engine oil INFINITI QX56 2008 Factory Workshop Manual
[x] Cancel search | Manufacturer: INFINITI, Model Year: 2008, Model line: QX56, Model: INFINITI QX56 2008Pages: 4083, PDF Size: 81.73 MB
Page 1799 of 4083
![INFINITI QX56 2008 Factory Workshop Manual EC-500
< ON-VEHICLE REPAIR >[VK56DE]
INTAKE VALVE TIMING CONTROL
INTAKE VALVE TIMING CONTROL
Intake Valve Timing Control Solenoid Valve (LH)INFOID:0000000001830643
REMOVAL
1. Remove engine room cover INFINITI QX56 2008 Factory Workshop Manual EC-500
< ON-VEHICLE REPAIR >[VK56DE]
INTAKE VALVE TIMING CONTROL
INTAKE VALVE TIMING CONTROL
Intake Valve Timing Control Solenoid Valve (LH)INFOID:0000000001830643
REMOVAL
1. Remove engine room cover](/img/42/57030/w960_57030-1798.png)
EC-500
< ON-VEHICLE REPAIR >[VK56DE]
INTAKE VALVE TIMING CONTROL
INTAKE VALVE TIMING CONTROL
Intake Valve Timing Control Solenoid Valve (LH)INFOID:0000000001830643
REMOVAL
1. Remove engine room cover using power tool. Refer to
EM-24, "Removal and Installation".
2. Remove air duct and resonator assembly. Refer to EM-24, "
Removal and Installation".
3. Remove drive belt. Refer to EM-13, "
Removal and Installation".
4. Disconnect Intake valve timing controlintake valve timing control solenoid valve connector (LH).
5. Remove Intake valve timing control solenoid valve (LH) (2) from Intake valve timing control solenoid valve cover (LH) (1).
INSTALLATION
Installation is in the reverse order of removal.
CAUTION:
Replace the O-ring (3) of the Intake valve timing co ntrol solenoid valve with a new one, then lubricate
O-ring with engine oil before installing.
Intake Valve Timing Control Solenoid Valve (RH)INFOID:0000000001830644
REMOVAL
1. Remove drive belt. Refer to EM-13, "Removal and Installation".
2. Disconnect Intake valve timing control solenoid valve connector (RH).
3. Remove Intake valve timing control solenoid valve (RH) (3) from Intake valve timing control solenoid valve cover (RH) (1).
INSTALLATION
Installation is in the reverse order of removal.
CAUTION:
Replace the O-ring (2) of the Intake valve timing co ntrol solenoid valve with a new one, then lubricate
O-ring with engine oil before installing.
AWBIA0145ZZ
Intake valve timing control sole-
noid valve bolt : 9.6 N·m (0.98 kg-m, 85 in-lb)
AWBIA0144ZZ
Intake valve timing control sole-
noid valve bolt: 9.6 N·m (0.98 kg-m, 85 in-lb)
Revision: March 2010
2008 QX56
Page 1800 of 4083
![INFINITI QX56 2008 Factory Workshop Manual INTAKE VALVE TIMING CONTROLEC-501
< ON-VEHICLE REPAIR > [VK56DE]
C
D
E
F
G H
I
J
K L
M A
EC
NP
O
Intake Valve Timing Control Position Sensor (LH)INFOID:0000000001830645
REMOVAL
1. Remove engine room c INFINITI QX56 2008 Factory Workshop Manual INTAKE VALVE TIMING CONTROLEC-501
< ON-VEHICLE REPAIR > [VK56DE]
C
D
E
F
G H
I
J
K L
M A
EC
NP
O
Intake Valve Timing Control Position Sensor (LH)INFOID:0000000001830645
REMOVAL
1. Remove engine room c](/img/42/57030/w960_57030-1799.png)
INTAKE VALVE TIMING CONTROLEC-501
< ON-VEHICLE REPAIR > [VK56DE]
C
D
E
F
G H
I
J
K L
M A
EC
NP
O
Intake Valve Timing Control Position Sensor (LH)INFOID:0000000001830645
REMOVAL
1. Remove engine room cover using power tool. Refer to
EM-24, "Removal and Installation".
2. Remove air duct and resonator assembly. Refer to EM-25, "
Removal and Installation".
3. Disconnect intake valve timing control position sensor connector (LH).
4. Remove intake valve timing control position sensor (LH) (1) from Intake valve timing control solenoid valve cover (LH) (3).
INSTALLATION
Installation is in the reverse order of removal.
CAUTION:
Replace the O-ring (2) of the intake valve timing control position sensor with a new one, then lubricate
O-ring with engine oil before installing.
Intake Valve Timing Cont rol Position Sensor (RH)INFOID:0000000001830646
REMOVAL
1. Remove engine room cover using power tool. Refer to EM-24, "Removal and Installation".
2. Disconnect intake valve timing control position sensor connector (RH).
3. Remove intake valve timing control position sensor (RH) (1) from Intake valve timing control solenoid valve cover (RH) (3).
INSTALLATION
Installation is in the reverse order of removal.
CAUTION:
Replace the O-ring (2) of the intake valve timing control position sensor with a new one, then lubricate
O-ring with engine oil before installing.
Camshaft Position Sensor (PHASE)INFOID:0000000001830647
REMOVAL
1. Remove engine room cover using power tool. Refer to EM-24, "Removal and Installation".
2. Remove air duct and resonator assembly. Refer to EM-25, "
Removal and Installation".
3. Disconnect camshaft position sensor connector.
AWBIA0141ZZ
Intake valve timing control position sensor bolt : 9.6 N·m (0.98 kg-m, 85 in-lb)
AWBIA0143ZZ
Intake valve timing control position sensor bolt : 9.6 N·m (0.98 kg-m, 85 in-lb)
Revision: March 2010 2008 QX56
Page 1801 of 4083
![INFINITI QX56 2008 Factory Workshop Manual EC-502
< ON-VEHICLE REPAIR >[VK56DE]
INTAKE VALVE TIMING CONTROL
4. Remove camshaft position sensor (2) from Intake valve timing
control solenoid valve cover (LH) (1).
