ECO DATSUN PICK-UP 1977 Workshop Manual
[x] Cancel search | Manufacturer: DATSUN, Model Year: 1977, Model line: PICK-UP, Model: DATSUN PICK-UP 1977Pages: 537, PDF Size: 35.48 MB
Page 159 of 537
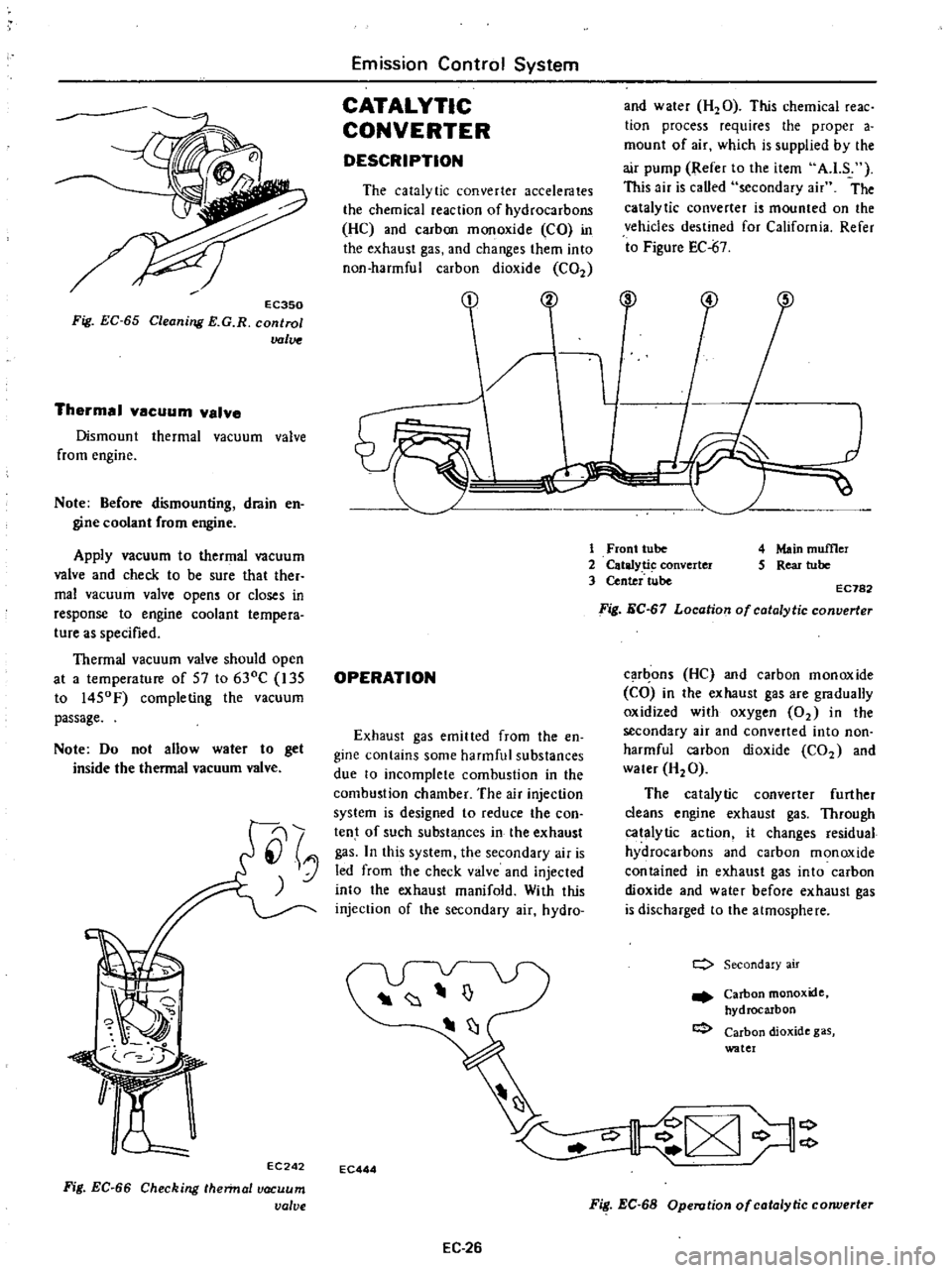
EC350
Fig
EC
65
Cleaning
E
G
R
control
valve
Thermal
vacuum
valve
Dismount
thermal
vacuum
valve
from
engine
Note
Before
dismounting
drain
en
gine
coolant
from
engine
Apply
vacuum
to
thermal
vacuum
valve
and
check
to
be
sure
thaI
ther
mal
vacuum
valve
opens
or
closes
in
response
to
engine
coolant
tempera
ture
as
specified
Thermal
vacuum
valve
should
open
at
a
temperature
of
57
to
630C
135
to
1450F
completing
the
vacuum
passage
Note
Do
not
allow
water
to
get
inside
the
thermal
vacuum
valve
EC242
Fig
EC
66
Checking
hennal
vacuum
valve
Emission
Control
System
CATALYTIC
CONVERTER
DESCRIPTION
The
catalytic
converter
accelerates
the
chemical
reaction
of
hydrocarbons
HC
and
carbon
monoxide
CO
in
the
exhaust
gas
and
changes
them
into
non
harmful
carbon
dioxide
C02
OPERATION
Exhaust
gas
emitted
from
the
en
gine
contains
some
harmful
substances
due
to
incomplete
combustion
in
the
combustion
chamber
The
air
injection
system
is
designed
to
reduce
the
con
tent
of
such
substances
in
the
exhaust
gas
In
this
system
the
secondary
air
is
led
from
the
check
valve
and
injected
into
the
exhaust
manifold
With
this
injection
of
the
secondary
air
hydro
EC444
EC
26
and
water
H20
This
chemical
reac
tion
process
requires
the
proper
a
mount
of
air
which
is
supplied
by
the
air
pump
Refer
to
the
item
AJ
S
This
air
is
caUed
secondary
air
The
catalytic
converter
is
mounted
on
the
vehicles
destined
for
California
Refer
to
Figure
EC
67
3
4
1
Front
tube
2
Catalyti
converter
3
Center
tube
4
Main
muffler
5
Rear
tube
EC782
Fig
EC
67
Location
of
catalytic
converter
car
ons
He
and
carbon
monoxide
CO
in
the
exhaust
gas
are
gradually
oxidized
with
oxygen
02
in
the
secondary
air
and
converted
into
non
harmful
carbon
dioxide
C02
and
water
H20
The
catalytic
converter
further
cleans
engine
exhaust
gas
Through
catalytic
action
it
changes
residual
hydrocarbons
and
carbon
monoxide
contained
in
exhaust
gas
into
carbon
dioxide
and
water
before
exhaust
gas
is
discharged
to
the
atmosphere
c
Secondary
air
Carbon
monoxide
hydrocarbon
Carbon
dioxide
gas
water
F
EC
68
Operution
of
catalytic
corwerter
Page 162 of 537
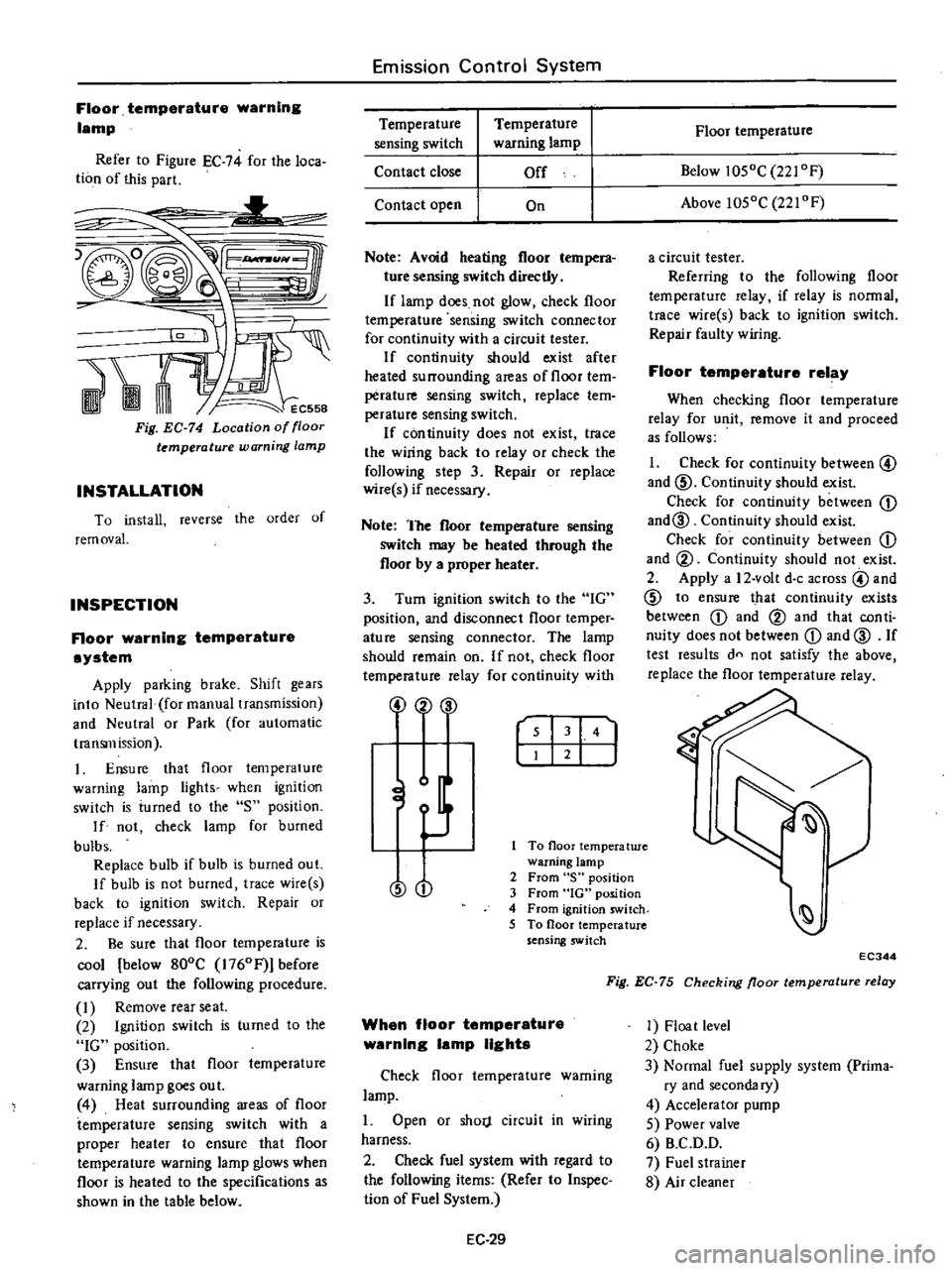
Floor
temparature
warning
lamp
Refer
to
Figure
EC
74
for
the
loca
tion
of
this
part
L
1t
1
RAt
Fig
EC
74
Location
of
floor
temperature
warning
lamp
INSTALLATION
To
install
reverse
the
order
of
rem
ovaL
INSPECTION
Floor
warning
temperature
system
Apply
parking
brake
Shift
gears
into
Neutral
foI
manual
transmission
and
Neutral
or
Park
for
automatic
transmission
1
Ensure
that
floor
temperature
warning
lamp
lights
when
ignition
switch
is
iumed
to
the
S
position
If
not
check
lamp
for
burned
bulbs
Replace
bulb
if
bulb
is
burned
out
If
bulb
is
not
burned
trace
wire
s
back
to
ignition
switch
Repair
or
replace
if
necessary
2
Be
sure
that
floor
temperature
is
cool
below
800C
