Control module JAGUAR XFR 2010 1.G Workshop Manual
[x] Cancel search | Manufacturer: JAGUAR, Model Year: 2010, Model line: XFR, Model: JAGUAR XFR 2010 1.GPages: 3039, PDF Size: 58.49 MB
Page 494 of 3039
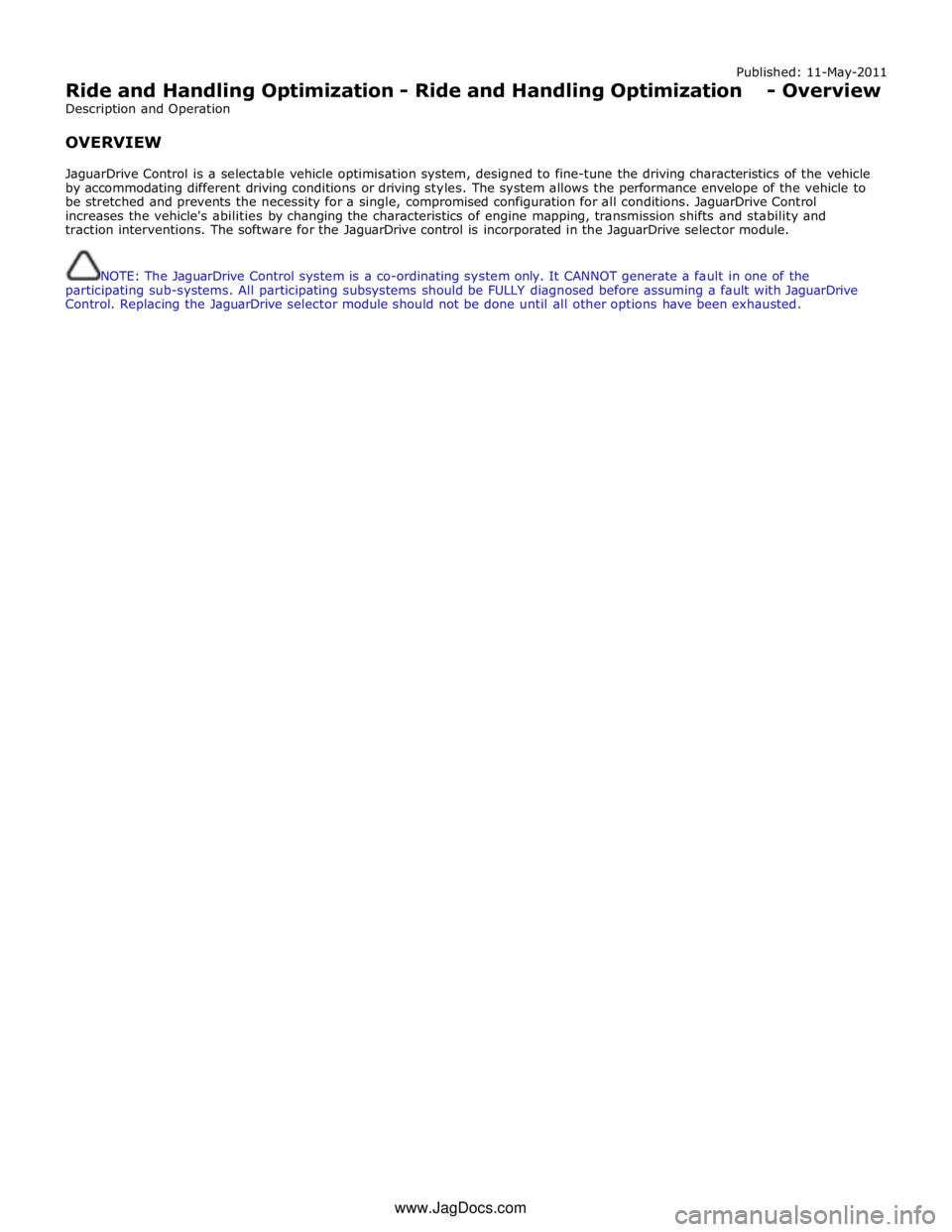
Published: 11-May-2011
Ride and Handling Optimization - Ride and Handling Optimization - Overview
Description and Operation
OVERVIEW
JaguarDrive Control is a selectable vehicle optimisation system, designed to fine-tune the driving characteristics of the vehicle
by accommodating different driving conditions or driving styles. The system allows the performance envelope of the vehicle to
be stretched and prevents the necessity for a single, compromised configuration for all conditions. JaguarDrive Control
increases the vehicle's abilities by changing the characteristics of engine mapping, transmission shifts and stability and
traction interventions. The software for the JaguarDrive control is incorporated in the JaguarDrive selector module.
NOTE: The JaguarDrive Control system is a co-ordinating system only. It CANNOT generate a fault in one of the
participating sub-systems. All participating subsystems should be FULLY diagnosed before assuming a fault with JaguarDrive
Control. Replacing the JaguarDrive selector module should not be done until all other options have been exhausted.
