DODGE TRUCK 1993 Service Repair Manual
Manufacturer: DODGE, Model Year: 1993, Model line: TRUCK, Model: DODGE TRUCK 1993Pages: 1502, PDF Size: 80.97 MB
Page 1451 of 1502
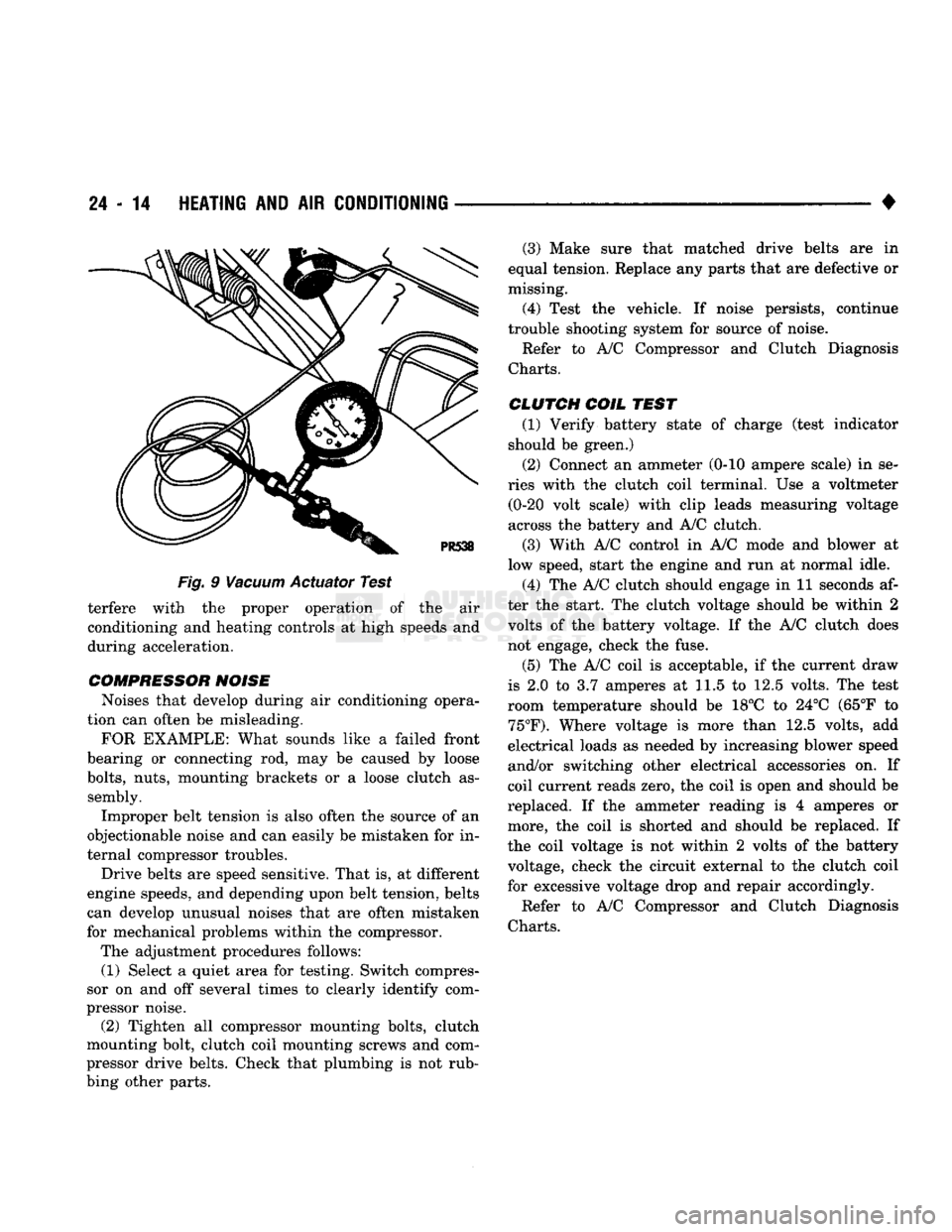
24 - 14
HEATING
AND AIR
CONDITIONING
•
Fig.
9
Vacuum
Actuator Test terfere with the proper operation of the air
conditioning and heating controls at high speeds and
during acceleration.
COMPRESSOR NOISE Noises that develop during air conditioning opera
tion can often be misleading.
FOR EXAMPLE: What sounds like a failed front
bearing or connecting rod, may be caused by loose
bolts,
nuts, mounting brackets or a loose clutch as sembly.
Improper belt tension is also often the source of an
objectionable noise and can easily be mistaken for in
ternal compressor troubles.
Drive belts are speed sensitive. That is, at different
engine speeds, and depending upon belt tension, belts
can develop unusual noises that are often mistaken
for mechanical problems within the compressor.
The adjustment procedures follows: (1) Select a quiet area for testing. Switch compres
sor on and off several times to clearly identify com
pressor noise. (2) Tighten all compressor mounting bolts, clutch
mounting bolt, clutch coil mounting screws and com
pressor drive belts. Check that plumbing is not rub
bing other parts. (3) Make sure that matched drive belts are in
equal tension. Replace any parts that are defective or
missing.
(4) Test the vehicle. If noise persists, continue
trouble shooting system for source of noise. Refer to A/C Compressor and Clutch Diagnosis
Charts.
CLUTCH COIL
TEST
(1) Verify battery state of charge (test indicator
should be green.)
(2) Connect an ammeter (0-10 ampere scale) in se
ries with the clutch coil terminal. Use a voltmeter (0-20 volt scale) with clip leads measuring voltage
across the battery and A/C clutch.
(3) With A/C control in A/C mode and blower at
low speed, start the engine and run at normal idle.
(4) The A/C clutch should engage in 11 seconds af
ter the start. The clutch voltage should be within 2
volts of the battery voltage. If the A/C clutch does not engage, check the fuse.
(5) The A/C coil is acceptable, if the current draw
is 2.0 to 3.7 amperes at 11.5 to 12.5 volts. The test
room temperature should be 18°C to 24°C (65°F to
75°F).
Where voltage is more than 12.5 volts, add
electrical loads as needed by increasing blower speed
and/or switching other electrical accessories on. If
coil current reads zero, the coil is open and should be
replaced. If the ammeter reading is 4 amperes or more, the coil is shorted and should be replaced. If
the coil voltage is not within 2 volts of the battery
voltage, check the circuit external to the clutch coil for excessive voltage drop and repair accordingly.
Refer to A/C Compressor and Clutch Diagnosis
Charts.
Page 1452 of 1502
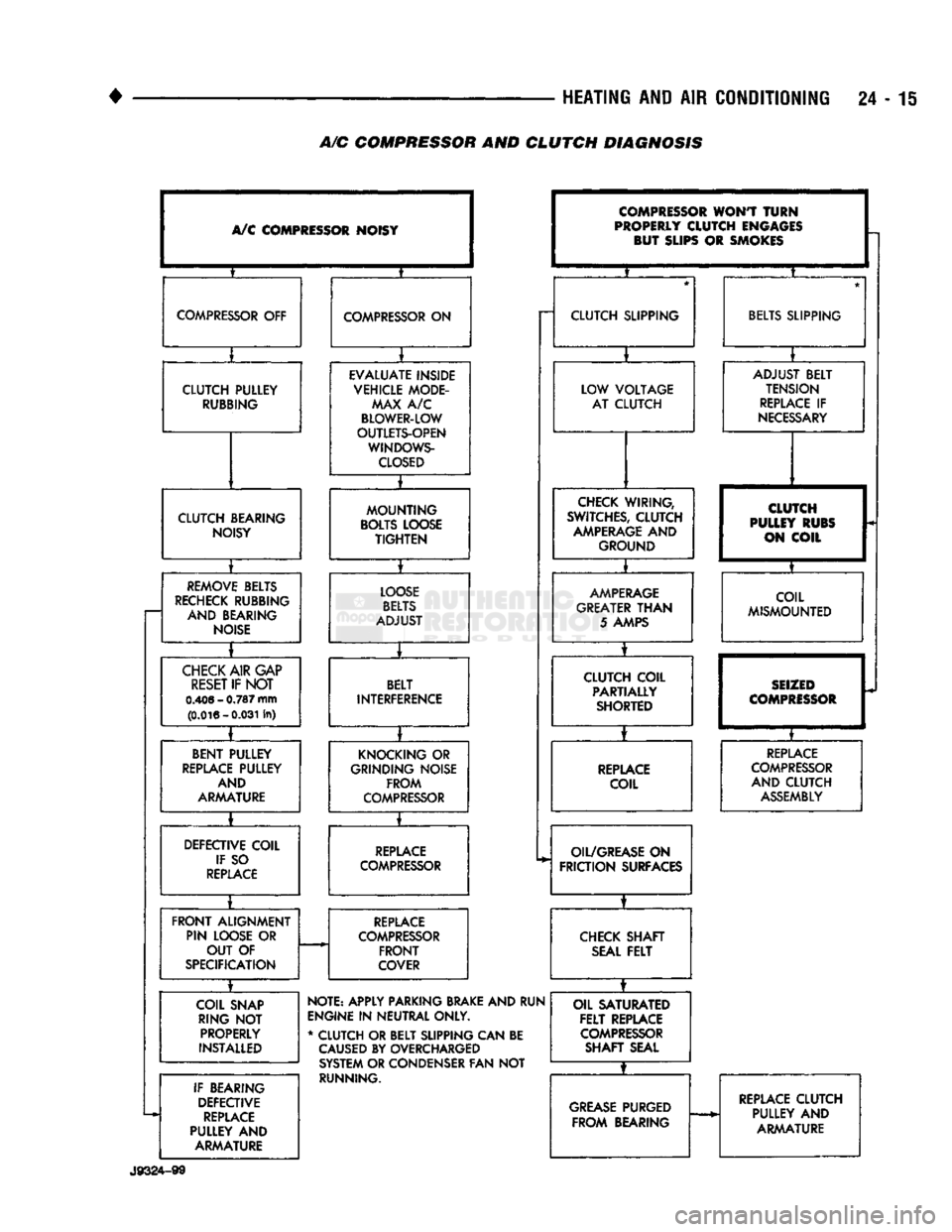
HEATING
AND AIR
CONDITIONING
24 -
A/C COMPRESSOR AND CLUTCH DIAGNOSIS
A/C
COMPRESSOR NOISY
?