1760Fj
before
carrying
out
the
following
procedure
I
Remove
rearseat
2
Ignition
switch
is
turned
to
the
IG
position
3
Ensure
that
floor
temperature
warning
lamp
goes
out
4
Heat
surrounding
areas
of
floor
temperature
sensing
switch
with
a
proper
heater
to
ensure
that
floor
temperature
warning
lamp
glows
when
floor
is
heated
to
the
specifications
as
shown
in
the
table
below
Emission
Control
System
Temperature
sensing
switch
Contact
close
Temperature
warning
lamp
Off
Contact
open
On
Note
Avoid
heating
floor
tempera
ture
sensing
switch
directly
If
lamp
does
not
glow
check
floor
temperature
sensing
switch
connector
for
continuity
with
a
circuit
tester
If
continuity
should
exist
after
heated
surrounding
areas
of
floor
tem
perature
sensing
switch
replace
tem
perature
sensing
switch
If
con
tinuity
does
not
exist
trace
the
wiring
back
to
relay
or
check
the
following
step
3
Repair
or
replace
wire
s
if
necessary
Note
The
floor
temperature
sensing
switch
may
be
heated
through
the
floor
by
a
proper
heater
3
Turn
ignition
switch
to
the
IG
position
and
disconnect
floor
temper
ature
sensing
connector
The
lamp
should
remain
on
If
not
check
floor
temperature
relay
for
continuity
with
2
00
r
I
141
J
To
floor
temperatwe
warning
lamp
2
From
S
position
3
From
IG
position
4
From
ignition
switch
5
To
floor
temperature
sensing
switch
O
When
floor
temperature
warning
lamp
lights
Check
floor
temperature
warning
lamp
1
Open
or
shorj
circuit
in
wiring
harness
2
Check
fuel
system
with
regard
to
the
following
items
Refer
to
Inspec
lion
of
Fuel
System
EC
29
Floor
temperature
Below
1050C
221
OF
Above
1050C
221
OF
a
circuit
tester
Referring
to
the
following
floor
temperature
relay
if
relay
is
normal
trace
wire
s
back
to
ignition
switch
Repair
faulty
wiring
Floor
temperature
relay
When
checking
floor
temperature
relay
for
unit
remove
it
and
proceed
as
follows
1
Check
for
continuity
between
@
and
ID
Continuity
should
exist
Check
for
continuity
between
CD
and@
Continuity
should
exist
Check
for
continuity
between
CD
and
@
Continuity
should
not
exist
2
Apply
a
12
volt
doc
across
@
and
ID
to
ensure
that
continuity
exists
between
CD
and
@
and
that
con
ti
nuity
does
not
between
CD
and
@
If
test
results
dn
not
satisfy
the
above
replace
the
floor
temperature
relay
EC344
Fig
EC
75
Checking
floor
temperature
relay
1
Float
level
2
Choke
3
Normal
fuel
supply
system
Prima
ry
and
secondary
4
Accelerator
pump
5
Power
valve
6
B
C
D
D
7
Fuel
strainer
8
Air
cleaner
Page 164 of 537
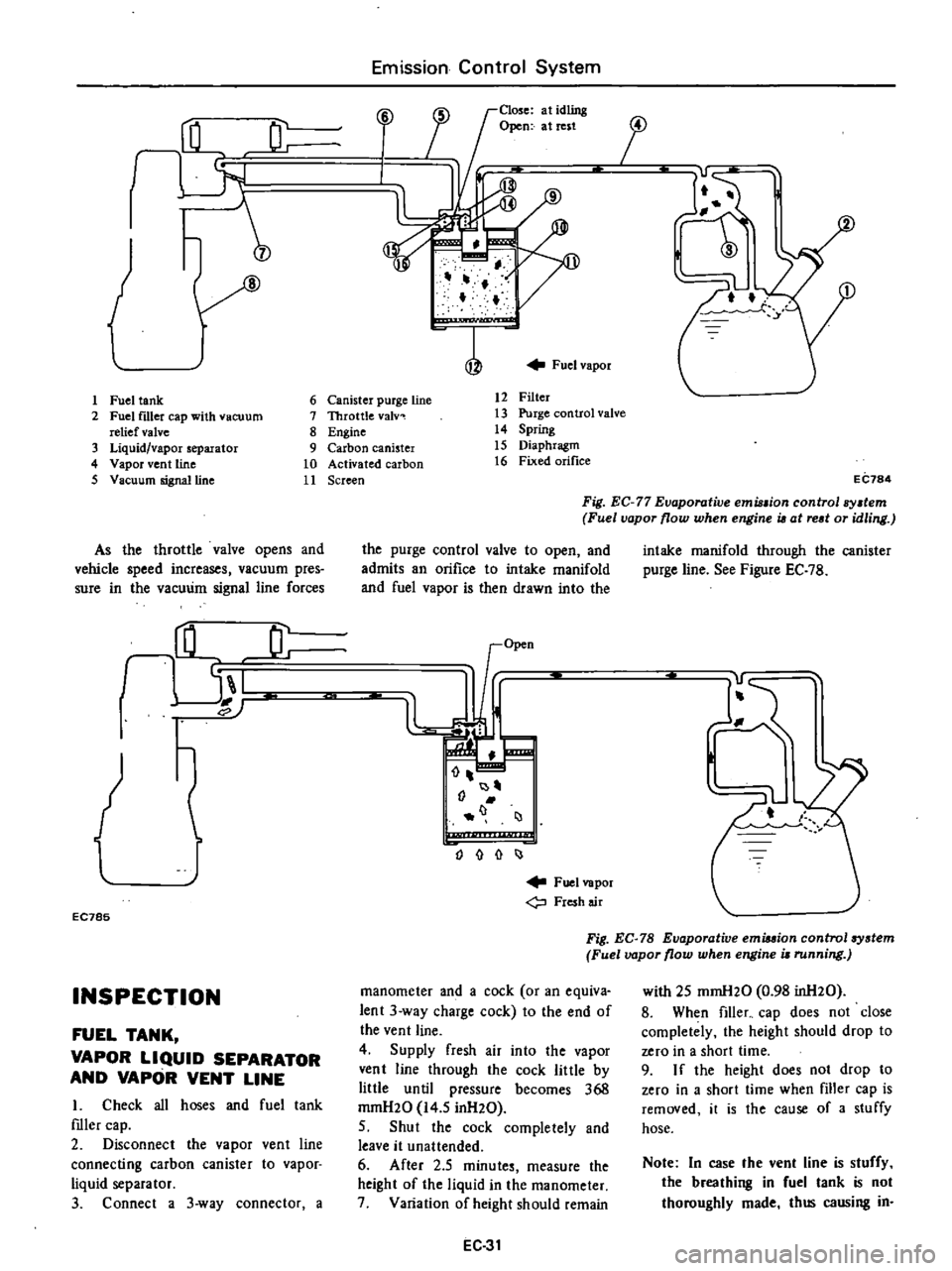
J
1
Fuel
tank
2
Fuel
f1l1er
cap
with
vacuum
relief
valve
3
Liquid
vapor
separator
4
Vapor
vent
line
5
Vacuum
signalUne
As
the
throttle
valve
opens
and
vehicle
speed
increases
vacuum
pres
sure
in
the
vacuum
signal
line
forces
rHL
JL
I
EC785
INSPECTION
FUEL
TANK
VAPOR
LIQUID
SEPARATOR
AND
VAPOR
VENT
LINE
I
Check
all
hoses
and
fuel
tank
mler
cap
2
Disconnect
the
vapor
vent
line
connecting
carbon
canister
to
vapor
liquid
separator
3
Connect
a
3
way
connector
a
Emission
Control
System
Close
at
idling
Open
at
rest
i
J
17
f
Fuel
vapor
