position
fuel
pump
assembly
about
I
meter
3
3
ft
above
fuel
level
of
fuel
strainer
and
connect
a
pipe
from
strainer
to
fuel
pump
Operate
rocker
arm
by
hand
If
fuel
is
drawn
up
soon
after
rocker
arm
is
released
fuel
pump
is
functioning
properly
ELECTRIC
FUEL
PUMP
CONTENTS
EF
11
EF
11
EF
12
DISASSEMBL
Y
ASSEMBL
Y
TROUBLE
DIAGNOSES
AND
CORRECTIONS
EF
12
EF
12
The
silicon
transistor
type
fuel
pump
consists
of
a
transistor
diodes
a
sole
I
Tr
lOsistor
6
Ou
tIet
valve
2
Plunger
7
Return
spring
3
Diaphragm
8
Filter
4
Diode
9
Magnet
5
Magnet
coil
10
Inlet
valve
INSPECTION
I
Disconnect
fuel
hose
at
pump
outlet
2
Connect
a
suitable
hose
approxi
mately
6
mm
0
24
in
inner
dia
meter
to
pump
outlet
ev
J
J
Note
If
diameter
is
too
small
the
following
proper
delivery
capacity
cannot
be
obtained
even
if
pump
functions
properly
EF
11
EF
13
noid
a
pump
mechanism
and
filter
parts
I
T
nsistor
2
Re
ist
f
I
3
Dinde
4
Signal
coil
5
Main
coil
6
Resistor
3
7
Zener
dlOdl
8
Resistor
2
EF719
Fig
EF
22
Construction
of
electric
fuel
pump
3
With
hose
outlet
in
a
higher
posi
tion
than
pump
operate
pump
and
check
delivery
capacity
for
more
than
15
seconds
4
The
capacity
should
be
I
400
cc
Page 110 of 537
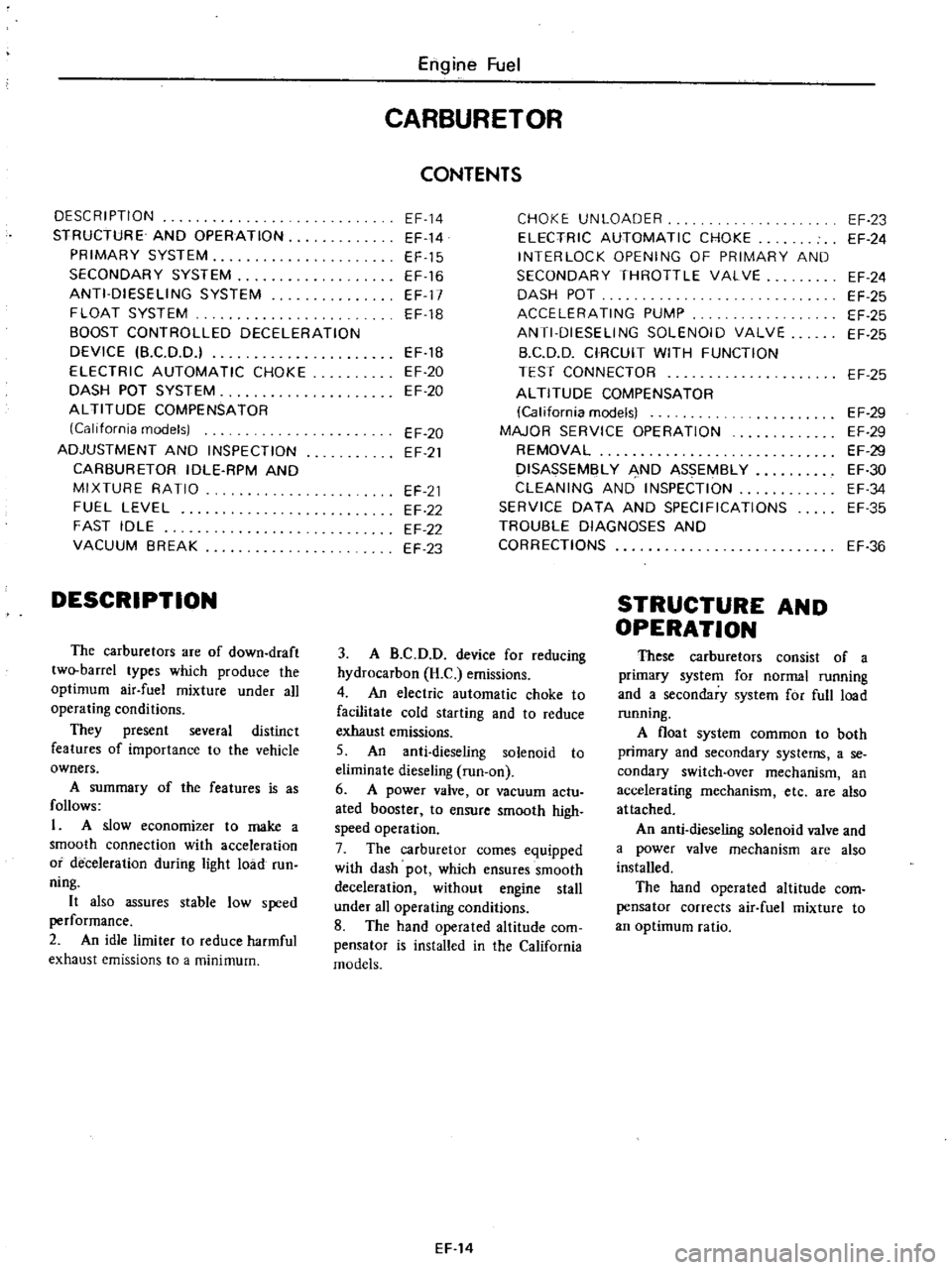
Engine
Fuel
CARBURETOR
CONTENTS
DESCRIPTION
EF
14
CHOKE
UNLOADER
EF
23
STRUCTURE
AND
OPERATION
EF
14
ELECTRIC
AUTOMATIC
CHOKE
EF
24
PRIMARY
SYSTEM
EF
15
INTERLOCK
OPENING
OF
PRIMARY
AND
SECONDARY
SYSTEM
EF
16
SECONDARY
THROTTLE
VALVE
EF
24
ANTI
DIESELING
SYSTEM
EF
17
DASH
POT
EF
25
FLOAT
SYSTEM
EF
18
ACCELERATING
PUMP
EF
25
BOOST
CONTROLLED
DECELERATION
ANTI
DIESELING
SOLENOID
VALVE
EF
25
DEVICE
B
C
D
D
EF
1B
B
C
D
D
CIRCUIT
WITH
FUNCTION
