key JAGUAR XFR 2010 1.G Workshop Manual
[x] Cancel search | Manufacturer: JAGUAR, Model Year: 2010, Model line: XFR, Model: JAGUAR XFR 2010 1.GPages: 3039, PDF Size: 58.49 MB
Page 3 of 3039
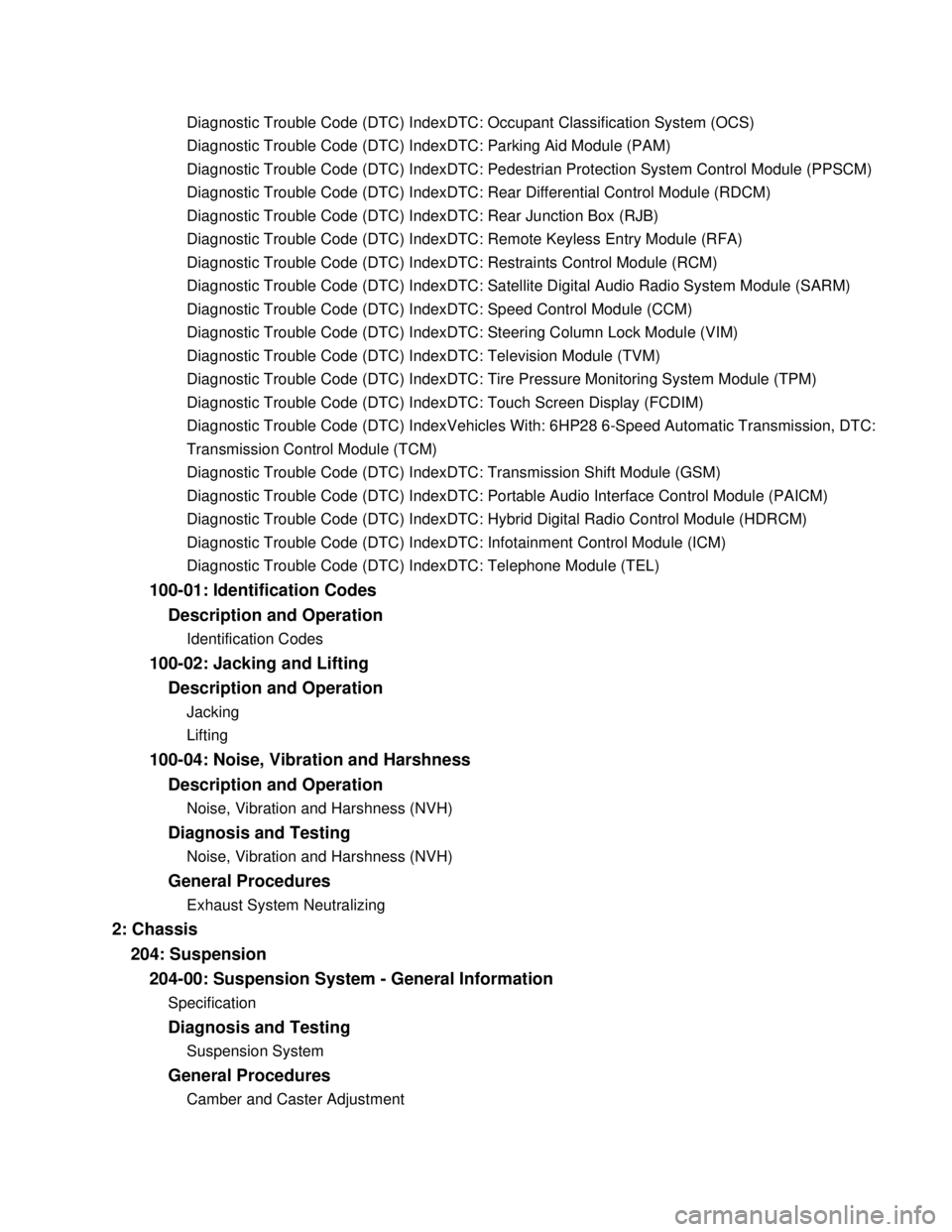
Diagnostic Trouble Code (DTC) IndexDTC: Occupant Classification System (OCS)
Diagnostic Trouble Code (DTC) IndexDTC: Parking Aid Module (PAM)
Diagnostic Trouble Code (DTC) IndexDTC: Pedestrian Protection System Control Module (PPSCM)
Diagnostic Trouble Code (DTC) IndexDTC: Rear Differential Control Module (RDCM)
Diagnostic Trouble Code (DTC) IndexDTC: Rear Junction Box (RJB)
Diagnostic Trouble Code (DTC) IndexDTC: Remote Keyless Entry Module (RFA)
Diagnostic Trouble Code (DTC) IndexDTC: Restraints Control Module (RCM)
Diagnostic Trouble Code (DTC) IndexDTC: Satellite Digital Audio Radio System Module (SARM)
Diagnostic Trouble Code (DTC) IndexDTC: Speed Control Module (CCM)
Diagnostic Trouble Code (DTC) IndexDTC: Steering Column Lock Module (VIM)
Diagnostic Trouble Code (DTC) IndexDTC: Television Module (TVM)
Diagnostic Trouble Code (DTC) IndexDTC: Tire Pressure Monitoring System Module (TPM)
Diagnostic Trouble Code (DTC) IndexDTC: Touch Screen Display (FCDIM)
Diagnostic Trouble Code (DTC) IndexVehicles With: 6HP28 6-Speed Automatic Transmission, DTC:
Transmission Control Module (TCM)
Diagnostic Trouble Code (DTC) IndexDTC: Transmission Shift Module (GSM)
Diagnostic Trouble Code (DTC) IndexDTC: Portable Audio Interface Control Module (PAICM)
Diagnostic Trouble Code (DTC) IndexDTC: Hybrid Digital Radio Control Module (HDRCM)
Diagnostic Trouble Code (DTC) IndexDTC: Infotainment Control Module (ICM)
Diagnostic Trouble Code (DTC) IndexDTC: Telephone Module (TEL)100-01: Identification Codes
Description and OperationIdentification Codes100-02: Jacking and Lifting
Description and OperationJacking
Lifting100-04: Noise, Vibration and Harshness
Description and OperationNoise, Vibration and Harshness (NVH)Diagnosis and TestingNoise, Vibration and Harshness (NVH)General ProceduresExhaust System Neutralizing2: Chassis
204: Suspension
204-00: Suspension System - General InformationSpecificationDiagnosis and TestingSuspension SystemGeneral ProceduresCamber and Caster Adjustment
Page 13 of 3039
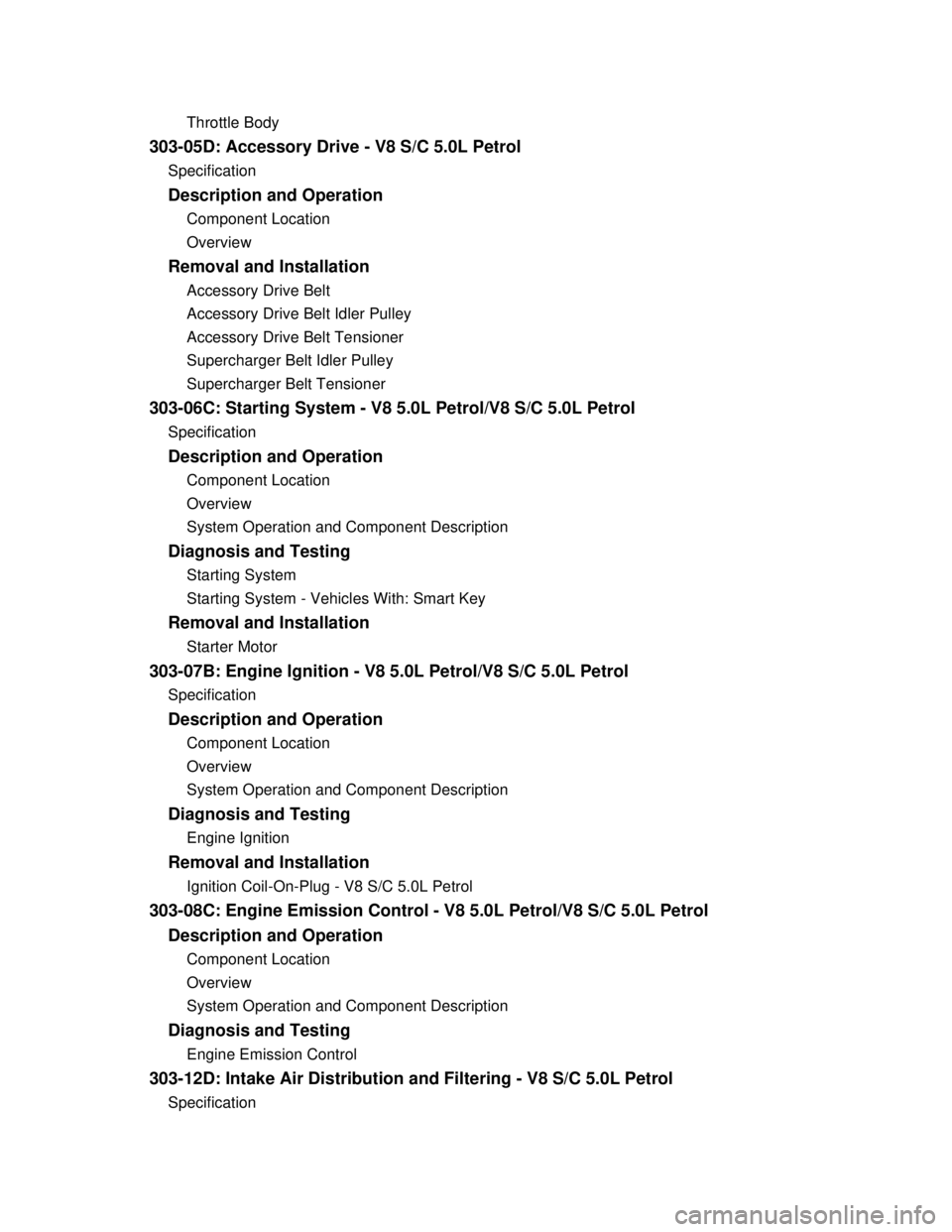
Throttle Body303-05D: Accessory Drive - V8 S/C 5.0L PetrolSpecificationDescription and OperationComponent Location
OverviewRemoval and InstallationAccessory Drive Belt
Accessory Drive Belt Idler Pulley
Accessory Drive Belt Tensioner
Supercharger Belt Idler Pulley
Supercharger Belt Tensioner303-06C: Starting System - V8 5.0L Petrol/V8 S/C 5.0L PetrolSpecificationDescription and OperationComponent Location
Overview
System Operation and Component DescriptionDiagnosis and TestingStarting System
