DODGE TRUCK 1993 Service Repair Manual
Manufacturer: DODGE, Model Year: 1993, Model line: TRUCK, Model: DODGE TRUCK 1993Pages: 1502, PDF Size: 80.97 MB
Page 201 of 1502
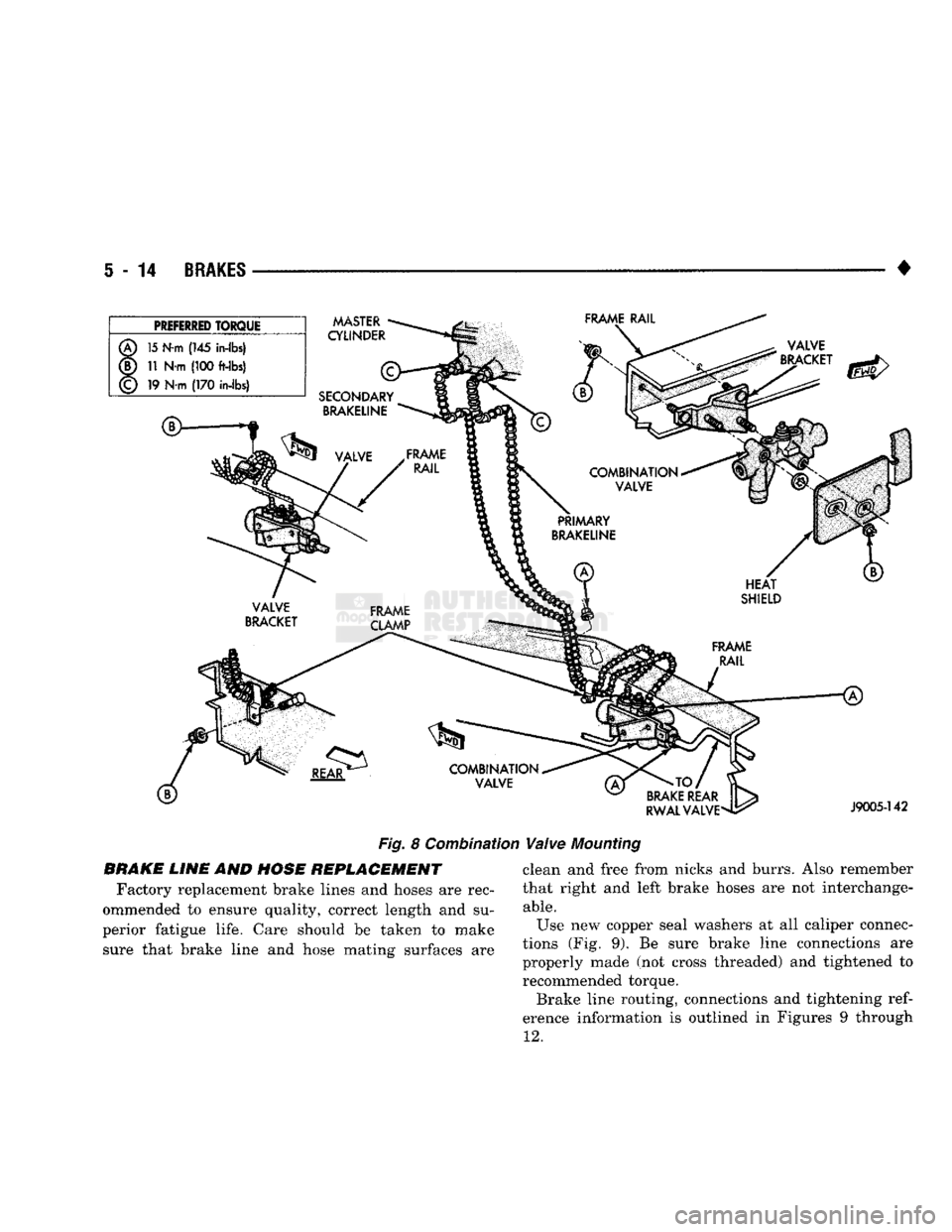
5
- 14
BRAKES
•
Fig. 8 Combinat
BRAKE LINE AND HOSE REPLACEMENT Factory replacement brake lines and hoses are rec
ommended to ensure quality, correct length and su
perior fatigue life. Care should be taken to make sure that brake line and hose mating surfaces are
Valve
Mounting
clean and free from nicks and burrs. Also remember
that right and left brake hoses are not interchange
able.
Use new copper seal washers at all caliper connec
tions (Fig. 9). Be sure brake line connections are
properly made (not cross threaded) and tightened to recommended torque.
Brake line routing, connections and tightening
ref
erence information is outlined in Figures 9 through
12.
