GEELY MK 2008 Repair Manual
Manufacturer: GEELY, Model Year: 2008, Model line: MK, Model: GEELY MK 2008Pages: 416, PDF Size: 25.19 MB
Page 51 of 416
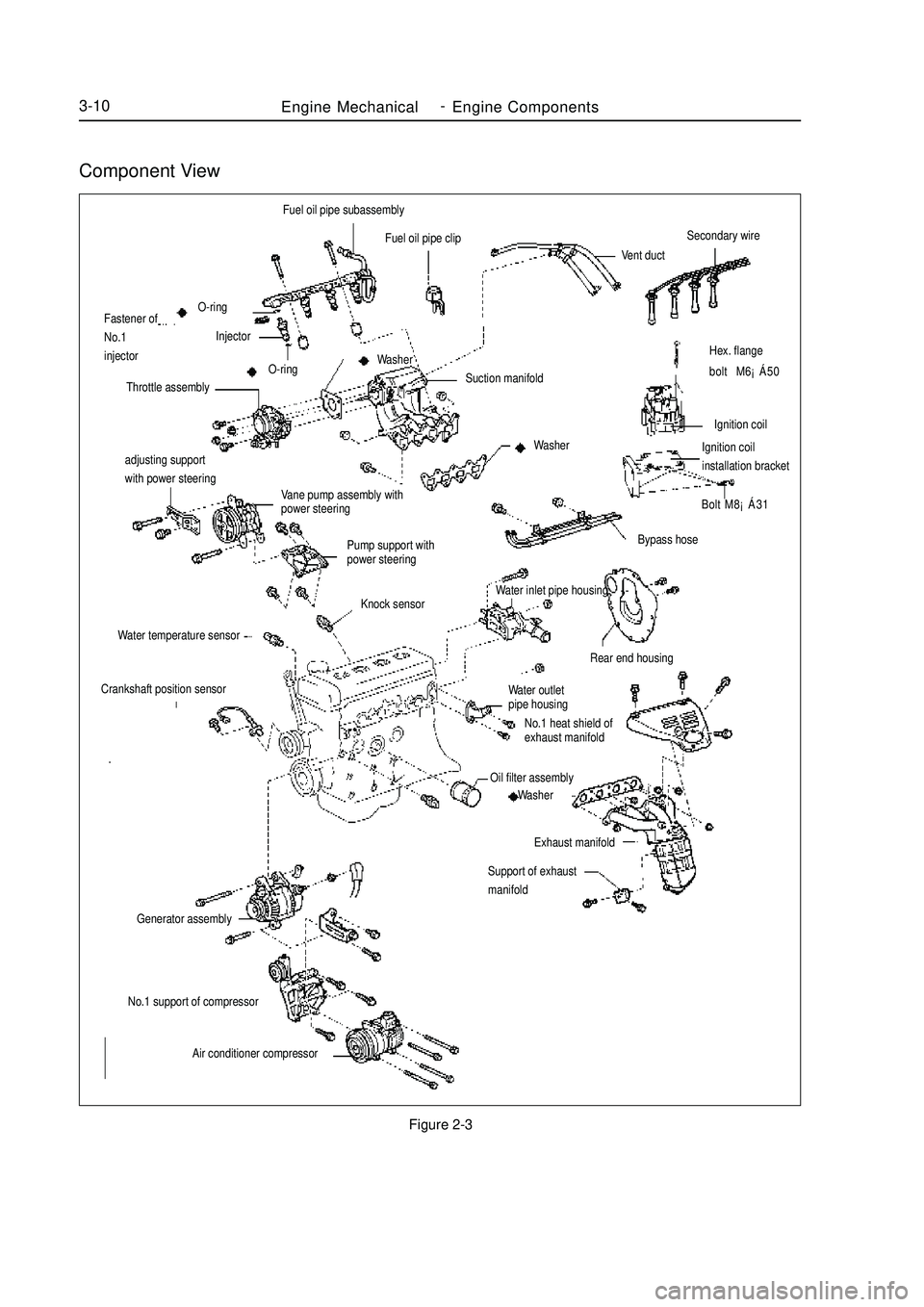
Component ViewFigure 2-3Engine MechanicalEngine Components3-10adjusting support
with power steering
Vane pump assembly with
power steering
Pump support with
power steeringHex. flange
bolt M6¡Á50
Ignition coil
Ignition coilinstallation bracket
Bolt M8¡Á31Fuel oil pipe subassembly
Fuel oil pipe clip
Vent ductSecondary wireBypass hose
Rear end housingWater outlet
pipe housing
No.1 heat shield of
exhaust manifoldOil filter assembly
Washer
Exhaust manifold
Support of exhaust
manifoldO-ring
Fastener of
No.1
injectorInjector
O-ring
Throttle assemblySuction manifold Washer
WasherKnock sensor
Water temperature sensorCrankshaft position sensorGenerator assemblyNo.1 support of compressor
Air conditioner compressorWater inlet pipe housing -
