DODGE TRUCK 1993 Service Repair Manual
Manufacturer: DODGE, Model Year: 1993, Model line: TRUCK, Model: DODGE TRUCK 1993Pages: 1502, PDF Size: 80.97 MB
Page 211 of 1502
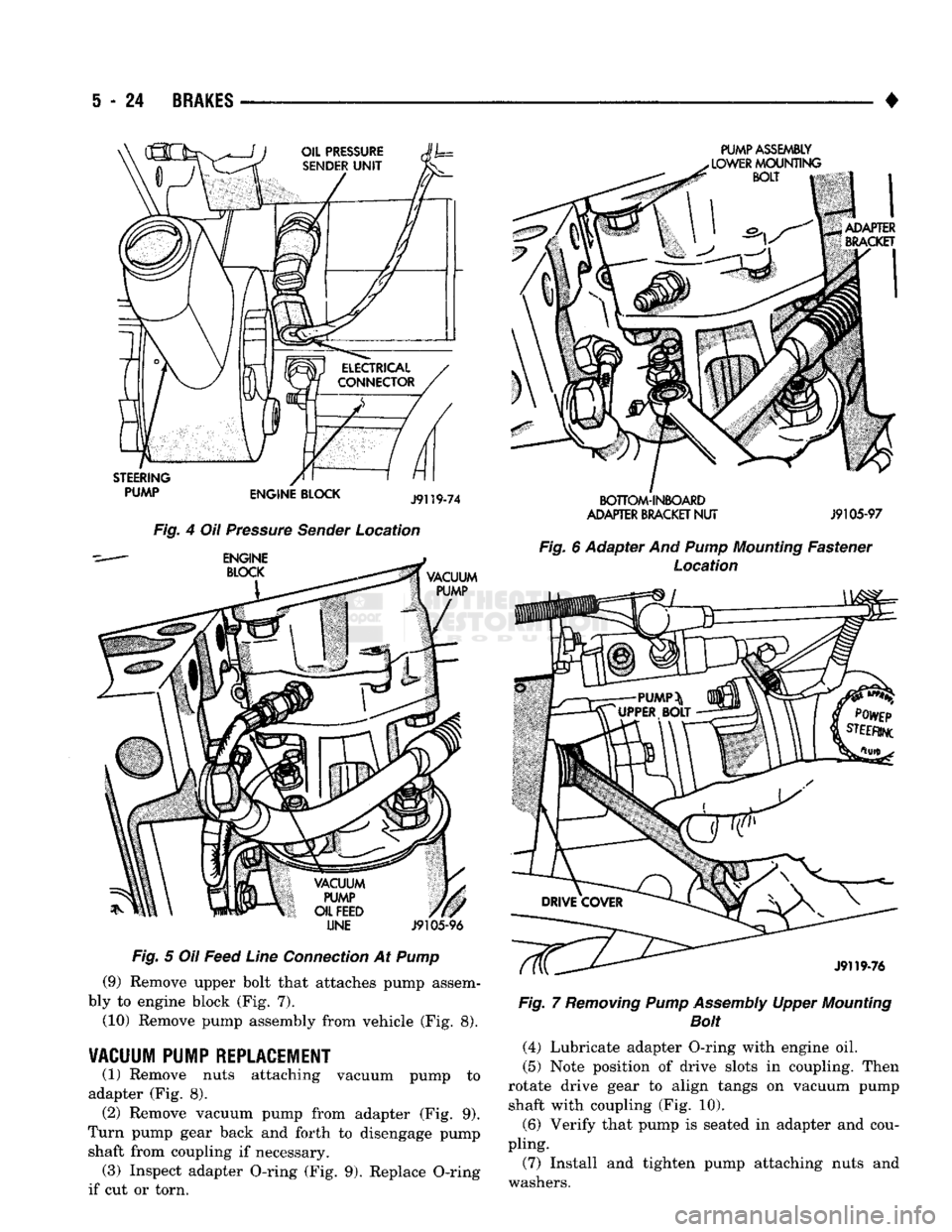
S
- 24
BRAKES
•
LINE
J9105-96
Fig. 5 Oil Feed Line Connection At Pump (9) Remove upper bolt that attaches pump assem
bly to engine block (Fig. 7).
(10) Remove pump assembly from vehicle (Fig. 8).
VACUUM PUMP REPLACEMENT
(1) Remove nuts attaching vacuum pump to
adapter (Fig. 8). (2) Remove vacuum pump from adapter (Fig. 9).
Turn pump gear back and forth to disengage pump shaft from coupling if necessary. (3) Inspect adapter O-ring (Fig. 9). Replace O-ring
if cut or torn.
PUMP ASSEMBLY
SOTTOM-INIOAiD
ADAPTER
BRACKET
NUT
J9105-97
Fig. 6 Adapter And
Pump
Mounting Fastener Location Fig. 7 Removing Pump Assembly Upper Mounting
Bolt
(4) Lubricate adapter O-ring with engine oil.
(5) Note position of drive slots in coupling. Then
rotate drive gear to align tangs on vacuum pump shaft with coupling (Fig. 10).
(6) Verify that pump is seated in adapter and cou
pling.
(7) Install and tighten pump attaching nuts and
washers.
Page 212 of 1502
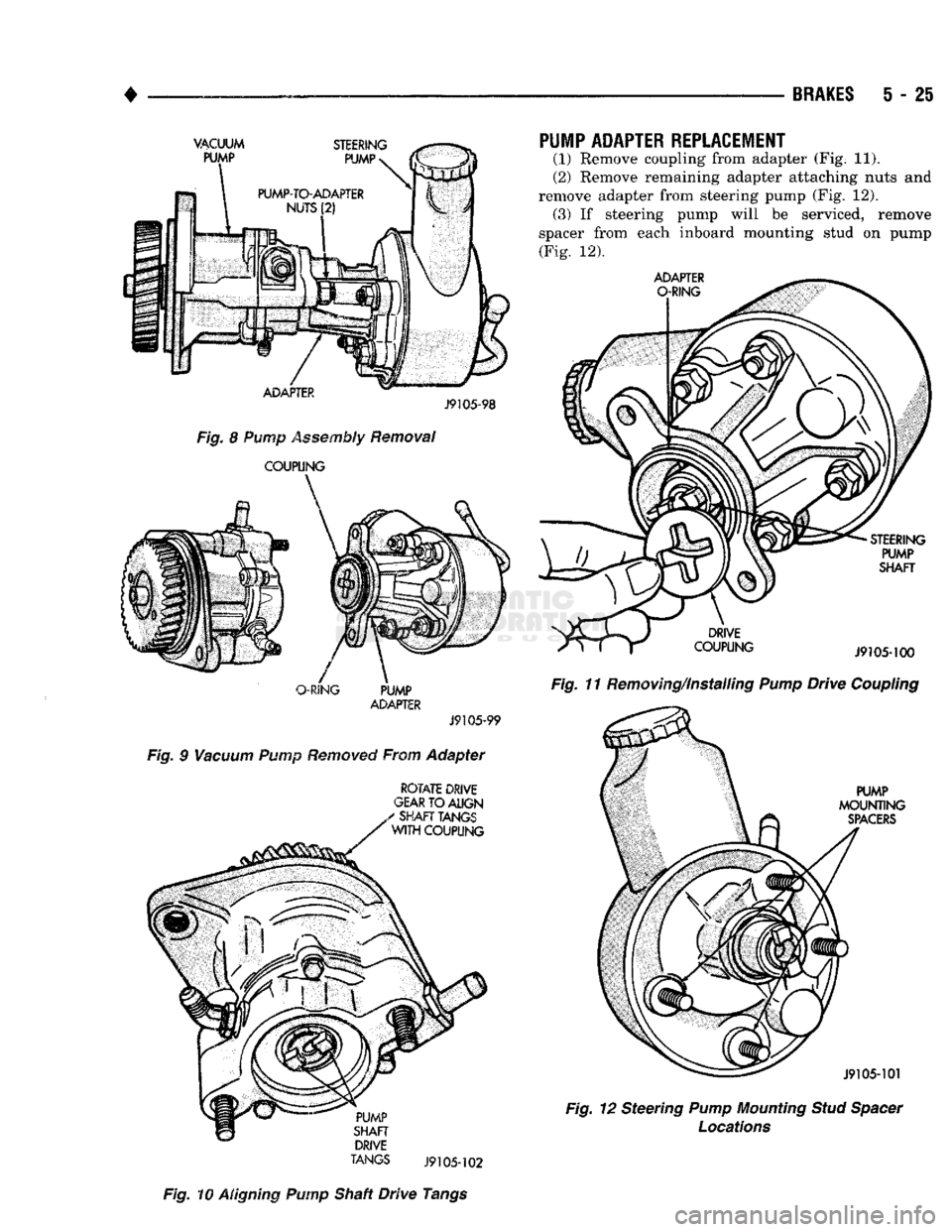
•
BRAKES
5 - 25
ADAPTER
J9105-98
Fig.
