DODGE TRUCK 1993 Service Repair Manual
Manufacturer: DODGE, Model Year: 1993, Model line: TRUCK, Model: DODGE TRUCK 1993Pages: 1502, PDF Size: 80.97 MB
Page 191 of 1502
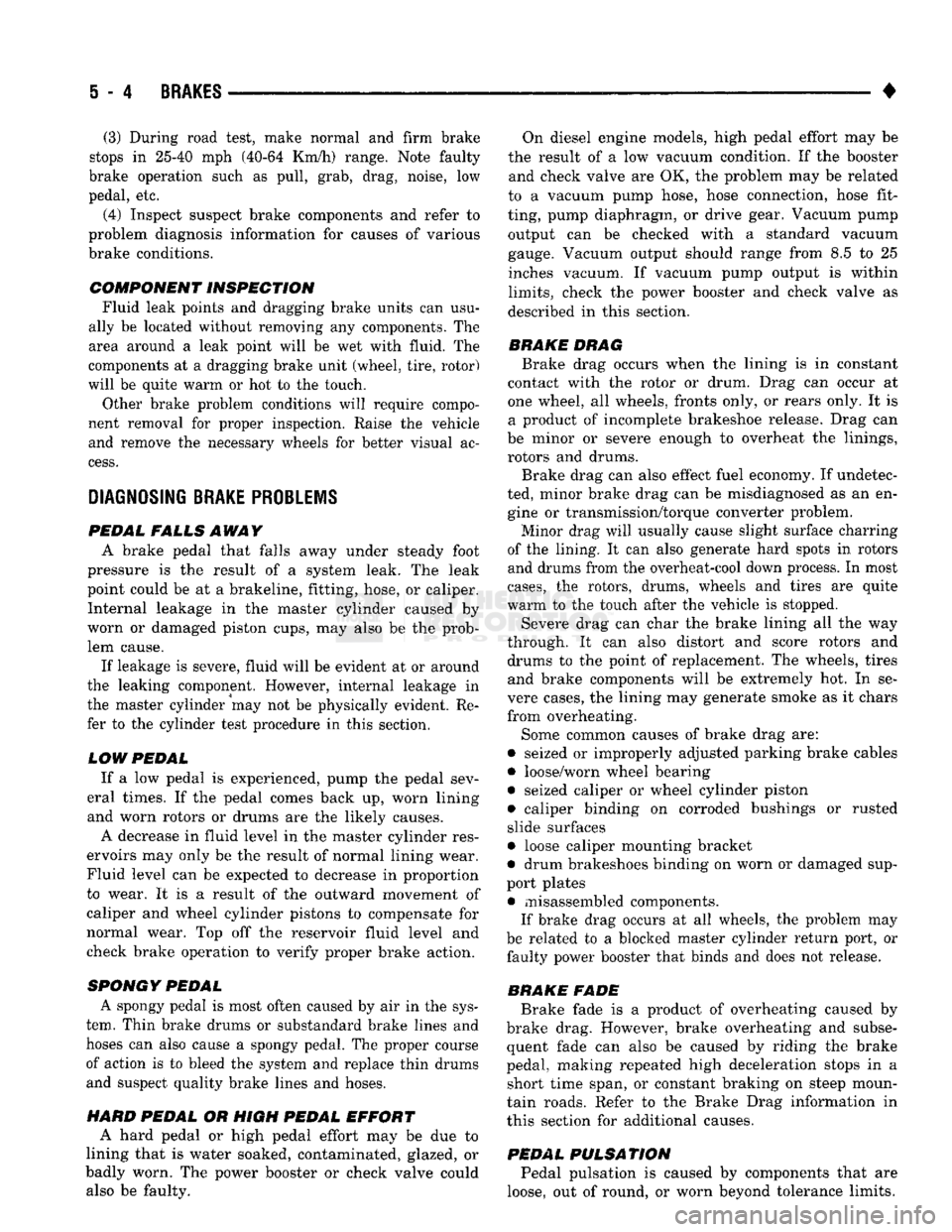
5
- 4
BRAKES
• (3) During road test, make normal and firm brake
stops in 25-40 mph (40-64 Km/h) range. Note faulty
brake operation such as pull, grab, drag, noise, low
pedal, etc.
(4) Inspect suspect brake components and refer to
problem diagnosis information for causes of various
brake conditions.
COMPONENT
INSPECTION
Fluid leak points and dragging brake units can usu
ally be located without removing any components. The
area around a leak point will be wet with fluid. The
components at a dragging brake unit (wheel, tire, rotor)
will be quite warm or hot to the touch.
Other brake problem conditions will require compo
nent removal for proper inspection. Raise the vehicle and remove the necessary wheels for better visual ac
cess.
DIAGNOSING BRAKE
PROBLEMS
PEDAL FALLS
AWAY
A
brake pedal that falls away under steady foot
pressure is the result of a system leak. The leak
point could be at a brakeline, fitting, hose, or caliper. Internal leakage in the master cylinder caused by
worn or damaged piston cups, may also be the prob lem cause.
If leakage is severe, fluid will be evident at or around
the leaking component. However, internal leakage in
the master cylinder may not be physically evident. Re fer to the cylinder test procedure in this section.
LOW PEDAL
If a low pedal is experienced, pump the pedal sev
eral times. If the pedal comes back up, worn lining
and worn rotors or drums are the likely causes.
A decrease in fluid level in the master cylinder res
ervoirs may only be the result of normal lining wear.
Fluid level can be expected to decrease in proportion to wear. It is a result of the outward movement of
caliper and wheel cylinder pistons to compensate for
normal wear. Top off the reservoir fluid level and
check brake operation to verify proper brake action.
SPONGY PEDAL. A spongy pedal is most often caused by air in the sys
tem. Thin brake drums or substandard brake lines and
hoses can also cause a spongy pedal. The proper course
of action is to bleed the system and replace thin drums and suspect quality brake lines and hoses.
HARD PEDAL
OR
HIGH
PEDAL
EFFORT
A hard pedal or high pedal effort may be due to
lining that is water soaked, contaminated, glazed, or
badly worn. The power booster or check valve could also be faulty. On diesel engine models, high pedal effort may be
the result of a low vacuum condition. If the booster and check valve are OK, the problem may be related
to a vacuum pump hose, hose connection, hose fit
ting, pump diaphragm, or drive gear. Vacuum pump output can be checked with a standard vacuum
gauge. Vacuum output should range from 8.5 to 25 inches vacuum. If vacuum pump output is within
limits,
check the power booster and check valve as
described in this section.
BRAKE DRAG
Brake drag occurs when the lining is in constant
contact with the rotor or drum. Drag can occur at
one wheel, all wheels, fronts only, or rears only. It is a product of incomplete brakeshoe release. Drag can
be minor or severe enough to overheat the linings,
rotors and drums.
Brake drag can also effect fuel economy. If undetec
ted, minor brake drag can be misdiagnosed as an en gine or transmission/torque converter problem.
Minor drag will usually cause slight surface charring
of the lining. It can also generate hard spots in rotors and drums from the overheat-cool down process. In most
cases,
the rotors, drums, wheels and tires are quite
warm to the touch after the vehicle is stopped.
Severe drag can char the brake lining all the way
through. It can also distort and score rotors and drums to the point of replacement. The wheels, tires and brake components will be extremely hot. In se
vere cases, the lining may generate smoke as it chars
from overheating.
Some common causes of brake drag are:
• seized or improperly adjusted parking brake cables
• loose/worn wheel bearing
• seized caliper or wheel cylinder piston
• caliper binding on corroded bushings or rusted
slide surfaces
• loose caliper mounting bracket
• drum brakeshoes binding on worn or damaged sup
port plates
• misassembled components. If brake drag occurs at all wheels, the problem may
be related to a blocked master cylinder return port, or faulty power booster that binds and does not release.
BRAKE FADE
Brake fade is a product of overheating caused by
brake drag. However, brake overheating and subse quent fade can also be caused by riding the brake
pedal, making repeated high deceleration stops in a short time span, or constant braking on steep moun
tain roads. Refer to the Brake Drag information in
this section for additional causes.
PEDAL
PULSA
TION
Pedal pulsation is caused by components that are
loose, out of round, or worn beyond tolerance limits.