6
Canister
purge
line
7
Throttle
valv
8
Engine
9
Carbon
canister
10
Activated
carbon
11
Screen
12
Filter
13
Purge
control
valve
14
Spring
15
Diaphragm
16
Fixed
orifice
i
j
EC784
Fig
EC
77
Evaporative
emu
ion
control
sy
tem
Fuel
vapor
flow
when
engine
i6
at
red
or
idling
the
purge
control
valve
to
open
and
admits
an
orifice
to
intake
manifold
and
fuel
vapor
is
then
drawn
into
the
I
J
o
I
Fuel
vapor
Fresh
air
intake
manifold
through
the
canister
purge
line
See
Figure
EC
7B
Fig
EC
78
Evaporative
emiuion
control
system
Fuel
vapor
flow
when
engine
i
running
manometer
and
a
cock
or
an
equiva
lent
3
way
charge
cock
to
the
end
of
the
vent
line
4
Supply
fresh
air
into
the
vapor
vent
line
through
the
cock
little
by
little
until
pressure
becomes
368
mrnH20
14
5
inH20
5
Shut
the
cock
completely
and
leave
it
unattended
6
After
2
5
minutes
measure
the
height
of
the
liquid
in
the
manometer
7
Variation
of
height
should
remain
EC
31
with
25
mmH20
0
98
inH20
8
When
filler
cap
does
not
close
completely
the
height
should
drop
to
zero
in
a
short
time
9
I
f
the
height
does
not
drop
to
zero
in
a
short
time
when
filler
cap
is
removed
it
is
the
cause
of
a
stuffy
hose
Note
In
case
the
vent
line
is
stuffy
the
breathing
in
fuel
tank
is
not
thoroughly
made
thus
causing
in
Page 179 of 537
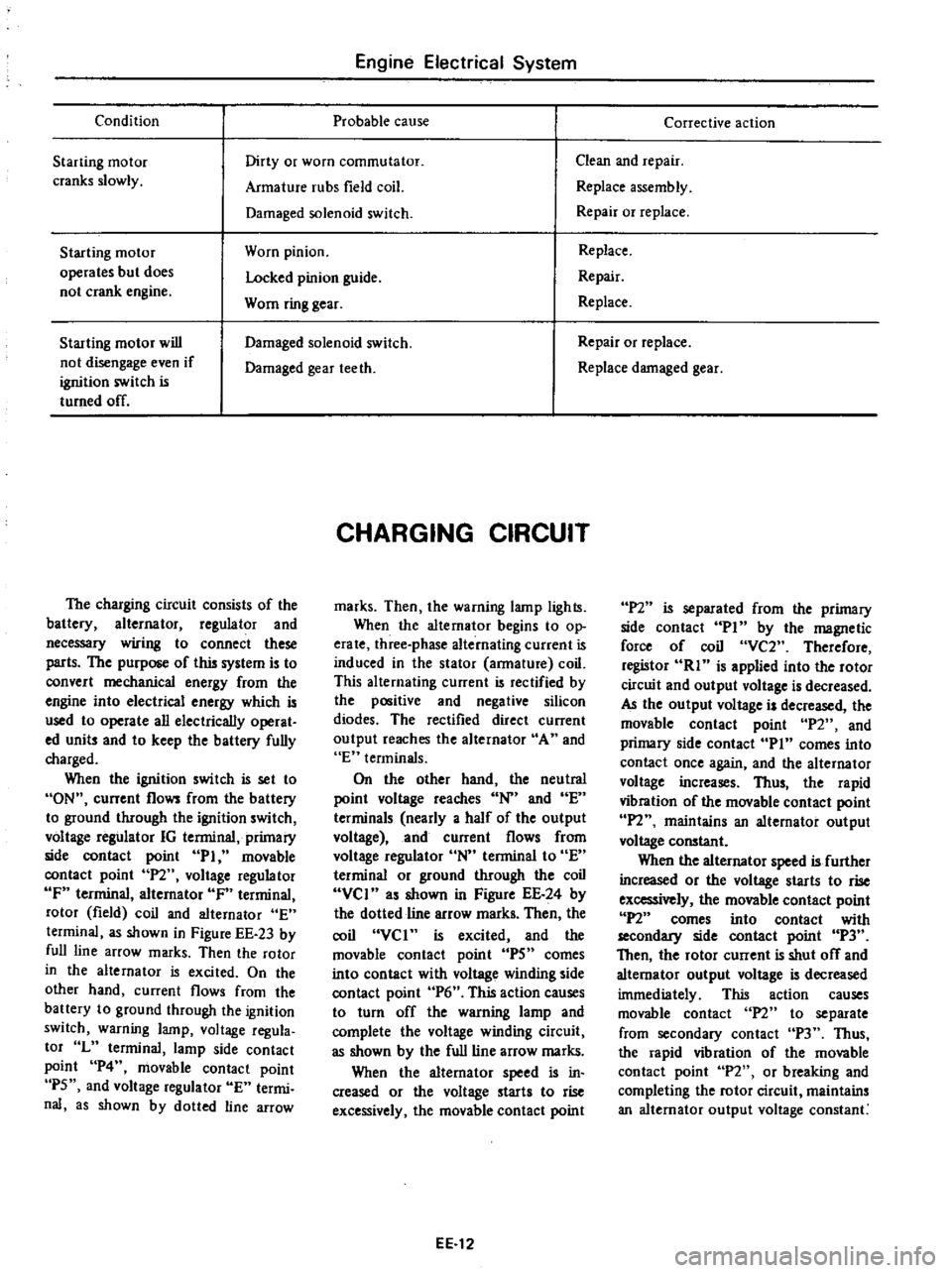
Condition
Engine
Electrical
System
Probable
cause
Starting
motor
cranks
slowly
Dirty
or
worn
commutator
Armature
rubs
field
coil
Damaged
solenoid
switch
Starting
motor
operates
but
does
not
crank
engine
Worn
pinion
Locked
pinion
guide
Worn
ring
gear
Starting
motor
will
not
disengage
even
if
ignition
switch
is
turned
off
Damaged
solenoid
switch
Damaged
gear
teeth
The
charging
circuit
consists
of
the
battery
alternator
regulator
and
necessary
wiring
to
connect
these
parts
The
purpose
of
this
system
is
to
convert
mechanical
energy
from
the
engine
into
electrical
energy
which
is
used
to
operate
all
electrically
operat
ed
units
and
to
keep
the
battery
fully
charged
When
the
ignition
switch
is
set
to
ON
current
flows
from
the
battery
to
ground
through
the
ignition
switch
voltage
regulator
IG
terminal
primary
side
contact
point
PI
movable
contact
point
P2
voltage
regulator
IF
terminal
alternator
IF
terminal
rotor
field
coil
and
alternator
E
terminal
as
shown
in
Figure
EE
23
by
full
line
arrow
marks
Then
the
rotor
in
the
alternator
is
excited
On
the
other
hand
current
flows
from
the
battery
to
ground
through
the
ignition
switch
warning
lamp
voltage
regula
tor
L
terminal
lamp
side
contact
point
P4
movable
contact
point
P5
and
voltage
regulator
E
termi
nal
as
shown
by
dotted
line
arrow
CHARGING
CIRCUIT
marks
Then
the
warning
lamp
lights
When
the
alternator
begins
to
op
erate
three
phase
alternating
current
is
induced
in
the
stator
armature
coil
This
alternating
current
is
rectified
by
the
positive
and
negative
silicon
diodes
The
rectified
direct
current
output
reaches
the
alternator
A
and
E
terminals
On
the
other
hand
the
neutral
point
voltage
reaches
N
and
E
terminals
nearly
a
half
of
the
output
voltage