COMPRESSOR
OFF
COMPRESSOR
ON
I
CLUTCH PULLEY
RUBBING
EVALUATE INSIDE
VEHICLE MODE- MAX
A/C
BLOWER-LOW
OUTLETS-OPEN WINDOWS-
CLOSED
EVALUATE INSIDE
VEHICLE MODE- MAX
A/C
BLOWER-LOW
OUTLETS-OPEN WINDOWS-
CLOSED
CLUTCH BEARING NOISY
MOUNTING
BOLTS
LOOSE
TIGHTEN
•
REMOVE
BELTS
RECHECK
RUBBING AND BEARING
NOISE
LOOSE
BELTS
ADJUST
*
»
CHECK
AIR
GAP
RESET
IF
NOT
0.406
-
0.787
mm (0.016-0.031 In)
BELT
INTERFERENCE
• I
BENT PULLEY
REPLACE
PULLEY AND
ARMATURE KNOCKING
OR
GRINDING NOISE
FROM
COMPRESSOR
_ *
DEFECTIVE COIL IF
SO
REPLACE REPLACE
COMPRESSOR
FRONT
ALIGNMENT PIN LOOSE
OR
OUT
OF
SPECIFICATION
REPLACE
COMPRESSOR
FRONT
COVER
COMPRESSOR
WONT
TURN
PROPERLY
CLUTCH ENGAGES BUT SLIPS
OR
SMOKES
CLUTCH SLIPPING LOW VOLTAGE AT CLUTCH
CHECK
WIRING,
SWITCHES,
CLUTCH
AMPERAGE
AND
GROUND
I
AMPERAGE
GREATER
THAN
5
AMPS
CLUTCH COIL PARTIALLY SHORTED
REPLACE
COIL
OIL/GREASE
ON
FRICTION
SURFACES
CHECK
SHAFT
SEAL
FELT
COIL SNAP RING
NOT
PROPERLY
INSTALLED
IF BEARING DEFECTIVE
REPLACE
PULLEY
AND
ARMATURE NOTE: APPLY PARKING
BRAKE
AND RUN
ENGINE
IN
NEUTRAL ONLY.
*
CLUTCH OR BELT SUPPING CAN BE
CAUSED
BY OVERCHARGED
SYSTEM
OR CONDENSER FAN
NOT
RUNNING. OIL SATURATED
FELT
REPLACE
COMPRESSOR
SHAFT SEAL ADJUST BELT
TENSION
REPLACE
IF
NECESSARY
CLUTCH
PULLEY RUBS ON COIL
COIL
MISMOUNTED
SEIZED
COMPRESSOR
T
REPLACE
COMPRESSOR
AND CLUTCH
ASSEMBLY
GREASE
PURGED
FROM
BEARING
REPLACE
CLUTCH
PULLEY
AND
ARMATURE
GREASE
PURGED
FROM
BEARING
REPLACE
CLUTCH
PULLEY
AND
ARMATURE
J9324-99
Page 1453 of 1502
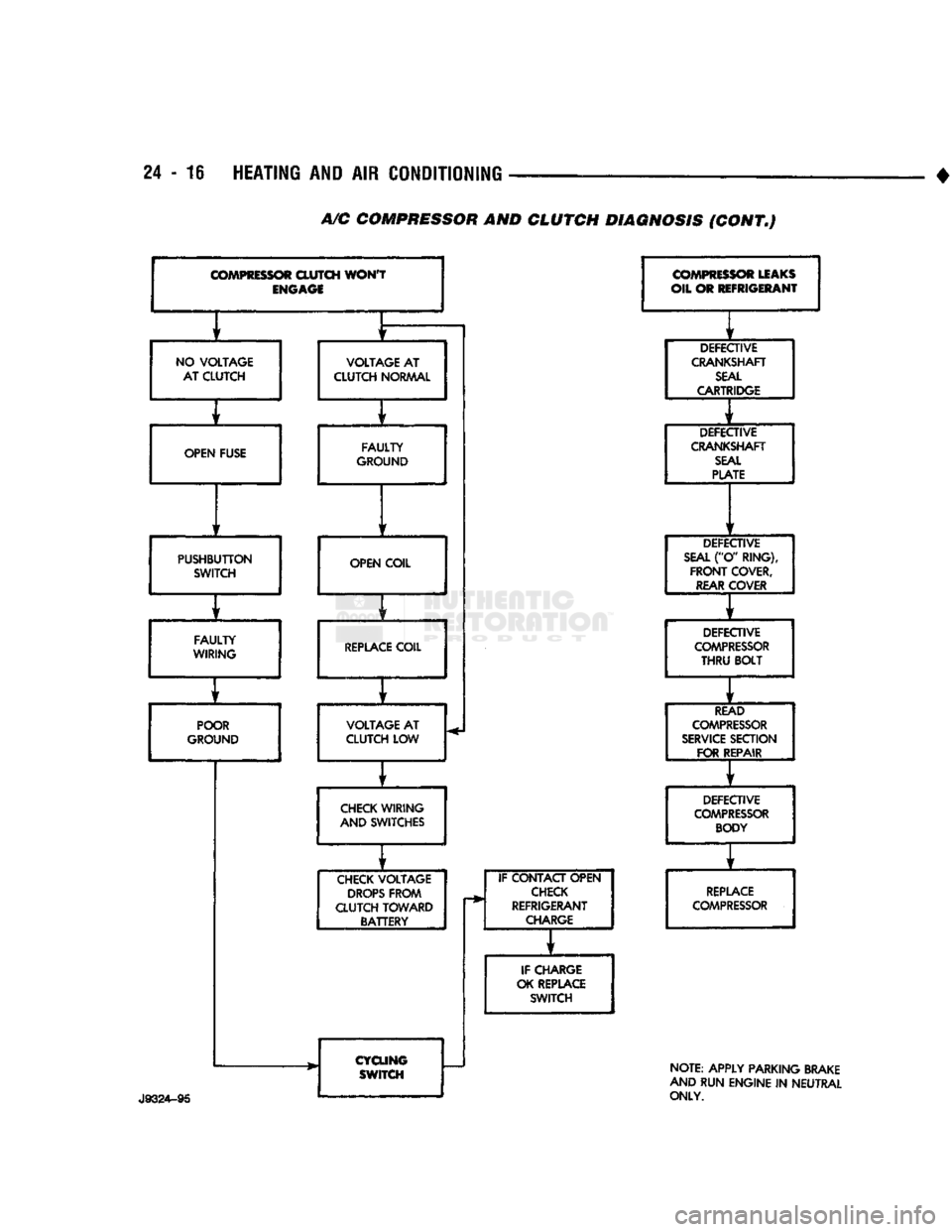
24 - 16 HEATING AND AIR CONDITIONING
A/C
COMPRESSOR AND CLUTCH DIAGNOSIS (CONT.)