8 Pump Assembly Removal
COUPLING
O-RING
PUMP
ADAPTER
J9105-99
Fig.
9
Vacuum
Pump
Removed
From Adapter
ROTATE
DRIVE
GEAR
TO
ALIGN
TANGS
J9105-102
Fig.
10 Aligning Pump Shaft Drive Tangs
PUMP ADAPTER REPLACEMENT
(1) Remove coupling from adapter (Fig. 11).
(2) Remove remaining adapter attaching nuts and
remove adapter from steering pump (Fig. 12). (3) If steering pump will be serviced, remove
spacer from each inboard mounting stud on pump (Fig, 12).
Fig.
11 Removing/Installing
Pump
Drive
Coupling
Fig.
12 Steering
Pump
Mounting
Stud
Spacer
Locations
Page 213 of 1502
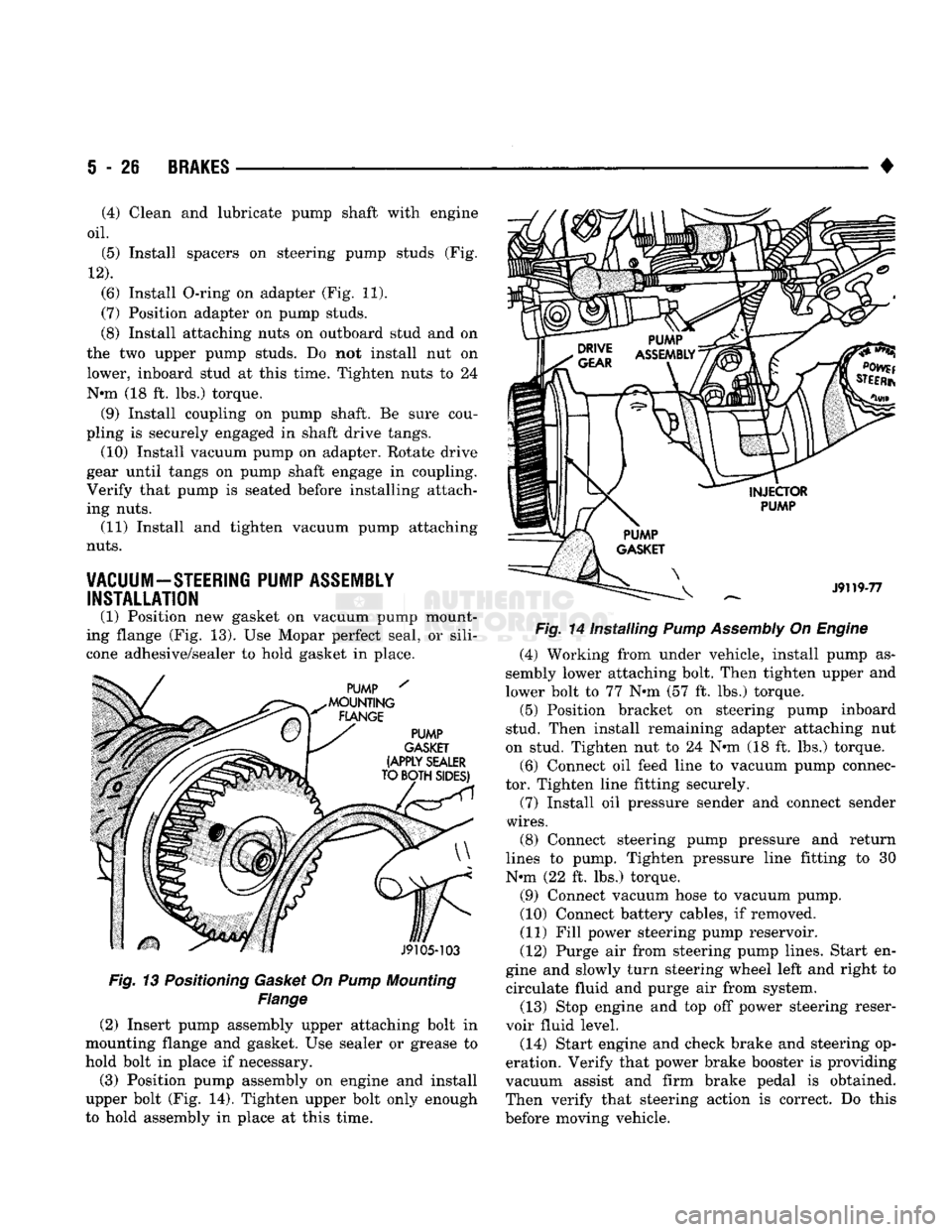
5
- 26
BRAKES
Fig. 13 Positioning Gasket On Pump Mounting
Flange
(2) Insert pump assembly upper attaching bolt in
mounting flange and gasket. Use sealer or grease to
hold bolt in place if necessary.
(3) Position pump assembly on engine and install
upper bolt (Fig. 14). Tighten upper bolt only enough
to hold assembly in place at this time. •
Fig. 14 Installing Pump Assembly On Engine (4) Working from under vehicle, install pump as
sembly lower attaching bolt. Then tighten upper and
lower bolt to 77 N»m (57 ft. lbs.) torque. (5) Position bracket on steering pump inboard
stud. Then install remaining adapter attaching nut
on stud. Tighten nut to 24 N«m (18 ft. lbs.) torque.
