FIAT UNO 1983 Service Repair Manual
Manufacturer: FIAT, Model Year: 1983, Model line: UNO, Model: FIAT UNO 1983Pages: 303, PDF Size: 10.36 MB
Page 141 of 303
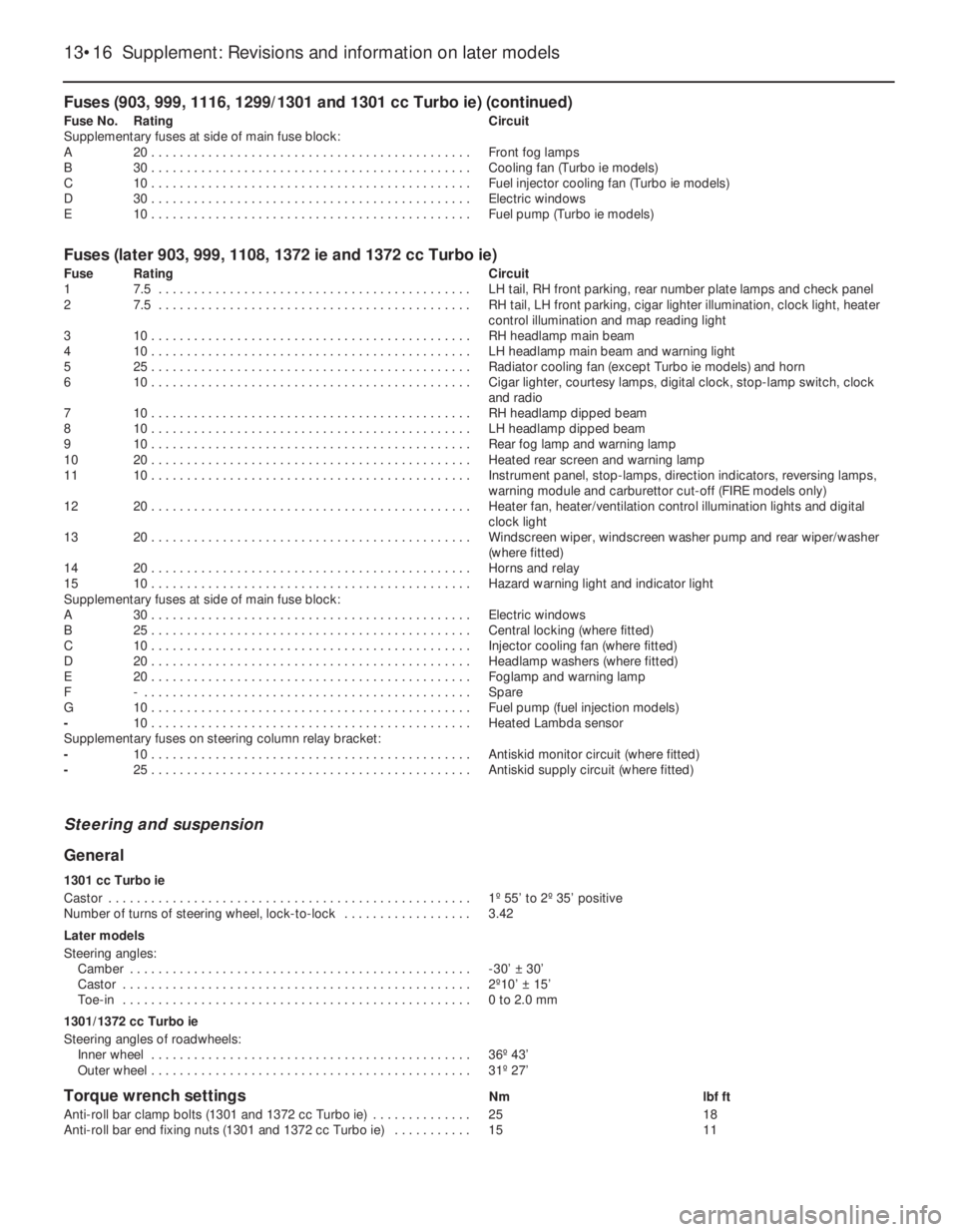
Fuses (903, 999, 1116, 1299/1301 and 1301 cc Turbo ie) (continued)
Fuse No. Rating Circuit
Supplementary fuses at side of main fuse block:
A 20 . . . . . . . . . . . . . . . . . . . . . . . . . . . . . . . . . . . . . . . . . . . . . Front fog lamps
B 30 . . . . . . . . . . . . . . . . . . . . . . . . . . . . . . . . . . . . . . . . . . . . . Cooling fan (Turbo ie models)
C 10 . . . . . . . . . . . . . . . . . . . . . . . . . . . . . . . . . . . . . . . . . . . . . Fuel injector cooling fan (Turbo ie models)
D 30 . . . . . . . . . . . . . . . . . . . . . . . . . . . . . . . . . . . . . . . . . . . . . Electric windows
E 10 . . . . . . . . . . . . . . . . . . . . . . . . . . . . . . . . . . . . . . . . . . . . . Fuel pump (Turbo ie models)
Fuses (later 903, 999, 1108, 1372 ie and 1372 cc Turbo ie)
Fuse Rating Circuit
1 7.5 . . . . . . . . . . . . . . . . . . . . . . . . . . . . . . . . . . . . . . . . . . . . LH tail, RH front parking, rear number plate lamps and check panel
2 7.5 . . . . . . . . . . . . . . . . . . . . . . . . . . . . . . . . . . . . . . . . . . . . RH tail, LH front parking, cigar lighter illumination, clock light, heater
control illumination and map reading light
3 10 . . . . . . . . . . . . . . . . . . . . . . . . . . . . . . . . . . . . . . . . . . . . . RH headlamp main beam
4 10 . . . . . . . . . . . . . . . . . . . . . . . . . . . . . . . . . . . . . . . . . . . . . LH headlamp main beam and warning light
5 25 . . . . . . . . . . . . . . . . . . . . . . . . . . . . . . . . . . . . . . . . . . . . . Radiator cooling fan (except Turbo ie models) and horn
6 10 . . . . . . . . . . . . . . . . . . . . . . . . . . . . . . . . . . . . . . . . . . . . . Cigar lighter, courtesy lamps, digital clock, stop-lamp switch, clock
and radio
7 10 . . . . . . . . . . . . . . . . . . . . . . . . . . . . . . . . . . . . . . . . . . . . . RH headlamp dipped beam
8 10 . . . . . . . . . . . . . . . . . . . . . . . . . . . . . . . . . . . . . . . . . . . . . LH headlamp dipped beam
9 10 . . . . . . . . . . . . . . . . . . . . . . . . . . . . . . . . . . . . . . . . . . . . . Rear fog lamp and warning lamp
10 20 . . . . . . . . . . . . . . . . . . . . . . . . . . . . . . . . . . . . . . . . . . . . . Heated rear screen and warning lamp
11 10 . . . . . . . . . . . . . . . . . . . . . . . . . . . . . . . . . . . . . . . . . . . . . Instrument panel, stop-lamps, direction indicators, reversing lamps,
warning module and carburettor cut-off (FIRE models only)
12 20 . . . . . . . . . . . . . . . . . . . . . . . . . . . . . . . . . . . . . . . . . . . . . Heater fan, heater/ventilation control illumination lights and digital
clock light
13 20 . . . . . . . . . . . . . . . . . . . . . . . . . . . . . . . . . . . . . . . . . . . . . Windscreen wiper, windscreen washer pump and rear wiper/washer
(where fitted)
14 20 . . . . . . . . . . . . . . . . . . . . . . . . . . . . . . . . . . . . . . . . . . . . . Horns and relay
15 10 . . . . . . . . . . . . . . . . . . . . . . . . . . . . . . . . . . . . . . . . . . . . . Hazard warning light and indicator light
Supplementary fuses at side of main fuse block:
A 30 . . . . . . . . . . . . . . . . . . . . . . . . . . . . . . . . . . . . . . . . . . . . . Electric windows