COMPRESSOR
CLUTCH
WON'T
ENGAGE
f
f
NO
VOLTAGE
VOLTAGE
AT
AT CLUTCH CLUTCH
NORMAL
f t
OPEN FUSE FAULTY
GROUND
f
1
PUSHBUTTON SWITCH OPEN COIL
f
FAULTY
WIRING
REPLACE
COIL
f
r
POOR
VOLTAGE
AT
GROUND CLUTCH LOW
f
CHECK
WIRING
AND SWITCHES
f
CHECK
VOLTAGE
DROPS
FROM
CLUTCH TOWARD BATTERY
CYCLING SWITCH IF CONTACT OPEN
CHECK
REFRIGERANT
CHARGE
IF CHARGE
OK REPLACE SWITCH
COMPRESSOR
LEAKS
OIL OR REFRIGERANT
DEFECTIVE
CRANKSHAFT
SEAL
CARTRIDGE
DEFECTIVE
CRANKSHAFT
SEAL
PLATE
DEFECTIVE
SEAL
("O' RING),
FRONT
COVER,
REAR
COVER
DEFECTIVE
COMPRESSOR
THRU
BOLT
READ
COMPRESSOR
SERVICE
SECTION FOR REPAIR
DEFECTIVE
COMPRESSOR
BODY
REPLACE
COMPRESSOR
NOTE: APPLY PARKING BRAKE
AND RUN ENGINE
IN
NEUTRAL
ONLY.
Page 1454 of 1502
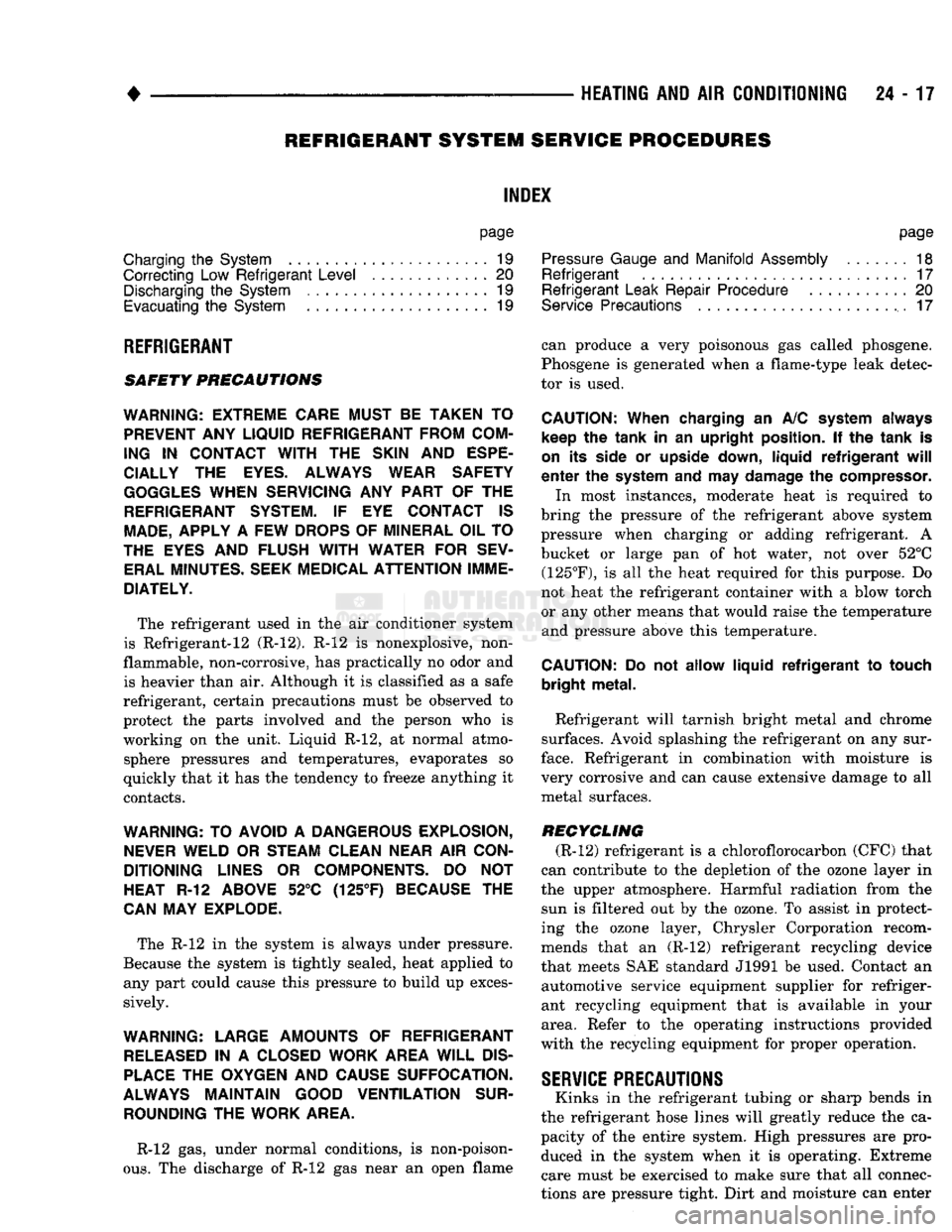
•
HEATING
AND
AIR
CONDITIONING
24-17 REFRIGERANT SYSTEM SERWICE PROCEDURES
INDEX
page
Charging
the
System
19
Correcting
Low
Refrigerant
Level
.............
20
Discharging
the
System
. 19
Evacuating
the
System
19
REFRIGERANT
SAFETY
PRECAUTIONS
WARNING: EXTREME CARE MUST
BE
TAKEN
TO
PREVENT
ANY LIQUID
REFRIGERANT FROM COM
ING
IN
CONTACT
WITH
THE
SKIN
AND
ESPE
CIALLY
THE
EYES.
ALWAYS WEAR SAFETY
GOGGLES WHEN SERVICING
ANY
PART
OF
THE
REFRIGERANT SYSTEM.
IF EYE
CONTACT
IS
MADE,
APPLY
A
FEW
DROPS
OF
MINERAL
OIL
TO
THE
EYES
AND
FLUSH
WITH
WATER
FOR
SEV
ERAL MINUTES.
SEEK
MEDICAL
ATTENTION
IMME
DIATELY.
The refrigerant used
in the air
conditioner system
is Refrigerant-12 (R-12).
R-12 is
nonexplosive, non
flammable, non-corrosive,
has
practically
no
odor
and
is heavier than
air.
Although
it is
classified
as a
safe
refrigerant, certain precautions must
be
observed
to
protect
the
parts involved
and the
person
who is
working
on the
unit. Liquid
R-12, at
normal atmo sphere pressures
and
temperatures, evaporates
so
quickly that
it has the
tendency
to
freeze anything
it
contacts.
WARNING:
TO
AVOID
A
DANGEROUS EXPLOSION,
NEVER
WELD
OR
STEAM CLEAN NEAR
AIR
CON
DITIONING
LINES
OR
COMPONENTS.
DO NOT
HEAT
R-12
ABOVE
52°C (125°F)
BECAUSE
THE
CAN
MAY
EXPLODE.
The
R-12 in the
system
is
always under pressure.
Because
the
system
is
tightly sealed, heat applied
to
any part could cause this pressure
to
build
up
excessively.
WARNING: LARGE AMOUNTS
OF
REFRIGERANT
RELEASED
IN A
CLOSED WORK AREA
WILL
DIS
PLACE
THE
OXYGEN
AND
CAUSE SUFFOCATION.
ALWAYS
MAINTAIN
GOOD
VENTILATION
SUR ROUNDING
THE
WORK AREA.
R-12
gas,
under normal conditions,
is
non-poison
ous.
The
discharge
of R-12 gas
near
an
open flame
page
Pressure Gauge
and
Manifold
Assembly
18
Refrigerant
. 17
Refrigerant
Leak Repair Procedure
20
Service Precautions
. 17
can produce
a
very poisonous
gas
called phosgene.
Phosgene
is
generated when
a
flame-type leak detec
tor
is
used.
CAUTION:
When charging
an A/C
system always
keep
the
tank
in an
upright position.
If the
tank
is
on
its
side
or
upside down,
liquid
refrigerant
will
enter
the
system
and may
damage
the
compressor.
In most instances, moderate heat
is
required
to
bring
the
pressure
of the
refrigerant above system
pressure when charging
or
adding refrigerant.
A
bucket
or
large
pan of hot
water,
not
over 52°C (125°F),
is all the
heat required
for
this purpose.
Do
not heat
the
refrigerant container with
a
blow torch
or
any
other means that would raise
the
temperature and pressure above this temperature.
CAUTION:
Do not
allow
liquid
refrigerant
to
touch
bright
metal.
Refrigerant will tarnish bright metal
and
chrome
surfaces. Avoid splashing
the
refrigerant
on any
sur
face.
Refrigerant
in
combination with moisture
is
very corrosive
and can
cause extensive damage
to all
metal surfaces.
