ECO DATSUN PICK-UP 1977 Workshop Manual
[x] Cancel search | Manufacturer: DATSUN, Model Year: 1977, Model line: PICK-UP, Model: DATSUN PICK-UP 1977Pages: 537, PDF Size: 35.48 MB
Page 130 of 537

CLEANING
AND
INSPECTION
Dirt
gum
wuler
or
l
arbon
con
taminatiun
in
or
on
exterior
moving
parts
of
a
arburctor
arc
often
respon
sihk
for
unsatisfactory
performance
For
this
reason
efficient
carbutetioll
dcpends
upon
careful
cleaning
and
inspection
while
servicing
I
Blow
all
passages
and
castings
with
compressed
air
and
blow
off
all
parts
until
dry
Note
Do
not
pass
drills
or
wires
through
calibrated
jet
or
passaaa
as
this
may
enlarge
orirlce
and
seriously
affect
carburetor
calibrs
lion
2
Check
all
parts
for
wear
If
wear
is
noted
damaged
parts
must
be
re
placed
Note
especially
the
following
Engine
Fuel
I
Check
float
needle
and
seat
for
wear
If
wear
is
noted
assembly
must
be
replaced
2
Check
throule
and
choke
shaft
bores
in
throtlle
chamber
and
choice
chamber
for
wear
or
out
of
roundness
3
Inspect
idle
adjusting
needle
for
burrs
or
ridges
Such
a
condition
re
quires
replacemen
1
3
Inspect
gaskets
0
see
if
they
appear
hard
or
briUle
or
if
edges
are
torn
or
distorted
If
any
such
condi
tion
i
noted
they
must
be
replaced
4
Check
filter
screen
for
dirt
or
lint
Clean
and
if
screen
is
distorted
or
remain
plugged
replace
5
Check
linkage
for
operating
condition
6
Inspect
operation
of
accelerating
pump
Pour
f
el
into
jloat
chamber
and
make
throtlle
lever
operate
Check
condition
of
fuel
injection
from
the
EF
34
accelerating
nowe
7
Push
connecting
rod
of
dia
phragm
chamber
and
block
passage
of
vacuum
with
finger
When
connecting
rod
becomes
free
check
for
leakage
of
air
or
damage
to
diaphragm
Jets
Carburetor
performance
depends
on
jet
and
air
bleed
That
is
why
these
components
must
be
fabricated
with
utmost
care
To
clean
them
use
cleaning
solvent
and
blow
air
on
them
Larger
inner
numbers
tamped
on
the
jet
indicate
larger
diameters
Ac
cordingly
main
and
slow
jets
with
lalger
nUmbers
provide
richer
mixture
the
smaller
the
numbers
the
leaner
the
mixture
Conversely
the
main
and
slow
air
bleeds
through
which
air
to
passes
through
make
the
fueLleaner
if
they
bear
larger
numbers
the
smaller
the
numbers
the
richer
the
fuel
Page 131 of 537
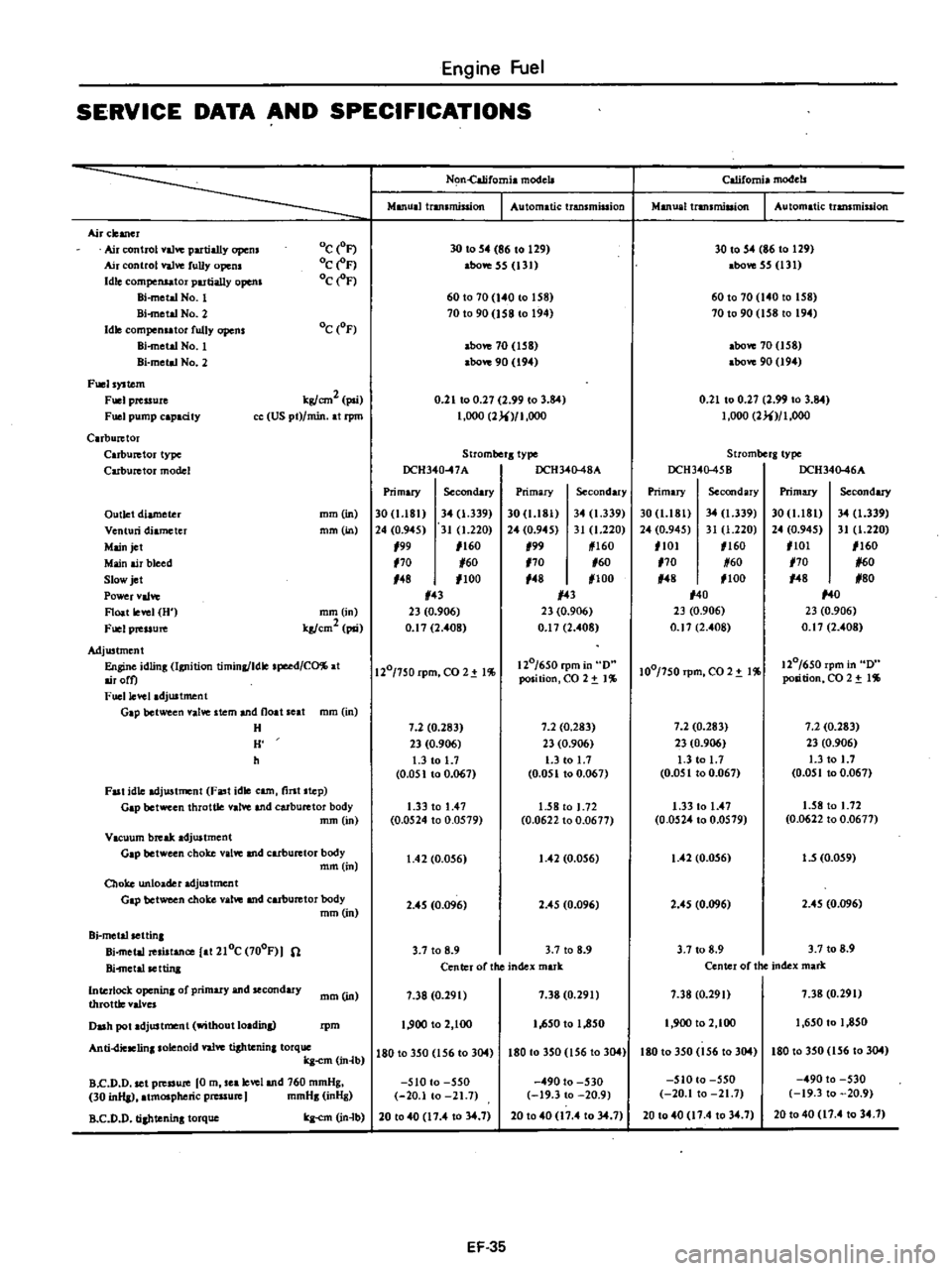
Engine
Fuel
SERVICE
DATA
AND
SPECIFICATIONS
Airclelllcr
Ail
control
val
partially
opem
Air
ntrol
valve
fuUy
opens
Idle
ompensatoI
partially
opens
Hi
mettiNo
l
Bi
metal
No
2
Idle
ompen
tor
fully
opens
Bi
metal
No
1
Hi
metd
No
2
Fuels
Stem
Fuel
prtuure
Fuel
pump
apacHy
C
rbu
tor
C
rbu
tor
type
Carburetor
model
Oc
oF
oCe
F
oCe
F
Oc
OF
kpJcm2
poi
US
pt
min
at
rpm
Outlet
diameter
Venturi
diameter
Main
jet
Main
air
bleed
Slow
jet
Power
val
Float
level
U
fuel
preuure
rom
in
mm
in
mm
in
kg
cm2
psi
Adjustment
Engine
idling
Ignition
timing
Idle
