JEEP CJ 1953 Service Manual
Manufacturer: JEEP, Model Year: 1953, Model line: CJ, Model: JEEP CJ 1953Pages: 376, PDF Size: 19.96 MB
Page 121 of 376
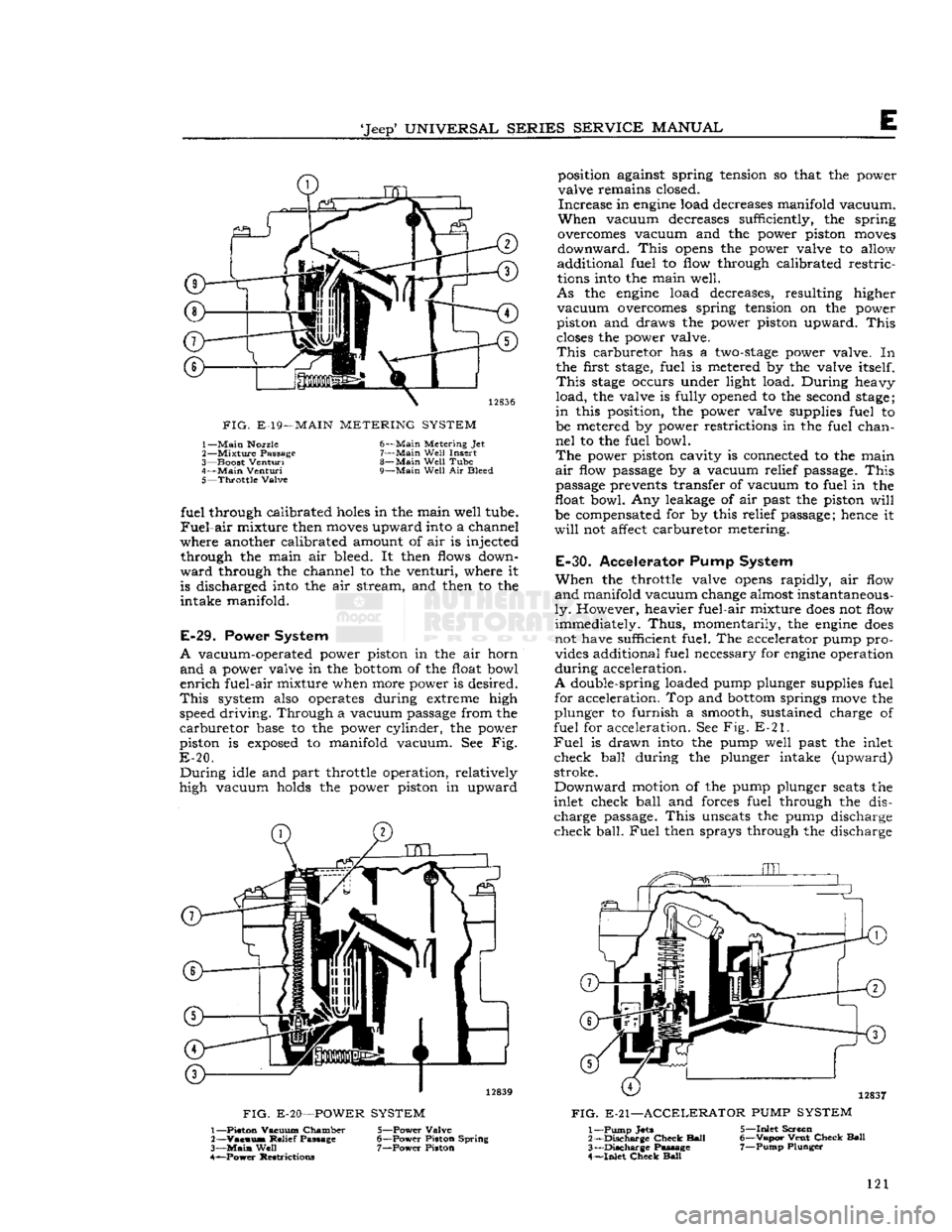
'Jeep'
UNIVERSAL SERIES SERVICE
MANUAL
FIG.