Page 192 of 1502
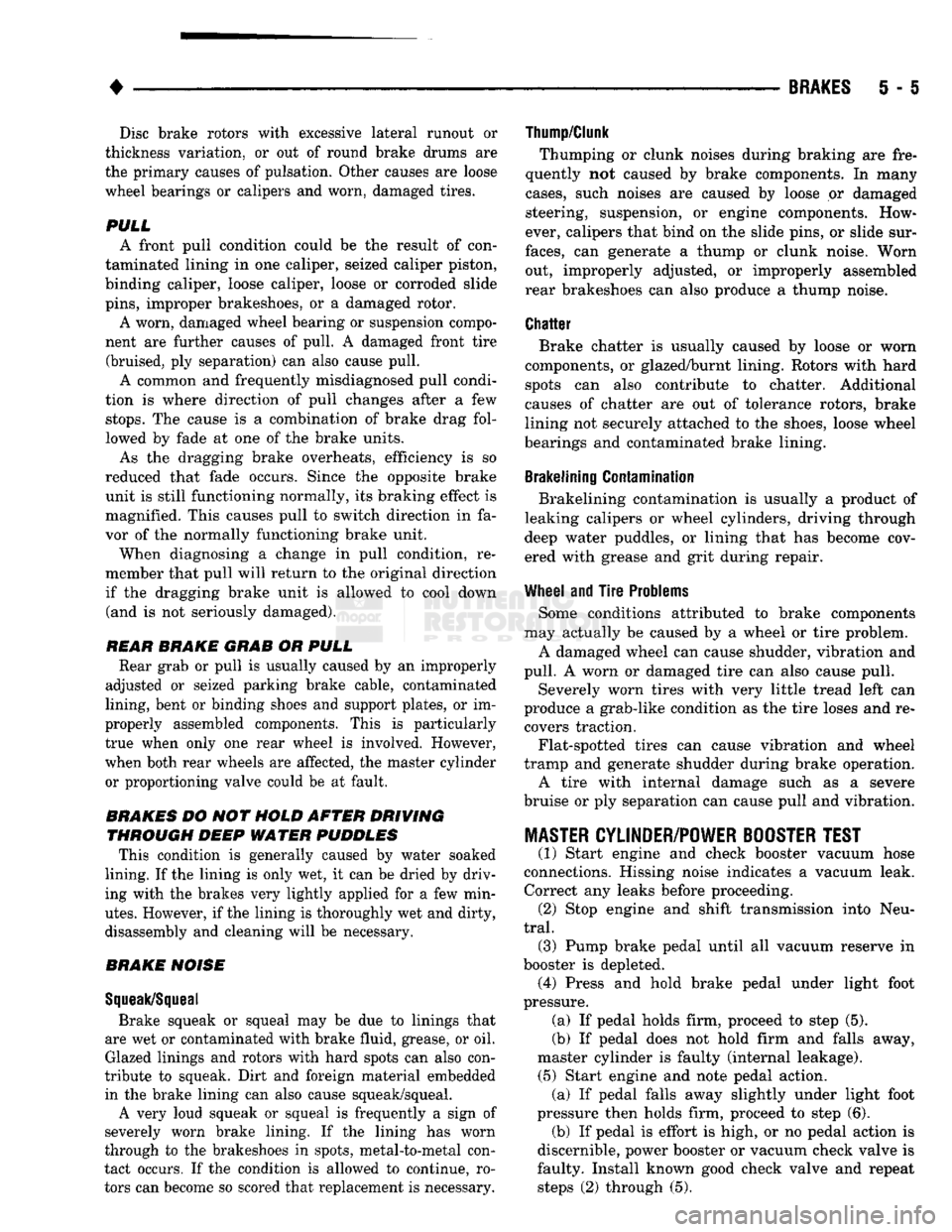
•
BRAKES
5 - 5 Disc brake rotors with excessive lateral runout or
thickness variation, or out of round brake drums are
the primary causes of pulsation. Other causes are loose
wheel bearings or calipers and worn, damaged tires.
PULL A
front pull condition could be the result of con
taminated lining in one caliper, seized caliper piston,
binding caliper, loose caliper, loose or corroded slide
pins,
improper brakeshoes, or a damaged rotor.
A worn, damaged wheel bearing or suspension compo
nent are further causes of pull. A damaged front tire (bruised, ply separation) can also cause pull.
A common and frequently misdiagnosed pull condi
tion is where direction of pull changes after a few
stops.
The cause is a combination of brake drag fol
lowed by fade at one of the brake units.
As the dragging brake overheats, efficiency is so
reduced that fade occurs. Since the opposite brake
unit is still functioning normally, its braking effect is
magnified. This causes pull to switch direction in fa
vor of the normally functioning brake unit.
When diagnosing a change in pull condition, re
member that pull will return to the original direction
if the dragging brake unit is allowed to cool down (and is not seriously damaged).
REAR BRAKE GRAB
OR
PULL
Rear grab or pull is usually caused by an improperly
adjusted or seized parking brake cable, contaminated
lining, bent or binding shoes and support plates, or im
properly assembled components. This is particularly
true when only one rear wheel is involved. However,
when both rear wheels are affected, the master cylinder or proportioning valve could be at fault.
BRAKES
DO NOT
HOLD
AFTER
DRIVING
THROUGH
DEEP
WATER
PUDDLES
This condition is generally caused by water soaked
lining. If the lining is only wet, it can be dried by driv
ing with the brakes very lightly applied for a few min
utes.
However, if the lining is thoroughly wet and dirty,
disassembly and cleaning will be necessary.
BRAKE NOISE
Squeak/Squeal
Brake squeak or squeal may be due to linings that
are wet or contaminated with brake fluid, grease, or oil. Glazed linings and rotors with hard spots can also con
tribute to squeak. Dirt and foreign material embedded in the brake lining can also cause squeak/squeal.
A very loud squeak or squeal is frequently a sign of
severely worn brake lining. If the lining has worn
through to the brakeshoes in spots, metal-to-metal con
tact occurs. If the condition is allowed to continue, ro tors can become so scored that replacement is necessary.
Thump/Clunk
Thumping or clunk noises during braking are fre
quently not caused by brake components. In many
cases,
such noises are caused by loose or damaged steering, suspension, or engine components. How
ever, calipers that bind on the slide pins, or slide sur
faces,
can generate a thump or clunk noise. Worn
out, improperly adjusted, or improperly assembled
rear brakeshoes can also produce a thump noise.
Chatter
Brake chatter is usually caused by loose or worn
components, or glazed/burnt lining. Rotors with hard
spots can also contribute to chatter. Additional
causes of chatter are out of tolerance rotors, brake
lining not securely attached to the shoes, loose wheel
bearings and contaminated brake lining.
Brakelining Contamination Brakelining contamination is usually a product of
leaking calipers or wheel cylinders, driving through
deep water puddles, or lining that has become cov
ered with grease and grit during repair.
Wheel and
Tire
Problems Some conditions attributed to brake components
may actually be caused by a wheel or tire problem.
A damaged wheel can cause shudder, vibration and
pull. A worn or damaged tire can also cause pull.
Severely worn tires with very little tread left can
produce a grab-like condition as the tire loses and re covers traction. Flat-spotted tires can cause vibration and wheel
tramp and generate shudder during brake operation. A tire with internal damage such as a severe
bruise or ply separation can cause pull and vibration.
MASTER
CYLINDER/POWER BOOSTER TEST
(1) Start engine and check booster vacuum hose
connections. Hissing noise indicates a vacuum leak. Correct any leaks before proceeding. (2) Stop engine and shift transmission into Neu
tral (3) Pump brake pedal until all vacuum reserve in
booster is depleted. (4) Press and hold brake pedal under light foot
pressure. (a) If pedal holds firm, proceed to step (5).
(b) If pedal does not hold firm and falls away,
master cylinder is faulty (internal leakage). (5) Start engine and note pedal action. (a) If pedal falls away slightly under light foot
pressure then holds firm, proceed to step (6). (b) If pedal is effort is high, or no pedal action is
discernible, power booster or vacuum check valve is
faulty. Install known good check valve and repeat steps (2) through (5).