ELECTRIC
AUTOMATIC
CHOKE
EF
20
TEST
CONNECTOR
EF
25
DASH
POT
SYSTEM
EF
20
ALTITUDE
COMPENSATOR
ALTITUDE
COMPENSATOR
California
modelsl
EF
29
California
models
EF
20
MAJOR
SERVICE
OPERATION
EF
29
ADJUSTMENT
AND
INSPECTION
EF
21
REMOVAL
EF
29
CARBURETOR
IDLE
RPM
AND
DISASSEMBLY
AND
ASSEMBLY
EF
30
MIXTURE
RATIO
EF
21
CLEANING
AND
INSPECTION
EF
34
FUEL
LEVEL
EF
22
SERVICE
DATA
AND
SPECIFICATIONS
EF
35
FAST
IDLE
EF
22
TROU8LE
DIAGNOSES
AND
VACUUM
BREAK
EF
23
CORRECTIONS
EF
36
DESCRIPTION
The
carburetors
are
of
down
draft
two
barrel
types
which
produce
the
optimum
air
fuel
mixture
under
all
operating
conditions
They
present
several
distinct
features
of
importance
to
the
vehicle
owners
A
summary
of
the
features
is
as
follows
1
A
slow
economizer
to
make
a
smooth
connection
with
acceleration
or
deceleration
during
light
load
run
ning
It
also
assures
stable
low
speed
performance
2
An
idle
limiter
to
reduce
harmful
exhaust
emissions
to
a
minimum
3
A
B
C
D
D
device
for
reducing
hydrocarbon
H
C
emissions
4
An
electric
automatic
choke
to
facilitate
cold
starting
and
to
reduce
exhaust
emissions
5
An
anti
dieseling
solenoid
to
eliminate
dieseling
run
on
6
A
power
valve
or
vacuum
actu
ated
booster
to
ensure
smooth
high
speed
operation
7
The
carburetor
comes
equipped
with
dash
pot
which
ensures
smooth
deceleration
without
engine
stall
under
all
operating
conditions
8
The
hand
operated
altitude
com
pensator
is
installed
in
the
California
models
EF
14
STRUCTURE
AND
OPERATION
These
carburetors
consist
of
a
primary
system
for
normal
running
and
a
secondary
system
for
full
load
running
A
float
system
common
to
both
primary
and
secondary
systems
a
se
condary
switch
over
mechanism