B 25 . . . . . . . . . . . . . . . . . . . . . . . . . . . . . . . . . . . . . . . . . . . . . Central locking (where fitted)
C 10 . . . . . . . . . . . . . . . . . . . . . . . . . . . . . . . . . . . . . . . . . . . . . Injector cooling fan (where fitted)
D 20 . . . . . . . . . . . . . . . . . . . . . . . . . . . . . . . . . . . . . . . . . . . . . Headlamp washers (where fitted)
E 20 . . . . . . . . . . . . . . . . . . . . . . . . . . . . . . . . . . . . . . . . . . . . . Foglamp and warning lamp
F - . . . . . . . . . . . . . . . . . . . . . . . . . . . . . . . . . . . . . . . . . . . . . . Spare
G 10 . . . . . . . . . . . . . . . . . . . . . . . . . . . . . . . . . . . . . . . . . . . . . Fuel pump (fuel injection models)
-10 . . . . . . . . . . . . . . . . . . . . . . . . . . . . . . . . . . . . . . . . . . . . . Heated Lambda sensor
Supplementary fuses on steering column relay bracket:
-10 . . . . . . . . . . . . . . . . . . . . . . . . . . . . . . . . . . . . . . . . . . . . . Antiskid monitor circuit (where fitted)
-25 . . . . . . . . . . . . . . . . . . . . . . . . . . . . . . . . . . . . . . . . . . . . . Antiskid supply circuit (where fitted)
Steering and suspension
General
1301 cc Turbo ie
Castor . . . . . . . . . . . . . . . . . . . . . . . . . . . . . . . . . . . . . . . . . . . . . . . . . . . 1º 55’ to 2º 35’ positive
Number of turns of steering wheel, lock-to-lock . . . . . . . . . . . . . . . . . . 3.42
Later models
Steering angles:
Camber . . . . . . . . . . . . . . . . . . . . . . . . . . . . . . . . . . . . . . . . . . . . . . . . -30’ ± 30’
Castor . . . . . . . . . . . . . . . . . . . . . . . . . . . . . . . . . . . . . . . . . . . . . . . . . 2º10’ ± 15’
Toe-in . . . . . . . . . . . . . . . . . . . . . . . . . . . . . . . . . . . . . . . . . . . . . . . . . 0 to 2.0 mm
1301/1372 cc Turbo ie
Steering angles of roadwheels:
Inner wheel . . . . . . . . . . . . . . . . . . . . . . . . . . . . . . . . . . . . . . . . . . . . . 36º 43’
Outer wheel . . . . . . . . . . . . . . . . . . . . . . . . . . . . . . . . . . . . . . . . . . . . . 31º 27’
Torque wrench settingsNm lbf ft
Anti-roll bar clamp bolts (1301 and 1372 cc Turbo ie) . . . . . . . . . . . . . . 25 18
Anti-roll bar end fixing nuts (1301 and 1372 cc Turbo ie) . . . . . . . . . . . 15 11
13•16 Supplement: Revisions and information on later models
Page 142 of 303
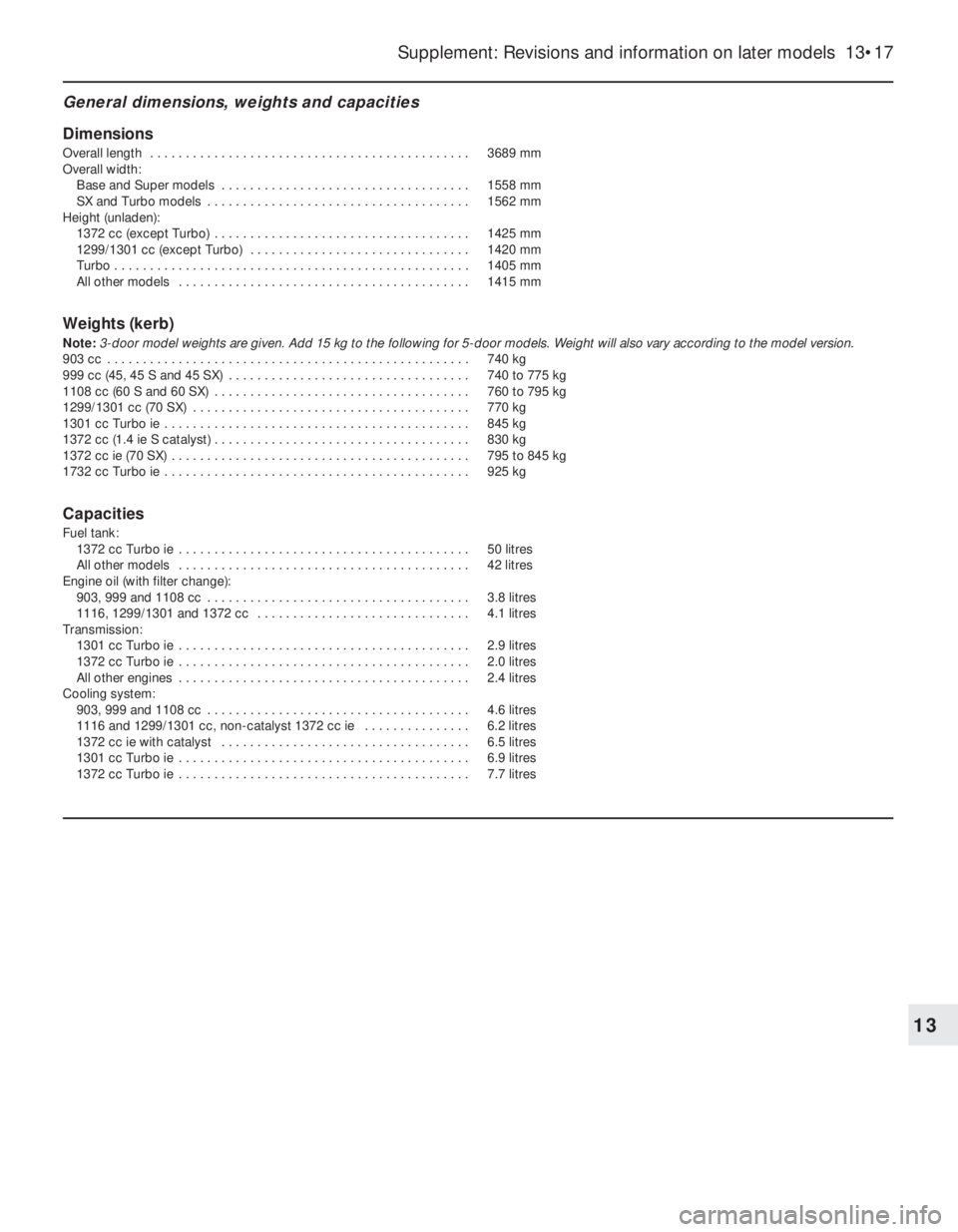
General dimensions, weights and capacities
Dimensions
Overall length . . . . . . . . . . . . . . . . . . . . . . . . . . . . . . . . . . . . . . . . . . . . . 3689 mm
Overall width:
Base and Super models . . . . . . . . . . . . . . . . . . . . . . . . . . . . . . . . . . . 1558 mm
SX and Turbo models . . . . . . . . . . . . . . . . . . . . . . . . . . . . . . . . . . . . . 1562 mm
Height (unladen):
1372 cc (except Turbo) . . . . . . . . . . . . . . . . . . . . . . . . . . . . . . . . . . . . 1425 mm
1299/1301 cc (except Turbo) . . . . . . . . . . . . . . . . . . . . . . . . . . . . . . . 1420 mm
Turbo . . . . . . . . . . . . . . . . . . . . . . . . . . . . . . . . . . . . . . . . . . . . . . . . . . 1405 mm
All other models . . . . . . . . . . . . . . . . . . . . . . . . . . . . . . . . . . . . . . . . . 1415 mm
Weights (kerb)
Note: 3-door model weights are given. Add 15 kg to the following for 5-door models. Weight will also vary according to the model version.