Page 193 of 1502
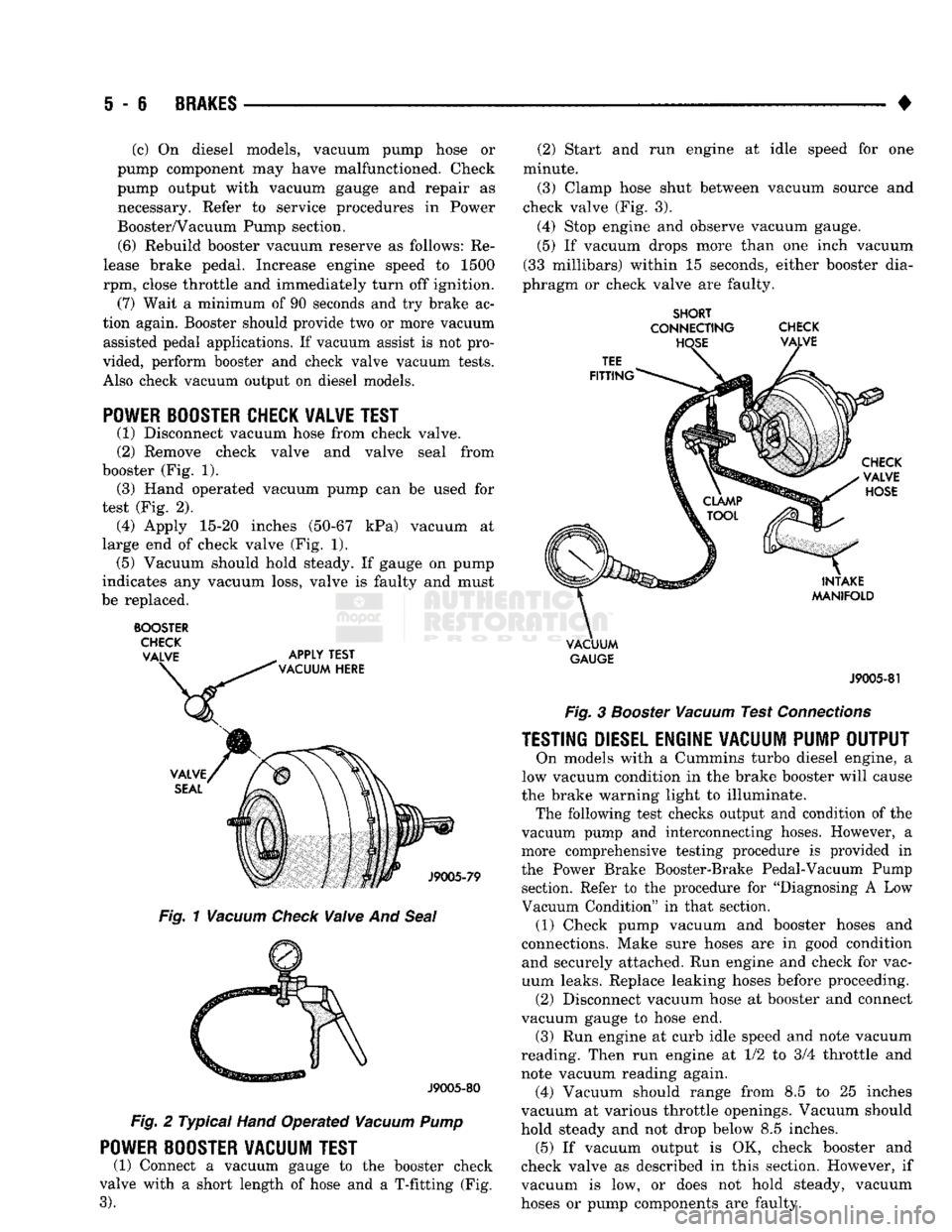
5
- 6
BRAKES
• (c) On diesel models, vacuum pump hose or
pump component may have malfunctioned. Check
pump output with vacuum gauge and repair as necessary. Refer to service procedures in Power
Booster/Vacuum Pump section.
(6) Rebuild booster vacuum reserve as follows: Re
lease brake pedal. Increase engine speed to 1500
rpm, close throttle and immediately turn off ignition. (7) Wait a minimum of 90 seconds and try brake ac
tion again. Booster should provide two or more vacuum assisted pedal applications. If vacuum assist is not pro
vided, perform booster and check valve vacuum tests.
Also check vacuum output on diesel models.
POWER
BOOSTER
CHECK
VALVE
TEST
(1) Disconnect vacuum hose from check valve.
(2) Remove check valve and valve seal from
booster (Fig. 1). (3) Hand operated vacuum pump can be used for
test (Fig. 2). (4) Apply 15-20 inches (50-67 kPa) vacuum at
large end of check valve (Fig. 1). (5) Vacuum should hold steady. If gauge on pump
indicates any vacuum loss, valve is faulty and must
be replaced.
BOOSTER
CHECK
VALVE
APPLY
TEST
\
VACUUM
HERE
Fig.
1
Vacuum
Check
Vaive
And
Seal
J9005-80
Fig.
2 Typical
Hand
Operated
Vacuum
Pump
POWER
BOOSTER
VACUUM
TEST
(1) Connect a vacuum gauge to the booster check
valve with a short length of hose and a T-fitting (Fig.
3).
(2) Start and run engine at idle speed for one
minute.
(3) Clamp hose shut between vacuum source and
check valve (Fig. 3).
(4) Stop engine and observe vacuum gauge.
(5) If vacuum drops more than one inch vacuum
(33 millibars) within 15 seconds, either booster dia
phragm or check valve are faulty.
SHORT
CONNECTING
CHECK
VACUUM
GAUGE
J9005-81
Fig.
3
Booster
Vacuum
Test
Connections
TESTING
DIESEL
ENGINE
VACUUM
PUMP
OUTPUT
On models with a Cummins turbo diesel engine, a
low vacuum condition in the brake booster will cause
the brake warning light to illuminate. The following test checks output and condition of the
vacuum pump and interconnecting hoses. However, a
more comprehensive testing procedure is provided in
the Power Brake Booster-Brake Pedal-Vacuum Pump section. Refer to the procedure for "Diagnosing A Low
Vacuum Condition" in that section. (1) Check pump vacuum and booster hoses and
connections. Make sure hoses are in good condition and securely attached. Run engine and check for vac
uum leaks. Replace leaking hoses before proceeding. (2) Disconnect vacuum hose at booster and connect
vacuum gauge to hose end. (3) Run engine at curb idle speed and note vacuum
reading. Then run engine at 1/2 to 3/4 throttle and
note vacuum reading again. (4) Vacuum should range from 8.5 to 25 inches
vacuum at various throttle openings. Vacuum should
hold steady and not drop below 8.5 inches. (5) If vacuum output is OK, check booster and
check valve as described in this section. However, if
vacuum is low, or does not hold steady, vacuum
hoses or pump components are faulty.
Page 194 of 1502
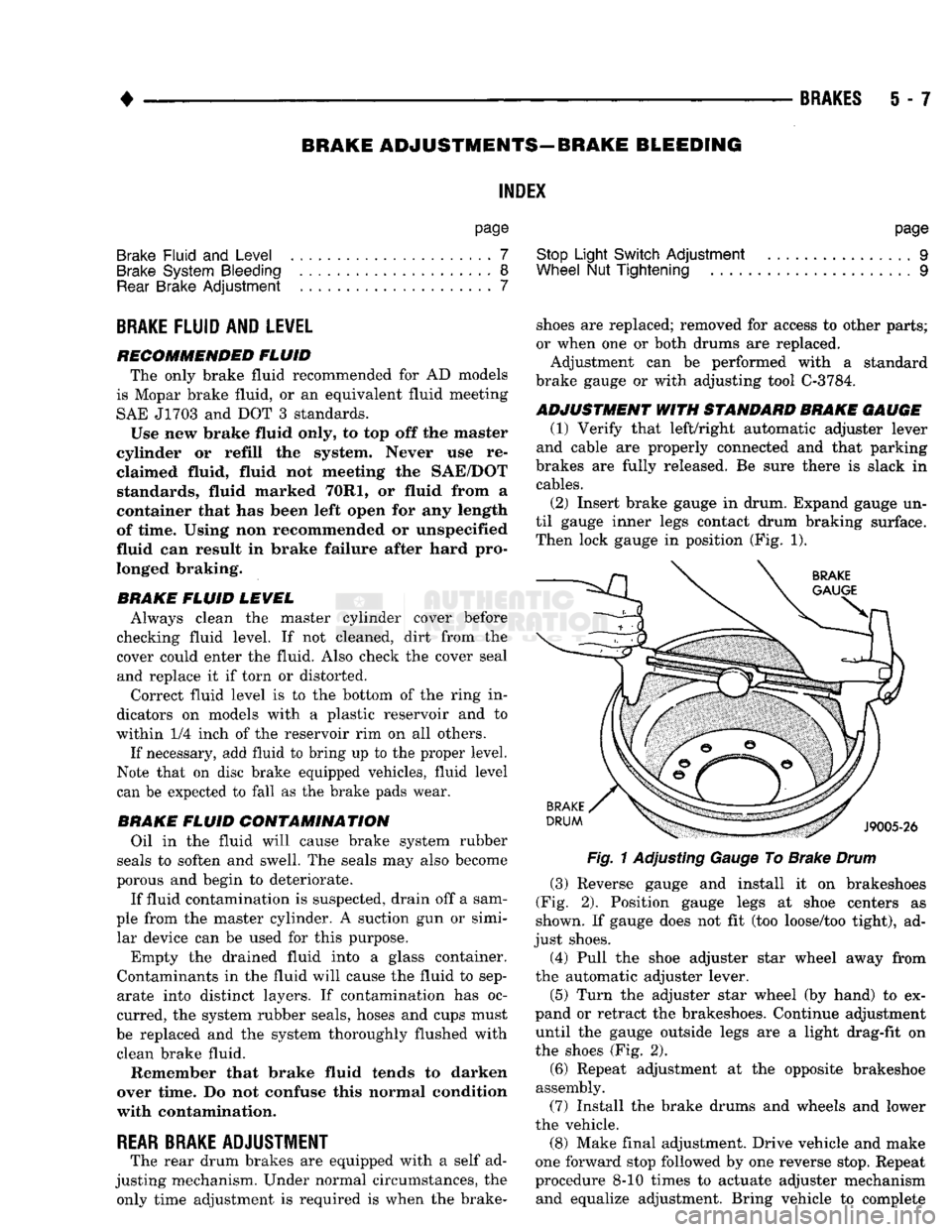
•
BRAKES
i - 7
BRAKE
ADJUSTMENTS-BRAKE
BLEEDING
INDEX
page
Brake
Fluid and Level 7
Brake
System
Bleeding 8
Rear
Brake
Adjustment 7
BRAKE
FLUID
AND
LEWEL
RECOMMENDED
FLUID The only brake fluid recommended for AD models
is Mopar brake fluid, or an equivalent fluid meeting SAE
J1703
and DOT 3 standards.