and
current
flows
from
voltage
regulator
N
terminal
to
E
terminal
or
ground
through
the
coil
VCI
as
shown
in
Figure
EE
24
by
the
dotted
line
arrow
marks
Then
the
coil
VCI
is
excited
and
the
movable
contact
point
IPS
comes
into
contact
with
voltage
winding
side
contact
point
P6
This
action
causes
to
turn
off
the
warning
lamp
and
complete
the
voltage
winding
circuit
as
shown
by
the
full
line
arrow
marks
When
the
alternator
speed
is
in
creased
or
the
voltage
starts
to
rise
excessively
the
movable
contact
point
EE
12
Corrective
action
Clean
and
repair
Replace
assembly
Repair
or
replace
Replace
Repair
Replace
Repair
or
replace
Replace
damaged
gear
P2
is
separated
from
the
primary
side
contact
PI
by
the
magnetic
force
of
coil
VC2
Therefore
registor
RI
is
applied
into
the
rotor
circuit
and
output
voltage
is
decreased
AJ
the
output
voltage
is
decreased
the
movable
contact
point
P2
and
primary
side
contact
Pin
comes
into
contact
once
again
and
the
alternator
voltage
increases
Thus
the
rapid
vibration
of
the
movable
contact
point
IPl
maintains
an
alternator
output
voltage
constant
When
the
alternator
speed
is
further
increased
or
the
voltage
starts
to
rise
excessively
the
movable
contact
point
P2
comes
into
contact
with
secondllJ
side
contact
point
P3
Then
the
rotor
current
is
shut
off
and
alternator
output
voltage
is
decreased
immediately
This
action
causes
movable
contact
n
to
separate
from
secondary
contact
P3
Thus
the
rapid
vibration
of
the
movable
contact
point
P2
or
breaking
and
completing
the
rotor
circuit
maintains
an
alternator
output
voltage
constant
Page 189 of 537
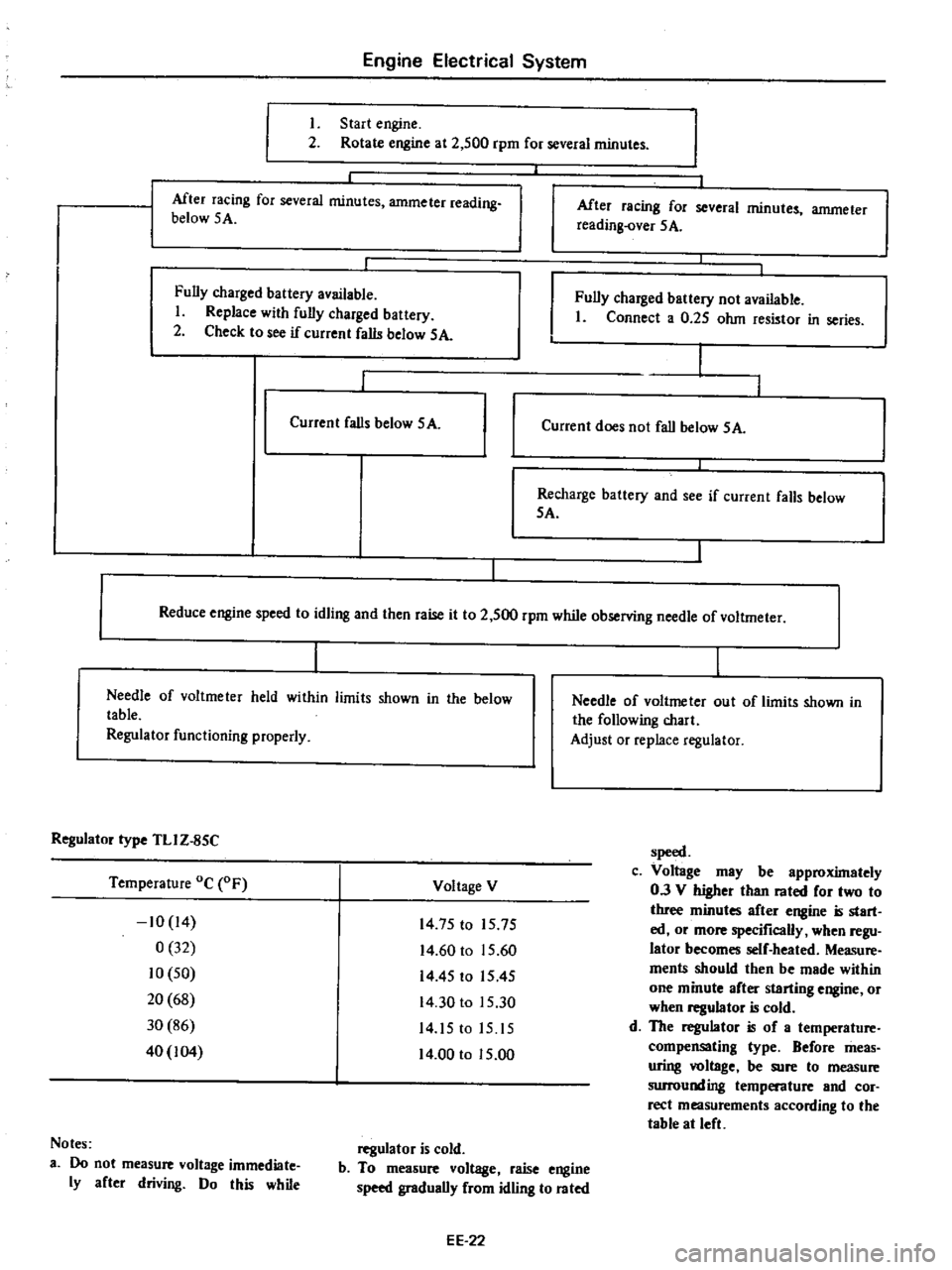
Engine
Electrical
System
I
Start
engine
2
Rotate
engine
at
2
500
rpm
for
several
minutes
Mter
racing
for
several
minutes
ammeter
reading
below
SA
After
racing
for
several
minutes
ammeter
reading
over
5
A
Fully
charged
battery
available
I
Replace
with
fully
charged
battery
2
Check
to
see
if
current
falls
below
SA
Fully
charged
battery
not
available
I
Connect
a
0
25
ohm
resistor
in
series
Current
falls
below
SA
Current
does
not
fall
below
SA
Recharge
battery
and
see
if
current
falls
below
SA
Reduce
engine
speed
to
idling
and
then
raise
it
to
2
500
rpm
while
observing
needle
of
voltmeter
Needle
of
voltmeter
held
within
limits
shown
in
the
below
table
Regulator
functioning
properly
Needle
of
voltme
ter
ou
t
of
limits
shown
in
the
following
chart
Adjust
or
replace
regulator
Regulator
type
TLI
Z
85C
Temperature
Oc
OF
Voltage
V
speed
c
Voltage
may
be
approximately
0
3
V
higher
than
rated
for
two
to
three
minutes
after
engine
is
start
ed
or
more
specifically
when
regu
lator
becomes
self
heated
Measure
ments
should
then
be
made
within
one
minute
after
starting
engine
or
when
regulator
is
cold
d
The
regulator
is
of
a
temperature
compensating
type
Before
meas
uring
voltage
be
sure
to
measure
surrounding
temperature
and
cor
rect
measurements
according
to
the
table
at
left
10
14
0
32
10
50
20
68
30
86
40
104
14
75
to
15
75
14
60
to
15
60
14
45
to
1545
14
30
to
15
30
14
15
to
15
15
14
00
to
15
00