an
accelerating
mechanism
etc
are
also
attached
An
anti
dieseling
solenoid
valve
and
a
power
valve
mechanism
are
also
installed
The
hand
operated
altitude
com
pensator
corrects
air
fuel
mixture
to
an
optimum
ratio
Page 111 of 537
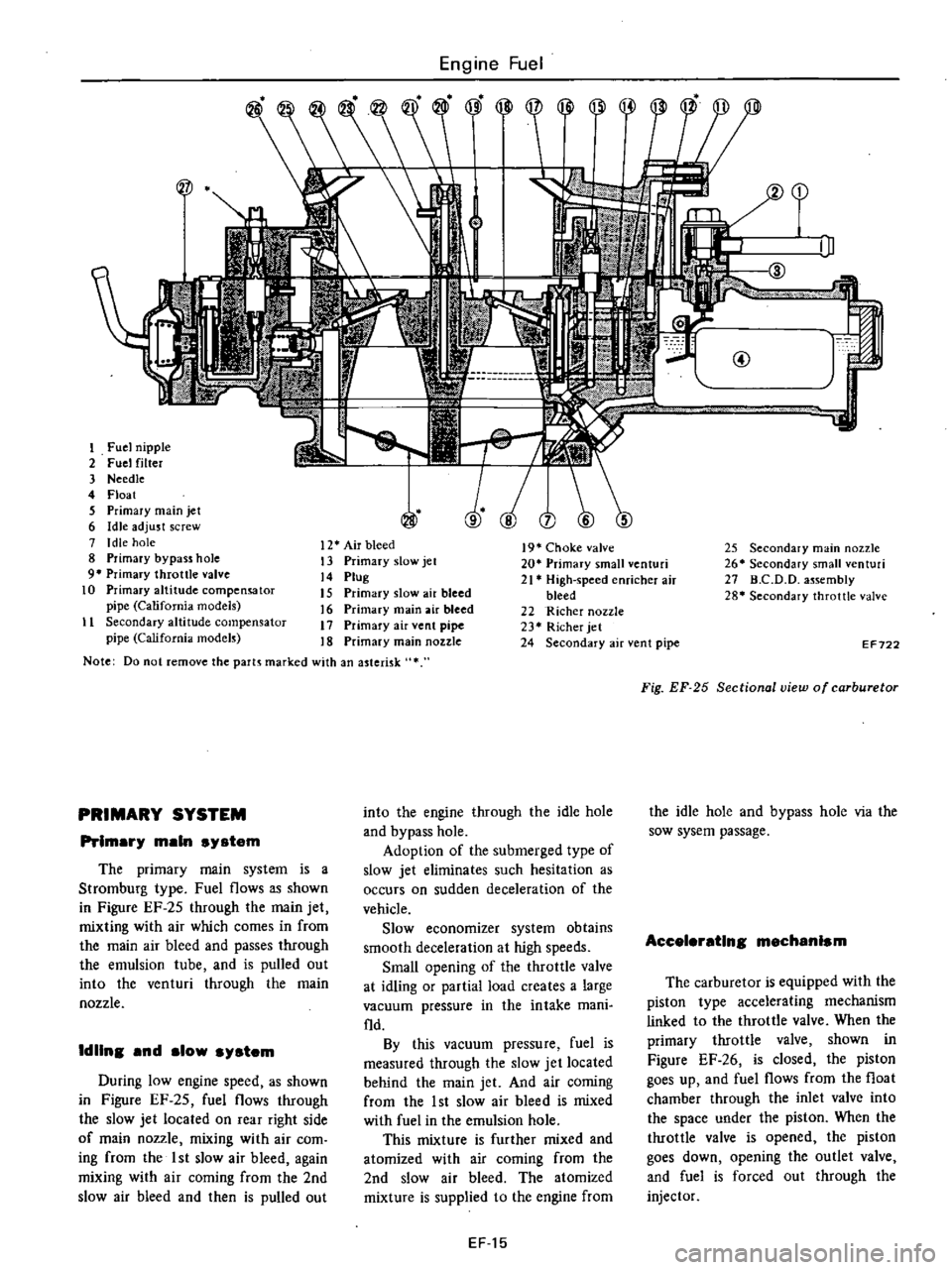
tZrJ
I
Fuel
nipple
2
Fuel
filter
3
Needle
4
Float
S
Primary
main
jet
6
Idle
adjust
screw
7
I
die
hole
8
Primary
bypass
hole
9
Primary
throttle
valve
10
Primary
altitude
compensator
pipe
California
models
11
Secondary
altitude
compensator
pipe
California
models
Engine
Fuel
jli@
I
12
Air
bleed
13
Primary
slow
jet
14
Plug
15
Primary
slow
air
bleed
6
Primary
main
air
bleed
17
Primary
air
vent
pipe
8
Primary
main
nOlzle
Note
Do
not
remove
the
parts
marked
with
an
asterisk
PRIMARY
SYSTEM
Prlmar
main
s
stem
The
primary
main
system
is
a
Stromburg
type
Fuel
flows
as
shown
in
Figure
EF
25
through
the
main
jet
mixting
with
air
which
comes
in
from
the
main
air
bleed
and
passes
through
the
emulsion
tube
and
is
pulled
out
into
the
venturi
through
the
main
nozzle
IdUns
and
slow
s
stem
During
low
engine
speed
as
shown
in
Figure
EF
25
fuel
flows
through
the
slow
jet
located
on
rear
right
side
of
main
nozzle
mixing
with
air
com
ing
from
the
1st
slow
air
bleed
again
mixing
with
air
coming
from
the
2nd
slow
air
bleed
and
then
is
pulled
out
I
III
@
19
Choke
valve
20
Primary
small
venturi
21
High
speed
enricher
air
bleed
22
Richer
nozzle
23
Richer
jet
24
Secondary
air
vent
pipe
into
the
engine
through
the
idle
hole
and
bypass
hole
Adoption
of
the
submerged
type
of
slow
jet
eliminates
such
hesitation
as
occurs
on
sudden
deceleration
of
the
vehicle
Slow
economizer
system
obtains
smooth
deceleration
at