speed
CO
at
mloro
Fuel
level
adjustment
Gap
between
Ive
stem
and
noat
at
mm
in
H
H
h
Fast
idle
adjwtmcnt
Fast
idle
earn
tint
step
Gap
between
throttle
IYe
and
carburetor
body
mm
in
Vacuum
break
adjustment
Gap
between
choke
alve
and
carburetor
body
mm
in
Choke
unloadel
adjusttncnt
Gap
between
choke
alw
and
carburetor
body
rom
in
Bi
metalsettinl
Bi
metal
resistance
at
2Ioe
700F
n
Bi
metalsettina
lnterloc
k
opcnina
of
primary
and
secondary
throtUc
valves
mmOn
Duh
pot
adjustment
without
loadin
I
m
Anti
diclClinasolenoid
valV
C
tiahtenina
torque
ka
m
in
lb
a
c
D
D
set
p
JSure
0
m
sea
level
and
760
mmHg
30
inlla
atmospheric
pressure
J
mmHa
inHg
R
C
D
D
tiahteninl
torque
kg
m
n
b
Nl
n
California
modell
Manual
transmiSsion
I
Automatic
transmission
California
modeb
Manual
transmission
I
Automatic
transmission
30
to
54
86
to
129
above
55
131
30
to
54
86
to
129
above
55
131
60
to
70
140
to
158
70
to
90
158
to
194
60
to
70
140
to
158
70
to
90
158
to
194
above
70
158
above
90
194
above
70
158
above
90
194
0
21
to
0
27
2
99
to
3
84
t
OOO
2
i
I
OOO
0
21
to
0
27
2
99
to
3
84
1
000
2
i
I
OOO
Strombcra
type
OCH340
7A
DCH340
48A
Stromt
rg
type
DCH34Q
45B
DCH340
46A
Primary
Secondary
Primary
Secondary
Primary
Secondary
Primary
Secondary
30
I8t
340
339
30
1
181
34
1
339
30
1
181
34
1
339
30
1
181
34
1
339
24
0
945
310
220
24
0
945
31
1
220
24
0
945
31
1
220
24
0
945
31
1
220
199
1160
199
1160
1101
1160
101
1160
170
160
170
160
170
60
170
1
60
148
1100
148
1100
148
1100
148
180
143
143
140
140
23
0
906
23
0
906
23
0
906
23
0
906
0
17
2
408
0
17
2
40B
0
17
2
408
0
17
2
408
1201750
rpm
CO
2
1
120
650
rpm
0
100
750rpm
C02
t
1
120
650
rpm
0
position
CO
2
t
1
position
CO
2
t
1
7
2
0
283
7
2
0
283
7
2
0
283
7
2
0
283
23
0
906
23
0
906
23
0
906
23
0
906
1
3
to
1
7
1
3
to
1
7
1
3
to
1
7
1
3
to
1
7
0
051
to
0
067
0
051
to
0
067
0
051
to
0
067
0
051
to
0
067
1
33
to
1
47
1
58
to
1
72
1
33
to
1
47
1
58
to
1
72
0
0524
to
0
0579
0
0622
to
0
0677
0
0524
to
0
0579
0
0622
to
0
0677
1
42
0
056
1
42
0
056
1
42
0
056
1
5
0
059
2
45
0
096
2
45
0
096
2
4
0
096
2
45
0
096
3
7
to
8
9
3
7
to
8
9
3
7
to
B
9
3
7
to
8
9
Center
of
the
ndex
mark
Center
of
the
index
mark
7
38
0
291
7
38
0
291
7
38
0
290
7
38
0
291
1
900
to
2
100
1
650
to
1
850
1
900
to
2
100
1
650
to
1
850
180
to
350
156
to
304
180
to
350
156
to
304
180
to
350
156
to
304
180
to
350
156
to
304
510
to
550
490
to
530
510
to
550
490
to
530
20
1
to
21
7
19
3
to
20
9
20
1
to
21
7
19
3
to
20
9
20
to
40
17
4
to
34
1
20
to
40
11
4
to
34
7
20
to
40
17
4
to
34
7
20
to
40
17
4
to
34
1
EF
35
Page 132 of 537
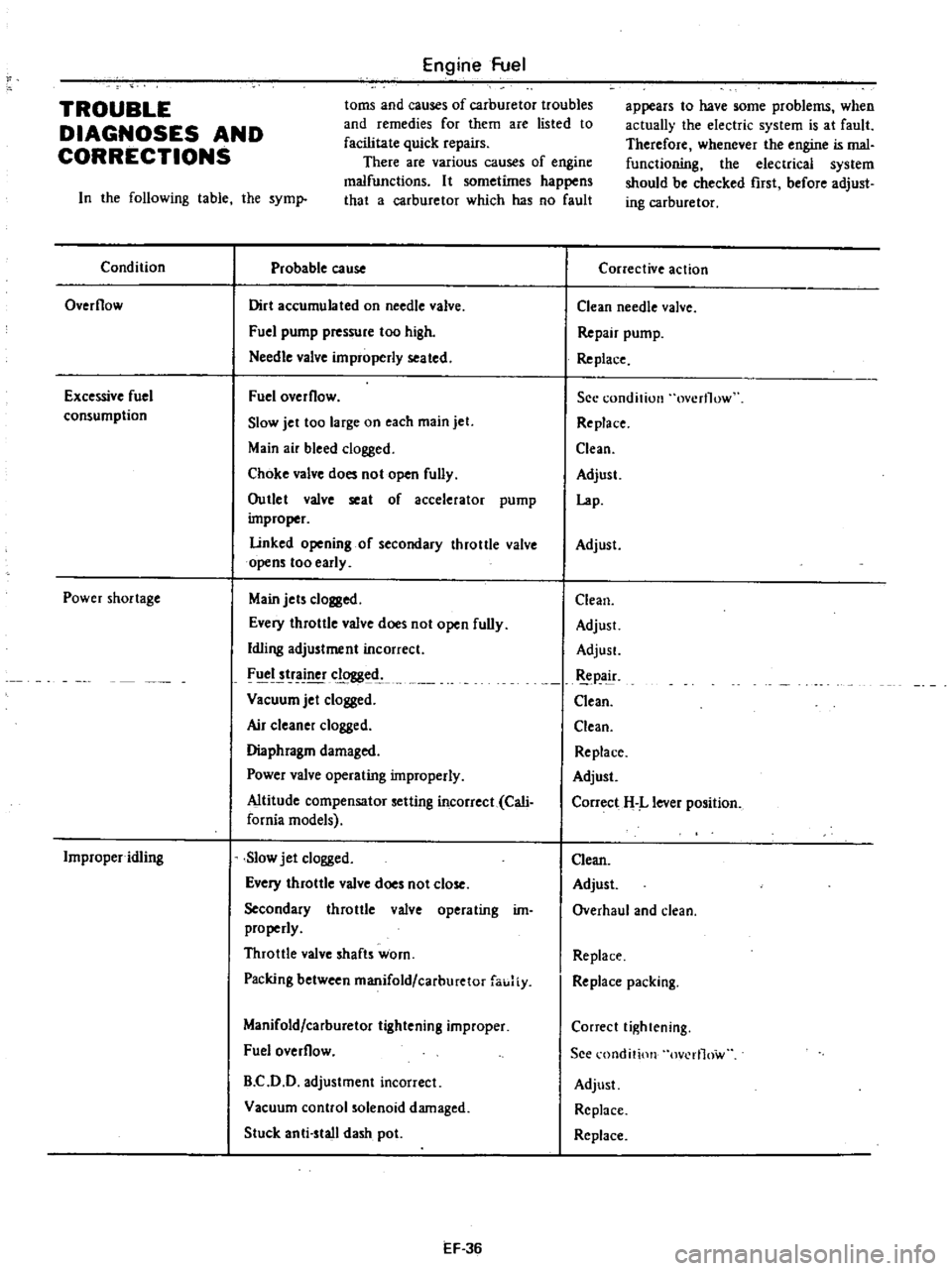
Engine
Fuel
toms
and
causes
of
carburetor
troubles
and
remedies
for
them
are
listed
to
facilitate
quick
repairs
There
are
various
causes
of
engine
malfunctions
It
sometimes
happens
that
a
carburetor
which
has
no
fault
TROUBLE
DIAGNOSES