Page 202 of 1502
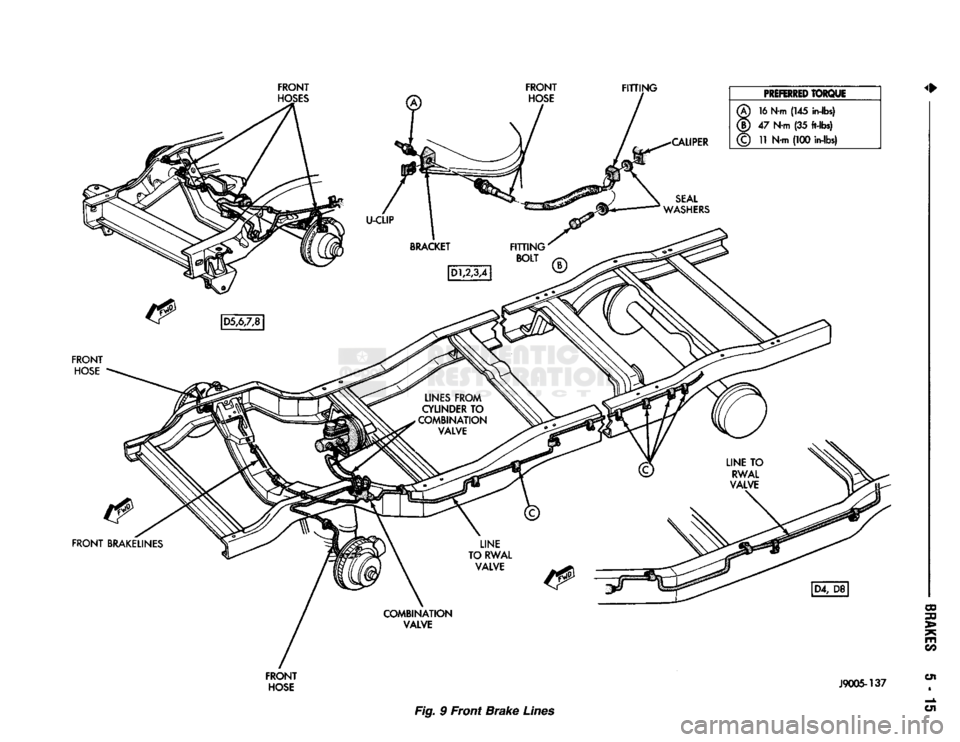
Fig. 9 Front Brake
Lines
Page 203 of 1502
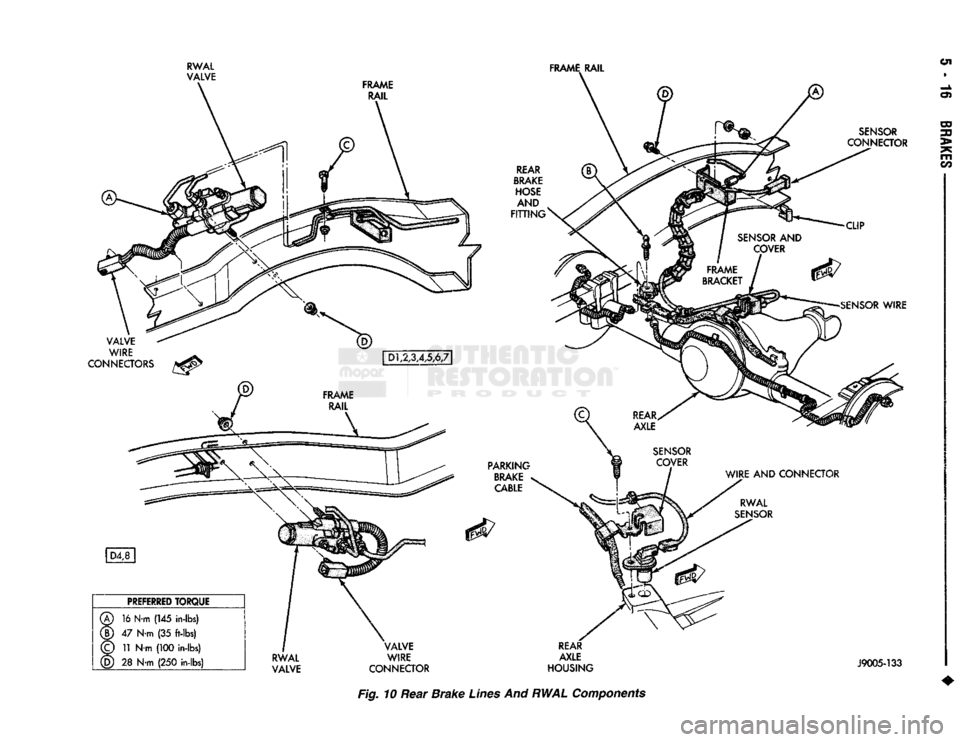
Fig. 10 Rear Brake Lines And
RWAL
Components
Page 204 of 1502
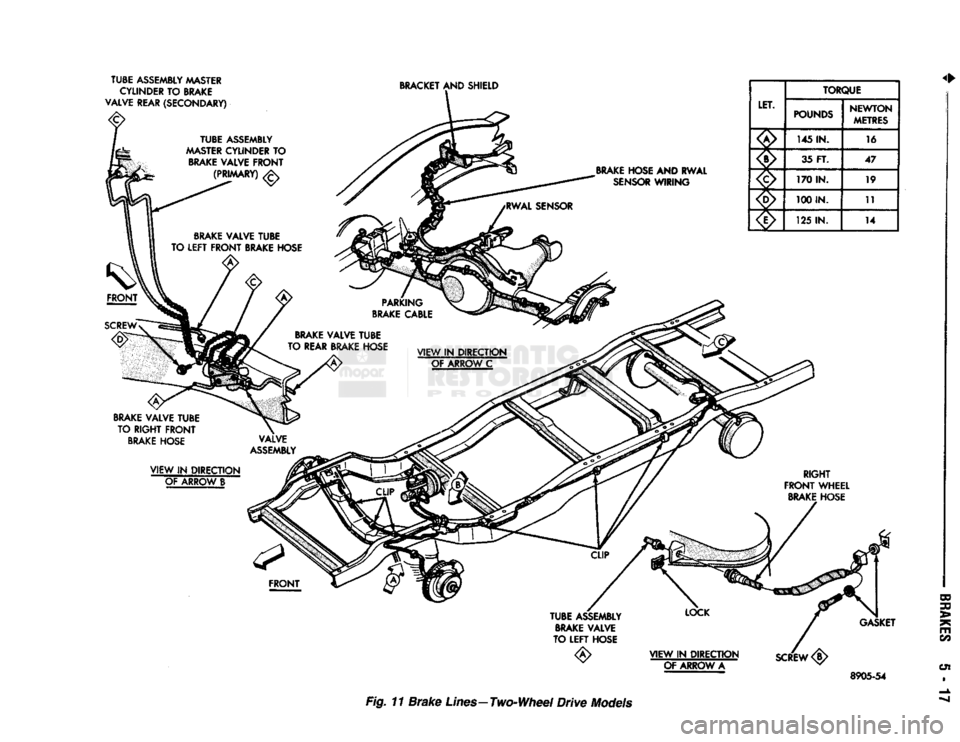
TUBE ASSEMBLY MASTER
CYLINDER TO BRAKE
VALVE REAR (SECONDARY)
BRACKET
AND SHIELD
BRAKE
HOSE AND RWAL
SENSOR
WIRING LET.
