Oil INFINITI M35 2006 Factory Service Manual
[x] Cancel search | Manufacturer: INFINITI, Model Year: 2006, Model line: M35, Model: INFINITI M35 2006Pages: 5621, PDF Size: 65.56 MB
Page 3428 of 5621

FSU-1
FRONT SUSPENSION
E SUSPENSION
CONTENTS
C
D
F
G
H
I
J
K
L
M
SECTION FSU
A
B
FSU
Revision: 2006 January2006 M35/M45
FRONT SUSPENSION
2WD
PRECAUTIONS .......................................................... 3
Caution ..................................................................... 3
PREPARATION ........................................................... 4
Special Service Tools [SST] ..................................... 4
Commercial Service Tools ........................................ 4
NOISE, VIBRATION AND HARSHNESS (NVH)
TROUBLESHOOTING ................................................ 5
NVH Troubleshooting Chart ..................................... 5
FRONT SUSPENSION ASSEMBLY ........................... 6
On-Vehicle Inspection and Service .......................... 6
INSPECTION OF LOWER BALL JOINT END
PLAY ..................................................................... 6
SHOCK ABSORBER INSPECTION ..................... 6
Wheel Alignment Inspection ..................................... 6
DESCRIPTION ...................................................... 6
PRELIMINARY CHECK ........................................ 6
GENERAL INFORMATION AND RECOMMEN-
DATIONS .............................................................. 6
THE ALIGNMENT PROCESS .............................. 7
INSPECTION OF CAMBER, CASTER AND
KINGPIN INCLINATION ANGLES ........................ 7
Components ............................................................. 8
Removal and Installation .......................................... 9
REMOVAL ........................................................
..... 9
INSTALLATION ................................................... 10
COIL SPRING AND SHOCK ABSORBER ................11
Removal and Installation ......................................... 11
REMOVAL ........................................................
.... 11
INSTALLATION .................................................... 11
Disassembly and Assembly .................................... 11
DISASSEMBLY .................................................... 11
INSPECTION AFTER DISASSEMBLY ............... 12
ASSEMBLY ......................................................... 12
TRANSVERSE LINK ................................................ 14
Removal and Installation ........................................ 14
REMOVAL ........................................................
... 14
INSPECTION AFTER REMOVAL ....................... 14
INSTALLATION ................................................... 15UPPER LINK ............................................................. 16
Removal and Installation ........................................ 16
REMOVAL ........................................................
... 16
INSPECTION AFTER REMOVAL ....................... 16
INSTALLATION ................................................... 16
STABILIZER BAR ..................................................... 18
Removal and Installation ........................................ 18
REMOVAL ........................................................
... 18
INSPECTION AFTER REMOVAL ....................... 18
INSTALLATION ................................................... 18
SERVICE DATA AND SPECIFICATIONS (SDS) ...... 19
Wheel Alignment (Unladen) .................................... 19
Ball Joint ....................................................