Use new brake fluid only, to top off the master
cylinder or refill the system* Never use re
claimed fluid, fluid not meeting the
SAE/DOT
standards, fluid marked 70R1, or fluid from a
container that has been left open for any length
of time. Using non recommended or unspecified
fluid can result in brake failure after hard pro longed braking.
BRAKE
FLUID
LEWEL Always clean the master cylinder cover before
checking fluid level. If not cleaned, dirt from the
cover could enter the fluid. Also check the cover seal
and replace it if torn or distorted.
Correct fluid level is to the bottom of the ring in
dicators on models with a plastic reservoir and to
within 1/4 inch of the reservoir rim on all others. If necessary, add fluid to bring up to the proper level.
Note that on disc brake equipped vehicles, fluid level can be expected to fall as the brake pads wear.
BRAKE
FLUID
CONTAMINATION
Oil in the fluid will cause brake system rubber
seals to soften and swell. The seals may also become
porous and begin to deteriorate.
If fluid contamination is suspected, drain off a sam
ple from the master cylinder. A suction gun or simi lar device can be used for this purpose.
Empty the drained fluid into a glass container.
Contaminants in the fluid will cause the fluid to sep
arate into distinct layers. If contamination has oc
curred, the system rubber seals, hoses and cups must
be replaced and the system thoroughly flushed with clean brake fluid.
Remember that brake fluid tends to darken
over time. Do not confuse this normal condition
with contamination.
REAR
BRAKE
ADJUSTMENT
The rear drum brakes are equipped with a self ad
justing mechanism. Under normal circumstances, the only time adjustment is required is when the brake-
page
Stop
Light Switch Adjustment 9
Wheel
Nut Tightening 9
shoes are replaced; removed for access to other parts; or when one or both drums are replaced.
Adjustment can be performed with a standard
brake gauge or with adjusting tool C-3784.
ADJUSTMENT
WITH
STANDARD
BRAKE
GAUGE
(1) Verify that left/right automatic adjuster lever
and cable are properly connected and that parking
brakes are fully released. Be sure there is slack in cables.
(2) Insert brake gauge in drum. Expand gauge un
til gauge inner legs contact drum braking surface. Then lock gauge in position (Fig. 1).
Fig.
1 Adjusting Gauge To Brake
Drum
(3) Reverse gauge and install it on brakeshoes
(Fig. 2). Position gauge legs at shoe centers as
shown. If gauge does not fit (too loose/too tight), ad
just shoes. (4) Pull the shoe adjuster star wheel away from
the automatic adjuster lever.
(5) Turn the adjuster star wheel (by hand) to ex
pand or retract the brakeshoes. Continue adjustment until the gauge outside legs are a light drag-fit on
the shoes (Fig. 2).
(6) Repeat adjustment at the opposite brakeshoe
assembly. (7) Install the brake drums and wheels and lower
the vehicle.
(8) Make final adjustment. Drive vehicle and make
one forward stop followed by one reverse stop. Repeat
procedure 8-10 times to actuate adjuster mechanism and equalize adjustment. Bring vehicle to complete
Page 195 of 1502
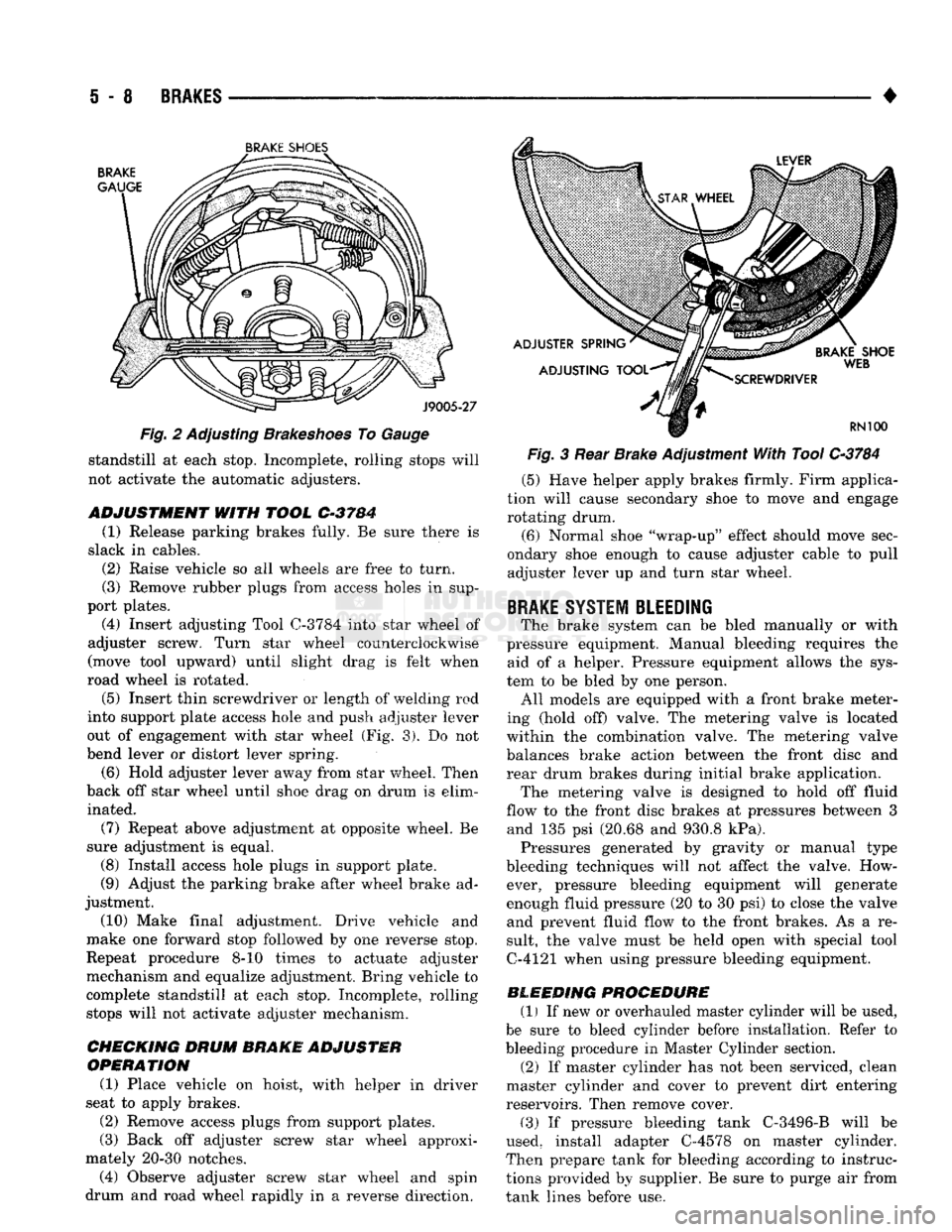
i - 8
BRAKES
•
BRAKE
SHOE'S
Fig. 2 Adjusting Brakeshoes To Gauge standstill at each stop. Incomplete, rolling stops will
not activate the automatic adjusters.
ADJUSTMENT
WITH
TOOL
C-3784
(1) Release parking brakes fully. Be sure there is
slack in cables. (2) Raise vehicle so all wheels are free to turn.
(3) Remove rubber plugs from access holes in sup
port plates. (4) Insert adjusting Tool
0-3784
into star wheel of
adjuster screw. Turn star wheel counterclockwise
(move tool upward) until slight drag is felt when
road wheel is rotated.
(5)
Insert thin screwdriver or length of welding rod
into support plate access hole and push adjuster lever
out of engagement with star wheel (Fig. 3). Do not
bend lever or distort lever spring.
(6) Hold adjuster lever away from star wheel. Then
back off star wheel until shoe drag on drum is elim inated.
(7) Repeat above adjustment at opposite wheel. Be
sure adjustment is equal. (8) Install access hole plugs in support plate.
(9) Adjust the parking brake after wheel brake ad
justment.
(10) Make final adjustment. Drive vehicle and
make one forward stop followed by one reverse stop.
Repeat procedure 8-10 times to actuate adjuster
mechanism and equalize adjustment. Bring vehicle to
complete standstill at each stop. Incomplete, rolling stops will not activate adjuster mechanism.
CHECKING DRUM
BRAKE ADJUSTER
OPERATION
(1) Place vehicle on hoist, with helper in driver
seat to apply brakes.
(2) Remove access plugs from support plates.
(3) Back off adjuster screw star wheel approxi
mately 20-30 notches. (4) Observe adjuster screw star wheel and spin
drum and road wheel rapidly in a reverse direction. Fig. 3 Rear Brake Adjustment With Tool
C-3784
(5) Have helper apply brakes firmly. Firm applica
tion will cause secondary shoe to move and engage rotating drum.
(6) Normal shoe "wrap-up" effect should move sec
ondary shoe enough to cause adjuster cable to pull adjuster lever up and turn star wheel.
