service INFINITI QX56 2011 Factory Service Manual
[x] Cancel search | Manufacturer: INFINITI, Model Year: 2011, Model line: QX56, Model: INFINITI QX56 2011Pages: 5598, PDF Size: 94.53 MB
Page 2631 of 5598
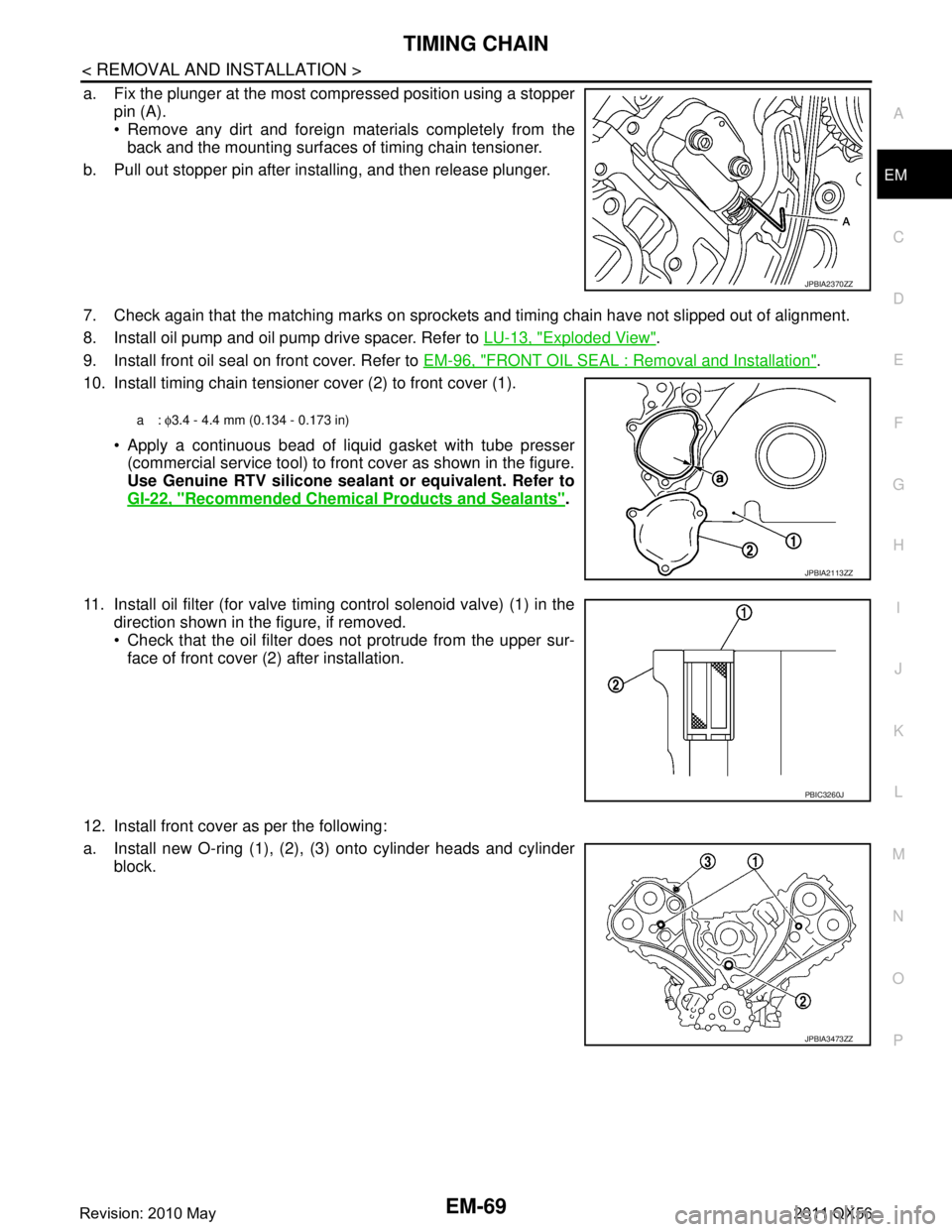
TIMING CHAINEM-69
< REMOVAL AND INSTALLATION >
C
DE
F
G H
I
J
K L
M A
EM
NP
O
a. Fix the plunger at the most compressed position using a stopper
pin (A).
Remove any dirt and foreign materials completely from theback and the mounting surfaces of timing chain tensioner.
b. Pull out stopper pin after installing, and then release plunger.
7. Check again that the matching marks on sprockets and timing chain have not slipped out of alignment.
8. Install oil pump and oil pump drive spacer. Refer to LU-13, "
Exploded View".
9. Install front oil seal on front cover. Refer to EM-96, "
FRONT OIL SEAL : Removal and Installation".
10. Install timing chain tensioner cover (2) to front cover (1).
Apply a continuous bead of liquid gasket with tube presser(commercial service tool) to front cover as shown in the figure.
Use Genuine RTV silicone seal ant or equivalent. Refer to
GI-22, "
Recommended Chemical Products and Sealants".
11. Install oil filter (for valve timing control solenoid valve) (1) in the direction shown in the figure, if removed.
Check that the oil filter does not protrude from the upper sur-
face of front cover (2) after installation.
12. Install front cover as per the following:
a. Install new O-ring (1), (2), (3) onto cylinder heads and cylinder block.
