JEEP CJ 1953 Manual Online
Manufacturer: JEEP, Model Year: 1953, Model line: CJ, Model: JEEP CJ 1953Pages: 376, PDF Size: 19.96 MB
Page 81 of 376
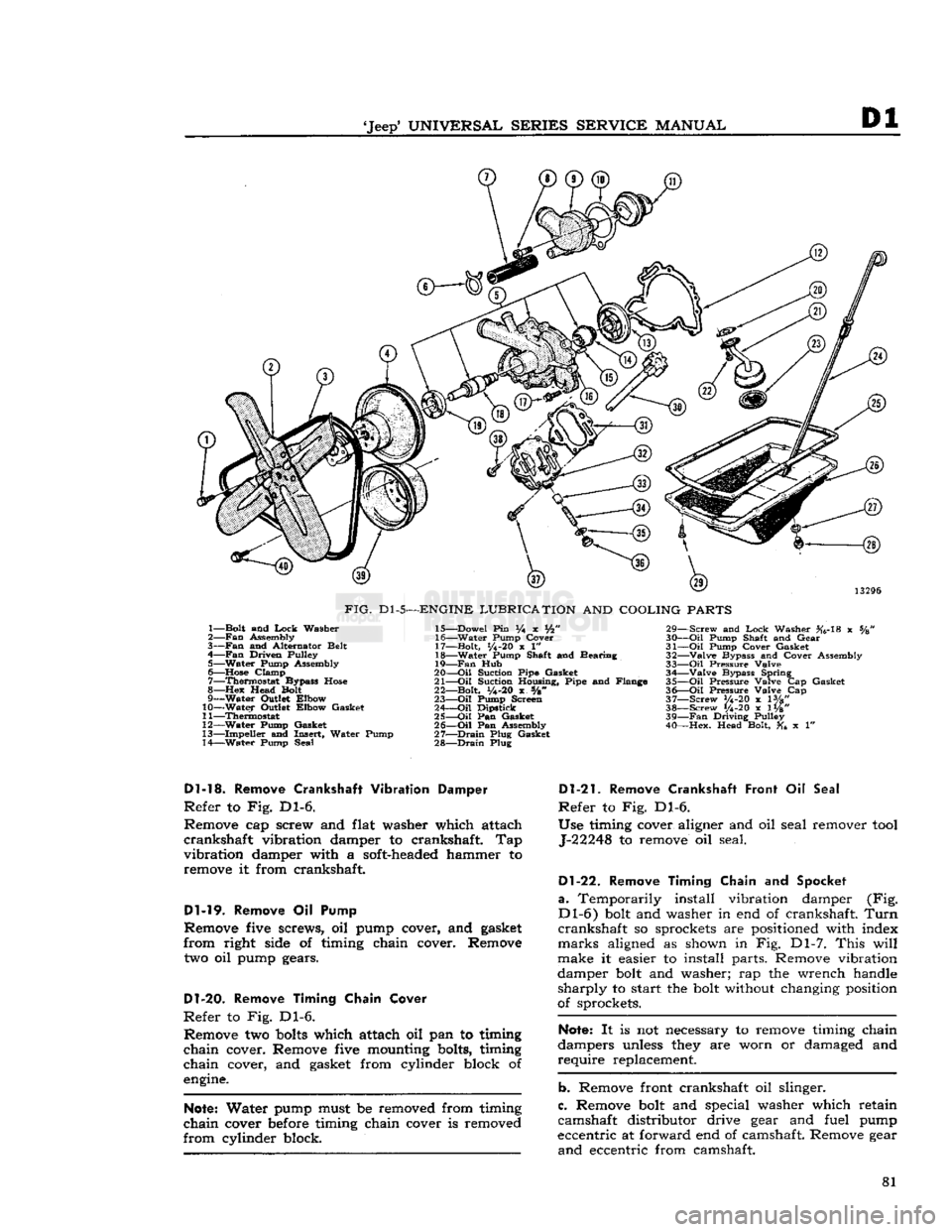
'Jeep'
UNIVERSAL
SERIES
SERVICE
MANUAL
Dl
13296
FIG.
Dl-5—ENGINE
LUBRICATION
AND
COOLING
PARTS
1— Bolt and
Lock
Washer
2—
Fan
Assembly
3—
Fan
and Alternator Belt
4—
Fan
Driven Pulley 5— Water Pump Assembly
6—
Hose
Clamp 7— Thermostat Bypass
Hose
8—Hex
Head Bolt
9— Water Outlet Elbow
10— Water Outlet Elbow Gasket
11— Thermostat
12— Water Pump Gasket
13— Impeller and Insert, Water Pump
14— Water Pump Seal 15— Dowel Pin % x Vfc"
16— Water Pump Cover
17— Bolt,
1/4-20
x 1"
18— Water Pump Shaft and Bearing
19—
Fan
Hub
20—
-Oil
Suction Pipe Gasket
21—
Oil
Suction Housing, Pipe and Flange
22— Bolt,
y4-20
x s/8"
23—
Oil
Pump Screen
24—
Oil
Dipstick
25—
Oil
Pan Gasket
26—
Oil
Pan Assembly
27—
Drain
Plug Gasket
28—
Drain
Plug 29— Screw and
Lock
Washer #6-18 x %
30—
Oil
Pump Shaft and Gear
31—
Oil
Pump Cover Gasket
32— Valve Bypass and Cover Assembly
33—
Oil
Pressure Valve 34— Valve Bypass Spring
35—
Oil
Pressure Valve Cap Gasket
36—
Oil
Pressure Valve Cap
37— Screw V4-20 x lVg"
38— Screw 1/4-20 x 1W' 39—
Fan
Driving Pulley
40— Hex. Head Bolt, x 1"
Dl-13.
Remove
Crankshaft
Vibration Damper
Refer
to Fig. Dl-6.
Remove cap screw and flat washer which attach
crankshaft
vibration damper to crankshaft. Tap
vibration
damper with a soft-headed hammer to remove it from crankshaft.
Dl-19.
Remove Oil Pump
Remove five screws, oil pump cover, and gasket
from
right side of timing chain cover. Remove
two oil pump gears.
D1-20.
Remove Timing Chain Cover
Refer
to Fig. Dl-6. Remove two
bolts
which attach oil pan to timing
chain
cover. Remove five mounting bolts, timing
chain
cover, and gasket from cylinder block of
engine.
Note:
Water pump must be removed from timing
chain
cover before timing chain cover is removed
from
cylinder block.
Dl-21.
Remove Crankshaft Front
Oil
Seal
Refer
to Fig. Dl-6.
Use timing cover aligner and oil seal remover
tool
J-22248 to remove oil seal.
Dl-22.
Remove Timing Chain
and
Spocket
a.
Temporarily install vibration damper (Fig.
Dl-6)
bolt and washer in end of crankshaft.
Turn
crankshaft
so sprockets are positioned with index
marks
aligned as shown in Fig. Dl-7.
This
will
make it easier to install parts. Remove vibration
damper bolt and washer; rap the wrench handle
sharply
to start the bolt without changing position
of sprockets.
Note:
It is not necessary to remove timing chain
dampers unless they are worn or damaged and
require
replacement.
b. Remove front crankshaft oil slinger.
c. Remove bolt and special washer which retain
camshaft distributor drive gear and fuel pump
eccentric at forward end of camshaft. Remove gear
and
eccentric from camshaft. 81
Page 82 of 376
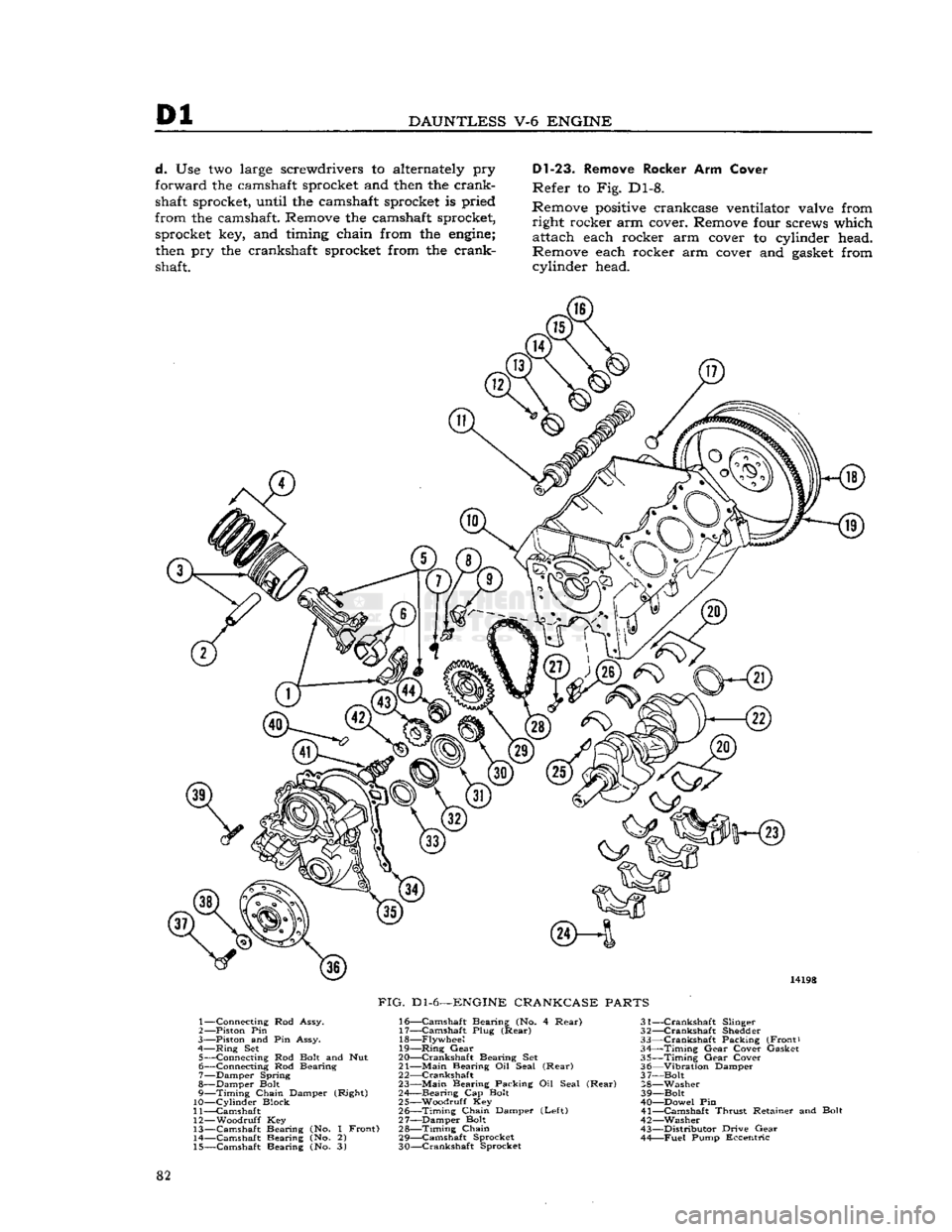
Dl
DAUNTLESS
V-6
ENGINE
d.
