JEEP CJ 1953 Service Manual
Manufacturer: JEEP, Model Year: 1953, Model line: CJ, Model: JEEP CJ 1953Pages: 376, PDF Size: 19.96 MB
Page 101 of 376
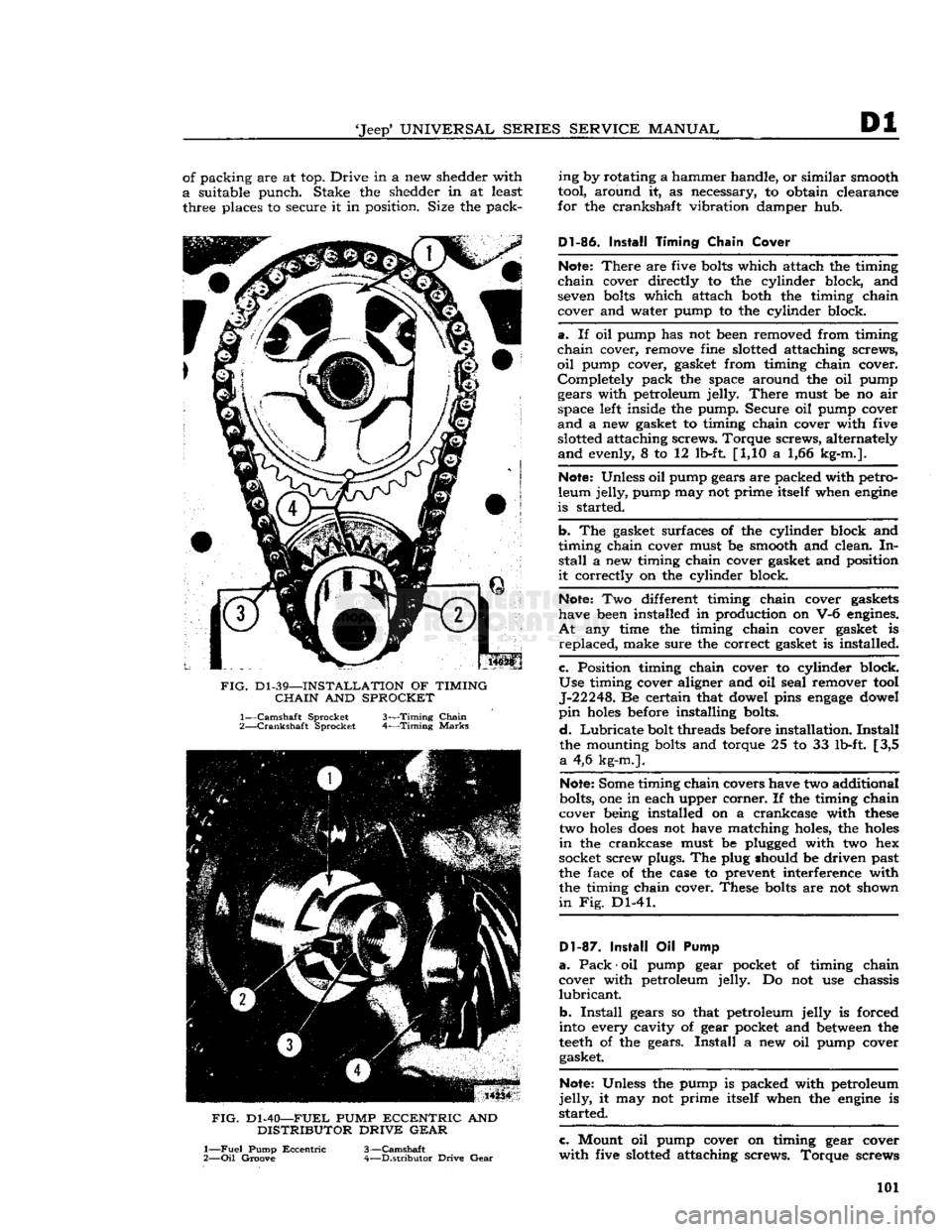
'Jeep*
UNIVERSAL
SERIES SERVICE
MANUAL
Dl
of packing are at top. Drive in a new shedder with
a
suitable punch. Stake the shedder in at least three places to secure it in position. Size the pack-
FIG.
Dl-39—INSTALLATION
OF
TIMING
CHAIN
AND
SPROCKET
1—
Camshaft
Sprocket 3—Timing
Chain
2—
Crankshaft
Sprocket 4—Timing
Marks
FIG.
Dl-40—FUEL
PUMP
ECCENTRIC
AND
DISTRIBUTOR
DRIVE GEAR
1—
Fuel
Pump
Eccentric
3—Camshaft
2—
Oil
Groove 4—Distributor Drive
Gear
ing by rotating a hammer handle, or similar smooth
tool, around it, as necessary, to obtain clearance
for the crankshaft vibration damper hub.
Dl-86.
Install
Timing
Chain
Cover
Note:
There
are five
bolts
which attach the timing
chain
cover directly to the cylinder block, and seven
bolts
which attach both the timing chain
cover and water pump to the cylinder block.
a.
If oil pump has not been removed from timing
chain
cover, remove fine slotted attaching screws,
oil
pump cover, gasket from timing chain cover. Completely pack the space around the oil pump gears with petroleum jelly.
There
must be no air
space left inside the pump. Secure oil pump cover
and
a new gasket to timing chain cover with five slotted attaching screws. Torque screws, alternately
and
evenly, 8 to 12 lb-ft [1,10 a 1,66 kg-m.].
Note:
Unless oil pump gears are packed with petro
leum jelly, pump may not prime itself when
engine
is started.
b.
The gasket surfaces of the cylinder block and
timing chain cover must be smooth and clean. In
stall
a new timing chain cover gasket and position
it
correctly on the cylinder block.
Note:
Two different timing chain cover gaskets
have been installed in production on V-6 engines.
At
any time the timing chain cover gasket is
replaced,
make sure the correct gasket is installed.
c.
Position timing chain cover to cylinder block.
Use
timing cover aligner and oil seal remover tool J-22248. Be certain that dowel pins
engage
dowel
pin
holes
before installing bolts.
d.
Lubricate
bolt threads before installation.
Install
the mounting
bolts
and torque 25 to 33 lb-ft. [3,5
a
4,6 kg-m.].
Note:
Some timing chain covers have two additional
bolts, one in each upper corner. If the timing chain
cover being installed on a crankcase with
these
two
holes
does
not have matching holes, the
holes
in
the crankcase must be plugged with two hex
socket screw plugs. The plug should be driven past
the face of the case to prevent interference with the timing chain cover. These
bolts
are not shown
in
Fig. Dl-41.
D1-87.
Install
Oil Pump
a.
Pack
•
oil pump gear pocket of timing chain
cover with petroleum jelly. Do not use chassis
lubricant.
b.
Install
gears so that petroleum jelly is forced
into every cavity of gear pocket and
between
the
teeth
of the gears.
Install
a new oil pump cover gasket.
Note:
Unless the pump is packed with petroleum
jelly,
it may not prime itself when the
engine
is
started.
c.
Mount oil pump cover on timing gear cover
with
five slotted attaching screws. Torque screws 101
Page 102 of 376
![JEEP CJ 1953 Service Manual
Dl
DAUNTLESS
V-6
ENGINE
FIG.
Dl-41—WATER
PUMP
AND
TIMING CHAIN COVER BOLT LOCATION
Cover
Bolts
alternately and evenly 8 to 12 lb-ft. [1,10 a 1,66
kg-m.].
Dl-88.
Install
Cranksh JEEP CJ 1953 Service Manual
Dl
DAUNTLESS
V-6
ENGINE
FIG.
Dl-41—WATER
PUMP
AND
TIMING CHAIN COVER BOLT LOCATION
Cover
Bolts
alternately and evenly 8 to 12 lb-ft. [1,10 a 1,66
kg-m.].
Dl-88.
Install
Cranksh](/img/16/57040/w960_57040-101.png)
Dl
DAUNTLESS
V-6
ENGINE
FIG.
Dl-41—WATER
PUMP
AND
TIMING CHAIN COVER BOLT LOCATION
Cover
Bolts
alternately and evenly 8 to 12 lb-ft. [1,10 a 1,66
kg-m.].
Dl-88.