Page 52 of 416
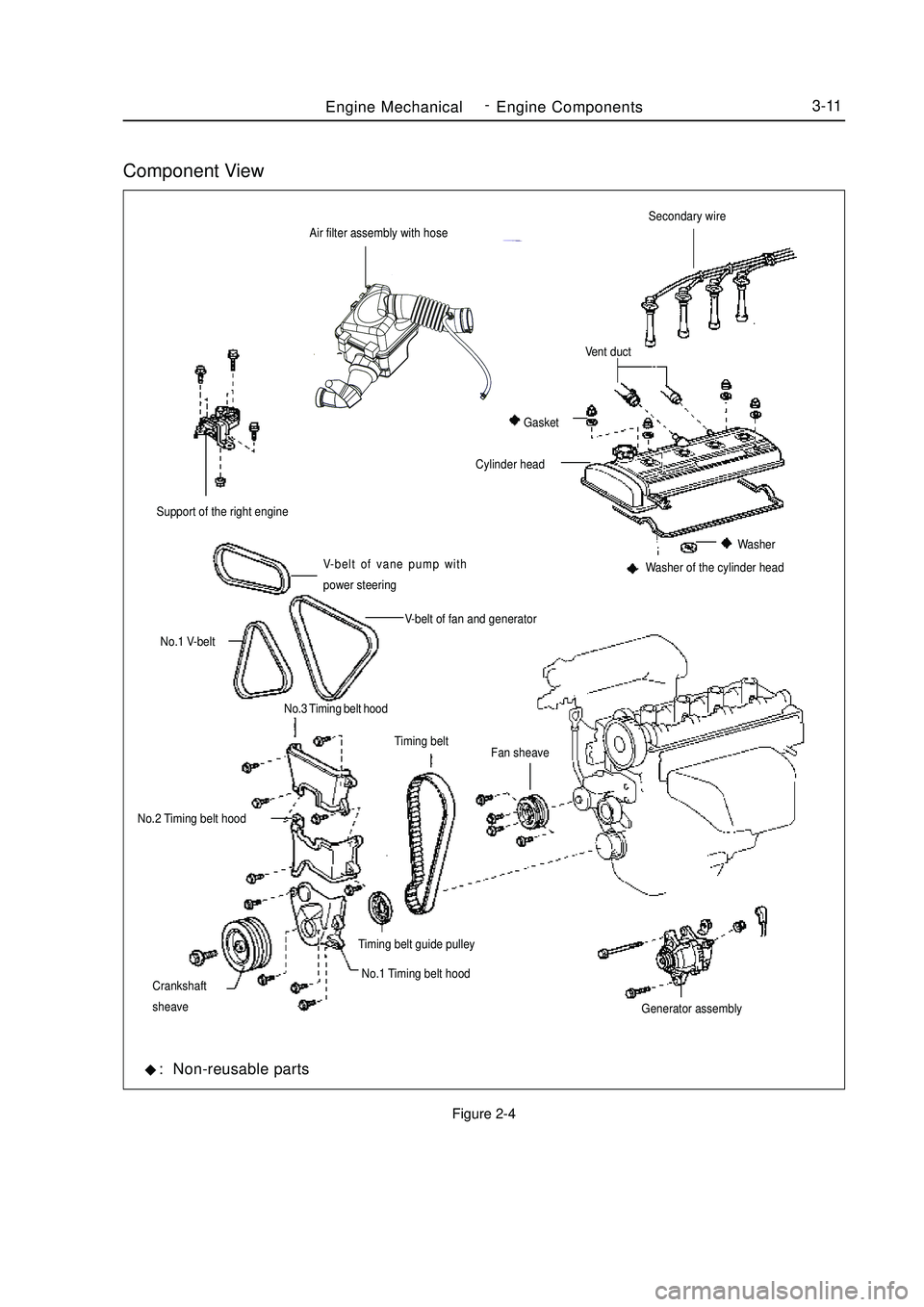
Component ViewFigure 2-4Air filter assembly with hoseEngine MechanicalEngine Components3-11V-belt of vane pump with
power steering Support of the right engine
V-belt of fan and generator
No.1 V-belt
No.3 Timing belt hood
No.2 Timing belt hood
No.1 Timing belt hoodFan sheaveSecondary wireWasher of the cylinder headCylinder headVent duct
Gasket
Washer
Timing belt
Timing belt guide pulley
Crankshaft
sheave
Generator assembly: Non-reusable parts -
Page 53 of 416
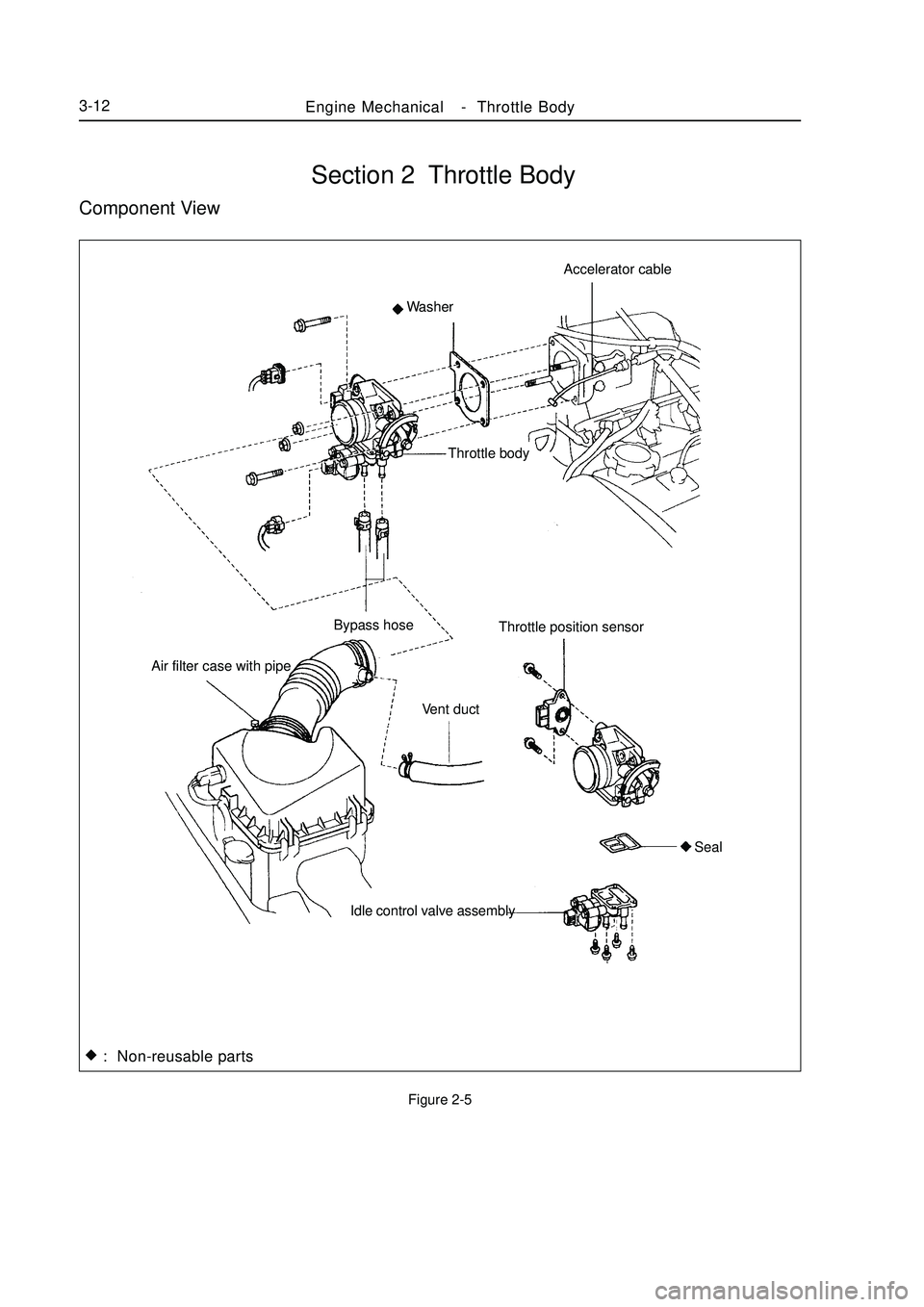
Section 2 Throttle BodyComponent ViewFigure 2-5Engine MechanicalThrottle Body3-12Washer
Throttle body
Air filter case with pipe
Idle control valve assemblySealAccelerator cable
Bypass hose
Throttle position sensor
Vent duct: Non-reusable parts -
Page 54 of 416

Dismounting/mounting and disassembly and assembly (see Figure 2-1~2-5).