JPBIA2370ZZ
a: φ3.4 - 4.4 mm (0.134 - 0.173 in)
JPBIA2113ZZ
PBIC3260J
JPBIA3473ZZ
Revision: 2010 May2011 QX56
Page 2632 of 5598
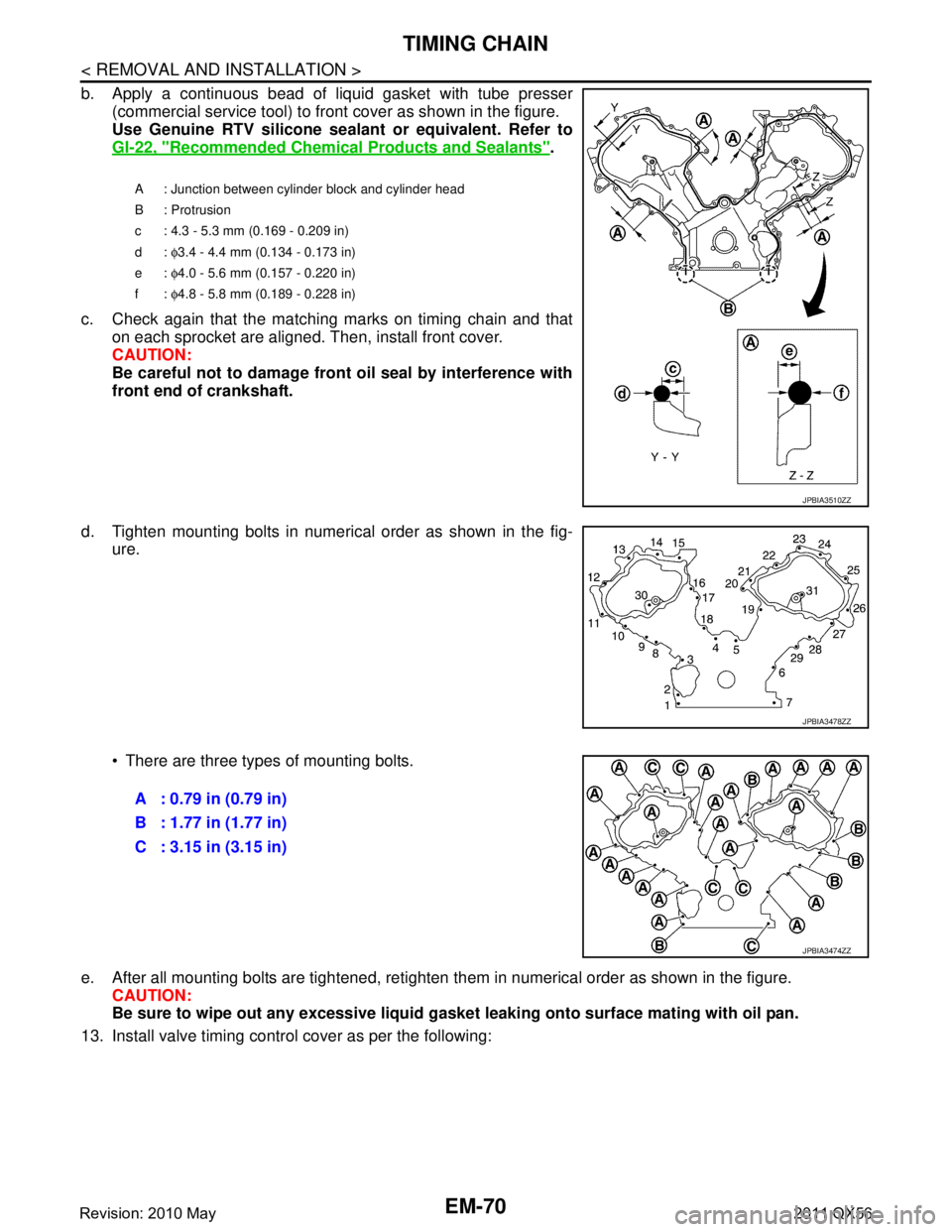
EM-70
< REMOVAL AND INSTALLATION >
TIMING CHAIN
b. Apply a continuous bead of liquid gasket with tube presser(commercial service tool) to front cover as shown in the figure.
Use Genuine RTV silicone seal ant or equivalent. Refer to
GI-22, "
Recommended Chemical Products and Sealants".
c. Check again that the matching marks on timing chain and that on each sprocket are aligned. Then, install front cover.
CAUTION:
Be careful not to damage front oil seal by interference with
front end of crankshaft.
d. Tighten mounting bolts in numerical order as shown in the fig- ure.
There are three types of mounting bolts.
e. After all mounting bolts are tightened, retighten t hem in numerical order as shown in the figure.
CAUTION:
Be sure to wipe out any excessive liquid gasket leaking onto surface mating with oil pan.
13. Install valve timing control cover as per the following:
A : Junction between cylinder block and cylinder head
B : Protrusion
c : 4.3 - 5.3 mm (0.169 - 0.209 in)
d: φ3.4 - 4.4 mm (0.134 - 0.173 in)
e: φ4.0 - 5.6 mm (0.157 - 0.220 in)
f: φ4.8 - 5.8 mm (0.189 - 0.228 in)
JPBIA3510ZZ