AND
CORRECTIONS
In
the
following
table
the
syml
Condition
Probable
cause
Overflow
Dirt
accumulated
on
needle
valve
Fuel
pump
pressure
too
high
Needle
valve
improperly
seated
Excessive
fuel
consumption
Fuel
overflow
Slow
jet
too
large
on
each
main
jet
Main
air
bleed
clogged
Choke
valve
does
not
open
fully
Outlet
valve
seat
of
accelerator
pump
improper
Linked
opening
of
secondary
throttle
valve
opens
too
early
Power
shortage
Main
jets
clogged
Every
throttle
valve
does
not
open
fully
Idling
adjustment
incorrect
FIICI
tr
clogged
Vacuum
jet
clogged
Air
c1eane
clogged
Diaphragm
damaged
Power
valve
operating
improperly
Altitude
compensator
setting
incorrect
Cali
fornia
models
Improper
idling
Slow
jet
clogged
Every
throttle
valve
does
not
close
Secondary
throttle
valve
operating
im
properly
Throttle
valve
shafts
worn
Packing
between
manifold
carburetor
fauJiy
Manifold
carburetor
tightening
improper
Fuel
overflow
B
C
D
D
adjustment
incorrect
Vacuum
control
solenoid
damaged
Stuck
anti
stall
dash
pot
EF
36
appears
to
have
some
problems
when
actually
the
electric
system
is
at
fault
Therefore
whenever
the
engine
is
mal
functioning
the
electrical
system
should
be
checked
rust
before
adjust
ing
carburetor
Corrective
action
Clean
needle
valve
Repair
pump
Re
place
See
condition
overflow
Replace
Clean
Adjust
Lap
Adjust
Clean
Adjust
AdjusL
pa
ir
Clean
Clean
Replace
Adjust
Correct
H
L
lever
position
Clean
Adjust
Overhaul
and
clean
Replace
Replace
packing
Correct
tightening
See
l
ondition
ov
rl1ow
Adjust
Replace
Replace
Page 133 of 537

Condition
Engine
hesitation
Engine
does
not
start
Engine
Fuel
Probable
cause
Main
jet
or
slow
jet
clogged
By
pass
hole
idle
passage
dogged
Emulsion
tube
dogged
Idling
adjustment
incorrect
Secondary
throttle
valve
operating
im
properly
Altitude
compensator
setting
incorrect
Cali
fornia
models
Fuel
overflows
No
fuel
Idling
adjustment
incorrect
Fast
idle
adjustment
incorrect
Damaged
anti
dieseling
solenoid
EF
37
Corrective
action
Clean
Clean
tube
Clean
Adjust
Overhaul
and
clean
Correct
H
L
lever
position
See
condition
overflow
Check
pump
fuel
pipe
and
needle
valve
Adjust
Adjust
Replace
Page 139 of 537
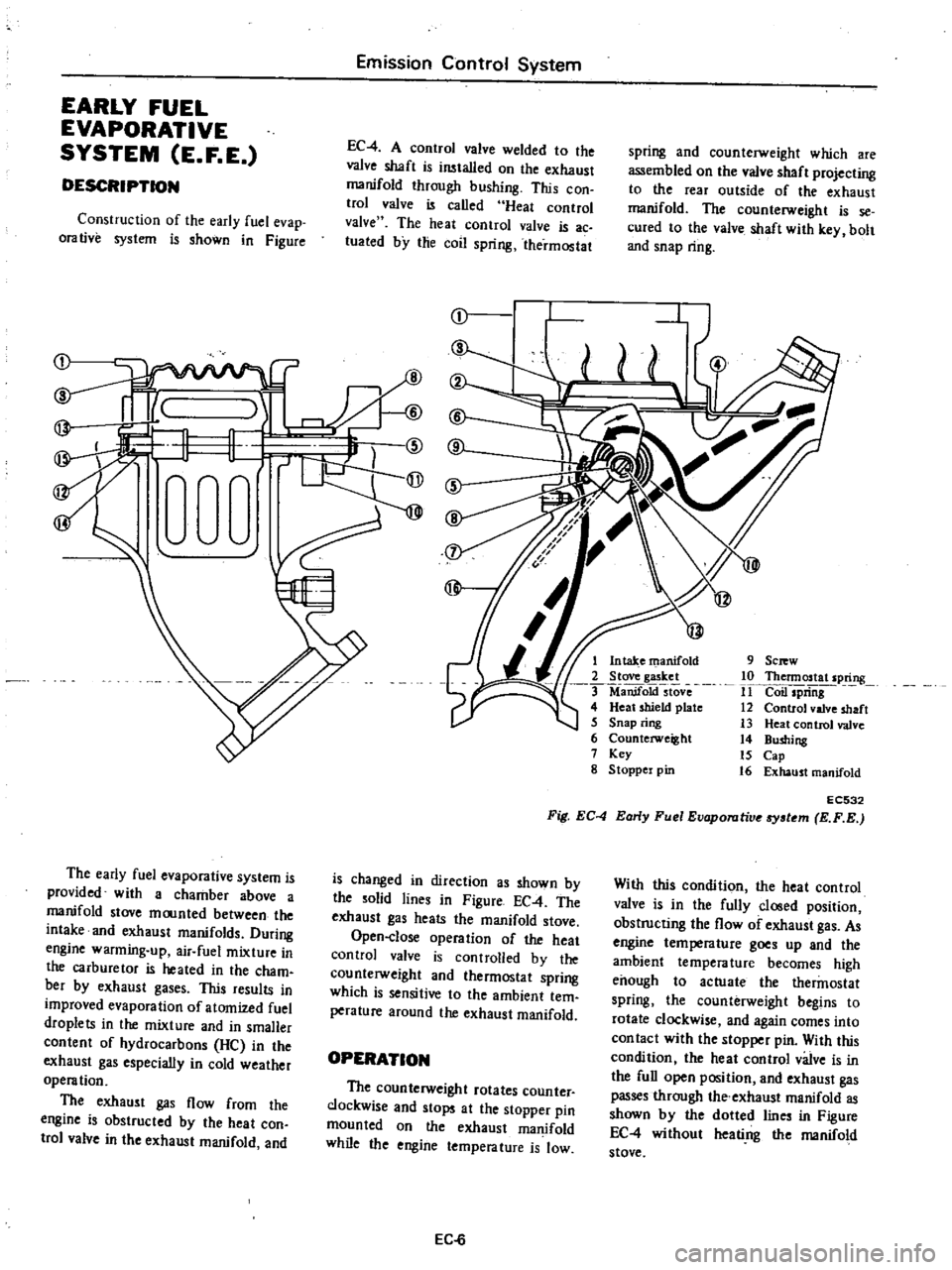
Emission
Control
System
EARLY
FUEL
EVAPORATIVE
SYSTEM
E
F
E
DESCRIPTION
spring
and
counterweight
which
are
assembled
on
the
valve
shaft
projecting
to
the
rear
outside
of
the
exhaust
manifold
The
counterweight
is
se
cured
to
the
valve
shaft
with
key
bolt
and
snap
ring
EC
4
A
control
valve
welded
to
the
valve
shaft
is
wtalled
on
the
exhaust
manifold
through
bushing
This
con
trol
valve
is
called
Heat
control
valve
The
heat
control
valve
is
ac
luated
by
the
coil
spring
thermostat
Construction
of
the
early
fuel
evap
orative
system
is
shown
in
Figure
r
I
1
@
rW
9
Sc
w
10
Thennostat
spring
11
Coil
spriiig
12
Control
valve
shaft
13
Heat