Install
Crankshaft
Vibration
Damper
a.
Lubricate
the vibration damper hub
before
in
stallation to prevent
damage
to the crankshaft
front oil seal during installation and when the
engine
is first started.
b.
Install
the vibration damper on the crankshaft.
Secure it with its attaching flat washer and screw.
Torque
the screw to a minimum of 140 lb-ft.
[19,35
kg-m.].
Dl-89.
Install
Crankshaft Pulley
Secure the crankshaft pulley to the crankshaft
vibration
damper with six screws. Torque screws 18 to 25 lb-ft. [2,5 a 3,4 kg-m.].
Dl-90.
Install
Oil
Level
Dipstick
Insert
oil level dipstick
into
the dipstick tube.
Dl-91.
Install
Oil
Pressure Sending Unit
Install
oil pressure sending unit in cylinder block.
Connect electrical wiring harness to unit.
Dl-92.
Install Starting Motor
Secure starting motor and
solenoid
assembly to
the flywheel housing and cylinder block with two attaching screws. Torque screw, which attaches this
assembly to the flywheel housing, 30 to 40 lb-ft. [4,1 a 5,5 kg-m.]. Torque screw, which attaches
bracket
to cylinder block, 10 to 12 lb-ft. [1,4 a 1,7 kg-m.].
Dl-93.
Install
Oil
Filter
Install
a new oil filter
element
at oil filter nipple,
at
left
side
of timing chain cover. Torque 10 to 15 lb-ft. [1,38 a 2,07 kg-m.].
D1-94. Install Water Pump
Be
certain that mating surfaces of the water pump
and
timing chain cover are clean.
Install
a new
gasket
on the pump flange. Secure the pump and
alternator adjustment bracket to the cover with
nine attaching bolts. Torque
bolts
6 to 8 lb-ft. [0,83 a 1,10 kg-m.]. Refer to Fig. Dl-41.
D1-9S.
Install
Cooling Fan
Secure the cooling fan, fan hub, and fan drive
pulley to the water pump shaft
flange
with four
attaching screws. Torque screws 17 to 23 lb-ft. [2,35 a 3,18 kg-m.].
Dl-96.
Install
Alternator
and Fan
Belt
Mount the alternator and bracket assembly on
right
cylinder head with two attaching screws.
Torque
screws 30 to 40 lb-ft. [4,1 a 5,5 kg-m.].
Fasten
the alternator
loosely
to its adjustment
bracket
with attaching flat washer and nut.
Install
the fan
belt
on its pulleys. Pivot the alternator
outward,
away from cylinder block, to apply fan
belt
tension. Adjust fan
belt
tension to 80 lb. [36,2 kg.];
tighten
alternator-to-adjustment bracket
nut to secure adjustment
setting.
Connect wiring
harness to alternator.
Dl-97.
Install
Fuel Pump
Install
two mounting
bolts
and new
gasket
on
flange
of fuel pump. Secure pump to timing chain cover with screws; torque screws 17 to 23 lb-ft. [2,35 a 3,8 kg-m.]. Connect
output
fuel line to
pump.
Dl-98.
Install Exhaust Manifold
Secure each of two exhaust manifolds to corre
sponding cylinder head with five attaching screws,
and
one nut. Torque screws and nut 15 to 20 lb-ft. [2,07 a 2,8 kg-m.]. See Fig. Dl-42.
Dl-99.
Install Distributor
Insert
distributor drive gear
into
distributor mount-
FIG.
Dl-42—EXHAUST
MANIFOLD INSTALLATION
1—Torque
Bolts—15
to 20
lb-ft.
[2,07 a 2,8
kg-m.]
102
Page 103 of 376
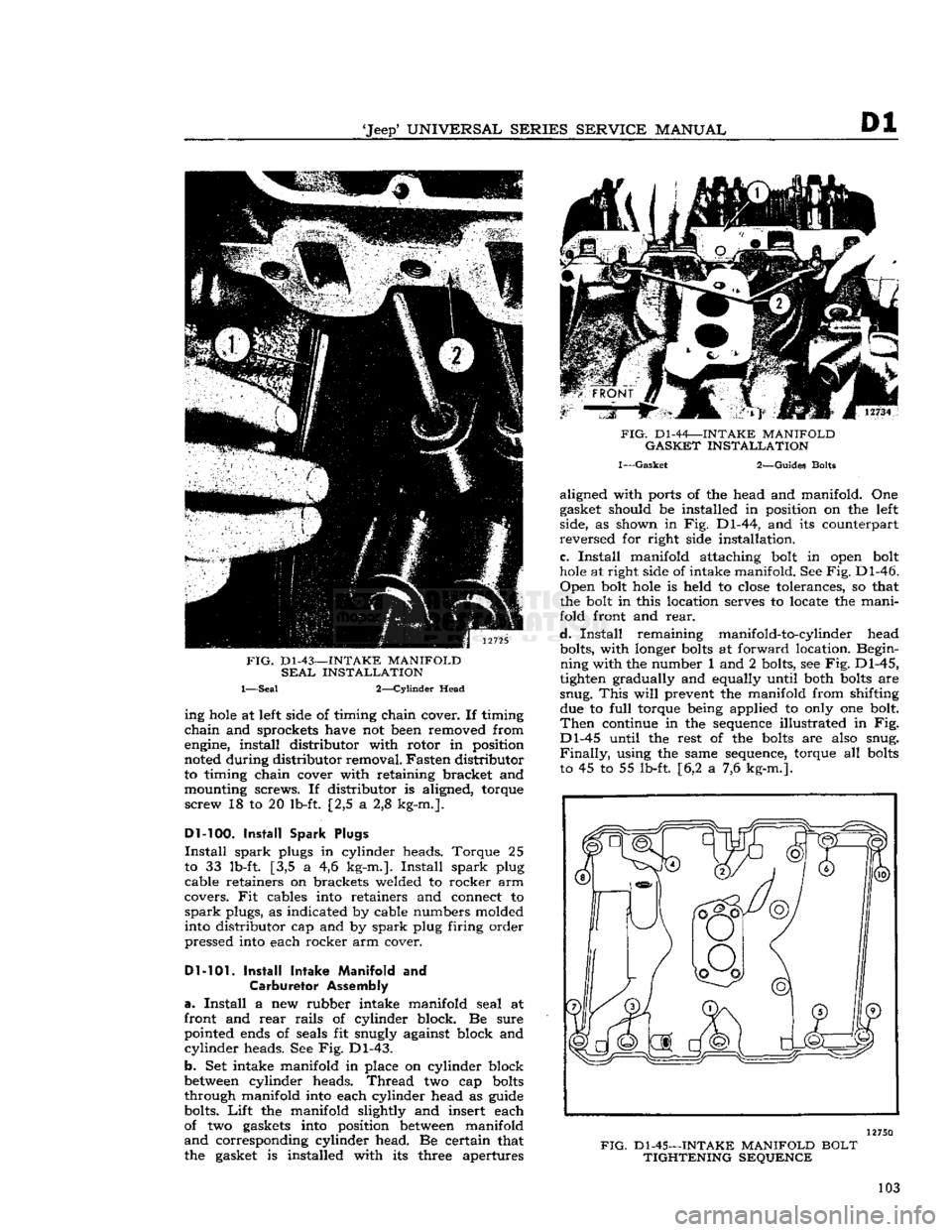
'Jeep1
UNIVERSAL
SERIES
SERVICE
MANUAL
Dl
FIG.
D1-43—INTAKE
MANIFOLD
SEAL
INSTALLATION
1—Seal 2—Cylinder Head ing
hole
at left side of timing chain cover. If timing
chain
and sprockets have not been removed from
engine, install distributor with rotor in position
noted during distributor removal. Fasten distributor
to timing chain cover with retaining bracket and
mounting screws. If distributor is aligned, torque
screw
18 to 20 lb-ft. [2,5 a 2,8 kg-m.].
Dl-100.
Install Spark Plugs
Install
spark
plugs in cylinder heads. Torque 25
to 33 lb-ft. [3,5 a 4,6 kg-m.].
Install
spark
plug cable retainers on brackets welded to rocker arm
covers. Fit cables into retainers and connect to
spark
plugs, as indicated by cable numbers molded
into distributor cap and by
spark
plug firing order
pressed into each rocker arm cover.