BRAKE
SYSTEM BLEEDING
The brake system can be bled manually or with
pressure equipment. Manual bleeding requires the aid of a helper. Pressure equipment allows the sys
tem to be bled by one person. All models are equipped with a front brake meter
ing (hold off) valve. The metering valve is located
within the combination valve. The metering valve balances brake action between the front disc and
rear drum brakes during initial brake application. The metering valve is designed to hold off fluid
flow to the front disc brakes at pressures between 3 and 135 psi (20.68 and 930.8 kPa). Pressures generated by gravity or manual type
bleeding techniques will not affect the valve. How ever, pressure bleeding equipment will generate
enough fluid pressure (20 to 30 psi) to close the valve and prevent fluid flow to the front brakes. As a re
sult, the valve must be held open with special tool
C-4121 when using pressure bleeding equipment.
BLEEDING PROCEDURE (1) If new or overhauled master cylinder will be used,
be sure to bleed cylinder before installation. Refer to
bleeding procedure in Master Cylinder section. (2) If master cylinder has not been serviced, clean
master cylinder and cover to prevent dirt entering
reservoirs. Then remove cover.
(3) If pressure bleeding tank C-3496-B will be
used, install adapter C-4578 on master cylinder.
Then prepare tank for bleeding according to instruc
tions provided by supplier. Be sure to purge air from
tank lines before use.
Page 196 of 1502
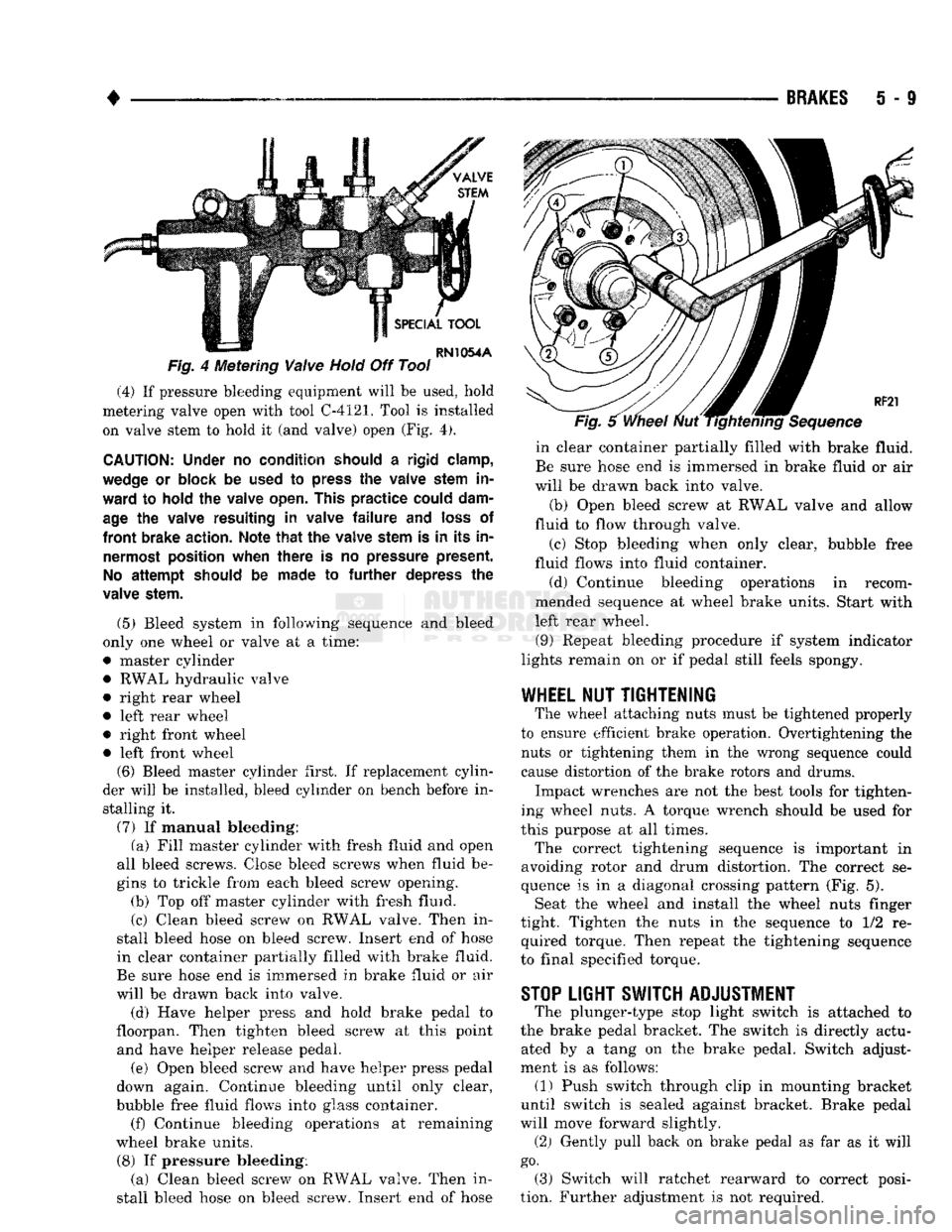
BRAKES
i - 9
Fig.
4 Metering
Valve
Hold
Off Tool (4) If pressure bleeding equipment will be used, hold
metering valve open with tool C-4121. Tool is installed on valve stem to hold it (and valve) open (Fig. 4).
CAUTION:
Under
no
condition should
a
rigid clamp,
wedge
or
block
be
used
to
press
the
valve stem
in
ward
to
hold
the
valve open. This
practice
could dam
age
the
valve resulting
in
valve
failure and
loss
of
front
brake action. Note
that the
valve stem
is in its in
nermost position when
there
is no
pressure present.
No
attempt
should
be
made
to further
depress
the
valve stem.
(5) Bleed system in following sequence and bleed
only one wheel or valve at a time:
• master cylinder • RWAL hydraulic valve
• right rear wheel
• left rear wheel
• right front wheel • left front wheel (6) Bleed master cylinder first. If replacement cylin
der will be installed, bleed cylinder on bench before in stalling it.
(7) If manual bleeding: (a) Fill master cylinder with fresh fluid and open
all bleed screws. Close bleed screws when fluid be
gins to trickle from each bleed screw opening. (b) Top off master cylinder with fresh fluid.
(c) Clean bleed screw on RWAL valve. Then in
stall bleed hose on bleed screw. Insert end of hose
in clear container partially filled with brake fluid.
Be sure hose end is immersed in brake fluid or air
will be drawn back into valve.
(d) Have helper press and hold brake pedal to
floorpan. Then tighten bleed screw at this point and have helper release pedal.
(e) Open bleed screw and have helper press pedal
down again. Continue bleeding until only clear,
bubble free fluid flows into glass container. (f) Continue bleeding operations at remaining
wheel brake units.
(8) If pressure bleeding: (a) Clean bleed screw on RWAL valve. Then in
stall bleed hose on bleed screw. Insert end of hose in clear container partially filled with brake fluid.
Be sure hose end is immersed in brake fluid or air
will be drawn back into valve.
(b) Open bleed screw at RWAL valve and allow
fluid to flow through valve.
(c) Stop bleeding when only clear, bubble free
fluid flows into fluid container.
(d) Continue bleeding operations in recom
mended sequence at wheel brake units. Start with
left rear wheel.
(9) Repeat bleeding procedure if system indicator
lights remain on or if pedal still feels spongy.
WHEEL
NUT
TIGHTENING
The wheel attaching nuts must be tightened properly
to ensure efficient brake operation. Overtightening the nuts or tightening them in the wrong sequence could
cause distortion of the brake rotors and drums.
Impact wrenches are not the best tools for tighten
ing wheel nuts. A torque wrench should be used for
this purpose at all times.
The correct tightening sequence is important in
avoiding rotor and drum distortion. The correct se
quence is in a diagonal crossing pattern (Fig. 5). Seat the wheel and install the wheel nuts finger
tight. Tighten the nuts in the sequence to 1/2 re quired torque. Then repeat the tightening sequence
to final specified torque.
STOP
LIGHT SWITCH ADJUSTMENT
The plunger-type stop light switch is attached to
the brake pedal bracket. The switch is directly actu ated by a tang on the brake pedal. Switch adjust
ment is as follows: (1) Push switch through clip in mounting bracket
until switch is sealed against bracket. Brake pedal
will move forward slightly.
(2) Gently pull back on brake pedal as far as it will
go.
(3) Switch will ratchet rearward to correct posi
tion. Further adjustment is not required.