INSTALLATION
Installation is in INFINITI QX56 2008 Factory Workshop Manual EC-502
< ON-VEHICLE REPAIR >[VK56DE]
INTAKE VALVE TIMING CONTROL
4. Remove camshaft position sensor (2) from Intake valve timing
control solenoid valve cover (LH) (1).
INSTALLATION
Installation is in](/img/42/57030/w960_57030-1800.png)
EC-502
< ON-VEHICLE REPAIR >[VK56DE]
INTAKE VALVE TIMING CONTROL
4. Remove camshaft position sensor (2) from Intake valve timing
control solenoid valve cover (LH) (1).
INSTALLATION
Installation is in the reverse order of removal.
CAUTION:
Replace the O-ring (3) of the cam shaft position sensor with a new on e, then lubricate O-ring with
engine oil before installing.
AWBIA0142ZZ
Camshaft position sensor bolt : 9.6 N·m (0.98 kg-m, 85 in-lb)
Revision: March 2010 2008 QX56
Page 1804 of 4083
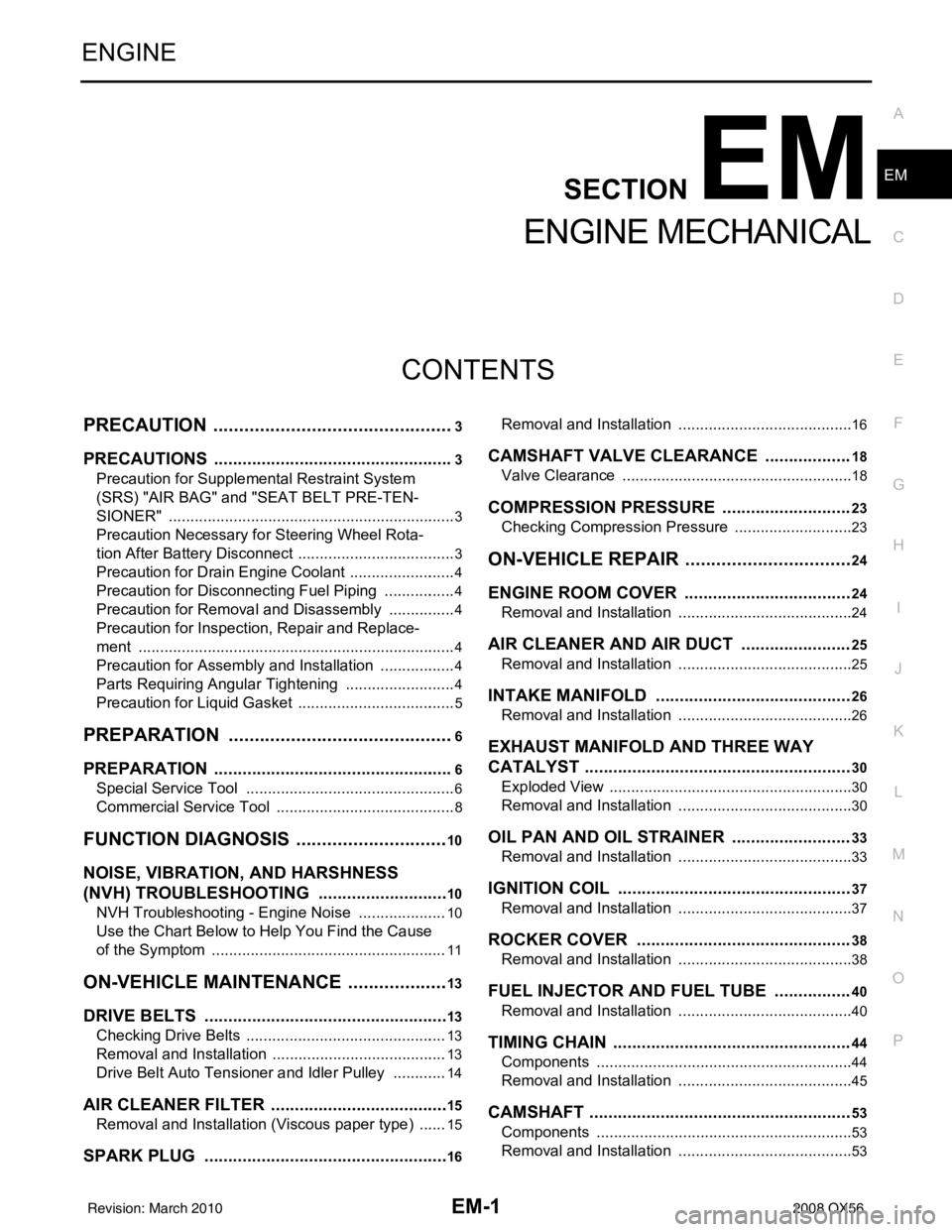
EM-1
ENGINE
C
DE
F
G H
I
J
K L
M
SECTION EM
A
EM
N
O P
CONTENTS
ENGINE MECHANICAL
PRECAUTION ....... ........................................3
PRECAUTIONS .............................................. .....3
Precaution for Supplemental Restraint System
(SRS) "AIR BAG" and "SEAT BELT PRE-TEN-
SIONER" ............................................................. ......
3
Precaution Necessary for Steering Wheel Rota-
tion After Battery Disconnect ............................... ......
3
Precaution for Drain Engine Coolant .........................4
Precaution for Disconnecting Fuel Piping .................4
Precaution for Removal and Disassembly ................4
Precaution for Inspection, Repair and Replace-
ment .................................................................... ......
4
Precaution for Assembly and Installation ..................4
Parts Requiring Angular Tightening ..........................4
Precaution for Liquid Gasket ............................... ......5
PREPARATION ............................................6
PREPARATION .............................................. .....6
Special Service Tool ........................................... ......6
Commercial Service Tool ..........................................8
FUNCTION DIAGNOSIS ..............................10
NOISE, VIBRATION, AND HARSHNESS
(NVH) TROUBLESHOOTING ........................ ....
