DODGE RAM 2001 Service Repair Manual
Manufacturer: DODGE, Model Year: 2001, Model line: RAM, Model: DODGE RAM 2001Pages: 2889, PDF Size: 68.07 MB
Page 2751 of 2889
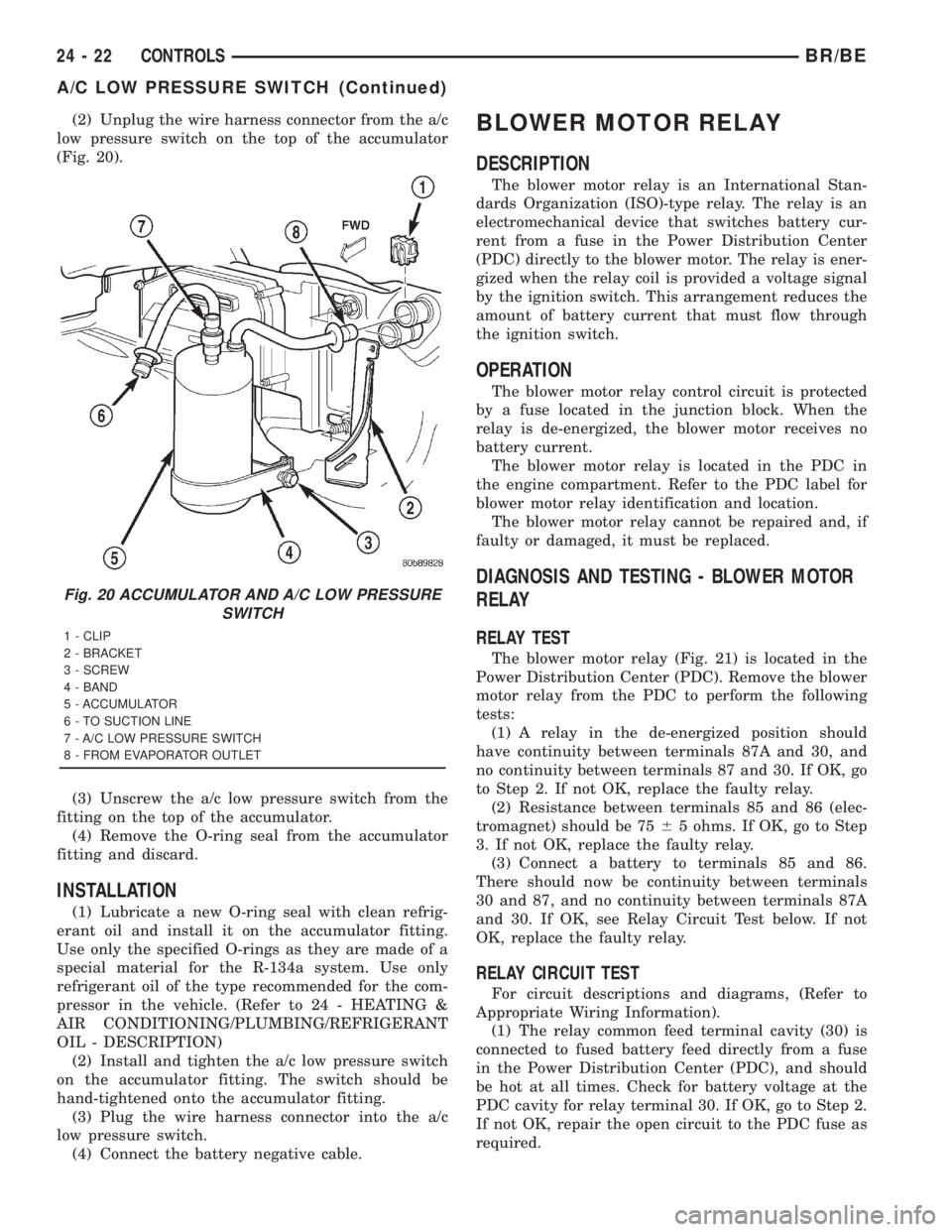
(2) Unplug the wire harness connector from the a/c
low pressure switch on the top of the accumulator
(Fig. 20).
(3) Unscrew the a/c low pressure switch from the
fitting on the top of the accumulator.
(4) Remove the O-ring seal from the accumulator
fitting and discard.
INSTALLATION
(1) Lubricate a new O-ring seal with clean refrig-
erant oil and install it on the accumulator fitting.
Use only the specified O-rings as they are made of a
special material for the R-134a system. Use only
refrigerant oil of the type recommended for the com-
pressor in the vehicle. (Refer to 24 - HEATING &
AIR CONDITIONING/PLUMBING/REFRIGERANT
OIL - DESCRIPTION)
(2) Install and tighten the a/c low pressure switch
on the accumulator fitting. The switch should be
hand-tightened onto the accumulator fitting.
(3) Plug the wire harness connector into the a/c
low pressure switch.
(4) Connect the battery negative cable.
BLOWER MOTOR RELAY
DESCRIPTION
The blower motor relay is an International Stan-
dards Organization (ISO)-type relay. The relay is an
electromechanical device that switches battery cur-
rent from a fuse in the Power Distribution Center
(PDC) directly to the blower motor. The relay is ener-
gized when the relay coil is provided a voltage signal
by the ignition switch. This arrangement reduces the
amount of battery current that must flow through
the ignition switch.
OPERATION
The blower motor relay control circuit is protected
by a fuse located in the junction block. When the
relay is de-energized, the blower motor receives no
battery current.
The blower motor relay is located in the PDC in
the engine compartment. Refer to the PDC label for
blower motor relay identification and location.
The blower motor relay cannot be repaired and, if
faulty or damaged, it must be replaced.
DIAGNOSIS AND TESTING - BLOWER MOTOR
RELAY
RELAY TEST
The blower motor relay (Fig. 21) is located in the
Power Distribution Center (PDC). Remove the blower
motor relay from the PDC to perform the following
tests:
(1) A relay in the de-energized position should
have continuity between terminals 87A and 30, and
no continuity between terminals 87 and 30. If OK, go
to Step 2. If not OK, replace the faulty relay.
(2) Resistance between terminals 85 and 86 (elec-
tromagnet) should be 7565 ohms. If OK, go to Step
3. If not OK, replace the faulty relay.
(3) Connect a battery to terminals 85 and 86.
There should now be continuity between terminals
30 and 87, and no continuity between terminals 87A
and 30. If OK, see Relay Circuit Test below. If not
OK, replace the faulty relay.
RELAY CIRCUIT TEST
For circuit descriptions and diagrams, (Refer to
Appropriate Wiring Information).
(1) The relay common feed terminal cavity (30) is
connected to fused battery feed directly from a fuse
in the Power Distribution Center (PDC), and should
be hot at all times. Check for battery voltage at the
PDC cavity for relay terminal 30. If OK, go to Step 2.
If not OK, repair the open circuit to the PDC fuse as
required.