high
speeds
Small
opening
of
the
throttle
valve
at
idling
or
partial
load
creates
a
large
vacuum
pressure
in
the
intake
mani
fld
By
this
vacuum
pressure
fuel
is
measured
through
the
slow
jet
located
behind
the
main
jet
And
air
coming
from
the
1st
slow
air
bleed
is
mixed
with
fuel
in
the
emulsion
hole
This
mixture
is
further
mixed
and
atomized
with
air
coming
from
the
2nd
slow
air
bleed
The
atomized
mixture
is
supplied
to
the
engine
from
EF15
25
Secondary
main
nozzle
26
Secondary
small
enturi
27
D
C
D
D
a
sembly
28
Secondary
throttle
valve
EF722
Fig
EF
25
Sectional
view
of
carburetor
the
idle
hole
and
bypass
hole
via
the
sow
sysem
passage
Accele
atlns
mechanism
The
carburetor
is
equipped
with
the
piston
type
accelerating
mechanism
linked
to
the
throttle
valve
When
the
primary
throttle
valve
shown
in
Figure
EF
26
is
closed
the
piston
goes
up
and
fuel
flows
from
the
float
chamber
through
the
inlet
valve
into
the
space
under
the
piston
When
the
throttle
valve
is
opened
the
piston
goes
down
opening
the
outlet
valve
and
fuel
is
forced
out
through
the
injector
Page 112 of 537
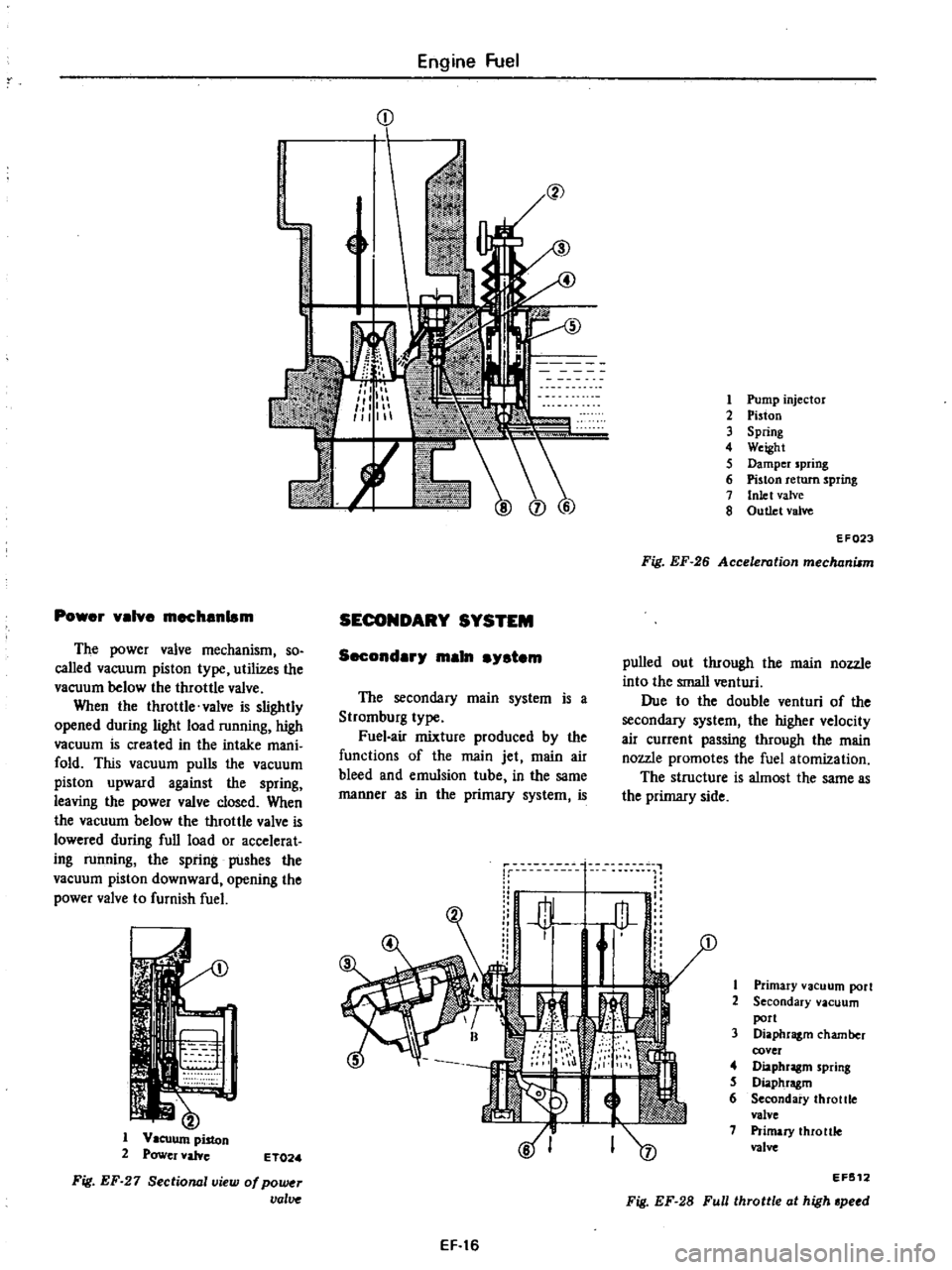
Engine
Fuel
1
L
if
1
Pump
injector
2
Piston
3
Spring
4
Weight
5
Damper
spring
6
Piston
return
spring
7
Inlet
valve
8
Outlet
valve
EF023
Fig
EF
26
Acceleration
mechanism
Power
valve
mechanism
SECONDARY
SYSTEM
The
power
valve
mechanism
so
called
vacuum
piston
type
utilizes
the
vacuum
below
the
throttle
valve
When
the
throttle
valve
is
slightly
opened
during
light
load
running
high
vacuum
is
created
in
the
intake
mani
fold
This
vacuum
pulls
the
vacuum
piston
upward
against
the
spring
leaving
the
power
valve
closed
When
the
vacuum
below
the
throttle