............. 19
Wheelarch Height (Unladen*) ................................. 19
AWD
PRECAUTIONS ........................................................ 20
Caution ................................................................... 20
PREPARATION ......................................................... 21
Special Service Tools [SST] ................................... 21
Commercial Service Tools ...................................... 21
NOISE, VIBRATION AND HARSHNESS (NVH)
TROUBLESHOOTING .............................................. 22
NVH Troubleshooting Chart ................................... 22
FRONT SUSPENSION ASSEMBLY ......................... 23
On-Vehicle Inspection and Service ......................... 23
INSPECTION OF LOWER BALL JOINT END
PLAY .................................................................... 23
SHOCK ABSORBER INSPECTION .................... 23
Wheel Alignment Inspection ................................... 23
DESCRIPTION .................................................... 23
PRELIMINARY CHECK ....................................... 23
GENERAL INFORMATION AND RECOMMEN-
DATIONS ............................................................. 23
THE ALIGNMENT PROCESS ............................. 24
INSPECTION OF CAMBER, CASTER AND
KINGPIN INCLINATION ANGLES ....................... 24
Page 3429 of 5621
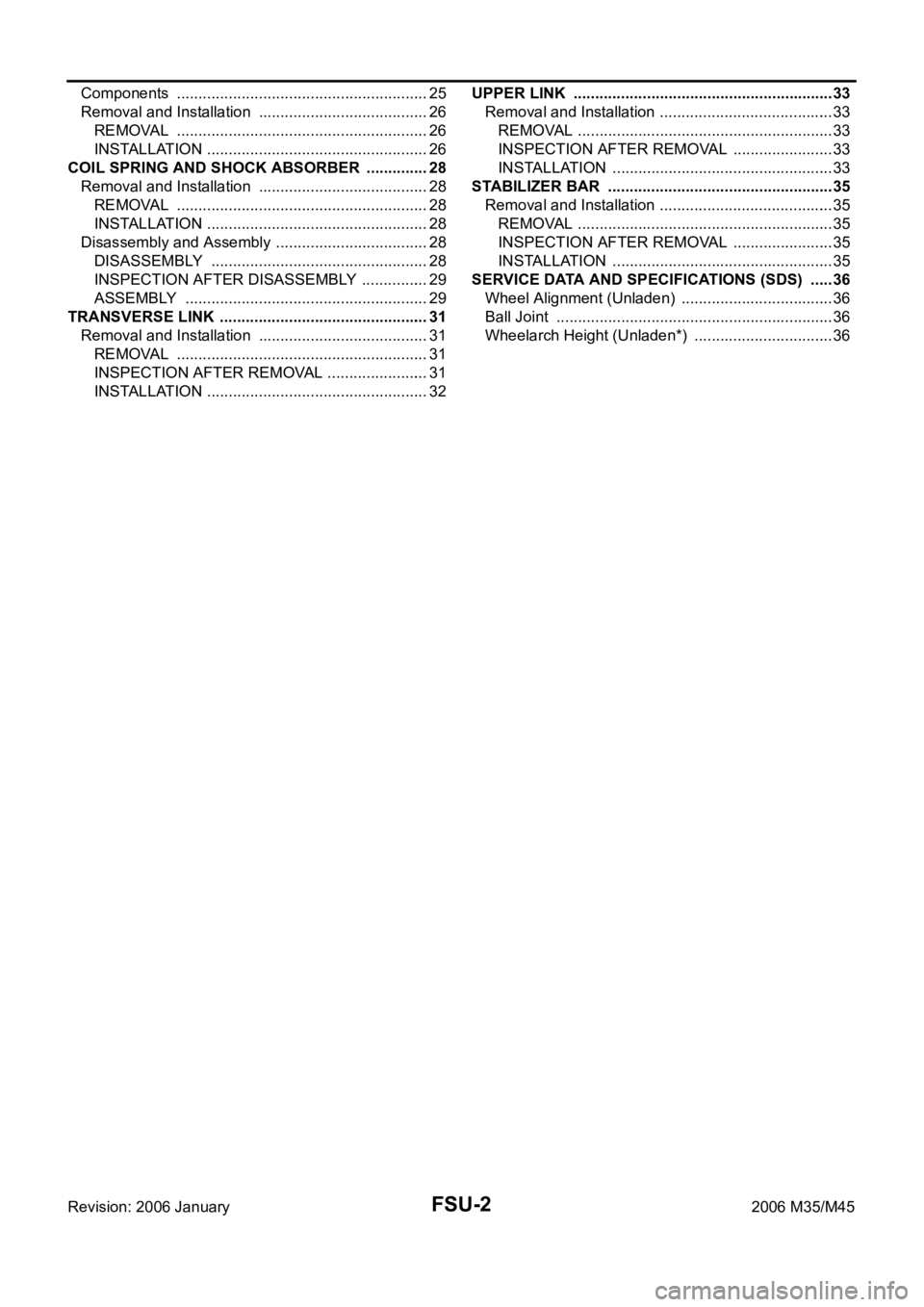
FSU-2Revision: 2006 January2006 M35/M45 Components ........................................................... 25
Removal and Installation ........................................ 26
REMOVAL ........................................................