Page 197 of 1502
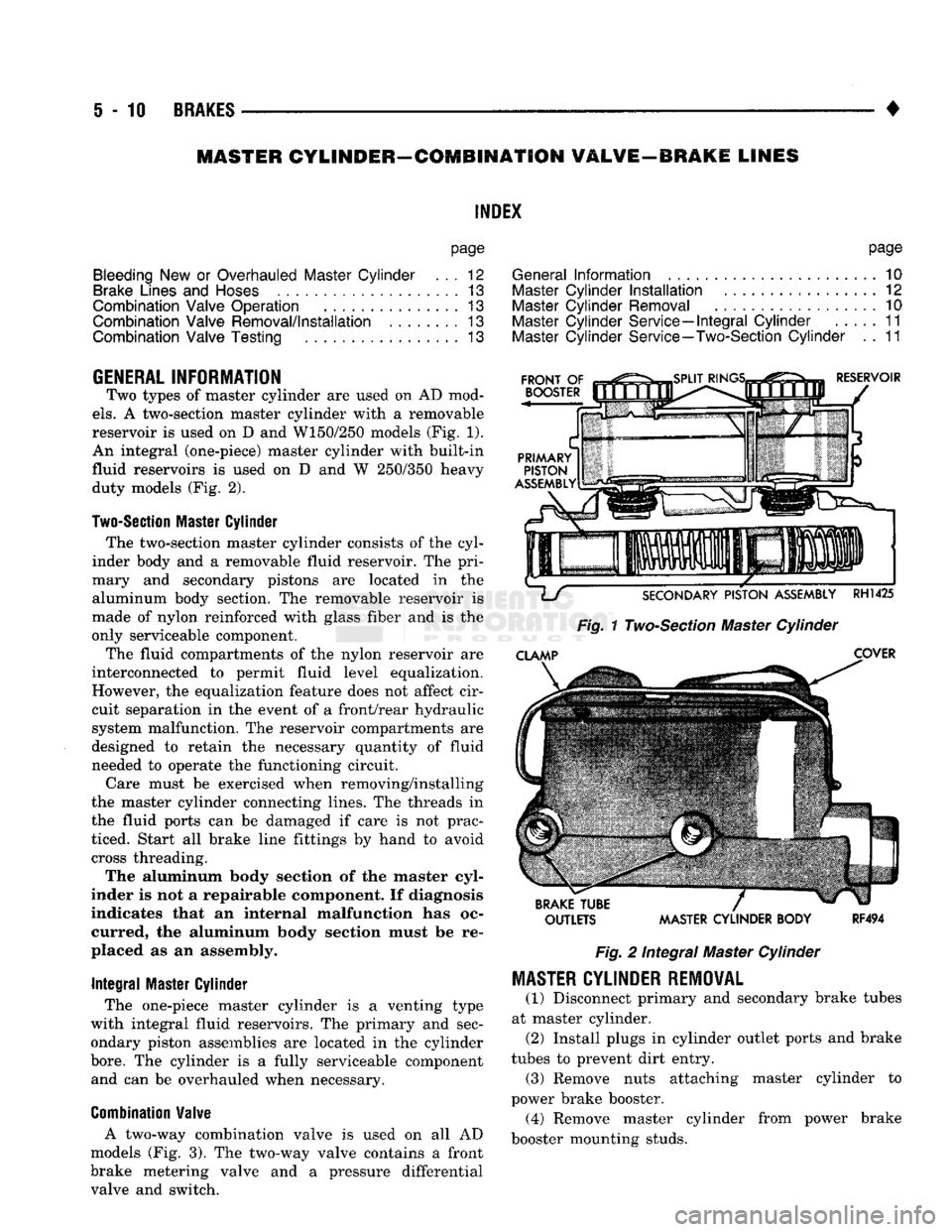
S
- 10
BRAKES
•
MASTER CYLINDER—COMBINATION
VALVE—BRAKE
LINES
INDEX
page
Bleeding
New
or
Overhauled Master Cylinder
. . . 12
Brake
Lines
and
Hoses
13
Combination Valve Operation
13
Combination Valve Removal/Installation
........
13
Combination Valve Testing
.................
13
page
General
Information
. 10
Master
Cylinder
Installation
12
Master
Cylinder Removal
10
Master
Cylinder Service—Integral Cylinder
11
Master
Cylinder Service—Two-Section Cylinder
. . 11
GENERAL
INFORMATION
Two types
of
master cylinder
are
used
on AD
mod
els.
A
two-section master cylinder with
a
removable
reservoir
is
used
on D and
W150/250 models
(Fig.
1).
An integral (one-piece) master cylinder with built-in
fluid reservoirs
is
used
on D and W
250/350 heavy duty models
(Fig.
2).
Two-Section
Master
Cylinder
The two-section master cylinder consists
of
the
cyl
inder body
and a
removable fluid reservoir.
The
pri
mary
and
secondary pistons
are
located
in the
aluminum body section.
The
removable reservoir
is
made
of
nylon reinforced with glass fiber
and is the
only serviceable component.
The fluid compartments
of the
nylon reservoir
are
interconnected
to
permit fluid level equalization.
However,
the
equalization feature does
not
affect cir
cuit separation
in the
event
of a
front/rear hydraulic
system malfunction.
The
reservoir compartments
are
designed
to
retain
the
necessary quantity
of
fluid
needed
to
operate
the
functioning circuit.
Care must
be
exercised when removing/installing
the master cylinder connecting lines.
The
threads
in
the fluid ports
can be
damaged
if
care
is not
prac
ticed. Start
all
brake line fittings
by
hand
to
avoid cross threading.
The aluminum body section
of the
master cyl
inder
is not a
repairable component.
If
diagnosis
indicates that
an
internal malfunction
has oc
curred,
the
aluminum body section must
be re
placed
as an
assembly.
Integral
Master Cylinder
The one-piece master cylinder
is a
venting type
with integral fluid reservoirs.
The
primary
and
sec
ondary piston assemblies
are
located
in the
cylinder
bore.
The
cylinder
is a
fully serviceable component and
can be
overhauled when necessary.
Combination
Valve
A two-way combination valve
is
used
on all AD
models
(Fig.
3). The
two-way valve contains
a
front
brake metering valve
and a
pressure differential valve
and
switch.
OUTLETS MASTER CYLINDER BODY
RF494
Fig.
2
Integral Master Cylinder
MASTER
CYLINDER REMOVAL
(1) Disconnect primary
and
secondary brake tubes
at master cylinder. (2) Install plugs
in
cylinder outlet ports
and
brake
tubes
to
prevent dirt entry. (3) Remove nuts attaching master cylinder
to
power brake booster. (4) Remove master cylinder from power brake
booster mounting studs.
Page 198 of 1502
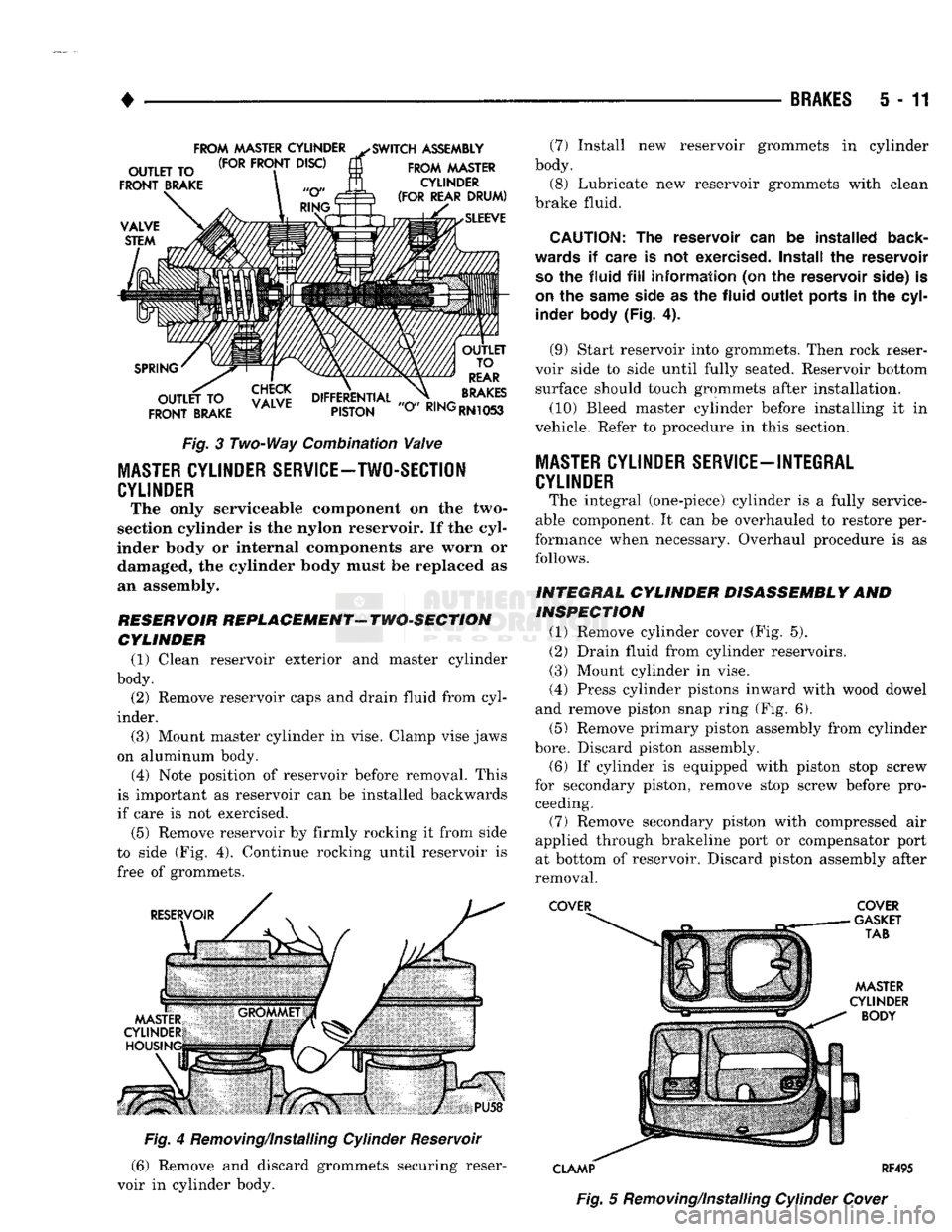
•
BRAKES
5 - 11
FROM
MASTER CYLINDER
^SWITCH
ASSEMBLY
Fig.