control
valve
14
Bushing
15
Cap
16
Exhaust
manifold
1
Intake
manifold
2
Stove
gasket
ManifoktstOve
4
Heat
shield
plate
5
Snap
ring
6
Counterweight
7
Key
g
Stoppel
pin
EC532
Fig
EC
4
Early
Fuel
Evaporutive
tem
E
F
E
The
early
fuel
evaporative
system
is
provided
with
a
chamber
above
a
manifold
stove
moonted
between
the
intake
and
exhaust
manifolds
During
engine
warming
up
air
fuel
mixture
in
the
carburetor
is
heated
in
the
cham
bet
by
exhaust
gases
This
results
in
improved
evaporation
of
atomized
fuel
droplets
in
the
mixture
and
in
smaller
content
of
hydrocarbons
He
in
the
exhaust
gas
especially
in
cold
weather
operation
The
exhaust
gas
flow
from
the
engine
is
obstructed
by
the
heat
con
trol
valve
in
the
exhaust
manifold
and
is
changed
in
direction
as
shown
by
the
solid
lines
in
Figure
EC
4
The
exhaust
gas
heats
the
manifold
stove
Open
close
operation
of
the
heat
control
valve
is
controlled
by
the
counterweight
and
thermostat
spring
which
is
sensitive
to
the
ambient
tem
perature
around
the
exhaust
manifold
With
this
condition
the
heat
control
valve
is
in
the
fully
closed
position
obstructing
the
flow
of
exhaust
gas
As
engine
tempera
lure
goes
up
and
the
ambient
temperature
becomes
high
enough
to
actuate
the
thermostat
spring
the
counterweight
begins
to
rotate
clockwise
and
again
comes
into
con
tact
with
the
stopper
pin
With
this
condition
the
heat
control
valve
is
in
the
full
open
position
and
exhaust
gas
passes
through
the
exhaust
manifold
as
shown
by
the
dotted
lines
in
Figure
EC
4
without
heati
ng
the
manifold
stove
OPERATION
The
counterweight
rotates
counter
clockwise
and
stops
at
the
stopper
pin
mounted
on
the
exhaust
manifold
while
the
engine
temperature
is
low
EC
6
Page 144 of 537
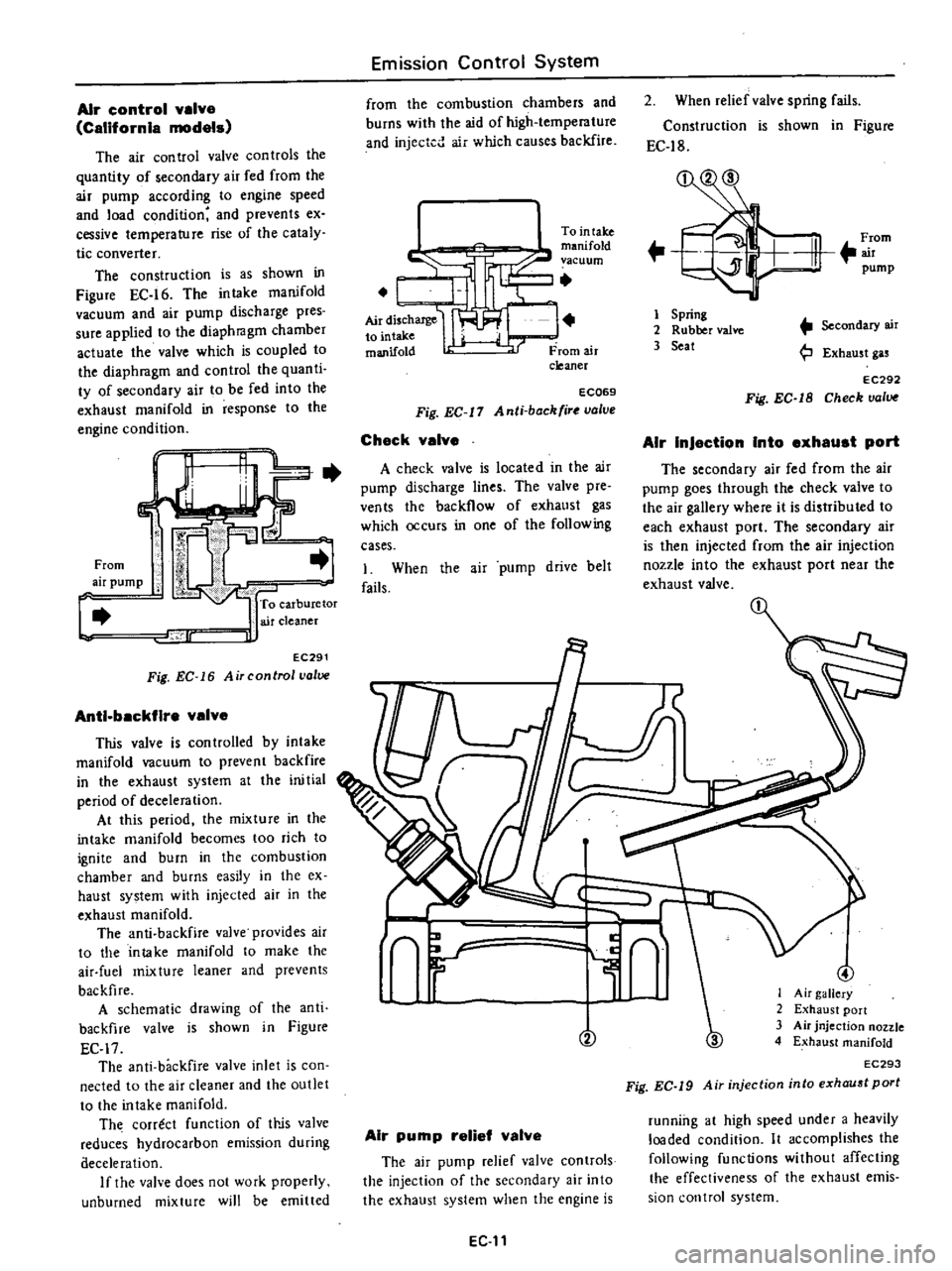
Air
control
valve
CalifornIa
models
The
air
control
valve
con
troIs
the
quantity
of
secondary
air
fed
from
the
air
pump
according
to
engine
speed
and
load
condition
and
prevents
ex
cessive
temperature
rise
of
the
cataly
tic
converter
The
construction
is
as
shown
in
Figure
EC
16
The
intake
manifold
vacuum
and
air
pump
discharge
pres
sure
applied
to
the
diaphragm
chamber
actuate
the
valve
which
is
coupled
to
the
diaphragm
and
control
the
quanti
ty
of
secondary
air
to
be
fed
into
the
exhaust
manifold
in
response
to
the
engine
condition
c
From
air
pump
To
carburetor
air
cleaner
lr
J
EC291
Fig
EC
16
Air
control
valve
Anti
backfire
valve
This
valve
is
con
trolled
by
intake
manifold
vacuum
to
prevent
backfire
in
the
exhaust
system
at
the
ini
tial
period
of
deceleration
At
this
period
the
mixture
in
the
intake
manifold
becomes
too
rich
to
ignite
and
burn
in
the
combustion
chamber
and
burns
easily
in
the
ex
haust
system
with
injected
air
in
the
exhaust
manifold
The
anti
backfire
valve
provides
air
to
the
intake
manifold
to
make
the
air
fuel
mixture
leaner
and
prevents