TORQUE
LET. POUNDS NEWTON
METRES
x!^ 145 IN.
16
XX 35 FT.
47
170 IN. 19
100 IN.
11
125
IN.
14
BRAKE
VALVE TUBE
TO RIGHT FRONT
BRAKE
HOSE
VIEW IN DIRECTION OF ARROW A
SCREW
<§>
GASKET
8905-54
Fig. 11
Brake
Lines—Two-Wheel
Drive
Models
Page 205 of 1502
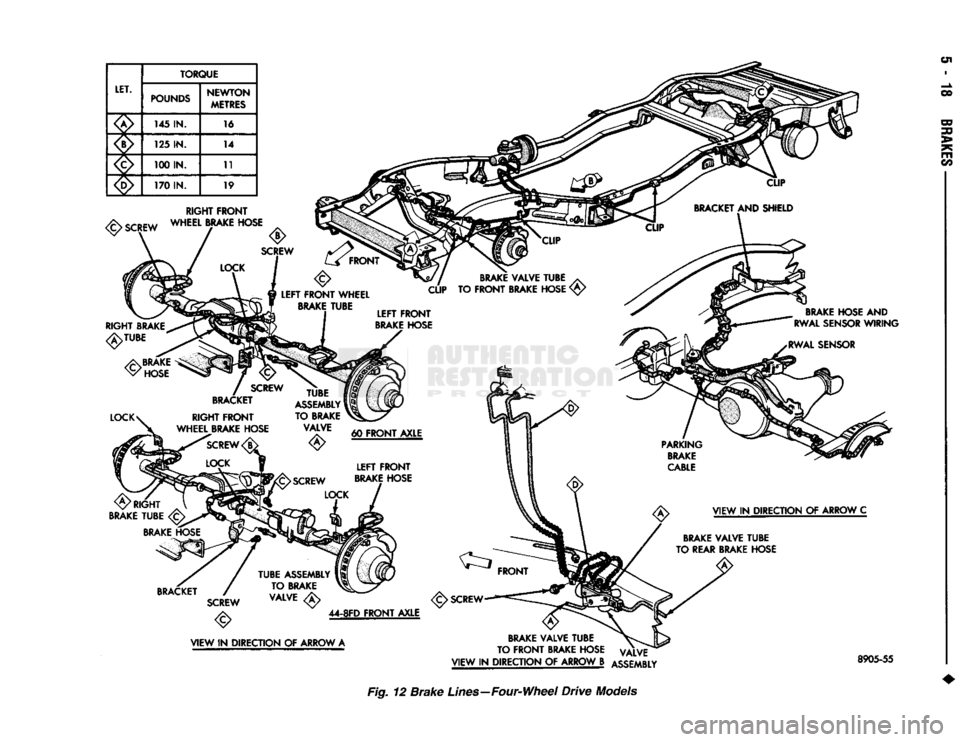
LET.
TORQUE
LET. POUNDS
NEWTON
METRES
145 IN. 16
125 IN. 14
100 IN. 11
170 IN. 19
SCREW
RIGHT
BRAKE
TUBE
RIGHT
BRAKE
TUBE
BRAKE HOSE BRAKE
VALVE
TUBE
TO
FRONT
BRAKE HOSE
VALVE
VIEW
IN
DIRECTION
OF
ARROW
B
ASSEMBLY
8905-55
Fig. 12 Brake Lines—Four-Wheel Drive Models
Page 206 of 1502
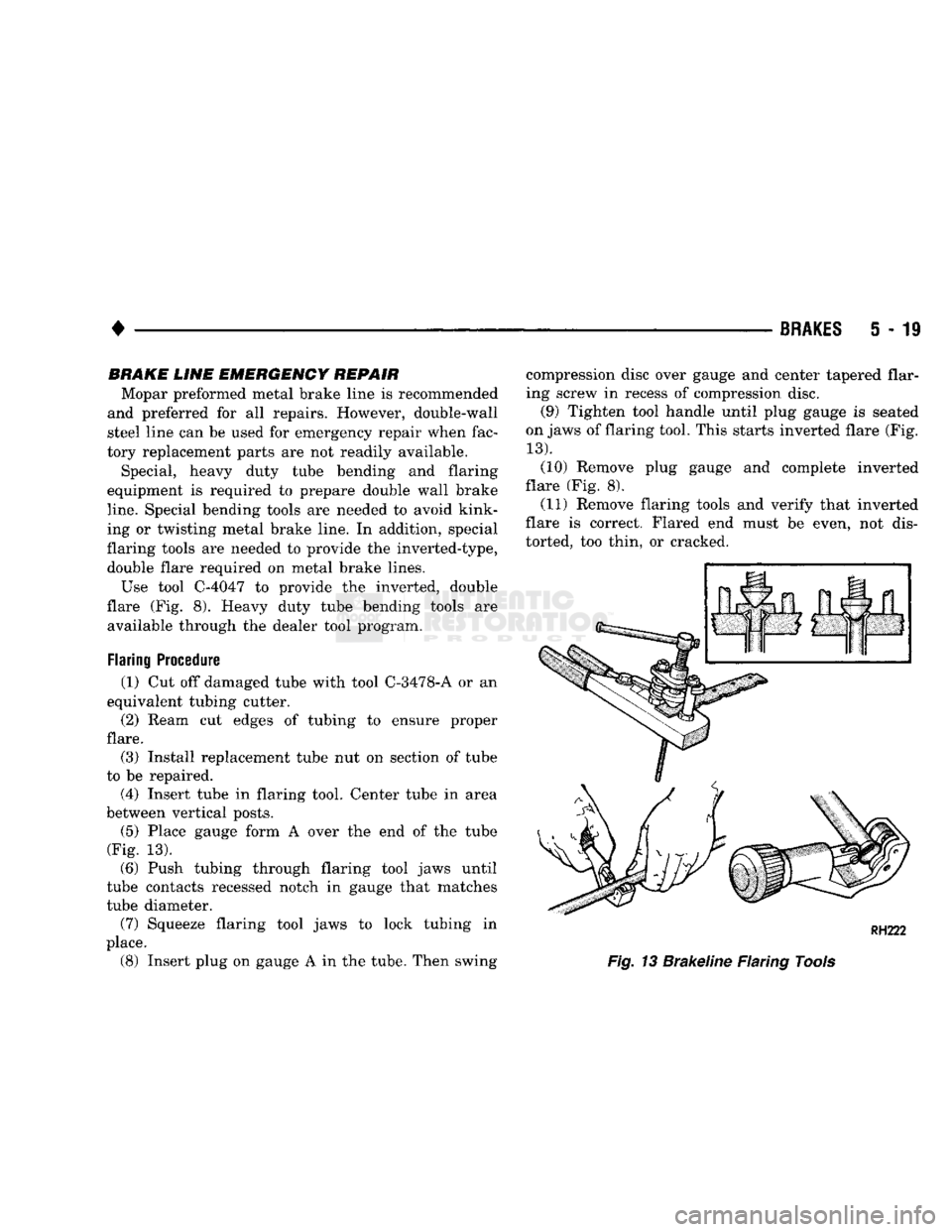
•
BRAKES
5-19 BRAKE LINE EMERGENCY REPAIR
Mopar preformed metal brake line is recommended
and preferred for all repairs. However, double-wall
steel line can be used for emergency repair when fac
tory replacement parts are not readily available.
Special, heavy duty tube bending and flaring
equipment is required to prepare double wall brake
line.
Special bending tools are needed to avoid kink ing or twisting metal brake line. In addition, special
flaring tools are needed to provide the inverted-type, double flare required on metal brake lines.
Use tool C-4047 to provide the inverted, double
flare (Fig. 8). Heavy duty tube bending tools are available through the dealer tool program.