Starting System - Vehicles With: Smart KeyRemoval and InstallationStarter Motor303-07B: Engine Ignition - V8 5.0L Petrol/V8 S/C 5.0L PetrolSpecificationDescription and OperationComponent Location
Overview
System Operation and Component DescriptionDiagnosis and TestingEngine IgnitionRemoval and InstallationIgnition Coil-On-Plug - V8 S/C 5.0L Petrol303-08C: Engine Emission Control - V8 5.0L Petrol/V8 S/C 5.0L Petrol
Description and OperationComponent Location
Overview
System Operation and Component DescriptionDiagnosis and TestingEngine Emission Control303-12D: Intake Air Distribution and Filtering - V8 S/C 5.0L PetrolSpecification
Page 24 of 3039
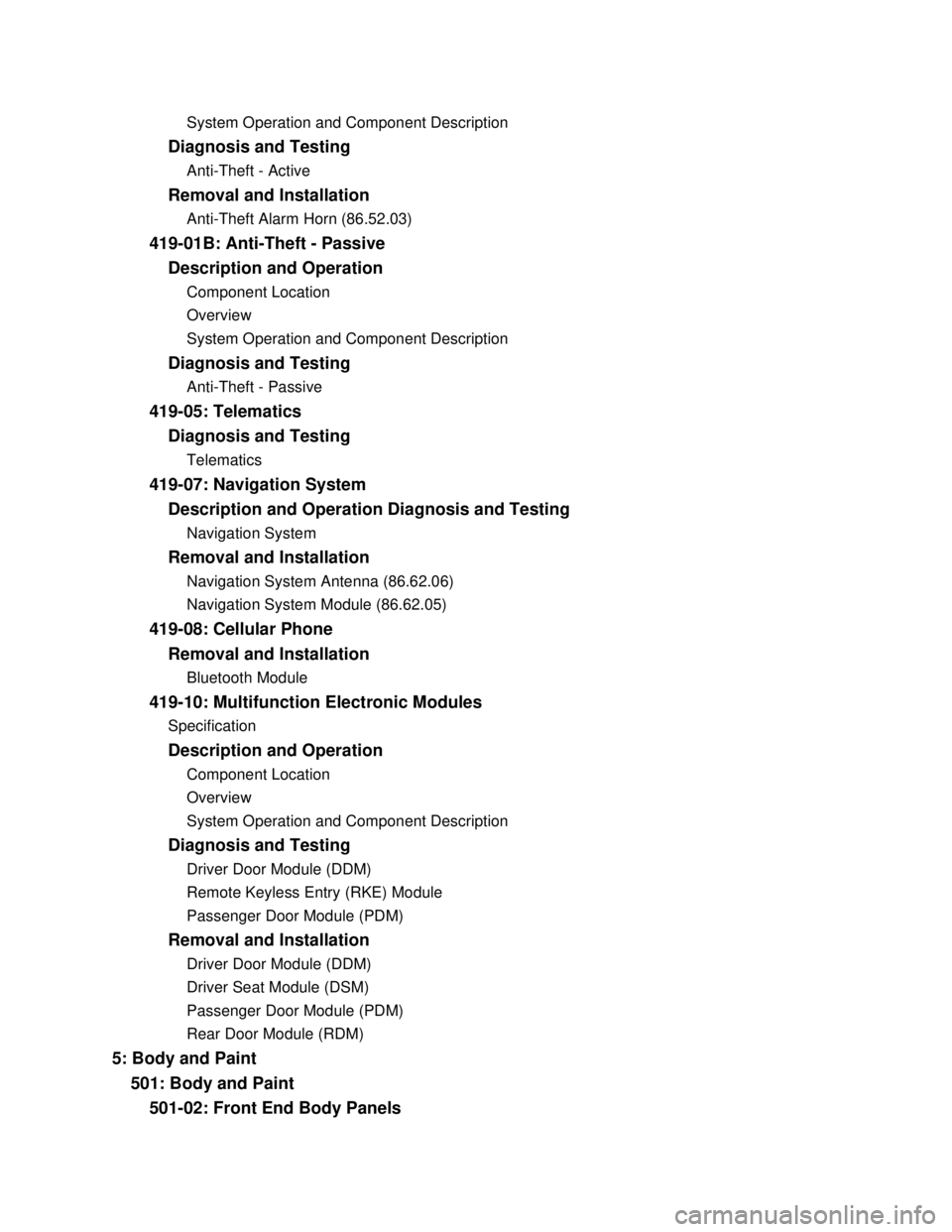
System Operation and Component DescriptionDiagnosis and TestingAnti-Theft - ActiveRemoval and InstallationAnti-Theft Alarm Horn (86.52.03)419-01B: Anti-Theft - Passive
Description and OperationComponent Location
Overview
System Operation and Component DescriptionDiagnosis and TestingAnti-Theft - Passive419-05: Telematics
Diagnosis and TestingTelematics419-07: Navigation System
Description and Operation Diagnosis and TestingNavigation SystemRemoval and InstallationNavigation System Antenna (86.62.06)
Navigation System Module (86.62.05)419-08: Cellular Phone
Removal and InstallationBluetooth Module419-10: Multifunction Electronic ModulesSpecificationDescription and OperationComponent Location
Overview
System Operation and Component DescriptionDiagnosis and TestingDriver Door Module (DDM)
Remote Keyless Entry (RKE) Module
Passenger Door Module (PDM)Removal and InstallationDriver Door Module (DDM)
Driver Seat Module (DSM)
Passenger Door Module (PDM)
Rear Door Module (RDM)5: Body and Paint
501: Body and Paint
501-02: Front End Body Panels
Page 49 of 3039
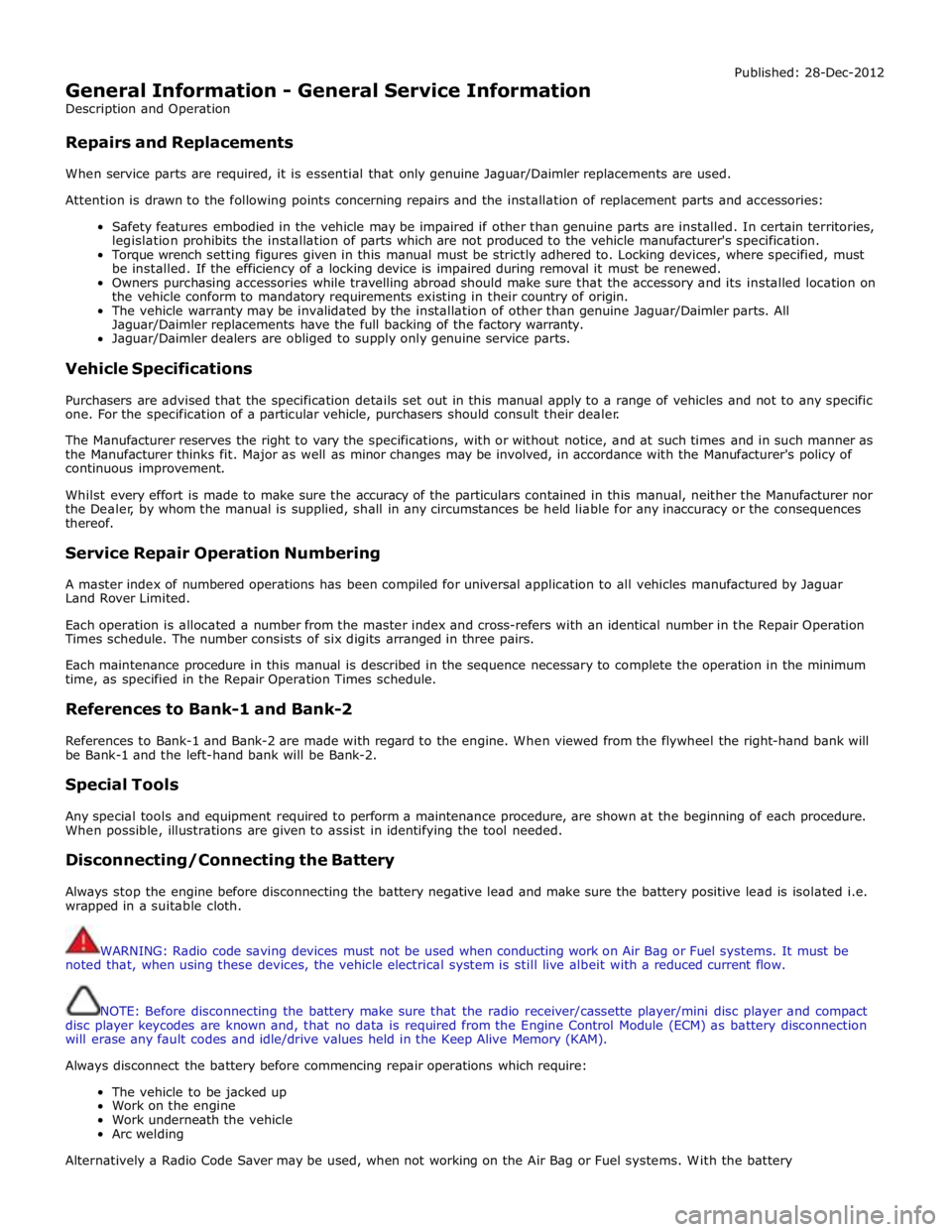
General Information - General Service Information
Description and Operation
Repairs and Replacements Published: 28-Dec-2012
When service parts are required, it is essential that only genuine Jaguar/Daimler replacements are used.
Attention is drawn to the following points concerning repairs and the installation of replacement parts and accessories:
Safety features embodied in the vehicle may be impaired if other than genuine parts are installed. In certain territories,
legislation prohibits the installation of parts which are not produced to the vehicle manufacturer's specification.
Torque wrench setting figures given in this manual must be strictly adhered to. Locking devices, where specified, must
be installed. If the efficiency of a locking device is impaired during removal it must be renewed.
Owners purchasing accessories while travelling abroad should make sure that the accessory and its installed location on
the vehicle conform to mandatory requirements existing in their country of origin.