Notes
3
Do
not
measure
voltage
immediate
ly
after
driving
Do
this
while
regulator
is
cold
b
To
measure
voltage
raise
engine
speed
gradually
from
idling
to
rated
EE
22
Page 193 of 537
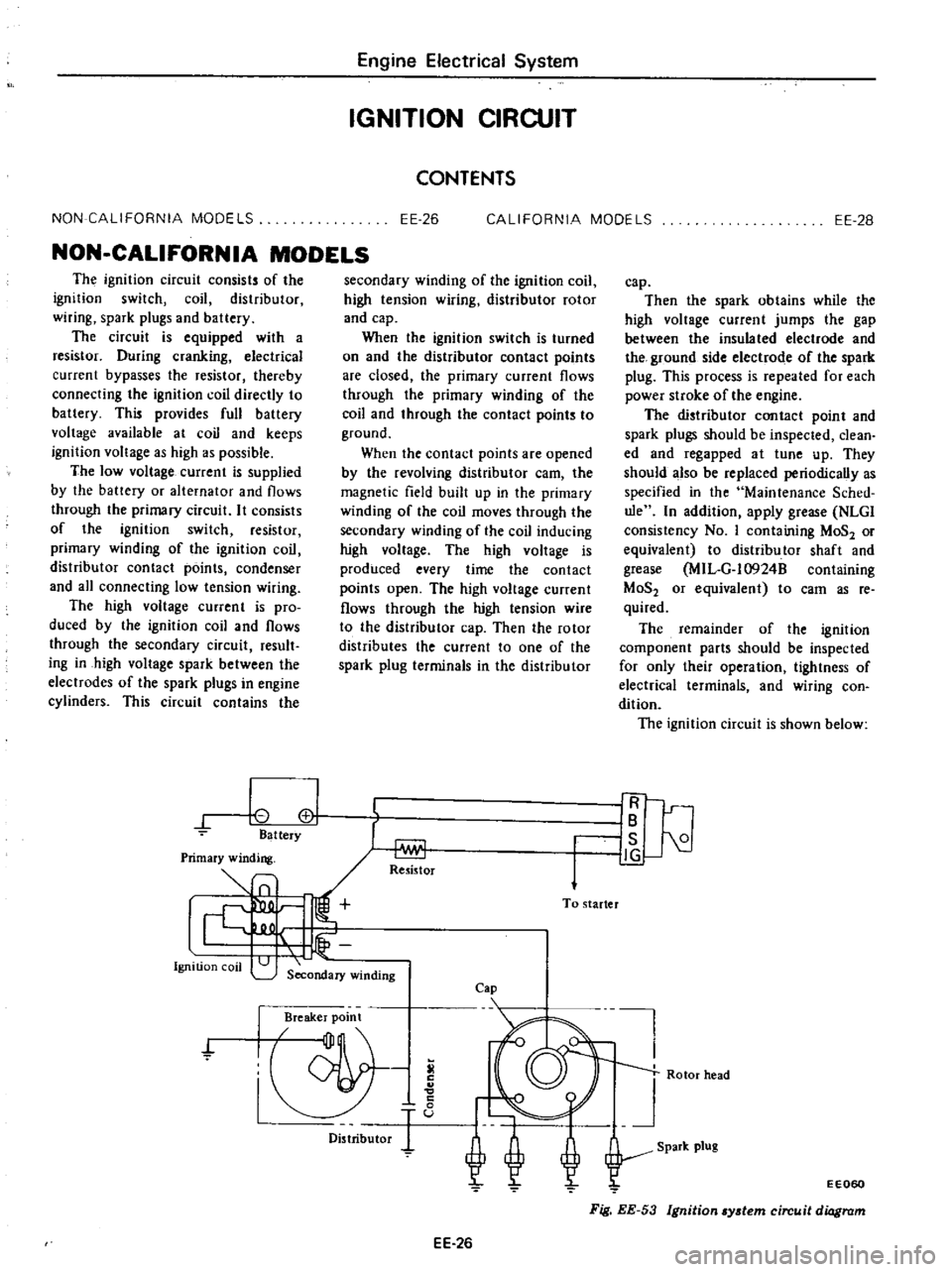
NON
CALIFORNIA
MODELS
Engine
Electrical
System
IGNITION
CIRCUIT
CONTENTS
EE
26
CALIFORNIA
MODELS
EE
2B
NON
CALIFORNIA
MODELS
The
ignition
circuit
consists
of
the
ignition
switch
coil
distributor
wiring
spark
plugs
and
battery
The
circuit
is
equipped
with
a
resistor
During
cranking
electrical
current
bypasses
the
resistor
thereby
connecting
the
ignition
coil
directly
to
battery
This
provides
full
battery
voltage
available
at
coil
and
keeps
ignition
voltage
as
high
as
possible
The
low
voltage
current
is
supplied
by
the
battery
or
alternator
and
flows
through
the
primary
circuit
It
consists
of
the
ignition
switch
resistor
primary
winding
of
the
ignition
coil
distributor
contact
points
condenser
and
all
connecting
low
tension
wiring
The
high
voltage
current
is
pro
duced
by
the
ignition
coil
and
flows
through
the
secondary
circuit
result
ing
in
high
voltage
spark
between
the
electrodes
of
the
spark
plugs
in
engine
cylinders
This
circuit
contains
the
0
cl
Battery
Ignition
coil
secondary
winding
of
the
ignition
coil
high
tension
wiring
distributor
rotor
and
cap
When
the
ignition
switch
is
turned
on
and
the
distributor
contact
points
are
closed
the
primary
current
flows
through
the
primary
winding
of
the
coil
and
through
the
contact
points
to
ground
When
the
contact
points
are
opened
by
the
revolving
distributor
earn
the
magnetic
field
built
up
in
the
primary
winding
of
the
coil
moves
through
the
secondary
winding
of
the
coil
inducing
high
voltage
The
high
voltage
is
produced
every
time
the
contact
points
open
The
high
voltage
current
flows
through
the
high
tension
wire
to
the
distributor
cap
Then
the
rotor
distributes
the
current
to
one
of
the
spark
plug
terminals
in
the
distributor
Re5istor
To
starter
Secondary
winding
Cap
Breaker
point
f
Distributor
EE
26
cap
Then
the
spark
obtains
while
the
high
voltage
current
jumps
the
gap
between
the
insulated
electrode
and
the
ground
side
electrode
of
the
spark
plug
This
process
is
repeated
for
each
power
stroke
of
the
engine
The
distributor
contact
point
and
spark
plugs
should
be
inspected
clean
ed
and
regapped
at
tune
up
They
should
also
be
replaced
periodically
as
specified
in
the
Maintenance
Sched
ule
In
addition
apply
grease
NLGl
consistency
No
I
containing
MoS2
or
equivalent
to
distributor
shaft
and
grease
MIL
G
l0924B
containing
MoS2
or
equivalent
to
cam
as
reo
quired
The
remainder
of
the
ignition
component
parts
should
be
inspected
for
only
their
operation
tightness
of
electrical
terminals
and
wiring
con
dition
The
ignition
circuit
is
shown
below
IR
IB
I
is
21
J
g
Rotor
head
EE060
Fig
EE
53
Ignition
ydem
circuit
diagram
Page 195 of 537
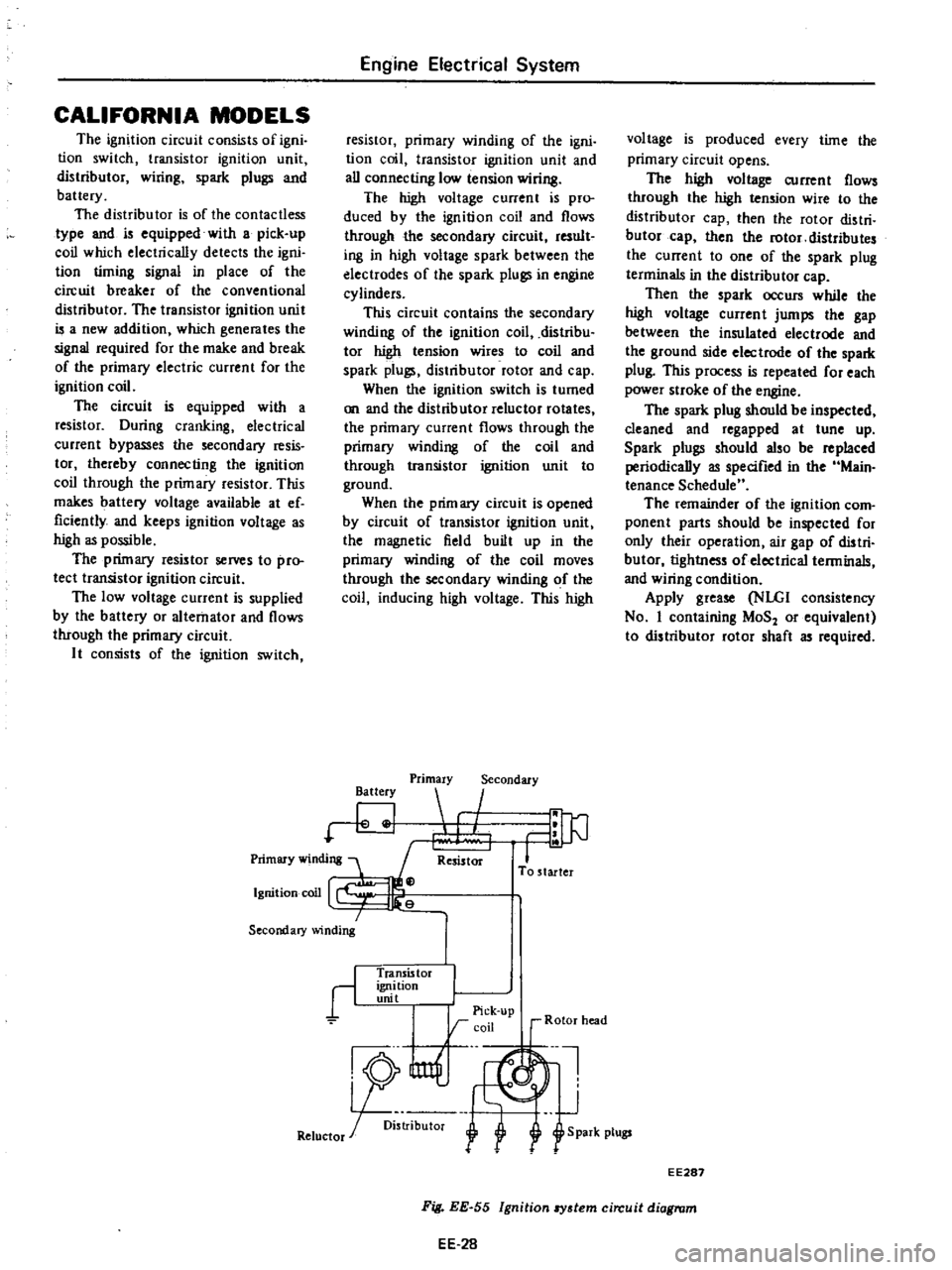
Primary
winding
1
Ignition
coo
I
Secondary
winding
CALIFORNIA
MODELS
The
ignition
circuit
consists
of
igni
tion
switch
transistor
ignition
unit
distributor