www.JagDocs.com
Page 495 of 3039
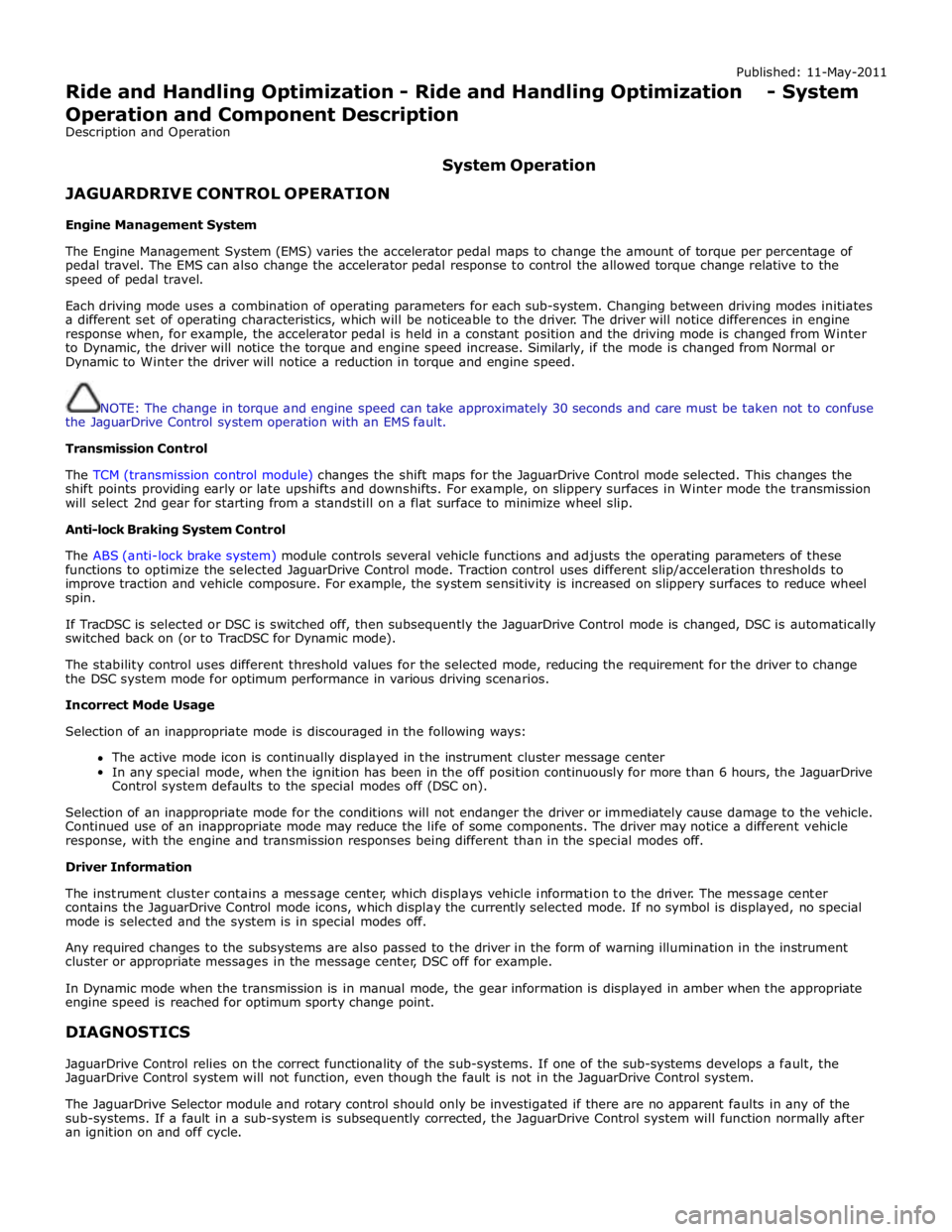
Published: 11-May-2011
Ride and Handling Optimization - Ride and Handling Optimization - System
Operation and Component Description
Description and Operation
JAGUARDRIVE CONTROL OPERATION
Engine Management System System Operation
The Engine Management System (EMS) varies the accelerator pedal maps to change the amount of torque per percentage of
pedal travel. The EMS can also change the accelerator pedal response to control the allowed torque change relative to the
speed of pedal travel.
Each driving mode uses a combination of operating parameters for each sub-system. Changing between driving modes initiates
a different set of operating characteristics, which will be noticeable to the driver. The driver will notice differences in engine
response when, for example, the accelerator pedal is held in a constant position and the driving mode is changed from Winter
to Dynamic, the driver will notice the torque and engine speed increase. Similarly, if the mode is changed from Normal or
Dynamic to Winter the driver will notice a reduction in torque and engine speed.
NOTE: The change in torque and engine speed can take approximately 30 seconds and care must be taken not to confuse
the JaguarDrive Control system operation with an EMS fault.
Transmission Control
The TCM (transmission control module) changes the shift maps for the JaguarDrive Control mode selected. This changes the
shift points providing early or late upshifts and downshifts. For example, on slippery surfaces in Winter mode the transmission
will select 2nd gear for starting from a standstill on a flat surface to minimize wheel slip.
Anti-lock Braking System Control
The ABS (anti-lock brake system) module controls several vehicle functions and adjusts the operating parameters of these
functions to optimize the selected JaguarDrive Control mode. Traction control uses different slip/acceleration thresholds to
improve traction and vehicle composure. For example, the system sensitivity is increased on slippery surfaces to reduce wheel
spin.
If TracDSC is selected or DSC is switched off, then subsequently the JaguarDrive Control mode is changed, DSC is automatically
switched back on (or to TracDSC for Dynamic mode).
The stability control uses different threshold values for the selected mode, reducing the requirement for the driver to change
the DSC system mode for optimum performance in various driving scenarios.
Incorrect Mode Usage
Selection of an inappropriate mode is discouraged in the following ways:
The active mode icon is continually displayed in the instrument cluster message center
In any special mode, when the ignition has been in the off position continuously for more than 6 hours, the JaguarDrive
Control system defaults to the special modes off (DSC on).
Selection of an inappropriate mode for the conditions will not endanger the driver or immediately cause damage to the vehicle.
Continued use of an inappropriate mode may reduce the life of some components. The driver may notice a different vehicle
response, with the engine and transmission responses being different than in the special modes off.
Driver Information
The instrument cluster contains a message center, which displays vehicle information to the driver. The message center
contains the JaguarDrive Control mode icons, which display the currently selected mode. If no symbol is displayed, no special
mode is selected and the system is in special modes off.
Any required changes to the subsystems are also passed to the driver in the form of warning illumination in the instrument
cluster or appropriate messages in the message center, DSC off for example.
In Dynamic mode when the transmission is in manual mode, the gear information is displayed in amber when the appropriate
engine speed is reached for optimum sporty change point.