903 cc . . . . . . . . . . . . . . . . . . . . . . . . . . . . . . . . . . . . . . . . . . . . . . . . . . . 740 kg
999 cc (45, 45 S and 45 SX) . . . . . . . . . . . . . . . . . . . . . . . . . . . . . . . . . . 740 to 775 kg
1108 cc (60 S and 60 SX) . . . . . . . . . . . . . . . . . . . . . . . . . . . . . . . . . . . . 760 to 795 kg
1299/1301 cc (70 SX) . . . . . . . . . . . . . . . . . . . . . . . . . . . . . . . . . . . . . . . 770 kg
1301 cc Turbo ie . . . . . . . . . . . . . . . . . . . . . . . . . . . . . . . . . . . . . . . . . . . 845 kg
1372 cc (1.4 ie S catalyst) . . . . . . . . . . . . . . . . . . . . . . . . . . . . . . . . . . . . 830 kg
1372 cc ie (70 SX) . . . . . . . . . . . . . . . . . . . . . . . . . . . . . . . . . . . . . . . . . . 795 to 845 kg
1732 cc Turbo ie . . . . . . . . . . . . . . . . . . . . . . . . . . . . . . . . . . . . . . . . . . . 925 kg
Capacities
Fuel tank:
1372 cc Turbo ie . . . . . . . . . . . . . . . . . . . . . . . . . . . . . . . . . . . . . . . . . 50 litres
All other models . . . . . . . . . . . . . . . . . . . . . . . . . . . . . . . . . . . . . . . . . 42 litres
Engine oil (with filter change):
903, 999 and 1108 cc . . . . . . . . . . . . . . . . . . . . . . . . . . . . . . . . . . . . . 3.8 litres
1116, 1299/1301 and 1372 cc . . . . . . . . . . . . . . . . . . . . . . . . . . . . . . 4.1 litres
Transmission:
1301 cc Turbo ie . . . . . . . . . . . . . . . . . . . . . . . . . . . . . . . . . . . . . . . . . 2.9 litres
1372 cc Turbo ie . . . . . . . . . . . . . . . . . . . . . . . . . . . . . . . . . . . . . . . . . 2.0 litres
All other engines . . . . . . . . . . . . . . . . . . . . . . . . . . . . . . . . . . . . . . . . . 2.4 litres
Cooling system:
903, 999 and 1108 cc . . . . . . . . . . . . . . . . . . . . . . . . . . . . . . . . . . . . . 4.6 litres
1116 and 1299/1301 cc, non-catalyst 1372 cc ie . . . . . . . . . . . . . . . 6.2 litres
1372 cc ie with catalyst . . . . . . . . . . . . . . . . . . . . . . . . . . . . . . . . . . . 6.5 litres
1301 cc Turbo ie . . . . . . . . . . . . . . . . . . . . . . . . . . . . . . . . . . . . . . . . . 6.9 litres
1372 cc Turbo ie . . . . . . . . . . . . . . . . . . . . . . . . . . . . . . . . . . . . . . . . . 7.7 litres
Supplement: Revisions and information on later models 13•17
13
Page 143 of 303
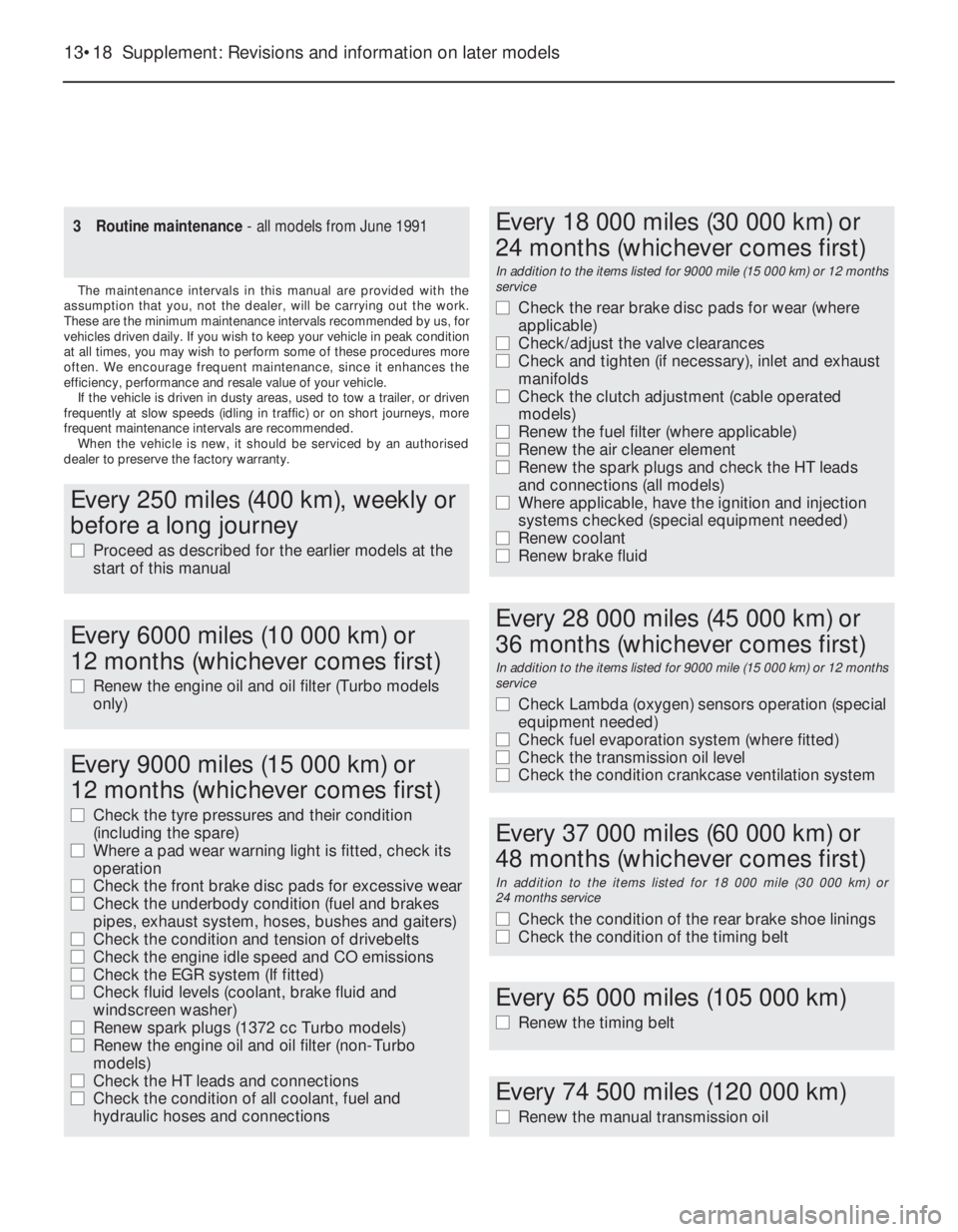
13•18 Supplement: Revisions and information on later models
Every 9000 miles (15 000 km) or
12 months (whichever comes first)
m mCheck the tyre pressures and their condition
(including the spare)
m mWhere a pad wear warning light is fitted, check its
operation
m mCheck the front brake disc pads for excessive wear
m mCheck the underbody condition (fuel and brakes
pipes, exhaust system, hoses, bushes and gaiters)
m mCheck the condition and tension of drivebelts
m mCheck the engine idle speed and CO emissions
m mCheck the EGR system (If fitted)
m mCheck fluid levels (coolant, brake fluid and
windscreen washer)
m mRenew spark plugs (1372 cc Turbo models)
m mRenew the engine oil and oil filter (non-Turbo
models)
m mCheck the HT leads and connections
m mCheck the condition of all coolant, fuel and
hydraulic hoses and connections
Every 18 000 miles (30 000 km) or
24 months (whichever comes first)
In addition to the items listed for 9000 mile (15 000 km) or 12 months
service
m mCheck the rear brake disc pads for wear (where
applicable)
m mCheck/adjust the valve clearances
m mCheck and tighten (if necessary), inlet and exhaust
manifolds
m mCheck the clutch adjustment (cable operated
models)
m mRenew the fuel filter (where applicable)
m mRenew the air cleaner element
m mRenew the spark plugs and check the HT leads
and connections (all models)
m mWhere applicable, have the ignition and injection
systems checked (special equipment needed)
m mRenew coolant
m mRenew brake fluid
Every 28 000 miles (45 000 km) or
36 months (whichever comes first)
In addition to the items listed for 9000 mile (15 000 km) or 12 months
service
m mCheck Lambda (oxygen) sensors operation (special
equipment needed)
m mCheck fuel evaporation system (where fitted)
m mCheck the transmission oil level
m mCheck the condition crankcase ventilation system
Every 37 000 miles (60 000 km) or
48 months (whichever comes first)
In addition to the items listed for 18 000 mile (30 000 km) or
24 months service
m mCheck the condition of the rear brake shoe linings
m mCheck the condition of the timing belt
Every 65 000 miles (105 000 km)
m
mRenew the timing belt
Every 74 500 miles (120 000 km)
m
mRenew the manual transmission oil
Every 250 miles (400 km), weekly or
before a long journey
m mProceed as described for the earlier models at the
start of this manual
Every 6000 miles (10 000 km) or
12 months (whichever comes first)
m mRenew the engine oil and oil filter (Turbo models
only)
3 Routine maintenance- all models from June 1991
The maintenance intervals in this manual are provided with the
assumption that you, not the dealer, will be carrying out the work.
These are the minimum maintenance intervals recommended by us, for
vehicles driven daily. If you wish to keep your vehicle in peak condition
at all times, you may wish to perform some of these procedures more
often. We encourage frequent maintenance, since it enhances the
efficiency, performance and resale value of your vehicle.
If the vehicle is driven in dusty areas, used to tow a trailer, or driven
frequently at slow speeds (idling in traffic) or on short journeys, more
frequent maintenance intervals are recommended.
When the vehicle is new, it should be serviced by an authorised
dealer to preserve the factory warranty.