The vehicle warranty may be invalidated by the installation of other than genuine Jaguar/Daimler parts. All
Jaguar/Daimler replacements have the full backing of the factory warranty.
Jaguar/Daimler dealers are obliged to supply only genuine service parts.
Vehicle Specifications
Purchasers are advised that the specification details set out in this manual apply to a range of vehicles and not to any specific
one. For the specification of a particular vehicle, purchasers should consult their dealer.
The Manufacturer reserves the right to vary the specifications, with or without notice, and at such times and in such manner as
the Manufacturer thinks fit. Major as well as minor changes may be involved, in accordance with the Manufacturer's policy of
continuous improvement.
Whilst every effort is made to make sure the accuracy of the particulars contained in this manual, neither the Manufacturer nor
the Dealer, by whom the manual is supplied, shall in any circumstances be held liable for any inaccuracy or the consequences
thereof.
Service Repair Operation Numbering
A master index of numbered operations has been compiled for universal application to all vehicles manufactured by Jaguar
Land Rover Limited.
Each operation is allocated a number from the master index and cross-refers with an identical number in the Repair Operation
Times schedule. The number consists of six digits arranged in three pairs.
Each maintenance procedure in this manual is described in the sequence necessary to complete the operation in the minimum
time, as specified in the Repair Operation Times schedule.
References to Bank-1 and Bank-2
References to Bank-1 and Bank-2 are made with regard to the engine. When viewed from the flywheel the right-hand bank will
be Bank-1 and the left-hand bank will be Bank-2.
Special Tools
Any special tools and equipment required to perform a maintenance procedure, are shown at the beginning of each procedure.
When possible, illustrations are given to assist in identifying the tool needed.
Disconnecting/Connecting the Battery
Always stop the engine before disconnecting the battery negative lead and make sure the battery positive lead is isolated i.e.
wrapped in a suitable cloth.
WARNING: Radio code saving devices must not be used when conducting work on Air Bag or Fuel systems. It must be
noted that, when using these devices, the vehicle electrical system is still live albeit with a reduced current flow.
NOTE: Before disconnecting the battery make sure that the radio receiver/cassette player/mini disc player and compact
disc player keycodes are known and, that no data is required from the Engine Control Module (ECM) as battery disconnection
will erase any fault codes and idle/drive values held in the Keep Alive Memory (KAM).
