DODGE RAM 2002 Service Repair Manual
Manufacturer: DODGE, Model Year: 2002, Model line: RAM, Model: DODGE RAM 2002Pages: 2255, PDF Size: 62.07 MB
Page 1451 of 2255
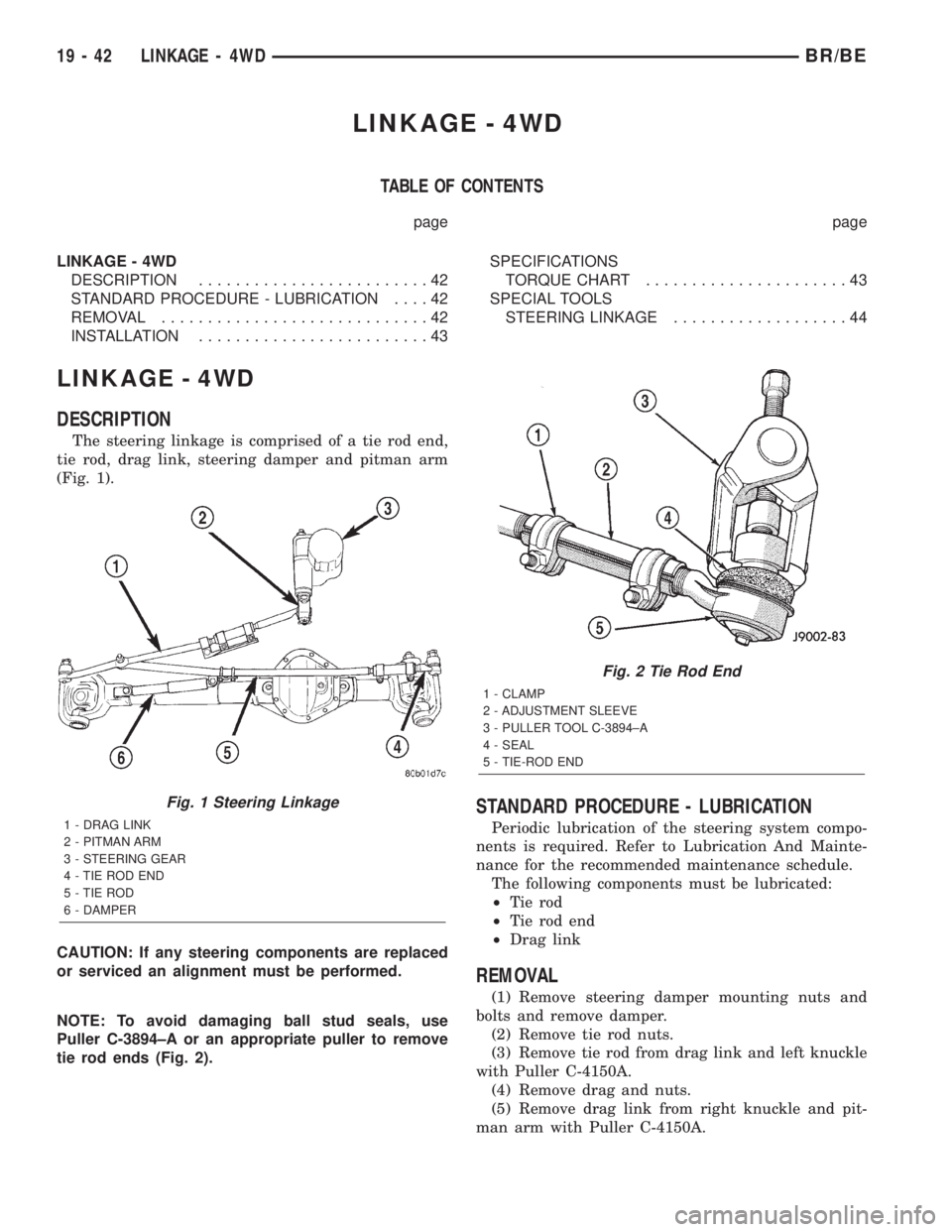
LINKAGE - 4WD
TABLE OF CONTENTS
page page
LINKAGE - 4WD
DESCRIPTION.........................42
STANDARD PROCEDURE - LUBRICATION....42
REMOVAL.............................42
INSTALLATION.........................43SPECIFICATIONS
TORQUE CHART......................43
SPECIAL TOOLS
STEERING LINKAGE...................44
LINKAGE - 4WD
DESCRIPTION
The steering linkage is comprised of a tie rod end,
tie rod, drag link, steering damper and pitman arm
(Fig. 1).
CAUTION: If any steering components are replaced
or serviced an alignment must be performed.
NOTE: To avoid damaging ball stud seals, use
Puller C-3894±A or an appropriate puller to remove
tie rod ends (Fig. 2).
STANDARD PROCEDURE - LUBRICATION
Periodic lubrication of the steering system compo-
nents is required. Refer to Lubrication And Mainte-
nance for the recommended maintenance schedule.
The following components must be lubricated:
²Tie rod
²Tie rod end
²Drag link
REMOVAL
(1) Remove steering damper mounting nuts and
bolts and remove damper.
(2) Remove tie rod nuts.
(3) Remove tie rod from drag link and left knuckle
with Puller C-4150A.
(4) Remove drag and nuts.
(5) Remove drag link from right knuckle and pit-
man arm with Puller C-4150A.