Page 144 of 303
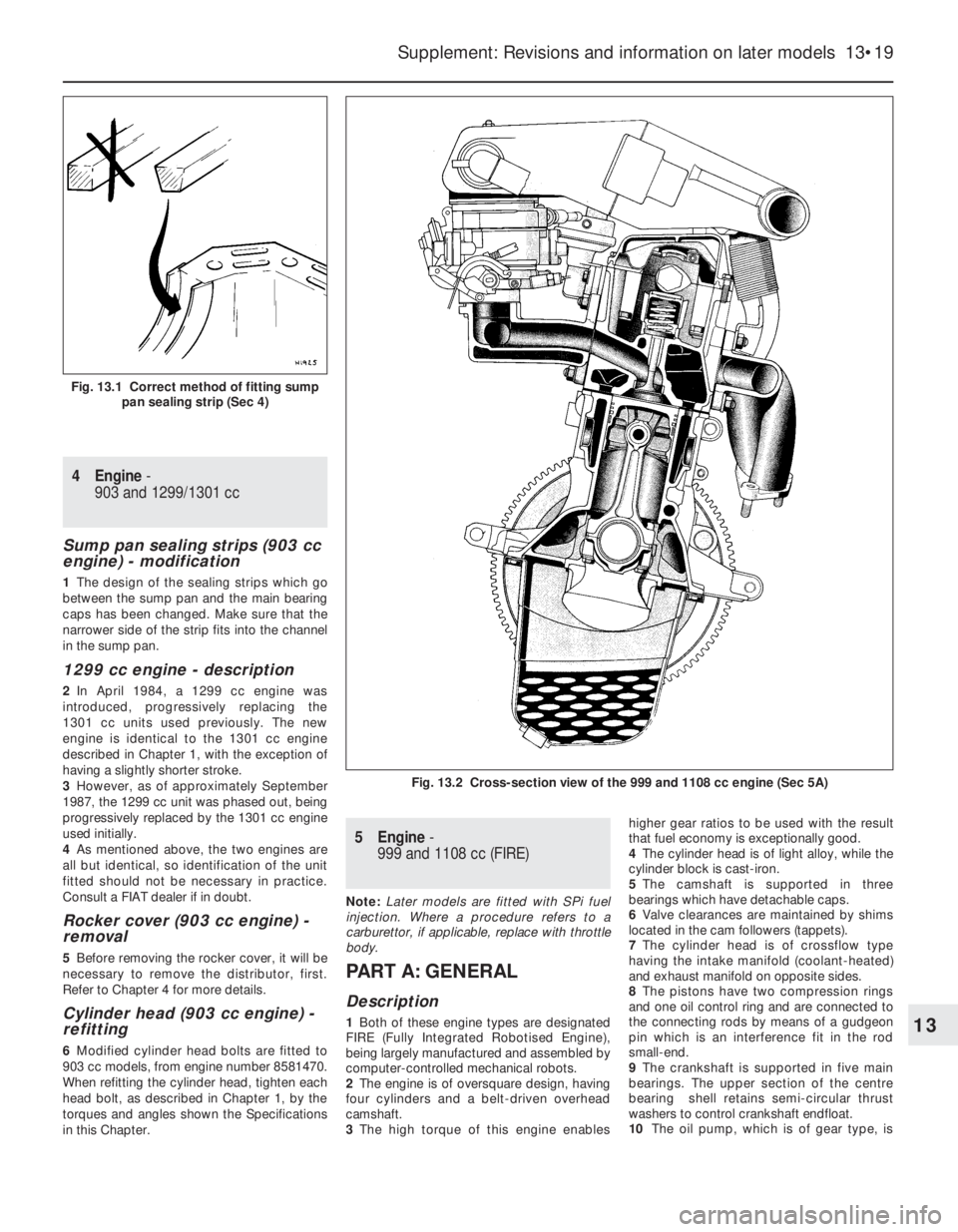
4 Engine-
903 and 1299/1301 cc
Sump pan sealing strips (903 cc
engine) - modification
1The design of the sealing strips which go
between the sump pan and the main bearing
caps has been changed. Make sure that the
narrower side of the strip fits into the channel
in the sump pan.
1299 cc engine - description
2In April 1984, a 1299 cc engine was
introduced, progressively replacing the
1301 cc units used previously. The new
engine is identical to the 1301 cc engine
described in Chapter 1, with the exception of
having a slightly shorter stroke.
3However, as of approximately September
1987, the 1299 cc unit was phased out, being
progressively replaced by the 1301 cc engine
used initially.
4As mentioned above, the two engines are
all but identical, so identification of the unit
fitted should not be necessary in practice.
Consult a FIAT dealer if in doubt.
Rocker cover (903 cc engine) -
removal
5Before removing the rocker cover, it will be
necessary to remove the distributor, first.
Refer to Chapter 4 for more details.
Cylinder head (903 cc engine) -
refitting
6Modified cylinder head bolts are fitted to
903 cc models, from engine number 8581470.
When refitting the cylinder head, tighten each
head bolt, as described in Chapter 1, by the
torques and angles shown the Specifications
in this Chapter.
5 Engine-
999 and 1108 cc (FIRE)
Note:Later models are fitted with SPi fuel
injection. Where a procedure refers to a
carburettor, if applicable, replace with throttle
body.
PART A: GENERAL
Description
1Both of these engine types are designated
FIRE (Fully Integrated Robotised Engine),
being largely manufactured and assembled by
computer-controlled mechanical robots.
2The engine is of oversquare design, having
four cylinders and a belt-driven overhead
camshaft.
3The high torque of this engine enableshigher gear ratios to be used with the result
that fuel economy is exceptionally good.
4The cylinder head is of light alloy, while the
cylinder block is cast-iron.
5The camshaft is supported in three
bearings which have detachable caps.
6Valve clearances are maintained by shims
located in the cam followers (tappets).
7The cylinder head is of crossflow type
having the intake manifold (coolant-heated)
and exhaust manifold on opposite sides.
8The pistons have two compression rings
and one oil control ring and are connected to
the connecting rods by means of a gudgeon
pin which is an interference fit in the rod
small-end.
9The crankshaft is supported in five main
bearings. The upper section of the centre
bearing shell retains semi-circular thrust
washers to control crankshaft endfloat.
10The oil pump, which is of gear type, is
Supplement: Revisions and information on later models 13•19
Fig. 13.2 Cross-section view of the 999 and 1108 cc engine (Sec 5A)
Fig. 13.1 Correct method of fitting sump
pan sealing strip (Sec 4)
13
Page 145 of 303
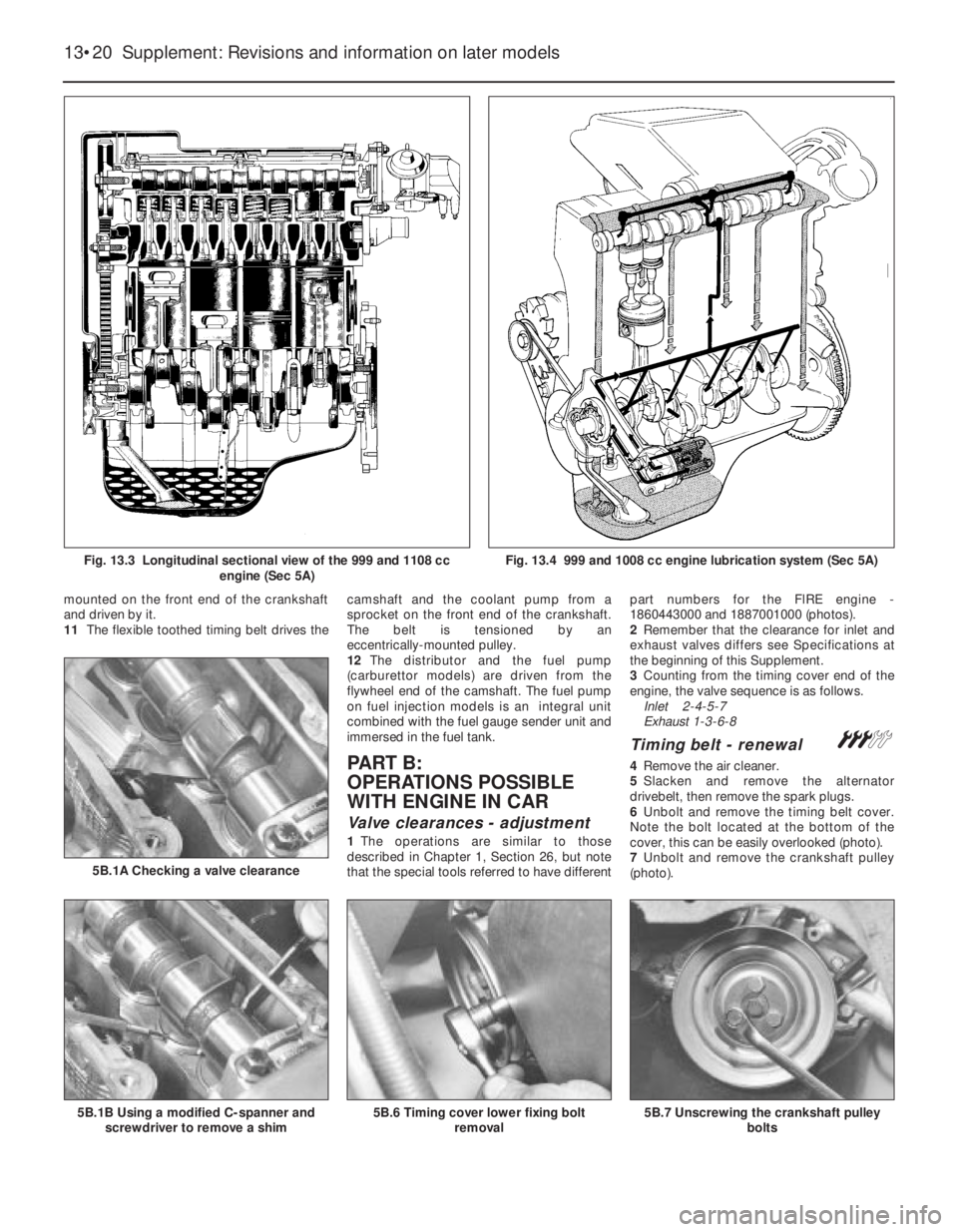
mounted on the front end of the crankshaft
and driven by it.