3 Two-Way Combination
Valve
MASTER
CYLINDER SERVICE-TWO-SECTION
CYLINDER
The only serviceable component on the two-
section cylinder is the nylon reservoir. If the cyl
inder body or internal components are worn or damaged, the cylinder body must be replaced as
an assembly.
RESERVOIR REPLACEMENT- TWO-SECTION CYLINDER (1) Clean reservoir exterior and master cylinder
body. (2) Remove reservoir caps and drain fluid from cyl
inder. (3) Mount master cylinder in vise. Clamp vise jaws
on aluminum body.
(4) Note position of reservoir before removal. This
is important as reservoir can be installed backwards
if care is not exercised.
(5) Remove reservoir by firmly rocking it from side
to side (Fig. 4). Continue rocking until reservoir is
free of grommets.
Fig.
4 Removing/Installing Cylinder Reservoir
(6) Remove and discard grommets securing reser
voir in cylinder body. (7) Install new reservoir grommets in cylinder
body. (8) Lubricate new reservoir grommets with clean
brake fluid.
CAUTION:
The reservoir can be installed
back
wards
if care is not
exercised.
Install the reservoir
so
the fluid
fill
information (on the reservoir
side)
is
on
the
same
side
as the fluid outlet
ports
in the
cyl
inder
body
(Fig. 4).
(9) Start reservoir into grommets. Then rock reser
voir side to side until fully seated. Reservoir bottom surface should touch grommets after installation.
(10) Bleed master cylinder before installing it in
vehicle. Refer to procedure in this section.
MASTER CYLINDER SERVICE-INTEGRAL
CYLINDER
The integral (one-piece) cylinder is a fully service
able component. It can be overhauled to restore per
formance when necessary. Overhaul procedure is as follows.
INTEGRAL CYLINDER DISASSEMBLY AND INSPECTION
(1) Remove cylinder cover (Fig. 5). (2) Drain fluid from cylinder reservoirs.
(3) Mount cylinder in vise.
(4) Press cylinder pistons inward with wood dowel
and remove piston snap ring (Fig. 6).
(5) Remove primary piston assembly from cylinder
bore.
Discard piston assembly.
(6) If cylinder is equipped with piston stop screw
for secondary piston, remove stop screw before pro ceeding. (7) Remove secondary piston with compressed air
applied through brakeline port or compensator port
at bottom of reservoir. Discard piston assembly after
removal.
COVER COVER
CLAMP RF495 Fig.
5 Removing/Installing Cylinder
Cover
Page 199 of 1502
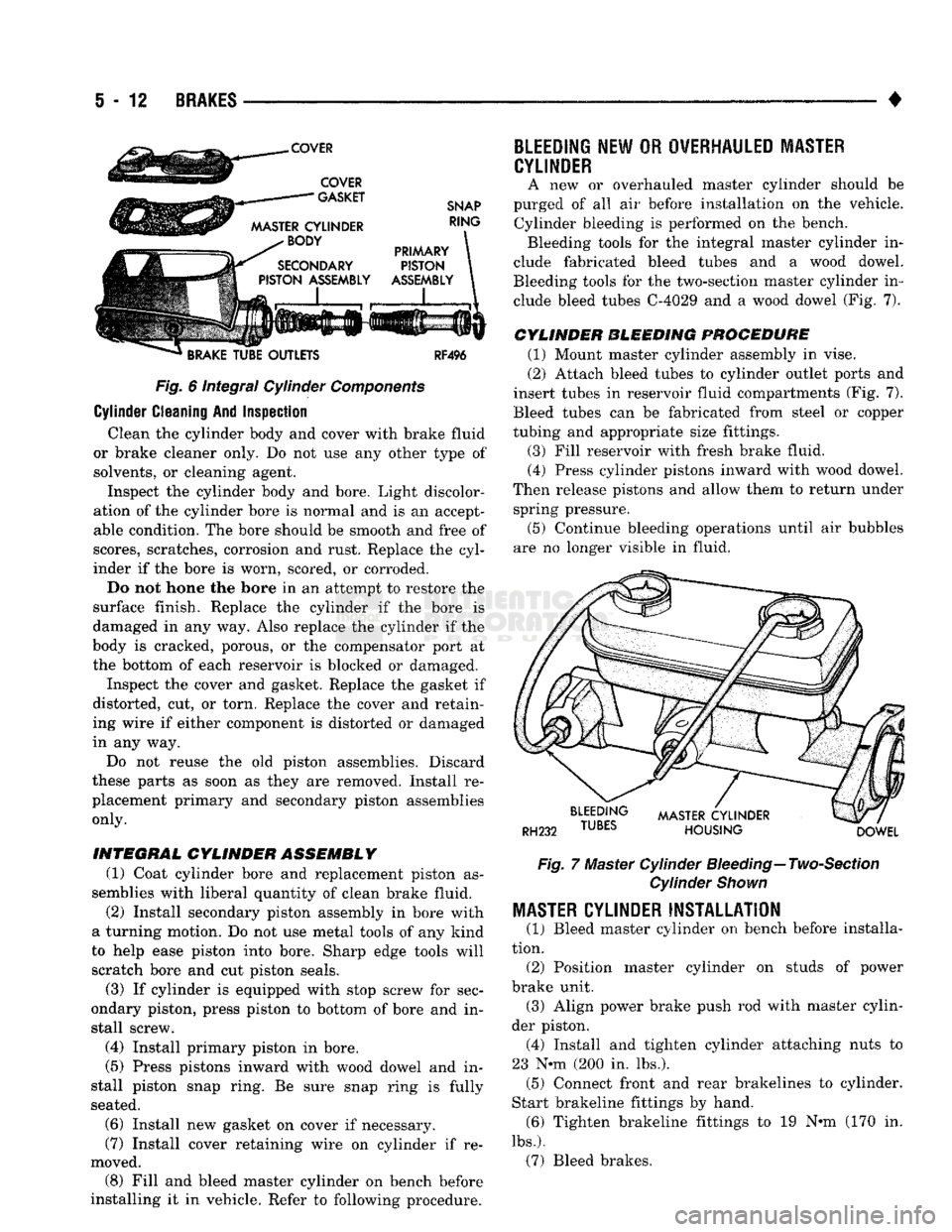
i - 12
BRAKES
•
Fig.
6 integral Cylinder
Components
Cylinder Cleaning And Inspection Clean the cylinder body and cover with brake fluid
or brake cleaner only. Do not use any other type of solvents, or cleaning agent. Inspect the cylinder body and bore. Light discolor
ation of the cylinder bore is normal and is an accept
able condition. The bore should be smooth and free of
scores, scratches, corrosion and rust. Replace the cyl
inder if the bore is worn, scored, or corroded.
Do not hone the bore in an attempt to restore the
surface finish. Replace the cylinder if the bore is
damaged in any way. Also replace the cylinder if the
body is cracked, porous, or the compensator port at
the bottom of each reservoir is blocked or damaged.
Inspect the cover and gasket. Replace the gasket if
distorted, cut, or torn. Replace the cover and retain
ing wire if either component is distorted or damaged
in any way.
Do not reuse the old piston assemblies. Discard
these parts as soon as they are removed. Install re
placement primary and secondary piston assemblies
only.
INTEGRAL
CYLINDER ASSEMBLY
(1) Coat cylinder bore and replacement piston as
semblies with liberal quantity of clean brake fluid.
(2) Install secondary piston assembly in bore with
a turning motion. Do not use metal tools of any kind
to help ease piston into bore. Sharp edge tools will
scratch bore and cut piston seals.
(3) If cylinder is equipped with stop screw for sec
ondary piston, press piston to bottom of bore and in
stall screw.
(4) Install primary piston in bore.
(5) Press pistons inward with wood dowel and in
stall piston snap ring. Be sure snap ring is fully
seated.
(6) Install new gasket on cover if necessary.
(7) Install cover retaining wire on cylinder if re
moved. (8) Fill and bleed master cylinder on bench before
installing it in vehicle. Refer to following procedure.
BLEEDING
NEW
OR
OVERHAULED MASTER
CYLINDER
A new or overhauled master cylinder should be
purged of all air before installation on the vehicle. Cylinder bleeding is performed on the bench. Bleeding tools for the integral master cylinder in
clude fabricated bleed tubes and a wood dowel.