Flaring Procedure (1) Cut off damaged tube with tool C-3478-A or an
equivalent tubing cutter.
(2) Ream cut edges of tubing to ensure proper
flare.
(3) Install replacement tube nut on section of tube
to be repaired. (4) Insert tube in flaring tool. Center tube in area
between vertical posts.
(5) Place gauge form A over the end of the tube
(Fig. 13).
(6) Push tubing through flaring tool jaws until
tube contacts recessed notch in gauge that matches
tube diameter.
(7) Squeeze flaring tool jaws to lock tubing in
place. (8) Insert plug on gauge A in the tube. Then swing compression disc over gauge and center tapered flar
ing screw in recess of compression disc (9) Tighten tool handle until plug gauge is seated
on jaws of flaring tool. This starts inverted flare (Fig.
13).
(10) Remove plug gauge and complete inverted
flare (Fig. 8). (11) Remove flaring tools and verify that inverted
flare is correct. Flared end must be even, not dis
torted, too thin, or cracked.
RH222
Fig. 13 Brakeline Flaring Tools
Page 207 of 1502
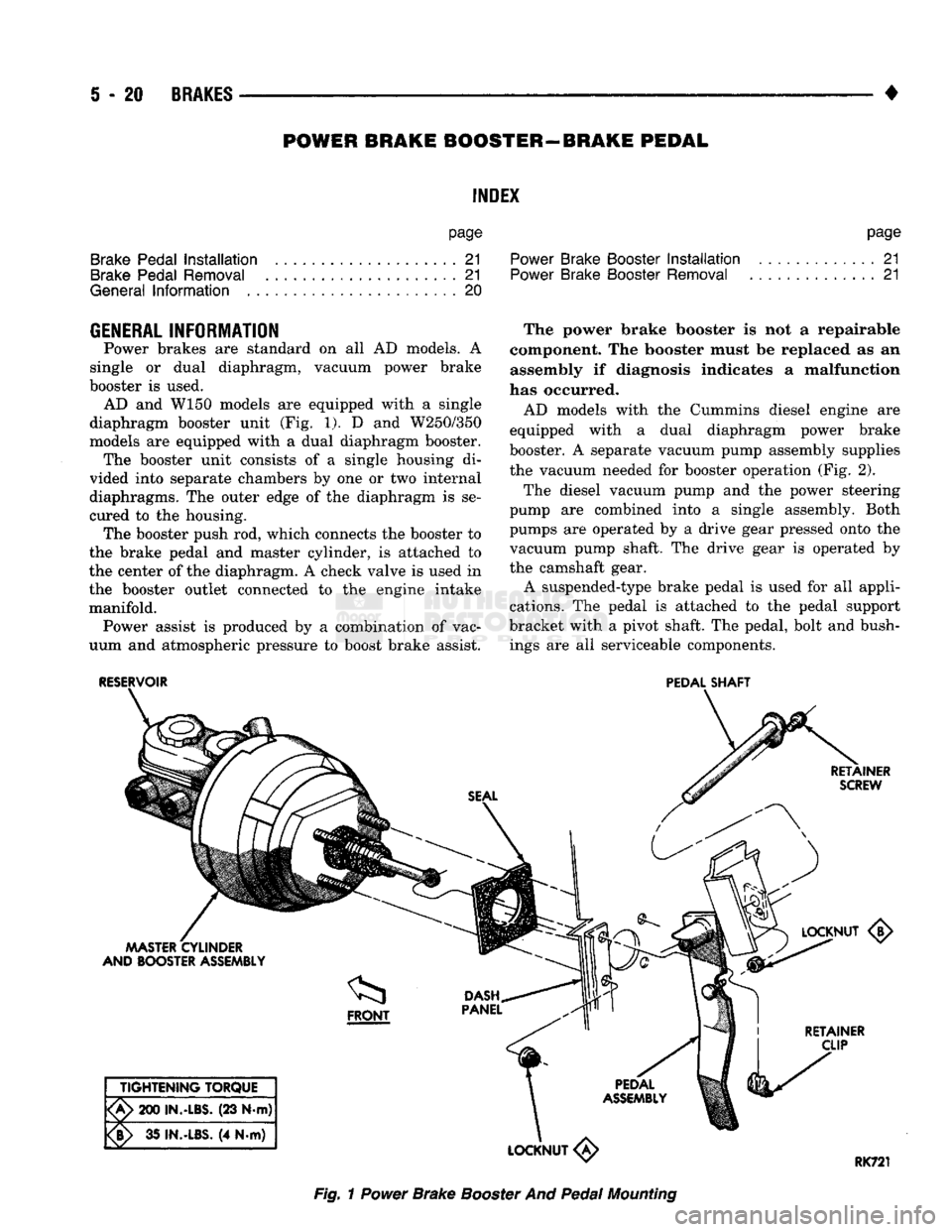
5
- 20
BRAKES
•
POWER BRAKE BOOSTER—BRAKE PEDAL
INDEX
page
Brake Pedal
Installation
21
Brake Pedal Removal
21
General
Information
.......................