Dl-101.
Install Intake Manifold
and
Carburetor
Assembly
a.
Install
a new rubber intake manifold seal at
front and
rear
rails
of cylinder block. Be sure
pointed ends of seals fit snugly against block and
cylinder
heads. See Fig. Dl-43.
b.
Set intake manifold in place on cylinder block
between
cylinder heads.
Thread
two cap
bolts
through manifold into each cylinder head as guide
bolts.
Lift
the manifold slightly and insert each
of two gaskets into position
between
manifold
and
corresponding cylinder head. Be certain that
the gasket is installed with its three apertures
FIG.
Dl-44—INTAKE
MANIFOLD
GASKET
INSTALLATION
1—Gasket
2—Guides Bolts aligned with ports of the head and manifold. One
gasket should be installed in position on the left
side, as shown in Fig. Dl-44, and its counterpart
reversed
for right side installation.
c.
Install
manifold attaching bolt in open bolt
hole
at right side of intake manifold. See
Fig.
Dl-46.
Open
bolt
hole
is held to
close
tolerances, so that
the bolt in this location serves to locate the mani
fold front and
rear.
d.
Install
remaining manifold-to-cylinder head bolts, with longer
bolts
at forward location. Begin
ning
with the number 1 and 2 bolts, see
Fig.
Dl-45,
tighten gradually and equally until both
bolts
are
snug.
This
will
prevent the manifold from shifting due to
full
torque being applied to only one bolt.
Then
continue in the sequence illustrated in Fig.
Dl-45
until the rest of the
bolts
are also snug.
Finally,
using the same sequence, torque all
bolts
to 45 to 55 lb-ft. [6,2 a 7,6 kg-m.].
12750
FIG.
Dl-45—INTAKE
MANIFOLD
BOLT
TIGHTENING
SEQUENCE
103
Page 104 of 376
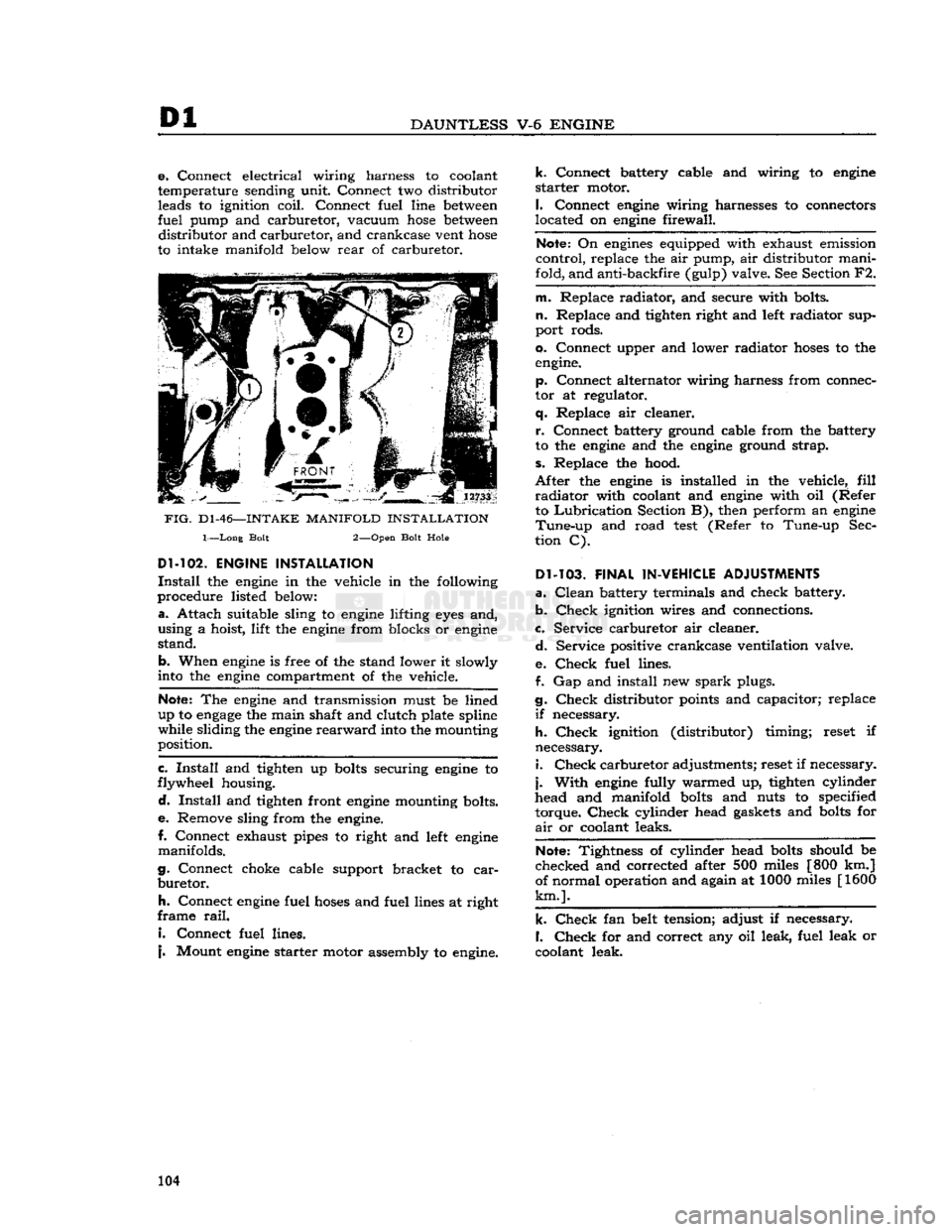
Dl
DAUNTLESS
V-6
ENGINE
e.
Connect electrical wiring harness to coolant
temperature sending unit. Connect two distributor leads to ignition coil. Connect fuel line
between
fuel pump and carburetor, vacuum
hose
between
distributor and carburetor, and crankcase vent
hose
to intake manifold
below
rear
of carburetor.
FIG.
D1-46—-INTAKE
MANIFOLD
INSTALLATION
1—Long Bolt 2—Open Bolt Hole
Dl-102.
ENGINE INSTALLATION
Install
the
engine
in the vehicle in the following
procedure listed
below:
a.
Attach suitable sling to
engine
lifting
eyes
and,
using a hoist, lift the
engine
from blocks or
engine
stand.
b. When
engine
is free of the stand lower it slowly
into
the
engine
compartment of the vehicle.
Note:
The
engine
and transmission must be lined
up to
engage
the main shaft and clutch plate spline
while sliding the
engine
rearward
into
the mounting
position.
c.
Install
and tighten up
bolts
securing
engine
to
flywheel housing.
d.
Install
and tighten front
engine
mounting bolts.
e.
Remove sling from the
engine.
I.
Connect exhaust pipes to right and
left
engine
manifolds.
g. Connect choke cable support bracket to
car
buretor.
h.
Connect
engine
fuel
hoses
and fuel lines at right
frame
rail.
I.
Connect fuel lines.
j.
Mount
engine
starter motor assembly to
engine.
k.
Connect battery cable and wiring to
engine
starter
motor.
I.
Connect
engine
wiring harnesses to connectors
located on
engine
firewall.
Note:
On
engines
equipped with exhaust emission
control, replace the air pump, air distributor mani
fold, and anti-backfire (gulp) valve. See Section F2.
m. Replace radiator, and secure with bolts,
n.
Replace and tighten right and
left
radiator sup
port rods.
0. Connect upper and lower radiator
hoses
to the
engine.
p. Connect alternator wiring harness from connec
tor at regulator,
q.
Replace air cleaner.
r.
Connect battery ground cable from the battery
to the
engine
and the
engine
ground strap,
s.
Replace the hood.
After
the
engine
is installed in the vehicle,
fill
radiator
with coolant and
engine
with oil (Refer to
Lubrication
Section B), then perform an
engine
Tune-up
and road
test
(Refer to Tune-up Sec
tion C).
Dl-103.
FINAL IN-VEHICLE ADJUSTMENTS
a.
Clean
battery terminals and check battery.
b.
Check
ignition wires and connections.
c. Service carburetor air cleaner.
d.
Service positive crankcase ventilation valve.
e.
Check
fuel lines.
f. Gap and install new
spark
plugs.
g.