Always disconnect the battery before commencing repair operations which require:
The vehicle to be jacked up
Work on the engine
Work underneath the vehicle
Arc welding
Alternatively a Radio Code Saver may be used, when not working on the Air Bag or Fuel systems. With the battery
Page 50 of 3039
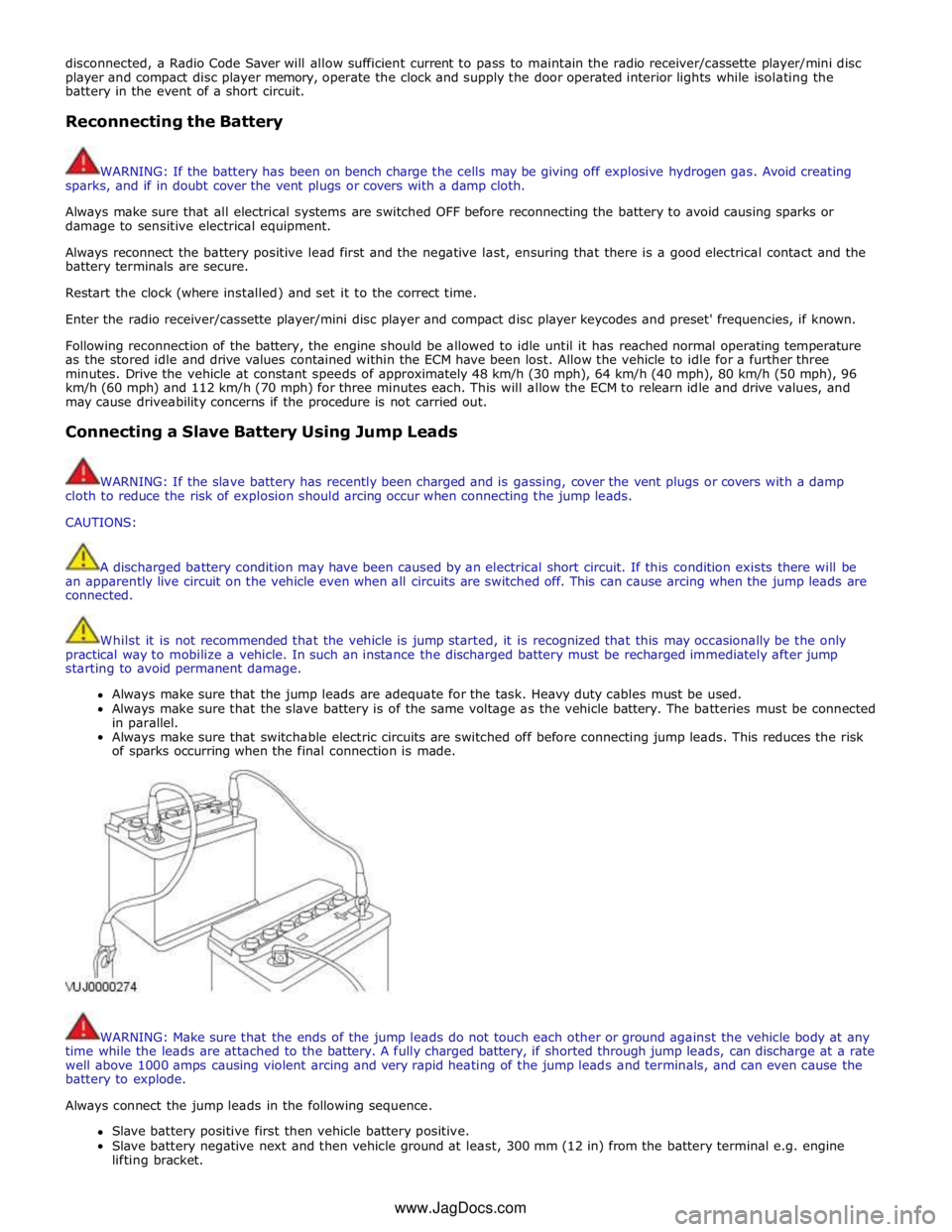
disconnected, a Radio Code Saver will allow sufficient current to pass to maintain the radio receiver/cassette player/mini disc
player and compact disc player memory, operate the clock and supply the door operated interior lights while isolating the
battery in the event of a short circuit.
Reconnecting the Battery
WARNING: If the battery has been on bench charge the cells may be giving off explosive hydrogen gas. Avoid creating
sparks, and if in doubt cover the vent plugs or covers with a damp cloth.
Always make sure that all electrical systems are switched OFF before reconnecting the battery to avoid causing sparks or
damage to sensitive electrical equipment.
Always reconnect the battery positive lead first and the negative last, ensuring that there is a good electrical contact and the
battery terminals are secure.
Restart the clock (where installed) and set it to the correct time.
Enter the radio receiver/cassette player/mini disc player and compact disc player keycodes and preset' frequencies, if known.
Following reconnection of the battery, the engine should be allowed to idle until it has reached normal operating temperature
as the stored idle and drive values contained within the ECM have been lost. Allow the vehicle to idle for a further three
minutes. Drive the vehicle at constant speeds of approximately 48 km/h (30 mph), 64 km/h (40 mph), 80 km/h (50 mph), 96
km/h (60 mph) and 112 km/h (70 mph) for three minutes each. This will allow the ECM to relearn idle and drive values, and
may cause driveability concerns if the procedure is not carried out.
Connecting a Slave Battery Using Jump Leads
WARNING: If the slave battery has recently been charged and is gassing, cover the vent plugs or covers with a damp
cloth to reduce the risk of explosion should arcing occur when connecting the jump leads.
CAUTIONS:
A discharged battery condition may have been caused by an electrical short circuit. If this condition exists there will be
an apparently live circuit on the vehicle even when all circuits are switched off. This can cause arcing when the jump leads are
connected.
Whilst it is not recommended that the vehicle is jump started, it is recognized that this may occasionally be the only
practical way to mobilize a vehicle. In such an instance the discharged battery must be recharged immediately after jump
starting to avoid permanent damage.
Always make sure that the jump leads are adequate for the task. Heavy duty cables must be used.
Always make sure that the slave battery is of the same voltage as the vehicle battery. The batteries must be connected
in parallel.
Always make sure that switchable electric circuits are switched off before connecting jump leads. This reduces the risk
of sparks occurring when the final connection is made.
WARNING: Make sure that the ends of the jump leads do not touch each other or ground against the vehicle body at any
time while the leads are attached to the battery. A fully charged battery, if shorted through jump leads, can discharge at a rate
well above 1000 amps causing violent arcing and very rapid heating of the jump leads and terminals, and can even cause the
battery to explode.
Always connect the jump leads in the following sequence.
Slave battery positive first then vehicle battery positive.