valve
is
lowered
during
full
load
or
accelerat
ing
running
the
spring
pushes
the
vacuum
piston
downward
opening
the
power
valve
to
furnish
fuel
Secondary
main
lIYlltem
pulled
out
through
the
main
nozzle
into
the
small
venturi
Due
to
the
double
venturi
of
the
secondary
system
the
higher
velocity
air
current
passing
through
the
main
nozzle
promotes
the
fuel
atomization
The
structure
is
almost
the
same
as
the
primary
side
The
secondary
main
system
is
a
Stromburg
type
Fuel
air
mixture
produced
by
the
functions
of
the
main
jet
main
air
bleed
and
emulsion
tube
in
the
same
manner
as
in
the
primary
system
is
11
1
I
1
1
Primary
vacuum
port
2
Secondary
vacuum
port
3
Diaphragm
chamber
cover
of
Diaphragm
spring
S
Diaphragm
6
Secondary
throttle
valve
7
Primary
theo
nle
valve
lWll
I
1
11
l
v
1
Vacuum
piston
2
Power
valve
ET02
a
EF
512
Fig
EF
27
Sectional
view
of
po
r
valve
Fig
EF
28
Full
throttle
al
high
peed
EF
16
Page 113 of 537
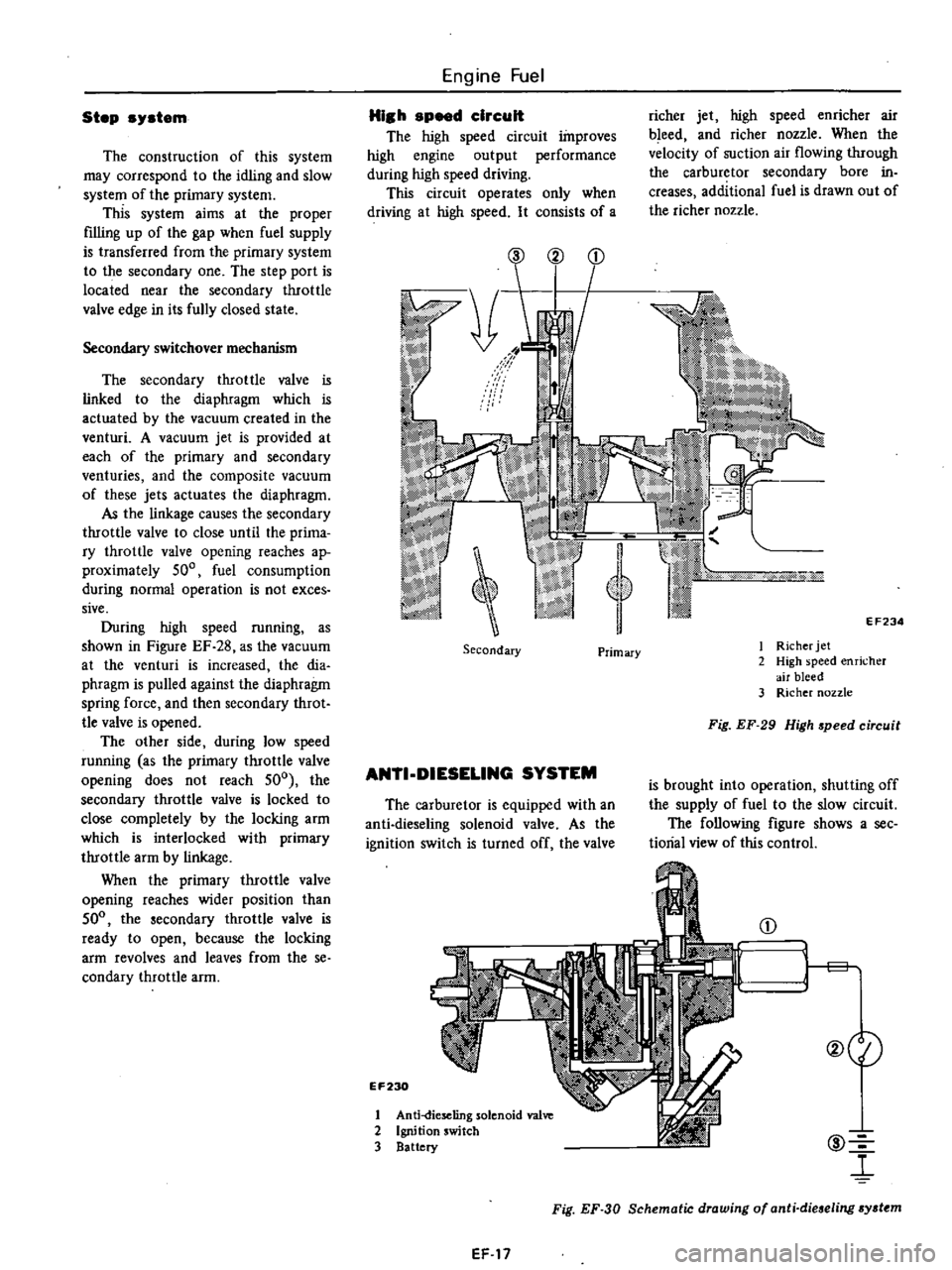
Step
system
The
construction
of
this
system
may
correspond
to
the
idling
and
slow
system
of
the
primary
system
Tlris
system
aims
at
the
proper
filling
up
of
the
gap
when
fuel
supply
is
transferred
from
the
primary
system
to
the
secondary
one
The
step
port
is
located
near
the
secondary
throttle
valve
edge
in
its
fully
closed
state
Secondary
switchover
mechanism
The
secondary
throttle
valve
is
linked
to
the
diaphragm
which
is
actuated
by
the
vacuum
created
in
the
venturi
A
vacuum
jet
is
provided
at
each
of
the
primary
and
secondary
venturies
and
the
composite
vacuum
of
these
jets
actuates
the
diaphragm
As
the
linkage
causes
the
secondary
throttle
valve
to
close
until
the
prima
ry
throttle
valve