DIAGNOSTICS
JaguarDrive Control relies on the correct functionality of the sub-systems. If one of the sub-systems develops a fault, the
JaguarDrive Control system will not function, even though the fault is not in the JaguarDrive Control system.
The JaguarDrive Selector module and rotary control should only be investigated if there are no apparent faults in any of the
sub-systems. If a fault in a sub-system is subsequently corrected, the JaguarDrive Control system will function normally after
an ignition on and off cycle.
Page 496 of 3039
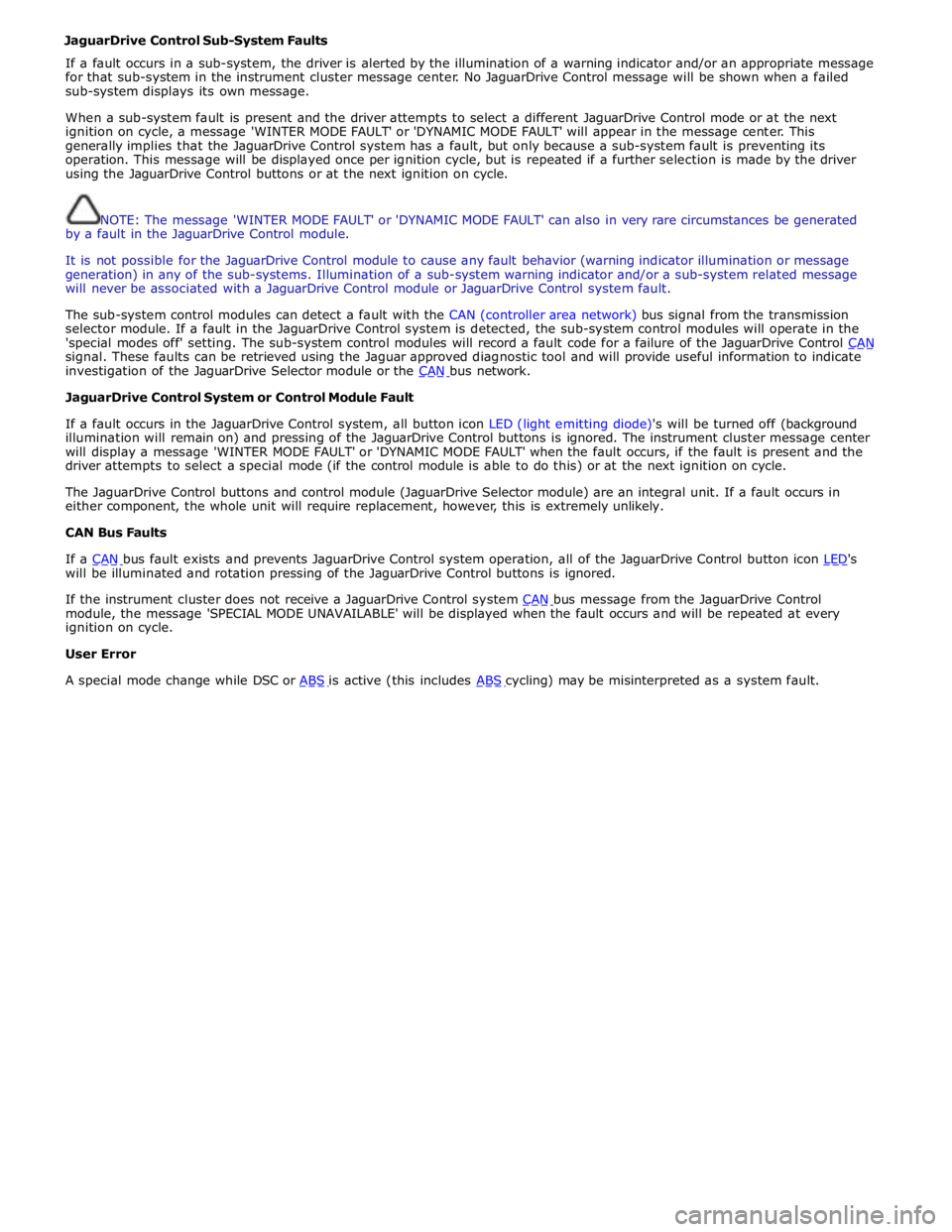
JaguarDrive Control Sub-System Faults
If a fault occurs in a sub-system, the driver is alerted by the illumination of a warning indicator and/or an appropriate message
for that sub-system in the instrument cluster message center. No JaguarDrive Control message will be shown when a failed
sub-system displays its own message.
When a sub-system fault is present and the driver attempts to select a different JaguarDrive Control mode or at the next
ignition on cycle, a message 'WINTER MODE FAULT' or 'DYNAMIC MODE FAULT' will appear in the message center. This
generally implies that the JaguarDrive Control system has a fault, but only because a sub-system fault is preventing its
operation. This message will be displayed once per ignition cycle, but is repeated if a further selection is made by the driver
using the JaguarDrive Control buttons or at the next ignition on cycle.
NOTE: The message 'WINTER MODE FAULT' or 'DYNAMIC MODE FAULT' can also in very rare circumstances be generated
by a fault in the JaguarDrive Control module.
It is not possible for the JaguarDrive Control module to cause any fault behavior (warning indicator illumination or message
generation) in any of the sub-systems. Illumination of a sub-system warning indicator and/or a sub-system related message
will never be associated with a JaguarDrive Control module or JaguarDrive Control system fault.
The sub-system control modules can detect a fault with the CAN (controller area network) bus signal from the transmission
selector module. If a fault in the JaguarDrive Control system is detected, the sub-system control modules will operate in the
'special modes off' setting. The sub-system control modules will record a fault code for a failure of the JaguarDrive Control CAN signal. These faults can be retrieved using the Jaguar approved diagnostic tool and will provide useful information to indicate
investigation of the JaguarDrive Selector module or the CAN bus network. JaguarDrive Control System or Control Module Fault
If a fault occurs in the JaguarDrive Control system, all button icon LED (light emitting diode)'s will be turned off (background
illumination will remain on) and pressing of the JaguarDrive Control buttons is ignored. The instrument cluster message center
will display a message 'WINTER MODE FAULT' or 'DYNAMIC MODE FAULT' when the fault occurs, if the fault is present and the
driver attempts to select a special mode (if the control module is able to do this) or at the next ignition on cycle.