(6) Connect oil feed line to vacuum pump connec
tor. Tighten line fitting securely.
(7) Install oil pressure sender and connect sender
wires.
(8) Connect steering pump pressure and return
lines to pump. Tighten pressure line fitting to 30
N-m (22 ft. lbs.) torque.
(9) Connect vacuum hose to vacuum pump.
(10) Connect battery cables, if removed.
(11) Fill power steering pump reservoir.
(12) Purge air from steering pump lines. Start en
gine and slowly turn steering wheel left and right to circulate fluid and purge air from system.
(13) Stop engine and top off power steering reser
voir fluid level.
(14) Start engine and check brake and steering op
eration. Verify that power brake booster is providing
vacuum assist and firm brake pedal is obtained.
Then verify that steering action is correct. Do this
before moving vehicle.
(4) Clean and lubricate pump shaft with engine
oil.
(5) Install spacers on steering pump studs (Fig.
12).
(6) Install O-ring on adapter (Fig. 11).
(7) Position adapter on pump studs.
(8) Install attaching nuts on outboard stud and on
the two upper pump studs. Do not install nut on
lower, inboard stud at this time. Tighten nuts to 24
N-m (18 ft. lbs.) torque. (9) Install coupling on pump shaft. Be sure cou
pling is securely engaged in shaft drive tangs. (10) Install vacuum pump on adapter. Rotate drive
gear until tangs on pump shaft engage in coupling.
Verify that pump is seated before installing attach
ing nuts. (11) Install and tighten vacuum pump attaching
nuts.
VACUUM-STEERING PUMP ASSEMBLY INSTALLATION
(1) Position new gasket on vacuum pump mount
ing flange (Fig. 13). Use Mopar perfect seal, or sili
cone adhesive/sealer to hold gasket in place.
Page 214 of 1502
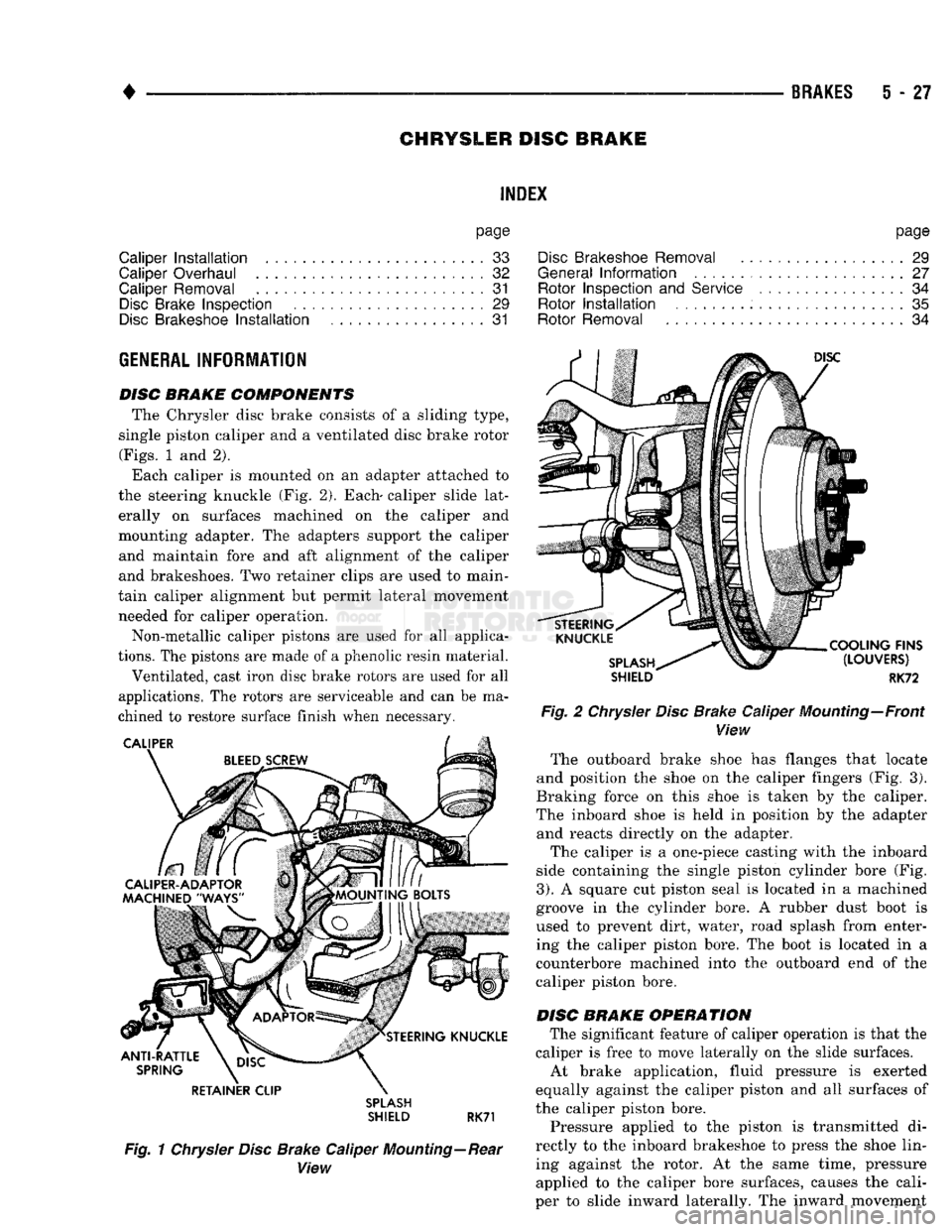
•
BRAKES
5 - 27 CHRYSLER
DISC
BRAKE
INDEX
page
Caliper
Installation
. 33
Caliper Overhaul
32
Caliper Removal
31
Disc
Brake Inspection
29
Disc
Brakeshoe
Installation
, 31
GENERAL
INFORMATION
DISC BRAKE COMPONENTS The Chrysler disc brake consists of a sliding type,
single piston caliper and a ventilated disc brake rotor
(Figs.
1 and 2).
Each caliper is mounted on an adapter attached to
the steering knuckle (Fig. 2). Each- caliper slide lat erally on surfaces machined on the caliper and
mounting adapter. The adapters support the caliper and maintain fore and aft alignment of the caliper
and brakeshoes. Two retainer clips are used to main
tain caliper alignment but permit lateral movement needed for caliper operation.
Non-metallic caliper pistons are used for all applica
tions.
The pistons are made of a phenolic resin material.
Ventilated, cast iron disc brake rotors are used for all
applications. The rotors are serviceable and can be ma
chined to restore surface finish when necessary. RETAINER CLIP
SPLASH
SHIELD RK71
Fig. 1 Chrysler Disc Brake Caliper Mounting—Rear View
page
Disc
Brakeshoe Removal
29
General
Information
....................... 27
Rotor Inspection
and
Service
................ 34
Rotor
Installation
. 35
Rotor Removal
34
SHIELD
RK72
Fig. 2 Chrysler Disc Brake Caliper Mounting—Front View The outboard brake shoe has flanges that locate
and position the shoe on the caliper fingers (Fig. 3).
Braking force on this shoe is taken by the caliper.
The inboard shoe is held in position by the adapter and reacts directly on the adapter.