wiring
spark
plugs
and
battery
The
distributor
is
of
the
contactless
type
and
is
equipped
with
a
pick
up
coil
which
electrically
detects
the
igni
tion
timing
signal
in
place
of
the
circuit
breaker
of
the
conventional
distributor
The
transistor
ignition
unit
is
a
new
addition
which
generates
the
signal
required
for
the
make
and
break
of
the
primary
electric
current
for
the
ignition
coil
The
circuit
is
equipped
with
a
resistor
During
cranking
electrical
current
bypasses
the
secondary
resis
tor
thereby
connecting
the
ignition
coil
through
the
primary
resistor
This
makes
battery
voltage
available
at
ef
ficiently
and
keeps
ignition
voltage
as
high
as
possible
The
primary
resistor
selVeS
to
pro
tect
transistor
ignition
circuit
The
low
voltage
current
is
supplied
by
the
battery
or
alternator
and
flows
through
the
primary
circuit
It
consists
of
the
ignition
switch
Engine
Electrical
System
resistor
primary
winding
of
the
igni
tion
coil
transistor
ignition
unit
and
all
connecting
low
tension
wiring
The
high
voltage
current
is
pro
duced
by
the
ignition
coil
and
flows
through
the
secondary
circuit
result
ing
in
high
voltage
spark
between
the
electrodes
of
the
spark
plugs
in
engine
cylinders
This
circuit
contains
the
secondary
winding
of
the
ignition
coil
distribu
tor
high
tension
wires
to
coil
and
spark
plugs
distributor
rotor
and
cap
When
the
ignition
switch
is
turned
on
and
the
distributor
reluctor
rotates
the
primary
current
flows
through
the
primary
winding
of
the
coil
and
through
transistor
ignition
unit
to
ground
When
the
prim
ary
circuit
is
opened
by
circuit
of
transistor
ignition
unit
the
magnetic
field
built
up
in
the
primary
winding
of
the
coil
moves
through
the
secondary
winding
of
the
coil
inducing
high
voltage
This
high
Battery
Primary
Secondary
I
Resistor
To
starter
r
Transis
tor
ignition
unit
I
I
Pick
up
rcoil
r
Rotor
head
nl
J
R5
U1f
1
Retuctor
r
oi
l
f
S
park
plugs
voltage
is
produced
every
time
the
primary
circuit
opens
The
high
voltage
current
flows
through
the
high
tension
wire
to
the
distributor
cap
then
the
rotor
distri
butor
cap
then
the
rotor
distributes
the
current
to
one
of
the
spark
plug
terminals
in
the
distributor
cap
Then
the
spark
occurs
while
the
high
voltage
current
jumps
the
gap
between
the
insulated
electrode
and
the
ground
side
electrode
of
the
spark
plug
This
process
is
repeated
for
each
power
stroke
of
the
engine
The
spark
plug
should
be
inspected
cleaned
and
regapped
at
tune
up
Spark
plugs
should
also
be
replaced
periodically
as
specified
in
the
Main
tenance
Schedule
The
remainder
of
the
ignition
com
ponent
parts
should
be
inspected
for
only
their
operation
air
gap
of
distri
butor
tightness
of
electrical
terminals
and
wiring
condition
Apply
grease
NLGI
consistency
No
I
containing
MoS
or
equivalent
to
distributor
rotor
shaft
as
required
EE287
EE
28
Fig
EE
55
Ignition
8Y3tem
circuit
diagram
Page 200 of 537
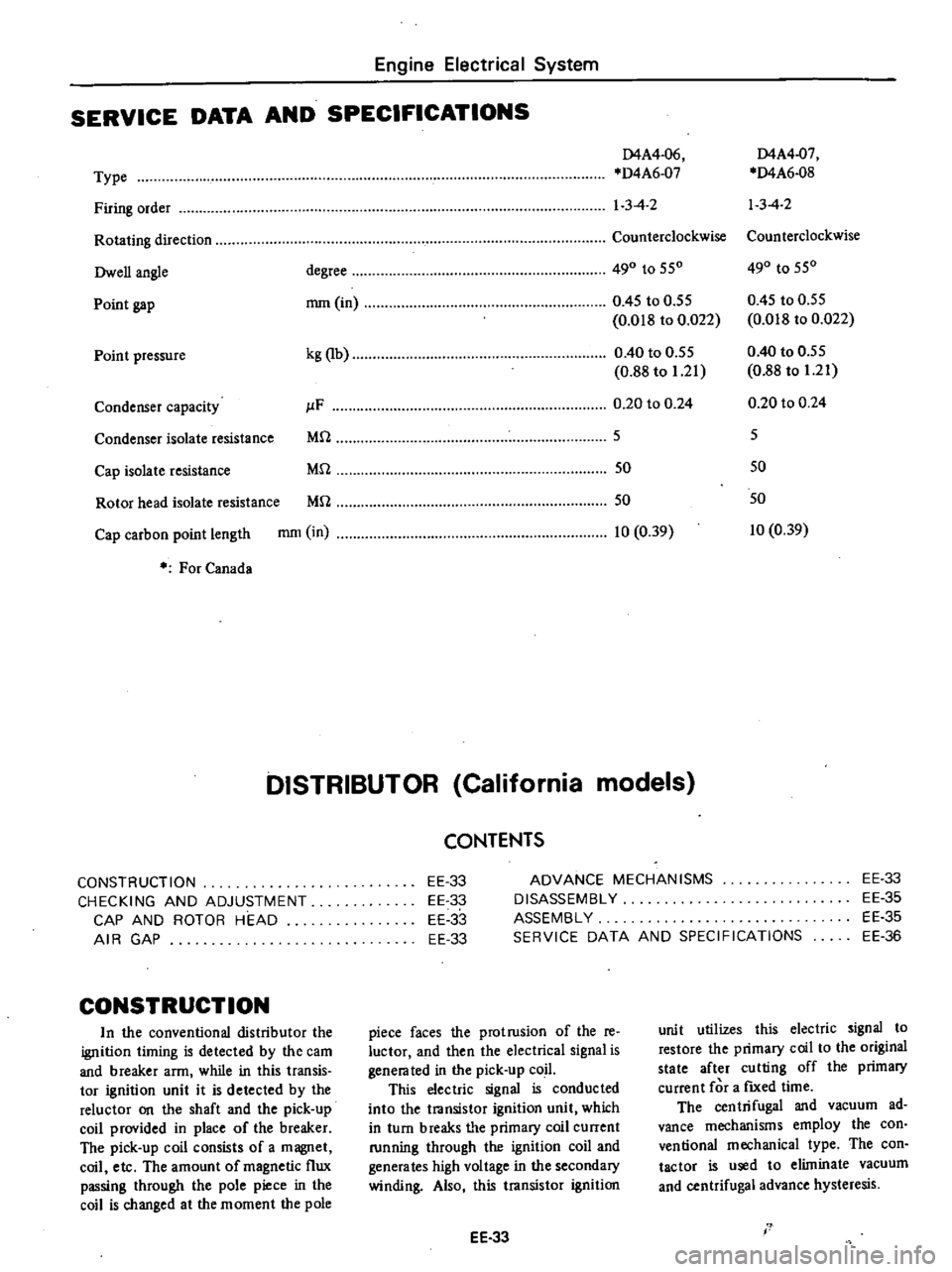
Engine
Electrical
System
SERVICE
DATA
AND
SPECIFICATIONS
D4A4
06
D4A4
07
Type
D4A6
07
D4A6
08
Firing
order
1
3
4
2
13
4
2