The JaguarDrive Control buttons and control module (JaguarDrive Selector module) are an integral unit. If a fault occurs in
either component, the whole unit will require replacement, however, this is extremely unlikely.
CAN Bus Faults
If a CAN bus fault exists and prevents JaguarDrive Control system operation, all of the JaguarDrive Control button icon LED's will be illuminated and rotation pressing of the JaguarDrive Control buttons is ignored.
If the instrument cluster does not receive a JaguarDrive Control system CAN bus message from the JaguarDrive Control module, the message 'SPECIAL MODE UNAVAILABLE' will be displayed when the fault occurs and will be repeated at every
ignition on cycle.
User Error
A special mode change while DSC or ABS is active (this includes ABS cycling) may be misinterpreted as a system fault.
Page 497 of 3039

JAGUARDRIVE CONTROL DESCRIPTION Component Description
Item Description 1 Winter mode button 2 DSC/TracDSC mode button 3 ASL (automatic speed limiter) - Reference only, not part of JaguarDrive system 4 Dynamic mode (Supercharged models only) The system is controlled by buttons adjacent to the JaguarDrive Selector located on the floor console. The buttons allow the
selection of one of the following 3 modes:
Special modes off
Winter mode
Dynamic mode (Supercharged models only).
The instrument cluster will display the selected JaguarDrive Control mode in the message center.
The JaguarDrive Control system uses a combination of a number of vehicle sub-systems to achieve the required vehicle
characteristics for the mode selected. The following sub-systems make up the JaguarDrive Control system:
The Engine Management System (EMS)
Automatic transmission
Brake system.
The JaguarDrive Control software is stored in the JaguarDrive Selector module located below the JaguarDrive selector. The
module detects the selection made using the buttons and transmits a signal on the high speed CAN bus, which is received by each of the sub-system control modules.
Each of the affected sub-system control modules contain software, which applies the correct operating parameters to their
controlled system for the JaguarDrive Control mode selection made.
Each sub-system control module also provides a feedback for the selected mode so that the JaguarDrive Control software can
check that all systems have changed to the correct operating parameters.
NOTE: The JaguarDrive Control system is a co-ordinating system only. It CANNOT generate a fault in one of the
participating sub-systems. All participating sub-systems should be FULLY diagnosed before assuming a fault with JaguarDrive
Control. Replacing the JaguarDrive Selector module should not be done until all other options have been exhausted. JAGUARDRIVE CONTROLS
Page 501 of 3039
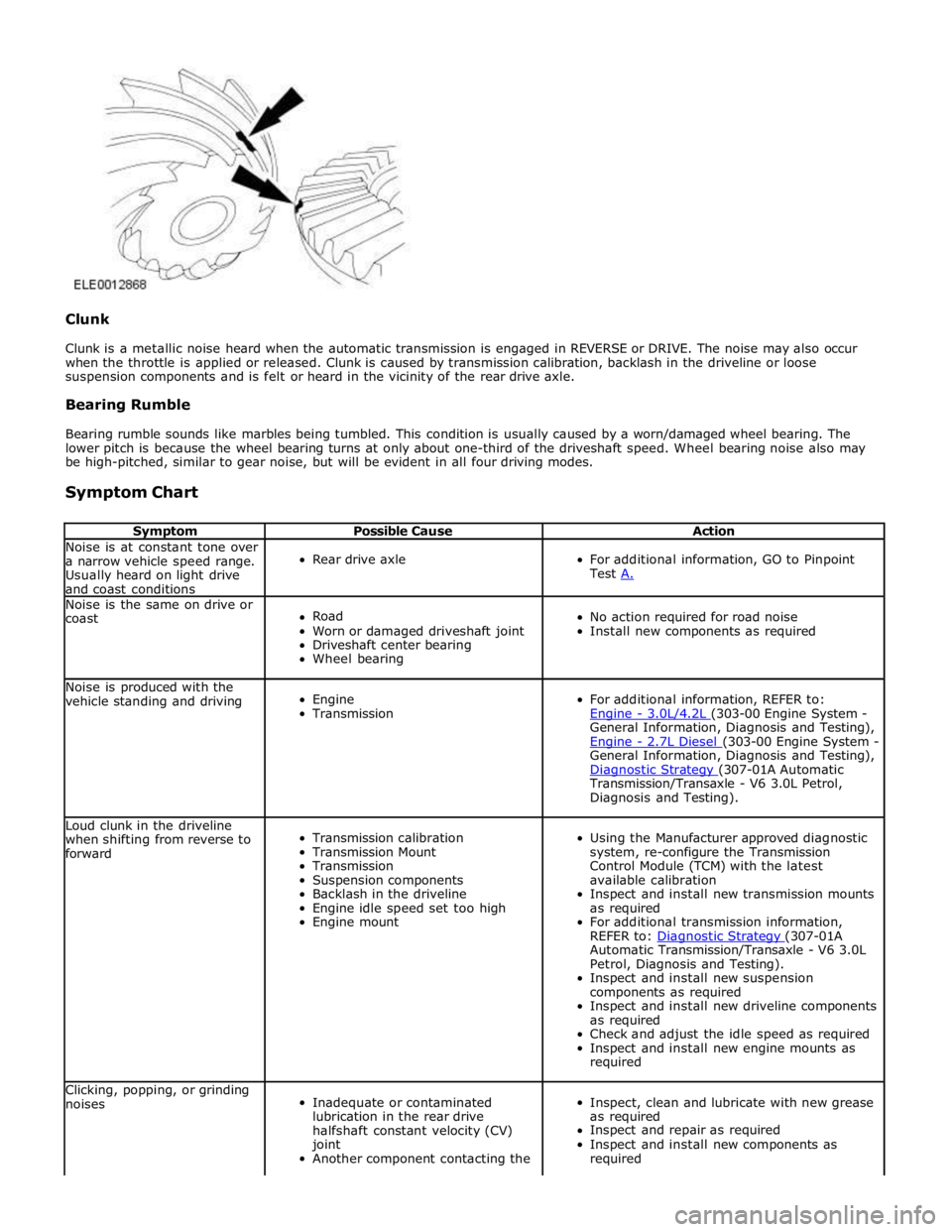
Clunk
Clunk is a metallic noise heard when the automatic transmission is engaged in REVERSE or DRIVE. The noise may also occur
when the throttle is applied or released. Clunk is caused by transmission calibration, backlash in the driveline or loose
suspension components and is felt or heard in the vicinity of the rear drive axle.