The caliper is a one-piece casting with the inboard
side containing the single piston cylinder bore (Fig.
3).
A square cut piston seal is located in a machined
groove in the cylinder bore. A rubber dust boot is used to prevent dirt, water, road splash from enter
ing the caliper piston bore. The boot is located in a
counterbore machined into the outboard end of the
caliper piston bore.
DISC BRAKE OPERATION The significant feature of caliper operation is that the
caliper is free to move laterally on the slide surfaces. At brake application, fluid pressure is exerted
equally against the caliper piston and all surfaces of
the caliper piston bore.
Pressure applied to the piston is transmitted di
rectly to the inboard brakeshoe to press the shoe lin ing against the rotor. At the same time, pressure applied to the caliper bore surfaces, causes the cali
per to slide inward laterally. The inward movement
Page 215 of 1502
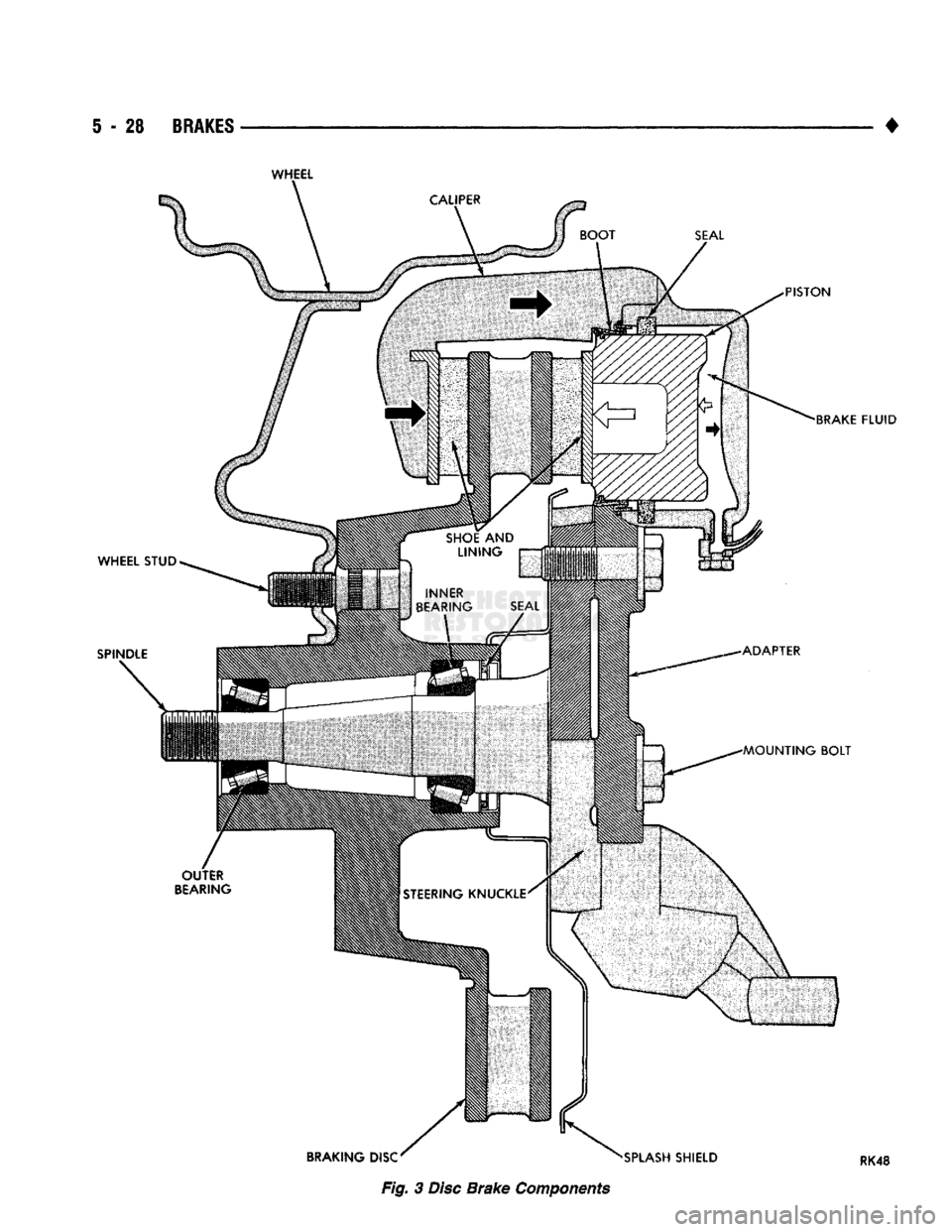
RK48
Page 216 of 1502
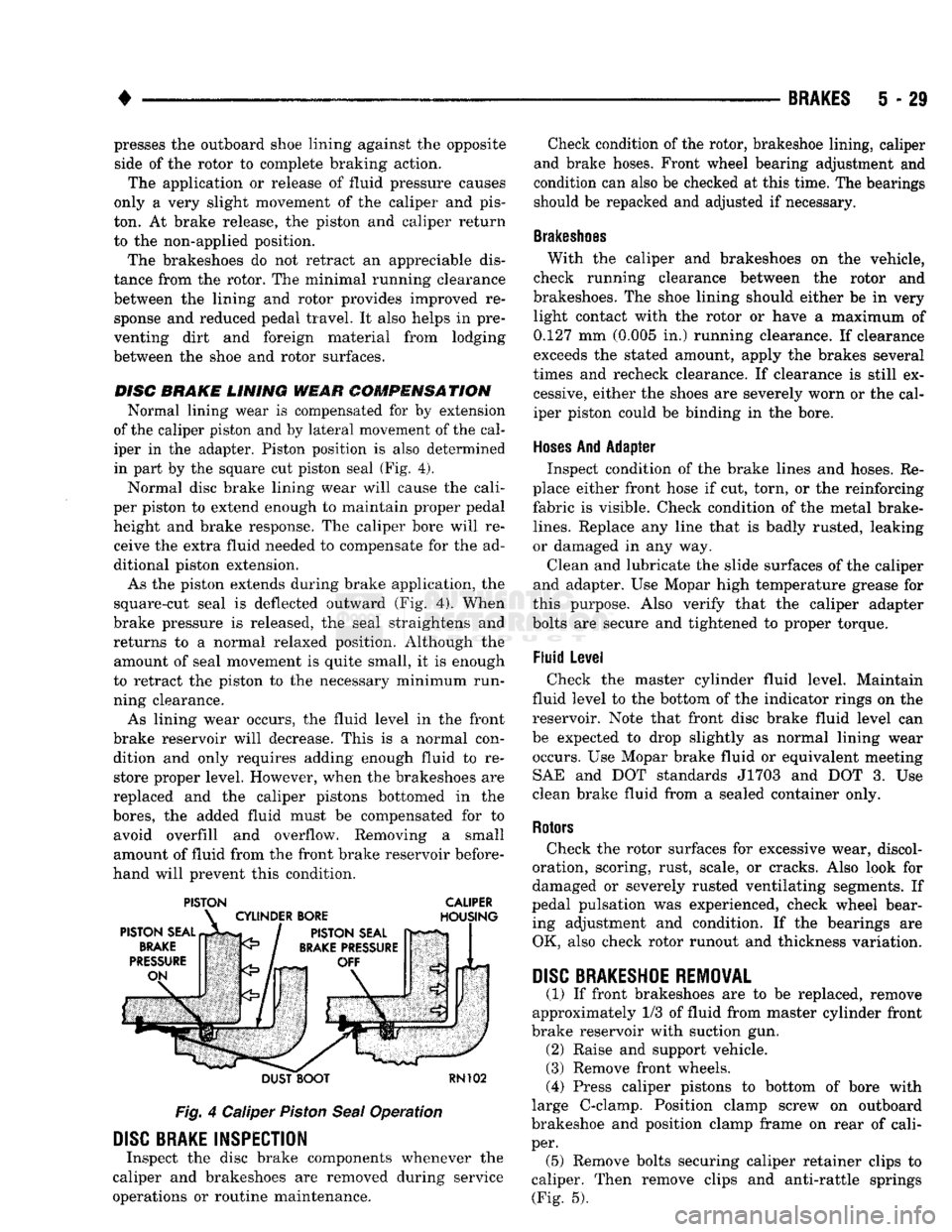
•
BRAKES
5 - 29 presses the outboard shoe lining against the opposite
side of the rotor to complete braking action.
