ECO mode DATSUN PICK-UP 1977 Owner's Guide
[x] Cancel search | Manufacturer: DATSUN, Model Year: 1977, Model line: PICK-UP, Model: DATSUN PICK-UP 1977Pages: 537, PDF Size: 35.48 MB
Page 307 of 537
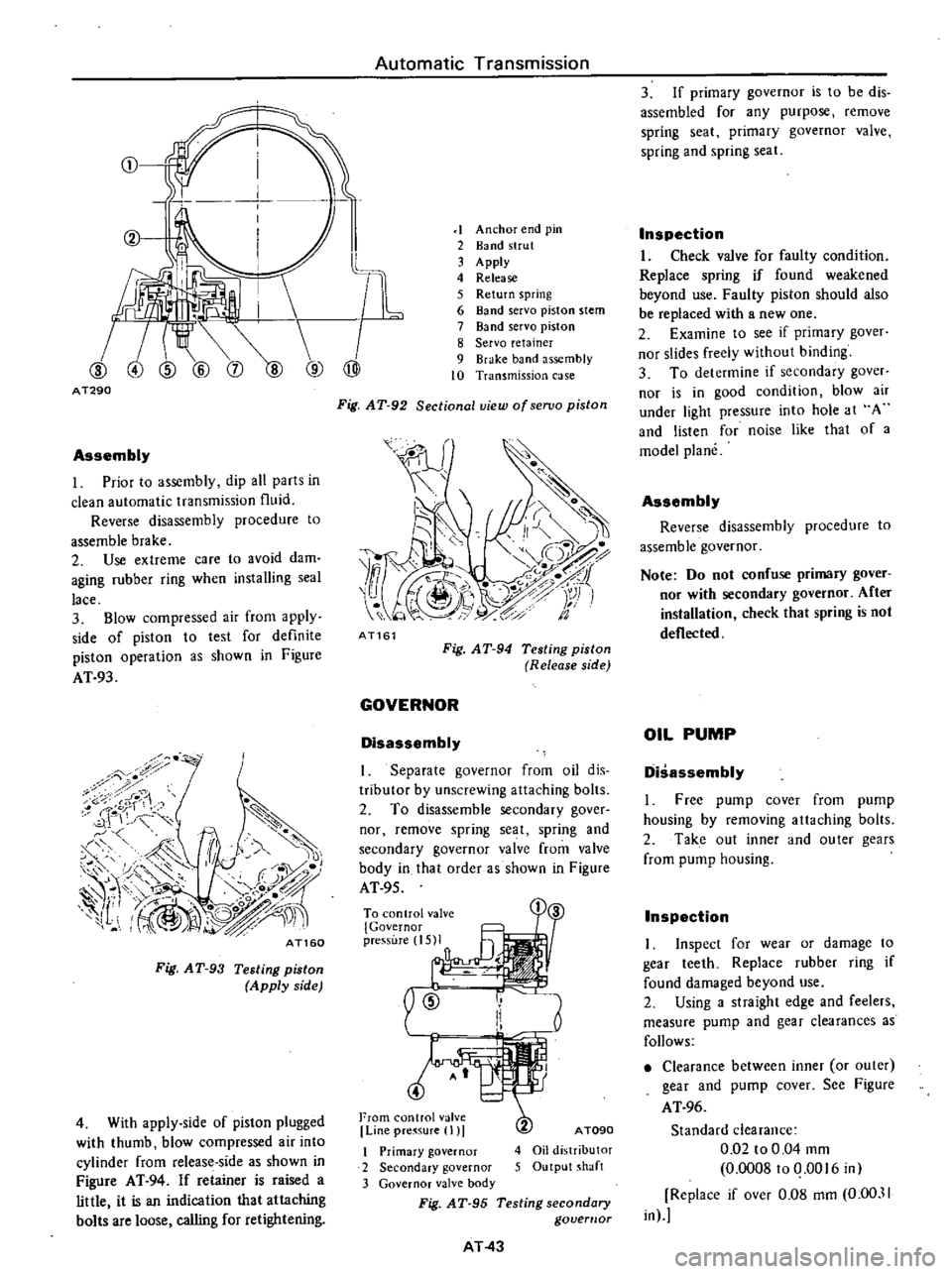
Automatic
Transmission
i
r
11
I
@
@
j
A
T290
Assembly
I
Prior
to
assembly
dip
all
parts
in
clean
automatic
transmission
fluid
Reverse
disassembly
procedure
to
assemble
brake
2
Use
extreme
care
to
avoid
dam
aging
rubber
ring
when
installing
seal
lace
3
Blow
compressed
air
from
apply
side
of
piston
to
test
for
definite
piston
operation
as
shown
in
Figure
AT
93
7
i
8
ror
1
1
r
c
f
f
A
J
II
1
0
c
r
1
1
I
@
L
O
j
0
n
iJ
fl
IV
I
AT160
Fig
AT
93
Testing
piston
Apply
side
4
With
apply
side
of
piston
plugged
with
thumb
blow
compressed
air
into
cylinder
from
release
side
as
shown
in
Figure
AT
94
If
retainer
is
raised
a
little
it
is
an
indication
that
attaching
bolts
are
loose
calling
for
retightening
1
Anchor
end
pin
2
Band
strut
3
Apply
4
Release
5
Return
spring
6
Band
servo
piston
stem
7
Band
servo
piston
8
Servo
retainer
9
Brake
band
assembly
10
Transmission
case
Fig
AT
92
Sectional
view
ofseruo
piston
7
o
i
J
1S
I
z
1
Y
i
1
t
9
c
fa
AT161
Fig
AT
94
Testing
piston
Release
side
GOVERNOR
Disassembly
I
Separate
governor
from
oil
dis
tributor
by
unscrewing
attaching
bolts
2
To
disassemble
secondary
gover
nor
remove
spring
seat
spring
and
secondary
governor
valve
from
valve
body
in
that
order
as
shown
in
Figure
AT
95
To
control
val
i
1
3
5MI
n
ID
r
Ii
I
4
From
control
valve
Line
pre
sure
I
I
A
TOgO
4
Oil
distributor
5
Output
shaft
I
Primary
governor
2
Secondary
governor
3
Governor
valve
body
Fig
AT
95
Testing
secondary
govemor
AT
43
3
If
primary
governor
is
to
be
dis
assembled
for
any
purpose
remove
spring
seat
primary
governor
valve
spring
and
spring
seat
Inspection
I
Check
valve
for
faulty
condition
Replace
spring
if
found
weakened
beyond
use
Faulty
piston
should
also
be
replaced
with
a
new
one
2
Examine
to
see
if
primary
gover
nor
slides
freely
without
binding
3
To
determine
if
secondary
gaver
nor
is
in
good
condition
blow
air
under
light
pressure
into
hole
at
A
and
listen
for
noise