Use two large screwdrivers to alternately pry
forward the camshaft sprocket and
then
the crankÂ
shaft sprocket, until the camshaft sprocket is pried
from the camshaft. Remove the camshaft sprocket, sprocket key, and timing chain from the
engine;
then
pry the crankshaft sprocket from the crankÂshaft.
Dl-23.
Remove Rocker Arm Cover
Refer to Fig. Dl-8.
Remove
positive
crankcase ventilator valve from right rocker arm cover. Remove four screws which attach each rocker arm cover to cylinder head.
Remove each rocker arm cover and
gasket
from cylinder head. 14198
FIG.
Dl-6—ENGINE
CRANKCASE
PARTS
1— Connecting Rod Assy.
2— —Piston Pin
3—
Piston and Pin Assy.
4—
Ring
Set 5— Connecting Rod
Bolt
and Nut
6— Connecting Rod Bearing
7— Damper Spring
8— Damper
Bolt
9—
Timing
Chain Damper (Right)
10—
Cylinder
Block
11— Camshaft
12—
Woodruff
Key
13— Camshaft Bearing (No. 1 Front) 14— Camshaft Bearing (No. 2)
15— Camshaft Bearing (No. 3) 16—
Camshaft
Bearing (No. 4
Rear)
31-
17—
Camshaft
Plug
(Rear)
32-18—
Flywheel
33-
19—
Ring
Gear
34-
20— Crankshaft Bearing Set 35-
21—
Main
Bearing Oil Seal
(Rear)
36-
2 2—Crankshaft 3 7-
23—
Main
Bearing Packing Oil Seal
(Rear)
28-
24— Bearing Cap
Bolt
39-
25— Woodruff Key 40-
26—
Timing
Chain Damper
(Left)
41-
27— Damper Bolt 42- 28—
Timing
Chain
43-
29—
Camshaft
Sprocket 44-
30— Crankshaft Sprocket
—Crankshaft
Slinger
—Crankshaft
Shedder
—Crankshaft
Packing (Front)
—Timing
Gear
Cover Gasket
—Timing
Gear
Cover
—Vibration
Damper
-Bolt
-Washer
-Bolt
—Dowel Pin
-Camshaft
Thrust
Retainer and Bolt
—Washer
-Distributor
Drive
Gear
—Fuel
Pump Eccentric
82
Page 83 of 376
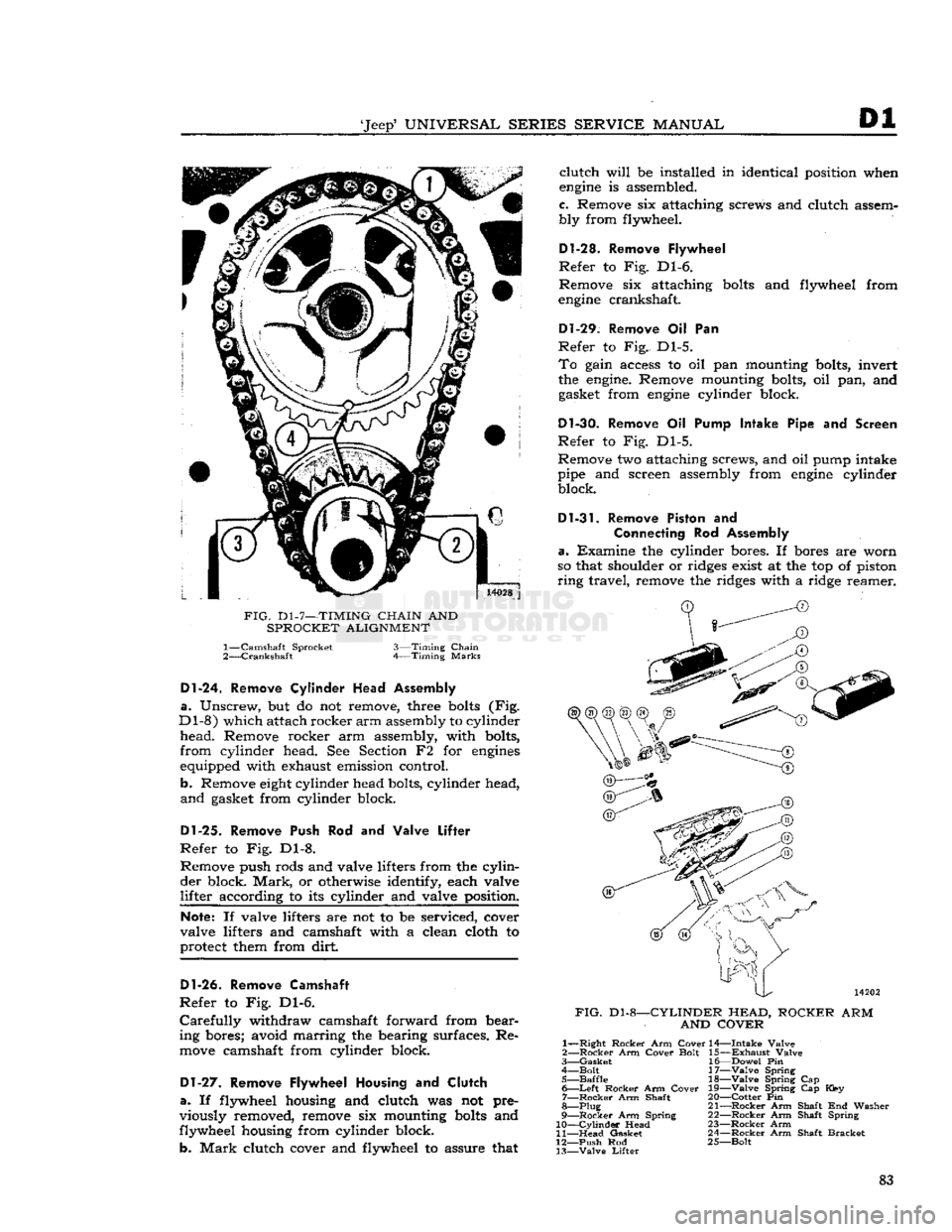
'Jeep'
UNIVERSAL
SERIES SERVICE
MANUAL
Dl
14028
j
FIG.
D1-7—TIMING
CHAIN
AND
SPROCKET ALIGNMENT 1—
Camshaft Sprocket
2—
Crankshaft
3—Timing
Chain
Timing
Marks
Dl-24.
Remove
Cylinder
Head Assembly
a.
Unscrew, but do not remove, three
bolts
(Fig.
Dl-8)
which attach rocker
arm
assembly to cylinder
head.
Remove rocker arm assembly, with bolts,
from
cylinder head. See Section F2 for
engines
equipped with exhaust emission control.
b. Remove
eight
cylinder head bolts, cylinder head,
and
gasket from cylinder block.
Dl-25.
Remove Push Rod and Valve
Lifter
Refer
to Fig. Dl-8. Remove push rods and valve lifters from the
cylinÂ
der
block.
Mark,
or otherwise identify, each valve
lifter
according to its cylinder and valve position.
Note:
If valve lifters are not to be serviced, cover
valve lifters and camshaft with a clean cloth to
protect them from dirt
Dl-26.
Remove Camshaft
Refer
to Fig. Dl-6.
Carefully
withdraw camshaft forward from bearÂ
ing bores; avoid marring the bearing surfaces. ReÂ
move
camshaft from cylinder block.
Dl-27.
Remove Flywheel Housing and
Clutch
a.
If flywheel housing and clutch was not preÂ
viously removed, remove six mounting
bolts
and
flywheel housing from cylinder block.
b.
Mark
clutch cover and flywheel to assure that
clutch
will
be installed in identical position when
engine
is assembled.
c. Remove six attaching screws and clutch assemÂ
bly from flywheel.
D1-28. Remove Flywheel
Refer
to Fig. Dl-6.
Remove six attaching
bolts
and flywheel from
engine
crankshaft.
Dl-29.
Remove Oil Pan
Refer
to Fig. Dl-5.
To
gain access to oil pan mounting bolts, invert
the
engine.
Remove mounting bolts, oil pan, and gasket from
engine
cylinder block.
Dl-30.
Remove Oil Pump Intake Pipe and Screen
Refer
to Fig. Dl-5.