Fig. 1 Steering Linkage
1 - DRAG LINK
2 - PITMAN ARM
3 - STEERING GEAR
4 - TIE ROD END
5 - TIE ROD
6 - DAMPER
Fig. 2 Tie Rod End
1 - CLAMP
2 - ADJUSTMENT SLEEVE
3 - PULLER TOOL C-3894±A
4 - SEAL
5 - TIE-ROD END
19 - 42 LINKAGE - 4WDBR/BE
Page 1452 of 2255
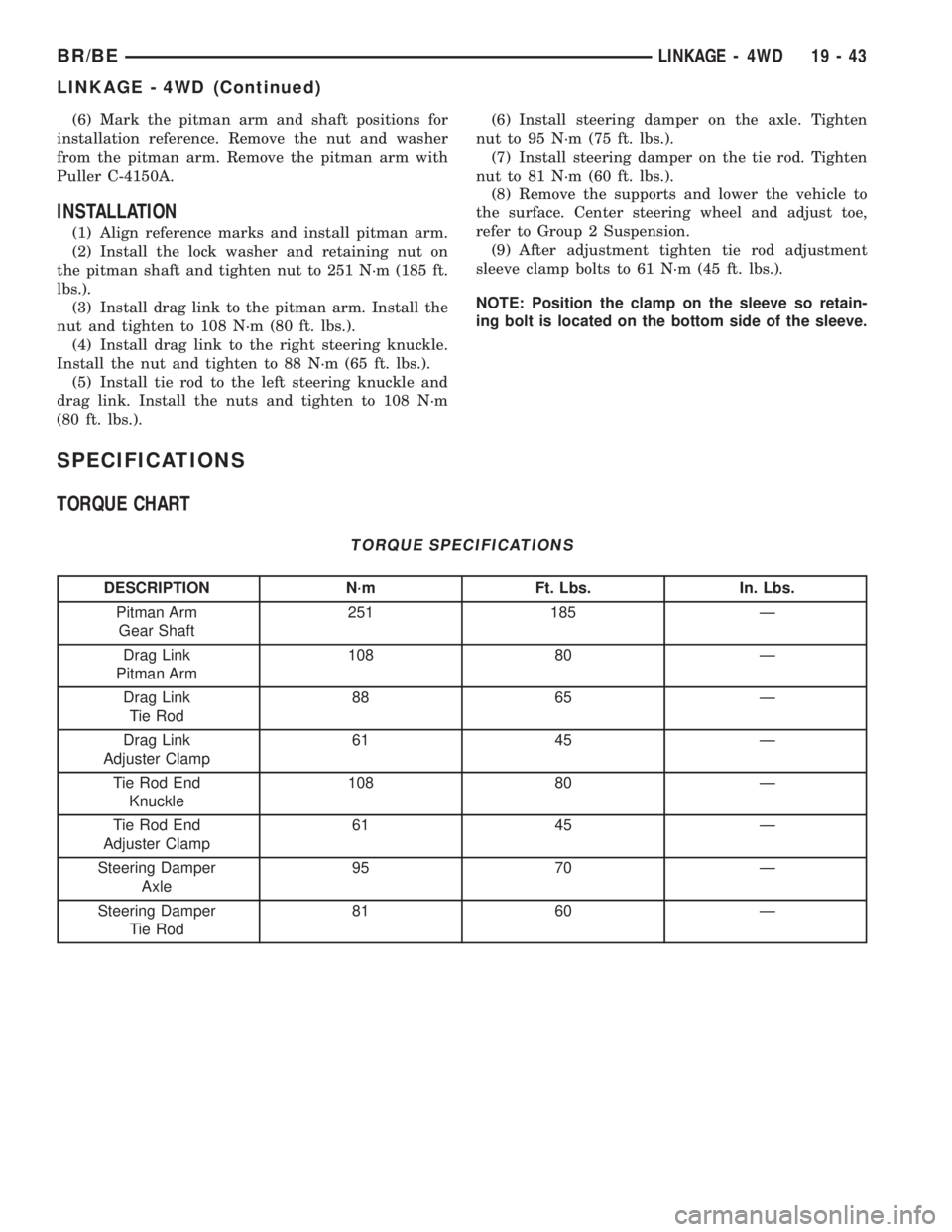
(6) Mark the pitman arm and shaft positions for
installation reference. Remove the nut and washer
from the pitman arm. Remove the pitman arm with
Puller C-4150A.
INSTALLATION
(1) Align reference marks and install pitman arm.
(2) Install the lock washer and retaining nut on
the pitman shaft and tighten nut to 251 N´m (185 ft.
lbs.).
(3) Install drag link to the pitman arm. Install the
nut and tighten to 108 N´m (80 ft. lbs.).
(4) Install drag link to the right steering knuckle.
Install the nut and tighten to 88 N´m (65 ft. lbs.).
(5) Install tie rod to the left steering knuckle and
drag link. Install the nuts and tighten to 108 N´m
(80 ft. lbs.).(6) Install steering damper on the axle. Tighten
nut to 95 N´m (75 ft. lbs.).
(7) Install steering damper on the tie rod. Tighten
nut to 81 N´m (60 ft. lbs.).
(8) Remove the supports and lower the vehicle to
the surface. Center steering wheel and adjust toe,
refer to Group 2 Suspension.
(9) After adjustment tighten tie rod adjustment
sleeve clamp bolts to 61 N´m (45 ft. lbs.).
NOTE: Position the clamp on the sleeve so retain-
ing bolt is located on the bottom side of the sleeve.
SPECIFICATIONS
TORQUE CHART
TORQUE SPECIFICATIONS
DESCRIPTION N´m Ft. Lbs. In. Lbs.
Pitman Arm
Gear Shaft251 185 Ð
Drag Link
Pitman Arm108 80 Ð
Drag Link
Tie Rod88 65 Ð
Drag Link
Adjuster Clamp61 45 Ð
Tie Rod End
Knuckle108 80 Ð
Tie Rod End
Adjuster Clamp61 45 Ð
Steering Damper
Axle95 70 Ð
Steering Damper
Tie Rod81 60 Ð
BR/BELINKAGE - 4WD 19 - 43
LINKAGE - 4WD (Continued)
Page 1453 of 2255
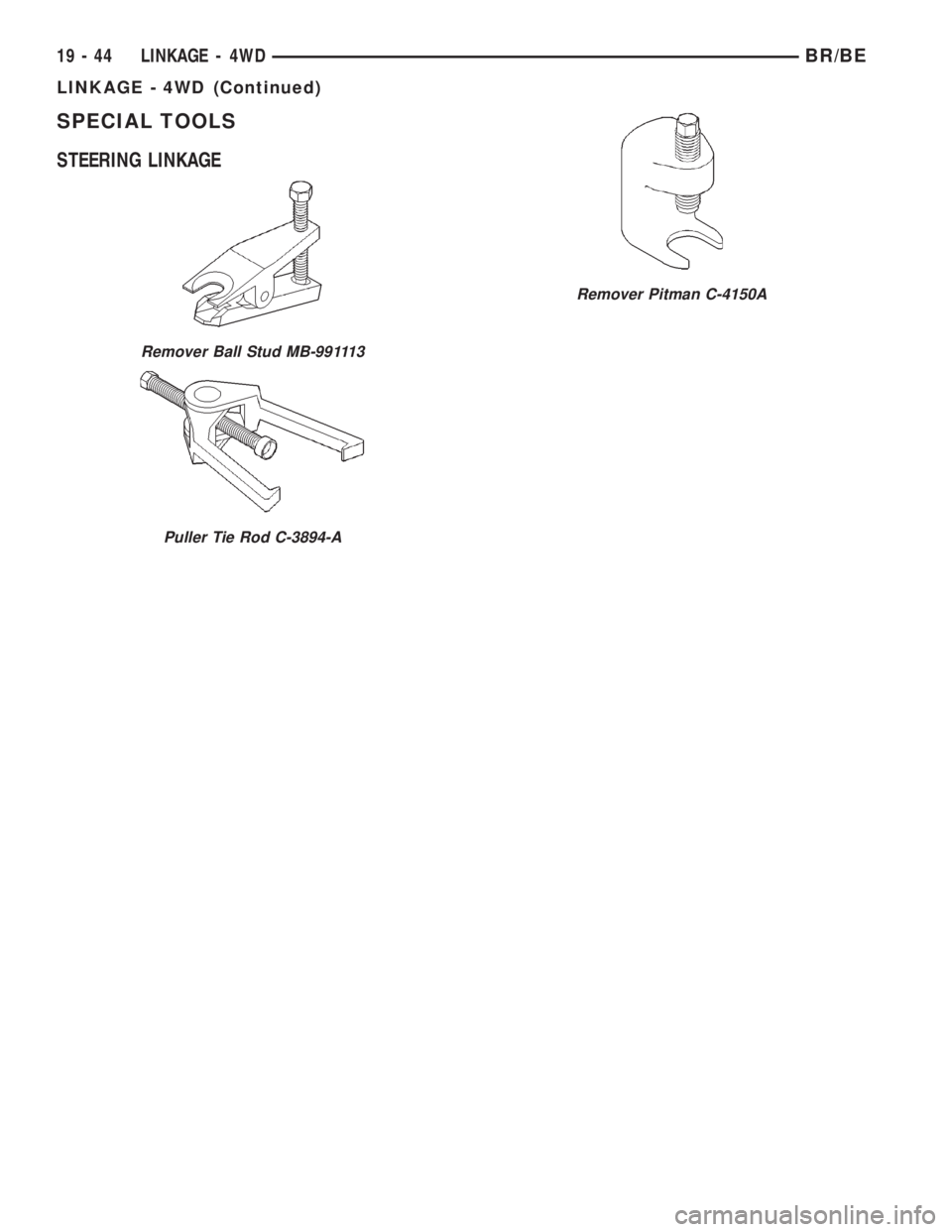
SPECIAL TOOLS
STEERING LINKAGE
Remover Ball Stud MB-991113
Puller Tie Rod C-3894-A
Remover Pitman C-4150A
19 - 44 LINKAGE - 4WDBR/BE
LINKAGE - 4WD (Continued)
Page 1454 of 2255
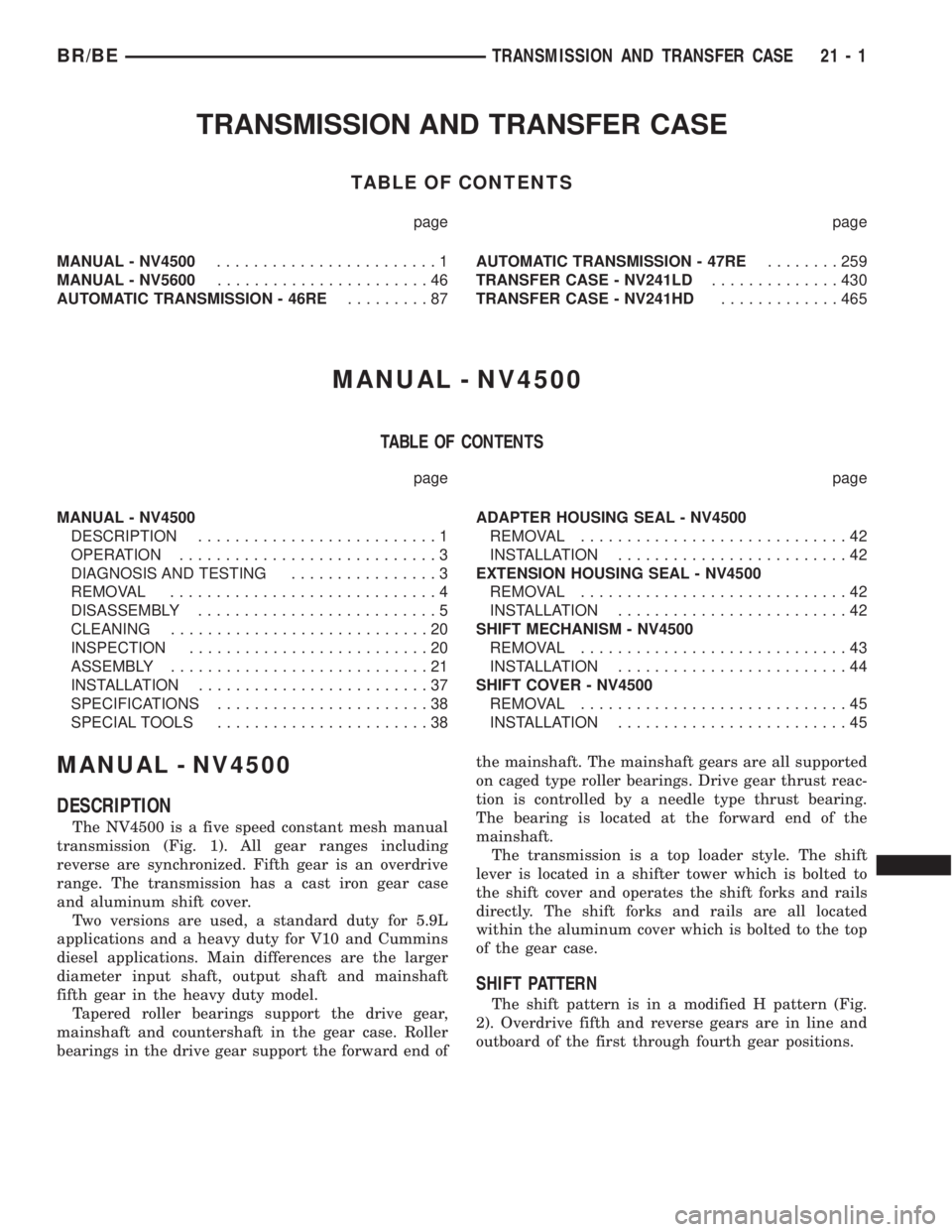
