DODGE TRUCK 1993 Service Repair Manual
Manufacturer: DODGE, Model Year: 1993, Model line: TRUCK, Model: DODGE TRUCK 1993Pages: 1502, PDF Size: 80.97 MB
Page 171 of 1502
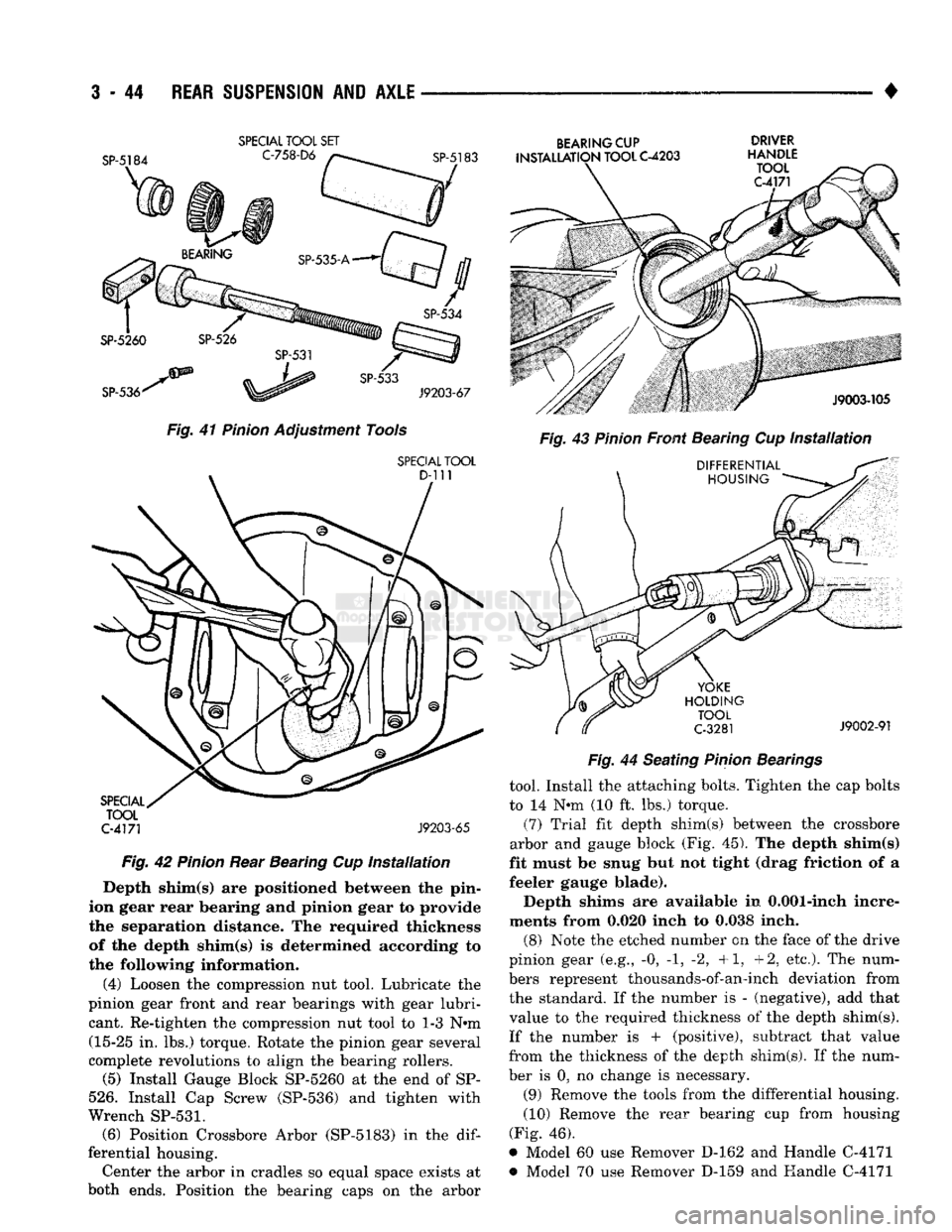
3
- 44
REAR SUSPENSION
AND
AXLE
— __—_ . _ •
SPECIAL
TOOL
SET
Fig.
41
Pinion
Adjustment Tools
SPECIAL
TOOL
C-4171
J9203-65
Fig.
42
Pinion
Rear Bearing Cup
Installation
Depth shim(s) are positioned between the pin
ion gear rear bearing and pinion gear to provide
the separation distance. The required thickness of the depth shim(s) is determined according to
the following information.
(4) Loosen the compression nut tool. Lubricate the
pinion gear front and rear bearings with gear lubri cant. Re-tighten the compression nut tool to 1-3 N-m (15-25 in. lbs.) torque. Rotate the pinion gear several
complete revolutions to align the bearing rollers.
(5) Install Gauge Block SP-5260 at the end of SP-
526.
Install Cap Screw (SP-536) and tighten with
Wrench
SP-531.
(6) Position Crossbore Arbor (SP-5183) in the
dif
ferential housing. Center the arbor in cradles so equal space exists at
both ends. Position the bearing caps on the arbor
BEARING
CUP DRIVER
INSTALLATION
TOOL
C-4203
HANDLE
Fig.
44 Seating
Pinion
Bearings
tool. Install the attaching bolts. Tighten the cap bolts
to 14 N-m (10 ft. lbs.) torque.
(7) Trial fit depth shim(s) between the crossbore
arbor and gauge block (Fig. 45). The depth shim(s)
fit must be snug but not tight (drag friction of a
feeler gauge blade).
Depth shims are available in 0.001-inch incre
ments from 0.020 inch to 0.038 inch.
(8) Note the etched number on the face of the drive
pinion gear (e.g., -0, -1, -2, +1, +2, etc.). The num
bers represent thousands-of-an-inch deviation from the standard. If the number is - (negative), add that
value to the required thickness of the depth shim(s).
If the number is + (positive), subtract that value
from the thickness of the depth shim(s). If the num
ber is 0, no change is necessary.
(9) Remove the tools from the differential housing.