20
page
Power Brake Booster
Installation
.............
21
Power Brake Booster Removal
21
GENERAL
INFORMATION
Power brakes
are
standard
on all AD
models.
A
single
or
dual diaphragm, vacuum power brake
booster
is
used. AD
and W150
models
are
equipped with
a
single
diaphragm booster unit
(Fig. 1). D and
W250/350
models
are
equipped with
a
dual diaphragm booster. The booster unit consists
of a
single housing
di
vided into separate chambers
by one or two
internal
diaphragms.
The
outer edge
of the
diaphragm
is se
cured
to the
housing. The booster push
rod,
which connects
the
booster
to
the brake pedal
and
master cylinder,
is
attached
to
the center
of the
diaphragm.
A
check valve
is
used
in
the booster outlet connected
to the
engine intake manifold. Power assist
is
produced
by a
combination
of
vac
uum
and
atmospheric pressure
to
boost brake assist. The power brake booster
is not a
repairable
component.
The
booster must
be
replaced
as an
assembly
if
diagnosis indicates
a
malfunction
has occurred.
AD models with
the
Cummins diesel engine
are
equipped with
a
dual diaphragm power brake
booster.
A
separate vacuum pump assembly supplies the vacuum needed
for
booster operation
(Fig. 2).
The diesel vacuum pump
and the
power steering
pump
are
combined into
a
single assembly. Both
pumps
are
operated
by a
drive gear pressed onto
the
vacuum pump shaft.
The
drive gear
is
operated
by
the camshaft gear. A suspended-type brake pedal
is
used
for all
appli
cations.
The
pedal
is
attached
to the
pedal support
bracket with
a
pivot shaft.
The
pedal, bolt
and
bush ings
are all
serviceable components.
RESERVOIR
PEDAL
SHAFT
RETAINER
SCREW
MASTER
CYLINDER
AND BOOSTER
ASSEMBLY <5>
I
RETAINER
CLIP
TIGHTENING
TORQUE
'A>
200
IN.-LBS.
(23 N-m)
¥>
35
IN.-LBS.
(4 N.m)
LOCKNUT
«
RK721
Fig.
1
Power
Brake
Booster
And
Pedal
Mounting
Page 208 of 1502
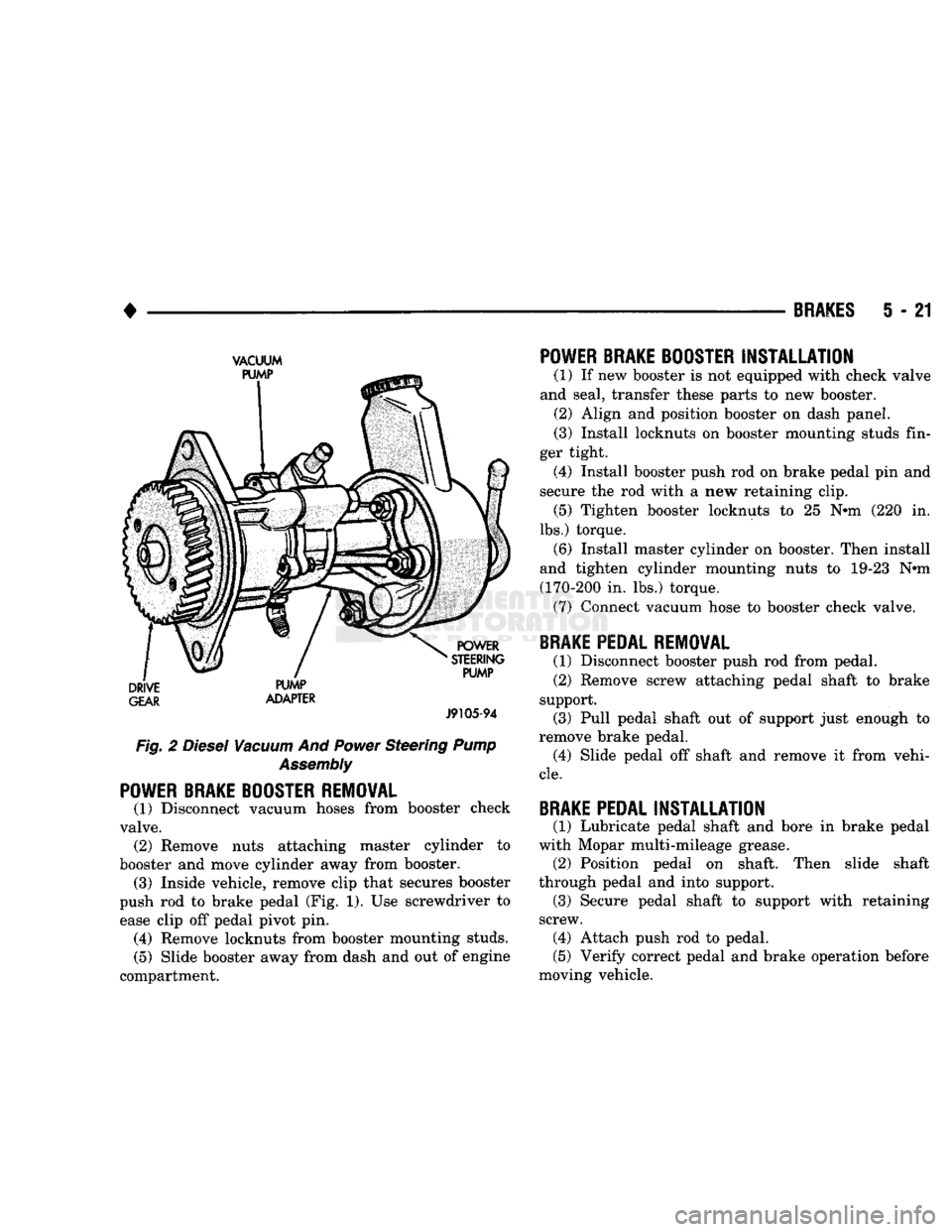
•
BRAKES
5 - 21
VACUUM