... 26
INSTALLATION .................................................... 26
COIL SPRING AND SHOCK ABSORBER ............... 28
Removal and Installation ........................................ 28
REMOVAL ........................................................
... 28
INSTALLATION .................................................... 28
Disassembly and Assembly .................................... 28
DISASSEMBLY ................................................... 28
INSPECTION AFTER DISASSEMBLY ................ 29
ASSEMBLY ......................................................... 29
TRANSVERSE LINK ................................................. 31
Removal and Installation ........................................ 31
REMOVAL ........................................................
... 31
INSPECTION AFTER REMOVAL ........................ 31
INSTALLATION .................................................... 32UPPER LINK ............................................................. 33
Removal and Installation ......................................... 33
REMOVAL ............................................................ 33
INSPECTION AFTER REMOVAL ........................ 33
INSTALLATION .................................................... 33
STABILIZER BAR ..................................................... 35
Removal and Installation ......................................... 35
REMOVAL ............................................................ 35
INSPECTION AFTER REMOVAL ........................ 35
INSTALLATION .................................................... 35
SERVICE DATA AND SPECIFICATIONS (SDS) ...... 36
Wheel Alignment (Unladen) .................................... 36
Ball Joint ................................................................. 36
Wheelarch Height (Unladen*) ................................. 36
Page 3430 of 5621
![INFINITI M35 2006 Factory Service Manual PRECAUTIONS
FSU-3
[2WD]
C
D
F
G
H
I
J
K
L
MA
B
FSU
Revision: 2006 January2006 M35/M45
[2WD]PRECAUTIONSPFP:00001
CautionNES000I6
When installing rubber bushings, the final tightening must be c INFINITI M35 2006 Factory Service Manual PRECAUTIONS
FSU-3
[2WD]
C
D
F
G
H
I
J
K
L
MA
B
FSU
Revision: 2006 January2006 M35/M45
[2WD]PRECAUTIONSPFP:00001
CautionNES000I6
When installing rubber bushings, the final tightening must be c](/img/42/57023/w960_57023-3429.png)
PRECAUTIONS
FSU-3
[2WD]
C
D
F
G
H
I
J
K
L
MA
B
FSU
Revision: 2006 January2006 M35/M45
[2WD]PRECAUTIONSPFP:00001
CautionNES000I6
When installing rubber bushings, the final tightening must be carried out under unladen conditions with
tires on ground. Oil might shorten the life of rubber bushings. Be sure to wipe off any spilled oil.
–Unladen conditions mean that fuel, engine coolant and lubricant are full. Spare tire, jack, hand tools and
mats are in designated positions.
After servicing suspension parts, be sure to check wheel alignment.
Self-lock nuts are not reusable. Always use new ones when installing. Since new self-lock nuts are pre-
oiled, tighten as they are.
Page 3431 of 5621
![INFINITI M35 2006 Factory Service Manual FSU-4
[2WD]
PREPARATION
Revision: 2006 January2006 M35/M45
PREPARATIONPFP:00002
Special Service Tools [SST]NES000I7
The actual shapes of Kent-Moore tools may differ from those of special service tools INFINITI M35 2006 Factory Service Manual FSU-4
[2WD]
PREPARATION
Revision: 2006 January2006 M35/M45
PREPARATIONPFP:00002
Special Service Tools [SST]NES000I7
The actual shapes of Kent-Moore tools may differ from those of special service tools](/img/42/57023/w960_57023-3430.png)
FSU-4
[2WD]
PREPARATION
Revision: 2006 January2006 M35/M45
PREPARATIONPFP:00002
Special Service Tools [SST]NES000I7
The actual shapes of Kent-Moore tools may differ from those of special service tools illustrated here.