10
NVH Troubleshooting - Engine Noise ................. ....10
Use the Chart Below to Help You Find the Cause
of the Symptom .......................................................
11
ON-VEHICLE MAINTENANCE ....................13
DRIVE BELTS ................................................ ....13
Checking Drive Belts ........................................... ....13
Removal and Installation .........................................13
Drive Belt Auto Tensioner and Idler Pulley ......... ....14
AIR CLEANER FILTER ......................................15
Removal and Installation (Viscous paper type) ... ....15
SPARK PLUG ................................................ ....16
Removal and Installation ..................................... ....16
CAMSHAFT VALVE CLEARANCE ..................18
Valve Clearance ......................................................18
COMPRESSION PRESSURE ...........................23
Checking Compression Pressure ............................23
ON-VEHICLE REPAIR .................................24
ENGINE ROOM COVER ...................................24
Removal and Installation ..................................... ....24
AIR CLEANER AND AIR DUCT .......................25
Removal and Installation .........................................25
INTAKE MANIFOLD .........................................26
Removal and Installation .........................................26
EXHAUST MANIFOLD AND THREE WAY
CATALYST ........................................................
30
Exploded View .........................................................30
Removal and Installation .........................................30
OIL PAN AND OIL STRAINER .........................33
Removal and Installation .........................................33
IGNITION COIL .................................................37
Removal and Installation .........................................37
ROCKER COVER .............................................38
Removal and Installation .........................................38
FUEL INJECTOR AND FUEL TUBE ................40
Removal and Installation .........................................40
TIMING CHAIN ..................................................44
Components ........................................................ ....44
Removal and Installation .........................................45
CAMSHAFT .......................................................53
Components ............................................................53
Removal and Installation .........................................53
Revision: March 2010 2008 QX56
Page 1805 of 4083
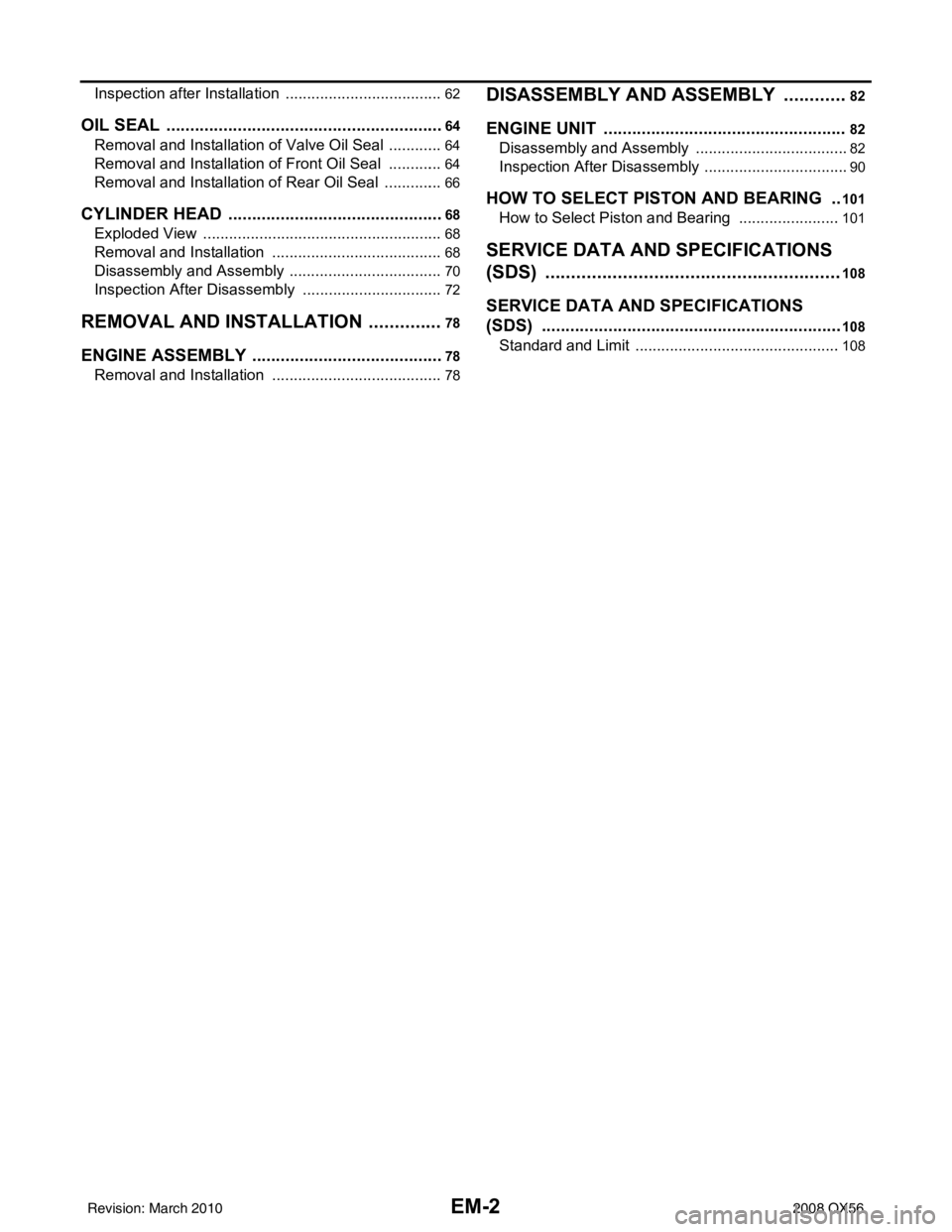
EM-2
Inspection after Installation .....................................62
OIL SEAL ........................................................ ...64
Removal and Installation of Valve Oil Seal .......... ...64
Removal and Installation of Front Oil Seal .............64
Removal and Installation of Rear Oil Seal ..............66
CYLINDER HEAD ..............................................68
Exploded View ..................................................... ...68
Removal and Installation ........................................68
Disassembly and Assembly ....................................70
Inspection After Disassembly .................................72
REMOVAL AND INSTAL LATION ...............78
ENGINE ASSEMBLY ...................................... ...78
Removal and Installation ..................................... ...78
DISASSEMBLY AND ASSEMBLY ............82
ENGINE UNIT ....................................................82
Disassembly and Assembly ................................. ...82
Inspection After Disassembly ..................................90
HOW TO SELECT PISTON AND BEARING ...101
How to Select Piston and Bearing ....................... .101
SERVICE DATA AND SPECIFICATIONS
(SDS) ........ .................................................