Rotating
direction
Counterclockwise
Counterclockwise
Owen
angle
degree
490
to
550
490
to
550
Point
gap
mm
in
0
45
to
0
55
0
45
to
0
55
0
018
to
0
022
0
018
to
0
022
Point
pressure
kg
lb
0
40
to
0
55
0
40
to
0
55
0
88
to
1
21
0
88
to
1
21
Condenser
capacity
JlF
0
20
to
0
24
0
20
to
0
24
Condenser
isolate
resistance
Mrl
5
5
Cap
isolate
resistance
Mrl
50
50
Rotor
head
isolate
resistance
Mrl
50
50
Cap
carbon
point
length
mm
in
10
0
39
10
0
39
For
Canada
DISTRIBUTOR
California
models
CONSTRUCTION
CHECKING
AND
ADJUSTMENT
CAP
AND
ROTOR
HEAD
AIR
GAP
CONSTRUCTION
In
the
conventional
distributor
the
ignition
liming
is
detected
by
the
cam
and
breaker
arm
while
in
this
transis
tor
ignition
unit
it
is
detected
by
the
reluctor
on
the
shaft
and
the
pick
up
coil
provided
in
place
of
the
breaker
The
pick
up
coil
consists
of
a
magnet
coil
etc
The
amount
of
magnetic
flux
passing
through
the
pole
piece
in
the
coil
is
changed
at
the
moment
the
pole
CONTENTS
EE
33
EE
33
EE
33
EE
33
ADVANCE
MECHANISMS
DISASSEMBLY
ASSEMBLY
SERVICE
DATA
AND
SPECIFICATIONS
EE
33
EE
35
EE
35
EE
36
piece
faces
the
protrusion
of
the
re
luctor
and
then
the
electrical
signal
is
genera
ted
in
the
pick
up
coil
This
electric
signal
is
conducted
into
the
transistor
ignition
unit
which
in
turn
breaks
tI
e
primary
coil
current
running
through
the
ignition
coil
and
generates
high
voltage
in
the
secondary
winding
Also
this
transistor
ignition
EE
33
unit
utilizes
this
electric
signal
to
restore
the
primary
coil
to
the
original
state
after
cutting
off
the
primary
current
for
a
fIXed
time
The
centrifugal
and
vacuum
ad
vance
mechanisms
employ
the
con
ventional
mechanical
type
The
con
tactor
is
used
to
eliminate
vacuum
and
centrifugal
advance
hysteresis
I
Page 206 of 537
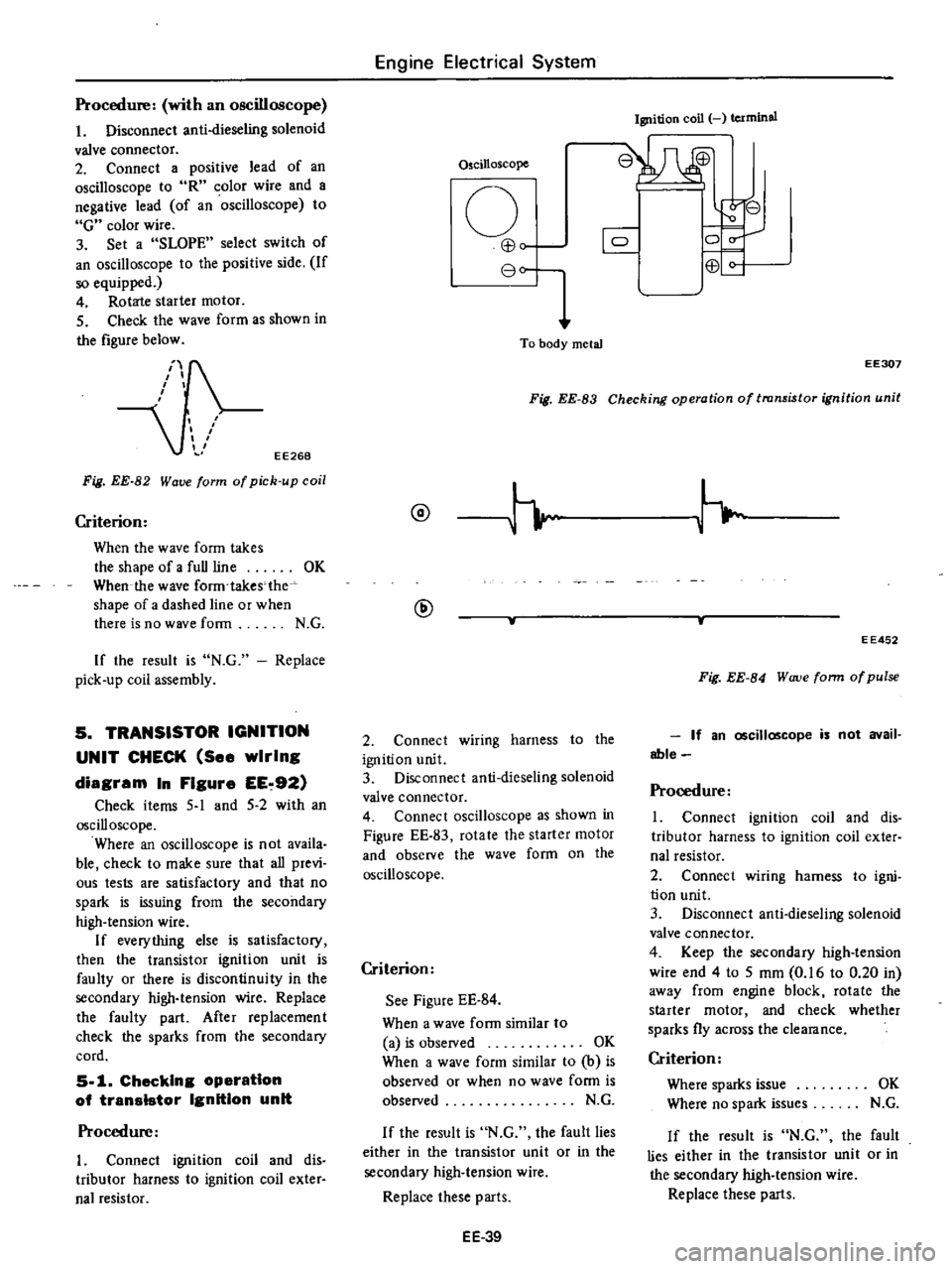
Procedure
with
an
oscilloscope
1
Disconnect
anti
dieseling
solenoid
valve
connector
2
Connect
a
positive
lead
of
an
oscilloscope
to
R
olor
wire
and
a
negative
lead
of
an
oscilloscope
to
G
color
wire
3
Set
a
SLOPE
select
switch
of
an
oscilloscope
to
the
positive
side
If
so
equipped
4
Rotate
starter
motor
5
Check
the
wave
form
as
shown
in
the
figure
below
EE268
Fig
EE
82
Wave
form
of
pick
up
coil
Criterion
When
the
wave
form
takes
the
shape
of
a
full
line
OK
When
the
wave
form
takes
the
shape
of
a
dashed
line
or
when
there
is
no
wave
form
N
G
If
the
result
is
N
G
Replace
pick
up
coil
assembly
5
TRANSISTOR
IGNITION
UNIT
CHECK
See
wiring
diagram
In
Figure
EE
92
Check
items
5
1
and
5
2
with
an
oscilloscope
Where
an
oscilloscope
is
not
availa
ble
check
to
make
sure
that
all
previ
ous
tests
are
satisfactory
and
that
no
spark
is
issuing
from
the
secondary
high
tension
wire
If
everything
else
is
satisfactory
then
the
transistor
ignition
unit
is
faulty
or
there
is
discontinuity
in
the
secondary
high
tension
wire
Replace
the
faulty
part
After
replacement
check
the
sparks
from
the
secondary
cord
5
1
Checking
operatIon
of
transIstor
Ignition
unit
Procedure
I
Connect
ignition
coil
and
dis
tributor
harness
to
ignition
coil
exter
nal
resistor
Engine
Electrical