Commercial Service ToolsNES000I8
Tool number
(Kent-Moore No.)
Tool nameDescription
KV991040S0
(—)
CCK gauge attachment
1. Plate
2. Guide bolt
3. Nut
4. Spring
5. Center plate
6. KV99104020 Adapter A
a: 72 mm (2.83 in) dia.
7. KV99104030 Adapter B
b: 65 mm (2.56 in) dia.
8. KV99104040 Adapter C
c: 57 mm (2.24 in) dia.
9. KV99104050 Adapter D
d: 53.4 mm (2.102 in) dia.Measuring wheel alignment
ST35652000
(—)
Strut attachmentDisassembling and assembling shock
absorber
ST3127S000
(See J-25765-A)
Preload Gauge
1. GG91030000
(J-25765-A)
Torque wrench
2. HT62940000
(—)
Socket adapter
3. HT62900000
(—)
Socket adapterMeasuring rotating torque of ball joint
S-NT498
ZZA0807D
NT124
Tool nameDescription
Power tool
Removing wheel nuts
Removing torque member fixing bolts
Removing undercover
Removing front suspension compo-
nents parts
Removing hub lock nut
Spring compressor Removing and installing coil springPBIC0190E
S-NT717
Page 3433 of 5621
![INFINITI M35 2006 Factory Service Manual FSU-6
[2WD]
FRONT SUSPENSION ASSEMBLY
Revision: 2006 January2006 M35/M45
FRONT SUSPENSION ASSEMBLYPFP:54010
On-Vehicle Inspection and ServiceNES000IA
Make sure the mounting conditions (looseness, INFINITI M35 2006 Factory Service Manual FSU-6
[2WD]
FRONT SUSPENSION ASSEMBLY
Revision: 2006 January2006 M35/M45
FRONT SUSPENSION ASSEMBLYPFP:54010
On-Vehicle Inspection and ServiceNES000IA
Make sure the mounting conditions (looseness,](/img/42/57023/w960_57023-3432.png)
FSU-6
[2WD]
FRONT SUSPENSION ASSEMBLY
Revision: 2006 January2006 M35/M45
FRONT SUSPENSION ASSEMBLYPFP:54010
On-Vehicle Inspection and ServiceNES000IA
Make sure the mounting conditions (looseness, back lash) of each component and component conditions
(wear, damage) are normal.
INSPECTION OF LOWER BALL JOINT END PLAY
1. Set front wheels in a straight-ahead position. Do not depress brake pedal.
2. Place an iron bar or similar tool between transverse link and steering knuckle.
3. Measure axial end play by prying it up and down.
CAUTION:
Be careful not to damage ball joint boot. Do not damage the installation position by applying
excessive force.
SHOCK ABSORBER INSPECTION
Check for oil leakage, damage and breakage of installation positions.
Wheel Alignment InspectionNES000IB
DESCRIPTION
Measure wheel alignment under unladen conditions.
NOTE:
“Unladen conditions” means that fuel, engine coolant, and lubricant are full. Spare tire, jack, hand tools and
mats are in designated positions.
PRELIMINARY CHECK
Check the following:
1. Tires for improper air pressure and wear.
2. Road wheels for runout. Refer to WT-6, "
ROAD WHEEL" .
3. Wheel bearing axial end play. Refer to FAX-5, "
WHEEL BEARING INSPECTION" .
4. Transverse link ball joint axial end play. Refer to FSU-14, "
INSPECTION AFTER REMOVAL" .
5. Shock absorber operation.
6. Each mounting part of axle and suspension for looseness and deformation.
7. Each of suspension member, shock absorber, upper link and transverse link for cracks, deformation and
other damage.
8. Vehicle height (posture).
GENERAL INFORMATION AND RECOMMENDATIONS
A four-wheel thrust alignment should be performed.