The application or release of fluid pressure causes
only a very slight movement of the caliper and pis
ton. At brake release, the piston and caliper return
to the non-applied position.
The brakeshoes do not retract an appreciable dis
tance from the rotor. The minimal running clearance
between the lining and rotor provides improved re sponse and reduced pedal travel. It also helps in pre
venting dirt and foreign material from lodging
between the shoe and rotor surfaces.
DISC
BRAKE
LINING WEAR COMPENSATION
Normal lining wear is compensated for by extension
of the caliper piston and by lateral movement of the cal
iper in the adapter. Piston position is also determined
in part by the square cut piston seal (Fig. 4).
Normal disc brake lining wear will cause the cali
per piston to extend enough to maintain proper pedal height and brake response. The caliper bore will receive the extra fluid needed to compensate for the ad
ditional piston extension.
As the piston extends during brake application, the
square-cut seal is deflected outward (Fig. 4). When
brake pressure is released, the seal straightens and
returns to a normal relaxed position. Although the amount of seal movement is quite small, it is enough
to retract the piston to the necessary minimum run
ning clearance.
As lining wear occurs, the fluid level in the front
brake reservoir will decrease. This is a normal con dition and only requires adding enough fluid to restore proper level. However, when the brakeshoes are
replaced and the caliper pistons bottomed in the
bores,
the added fluid must be compensated for to avoid overfill and overflow. Removing a small
amount of fluid from the front brake reservoir before
hand will prevent this condition.
PISTON CALIPER
DUST BOOT
RN102
Fig.
4 Caliper
Piston
Seal
Operation
DISC
BRAKE INSPECTION
Inspect the disc brake components whenever the
caliper and brakeshoes are removed during service
operations or routine maintenance. Check condition of the rotor, brakeshoe lining, caliper
and brake hoses. Front wheel bearing adjustment and
condition can also be checked at this time. The bearings
should be repacked and adjusted if necessary.
Brakeshoes
With the caliper and brakeshoes on the vehicle,
check running clearance between the rotor and
brakeshoes. The shoe lining should either be in very light contact with the rotor or have a maximum of
0.127 mm (0.005 in.) running clearance. If clearance
exceeds the stated amount, apply the brakes several
times and recheck clearance. If clearance is still ex cessive, either the shoes are severely worn or the cal
iper piston could be binding in the bore.
Hoses
And Adapter Inspect condition of the brake lines and hoses. Re
place either front hose if cut, torn, or the reinforcing
fabric is visible. Check condition of the metal brake-
lines.
Replace any line that is badly rusted, leaking
or damaged in any way.
Clean and lubricate the slide surfaces of the caliper
and adapter. Use Mopar high temperature grease for
this purpose. Also verify that the caliper adapter
bolts are secure and tightened to proper torque.
Fluid Level Check the master cylinder fluid level. Maintain
fluid level to the bottom of the indicator rings on the
reservoir. Note that front disc brake fluid level can
be expected to drop slightly as normal lining wear occurs. Use Mopar brake fluid or equivalent meeting SAE and DOT standards J1703 and DOT 3. Use
clean brake fluid from a sealed container only.
Rotors
Check the rotor surfaces for excessive wear, discol
oration, scoring, rust, scale, or cracks. Also look for
damaged or severely rusted ventilating segments. If
pedal pulsation was experienced, check wheel bear ing adjustment and condition. If the bearings are OK, also check rotor runout and thickness variation.
DISC
BRAKESHOE
REMOVAL
(1) If front brakeshoes are to be replaced, remove
approximately 1/3 of fluid from master cylinder front
brake reservoir with suction gun. (2) Raise and support vehicle.
(3) Remove front wheels.
(4) Press caliper pistons to bottom of bore with
large C-clamp. Position clamp screw on outboard
brakeshoe and position clamp frame on rear of cali
per. (5) Remove bolts securing caliper retainer clips to
caliper. Then remove clips and anti-rattle springs (Fig. 5).
Page 217 of 1502
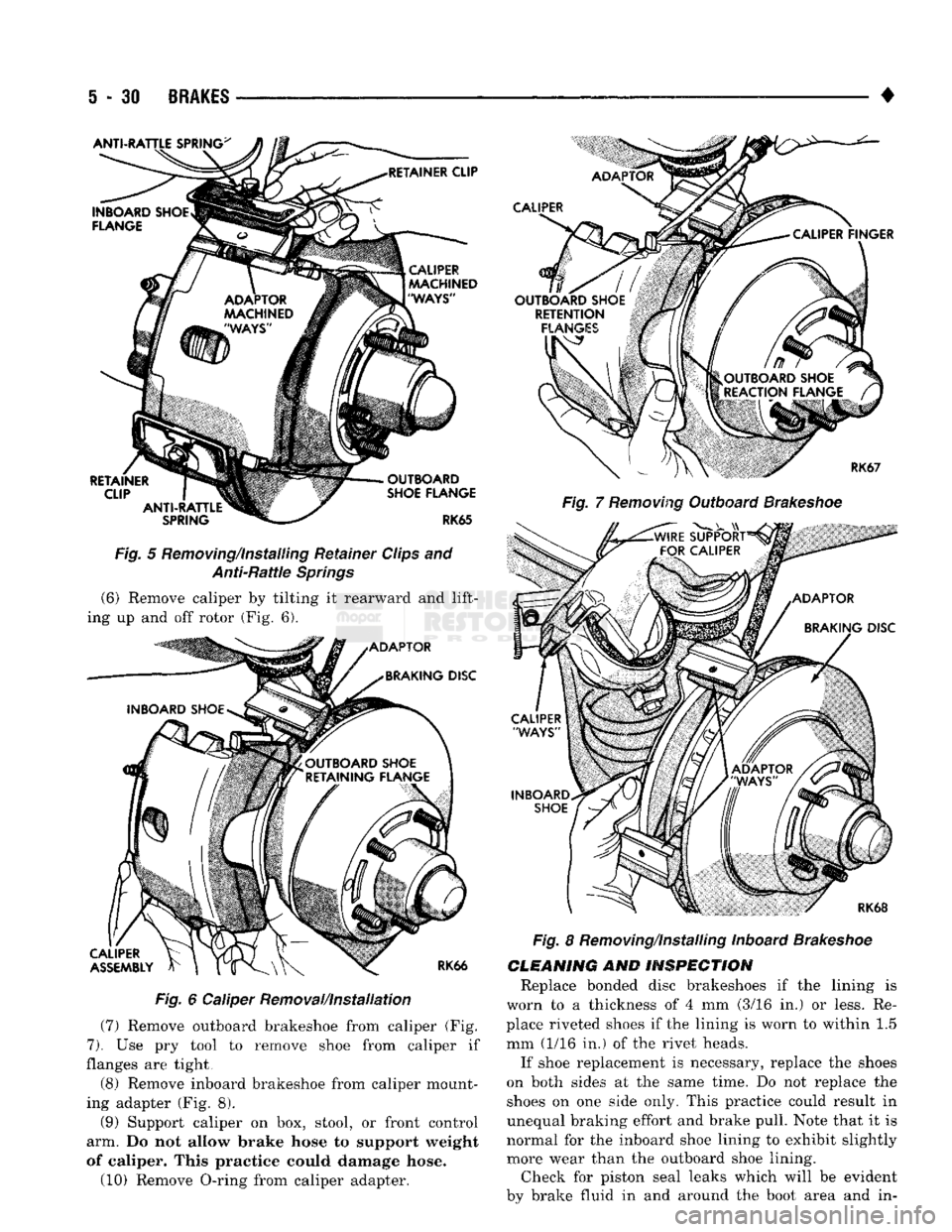
5 - 31
BRAKES
Fig.