108
SERVICE DATA AND SPECIFICATIONS
(SDS) .............................................................. ..
108
Standard and Limit ............................................... .108
Revision: March 2010 2008 QX56
Page 1807 of 4083
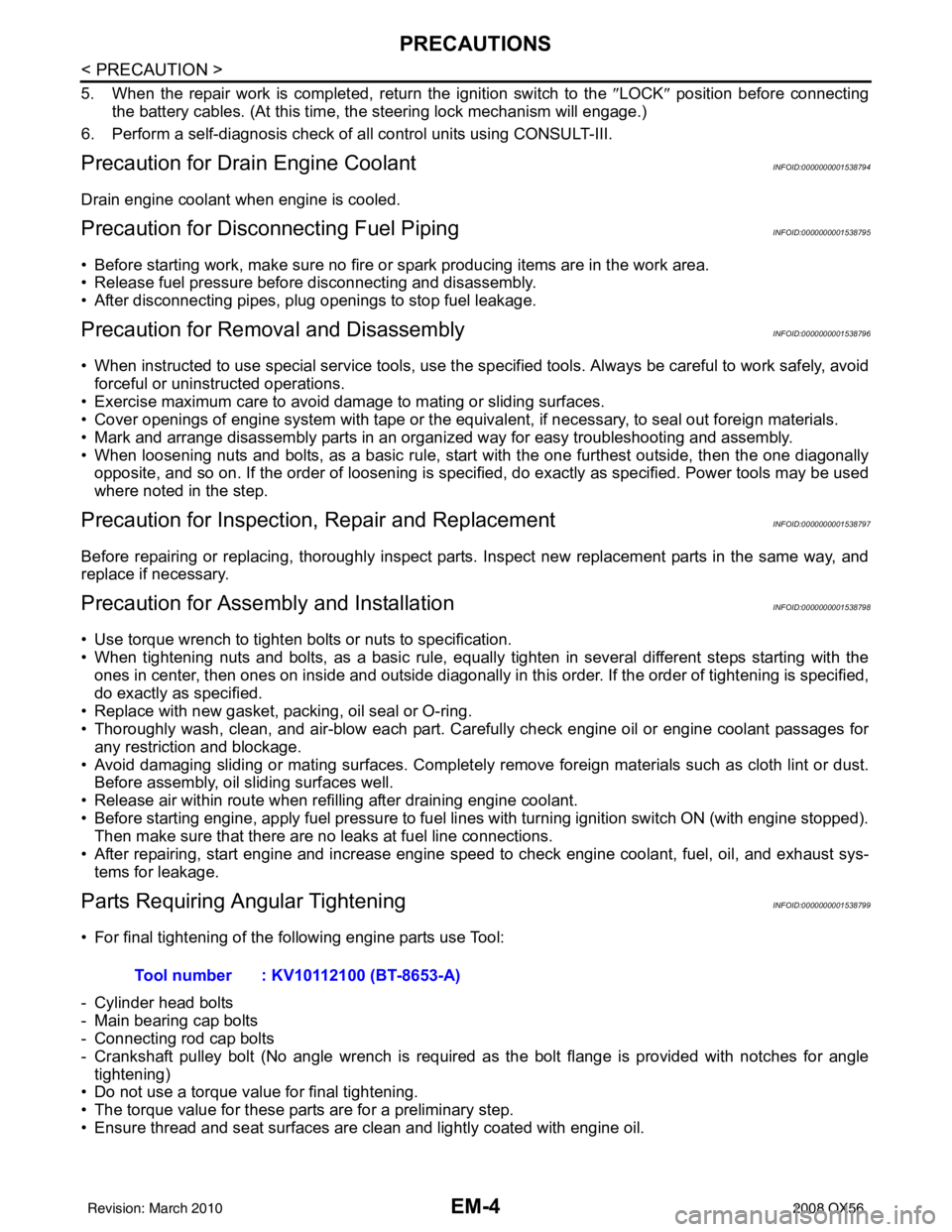
EM-4
< PRECAUTION >
PRECAUTIONS
5. When the repair work is completed, return the ignition switch to the ″LOCK ″ position before connecting
the battery cables. (At this time, the steering lock mechanism will engage.)
6. Perform a self-diagnosis check of a ll control units using CONSULT-III.
Precaution for Drain Engine CoolantINFOID:0000000001538794
Drain engine coolant when engine is cooled.
Precaution for Disconnecting Fuel PipingINFOID:0000000001538795
• Before starting work, make sure no fire or spark producing items are in the work area.
• Release fuel pressure before disconnecting and disassembly.
• After disconnecting pipes, plug openings to stop fuel leakage.
Precaution for Removal and DisassemblyINFOID:0000000001538796
• When instructed to use special service tools, use the s pecified tools. Always be careful to work safely, avoid
forceful or uninstructed operations.
• Exercise maximum care to avoid damage to mating or sliding surfaces.
• Cover openings of engine system with tape or the equivalent, if necessary, to seal out foreign materials.
• Mark and arrange disassembly parts in an organi zed way for easy troubleshooting and assembly.
• When loosening nuts and bolts, as a basic rule, start with the one furthest outside, then the one diagonally opposite, and so on. If the order of loosening is specified, do exactly as specified. Power tools may be used
where noted in the step.
Precaution for Inspection, Repair and ReplacementINFOID:0000000001538797
Before repairing or replacing, thoroughly inspect parts. Inspect new replacement parts in the same way, and
replace if necessary.
Precaution for Assembly and InstallationINFOID:0000000001538798
• Use torque wrench to tighten bolts or nuts to specification.