Slave battery negative next and then vehicle ground at least, 300 mm (12 in) from the battery terminal e.g. engine
lifting bracket. www.JagDocs.com
Page 54 of 3039
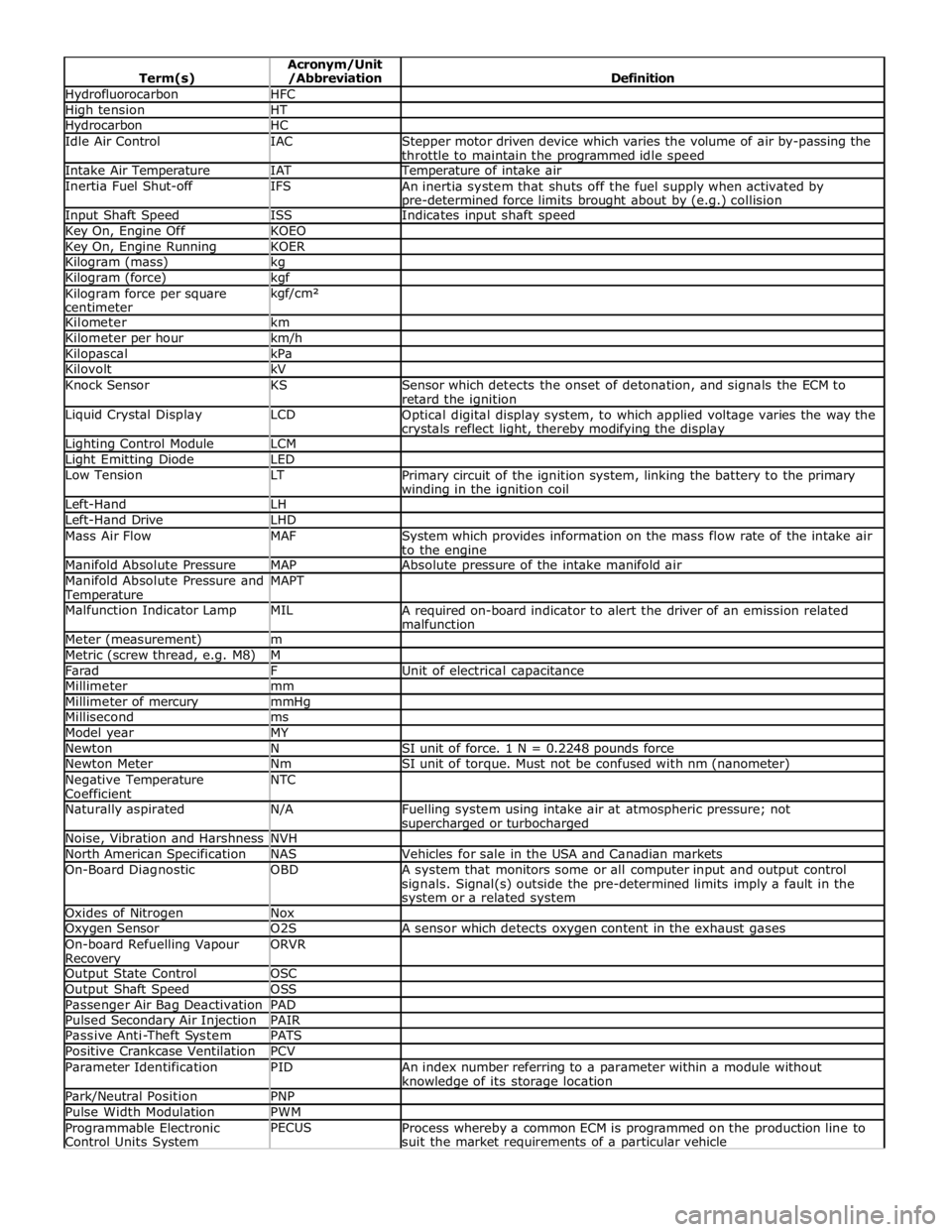
Hydrofluorocarbon HFC High tension HT Hydrocarbon HC Idle Air Control IAC
Stepper motor driven device which varies the volume of air by-passing the
throttle to maintain the programmed idle speed Intake Air Temperature IAT Temperature of intake air Inertia Fuel Shut-off IFS
An inertia system that shuts off the fuel supply when activated by pre-determined force limits brought about by (e.g.) collision Input Shaft Speed ISS Indicates input shaft speed Key On, Engine Off KOEO Key On, Engine Running KOER Kilogram (mass) kg Kilogram (force) kgf Kilogram force per square
centimeter kgf/cm²
Kilometer km Kilometer per hour km/h Kilopascal kPa Kilovolt kV Knock Sensor KS
Sensor which detects the onset of detonation, and signals the ECM to
retard the ignition Liquid Crystal Display LCD
Optical digital display system, to which applied voltage varies the way the crystals reflect light, thereby modifying the display Lighting Control Module LCM Light Emitting Diode LED Low Tension LT
Primary circuit of the ignition system, linking the battery to the primary winding in the ignition coil Left-Hand LH Left-Hand Drive LHD Mass Air Flow MAF
System which provides information on the mass flow rate of the intake air
to the engine Manifold Absolute Pressure MAP Absolute pressure of the intake manifold air Manifold Absolute Pressure and Temperature MAPT
Malfunction Indicator Lamp MIL
A required on-board indicator to alert the driver of an emission related
malfunction Meter (measurement) m Metric (screw thread, e.g. M8) M Farad F Unit of electrical capacitance Millimeter mm Millimeter of mercury mmHg Millisecond ms Model year MY Newton N SI unit of force. 1 N = 0.2248 pounds force Newton Meter Nm SI unit of torque. Must not be confused with nm (nanometer) Negative Temperature
Coefficient NTC
Naturally aspirated N/A
Fuelling system using intake air at atmospheric pressure; not supercharged or turbocharged Noise, Vibration and Harshness NVH North American Specification NAS Vehicles for sale in the USA and Canadian markets On-Board Diagnostic OBD
A system that monitors some or all computer input and output control
signals. Signal(s) outside the pre-determined limits imply a fault in the system or a related system Oxides of Nitrogen Nox Oxygen Sensor O2S A sensor which detects oxygen content in the exhaust gases On-board Refuelling Vapour Recovery ORVR
Output State Control OSC Output Shaft Speed OSS Passenger Air Bag Deactivation PAD Pulsed Secondary Air Injection PAIR Passive Anti-Theft System PATS Positive Crankcase Ventilation PCV Parameter Identification PID
An index number referring to a parameter within a module without knowledge of its storage location Park/Neutral Position PNP Pulse Width Modulation PWM Programmable Electronic
Control Units System PECUS
Process whereby a common ECM is programmed on the production line to
suit the market requirements of a particular vehicle
Page 55 of 3039
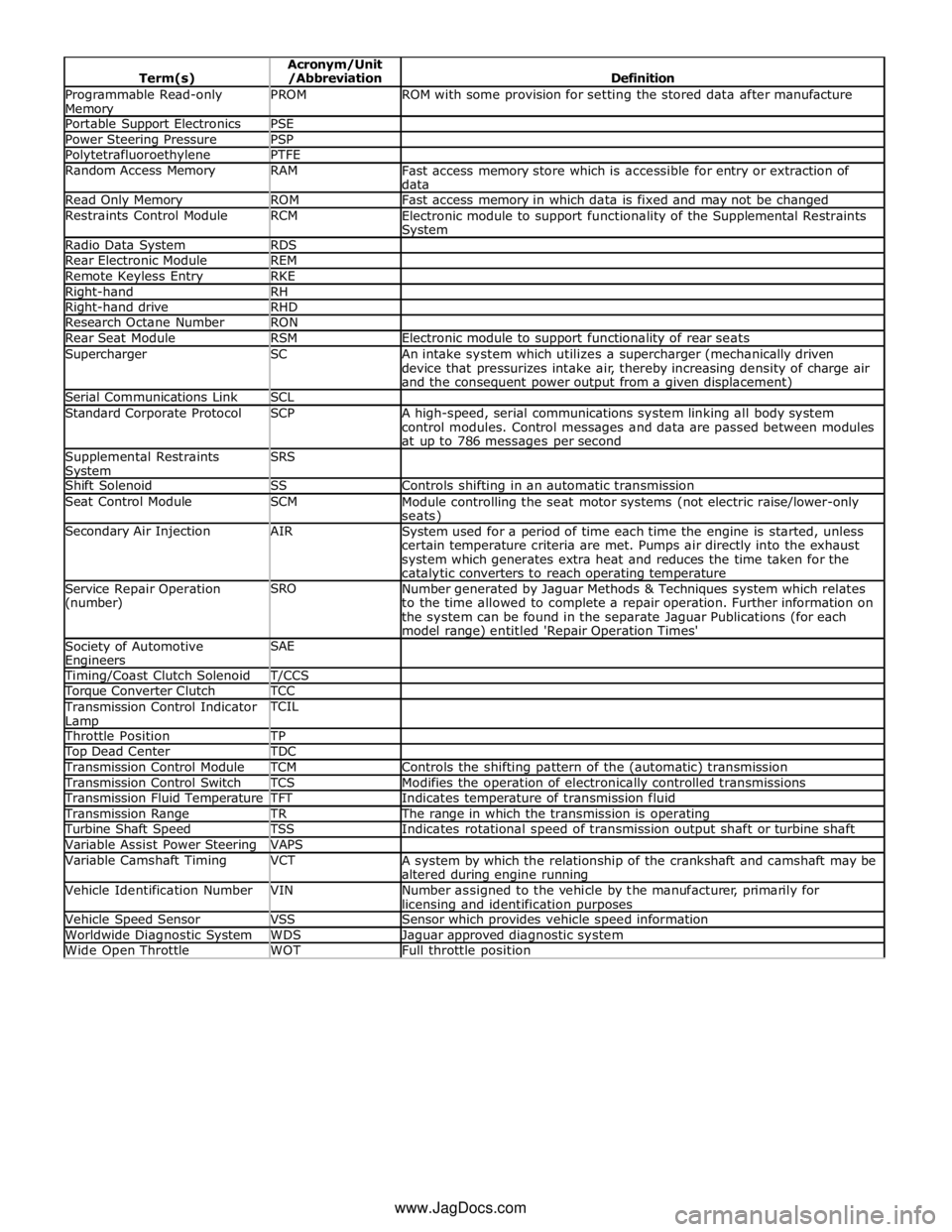
Programmable Read-only Memory PROM ROM with some provision for setting the stored data after manufacture Portable Support Electronics PSE Power Steering Pressure PSP Polytetrafluoroethylene PTFE Random Access Memory RAM
Fast access memory store which is accessible for entry or extraction of