JPBIA3478ZZ
A : 0.79 in (0.79 in)
B : 1.77 in (1.77 in)
C : 3.15 in (3.15 in)
JPBIA3474ZZ
Revision: 2010 May2011 QX56
Page 2633 of 5598
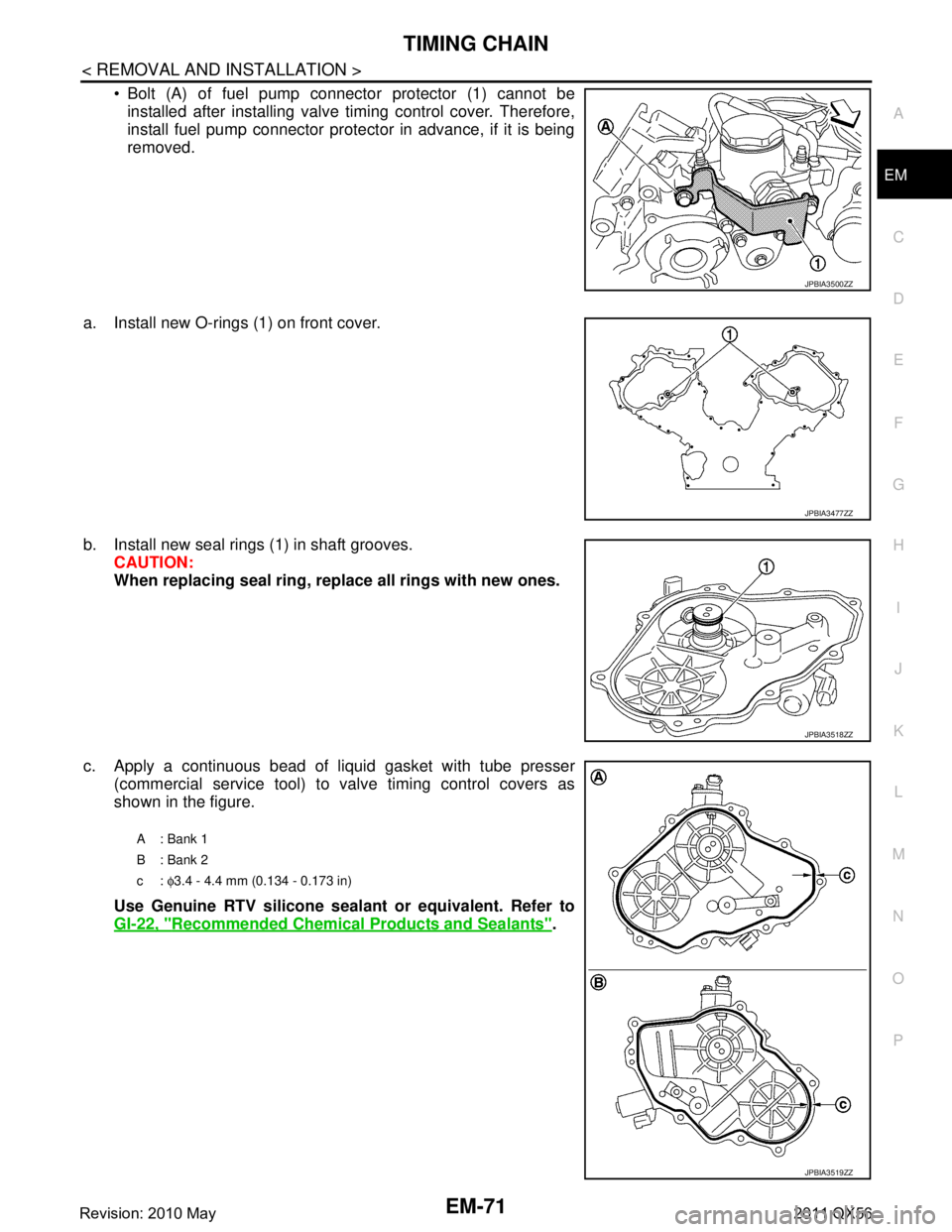
TIMING CHAINEM-71
< REMOVAL AND INSTALLATION >
C
DE
F
G H
I
J
K L
M A
EM
NP
O
Bolt (A) of fuel pump connector protector (1) cannot be
installed after installing valve timing control cover. Therefore,
install fuel pump connector protector in advance, if it is being
removed.
a. Install new O-rings (1) on front cover.
b. Install new seal rings (1) in shaft grooves. CAUTION:
When replacing seal ring, replace all rings with new ones.
c. Apply a continuous bead of liquid gasket with tube presser (commercial service tool) to valve timing control covers as
shown in the figure.
Use Genuine RTV silicone seal ant or equivalent. Refer to
GI-22, "
Recommended Chemical Products and Sealants".
JPBIA3500ZZ
JPBIA3477ZZ
JPBIA3518ZZ
A : Bank 1
B : Bank 2
c: φ3.4 - 4.4 mm (0.134 - 0.173 in)
JPBIA3519ZZ
Revision: 2010 May2011 QX56
Page 2639 of 5598
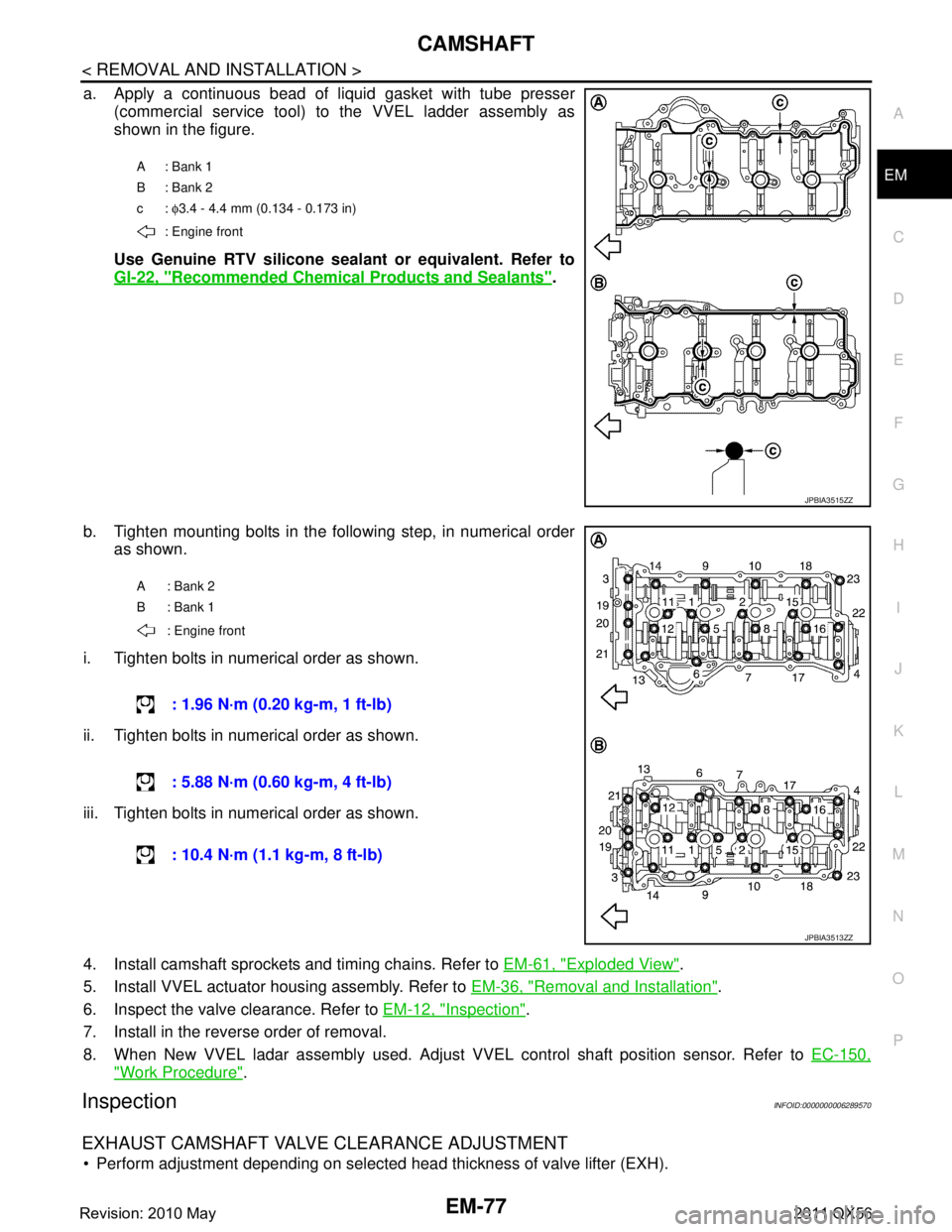
CAMSHAFTEM-77
< REMOVAL AND INSTALLATION >
C
DE
F
G H
I
J
K L
M A
EM
NP
O
a. Apply a continuous bead of liquid gasket with tube presser
(commercial service tool) to the VVEL ladder assembly as
shown in the figure.