• When tightening nuts and bolts, as a basic rule, equally tighten in several different steps starting with theones in center, then ones on inside and outside diagonally in this order. If the order of tightening is specified,
do exactly as specified.
• Replace with new gasket, packing, oil seal or O-ring.
• Thoroughly wash, clean, and air-blow each part. Carefully check engine oil or engine coolant passages for any restriction and blockage.
• Avoid damaging sliding or mating surfaces. Completely remove foreign materials such as cloth lint or dust. Before assembly, oil sliding surfaces well.
• Release air within route when refilling after draining engine coolant.
• Before starting engine, apply fuel pressure to fuel lines with turning ignition switch ON (with engine stopped). Then make sure that there are no leaks at fuel line connections.
• After repairing, start engine and increase engine s peed to check engine coolant, fuel, oil, and exhaust sys-
tems for leakage.
Parts Requiring Angular TighteningINFOID:0000000001538799
• For final tightening of the following engine parts use Tool:
- Cylinder head bolts
- Main bearing cap bolts
- Connecting rod cap bolts
- Crankshaft pulley bolt (No angle wrench is required as the bolt flange is provided with notches for angle tightening)
• Do not use a torque value for final tightening.
• The torque value for these parts are for a preliminary step.
• Ensure thread and seat surfaces are clean and lightly coated with engine oil. Tool number : KV10112100 (BT-8653-A)
Revision: March 2010
2008 QX56
Page 1808 of 4083
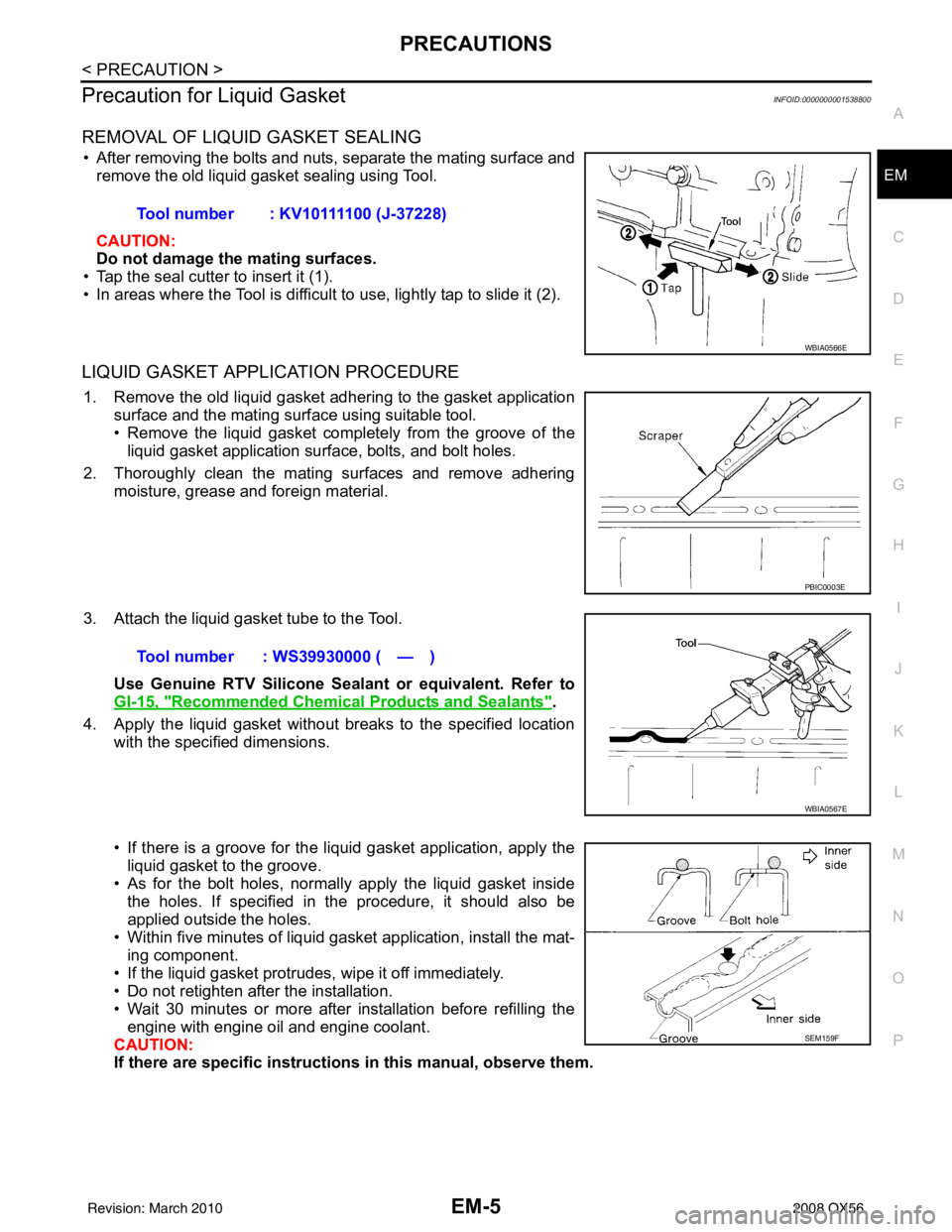
PRECAUTIONSEM-5
< PRECAUTION >
C
DE
F
G H
I
J
K L
M A
EM
NP
O
Precaution for Liquid GasketINFOID:0000000001538800
REMOVAL OF LIQUID GASKET SEALING
• After removing the bolts and nuts, separate the mating surface and
remove the old liquid gasket sealing using Tool.
CAUTION:
Do not damage the mating surfaces.
• Tap the seal cutter to insert it (1).
• In areas where the Tool is difficult to use, lightly tap to slide it (2).
LIQUID GASKET APPLICATION PROCEDURE
1. Remove the old liquid gasket adhering to the gasket application surface and the mating surface using suitable tool.
• Remove the liquid gasket completely from the groove of the
liquid gasket application surface, bolts, and bolt holes.