Check
distributor
points
and capacitor; replace
if
necessary.
h.
Check
ignition (distributor) timing; reset if
necessary. 1.
Check
carburetor adjustments; reset if necessary,
j.
With
engine
fully warmed up, tighten cylinder
head and manifold
bolts
and nuts to specified
torque.
Check
cylinder head
gaskets
and
bolts
for
air
or coolant leaks.
Note:
Tightness of cylinder head
bolts
should be
checked and corrected after 500 miles [800 km.]
of normal operation and again at 1000 miles [1600
km.].
k.
Check
fan belt tension; adjust if necessary.
I.
Check
for and correct any oil leak, fuel leak or
coolant leak. 104
Page 105 of 376
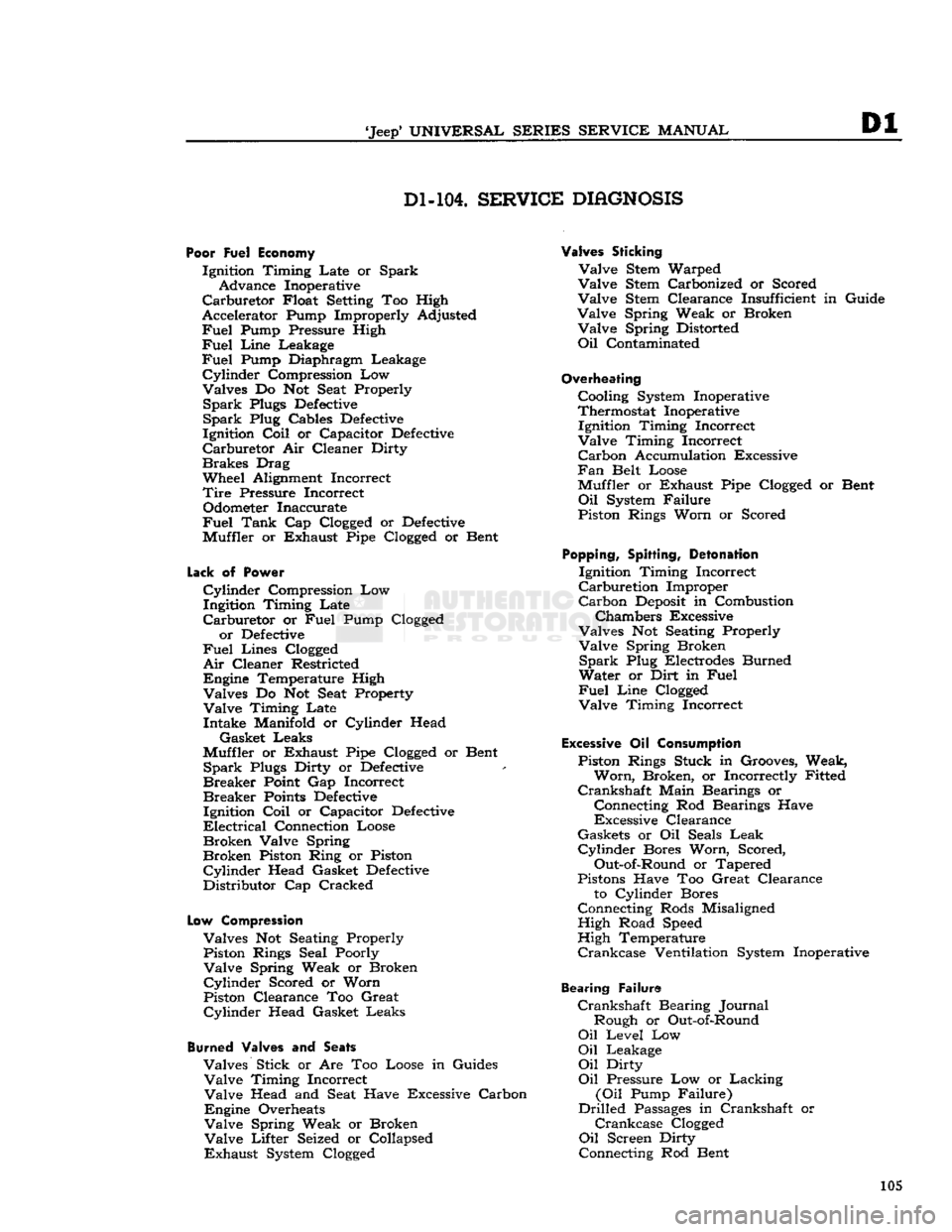
'Jeep'
UNIVERSAL
SERIES SERVICE
MANUAL
Dl
Dl-104.
SERVICE
DIAGNOSIS
Poor Fuel Economy
Ignition Timing Late or Spark Advance Inoperative
Carburetor
Float Setting Too High
Accelerator Pump Improperly Adjusted
Fuel
Pump Pressure High
Fuel
Line
Leakage
Fuel
Pump Diaphragm Leakage
Cylinder
Compression Low
Valves Do Not Seat Properly
Spark
Plugs
Defective
Spark
Plug Cables
Defective
Ignition
Coil
or Capacitor
Defective
Carburetor
Air Cleaner Dirty
Brakes
Drag
Wheel Alignment Incorrect
Tire
Pressure Incorrect Odometer Inaccurate
Fuel
Tank
Cap Clogged or
Defective
Muffler or Exhaust Pipe Clogged or Bent
Lack
of
Power
Cylinder
Compression Low
Ingitdon Timing Late
Carburetor
or
Fuel
Pump Clogged or
Defective
Fuel
Lines Clogged
Air
Cleaner Restricted
Engine Temperature High Valves Do Not Seat Property
Valve
Timing Late Intake Manifold or Cylinder Head
Gasket Leaks
Muffler or Exhaust Pipe Clogged or Bent
Spark
Plugs Dirty or
Defective
Breaker
Point Gap Incorrect
Breaker
Points
Defective
Ignition
Coil
or Capacitor
Defective
Electrical
Connection Loose
Broken
Valve Spring
Broken
Piston Ring or Piston
Cylinder
Head Gasket
Defective
Distributor Cap Cracked
Low
Compression
Valves Not Seating Properly Piston Rings Seal Poorly
Valve
Spring Weak or Broken
Cylinder
Scored or Worn
Piston Clearance Too Great
Cylinder
Head Gasket Leaks
Burned
Valves and
Seats
Valves Stick or Are Too Loose in Guides
Valve
Timing Incorrect
Valve
Head and Seat Have Excessive Carbon
Engine Overheats
Valve
Spring Weak or Broken
Valve
Lifter Seized or Collapsed
Exhaust
System Clogged
Valves Sticking
Valve
Stem Warped
Valve
Stem Carbonized or Scored
Valve
Stem Clearance Insufficient in Guide
Valve
Spring Weak or Broken
Valve
Spring Distorted
Oil
Contaminated
Overheating
Cooling System Inoperative
Thermostat Inoperative Ignition Timing Incorrect
Valve
Timing Incorrect
Carbon
Accumulation Excessive
Fan
Belt Loose
Muffler or Exhaust Pipe Clogged or Bent
Oil
System Failure
Piston Rings Worn or Scored
Popping,
Spitting,
Detonation
Ignition Timing Incorrect
Carburetion
Improper
Carbon
Deposit
in Combustion
Chambers Excessive
Valves Not Seating Properly
Valve
Spring Broken