TRANSMISSION AND TRANSFER CASE
TABLE OF CONTENTS
page page
MANUAL - NV4500........................1
MANUAL - NV5600.......................46
AUTOMATIC TRANSMISSION - 46RE.........87AUTOMATIC TRANSMISSION - 47RE........259
TRANSFER CASE - NV241LD..............430
TRANSFER CASE - NV241HD.............465
MANUAL - NV4500
TABLE OF CONTENTS
page page
MANUAL - NV4500
DESCRIPTION..........................1
OPERATION............................3
DIAGNOSIS AND TESTING................3
REMOVAL.............................4
DISASSEMBLY..........................5
CLEANING............................20
INSPECTION..........................20
ASSEMBLY............................21
INSTALLATION.........................37
SPECIFICATIONS.......................38
SPECIAL TOOLS.......................38ADAPTER HOUSING SEAL - NV4500
REMOVAL.............................42
INSTALLATION.........................42
EXTENSION HOUSING SEAL - NV4500
REMOVAL.............................42
INSTALLATION.........................42
SHIFT MECHANISM - NV4500
REMOVAL.............................43
INSTALLATION.........................44
SHIFT COVER - NV4500
REMOVAL.............................45
INSTALLATION.........................45
MANUAL - NV4500
DESCRIPTION
The NV4500 is a five speed constant mesh manual
transmission (Fig. 1). All gear ranges including
reverse are synchronized. Fifth gear is an overdrive
range. The transmission has a cast iron gear case
and aluminum shift cover.
Two versions are used, a standard duty for 5.9L
applications and a heavy duty for V10 and Cummins
diesel applications. Main differences are the larger
diameter input shaft, output shaft and mainshaft
fifth gear in the heavy duty model.
Tapered roller bearings support the drive gear,
mainshaft and countershaft in the gear case. Roller
bearings in the drive gear support the forward end ofthe mainshaft. The mainshaft gears are all supported
on caged type roller bearings. Drive gear thrust reac-
tion is controlled by a needle type thrust bearing.
The bearing is located at the forward end of the
mainshaft.