11The flexible toothed timing belt drives thecamshaft and the coolant pump from a
sprocket on the front end of the crankshaft.
The belt is tensioned by an
eccentrically-mounted pulley.
12The distributor and the fuel pump
(carburettor models) are driven from the
flywheel end of the camshaft. The fuel pump
on fuel injection models is an integral unit
combined with the fuel gauge sender unit and
immersed in the fuel tank.
PART B:
OPERATIONS POSSIBLE
WITH ENGINE IN CAR
Valve clearances - adjustment
1The operations are similar to those
described in Chapter 1, Section 26, but note
that the special tools referred to have differentpart numbers for the FlRE engine -
1860443000 and 1887001000 (photos).
2Remember that the clearance for inlet and
exhaust valves differs see Specifications at
the beginning of this Supplement.
3Counting from the timing cover end of the
engine, the valve sequence is as follows.
Inlet 2-4-5-7
Exhaust 1-3-6-8
Timing belt - renewal #
4Remove the air cleaner.
5Slacken and remove the alternator
drivebelt, then remove the spark plugs.
6Unbolt and remove the timing belt cover.
Note the bolt located at the bottom of the
cover, this can be easily overlooked (photo).
7Unbolt and remove the crankshaft pulley
(photo).
13•20 Supplement: Revisions and information on later models
5B.7 Unscrewing the crankshaft pulley
bolts5B.6 Timing cover lower fixing bolt
removal5B.1B Using a modified C-spanner and
screwdriver to remove a shim
5B.1A Checking a valve clearance
Fig. 13.3 Longitudinal sectional view of the 999 and 1108 cc
engine (Sec 5A)Fig. 13.4 999 and 1008 cc engine lubrication system (Sec 5A)
Page 146 of 303
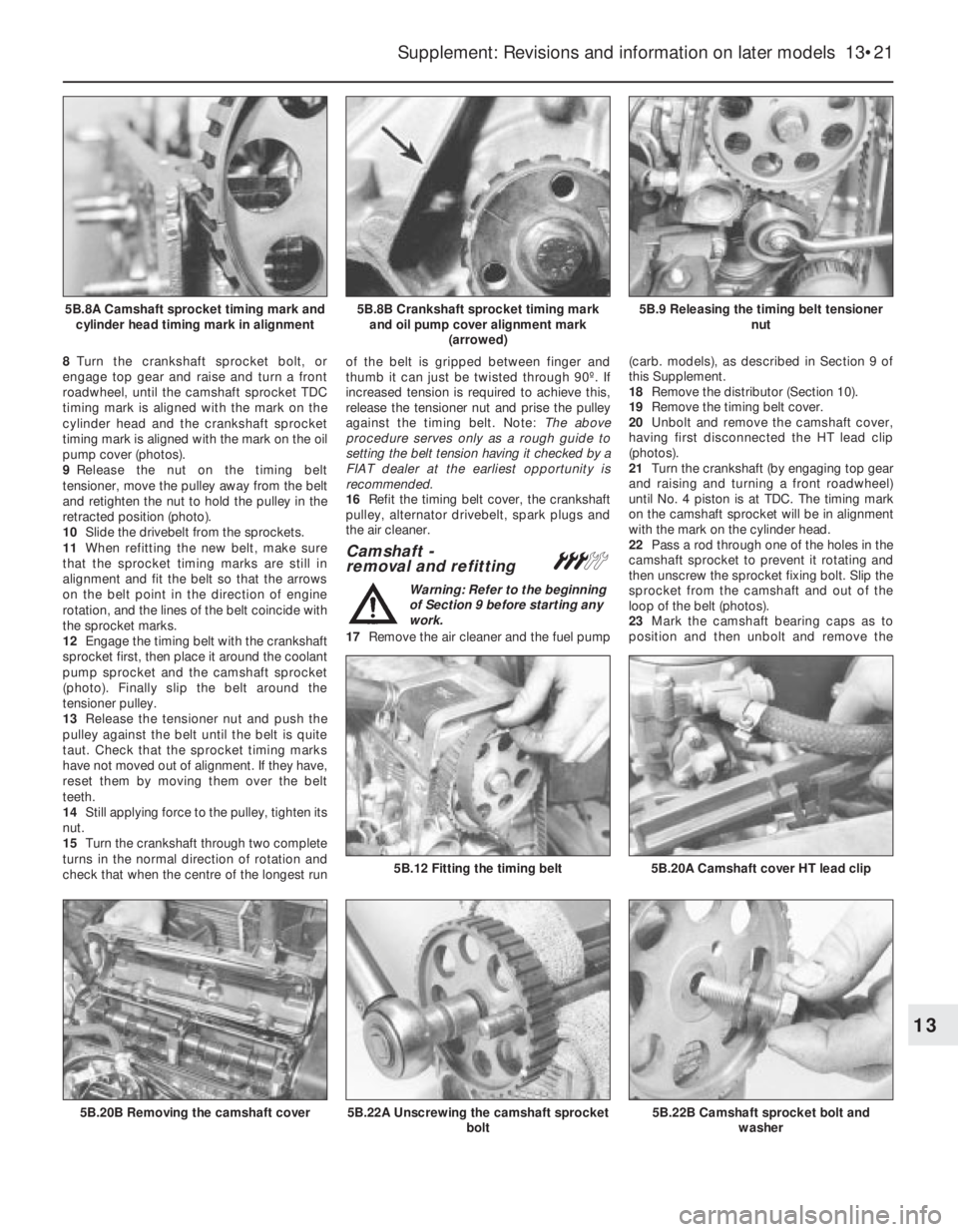
8Turn the crankshaft sprocket bolt, or
engage top gear and raise and turn a front
roadwheel, until the camshaft sprocket TDC
timing mark is aligned with the mark on the
cylinder head and the crankshaft sprocket
timing mark is aligned with the mark on the oil
pump cover (photos).
9Release the nut on the timing belt
tensioner, move the pulley away from the belt
and retighten the nut to hold the pulley in the
retracted position (photo).
10Slide the drivebelt from the sprockets.
11When refitting the new belt, make sure
that the sprocket timing marks are still in
alignment and fit the belt so that the arrows
on the belt point in the direction of engine
rotation, and the lines of the belt coincide with
the sprocket marks.
12Engage the timing belt with the crankshaft
sprocket first, then place it around the coolant
pump sprocket and the camshaft sprocket
(photo). Finally slip the belt around the
tensioner pulley.
13Release the tensioner nut and push the
pulley against the belt until the belt is quite
taut. Check that the sprocket timing marks
have not moved out of alignment. If they have,
reset them by moving them over the belt
teeth.
14Still applying force to the pulley, tighten its
nut.
15Turn the crankshaft through two complete
turns in the normal direction of rotation and
check that when the centre of the longest runof the belt is gripped between finger and
thumb it can just be twisted through 90º. If
increased tension is required to achieve this,
release the tensioner nut and prise the pulley
against the timing belt. Note: The above
procedure serves only as a rough guide to
setting the belt tension having it checked by a
FIAT dealer at the earliest opportunity is
recommended.
16Refit the timing belt cover, the crankshaft
pulley, alternator drivebelt, spark plugs and
the air cleaner.
Camshaft -
removal and refitting#
Warning: Refer to the beginning
of Section 9 before starting any
work.
17Remove the air cleaner and the fuel pump(carb. models), as described in Section 9 of
this Supplement.
18Remove the distributor (Section 10).
19Remove the timing belt cover.
20Unbolt and remove the camshaft cover,
having first disconnected the HT lead clip
(photos).
21Turn the crankshaft (by engaging top gear
and raising and turning a front roadwheel)
until No. 4 piston is at TDC. The timing mark
on the camshaft sprocket will be in alignment
with the mark on the cylinder head.
22Pass a rod through one of the holes in the
camshaft sprocket to prevent it rotating and
then unscrew the sprocket fixing bolt. Slip the
sprocket from the camshaft and out of the
loop of the belt (photos).