Fig. 20 ACCUMULATOR AND A/C LOW PRESSURE
SWITCH
1 - CLIP
2 - BRACKET
3 - SCREW
4 - BAND
5 - ACCUMULATOR
6 - TO SUCTION LINE
7 - A/C LOW PRESSURE SWITCH
8 - FROM EVAPORATOR OUTLET
24 - 22 CONTROLSBR/BE
A/C LOW PRESSURE SWITCH (Continued)
Page 2752 of 2889
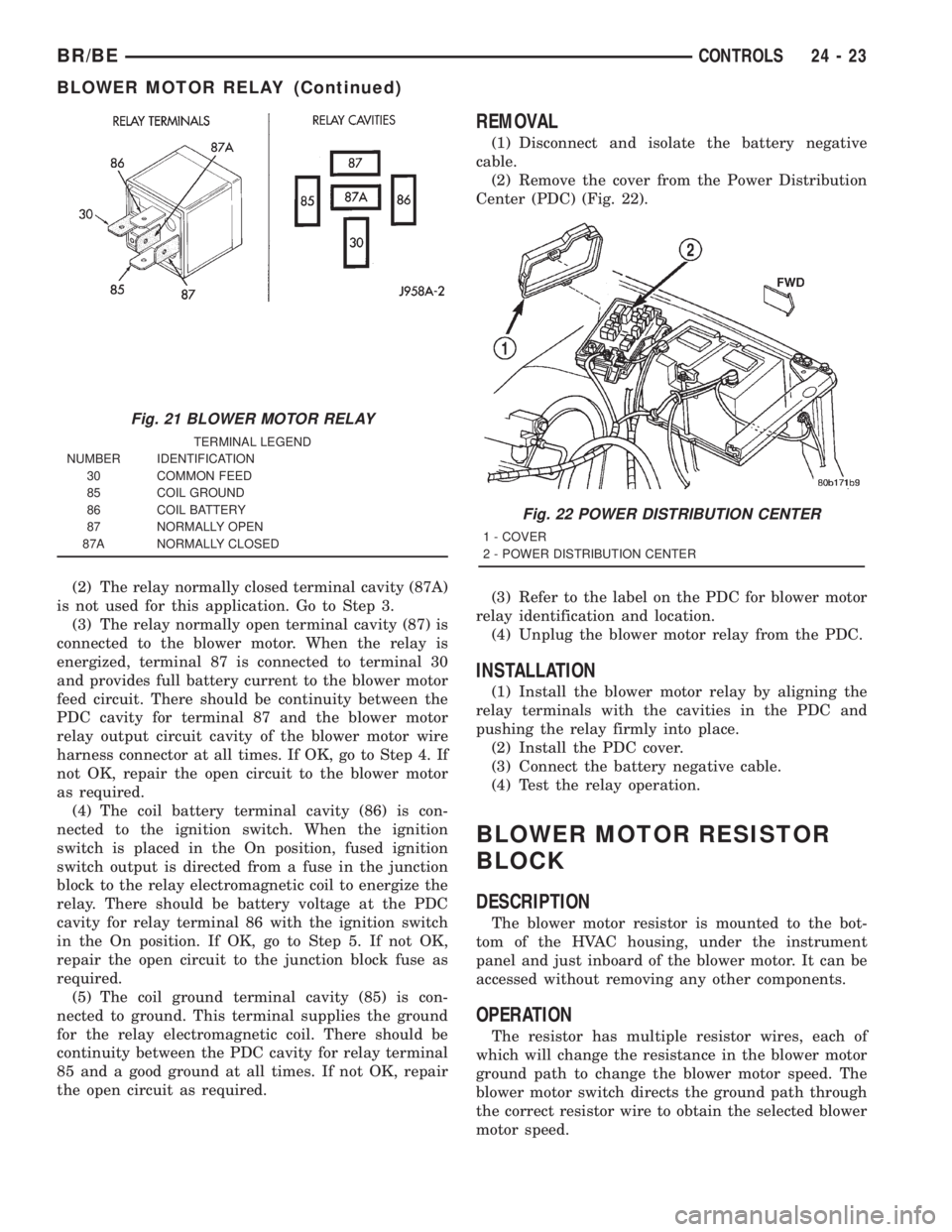
(2) The relay normally closed terminal cavity (87A)
is not used for this application. Go to Step 3.
(3) The relay normally open terminal cavity (87) is
connected to the blower motor. When the relay is
energized, terminal 87 is connected to terminal 30
and provides full battery current to the blower motor
feed circuit. There should be continuity between the
PDC cavity for terminal 87 and the blower motor
relay output circuit cavity of the blower motor wire
harness connector at all times. If OK, go to Step 4. If
not OK, repair the open circuit to the blower motor
as required.
(4) The coil battery terminal cavity (86) is con-
nected to the ignition switch. When the ignition
switch is placed in the On position, fused ignition
switch output is directed from a fuse in the junction
block to the relay electromagnetic coil to energize the
relay. There should be battery voltage at the PDC
cavity for relay terminal 86 with the ignition switch
in the On position. If OK, go to Step 5. If not OK,
repair the open circuit to the junction block fuse as
required.
(5) The coil ground terminal cavity (85) is con-
nected to ground. This terminal supplies the ground
for the relay electromagnetic coil. There should be
continuity between the PDC cavity for relay terminal
85 and a good ground at all times. If not OK, repair
the open circuit as required.
REMOVAL
(1) Disconnect and isolate the battery negative
cable.
(2) Remove the cover from the Power Distribution
Center (PDC) (Fig. 22).
(3) Refer to the label on the PDC for blower motor
relay identification and location.
(4) Unplug the blower motor relay from the PDC.
INSTALLATION
(1) Install the blower motor relay by aligning the
relay terminals with the cavities in the PDC and
pushing the relay firmly into place.
(2) Install the PDC cover.
(3) Connect the battery negative cable.
(4) Test the relay operation.
BLOWER MOTOR RESISTOR
BLOCK
DESCRIPTION
The blower motor resistor is mounted to the bot-
tom of the HVAC housing, under the instrument
panel and just inboard of the blower motor. It can be
accessed without removing any other components.
OPERATION
The resistor has multiple resistor wires, each of
which will change the resistance in the blower motor
ground path to change the blower motor speed. The
blower motor switch directs the ground path through
the correct resistor wire to obtain the selected blower
motor speed.
Fig. 21 BLOWER MOTOR RELAY
TERMINAL LEGEND
NUMBER IDENTIFICATION
30 COMMON FEED
85 COIL GROUND
86 COIL BATTERY
87 NORMALLY OPEN
87A NORMALLY CLOSED
Fig. 22 POWER DISTRIBUTION CENTER
1 - COVER
2 - POWER DISTRIBUTION CENTER
BR/BECONTROLS 24 - 23
BLOWER MOTOR RELAY (Continued)
Page 2753 of 2889
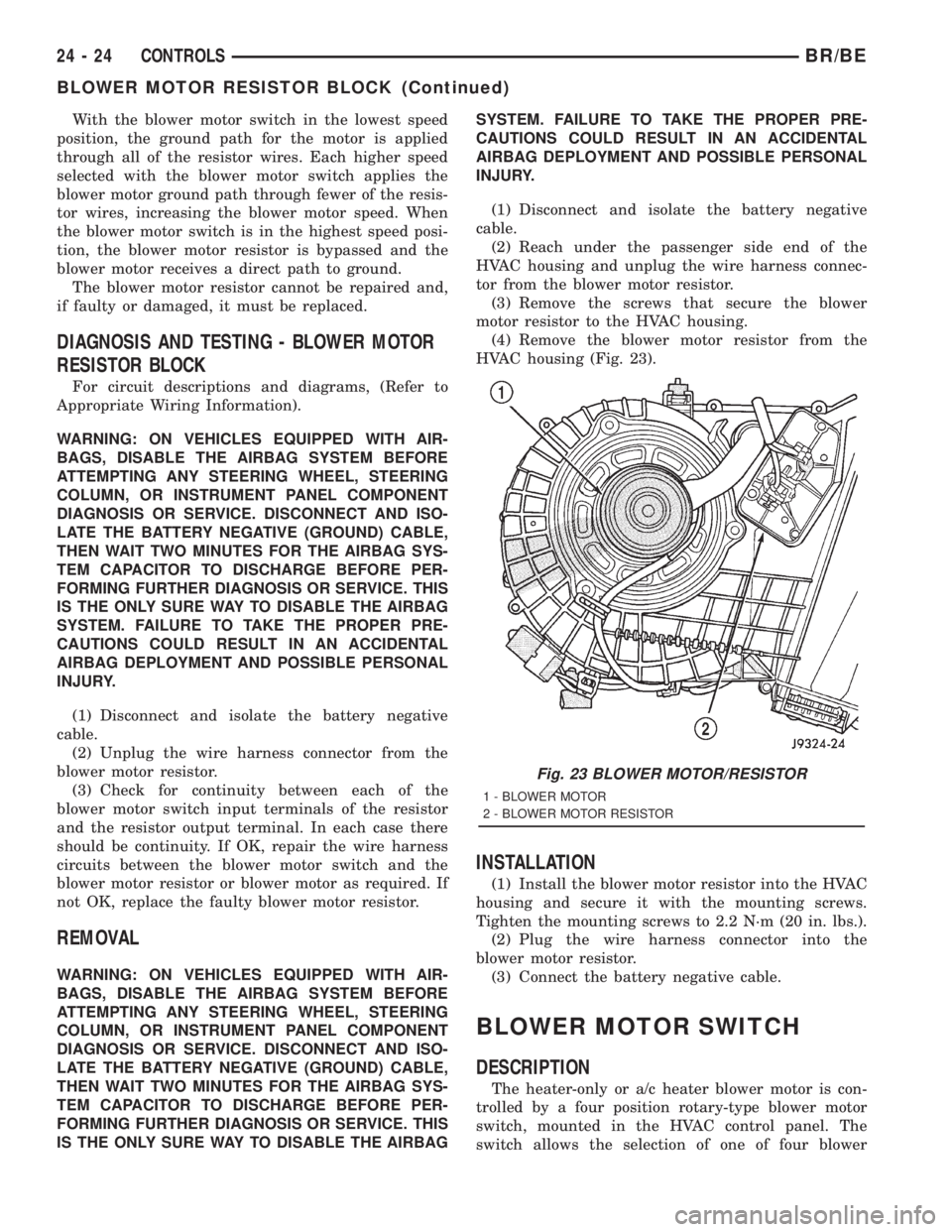
With the blower motor switch in the lowest speed
position, the ground path for the motor is applied
through all of the resistor wires. Each higher speed
selected with the blower motor switch applies the
blower motor ground path through fewer of the resis-
tor wires, increasing the blower motor speed. When
the blower motor switch is in the highest speed posi-
tion, the blower motor resistor is bypassed and the
blower motor receives a direct path to ground.