GEAR
ADAPTER
J9105-94
Fig. 2
Diesel
Vacuum
And
Power
Steering
Pump
Assembly
POWER BRAKE BOOSTER REMOVAL
(1) Disconnect vacuum hoses from booster check
valve. (2) Remove nuts attaching master cylinder to
booster and move cylinder away from booster. (3) Inside vehicle, remove clip that secures booster
push rod to brake pedal (Fig. 1). Use screwdriver to ease clip off pedal pivot pin. (4) Remove locknuts from booster mounting studs.
(5) Slide booster away from dash and out of engine
compartment.
POWER BRAKE BOOSTER
INSTALLATION
(1) If new booster is not equipped with check valve
and seal, transfer these parts to new booster. (2) Align and position booster on dash panel.
(3) Install locknuts on booster mounting studs fin
ger tight. (4) Install booster push rod on brake pedal pin and
secure the rod with a new retaining clip. (5) Tighten booster locknuts to 25 Nth (220 in.
lbs.) torque. (6) Install master cylinder on booster. Then install
and tighten cylinder mounting nuts to 19-23 Nnn
(170-200 in. lbs.) torque. (7) Connect vacuum hose to booster check valve.
BRAKE PEDAL REMOVAL
(1) Disconnect booster push rod from pedal. (2) Remove screw attaching pedal shaft to brake
support. (3) Pull pedal shaft out of support just enough to
remove brake pedal. (4) Slide pedal off shaft and remove it from vehi
cle.
BRAKE PEDAL
INSTALLATION
(1) Lubricate pedal shaft and bore in brake pedal
with Mopar multi-mileage grease. (2) Position pedal on shaft. Then slide shaft
through pedal and into support. (3) Secure pedal shaft to support with retaining
screw. (4) Attach push rod to pedal.
(5) Verify correct pedal and brake operation before
moving vehicle.
Page 209 of 1502
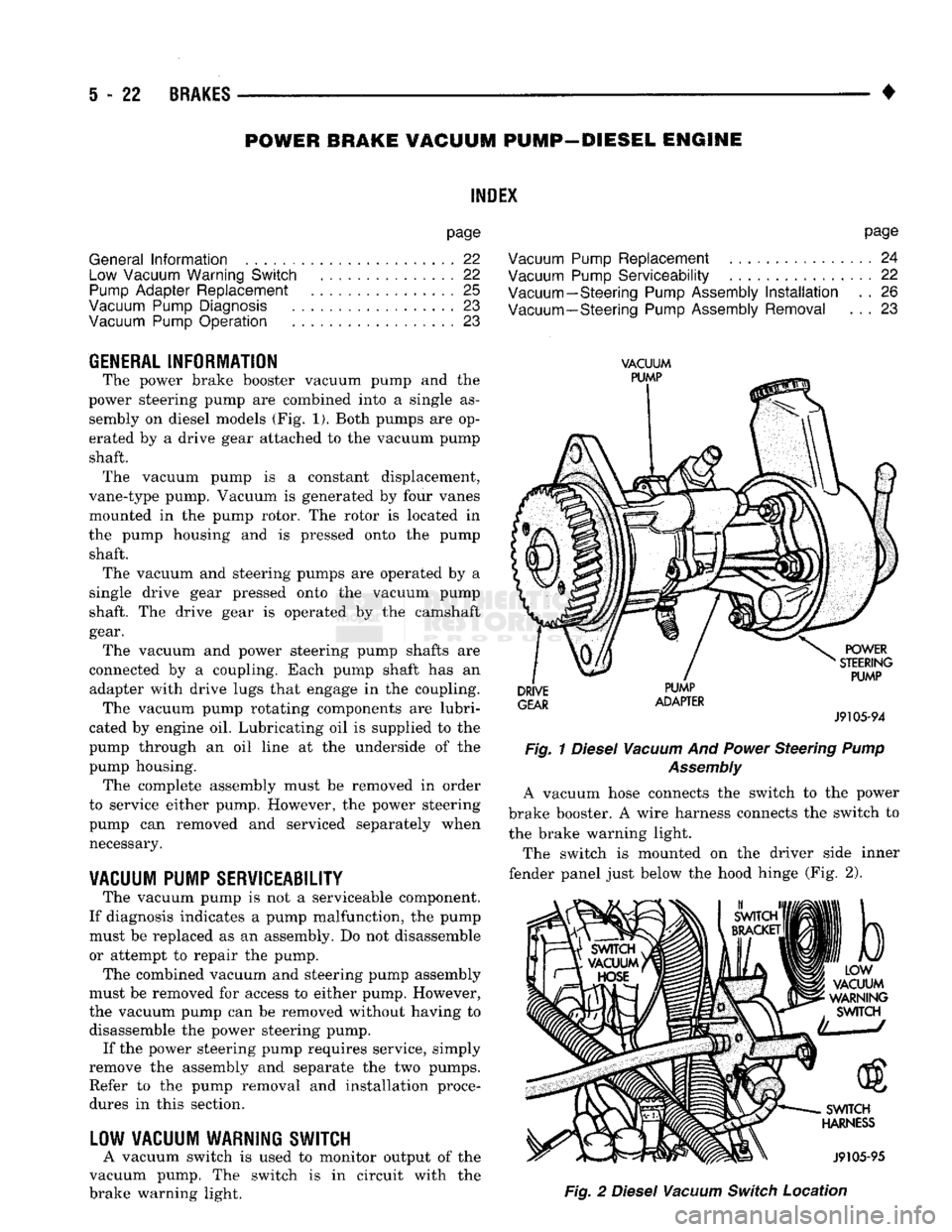
5
- 22
BRAKES
POWER BRAKE
VACUUM
PUMP—DIESEL ENGINE
INDEX
page
General
Information
22
Low
Vacuum
Warning
Switch
22
Pump
Adapter
Replacement
. 25
Vacuum
Pump
Diagnosis
..................
