FIAT UNO 1983 Service Manual Online
Manufacturer: FIAT, Model Year: 1983, Model line: UNO, Model: FIAT UNO 1983Pages: 303, PDF Size: 10.36 MB
Page 81 of 303
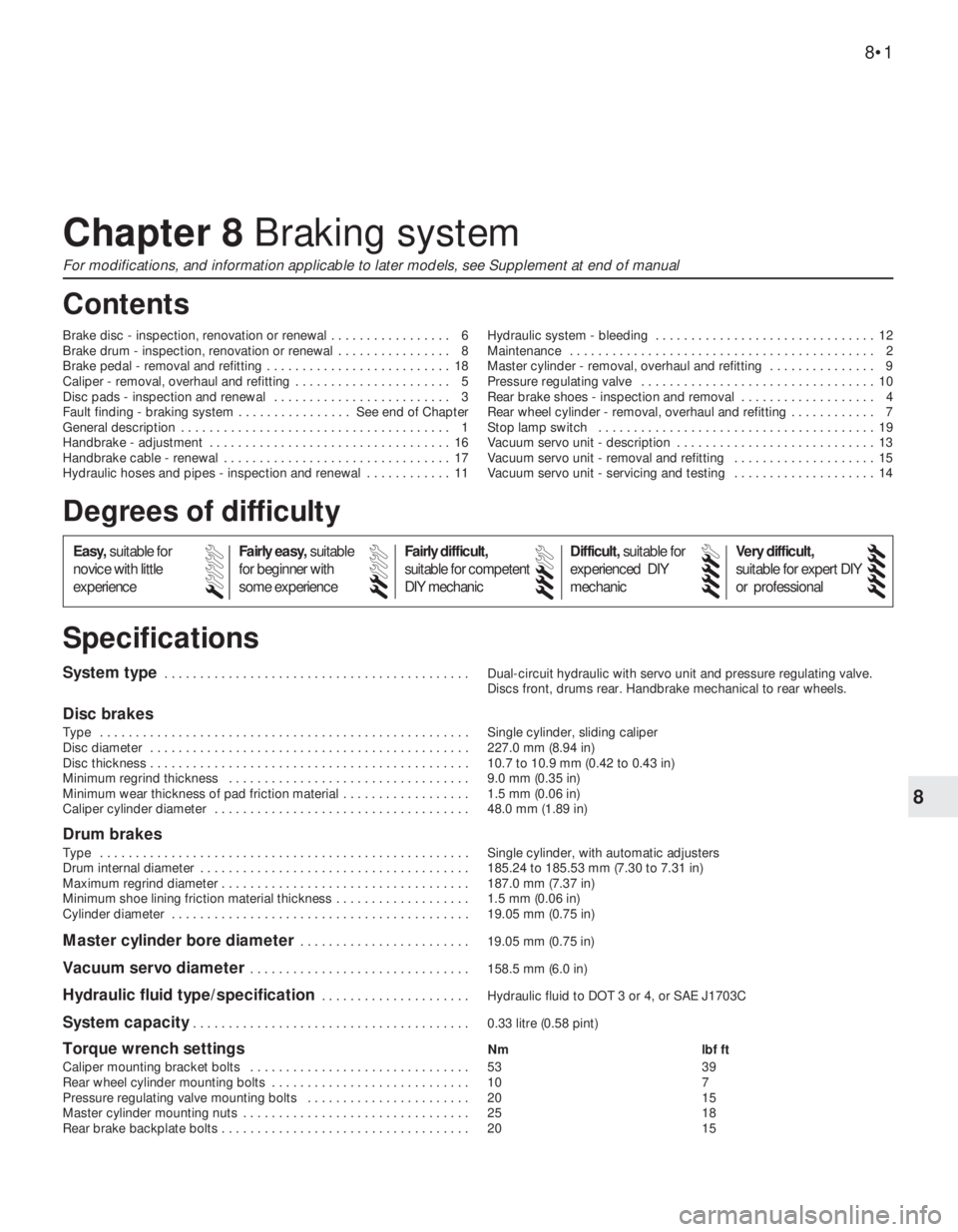
8
System type . . . . . . . . . . . . . . . . . . . . . . . . . . . . . . . . . . . . . . . . . . . Dual-circuit hydraulic with servo unit and pressure regulating valve.
Discs front, drums rear. Handbrake mechanical to rear wheels.
Disc brakes
Type . . . . . . . . . . . . . . . . . . . . . . . . . . . . . . . . . . . . . . . . . . . . . . . . . . . . Single cylinder, sliding caliper
Disc diameter . . . . . . . . . . . . . . . . . . . . . . . . . . . . . . . . . . . . . . . . . . . . . 227.0 mm (8.94 in)
Disc thickness . . . . . . . . . . . . . . . . . . . . . . . . . . . . . . . . . . . . . . . . . . . . . 10.7 to 10.9 mm (0.42 to 0.43 in)
Minimum regrind thickness . . . . . . . . . . . . . . . . . . . . . . . . . . . . . . . . . . 9.0 mm (0.35 in)
Minimum wear thickness of pad friction material . . . . . . . . . . . . . . . . . . 1.5 mm (0.06 in)
Caliper cylinder diameter . . . . . . . . . . . . . . . . . . . . . . . . . . . . . . . . . . . . 48.0 mm (1.89 in)
Drum brakes
Type . . . . . . . . . . . . . . . . . . . . . . . . . . . . . . . . . . . . . . . . . . . . . . . . . . . . Single cylinder, with automatic adjusters
Drum internal diameter . . . . . . . . . . . . . . . . . . . . . . . . . . . . . . . . . . . . . . 185.24 to 185.53 mm (7.30 to 7.31 in)
Maximum regrind diameter . . . . . . . . . . . . . . . . . . . . . . . . . . . . . . . . . . . 187.0 mm (7.37 in)
Minimum shoe lining friction material thickness . . . . . . . . . . . . . . . . . . . 1.5 mm (0.06 in)
Cylinder diameter . . . . . . . . . . . . . . . . . . . . . . . . . . . . . . . . . . . . . . . . . . 19.05 mm (0.75 in)
Master cylinder bore diameter . . . . . . . . . . . . . . . . . . . . . . . . 19.05 mm (0.75 in)
Vacuum servo diameter . . . . . . . . . . . . . . . . . . . . . . . . . . . . . . . 158.5 mm (6.0 in)
Hydraulic fluid type/specification . . . . . . . . . . . . . . . . . . . . . Hydraulic fluid to DOT 3 or 4, or SAE J1703C
System capacity . . . . . . . . . . . . . . . . . . . . . . . . . . . . . . . . . . . . . . . 0.33 litre (0.58 pint)
Torque wrench settingsNm lbf ft
Caliper mounting bracket bolts . . . . . . . . . . . . . . . . . . . . . . . . . . . . . . . 53 39
Rear wheel cylinder mounting bolts . . . . . . . . . . . . . . . . . . . . . . . . . . . . 10 7
Pressure regulating valve mounting bolts . . . . . . . . . . . . . . . . . . . . . . . 20 15
Master cylinder mounting nuts . . . . . . . . . . . . . . . . . . . . . . . . . . . . . . . . 25 18
Rear brake backplate bolts . . . . . . . . . . . . . . . . . . . . . . . . . . . . . . . . . . . 20 15
Chapter 8 Braking system
For modifications, and information applicable to later models, see Supplement at end of manual
Brake disc - inspection, renovation or renewal . . . . . . . . . . . . . . . . . 6
Brake drum - inspection, renovation or renewal . . . . . . . . . . . . . . . . 8
Brake pedal - removal and refitting . . . . . . . . . . . . . . . . . . . . . . . . . . 18
Caliper - removal, overhaul and refitting . . . . . . . . . . . . . . . . . . . . . . 5
Disc pads - inspection and renewal . . . . . . . . . . . . . . . . . . . . . . . . . 3
Fault finding - braking system . . . . . . . . . . . . . . . . See end of Chapter
General description . . . . . . . . . . . . . . . . . . . . . . . . . . . . . . . . . . . . . . 1
Handbrake - adjustment . . . . . . . . . . . . . . . . . . . . . . . . . . . . . . . . . . 16
Handbrake cable - renewal . . . . . . . . . . . . . . . . . . . . . . . . . . . . . . . . 17
Hydraulic hoses and pipes - inspection and renewal . . . . . . . . . . . . 11Hydraulic system - bleeding . . . . . . . . . . . . . . . . . . . . . . . . . . . . . . . 12
Maintenance . . . . . . . . . . . . . . . . . . . . . . . . . . . . . . . . . . . . . . . . . . . 2
Master cylinder - removal, overhaul and refitting . . . . . . . . . . . . . . . 9
Pressure regulating valve . . . . . . . . . . . . . . . . . . . . . . . . . . . . . . . . . 10
Rear brake shoes - inspection and removal . . . . . . . . . . . . . . . . . . . 4