Use Genuine RTV silicone seal ant or equivalent. Refer to
GI-22, "
Recommended Chemical Products and Sealants".
b. Tighten mounting bolts in the following step, in numerical order as shown.
i. Tighten bolts in numerical order as shown.
ii. Tighten bolts in numerical order as shown.
iii. Tighten bolts in numerical order as shown.
4. Install camshaft sprockets and timing chains. Refer to EM-61, "
Exploded View".
5. Install VVEL actuator housing assembly. Refer to EM-36, "
Removal and Installation".
6. Inspect the valve clearance. Refer to EM-12, "
Inspection".
7. Install in the reverse order of removal.
8. When New VVEL ladar assembly used. Adjust VVEL control shaft position sensor. Refer to EC-150,
"Work Procedure".
InspectionINFOID:0000000006289570
EXHAUST CAMSHAFT VALVE CLEARANCE ADJUSTMENT
Perform adjustment depending on selected head thickness of valve lifter (EXH).
A: Bank 1
B: Bank 2
c: φ3.4 - 4.4 mm (0.134 - 0.173 in)
: Engine front
JPBIA3515ZZ
A: Bank 2
B: Bank 1
: Engine front
: 1.96 N·m (0.20 kg-m, 1 ft-lb)
: 5.88 N·m (0.60 kg-m, 4 ft-lb)
: 10.4 N·m (1.1 kg-m, 8 ft-lb)
JPBIA3513ZZ
Revision: 2010 May2011 QX56
Page 2652 of 5598
![INFINITI QX56 2011 Factory Service Manual
EM-90
< REMOVAL AND INSTALLATION >
CYLINDER HEAD
b. Drive out valve guide (EXH) with a press [under a 20 kN (2 ton,2.2 US ton, 2.0 lmp ton) pressure] or a hammer and the valve
guide drift (commercial INFINITI QX56 2011 Factory Service Manual
EM-90
< REMOVAL AND INSTALLATION >
CYLINDER HEAD
b. Drive out valve guide (EXH) with a press [under a 20 kN (2 ton,2.2 US ton, 2.0 lmp ton) pressure] or a hammer and the valve
guide drift (commercial](/img/42/57033/w960_57033-2651.png)
EM-90
< REMOVAL AND INSTALLATION >
CYLINDER HEAD
b. Drive out valve guide (EXH) with a press [under a 20 kN (2 ton,2.2 US ton, 2.0 lmp ton) pressure] or a hammer and the valve
guide drift (commercial service tool).
WARNING:
Cylinder head contains heat . When working, wear protec-
tive equipment to avo id getting burned.
ASSEMBLY
1. Install valve guide (EXH), if removed.
Replace with oversized [0.2 mm (0.008 in)] valve guide (EXH).
a. Using the valve guide reamer (commercial service tool) (A), ream cylinder head valve guide (EXH) hole.
b. Heat cylinder head to 110 to 130 °C (230 to 266 °F) by soaking in
heated oil (A).
c. Using the valve guide drift (commercial service tool), press valve guide (EXH) from camshaft side to the dimensions as shown in
the figure.
WARNING:
Cylinder head contains heat . When working, wear protec-
tive equipment to avo id getting burned.
SEM931C
Oversize (service) [0.2 mm (0.008 in)]:
: Refer to EM-135, "
CylinderHead".
JPBIA0185ZZ
JPBIA0184ZZ
Projection (A)
: Refer to EM-135, "
CylinderHead".