opening
reaches
ap
proximately
500
fuel
consumption
during
normal
operation
is
not
exces
sive
During
high
speed
running
as
shown
in
Figure
EF
28
as
the
vacuum
at
the
venturi
is
increased
the
dia
phragm
is
pulled
against
the
diaphragm
spring
force
and
then
secondary
throt
tie
valve
is
opened
The
other
side
during
low
speed
running
as
the
primary
throttle
valve
opening
does
not
reach
500
the
secondary
throttle
valve
is
locked
to
close
completely
by
the
locking
arm
which
is
interlocked
with
primary
throttle
arm
by
linkage
When
the
primary
throttle
valve
opening
reaches
wider
position
than
500
the
secondary
throttle
valve
is
ready
to
open
because
the
locking
arm
revolves
and
leaves
from
the
se
condary
throttle
arm
Engine
Fuel
HI
h
speed
circuit
The
high
speed
circuit
improves
high
engine
output
performance
during
high
speed
driving
This
circuit
operates
only
when
driving
at
high
speed
It
consists
of
a
richer
jet
high
speed
enricher
air
bleed
and
richer
nozzle
When
the
velocity
of
suction
air
flowing
through
the
carburetor
secondary
bore
in
creases
additional
fuel
is
drawn
out
of
the
richer
nozzle
@
2
EF234
Secondary
I
Richer
jet
2
High
speed
enricher
air
bleed
3
Richer
nozzle
Primary
Fig
EF
29
High
speed
circuit
ANTI
DIESELlNG
SYSTEM
is
brought
into
operation
shutting
off
the
supply
of
fuel
to
the
slow
circuit
The
following
figure
shows
a
see
tiorial
view
of
this
control
The
carburetor
is
equipped
with
an
anti
dieseling
solenoid
valve
As
the
ignition
switch
is
turned
off
the
valve
EF230
@
l
CD
1
1
g
@eI
1
Anti
dieseling
solenoid
va1
2
Ignition
switch
3
Battery
Fig
EF
30
Schematic
drawing
of
anti
dieseling
sydtm
EF
17
Page 114 of 537