Spark
Plug Electrodes Burned
Water or Dirt in
Fuel
Fuel
Line
Clogged
Valve
Timing Incorrect
Excessive
Oil
Consumption
Piston Rings Stuck in Grooves, Weak,
Worn,
Broken, or Incorrectly Fitted
Crankshaft
Main Bearings or
Connecting Rod Bearings Have
Excessive Clearance
Gaskets or Oil Seals
Leak
Cylinder
Bores Worn, Scored,
Out-of-Round or Tapered
Pistons Have Too Great Clearance to Cylinder Bores
Connecting Rods Misaligned High Road Speed
High Temperature
Crankcase
Ventilation System Inoperative
Bearing Failure
Crankshaft
Bearing Journal Rough or Out-of-Round
Oil
Level Low
Oil
Leakage
Oil
Dirty
Oil
Pressure Low or Lacking
(Oil
Pump Failure)
Drilled
Passages
in Crankshaft or
Crankcase
Clogged
Oil
Screen Dirty
Connecting Rod Bent 105
Page 106 of 376
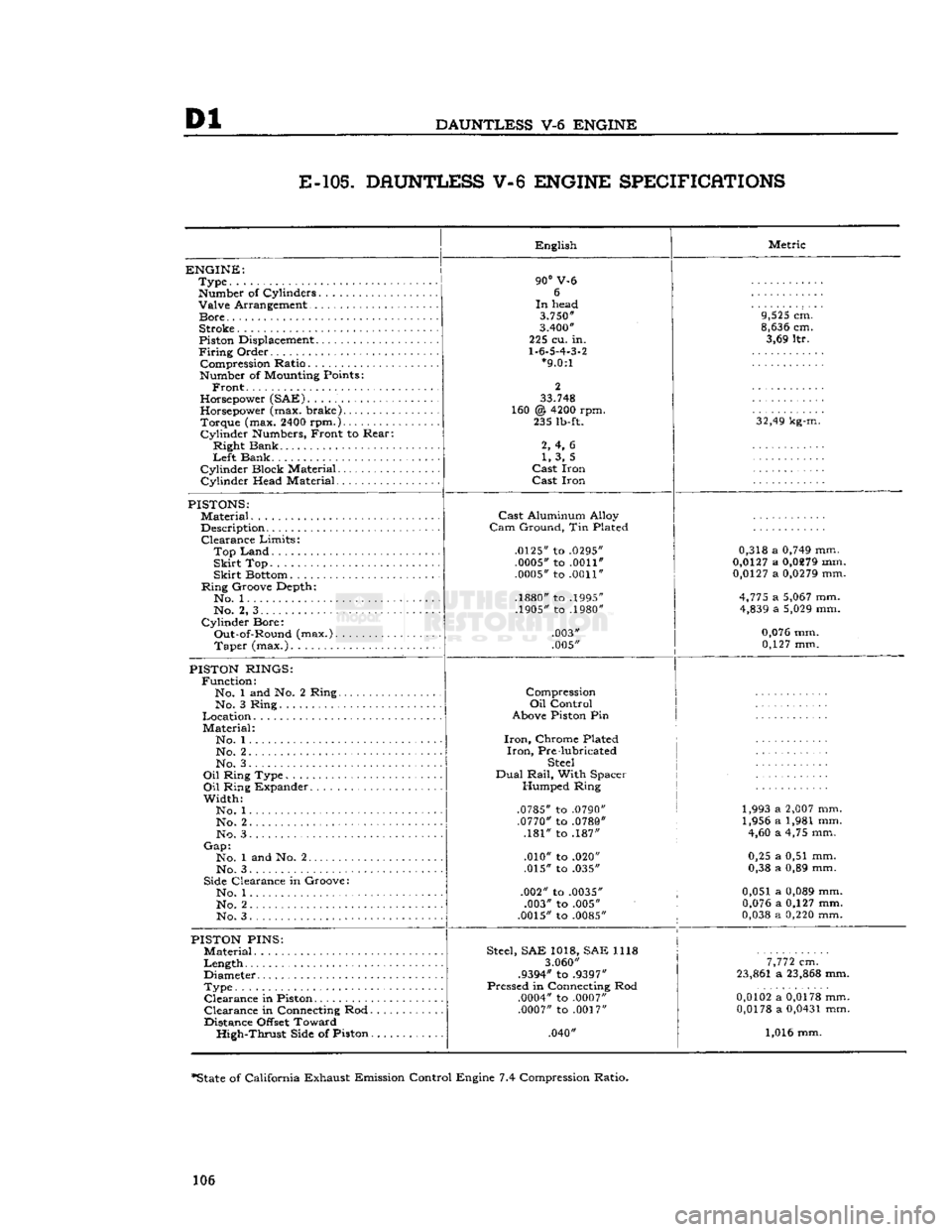
Dl
DAUNTLESS
V-6
ENGINE
E-105.
DAUNTLESS V-6 ENGINE SPECIFICATIONS
ENGINE:
Type
Number
of Cylinders Valve Arrangement
Bore
Stroke
Piston
Displacement
Firing
Order Compression Ratio
Number
of
Mounting
Points:
Front.
Horsepower
(SAE)
Horsepower
(max. brake) Torque (max.
2400
rpm.)
Cylinder
Numbers,
Front to Rear:
Right Bank
Left
Bank
Cylinder Block Material
Cylinder Head Material English
90°
V-6 6
In
head
3.750"
3.400"
225 cu. in.
1.6.5.4.3.2
*9.0:1
2
33.748
160 @
4200
rpm. 235
lb-ft.
2, 4, 6 1, 3, 5
Cast
Iron
Cast
Iron Metric
9,525
cm.
8,636
cm. 3,69 ltr.
32,49
kg-m.
PISTONS:
Material
Description Clearance Limits:
Top
Land
Skirt
Top
Skirt
Bottom
Ring Groove Depth*. No. 1
No. 2, 3
Cylinder Bore: Out-of-Round (max.). Taper (max.)
Cast
Aluminum Alloy
Cam
Ground, Tin Plated
.0125"
to
.0295" .0005"
to
.0011"
.0005"
to
.0011"
.1880"
to
.1995"
.1905"
to
.1980"
.003"
.005" 0,318 a
0,749
mm.
0,0127
a
0,0279
mm.
0,0127
a
0,0279
mm.
4,775
a
5,067
mm.
4,839
a
5,029
mm.
0,076
mm. 0,127 mm.
PISTON
RINGS:
Function: No. 1 and No. 2 Ring.. No. 3 Ring
Location
Material: No. 1...
No. 2 No. 3.
Oil
Ring Type
Oil
Ring Expander
Width: No. 1
No. 2. .
No. 3
Gap:
No. 1 and No. 2
No. 3
Side
Clearance in Groove: No. 1
No. 2
No. 3 Compression
Oil
Control
Above
Piston
Pin
Iron,
Chrome Plated
Iron,
Pre lubricated
Steel
Dual
Rail,
With Spacer Humped Ring
.0785"
to
.0790" .0770"
to
.0780"
.181" to .187"
.010" to .020"
.015" to .035"
.002" to
.0035"
.003" to .005"
.0015"
to
.0085"
1,993 a
2,007
mm.
1,956 a 1,981 mm. 4,60 a 4,75 mm.
0,25 a 0,51 mm.
0,38 a 0,89 mm.
0,051 a
0,089
mm.
0,076
a 0,127 mm.
0,038
a
0,220
mm.
PISTON
PINS:
Material
Length
Diameter
Type Clearance in
Piston
Clearance in
Connecting
Rod.
Distance
Offset
Toward High-Thrust
Side
of Piston.
Steel,
SAE 1018, SAE 1118
3.060"
.9394"
to
.9397"
Pressed in
Connecting
Rod
.0004"
to
.0007" .0007"
to
.0017"
.040"
7,772
cm.
23,861
a
23,868
mm.
0,0102
a
0,0178
mm.
0,0178
a
0,0431
mm.
1,016 mm.
*State
of California Exhaust Emission Control Engine 7.4 Compression Ratio.