1. Drain the coolant.
Warning: Do not remove the radiator cover, liquid under pressure or steam (likely to eject) while the engine
and the radiator are still hot in order to avoid scalding.
(1) Remove the radiator cover.
(2) Remove the plug of the radiator, and discharge the coolant.
2. Remove the cable of the accelerator.
Release the nut and remove the cable of the accelerator.
3. Remove the air filter hood with hose.
(1) Disconnect the connector and the wire fastening device of the suction temperature sensor.
(2) Disconnect the vent duct from the air filter hose.
(3) Release the clamping collar bolt of the air filter hose.
(4) Release 2 clamps on the air filter hood.
(5) Disconnect the air filter hose from the throttle body, and remove the air filter hood together with the hose.Figure 2-6
Figure 2-7
Figure 2-8Engine MechanicalThrottle Body3-134. Remove the throttle body assembly (see Fig. 2-6).
(1) Disconnect the connector of the throttle position sensor.
(2) Disconnect the connector of ISC valve.
(3) Remove 2 bolts and 2 nuts, and remove the throttle body from
the suction manifold (see Fig. 2-7).
(4) Disconnect 2 bypass hoses, remove and check the throttle
body (see Fig. 2-8).
Check:
a. Check whether the throttle shaft shakes.
b. Check whether there is any block at each state.
c. Check whether the throttle can open and close smoothly.
d. Check whether there is a gap between the check screw and the
rod of the throttle when the throttle is at CLOSE position.
Attention:
Do not adjust the check screw of the throttle.
If the operation deviates from specifications, replace the
throttle.
(5) Remove the washer of the throttle body.
5. Dismantle throttle body idle speed control valve assembly.
Detach 4 screws, idle speed control valve and washer.
6. Detach throttle position sensor
Detach 2 screws and throttle position sensor.Coolant Bypass Pipe -
Page 55 of 416
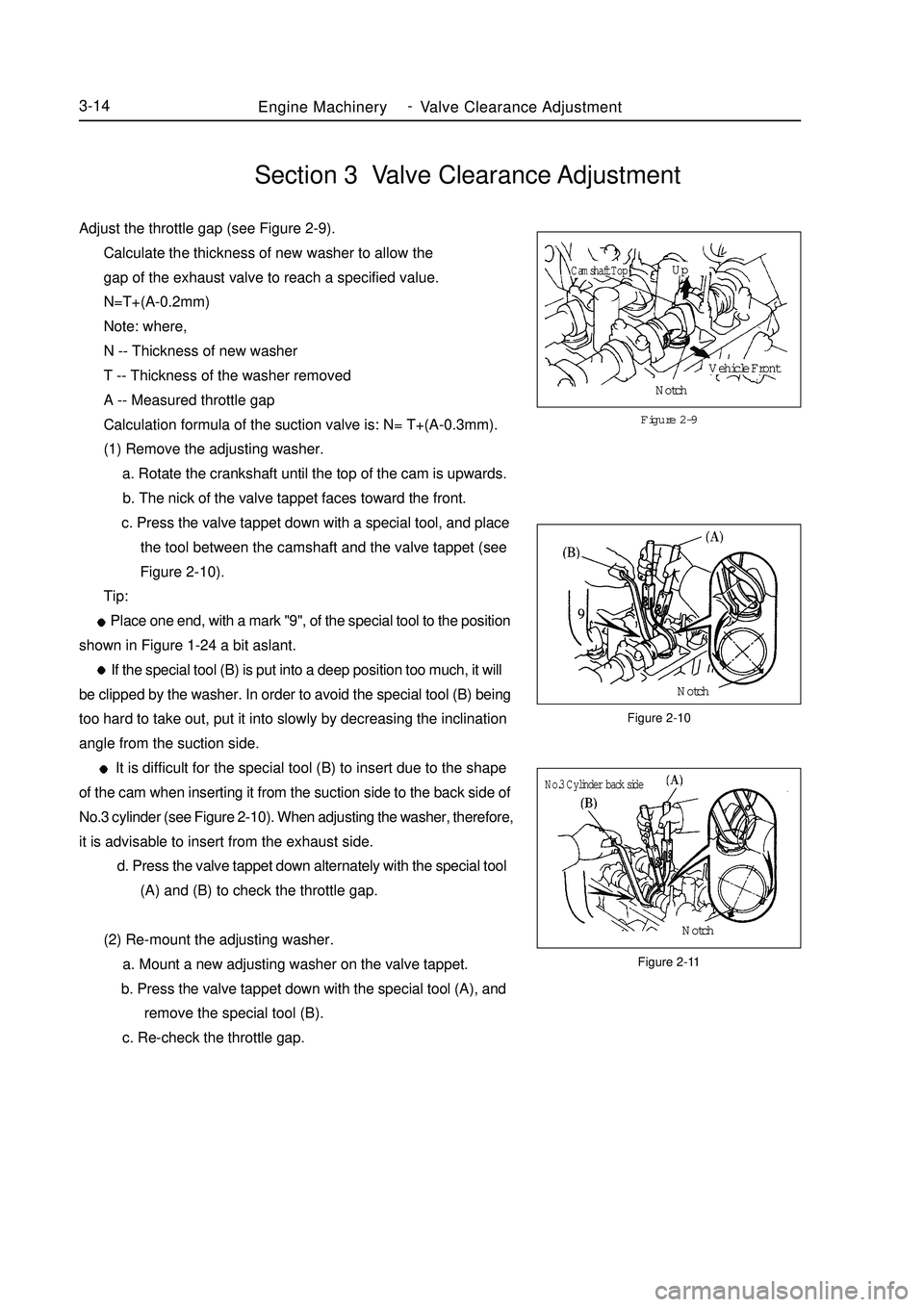
Section 3 Valve Clearance AdjustmentAdjust the throttle gap (see Figure 2-9).