E-19—
MAIN
METERING SYSTEM
1—
Main
Nozzle
2—
Mixture
Passage
3—
Boost
Venturi
4—
Main
Venturi
5—
Throttle
Valve 6—
Main
Metering Jet
7—
Main
Well
Insert
8—
Main
Well
Tube
9—
Main
Well
Air Bleed fuel through calibrated
holes
in the main well tube.
Fuel-air
mixture then
moves
upward into a channel
where another calibrated amount of air is injected through the main air bleed. It then flows down
ward
through the channel to the venturi, where it is discharged into the air stream, and then to the
intake manifold.
E-29.
Power System
A
vacuum-operated power piston in the air horn
and
a power valve in the
bottom
of the float bowl
enrich
fuel-air mixture when more power is desired.
This
system also operates during extreme high
speed driving. Through a vacuum passage from the
carburetor
base to the power cylinder, the power
piston is
exposed
to manifold vacuum. See Fig.
E-20.
During
idle and part throttle operation, relatively
high vacuum holds the power piston in upward
FIG.
E-20—POWER
SYSTEM
position against spring tension so that the power
valve remains closed.
Increase
in
engine
load decreases manifold vacuum.
When
vacuum decreases sufficiently, the spring
overcomes vacuum and the power piston
moves
downward.
This
opens
the power valve to allow
additional fuel to flow through calibrated restric
tions into the main well.
As
the
engine
load decreases, resulting higher
vacuum
overcomes spring tension on the power
piston and draws the power piston upward.
This
closes
the power valve.
This
carburetor has a
two-stage
power valve. In
the first
stage,
fuel is metered by the valve itself.
This
stage
occurs under light load. During heavy
load,
the valve is fully opened to the second
stage;
in
this position, the power valve supplies fuel to
be metered by power restrictions in the fuel chan
nel
to the fuel bowl.
The
power piston cavity is connected to the main
air
flow passage by a vacuum relief passage.
This
passage prevents transfer of vacuum to fuel in the
float bowl. Any leakage of air past the piston
will
be compensated for by this relief passage; hence it
will
not affect carburetor metering.
E-30.
Accelerator Pump System
When
the throttle valve
opens
rapidly, air flow
and
manifold vacuum change almost instantaneous
ly.
However, heavier fuel-air mixture
does
not flow immediately.
Thus,
momentarily, the
engine
does
not have sufficient fuel. The accelerator pump pro vides additional fuel necessary for
engine
operation
during
acceleration.
A
double-spring loaded pump plunger supplies fuel for acceleration. Top and
bottom
springs
move
the
plunger to furnish a smooth, sustained charge of
fuel for acceleration. See Fig. E-21.
Fuel
is drawn into the pump well past the inlet
check ball during the plunger intake (upward)
stroke.
Downward
motion of the pump plunger
seats
the
inlet check ball and forces fuel through the dis charge
passage.
This
unseats
the pump discharge
check
ball.
Fuel
then sprays through the discharge
12837
FIG.