106
Page 107 of 376
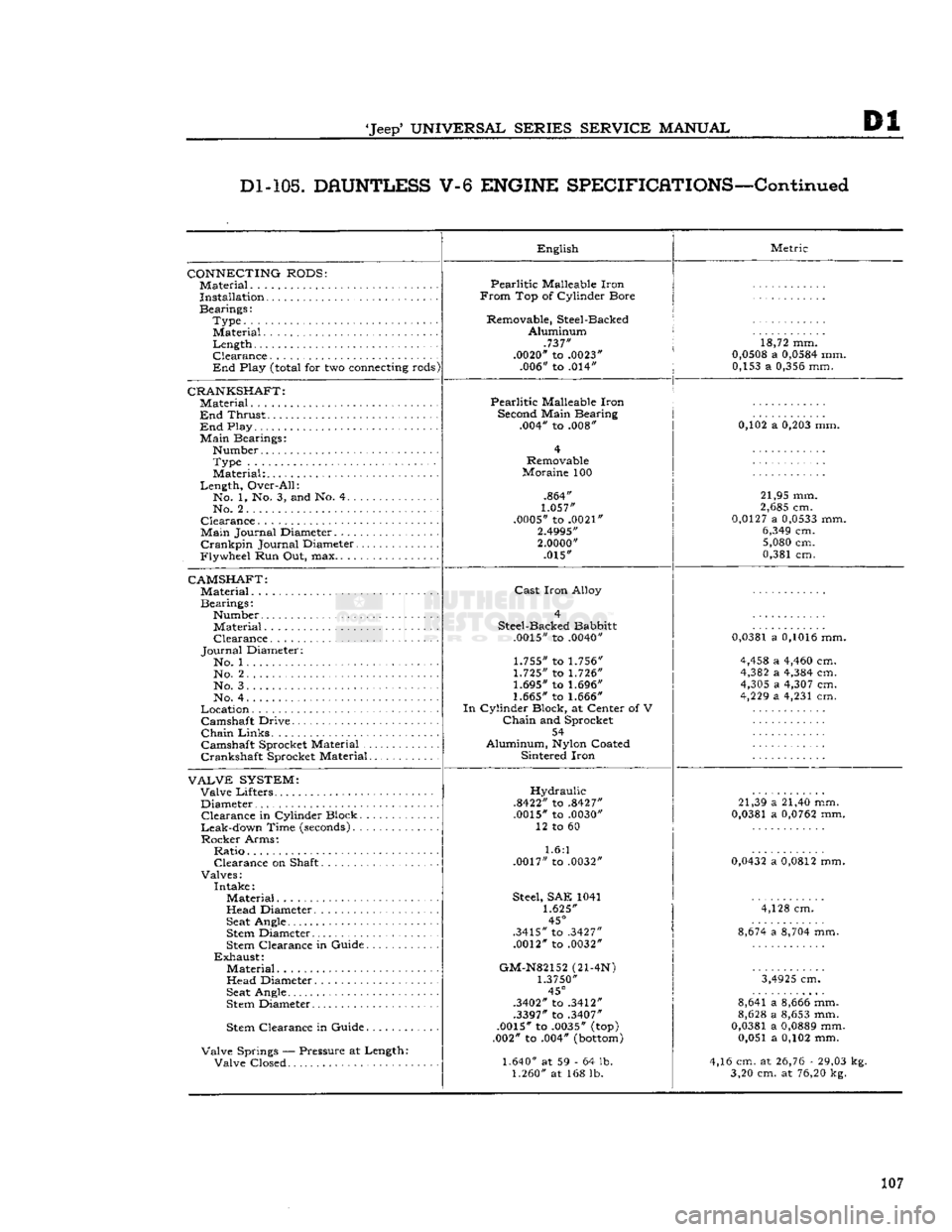
'Jeep*
UNIVERSAL
SERIES
SERVICE
MANUAL
Dl
Dl-105.
DAUNTLESS
V-6
ENGINE
SPECIFICATIONS—Continued
CONNECTING
RODS:
Material
Installation
Bearings: Type........
Material.
Length Clearance
End
Play
(total
for two
connecting
rods)
CRANKSHAFT:
Material ,
End
Thrust
End
Play
Main
Bearings: Number Type
Material:
Length, Over-All: No. 1, No. 3, and No. 4
No. 2
Clearance
Main
Journal Diameter.
Crankpin
Journal Diameter
Flywheel Run Out, max
CAMSHAFT:
Material
Bearings: Number Material Clearance
Journal
Diameter: No. 1 No. 2
No. 3.
No. 4
Location Camshaft Drive
Chain
Links
Camshaft Sprocket Material
Crankshaft Sprocket Material
VALVE
SYSTEM:
Valve Lifters Diameter Clearance in Cylinder Block
Leak-down Time
(seconds)
Rocker Arms: Ratio Clearance on Shaft
Valves: Intake: Material
Head Diameter
Seat
Angle
Stem
Diameter
Stem
Clearance in Guide
Exhaust:
Material Head Diameter
Seat
Angle
Stem
Diameter
Stem
Clearance in Guide
Valve Springs — Pressure at Length: Valve Closed English
Pearlitic Malleable Iron
From
Top of Cylinder Bore
Removable, Steel-Backed Aluminum .737"
.0020"
to
.0023"
.006" to .014" Metric
18,72 mm.
0,0508
a
0,0584
mm. 0,153 a
0,356
mm.
Pearlitic Malleable Iron
Second
Main Bearing .004" to .008"
Removable
Moraine 100
.864"
1.057"
.0005"
to
.0021"
2.4995"
2.0000"
.015" 0,102 a
0,203
mm.
21,95 mm.
2,685
cm.
0,0127
a
0,0533
mm.
6,349
cm.
5,080
cm.
0,381 cm.
Cast
Iron Alloy
Steel-Backed Babbitt
.0015"
to
.0040"
1.755"
to
1.756"
1.725"
to
1.726"
1.695"
to
1.696"
1.665"
to
1.666"
In
Cylinder Block, at Center of V
Chain
and Sprocket 54
Aluminum,
Nylon
Coated Sintered Iron
0,0381
a
0,1016
mm.
4,458
a
4,460
cm.
4,382
a
4,384
cm.
4,305
a
4,307
cm.
4,229
a 4,231 cm.
Hydraulic
.8422"
to
.8427"
.0015"
to
.0030"
12 to 60
1.6:1
.0017"
to
.0032"
Steel,
SAE 1041
1.625"
45°
.3415"
to
.3427"
.0012"
to
.0032"
GM-N82152
(21-4N)
1.3750"
45°
.3402"
to
.3412"
.3397"
to
.3407"
.0015"
to
.0035"
(top)
.002" to .004"
(bottom)
1.640"
at 59 - 64 lb.
1.260"
at 168 lb. 21,39 a 21,40 mm.
0,0381
a
0,0762
mm.
0,0432
a
0,0812
mm. 4,128 cm.
8,674
a
8,704
mm.
3,4925
cm.
8,641 a
8,666
mm.
8,628
a
8,653
mm.
0,0381
a
0,0889
mm. 0,051 a 0,102 mm.
4,16 cm. at
26,76
-
29,03
kg. 3,20 cm. at
76,20
kg.
107
Page 108 of 376
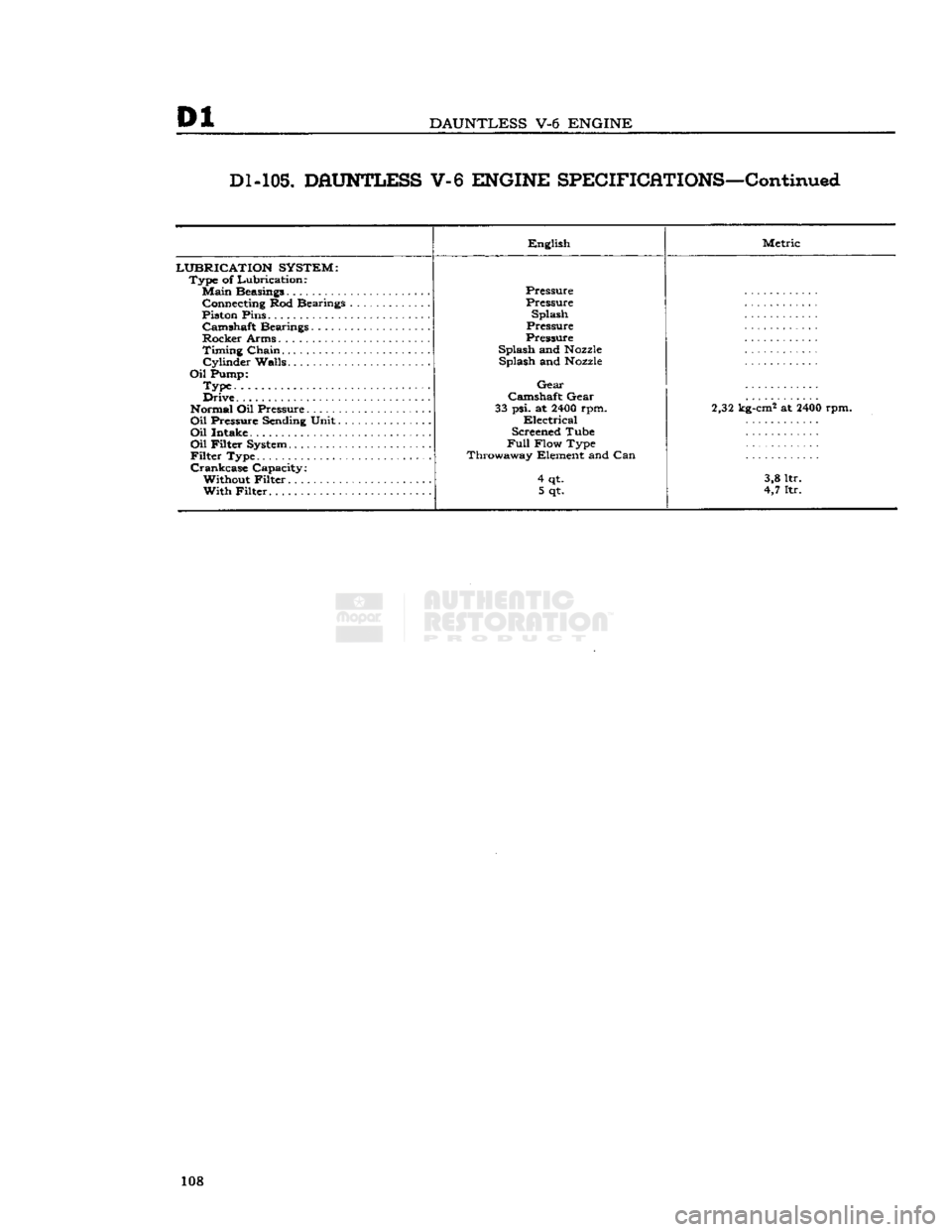
Dl
DAUNTLESS
V-6
ENGINE
D1-10S. DAUNTLESS V-6 ENGINE SPECIFICATIONS—Continued
LUBRICATION SYSTEM:
Type of Lubrication:
Main
Beasings
Connecting
Rod Bearings
Piston
Pins. Camshaft Bearings
Rocker Arms
Timing
Chain
Cylinder
Walls
Oil
Pump: Type
Drive
Normal Oil Pressure
Oil
Pressure
Sending
Unit. .