Calculate the thickness of new washer to allow the
gap of the exhaust valve to reach a specified value.
N=T+(A-0.2mm)
Note: where,
N -- Thickness of new washer
T -- Thickness of the washer removed
A -- Measured throttle gap
Calculation formula of the suction valve is: N= T+(A-0.3mm).
(1) Remove the adjusting washer.
a. Rotate the crankshaft until the top of the cam is upwards.
b. The nick of the valve tappet faces toward the front.
c. Press the valve tappet down with a special tool, and place
the tool between the camshaft and the valve tappet (see
Figure 2-10).
Tip:
Place one end, with a mark "9", of the special tool to the position
shown in Figure 1-24 a bit aslant.
If the special tool (B) is put into a deep position too much, it will
be clipped by the washer. In order to avoid the special tool (B) being
too hard to take out, put it into slowly by decreasing the inclination
angle from the suction side.
It is difficult for the special tool (B) to insert due to the shape
of the cam when inserting it from the suction side to the back side of
No.3 cylinder (see Figure 2-10). When adjusting the washer, therefore,
it is advisable to insert from the exhaust side.
d. Press the valve tappet down alternately with the special tool
(A) and (B) to check the throttle gap.
(2) Re-mount the adjusting washer.
a. Mount a new adjusting washer on the valve tappet.
b. Press the valve tappet down with the special tool (A), and
remove the special tool (B).