like
that
of
a
model
plane
Assembly
Reverse
disassembly
procedure
to
assemble
governor
Note
Do
not
confuse
primary
gover
nor
with
secondary
governor
After
installation
check
that
spring
is
not
deflected
OIL
PUMP
Disassembly
I
Free
pump
cover
from
pump
housing
by
removing
attaching
bolts
2
Take
out
inner
and
outer
gears
from
pump
housing
Inspection
I
Inspect
for
wear
or
damage
to
gear
teeth
Replace
rubber
ring
if
found
damaged
beyond
use
2
Using
a
straight
edge
and
feelers
measure
pump
and
gear
clearances
as
follows
Clearance
between
inner
or
outer
gear
and
pump
cover
See
Figure
AT
96
Standard
clearance
0
02
to
0
04
mm
0
0008100
0016
in
Replace
if
over
0
08
mm
0
00
11
in
Page 373 of 537
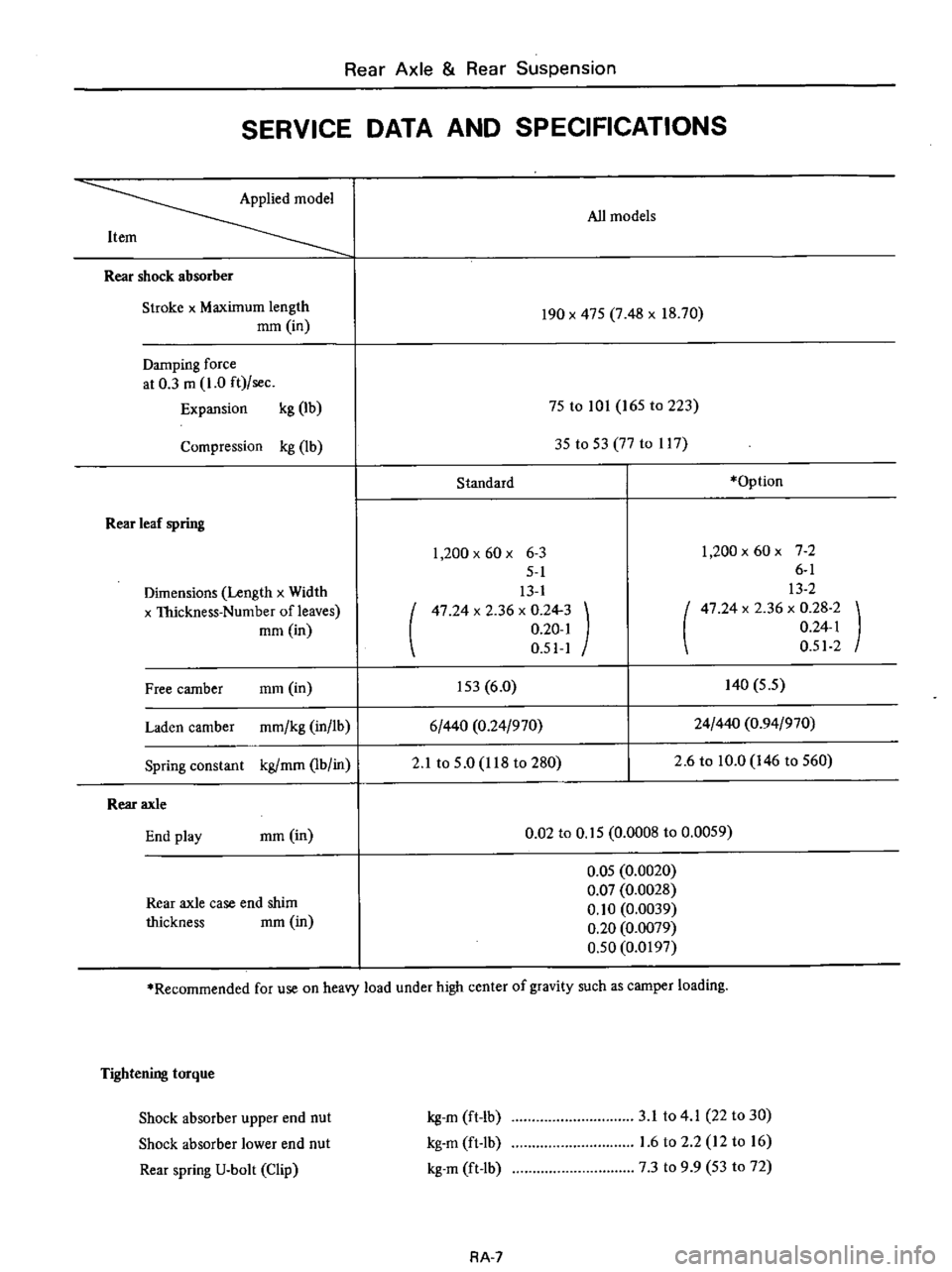
Rear
Axle
Rear
Suspension
SERVICE
DATA
AND
SPECIFICATIONS
Applied
model
All
models
Item
Rear
shock
absorber
Stroke
x
Maximum
length
mOl
in
190
x
47S
7
48
x
18
70
Damping
force
at
0
3
m
1
0
ft
sec
Expansion
kg
lb
75
to
101
165
to
223
Compression
kg
lb
3S
to
S3
77
to
1l7
Standard
Option
Rear
leaf
spring
Dimensions
Length
x
Width
x
Thickness
Number
of
leaves
mOl
in
1
200
x
60
x
6
3
5
1
13
1
47
24
x
2
36
x
0
24
3
0
20
1
0
51
1
1
200x60x
72
6
1
13
2
47
24
x
2
36
x
0
28
2
0
24
1
0
512
Free
camber
mOl
in
IS3
6
0
140
S
5
Laden
camber
mmlkg
in
lb
6
440
0
24
970
24
440
0
94
970
Spring
constant
kg
mOl
lb
in
2
1
to
S
O
118
to
280
2
6
to
10
0
146
to
S60
Rear
axle
End
play
mOl
in
0
02
to
O
IS
0
0008
to
0
0059
Rear
axle
case
end
shim
thickness
mm
in
O
OS
0
0020
0
07
0
0028
0
10
0
0039
0
20
0
0079
0
50
0
0197
Recommended
for
use
on
heavy
load
under
high
center
of
gravity
such
as
camper
loading
Tightening
torque
Shock
absorber
upper
end
nut
Shock
absorber
lower
end
nut
Rear
spring
U
bolt
Clip
kg
m
ft
lb
kg
m
ft
Ib
kg
m
ft
lb
3
1
to
4
1
22
to
30
1
6
to
2
2
12
to
16
7
3
to
9
9
53
to
72
RA
7
Page 377 of 537
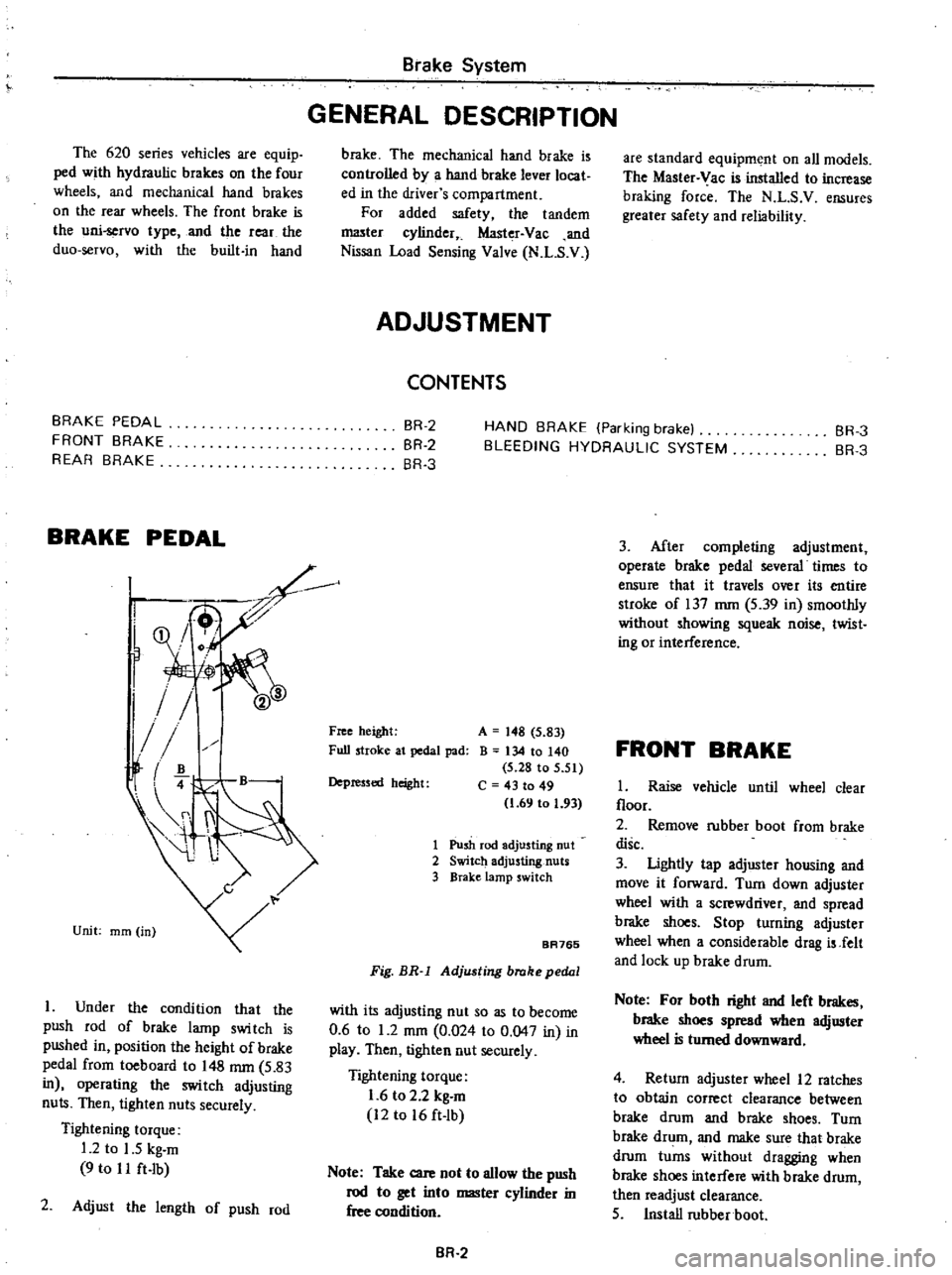
The
620
series
vehicles
are
equip
ped
with
hydraulic
brakes
on
the
four
wheels
and
mechanical
hand
brakes
on
the
rear
wheels
The
front
brake
is
the
uni
servo
type
and
the
rear
the
duo
servo
with
the
built
in
hand
BRAKE
PEDAL
FRONT
BRAKE
REAR
BRAKE
BRAKE
PEDAL
Qi