The blower motor resistor cannot be repaired and,
if faulty or damaged, it must be replaced.
DIAGNOSIS AND TESTING - BLOWER MOTOR
RESISTOR BLOCK
For circuit descriptions and diagrams, (Refer to
Appropriate Wiring Information).
WARNING: ON VEHICLES EQUIPPED WITH AIR-
BAGS, DISABLE THE AIRBAG SYSTEM BEFORE
ATTEMPTING ANY STEERING WHEEL, STEERING
COLUMN, OR INSTRUMENT PANEL COMPONENT
DIAGNOSIS OR SERVICE. DISCONNECT AND ISO-
LATE THE BATTERY NEGATIVE (GROUND) CABLE,
THEN WAIT TWO MINUTES FOR THE AIRBAG SYS-
TEM CAPACITOR TO DISCHARGE BEFORE PER-
FORMING FURTHER DIAGNOSIS OR SERVICE. THIS
IS THE ONLY SURE WAY TO DISABLE THE AIRBAG
SYSTEM. FAILURE TO TAKE THE PROPER PRE-
CAUTIONS COULD RESULT IN AN ACCIDENTAL
AIRBAG DEPLOYMENT AND POSSIBLE PERSONAL
INJURY.
(1) Disconnect and isolate the battery negative
cable.
(2) Unplug the wire harness connector from the
blower motor resistor.
(3) Check for continuity between each of the
blower motor switch input terminals of the resistor
and the resistor output terminal. In each case there
should be continuity. If OK, repair the wire harness
circuits between the blower motor switch and the
blower motor resistor or blower motor as required. If
not OK, replace the faulty blower motor resistor.
REMOVAL
WARNING: ON VEHICLES EQUIPPED WITH AIR-
BAGS, DISABLE THE AIRBAG SYSTEM BEFORE
ATTEMPTING ANY STEERING WHEEL, STEERING
COLUMN, OR INSTRUMENT PANEL COMPONENT
DIAGNOSIS OR SERVICE. DISCONNECT AND ISO-
LATE THE BATTERY NEGATIVE (GROUND) CABLE,
THEN WAIT TWO MINUTES FOR THE AIRBAG SYS-
TEM CAPACITOR TO DISCHARGE BEFORE PER-
FORMING FURTHER DIAGNOSIS OR SERVICE. THIS
IS THE ONLY SURE WAY TO DISABLE THE AIRBAGSYSTEM. FAILURE TO TAKE THE PROPER PRE-
CAUTIONS COULD RESULT IN AN ACCIDENTAL
AIRBAG DEPLOYMENT AND POSSIBLE PERSONAL
INJURY.
(1) Disconnect and isolate the battery negative
cable.
(2) Reach under the passenger side end of the
HVAC housing and unplug the wire harness connec-
tor from the blower motor resistor.
(3) Remove the screws that secure the blower
motor resistor to the HVAC housing.
(4) Remove the blower motor resistor from the
HVAC housing (Fig. 23).
INSTALLATION
(1) Install the blower motor resistor into the HVAC
housing and secure it with the mounting screws.
Tighten the mounting screws to 2.2 N´m (20 in. lbs.).
(2) Plug the wire harness connector into the
blower motor resistor.
(3) Connect the battery negative cable.
BLOWER MOTOR SWITCH
DESCRIPTION
The heater-only or a/c heater blower motor is con-
trolled by a four position rotary-type blower motor
switch, mounted in the HVAC control panel. The
switch allows the selection of one of four blower
Fig. 23 BLOWER MOTOR/RESISTOR
1 - BLOWER MOTOR
2 - BLOWER MOTOR RESISTOR
24 - 24 CONTROLSBR/BE
BLOWER MOTOR RESISTOR BLOCK (Continued)
Page 2754 of 2889
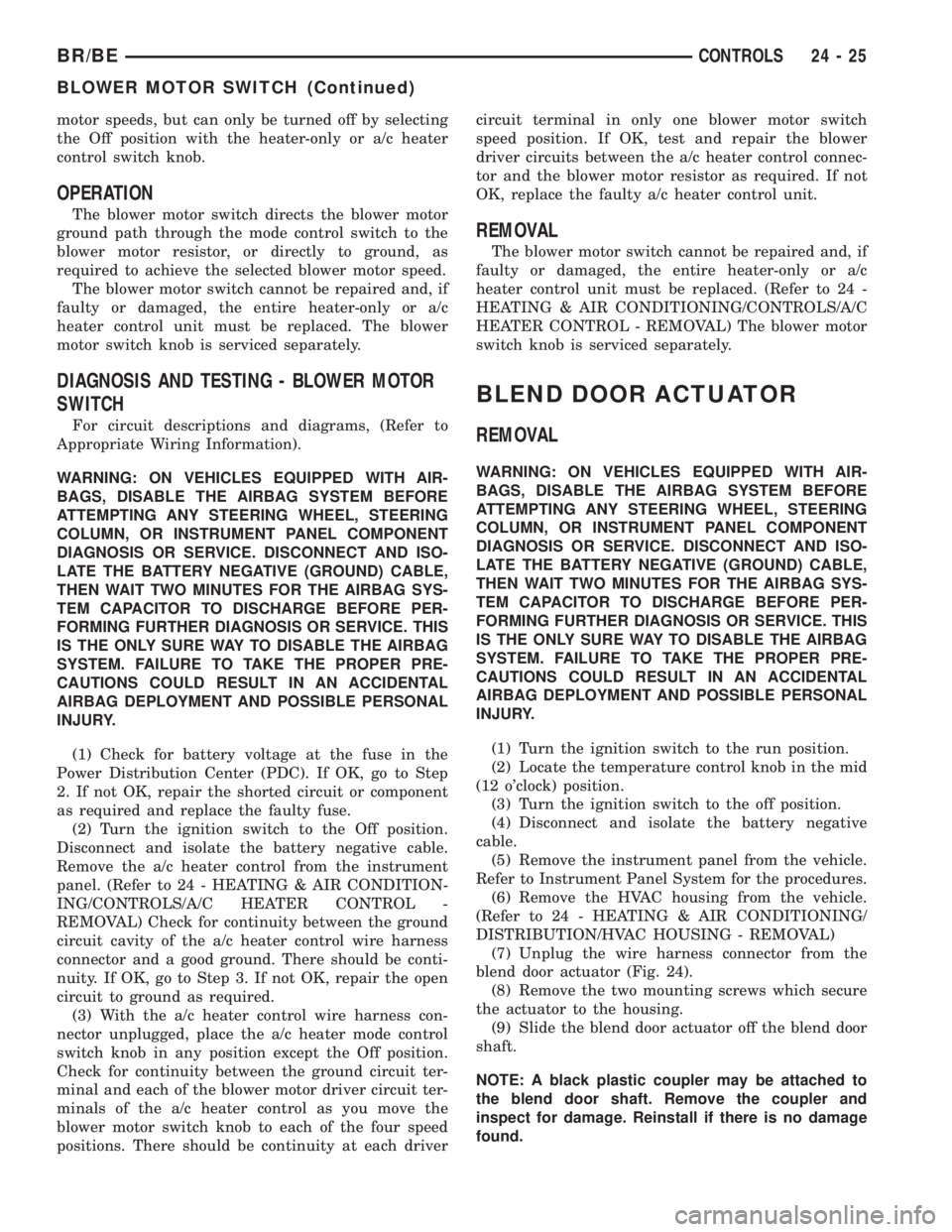
motor speeds, but can only be turned off by selecting
the Off position with the heater-only or a/c heater
control switch knob.
OPERATION
The blower motor switch directs the blower motor
ground path through the mode control switch to the
blower motor resistor, or directly to ground, as
required to achieve the selected blower motor speed.
The blower motor switch cannot be repaired and, if
faulty or damaged, the entire heater-only or a/c
heater control unit must be replaced. The blower
motor switch knob is serviced separately.
DIAGNOSIS AND TESTING - BLOWER MOTOR
SWITCH
For circuit descriptions and diagrams, (Refer to
Appropriate Wiring Information).
WARNING: ON VEHICLES EQUIPPED WITH AIR-
BAGS, DISABLE THE AIRBAG SYSTEM BEFORE
ATTEMPTING ANY STEERING WHEEL, STEERING
COLUMN, OR INSTRUMENT PANEL COMPONENT
DIAGNOSIS OR SERVICE. DISCONNECT AND ISO-
LATE THE BATTERY NEGATIVE (GROUND) CABLE,
THEN WAIT TWO MINUTES FOR THE AIRBAG SYS-
TEM CAPACITOR TO DISCHARGE BEFORE PER-
FORMING FURTHER DIAGNOSIS OR SERVICE. THIS
IS THE ONLY SURE WAY TO DISABLE THE AIRBAG
SYSTEM. FAILURE TO TAKE THE PROPER PRE-
CAUTIONS COULD RESULT IN AN ACCIDENTAL
AIRBAG DEPLOYMENT AND POSSIBLE PERSONAL
INJURY.