The transmission is a top loader style. The shift
lever is located in a shifter tower which is bolted to
the shift cover and operates the shift forks and rails
directly. The shift forks and rails are all located
within the aluminum cover which is bolted to the top
of the gear case.
SHIFT PATTERN
The shift pattern is in a modified H pattern (Fig.
2). Overdrive fifth and reverse gears are in line and
outboard of the first through fourth gear positions.
BR/BETRANSMISSION AND TRANSFER CASE 21 - 1
Page 1455 of 2255
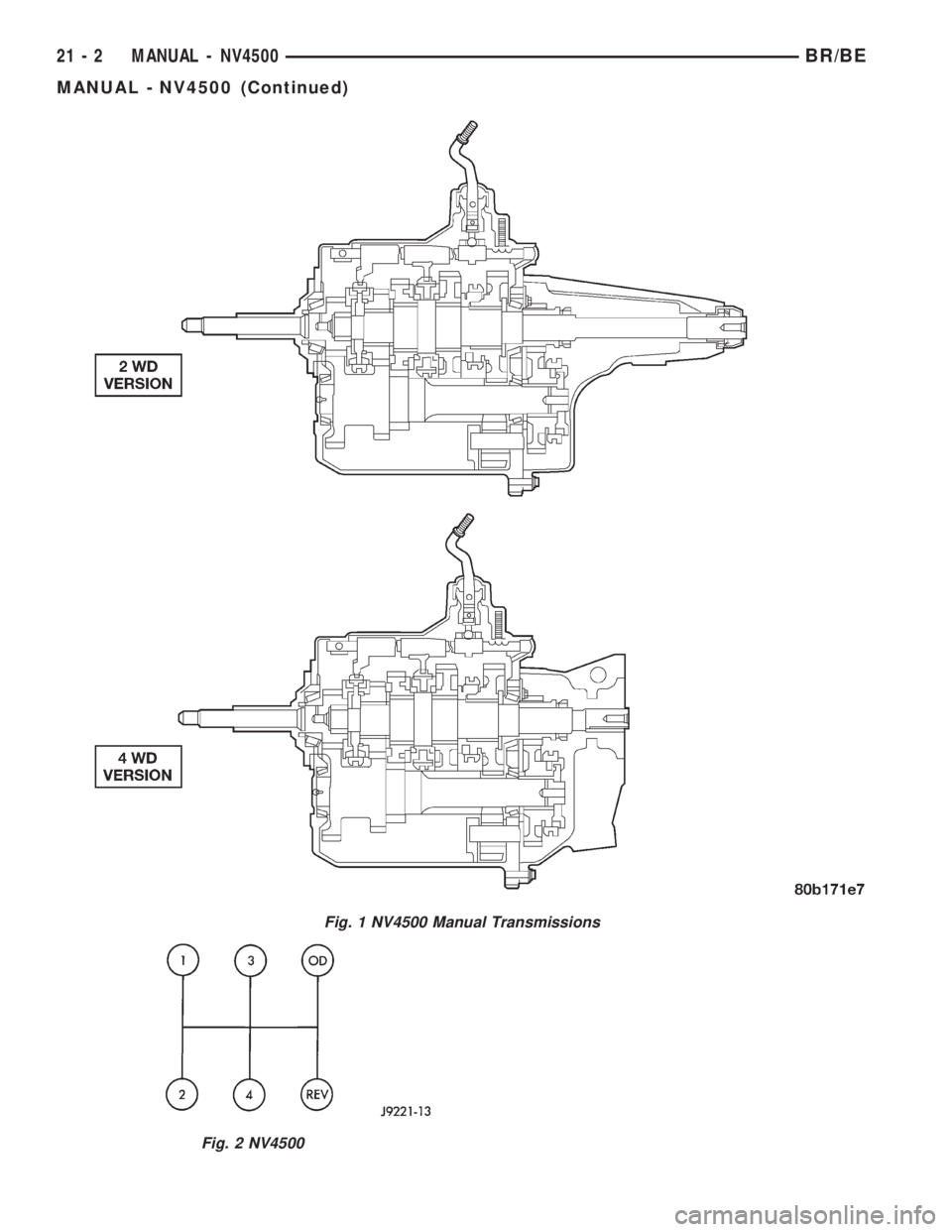
Fig. 1 NV4500 Manual Transmissions
Fig. 2 NV4500
21 - 2 MANUAL - NV4500BR/BE
MANUAL - NV4500 (Continued)
Page 1456 of 2255
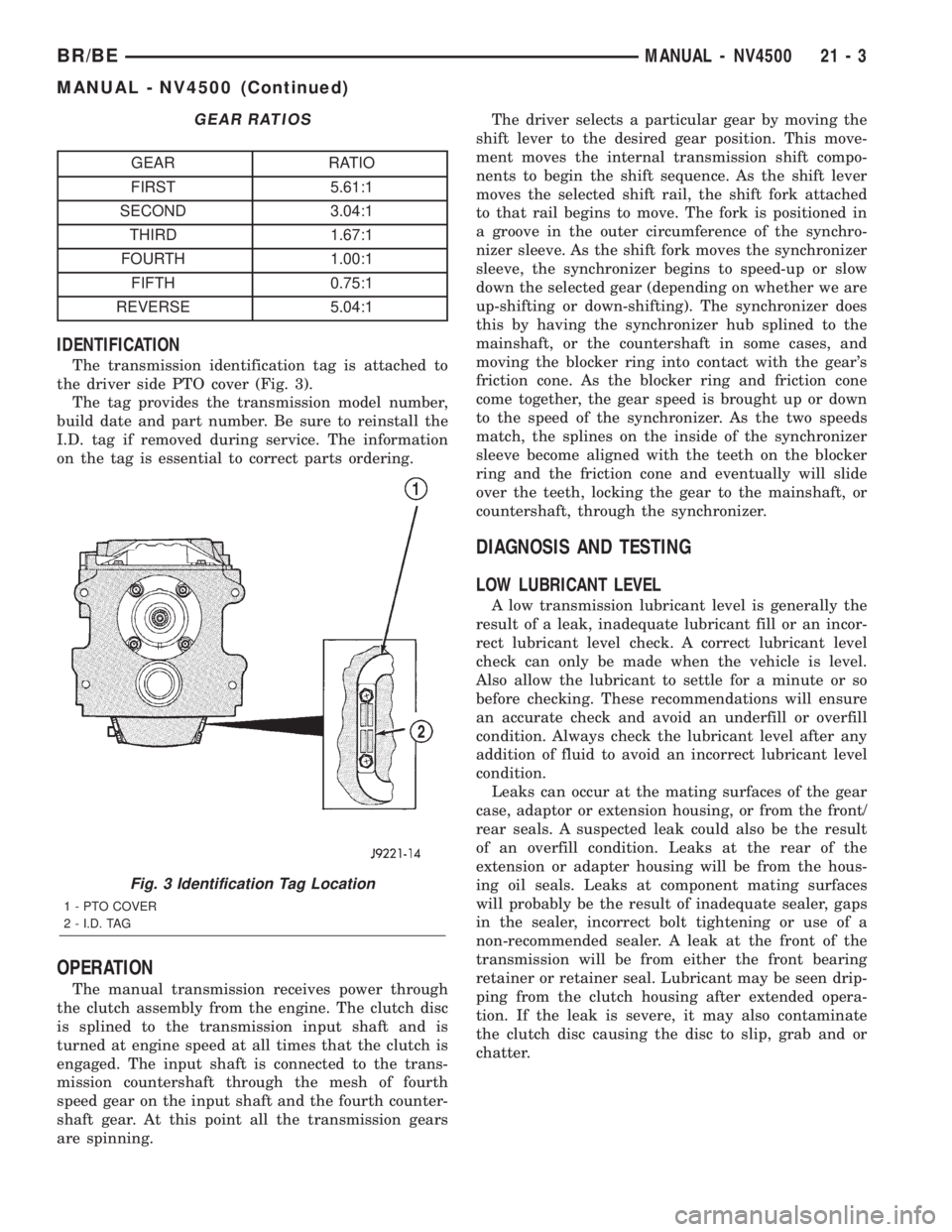
GEAR RATIOS
GEAR RATIO
FIRST 5.61:1
SECOND 3.04:1
THIRD 1.67:1
FOURTH 1.00:1
FIFTH 0.75:1
REVERSE 5.04:1
IDENTIFICATION
The transmission identification tag is attached to
the driver side PTO cover (Fig. 3).