JPBIA0186ZZ
Revision: 2010 May2011 QX56
Page 2653 of 5598
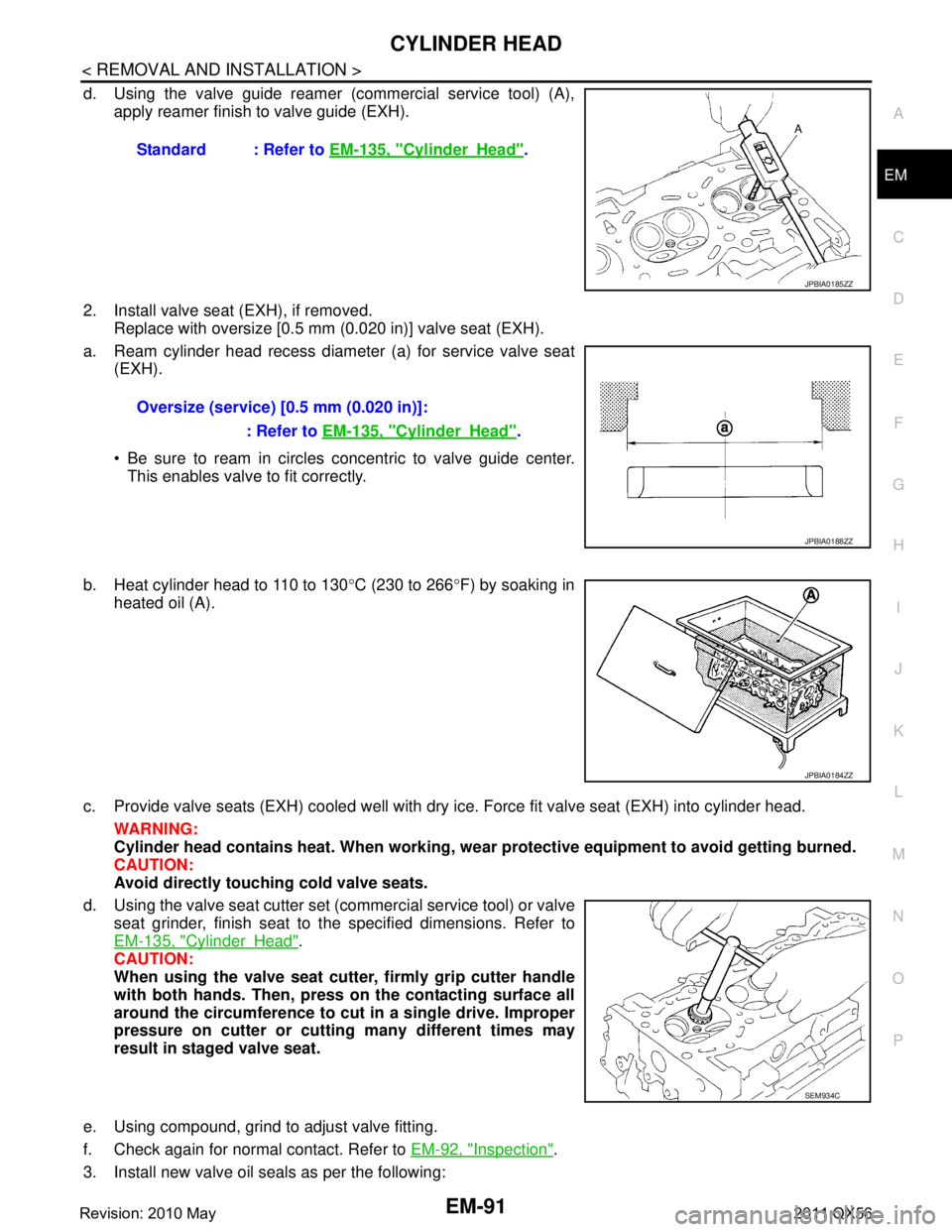
CYLINDER HEADEM-91
< REMOVAL AND INSTALLATION >
C
DE
F
G H
I
J
K L
M A
EM
NP
O
d. Using the valve guide reamer (commercial service tool) (A),
apply reamer finish to valve guide (EXH).
2. Install valve seat (EXH), if removed. Replace with oversize [0.5 mm (0.020 in)] valve seat (EXH).
a. Ream cylinder head recess diameter (a) for service valve seat (EXH).
Be sure to ream in circles concentric to valve guide center.
This enables valve to fit correctly.
b. Heat cylinder head to 110 to 130 °C (230 to 266 °F) by soaking in
heated oil (A).
c. Provide valve seats (EXH) cooled well with dry ice. Force fit valve seat (EXH) into cylinder head. WARNING:
Cylinder head contains heat. When working, w ear protective equipment to avoid getting burned.
CAUTION:
Avoid directly touching cold valve seats.
d. Using the valve seat cutter set (commercial service tool) or valve seat grinder, finish seat to the specified dimensions. Refer to
EM-135, "
CylinderHead".
CAUTION:
When using the valve seat cutt er, firmly grip cutter handle
with both hands. Then, press on the contacting surface all
around the circumference to cu t in a single drive. Improper
pressure on cutter or cutting many different times may
result in staged valve seat.
e. Using compound, grind to adjust valve fitting.
f. Check again for normal contact. Refer to EM-92, "
Inspection".
3. Install new valve oil seals as per the following: Standard : Refer to
EM-135, "
CylinderHead".
JPBIA0185ZZ
Oversize (service) [0.5 mm (0.020 in)]:
: Refer to EM-135, "
CylinderHead".