(1) Check for battery voltage at the fuse in the
Power Distribution Center (PDC). If OK, go to Step
2. If not OK, repair the shorted circuit or component
as required and replace the faulty fuse.
(2) Turn the ignition switch to the Off position.
Disconnect and isolate the battery negative cable.
Remove the a/c heater control from the instrument
panel. (Refer to 24 - HEATING & AIR CONDITION-
ING/CONTROLS/A/C HEATER CONTROL -
REMOVAL) Check for continuity between the ground
circuit cavity of the a/c heater control wire harness
connector and a good ground. There should be conti-
nuity. If OK, go to Step 3. If not OK, repair the open
circuit to ground as required.
(3) With the a/c heater control wire harness con-
nector unplugged, place the a/c heater mode control
switch knob in any position except the Off position.
Check for continuity between the ground circuit ter-
minal and each of the blower motor driver circuit ter-
minals of the a/c heater control as you move the
blower motor switch knob to each of the four speed
positions. There should be continuity at each drivercircuit terminal in only one blower motor switch
speed position. If OK, test and repair the blower
driver circuits between the a/c heater control connec-
tor and the blower motor resistor as required. If not
OK, replace the faulty a/c heater control unit.
REMOVAL
The blower motor switch cannot be repaired and, if
faulty or damaged, the entire heater-only or a/c
heater control unit must be replaced. (Refer to 24 -
HEATING & AIR CONDITIONING/CONTROLS/A/C
HEATER CONTROL - REMOVAL) The blower motor
switch knob is serviced separately.
BLEND DOOR ACTUATOR
REMOVAL
WARNING: ON VEHICLES EQUIPPED WITH AIR-
BAGS, DISABLE THE AIRBAG SYSTEM BEFORE
ATTEMPTING ANY STEERING WHEEL, STEERING
COLUMN, OR INSTRUMENT PANEL COMPONENT
DIAGNOSIS OR SERVICE. DISCONNECT AND ISO-
LATE THE BATTERY NEGATIVE (GROUND) CABLE,
THEN WAIT TWO MINUTES FOR THE AIRBAG SYS-
TEM CAPACITOR TO DISCHARGE BEFORE PER-
FORMING FURTHER DIAGNOSIS OR SERVICE. THIS
IS THE ONLY SURE WAY TO DISABLE THE AIRBAG
SYSTEM. FAILURE TO TAKE THE PROPER PRE-
CAUTIONS COULD RESULT IN AN ACCIDENTAL
AIRBAG DEPLOYMENT AND POSSIBLE PERSONAL
INJURY.
(1) Turn the ignition switch to the run position.
(2) Locate the temperature control knob in the mid
(12 o'clock) position.
(3) Turn the ignition switch to the off position.
(4) Disconnect and isolate the battery negative
cable.
(5) Remove the instrument panel from the vehicle.
Refer to Instrument Panel System for the procedures.
(6) Remove the HVAC housing from the vehicle.
(Refer to 24 - HEATING & AIR CONDITIONING/
DISTRIBUTION/HVAC HOUSING - REMOVAL)
(7) Unplug the wire harness connector from the
blend door actuator (Fig. 24).
(8) Remove the two mounting screws which secure
the actuator to the housing.
(9) Slide the blend door actuator off the blend door
shaft.
NOTE: A black plastic coupler may be attached to
the blend door shaft. Remove the coupler and
inspect for damage. Reinstall if there is no damage
found.
BR/BECONTROLS 24 - 25
BLOWER MOTOR SWITCH (Continued)
Page 2755 of 2889
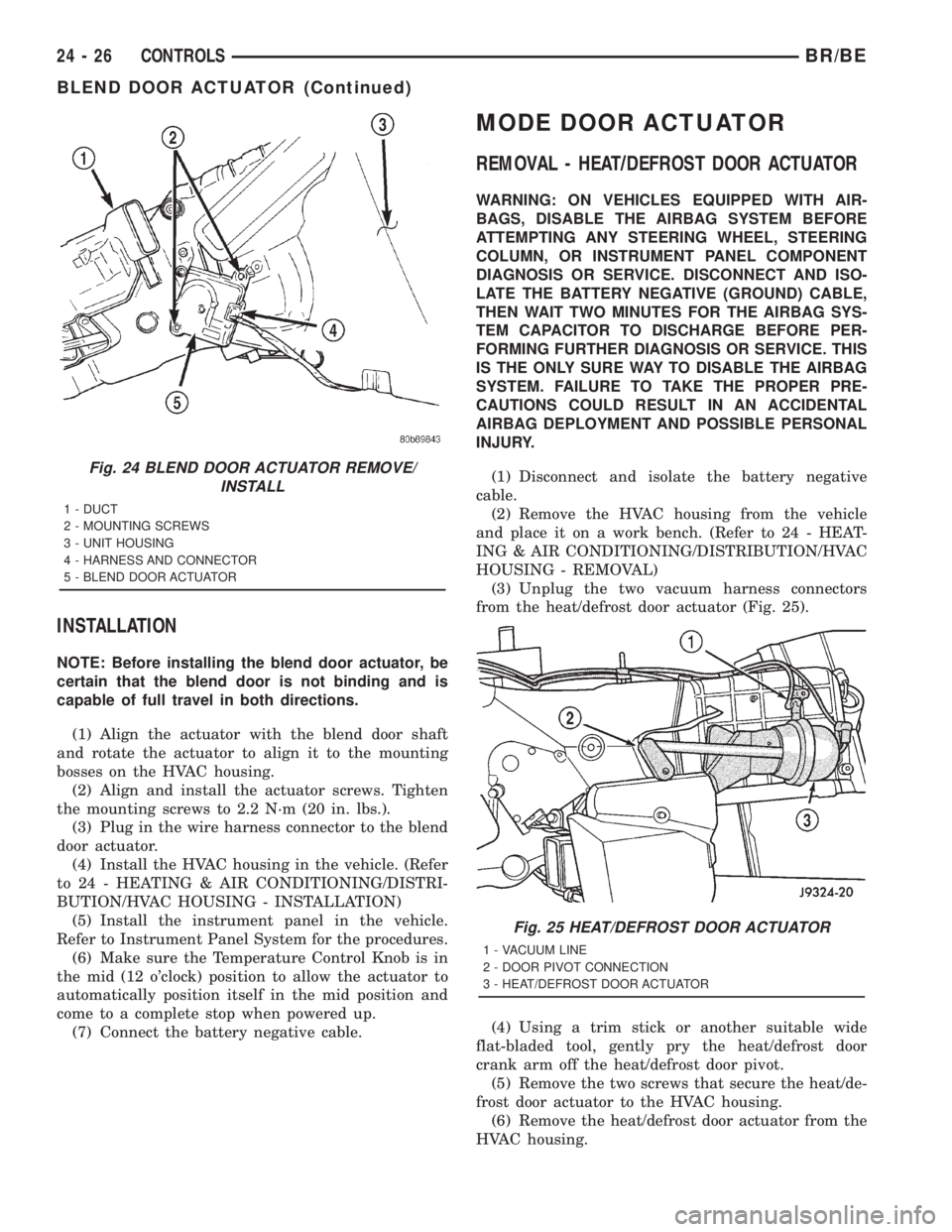
INSTALLATION
NOTE: Before installing the blend door actuator, be
certain that the blend door is not binding and is
capable of full travel in both directions.
(1) Align the actuator with the blend door shaft
and rotate the actuator to align it to the mounting
bosses on the HVAC housing.
(2) Align and install the actuator screws. Tighten
the mounting screws to 2.2 N´m (20 in. lbs.).
(3) Plug in the wire harness connector to the blend
door actuator.
(4) Install the HVAC housing in the vehicle. (Refer
to 24 - HEATING & AIR CONDITIONING/DISTRI-
BUTION/HVAC HOUSING - INSTALLATION)
(5) Install the instrument panel in the vehicle.
Refer to Instrument Panel System for the procedures.
(6) Make sure the Temperature Control Knob is in
the mid (12 o'clock) position to allow the actuator to
automatically position itself in the mid position and
come to a complete stop when powered up.
(7) Connect the battery negative cable.