(10) Remove the rear bearing cup from housing
(Fig. 46),
* Model 60 use Remover D-162 and Handle C-4171 *> Model 70 use Remover D-159 and Handle C-4171
Page 172 of 1502
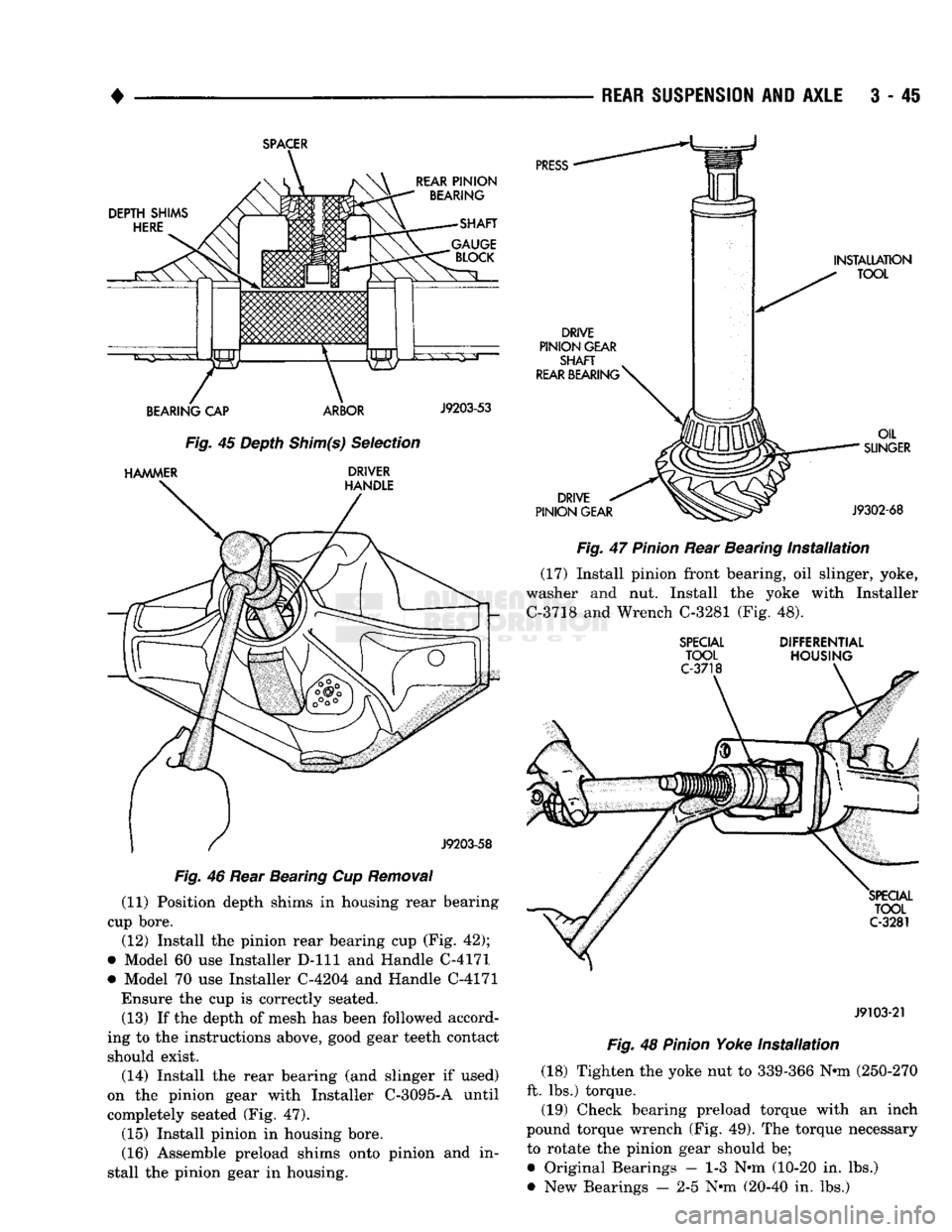
•
REAR
SUSPENSION
AND
AXLE
3 - 4S
SPACER
DEPTH SHIMS
HERE
REAR
PINION
BEARING
SHAFT
BEARING
CAP ARBOR
J9203-53
Fig.
45 Depth
Shim(s)
Selection
HAMMER
DRIVER HANDLE
J9203-58
Fig.
46 Rear Bearing Cup
Removal
(11) Position depth shims in housing rear bearing
cup bore.
(12) Install the pinion rear bearing cup (Fig. 42);
• Model 60 use Installer D-lll and Handle C-4171
• Model 70 use Installer C-4204 and Handle C-4171 Ensure the cup is correctly seated.
(13) If the depth of mesh has been followed accord
ing to the instructions above, good gear teeth contact
should exist.
(14) Install the rear bearing (and slinger if used)
on the pinion gear with Installer C-3095-A until
completely seated (Fig. 47).
(15) Install pinion in housing bore.
(16) Assemble preload shims onto pinion and in
stall the pinion gear in housing.
PRESS
DRIVE
PINION GEAR
SHAFT
REAR
BEARING
^
INSTALLATION
TOOL
DRIVE
PINION GEAR OIL
SUNGER
J9302-68
Fig.
47
Pinion
Rear Bearing
Installation
(17) Install pinion front bearing, oil slinger, yoke,
washer and nut. Install the yoke with Installer
C-3718 and Wrench C-3281 (Fig. 48).
SPECIAL
TOOL
C-3718
DIFFERENTIAL
HOUSING
SPECIAL
TOOL
C-3281
J9103-21
Fig.
48
Pinion
Yoke
Installation
(18) Tighten the yoke nut to 339-366 Nnn (250-270
ft. lbs.) torque.
(19) Check bearing preload torque with an inch
pound torque wrench (Fig. 49). The torque necessary to rotate the pinion gear should be;
• Original Bearings — 1-3 Nnn (10-20 in. lbs.)
• New Bearings — 2-5 Nnn (20-40 in. lbs.)
Page 173 of 1502
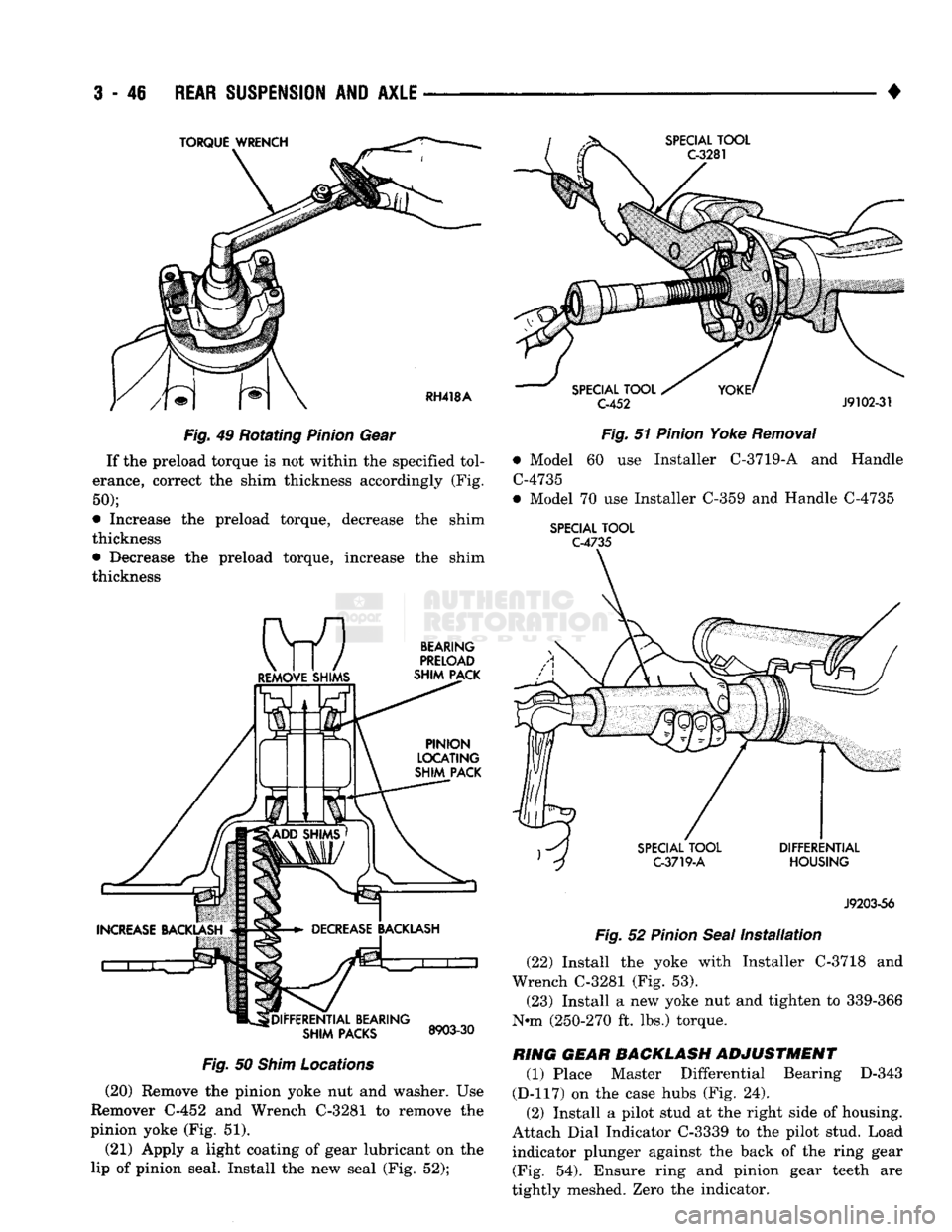
3
- 48
REAR SUSPENSION
AND
AXLE
Fig.