Bearing Rumble
Bearing rumble sounds like marbles being tumbled. This condition is usually caused by a worn/damaged wheel bearing. The
lower pitch is because the wheel bearing turns at only about one-third of the driveshaft speed. Wheel bearing noise also may
be high-pitched, similar to gear noise, but will be evident in all four driving modes.
Symptom Chart
Symptom Possible Cause Action Noise is at constant tone over
a narrow vehicle speed range.
Usually heard on light drive
and coast conditions
Rear drive axle
For additional information, GO to Pinpoint
Test A. Noise is the same on drive or
coast
Road
Worn or damaged driveshaft joint
Driveshaft center bearing
Wheel bearing
No action required for road noise
Install new components as required Noise is produced with the
vehicle standing and driving
Engine
Transmission
For additional information, REFER to:
Engine - 3.0L/4.2L (303-00 Engine System - General Information, Diagnosis and Testing),
Engine - 2.7L Diesel (303-00 Engine System - General Information, Diagnosis and Testing),
Diagnostic Strategy (307-01A Automatic Transmission/Transaxle - V6 3.0L Petrol,
Diagnosis and Testing). Loud clunk in the driveline
when shifting from reverse to
forward
Transmission calibration
Transmission Mount
Transmission
Suspension components
Backlash in the driveline
Engine idle speed set too high
Engine mount
Using the Manufacturer approved diagnostic
system, re-configure the Transmission
Control Module (TCM) with the latest
available calibration
Inspect and install new transmission mounts
as required
For additional transmission information,
REFER to: Diagnostic Strategy (307-01A Automatic Transmission/Transaxle - V6 3.0L
Petrol, Diagnosis and Testing).
Inspect and install new suspension
components as required
Inspect and install new driveline components
as required
Check and adjust the idle speed as required
Inspect and install new engine mounts as
required Clicking, popping, or grinding
noises
Inadequate or contaminated
lubrication in the rear drive
halfshaft constant velocity (CV)
joint
Another component contacting the
Inspect, clean and lubricate with new grease
as required
Inspect and repair as required
Inspect and install new components as
required
Page 532 of 3039
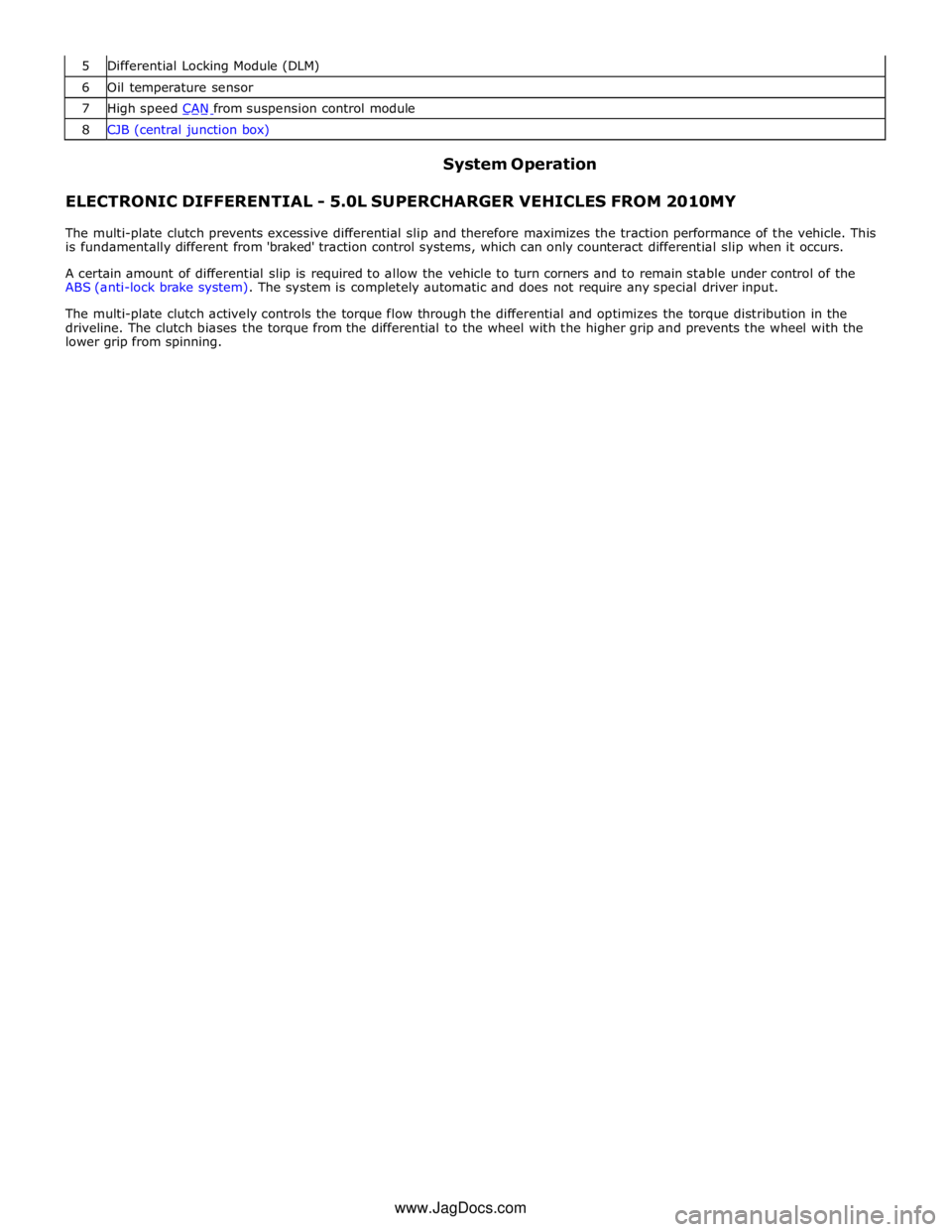
6 Oil temperature sensor 7 High speed CAN from suspension control module 8 CJB (central junction box)
System Operation
ELECTRONIC
DIFFERENTIAL
-
5.0L
SUPERCHARGER
VEHICLES
FROM
2010MY
The
multi-plate
clutch
prevents
excessive
differential
slip and
therefore
maximizes
the
traction
performance
of
the
vehicle.