The tag provides the transmission model number,
build date and part number. Be sure to reinstall the
I.D. tag if removed during service. The information
on the tag is essential to correct parts ordering.
OPERATION
The manual transmission receives power through
the clutch assembly from the engine. The clutch disc
is splined to the transmission input shaft and is
turned at engine speed at all times that the clutch is
engaged. The input shaft is connected to the trans-
mission countershaft through the mesh of fourth
speed gear on the input shaft and the fourth counter-
shaft gear. At this point all the transmission gears
are spinning.The driver selects a particular gear by moving the
shift lever to the desired gear position. This move-
ment moves the internal transmission shift compo-
nents to begin the shift sequence. As the shift lever
moves the selected shift rail, the shift fork attached
to that rail begins to move. The fork is positioned in
a groove in the outer circumference of the synchro-
nizer sleeve. As the shift fork moves the synchronizer
sleeve, the synchronizer begins to speed-up or slow
down the selected gear (depending on whether we are
up-shifting or down-shifting). The synchronizer does
this by having the synchronizer hub splined to the
mainshaft, or the countershaft in some cases, and
moving the blocker ring into contact with the gear's
friction cone. As the blocker ring and friction cone
come together, the gear speed is brought up or down
to the speed of the synchronizer. As the two speeds
match, the splines on the inside of the synchronizer
sleeve become aligned with the teeth on the blocker
ring and the friction cone and eventually will slide
over the teeth, locking the gear to the mainshaft, or
countershaft, through the synchronizer.
DIAGNOSIS AND TESTING
LOW LUBRICANT LEVEL
A low transmission lubricant level is generally the
result of a leak, inadequate lubricant fill or an incor-
rect lubricant level check. A correct lubricant level
check can only be made when the vehicle is level.
Also allow the lubricant to settle for a minute or so
before checking. These recommendations will ensure
an accurate check and avoid an underfill or overfill
condition. Always check the lubricant level after any
addition of fluid to avoid an incorrect lubricant level
condition.
Leaks can occur at the mating surfaces of the gear
case, adaptor or extension housing, or from the front/
rear seals. A suspected leak could also be the result
of an overfill condition. Leaks at the rear of the
extension or adapter housing will be from the hous-
ing oil seals. Leaks at component mating surfaces
will probably be the result of inadequate sealer, gaps
in the sealer, incorrect bolt tightening or use of a
non-recommended sealer. A leak at the front of the
transmission will be from either the front bearing
retainer or retainer seal. Lubricant may be seen drip-
ping from the clutch housing after extended opera-
tion. If the leak is severe, it may also contaminate
the clutch disc causing the disc to slip, grab and or
chatter.
Fig. 3 Identification Tag Location
1 - PTO COVER
2 - I.D. TAG
BR/BEMANUAL - NV4500 21 - 3
MANUAL - NV4500 (Continued)
Page 1457 of 2255
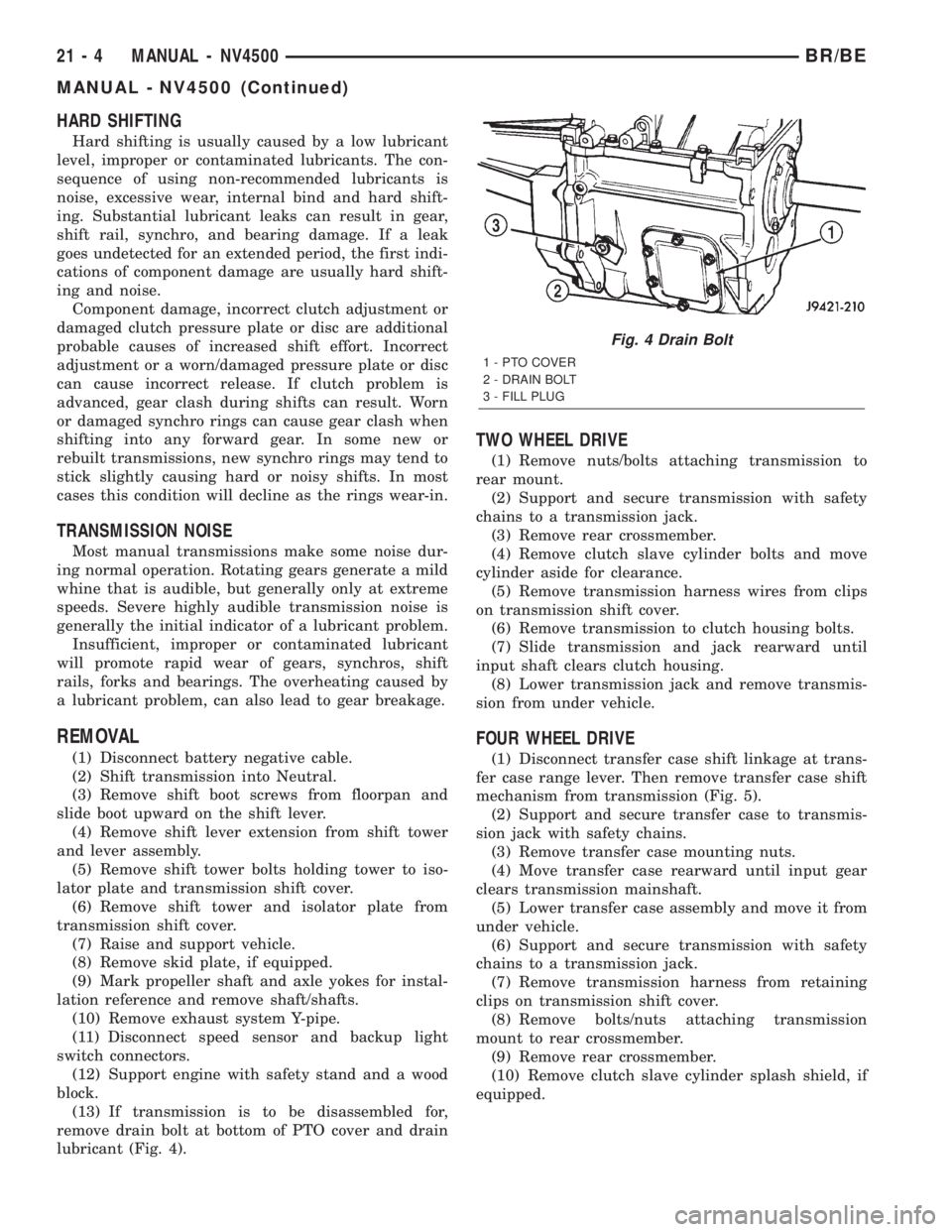
HARD SHIFTING
Hard shifting is usually caused by a low lubricant
level, improper or contaminated lubricants. The con-
sequence of using non-recommended lubricants is
noise, excessive wear, internal bind and hard shift-
ing. Substantial lubricant leaks can result in gear,
shift rail, synchro, and bearing damage. If a leak
goes undetected for an extended period, the first indi-
cations of component damage are usually hard shift-
ing and noise.