Remove two attaching screws, and oil pump intake
pipe and screen assembly from
engine
cylinder block.
Dl-31.
Remove Piston and
Connecting
Rod Assembly
a.
Examine the cylinder bores. If bores are worn
so that shoulder or ridges exist at the top of piston
ring
travel, remove the ridges with a ridge reamer.
FIG.
Dl-8-
-CYLINDER HEAD,
AND COVER
ROCKER
ARM
1—
—Right
Rocker
Arm
Cover
2—
Rocker
Arm
Cover
Bolt
3—
Gasket
4—
Bolt
5—
Baffle
6—
Left
Rocker
Arm
Cover
7—
Rocker
Arm Shaft
8—Plug
9—
Rocker
Arm Spring
10—
Cylinder
Head
11—
Head
Gasket
12—
Push
Rod
13—
Valve
Lifter
14—
Intake
Valve
15—
Exhaust
Valve
16—
Dowel
Pin
17—
Valve
Spring 18—
Valve
Spring Cap
19—
Valve
Spring Cap Key
20—
Cotter
Pin
21—
Rocker
Arm Shaft End Washer
22—
Rocker
Arm Shaft Spring
23—
Rocker
Arm
24—
Rocker
Arm Shaft
Bracket
25—
Bolt
83
Page 84 of 376
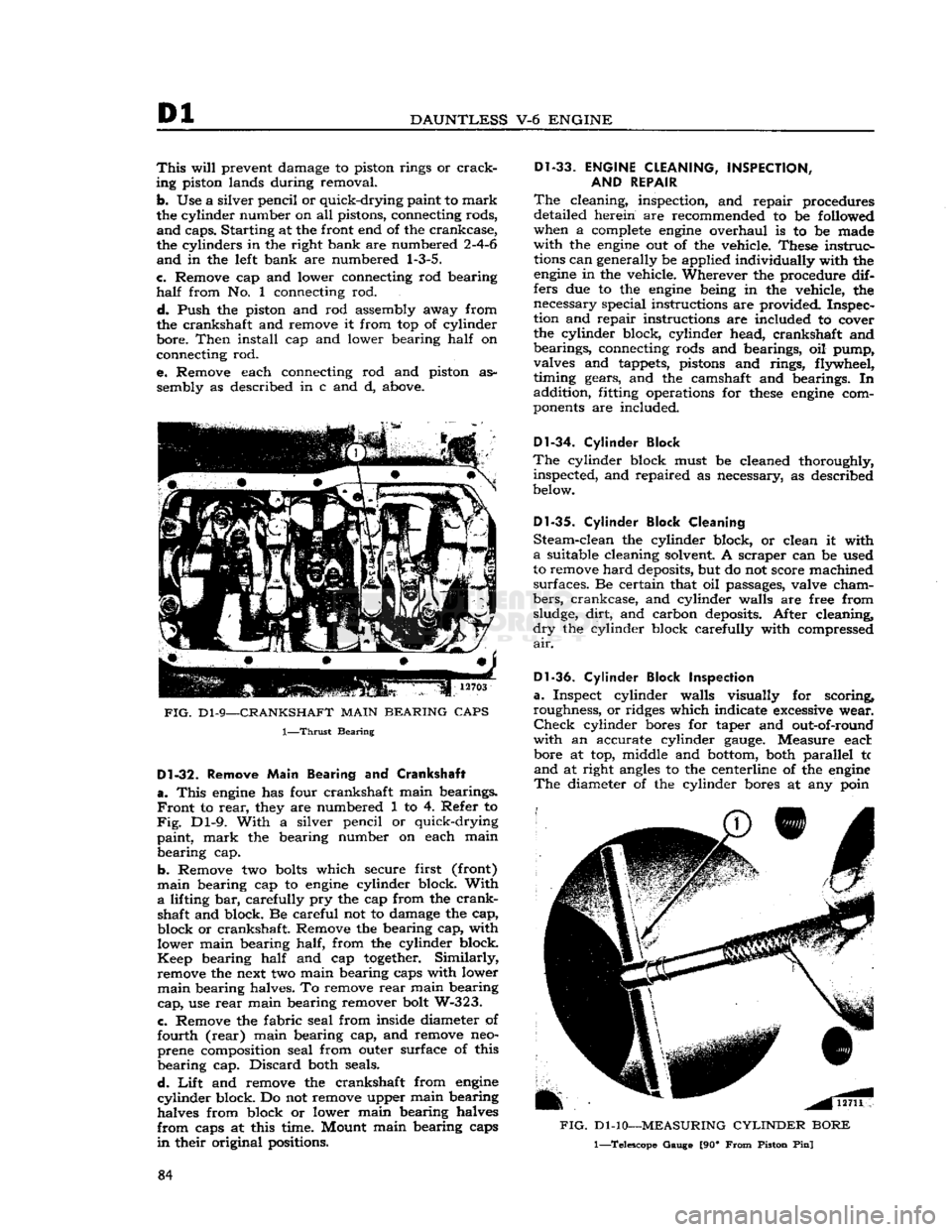
Dl
DAUNTLESS
V-6
ENGINE
This
will
prevent damage to piston rings or
crackÂ
ing piston lands during removal.
b. Use a silver pencil or quick-drying paint to mark
the cylinder number on all pistons, connecting rods,
and
caps. Starting at the front end of the crankcase,
the cylinders in the right bank are numbered 2-4-6
and
in the
left
bank are numbered
1-3-5.
c. Remove cap and lower connecting rod bearing
half
from No. 1 connecting rod.
d.
Push the piston and rod assembly away from
the crankshaft and remove it from top of cylinder bore. Then install cap and lower bearing half on
connecting rod.
e. Remove each connecting rod and piston as sembly as described in c and d, above.
FIG.
D1-9—CRANKSHAFT
MAIN
BEARING
CAPS
1—Thrust
Bearing
D1-32.
Remove
Main
Bearing and Crankshaft
a.
This
engine
has four crankshaft main bearings.
Front
to
rear,
they are numbered 1 to 4. Refer to
Fig.
Dl-9. With a silver pencil or quick-drying
paint, mark the bearing number on each main bearing cap.
b. Remove two
bolts
which secure first (front)
main
bearing cap to
engine
cylinder block. With
a
lifting bar, carefully pry the cap from the crank shaft and block. Be careful not to damage the cap,
block or crankshaft. Remove the bearing cap, with
lower main bearing half, from the cylinder block.
Keep
bearing half and cap
together.
Similarly, remove the next two main bearing caps with lower
main
bearing halves. To remove
rear
main bearing
cap,
use
rear
main bearing remover bolt W-323.
c. Remove the fabric seal from inside diameter of
fourth (rear) main bearing cap, and remove neo-
prene composition seal from outer surface of this
bearing cap. Discard both seals.
d.
Lift
and remove the crankshaft from
engine
cylinder
block. Do not remove upper main bearing
halves from block or lower main bearing halves
from
caps at this time. Mount main bearing caps
in
their original positions.
Dl-33.
ENGINE
CLEANING,
INSPECTION,
AND
REPAIR
The
cleaning, inspection, and repair procedures
detailed herein are recommended to be followed
when a
complete
engine
overhaul is to be made
with the
engine
out of the vehicle. These instrucÂ
tions
can generally be applied individually with the
engine
in the vehicle. Wherever the procedure difÂ
fers due to the
engine
being in the vehicle, the necessary special instructions are provided. InspecÂ
tion and repair instructions are included to cover
the cylinder block, cylinder head, crankshaft and bearings, connecting rods and bearings, oil pump,
valves and tappets, pistons and rings, flywheel,
timing gears, and the camshaft and bearings. In
addition, fitting operations for
these
engine
comÂ
ponents
are included.
D1-34.
Cylinder Block
The
cylinder block must be cleaned thoroughly, inspected, and repaired as necessary, as described
below.
Dl-35.
Cylinder Block Cleaning
Steam-clean the cylinder block, or clean it with
a
suitable cleaning solvent A scraper can be used
to remove
hard
deposits, but do not score machined
surfaces. Be certain that oil passages, valve chamÂ
bers,
crankcase, and cylinder walls are free from sludge, dirt, and carbon deposits. After cleaning,
dry
the cylinder block carefully with compressed
air.
Dl-36.
Cylinder Block Inspection
a.
Inspect cylinder walls visually for scoring,
roughness, or ridges which indicate excessive wear.
Check
cylinder bores for taper and out-of-round
with an accurate cylinder
gauge.
Measure eact bore at top, middle and bottom, both parallel tc
and
at right
angles
to the centerline of the
engine
The
diameter of the cylinder bores at any poin
FIG.