This
is
fundamentally
different
from
'braked'
traction
control
systems,
which
can
only
counteract
differential
slip when it
occurs.
A
certain
amount
of
differential
slip is
required
to
allow
the
vehicle
to
turn
corners
and
to
remain
stable
under
control
of
the
ABS
(anti-lock
brake
system).
The
system
is
completely
automatic and
does
not
require
any
special
driver
input.
The
multi-plate
clutch
actively
controls
the
torque
flow
through
the
differential
and
optimizes
the
torque
distribution in
the
driveline.
The
clutch
biases
the
torque
from
the
differential
to
the
wheel
with the
higher
grip
and prevents
the
wheel
with the
lower
grip
from
spinning.
www.JagDocs.com
Page 533 of 3039
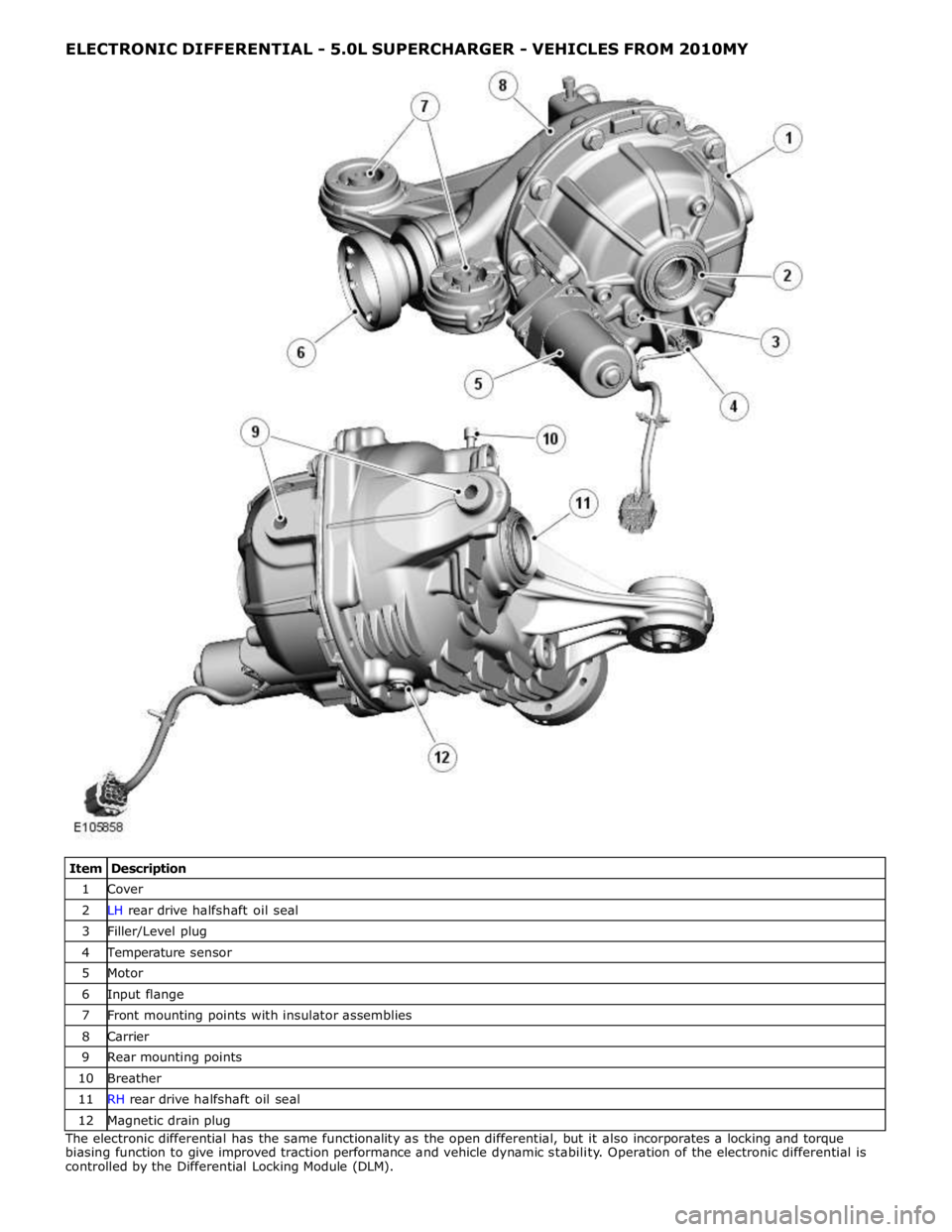
ELECTRONIC DIFFERENTIAL - 5.0L SUPERCHARGER - VEHICLES FROM 2010MY
Item Description 1 Cover 2 LH rear drive halfshaft oil seal 3 Filler/Level plug 4 Temperature sensor 5 Motor 6 Input flange 7 Front mounting points with insulator assemblies 8 Carrier 9 Rear mounting points 10 Breather 11 RH rear drive halfshaft oil seal 12 Magnetic drain plug The electronic differential has the same functionality as the open differential, but it also incorporates a locking and torque
biasing function to give improved traction performance and vehicle dynamic stability. Operation of the electronic differential is
controlled by the Differential Locking Module (DLM).