System
Oscilloscope
o
EB
80
To
body
metal
Ignition
coil
terminal
8W
r
8
0
C
0
EB
Fig
EE
83
Checking
operation
of
transistor
ignition
unit
EE307
@
@
2
Connect
wiring
harness
to
the
ignition
unit
3
Disconnect
anti
dieseling
solenoid
valve
connector
4
Connect
oscilloscope
as
shown
in
Figure
EE
83
rotate
the
starter
motor
and
observe
the
wave
form
on
the
oscilloscope
Criterion
See
Figure
EE
84
When
a
wave
form
similar
to
a
is
observed
OK
When
a
wave
form
similar
to
b
is
obseIVed
or
when
no
wave
form
is
observed
N
G
If
the
result
is
N
G
the
fault
lies
either
in
the
transistor
unit
or
in
the
secondary
high
tension
wire
Replace
these
parts
EE
39
EE452
Fig
EE
84
W
uve
form
of
pulse
If
an
oscilloscope
is
not
avail
able
Procedure
1
Connect
ignition
coil
and
dis
tributor
harness
to
ignition
coil
exter
nal
resistor
2
Connect
wiring
harness
to
igni
tion
unit
3
Disconnect
anti
dieseling
solenoid
valve
connector
4
Keep
the
secondary
high
tension
wire
end
4
to
5
mm
0
16
to
0
20
in
away
from
engine
block
rotate
the
starter
motor
and
check
whether
sparks
fly
across
the
clearance
Criterion
Where
sparks
issue
OK
Where
no
spark
issues
N
G
If
the
result
is
N
G
the
fault
lies
either
in
the
transistor
unit
or
in
the
secondary
high
tension
wire
Replace
these
paris
Page 207 of 537
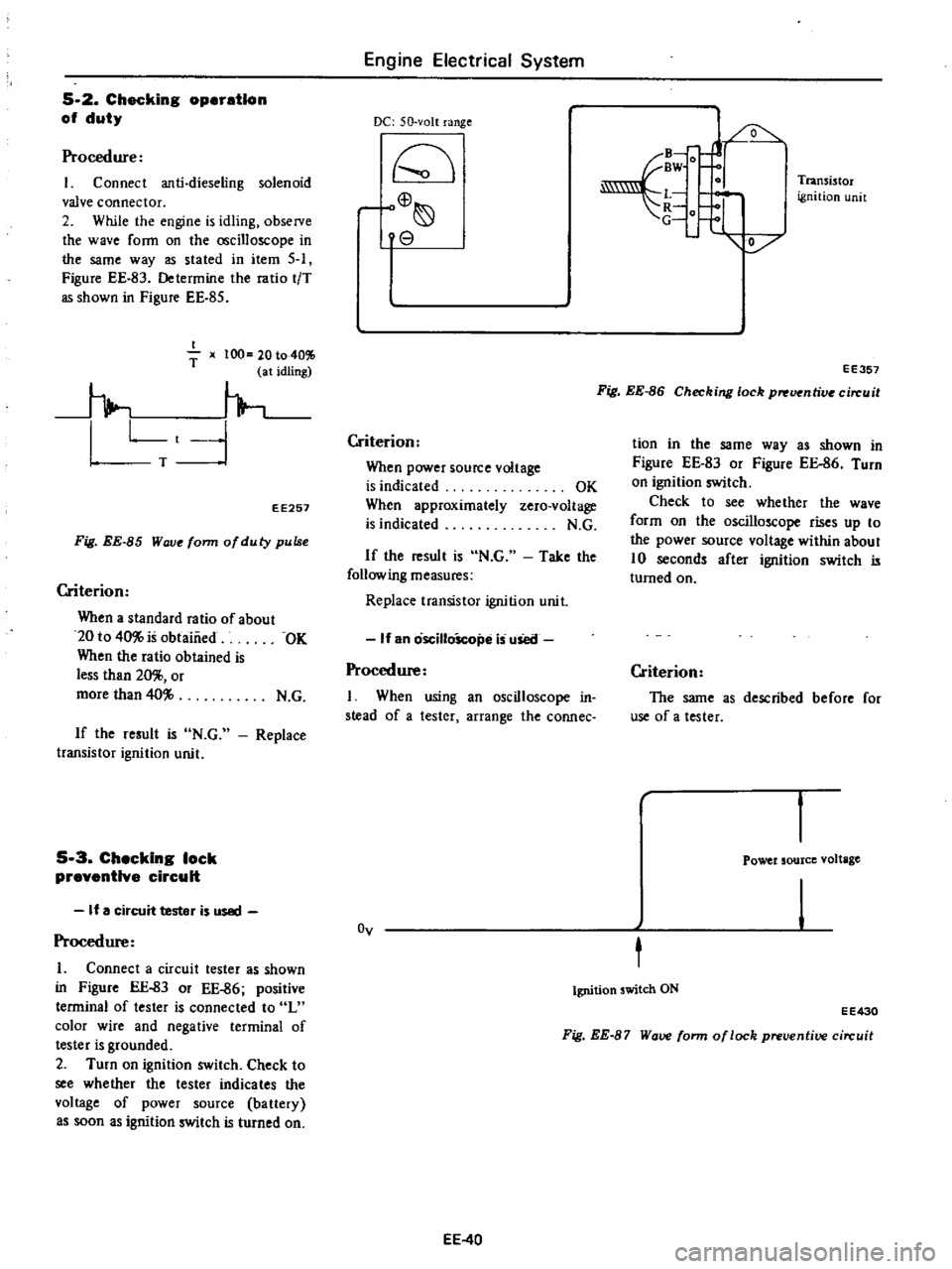
5
2
Checking
operation
of
duty
Procedure
Connect
anti
dieseling
solenoid
valve
connector
2
While
the
engine
is
idling
observe
the
wave
ronn
on
the
oscilloscope
in
the
same
way
as
stated
in
item
5
Figure
EE
83
Determine
the
ratio
tiT
as
shown
in
Figure
EE
85
I
T
x
100
20
to
401
1
at
idling
h
Lt
1
T
EE257
Fig
EE
85
Wove
form
ofduty
pulse
Criterion
When
a
standard
ratio
of
about
20
to
40
is
obtaiiied
OK
When
the
ratio
obtained
is
less
than
20
or
more
than
40
N
G
If
the
result
is
N
G
transistor
ignition
unit
Replace
5
3
Checking
lock
preventive
circuit
If
a
circuit
tester
is
used
Procedure
1
Connect
a
circuit
tester
as
shown
in
Figure
EE
83
or
EE
86
positive
terminal
of
tester
is
connected
to
L
color
wire
and
negative
terminal
of
tester
is
grounded
2
Turn
on
ignition
switch
Check
to
see
whether
the
tester
indicates
the
vol
age
of
power
source
ba
t1ery
as
soon
as
ignition
switch
is
turned
on
Engine
Electrical
System
DC
50
volt
range
rC
o
8
Criterion
When
power
source
voltage
is
indicated
When
approximately
is
indicated
OK
zero
voltage
N
G
If
the
result
is
N
G
Take
the
following
measures
Replace
transistor
ignition
unit
If
an
oscilloScope
is
uSetl
Procedure
I
When
using
an
oscilloscope
in
stead
of
a
tester
arrange
the
connec
Oy
EE
40
B
fJ
BW
O
L
t
1
V
Transi
tor
ignition
unit
EE357
Fig
EE
86
Checking
lock
p
uentive
circuit
tion
in
the
same
way
as
shown
in
Figure
EE
83
or
Figure
EE
86
Turn
on
ignition
switch
Check
to
see
whether
the
wave
form
on
the
oscilloscope
rises
up
to
the
power
source
voltage
within
about
10
seconds
after
ignition
switch
is
turned
on
Criterion
The
same
as
described
before
for
use
of
a
tester
Power
source
voltage
t
Ignition
switch
ON
EE430
Fig
EE
87
Wave
form
of
lock
preventive
circuit