Dl-10—MEASURING
CYLINDER
BORE
1—Telescope Gauge [90*
From
Piston Pin]
84
Page 85 of 376
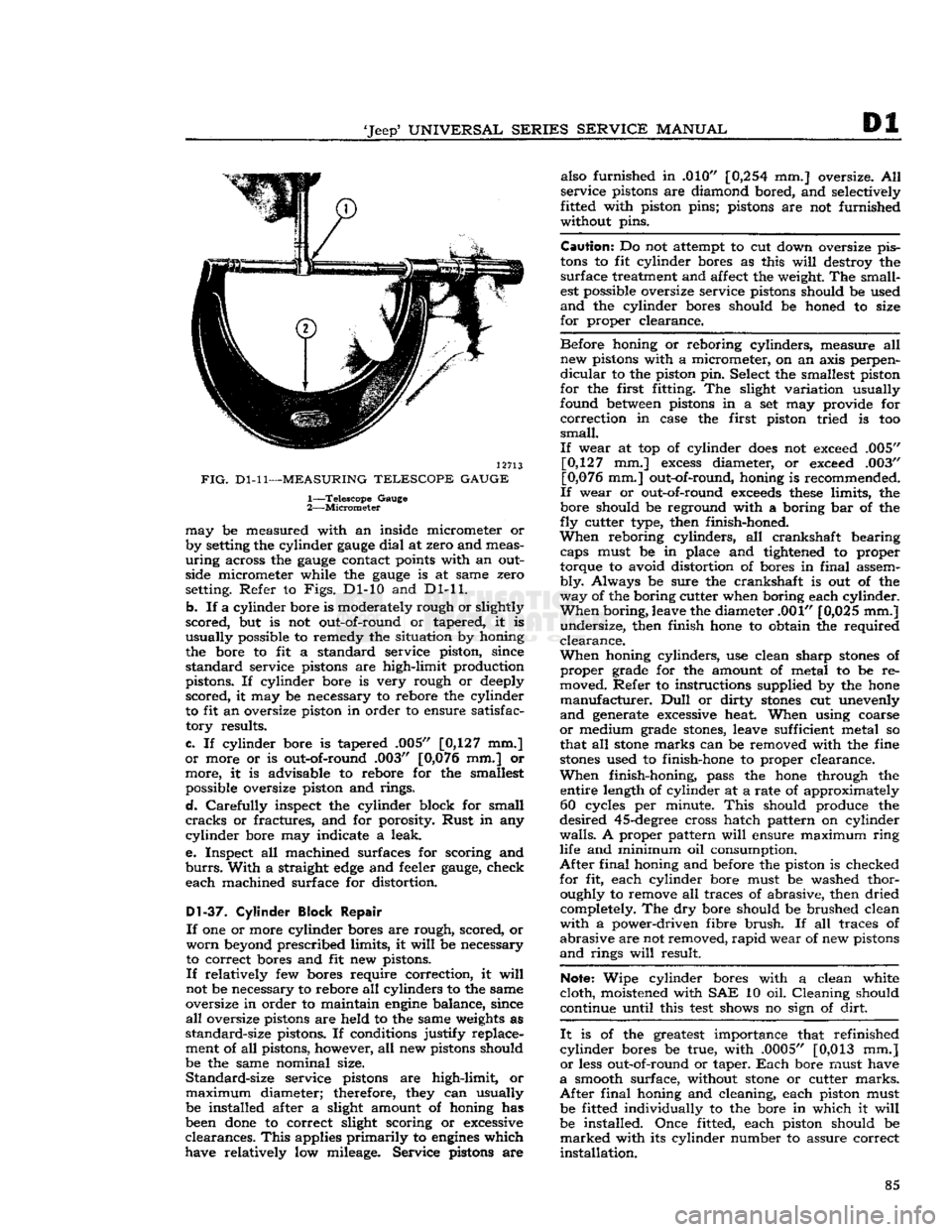
'Jeep*
UNIVERSAL
SERIES SERVICE
MANUAL
Dl
12713
FIG.
Dl-11—MEASURING
TELESCOPE GAUGE
1—
Telescope
Gauge
2—
Micrometer
may
be measured with an inside micrometer or
by setting the cylinder
gauge
dial
at zero and measÂ
uring
across the
gauge
contact points with an outÂside micrometer while the
gauge
is at same zero
setting. Refer to
Figs.
Dl-10 and Dl-11.
b.
If a cylinder bore is moderately rough or slightly
scored,
but is not out-of-round or tapered, it is
usually
possible to remedy the situation by honing
the bore to fit a standard service piston, since
standard
service pistons are high-limit production
pistons. If cylinder bore is very rough or deeply
scored,
it may be necessary to rebore the cylinder
to fit an oversize piston in order to ensure satisfacÂ
tory
results.
c.
If cylinder bore is tapered .005" [0,127 mm.]
or
more or is out-of-round .003" [0,076 mm.] or
more,
it is advisable to rebore for the smallest possible oversize piston and rings.
d.
Carefully
inspect the cylinder block for small
cracks
or fractures, and for porosity.
Rust
in any
cylinder
bore may indicate a leak.
e.
Inspect all machined surfaces for scoring and
burrs.
With
a straight
edge
and feeler
gauge,
check
each
machined surface for distortion.
D1-37.
Cylinder Block Repair
If
one or more cylinder bores are rough, scored, or
worn
beyond prescribed limits, it
will
be necessary
to correct bores and fit new pistons.
If
relatively few bores require correction, it
will
not be necessary to rebore all cylinders to the same
oversize in order to maintain
engine
balance, since
all
oversize pistons are held to the same weights as
standard-size
pistons. If conditions justify replaceÂ
ment of all pistons, however, all new pistons should
be the same nominal size.
Standard-size
service pistons are high-limit, or
maximum
diameter; therefore, they can usually be installed after a slight amount of honing has
been
done
to correct slight scoring or excessive
clearances.
This
applies
primarily
to
engines
which
have relatively low mileage. Service pistons are also furnished in .010"
[0,254
mm.] oversize. All
service
pistons are diamond bored, and selectively
fitted with piston pins; pistons are not furnished
without pins.
Caution:
Do not attempt to cut down oversize pisÂ
tons
to fit cylinder bores as this
will
destroy the
surface
treatment and affect the weight. The smallÂ
est possible oversize service pistons should be used
and
the cylinder bores should be honed to size
for
proper clearance.
Before
honing or reboring cylinders, measure all new pistons with a micrometer, on an axis perpenÂ
dicular
to the piston pin. Select the smallest piston
for
the first fitting. The slight variation usually
found between pistons in a set may provide for
correction
in case the first piston tried is too
small.
If
wear at top of cylinder
does
not exceed .005" [0,127 mm.]
excess
diameter, or exceed .003"
[0,076 mm.] out-of-round, honing is recommended.
If
wear or out-of-round
exceeds
these
limits, the
bore should be reground with a boring bar of the
fly
cutter type, then finish-honed.
When
reboring cylinders, all crankshaft bearing caps must be in place and tightened to proper
torque to avoid distortion of bores in
final
assemÂ
bly.
Always be sure the crankshaft is out of the
way
of the boring cutter when boring each cylinder.
When
boring, leave the diameter .001" [0,025 mm.]
undersize,
then finish hone to obtain the required
clearance.
When
honing cylinders, use clean sharp
stones
of
proper
grade for the amount of metal to be reÂ
moved. Refer to instructions supplied by the hone
manufacturer.
Dull
or dirty
stones
cut unevenly
and
generate excessive heat. When using coarse
or
medium grade
stones,
leave sufficient metal so
that all
stone
marks can be removed with the fine
stones
used to finish-hone to proper clearance.
When
finish-honing, pass the hone through the entire length of cylinder at a rate of approximately 60 cycles per minute.
This
should produce the
desired
45-degree
cross hatch pattern on cylinder
walls.
A proper pattern
will
ensure maximum
ring
life and minimum oil consumption.
After
final
honing and before the piston is checked
for
fit, each cylinder bore must be washed thor oughly to remove all traces of abrasive, then dried completely. The dry bore should be brushed clean
with
a power-driven fibre
brush.
If all traces of
abrasive
are not removed,
rapid
wear of new pistons
and
rings
will
result.
Note:
Wipe cylinder bores with a clean white
cloth,
moistened with SAE 10 oil. Cleaning should
continue until this
test
shows no sign of
dirt.
It
is of the greatest importance that refinished
cylinder
bores be true, with .0005" [0,013 mm.]
or
less out-of-round or taper.
Each
bore must have
a
smooth surface, without
stone
or cutter
marks.
After
final
honing and cleaning, each piston must be fitted individually to the bore in which it
will
be installed. Once fitted, each piston should be
marked
with its cylinder number to assure correct
installation.
85
Page 86 of 376
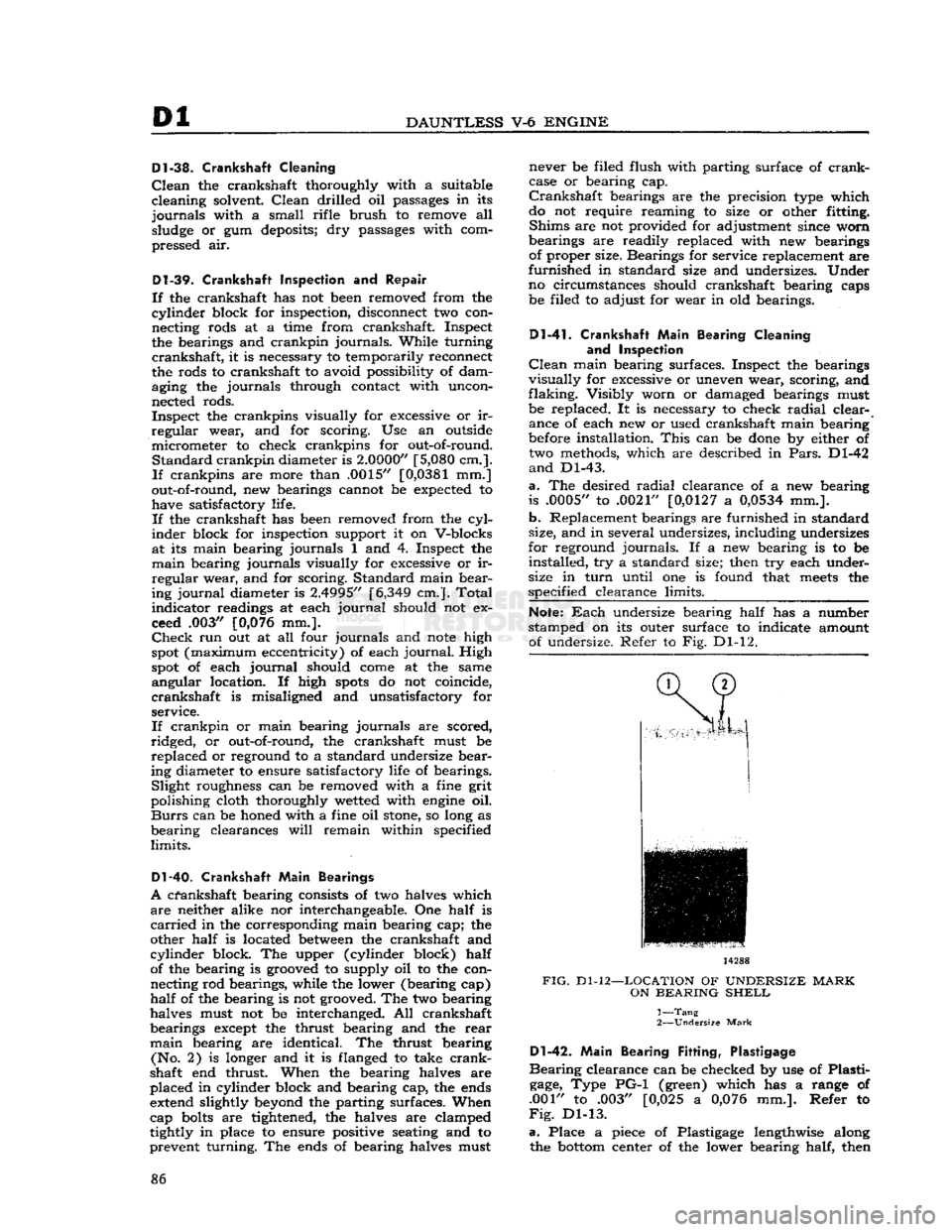
Dl
DAUNTLESS
V-6
ENGINE
Dl-38.