2. Thoroughly clean the mating surfaces and remove adhering moisture, grease and foreign material.
3. Attach the liquid gasket tube to the Tool. Use Genuine RTV Silicone Sealant or equivalent. Refer to
GI-15, "
Recommended Chemical Products and Sealants".
4. Apply the liquid gasket without breaks to the specified location with the specified dimensions.
• If there is a groove for the liquid gasket application, apply theliquid gasket to the groove.
• As for the bolt holes, normally apply the liquid gasket inside
the holes. If specified in the procedure, it should also be
applied outside the holes.
• Within five minutes of liquid gasket application, install the mat-
ing component.
• If the liquid gasket protrudes, wipe it off immediately.
• Do not retighten after the installation.
• Wait 30 minutes or more after installation before refilling the engine with engine oil and engine coolant.
CAUTION:
If there are specific instructions in this manual, observe them.
Tool number : KV10111100 (J-37228)
WBIA0566E
PBIC0003E
Tool number : WS39930000 ( — )
WBIA0567E
SEM159F
Revision: March 2010
2008 QX56
Page 1814 of 4083
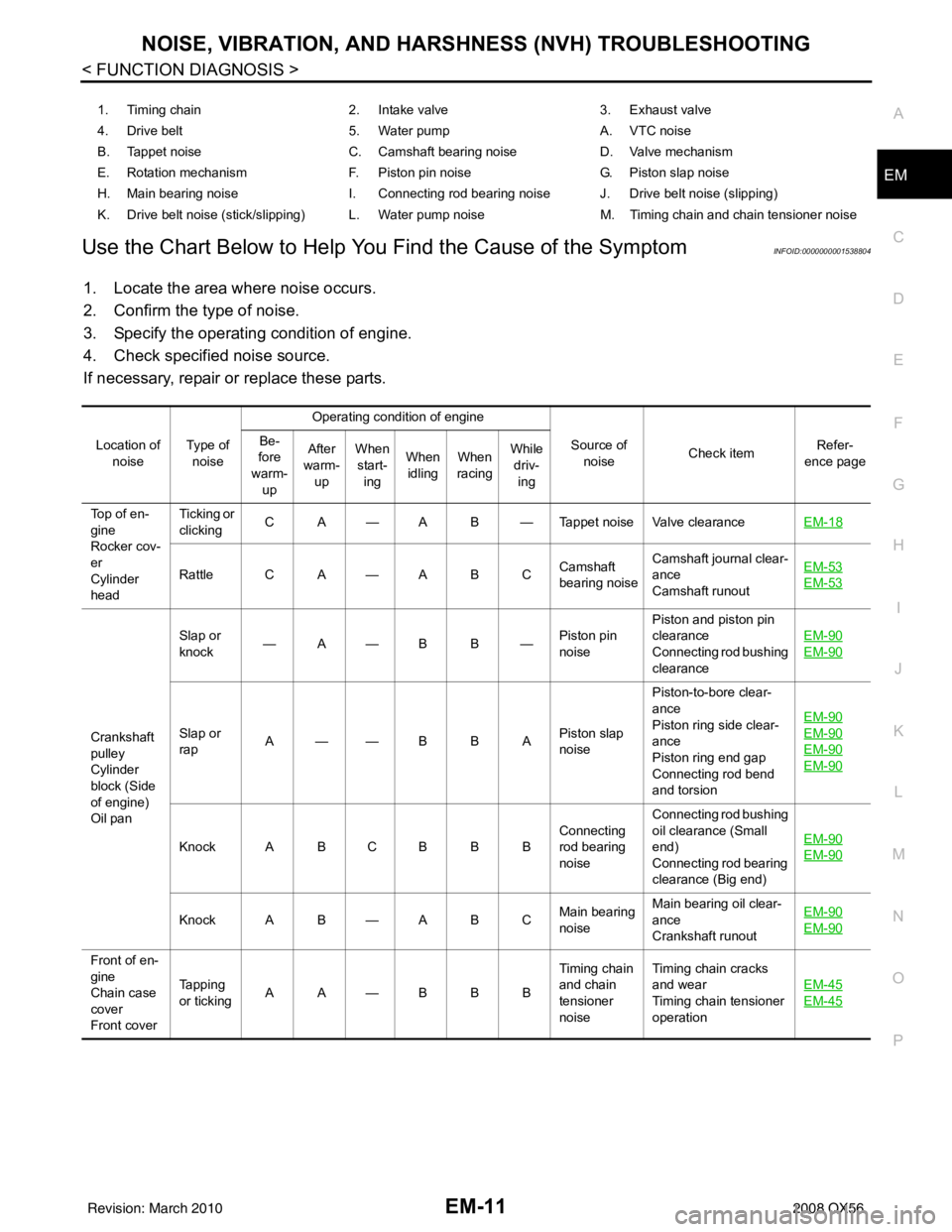
NOISE, VIBRATION, AND HARSHNESS (NVH) TROUBLESHOOTINGEM-11
< FUNCTION DIAGNOSIS >
C
DE
F
G H
I
J
K L
M A
EM
NP
O
Use the Chart Below to Help You
Find the Cause of the SymptomINFOID:0000000001538804
1. Locate the area where noise occurs.
2. Confirm the type of noise.
3. Specify the operating condition of engine.
4. Check specified noise source.
If necessary, repair or replace these parts.