Oil
Intake
Oil
Filter
System
Filter
Type
Crankcase
Capacity:
Without
Filter
With
Filter.
English
Pressure
Pressure Splash
Pressure
Pressure
Splash and
Nozzle
Splash and
Nozzle
Gear
Camshaft Gear
33
psi. at
2400
rpm.
Electrical
Screened
Tube
Full
Flow Type
Throwaway Element and Can
4 qt.
5
qt. Metric
2,32 kg-cm2 at
2400
rpm.
3,8
ltr.
4,7 ltr. 108
Page 109 of 376
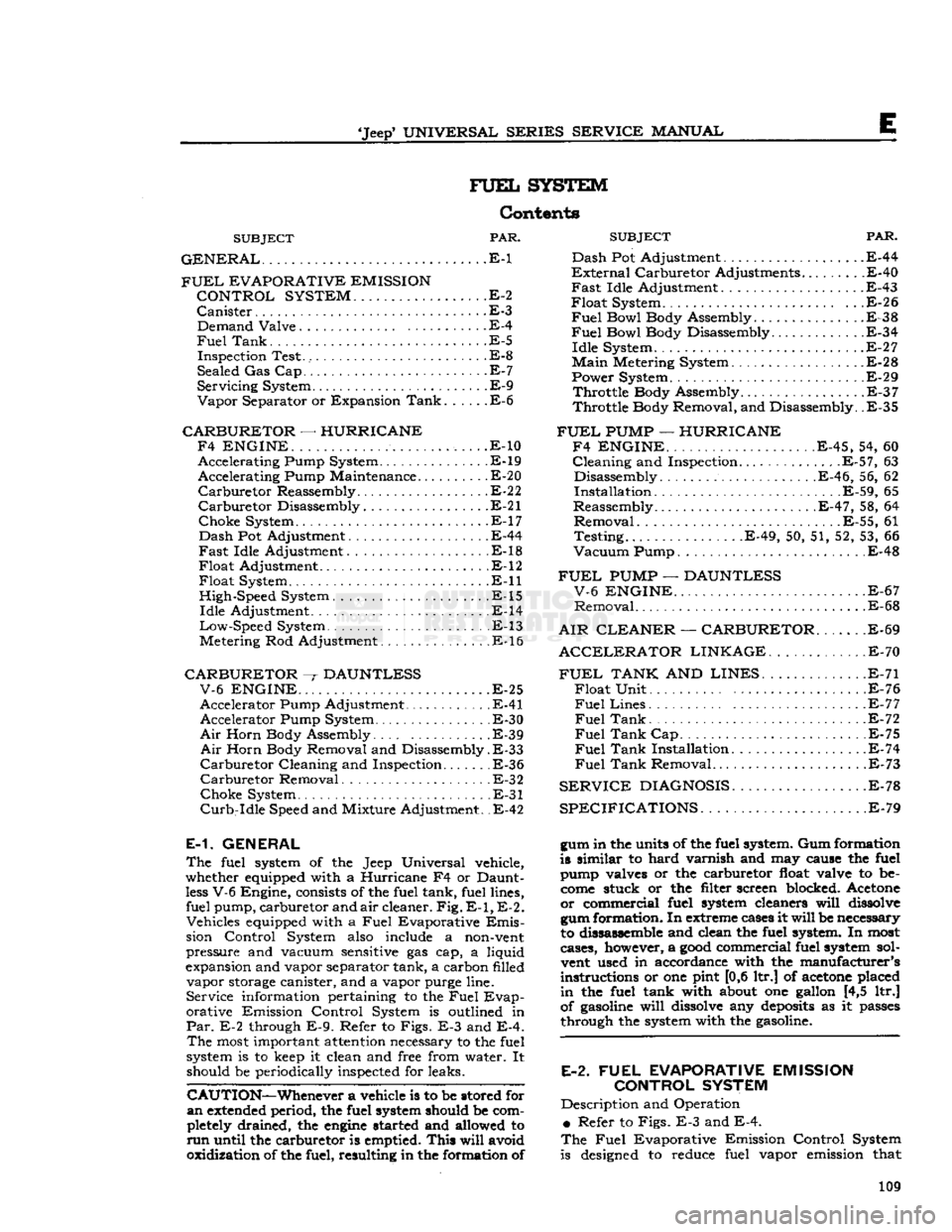
'Jeep*
UNIVERSAL SERIES SERVICE
MANUAL
E
FUEL
SYSTEM
Contents
SUBJECT
PAR.
GENERAL
E-1 Dash
FUEL
EVAPORATIVE EMISSION
?*^r
CONTROL SYSTEM
..E-2
Canister
.E-3 . Demand Valve E-4
Fuel
Tank.
.E-5
Inspection Test. E-8
Sealed Gas Cap. E-7
Servicing
System E-9
Vapor
Separator or Expansion
Tank
E-6
CARBURETOR
—
HURRICANE F4 ENGINE.
. .
......
..... ,. . .E-10 Accelerating Pump System.............. .E-19 Accelerating Pump Maintenance E-20
Carburetor
Reassembly
E-2
2
Carburetor
Disassembly E-21
Choke
System E-17
Dash
Pot Adjustment E-44
Fast
Idle Adjustment E-18
Float
Adjustment E-12
Float
System. E-ll
High-Speed System . .E-15
Idle
Adjustment .E-14
Low-Speed
System . E-13
Metering Rod Adjustment E-16
CARBURETOR
~r
DAUNTLESS V-6 ENGINE
.E-25
Accelerator Pump Adjustment E-41 Accelerator Pump System. . E-30
Air
Horn Body Assembly E-39
Air
Horn Body Removal and Disassembly.
E-33
Carburetor
Cleaning and Inspection E-36
Carburetor
Removal E-32
Choke
System E-31
Curb-Idle
Speed and Mixture Adjustment. .E-42
E-1. GENERAL
The
fuel system of the Jeep Universal vehicle,
whether equipped with a Hurricane F4 or Daunt
less
V-6 Engine,
consists
of the fuel tank, fuel lines, fuel pump, carburetor and
air
cleaner.
Fig. E-1, E-2.