5 Removing/installing Retainer Clips and Anti-Rattle Springs (6) Remove caliper by tilting it rearward and lift
ing up and off rotor (Fig. 6).
Fig.
6 Caliper Removal/Installation
(7) Remove outboard brakeshoe from caliper (Fig.
7).
Use pry tool to remove shoe from caliper if
flanges are tight,
(8) Remove inboard brakeshoe from caliper mount
ing adapter (Fig. 8). (9) Support caliper on box, stool, or front control
arm. Do not allow brake hose to support weight
of caliper. This practice could damage hose.
(10) Remove O-ring from caliper adapter. •
Fig.
7
Removing
Outboard
Brakeshoe
Fig.
8 Removing/Installing Inboard
Brakeshoe
CLEANING
AND
INSPECTION
Replace bonded disc brakeshoes if the lining is
worn to a thickness of 4 mm (3/16 in.) or less. Re
place riveted shoes if the lining is worn to within 1.5
mm (1/16 in.) of the rivet heads.
If shoe replacement is necessary, replace the shoes
on both sides at the same time. Do not replace the shoes on one side only. This practice could result in
unequal braking effort and brake pull. Note that it is
normal for the inboard shoe lining to exhibit slightly more wear than the outboard shoe lining. Check for piston seal leaks which will be evident
by brake fluid in and around the boot area and in-
Page 218 of 1502
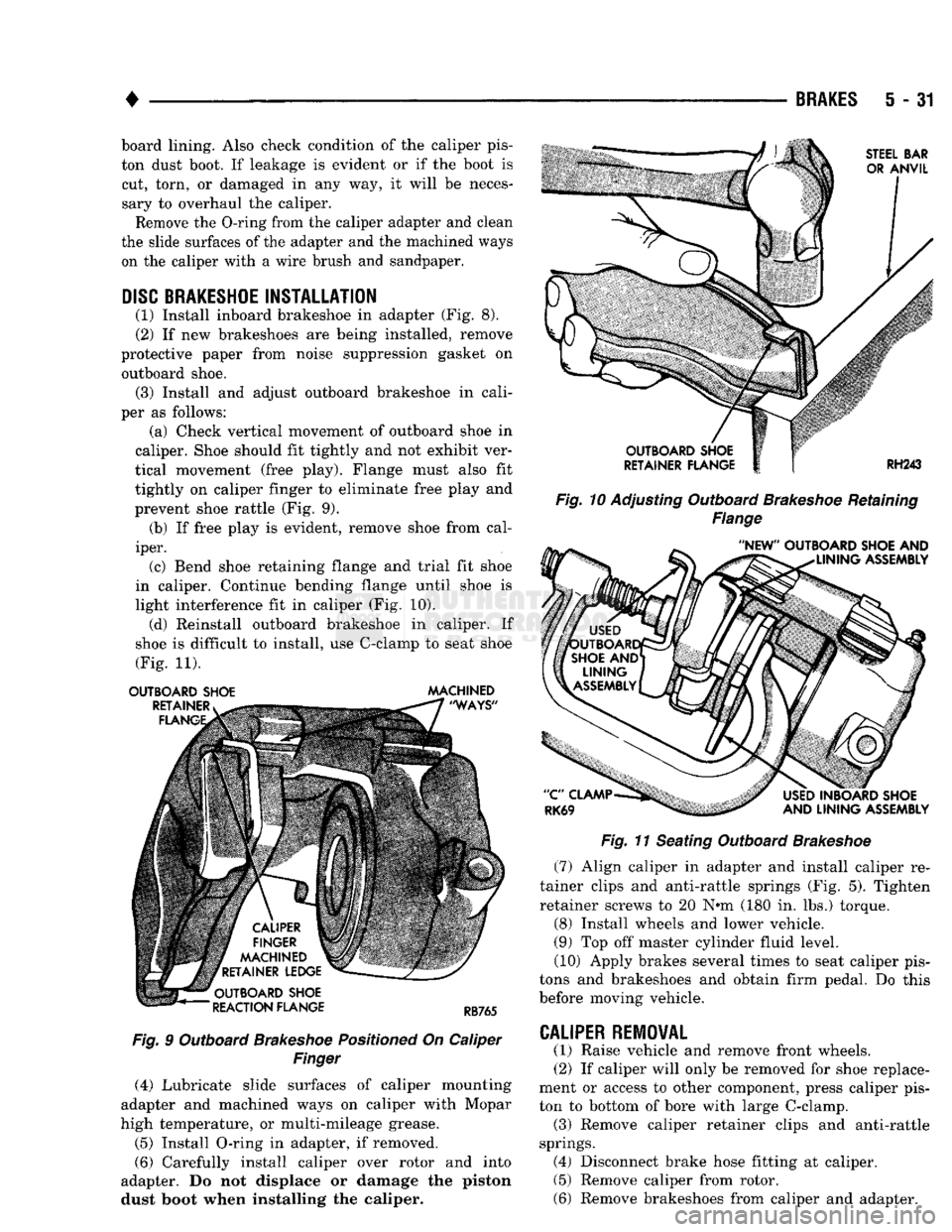
•
BRAKES
5 - 31 board lining. Also check condition of the caliper pis
ton dust boot. If leakage is evident or if the boot is
cut, torn, or damaged in any way, it will be necessary to overhaul the caliper.
Remove the O-ring from the caliper adapter and clean
the slide surfaces of the adapter and the machined ways on the caliper with a wire brush and sandpaper.