f
l
II
t
Unit
mm
in
I
Under
the
condition
that
the
push
rod
of
brake
lamp
swi
tch
is
pushed
in
position
the
height
of
brake
pedal
from
toeboard
to
148
mm
5
83
in
operating
the
switch
adjusting
nuts
Then
tighten
nuts
securely
Tightening
torque
1
2
to
1
5
kg
m
9
to
I
I
ft
Ib
2
Adjust
the
length
of
push
rod
Brake
System
GENERAL
DESCRIPTION
brake
The
mechanical
hand
brake
is
controlled
by
a
hand
brake
lever
locat
ed
in
the
driver
s
compartment
For
added
safety
the
tandem
I
1lI3ter
cylinder
Master
Vac
and
Nissan
Load
Sensing
Valve
N
L
S
V
ADJUSTMENT
CONTENTS
are
standard
equipment
on
all
models
The
Master
Vac
is
installed
to
increase
braking
force
The
N
L
S
V
ensures
greater
safety
and
reliability
BR
2
BR
2
BR
3
HAND
BRAKE
Parking
brake
BLEEDING
HYDRAULIC
SYSTEM
BR
3
BR
3
Free
height
Full
stroke
at
pedal
pad
A
148
5
83
B
134
10
140
5
28
to
5
51
C
43
to
49
1
69
to
1
93
Depressed
height
1
Push
rod
adjusting
nut
2
Switch
adjusting
nuts
3
BraKe
lamp
switch
BA765
Fig
BR
l
Adjusting
brake
pedal
with
its
adjusting
nut
so
as
to
become
0
6
to
1
2
mOl
0
024
to
0
047
in
in
play
Then
tigh1en
nut
securely
Tightening
torque
1
6
to
2
2
kg
m
12
to
16
ft
lb
Note
Take
care
not
to
allow
the
push
rod
to
get
into
master
cylinder
in
free
condition
BR
2
3
After
completing
adjustment
operate
brake
pedal
several
times
to
ensure
that
it
travels
over
its
entire
stroke
of
137
mm
5
39
in
smoothly
without
showing
squeak
noise
twist
ing
or
interference
FRONT
BRAKE
1
Raise
vehicle
until
wheel
clear
floor
2
Remove
rubber
boot
from
brake
disc
3
Ughtly
tap
adjuster
housing
and
move
it
forward
Turn
down
adjuster
wheel
with
a
screwdriver
and
spread
brake
shoes
Stop
turning
adjuster
wheel
when
a
considerable
drag
is
Jelt
and
lock
up
brake
drum
Note
For
both
right
and
left
brakes
brake
shoes
spread
when
adjuster
wheel
is
turned
downward
4
Return
adjuster
wheel
12
ratches
to
obtain
correct
clearance
between
brake
drum
and
brake
shoes
Turn
brake
drum
and
make
sure
that
brake
drum
turns
without
dragging
when
brake
shoes
interfere
with
brake
drum
then
readjust
clearance
5
Install
rubber
boot
Page 380 of 537
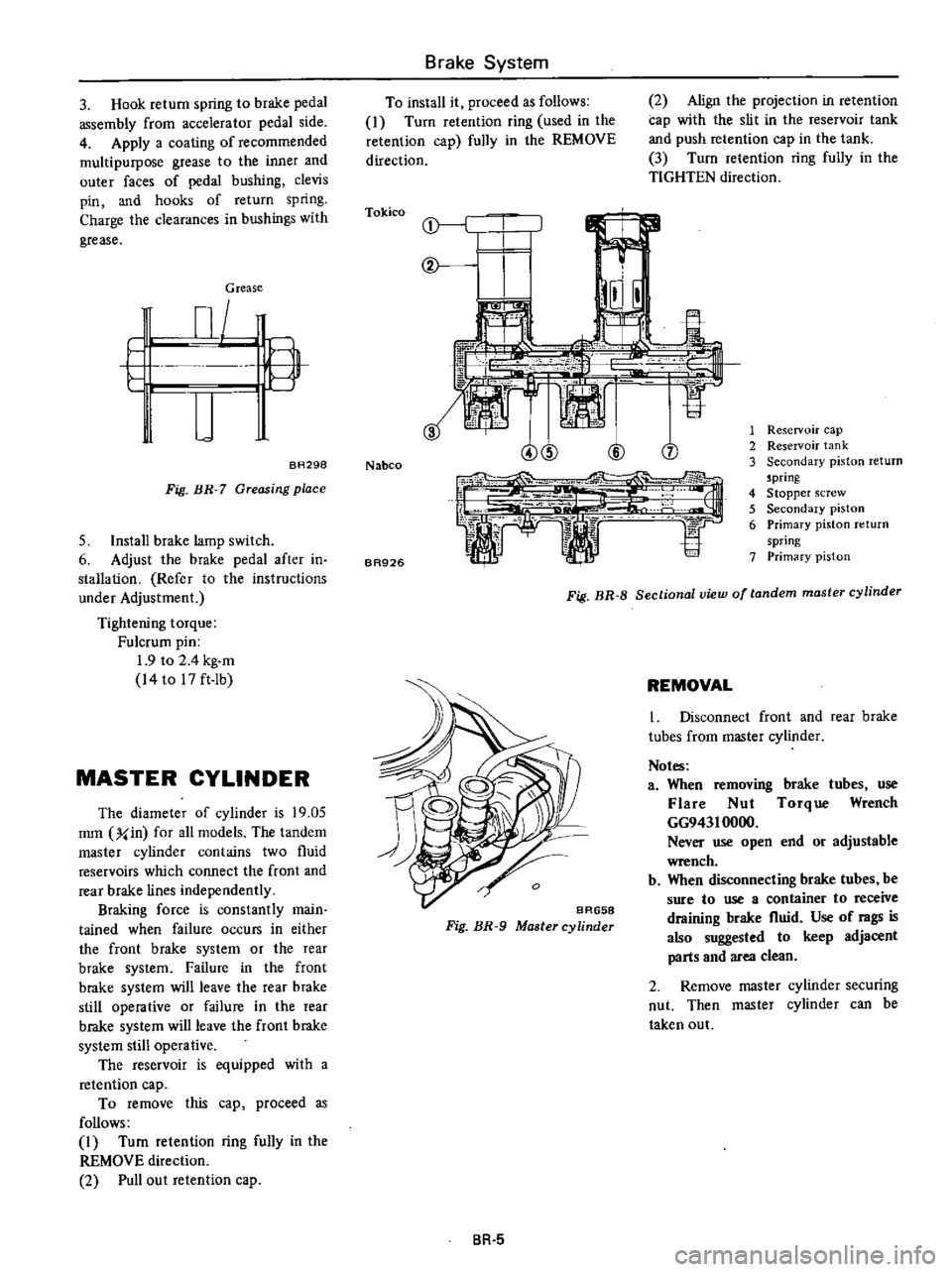
3
Hook