23Mark the camshaft bearing caps as to
position and then unbolt and remove the
Supplement: Revisions and information on later models 13•21
5B.9 Releasing the timing belt tensioner
nut5B.8B Crankshaft sprocket timing mark
and oil pump cover alignment mark
(arrowed)5B.8A Camshaft sprocket timing mark and
cylinder head timing mark in alignment
5B.22B Camshaft sprocket bolt and
washer5B.22A Unscrewing the camshaft sprocket
bolt
5B.20A Camshaft cover HT lead clip5B.12 Fitting the timing belt
5B.20B Removing the camshaft cover
13
Page 147 of 303
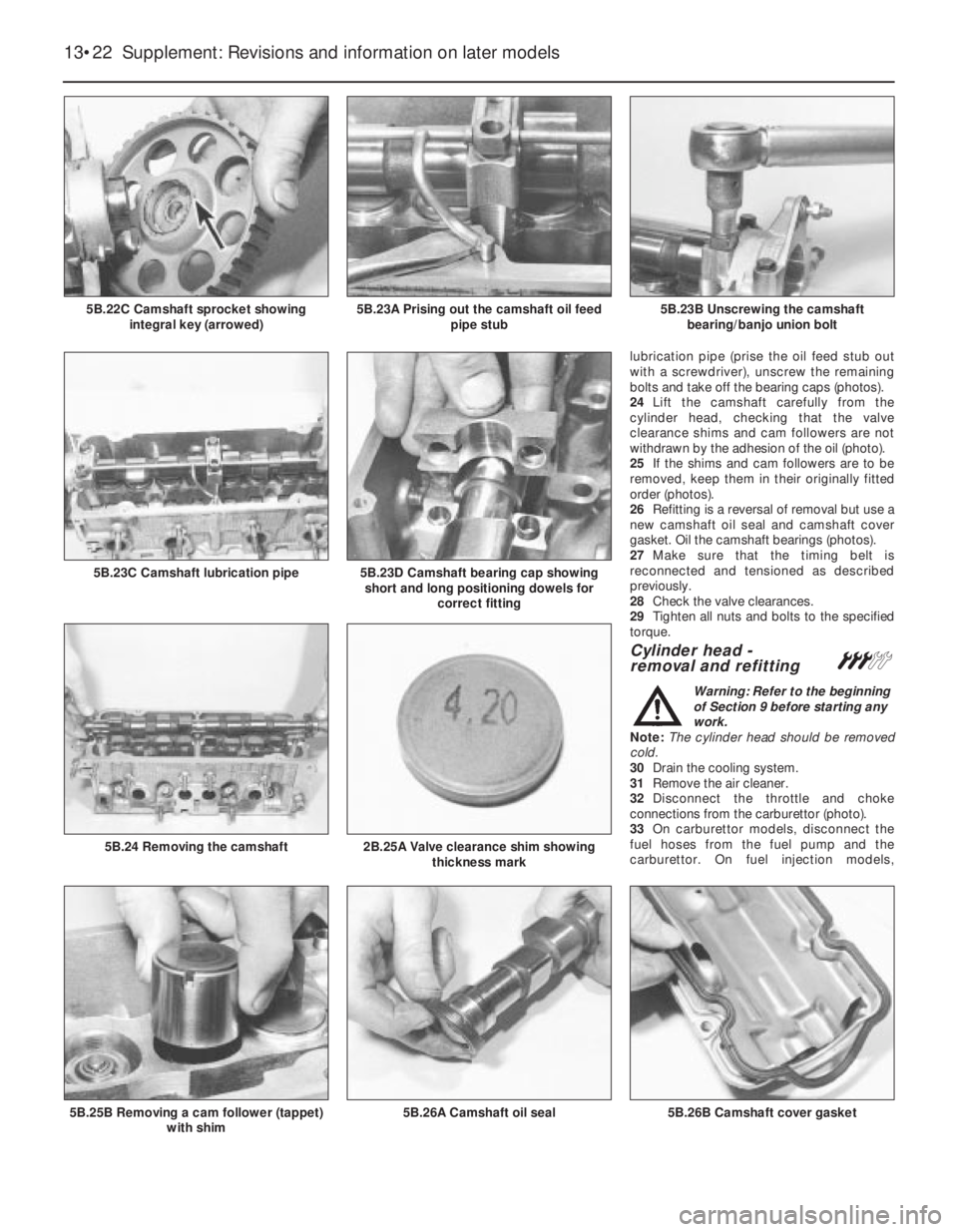
lubrication pipe (prise the oil feed stub out
with a screwdriver), unscrew the remaining
bolts and take off the bearing caps (photos).
24Lift the camshaft carefully from the
cylinder head, checking that the valve
clearance shims and cam followers are not
withdrawn by the adhesion of the oil (photo).
25If the shims and cam followers are to be
removed, keep them in their originally fitted
order (photos).
26Refitting is a reversal of removal but use a
new camshaft oil seal and camshaft cover
gasket. Oil the camshaft bearings (photos).
27Make sure that the timing belt is
reconnected and tensioned as described
previously.
28Check the valve clearances.
29Tighten all nuts and bolts to the specified
torque.
Cylinder head -
removal and refitting#
Warning: Refer to the beginning
of Section 9 before starting any
work.
Note: The cylinder head should be removed
cold.
30Drain the cooling system.
31Remove the air cleaner.
32Disconnect the throttle and choke
connections from the carburettor (photo).
33On carburettor models, disconnect the
fuel hoses from the fuel pump and the
carburettor. On fuel injection models,
13•22 Supplement: Revisions and information on later models
5B.26B Camshaft cover gasket5B.26A Camshaft oil seal5B.25B Removing a cam follower (tappet)
with shim
2B.25A Valve clearance shim showing
thickness mark5B.24 Removing the camshaft
5B.23D Camshaft bearing cap showing
short and long positioning dowels for
correct fitting5B.23C Camshaft lubrication pipe
5B.23B Unscrewing the camshaft
bearing/banjo union bolt5B.23A Prising out the camshaft oil feed
pipe stub5B.22C Camshaft sprocket showing
integral key (arrowed)
Page 148 of 303
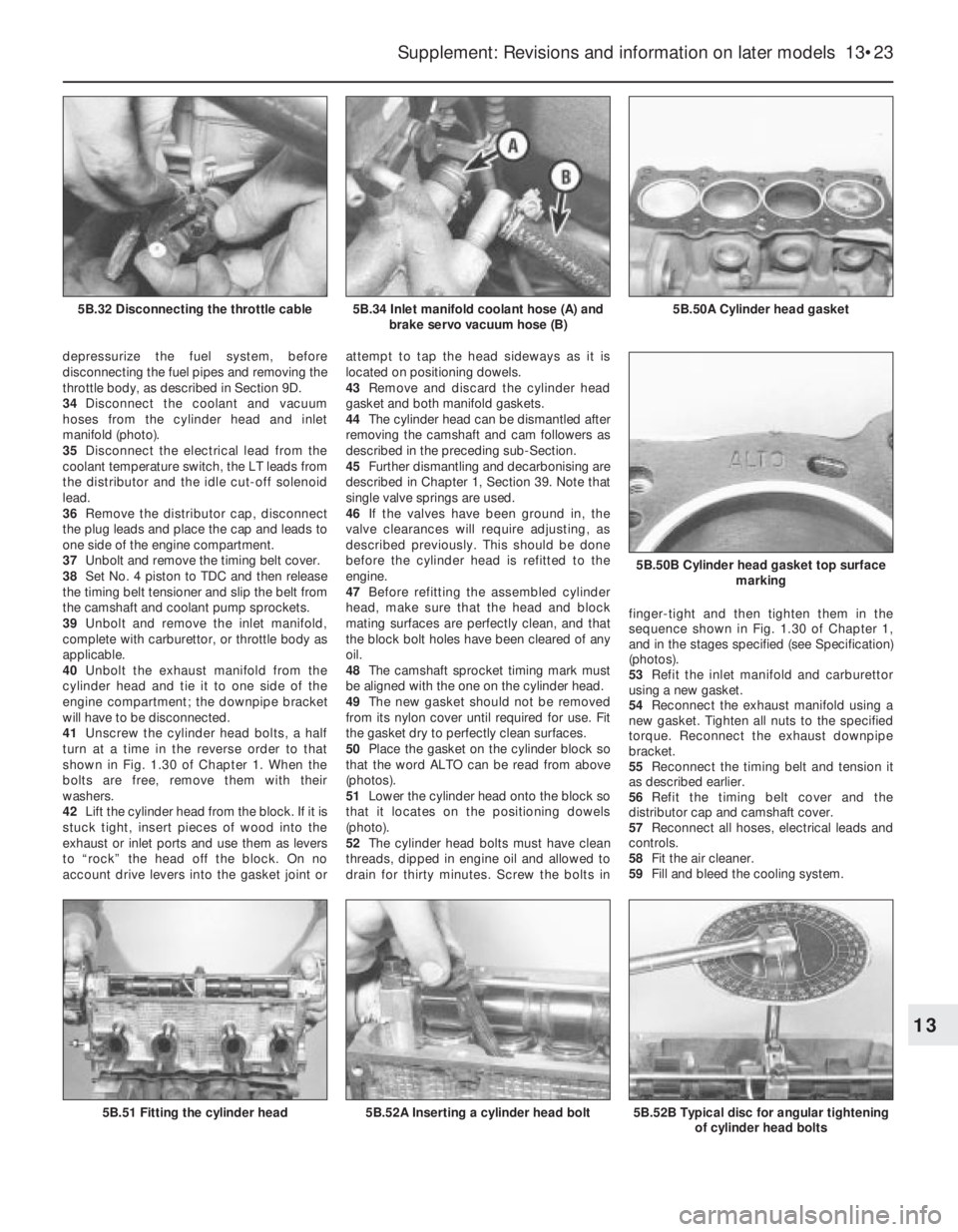
depressurize the fuel system, before
disconnecting the fuel pipes and removing the
throttle body, as described in Section 9D.