49 Rotating
Pinion
Gear If the preload torque is not within the specified tol
erance, correct the shim thickness accordingly (Fig. 50);
• Increase the preload torque, decrease the shim
thickness
• Decrease the preload torque, increase the shim
thickness
Fig.
50
Shim
Locations
(20) Remove the pinion yoke nut and washer. Use
Remover C-452 and Wrench C-3281 to remove the
pinion yoke (Fig. 51).
(21) Apply a light coating of gear lubricant on the
lip of pinion seal. Install the new seal (Fig. 52); •
C-452
J9102-31
Fig.
51
Pinion
Yoke
Removal
• Model 60 use Installer C-3719-A and Handle C-4735
• Model 70 use Installer C-359 and Handle C-4735
SPECIAL
TOOL
C-4735
J9203-56
Fig.
52
Pinion
Seal
Installation
(22) Install the yoke with Installer C-3718 and
Wrench C-3281 (Fig. 53). (23) Install a new yoke nut and tighten to 339-366
N-m (250-270 ft. lbs.) torque.
RING GEAR BACKLASH
ADJUSTMENT
(1) Place Master Differential Bearing D-343
(D-117) on the case hubs (Fig. 24).
(2) Install a pilot stud at the right side of housing.
Attach Dial Indicator C-3339 to the pilot stud. Load
indicator plunger against the back of the ring gear (Fig. 54). Ensure ring and pinion gear teeth are
tightly meshed. Zero the indicator.
Page 174 of 1502
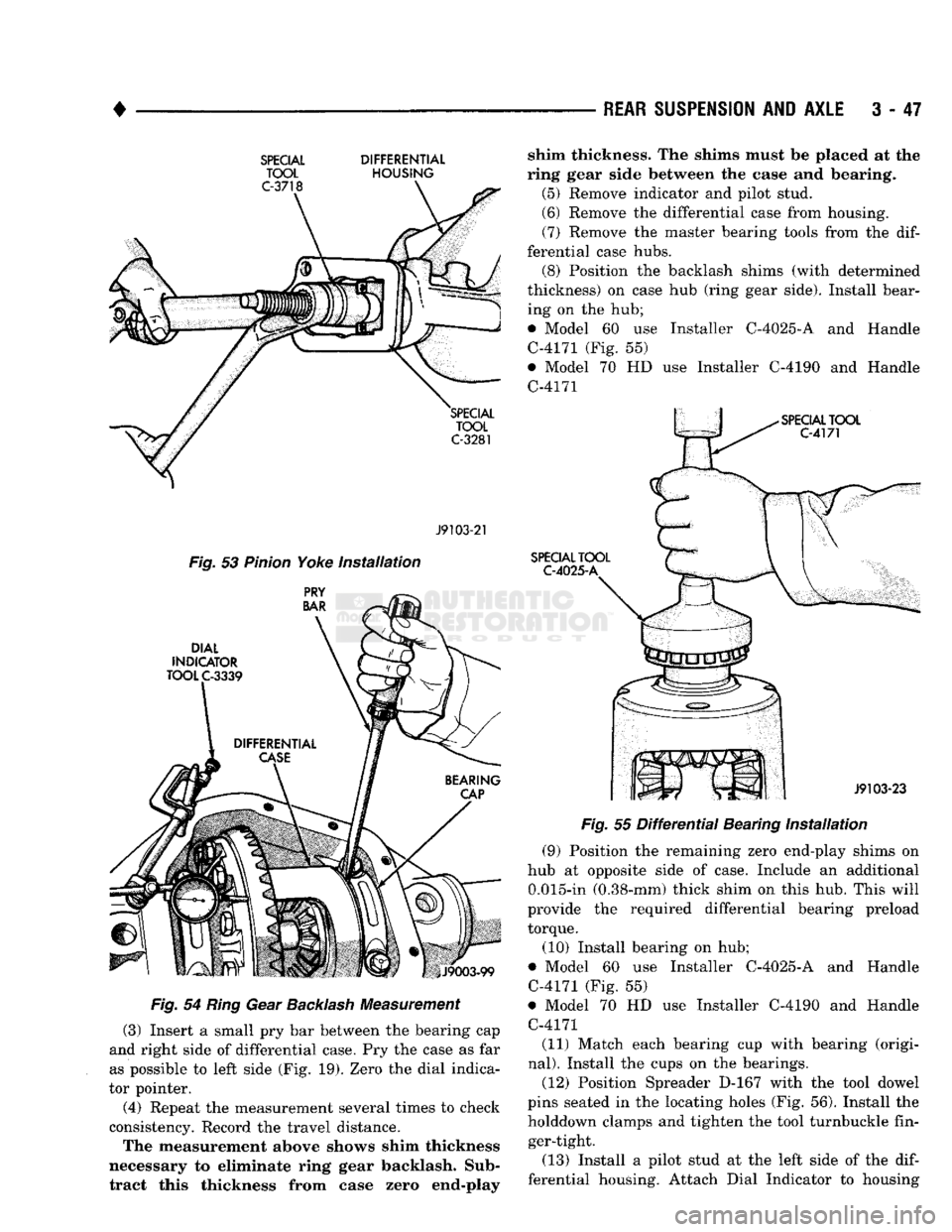
•
REAR SUSPENSION
AND
AXLE
3 - 47
SPECIAL DIFFERENTIAL
TOOL
HOUSING
J9103-21
Fig.
53
Pinion
Yoke
installation
Fig.
54
Ring
Gear
Backlash
Measurement
(3) Insert
a
small
pry bar
between
the
bearing
cap
and right side
of
differential case.
Pry the
case
as far
as possible
to
left side
(Fig. 19).
Zero
the
dial indica
tor pointer.
(4) Repeat
the
measurement several times
to
check
consistency. Record
the
travel distance.
The measurement above shows shim thickness
necessary
to
eliminate ring gear backlash. Sub tract this thickness from case zero end-play shim thickness.
The
shims must
be
placed
at the
ring gear side between
the
case
and
bearing. (5) Remove indicator
and
pilot stud.