Component damage, incorrect clutch adjustment or
damaged clutch pressure plate or disc are additional
probable causes of increased shift effort. Incorrect
adjustment or a worn/damaged pressure plate or disc
can cause incorrect release. If clutch problem is
advanced, gear clash during shifts can result. Worn
or damaged synchro rings can cause gear clash when
shifting into any forward gear. In some new or
rebuilt transmissions, new synchro rings may tend to
stick slightly causing hard or noisy shifts. In most
cases this condition will decline as the rings wear-in.
TRANSMISSION NOISE
Most manual transmissions make some noise dur-
ing normal operation. Rotating gears generate a mild
whine that is audible, but generally only at extreme
speeds. Severe highly audible transmission noise is
generally the initial indicator of a lubricant problem.
Insufficient, improper or contaminated lubricant
will promote rapid wear of gears, synchros, shift
rails, forks and bearings. The overheating caused by
a lubricant problem, can also lead to gear breakage.
REMOVAL
(1) Disconnect battery negative cable.
(2) Shift transmission into Neutral.
(3) Remove shift boot screws from floorpan and
slide boot upward on the shift lever.
(4) Remove shift lever extension from shift tower
and lever assembly.
(5) Remove shift tower bolts holding tower to iso-
lator plate and transmission shift cover.
(6) Remove shift tower and isolator plate from
transmission shift cover.
(7) Raise and support vehicle.
(8) Remove skid plate, if equipped.
(9) Mark propeller shaft and axle yokes for instal-
lation reference and remove shaft/shafts.
(10) Remove exhaust system Y-pipe.
(11) Disconnect speed sensor and backup light
switch connectors.
(12) Support engine with safety stand and a wood
block.
(13) If transmission is to be disassembled for,
remove drain bolt at bottom of PTO cover and drain
lubricant (Fig. 4).
TWO WHEEL DRIVE
(1) Remove nuts/bolts attaching transmission to
rear mount.
(2) Support and secure transmission with safety
chains to a transmission jack.
(3) Remove rear crossmember.
(4) Remove clutch slave cylinder bolts and move
cylinder aside for clearance.
(5) Remove transmission harness wires from clips
on transmission shift cover.
(6) Remove transmission to clutch housing bolts.
(7) Slide transmission and jack rearward until
input shaft clears clutch housing.
(8) Lower transmission jack and remove transmis-
sion from under vehicle.
FOUR WHEEL DRIVE
(1) Disconnect transfer case shift linkage at trans-
fer case range lever. Then remove transfer case shift
mechanism from transmission (Fig. 5).
(2) Support and secure transfer case to transmis-
sion jack with safety chains.
(3) Remove transfer case mounting nuts.
(4) Move transfer case rearward until input gear
clears transmission mainshaft.
(5) Lower transfer case assembly and move it from
under vehicle.
(6) Support and secure transmission with safety
chains to a transmission jack.
(7) Remove transmission harness from retaining
clips on transmission shift cover.
(8) Remove bolts/nuts attaching transmission
mount to rear crossmember.
(9) Remove rear crossmember.
(10) Remove clutch slave cylinder splash shield, if
equipped.
Fig. 4 Drain Bolt
1 - PTO COVER
2 - DRAIN BOLT
3 - FILL PLUG
21 - 4 MANUAL - NV4500BR/BE
MANUAL - NV4500 (Continued)
Page 1458 of 2255
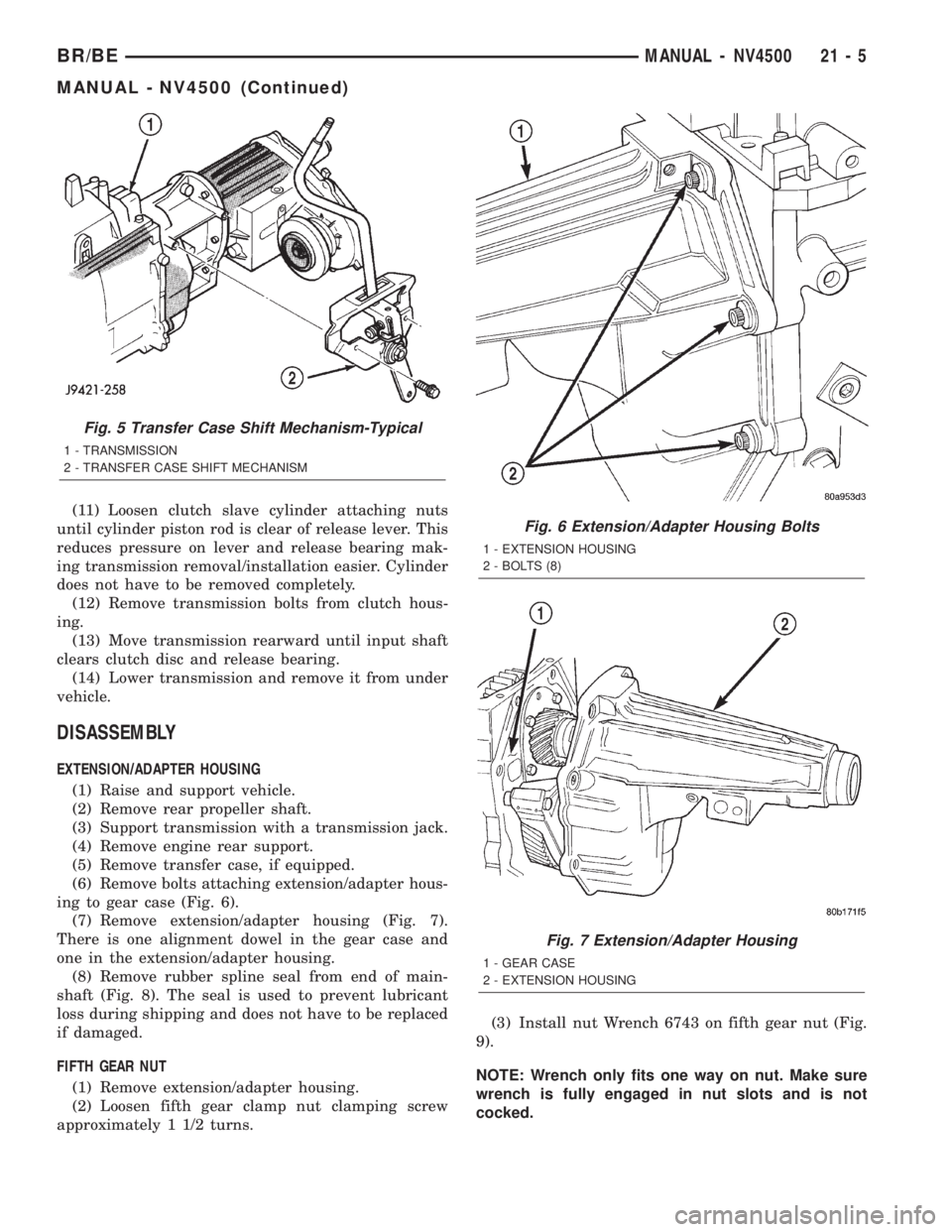
(11) Loosen clutch slave cylinder attaching nuts
until cylinder piston rod is clear of release lever. This
reduces pressure on lever and release bearing mak-
ing transmission removal/installation easier. Cylinder
does not have to be removed completely.