DISC
BRAKESHOE
INSTALLATION
(1) Install inboard brakeshoe in adapter (Fig. 8).
(2) If new brakeshoes are being installed, remove
protective paper from noise suppression gasket on outboard shoe. (3) Install and adjust outboard brakeshoe in cali
per as follows: (a) Check vertical movement of outboard shoe in
caliper. Shoe should fit tightly and not exhibit ver
tical movement (free play). Flange must also fit
tightly on caliper finger to eliminate free play and
prevent shoe rattle (Fig. 9). (b) If free play is evident, remove shoe from cal
iper. (c) Bend shoe retaining flange and trial fit shoe
in caliper. Continue bending flange until shoe is
light interference fit in caliper (Fig. 10). (d) Reinstall outboard brakeshoe in caliper. If
shoe is difficult to install, use C-clamp to seat shoe
(Fig. 11).
OUTBOARD SHOE MACHINED
Fig.
9 Outboard
Brakeshoe
Positioned
On Caliper
Finger
(4) Lubricate slide surfaces of caliper mounting
adapter and machined ways on caliper with Mopar
high temperature, or multi-mileage grease.
(5) Install O-ring in adapter, if removed.
(6) Carefully install caliper over rotor and into
adapter. Do not displace or damage the piston dust boot when installing the caliper.
Fig. 10
Adjusting Outboard
Brakeshoe
Retaining
Flange
Fig.
11 Seating Outboard
Brakeshoe
(7) Align caliper in adapter and install caliper re
tainer clips and anti-rattle springs (Fig. 5). Tighten
retainer screws to 20 N«m (180 in. lbs.) torque.
(8) Install wheels and lower vehicle.
(9) Top off master cylinder fluid level. (10) Apply brakes several times to seat caliper pis
tons and brakeshoes and obtain firm pedal. Do this
before moving vehicle.
CALIPER
REMOVAL
(1) Raise vehicle and remove front wheels.
(2) If caliper will only be removed for shoe replace
ment or access to other component, press caliper pis
ton to bottom of bore with large C-clamp. (3) Remove caliper retainer clips and anti-rattle
springs. (4) Disconnect brake hose fitting at caliper. (5) Remove caliper from rotor.
(6) Remove brakeshoes from caliper and adapter.
Page 219 of 1502
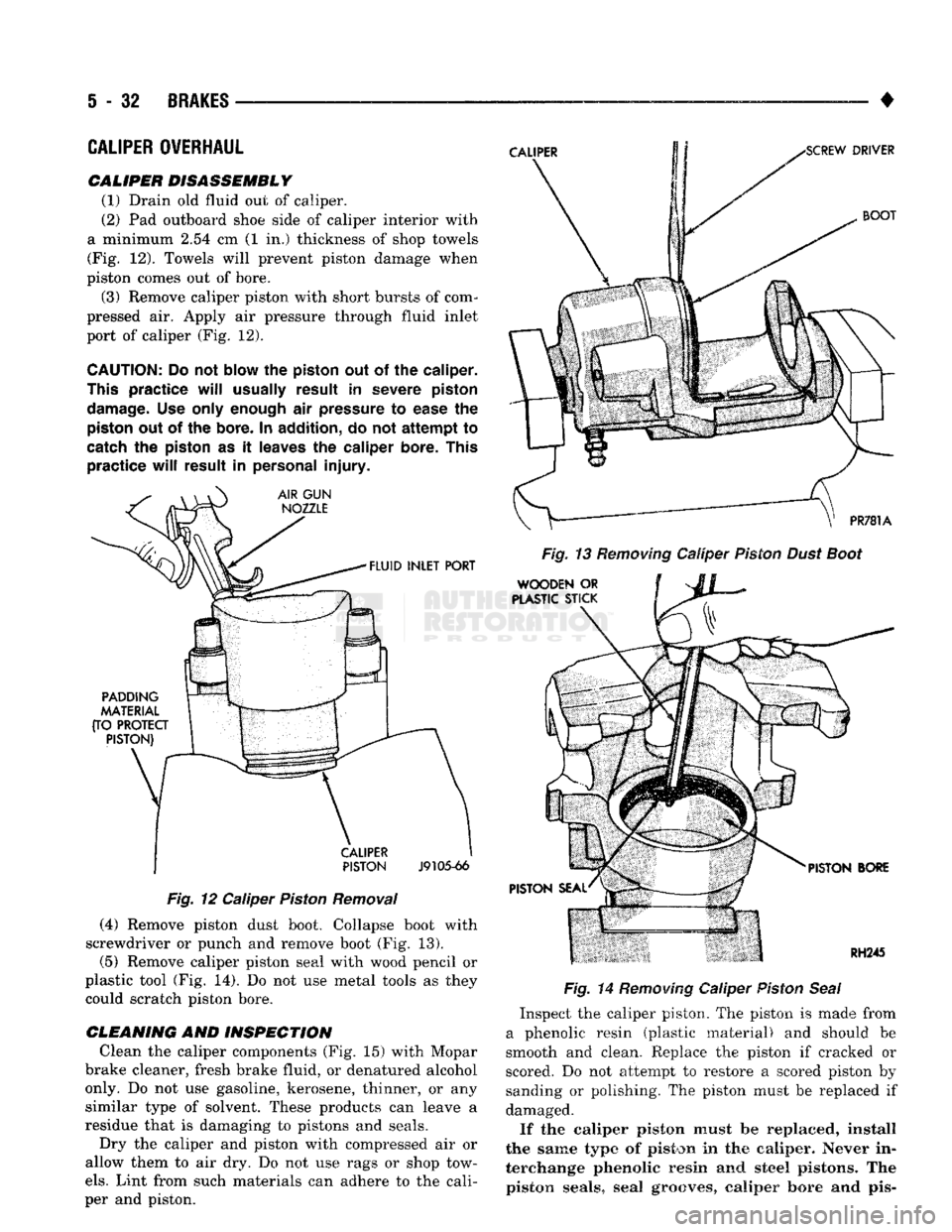
5
- 32
BRAKES
•
CALIPER
OVERHAUL
CALIPER DISASSEMBLY (1) Drain
old
fluid
out of
caliper.
(2)
Pad
outboard shoe side
of
caliper interior with
a minimum
2.54 cm (1 in.)
thickness
of
shop towels (Fig.
12).
Towels will prevent piston damage when
piston comes
out of
bore.
(3) Remove caliper piston with short bursts
of
com
pressed
air.
Apply
air
pressure through fluid inlet
port
of
caliper
(Fig. 12).
CAUTION:
Do
not
blow
the
piston
out of the
caliper.
This
practice
will
usually
result
in
severe piston
damage.
Use
only enough
air
pressure
to
ease
the
piston
out of the
bore.
In
addition,
do not
attempt
to
catch
the
piston
as it
leaves
the
caliper
bore. This
practice
will
result
in
personal
injury.
Fig.
12
Caliper Piston Removal
(4) Remove piston dust boot. Collapse boot with
screwdriver
or
punch
and
remove boot
(Fig. 13).