34Disconnect the coolant and vacuum
hoses from the cylinder head and inlet
manifold (photo).
35Disconnect the electrical lead from the
coolant temperature switch, the LT leads from
the distributor and the idle cut-off solenoid
lead.
36Remove the distributor cap, disconnect
the plug leads and place the cap and leads to
one side of the engine compartment.
37Unbolt and remove the timing belt cover.
38Set No. 4 piston to TDC and then release
the timing belt tensioner and slip the belt from
the camshaft and coolant pump sprockets.
39Unbolt and remove the inlet manifold,
complete with carburettor, or throttle body as
applicable.
40Unbolt the exhaust manifold from the
cylinder head and tie it to one side of the
engine compartment; the downpipe bracket
will have to be disconnected.
41Unscrew the cylinder head bolts, a half
turn at a time in the reverse order to that
shown in Fig. 1.30 of Chapter 1. When the
bolts are free, remove them with their
washers.
42Lift the cylinder head from the block. If it is
stuck tight, insert pieces of wood into the
exhaust or inlet ports and use them as levers
to “rock” the head off the block. On no
account drive levers into the gasket joint orattempt to tap the head sideways as it is
located on positioning dowels.
43Remove and discard the cylinder head
gasket and both manifold gaskets.
44The cylinder head can be dismantled after
removing the camshaft and cam followers as
described in the preceding sub-Section.
45Further dismantling and decarbonising are
described in Chapter 1, Section 39. Note that
single valve springs are used.
46If the valves have been ground in, the
valve clearances will require adjusting, as
described previously. This should be done
before the cylinder head is refitted to the
engine.
47Before refitting the assembled cylinder
head, make sure that the head and block
mating surfaces are perfectly clean, and that
the block bolt holes have been cleared of any
oil.
48The camshaft sprocket timing mark must
be aligned with the one on the cylinder head.
49The new gasket should not be removed
from its nylon cover until required for use. Fit
the gasket dry to perfectly clean surfaces.
50Place the gasket on the cylinder block so
that the word ALTO can be read from above
(photos).
51Lower the cylinder head onto the block so
that it locates on the positioning dowels
(photo).
52The cylinder head bolts must have clean
threads, dipped in engine oil and allowed to
drain for thirty minutes. Screw the bolts infinger-tight and then tighten them in the
sequence shown in Fig. 1.30 of Chapter 1,
and in the stages specified (see Specification)
(photos).
53Refit the inlet manifold and carburettor
using a new gasket.
54Reconnect the exhaust manifold using a
new gasket. Tighten all nuts to the specified
torque. Reconnect the exhaust downpipe
bracket.
55Reconnect the timing belt and tension it
as described earlier.
56Refit the timing belt cover and the
distributor cap and camshaft cover.
57Reconnect all hoses, electrical leads and
controls.
58Fit the air cleaner.
59Fill and bleed the cooling system.
Supplement: Revisions and information on later models 13•23
5B.50A Cylinder head gasket5B.34 Inlet manifold coolant hose (A) and
brake servo vacuum hose (B)5B.32 Disconnecting the throttle cable
5B.52B Typical disc for angular tightening
of cylinder head bolts
5B.50B Cylinder head gasket top surface
marking
5B.52A Inserting a cylinder head bolt5B.51 Fitting the cylinder head
13
Page 149 of 303
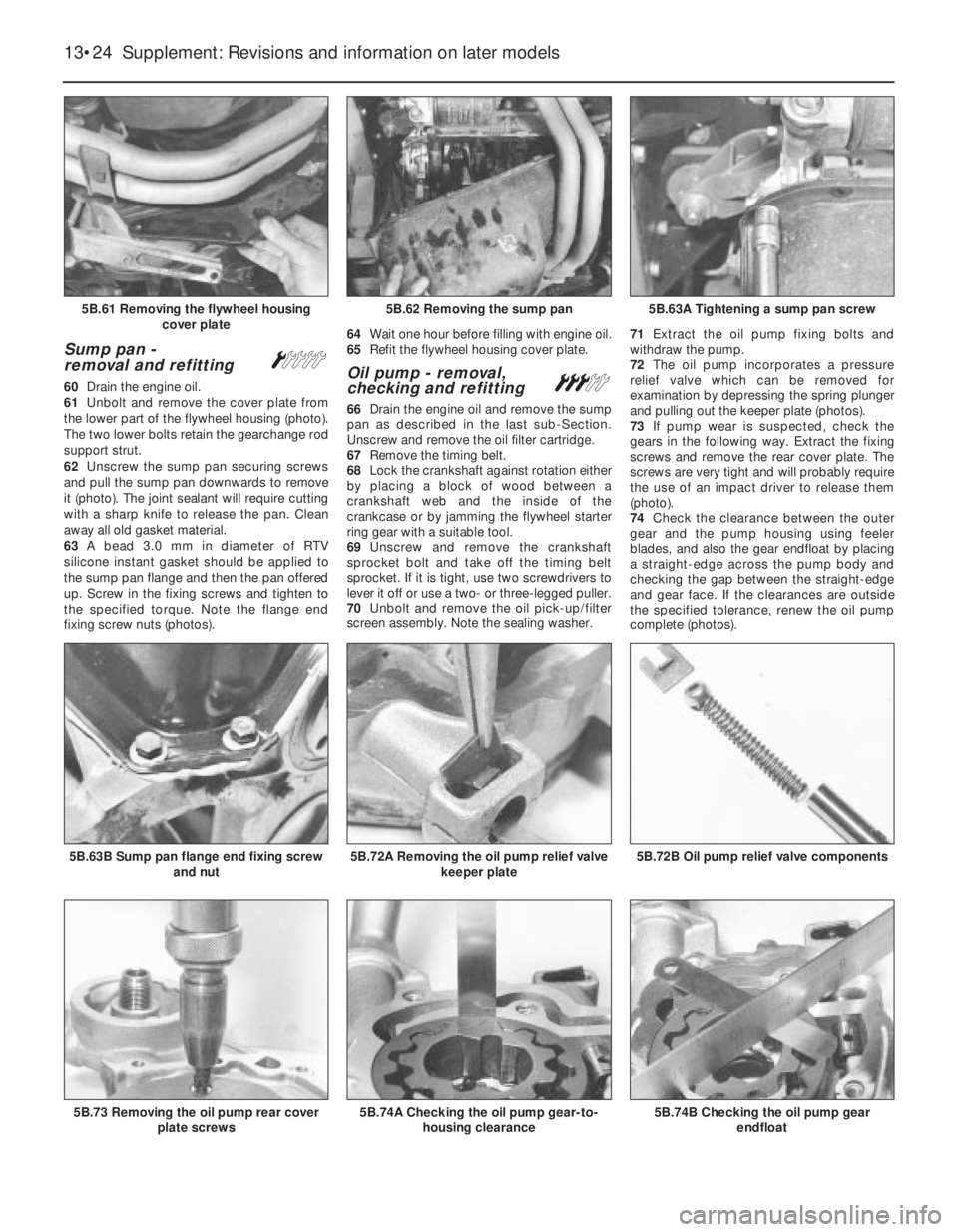
Sump pan -
removal and refitting Á
60Drain the engine oil.
61Unbolt and remove the cover plate from
the lower part of the flywheel housing (photo).
The two lower bolts retain the gearchange rod
support strut.
62Unscrew the sump pan securing screws
and pull the sump pan downwards to remove
it (photo). The joint sealant will require cutting
with a sharp knife to release the pan. Clean
away all old gasket material.
63A bead 3.0 mm in diameter of RTV
silicone instant gasket should be applied to
the sump pan flange and then the pan offered
up. Screw in the fixing screws and tighten to
the specified torque. Note the flange end
fixing screw nuts (photos).64Wait one hour before filling with engine oil.
65Refit the flywheel housing cover plate.Oil pump - removal,
checking and refitting#
66Drain the engine oil and remove the sump
pan as described in the last sub-Section.
Unscrew and remove the oil filter cartridge.
67Remove the timing belt.
68Lock the crankshaft against rotation either
by placing a block of wood between a
crankshaft web and the inside of the
crankcase or by jamming the flywheel starter
ring gear with a suitable tool.