return
spring
to
brake
pedal
assembly
from
accelerator
pedal
side
4
Apply
a
coating
of
recommended
multipurpose
grease
to
the
inner
and
outer
faces
of
pedal
bushing
clevis
pin
and
hooks
of
return
spring
Charge
the
clearances
in
bushings
with
grease
Grease
m
n
L
g
U
BR298
Fig
BH
7
Greasing
place
5
lnstali
brake
lamp
switch
6
Adjust
the
brake
pedal
after
in
stallation
Refer
to
the
instructions
under
Adjustment
Tightening
torque
Fulcrum
pin
1
9
to
2
4
kg
m
14to
17ft
ib
MASTER
CYLINDER
The
diameter
of
cylinder
is
19
05
mm
y
in
for
all
models
The
tandem
master
cylinder
contains
two
fluid
reservoirs
which
connect
the
front
and
rear
brake
lines
independently
Braking
force
is
constantly
main
tained
when
failure
occurs
in
either
the
front
brake
system
or
the
rear
brake
system
Failure
in
the
front
brake
system
will
leave
the
rear
brake
still
operative
or
failure
in
the
rear
brake
system
will
leave
the
front
brake
system
still
operative
The
reservoir
is
eq
ui
pped
with
a
retention
cap
To
remove
this
cap
proceed
as
follows
I
Tum
retention
ring
fully
in
the
REMOVE
direction
2
Pull
out
retention
cap
Brake
System
To
install
it
proceed
as
follows
I
Turn
retention
ring
used
in
the
retention
cap
fully
in
the
REMOVE
direction
Tokico
@
1tr
I
I
I
j
1
Nabco
BR926
2
Align
the
projection
in
retention
cap
with
the
slit
in
the
reservoir
tank
and
push
retention
cap
in
the
tank
3
Turn
retention
ring
fully
in
the
TIGHTEN
direction
00
CD
1
Reservoir
cap
2
Reservoir
tank
3
Secondary
piston
return
5pring
4
Stopper
screw
5
Secondary
piston
6
Primary
piston
return
spring
7
Primary
piston
Fig
BR
B
Sectional
view
of
tandem
master
cylinder
o
BR658
Fig
BR
9
Master
cylinder
BR
5
REMOVAL
1
Disconnect
front
and
rear
brake
tubes
from
master
cylinder
Notes
a
When
removing
brake
tubes
use
Flare
Nut
Torque
Wrench
GG94310000
Never
use
open
end
or
adjustable
wrench
b
When
disconnecting
brake
tubes
be
sure
to
use
a
container
to
receive
draining
brake
flnid
Use
of
rags
is
also
suggested
to
keep
adjacent
parts
and
area
clean
2
Remove
master
cylinder
securing
nut
Then
master
cylinder
can
be
taken
out
Page 389 of 537
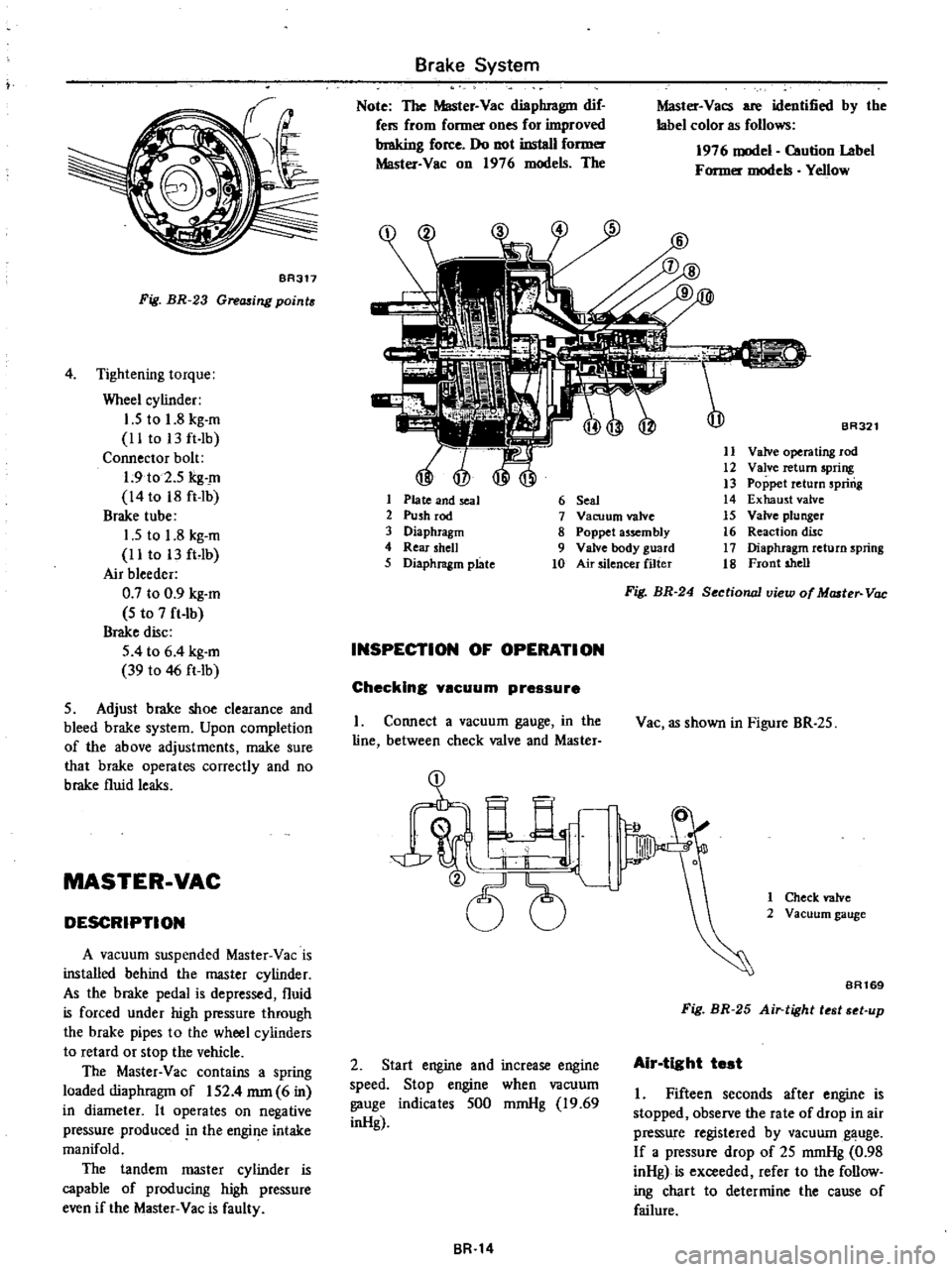