–This type of alignment is recommended for any NISSAN/INFINITI vehicle.
–The four-wheel “thrust” process helps ensure that the vehicle is properly aligned and the steering wheel is
centered.
–The alignment rack itself should be capable of accepting any NISSAN/INFINITI vehicle.
–The rack should be checked to ensure that it is level.
Make sure the machine is properly calibrated.
–Your alignment equipment should be regularly calibrated in order to give correct information.
–Check with the manufacturer of your specific equipment for their recommended Service/Calibration
Schedule.Axial end play : 0 mm (0 in)
Page 3436 of 5621
![INFINITI M35 2006 Factory Service Manual FRONT SUSPENSION ASSEMBLY
FSU-9
[2WD]
C
D
F
G
H
I
J
K
L
MA
B
FSU
Revision: 2006 January2006 M35/M45
Refer to GI section for symbol marks in the figure. Refer to GI-9, "HOW TO USE THIS MANUAL" INFINITI M35 2006 Factory Service Manual FRONT SUSPENSION ASSEMBLY
FSU-9
[2WD]
C
D
F
G
H
I
J
K
L
MA
B
FSU
Revision: 2006 January2006 M35/M45
Refer to GI section for symbol marks in the figure. Refer to GI-9, "HOW TO USE THIS MANUAL"](/img/42/57023/w960_57023-3435.png)
FRONT SUSPENSION ASSEMBLY
FSU-9
[2WD]
C
D
F
G
H
I
J
K
L
MA
B
FSU
Revision: 2006 January2006 M35/M45
Refer to GI section for symbol marks in the figure. Refer to GI-9, "HOW TO USE THIS MANUAL" .
Removal and Installation NES000ID
REMOVAL
1. For VK45DE engine models, disconnect related electric wires and hoses from engine assembly to remove
front suspension member with engine assembly. Refer to EM-244, "
ENGINE ASSEMBLY" .
2. Remove cowl top panel and hood. Refer to EI-18, "
COWL TOP" , EI-17, "HOOD" .
3. For VQ35DE engine models, install engine slinger, and then hoist engine. Refer to EM-113, "
Removal and
Installation (2WD Models)" .
4. Remove tires from vehicle with a power tool.
5. Remove wheel sensor from steering knuckle. Refer to BRC-57, "
WHEEL SENSOR" .
CAUTION:
Do not pull on wheel sensor harness.
6. Remove brake hose bracket. Refer to BR-12, "
BRAKE TUBE AND HOSE" .
7. Remove undercover with a power tool.
8. Remove cotter pin (1), and then loosen the nut.
9. Remove steering outer socket (2) from steering knuckle (3) so
as not to damage ball joint boot (4) using the ball joint remover
(suitable tool).
CAUTION:
Temporarily tighten the nut to prevent damage to threads
and to prevent the ball joint remover (suitable tool) from
suddenly coming off.
10. Remove the mounting nut on the upper side of stabilizer con-
necting rod with a power tool, and then remove stabilizer con-
necting rod from transverse link.
11. Separate steering gear assembly and lower joint. Refer to PS-13, "
STEERING COLUMN" .
12. Remove rack stay. Refer to FSU-8, "
Components" .
13. Remove steering hydraulic piping bracket from front suspension member. Refer to PS-38, "
HYDRAULIC
LINE" .
14. Remove the mounting nut and bolt on the lower side of shock absorber with a power tool, and then
remove shock absorber from transverse link.
15. Remove cotter pin of transverse link and steering knuckle, and then loosen nut.
16. Set jack under front suspension member.
17. Remove transverse link from steering knuckle so as not to damage ball joint boot using the ball joint
remover (suitable tool)
CAUTION:
Temporarily tighten the nut to prevent damage to threads and to prevent ball joint remover (suit-
able tool) from suddenly coming off.
18. Remove the mounting nuts of engine mounting insulator. Refer to EM-113, "
ENGINE ASSEMBLY" .