JPBIA0188ZZ
JPBIA0184ZZ
SEM934C
Revision: 2010 May2011 QX56
Page 2665 of 5598
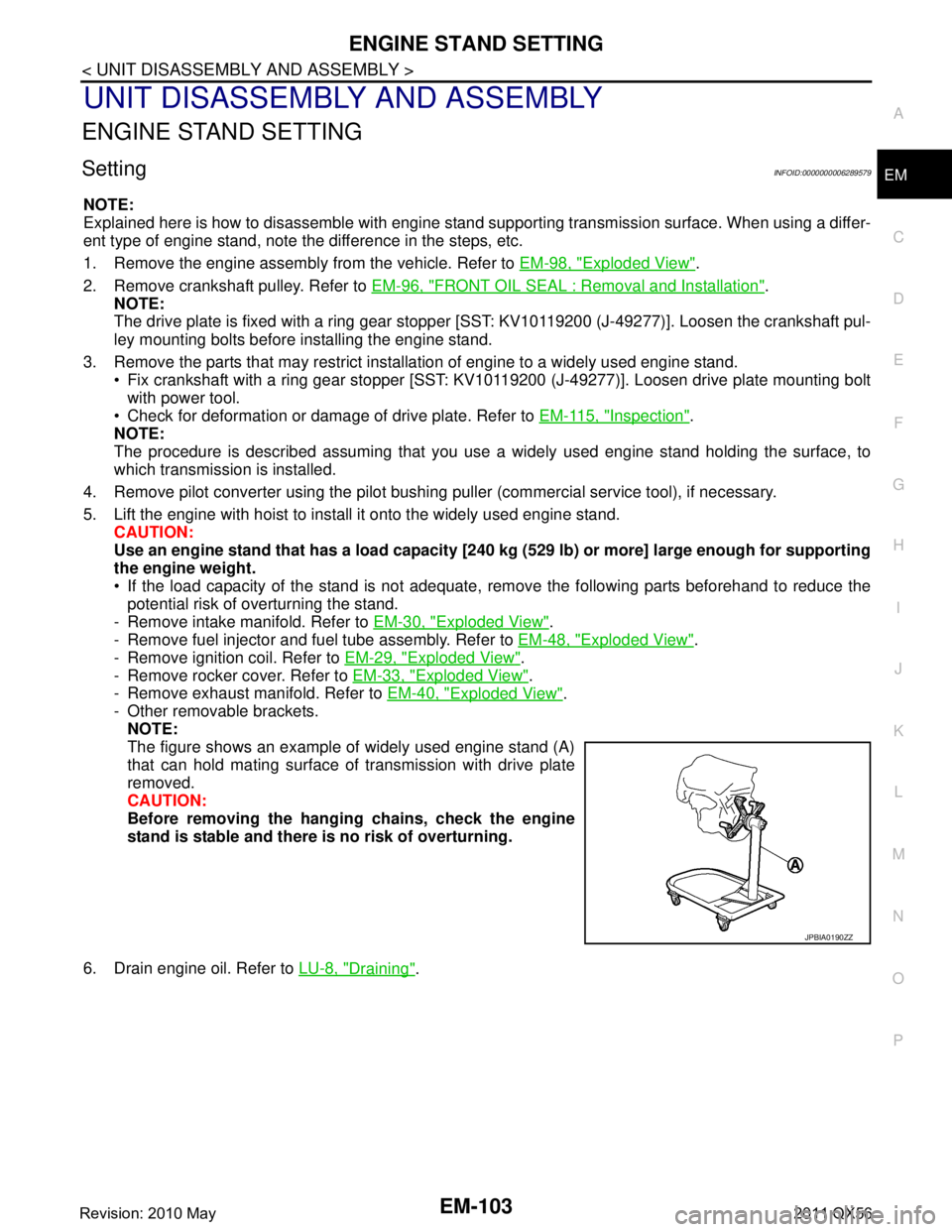
ENGINE STAND SETTINGEM-103
< UNIT DISASSEMBLY AND ASSEMBLY >
C
DE
F
G H
I
J
K L
M A
EM
NP
O
UNIT DISASSEMBLY AND ASSEMBLY
ENGINE STAND SETTING
SettingINFOID:0000000006289579
NOTE:
Explained here is how to disassemble with engine stand s
upporting transmission surface. When using a differ-
ent type of engine stand, note the difference in the steps, etc.
1. Remove the engine assembly from the vehicle. Refer to EM-98, "
Exploded View".
2. Remove crankshaft pulley. Refer to EM-96, "
FRONT OIL SEAL : Removal and Installation".
NOTE:
The drive plate is fixed with a ring gear stopper [SST: KV10119200 (J-49277)]. Loosen the crankshaft pul-
ley mounting bolts before installing the engine stand.
3. Remove the parts that may restrict installation of engine to a widely used engine stand. Fix crankshaft with a ring gear stopper [SST: KV10119200 (J-49277)]. Loosen drive plate mounting bolt
with power tool.
Check for deformation or damage of drive plate. Refer to EM-115, "
Inspection".
NOTE:
The procedure is described assuming that you us e a widely used engine stand holding the surface, to
which transmission is installed.
4. Remove pilot converter using the pilot bushing puller (commercial service tool), if necessary.
5. Lift the engine with hoist to inst all it onto the widely used engine stand.
CAUTION:
Use an engine stand that has a load capacity [240 kg (529 lb) or more] large enough for supporting
the engine weight.
If the load capacity of the stand is not adequate, remove the following parts beforehand to reduce the potential risk of overturning the stand.
- Remove intake manifold. Refer to EM-30, "
Exploded View".
- Remove fuel injector and fuel tube assembly. Refer to EM-48, "
Exploded View".
- Remove ignition coil. Refer to EM-29, "
Exploded View".
- Remove rocker cover. Refer to EM-33, "
Exploded View".
- Remove exhaust manifold. Refer to EM-40, "
Exploded View".
- Other removable brackets. NOTE:
The figure shows an example of widely used engine stand (A)
that can hold mating surface of transmission with drive plate
removed.
CAUTION:
Before removing the hang ing chains, check the engine
stand is stable and there is no risk of overturning.
6. Drain engine oil. Refer to LU-8, "
Draining".