23
Vacuum
Pump
Operation
..................
23
page
Vacuum
Pump
Replacement
24
Vacuum
Pump
Serviceability
22
Vacuum—Steering
Pump
Assembly
Installation
. . 26
Vacuum—Steering
Pump
Assembly
Removal
... 23
GENERAL
INFORMATION
The power brake booster vacuum pump
and the
power steering pump
are
combined into
a
single
as
sembly
on
diesel models
(Fig. 1).
Both pumps
are op
erated
by a
drive gear attached
to the
vacuum pump shaft. The vacuum pump
is a
constant displacement,
vane-type pump. Vacuum
is
generated
by
four vanes
mounted
in the
pump rotor.
The
rotor
is
located
in
the pump housing
and is
pressed onto
the
pump shaft. The vacuum
and
steering pumps
are
operated
by a
single drive gear pressed onto
the
vacuum pump
shaft.
The
drive gear
is
operated
by the
camshaft
gear. The vacuum
and
power steering pump shafts
are
connected
by a
coupling. Each pump shaft
has an
adapter with drive lugs that engage
in the
coupling. The vacuum pump rotating components
are
lubri
cated
by
engine
oil.
Lubricating
oil is
supplied
to the
pump through
an oil
line
at the
underside
of the
pump housing. The complete assembly must
be
removed
in
order
to service either pump. However,
the
power steering
pump
can
removed
and
serviced separately when necessary.
VACUUM
PUMP
SERVICEABILITY
The vacuum pump
is not a
serviceable component.
If diagnosis indicates
a
pump malfunction,
the
pump must
be
replaced
as an
assembly.
Do not
disassemble
or attempt
to
repair
the
pump.
The combined vacuum
and
steering pump assembly
must
be
removed
for
access
to
either pump. However,
the vacuum pump
can be
removed without having
to
disassemble
the
power steering pump. If
the
power steering pump requires service, simply
remove
the
assembly
and
separate
the two
pumps. Refer
to the
pump removal
and
installation procedures
in
this section.
LOW
VACUUM
WARNING
SWITCH
A vacuum switch
is
used
to
monitor output
of the
vacuum pump.
The
switch
is in
circuit with
the
brake warning light.
VACUUM
PUMP
DRIVE
GEAR
PUMP
ADAPTER
POWER
STEERING
PUMP
J9105-94
Fig.
1
Diesel
Vacuum
And
Power
Steering
Pump
Assembly
A vacuum hose connects
the
switch
to the
power
brake booster.
A
wire harness connects
the
switch
to
the brake warning light.
The switch
is
mounted
on the
driver side inner
fender panel just below
the
hood hinge
(Fig. 2),
b
LOW
VACUUM
WARNING
SWITCH
SWITCH
HARNESS
J9105-95
Fig.