19. Remove the mounting bolts of member bracket, and then remove member bracket from front suspension
member with a power tool. Refer to FSU-8, "
Components" .
20. Remove the mounting nut and bolts of member stay, and then remove member stay from front suspension
member and vehicle with a power tool.
21. Remove the mounting nut of front suspension member with a power tool. Refer to FSU-8, "
Components" .
22. For VQ35DE engine models, gradually lower a jack to remove front suspension assembly from vehicle.
1. Shock absorber mounting bracket 2. Bound bumper 3. Rubber seat
4. Coil spring 5. Shock absorber 6. Upper link
7. Steering knuckle 8. Transverse link 9. Washer
10. Steering stopper bracket 11. Stabilizer connecting rod 12. Stabilizer bar
13. Stabilizer bushing 14. Stabilizer clamp 15. Front suspension member
16. Rack stay 17. Member stay 18. Member bracket
19. Clamp 20. Cotter pin 21. Stopper rubber
SGIA1183E
Page 3438 of 5621
![INFINITI M35 2006 Factory Service Manual COIL SPRING AND SHOCK ABSORBER
FSU-11
[2WD]
C
D
F
G
H
I
J
K
L
MA
B
FSU
Revision: 2006 January2006 M35/M45
COIL SPRING AND SHOCK ABSORBERPFP:55302
Removal and InstallationNES000IE
REMOVAL
1. Remove tir INFINITI M35 2006 Factory Service Manual COIL SPRING AND SHOCK ABSORBER
FSU-11
[2WD]
C
D
F
G
H
I
J
K
L
MA
B
FSU
Revision: 2006 January2006 M35/M45
COIL SPRING AND SHOCK ABSORBERPFP:55302
Removal and InstallationNES000IE
REMOVAL
1. Remove tir](/img/42/57023/w960_57023-3437.png)
COIL SPRING AND SHOCK ABSORBER
FSU-11
[2WD]
C
D
F
G
H
I
J
K
L
MA
B
FSU
Revision: 2006 January2006 M35/M45
COIL SPRING AND SHOCK ABSORBERPFP:55302
Removal and InstallationNES000IE
REMOVAL
1. Remove tires from vehicle with a power tool.
2. Remove harness of wheel sensor from shock absorber. Refer to BRC-57, "
WHEEL SENSOR" .
CAUTION:
Do not pull on wheel sensor harness.
3. Remove brake hose bracket. Refer to BR-12, "
BRAKE TUBE AND HOSE" .
4. Remove the mounting nut on the upper side of stabilizer connecting rod with a power tool, and then
remove stabilizer connecting rod from transverse link.
5. Remove mounting nut and bolt on the lower side of shock absorber with a power tool, and then remove
shock absorber from transverse link.
6. Remove cotter pin of transverse link and steering knuckle, and then loosen nut.
7. Remove transverse link from steering knuckle so as not to damage ball joint boot using the ball joint
remover (suitable tool).
CAUTION:
Temporarily tighten the nut to prevent damage to threads and to prevent ball joint remover (suit-
able tool) from suddenly coming off.
8. Remove the mounting nuts of shock absorber mounting bracket, then remove shock absorber from vehi-
cle.
INSTALLATION
Installation is the reverse order of removal. For tightening torque, refer to FSU-8, "Components" .
Perform final tightening of bolt and nut at the shock absorber lower side (rubber bushing), under unladen
conditions with tires on level ground. Check wheel alignment. Refer to FSU-6, "
Wheel Alignment Inspec-
tion" .
Adjust neutral position of steering angle sensor after checking wheel alignment. Refer to BRC-6, "Adjust-
ment of Steering Angle Sensor Neutral Position" .
Check wheel sensor harness for proper connection. Refer to BRC-57, "WHEEL SENSOR" .
Disassembly and AssemblyNES000IF
DISASSEMBLY
CAUTION:
Do not damage shock absorber piston rod when removing components from shock absorber.