Rear wheel cylinder - removal, overhaul and refitting . . . . . . . . . . . . 7
Stop lamp switch . . . . . . . . . . . . . . . . . . . . . . . . . . . . . . . . . . . . . . . 19
Vacuum servo unit - description . . . . . . . . . . . . . . . . . . . . . . . . . . . . 13
Vacuum servo unit - removal and refitting . . . . . . . . . . . . . . . . . . . . 15
Vacuum servo unit - servicing and testing . . . . . . . . . . . . . . . . . . . . 14
8•1
Specifications Contents
Easy,suitable for
novice with little
experienceFairly easy,suitable
for beginner with
some experienceFairly difficult,
suitable for competent
DIY mechanic
Difficult,suitable for
experienced DIY
mechanicVery difficult,
suitable for expert DIY
or professional
Degrees of difficulty
54321
Page 82 of 303
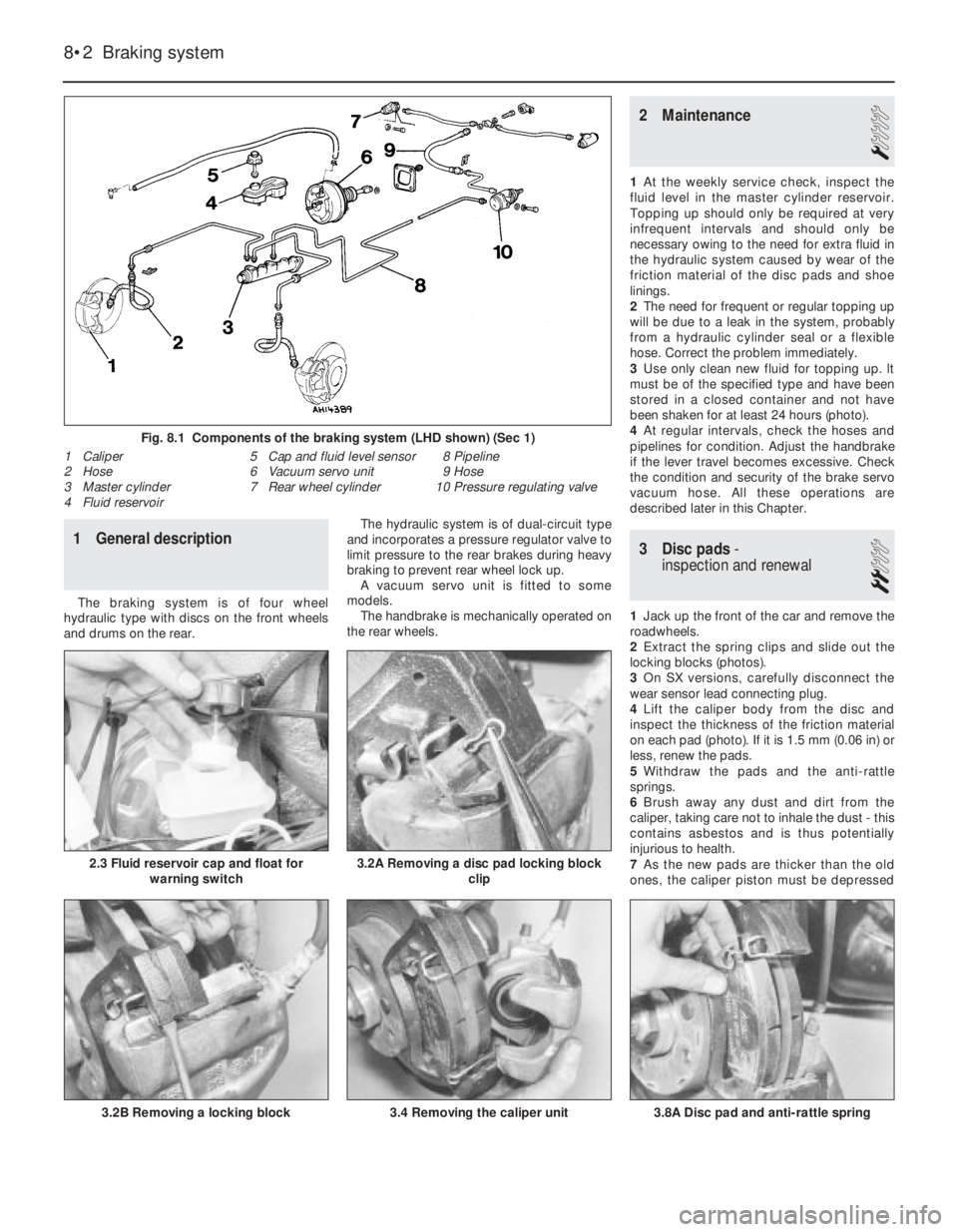
3.4 Removing the caliper unit
1 General description
The braking system is of four wheel
hydraulic type with discs on the front wheels
and drums on the rear.The hydraulic system is of dual-circuit type
and incorporates a pressure regulator valve to
limit pressure to the rear brakes during heavy
braking to prevent rear wheel lock up.
A vacuum servo unit is fitted to some
models.
The handbrake is mechanically operated on
the rear wheels.
2 Maintenance
1
1At the weekly service check, inspect the
fluid level in the master cylinder reservoir.
Topping up should only be required at very
infrequent intervals and should only be
necessary owing to the need for extra fluid in
the hydraulic system caused by wear of the
friction material of the disc pads and shoe
linings.
2The need for frequent or regular topping up
will be due to a leak in the system, probably
from a hydraulic cylinder seal or a flexible
hose. Correct the problem immediately.
3Use only clean new fluid for topping up. lt
must be of the specified type and have been
stored in a closed container and not have
been shaken for at least 24 hours (photo).
4At regular intervals, check the hoses and
pipelines for condition. Adjust the handbrake
if the lever travel becomes excessive. Check
the condition and security of the brake servo
vacuum hose. All these operations are
described later in this Chapter.
3 Disc pads-
inspection and renewal
2
1Jack up the front of the car and remove the
roadwheels.
2Extract the spring clips and slide out the
locking blocks (photos).
3On SX versions, carefully disconnect the
wear sensor lead connecting plug.
4Lift the caliper body from the disc and
inspect the thickness of the friction material
on each pad (photo). If it is 1.5 mm (0.06 in) or
less, renew the pads.
5Withdraw the pads and the anti-rattle
springs.
6Brush away any dust and dirt from the
caliper, taking care not to inhale the dust - this
contains asbestos and is thus potentially
injurious to health.
7As the new pads are thicker than the old
ones, the caliper piston must be depressed
8•2 Braking system
3.8A Disc pad and anti-rattle spring
Fig. 8.1 Components of the braking system (LHD shown) (Sec 1)
1 Caliper
2 Hose
3 Master cylinder
4 Fluid reservoir5 Cap and fluid level sensor
6 Vacuum servo unit
7 Rear wheel cylinder8 Pipeline
9 Hose
10 Pressure regulating valve
3.2B Removing a locking block
3.2A Removing a disc pad locking block
clip2.3 Fluid reservoir cap and float for
warning switch
Page 83 of 303
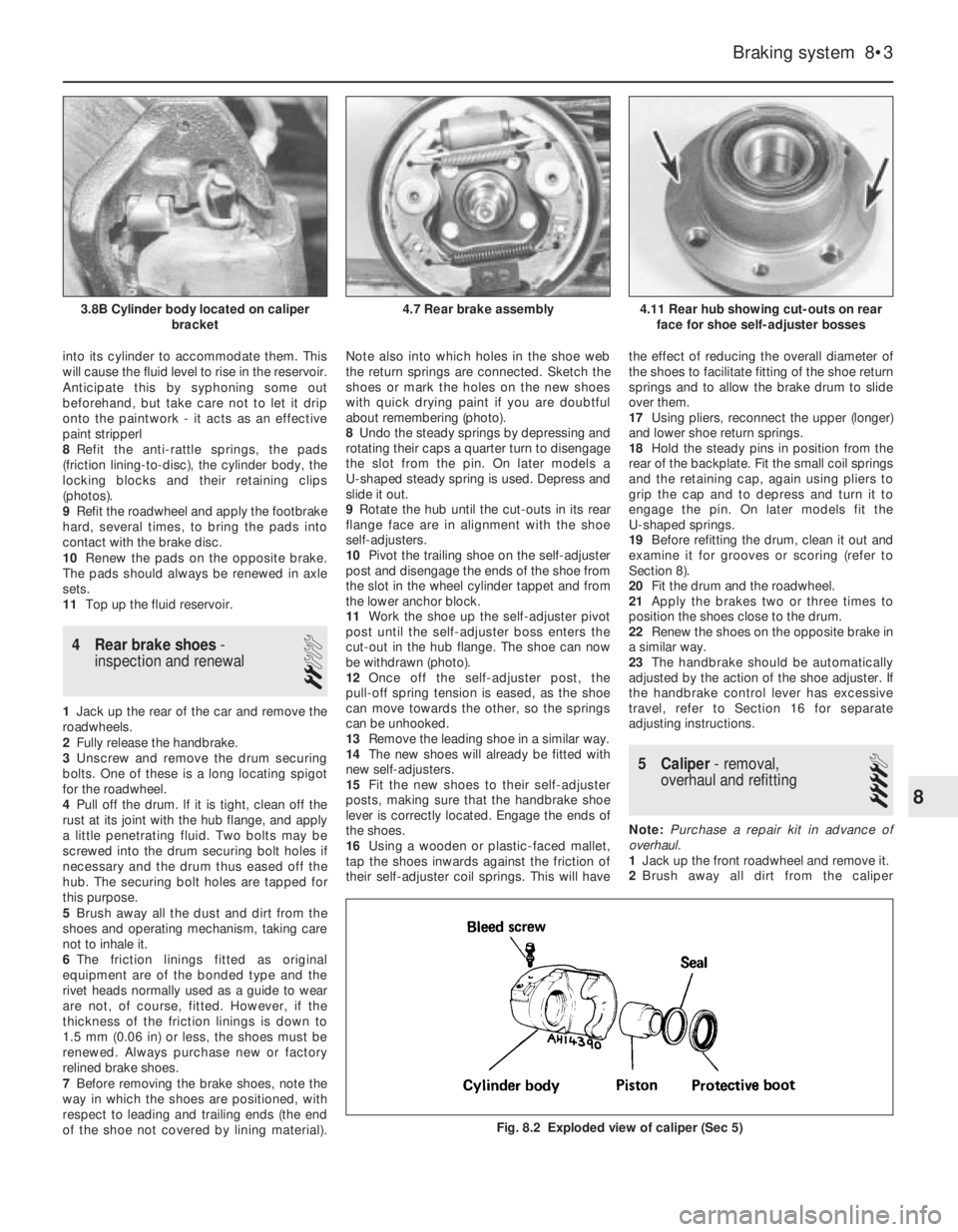
into its cylinder to accommodate them. This
will cause the fluid level to rise in the reservoir.
Anticipate this by syphoning some out
beforehand, but take care not to let it drip
onto the paintwork - it acts as an effective
paint stripperl
8Refit the anti-rattle springs, the pads
(friction lining-to-disc), the cylinder body, the
locking blocks and their retaining clips
(photos).
9Refit the roadwheel and apply the footbrake
hard, several times, to bring the pads into
contact with the brake disc.
10Renew the pads on the opposite brake.
The pads should always be renewed in axle
sets.
11Top up the fluid reservoir.
4 Rear brake shoes-
inspection and renewal
2
1Jack up the rear of the car and remove the
roadwheels.
2Fully release the handbrake.
3Unscrew and remove the drum securing
bolts. One of these is a long locating spigot
for the roadwheel.