2
Diesel
Vacuum
Switch
Location
Page 210 of 1502
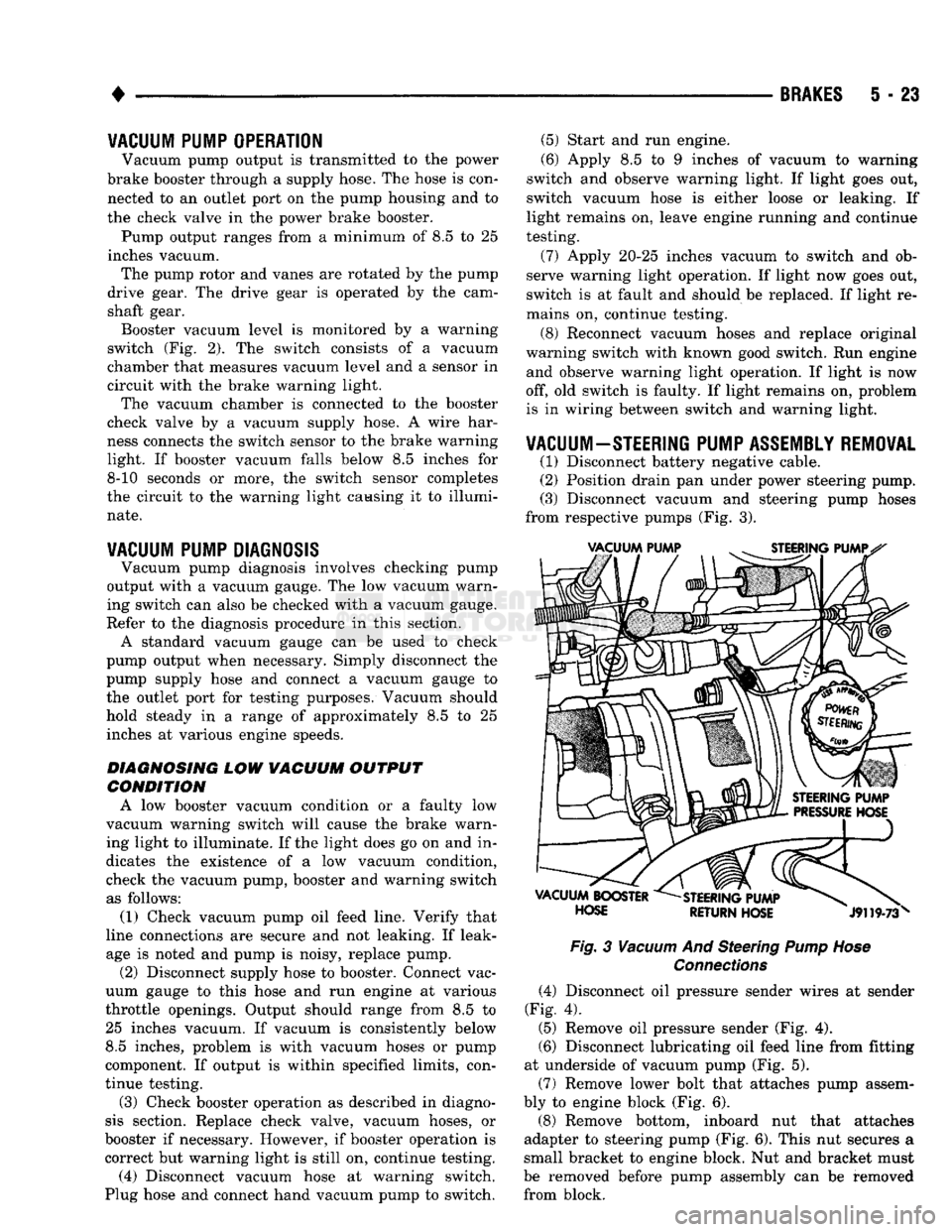
•
BRAKES
5 - 23
VACUUM PUMP OPERATION
Vacuum pump output is transmitted to the power
brake booster through a supply hose. The hose is con nected to an outlet port on the pump housing and to
the check valve in the power brake booster.
Pump output ranges from a minimum of 8.5 to 25
inches vacuum. The pump rotor and vanes are rotated by the pump
drive gear. The drive gear is operated by the cam
shaft gear. Booster vacuum level is monitored by a warning
switch (Fig. 2). The switch consists of a vacuum
chamber that measures vacuum level and a sensor in
circuit with the brake warning light. The vacuum chamber is connected to the booster
check valve by a vacuum supply hose. A wire har
ness connects the switch sensor to the brake warning
light. If booster vacuum falls below 8.5 inches for 8-10 seconds or more, the switch sensor completes
the circuit to the warning light causing it to illumi
nate.
VACUUM PUMP DIAGNOSIS
Vacuum pump diagnosis involves checking pump
output with a vacuum gauge. The low vacuum warn
ing switch can also be checked with a vacuum gauge.
Refer to the diagnosis procedure in this section. A standard vacuum gauge can be used to check
pump output when necessary. Simply disconnect the
pump supply hose and connect a vacuum gauge to
the outlet port for testing purposes. Vacuum should
hold steady in a range of approximately 8.5 to 25 inches at various engine speeds.
DIAGNOSING LOW VACUUM OUTPUT CONDITION A low booster vacuum condition or a faulty low
vacuum warning switch will cause the brake warn ing light to illuminate. If the light does go on and in
dicates the existence of a low vacuum condition,
check the vacuum pump, booster and warning switch
as follows:
(1) Check vacuum pump oil feed line. Verify that
line connections are secure and not leaking. If leak age is noted and pump is noisy, replace pump.
(2) Disconnect supply hose to booster. Connect vac
uum gauge to this hose and run engine at various
throttle openings. Output should range from 8.5 to 25 inches vacuum. If vacuum is consistently below
8.5 inches, problem is with vacuum hoses or pump
component. If output is within specified limits, con
tinue testing.
(3) Check booster operation as described in diagno
sis section. Replace check valve, vacuum hoses, or
booster if necessary. However, if booster operation is correct but warning light is still on, continue testing. (4) Disconnect vacuum hose at warning switch.
Plug hose and connect hand vacuum pump to switch. (5) Start and run engine.
(6) Apply 8.5 to 9 inches of vacuum to warning
switch and observe warning light. If light goes out,
switch vacuum hose is either loose or leaking. If
light remains on, leave engine running and continue
testing.
(7) Apply 20-25 inches vacuum to switch and ob
serve warning light operation. If light now goes out,
switch is at fault and should be replaced. If light re
mains on, continue testing.
(8) Reconnect vacuum hoses and replace original
warning switch with known good switch. Run engine and observe warning light operation. If light is now
off, old switch is faulty. If light remains on, problem
is in wiring between switch and warning light.
VACUUM-STEERING PUMP
ASSEMBLY
REMOVAL
(1) Disconnect battery negative cable.
(2) Position drain pan under power steering pump.
(3) Disconnect vacuum and steering pump hoses
from respective pumps (Fig. 3).
Fig.
3
Vacuum
And Steering
Pump Hose
Connections
(4) Disconnect oil pressure sender wires at sender
(Fig. 4).
(5) Remove oil pressure sender (Fig. 4).
(6) Disconnect lubricating oil feed line from fitting
at underside of vacuum pump (Fig. 5).
(7) Remove lower bolt that attaches pump assem
bly to engine block (Fig. 6).
(8) Remove bottom, inboard nut that attaches
adapter to steering pump (Fig. 6). This nut secures a
small bracket to engine block. Nut and bracket must
be removed before pump assembly can be removed from block.