data Read Only Memory ROM Fast access memory in which data is fixed and may not be changed Restraints Control Module RCM
Electronic module to support functionality of the Supplemental Restraints System Radio Data System RDS Rear Electronic Module REM Remote Keyless Entry RKE Right-hand RH Right-hand drive RHD Research Octane Number RON Rear Seat Module RSM Electronic module to support functionality of rear seats Supercharger SC
An intake system which utilizes a supercharger (mechanically driven
device that pressurizes intake air, thereby increasing density of charge air
and the consequent power output from a given displacement) Serial Communications Link SCL Standard Corporate Protocol SCP
A high-speed, serial communications system linking all body system
control modules. Control messages and data are passed between modules
at up to 786 messages per second Supplemental Restraints System SRS
Shift Solenoid SS Controls shifting in an automatic transmission Seat Control Module SCM
Module controlling the seat motor systems (not electric raise/lower-only seats) Secondary Air Injection AIR
System used for a period of time each time the engine is started, unless
certain temperature criteria are met. Pumps air directly into the exhaust
system which generates extra heat and reduces the time taken for the catalytic converters to reach operating temperature Service Repair Operation
(number) SRO
Number generated by Jaguar Methods & Techniques system which relates
to the time allowed to complete a repair operation. Further information on
the system can be found in the separate Jaguar Publications (for each
model range) entitled 'Repair Operation Times' Society of Automotive Engineers SAE
Timing/Coast Clutch Solenoid T/CCS Torque Converter Clutch TCC Transmission Control Indicator
Lamp TCIL
Throttle Position TP Top Dead Center TDC Transmission Control Module TCM Controls the shifting pattern of the (automatic) transmission Transmission Control Switch TCS Modifies the operation of electronically controlled transmissions Transmission Fluid Temperature TFT Indicates temperature of transmission fluid Transmission Range TR The range in which the transmission is operating Turbine Shaft Speed TSS Indicates rotational speed of transmission output shaft or turbine shaft Variable Assist Power Steering VAPS Variable Camshaft Timing VCT
A system by which the relationship of the crankshaft and camshaft may be
altered during engine running Vehicle Identification Number VIN
Number assigned to the vehicle by the manufacturer, primarily for licensing and identification purposes Vehicle Speed Sensor VSS Sensor which provides vehicle speed information Worldwide Diagnostic System WDS Jaguar approved diagnostic system Wide Open Throttle WOT Full throttle position www.JagDocs.com
Page 73 of 3039
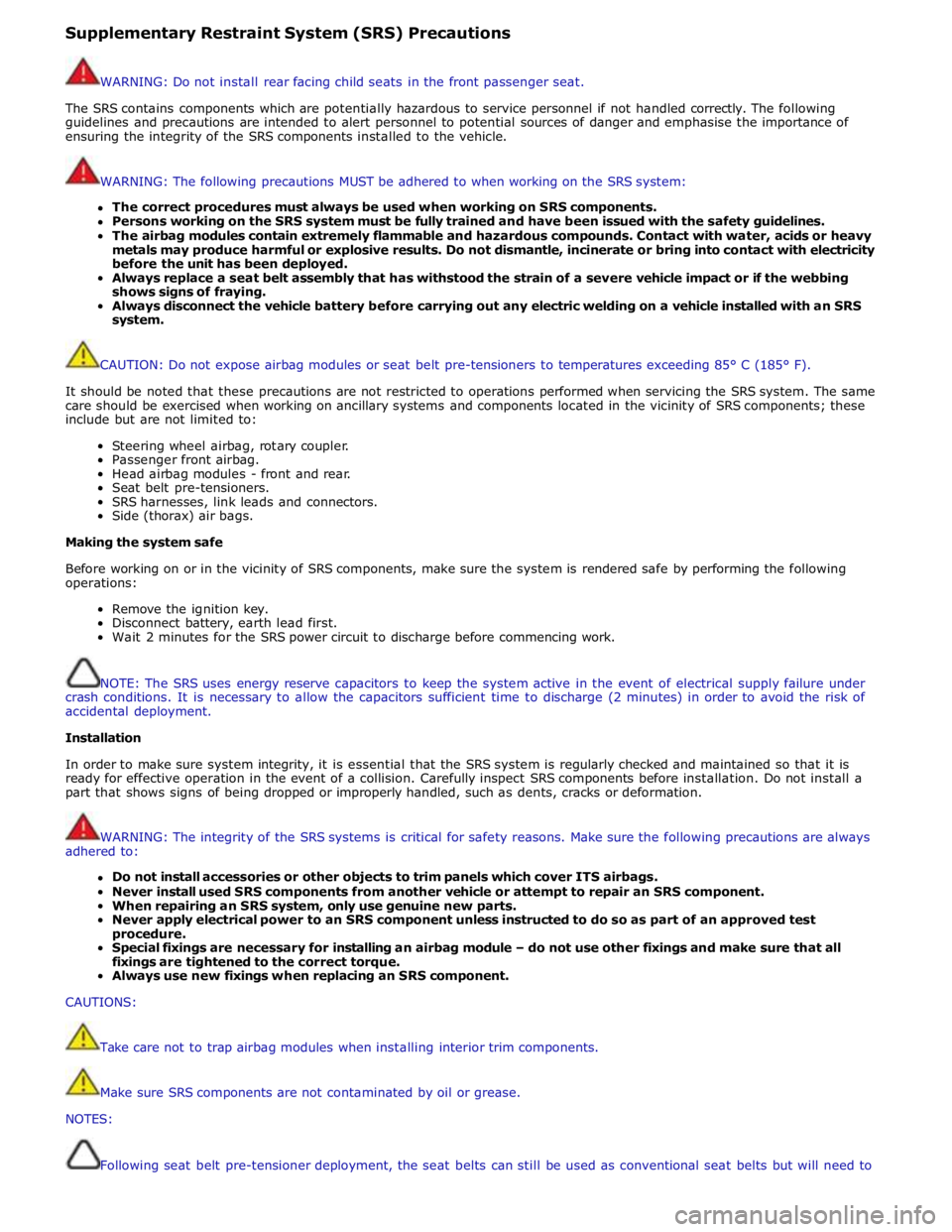
Supplementary Restraint System (SRS) Precautions
WARNING: Do not install rear facing child seats in the front passenger seat.
The SRS contains components which are potentially hazardous to service personnel if not handled correctly. The following
guidelines and precautions are intended to alert personnel to potential sources of danger and emphasise the importance of
ensuring the integrity of the SRS components installed to the vehicle.
WARNING: The following precautions MUST be adhered to when working on the SRS system:
The correct procedures must always be used when working on SRS components.
Persons working on the SRS system must be fully trained and have been issued with the safety guidelines.