4Pull off the drum. lf it is tight, clean off the
rust at its joint with the hub flange, and apply
a little penetrating fluid. Two bolts may be
screwed into the drum securing bolt holes if
necessary and the drum thus eased off the
hub. The securing bolt holes are tapped for
this purpose.
5Brush away all the dust and dirt from the
shoes and operating mechanism, taking care
not to inhale it.
6The friction linings fitted as original
equipment are of the bonded type and the
rivet heads normally used as a guide to wear
are not, of course, fitted. However, if the
thickness of the friction linings is down to
1.5 mm (0.06 in) or less, the shoes must be
renewed. Always purchase new or factory
relined brake shoes.
7Before removing the brake shoes, note the
way in which the shoes are positioned, with
respect to leading and trailing ends (the end
of the shoe not covered by lining material).Note also into which holes in the shoe web
the return springs are connected. Sketch the
shoes or mark the holes on the new shoes
with quick drying paint if you are doubtful
about remembering (photo).
8Undo the steady springs by depressing and
rotating their caps a quarter turn to disengage
the slot from the pin. On later models a
U-shaped steady spring is used. Depress and
slide it out.
9Rotate the hub until the cut-outs in its rear
flange face are in alignment with the shoe
self-adjusters.
10Pivot the trailing shoe on the self-adjuster
post and disengage the ends of the shoe from
the slot in the wheel cylinder tappet and from
the lower anchor block.
11Work the shoe up the self-adjuster pivot
post until the self-adjuster boss enters the
cut-out in the hub flange. The shoe can now
be withdrawn (photo).
12Once off the self-adjuster post, the
pull-off spring tension is eased, as the shoe
can move towards the other, so the springs
can be unhooked.
13Remove the leading shoe in a similar way.
14The new shoes will already be fitted with
new self-adjusters.
15Fit the new shoes to their self-adjuster
posts, making sure that the handbrake shoe
lever is correctly located. Engage the ends of
the shoes.
16Using a wooden or plastic-faced mallet,
tap the shoes inwards against the friction of
their self-adjuster coil springs. This will havethe effect of reducing the overall diameter of
the shoes to facilitate fitting of the shoe return
springs and to allow the brake drum to slide
over them.
17Using pliers, reconnect the upper (longer)
and lower shoe return springs.
18Hold the steady pins in position from the
rear of the backplate. Fit the small coil springs
and the retaining cap, again using pliers to
grip the cap and to depress and turn it to
engage the pin. On later models fit the
U-shaped springs.
19Before refitting the drum, clean it out and
examine it for grooves or scoring (refer to
Section 8).
20Fit the drum and the roadwheel.
21Apply the brakes two or three times to
position the shoes close to the drum.
22Renew the shoes on the opposite brake in
a similar way.
23The handbrake should be automatically
adjusted by the action of the shoe adjuster. If
the handbrake control lever has excessive
travel, refer to Section 16 for separate
adjusting instructions.
5 Caliper- removal,
overhaul and refitting
4
Note: Purchase a repair kit in advance of
overhaul.
1Jack up the front roadwheel and remove it.
2Brush away all dirt from the caliper
Braking system 8•3
4.11 Rear hub showing cut-outs on rear
face for shoe self-adjuster bosses4.7 Rear brake assembly3.8B Cylinder body located on caliper
bracket
Fig. 8.2 Exploded view of caliper (Sec 5)
8
Page 84 of 303
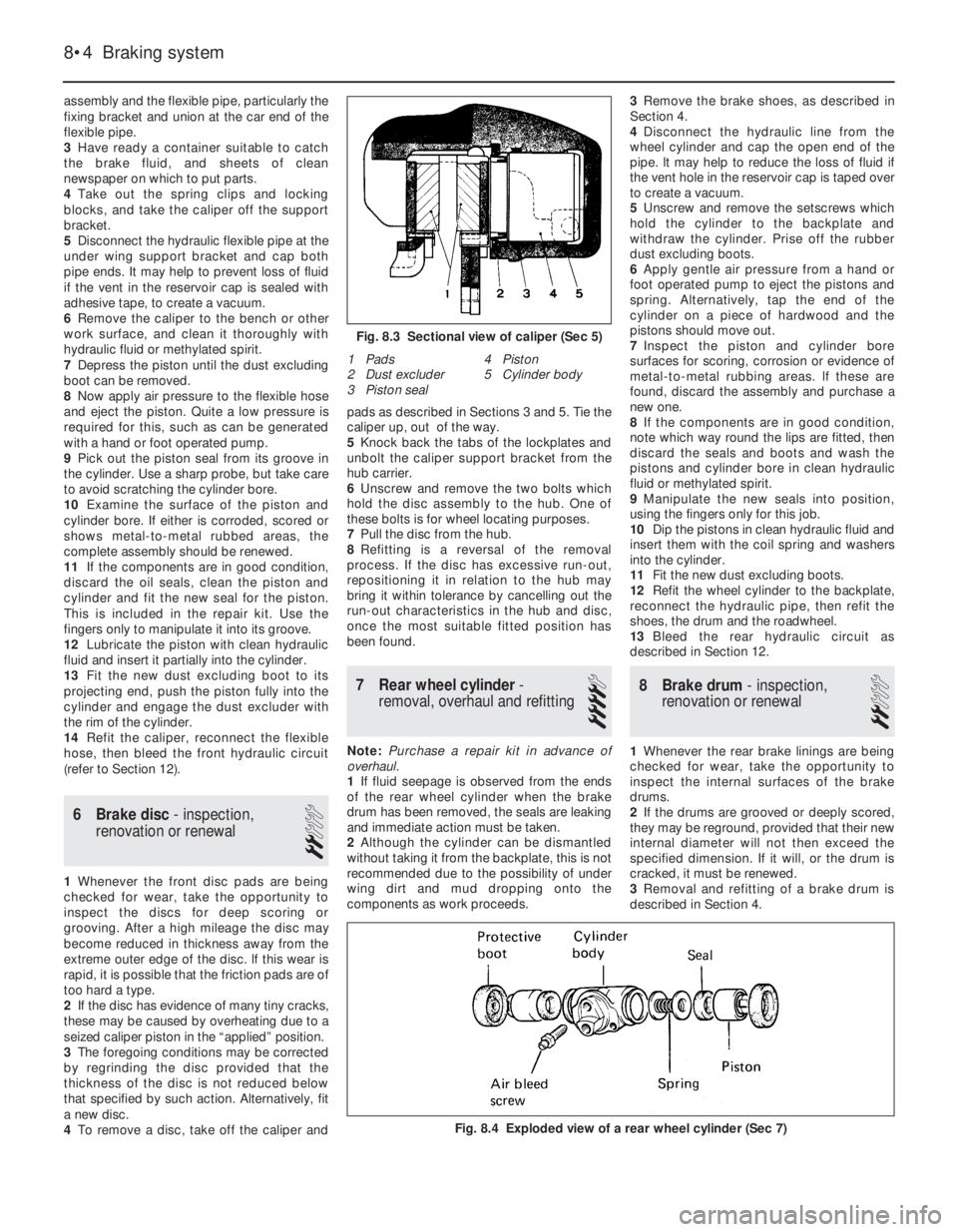
assembly and the flexible pipe, particularly the
fixing bracket and union at the car end of the
flexible pipe.
3Have ready a container suitable to catch
the brake fluid, and sheets of clean
newspaper on which to put parts.
4Take out the spring clips and locking
blocks, and take the caliper off the support
bracket.
5Disconnect the hydraulic flexible pipe at the
under wing support bracket and cap both
pipe ends. It may help to prevent loss of fluid
if the vent in the reservoir cap is sealed with
adhesive tape, to create a vacuum.
6Remove the caliper to the bench or other
work surface, and clean it thoroughly with
hydraulic fluid or methylated spirit.
7Depress the piston until the dust excluding
boot can be removed.
8Now apply air pressure to the flexible hose
and eject the piston. Quite a low pressure is
required for this, such as can be generated
with a hand or foot operated pump.
9Pick out the piston seal from its groove in
the cylinder. Use a sharp probe, but take care
to avoid scratching the cylinder bore.
10Examine the surface of the piston and
cylinder bore. If either is corroded, scored or
shows metal-to-metal rubbed areas, the
complete assembly should be renewed.
11If the components are in good condition,
discard the oil seals, clean the piston and
cylinder and fit the new seal for the piston.
This is included in the repair kit. Use the
fingers only to manipulate it into its groove.
12Lubricate the piston with clean hydraulic
fluid and insert it partially into the cylinder.
13Fit the new dust excluding boot to its
projecting end, push the piston fully into the
cylinder and engage the dust excluder with
the rim of the cylinder.
14Refit the caliper, reconnect the flexible
hose, then bleed the front hydraulic circuit
(refer to Section 12).
6 Brake disc- inspection,
renovation or renewal
2
1Whenever the front disc pads are being
checked for wear, take the opportunity to
inspect the discs for deep scoring or
grooving. After a high mileage the disc may
become reduced in thickness away from the
extreme outer edge of the disc. lf this wear is
rapid, it is possible that the friction pads are of
too hard a type.
2If the disc has evidence of many tiny cracks,
these may be caused by overheating due to a
seized caliper piston in the “applied” position.
3The foregoing conditions may be corrected
by regrinding the disc provided that the
thickness of the disc is not reduced below
that specified by such action. Alternatively, fit
a new disc.
4To remove a disc, take off the caliper andpads as described in Sections 3 and 5. Tie the
caliper up, out of the way.
5Knock back the tabs of the lockplates and
unbolt the caliper support bracket from the
hub carrier.
6Unscrew and remove the two bolts which
hold the disc assembly to the hub. One of
these bolts is for wheel locating purposes.
7Pull the disc from the hub.
8Refitting is a reversal of the removal
process. If the disc has excessive run-out,
repositioning it in relation to the hub may
bring it within tolerance by cancelling out the
run-out characteristics in the hub and disc,
once the most suitable fitted position has
been found.
7 Rear wheel cylinder-
removal, overhaul and refitting
4
Note: Purchase a repair kit in advance of
overhaul.
1If fluid seepage is observed from the ends
of the rear wheel cylinder when the brake
drum has been removed, the seals are leaking
and immediate action must be taken.
2Although the cylinder can be dismantled
without taking it from the backplate, this is not
recommended due to the possibility of under
wing dirt and mud dropping onto the
components as work proceeds. 3Remove the brake shoes, as described in
Section 4.