backfire
A
schematic
drawing
of
the
anti
backfire
valve
is
shown
in
Figure
EC
17
The
anti
backfire
valve
inlet
is
con
nected
to
the
air
cleaner
and
the
outlet
to
the
intake
manifold
Th
correct
function
of
It
jS
valve
reduces
hydrocarbon
emission
during
aeceleration
If
the
valve
does
not
work
properly
unburned
mixture
will
be
emitted
Emission
Control
System
from
the
combustion
chambers
and
burns
with
the
aid
of
high
temperature
and
injected
air
which
causes
backfire
I
Tointake
c
manifold
vacuum
I
L
AirdisChaJ1le
I
to
mtake
manifold
From
air
cleaner
ECQ69
Fig
EC
11
Anti
back
ir
valve
Check
valve
A
check
valve
is
located
in
the
air
pump
discharge
lines
The
valve
pre
ven
ts
the
backflow
of
exhaust
gas
which
occurs
in
one
of
the
following
cases
1
When
the
air
pump
drive
belt
fails
2
When
relief
valve
spring
fails
Construction
is
shown
in
Figure
EC
18
F
rom
m
pump
1
Spring
2
Rubber
valve
3
Seat
Secondary
air
Exhaust
gas
EC292
Fig
EC
1B
Check
valve
AIr
InJaction
Into
axhaust
port
The
secondary
air
fed
from
the
air
pump
goes
through
the
check
valve
to
the
air
gallery
where
it
is
distributed
to
each
exhaust
port
The
secondary
air
is
then
injected
from
the
air
injection
nozzle
into
the
exhaust
port
near
the
exhaust
valve
n
L
y
r
V
Air
pump
relief
valve
The
air
pump
relief
valve
controls
the
injection
of
the
secondary
air
into
the
exhaust
system
when
the
engine
is
EG
11
3
I
Air
gallery
2
Exhaust
port
3
Air
jnjection
nozzle
4
Exhaust
manifold
EC293
Fig
EC
19
Air
injection
into
exhaust
port
running
at
high
speed
under
a
heavily
loaded
condition
It
accomplishes
the
following
functions
without
affecting
the
effectiveness
of
the
exhaust
emis
sion
control
system
Page 145 of 537
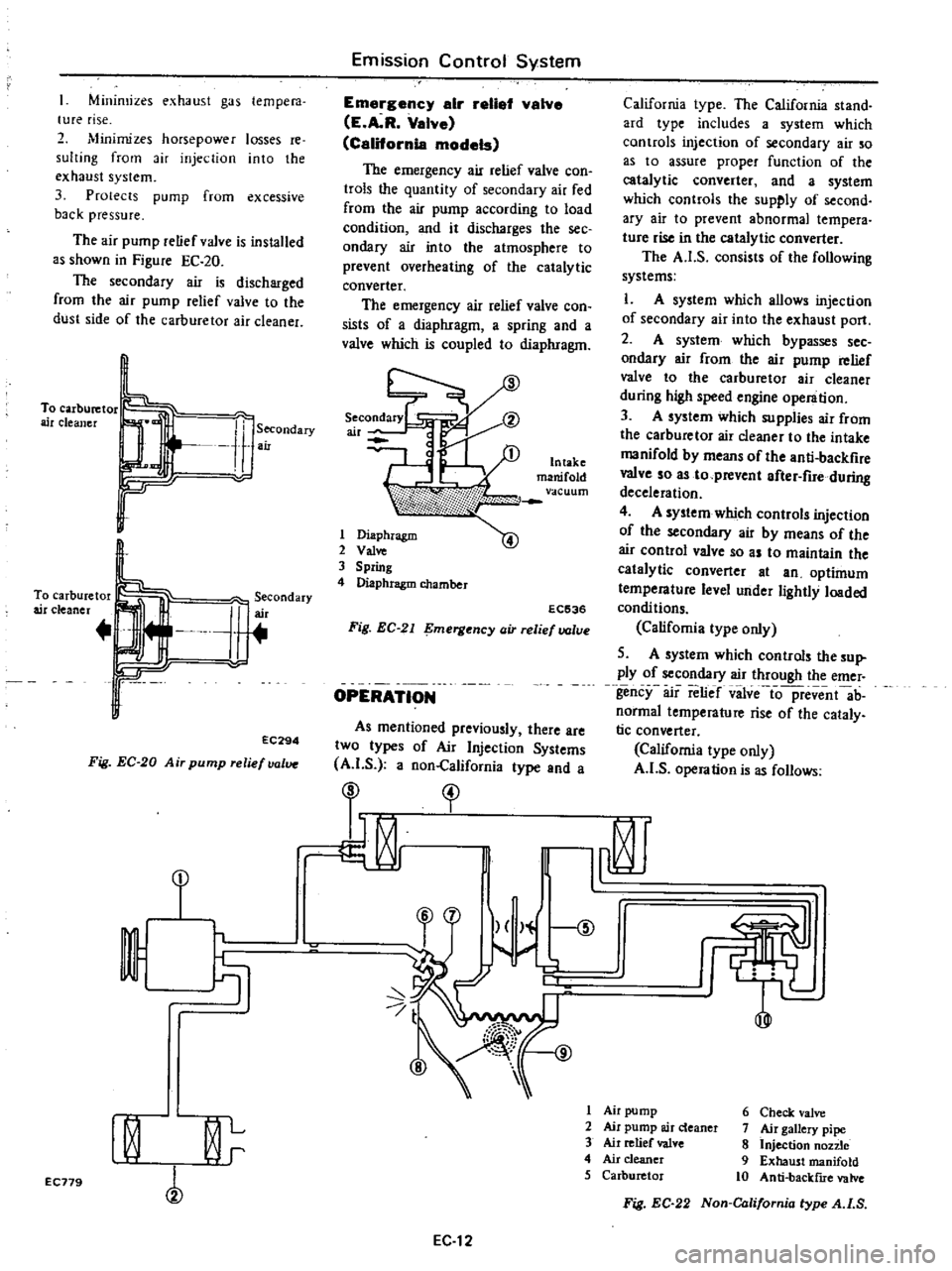
Minimizes
exhaust
gas
tempera
lure
rise
2
Minimizes
horsepower
losses
re
suiting
from
air
injection
into
the
exhaust
system
3
Protects
pump
from
excessive
back
pressure
The
air
pump
relief
valve
is
installed
as
shown
in
Figure
EC
20
The
secondary
air
is
discharged
from
the
air
pump
relief
valve
to
the
dust
side
of
the
carburetor
air
cleaner
To
carburetor
air
cleaner
Secondary
air
To
carburetor
air
cleaner
J
erCOndary
r
r
EC294
Fig
EC
20
Air
pump
relief
valve
Emission
Control
System
Emargency
air
retial
valve
E
A
R
Valve
California
models
The
emergency
air
relief
valve
con
trols
the
quantity
of
secondary
air
fed
from
the
air
pump
according
to
load
condition
and
it
discharges
the
see
ondary
air
into
the
atmosphere
to
prevent
overheating
of
the
catalytic
converter
The
emergency
air
relief
valve
con
sists
of
a
diaphragm
a
spring
and
a
valve
which
is
coupled
to
diaphragm
1
Diaphragm
2
Val
3
Spring
4
Diaphragm
chamber
EC536
Fig
EC
21
mergency
air
relief
valve
OPERATION
As
mentioned
previously
there
are
two
types
of
Air
Injection
Systems
A
I
S
a
non
California
type
and
a
California
type