MODE DOOR ACTUATOR
REMOVAL - HEAT/DEFROST DOOR ACTUATOR
WARNING: ON VEHICLES EQUIPPED WITH AIR-
BAGS, DISABLE THE AIRBAG SYSTEM BEFORE
ATTEMPTING ANY STEERING WHEEL, STEERING
COLUMN, OR INSTRUMENT PANEL COMPONENT
DIAGNOSIS OR SERVICE. DISCONNECT AND ISO-
LATE THE BATTERY NEGATIVE (GROUND) CABLE,
THEN WAIT TWO MINUTES FOR THE AIRBAG SYS-
TEM CAPACITOR TO DISCHARGE BEFORE PER-
FORMING FURTHER DIAGNOSIS OR SERVICE. THIS
IS THE ONLY SURE WAY TO DISABLE THE AIRBAG
SYSTEM. FAILURE TO TAKE THE PROPER PRE-
CAUTIONS COULD RESULT IN AN ACCIDENTAL
AIRBAG DEPLOYMENT AND POSSIBLE PERSONAL
INJURY.
(1) Disconnect and isolate the battery negative
cable.
(2) Remove the HVAC housing from the vehicle
and place it on a work bench. (Refer to 24 - HEAT-
ING & AIR CONDITIONING/DISTRIBUTION/HVAC
HOUSING - REMOVAL)
(3) Unplug the two vacuum harness connectors
from the heat/defrost door actuator (Fig. 25).
(4) Using a trim stick or another suitable wide
flat-bladed tool, gently pry the heat/defrost door
crank arm off the heat/defrost door pivot.
(5) Remove the two screws that secure the heat/de-
frost door actuator to the HVAC housing.
(6) Remove the heat/defrost door actuator from the
HVAC housing.
Fig. 24 BLEND DOOR ACTUATOR REMOVE/
INSTALL
1 - DUCT
2 - MOUNTING SCREWS
3 - UNIT HOUSING
4 - HARNESS AND CONNECTOR
5 - BLEND DOOR ACTUATOR
Fig. 25 HEAT/DEFROST DOOR ACTUATOR
1 - VACUUM LINE
2 - DOOR PIVOT CONNECTION
3 - HEAT/DEFROST DOOR ACTUATOR
24 - 26 CONTROLSBR/BE
BLEND DOOR ACTUATOR (Continued)
Page 2756 of 2889
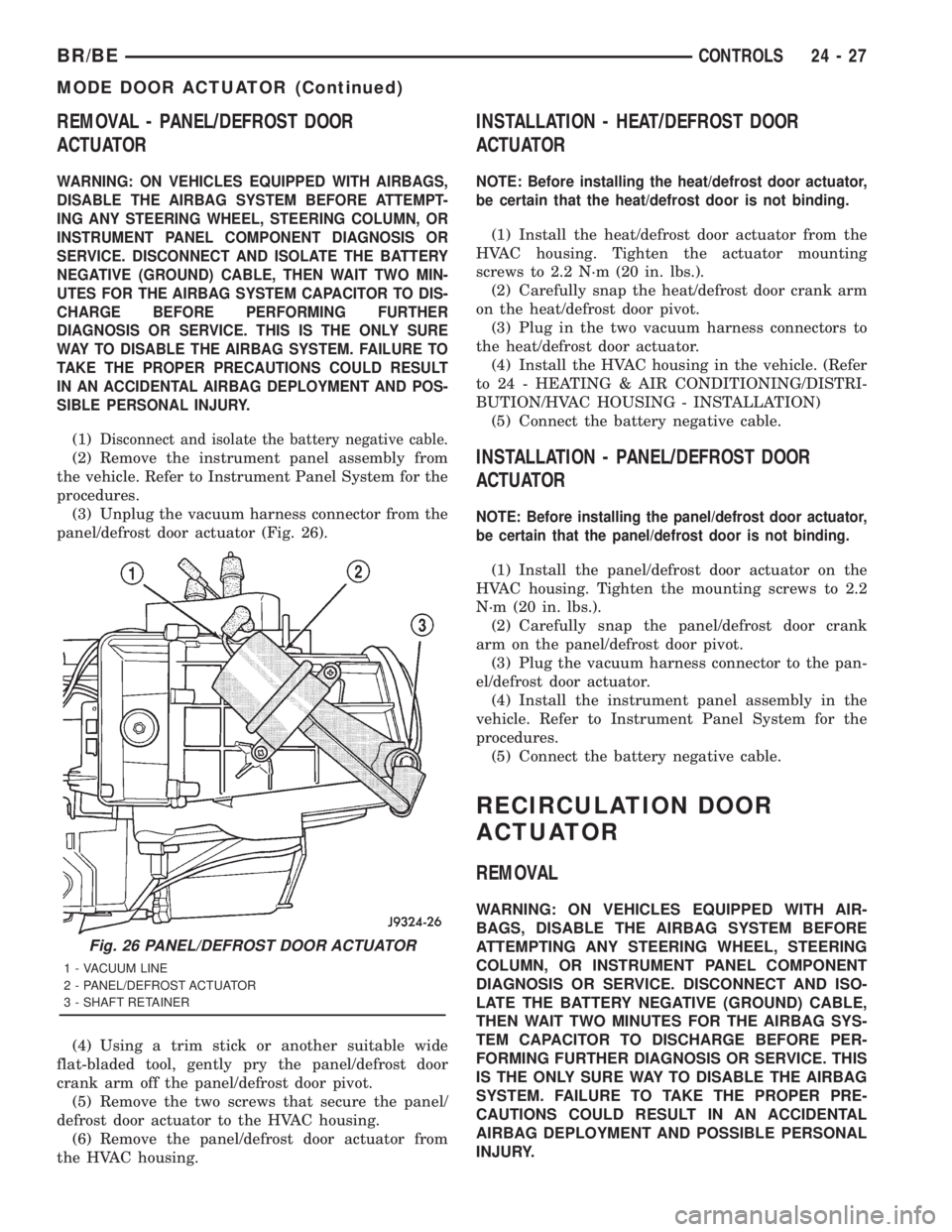
REMOVAL - PANEL/DEFROST DOOR
ACTUATOR
WARNING: ON VEHICLES EQUIPPED WITH AIRBAGS,
DISABLE THE AIRBAG SYSTEM BEFORE ATTEMPT-
ING ANY STEERING WHEEL, STEERING COLUMN, OR
INSTRUMENT PANEL COMPONENT DIAGNOSIS OR
SERVICE. DISCONNECT AND ISOLATE THE BATTERY
NEGATIVE (GROUND) CABLE, THEN WAIT TWO MIN-
UTES FOR THE AIRBAG SYSTEM CAPACITOR TO DIS-
CHARGE BEFORE PERFORMING FURTHER
DIAGNOSIS OR SERVICE. THIS IS THE ONLY SURE
WAY TO DISABLE THE AIRBAG SYSTEM. FAILURE TO
TAKE THE PROPER PRECAUTIONS COULD RESULT
IN AN ACCIDENTAL AIRBAG DEPLOYMENT AND POS-
SIBLE PERSONAL INJURY.
(1)Disconnect and isolate the battery negative cable.
(2) Remove the instrument panel assembly from
the vehicle. Refer to Instrument Panel System for the
procedures.
(3) Unplug the vacuum harness connector from the
panel/defrost door actuator (Fig. 26).
(4) Using a trim stick or another suitable wide
flat-bladed tool, gently pry the panel/defrost door
crank arm off the panel/defrost door pivot.
(5) Remove the two screws that secure the panel/
defrost door actuator to the HVAC housing.
(6) Remove the panel/defrost door actuator from
the HVAC housing.
INSTALLATION - HEAT/DEFROST DOOR
ACTUATOR
NOTE: Before installing the heat/defrost door actuator,
be certain that the heat/defrost door is not binding.
(1) Install the heat/defrost door actuator from the
HVAC housing. Tighten the actuator mounting
screws to 2.2 N´m (20 in. lbs.).
(2) Carefully snap the heat/defrost door crank arm
on the heat/defrost door pivot.
(3) Plug in the two vacuum harness connectors to
the heat/defrost door actuator.
(4) Install the HVAC housing in the vehicle. (Refer
to 24 - HEATING & AIR CONDITIONING/DISTRI-
BUTION/HVAC HOUSING - INSTALLATION)
(5) Connect the battery negative cable.
INSTALLATION - PANEL/DEFROST DOOR
ACTUATOR
NOTE: Before installing the panel/defrost door actuator,
be certain that the panel/defrost door is not binding.
(1) Install the panel/defrost door actuator on the
HVAC housing. Tighten the mounting screws to 2.2
N´m (20 in. lbs.).
(2) Carefully snap the panel/defrost door crank
arm on the panel/defrost door pivot.
(3) Plug the vacuum harness connector to the pan-
el/defrost door actuator.
(4) Install the instrument panel assembly in the
vehicle. Refer to Instrument Panel System for the
procedures.
(5) Connect the battery negative cable.