1. Timing chain 2. Intake valve3. Exhaust valve
4. Drive belt 5. Water pumpA. VTC noise
B. Tappet noise C. Camshaft bearing noiseD. Valve mechanism
E. Rotation mechanism F. Piston pin noise G. Piston slap noise
H. Main bearing noise I. Connecting rod bearing noise J. Drive belt noise (slipping)
K. Drive belt noise (stick/slipping) L. Water pump noise M. Timing chain and chain tensioner noise
Location of noise Ty p e o f
noise Operating condition of engine
Source of noise Check item Refer-
ence page
Be-
fore
warm-
up After
warm- up When
start- ing When
idling When
racing While
driv- ing
Top of en-
gine
Rocker cov-
er
Cylinder
head Ticking or
clicking
C A — A B — Tappet noise Valve clearance
EM-18
Rattle C A — A B CCamshaft
bearing noiseCamshaft journal clear-
ance
Camshaft runout EM-53EM-53
Crankshaft
pulley
Cylinder
block (Side
of engine)
Oil panSlap or
knock
—A—B B—
Piston pin
noisePiston and piston pin
clearance
Connecting rod bushing
clearance
EM-90
EM-90
Slap or
rap
A——B B A
Piston slap
noisePiston-to-bore clear-
ance
Piston ring side clear-
ance
Piston ring end gap
Connecting rod bend
and torsion EM-90EM-90
EM-90
EM-90
Knock A B C B B B
Connecting
rod bearing
noiseConnecting rod bushing
oil clearance (Small
end)
Connecting rod bearing
clearance (Big end)
EM-90EM-90
Knock A B — A B C
Main bearing
noiseMain bearing oil clear-
ance
Crankshaft runout EM-90EM-90
Front of en-
gine
Chain case
cover
Front coverTapping
or ticking
AA—BBB Timing chain
and chain
tensioner
noiseTiming chain cracks
and wear
Timing chain tensioner
operation
EM-45
EM-45
Revision: March 2010
2008 QX56
Page 1819 of 4083
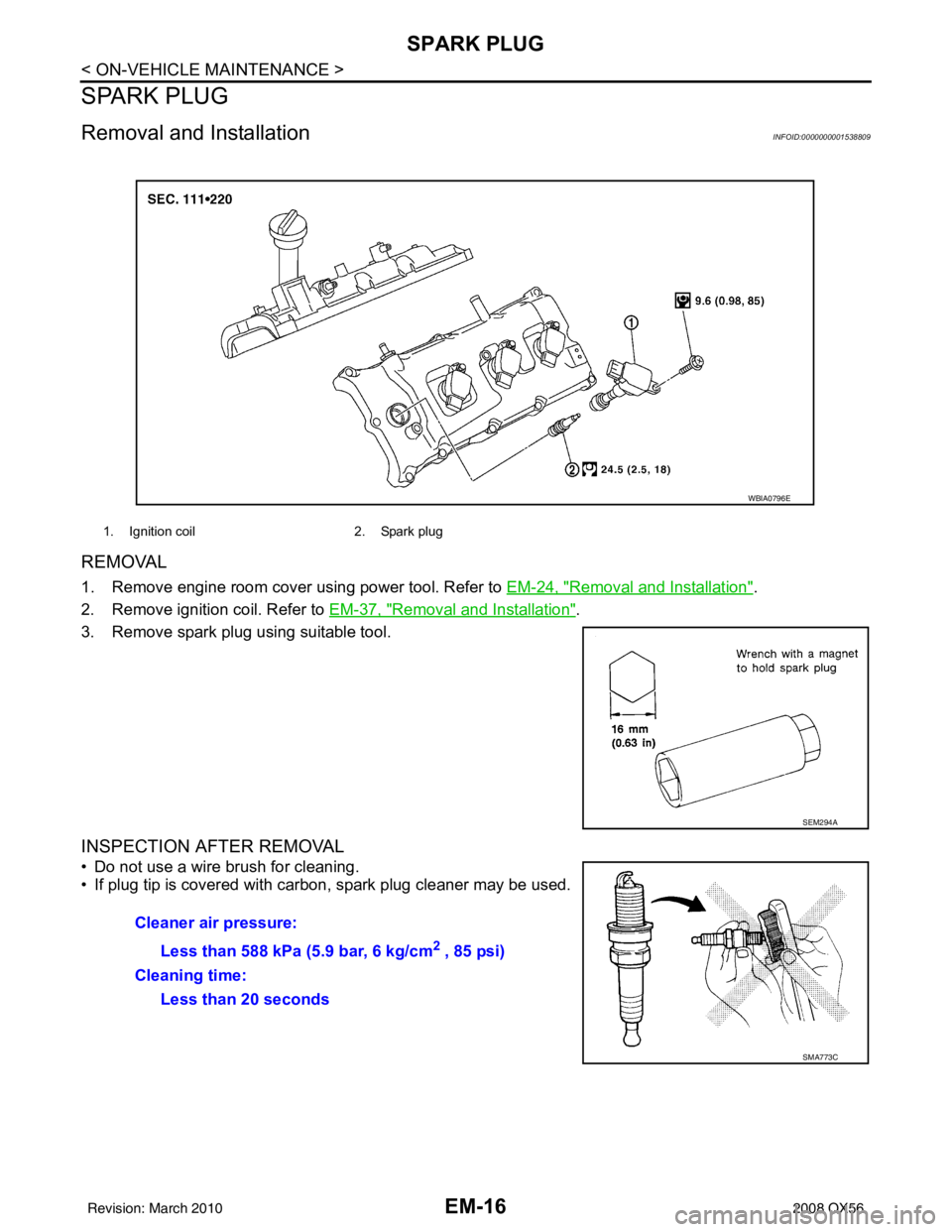
EM-16
< ON-VEHICLE MAINTENANCE >
SPARK PLUG
SPARK PLUG
Removal and InstallationINFOID:0000000001538809
REMOVAL
1. Remove engine room cover using power tool. Refer to EM-24, "Removal and Installation".
2. Remove ignition coil. Refer to EM-37, "
Removal and Installation".
3. Remove spark plug using suitable tool.
INSPECTION AFTER REMOVAL
• Do not use a wire brush for cleaning.
• If plug tip is covered with carbon, spark plug cleaner may be used.