(12) Remove transmission bolts from clutch hous-
ing.
(13) Move transmission rearward until input shaft
clears clutch disc and release bearing.
(14) Lower transmission and remove it from under
vehicle.
DISASSEMBLY
EXTENSION/ADAPTER HOUSING
(1) Raise and support vehicle.
(2) Remove rear propeller shaft.
(3) Support transmission with a transmission jack.
(4) Remove engine rear support.
(5) Remove transfer case, if equipped.
(6) Remove bolts attaching extension/adapter hous-
ing to gear case (Fig. 6).
(7) Remove extension/adapter housing (Fig. 7).
There is one alignment dowel in the gear case and
one in the extension/adapter housing.
(8) Remove rubber spline seal from end of main-
shaft (Fig. 8). The seal is used to prevent lubricant
loss during shipping and does not have to be replaced
if damaged.
FIFTH GEAR NUT
(1) Remove extension/adapter housing.
(2) Loosen fifth gear clamp nut clamping screw
approximately 1 1/2 turns.(3) Install nut Wrench 6743 on fifth gear nut (Fig.
9).
NOTE: Wrench only fits one way on nut. Make sure
wrench is fully engaged in nut slots and is not
cocked.
Fig. 5 Transfer Case Shift Mechanism-Typical
1 - TRANSMISSION
2 - TRANSFER CASE SHIFT MECHANISM
Fig. 6 Extension/Adapter Housing Bolts
1 - EXTENSION HOUSING
2 - BOLTS (8)
Fig. 7 Extension/Adapter Housing
1 - GEAR CASE
2 - EXTENSION HOUSING
BR/BEMANUAL - NV4500 21 - 5
MANUAL - NV4500 (Continued)
Page 1459 of 2255
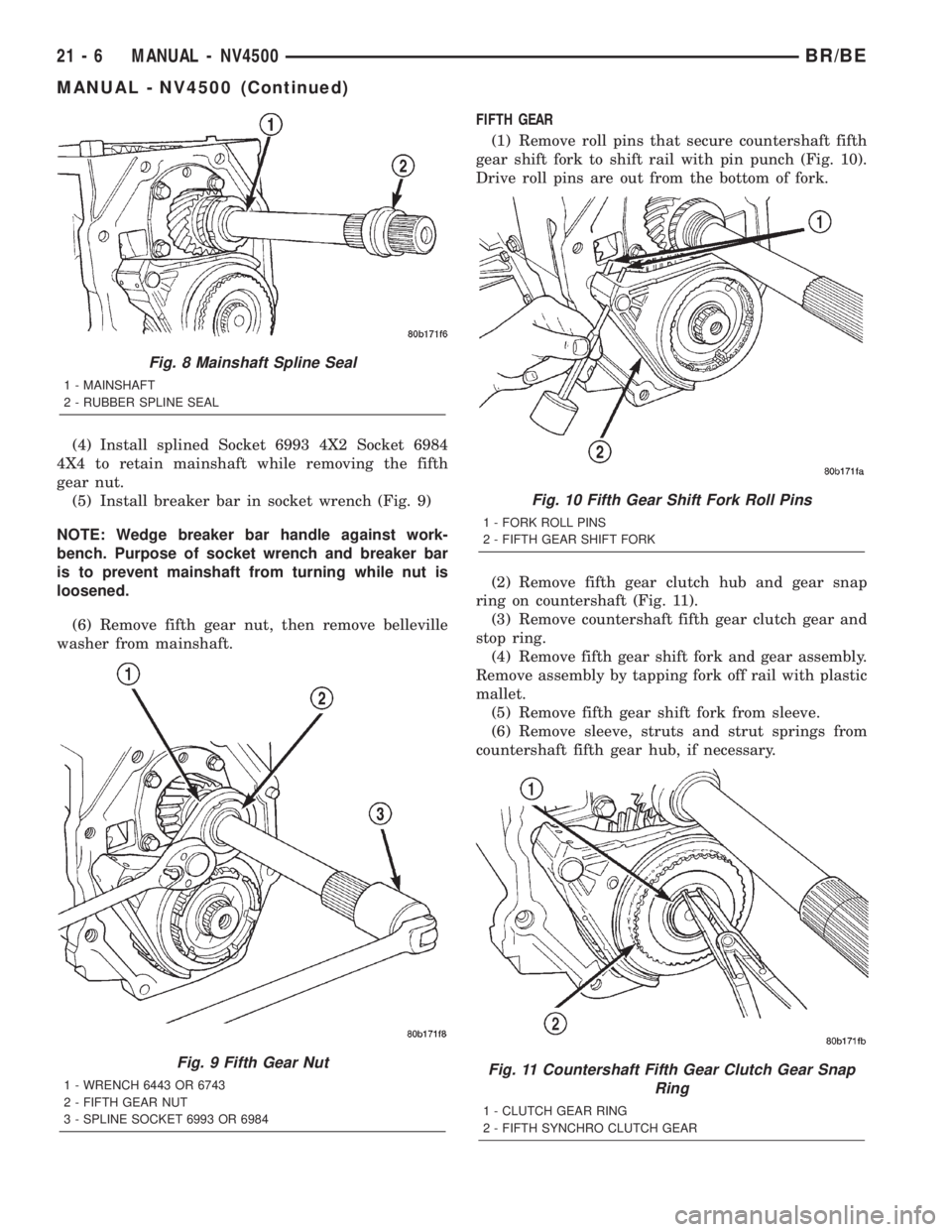
(4) Install splined Socket 6993 4X2 Socket 6984
4X4 to retain mainshaft while removing the fifth
gear nut.
(5) Install breaker bar in socket wrench (Fig. 9)
NOTE: Wedge breaker bar handle against work-
bench. Purpose of socket wrench and breaker bar
is to prevent mainshaft from turning while nut is
loosened.