(5) Remove caliper piston seal with wood pencil
or
plastic tool
(Fig. 14). Do not use
metal tools
as
they could scratch piston bore.
CLEANING
AND
INSPECTION Clean
the
caliper components
(Fig. 15)
with Mopar
brake cleaner, fresh brake fluid,
or
denatured alcohol only.
Do not use
gasoline, kerosene, thinner,
or any
similar type
of
solvent. These products
can
leave
a
residue that
is
damaging
to
pistons
and
seals. Dry
the
caliper
and
piston with compressed
air or
allow them
to air dry. Do not use
rags
or
shop tow
els.
Lint from such materials
can
adhere
to the
cali
per
and
piston. Fig. 14 Removing Caliper Piston Seal
Inspect
the
caliper piston.
The
piston
is
made from
a phenolic resin (plastic material)
and
should
be
smooth
and
clean. Replace
the
piston
if
cracked
or
scored.
Do not
attempt
to
restore
a
scored piston
by
sanding
or
polishing.
The
piston must
be
replaced
if
damaged.
If
the
caliper piston must
be
replaced, install
the same
type
of
piston
in the
caliper.
Never
in
terchange phenolic resin
and
steel
pistons.
The
piston seals,
seal
grooves,
caliper bore
and pis-
Page 220 of 1502
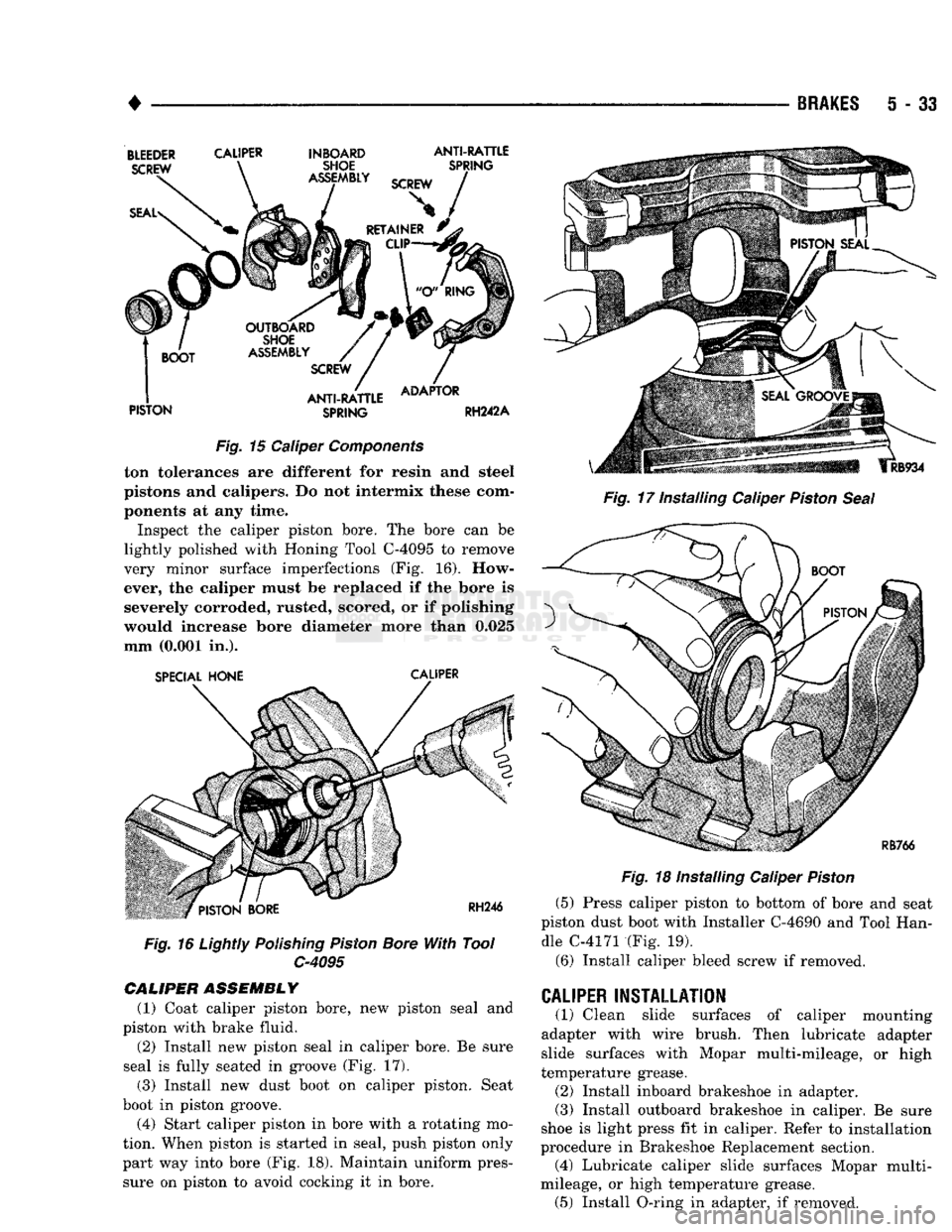
•
BRAKES
5
- 33
BLEEDER
CALIPER
INBOARD
ANTI-RATTLE
PISTON
SPRING
RH242A
Fig.
15
Caliper Components ton tolerances
are
different
for
resin
and
steel
pistons
and
calipers.
Do not
intermix these com
ponents
at any
time. Inspect
the
caliper piston bore.
The
bore
can be
lightly polished with Honing Tool C-4095
to
remove
very minor surface imperfections
(Fig. 16).
How
ever,
the
caliper must
be
replaced
if the
bore
is
severely corroded, rusted, scored,
or if
polishing
would increase bore diameter more than 0.025
mm (0.001
in.).
Fig. 16 Lightly Polishing Piston Bore With Tool
C-4095
CALIPER ASSEMBLY (1) Coat caliper piston bore,
new
piston seal
and
piston with brake fluid.
(2) Install
new
piston seal
in
caliper bore.
Be
sure
seal
is
fully seated
in
groove
(Fig. 17).
(3) Install
new
dust boot
on
caliper piston. Seat
boot
in
piston groove.
(4) Start caliper piston
in
bore with
a
rotating
mo
tion. When piston
is
started
in
seal, push piston only
part
way
into bore
(Fig. 18).
Maintain uniform pres sure
on
piston
to
avoid cocking
it in
bore.
Fig.
17 Installing Caliper
Piston
Seal
Fig.
18 Installing Caliper
Piston
(5) Press caliper piston
to
bottom
of
bore
and
seat
piston dust boot with Installer C-4690
and
Tool Han dle C-4171
(Fig. 19).
(6) Install caliper bleed screw
if
removed.
CALIPER
INSTALLATION
(1) Clean slide surfaces
of
caliper mounting
adapter with wire brush. Then lubricate adapter
slide surfaces with Mopar multi-mileage,
or
high
temperature grease.
(2) Install inboard brakeshoe
in
adapter.
(3) Install outboard brakeshoe
in
caliper.
Be
sure
shoe
is
light press
fit in
caliper. Refer
to
installation
procedure
in
Brakeshoe Replacement section. (4) Lubricate caliper slide surfaces Mopar multi-
mileage,
or
high temperature grease. (5) Install O-ring
in
adapter,
if
removed.