c. Re-check the throttle gap.Figure 2-9
Figure 2-10
Figure 2-11Engine MachineryValve Clearance Adjustment3-14Camshaft TopUp
Vehicle Front
NotchNotchNotchNo.3 Cylinder back side -
Page 56 of 416
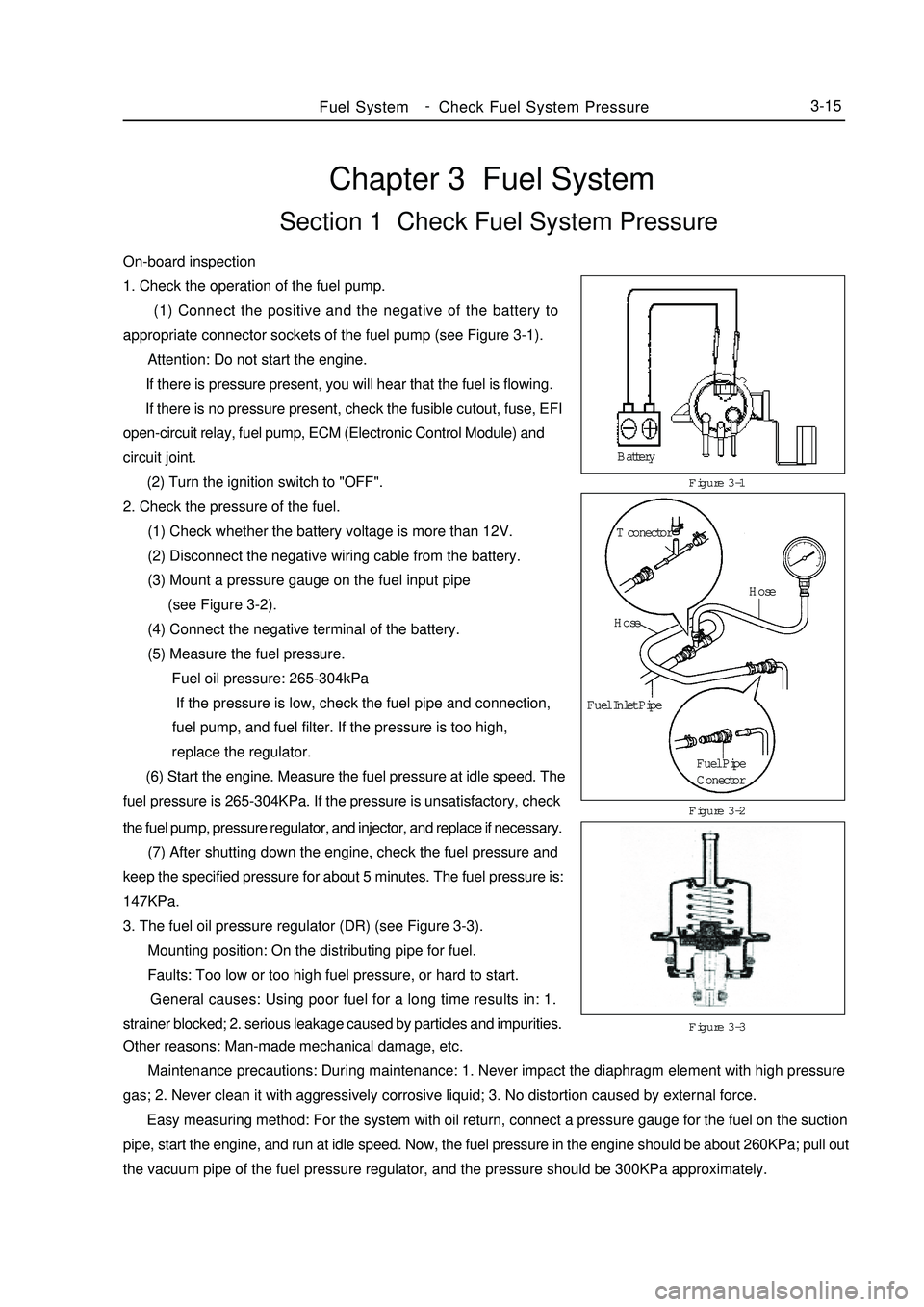
Chapter 3 Fuel SystemSection 1 Check Fuel System PressureOn-board inspection
1. Check the operation of the fuel pump.
(1) Connect the positive and the negative of the battery to
appropriate connector sockets of the fuel pump (see Figure 3-1).
Attention: Do not start the engine.
If there is pressure present, you will hear that the fuel is flowing.
If there is no pressure present, check the fusible cutout, fuse, EFI
open-circuit relay, fuel pump, ECM (Electronic Control Module) and
circuit joint.
(2) Turn the ignition switch to "OFF".
2. Check the pressure of the fuel.
(1) Check whether the battery voltage is more than 12V.
(2) Disconnect the negative wiring cable from the battery.
(3) Mount a pressure gauge on the fuel input pipe
(see Figure 3-2).
(4) Connect the negative terminal of the battery.
(5) Measure the fuel pressure.
Fuel oil pressure: 265-304kPa
If the pressure is low, check the fuel pipe and connection,
fuel pump, and fuel filter. If the pressure is too high,
replace the regulator.
(6) Start the engine. Measure the fuel pressure at idle speed. The
fuel pressure is 265-304KPa. If the pressure is unsatisfactory, checkFigure 3-1
Figure 3-3 Figure 3-2Fuel SystemCheck Fuel System Pressure3-15the fuel pump, pressure regulator, and injector, and replace if necessary.
(7) After shutting down the engine, check the fuel pressure and
keep the specified pressure for about 5 minutes. The fuel pressure is:
147KPa.
3. The fuel oil pressure regulator (DR) (see Figure 3-3).
Mounting position: On the distributing pipe for fuel.
Faults: Too low or too high fuel pressure, or hard to start.
General causes: Using poor fuel for a long time results in: 1.
strainer blocked; 2. serious leakage caused by particles and impurities.
Other reasons: Man-made mechanical damage, etc.
Maintenance precautions: During maintenance: 1. Never impact the diaphragm element with high pressure
gas; 2. Never clean it with aggressively corrosive liquid; 3. No distortion caused by external force.
Easy measuring method: For the system with oil return, connect a pressure gauge for the fuel on the suction
pipe, start the engine, and run at idle speed. Now, the fuel pressure in the engine should be about 260KPa; pull out
the vacuum pipe of the fuel pressure regulator, and the pressure should be 300KPa approximately.Battery
T conector
Hose
Hose
Fuel Inlet Pipe
Fuel Pipe
Conector -
Page 57 of 416
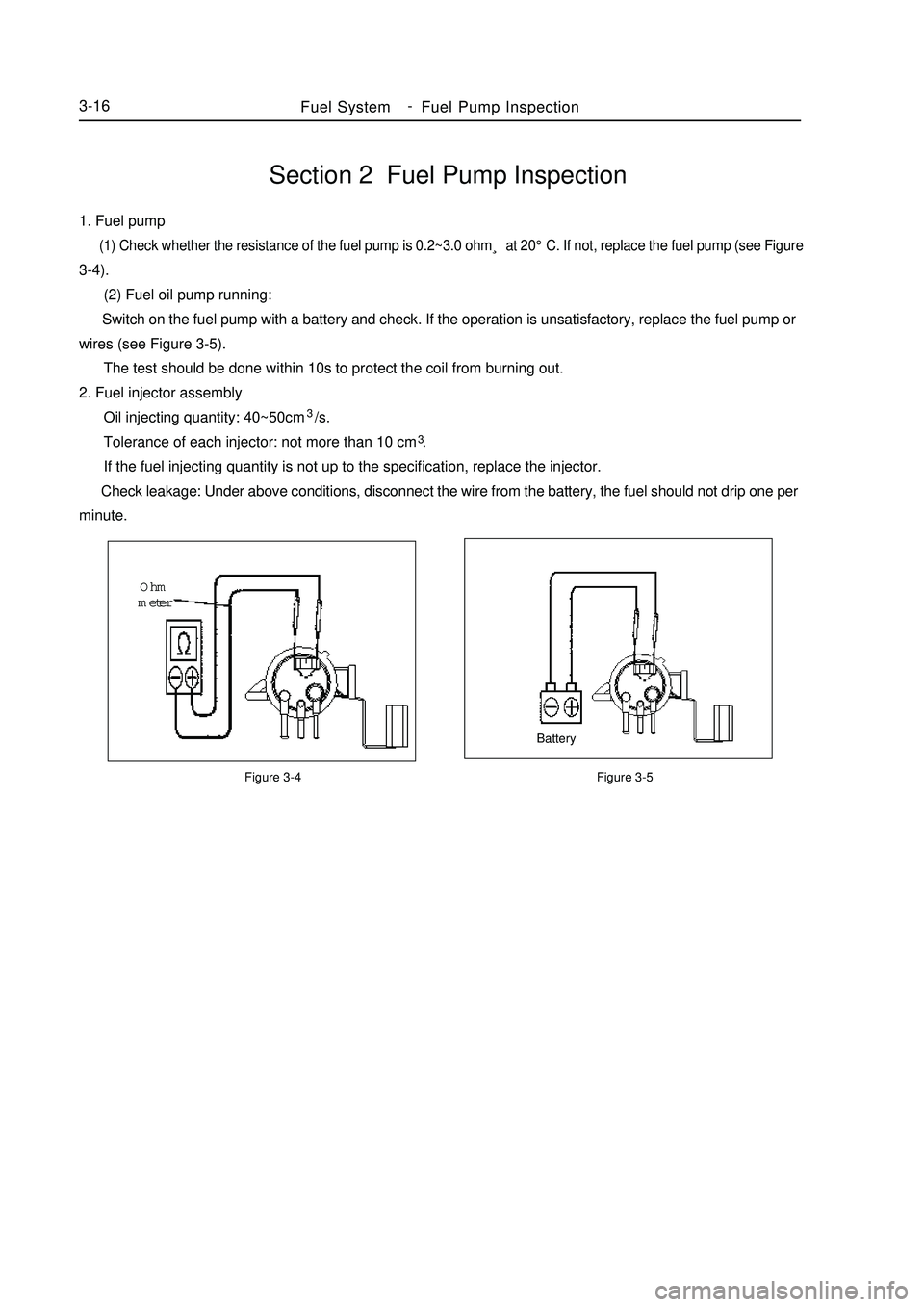
Section 2 Fuel Pump Inspection1. Fuel pump (1) Check whether the resistance of the fuel pump is 0.2~3.0 ohm¸ at 20°C. If not, replace the fuel pump (see Figure3-4).