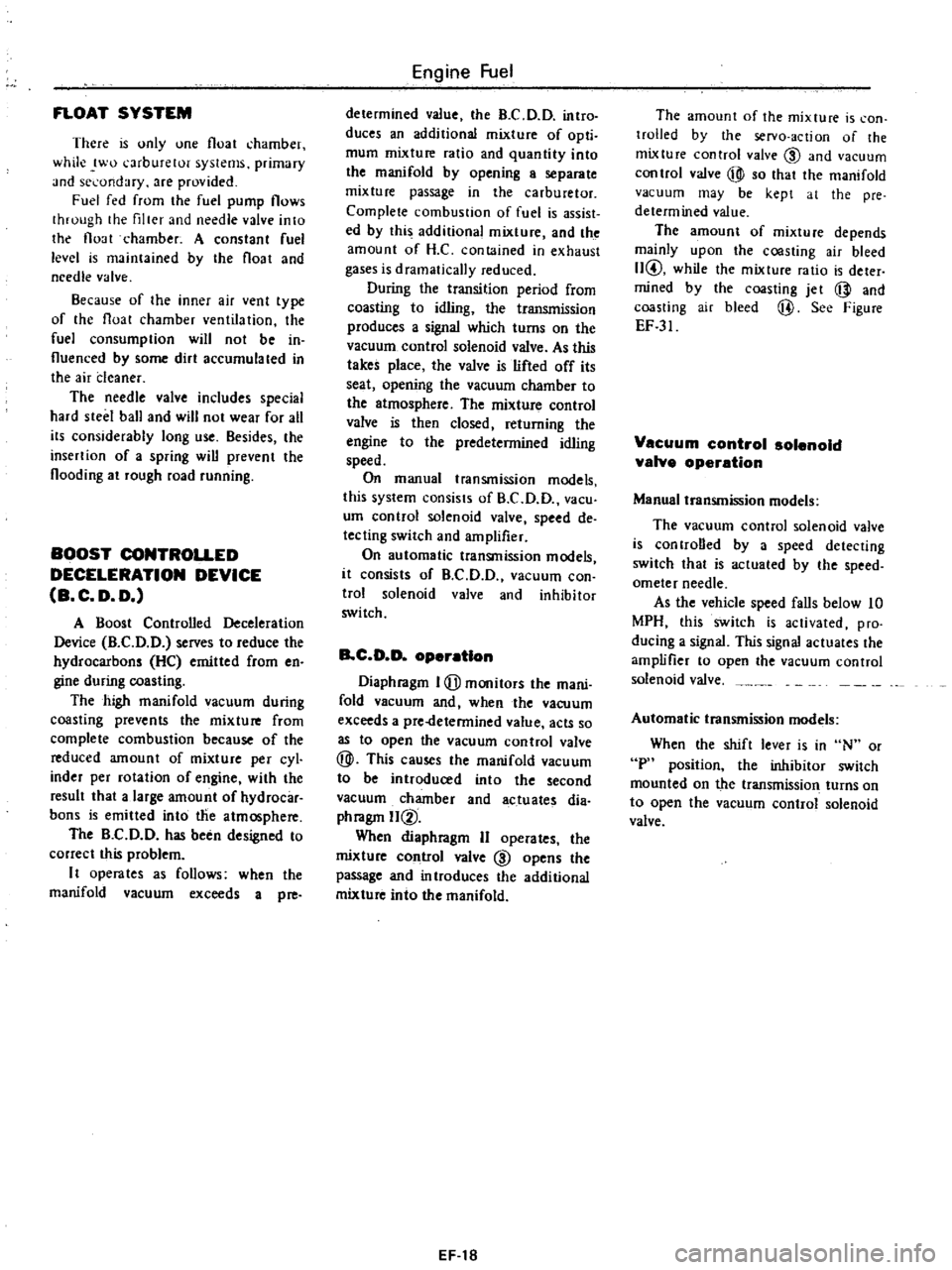
FLOAT
SYSTEM
There
IS
only
one
float
chamber
while
two
l
arburetor
systems
primary
Jnd
st
l
ondary
are
provided
Fuel
fed
from
the
fuel
pump
flows
through
the
filler
and
needle
valve
into
the
flo
t
chamber
A
constant
fuel
level
is
maintained
by
the
float
and
needle
valve
Because
of
the
inner
air
vent
type
of
the
float
chamber
ventilation
the
fuel
consumption
will
not
be
in
fluenced
by
some
dirt
accumulated
in
the
air
deaner
The
needle
valve
includes
special
hard
steel
ball
and
will
not
wear
for
all
its
considerably
long
use
Besides
the
inserrion
of
a
spring
wiU
prevent
the
flooding
at
rough
road
running
BOOST
CONTROLLED
DECELERATION
DEVICE
B
C
D
D
A
Boost
Controlled
Deceleration
Device
B
C
D
D
serves
to
reduce
the
hydrocarbons
He
emitted
from
en
gine
during
coasting
The
high
manifold
vacuum
during
coasting
prevents
the
mixture
from
complete
combustion
because
of
the
reduced
amount
of
mixture
per
cyl
inder
per
rotation
of
engine
with
the
result
that
a
large
amount
of
hydrocar
bons
is
emitted
into
tile
atmosphere
The
B
C
D
D
has
been
designed
to
correct
this
problem
It
opern
tes
as
follows
when
the
manifold
vacuum
exceeds
a
pre
Engine
Fuel
determined
value
the
B
C
D
D
intro
duces
an
additional
mixture
of
opti
mum
mixture
ratio
and
quantity
into
the
manifold
by
opening
a
separate
mixture
passage
in
the
carburetor
Complete
combustion
of
fuel
is
assist
ed
by
this
additional
mixture
and
the
amount
of
H
C
contained
in
exhaust
gases
is
dramatically
reduced
During
the
transition
period
from
coasting
to
idling
the
transmission
produces
a
signal
which
turns
on
the
vacuum
control
solenoid
valve
As
this
takes
place
the
valve
is
lifted
off