4Disconnect the hydraulic line from the
wheel cylinder and cap the open end of the
pipe. lt may help to reduce the loss of fluid if
the vent hole in the reservoir cap is taped over
to create a vacuum.
5Unscrew and remove the setscrews which
hold the cylinder to the backplate and
withdraw the cylinder. Prise off the rubber
dust excluding boots.
6Apply gentle air pressure from a hand or
foot operated pump to eject the pistons and
spring. Alternatively, tap the end of the
cylinder on a piece of hardwood and the
pistons should move out.
7Inspect the piston and cylinder bore
surfaces for scoring, corrosion or evidence of
metal-to-metal rubbing areas. lf these are
found, discard the assembly and purchase a
new one.
8If the components are in good condition,
note which way round the lips are fitted, then
discard the seals and boots and wash the
pistons and cylinder bore in clean hydraulic
fluid or methylated spirit.
9Manipulate the new seals into position,
using the fingers only for this job.
10Dip the pistons in clean hydraulic fluid and
insert them with the coil spring and washers
into the cylinder.
11Fit the new dust excluding boots.
12Refit the wheel cylinder to the backplate,
reconnect the hydraulic pipe, then refit the
shoes, the drum and the roadwheel.
13Bleed the rear hydraulic circuit as
described in Section 12.
8 Brake drum- inspection,
renovation or renewal
2
1Whenever the rear brake linings are being
checked for wear, take the opportunity to
inspect the internal surfaces of the brake
drums.
2If the drums are grooved or deeply scored,
they may be reground, provided that their new
internal diameter will not then exceed the
specified dimension. If it will, or the drum is
cracked, it must be renewed.
3Removal and refitting of a brake drum is
described in Section 4.
8•4 Braking system
Fig. 8.4 Exploded view of a rear wheel cylinder (Sec 7)
1 Pads
2 Dust excluder
3 Piston seal4 Piston
5 Cylinder body
Fig. 8.3 Sectional view of caliper (Sec 5)
Page 85 of 303
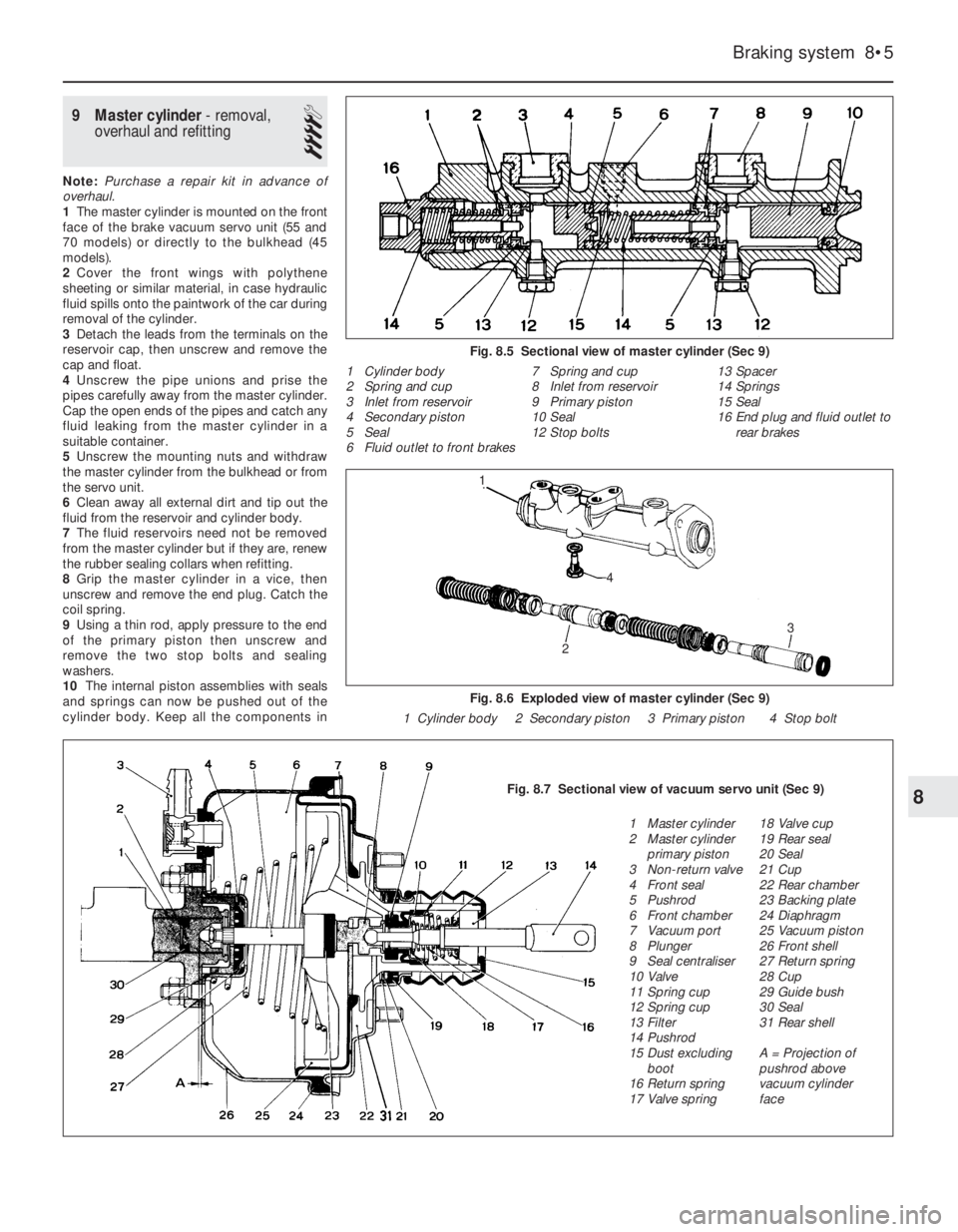
9 Master cylinder- removal,
overhaul and refitting
4
Note: Purchase a repair kit in advance of
overhaul.
1The master cylinder is mounted on the front
face of the brake vacuum servo unit (55 and
70 models) or directly to the bulkhead (45
models).
2Cover the front wings with polythene
sheeting or similar material, in case hydraulic
fluid spills onto the paintwork of the car during
removal of the cylinder.
3Detach the leads from the terminals on the
reservoir cap, then unscrew and remove the
cap and float.
4Unscrew the pipe unions and prise the
pipes carefully away from the master cylinder.
Cap the open ends of the pipes and catch any
fluid leaking from the master cylinder in a
suitable container.
5Unscrew the mounting nuts and withdraw
the master cylinder from the bulkhead or from
the servo unit.
6Clean away all external dirt and tip out the
fluid from the reservoir and cylinder body.
7The fluid reservoirs need not be removed
from the master cylinder but if they are, renew
the rubber sealing collars when refitting.
8Grip the master cylinder in a vice, then
unscrew and remove the end plug. Catch the
coil spring.
9Using a thin rod, apply pressure to the end
of the primary piston then unscrew and
remove the two stop bolts and sealing
washers.
10The internal piston assemblies with seals
and springs can now be pushed out of the
cylinder body. Keep all the components in
Braking system 8•5
Fig. 8.5 Sectional view of master cylinder (Sec 9)
1 Cylinder body
2 Spring and cup
3 Inlet from reservoir
4 Secondary piston
5 Seal
6 Fluid outlet to front brakes7 Spring and cup
8 Inlet from reservoir
9 Primary piston
10 Seal
12 Stop bolts13 Spacer
14 Springs
15 Seal
16 End plug and fluid outlet to
rear brakes
Fig. 8.6 Exploded view of master cylinder (Sec 9)
1 Cylinder body 2 Secondary piston 3 Primary piston 4 Stop bolt
8Fig. 8.7 Sectional view of vacuum servo unit (Sec 9)
1 Master cylinder
2 Master cylinder
primary piston
3 Non-return valve
4 Front seal
5 Pushrod
6 Front chamber
7 Vacuum port
8 Plunger
9 Seal centraliser
10 Valve
11 Spring cup
12 Spring cup
13 Filter
14 Pushrod
15 Dust excluding
boot
16 Return spring
17 Valve spring18 Valve cup
19 Rear seal
20 Seal
21 Cup
22 Rear chamber
23 Backing plate
24 Diaphragm
25 Vacuum piston
26 Front shell
27 Return spring
28 Cup
29 Guide bush
30 Seal
31 Rear shell
A = Projection of
pushrod above
vacuum cylinder
face
2
3
1
4
Page 86 of 303
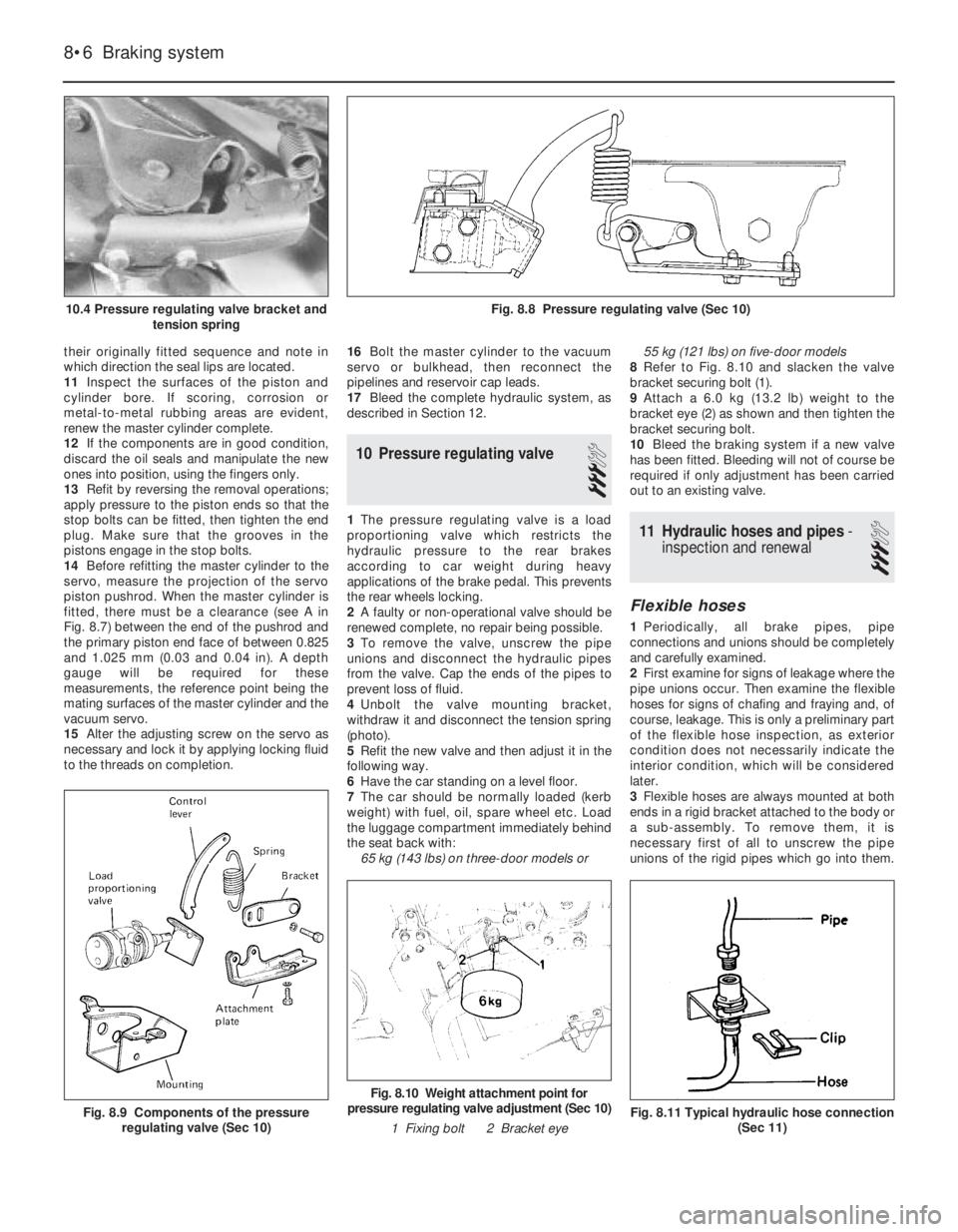
their originally fitted sequence and note in
which direction the seal lips are located.