69Unscrew and remove the crankshaft
sprocket bolt and take off the timing belt
sprocket. If it is tight, use two screwdrivers to
lever it off or use a two- or three-legged puller.
70Unbolt and remove the oil pick-up/filter
screen assembly. Note the sealing washer.71Extract the oil pump fixing bolts and
withdraw the pump.
72The oil pump incorporates a pressure
relief valve which can be removed for
examination by depressing the spring plunger
and pulling out the keeper plate (photos).
73If pump wear is suspected, check the
gears in the following way. Extract the fixing
screws and remove the rear cover plate. The
screws are very tight and will probably require
the use of an impact driver to release them
(photo).
74Check the clearance between the outer
gear and the pump housing using feeler
blades, and also the gear endfloat by placing
a straight-edge across the pump body and
checking the gap between the straight-edge
and gear face. If the clearances are outside
the specified tolerance, renew the oil pump
complete (photos).
13•24 Supplement: Revisions and information on later models
5B.74B Checking the oil pump gear
endfloat5B.74A Checking the oil pump gear-to-
housing clearance5B.73 Removing the oil pump rear cover
plate screws
5B.72B Oil pump relief valve components5B.72A Removing the oil pump relief valve
keeper plate5B.63B Sump pan flange end fixing screw
and nut
5B.63A Tightening a sump pan screw5B.62 Removing the sump pan5B.61 Removing the flywheel housing
cover plate
Page 150 of 303
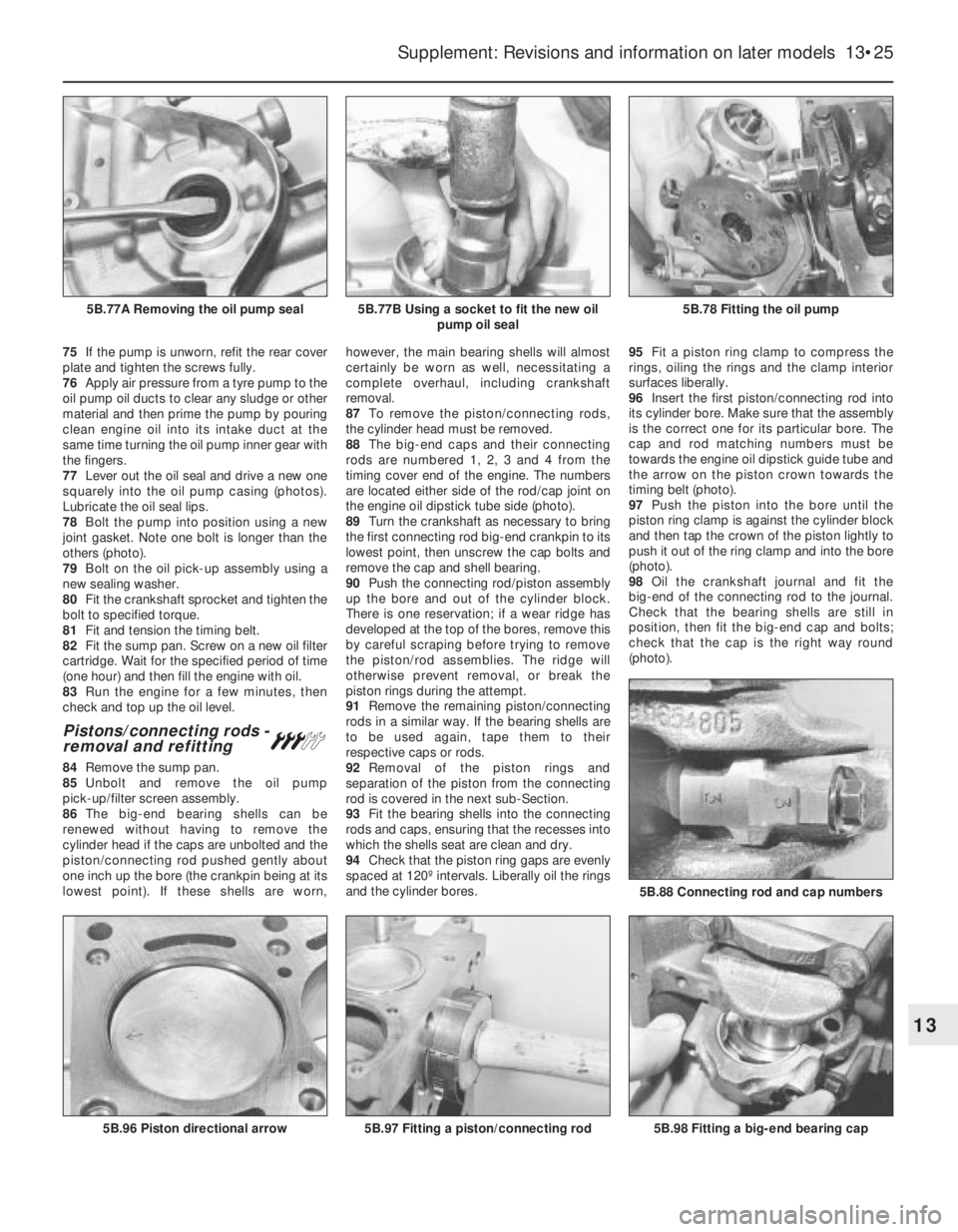
75If the pump is unworn, refit the rear cover
plate and tighten the screws fully.
76Apply air pressure from a tyre pump to the
oil pump oil ducts to clear any sludge or other
material and then prime the pump by pouring
clean engine oil into its intake duct at the
same time turning the oil pump inner gear with
the fingers.
77Lever out the oil seal and drive a new one
squarely into the oil pump casing (photos).
Lubricate the oil seal lips.
78Bolt the pump into position using a new
joint gasket. Note one bolt is longer than the
others (photo).
79Bolt on the oil pick-up assembly using a
new sealing washer.
80Fit the crankshaft sprocket and tighten the
bolt to specified torque.
81Fit and tension the timing belt.
82Fit the sump pan. Screw on a new oil filter
cartridge. Wait for the specified period of time
(one hour) and then fill the engine with oil.
83Run the engine for a few minutes, then
check and top up the oil level.
Pistons/connecting rods -
removal and refitting#
84Remove the sump pan.
85Unbolt and remove the oil pump
pick-up/filter screen assembly.
86The big-end bearing shells can be
renewed without having to remove the
cylinder head if the caps are unbolted and the
piston/connecting rod pushed gently about
one inch up the bore (the crankpin being at its
lowest point). If these shells are worn,however, the main bearing shells will almost
certainly be worn as well, necessitating a
complete overhaul, including crankshaft
removal.
87To remove the piston/connecting rods,
the cylinder head must be removed.
88The big-end caps and their connecting
rods are numbered 1, 2, 3 and 4 from the
timing cover end of the engine. The numbers
are located either side of the rod/cap joint on
the engine oil dipstick tube side (photo).
89Turn the crankshaft as necessary to bring
the first connecting rod big-end crankpin to its
lowest point, then unscrew the cap bolts and
remove the cap and shell bearing.
90Push the connecting rod/piston assembly
up the bore and out of the cylinder block.
There is one reservation; if a wear ridge has
developed at the top of the bores, remove this
by careful scraping before trying to remove
the piston/rod assemblies. The ridge will
otherwise prevent removal, or break the
piston rings during the attempt.
91Remove the remaining piston/connecting
rods in a similar way. If the bearing shells are
to be used again, tape them to their
respective caps or rods.
92Removal of the piston rings and
separation of the piston from the connecting
rod is covered in the next sub-Section.
93Fit the bearing shells into the connecting
rods and caps, ensuring that the recesses into
which the shells seat are clean and dry.
94Check that the piston ring gaps are evenly
spaced at 120º intervals. Liberally oil the rings
and the cylinder bores.95Fit a piston ring clamp to compress the
rings, oiling the rings and the clamp interior
surfaces liberally.
96Insert the first piston/connecting rod into
its cylinder bore. Make sure that the assembly
is the correct one for its particular bore. The
cap and rod matching numbers must be
towards the engine oil dipstick guide tube and
the arrow on the piston crown towards the
timing belt (photo).
97Push the piston into the bore until the
piston ring clamp is against the cylinder block
and then tap the crown of the piston lightly to
push it out of the ring clamp and into the bore
(photo).
98Oil the crankshaft journal and fit the
big-end of the connecting rod to the journal.
Check that the bearing shells are still in
position, then fit the big-end cap and bolts;
check that the cap is the right way round
(photo).
Supplement: Revisions and information on later models 13•25
5B.78 Fitting the oil pump5B.77B Using a socket to fit the new oil
pump oil seal5B.77A Removing the oil pump seal
5B.98 Fitting a big-end bearing cap
5B.88 Connecting rod and cap numbers
5B.97 Fitting a piston/connecting rod5B.96 Piston directional arrow
13