RECYCLING
(R-12) refrigerant
is a
chloroflorocarbon
(CFC)
that
can contribute
to the
depletion
of the
ozone layer
in
the upper atmosphere. Harmful radiation from
the
sun
is
filtered
out by the
ozone.
To
assist
in
protect
ing
the
ozone layer, Chrysler Corporation recom
mends that
an
(R-12) refrigerant recycling device
that meets
SAE
standard
J1991 be
used. Contact
an
automotive service equipment supplier
for
refriger
ant recycling equipment that
is
available
in
your
area. Refer
to the
operating instructions provided
with
the
recycling equipment
for
proper operation.
SERVICE
PRECAUTIONS
Kinks
in the
refrigerant tubing
or
sharp bends
in
the refrigerant hose lines will greatly reduce
the ca
pacity
of the
entire system. High pressures
are
produced
in the
system when
it is
operating. Extreme
care must
be
exercised
to
make sure that
all
connec
tions
are
pressure tight. Dirt
and
moisture
can
enter
Page 1455 of 1502
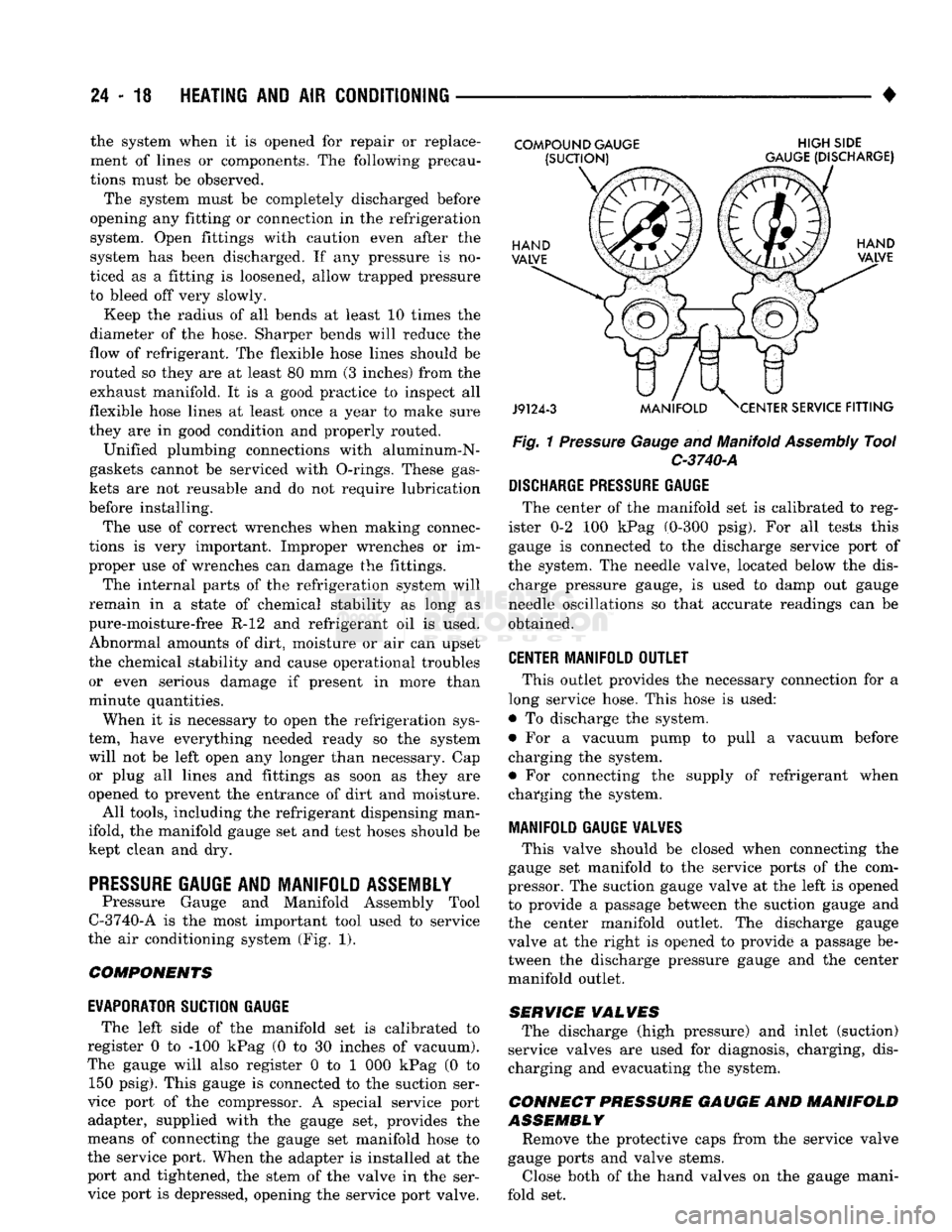
24 - 18
HEATING
AND AIR
CONDITIONING
• the system when it is opened for repair or replace
ment of lines or components, The following precau
tions must be observed.
The system must be completely discharged before
opening any fitting or connection in the refrigeration
system. Open fittings with caution even after the
system has been discharged. If any pressure is no
ticed as a fitting is loosened, allow trapped pressure
to bleed off very slowly.
Keep the radius of all bends at least 10 times the
diameter of the hose. Sharper bends will reduce the
flow of refrigerant. The flexible hose lines should be routed so they are at least 80 mm (3 inches) from the exhaust manifold. It is a good practice to inspect all
flexible hose lines at least once a year to make sure they are in good condition and properly routed.
Unified plumbing connections with aluminum-N-
gaskets cannot be serviced with O-rings. These gas
kets are not reusable and do not require lubrication
before installing.
The use of correct wrenches when making connec
tions is very important. Improper wrenches or im
proper use of wrenches can damage the fittings.
The internal parts of the refrigeration system will
remain in a state of chemical stability as long as
pure-moisture-free R-12 and refrigerant oil is used. Abnormal amounts of dirt, moisture or air can upset
the chemical stability and cause operational troubles or even serious damage if present in more than
minute quantities.
When it is necessary to open the refrigeration sys
tem, have everything needed ready so the system
will not be left open any longer than necessary. Cap
or plug all lines and fittings as soon as they are
opened to prevent the entrance of dirt and moisture. All tools, including the refrigerant dispensing man
ifold, the manifold gauge set and test hoses should be
kept clean and dry.
PRESSURE
GAUGE AND MANIFOLD
ASSEMBLY
Pressure Gauge and Manifold Assembly Tool
C-3740-A is the most important tool used to service
the air conditioning system (Fig. 1).
COMPONENTS
E¥AP0RAT0R SUCTiOl GAUiE
The left side of the manifold set is calibrated to
register 0 to -100 kPag (0 to 30 inches of vacuum).
The gauge will also register 0 to 1 000 kPag (0 to 150 psig). This gauge is connected to the suction ser
vice port of the compressor. A special service port adapter, supplied with the gauge set, provides the
means of connecting the gauge set manifold hose to
the service port. When the adapter is installed at the
port and tightened, the stem of the valve in the ser vice port is depressed, opening the service port valve.
COMPOUND GAUGE
HIGH
SIDE
Fig.
1
Pressure
Gauge and Manifold
Assembly
Tool
C-3740-A
DISCHARGE
PRESSURE
GAUGE
The center of the manifold set is calibrated to reg
ister 0-2 100 kPag (0-300 psig). For all tests this
gauge is connected to the discharge service port of
the system. The needle valve, located below the dis charge pressure gauge, is used to damp out gauge
needle oscillations so that accurate readings can be
obtained.
CENTER
MANIFOLD
OUTLET
This outlet provides the necessary connection for a
long service hose. This hose is used:
• To discharge the system.
• For a vacuum pump to pull a vacuum before charging the system.
• For connecting the supply of refrigerant when charging the system.
MANIFOLD GAUGE WALWES
This valve should be closed when connecting the
gauge set manifold to the service ports of the com
pressor. The suction gauge valve at the left is opened to provide a passage between the suction gauge and
the center manifold outlet. The discharge gauge
valve at the right is opened to provide a passage be
tween the discharge pressure gauge and the center manifold outlet.
SERVICE VALVES The discharge (high pressure) and inlet (suction)
service valves are used for diagnosis, charging, dis
charging and evacuating the system.
CONNECT PRESSURE GAUGE AND MANIFOLD
ASSEMBLY
Remove the protective caps from the service valve
gauge ports and valve stems.
Close both of the hand valves on the gauge mani
fold set.