(2) Fuel oil pump running:
Switch on the fuel pump with a battery and check. If the operation is unsatisfactory, replace the fuel pump or
wires (see Figure 3-5).
The test should be done within 10s to protect the coil from burning out.
2. Fuel injector assembly
Oil injecting quantity: 40~50cm3/s.
Tolerance of each injector: not more than 10 cm3.
If the fuel injecting quantity is not up to the specification, replace the injector.
Check leakage: Under above conditions, disconnect the wire from the battery, the fuel should not drip one per
minute.Figure 3-4 Figure 3-5BatteryOhm
meterFuel SystemFuel Pump Inspection3-16 -
Page 58 of 416
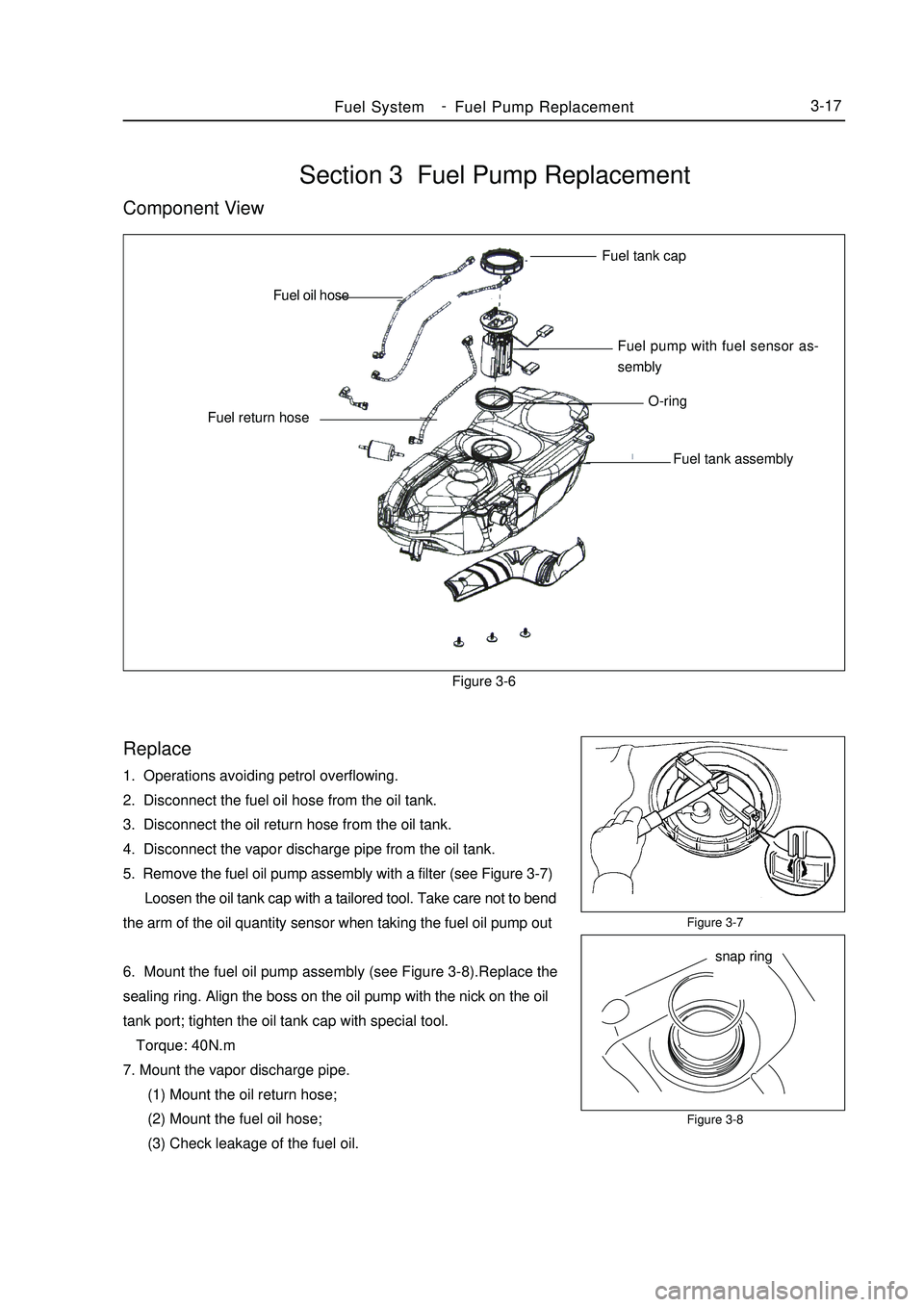
Section 3 Fuel Pump ReplacementComponent ViewFigure 3-6Replace1. Operations avoiding petrol overflowing.