E-21—ACCELERATOR
PUMP
SYSTEM
1— Piston Vacuum Chamber
2—
Vacuus*
Relief Passage
3—
Main
Well
4— ^Power Restrictions 5— Power Valve
6— Power Piston Spring 7— Power Piston 1— Pump
Jets
2—
Discharge
Check
Ball
3—
Discharge
Passage
4—
Inlet
Check
Ball
5—
Inlet
Screen
6—
Vapor
Vent
Check
Ball
7—
Pump
Plunger
121
Page 122 of 376
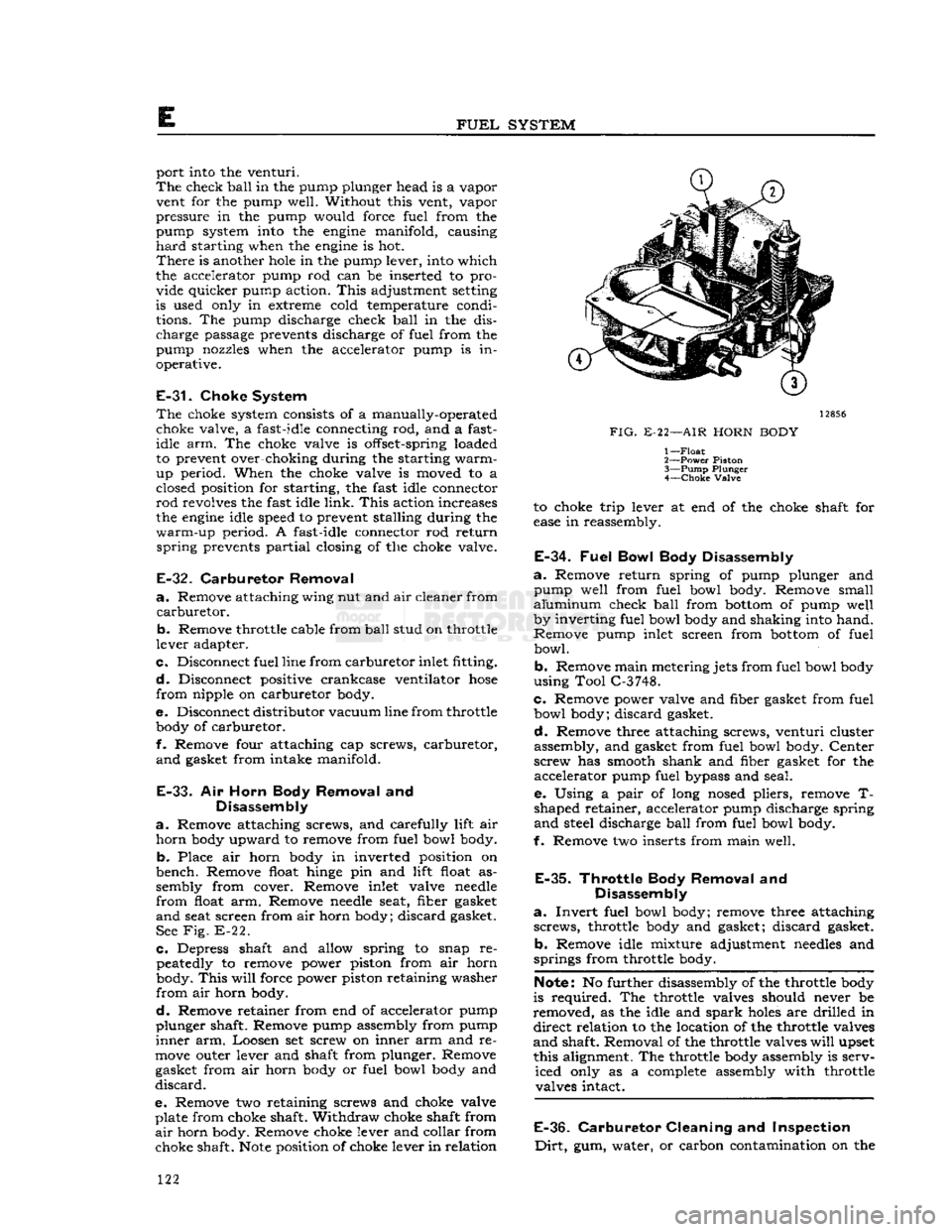
E
FUEL
SYSTEM
port into the venturi.
The
check
ball
in the pump plunger head is a vapor
vent for the pump well. Without this vent, vapor
pressure in the pump would force fuel from the
pump system into the
engine
manifold, causing
hard
starting when the
engine
is hot.
There
is another
hole
in the pump lever, into which
the accelerator pump rod can be inserted to pro vide quicker pump action.
This
adjustment setting
is used only in extreme cold temperature condi tions. The pump discharge check
ball
in the dis
charge passage prevents discharge of fuel from the
pump nozzles when the accelerator pump is in
operative.
E-31.
Choke System
The
choke system consists of a manually-operated
choke valve, a fast-idle connecting rod, and a fast-
idle arm. The choke valve is offset-spring loaded
to prevent over-choking during the starting
warm-
up period. When the choke valve is moved to a
closed position for starting, the fast idle connector
rod
revolves the fast idle
link.