f
BR317
Fig
BR
23
Gre
ing
point
4
Tightening
torque
Wheel
cylinder
J
S
to
1
8
kg
m
II
to
13ft
Ib
Connector
bolt
1
9
to
2
5
kg
m
14
to
18
ft
Ib
Brake
tube
1
5
to
1
8
kg
m
II
to
13
ft
Ib
Air
bleeder
0
7
to
0
9
kg
m
S
to
7
ft
Ib
Brake
disc
5
4
to
6
4
kg
m
39
to
46
ft
Ib
S
Adjust
brake
shoe
clearance
and
bleed
brake
system
Upon
completion
of
the
above
adjustments
make
sure
that
brake
operates
correctly
and
no
brake
fluid
leaks
MASTER
VAC
DESCRIPTION
A
vacuum
suspended
Master
Vac
is
installed
behind
the
master
cylinder
As
the
brake
pedal
is
depressed
fluid
is
forced
under
high
pressure
through
the
brake
pipes
to
the
wheel
cylinders
to
retard
or
stop
the
vehicle
The
Master
Vac
contains
a
spring
loaded
diaphragm
of
IS2
4
mm
6
in
in
diameter
It
operates
on
negative
pressure
produced
n
the
engine
intake
manifold
The
tandem
master
cylinder
is
capable
of
producing
high
pressure
even
if
the
Master
Vac
is
faulty
Brake
System
Note
The
Master
Vac
diaphragm
dif
fers
from
fonner
ones
for
improved
braking
force
Do
not
install
fonner
Master
Vac
on
1976
models
The
1
Plate
and
seal
2
Push
rod
3
Diaphragm
4
Rear
shell
5
Diaphragm
plate
Master
Vacs
are
identified
by
the
label
color
as
follows
1976
model
Caution
Label
Former
models
YeJlow
BR321
11
Valve
operating
rod
12
Valve
return
spring
13
Poppet
return
spring
14
Exhaust
valve
15
Valve
plunger
16
Reaction
disc
17
Diaphragm
return
spring
18
Front
shell
6
Seal
7
Vacuum
valve
8
Poppet
assembly
9
Valve
body
guard
10
Air
silencer
filter
INSPECTION
OF
OPERATION
Checking
yscuum
pressure
I
Connect
a
vacuum
gauge
in
the
line
between
check
valve
and
Master
2
Start
engine
and
increase
engine
speed
Stop
engine
when
vacuum
gauge
indicates
SOO
mmHg
19
69
inHg
BR
14
Fig
BR
24
Sectionall1iew
of
Master
Vac
Vac
as
shown
in
Figure
BR
25
1
Check
valve
2
Vacuum
gauge
BA169
Fig
BR
25
Air
tight
t
t
t
up
Air
tight
test
I
Fifteen
seconds
after
engine
is
stopped
observe
the
rate
of
drop
in
air
pressure
registered
by
vacuum
gauge
If
a
pressure
drop
of
25
mmHg
0
98
inHg
is
exceeded
refer
to
the
follow
ing
chart
to
determine
the
cause
of
failure
Page 402 of 537
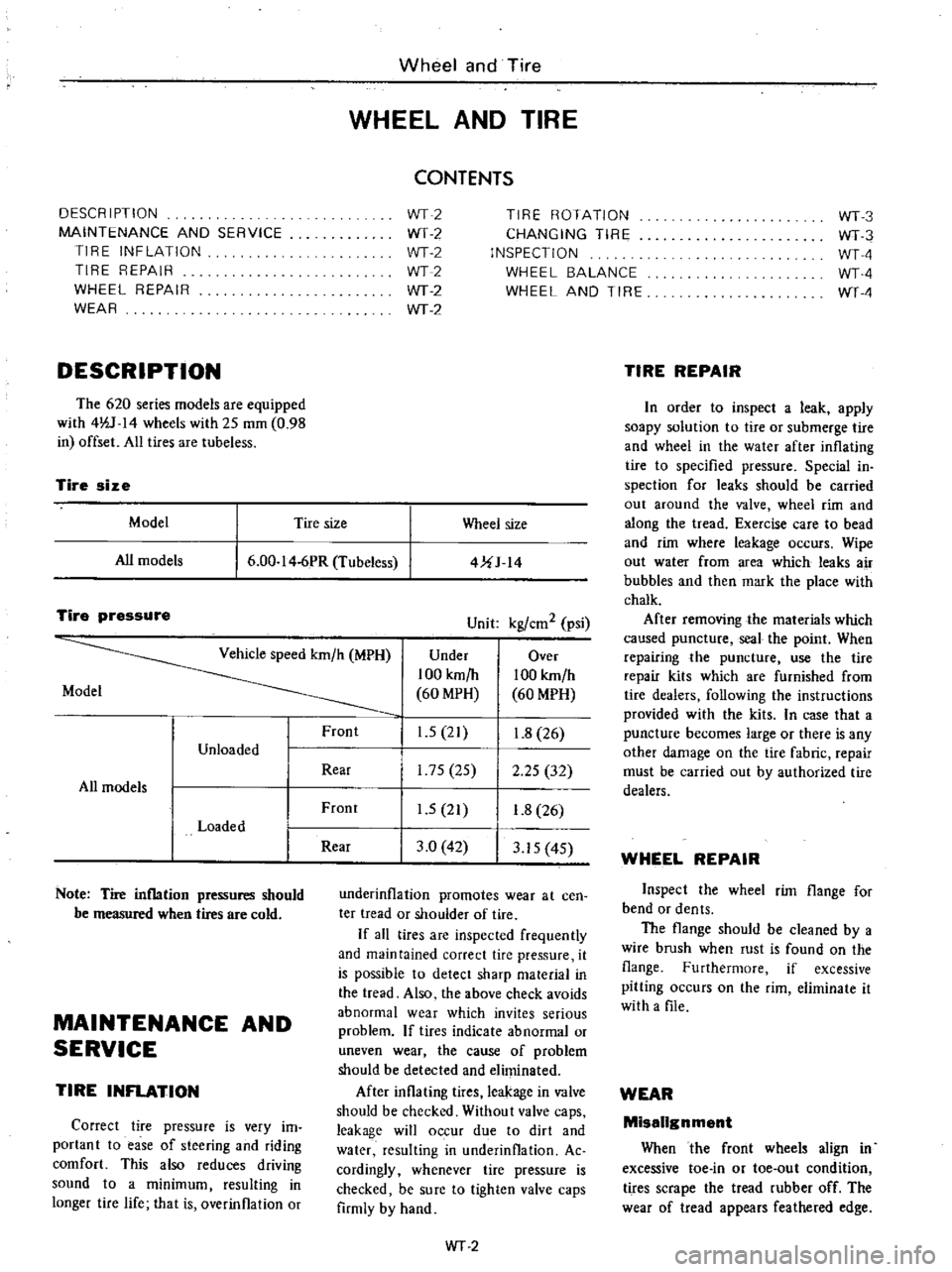