(6) Remove
the
differential case from housing.
(7) Remove
the
master bearing tools from
the dif
ferential case hubs. (8) Position
the
backlash shims (with determined
thickness)
on
case
hub
(ring gear side). Install bear ing
on the hub;
• Model
60 use
Installer C-4025-A
and
Handle
C-4171
(Fig. 55)
• Model
70 HD use
Installer C-4190
and
Handle
C-4171
Fig.
55
Differential
Bearing
Installation
(9) Position
the
remaining zero end-play shims
on
hub
at
opposite side
of
case. Include
an
additional 0.015-in (0.38-mm) thick shim
on
this
hub.
This will
provide
the
required differential bearing preload
torque.
(10) Install bearing
on hub;
• Model
60 use
Installer C-4025-A
and
Handle
C-4171
(Fig. 55)
• Model
70 HD use
Installer C-4190
and
Handle
C-4171 (11) Match each bearing
cup
with bearing (origi
nal).
Install
the
cups
on the
bearings. (12) Position Spreader
D-167
with
the
tool dowel
pins seated
in the
locating holes
(Fig. 56).
Install
the
holddown clamps
and
tighten
the
tool turnbuckle fin ger-tight.
(13) Install
a
pilot stud
at the
left side
of the dif
ferential housing. Attach Dial Indicator
to
housing
Page 175 of 1502
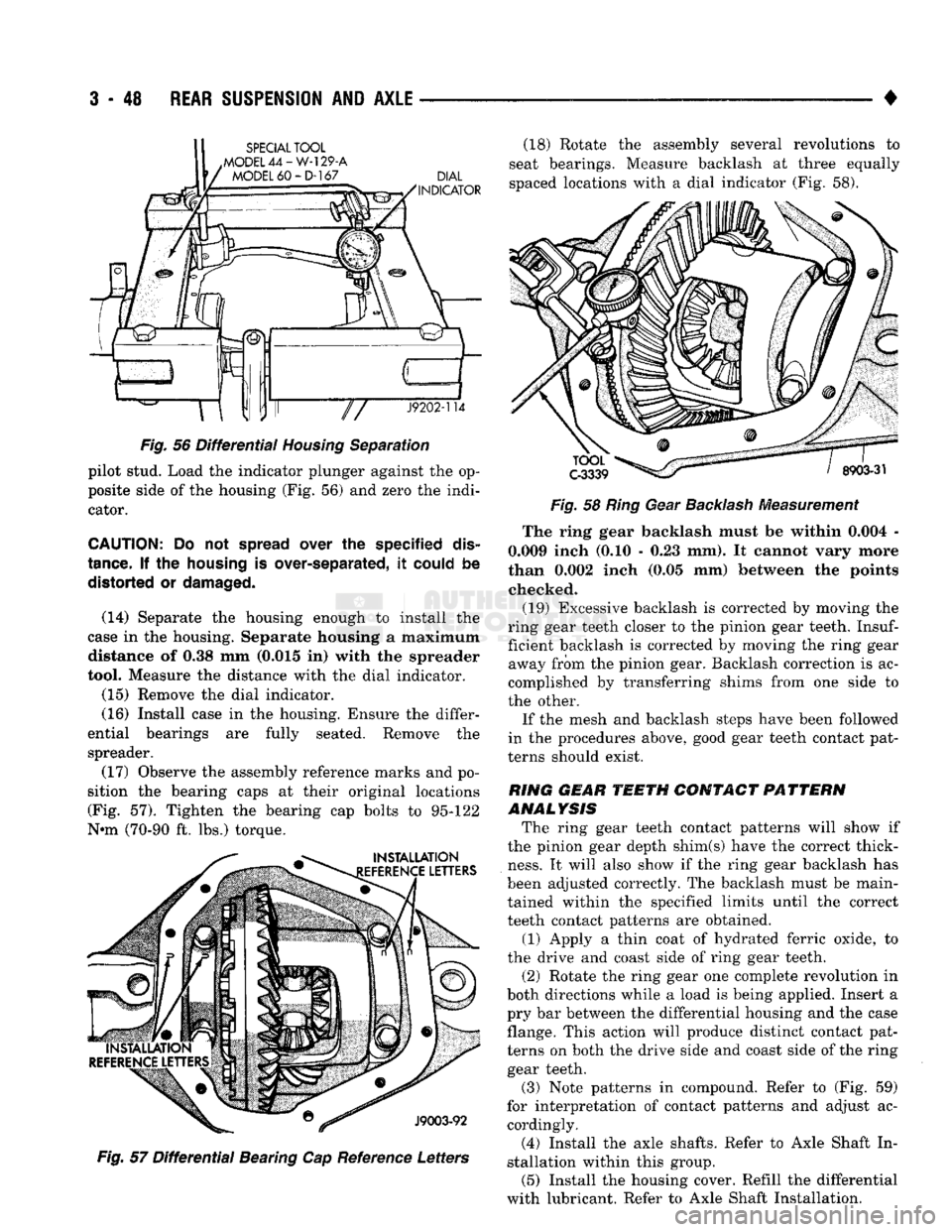
3
- 48
REAR
SUSPENSION
AND
AXLE
•
SPECIAL
TOOL
.MODEL
44-W-129-A
MODEL
60-D-167 (18) Rotate the assembly several revolutions to
seat bearings. Measure backlash at three equally
spaced locations with a dial indicator (Fig. 58).
Fig.
56
Differential
Housing
Separation pilot stud. Load the indicator plunger against the op
posite side of the housing (Fig. 56) and zero the indi
cator.
CAUTION:
Do not
spread
over the specified
dis
tance.
If the
housing
is over-separated, it
could
be distorted or
damaged.
(14) Separate the housing enough to install the
case in the housing. Separate housing a maximum distance of 0.38 mm (0.015 in) with the spreader
tool. Measure the distance with the dial indicator.
(15) Remove the dial indicator.
(16) Install case in the housing. Ensure the differ
ential bearings are fully seated. Remove the spreader.
(17) Observe the assembly reference marks and po
sition the bearing caps at their original locations
(Fig. 57). Tighten the bearing cap bolts to 95-122
N*m (70-90 ft. lbs.) torque.
INSTALLATION
EFERENCE
LETTERS
TOOL
C-3339
8903-31
©
^
J9003-92
Fig.
57
Differential
Bearing Cap Reference Letters
Fig.
58
Ring
Gear
Backlash
Measurement
The ring gear backlash must be within 0.004 -
0.009 inch (0.10 - 0.23 mm). It cannot vary more
than 0.002 inch (0.05 mm) between the points checked. (19) Excessive backlash is corrected by moving the
ring gear teeth closer to the pinion gear teeth.
Insuf
ficient backlash is corrected by moving the ring gear away from the pinion gear. Backlash correction is ac
complished by transferring shims from one side to
the other.
If the mesh and backlash steps have been followed
in the procedures above, good gear teeth contact pat
terns should exist.
RING
GEAR
TEETH
CONTACT
PATTERN
ANALYSIS
The ring gear teeth contact patterns will show if
the pinion gear depth shim(s) have the correct thick
ness.
It will also show if the ring gear backlash has
been adjusted correctly. The backlash must be main
tained within the specified limits until the correct
teeth contact patterns are obtained.