This
action increases
the
engine
idle speed to prevent stalling during the
warm-up
period. A fast-idle connector rod return
spring
prevents
partial
closing of the choke valve.
E-32.
Carburetor
Removal
a.
Remove attaching wing nut and air cleaner from
carburetor.
b. Remove throttle cable from
ball
stud on throttle
lever adapter.
c.
Disconnect fuel line from carburetor inlet fitting.
d.
Disconnect positive crankcase ventilator
hose
from
nipple on carburetor body.
e. Disconnect distributor vacuum line from throttle body of carburetor.
f. Remove four attaching cap screws, carburetor,
and
gasket from intake manifold.
E-33.
Air
Horn
Body Removal and Disassembly
a.
Remove attaching screws, and carefully lift air
horn
body upward to remove from fuel bowl body.
b. Place air horn body in inverted position on
bench. Remove float hinge pin and lift float as sembly from cover. Remove inlet valve
needle
from
float arm. Remove
needle
seat, fiber gasket
and
seat screen from air horn body; discard gasket. See Fig. E-22.
c.
Depress shaft and allow spring to snap re peatedly to remove power piston from air horn body.
This
will
force power piston retaining washer
from
air horn body.
d.
Remove retainer from end of accelerator pump
plunger shaft. Remove pump assembly from pump
inner
arm. Loosen set screw on inner arm and re
move
outer lever and shaft from plunger. Remove gasket from air horn body or fuel bowl body and
discard.
e. Remove two retaining screws and choke valve plate from choke shaft. Withdraw choke shaft from
air
horn body. Remove choke lever and collar from
choke shaft.
Note
position of choke lever in relation
12856
FIG.
E-22—AIR HORN BODY
1
—
Float
2— Power Piston
3—
Pump
Plunger
4—
Choke
Valve to choke trip lever at end of the choke shaft for
ease
in reassembly.
E-34.
Fuel
Bowl Body Disassembly
a.
Remove return spring of pump plunger and pump well from fuel bowl body. Remove small
aluminum
check
ball
from
bottom
of pump well
by inverting fuel bowl body and shaking into hand. Remove pump inlet screen from
bottom
of fuel bowl.
b. Remove main metering jets from fuel bowl body
using Tool C-3748.
c.
Remove power valve and fiber gasket from fuel bowl body; discard gasket.
d.
Remove three attaching screws, venturi cluster
assembly, and gasket from fuel bowl body. Center
screw has smooth shank and fiber gasket for the accelerator pump fuel bypass and seal.
e. Using a
pair
of long nosed pliers, remove T-
shaped retainer, accelerator pump discharge spring
and
steel discharge
ball
from fuel bowl body.
f. Remove two inserts from main well.
E-35.
Throttle Body Removal and Disassembly
a.
Invert
fuel bowl body; remove three attaching
screws,
throttle body and gasket; discard gasket.
b. Remove idle mixture adjustment
needles
and
springs from throttle body.
Note:
No further disassembly of the throttle body
is required. The throttle valves should never be
removed, as the idle and
spark
holes
are drilled in
direct
relation to the location of the throttle valves
and
shaft. Removal of the throttle valves
will
upset
this alignment. The throttle body assembly is serv iced only as a complete assembly with throttle valves intact.
E-36.