Page 1456 of 1502
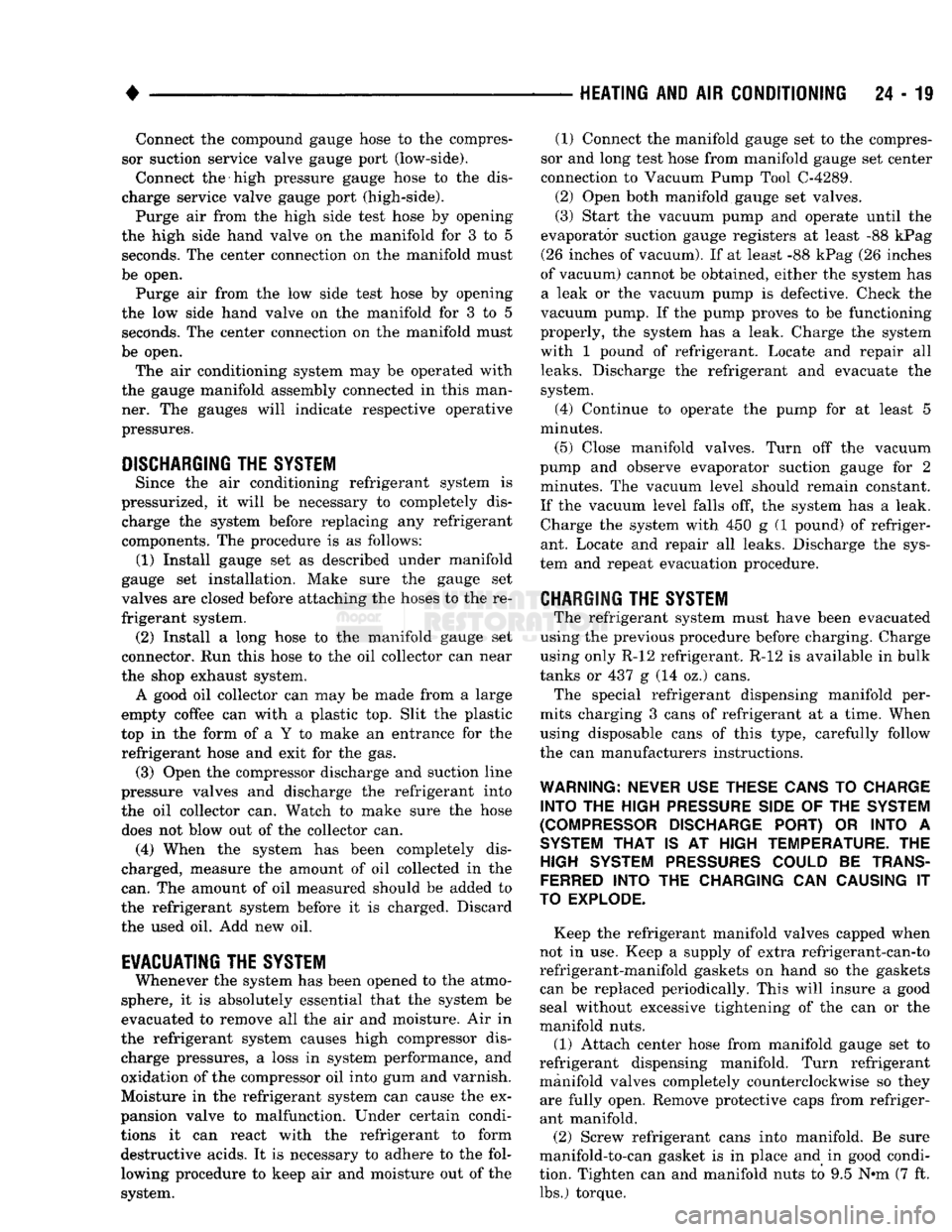
•
HEATING
AND
AIR
CONDITIONING
24 - 19
Connect
the
compound gauge hose
to the
compres
sor suction service valve gauge port (low-side).
Connect
the
high pressure gauge hose
to the
dis
charge service valve gauge port (high-side). Purge
air
from
the
high side test hose
by
opening
the high side hand valve
on the
manifold
for 3 to 5
seconds.
The
center connection
on the
manifold must
be open.
Purge
air
from
the low
side test hose
by
opening
the
low
side hand valve
on the
manifold
for 3 to 5
seconds.
The
center connection
on the
manifold must
be open.
The
air
conditioning system
may be
operated with
the gauge manifold assembly connected
in
this man
ner.
The
gauges will indicate respective operative
pressures.
DISCHARGING
THE SYSTEM
Since
the air
conditioning refrigerant system
is
pressurized,
it
will
be
necessary
to
completely dis charge
the
system before replacing
any
refrigerant
components.
The
procedure
is as
follows: (1) Install gauge
set as
described under manifold
gauge
set
installation. Make sure
the
gauge
set
valves
are
closed before attaching
the
hoses
to the re
frigerant system. (2) Install
a
long hose
to the
manifold gauge
set
connector.
Run
this hose
to the oil
collector
can
near
the shop exhaust system. A good
oil
collector
can may be
made from
a
large
empty coffee
can
with
a
plastic
top.
Slit
the
plastic
top
in the
form
of a Y to
make
an
entrance
for the
refrigerant hose
and
exit
for the gas.
(3) Open
the
compressor discharge
and
suction line
pressure valves
and
discharge
the
refrigerant into
the
oil
collector
can.
Watch
to
make sure
the
hose does
not
blow
out of the
collector
can.
(4) When
the
system
has
been completely dis
charged, measure
the
amount
of oil
collected
in the
can.
The
amount
of oil
measured should
be
added
to
the refrigerant system before
it is
charged. Discard
the used
oil. Add new oil.
EVACUATING
THE SYSTEM
Whenever
the
system
has
been opened
to the
atmo
sphere,
it is
absolutely essential that
the
system
be
evacuated
to
remove
all the air and
moisture.
Air in
the refrigerant system causes high compressor dis charge pressures,
a
loss
in
system performance,
and
oxidation
of the
compressor
oil
into
gum and
varnish.
Moisture
in the
refrigerant system
can
cause
the ex
pansion valve
to
malfunction. Under certain condi
tions
it can
react with
the
refrigerant
to
form destructive acids.
It is
necessary
to
adhere
to the
fol
lowing procedure
to
keep
air and
moisture
out of the
system. (1) Connect
the
manifold gauge
set to the
compres
sor
and
long test hose from manifold gauge
set
center
connection
to
Vacuum Pump Tool C-4289. (2) Open both manifold gauge
set
valves.
(3) Start
the
vacuum pump
and
operate until
the
evaporator suction gauge registers
at
least
-88
kPag (26 inches
of
vacuum).
If at
least
-88
kPag
(26
inches
of vacuum) cannot
be
obtained, either
the
system
has
a leak
or the
vacuum pump
is
defective. Check
the
vacuum pump.
If the
pump proves
to be
functioning
properly,
the
system
has a
leak. Charge
the
system
with
1
pound
of
refrigerant. Locate
and
repair
all
leaks.
Discharge
the
refrigerant
and
evacuate
the
system.
(4) Continue
to
operate
the
pump
for at
least
5
minutes.
(5) Close manifold valves. Turn
off the
vacuum
pump
and
observe evaporator suction gauge
for 2
minutes.
The
vacuum level should remain constant.
If
the
vacuum level falls
off, the
system
has a
leak. Charge
the
system with
450 g (1
pound)
of
refriger
ant. Locate
and
repair
all
leaks. Discharge
the
sys
tem
and
repeat evacuation procedure.
CHARGING
THE
SYSTEM
The refrigerant system must have been evacuated
using
the
previous procedure before charging. Charge
using only
R-12
refrigerant.
R-12 is
available
in
bulk
tanks
or 437 g (14 oz.)
cans. The special refrigerant dispensing manifold per
mits charging
3
cans
of
refrigerant
at a
time. When
using disposable cans
of
this type, carefully follow
the
can
manufacturers instructions.
WARNING: NEVER USE THESE CANS
TO
CHARGE
INTO
THE
HIGH
PRESSURE SIDE
OF
THE
SYSTEM
(COMPRESSOR
DISCHARGE PORT)
OR
INTO
A
SYSTEM
THAT
IS AT
HIGH
TEMPERATURE.
THE
HIGH
SYSTEM PRESSURES COULD
BE
TRANS
FERRED
INTO
THE
CHARGING
CAN
CAUSING
IT
TO EXPLODE.
Keep
the
refrigerant manifold valves capped when
not
in use.
Keep
a
supply
of
extra refrigerant-can-to
refrigerant-manifold gaskets
on
hand
so the
gaskets can
be
replaced periodically. This will insure
a
good
seal without excessive tightening
of the can or the
manifold nuts.
(1) Attach center hose from manifold gauge
set to
refrigerant dispensing manifold. Turn refrigerant manifold valves completely counterclockwise
so
they are fully open. Remove protective caps from refriger
ant manifold.
(2) Screw refrigerant cans into manifold.
Be
sure
manifold-to-can gasket
is in
place
and in
good condi
tion. Tighten
can and
manifold nuts
to 9.5 N»m (7 ft.
lbs.) torque.