(1) Apply a thin coat of hydrated ferric oxide, to
the drive and coast side of ring gear teeth. (2) Rotate the ring gear one complete revolution in
both directions while a load is being applied. Insert a pry bar between the differential housing and the case
flange. This action will produce distinct contact pat
terns on both the drive side and coast side of the ring gear teeth.
(3) Note patterns in compound. Refer to (Fig. 59)
for interpretation of contact patterns and adjust ac cordingly.
(4) Install the axle shafts. Refer to Axle Shaft In
stallation within this group. (5) Install the housing cover. Refill the differential
with lubricant. Refer to Axle Shaft Installation.
Page 176 of 1502
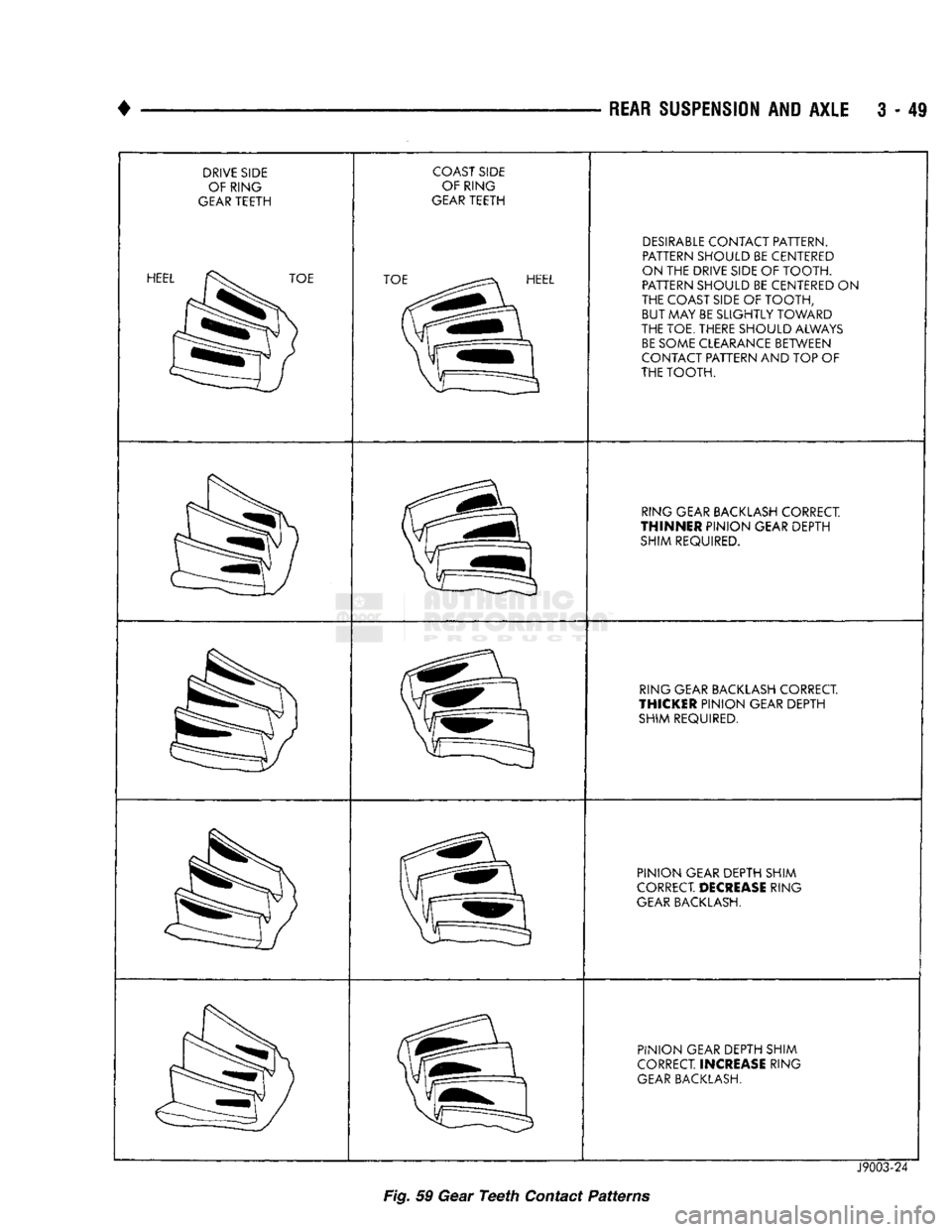
•
REAR SUSPENSION AND AXLE 3 - 49
DRIVE SIDE OF RING
GEAR TEETH
HEE^^^^^^^TOE COAST SIDE
OF RING
GEAR TEETH
TOE^^^^^^^^^EL DESIRABLE CONTACT PATTERN.
PATTERN SHOULD BE CENTERED
ON THE DRIVE SIDE
OF
TOOTH. PATTERN SHOULD BE CENTERED
ON
THE COAST SIDE
OF
TOOTH, BUT MAY BE SLIGHTLY TOWARD
THE TOE. THERE SHOULD ALWAYS BE SOME CLEARANCE BETWEEN
CONTACT PATTERN
AND
TOP
OF
THE TOOTH.
RING GEAR BACKLASH CORRECT
THINNER
PINION GEAR DEPTH SHIM REQUIRED.
RING GEAR BACKLASH CORRECT
THICKER
PINION GEAR DEPTH SHIM REQUIRED.
PINION GEAR DEPTH SHIM
CORRECT
DECREASE
RING
GEAR BACKLASH.
PINION GEAR DEPTH SHIM
CORRECT.
INCREASE
RING
GEAR BACKLASH.