Bleeding tools for the two-section master cylinder in clude bleed tubes C-4029 and a wood dowel (Fig. 7).
CYLINDER BLEEDING PROCEDURE
(1) Mount master cylinder assembly in vise.
(2) Attach bleed tubes to cylinder outlet ports and
insert tubes in reservoir fluid compartments (Fig. 7).
Bleed tubes can be fabricated from steel or copper
tubing and appropriate size fittings.
(3) Fill reservoir with fresh brake fluid. (4) Press cylinder pistons inward with wood dowel.
Then release pistons and allow them to return under spring pressure.
(5) Continue bleeding operations until air bubbles
are no longer visible in fluid.
Fig.
7 Master Cylinder
Bleeding—
Two-Section
Cylinder
Shown
MASTER
CYLINDER INSTALLATION
(1) Bleed master cylinder on bench before installa
tion. (2) Position master cylinder on studs of power
brake unit. (3) Align power brake push rod with master cylin
der piston. (4) Install and tighten cylinder attaching nuts to
23 N-m (200 in. lbs.). (5) Connect front and rear brakelines to cylinder.
Start brakeline fittings by hand. (6) Tighten brakeline fittings to 19 N«m (170 in.
lbs.).
(7) Bleed brakes.
Page 200 of 1502
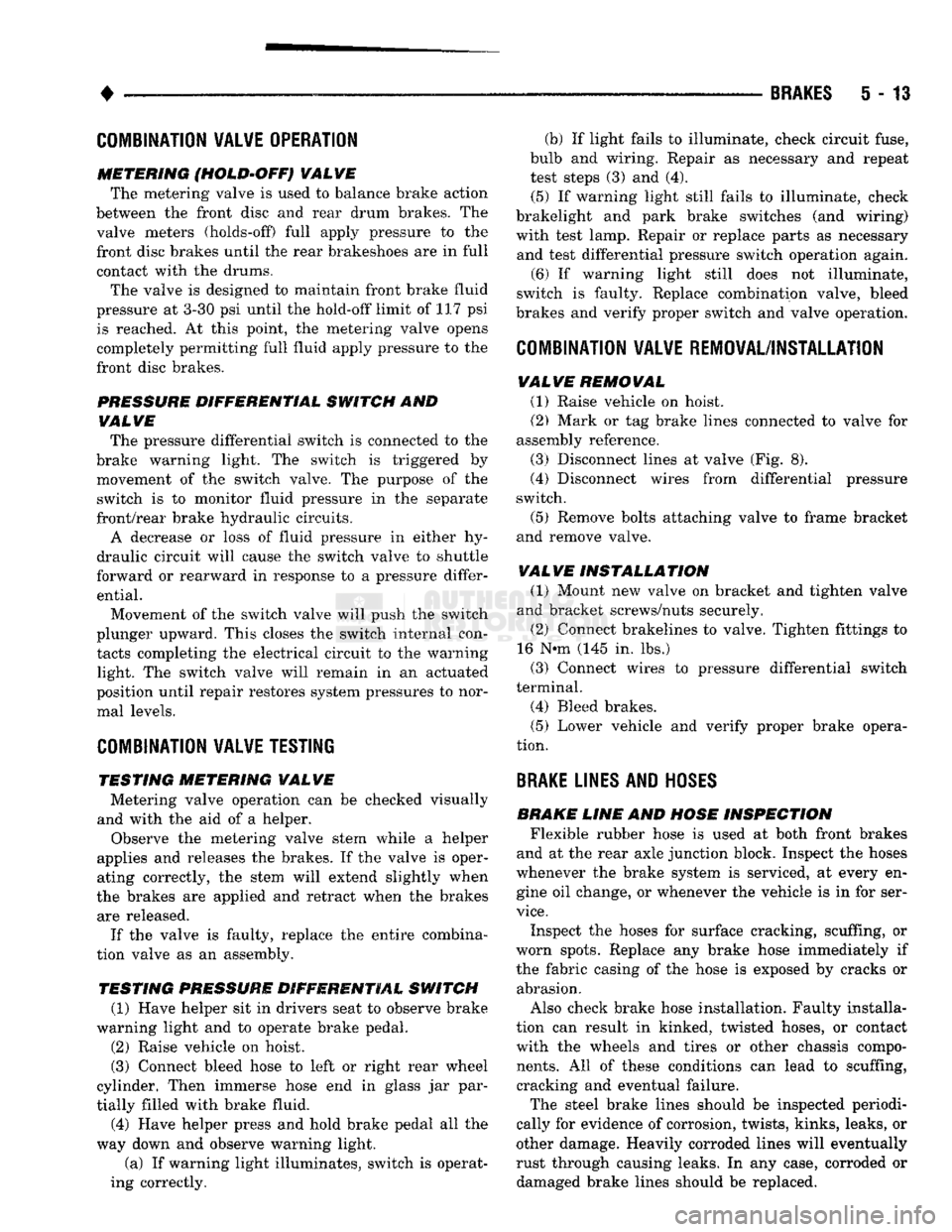
•
BRAKES
5 - 13
COMBINATION VALVE OPERATION
METERING (HOLD-OFF) VALVE The metering valve is used to balance brake action
between the front disc and rear drum brakes. The
valve meters (holds-off) full apply pressure to the front disc brakes until the rear brakeshoes are in full
contact with the drums.
The valve is designed to maintain front brake fluid
pressure at 3-30 psi until the hold-off limit of 117 psi is reached. At this point, the metering valve opens completely permitting full fluid apply pressure to the
front disc brakes.
PRESSURE DIFFERENTIAL SWITCH AND VALVE The pressure differential switch is connected to the
brake warning light. The switch is triggered by movement of the switch valve. The purpose of the switch is to monitor fluid pressure in the separate
front/rear brake hydraulic circuits.
A decrease or loss of fluid pressure in either hy
draulic circuit will cause the switch valve to shuttle
forward or rearward in response to a pressure differ ential.
Movement of the switch valve will push the switch
plunger upward. This closes the switch internal con tacts completing the electrical circuit to the warning light. The switch valve will remain in an actuated
position until repair restores system pressures to nor mal levels.
COMBINATION VALVE TESTING
TESTING METERING VALVE Metering valve operation can be checked visually
and with the aid of a helper.
Observe the metering valve stem while a helper
applies and releases the brakes. If the valve is oper
ating correctly, the stem will extend slightly when
the brakes are applied and retract when the brakes are released.
If the valve is faulty, replace the entire combina
tion valve as an assembly.
TESTING PRESSURE DIFFERENTIAL SWITCH (1) Have helper sit in drivers seat to observe brake
warning light and to operate brake pedal.
(2) Raise vehicle on hoist.
(3) Connect bleed hose to left or right rear wheel
cylinder. Then immerse hose end in glass jar par
tially filled with brake fluid.
(4) Have helper press and hold brake pedal all the
way down and observe warning light.
(a) If warning light illuminates, switch is operat
ing correctly. (b) If light fails to illuminate, check circuit fuse,
bulb and wiring. Repair as necessary and repeat test steps (3) and (4). (5) If warning light still fails to illuminate, check
brakelight and park brake switches (and wiring) with test lamp. Repair or replace parts as necessary and test differential pressure switch operation again.
(6) If warning light still does not illuminate,
switch is faulty. Replace combination valve, bleed
brakes and verify proper switch and valve operation.
COMBINATION VALVE REMOVAL/INSTALLATION
VALVE REMOVAL (1) Raise vehicle on hoist.
(2) Mark or tag brake lines connected to valve for
assembly reference.
(3) Disconnect lines at valve (Fig. 8).
(4) Disconnect wires from differential pressure
switch.
(5) Remove bolts attaching valve to frame bracket
and remove valve.
VALVE INSTALLATION (1) Mount new valve on bracket and tighten valve
and bracket screws/nuts securely.
(2) Connect brakelines to valve. Tighten fittings to
16 N*m (145 in. lbs.)
(3) Connect wires to pressure differential switch
terminal. (4) Bleed brakes.
(5) Lower vehicle and verify proper brake opera
tion.
BRAKE
LINES AND
HOSES
BRAKE LINE AND HOSE INSPECTION Flexible rubber hose is used at both front brakes
and at the rear axle junction block. Inspect the hoses
whenever the brake system is serviced, at every en gine oil change, or whenever the vehicle is in for ser
vice.
Inspect the hoses for surface cracking, scuffing, or
worn spots. Replace any brake hose immediately if
the fabric casing of the hose is exposed by cracks or abrasion.
Also check brake hose installation. Faulty installa
tion can result in kinked, twisted hoses, or contact with the wheels and tires or other chassis compo
nents.
All of these conditions can lead to scuffing,
cracking and eventual failure.
The steel brake lines should be inspected periodi
cally for evidence of corrosion, twists, kinks, leaks, or
other damage. Heavily corroded lines will eventually
rust through causing leaks. In any case, corroded or damaged brake lines should be replaced.