11Inspect the surfaces of the piston and
cylinder bore. If scoring, corrosion or
metal-to-metal rubbing areas are evident,
renew the master cylinder complete.
12If the components are in good condition,
discard the oil seals and manipulate the new
ones into position, using the fingers only.
13Refit by reversing the removal operations;
apply pressure to the piston ends so that the
stop bolts can be fitted, then tighten the end
plug. Make sure that the grooves in the
pistons engage in the stop bolts.
14Before refitting the master cylinder to the
servo, measure the projection of the servo
piston pushrod. When the master cylinder is
fitted, there must be a clearance (see A in
Fig. 8.7) between the end of the pushrod and
the primary piston end face of between 0.825
and 1.025 mm (0.03 and 0.04 in). A depth
gauge will be required for these
measurements, the reference point being the
mating surfaces of the master cylinder and the
vacuum servo.
15Alter the adjusting screw on the servo as
necessary and lock it by applying locking fluid
to the threads on completion.16Bolt the master cylinder to the vacuum
servo or bulkhead, then reconnect the
pipelines and reservoir cap leads.
17Bleed the complete hydraulic system, as
described in Section 12.
10 Pressure regulating valve
3
1The pressure regulating valve is a load
proportioning valve which restricts the
hydraulic pressure to the rear brakes
according to car weight during heavy
applications of the brake pedal. This prevents
the rear wheels locking.
2A faulty or non-operational valve should be
renewed complete, no repair being possible.
3To remove the valve, unscrew the pipe
unions and disconnect the hydraulic pipes
from the valve. Cap the ends of the pipes to
prevent loss of fluid.
4Unbolt the valve mounting bracket,
withdraw it and disconnect the tension spring
(photo).
5Refit the new valve and then adjust it in the
following way.
6Have the car standing on a level floor.
7The car should be normally loaded (kerb
weight) with fuel, oil, spare wheel etc. Load
the luggage compartment immediately behind
the seat back with:
65 kg (143 lbs) on three-door models or 55 kg (121 lbs) on five-door models
8Refer to Fig. 8.10 and slacken the valve
bracket securing bolt (1).
9Attach a 6.0 kg (13.2 lb) weight to the
bracket eye (2) as shown and then tighten the
bracket securing bolt.
10Bleed the braking system if a new valve
has been fitted. Bleeding will not of course be
required if only adjustment has been carried
out to an existing valve.11 Hydraulic hoses and pipes-
inspection and renewal
3
Flexible hoses
1Periodically, all brake pipes, pipe
connections and unions should be completely
and carefully examined.
2First examine for signs of leakage where the
pipe unions occur. Then examine the flexible
hoses for signs of chafing and fraying and, of
course, leakage. This is only a preliminary part
of the flexible hose inspection, as exterior
condition does not necessarily indicate the
interior condition, which will be considered
later.
3Flexible hoses are always mounted at both
ends in a rigid bracket attached to the body or
a sub-assembly. To remove them, it is
necessary first of all to unscrew the pipe
unions of the rigid pipes which go into them.
8•6 Braking system
Fig. 8.11 Typical hydraulic hose connection
(Sec 11)
Fig. 8.10 Weight attachment point for
pressure regulating valve adjustment (Sec 10)
1 Fixing bolt 2 Bracket eye
Fig. 8.9 Components of the pressure
regulating valve (Sec 10)
Fig. 8.8 Pressure regulating valve (Sec 10)10.4 Pressure regulating valve bracket and
tension spring
Page 87 of 303
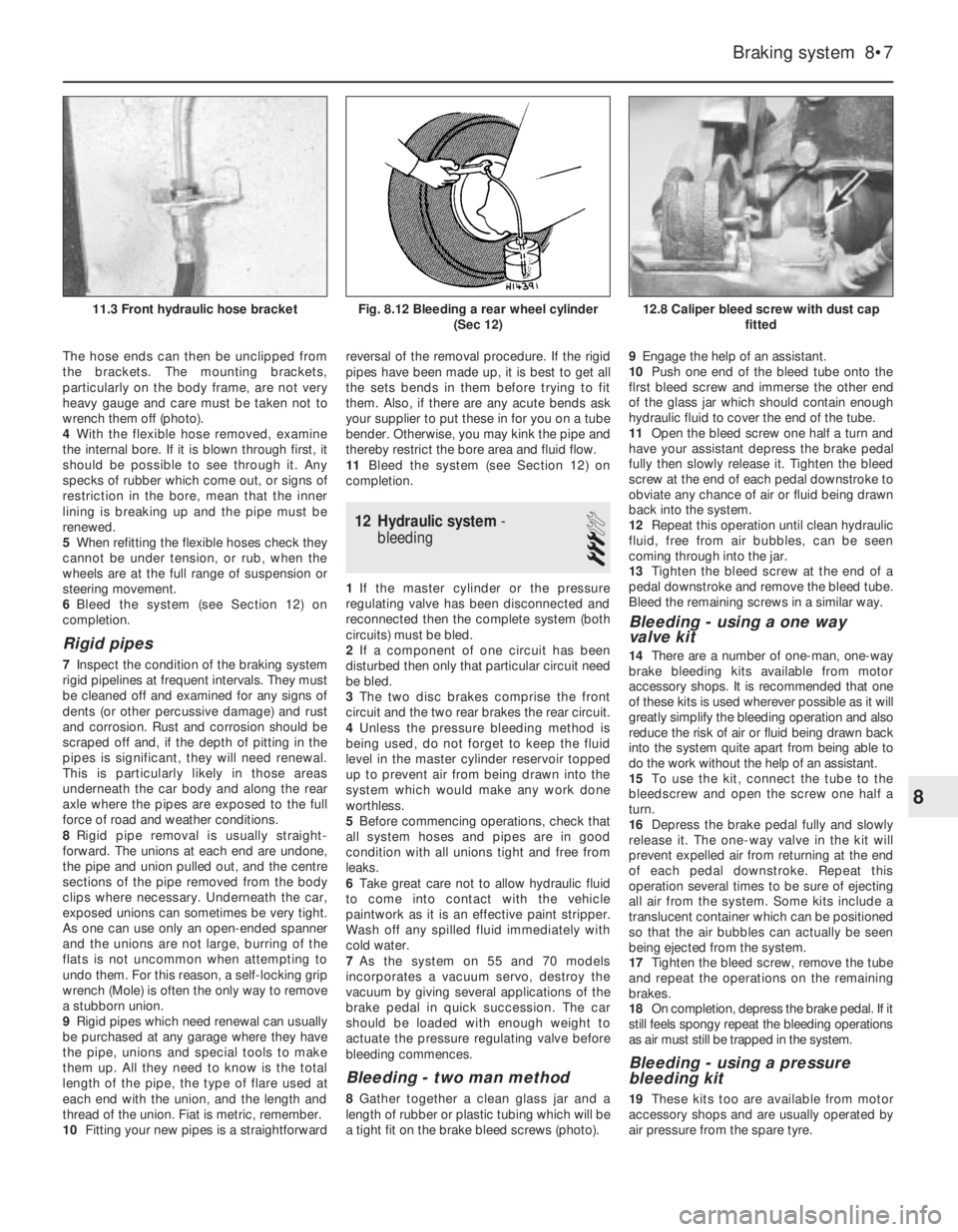
The hose ends can then be unclipped from
the brackets. The mounting brackets,
particularly on the body frame, are not very
heavy gauge and care must be taken not to
wrench them off (photo).
4With the flexible hose removed, examine
the internal bore. If it is blown through first, it
should be possible to see through it. Any
specks of rubber which come out, or signs of
restriction in the bore, mean that the inner
lining is breaking up and the pipe must be
renewed.
5When refitting the flexible hoses check they
cannot be under tension, or rub, when the
wheels are at the full range of suspension or
steering movement.
6Bleed the system (see Section 12) on
completion.
Rigid pipes
7Inspect the condition of the braking system
rigid pipelines at frequent intervals. They must
be cleaned off and examined for any signs of
dents (or other percussive damage) and rust
and corrosion. Rust and corrosion should be
scraped off and, if the depth of pitting in the
pipes is significant, they will need renewal.
This is particularly likely in those areas
underneath the car body and along the rear
axle where the pipes are exposed to the full
force of road and weather conditions.