Vehicles equipped with a
Fuel
Evaporative
Emis
sion Control System
also
include a
non-vent
pressure and vacuum
sensitive
gas cap, a liquid
expansion and vapor separator tank, a carbon filled vapor
storage
canister, and a vapor purge line. Service information pertaining to the
Fuel
Evap
orative Emission Control System is outlined in
Par.
E-2 through
E-9.
Refer to Figs. E-3 and E-4.
The
most
important
attention
necessary to the fuel
system is to
keep
it clean and free from water. It should be periodically inspected for leaks.
CAUTION—Whenever
a vehicle is to be stored for
an
extended
period, the fuel system should be com
pletely
drained, the
engine
started and allowed to
run
until the carburetor is emptied.
This
will
avoid
oxidization of the fuel, resulting in the formation of
SUBJECT
PAR.
Pot Adjustment .E-44
nal
Carburetor Adjustments.........E-40
Idle
Adjustment
.
E-43 System . . .E-26
Bowl
Body Assembly E-38
Fuel
Bowl Body Disassembly E-34
Idle
System E-27
Main
Metering System E-28
Power System . E-29
Throttle
Body Assembly .E-37
Throttle
Body Removal, and Disassembly. .E-35
FUEL
PUMP
—
HURRICANE F4 ENGINE.
E-45, 54, 60
Cleaning
and Inspection.............
.E-57,
63 Disassembly E-46, 56, 62
Installation E-59, 65
Reassembly
.E-47,
58, 64
Removal
E-55, 61
Testing.
E-49, 50, 51, 52, 53, 66
Vacuum
Pump E-48
FUEL
PUMP
—
DAUNTLESS V-6 ENGINE
E-67
Removal
E-68
AIR CLEANER
—
CARBURETOR
E-69
ACCELERATOR
LINKAGE
.E-70
FUEL
TANK
AND
LINES
E-71
Float
Unit . .E-76
Fuel
Lines E-77
Fuel
Tank
. . .E-72
Fuel
Tank
Cap E-75
Fuel
Tank
Installation. E-74
Fuel
Tank
Removal E-73
SERVICE
DIAGNOSIS
E-78
SPECIFICATIONS.
E-79
gum in the units of the fuel system. Gum formation
is similar to hard varnish and may cause the fuel
pump valves or the carburetor
float
valve to be
come
stuck or the filter screen blocked. Acetone or commercial fuel system cleaners
will
dissolve
gum formation. In
extreme
cases
it
will
be necessary
to dissassemble and clean the fuel system. In
most
cases, however, a
good
commercial fuel system sol
vent
used in accordance with the manufacturer's
instructions or one pint [0,6 ltr.] of
acetone
placed
in
the fuel tank with
about
one gallon [4,5 ltr.]
of
gasoline
will
dissolve
any
deposits
as it
passes
through the system with the
gasoline.
E-2.
FUEL
EVAPORATIVE EMISSION CONTROL SYSTEM
Description and Operation
•
Refer to Figs. E-3 and E-4.
The
Fuel
Evaporative Emission Control System
is
designed
to reduce fuel vapor emission that 109
Page 110 of 376
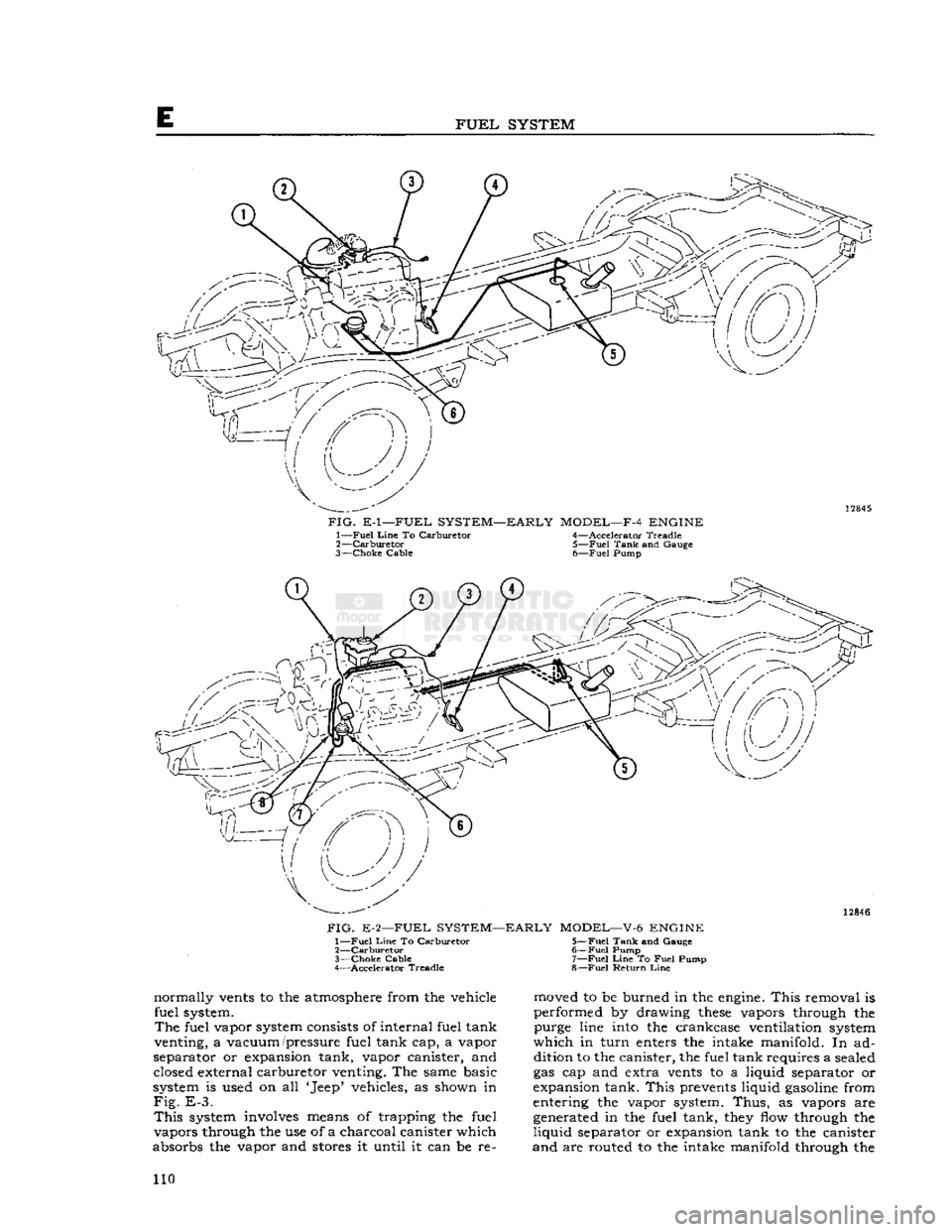
E
FUEL
SYSTEM
FIG.
E-1—FUEL SYSTEM—EARLY MODEL—F-4 ENGINE 1—
Fuel
Line
To Carburetor 4—Accelerator Treadle
2— Carburetor 5—Fuel Tank and Gauge
3— Choke Cable 6—Fuel Pump
FIG.
E-2—FUEL SYSTEM—EARLY
MODEL—V-6
ENGINE 1—
Fuel
Line
To Carburetor 5—Fuel Tank and Gauge
2—
Carburetor 6—Fuel Pump
3— Choke Cable 7—Fuel
Line
To Fuel Pump
4—
Accelerator
Treadle 8—Fuel Return
Line
normally
vents
to the atmosphere from the vehicle
fuel system.
The
fuel vapor system consists of internal fuel tank
venting, a vacuum /pressure fuel tank cap, a vapor
separator or expansion tank, vapor canister, and closed external carburetor venting. The same basic
system is used on all 'Jeep' vehicles, as shown in
Fig. E-3.
This
system involves means of trapping the fuel
vapors through the use of a charcoal canister which
absorbs the vapor and stores it until it can be re moved to be burned in the
engine.
This
removal is
performed by drawing
these
vapors through the purge line
into
the crankcase ventilation system
which
in
turn
enters the intake manifold. In ad dition to the canister, the fuel tank requires a sealed
gas cap and extra
vents
to a liquid separator or
expansion tank.
This
prevents liquid
gasoline
from entering the vapor system.
Thus,
as vapors are generated in the fuel tank,
they
flow through the
liquid
separator or expansion tank to the canister
and
are routed to the intake manifold through the 110