2. Disconnect the fuel oil hose from the oil tank.
3. Disconnect the oil return hose from the oil tank.
4. Disconnect the vapor discharge pipe from the oil tank.
5. Remove the fuel oil pump assembly with a filter (see Figure 3-7)
Loosen the oil tank cap with a tailored tool. Take care not to bend
the arm of the oil quantity sensor when taking the fuel oil pump out
6. Mount the fuel oil pump assembly (see Figure 3-8).Replace the
sealing ring. Align the boss on the oil pump with the nick on the oil
tank port; tighten the oil tank cap with special tool.
Torque: 40N.m
7. Mount the vapor discharge pipe.
(1) Mount the oil return hose;
(2) Mount the fuel oil hose;
(3) Check leakage of the fuel oil.Figure 3-7
Figure 3-8Fuel SystemFuel Pump Replacement3-17Fuel tank cap
Fuel pump with fuel sensor as-
sembly
O-ring
Fuel tank assembly Fuel return hoseFuel oil hose
snap ring -
Page 59 of 416
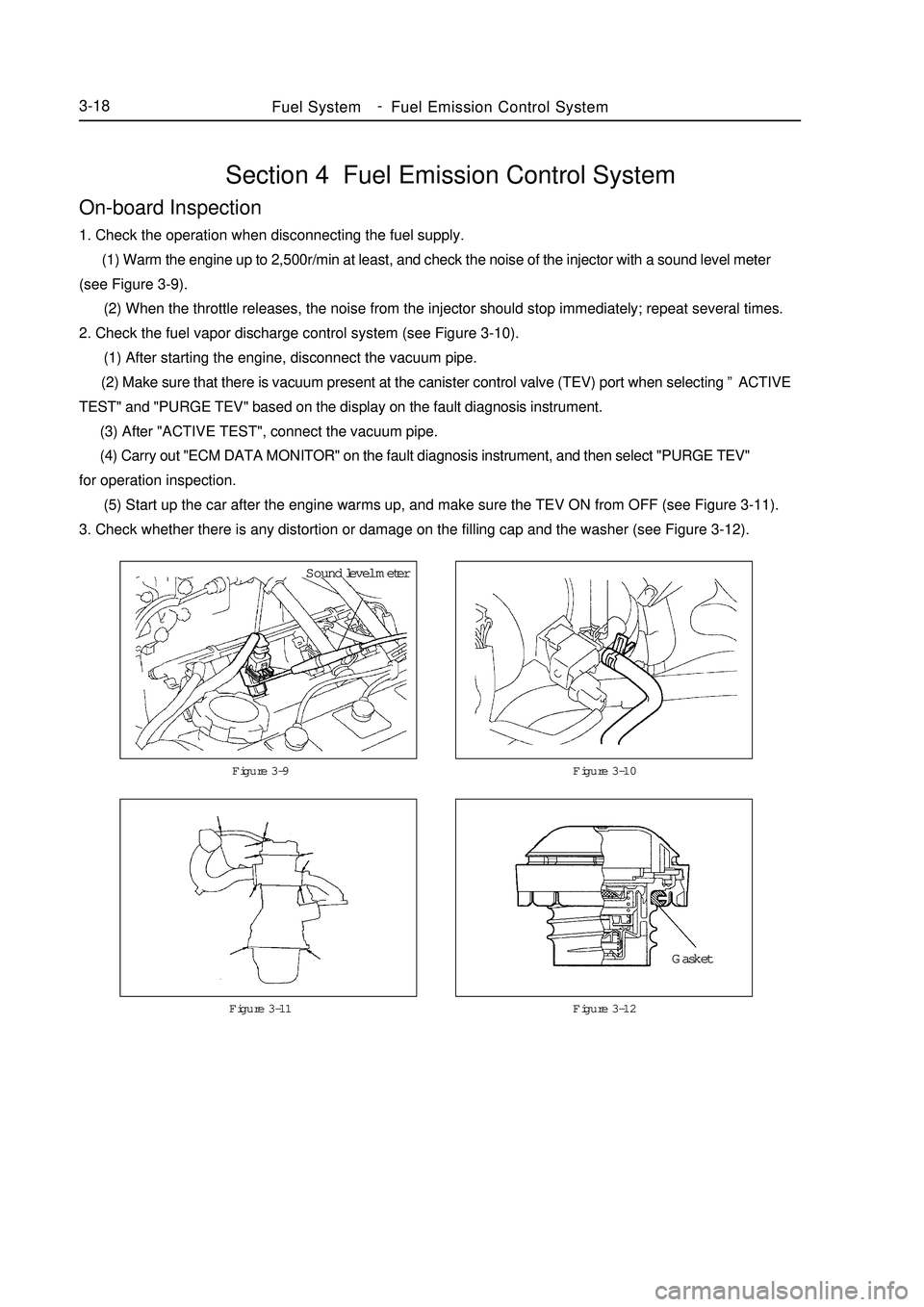
Section 4 Fuel Emission Control SystemOn-board Inspection1. Check the operation when disconnecting the fuel supply.
(1) Warm the engine up to 2,500r/min at least, and check the noise of the injector with a sound level meter
(see Figure 3-9).
(2) When the throttle releases, the noise from the injector should stop immediately; repeat several times.
2. Check the fuel vapor discharge control system (see Figure 3-10).
(1) After starting the engine, disconnect the vacuum pipe.
(2) Make sure that there is vacuum present at the canister control valve (TEV) port when selecting ”ACTIVE
TEST" and "PURGE TEV" based on the display on the fault diagnosis instrument.
(3) After "ACTIVE TEST", connect the vacuum pipe.