its
seat
opening
the
vacuum
chamber
to
the
atmosphere
The
mixture
control
valve
is
then
closed
returning
the
engine
to
the
predetermined
idling
speed
On
manual
transmission
models
this
system
consists
of
B
C
D
D
vacuo
urn
control
solenoid
valve
speed
de
tecting
switch
and
amplifier
On
automatic
transmission
models
it
consists
of
B
C
D
D
vacuum
con
trol
solenoid
valve
and
inhibitor
switch
B
C
D
D
operation
Diaphragm
I
Qj
monitors
the
mani
fold
vacuum
and
when
the
vacuum
exceeds
a
pre
fetermined
value
acts
so
as
to
open
the
vacuum
control
valve
@
This
causes
the
manifold
vacu
urn
to
be
introduced
into
the
second
vacuum
chamber
and
actuates
dia
phragm
ll@
When
diaphrngm
II
operates
the
mixture
control
valve
@
opens
the
passage
and
introduces
the
additional
mixture
into
the
manifold
EF
18
The
amount
of
the
mixture
is
con
trolled
by
the
servo
action
of
the
mixture
control
valve
CID
and
vacuum
control
valve
@
so
that
the
manifold
vacuum
may
be
kept
at
the
pre
determined
value
The
amount
of
mixture
depends
mainly
upon
the
coasting
air
bleed
II@
while
the
mixture
ratio
is
deter
mined
by
the
coasting
jet
@
and
coasting
air
bleed
@
See
Figure
EF
31
Vacuum
control
solenoid
valve
operation
Manual
transmission
models
The
vacuum
control
solenoid
valve
is
con
troDed
by
a
speed
detecting
switch
that
is
actuated
by
the
speed
ometer
needle
As
the
vehicle
speed
falls
below
10
MPH
this
switch
is
activated
pro
ducing
a
signal
This
signal
actuates
the
amplifier
to
open
the
vacuum
control
solenoid
valve
Automatic
transmission
models
When
the
shift
lever
is
in
N
or
P
position
the
inhibitor
switch
mounted
on
the
transmission
turns
on
to
open
the
vacuum
control
solenoid
valve