1. Install strut attachment [SST] to shock absorber and secure it in
a vise.
CAUTION:
When installing the strut attachment to shock absorber,
wrap a shop cloth around strut to protect it from damage.
SEIA0296E
Page 3439 of 5621
![INFINITI M35 2006 Factory Service Manual FSU-12
[2WD]
COIL SPRING AND SHOCK ABSORBER
Revision: 2006 January2006 M35/M45
2. Using a spring compressor (commercial service tool), compress
coil spring between rubber seat and spring lower seat (o INFINITI M35 2006 Factory Service Manual FSU-12
[2WD]
COIL SPRING AND SHOCK ABSORBER
Revision: 2006 January2006 M35/M45
2. Using a spring compressor (commercial service tool), compress
coil spring between rubber seat and spring lower seat (o](/img/42/57023/w960_57023-3438.png)
FSU-12
[2WD]
COIL SPRING AND SHOCK ABSORBER
Revision: 2006 January2006 M35/M45
2. Using a spring compressor (commercial service tool), compress
coil spring between rubber seat and spring lower seat (on shock
absorber) until coil spring with a spring compressor is free.
CAUTION:
Be sure a spring compressor is securely attached coil
spring. Compress coil spring
3. Make sure coil spring with a spring compressor between rubber
seat and spring lower seat (shock absorber) is free and then
remove piston rod lock nut while securing the piston rod tip so
that piston rod does not turn.
4. Remove shock absorber mounting bracket, rubber seat, bound
bumper from shock absorber.
5. Remove coil spring with a spring compressor, and then gradually release a spring compressor.
CAUTION:
Loosen while making sure coil spring attachment position does not move.
6. Remove the strut attachment from shock absorber.
INSPECTION AFTER DISASSEMBLY
Shock Absorber Inspection
Check the following:
Shock absorber for deformation, cracks or damage, and replace it if a malfunction is detected.
Piston rod for damage, uneven wear or distortion, and replace it if a malfunction is detected.
For oil leakage, and replace it if a malfunction is detected.
Shock Absorber Mounting Bracket and Rubber Parts Inspection
Check shock absorber mounting bracket for cracks and rubber parts for wear. Replace it if a malfunction is
detected.
Coil Spring Inspection
Check coil spring for cracks, wear or damage, and replace it if a malfunction is detected.
ASSEMBLY
CAUTION:
Do not damage shock absorber piston rod when installing components to shock absorber.
1. Install strut attachment [SST] to shock absorber and secure it in
a vise.
CAUTION:
When installing the strut attachment to shock absorber,
wrap a shop cloth around strut to protect it from damage.
2. Compress coil spring using a spring compressor (commercial
service tool), and install it onto shock absorber.
SEIA0297E
SEIA0296E
SEIA0297E
Page 3440 of 5621
![INFINITI M35 2006 Factory Service Manual COIL SPRING AND SHOCK ABSORBER
FSU-13
[2WD]
C
D
F
G
H
I
J
K
L
MA
B
FSU
Revision: 2006 January2006 M35/M45
CAUTION:
Install coil spring as shown in the figure with large diame-
ter side [100 mm (3.94 i INFINITI M35 2006 Factory Service Manual COIL SPRING AND SHOCK ABSORBER
FSU-13
[2WD]
C
D
F
G
H
I
J
K
L
MA
B
FSU
Revision: 2006 January2006 M35/M45
CAUTION:
Install coil spring as shown in the figure with large diame-
ter side [100 mm (3.94 i](/img/42/57023/w960_57023-3439.png)
COIL SPRING AND SHOCK ABSORBER
FSU-13
[2WD]
C
D
F
G
H
I
J
K
L
MA
B
FSU
Revision: 2006 January2006 M35/M45
CAUTION:
Install coil spring as shown in the figure with large diame-
ter side [100 mm (3.94 in)] up and small diameter side [90
mm (3.54 in)] down. (Distinction marks are 4.75 and 5.75
turn from the lower side end.)