1. Ignition coil 2. Spark plug
WBIA0796E
SEM294A
Cleaner air pressure:
Less than 588 kPa (5.9 bar, 6 kg/cm
2 , 85 psi)
Cleaning time: Less than 20 seconds
SMA773C
Revision: March 2010 2008 QX56
Page 1826 of 4083
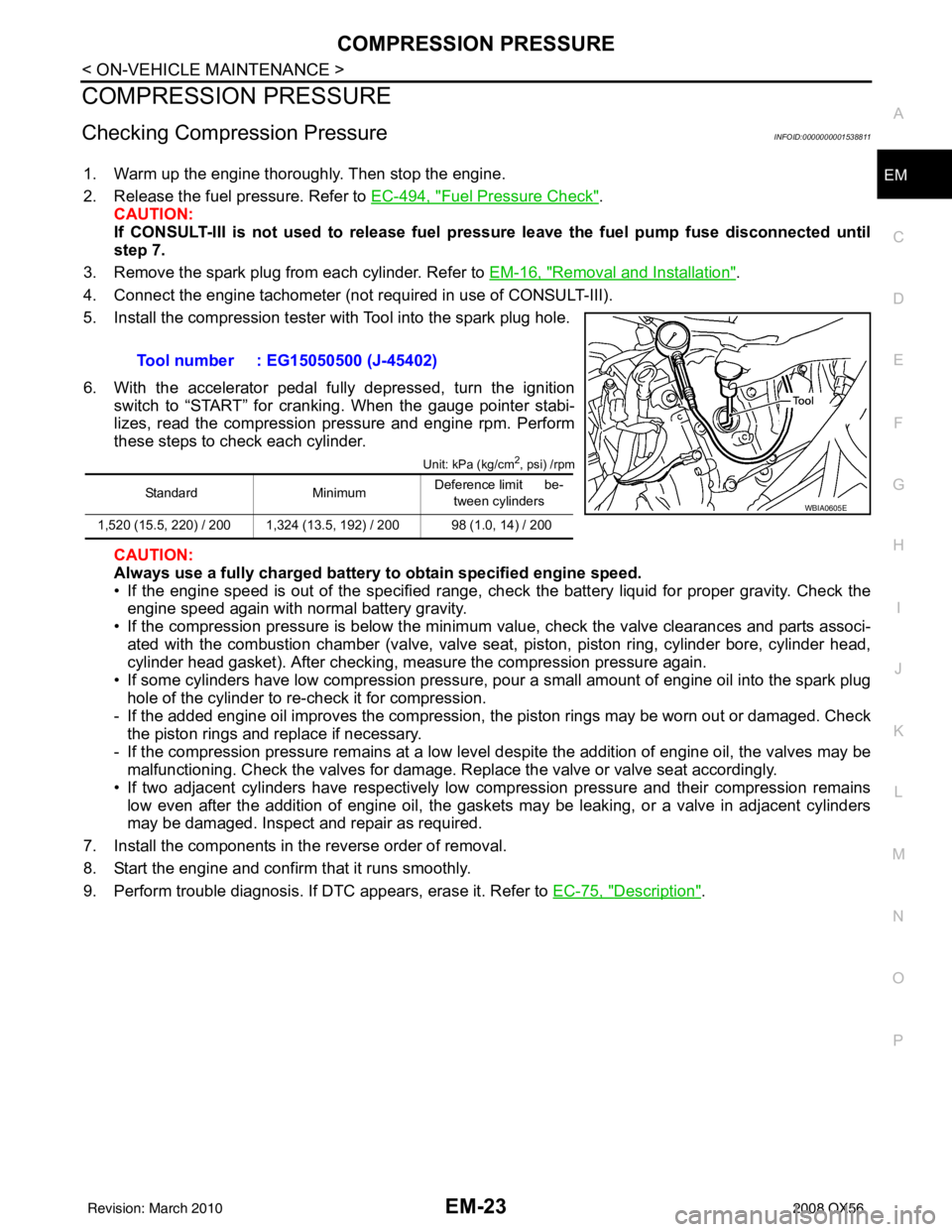
COMPRESSION PRESSUREEM-23
< ON-VEHICLE MAINTENANCE >
C
DE
F
G H
I
J
K L
M A
EM
NP
O
COMPRESSION PRESSURE
Checking Compression PressureINFOID:0000000001538811
1. Warm up the engine thoroughly. Then stop the engine.
2. Release the fuel pressure. Refer to EC-494, "
Fuel Pressure Check".
CAUTION:
If CONSULT-III is not used to release fuel pressure leave the fuel pump fuse disconnected until
step 7.
3. Remove the spark plug from each cylinder. Refer to EM-16, "
Removal and Installation".
4. Connect the engine tachometer (not required in use of CONSULT-III).
5. Install the compression tester with Tool into the spark plug hole.
6. With the accelerator pedal fully depressed, turn the ignition switch to “START” for cranking. When the gauge pointer stabi-
lizes, read the compression pressure and engine rpm. Perform
these steps to check each cylinder.
Unit: kPa (kg/cm2, psi) /rpm
CAUTION:
Always use a fully charged battery to obtain specified engine speed.
• If the engine speed is out of the specified range, check the battery liquid for proper gravity. Check the engine speed again with normal battery gravity.
• If the compression pressure is below the minimum value, check the valve clearances and parts associ-
ated with the combustion chamber (valve, valve seat , piston, piston ring, cylinder bore, cylinder head,
cylinder head gasket). After checking, measure the compression pressure again.
• If some cylinders have low compression pressure, pour a small amount of engine oil into the spark plug hole of the cylinder to re-check it for compression.
- If the added engine oil improves the compression, t he piston rings may be worn out or damaged. Check
the piston rings and replace if necessary.
- If the compression pressure remains at a low level despite the addition of engine oil, the valves may be malfunctioning. Check the valves for damage. Replace the valve or valve seat accordingly.
• If two adjacent cylinders have respectively low compression pressure and their compression remains low even after the addition of engine oil, the gaskets may be leaking, or a valve in adjacent cylinders
may be damaged. Inspect and repair as required.
7. Install the components in the reverse order of removal.
8. Start the engine and confirm that it runs smoothly.
9. Perform trouble diagnosis. If DTC appears, erase it. Refer to EC-75, "
Description".
Tool number : EG15050500 (J-45402)
Standard
MinimumDeference limit be-
tween cylinders
1,520 (15.5, 220) / 200 1,324 (13.5, 192) / 200 98 (1.0, 14) / 200WBIA0605E
Revision: March 2010 2008 QX56