(6) Remove fifth gear nut, then remove belleville
washer from mainshaft.FIFTH GEAR
(1) Remove roll pins that secure countershaft fifth
gear shift fork to shift rail with pin punch (Fig. 10).
Drive roll pins are out from the bottom of fork.
(2) Remove fifth gear clutch hub and gear snap
ring on countershaft (Fig. 11).
(3) Remove countershaft fifth gear clutch gear and
stop ring.
(4) Remove fifth gear shift fork and gear assembly.
Remove assembly by tapping fork off rail with plastic
mallet.
(5) Remove fifth gear shift fork from sleeve.
(6) Remove sleeve, struts and strut springs from
countershaft fifth gear hub, if necessary.
Fig. 8 Mainshaft Spline Seal
1 - MAINSHAFT
2 - RUBBER SPLINE SEAL
Fig. 9 Fifth Gear Nut
1 - WRENCH 6443 OR 6743
2 - FIFTH GEAR NUT
3 - SPLINE SOCKET 6993 OR 6984
Fig. 10 Fifth Gear Shift Fork Roll Pins
1 - FORK ROLL PINS
2 - FIFTH GEAR SHIFT FORK
Fig. 11 Countershaft Fifth Gear Clutch Gear Snap
Ring
1 - CLUTCH GEAR RING
2 - FIFTH SYNCHRO CLUTCH GEAR
21 - 6 MANUAL - NV4500BR/BE
MANUAL - NV4500 (Continued)
Page 1460 of 2255
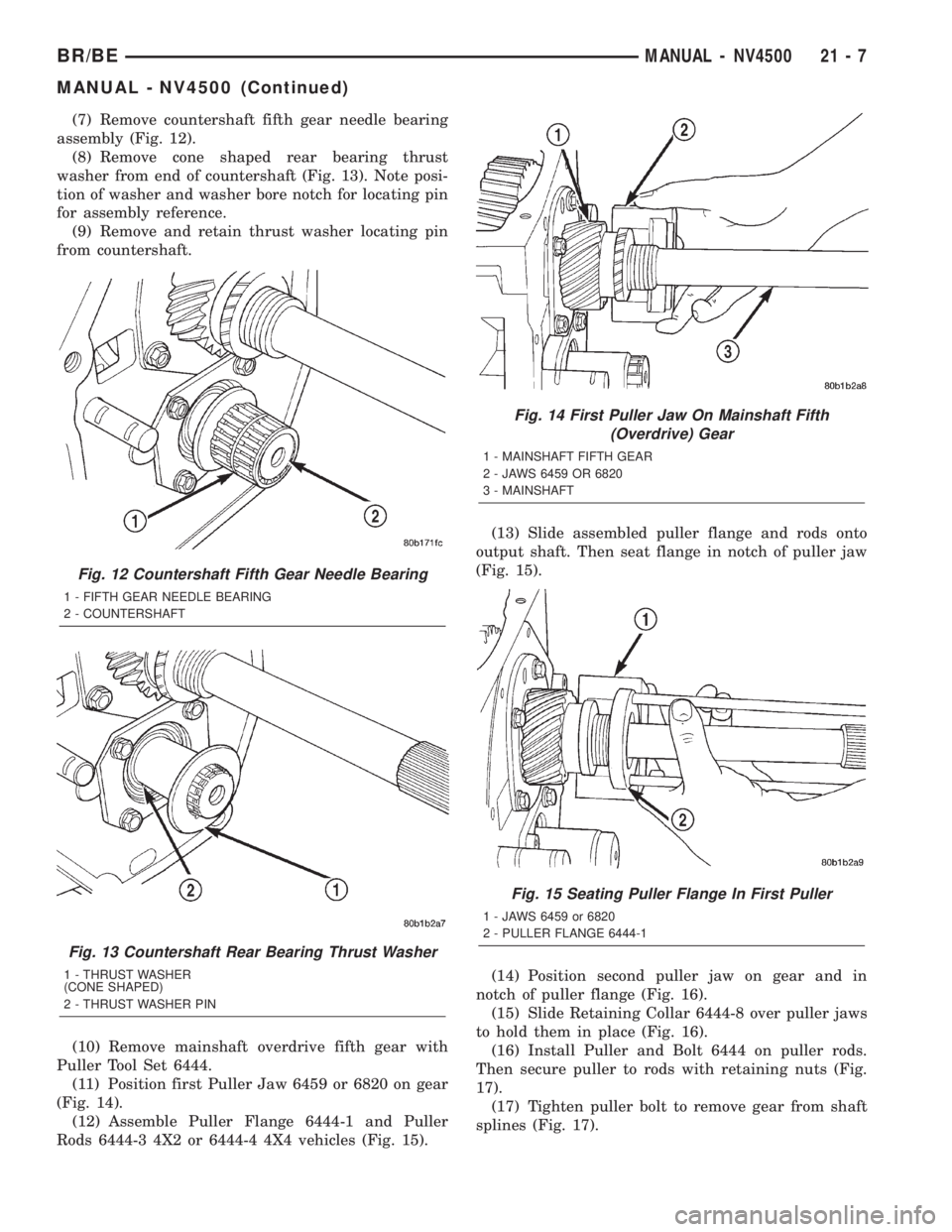
(7) Remove countershaft fifth gear needle bearing
assembly (Fig. 12).
(8) Remove cone shaped rear bearing thrust
washer from end of countershaft (Fig. 13). Note posi-
tion of washer and washer bore notch for locating pin
for assembly reference.
(9) Remove and retain thrust washer locating pin
from countershaft.
(10) Remove mainshaft overdrive fifth gear with
Puller Tool Set 6444.
(11) Position first Puller Jaw 6459 or 6820 on gear
(Fig. 14).
(12) Assemble Puller Flange 6444-1 and Puller
Rods 6444-3 4X2 or 6444-4 4X4 vehicles (Fig. 15).(13) Slide assembled puller flange and rods onto
output shaft. Then seat flange in notch of puller jaw
(Fig. 15).
(14) Position second puller jaw on gear and in
notch of puller flange (Fig. 16).
(15) Slide Retaining Collar 6444-8 over puller jaws
to hold them in place (Fig. 16).
(16) Install Puller and Bolt 6444 on puller rods.
Then secure puller to rods with retaining nuts (Fig.
17).
(17) Tighten puller bolt to remove gear from shaft
splines (Fig. 17).
Fig. 12 Countershaft Fifth Gear Needle Bearing
1 - FIFTH GEAR NEEDLE BEARING
2 - COUNTERSHAFT
Fig. 13 Countershaft Rear Bearing Thrust Washer
1 - THRUST WASHER
(CONE SHAPED)
2 - THRUST WASHER PIN
Fig. 14 First Puller Jaw On Mainshaft Fifth
(Overdrive) Gear
1 - MAINSHAFT FIFTH GEAR
2 - JAWS 6459 OR 6820
3 - MAINSHAFT
Fig. 15 Seating Puller Flange In First Puller
1 - JAWS 6459 or 6820
2 - PULLER FLANGE 6444-1
BR/BEMANUAL - NV4500 21 - 7
MANUAL - NV4500 (Continued)