Crankshaft
Cleaning
Clean
the crankshaft thoroughly with a suitable
cleaning solvent.
Clean
drilled oil
passages
in its
journals
with a small rifle brush to remove all
sludge
or gum deposits; dry
passages
with comÂ
pressed air.
Dl-39.
Crankshaft
Inspection
and
Repair
If
the crankshaft has not
been
removed from the
cylinder
block for inspection, disconnect two con necting rods at a time from crankshaft. Inspect
the bearings and crankpin journals. While turning
crankshaft,
it is necessary to temporarily reconnect
the rods to crankshaft to avoid possibility of dam aging the journals through contact with unconÂ
nected rods.
Inspect the crankpins visually for excessive or irÂ
regular
wear, and for scoring. Use an
outside
micrometer to check crankpins for out-of-round.
Standard
crankpin
diameter is
2.0000"
[5,080
cm.].
If
crankpins are more than .0015"
[0,0381
mm.]
out-of-round, new bearings cannot be
expected
to
have satisfactory life.
If
the crankshaft has
been
removed from the
cylÂ
inder
block for inspection support it on V-blocks
at its main bearing journals 1 and 4. Inspect the
main
bearing journals visually for excessive or irÂ
regular
wear, and for scoring. Standard main bearÂ
ing
journal
diameter is 2.4995"
[6,349
cm.].
Total
indicator readings at each
journal
should not exÂ
ceed .003"
[0,076
mm.].
Check
run out at all four journals and
note
high
spot
(maximum eccentricity) of each
journal.
High
spot
of each
journal
should
come
at the same
angular
location. If high
spots
do not coincide,
crankshaft
is misaligned and unsatisfactory for
service.
If
crankpin or main bearing journals are scored,
ridged, or out-of-round, the crankshaft must be replaced or reground to a standard undersize bearÂ
ing diameter to ensure satisfactory life of bearings. Slight roughness can be removed with a fine grit
polishing cloth thoroughly
wetted
with
engine
oil.
Burrs
can
be
honed with a fine oil
stone,
so long as
bearing clearances
will
remain within specified
limits.
Dl-40.
Crankshaft
Main
Bearings
A
crankshaft bearing consists of two halves which
are
neither alike nor interchangeable. One half is
carried
in the corresponding main bearing cap; the
other half is located
between
the crankshaft and
cylinder
block. The upper (cylinder block) half
of the bearing is grooved to supply oil to the con necting rod bearings, while the lower (bearing cap)
half
of the bearing is not grooved. The two bearing
halves must not be interchanged. All crankshaft
bearings
except
the thrust bearing and the
rear
main
bearing are identical. The thrust bearing (No. 2) is longer and it is flanged to take
crankÂ
shaft end thrust. When the bearing halves are
placed in cylinder block and bearing cap, the
ends
extend slightly beyond the parting surfaces. When
cap
bolts
are tightened, the halves are clamped
tightly in place to ensure positive seating and to
prevent turning. The
ends
of bearing halves must never be filed flush with parting surface of
crankÂ
case or bearing cap.
Crankshaft
bearings are the precision type which
do not require reaming to size or other fitting.
Shims
are not provided for adjustment since worn
bearings are readily replaced with new bearings of proper size. Bearings for service replacement are
furnished
in standard size and undersizes. Under no circumstances should crankshaft bearing caps
be filed to adjust for wear in old bearings.
Dl-41.
Crankshaft
Main
Bearing
Cleaning
and
Inspection
Clean
main bearing surfaces. Inspect the bearings
visually
for excessive or uneven wear, scoring, and
flaking.
Visibly worn or damaged bearings must
be replaced. It is necessary to check
radial
clear ance of each new or used crankshaft main bearing
before installation.
This
can be
done
by either of two methods, which are described in
Pars.
Dl-42
and
Dl-43.
a.
The desired
radial
clearance of a new bearing
is .0005" to .0021"
[0,0127
a
0,0534
mm.].
b. Replacement bearings are furnished in standard
size, and in several undersizes, including undersizes
for reground journals. If a new bearing is to be installed, try a standard size; then try each underÂ
size in turn until one is found that
meets
the
specified clearance limits.
Note:
Each
undersize bearing half has a number
stamped on its outer surface to indicate amount of undersize. Refer to Fig. Dl-12. 14288
FIG.
Dl-12—LOCATION
OF
UNDERSIZE
MARK
ON
BEARING
SHELL
1—
Tang
2—
Undersize
Mark
Dl-42.
Main
Bearing
Fitting,
Plastigage
Bearing
clearance can be checked by use of PlastiÂ
gage,
Type PG-1 (green) which has a range of
.001" to .003" [0,025 a
0,076
mm.]. Refer to
Fig.
Dl-13.
a.
Place a piece of Plastigage lengthwise along the
bottom
center of the lower bearing half, then 86
Page 87 of 376
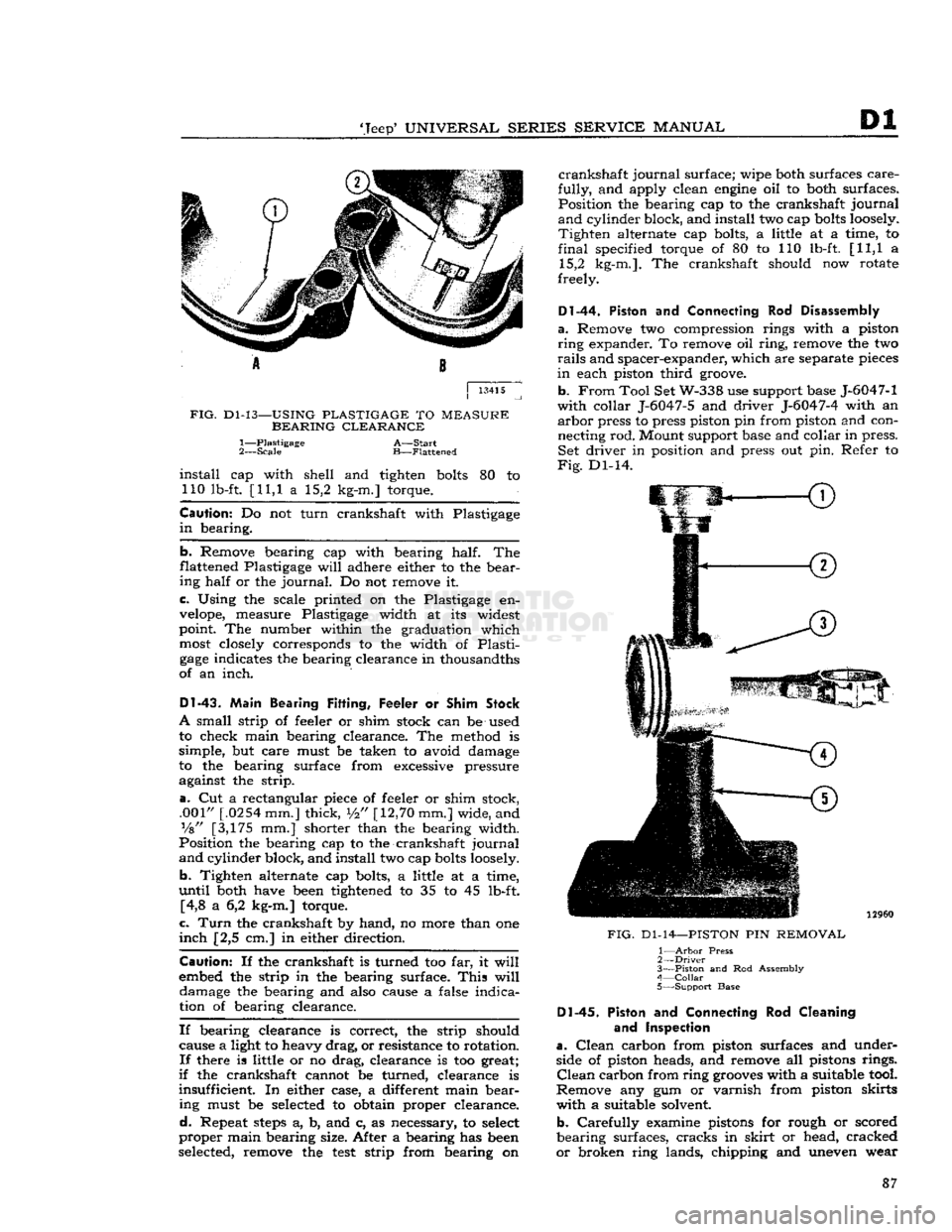
'Jeep'
UNIVERSAL
SERIES SERVICE
MANUAL
Dl
A 8
j
13415
FIG.