The
California
stand
ard
type
includes
a
system
which
controls
injection
of
secondary
air
so
as
to
assure
proper
function
of
the
catalytic
converter
and
a
system
which
controls
the
supply
of
second
ary
air
to
prevent
abnormal
tempera
tUfe
rise
in
the
catalytic
converter
The
A
I
S
consists
of
the
following
systems
L
A
system
which
allows
injection
of
secondary
air
into
the
exhaust
port
2
A
system
which
bypasses
sec
ondary
air
from
the
air
pump
relief
valve
to
the
carburetor
air
cleaner
during
high
speed
engine
operation
3
A
system
which
supplies
air
from
the
carburetor
air
cleaner
to
the
intake
manifold
by
means
of
the
anti
backfire
valve
so
as
to
prevent
after
fire
during
deceleration
4
A
system
which
controls
injection
of
the
secondary
air
by
means
of
the
air
control
valve
so
as
to
maintain
the
catalytic
converter
at
an
optimum
temperature
level
under
lightly
loaded
condi
tions
Califomia
type
only
5
A
system
which
controls
the
sup
ply
of
secondary
air
through
the
emer
gency
air
relief
vilve
io
pfevent
ab
normal
temperature
rise
of
the
cataly
tic
converter
California
type
only
A
I
S
operation
is
as
follows
I
I
t
1
r
9
I
Air
pump
6
Check
valve
I
0
L
2
Air
pump
air
deaner
7
Air
gallery
pipe
3
Air
relief
valve
8
Injection
non
e
r
4
Air
cleaner
9
Exhaust
manifold
5
Carburetor
10
Anti
backflIe
valve
EC179
Fig
EC
22
Non
California
type
A
I
S
EC
12
Page 146 of 537
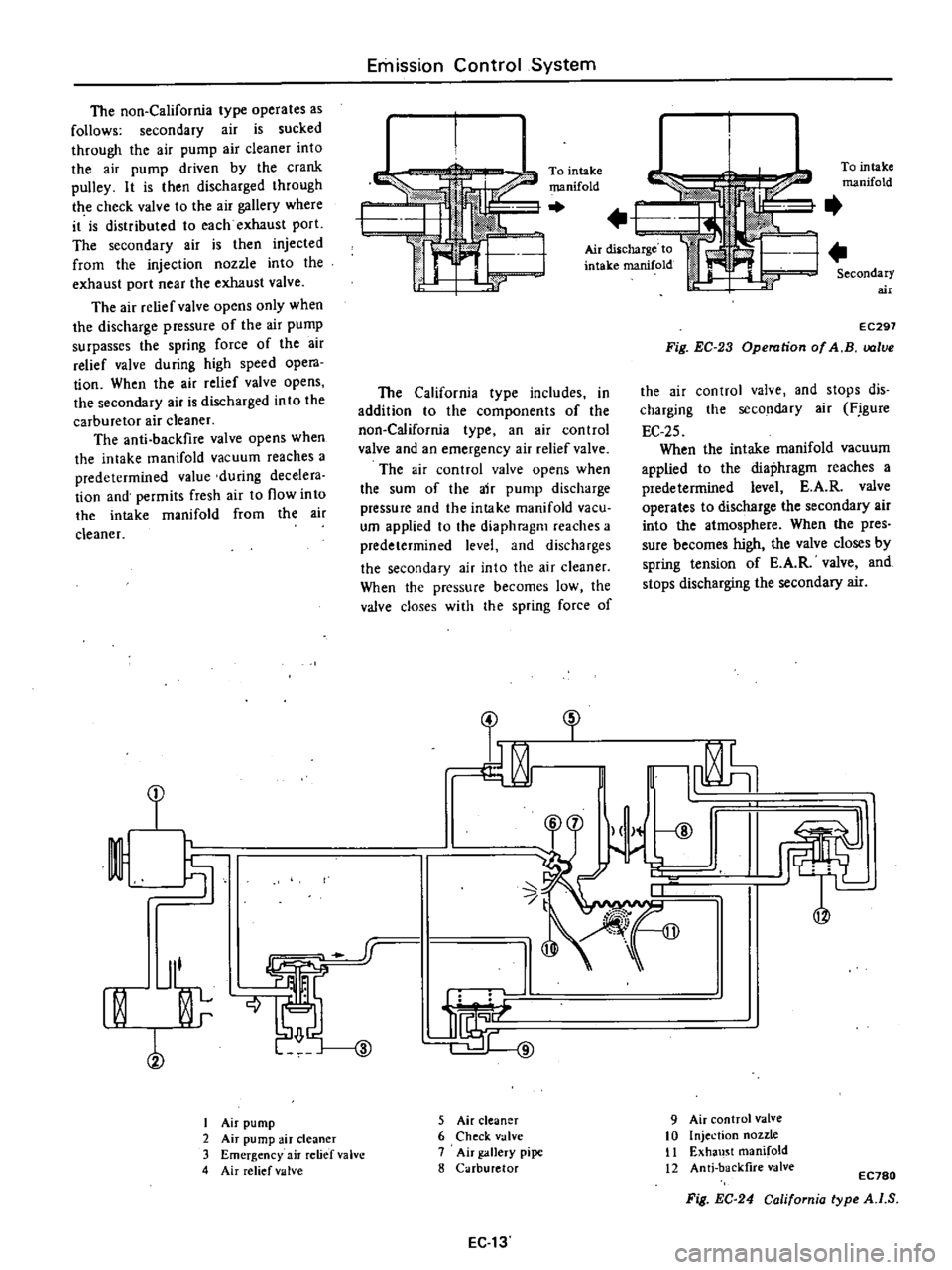
The
non
California
type
operates
as
follows
secondary
air
is
sucked
through
the
air
pump
air
cleaner
into
the
air
pump
driven
by
the
crank
pulley
It
is
then
discharged
through
the
check
valve
to
the
air
gallety
where
it
is
distributed
to
each
exhaust
porL
The
secondary
air
is
then
injected
from
the
injection
nozzle
into
the
exhaust
port
near
the
exhaust
valve
The
air
relief
valve
opens
only
when
the
discharge
pressure
of
the
air
pump
surpasses
the
spring
force
of
the
air
relief
valve
during
high
speed
opera
tion
When
the
air
relief
valve
opens
the
secondary
air
is
discharged
in
to
the
carburetor
air
c1eaner
The
anti
backfire
valve
opens
when
the
intake
manifold
vacuum
reaches
a
predetermined
value
during
decelera
tion
and
permits
fresh
air
to
now
into
the
intake
manifold
from
the
air
cleaner
f
I
Jl
rn
l
I
Air
pump
2
Air
pump
air
cleaner
3
Emergency
air
relief
valve
4
Air
relief
valve
riu
Qj
j
I
@
Emission
Control
System
To
intake
manifold
The
California
type
includes
in
addition
to
the
components
of
the
non
California
type
an
air
control
valve
and
an
emergency
air
relief
valve
The
air
control
valve
opens
when
the
sum
of
the
air
pump
discharge
pressure
and
the
intake
manifold
vacu
um
applied
to
the
diaphmgm
reaches
a
predetermined
level
and
discharges
the
secondary
air
into
the
air
cleaner
When
the
pressure
becomes
low
the
valve
doses
with
the
spring
force
of
3
5
Air
cleaner
6
Check