8Rigid pipe removal is usually straight-
forward. The unions at each end are undone,
the pipe and union pulled out, and the centre
sections of the pipe removed from the body
clips where necessary. Underneath the car,
exposed unions can sometimes be very tight.
As one can use only an open-ended spanner
and the unions are not large, burring of the
flats is not uncommon when attempting to
undo them. For this reason, a self-locking grip
wrench (Mole) is often the only way to remove
a stubborn union.
9Rigid pipes which need renewal can usually
be purchased at any garage where they have
the pipe, unions and special tools to make
them up. All they need to know is the total
length of the pipe, the type of flare used at
each end with the union, and the length and
thread of the union. Fiat is metric, remember.
10Fitting your new pipes is a straightforwardreversal of the removal procedure. If the rigid
pipes have been made up, it is best to get all
the sets bends in them before trying to fit
them. Also, if there are any acute bends ask
your supplier to put these in for you on a tube
bender. Otherwise, you may kink the pipe and
thereby restrict the bore area and fluid flow.
11Bleed the system (see Section 12) on
completion.
12 Hydraulic system-
bleeding
3
1If the master cylinder or the pressure
regulating valve has been disconnected and
reconnected then the complete system (both
circuits) must be bled.
2If a component of one circuit has been
disturbed then only that particular circuit need
be bled.
3The two disc brakes comprise the front
circuit and the two rear brakes the rear circuit.
4Unless the pressure bleeding method is
being used, do not forget to keep the fluid
level in the master cylinder reservoir topped
up to prevent air from being drawn into the
system which would make any work done
worthless.
5Before commencing operations, check that
all system hoses and pipes are in good
condition with all unions tight and free from
leaks.
6Take great care not to allow hydraulic fluid
to come into contact with the vehicle
paintwork as it is an effective paint stripper.
Wash off any spilled fluid immediately with
cold water.
7As the system on 55 and 70 models
incorporates a vacuum servo, destroy the
vacuum by giving several applications of the
brake pedal in quick succession. The car
should be loaded with enough weight to
actuate the pressure regulating valve before
bleeding commences.
Bleeding - two man method
8Gather together a clean glass jar and a
length of rubber or plastic tubing which will be
a tight fit on the brake bleed screws (photo).9Engage the help of an assistant.
10Push one end of the bleed tube onto the
flrst bleed screw and immerse the other end
of the glass jar which should contain enough
hydraulic fluid to cover the end of the tube.
11Open the bleed screw one half a turn and
have your assistant depress the brake pedal
fully then slowly release it. Tighten the bleed
screw at the end of each pedal downstroke to
obviate any chance of air or fluid being drawn
back into the system.
12Repeat this operation until clean hydraulic
fluid, free from air bubbles, can be seen
coming through into the jar.
13Tighten the bleed screw at the end of a
pedal downstroke and remove the bleed tube.
Bleed the remaining screws in a similar way.
Bleeding - using a one way
valve kit
14There are a number of one-man, one-way
brake bleeding kits available from motor
accessory shops. It is recommended that one
of these kits is used wherever possible as it will
greatly simplify the bleeding operation and also
reduce the risk of air or fluid being drawn back
into the system quite apart from being able to
do the work without the help of an assistant.
15To use the kit, connect the tube to the
bleedscrew and open the screw one half a
turn.
16Depress the brake pedal fully and slowly
release it. The one-way valve in the kit will
prevent expelled air from returning at the end
of each pedal downstroke. Repeat this
operation several times to be sure of ejecting
all air from the system. Some kits include a
translucent container which can be positioned
so that the air bubbles can actually be seen
being ejected from the system.
17Tighten the bleed screw, remove the tube
and repeat the operations on the remaining
brakes.
18On completion, depress the brake pedal. If it
still feels spongy repeat the bleeding operations
as air must still be trapped in the system.
Bleeding - using a pressure
bleeding kit
19These kits too are available from motor
accessory shops and are usually operated by
air pressure from the spare tyre.
Braking system 8•7
12.8 Caliper bleed screw with dust cap
fittedFig. 8.12 Bleeding a rear wheel cylinder
(Sec 12)11.3 Front hydraulic hose bracket
8
Page 88 of 303
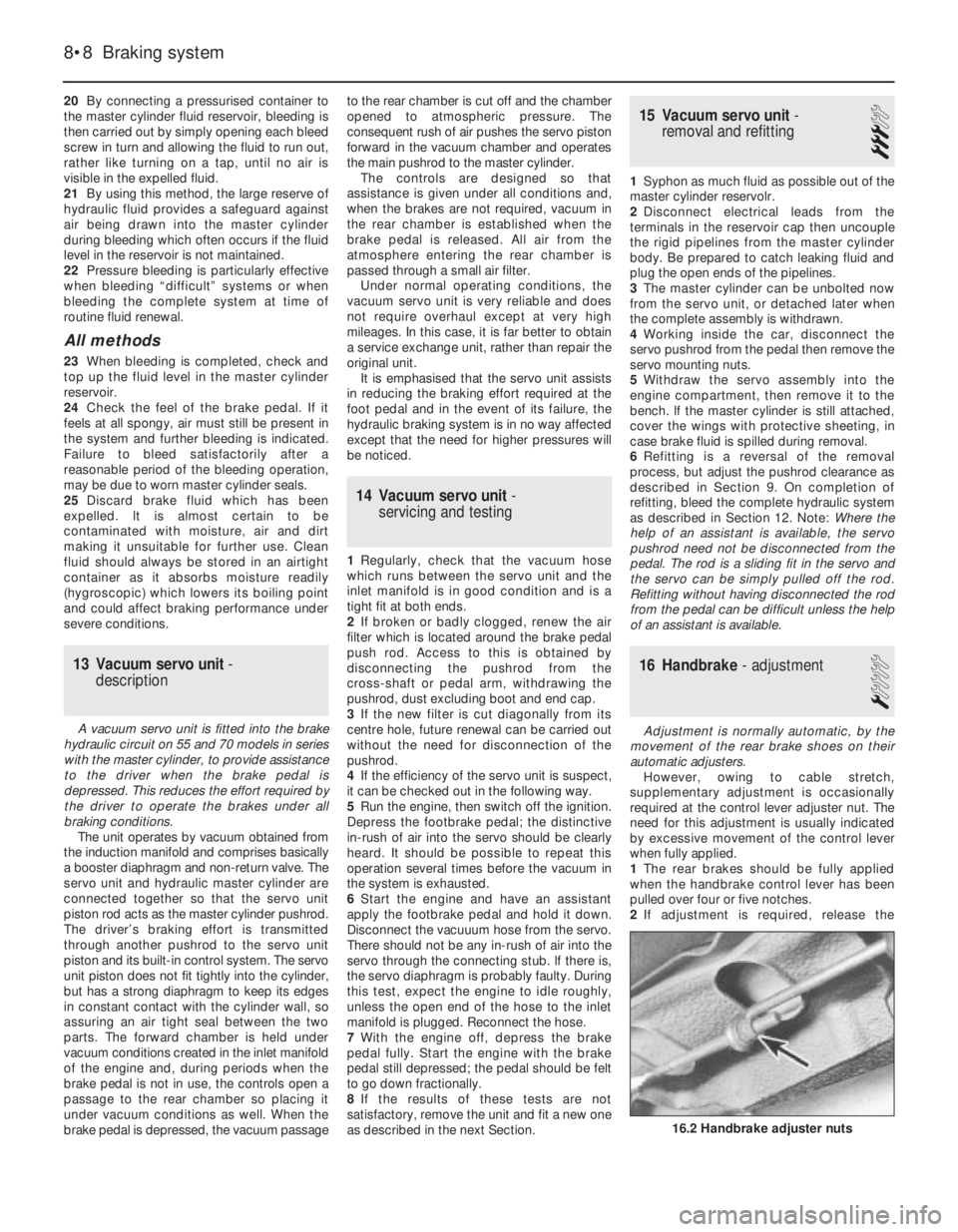
20By connecting a pressurised container to
the master cylinder fluid reservoir, bleeding is
then carried out by simply opening each bleed
screw in turn and allowing the fluid to run out,
rather like turning on a tap, until no air is
visible in the expelled fluid.
21By using this method, the large reserve of
hydraulic fluid provides a safeguard against
air being drawn into the master cylinder
during bleeding which often occurs if the fluid
level in the reservoir is not maintained.
22Pressure bleeding is particularly effective
when bleeding “difficult” systems or when
bleeding the complete system at time of
routine fluid renewal.
All methods
23When bleeding is completed, check and
top up the fluid level in the master cylinder
reservoir.
24Check the feel of the brake pedal. If it
feels at all spongy, air must still be present in
the system and further bleeding is indicated.
Failure to bleed satisfactorily after a
reasonable period of the bleeding operation,
may be due to worn master cylinder seals.
25Discard brake fluid which has been
expelled. lt is almost certain to be
contaminated with moisture, air and dirt
making it unsuitable for further use. Clean
fluid should always be stored in an airtight
container as it absorbs moisture readily
(hygroscopic) which lowers its boiling point
and could affect braking performance under
severe conditions.
13 Vacuum servo unit-
description
A vacuum servo unit is fitted into the brake
hydraulic circuit on 55 and 70 models in series
with the master cylinder, to provide assistance
to the driver when the brake pedal is
depressed. This reduces the effort required by
the driver to operate the brakes under all
braking conditions.
The unit operates by vacuum obtained from
the induction manifold and comprises basically
a booster diaphragm and non-return valve. The
servo unit and hydraulic master cylinder are
connected together so that the servo unit
piston rod acts as the master cylinder pushrod.
The driver’s braking effort is transmitted
through another pushrod to the servo unit
piston and its built-in control system. The servo
unit piston does not fit tightly into the cylinder,
but has a strong diaphragm to keep its edges
in constant contact with the cylinder wall, so
assuring an air tight seal between the two
parts. The forward chamber is held under
vacuum conditions created in the inlet manifold
of the engine and, during periods when the
brake pedal is not in use, the controls open a
passage to the rear chamber so placing it
under vacuum conditions as well. When the
brake pedal is depressed, the vacuum passageto the rear chamber is cut off and the chamber
opened to atmospheric pressure. The
consequent rush of air pushes the servo piston
forward in the vacuum chamber and operates
the main pushrod to the master cylinder.