DESCRIPTION
MAINTENANCE
AND
SERVICE
TIRE
INFLATION
TIRE
REPAIR
WHEEL
REPAIR
WEAR
DESCRIPTION
The
620
series
models
are
equipped
with
4lV
14
wheels
with
25
mOl
0
98
in
offset
All
tires
are
tubeless
Wheel
and
Tire
WHEEL
AND
TIRE
CONTENTS
WT2
WT
2
WT2
WT2
WT
2
WT
2
TIRE
ROTATION
CHANGING
TIRE
INSPECTION
WHEEL
BALANCE
WHEEL
AND
TIRE
Tire
size
Model
Tire
size
Wheel
size
All
models
6
00
I
4
6PR
Tubeless
4UJ
14
Tire
pressure
Unit
kgl
em
2
psi
Vehicle
speed
km
h
MPH
Under
Over
100
km
h
100
km
h
Model
60
MPH
60
MPH
Front
1
5
21
1
8
26
Unloaded
Rear
175
25
2
25
32
All
models
Front
1
5
21
1
8
26
Loaded
Rear
3
0
42
3
15
4S
Note
Tire
inflation
pressures
should
be
measured
when
tires
are
cold
MAINTENANCE
AND
SERVICE
TIRE
INFLATION
Correct
tire
pressure
is
very
im
portant
to
ease
of
steering
and
riding
comfort
This
also
reduces
driving
sound
to
a
minimum
resulting
in
longer
tire
life
that
is
overinflation
or
underinflation
promotes
wear
at
cen
ter
tread
or
shouider
of
tire
If
aU
tires
are
inspected
frequently
and
maintained
correct
tire
pressure
it
is
possible
to
detect
sharp
material
in
the
tread
Also
the
above
check
avoids
abnormal
wear
which
invites
serious
problem
If
tires
indicate
abnormal
or
uneven
wear
the
cause
of
problem
should
be
detected
and
eliminated
After
inflating
tires
leakage
in
valve
should
be
checked
Without
valve
caps
leakage
will
occur
due
to
dirt
and
water
resulting
in
underinflation
Ac
cordingly
whenever
tire
pressure
is
checked
be
sure
to
tighten
valve
caps
firmly
by
hand
WT
2
WT3
WT3
WTA
WTA
WT
4
TIRE
REPAIR
In
order
to
inspect
a
leak
apply
soapy
solution
to
tire
or
submerge
tire
and
wheei
in
the
water
after
inflating
tire
to
specified
pressure
Special
in
spection
for
leaks
should
be
carried
out
around
the
valve
wheel
rim
and
along
the
tread
Exercise
care
to
bead
and
rim
where
leakage
occurs
Wipe
out
water
from
area
which
leaks
air
bubbles
and
then
mark
the
place
with
chalk
After
removing
the
materials
which
caused
puncture
seal
the
point
When
repairing
the
puncture
use
the
tire
repair
kits
which
are
furnished
from
tire
dealers
following
the
instructions
provided
with
the
kits
In
case
that
a
puncture