valve
7
Air
gallery
pipe
8
Carburetor
EC
13
To
intake
manifold
Air
diSlcharge
to
intake
manifold
Secondary
air
EC297
Fig
EC
23
Operation
of
A
B
lve
the
air
control
valve
and
stops
dis
charging
the
secondary
air
F
igure
EC
25
When
the
intake
manifold
vacuum
applied
to
the
diaphragm
reaches
a
predetermined
level
E
A
R
valve
operates
to
discharge
the
secondary
air
into
the
atmosphere
When
the
pres
sure
becomes
high
the
valve
closes
by
spring
tension
of
E
A
R
valve
and
stops
discharging
the
secondary
air
fl
t
9
Air
control
valve
10
Injection
nozzle
II
Exha
l
t
manifold
12
Anti
backfire
valve
EC780
Fig
EC
24
California
type
A
I
S
Page 155 of 537
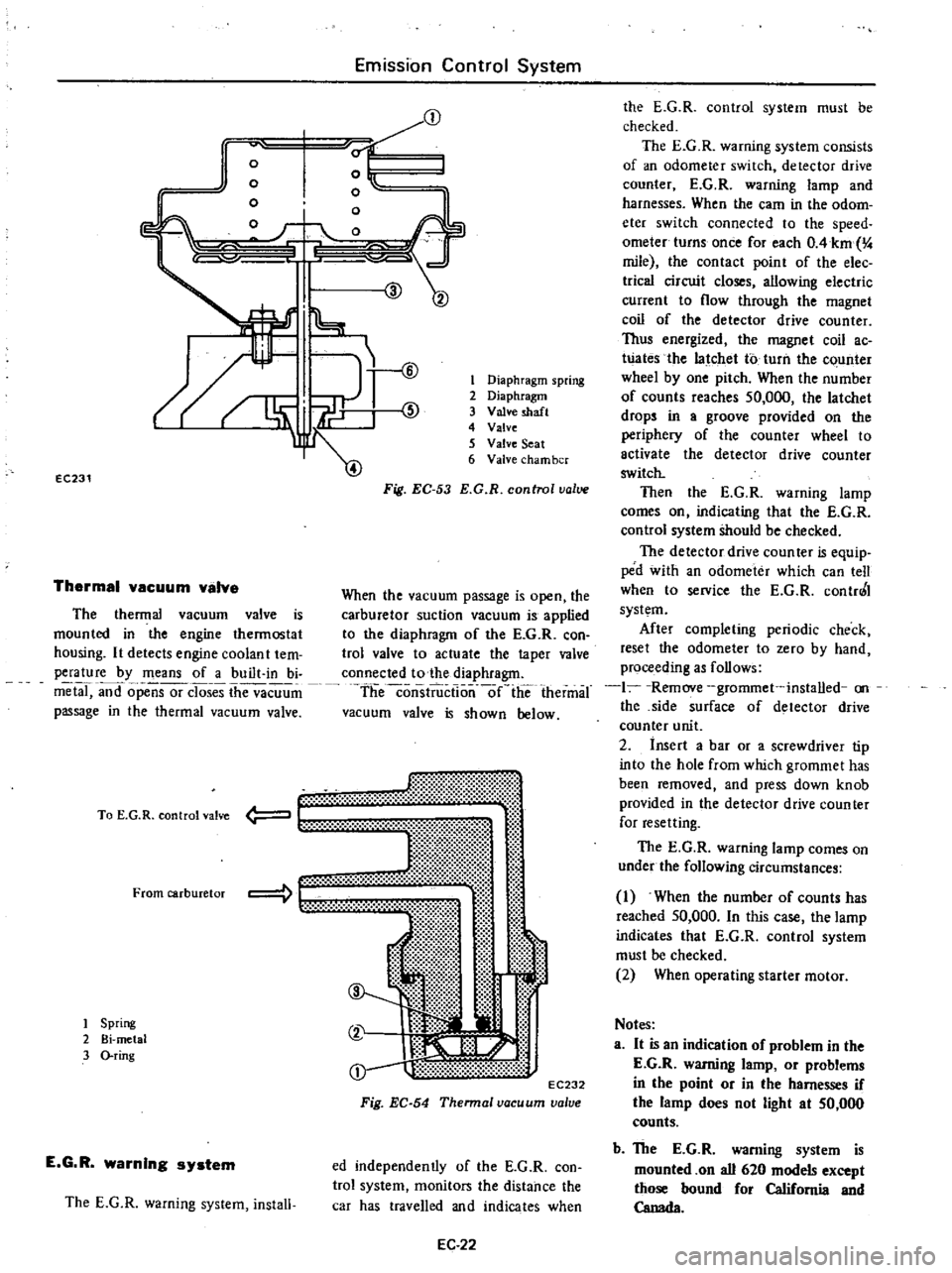
j
EC231
Thermal
vacuum
valva
o
o
m
Emission
Control
System
0
o
o
o
l
l
@
The
thermal
vacuum
valve
is
mounted
in
the
engine
thermostat
housing
It
detects
engine
coolan
t
tem
perature
by
means
of
a
built
in
bi
metal
and
opensor
closes
the
vacuum
passage
in
the
thermal
vacuum
valve
mt
li
t
00
t
EC232
Fig
EC
54
Thennal
vacuum
valve
To
E
G
R
control
valve
From
carburetor
1
Spring
2
Bi
metal
3
O
ring
E
G
R
warning
system
The
E
G
R
warning
system
install
1
Diaphragm
spring
2
Diaphragm
3
Valve
shaft
4
Valve
5
Valve
Seat
6
Valve
cham
ber
Fig
EC
53
E
G
R
control
value
When
the
vacuum
passage
is
open
the
carburetor
suction
vacuum
is
applied
to
the
diaphragm
of
the
E
G
R
con
trol
valve
to
actuate
the
taper
valve
connected
to
the
diaphragm
theconsiiiictlo
nlie
thermal
vacuum
valve
is
shown
below
ed
independently
of
the
E
G
R
con
trol
system
monitors
the
distance
the
car
has
travelled
and
indicates
when
EC
22
the
E
G
R
control
system
must
be
checked
The
E
G
R
warning
system
consists
of
an
odometer
switch
detector
drive
counter
E
G
R
warning
lamp
and
harnesses
When
the
earn
in
the
odom
eter
switch
connected
to
the
speed
ometer
turns
once
for
each
OAkm
4
mile
the
contact
point
of
the
elec
trica
circuit
closes
allowing
electric
current
to
flow
through
the
magnet
coil
of
the
detector
drive
counter
Thus
energized
the
magnet
coil
ac
Wates
the
latchet
to
turn
the
c
unter
wheel
by
one
pitch
When
the
number
of
counts
reaches
50
000
the
latchet
drops
in
a
groove
provided
on
the
periphery
of
the
counter
wheel
to
activate
the
detector
drive
counter
switch
Then
the
E
G
R
warning
lamp
comes
on
indicating
that
the
E
G
R
control
system
Should
be
checked
The
detector
drive
coun
teT
is
equip
ped
with
an
odometer
which
can
tell
when
to
service
the
E
G
R
contr0
I
system
After
completing
periodic
check
reset
the
odometer
to
zero
by
hand
proceeding
as
follows
1
Remove
grommet
installed
on
the
side
surface
of
detector
drive
counter
unit
2
insert
a
bar
or
a
screwdriver
tip
into
the
hole
from
which
grommet
has
been
removed
and
press
down
knob
provided
in
the
detector
drive
counter
for
resetting
The
E
G
R
warning
lamp
comes
on
under
the