Page 1457 of 1502
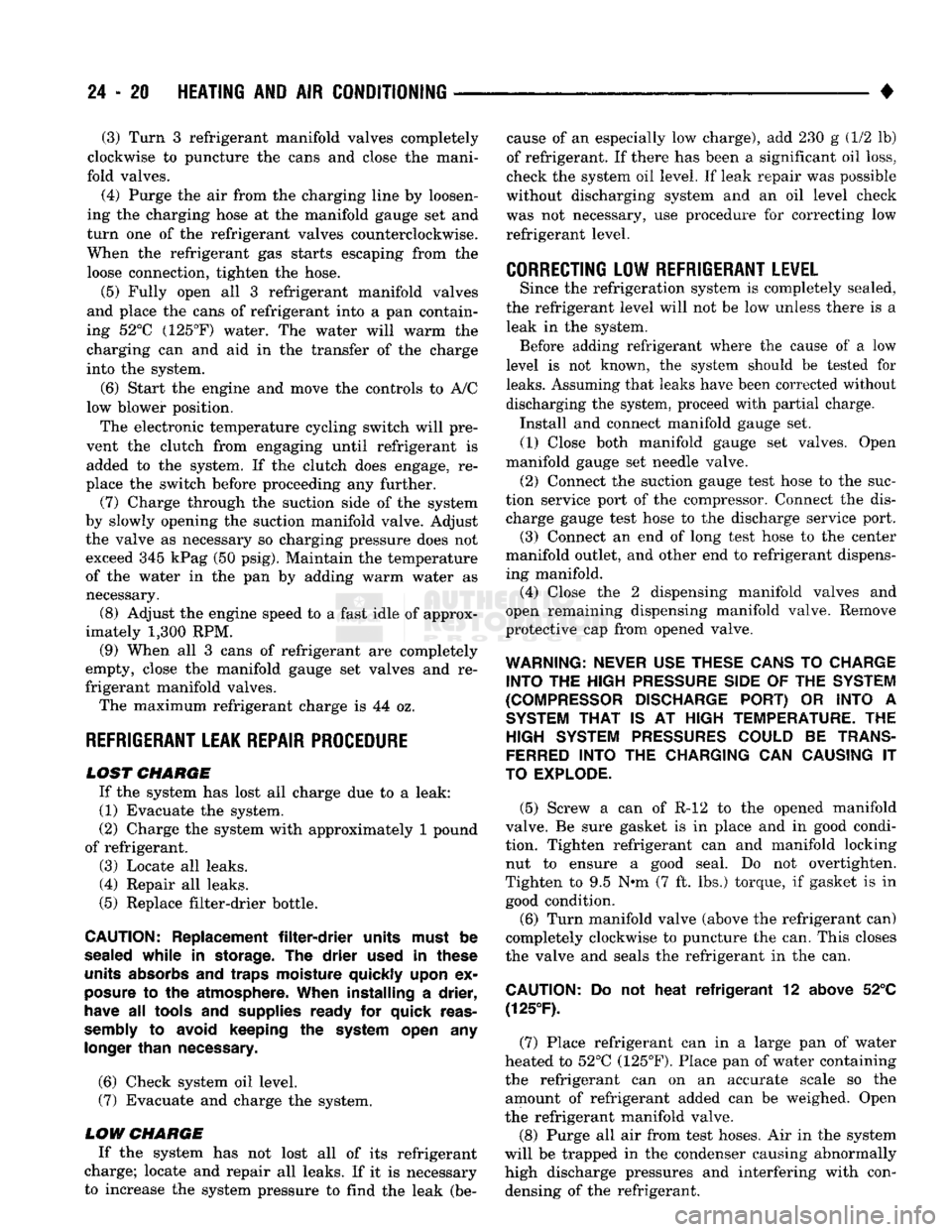
24
- 20
HEATING
AND AIR
CONDITIONING
• (3) Turn
3
refrigerant manifold valves completely
clockwise
to
puncture
the
cans
and
close
the
mani
fold valves.
(4) Purge
the air
from
the
charging line
by
loosen
ing
the
charging hose
at the
manifold gauge
set and
turn
one of the
refrigerant valves counterclockwise. When
the
refrigerant
gas
starts escaping from
the
loose connection, tighten
the
hose.
(5) Fully open
all 3
refrigerant manifold valves
and place
the
cans
of
refrigerant into
a pan
contain
ing 52°C (125°F) water.
The
water will warm
the
charging
can and aid in the
transfer
of the
charge
into
the
system.
(6) Start
the
engine
and
move
the
controls
to A/C
low blower position.
The electronic temperature cycling switch will pre
vent
the
clutch from engaging until refrigerant
is
added
to the
system.
If the
clutch does engage,
re
place
the
switch before proceeding
any
further. (7) Charge through
the
suction side
of the
system
by slowly opening
the
suction manifold valve. Adjust
the valve
as
necessary
so
charging pressure does
not
exceed
345
kPag
(50
psig). Maintain
the
temperature
of
the
water
in the pan by
adding warm water
as
necessary. (8) Adjust
the
engine speed
to a
fast idle
of
approx
imately
1,300 RPM.
(9) When
all 3
cans
of
refrigerant
are
completely
empty, close
the
manifold gauge
set
valves
and re
frigerant manifold valves. The maximum refrigerant charge
is 44 oz.
REFRIGERANT
LEAK REPAIR PROCEDURE
LOST CHARGE If
the
system
has
lost
all
charge
due to a
leak: (1) Evacuate
the
system.
(2) Charge
the
system with approximately
1
pound
of refrigerant. (3) Locate
all
leaks.
(4) Repair
all
leaks.
(5) Replace filter-drier bottle.
CAUTION:
Replacement
filter-drier
units
must
be
sealed
while
in
storage.
The
drier
used
in
these
units
absorbs
and
traps
moisture
quickly
upon
ex
posure
to the
atmosphere.
When
installing
a
drier,
have
all
tools
and
supplies ready
for
quick
reas
sembly
to
avoid keeping
the
system open
any
longer
than
necessary.
(6) Check system
oil
level. (7) Evacuate
and
charge
the
system.
LOW CHARGE If
the
system
has not
lost
all of its
refrigerant
charge; locate
and
repair
all
leaks.
If it is
necessary
to increase
the
system pressure
to
find
the
leak
(be
cause
of an
especially
low
charge),
add 230 g (1/2 lb)
of refrigerant.
If
there
has
been
a
significant
oil
loss,
check
the
system
oil
level.
If
leak repair
was
possible
without discharging system
and an oil
level check
was
not
necessary,
use
procedure
for
correcting
low
refrigerant level.
CORRECTING
LOW
REFRIGERANT LEVEL
Since
the
refrigeration system
is
completely sealed,
the refrigerant level will
not be low
unless there
is a
leak
in the
system. Before adding refrigerant where
the
cause
of a low
level
is not
known,
the
system should
be
tested
for
leaks.
Assuming that leaks have been corrected without
discharging
the
system, proceed with partial charge.
Install
and
connect manifold gauge
set.
(1) Close both manifold gauge
set
valves. Open
manifold gauge
set
needle valve.
(2) Connect
the
suction gauge test hose
to the
suc
tion service port
of the
compressor. Connect
the
dis charge gauge test hose
to the
discharge service port. (3) Connect
an end of
long test hose
to the
center
manifold outlet,
and
other
end to
refrigerant dispens ing manifold. (4) Close
the 2
dispensing manifold valves
and
open remaining dispensing manifold valve. Remove
protective
cap
from opened valve.
WARNING: NEVER
USE
THESE CANS
TO
CHARGE
INTO
THE
HIGH
PRESSURE SIDE
OF
THE
SYSTEM
(COMPRESSOR
DISCHARGE
PORT)
OR
INTO
A
SYSTEM
THAT
IS AT
HIGH
TEMPERATURE.
THE
HIGH
SYSTEM PRESSURES COULD
BE
TRANS
FERRED
INTO
THE
CHARGING
CAN
CAUSING
IT
TO EXPLODE.
(5) Screw
a can of R-12 to the
opened manifold
valve.
Be
sure gasket
is in
place
and in
good condi
tion. Tighten refrigerant
can and
manifold locking nut
to
ensure
a
good seal.
Do not
overtighten.
Tighten
to 9.5 N*m (7 ft. lbs.)
torque,
if
gasket
is in
good condition.
(6) Turn manifold valve (above
the
refrigerant
can)
completely clockwise
to
puncture
the can.
This closes
the valve
and
seals
the
refrigerant
in the can.
CAUTION:
Do not
heat refrigerant
12
above
52°C
(125°F).