J9003-24
Fig. 59 Gear
Teeth
Contact
Patterns
Page 177 of 1502
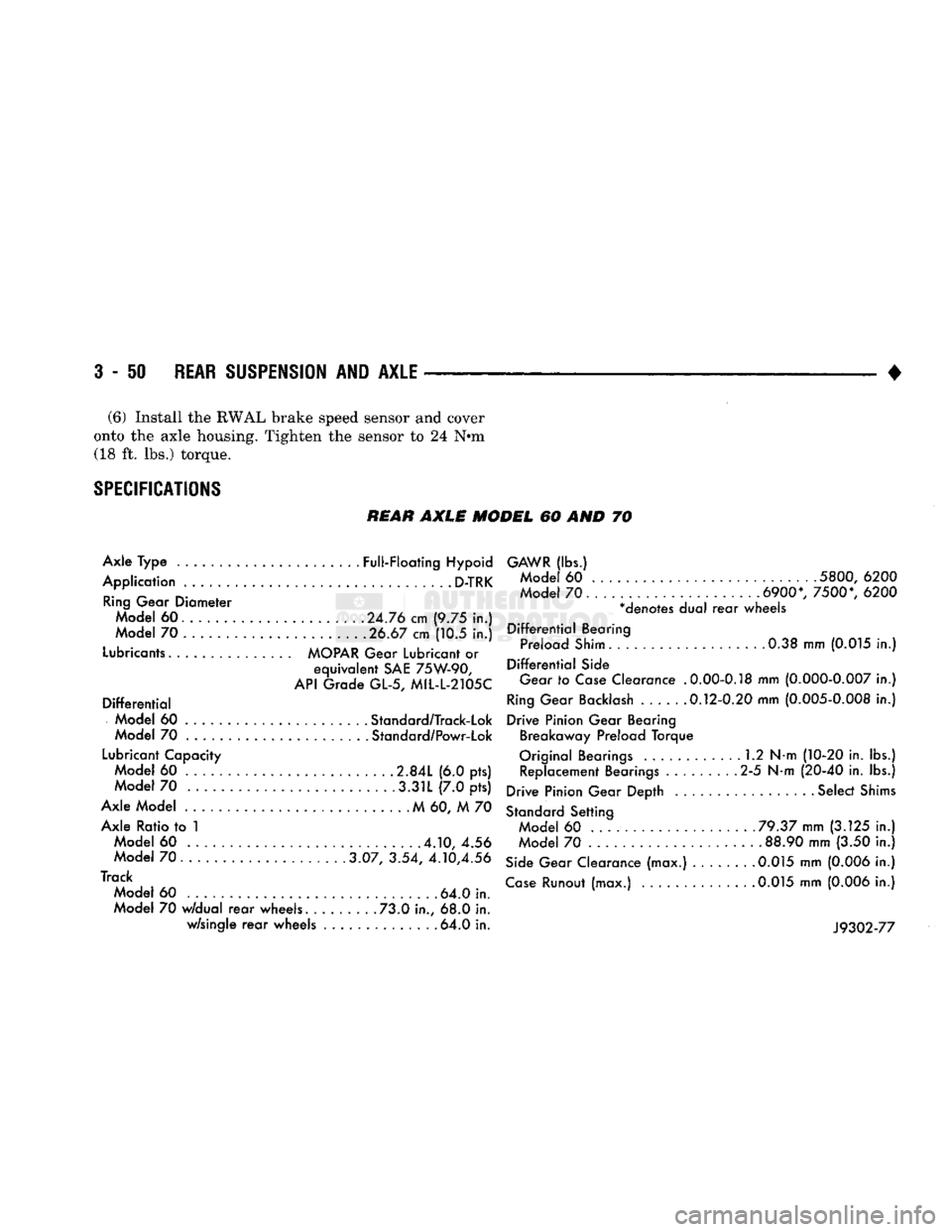
3
- 50
REAR
SUSPENSION
AND
AXLE
• (6)
Install
the
RWAL brake
speed
sensor
and
cover
onto
the
axle
housing.
Tighten
the
sensor
to 24 Nsm (18 ft. lbs.)
torque.
SPECIFICATIONS
REAR
AXLE MODEL 60 AND 70
Axle Type ......................
Full-Floating
Hypoid
Application
D-TRK
Ring
Gear Diameter Model 60. ............ .
.24.76
cm (9.75 in.)
Model 70 .................... .
.26.67
cm (10.5 in.)
Lubricants
MOPAR
Gear
Lubricant
or
equivalent
SAE
75W-90,
API
Grade GL-5, MIL-L-2105C
Differential
Model 60 .... . Standard/Track-Lok
Model 70 Standard/Powr-Lok
Lubricant
Capacity Model 60 .....
2.84L
(6.0 pts) Model 70 .3.31L (7.0 pts)
Axle Model M 60, M 70 Axle Ratio to 1 Model 60
.4.10,
4.56
Model
70......
3.07, 3.54,
4.10,4.56
Track Model 60 . 64.0 in.
Model 70
w/dual
rear
wheels. ....... .73.0 in., 68.0 in. w/single
rear
wheels ............. .64.0 in.
GAWR
(lbs.)
Mode
60
5800,
6200
Mode
70.
6900*,
7500*,
6200
*denotes dual
rear
wheels
Differential
Bearing Preload
Shim.
0.38 mm
(0.015
in.)
Differential
Side
Gear
to
Case
Clearance
.0.00-0.18
mm
(0.000-0.007
in.)
Ring
Gear
Backlash
.....
.0.12-0.20
mm
(0.005-0.008
in.)
Drive Pinion Gear Bearing Breakaway Preload Torque
Original Bearings 1.2 N-m
(10-20
in. lbs.) Replacement Bearings 2-5 N-m
(20-40
in. lbs.)
Drive Pinion Gear Depth ................. Select
Shims
Standard
Setting Model 60 ...
.79.37
mm
(3.125
in.)
Model 70 .
88.90
mm (3.50 in.)
Side
Gear Clearance (max.) 0.015 mm
(0.006
in.)
Case
Runout (max.)
.0.015
mm
(0.006
in.)
J9302-77
Page 178 of 1502
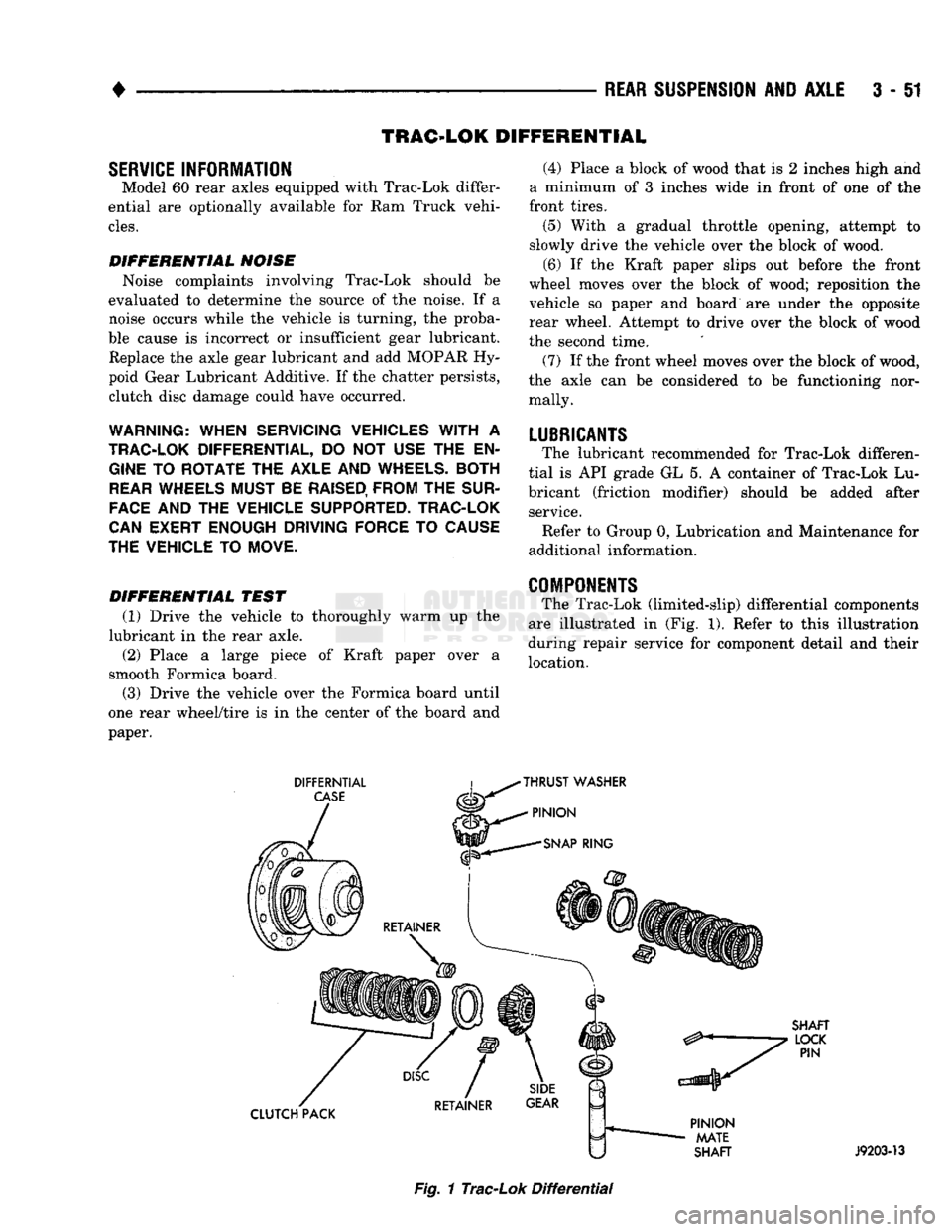
REAR
SUSPENSION
AND
AXLE
3 - 51
TRAC-LOK
DIFFERENTIAL
SERVICE
INFORMATION
Model
60 rear
axles equipped
with
Trac-Lok
differ
ential are optionally available for Ram Truck vehi
cles.