The controls are designed so that
assistance is given under all conditions and,
when the brakes are not required, vacuum in
the rear chamber is established when the
brake pedal is released. All air from the
atmosphere entering the rear chamber is
passed through a small air filter.
Under normal operating conditions, the
vacuum servo unit is very reliable and does
not require overhaul except at very high
mileages. In this case, it is far better to obtain
a service exchange unit, rather than repair the
original unit.
It is emphasised that the servo unit assists
in reducing the braking effort required at the
foot pedal and in the event of its failure, the
hydraulic braking system is in no way affected
except that the need for higher pressures will
be noticed.
14 Vacuum servo unit-
servicing and testing
1Regularly, check that the vacuum hose
which runs between the servo unit and the
inlet manifold is in good condition and is a
tight fit at both ends.
2If broken or badly clogged, renew the air
filter which is located around the brake pedal
push rod. Access to this is obtained by
disconnecting the pushrod from the
cross-shaft or pedal arm, withdrawing the
pushrod, dust excluding boot and end cap.
3If the new filter is cut diagonally from its
centre hole, future renewal can be carried out
without the need for disconnection of the
pushrod.
4If the efficiency of the servo unit is suspect,
it can be checked out in the following way.
5Run the engine, then switch off the ignition.
Depress the footbrake pedal; the distinctive
in-rush of air into the servo should be clearly
heard. It should be possible to repeat this
operation several times before the vacuum in
the system is exhausted.
6Start the engine and have an assistant
apply the footbrake pedal and hold it down.
Disconnect the vacuuum hose from the servo.
There should not be any in-rush of air into the
servo through the connecting stub. lf there is,
the servo diaphragm is probably faulty. During
this test, expect the engine to idle roughly,
unless the open end of the hose to the inlet
manifold is plugged. Reconnect the hose.
7With the engine off, depress the brake
pedal fully. Start the engine with the brake
pedal still depressed; the pedal should be felt
to go down fractionally.
8If the results of these tests are not
satisfactory, remove the unit and fit a new one
as described in the next Section.
15 Vacuum servo unit-
removal and refitting
3
1Syphon as much fluid as possible out of the
master cylinder reservolr.
2Disconnect electrical leads from the
terminals in the reservoir cap then uncouple
the rigid pipelines from the master cylinder
body. Be prepared to catch leaking fluid and
plug the open ends of the pipelines.
3The master cylinder can be unbolted now
from the servo unit, or detached later when
the complete assembly is withdrawn.
4Working inside the car, disconnect the
servo pushrod from the pedal then remove the
servo mounting nuts.
5Withdraw the servo assembly into the
engine compartment, then remove it to the
bench. lf the master cylinder is still attached,
cover the wings with protective sheeting, in
case brake fluid is spilled during removal.
6Refitting is a reversal of the removal
process, but adjust the pushrod clearance as
described in Section 9. On completion of
refitting, bleed the complete hydraulic system
as described in Section 12. Note: Where the
help of an assistant is available, the servo
pushrod need not be disconnected from the
pedal. The rod is a sliding fit in the servo and
the servo can be simply pulled off the rod.
Refitting without having disconnected the rod
from the pedal can be difficult unless the help
of an assistant is available.
16 Handbrake- adjustment
1
Adjustment is normally automatic, by the
movement of the rear brake shoes on their
automatic adjusters.
However, owing to cable stretch,
supplementary adjustment is occasionally
required at the control lever adjuster nut. The
need for this adjustment is usually indicated
by excessive movement of the control lever
when fully applied.
1The rear brakes should be fully applied
when the handbrake control lever has been
pulled over four or five notches.
2If adjustment is required, release the
8•8 Braking system
16.2 Handbrake adjuster nuts
Page 89 of 303
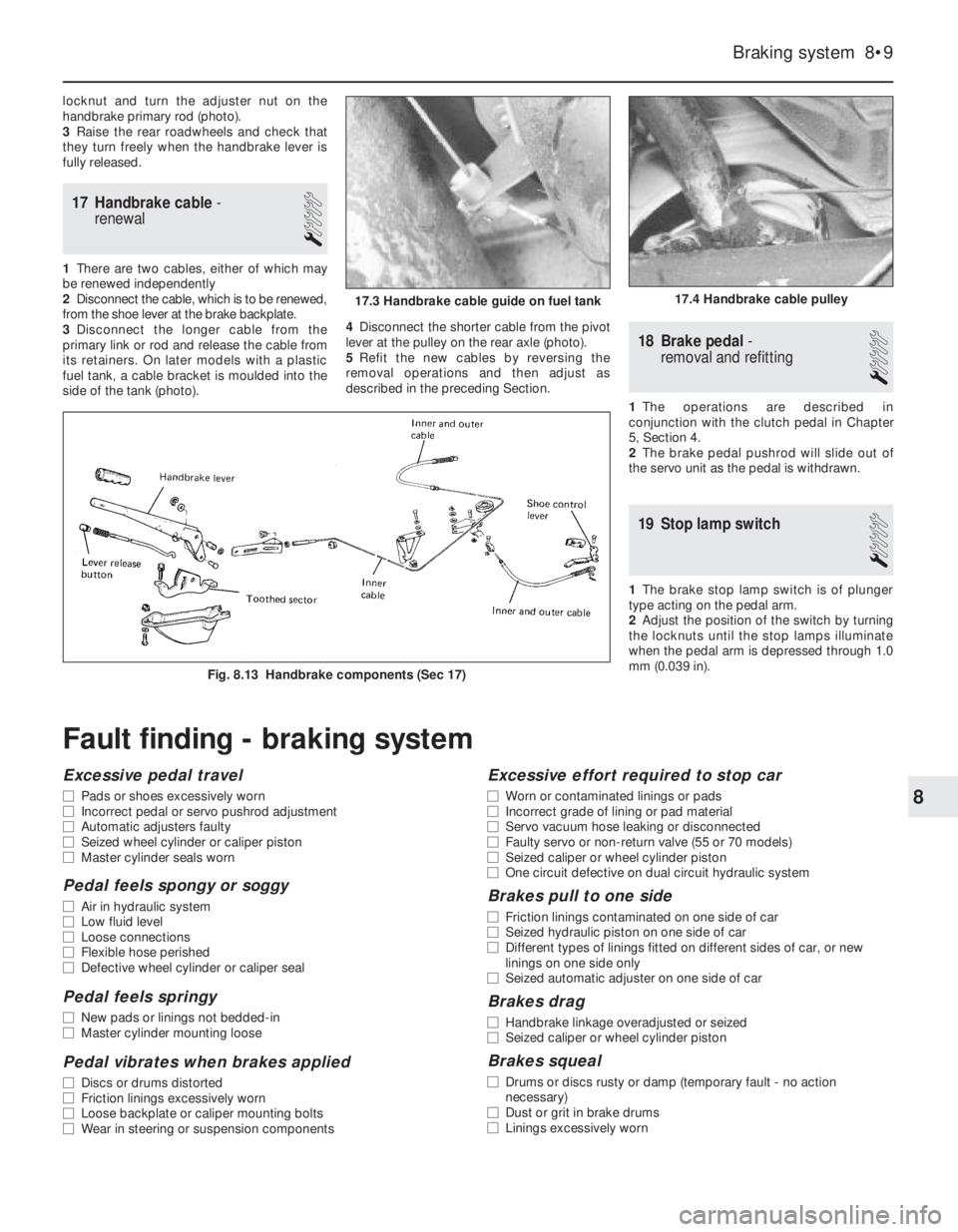
locknut and turn the adjuster nut on the
handbrake primary rod (photo).
3Raise the rear roadwheels and check that
they turn freely when the handbrake lever is
fully released.
17 Handbrake cable-
renewal
1
1There are two cables, either of which may
be renewed independently
2Disconnect the cable, which is to be renewed,
from the shoe lever at the brake backplate.
3Disconnect the longer cable from the
primary link or rod and release the cable from
its retainers. On later models with a plastic
fuel tank, a cable bracket is moulded into the
side of the tank (photo).4Disconnect the shorter cable from the pivot
lever at the pulley on the rear axle (photo).
5Refit the new cables by reversing the
removal operations and then adjust as
described in the preceding Section.
18 Brake pedal-
removal and refitting
1
1The operations are described in
conjunction with the clutch pedal in Chapter
5, Section 4.
2The brake pedal pushrod will slide out of
the servo unit as the pedal is withdrawn.
19 Stop lamp switch
1
1The brake stop lamp switch is of plunger
type acting on the pedal arm.
2Adjust the position of the switch by turning
the locknuts until the stop lamps illuminate
when the pedal arm is depressed through 1.0
mm (0.039 in).