becomes
large
or
there
is
any
other
damage
on
the
tire
fabric
repair
must
be
carried
out
by
authorized
tire
dealers
WHEEL
REPAIR
Inspect
the
wheel
rim
flange
for
bend
or
dents
The
flange
should
be
cleaned
by
a
wire
brush
when
rust
is
found
on
the
flange
Furthermore
if
excessive
pitting
occurs
on
the
rim
eliminate
it
with
a
file
WEAR
Missilgnment
When
the
front
wheels
align
in
excessive
toe
in
or
toe
out
condition
tires
scrape
the
tread
rubber
off
The
wear
of
tread
appears
feathered
edge
Page 418 of 537
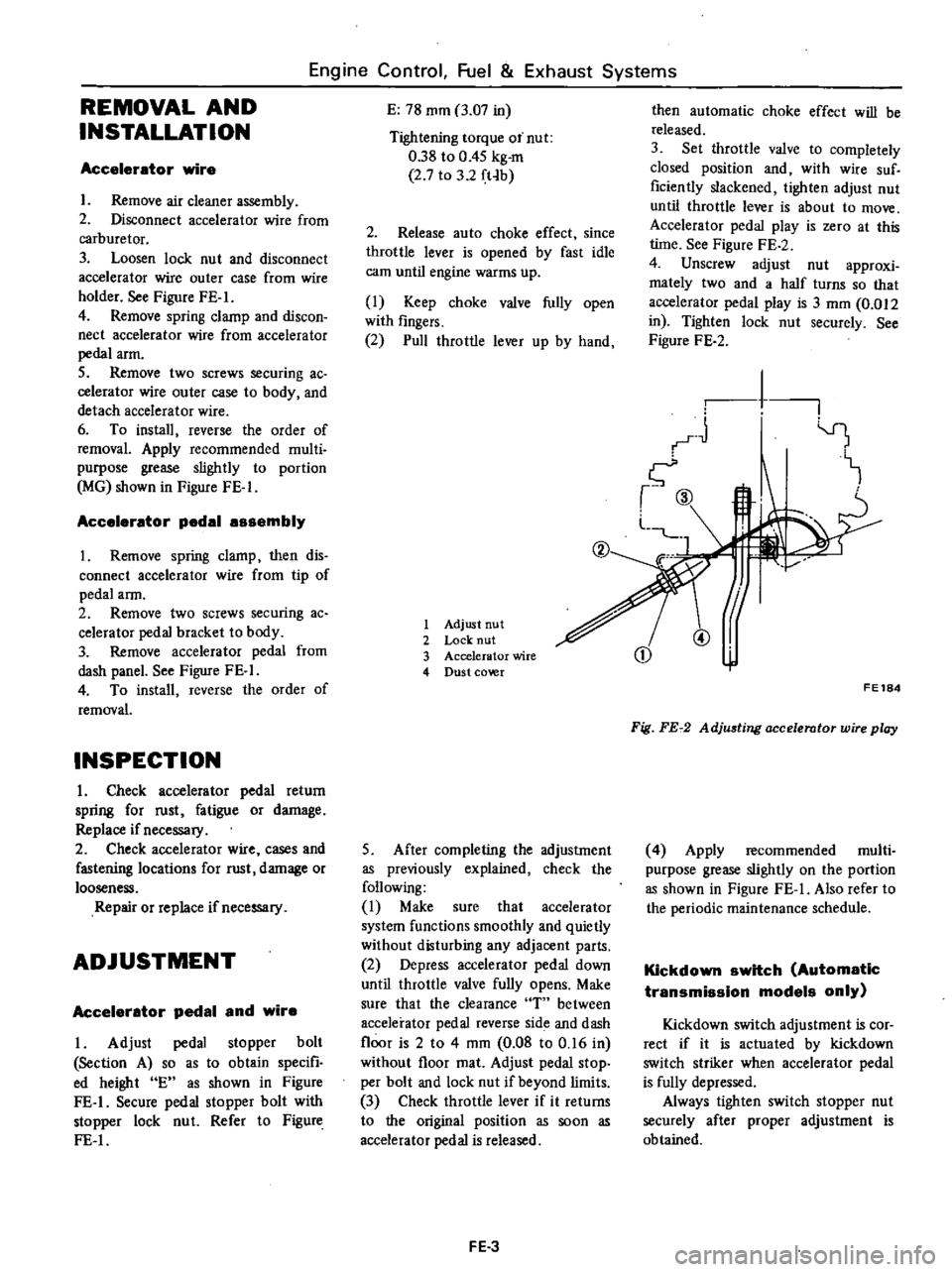
Engine
Control
Fuel
Exhaust
Systems
REMOVAL
AND
INSTALLATION
Accelerator
wire
I
Remove
air
cleaner
assembly
2
Disconnect
accelerator
wire
from
carburetor
3
Loosen
lock
nut
and
disconnect
accelerator
wire
outer
case
from
wire
holder
See
Figure
FE
I
4
Remove
spring
clamp
and
discon
nect
accelerator
wire
from
accelerator
pedal
arm
S
Remove
two
screws
securing
ac
celerator
wire
outer
case
to
body
and
detach
accelerator
wire
6
To
install
reverse
the
order
of
removal
Apply
recommended
multi
purpose
grease
slightly
to
portion
MG
shown
in
Figure
FE
I
Accelerator
pedal
assembly
I
Remove
spring
clamp
then
dis
connect
accelerator
wire
from
tip
of
pedal
ann
2
Remove
two
screws
securing
ac
celerator
pedal
bracket
to
body
3
Remove
accelerator
pedal
from
dash
panel
See
Figure
FE
I
4
To
install
reverse
the
order
of
removal
INSPECTION
I
Check
accelerator
pedal
return
spring
for
rust
fatigue
or
damage
Replace
if
necessary
2
Check
accelerator
wire
cases
and
fastening
locations
for
rust
damage
or
looseness
Repair
or
replace
if
necessary
ADJUSTMENT
Accelerstor
pedal
and
wire
Adjust
pedal
stopper
bolt
Section
A
so
as
to
obtain
specifi
ed
height
E
as
shown
in
Figure
FE
I
Secure
pedal
stopper
bolt
with
stopper
lock
nut
Refer
to
Figure
FE
I
E
78
mOl
3
07
in
Tightening
torque
01
nut
0
38
to
0
4S
kg
m
2
7
to
3
2
ft
b
2
Release
auto
choke
effect
since
throttle
lever
is
opened
by
fast
idle
earn
until
engine
warms
up
I
Keep
choke
valve
fully
open
with
fingers
2
Pull
throttle
lever
up
by
hand
1
Adjust
nut
2
Lock
nut
3
Accelerator
wire
4
Dust
co
r
5
After
completing
the
adjustment
as
previously
explained