Be sure a spring compress or is securely attached to coil
spring. Compress coil spring.
3. Apply soapy water to bound bumper. Insert bound bumper into
shock absorber mounting bracket, and then install it to shock
absorber together with rubber seat.
CAUTION:
Do not use machine oil.
Install shock absorber mounting bracket as shown in the fig-
ure.
CAUTION:
Coil spring is securely seated in spring mounting groove
of rubber seat.
The bottom part of spring should be at the position of A
point of spring seat.
4. Secure piston rod tip so that piston rod does not turn, then
tighten piston rod lock nut with specified torque.
5. Gradually release a spring compressor, and remove coil spring.
CAUTION:
Loosen while making sure coil spring attachment position
does not move.
6. Remove the strut attachment from shock absorber.
SEIA0661E
SEIA0662E
Page 3443 of 5621
![INFINITI M35 2006 Factory Service Manual FSU-16
[2WD]
UPPER LINK
Revision: 2006 January2006 M35/M45
UPPER LINKPFP:54524
Removal and InstallationNES000IH
REMOVAL
1. Remove tires from vehicle with a power tool.
2. Remove shock absorber. Refer INFINITI M35 2006 Factory Service Manual FSU-16
[2WD]
UPPER LINK
Revision: 2006 January2006 M35/M45
UPPER LINKPFP:54524
Removal and InstallationNES000IH
REMOVAL
1. Remove tires from vehicle with a power tool.
2. Remove shock absorber. Refer](/img/42/57023/w960_57023-3442.png)
FSU-16
[2WD]
UPPER LINK
Revision: 2006 January2006 M35/M45
UPPER LINKPFP:54524
Removal and InstallationNES000IH
REMOVAL
1. Remove tires from vehicle with a power tool.
2. Remove shock absorber. Refer to FSU-11, "
COIL SPRING AND SHOCK ABSORBER" .
3. Remove mounting nut and bolt with a power tool, and then remove upper link from steering knuckle.
4. Remove mounting nuts and bolts, and then remove upper link and stopper rubber from vehicle.
INSPECTION AFTER REMOVAL
Visual Inspection
Check the following:
Upper link and bushing for deformation, cracks or damage. Replace it if a malfunction is detected.
Ball joint boot for cracks or other damage, and also for grease leakage. Replace it if a malfunction is
detected.
Ball Joint Inspection
Manually move ball stud to confirm it moves smoothly with no binding.
Swing Torque Inspection
NOTE:
Before measurement, move ball stud at least ten times by hand to check for smooth movement.
Hook a spring balance at cutout on ball stud. Confirm spring bal-
ance measurement value is within specifications when ball stud
begins moving.
If it is outside the specified range, replace upper link assembly.
Rotating Torque Inspection
Attach mounting nut to ball stud. Make sure that rotating torque
is within specifications with a preload gauge [SST].
If it is outside the specified range, replace upper link assembly.
Axial End Play Inspection
Move tip of ball stud in axial direction to check for looseness.
If it is outside the specified range, replace upper link assembly.
INSTALLATION
Installation is the reverse order of removal. For tightening torque, refer to FSU-8, "Components" .
Perform final tightening of bolts and nuts at the vehicle installation position (rubber bushing) under
unladen conditions with tires on level ground. Check wheel alignment. Refer to FSU-6, "
Wheel Alignment
Inspection" . Swing torque
: 0 - 2.0 Nꞏm (0 - 0.2 kg-m, 0 - 17 in-lb)
Spring balance measurement
: 0 - 61.5 N (0 - 6.2 kg, 0 - 13.6 lb)
SEIA0523E
Rotating torque
: 0 - 2.0 Nꞏm (0 - 0.2 kg-m, 0 - 17 in-lb)
SDIA1150E
Axial end play : 0 mm (0 in)