RECIRCULATION DOOR
ACTUATOR
REMOVAL
WARNING: ON VEHICLES EQUIPPED WITH AIR-
BAGS, DISABLE THE AIRBAG SYSTEM BEFORE
ATTEMPTING ANY STEERING WHEEL, STEERING
COLUMN, OR INSTRUMENT PANEL COMPONENT
DIAGNOSIS OR SERVICE. DISCONNECT AND ISO-
LATE THE BATTERY NEGATIVE (GROUND) CABLE,
THEN WAIT TWO MINUTES FOR THE AIRBAG SYS-
TEM CAPACITOR TO DISCHARGE BEFORE PER-
FORMING FURTHER DIAGNOSIS OR SERVICE. THIS
IS THE ONLY SURE WAY TO DISABLE THE AIRBAG
SYSTEM. FAILURE TO TAKE THE PROPER PRE-
CAUTIONS COULD RESULT IN AN ACCIDENTAL
AIRBAG DEPLOYMENT AND POSSIBLE PERSONAL
INJURY.
Fig. 26 PANEL/DEFROST DOOR ACTUATOR
1 - VACUUM LINE
2 - PANEL/DEFROST ACTUATOR
3 - SHAFT RETAINER
BR/BECONTROLS 24 - 27
MODE DOOR ACTUATOR (Continued)
Page 2757 of 2889
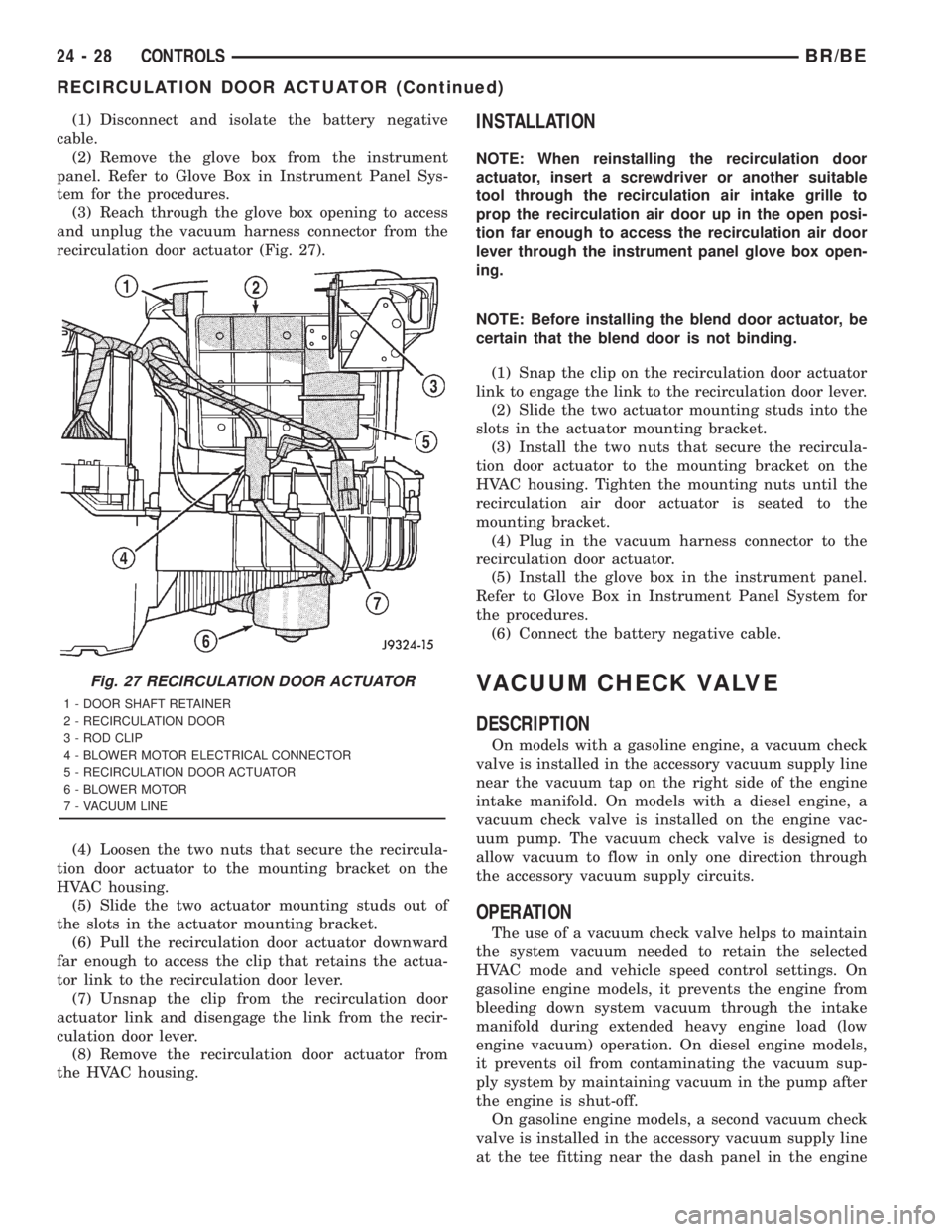
(1) Disconnect and isolate the battery negative
cable.
(2) Remove the glove box from the instrument
panel. Refer to Glove Box in Instrument Panel Sys-
tem for the procedures.
(3) Reach through the glove box opening to access
and unplug the vacuum harness connector from the
recirculation door actuator (Fig. 27).
(4) Loosen the two nuts that secure the recircula-
tion door actuator to the mounting bracket on the
HVAC housing.
(5) Slide the two actuator mounting studs out of
the slots in the actuator mounting bracket.
(6) Pull the recirculation door actuator downward
far enough to access the clip that retains the actua-
tor link to the recirculation door lever.
(7) Unsnap the clip from the recirculation door
actuator link and disengage the link from the recir-
culation door lever.
(8) Remove the recirculation door actuator from
the HVAC housing.INSTALLATION
NOTE: When reinstalling the recirculation door
actuator, insert a screwdriver or another suitable
tool through the recirculation air intake grille to
prop the recirculation air door up in the open posi-
tion far enough to access the recirculation air door
lever through the instrument panel glove box open-
ing.
NOTE: Before installing the blend door actuator, be
certain that the blend door is not binding.
(1) Snap the clip on the recirculation door actuator
link to engage the link to the recirculation door lever.
(2) Slide the two actuator mounting studs into the
slots in the actuator mounting bracket.
(3) Install the two nuts that secure the recircula-
tion door actuator to the mounting bracket on the
HVAC housing. Tighten the mounting nuts until the
recirculation air door actuator is seated to the
mounting bracket.
(4) Plug in the vacuum harness connector to the
recirculation door actuator.
(5) Install the glove box in the instrument panel.
Refer to Glove Box in Instrument Panel System for
the procedures.
(6) Connect the battery negative cable.
VACUUM CHECK VALVE
DESCRIPTION
On models with a gasoline engine, a vacuum check
valve is installed in the accessory vacuum supply line
near the vacuum tap on the right side of the engine
intake manifold. On models with a diesel engine, a
vacuum check valve is installed on the engine vac-
uum pump. The vacuum check valve is designed to
allow vacuum to flow in only one direction through
the accessory vacuum supply circuits.
OPERATION
The use of a vacuum check valve helps to maintain
the system vacuum needed to retain the selected
HVAC mode and vehicle speed control settings. On
gasoline engine models, it prevents the engine from
bleeding down system vacuum through the intake
manifold during extended heavy engine load (low
engine vacuum) operation. On diesel engine models,
it prevents oil from contaminating the vacuum sup-
ply system by maintaining vacuum in the pump after
the engine is shut-off.