check
the
following
I
Make
sure
that
accelerator
system
functions
smoothly
and
quietly
without
disturbing
any
adjacent
parts
2
Depress
accelerator
pedal
down
until
throttle
valve
fully
opens
Make
sure
that
the
clearance
T
between
accelerator
pedal
reverse
side
and
dash
floor
is
2
to
4
mm
0
08
to
0
16
in
without
floor
mat
Adjust
pedal
stop
per
bolt
and
lock
nut
if
beyond
limits
3
Check
throttle
lever
if
it
returns
to
the
original
position
as
soon
as
accelerator
pedal
is
released
FE
3
then
automatic
choke
effect
will
be
released
3
Set
throttle
valve
to
completely
closed
position
and
with
wire
suf
ficiently
slackened
lighten
adjust
nut
until
throttle
lever
is
about
to
move
Accelerator
pedal
play
is
zero
at
this
lime
See
Figure
FE
2
4
Unscrew
adjust
nut
approxi
mately
two
and
a
half
turns
so
that
accelerator
pedal
play
is
3
mOl
0
012
in
Tighten
lock
nut
securely
See
Figure
FE
2
1
I
1
CD
@
FE184
Fig
FE72
AdjU6ting
accelerator
wire
play
4
Apply
recommended
multi
purpose
grease
slightly
on
the
portion
as
shown
in
Figure
FE
I
Also
refer
to
the
periodic
maintenance
schedule
Kickdown
switch
Automatic
transmission
models
only
Kickdown
switch
adjustment
is
cor
rect
if
it
is
actuated
by
kickdown
switch
striker
when
accelerator
pedal
is
fully
depressed
Always
tighten
switch
stopper
nut
securely
after
proper
adjustment
is
obtained
Page 426 of 537
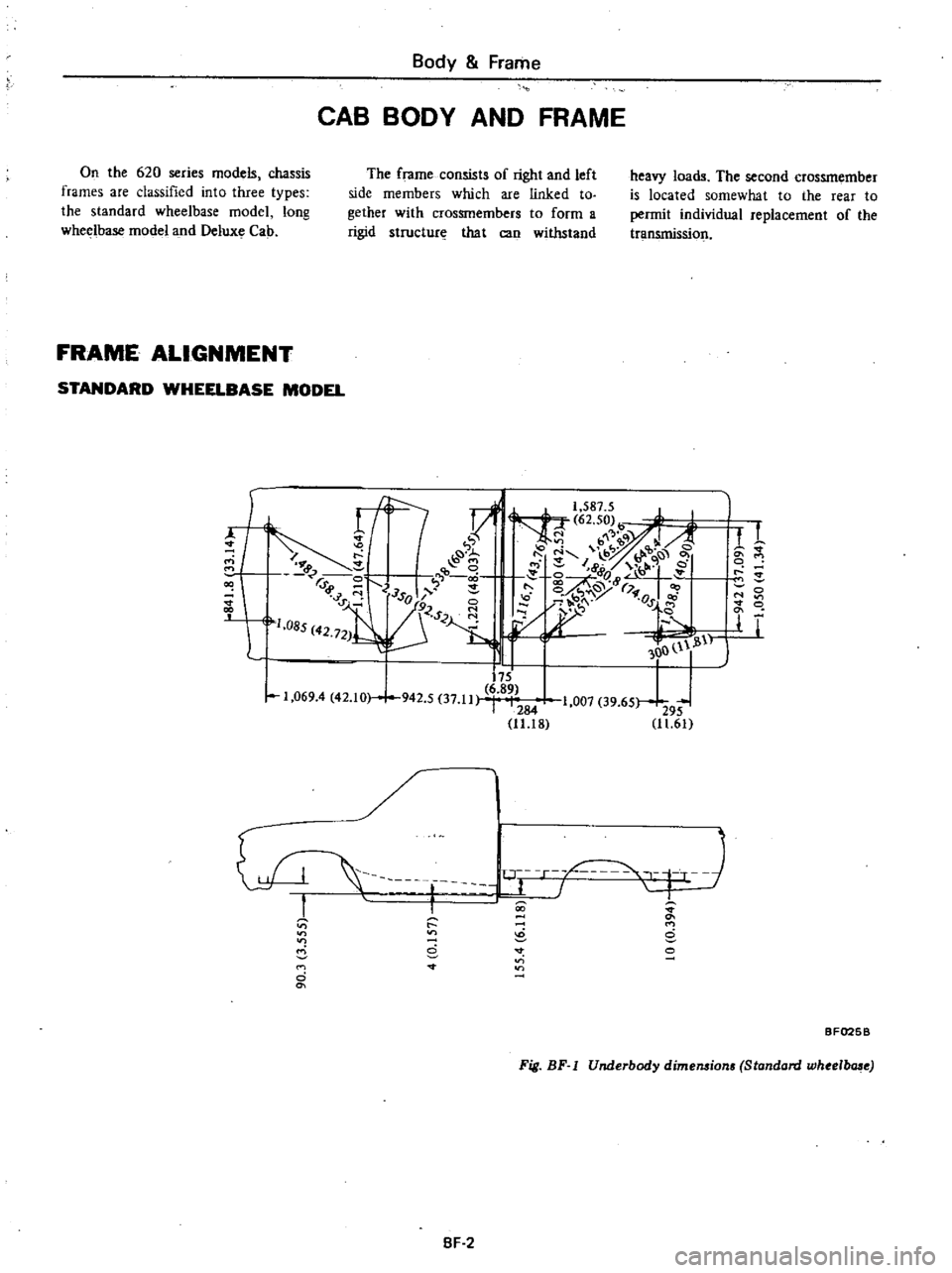
Body
Frame
CAB
BODY
AND
FRAME
On
the
620
series
models
chassis
frames
are
classified
into
three
types
the
standard
wheelbase
model
long
wheelbase
model
and
Deluxe
Cab
The
frame
consists
of
right
and
left
side
members
which
are
linked
to
gether
with
crossmembers
to
form
a
rigid
structure
that
can
withstand
heavy
loads
The
second
crossmember
is
located
somewhat
to
the
rear
to
permit
individual
replacement
of
the
transmissiol
FRAME
ALIGNMENT
STANDARD
WHEELBASE
MODEL
f
r1
1
587
5
J
I
1
X
62
50
I
b
q
J
A
1
7
I
b
9
9
8
I
1
e
t
r
0
ij
e
6
rd
r
r
1sol
1
1
9ClS
1
085
42
721
Cl
H
1
I
11
OO
l
1
i11
175
6
89
1
069
4
42
10
942
5
37
11
1007
39
65
I
284
295
11
18
11
61
00
d
M
o
8
r
r
c
8
o
r
T
L
BF025B
Fig
BF
I
Underbody
dime1l8ion
Standard
whee
b
e
SF
2