DIFFERENTIAL
NOISE
Noise complaints involving Trac-Lok should be
evaluated to determine the source of the noise. If a noise occurs while the vehicle is turning, the proba
ble cause is incorrect or insufficient gear lubricant. Replace the axle gear lubricant and add MOPAR Hy
poid Gear Lubricant Additive. If the chatter persists, clutch disc damage could have occurred.
WARNING: WHEN SERVICING VEHICLES
WITH
A
TRAC-LOK DIFFERENTIAL,
DO NOT
USE
THE EN
GINE
TO
ROTATE
THE
AXLE
AND
WHEELS.
BOTH
REAR
WHEELS MUST
BE
RAISED, FROM
THE
SUR
FACE
AND THE
VEHICLE SUPPORTED. TRAC-LOK
CAN EXERT ENOUGH DRIVING FORCE
TO
CAUSE
THE VEHICLE
TO
MOVE.
(4) Place a block of wood that is 2 inches high and
a minimum of 3 inches wide in front of one of the
front tires.
(5) With a gradual throttle opening, attempt to
slowly drive the vehicle over the block of wood.
(6) If the Kraft paper slips out before the front
wheel moves over the block of wood; reposition the vehicle so paper and board are under the opposite
rear wheel. Attempt to drive over the block of wood
the second time.
(7) If the front wheel moves over the block of wood,
the axle can be considered to be functioning nor mally.
LUBRICANTS
The lubricant recommended for Trac-Lok differen
tial is API grade GL 5. A container of Trac-Lok Lu
bricant (friction modifier) should be added after service. Refer to Group 0, Lubrication and Maintenance for
additional information.
DIFFERENTIAL
TEST
(1) Drive the vehicle to thoroughly warm up the
lubricant in the rear axle. (2) Place a large piece of Kraft paper over a
smooth Formica board.
(3) Drive the vehicle over the Formica board until
one rear wheel/tire is in the center of the board and
paper.
COMPONENTS
The Trac-Lok (limited-slip) differential components
are illustrated in (Fig. 1). Refer to this illustration
during repair service for component detail and their
location.
DIFFERNTIAL
CASE
THRUST
WASHER
PINION
SNAP
RING
SHAFT
LOCK
PIN
CLUTCH PACK
PINION
MATE
SHAFT
J9203-13
Fig.
1
Trac-Lok
Differential
Page 179 of 1502
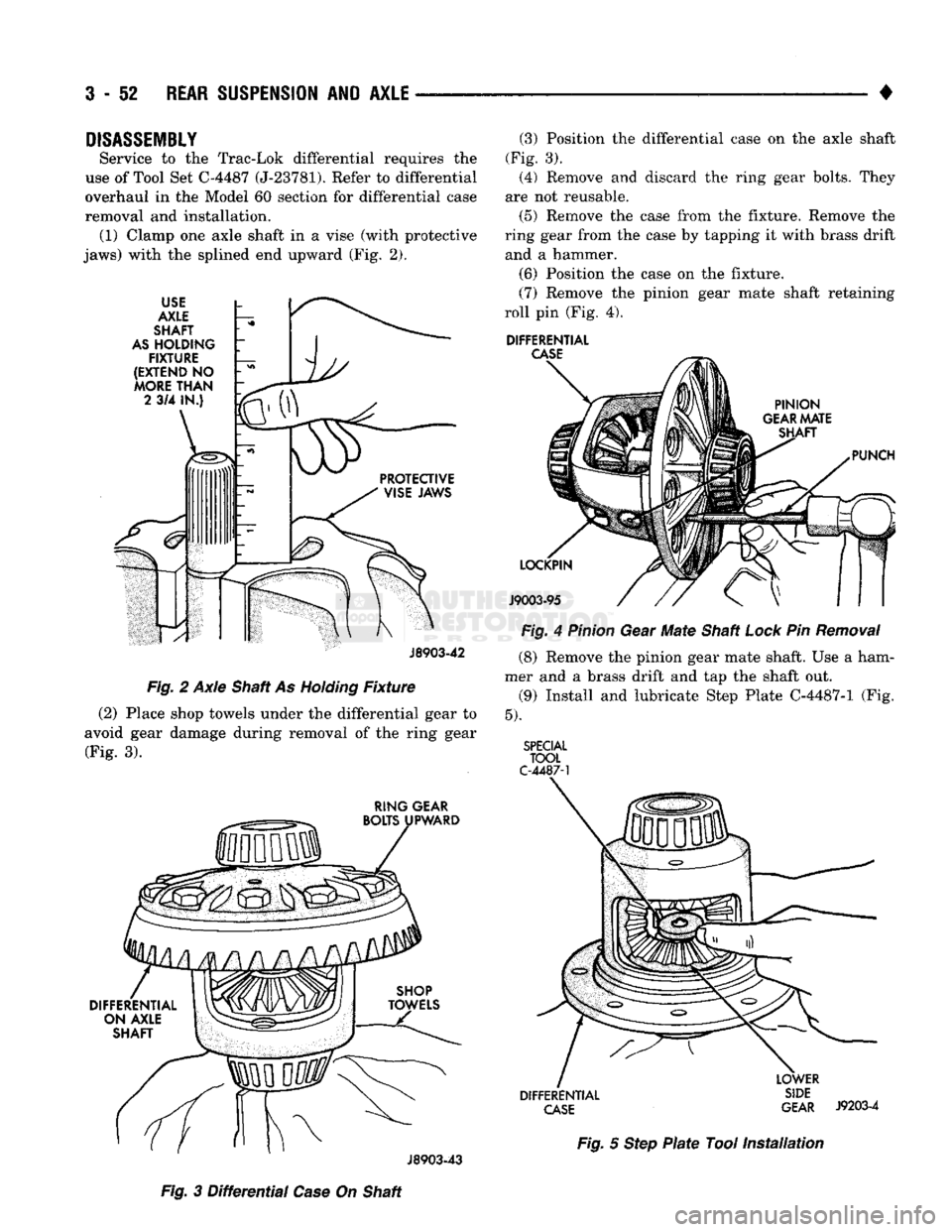
3
- 52
REAR SUSPENSION
AND
AXLE
DISASSEMBLY
Service to the Trac-Lok differential requires the
use of Tool Set C-4487 (J-23781). Refer to differential
overhaul in the Model 60 section for differential case
removal and installation. (1) Clamp one axle shaft in a vise (with protective
jaws) with the splined end upward (Fig. 2).