Braking system 8•9
Fig. 8.13 Handbrake components (Sec 17)
17.4 Handbrake cable pulley17.3 Handbrake cable guide on fuel tank
8
Fault finding - braking system
Excessive pedal travel
m mPads or shoes excessively worn
m mIncorrect pedal or servo pushrod adjustment
m mAutomatic adjusters faulty
m mSeized wheel cylinder or caliper piston
m mMaster cylinder seals worn
Pedal feels spongy or soggy
m
mAir in hydraulic system
m mLow fluid level
m mLoose connections
m mFlexible hose perished
m mDefective wheel cylinder or caliper seal
Pedal feels springy
m
mNew pads or linings not bedded-in
m mMaster cylinder mounting loose
Pedal vibrates when brakes applied
m
mDiscs or drums distorted
m mFriction linings excessively worn
m mLoose backplate or caliper mounting bolts
m mWear in steering or suspension components
Excessive effort required to stop car
m
mWorn or contaminated linings or pads
m mIncorrect grade of lining or pad material
m mServo vacuum hose leaking or disconnected
m mFaulty servo or non-return valve (55 or 70 models)
m mSeized caliper or wheel cylinder piston
m mOne circuit defective on dual circuit hydraulic system
Brakes pull to one side
m
mFriction linings contaminated on one side of car
m mSeized hydraulic piston on one side of car
m mDifferent types of linings fitted on different sides of car, or new
linings on one side only
m mSeized automatic adjuster on one side of car
Brakes drag
m
mHandbrake linkage overadjusted or seized
m mSeized caliper or wheel cylinder piston
Brakes squeal
m
mDrums or discs rusty or damp (temporary fault - no action
necessary)
m mDust or grit in brake drums
m mLinings excessively worn
Page 90 of 303
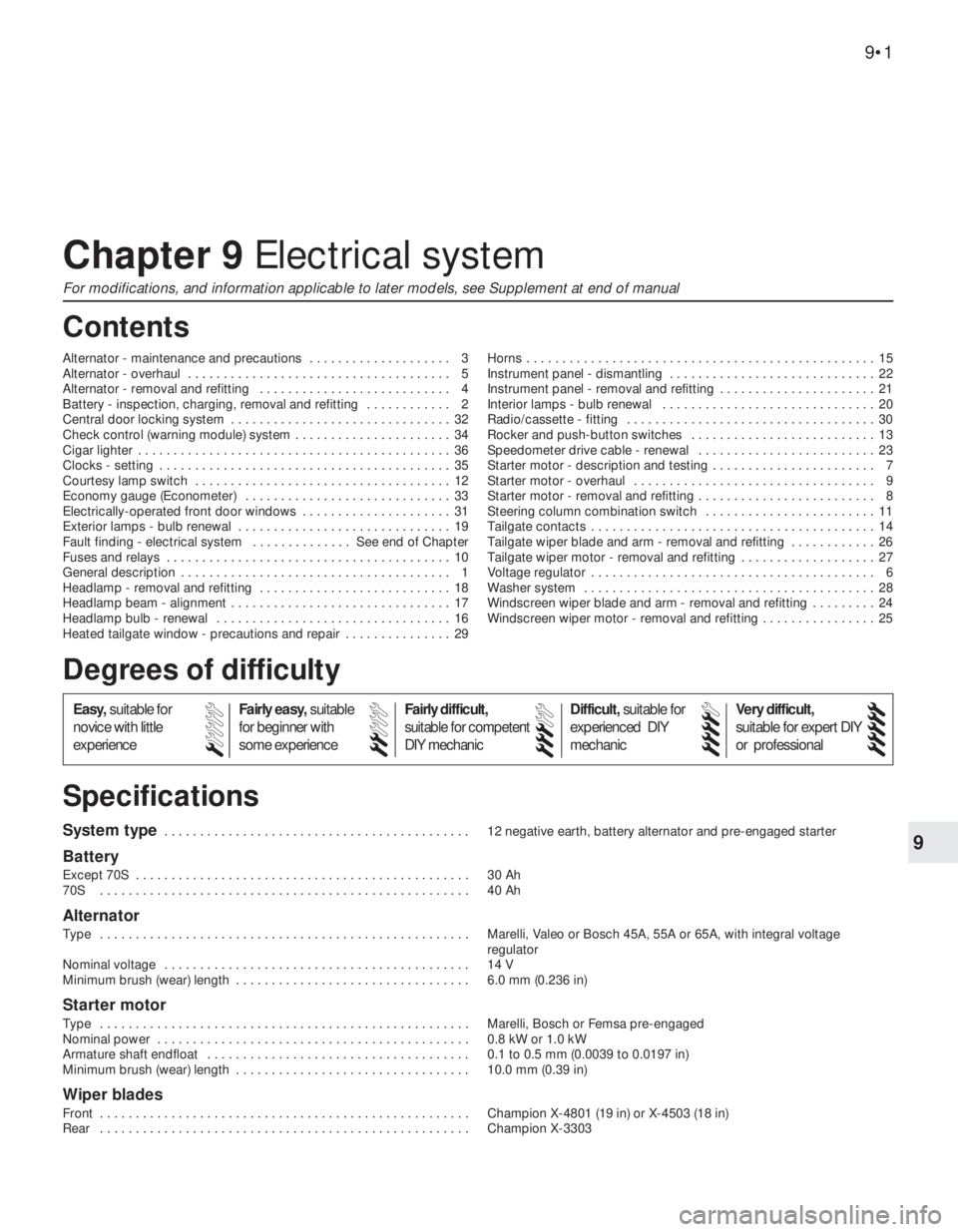
9System type . . . . . . . . . . . . . . . . . . . . . . . . . . . . . . . . . . . . . . . . . . . 12 negative earth, battery alternator and pre-engaged starter
Battery
Except 70S . . . . . . . . . . . . . . . . . . . . . . . . . . . . . . . . . . . . . . . . . . . . . . . 30 Ah
70S . . . . . . . . . . . . . . . . . . . . . . . . . . . . . . . . . . . . . . . . . . . . . . . . . . . . 40 Ah
Alternator
Type . . . . . . . . . . . . . . . . . . . . . . . . . . . . . . . . . . . . . . . . . . . . . . . . . . . . Marelli, Valeo or Bosch 45A, 55A or 65A, with integral voltage
regulator
Nominal voltage . . . . . . . . . . . . . . . . . . . . . . . . . . . . . . . . . . . . . . . . . . . 14 V
Minimum brush (wear) length . . . . . . . . . . . . . . . . . . . . . . . . . . . . . . . . . 6.0 mm (0.236 in)
Starter motor
Type . . . . . . . . . . . . . . . . . . . . . . . . . . . . . . . . . . . . . . . . . . . . . . . . . . . . Marelli, Bosch or Femsa pre-engaged
Nominal power . . . . . . . . . . . . . . . . . . . . . . . . . . . . . . . . . . . . . . . . . . . . 0.8 kW or 1.0 kW
Armature shaft endfloat . . . . . . . . . . . . . . . . . . . . . . . . . . . . . . . . . . . . . 0.1 to 0.5 mm (0.0039 to 0.0197 in)
Minimum brush (wear) length . . . . . . . . . . . . . . . . . . . . . . . . . . . . . . . . . 10.0 mm (0.39 in)
Wiper blades
Front . . . . . . . . . . . . . . . . . . . . . . . . . . . . . . . . . . . . . . . . . . . . . . . . . . . . Champion X-4801 (19 in) or X-4503 (18 in)
Rear . . . . . . . . . . . . . . . . . . . . . . . . . . . . . . . . . . . . . . . . . . . . . . . . . . . . Champion X-3303
Chapter 9 Electrical system
For modifications, and information applicable to later models, see Supplement at end of manual
Alternator - maintenance and precautions . . . . . . . . . . . . . . . . . . . . 3
Alternator - overhaul . . . . . . . . . . . . . . . . . . . . . . . . . . . . . . . . . . . . . 5
Alternator - removal and refitting . . . . . . . . . . . . . . . . . . . . . . . . . . . 4
Battery - inspection, charging, removal and refitting . . . . . . . . . . . . 2
Central door locking system . . . . . . . . . . . . . . . . . . . . . . . . . . . . . . . 32
Check control (warning module) system . . . . . . . . . . . . . . . . . . . . . . 34
Cigar lighter . . . . . . . . . . . . . . . . . . . . . . . . . . . . . . . . . . . . . . . . . . . . 36
Clocks - setting . . . . . . . . . . . . . . . . . . . . . . . . . . . . . . . . . . . . . . . . . 35
Courtesy lamp switch . . . . . . . . . . . . . . . . . . . . . . . . . . . . . . . . . . . . 12
Economy gauge (Econometer) . . . . . . . . . . . . . . . . . . . . . . . . . . . . . 33
Electrically-operated front door windows . . . . . . . . . . . . . . . . . . . . . 31
Exterior lamps - bulb renewal . . . . . . . . . . . . . . . . . . . . . . . . . . . . . . 19
Fault finding - electrical system . . . . . . . . . . . . . . See end of Chapter
Fuses and relays . . . . . . . . . . . . . . . . . . . . . . . . . . . . . . . . . . . . . . . . 10
General description . . . . . . . . . . . . . . . . . . . . . . . . . . . . . . . . . . . . . . 1
Headlamp - removal and refitting . . . . . . . . . . . . . . . . . . . . . . . . . . . 18
Headlamp beam - alignment . . . . . . . . . . . . . . . . . . . . . . . . . . . . . . . 17
Headlamp bulb - renewal . . . . . . . . . . . . . . . . . . . . . . . . . . . . . . . . . 16
Heated tailgate window - precautions and repair . . . . . . . . . . . . . . . 29Horns . . . . . . . . . . . . . . . . . . . . . . . . . . . . . . . . . . . . . . . . . . . . . . . . . 15
Instrument panel - dismantling . . . . . . . . . . . . . . . . . . . . . . . . . . . . . 22
Instrument panel - removal and refitting . . . . . . . . . . . . . . . . . . . . . . 21
Interior lamps - bulb renewal . . . . . . . . . . . . . . . . . . . . . . . . . . . . . . 20
Radio/cassette - fitting . . . . . . . . . . . . . . . . . . . . . . . . . . . . . . . . . . . 30
Rocker and push-button switches . . . . . . . . . . . . . . . . . . . . . . . . . . 13
Speedometer drive cable - renewal . . . . . . . . . . . . . . . . . . . . . . . . . 23
Starter motor - description and testing . . . . . . . . . . . . . . . . . . . . . . . 7
Starter motor - overhaul . . . . . . . . . . . . . . . . . . . . . . . . . . . . . . . . . . 9
Starter motor - removal and refitting . . . . . . . . . . . . . . . . . . . . . . . . . 8
Steering column combination switch . . . . . . . . . . . . . . . . . . . . . . . . 11
Tailgate contacts . . . . . . . . . . . . . . . . . . . . . . . . . . . . . . . . . . . . . . . . 14
Tailgate wiper blade and arm - removal and refitting . . . . . . . . . . . . 26
Tailgate wiper motor - removal and refitting . . . . . . . . . . . . . . . . . . . 27
Voltage regulator . . . . . . . . . . . . . . . . . . . . . . . . . . . . . . . . . . . . . . . . 6
Washer system . . . . . . . . . . . . . . . . . . . . . . . . . . . . . . . . . . . . . . . . . 28
Windscreen wiper blade and arm - removal and refitting . . . . . . . . . 24
Windscreen wiper motor - removal and refitting . . . . . . . . . . . . . . . . 25
9•1
Specifications Contents
Easy,suitable for
novice with little
experienceFairly easy,suitable
for beginner with
some experienceFairly difficult,
suitable for competent
DIY mechanic
Difficult,suitable for
experienced DIY
mechanicVery difficult,
suitable for expert DIY
or professional
Degrees of difficulty
54321