following
circumstances
1
When
the
number
of
counts
has
reached
50
000
In
this
case
the
lamp
indicates
that
E
G
R
control
system
must
be
checked
2
When
operating
starter
motor
Notes
a
It
is
an
indication
of
problem
in
the
E
G
R
warning
lamp
or
problems
in
the
point
or
in
the
harnesses
if
the
lamp
does
not
light
at
50
000
counts
b
The
E
G
R
warning
system
is
mounted
on
all
620
models
except
those
bound
for
California
and
Canada
Page 158 of 537
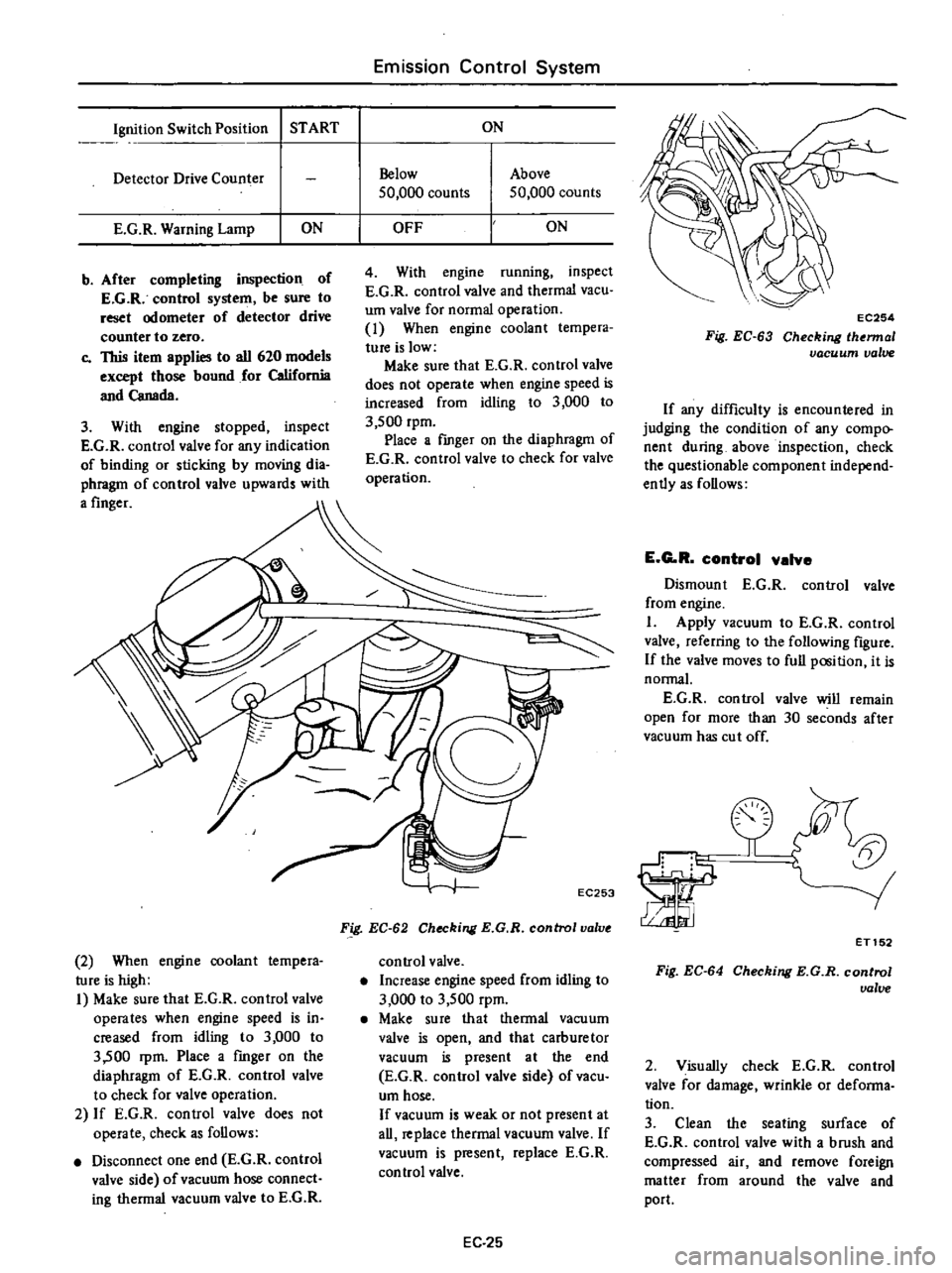
Ignition
Switch
Position
START
Detector
Drive
Counter
E
G
R
Warning
Lamp
ON
b
After
completing
inspection
of
E
G
R
control
system
be
sure
to
reset
odometer
of
detector
drive
counter
to
zero
c
This
item
applies
to
all
620
models
except
those
bound
for
California
and
Canada
3
With
engine
stopped
inspect
E
G
R
control
valve
for
any
indication
of
binding
or
sticking
by
moving
dia
phragm
of
control
valve
upwards
with
a
finger
2
When
engine
coolant
tempera
ture
is
high
I
Make
sure
that
E
G
R
control
valve
operates
when
engine
speed
is
in
creased
from
idling
to
3
000
to
3
500
rpm
Place
a
fmger
on
the
diaphragm
of
E
G
R
control
valve
to
check
for
valve
operation
2
If
E
G
R
control
valve
does
not
operate
check
as
follows
Disconnect
one
end
E
G
R
control
valve
side
of
vacuum
hose
connect
ing
thermal
vacuum
valve
to
E
G
R
Emission
Control
System
ON
Below
50
000
counts
Above
50
000
counts
OFF
ON
4
With
engine
running
inspect
E
G
R
control
valve
and
thermal
vacuo
um
valve
for
normal
operation
1
When
engine
coolant
tempera
ture
is
low
Make
sure
that
E
G
R
control
valve
does
not
operate
when
engine
speed
is
increased
from
idling
to
3
000
to
3
500
rpm
Place
a
fmger
on
the
diaphragm
of
E
G
R
control
valve
to
check
for
valve
operation
EC253
Fig
EC
62
Checking
E
G
R
control
valve
control
valve
Increase
engine
speed
from
idling
to
3
000
to
3
500
rpm
Make
su
re
that
thermal
vacu
um
valve
is
open
and
that
carburetor
vacuum
is
present
at
the
end
E
G
R
control
valve
side
of
vacu
um
hose
If
vacuum
is
weak
or
not
present
at
all
replace
thermal
vacuum
valve
If
vacuum
is
present
replace
E
G
R
control
valve
EC
25
EC254
Fig
EC
63
Checking
lhermal
vacuum
valve
If
any
difficulty
is
encountered
in
judging
the
condition
of
any
compo
nent
during
above
inspection
check
the
questionable
component
independ
ently
as
follows
E
G
R
control
valve
Dismount
E
G
R
control
valve
from
engine
I
Apply
vacuum
to
E
G
R
control
valve
referring
to
the
following
figure
If
the
valve
moves
to
full
position
it
is
normal
E
G
R
control
valve
will
remain
open
for
more
than
30
seconds
after
vacuum
has
cut
off
la
ET152
Fig
EC
64
Checking
E
G
R
control
ualue
2
Visually
check
E
G
R
control
valve
for
damage
wrinkle
or
defonna
tion
3
Clean
the
seating
surface
of
E
G
R
control
valve
with
a
brush
and
compressed
air
and
remove
foreign
matter
from
around
the
valve
and
port