(4) Carry out "ECM DATA MONITOR" on the fault diagnosis instrument, and then select "PURGE TEV"
for operation inspection.
(5) Start up the car after the engine warms up, and make sure the TEV ON from OFF (see Figure 3-11).
3. Check whether there is any distortion or damage on the filling cap and the washer (see Figure 3-12).Figure 3-9 Figure 3-10Fuel SystemFuel Emission Control System3-18Figure 3-11 Figure 3-12Sound level meter
Gasket -
Page 60 of 416
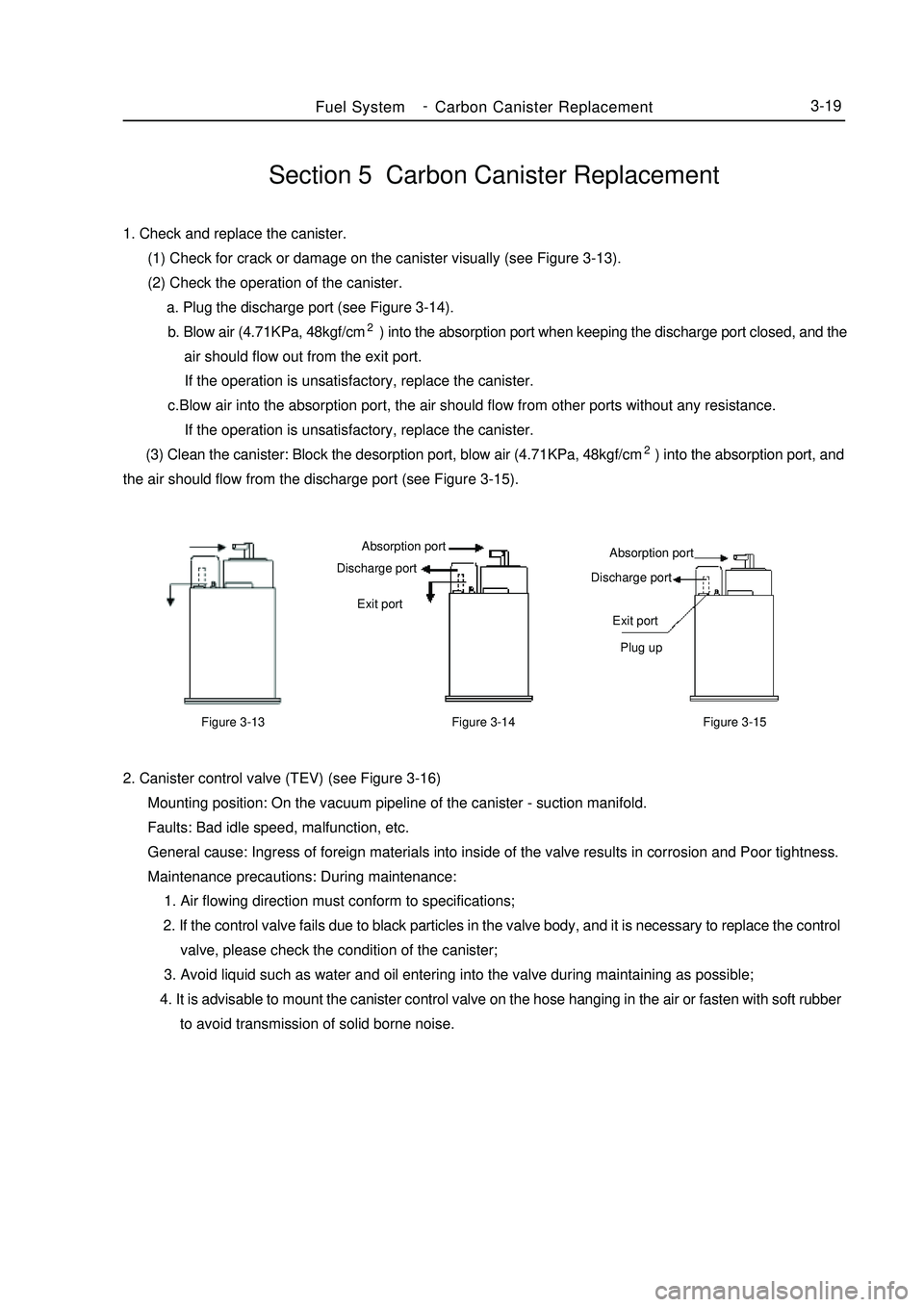
Section 5 Carbon Canister Replacement1. Check and replace the canister.
(1) Check for crack or damage on the canister visually (see Figure 3-13).
(2) Check the operation of the canister.
a. Plug the discharge port (see Figure 3-14).
b. Blow air (4.71KPa, 48kgf/cm2) into the absorption port when keeping the discharge port closed, and the
air should flow out from the exit port.
If the operation is unsatisfactory, replace the canister.
c.Blow air into the absorption port, the air should flow from other ports without any resistance.
If the operation is unsatisfactory, replace the canister.
(3) Clean the canister: Block the desorption port, blow air (4.71KPa, 48kgf/cm2) into the absorption port, and
the air should flow from the discharge port (see Figure 3-15).Fuel SystemCarbon Canister Replacement3-192. Canister control valve (TEV) (see Figure 3-16)
Mounting position: On the vacuum pipeline of the canister - suction manifold.
Faults: Bad idle speed, malfunction, etc.
General cause: Ingress of foreign materials into inside of the valve results in corrosion and Poor tightness.
Maintenance precautions: During maintenance:
1. Air flowing direction must conform to specifications;
2. If the control valve fails due to black particles in the valve body, and it is necessary to replace the control
valve, please check the condition of the canister;
3. Avoid liquid such as water and oil entering into the valve during maintaining as possible;
4. It is advisable to mount the canister control valve on the hose hanging in the air or fasten with soft rubber
to avoid transmission of solid borne noise.Figure 3-13Figure 3-15 Absorption port
Discharge port
Exit port
Plug upFigure 3-14Absorption port
Discharge port
Exit port -