(7) Place refrigerant
can in a
large
pan of
water
heated
to
52°C (125°F). Place
pan of
water containing
the refrigerant
can on an
accurate scale
so the
amount
of
refrigerant added
can be
weighed. Open
the refrigerant manifold valve.
(8) Purge
all air
from test hoses.
Air in the
system
will
be
trapped
in the
condenser causing abnormally
high discharge pressures
and
interfering with con densing
of the
refrigerant.
Page 1458 of 1502
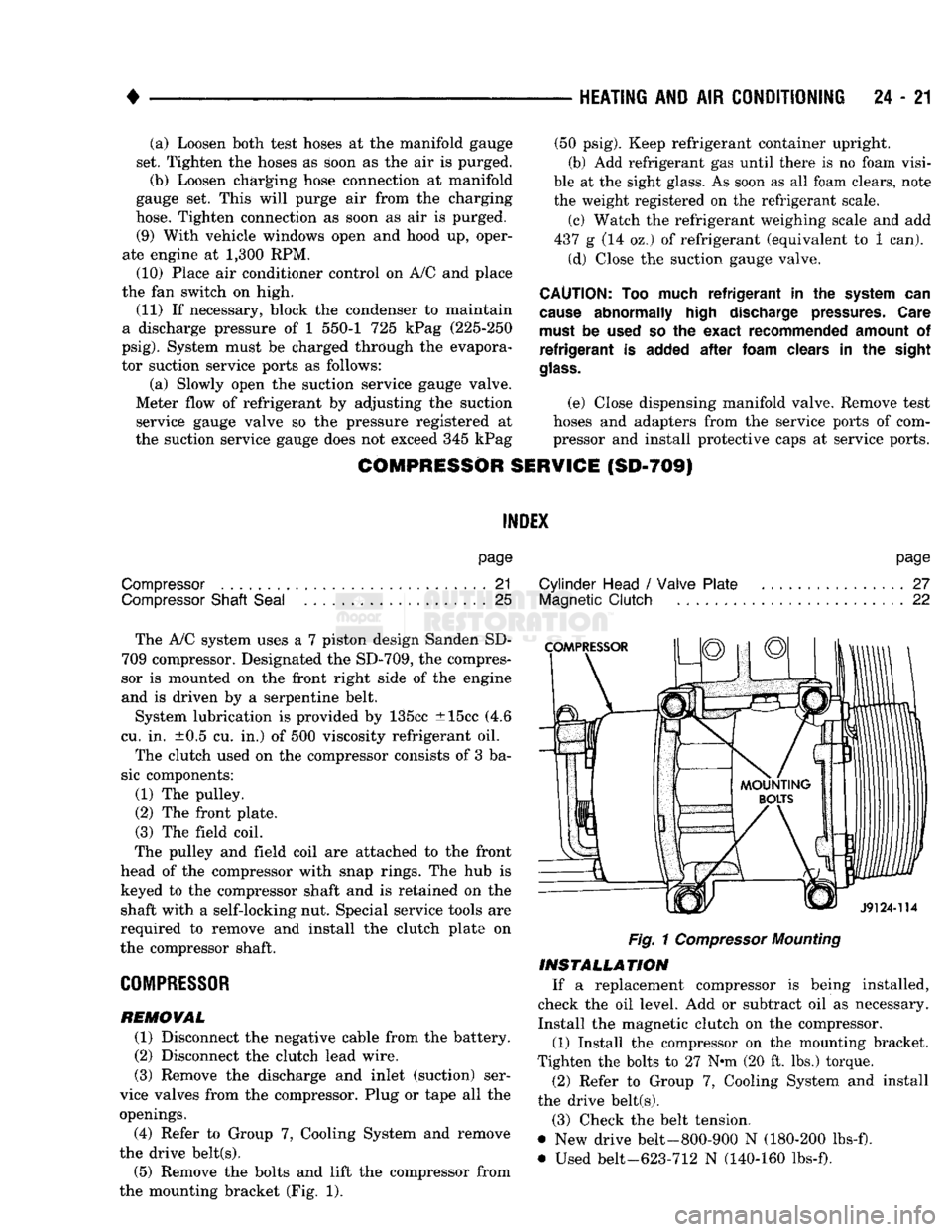
•
HEATING
AND AIR
CONDITIONING
24 - 21 (a) Loosen both test hoses at the manifold gauge
set. Tighten the hoses as soon as the air is purged. (b) Loosen charging hose connection at manifold
gauge set. This will purge air from the charging
hose.
Tighten connection as soon as air is purged.
(9) With vehicle windows open and hood up, oper
ate engine at 1,300 RPM. (10) Place air conditioner control on A/C and place
the fan switch on high. (11) If necessary, block the condenser to maintain
a discharge pressure of 1 550-1 725 kPag (225-250
psig).
System must be charged through the evapora
tor suction service ports as follows:
(a) Slowly open the suction service gauge valve.
Meter flow of refrigerant by adjusting the suction service gauge valve so the pressure registered at
the suction service gauge does not exceed 345 kPag
COMPRESSOR
J
(50
psig). Keep refrigerant container upright.
(b) Add refrigerant gas until there is no foam visi
ble at the sight glass. As soon as all foam clears, note the weight registered on the refrigerant scale.
(c) Watch the refrigerant weighing scale and add
437 g (14 oz.) of refrigerant (equivalent to 1 can).
(d) Close the suction gauge valve.
CAUTION:
TOO
much
refrigerant
in the
system
can
cause
abnormally high discharge pressures. Care
must
be
used
so the
exact recommended amount
of
refrigerant
is
added
after
foam clears
in the
sight
glass.
(e) Close dispensing manifold valve. Remove test
hoses and adapters from the service ports of com
pressor and install protective caps at service ports.
RVICE (SD-709)
INDEX
page
Compressor
21
Compressor
Shaft Seal
.................... 25
The A/C system uses a 7 piston design Sanden SD-
709 compressor. Designated the SD-709, the compres
sor is mounted on the front right side of the engine
and is driven by a serpentine belt.
System lubrication is provided by 135cc ±15cc (4.6
cu. in. ±0.5 cu. in.) of 500 viscosity refrigerant oil.
The clutch used on the compressor consists of 3 ba
sic components:
(1) The pulley.
(2) The front plate. (3) The field coil.
The pulley and field coil are attached to the front
head of the compressor with snap rings. The hub is keyed to the compressor shaft and is retained on the
shaft with a self-locking nut. Special service tools are
required to remove and install the clutch plate on
the compressor shaft.
COMPRESSOR
REMOVAL
(1) Disconnect the negative cable from the battery.
(2) Disconnect the clutch lead wire.
(3) Remove the discharge and inlet (suction) ser
vice valves from the compressor. Plug or tape all the
openings.
(4) Refer to Group 7, Cooling System and remove
the drive belt(s). (5) Remove the bolts and lift the compressor from
the mounting bracket (Fig. 1).
page
Cylinder Head
/
Valve Plate
27
Magnetic
Clutch
22
Fig.
1
Compressor
Mounting
INSTALLATION
If a replacement compressor is being installed,
check the oil level. Add or subtract oil as necessary.
Install the magnetic clutch on the compressor.
(1) Install the compressor on the mounting bracket.
Tighten the bolts to 27 N*m (20 ft. lbs.) torque.
(2) Refer to Group 7, Cooling System and install
the drive belt(s).
(3) Check the belt tension.
@ New drive belt-800-900 N (180-200 lbs-f).
• Used belt-623-712 N (140-160 lbs-f).