Page 534 of 3039
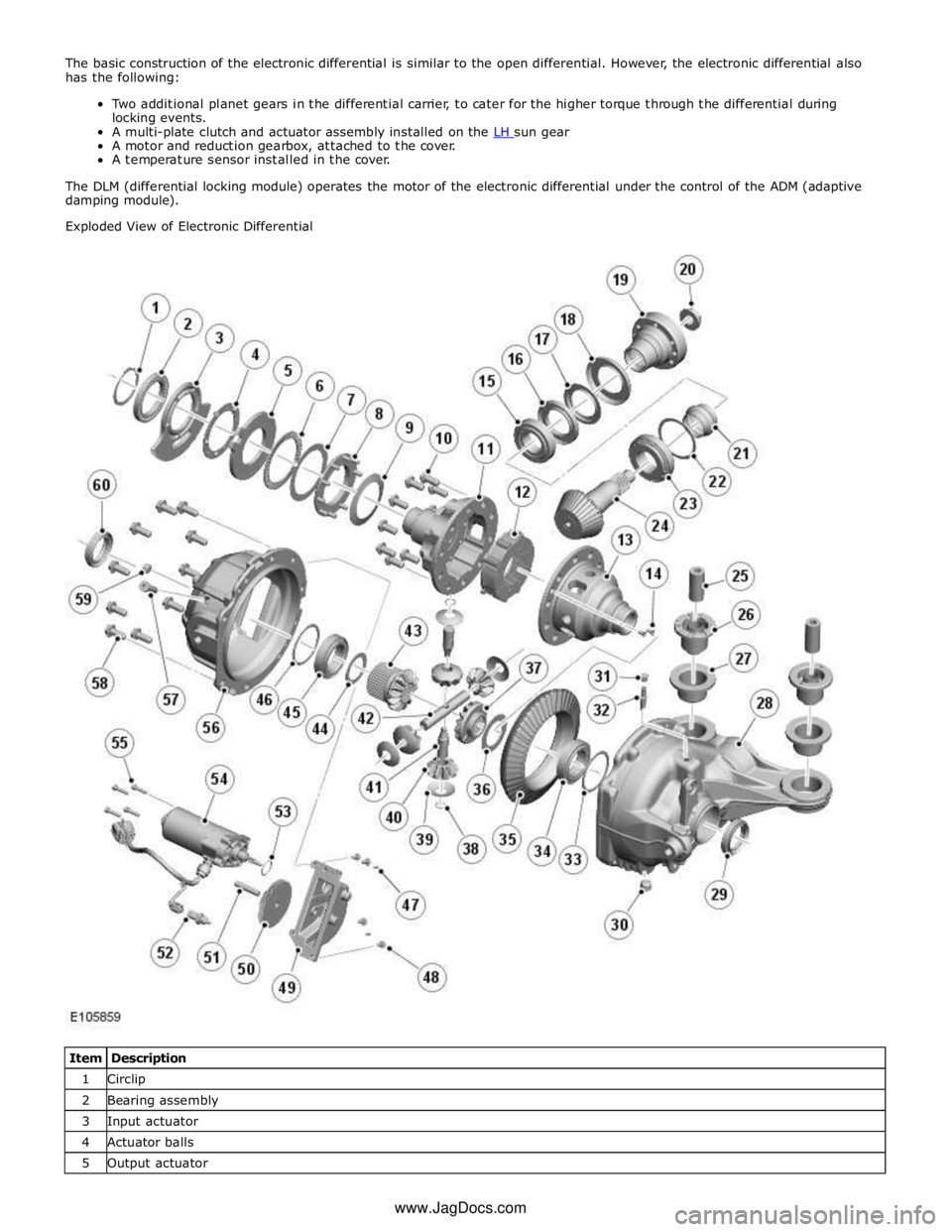
A motor and reduction gearbox, attached to the cover.
A temperature sensor installed in the cover.
The DLM (differential locking module) operates the motor of the electronic differential under the control of the ADM (adaptive
damping module).