On gasoline engine models, a second vacuum check
valve is installed in the accessory vacuum supply line
at the tee fitting near the dash panel in the engine
Fig. 27 RECIRCULATION DOOR ACTUATOR
1 - DOOR SHAFT RETAINER
2 - RECIRCULATION DOOR
3 - ROD CLIP
4 - BLOWER MOTOR ELECTRICAL CONNECTOR
5 - RECIRCULATION DOOR ACTUATOR
6 - BLOWER MOTOR
7 - VACUUM LINE
24 - 28 CONTROLSBR/BE
RECIRCULATION DOOR ACTUATOR (Continued)
Page 2758 of 2889
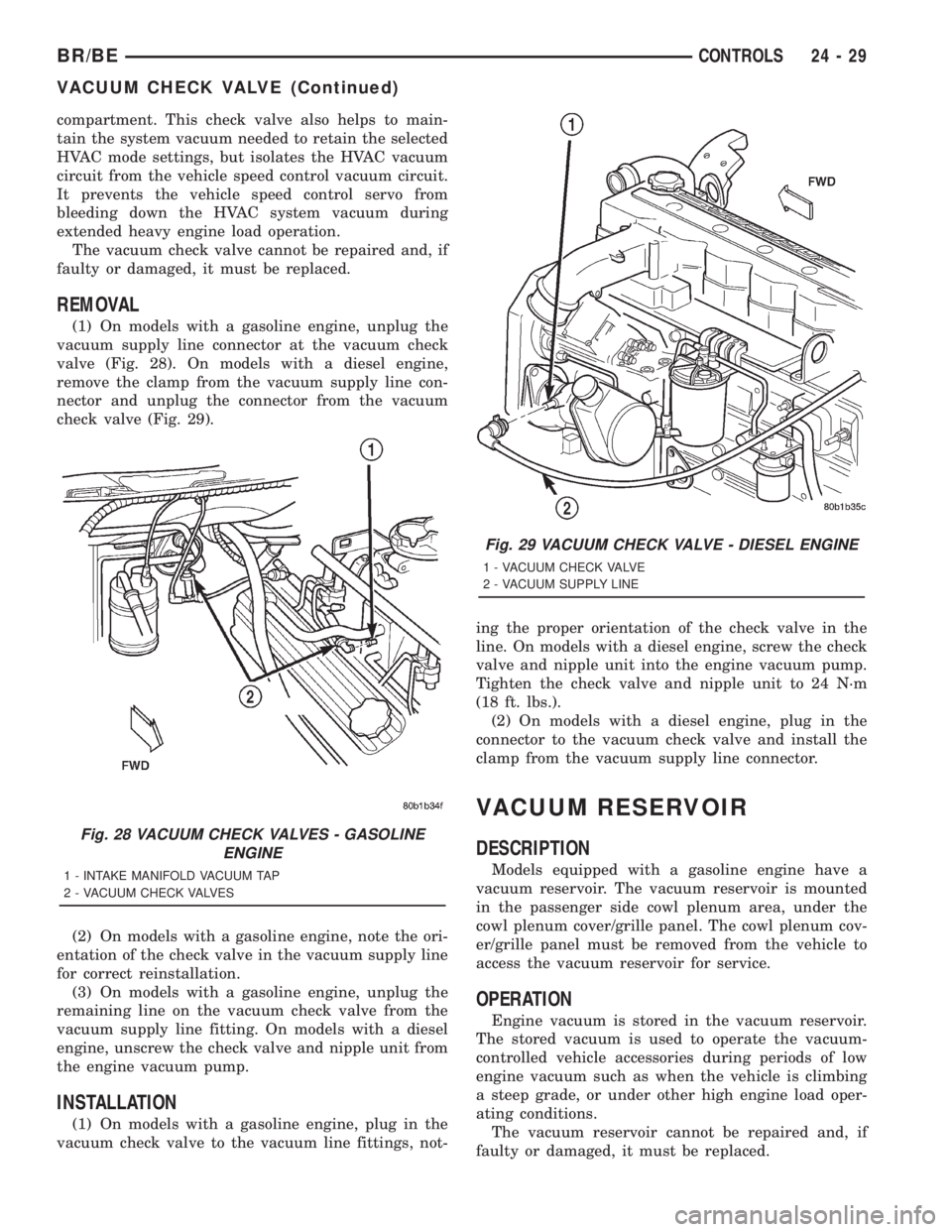
compartment. This check valve also helps to main-
tain the system vacuum needed to retain the selected
HVAC mode settings, but isolates the HVAC vacuum
circuit from the vehicle speed control vacuum circuit.
It prevents the vehicle speed control servo from
bleeding down the HVAC system vacuum during
extended heavy engine load operation.
The vacuum check valve cannot be repaired and, if
faulty or damaged, it must be replaced.
REMOVAL
(1) On models with a gasoline engine, unplug the
vacuum supply line connector at the vacuum check
valve (Fig. 28). On models with a diesel engine,
remove the clamp from the vacuum supply line con-
nector and unplug the connector from the vacuum
check valve (Fig. 29).
(2) On models with a gasoline engine, note the ori-
entation of the check valve in the vacuum supply line
for correct reinstallation.
(3) On models with a gasoline engine, unplug the
remaining line on the vacuum check valve from the
vacuum supply line fitting. On models with a diesel
engine, unscrew the check valve and nipple unit from
the engine vacuum pump.
INSTALLATION
(1) On models with a gasoline engine, plug in the
vacuum check valve to the vacuum line fittings, not-ing the proper orientation of the check valve in the
line. On models with a diesel engine, screw the check
valve and nipple unit into the engine vacuum pump.
Tighten the check valve and nipple unit to 24 N´m
(18 ft. lbs.).
(2) On models with a diesel engine, plug in the
connector to the vacuum check valve and install the
clamp from the vacuum supply line connector.
VACUUM RESERVOIR
DESCRIPTION
Models equipped with a gasoline engine have a
vacuum reservoir. The vacuum reservoir is mounted
in the passenger side cowl plenum area, under the
cowl plenum cover/grille panel. The cowl plenum cov-
er/grille panel must be removed from the vehicle to
access the vacuum reservoir for service.
OPERATION
Engine vacuum is stored in the vacuum reservoir.
The stored vacuum is used to operate the vacuum-
controlled vehicle accessories during periods of low
engine vacuum such as when the vehicle is climbing
a steep grade, or under other high engine load oper-
ating conditions.
The vacuum reservoir cannot be repaired and, if
faulty or damaged, it must be replaced.
Fig. 28 VACUUM CHECK VALVES - GASOLINE
ENGINE
1 - INTAKE MANIFOLD VACUUM TAP
2 - VACUUM CHECK VALVES
Fig. 29 VACUUM CHECK VALVE - DIESEL ENGINE
1 - VACUUM CHECK VALVE
2 - VACUUM SUPPLY LINE
BR/BECONTROLS 24 - 29
VACUUM CHECK VALVE (Continued)
Page 2759 of 2889
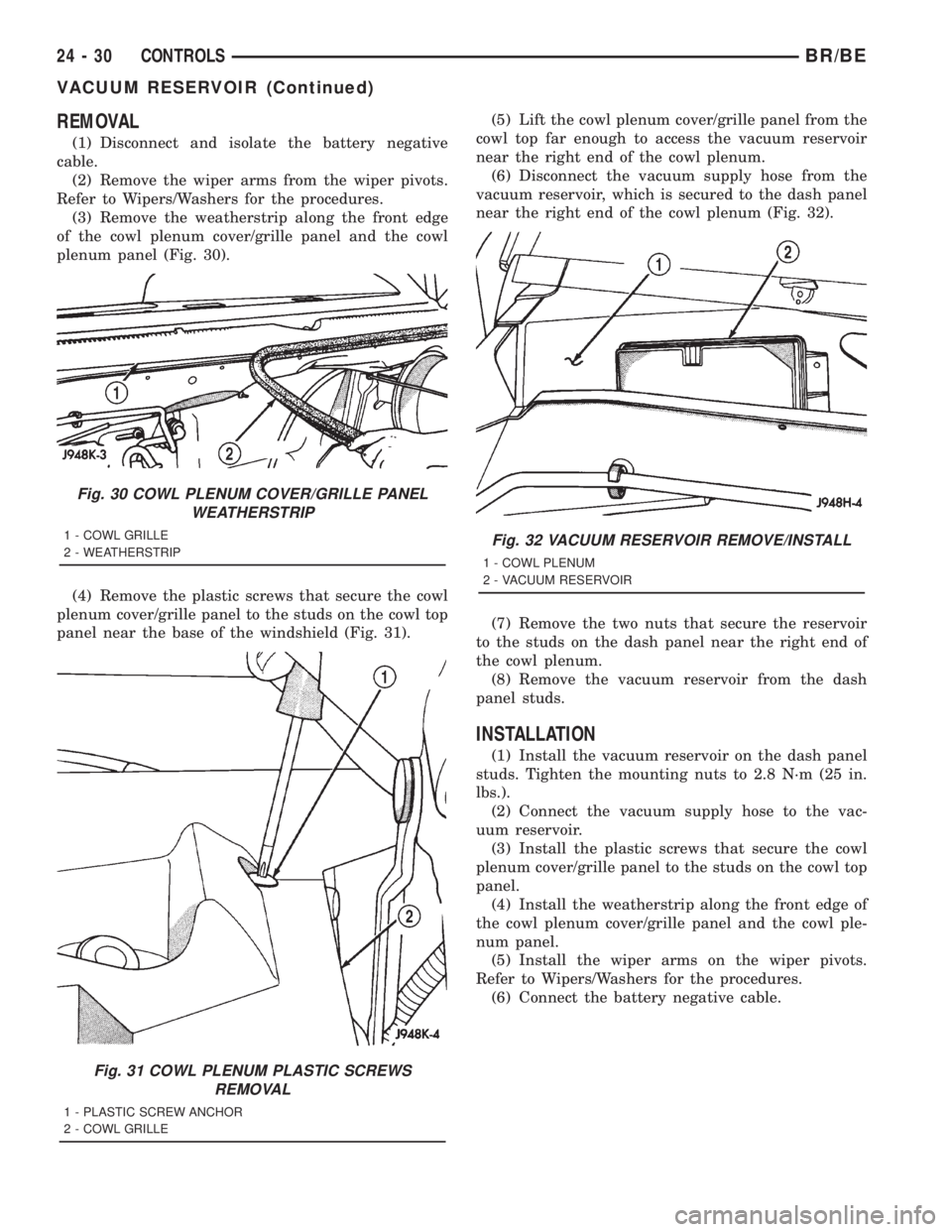
REMOVAL
(1) Disconnect and isolate the battery negative
cable.