Page 1459 of 1502
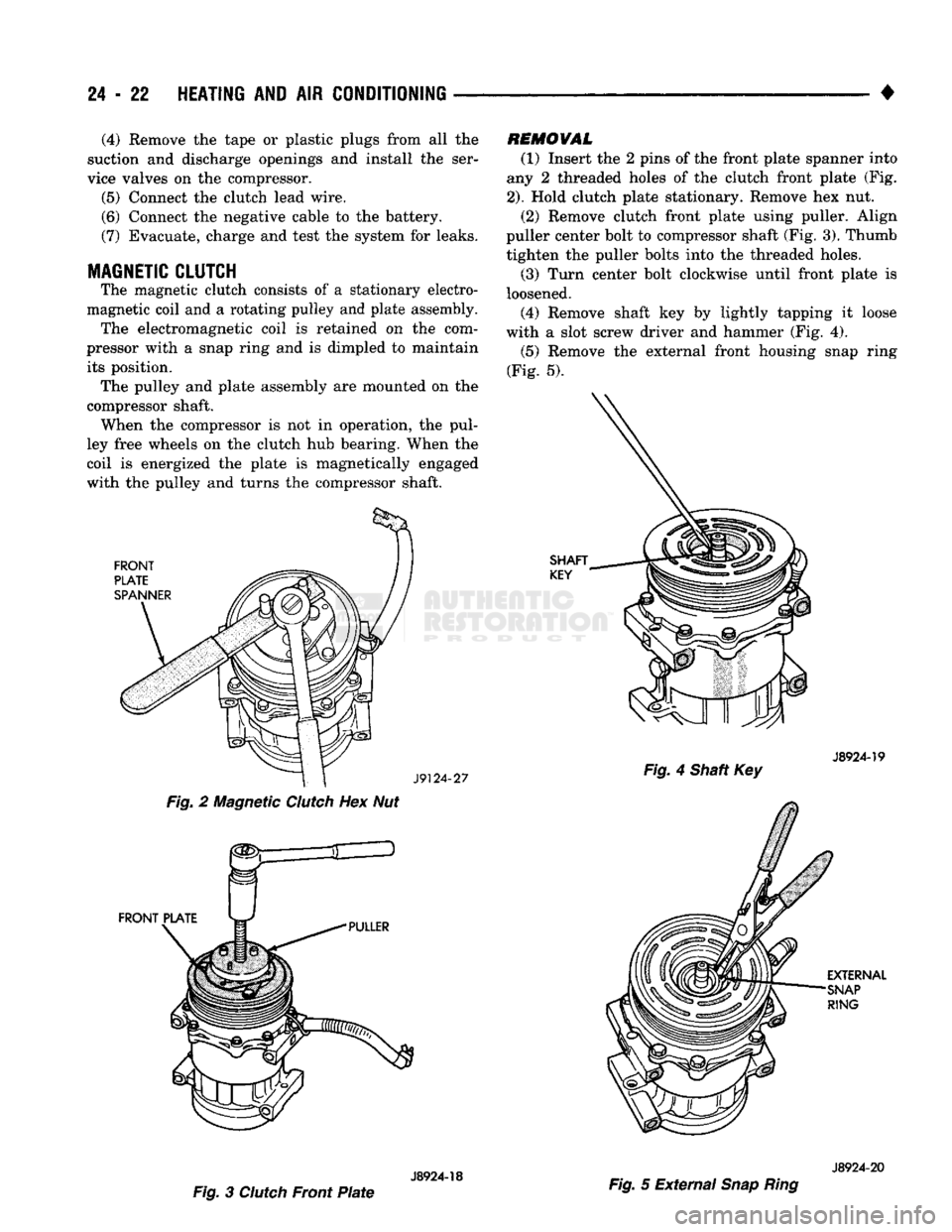
24 - 22
HEATING
AND AIR
CONDITIONING
•
(4)
Remove the tape or plastic plugs from all the
suction and discharge openings and install the ser
vice valves on the compressor.
(5)
Connect the clutch lead wire.
(6) Connect the negative cable to the battery.
(7)
Evacuate, charge and test the system for leaks.
MAGNETIC
CLUTCH
The magnetic clutch consists of a stationary electro
magnetic coil and a rotating pulley and plate assembly. The electromagnetic coil is retained on the com
pressor with a snap ring and is dimpled to maintain its position. The pulley and plate assembly are mounted on the
compressor shaft. When the compressor is not in operation, the pul
ley free wheels on the clutch hub bearing. When the
coil is energized the plate is magnetically engaged
with the pulley and turns the compressor shaft.
J8924-18
Fig.
3
Clutch
Front
Plate
REMOVAL
(1) Insert the 2 pins of the front plate spanner into
any 2 threaded holes of the clutch front plate (Fig.
2).
Hold clutch plate stationary. Remove hex nut. (2) Remove clutch front plate using puller. Align
puller center bolt to compressor shaft (Fig. 3). Thumb tighten the puller bolts into the threaded holes. (3) Turn center bolt clockwise until front plate is
loosened. (4) Remove shaft key by lightly tapping it loose
with a slot screw driver and hammer (Fig. 4).
(5)
Remove the external front housing snap ring
(Fig. 5).
J8924-19
Fig.
4 Shaft Key
J8924-20
Fig.
5 External
Snap Ring
Page 1460 of 1502
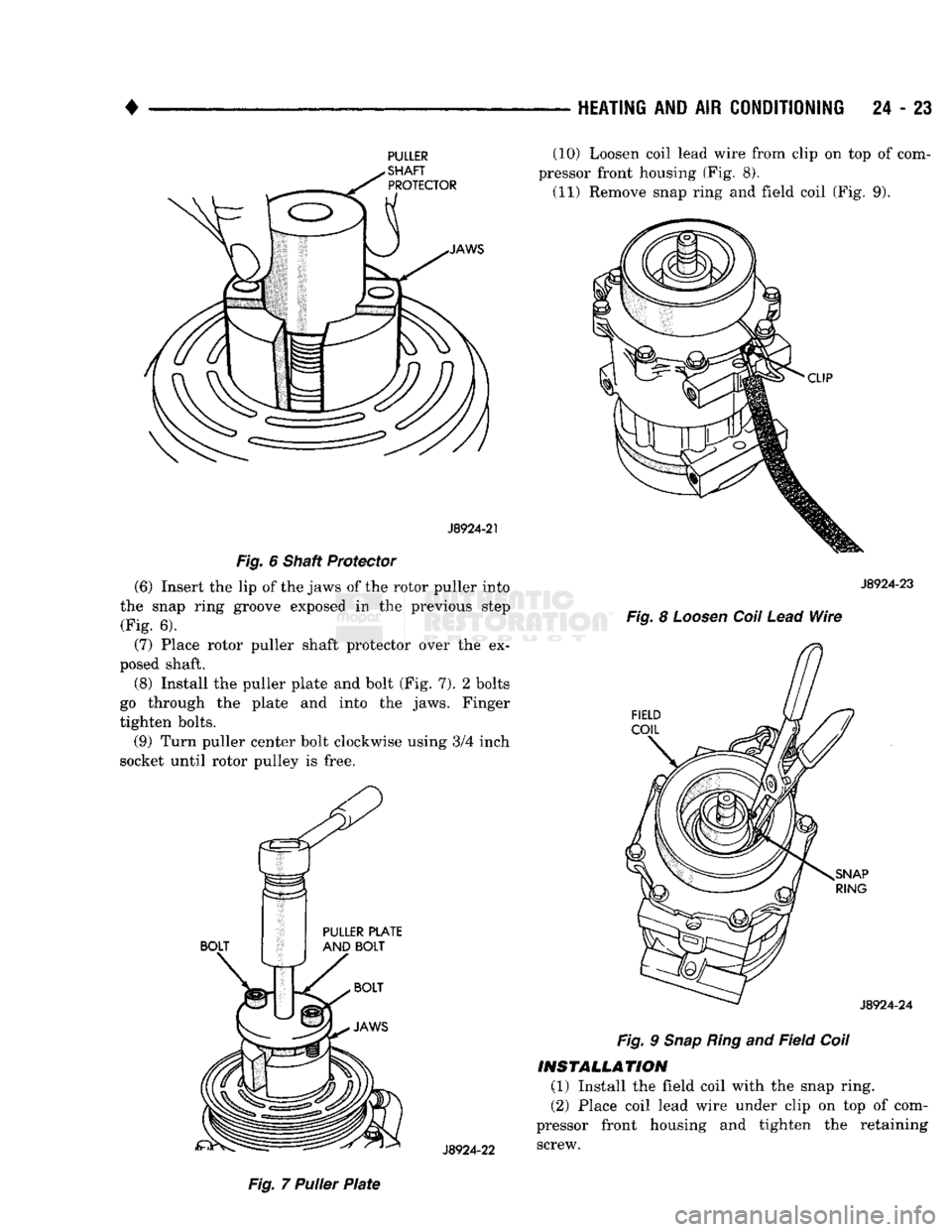
HEATING
AND AIR
CONDITIONING
24 - 23
PULLER
SHAFT
PROTECTOR
JAWS
(10) Loosen coil lead wire from clip on top of com
pressor front housing (Fig. 8). (11) Remove snap ring and field coil (Fig. 9).
J8924-21
Fig. 6 Shaft Protector
(6)
Insert the lip of the jaws of the rotor puller into
the snap ring groove exposed in the previous step (Fig. 6).
(7) Place rotor puller shaft protector over the ex
posed shaft.
(8) Install the puller plate and bolt (Fig. 7). 2 bolts
go through the plate and into the jaws. Finger
tighten bolts.
(9) Turn puller center bolt clockwise using 3/4 inch
socket until rotor pulley is free.
J8924-23
Fig. 8 Loosen Coil Lead Wire
FIELD
COIL
SNAP
RING
J8924-22
J8924-24
Fig. 9 Snap Ring and Field Coil
INSTALLATION (1) Install the field coil with the snap ring.
(2)
Place coil lead wire under clip on top of com
pressor front housing and tighten the retaining screw.
Fig. 7 Puller Plate