Exploded View of Electronic Differential
Item Description 1 Circlip 2 Bearing assembly 3 Input actuator 4 Actuator balls 5 Output actuator www.JagDocs.com
Page 536 of 3039
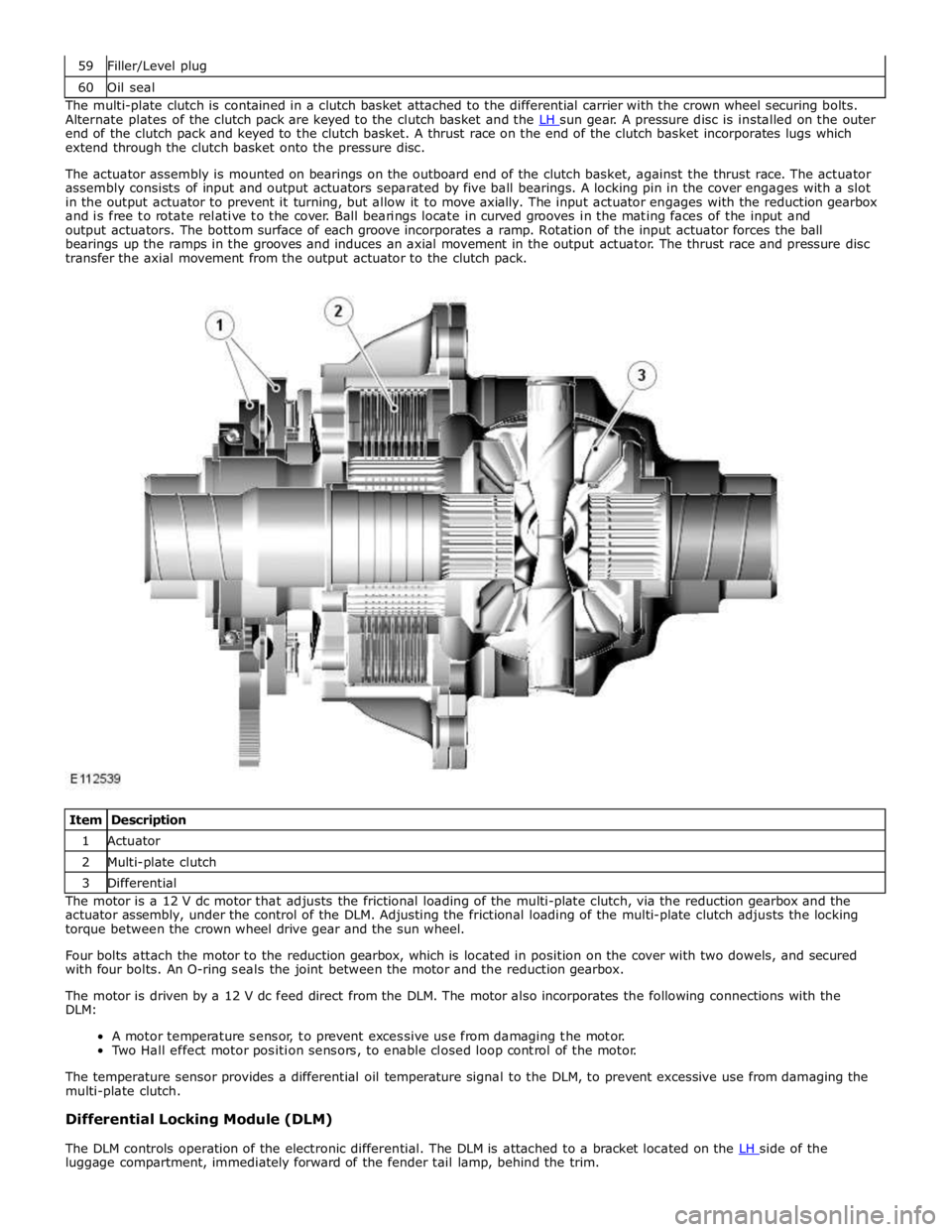
60 Oil seal The multi-plate clutch is contained in a clutch basket attached to the differential carrier with the crown wheel securing bolts.
Alternate plates of the clutch pack are keyed to the clutch basket and the LH sun gear. A pressure disc is installed on the outer end of the clutch pack and keyed to the clutch basket. A thrust race on the end of the clutch basket incorporates lugs which
extend through the clutch basket onto the pressure disc.
The actuator assembly is mounted on bearings on the outboard end of the clutch basket, against the thrust race. The actuator
assembly consists of input and output actuators separated by five ball bearings. A locking pin in the cover engages with a slot
in the output actuator to prevent it turning, but allow it to move axially. The input actuator engages with the reduction gearbox
and is free to rotate relative to the cover. Ball bearings locate in curved grooves in the mating faces of the input and
output actuators. The bottom surface of each groove incorporates a ramp. Rotation of the input actuator forces the ball
bearings up the ramps in the grooves and induces an axial movement in the output actuator. The thrust race and pressure disc
transfer the axial movement from the output actuator to the clutch pack.
Item Description 1 Actuator 2 Multi-plate clutch 3 Differential The motor is a 12 V dc motor that adjusts the frictional loading of the multi-plate clutch, via the reduction gearbox and the
actuator assembly, under the control of the DLM. Adjusting the frictional loading of the multi-plate clutch adjusts the locking
torque between the crown wheel drive gear and the sun wheel.
Four bolts attach the motor to the reduction gearbox, which is located in position on the cover with two dowels, and secured
with four bolts. An O-ring seals the joint between the motor and the reduction gearbox.
The motor is driven by a 12 V dc feed direct from the DLM. The motor also incorporates the following connections with the
DLM:
A motor temperature sensor, to prevent excessive use from damaging the motor.
Two Hall effect motor position sensors, to enable closed loop control of the motor.
The temperature sensor provides a differential oil temperature signal to the DLM, to prevent excessive use from damaging the
multi-plate clutch.
Differential Locking Module (DLM)
The DLM controls operation of the electronic differential. The DLM is attached to a bracket located on the LH side of the luggage compartment, immediately forward of the fender tail lamp, behind the trim.
Page 537 of 3039

bus allows the DLM to communicate with other systems on the vehicle.
A certain amount of differential slip is required to allow the vehicle to turn corners and to remain stable under control of the
ABS. The ADM monitors the driver's demands through primary vehicle controls and automatically sets the slip torque in the differential. The system is completely automatic and does not require any special driver input.
The differential strategy in the ADM includes:
A pre-loading function, increasing locking torque with increased driving torque.
A slip controller to decrease locking torque for optimum comfort, e.g. parking.
The ADM memorizes the position of the motor when the ignition is switched off.
CAN bus messages used by the ADM include wheel speed, steering angle, automatic transmission speed, temperature information, car configuration, axle ratios and mode inputs.
The ADM also sends messages via the CAN bus to tell other control modules on the network the status of the electronic differential. The clutch torque and default mode status are some of the main signals sent out by the ADM.
If the DLM or ADM are replaced, a Jaguar approved diagnostic system must be connected to the vehicle and the differential
self-calibration procedure must be performed. This procedure must also be performed if the motor or electronic differential is
replaced.
If a fault occurs with the electronic differential, the ADM, the DLM, or one of the required input signals, the ADM records an
error code and displays a warning in the message center.
The following messages can be displayed:
Message Description Chime E-DIFF NOT
AVAILABLE Differential temperature has reached the overheat threshold. System deactivated until temperature
returns within limits. Single E-DIFF FAULT Fault has occurred with electronic differential. System deactivated until fault rectified. Single