JPBIA0190ZZ
Revision: 2010 May2011 QX56
Page 2670 of 5598
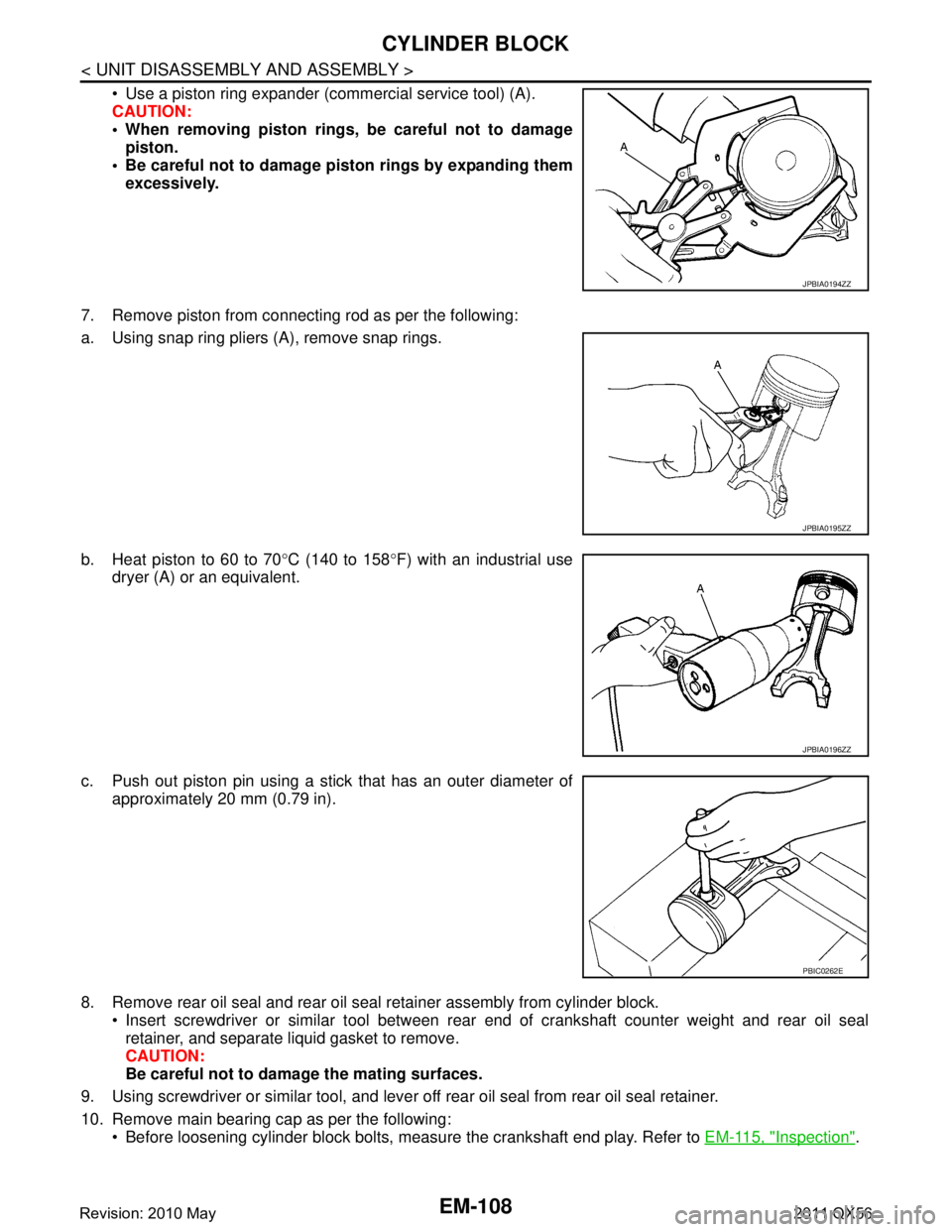
EM-108
< UNIT DISASSEMBLY AND ASSEMBLY >
CYLINDER BLOCK
Use a piston ring expander (commercial service tool) (A).
CAUTION:
When removing piston rings, be careful not to damagepiston.
Be careful not to damage piston rings by expanding them
excessively.
7. Remove piston from connecting rod as per the following:
a. Using snap ring pliers (A), remove snap rings.
b. Heat piston to 60 to 70 °C (140 to 158 °F) with an industrial use
dryer (A) or an equivalent.
c. Push out piston pin using a stick that has an outer diameter of approximately 20 mm (0.79 in).
8. Remove rear oil seal and rear oil seal retainer assembly from cylinder block. Insert screwdriver or similar tool between rear end of crankshaft counter weight and rear oil sealretainer, and separate liquid gasket to remove.
CAUTION:
Be careful not to damage the mating surfaces.
9. Using screwdriver or similar tool, and lever off rear oil seal from rear oil seal retainer.
10. Remove main bearing cap as per the following: Before loosening cylinder block bolts, measure the crankshaft end play. Refer to EM-115, "
Inspection".
JPBIA0194ZZ
JPBIA0195ZZ
JPBIA0196ZZ
PBIC0262E
Revision: 2010 May2011 QX56
Page 2671 of 5598
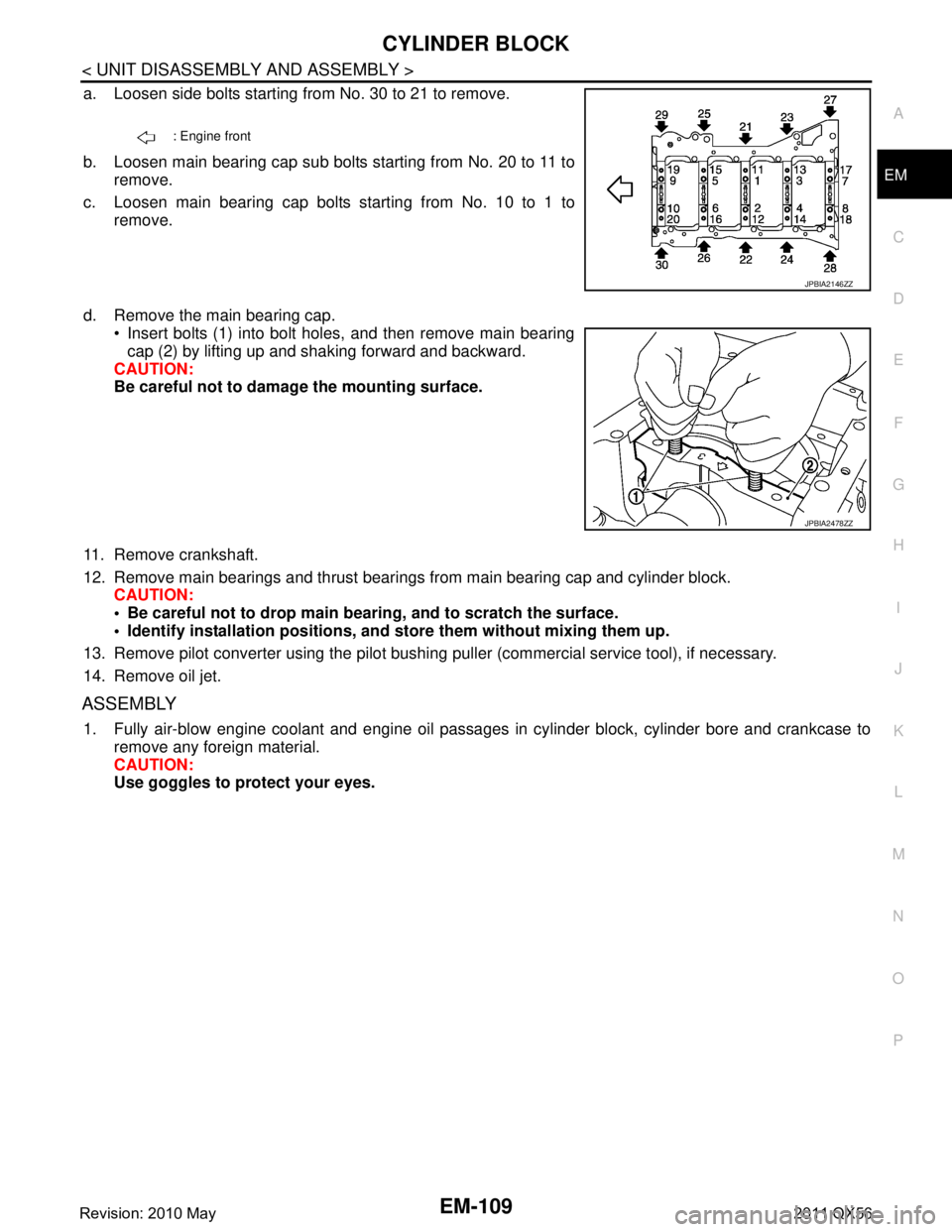
CYLINDER BLOCKEM-109
< UNIT DISASSEMBLY AND ASSEMBLY >
C
DE
F
G H
I
J
K L
M A
EM
NP
O
a. Loosen side bolts starting from No. 30 to 21 to remove.
b. Loosen main bearing cap sub bolts starting from No. 20 to 11 to
remove.
c. Loosen main bearing cap bolts starting from No. 10 to 1 to remove.
d. Remove the main bearing cap. Insert bolts (1) into bolt holes, and then remove main bearing
cap (2) by lifting up and shaking forward and backward.
CAUTION:
Be careful not to damage the mounting surface.
11. Remove crankshaft.
12. Remove main bearings and thrust bearings from main bearing cap and cylinder block. CAUTION:
Be careful not to drop main bear ing, and to scratch the surface.
Identify installation positions, and store them without mixing them up.
13. Remove pilot converter using the pilot bushing puller (commercial service tool), if necessary.
14. Remove oil jet.
ASSEMBLY
1. Fully air-blow engine coolant and engine oil passages in cylinder block, cylinder bore and crankcase to remove any foreign material.
CAUTION:
Use goggles to protect your eyes.
: Engine front
JPBIA2146ZZ
JPBIA2478ZZ
Revision: 2010 May2011 QX56
Page 2674 of 5598
![INFINITI QX56 2011 Factory Service Manual
EM-112
< UNIT DISASSEMBLY AND ASSEMBLY >
CYLINDER BLOCK
e. Tighten main bearing cap bolts (M12) in order of No. 1 - 10(clockwise).
CAUTION:
Use the angle wrench [SST: KV10112100 (BT8653-A)] (A) to
ch INFINITI QX56 2011 Factory Service Manual
EM-112
< UNIT DISASSEMBLY AND ASSEMBLY >
CYLINDER BLOCK
e. Tighten main bearing cap bolts (M12) in order of No. 1 - 10(clockwise).
CAUTION:
Use the angle wrench [SST: KV10112100 (BT8653-A)] (A) to
ch](/img/42/57033/w960_57033-2673.png)
EM-112
< UNIT DISASSEMBLY AND ASSEMBLY >
CYLINDER BLOCK
e. Tighten main bearing cap bolts (M12) in order of No. 1 - 10(clockwise).
CAUTION:
Use the angle wrench [SST: KV10112100 (BT8653-A)] (A) to
check tightening angl e. Never make judgment by visual
inspection.
f. Tighten main bearing cap sub bolts (M9) in order of No. 11 - 20. (clockwise)
g. Tighten side bolts (M10) in order of No. 21 - 30. After installing bolts, check that crankshaft can be rotated smoothly by hand.
Check the crankshaft end play. Refer to EM-137, "
CylinderBlock".
8. Install rear oil seal retainer. Apply a continuous bead of liquid gasket with tube presser
(commercial service tool) to rear oil seal retainer as shown in
the figure.
Use Genuine RTV silicone seal ant or equivalent. Refer to
GI-22, "
Recommended Chemical Products and Sealants".
9. Install rear oil seal on rear oil seal retainer.
Apply new engine oil to both oil seal lip (A) and dust seal lip(B).
Install it so that each seal lip is oriented as shown in the figure. CAUTION:
Be careful not to scratch or make burrs on circumference
of oil seal.
Press in rear oil seal (1) to the position as shown in the figure.
Using a suitable drift [outer diameter: 101 mm (3.98 in)].
Check the garter spring is in position and seal lips are not inverted.
10. Install piston to connecting rod as per the following: Angle tightening: 40 degrees
Angle tightening: 30 degrees
JPBIA2149ZZ
: 49.0 N·m (5.0 kg-m, 36 ft-lb)
A : Protrusion
b : 4.0 - 5.6 mm (0.157 - 0.220 in)
c:
φ3.4 - 4.4 mm (0.134 - 0.173 in)
JPBIA2102ZZ
: Engine inside
: Engine outside
JPBIA0054ZZ
B : Rear oil seal retainer rear end face
a : 0 - 0.5 mm (0 - 0.020 in)
JPBIA0152ZZ
Revision: 2010 May2011 QX56