USE
AXLE
SHAFT
AS
HOLDING
FIXTURE
(EXTEND
NO
MORE
THAN
2
3/4 IN.)
J8903-42
~
Fig. 2 Axle Shaft As
Holding
Fixture
(2)
Place shop towels under the differential gear to
avoid gear damage during removal of the ring gear (Fig. 3).
RING GEAR
BOLTS UPWARD
DIFFERENTIAL ON AXLE
SHAFT
(3) Position the differential case on the axle shaft
(Fig. 3). (4) Remove and discard the ring gear bolts. They
are not reusable.
(5) Remove the case from the fixture. Remove the
ring gear from the case by tapping it with brass drift and a hammer.
(6)
Position the case on the fixture.
(7) Remove the pinion gear mate shaft retaining
roll pin (Fig. 4).
DIFFERENTIAL
CASE
PINION
GEAR
MATE SHAFT
PUNCH
LOCKPIN
J9003-95
Fig. 4
Pinion
Gear Mate Shaft
Lock
Pin
Removal
(8) Remove the pinion gear mate shaft. Use a ham
mer and a brass drift and tap the shaft out.
(9)
Install and lubricate Step Plate C-4487-1 (Fig.
5).
SPECIAL
TOOL
C-4487-1
DIFFERENTIAL
CASE
LOWER
SIDE
GEAR
J9203-4
J8903-43
Fig.
5
Step
Plate
Tool
Installation
Fig.
3
Differential
Case
On Shaft
Page 180 of 1502
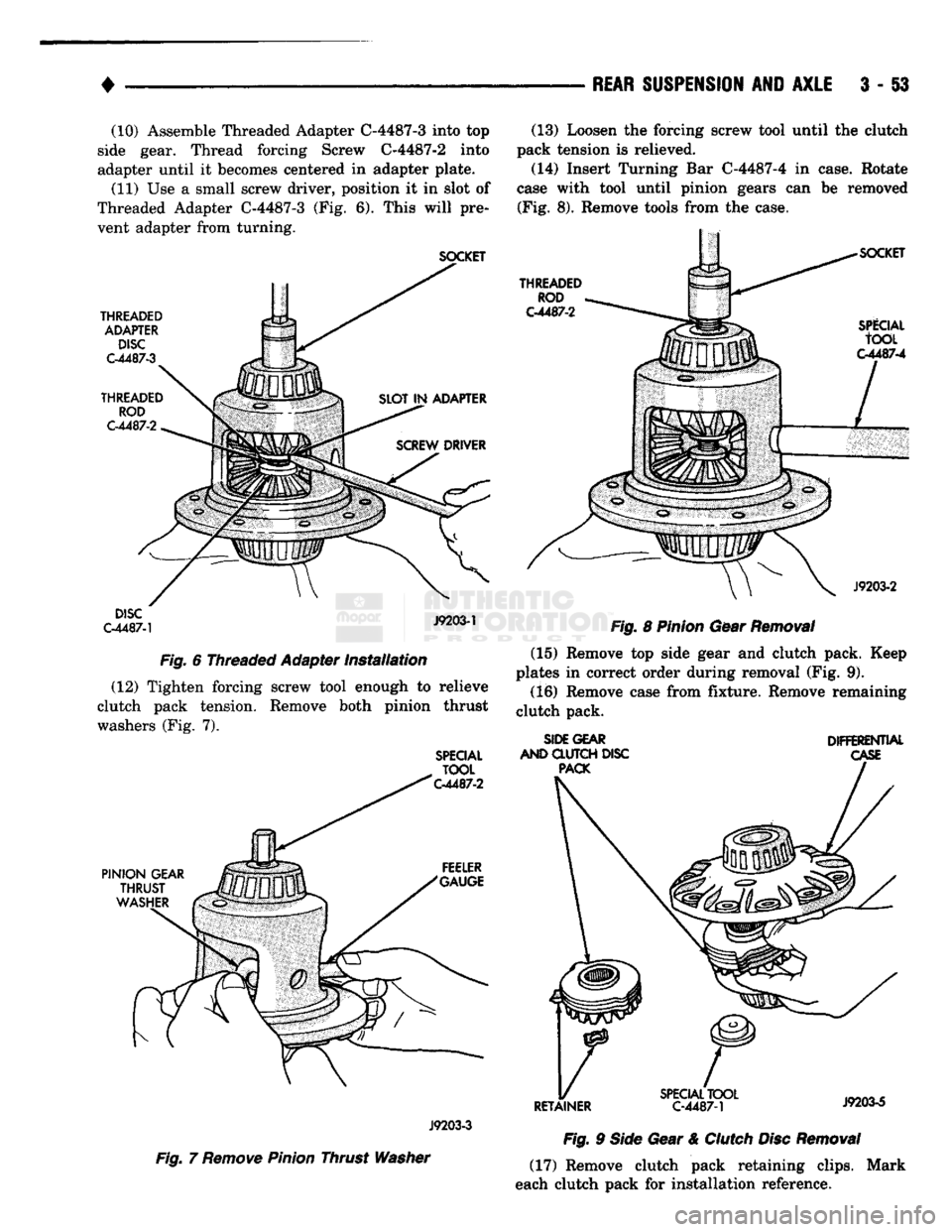
•
REAR SUSPENSION
AND
AXLE
3 - §3 (10) Assemble Threaded Adapter C-4487-3 into top
side gear. Thread forcing Screw C-4487-2 into
adapter until it becomes centered in adapter plate.
(11) Use a small screw driver, position it in slot of
Threaded Adapter C-4487-3 (Fig. 6). This will pre
vent adapter from turning.
SOCKET
THREADED ADAPTER DISC
C-4487-3
THREADED ROD
C-4487-2
DISC
C-4487-1
J9203-1
Fig. 6 Threaded Adapter Installation (12) Tighten forcing screw tool enough to relieve
clutch pack tension. Remove both pinion thrust
washers (Fig. 7).
SPECIAL
TOOL
C-4487-2
(13) Loosen the forcing screw tool until the clutch
pack tension is relieved.
(14) Insert Turning Bar C-4487-4 in case. Rotate
case with tool until pinion gears can be removed (Fig. 8). Remove tools from the case.
THREADED
ROD
C-4487-2
SPlCIAL
tOOL
C-4487-4
J9203-2
Fig. 8 Pinion Gear Removal (15) Remove top side gear and clutch pack. Keep
plates in correct order during removal (Fig. 9).
(16) Remove case from fixture. Remove remaining
clutch pack.
SIDE GEAR
AND CLUTCH DISC PACK DIFFERENTIAL
CASE
PINION
GEAR
THRUST
WASHER FEELER
"GAUGE
33
X
/
J9203-3
Fig. 7 Remove Pinion Thrust Washer
RETAINER
SPECIAL
TOOL
C-4487-1 J9203-5
Fig. 9 Side Gear & Clutch Disc Removal (17) Remove clutch pack retaining clips. Mark
each clutch pack for installation reference.