Dl-13—USING
PLASTIGAGE
TO
MEASURE
BEARING CLEARANCE
1— Plastigage
A—Start
2—
Scale
B—Flattened
install
cap with shell and tighten
bolts
80 to 110 lb-ft. [11,1 a 15,2 kg-m.] torque.
Caution:
Do not turn crankshaft with Plastigage
in
bearing.
b.
Remove bearing cap with bearing half. The
flattened Plastigage
will
adhere either to the bear ing half or the
journal.
Do not remove it.
c. Using the scale printed on the Plastigage enÂ
velope,
measure Plastigage width at its widest
point. The number within the graduation which
most
closely corresponds to the width of PlastiÂ
gage
indicates the bearing clearance in thousandths
of an inch.
DI-43.
Main Bearing
Fitting,
Feeler or
Shim
Stock
A
small strip of feeler or shim stock can be used
to check main bearing clearance. The method is
simple, but care must be taken to avoid damage
to the bearing surface from excessive pressure against the strip.
a.
Cut a rectangular piece of feeler or shim stock, .001"
[.0254
mm.] thick,
i/2"
[12,70
mm.] wide, and
Vs"
[3,175 mm.] shorter than the bearing width.
Position the bearing cap to the crankshaft journal
and
cylinder block, and install two cap
bolts
loosely.
b.
Tighten alternate cap bolts, a little at a time,
until
both have
been
tightened to 35 to 45 lb-ft. [4,8 a 6,2 kg-m.] torque.
c.
Turn
the crankshaft by hand, no more than one
inch
[2,5 cm.] in either direction.
Caution:
If the crankshaft is turned too far, it
will
embed the strip in the bearing surface.
This
will
damage the bearing and also cause a false indicaÂtion of bearing clearance.
If
bearing clearance is correct, the strip should cause a light to heavy drag, or resistance to rotation.
If
there is little or no drag, clearance is too great;
if
the crankshaft cannot be turned, clearance is
insufficient. In either case, a different main bear ing must be
selected
to obtain proper clearance.
d.
Repeat
steps
a, b, and c, as necessary, to
select
proper main bearing size. After a bearing has
been
selected, remove the
test
strip from bearing on
crankshaft
journal surface; wipe both surfaces careÂ
fully,
and apply clean
engine
oil to both surfaces. Position the bearing cap to the crankshaft journal
and
cylinder block, and install two cap
bolts
loosely.
Tighten
alternate cap bolts, a little at a time, to
final
specified torque of 80 to 110 lb-ft. [11,1 a 15,2 kg-m.]. The crankshaft should now rotate
freely.
Dl-44.
Piston
and
Connecting
Rod
Disassembly
a.
Remove two compression rings with a piston
ring
expander. To remove oil ring, remove the two
rails
and spacer-expander, which are separate
pieces
in
each piston third
groove.
b.
From
Tool Set W-338 use support base J-6047-1
with collar J-6047-5 and driver J-6047-4 with an
arbor
press to press piston pin from piston and conÂ
necting rod. Mount support base and collar in press. Set driver in position and press out pin. Refer to
Fig.
Dl-14.
FIG.
Dl-14—PISTON
PIN
REMOVAL
1—
Arbor
Press
2—
Driver
3—
Piston
and Rod Assembly
4—
Collar
•
5—Support Base Dl-45.
Piston
and
Connecting
Rod
Cleaning
and Inspection
a.
Clean
carbon from piston surfaces and underÂ
side of piston heads, and remove all pistons rings.
Clean
carbon from ring
grooves
with a suitable tool.
Remove any gum or varnish from piston skirts with a suitable solvent.
b.
Carefully examine pistons for rough or scored
bearing surfaces, cracks in
skirt
or head, cracked
or
broken ring lands, chipping and uneven wear 87
Page 88 of 376
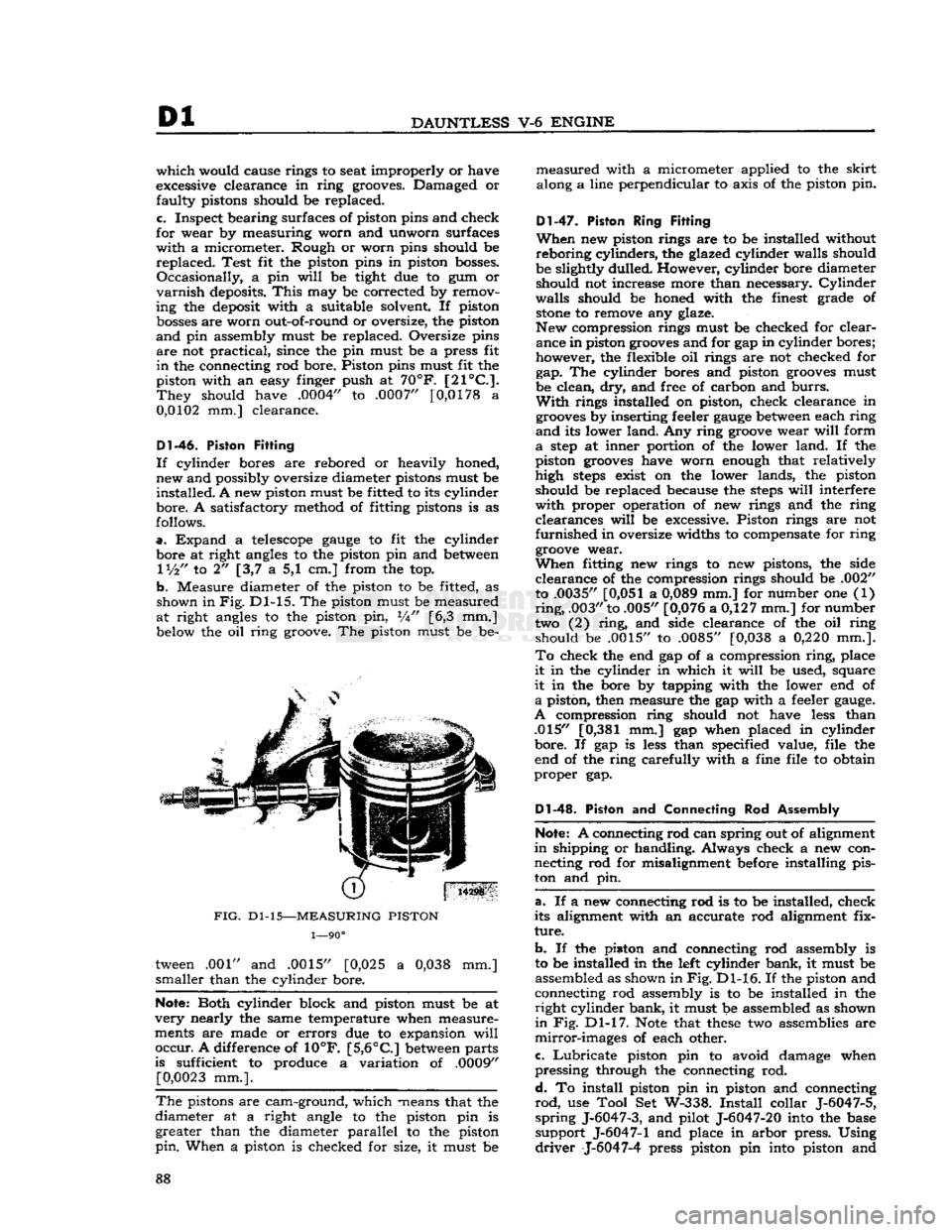
Pi
DAUNTLESS
Â¥-6
ENGINE
which
would cause rings to seat improperly or have
excessive clearance in
ring
grooves. Damaged or
faulty
pistons should be replaced,
c.
Inspect bearing surfaces of piston pins and check
for
wear by measuring worn and unworn surfaces
with
a micrometer. Rough or worn pins should be
replaced.
Test fit the piston pins in piston
bosses.
Occasionally,
a pin
will
be tight due to gum or
varnish
deposits.
This
may be corrected by removÂ
ing
the deposit with a suitable solvent. If piston
bosses
are worn out-of-round or oversize, the piston
and
pin assembly must be replaced. Oversize pins
are
not
practical,
since the pin must be a press fit
in
the connecting rod bore. Piston pins must fit the
piston with an easy finger push at
70°F.
[21°C.].
They
should have .0004" to .0007"
[0,0178
a
0,0102
mm.] clearance.
Dl-46.
Piston Fitting
If
cylinder bores are rebored or heavily honed,
new and possibly oversize diameter pistons must be
installed.
A new piston must be fitted to its cylinder
bore.
A satisfactory method of fitting pistons is as
follows.
a.
Expand
a
telescope
gauge
to fit the cylinder bore at right angles to the piston pin and
between
1
Vi"
to 2" [3,7 a 5,1 cm.] from the top.
b.
Measure diameter of the piston to be fitted, as
shown in
Fig.
Dl-15. The piston must be measured
at
right angles to the piston pin, W [6,3 mm.] below the oil
ring
groove. The piston must be be-
FIG.