The airbag modules contain extremely flammable and hazardous compounds. Contact with water, acids or heavy
metals may produce harmful or explosive results. Do not dismantle, incinerate or bring into contact with electricity
before the unit has been deployed.
Always replace a seat belt assembly that has withstood the strain of a severe vehicle impact or if the webbing
shows signs of fraying.
Always disconnect the vehicle battery before carrying out any electric welding on a vehicle installed with an SRS
system.
CAUTION: Do not expose airbag modules or seat belt pre-tensioners to temperatures exceeding 85° C (185° F).
It should be noted that these precautions are not restricted to operations performed when servicing the SRS system. The same
care should be exercised when working on ancillary systems and components located in the vicinity of SRS components; these
include but are not limited to:
Steering wheel airbag, rotary coupler.
Passenger front airbag.
Head airbag modules - front and rear.
Seat belt pre-tensioners.
SRS harnesses, link leads and connectors.
Side (thorax) air bags.
Making the system safe
Before working on or in the vicinity of SRS components, make sure the system is rendered safe by performing the following
operations:
Remove the ignition key.
Disconnect battery, earth lead first.
Wait 2 minutes for the SRS power circuit to discharge before commencing work.
NOTE: The SRS uses energy reserve capacitors to keep the system active in the event of electrical supply failure under
crash conditions. It is necessary to allow the capacitors sufficient time to discharge (2 minutes) in order to avoid the risk of
accidental deployment.
Installation
In order to make sure system integrity, it is essential that the SRS system is regularly checked and maintained so that it is
ready for effective operation in the event of a collision. Carefully inspect SRS components before installation. Do not install a
part that shows signs of being dropped or improperly handled, such as dents, cracks or deformation.
WARNING: The integrity of the SRS systems is critical for safety reasons. Make sure the following precautions are always
adhered to:
Do not install accessories or other objects to trim panels which cover ITS airbags.
Never install used SRS components from another vehicle or attempt to repair an SRS component.
When repairing an SRS system, only use genuine new parts.
Never apply electrical power to an SRS component unless instructed to do so as part of an approved test
procedure.
Special fixings are necessary for installing an airbag module – do not use other fixings and make sure that all
fixings are tightened to the correct torque.
Always use new fixings when replacing an SRS component.
CAUTIONS:
Take care not to trap airbag modules when installing interior trim components.
Make sure SRS components are not contaminated by oil or grease.
NOTES:
Following seat belt pre-tensioner deployment, the seat belts can still be used as conventional seat belts but will need to
Page 101 of 3039
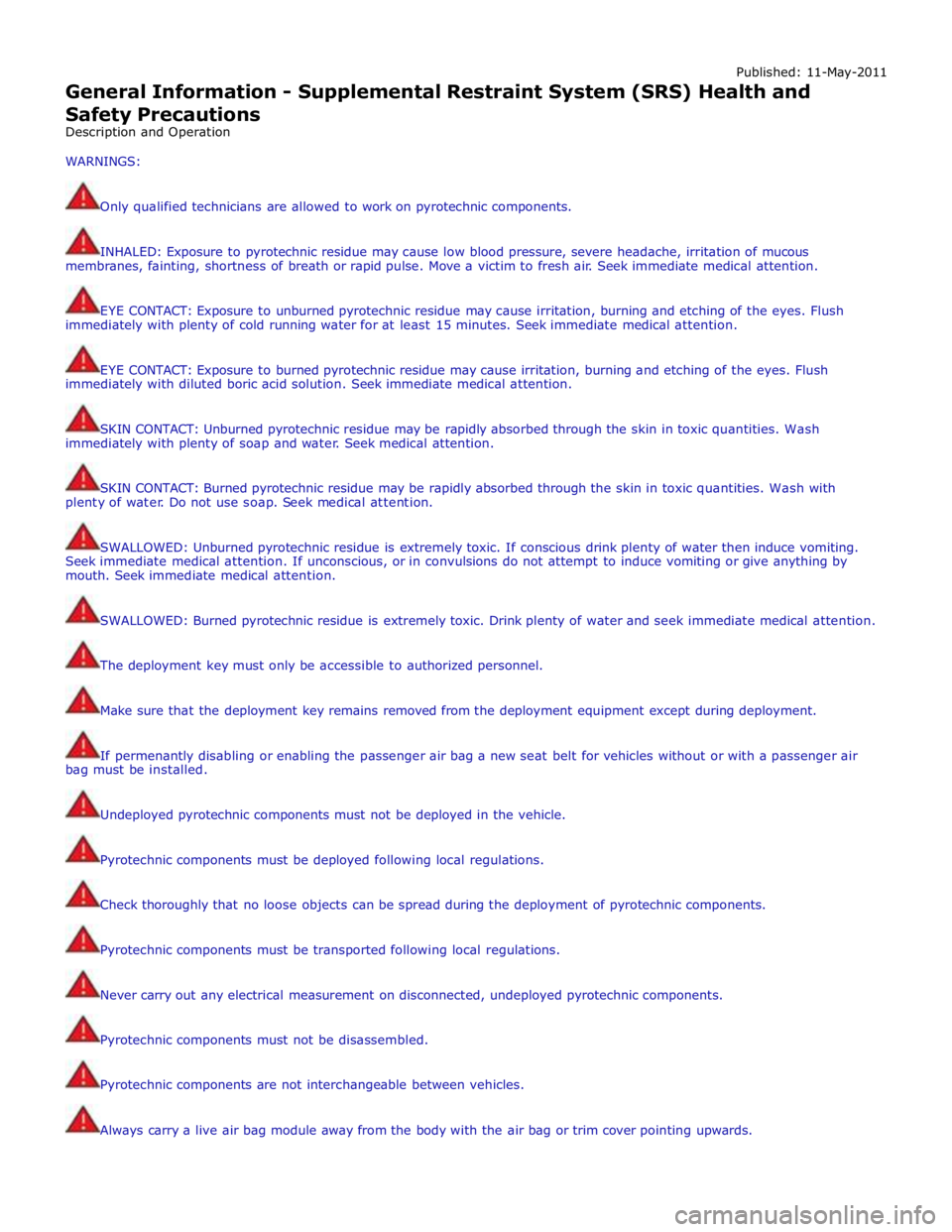
Published: 11-May-2011
General Information - Supplemental Restraint System (SRS) Health and
Safety Precautions
Description and Operation
WARNINGS:
Only qualified technicians are allowed to work on pyrotechnic components.
INHALED: Exposure to pyrotechnic residue may cause low blood pressure, severe headache, irritation of mucous
membranes, fainting, shortness of breath or rapid pulse. Move a victim to fresh air. Seek immediate medical attention.
EYE CONTACT: Exposure to unburned pyrotechnic residue may cause irritation, burning and etching of the eyes. Flush
immediately with plenty of cold running water for at least 15 minutes. Seek immediate medical attention.
EYE CONTACT: Exposure to burned pyrotechnic residue may cause irritation, burning and etching of the eyes. Flush
immediately with diluted boric acid solution. Seek immediate medical attention.
SKIN CONTACT: Unburned pyrotechnic residue may be rapidly absorbed through the skin in toxic quantities. Wash
immediately with plenty of soap and water. Seek medical attention.
SKIN CONTACT: Burned pyrotechnic residue may be rapidly absorbed through the skin in toxic quantities. Wash with
plenty of water. Do not use soap. Seek medical attention.
SWALLOWED: Unburned pyrotechnic residue is extremely toxic. If conscious drink plenty of water then induce vomiting.
Seek immediate medical attention. If unconscious, or in convulsions do not attempt to induce vomiting or give anything by
mouth. Seek immediate medical attention.
SWALLOWED: Burned pyrotechnic residue is extremely toxic. Drink plenty of water and seek immediate medical attention.
The deployment key must only be accessible to authorized personnel.
Make sure that the deployment key remains removed from the deployment equipment except during deployment.