(2) Remove the wiper arms from the wiper pivots.
Refer to Wipers/Washers for the procedures.
(3) Remove the weatherstrip along the front edge
of the cowl plenum cover/grille panel and the cowl
plenum panel (Fig. 30).
(4) Remove the plastic screws that secure the cowl
plenum cover/grille panel to the studs on the cowl top
panel near the base of the windshield (Fig. 31).(5) Lift the cowl plenum cover/grille panel from the
cowl top far enough to access the vacuum reservoir
near the right end of the cowl plenum.
(6) Disconnect the vacuum supply hose from the
vacuum reservoir, which is secured to the dash panel
near the right end of the cowl plenum (Fig. 32).
(7) Remove the two nuts that secure the reservoir
to the studs on the dash panel near the right end of
the cowl plenum.
(8) Remove the vacuum reservoir from the dash
panel studs.
INSTALLATION
(1) Install the vacuum reservoir on the dash panel
studs. Tighten the mounting nuts to 2.8 N´m (25 in.
lbs.).
(2) Connect the vacuum supply hose to the vac-
uum reservoir.
(3) Install the plastic screws that secure the cowl
plenum cover/grille panel to the studs on the cowl top
panel.
(4) Install the weatherstrip along the front edge of
the cowl plenum cover/grille panel and the cowl ple-
num panel.
(5) Install the wiper arms on the wiper pivots.
Refer to Wipers/Washers for the procedures.
(6) Connect the battery negative cable.
Fig. 30 COWL PLENUM COVER/GRILLE PANEL
WEATHERSTRIP
1 - COWL GRILLE
2 - WEATHERSTRIP
Fig. 31 COWL PLENUM PLASTIC SCREWS
REMOVAL
1 - PLASTIC SCREW ANCHOR
2 - COWL GRILLE
Fig. 32 VACUUM RESERVOIR REMOVE/INSTALL
1 - COWL PLENUM
2 - VACUUM RESERVOIR
24 - 30 CONTROLSBR/BE
VACUUM RESERVOIR (Continued)
Page 2760 of 2889
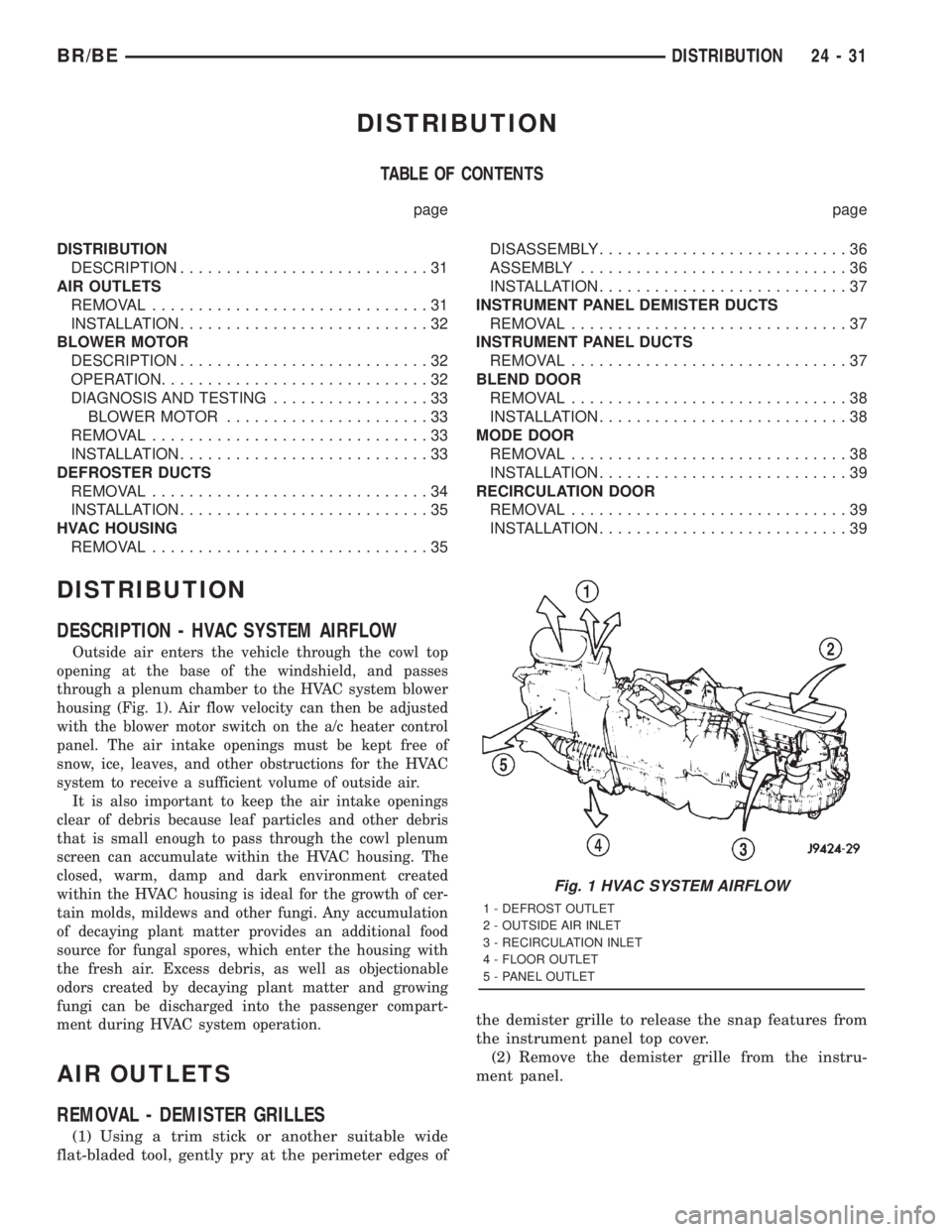
DISTRIBUTION
TABLE OF CONTENTS
page page
DISTRIBUTION
DESCRIPTION...........................31
AIR OUTLETS
REMOVAL..............................31
INSTALLATION...........................32
BLOWER MOTOR
DESCRIPTION...........................32
OPERATION.............................32
DIAGNOSIS AND TESTING.................33
BLOWER MOTOR......................33
REMOVAL..............................33
INSTALLATION...........................33
DEFROSTER DUCTS
REMOVAL..............................34
INSTALLATION...........................35
HVAC HOUSING
REMOVAL..............................35DISASSEMBLY...........................36
ASSEMBLY.............................36
INSTALLATION...........................37
INSTRUMENT PANEL DEMISTER DUCTS
REMOVAL..............................37
INSTRUMENT PANEL DUCTS
REMOVAL..............................37
BLEND DOOR
REMOVAL..............................38
INSTALLATION...........................38
MODE DOOR
REMOVAL..............................38
INSTALLATION...........................39
RECIRCULATION DOOR
REMOVAL..............................39
INSTALLATION...........................39
DISTRIBUTION
DESCRIPTION - HVAC SYSTEM AIRFLOW
Outside air enters the vehicle through the cowl top
opening at the base of the windshield, and passes
through a plenum chamber to the HVAC system blower
housing (Fig. 1). Air flow velocity can then be adjusted
with the blower motor switch on the a/c heater control
panel. The air intake openings must be kept free of
snow, ice, leaves, and other obstructions for the HVAC
system to receive a sufficient volume of outside air.
It is also important to keep the air intake openings
clear of debris because leaf particles and other debris
that is small enough to pass through the cowl plenum
screen can accumulate within the HVAC housing. The
closed, warm, damp and dark environment created
within the HVAC housing is ideal for the growth of cer-
tain molds, mildews and other fungi. Any accumulation
of decaying plant matter provides an additional food
source for fungal spores, which enter the housing with
the fresh air. Excess debris, as well as objectionable
odors created by decaying plant matter and growing
fungi can be discharged into the passenger compart-
ment during HVAC system operation.
AIR OUTLETS
REMOVAL - DEMISTER GRILLES
(1) Using a trim stick or another suitable wide
flat-bladed tool, gently pry at the perimeter edges ofthe demister grille to release the snap features from
the instrument panel top cover.
(2) Remove the demister grille from the instru-
ment panel.
Fig. 1 HVAC SYSTEM AIRFLOW
1 - DEFROST OUTLET
2 - OUTSIDE AIR INLET
3 - RECIRCULATION INLET
4 - FLOOR OUTLET
5 - PANEL OUTLET
BR/BEDISTRIBUTION 24 - 31