Dl-15—MEASURING
PISTON
1—90°
tween .001" and .0015" [0,025 a
0,038
mm.]
smaller
than the cylinder bore.
Note:
Both cylinder block and piston must be at
very
nearly the same temperature when measureÂ
ments are made or
errors
due to expansion
will
occur.
A difference of 10°F.
[5,6°C]
between
parts
is sufficient to produce a variation of .0009"
[0,0023
mm.].
The
pistons are cam-ground, which means that the
diameter at a right angle to the piston pin is
greater
than the diameter
parallel
to the piston
pin.
When a piston is checked for size, it must be
measured
with a micrometer applied to the
skirt
along a line
perpendicular
to axis of the piston pin.
Dl-47.
Piston Ring Fitting
When
new piston rings are to be installed without
reboring
cylinders,
the glazed cylinder walls should
be slightly dulled. However, cylinder bore diameter
should
not increase more than necessary.
Cylinder
walls
should be honed with the finest grade of
stone
to remove any glaze.
New compression rings must be checked for clear ance in piston
grooves
and for gap in cylinder bores;
however, the flexible oil rings are not checked for gap. The cylinder bores and piston
grooves
must
be clean, dry, and free of carbon and
burrs.
With
rings installed on piston, check clearance in
grooves
by inserting feeler
gauge
between
each
ring
and
its lower
land.
Any
ring
groove
wear
will
form
a
step
at inner portion of the lower
land.
If the
piston
grooves
have worn enough that relatively
high
steps
exist on the lower lands, the piston
should
be replaced because the
steps
will
interfere
with
proper operation of new rings and the
ring
clearances
will
be excessive. Piston rings are not
furnished
in oversize widths to compensate for
ring
groove
wear.
When
fitting new rings to new pistons, the side
clearance
of the compression rings should be .002" to .0035"
[0,051
a
0,089
mm.] for number one (1)
ring,
.003" to .005" [0,076 a 0,127 mm.] for number
two (2)
ring,
and side clearance of the oil
ring
should
be .0015" to .0085" [0,038 a
0,220
mm.].
To
check the end gap of a compression
ring,
place
it
in the cylinder in which it
will
be used, square
it
in the bore by tapping with the lower end of
a
piston, then measure the gap with a feeler
gauge.
A
compression
ring
should not have
less
than .015"
[0,381
mm.] gap when placed in cylinder
bore.
If gap is
less
than specified value, file the
end of the
ring
carefully with a fine file to obtain
proper
gap.
Dl-48.
Piston and Connecting Rod Assembly
Note:
A connecting rod can spring out of alignment
in
shipping or handling. Always check a new conÂ
necting rod for misalignment before installing pisÂ
ton and pin.
a.
If a new connecting rod is to be installed, check
its alignment with an accurate rod alignment fixÂ
ture.
b.
If the piston and connecting rod assembly is
to be installed in the left cylinder bank, it must be assembled as shown in
Fig.
Dl-16. If the piston and
connecting rod assembly is to be installed in the
right
cylinder bank, it must be assembled as shown
in
Fig. Dl-17.
Note
that
these
two assemblies are
mirror-images
of each other.
c.
Lubricate
piston pin to avoid damage when
pressing
through the connecting rod.
d.
To install piston pin in piston and connecting
rod,
use
Tool
Set W-338.
Install
collar J-6047-5,
spring
J-6047-3, and pilot J-6047-20 into the base
support
J-6047-1 and place in
arbor
press. Using
driver
J-6047-4 press piston pin into piston and 88
Page 89 of 376
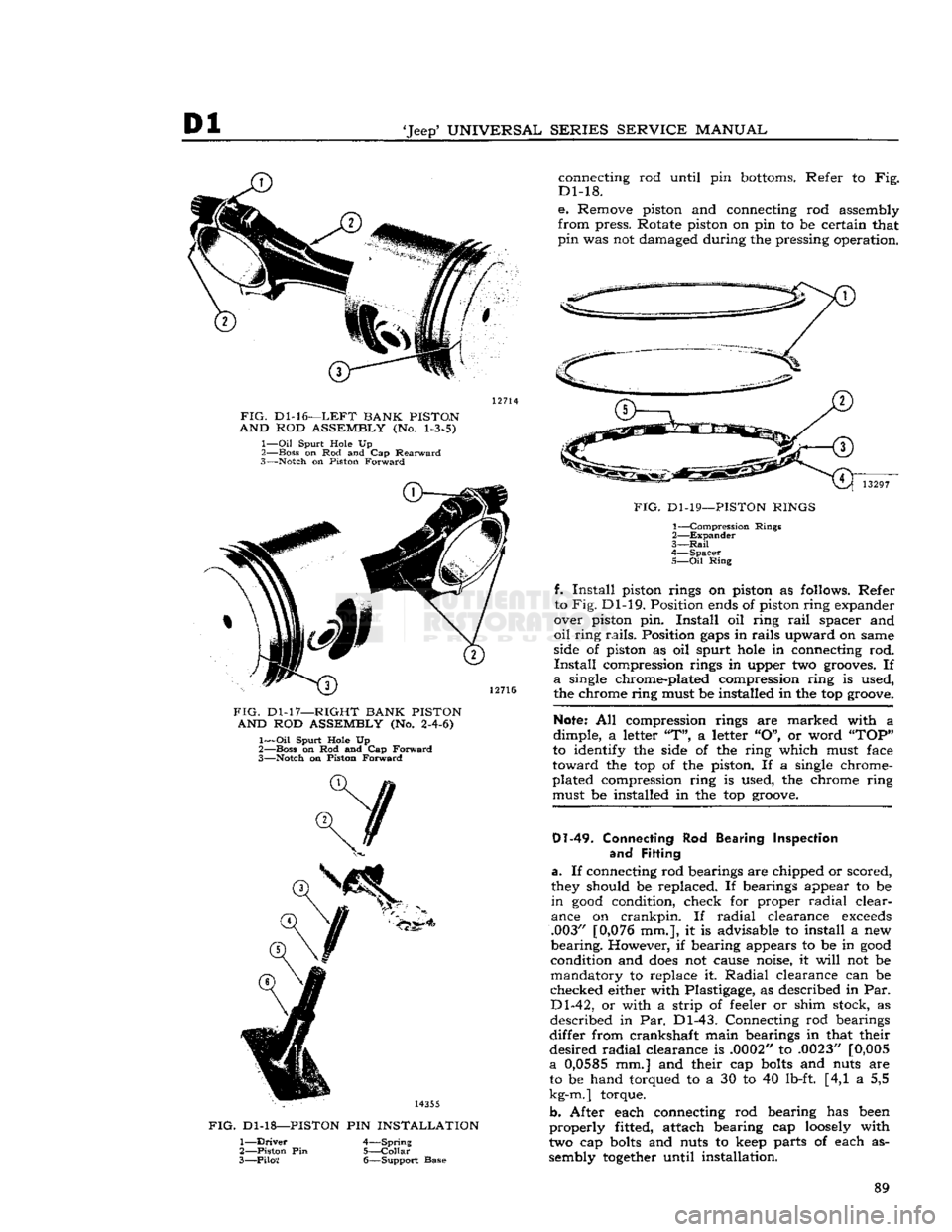
Dl
'Jeep5
UNIVERSAL
SERIES
SERVICE
MANUAL
FIG.
Dl-16—LEFT
BANK
PISTON
AND
ROD
ASSEMBLY
(No.
1-3-5)
1—
Oil
Spurt Hole Up
2— Boss on Rod and Cap
Rearward
3—
Notch on Piston
Forward
12716
FIG.
Dl-17—RIGHT
BANK
PISTON
AND
ROD
ASSEMBLY
(No. 2-4-6)
1—
Oil
Spurt Hole Up
2— Boss on Rod and Cap
Forward
3—
Notch on Piston
Forward
14355
FIG.
Dl-18—-PISTON
PIN
INSTALLATION
connecting rod until pin
bottoms.
Refer to Fig.
Dl-18.
e.
Remove piston and connecting rod assembly
from
press. Rotate piston on pin to be certain that
pin
was not damaged during the pressing operation. 13297
1—
Driver
2— Piston Pin
3—
Piloi
4—
Spring
5—
Collar
6—
Support
Base
FIG.
Dl-19—PISTON
RINGS
1—
Compression
Rings
2—
Expander
3—
Rail
4—
Spacer
5—
Oil
Ring
f.
Install
piston rings on piston as follows. Refer
to Fig. Dl-19. Position ends of piston ring expander
over piston pin.
Install
oil ring
rail
spacer and
oil
ring
rails.
Position
gaps
in rails upward on same
side of piston as oil spurt
hole
in connecting rod.
Install
compression rings in upper two grooves. If
a
single chrome-plated compression ring is used,
the chrome ring must be installed in the top groove.
Note:
All compression rings are marked with a
dimple, a letter
"T",
a letter
"O",
or word
"TOP"
to identify the side of the ring which must face
toward
the top of the piston. If a single chrome-
plated compression ring is used, the chrome ring must be installed in the top groove.
Dl-49.
Connecting
Rod
Bearing Inspection and Fitting
a.
If connecting rod bearings are chipped or scored,
they should be replaced. If bearings appear to be
in
good
condition, check for proper
radial
clearÂ
ance on crankpin. If
radial
clearance
exceeds
.003" [0,076 mm.], it is advisable to install a new
bearing.
However, if bearing appears to be in
good
condition and
does
not cause noise, it
will
not be mandatory to replace it.
Radial
clearance can be
checked either with Plastigage, as described in Par.