If permenantly disabling or enabling the passenger air bag a new seat belt for vehicles without or with a passenger air
bag must be installed.
Undeployed pyrotechnic components must not be deployed in the vehicle.
Pyrotechnic components must be deployed following local regulations.
Check thoroughly that no loose objects can be spread during the deployment of pyrotechnic components.
Pyrotechnic components must be transported following local regulations.
Never carry out any electrical measurement on disconnected, undeployed pyrotechnic components.
Pyrotechnic components must not be disassembled.
Pyrotechnic components are not interchangeable between vehicles.
Always carry a live air bag module away from the body with the air bag or trim cover pointing upwards.
Page 135 of 3039
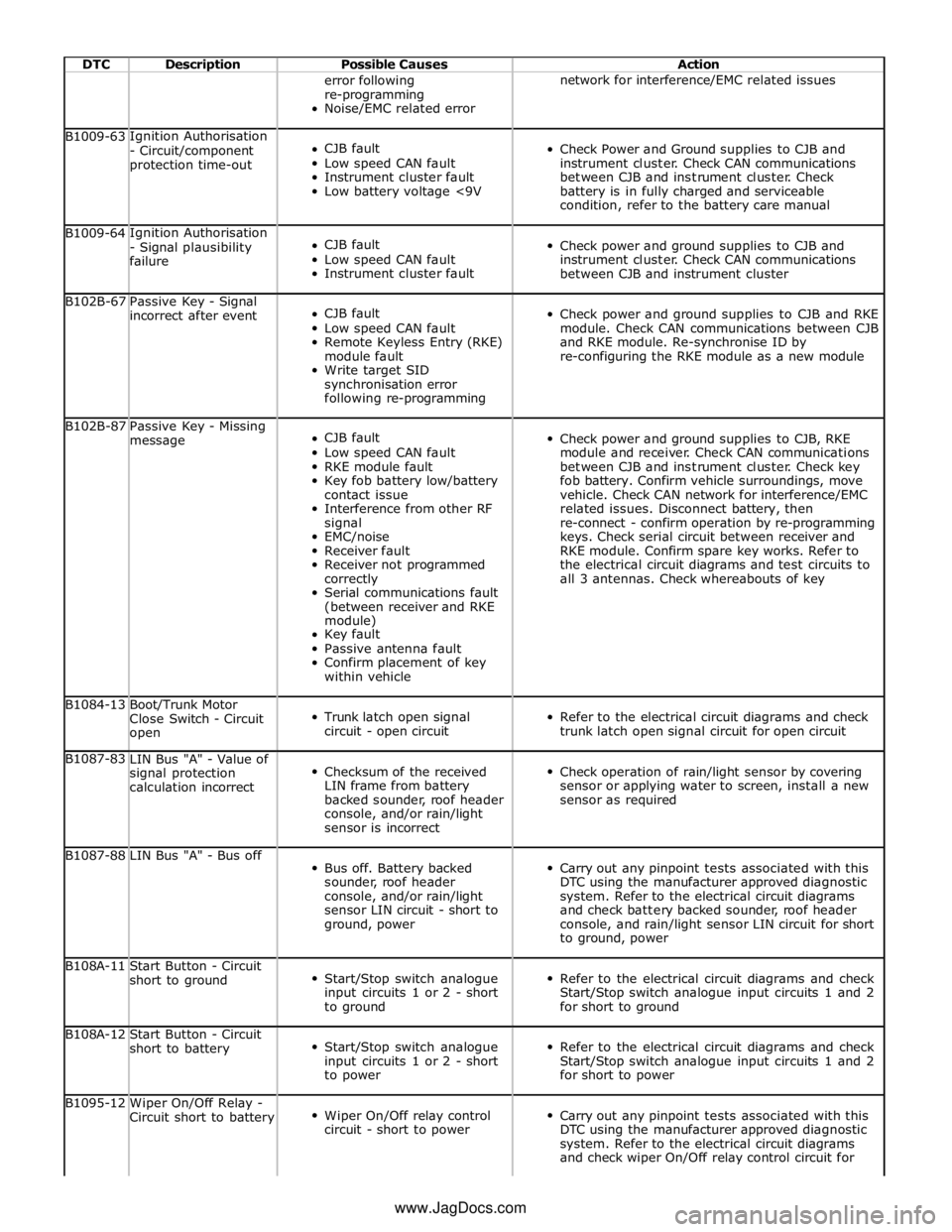
DTC Description Possible Causes Action error following
re-programming
Noise/EMC related error network for interference/EMC related issues B1009-63 Ignition Authorisation
- Circuit/component
protection time-out
CJB fault
Low speed CAN fault
Instrument cluster fault
Low battery voltage <9V
Check Power and Ground supplies to CJB and
instrument cluster. Check CAN communications
between CJB and instrument cluster. Check
battery is in fully charged and serviceable
condition, refer to the battery care manual B1009-64 Ignition Authorisation
- Signal plausibility
failure
CJB fault
Low speed CAN fault
Instrument cluster fault
Check power and ground supplies to CJB and
instrument cluster. Check CAN communications
between CJB and instrument cluster B102B-67
Passive Key - Signal
incorrect after event
CJB fault
Low speed CAN fault
Remote Keyless Entry (RKE)
module fault
Write target SID
synchronisation error
following re-programming
Check power and ground supplies to CJB and RKE
module. Check CAN communications between CJB
and RKE module. Re-synchronise ID by
re-configuring the RKE module as a new module B102B-87
Passive Key - Missing
message
CJB fault
Low speed CAN fault
RKE module fault
Key fob battery low/battery
contact issue
Interference from other RF
signal
EMC/noise
Receiver fault
Receiver not programmed
correctly
Serial communications fault
(between receiver and RKE
module)
Key fault
Passive antenna fault
Confirm placement of key
within vehicle
Check power and ground supplies to CJB, RKE
module and receiver. Check CAN communications
between CJB and instrument cluster. Check key
fob battery. Confirm vehicle surroundings, move
vehicle. Check CAN network for interference/EMC
related issues. Disconnect battery, then
re-connect - confirm operation by re-programming
keys. Check serial circuit between receiver and
RKE module. Confirm spare key works. Refer to
the electrical circuit diagrams and test circuits to
all 3 antennas. Check whereabouts of key B1084-13
Boot/Trunk Motor
Close Switch - Circuit
open
Trunk latch open signal
circuit - open circuit
Refer to the electrical circuit diagrams and check
trunk latch open signal circuit for open circuit B1087-83
LIN Bus "A" - Value of
signal protection
calculation incorrect
Checksum of the received
LIN frame from battery
backed sounder, roof header
console, and/or rain/light
sensor is incorrect
Check operation of rain/light sensor by covering
sensor or applying water to screen, install a new
sensor as required B1087-88 LIN Bus "A" - Bus off
Bus off. Battery backed
sounder, roof header
console, and/or rain/light
sensor LIN circuit - short to
ground, power
Carry out any pinpoint tests associated with this
DTC using the manufacturer approved diagnostic
system. Refer to the electrical circuit diagrams
and check battery backed sounder, roof header
console, and rain/light sensor LIN circuit for short
to ground, power B108A-11
Start Button - Circuit
short to ground
Start/Stop switch analogue
input circuits 1 or 2 - short
to ground
Refer to the electrical circuit diagrams and check
Start/Stop switch analogue input circuits 1 and 2
for short to ground B108A-12
Start Button - Circuit
short to battery
Start/Stop switch analogue
input circuits 1 or 2 - short
to power
Refer to the electrical circuit diagrams and check
Start/Stop switch analogue input circuits 1 and 2
for short to power B1095-12
Wiper On/Off Relay -
Circuit short to battery
Wiper On/Off relay control
circuit - short to power
Carry out any pinpoint tests associated with this
DTC using the manufacturer approved diagnostic
system. Refer to the electrical circuit diagrams
and check wiper On/Off relay control circuit for www.JagDocs.com