Dl-42,
or with a strip of feeler or shim stock, as
described in Par. Dl-43. Connecting rod bearings
differ from crankshaft main bearings in that their
desired
radial
clearance is .0002" to .0023" [0,005
a
0,0585
mm.] and their cap
bolts
and nuts are to be hand torqued to a 30 to 40 lb-ft. [4,1 a 5,5
kg-m.] torque.
b. After each connecting rod bearing has been
properly
fitted, attach bearing cap
loosely
with
two cap
bolts
and nuts to keep parts of each asÂ
sembly
together
until installation. 89
Page 90 of 376
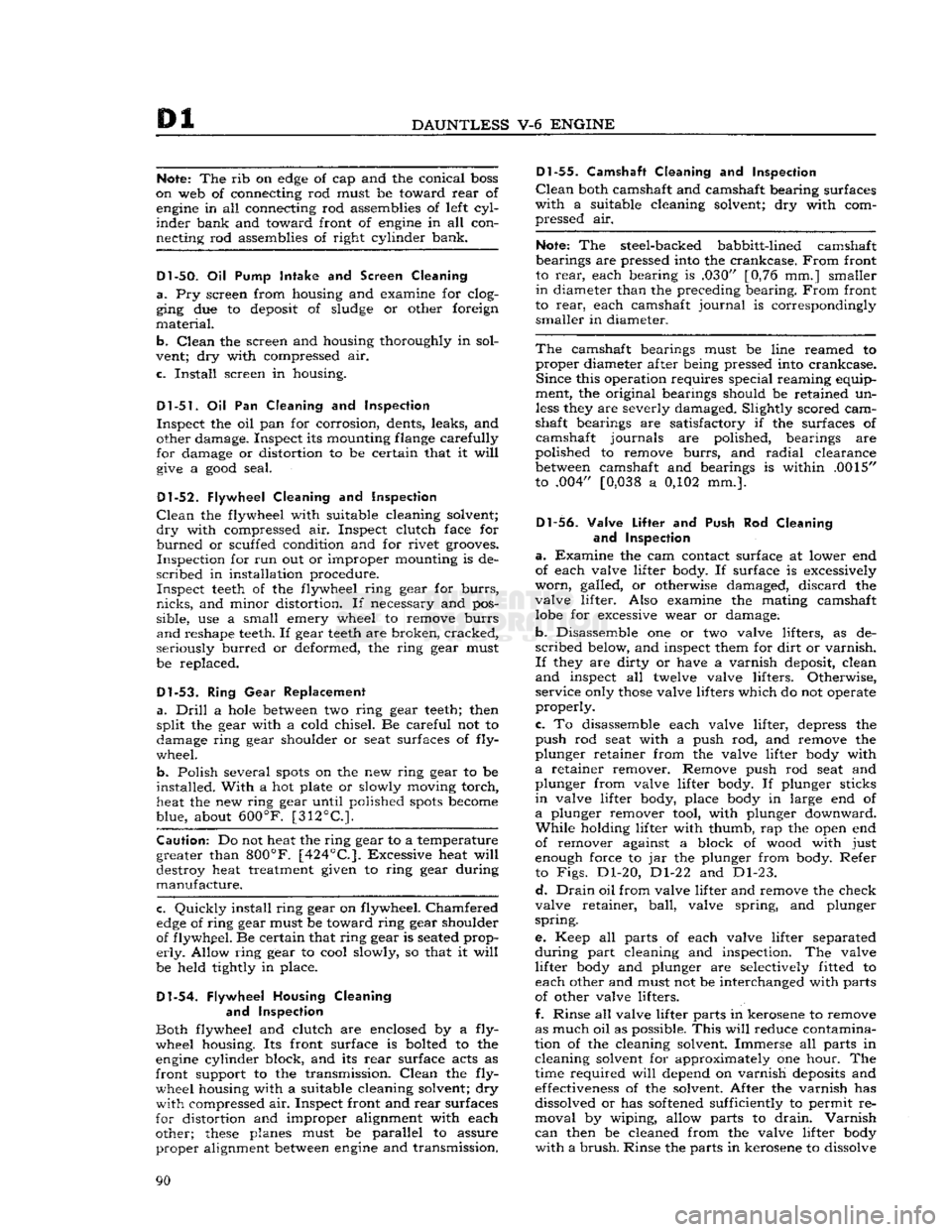
DAUNTLESS
V-6
ENGINE
Note:
The rib on
edge
of cap and the conical
boss
on web of connecting rod must be toward
rear
of
engine
in all connecting rod assemblies of left
cylÂ
inder
bank and toward front of
engine
in all conÂnecting rod assemblies of right cylinder bank.
Dl-50.
Oil
Pump Intake
and
Screen Cleaning
a.
Pry screen from housing and examine for clogÂ
ging due to deposit of sludge or other foreign
material.
b.
Clean
the screen and housing thoroughly in solÂ
vent; dry with compressed air.
c.
Install
screen in housing.
Dl-51.
Oil Pan Cleaning and Inspection
Inspect
the oil pan for corrosion, dents, leaks, and
other damage. Inspect its mounting flange carefully
for damage or distortion to be certain that it
will
give
a
good
seal.
Dl-52.
Flywheel Cleaning
and
Inspection
Clean
the flywheel with suitable cleaning solvent;
dry
with compressed air. Inspect clutch face for
burned
or scuffed condition and for rivet grooves.
Inspection
for run out or improper mounting is deÂ
scribed
in installation procedure.
Inspect
teeth
of the flywheel
ring
gear for
burrs,
nicks,
and minor distortion. If necessary and posÂ
sible, use a small emery wheel to remove
burrs
and
reshape teeth. If gear
teeth
are broken,
cracked,
seriously
burred
or deformed, the
ring
gear must be replaced.
Dl-53.
Ring Gear Replacement
a.
Drill
a
hole
between
two
ring
gear teeth; then
split
the gear with a cold chisel. Be careful not to
damage
ring
gear shoulder or seat surfaces of flyÂ
wheel.
b.
Polish several
spots
on the new
ring
gear to be
installed.
With
a hot plate or slowly moving torch,
heat the new
ring
gear until polished
spots
become
blue, about
600°F.
[312°C.].
Caution:
Do not heat the
ring
gear to a temperature
greater than
800°F.
[424°C.].
Excessive heat
will
destroy heat treatment given to
ring
gear during
manufacture.
c.
Quickly
install
ring
gear on flywheel. Chamfered
edge
of
ring
gear must be toward
ring
gear shoulder
of flywheel. Be certain that
ring
gear is seated propÂ
erly.
Allow
ring
gear to cool slowly, so that it
will
be held tightly in place.
Dl-54.
Flywheel Housing Cleaning and Inspection
Both
flywheel and clutch are enclosed by a flyÂ
wheel housing. Its front surface is bolted to the
engine
cylinder block, and its
rear
surface acts as
front
support to the transmission.
Clean
the fly wheel housing with a suitable cleaning solvent; dry
with
compressed air. Inspect front and
rear
surfaces
for distortion and improper alignment with each
other;
these
planes must be
parallel
to assure
proper
alignment
between
engine
and transmission.
Dl-55.
Camshaft Cleaning
and
Inspection
Clean
both camshaft and camshaft bearing surfaces
with
a suitable cleaning solvent; dry with comÂ
pressed air.
Note:
The steel-backed babbitt-lined camshaft
bearings are pressed into the crankcase.
From
front
to
rear,
each bearing is .030" [0,76 mm.] smaller
in
diameter than the preceding bearing.
From
front
to
rear,
each camshaft
journal
is correspondingly
smaller
in diameter.
The
camshaft bearings must be line reamed to
proper
diameter after being pressed into crankcase.
Since
this operation requires special reaming equipÂ
ment, the original bearings should be retained unÂ
less
they are severly damaged. Slightly scored camÂ
shaft bearings are satisfactory if the surfaces of camshaft journals are polished, bearings are
polished to remove
burrs,
and
radial
clearance
between
camshaft and bearings is within .0015"
to .004" [0,038 a 0,102 mm.].
Dl-56.
Valve Lifter
and
Push
Rod
Cleaning and Inspection
a.
Examine the cam contact surface at lower end of each valve lifter body. If surface is excessively
worn,
galled, or otherwise damaged, discard the
valve lifter. Also examine the mating camshaft
lobe
for excessive wear or damage.
b.
Disassemble one or two valve lifters, as deÂ
scribed
below, and inspect them for
dirt
or
varnish.
If
they are dirty or have a varnish deposit, clean
and
inspect all twelve valve lifters. Otherwise,
service
only
those
valve lifters which do not operate
properly.
c.
To disassemble each valve lifter, depress the
push
rod seat with a push rod, and remove the
plunger retainer from the valve lifter body with
a
retainer remover. Remove push rod seat and
plunger from valve lifter body. If plunger sticks
in
valve lifter body, place body in large end of
a
plunger remover tool, with plunger downward.
While
holding lifter with thumb, rap the open end
of remover against a block of wood with just enough force to jar the plunger from body. Refer to
Figs.
Dl-20, Dl-22 and Dl-23.
d.
Drain
oil from valve lifter and remove the check
valve retainer,
ball,
valve spring, and plunger
spring.
e. Keep all parts of each valve lifter separated
during
part cleaning and inspection. The valve
lifter
body and plunger are selectively fitted to each other and must not be interchanged with parts
of other valve lifters.
f. Rinse all valve lifter parts in kerosene to remove as much oil as possible.
This
will
reduce contaminaÂ
tion of the cleaning solvent. Immerse all parts in cleaning solvent for approximately one hour. The
time required
will
depend on varnish
deposits
and
effectiveness
of the solvent. After the varnish has
dissolved or has
softened
sufficiently to permit reÂ
moval
by wiping, allow parts to
drain.
Varnish
can
then be cleaned from the valve lifter body
with
a
brush.
Rinse the parts in kerosene to dissolve 90