Carburetor
Cleaning and Inspection
Dirt,
gum, water, or carbon contamination on the 122
Page 123 of 376
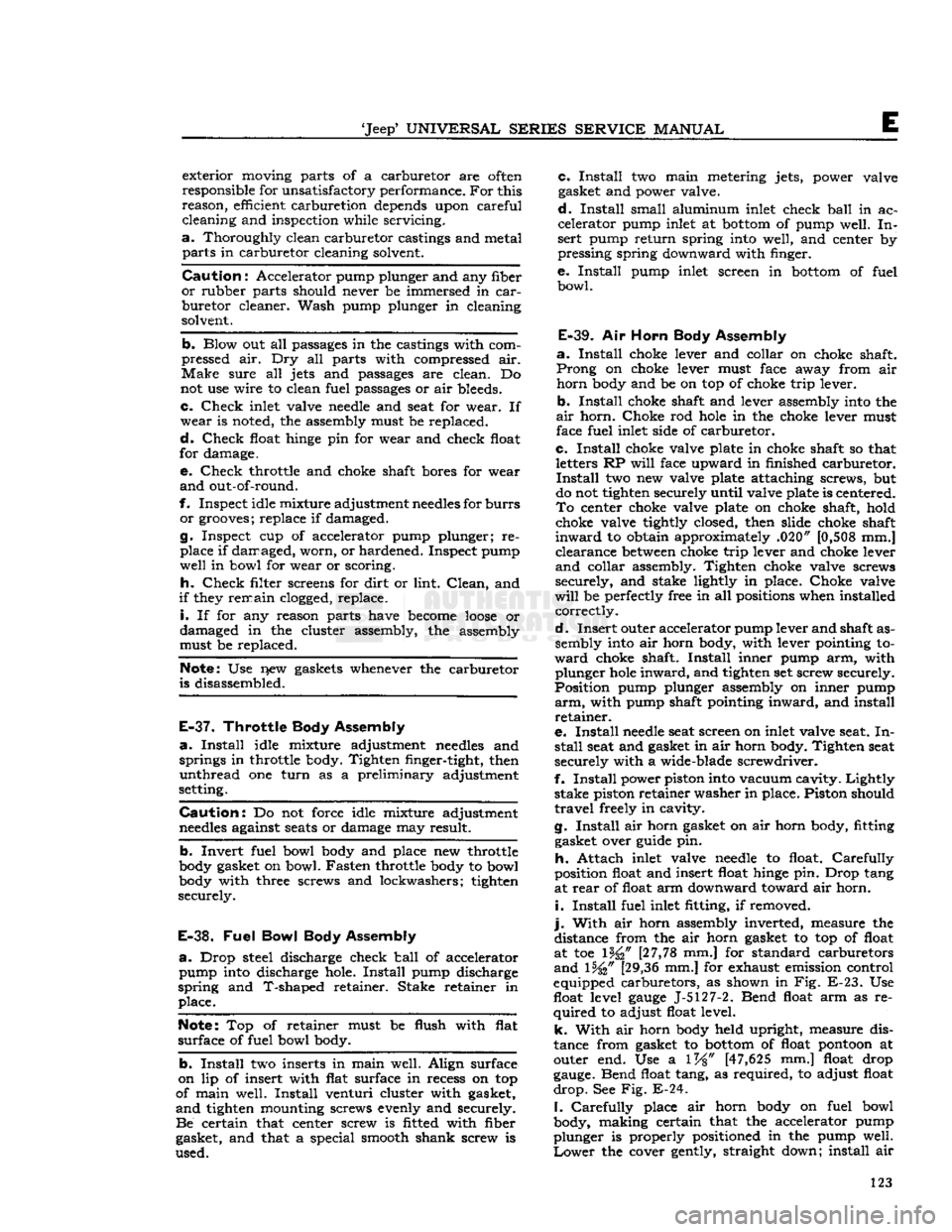
'Jeep9
UNIVERSAL
SERIES
SERVICE
MANUAL
E
exterior moving parts of a carburetor are
often
responsible for unsatisfactory performance.
For
this
reason,
efficient carburetion depends upon careful cleaning and inspection while servicing.
a.
Thoroughly clean carburetor castings and metal
parts
in carburetor cleaning solvent.
Caution:
Accelerator pump plunger and any fiber
or
rubber parts should never be immersed in
car
buretor
cleaner. Wash pump plunger in cleaning
solvent.
b.
Blow out all passages in the castings with com
pressed air. Dry all parts with compressed air.
Make
sure all jets and passages are clean. Do
not use wire to clean fuel passages or air bleeds.
c.
Check
inlet valve
needle
and seat for wear. If
wear
is noted, the assembly must be replaced.
d.
Check
float hinge pin for wear and check float
for damage.
e.
Check
throttle and choke shaft bores for wear
and
out-of-round.
f. Inspect idle mixture adjustment
needles
for
burrs
or
grooves; replace if damaged.
g. Inspect cup of accelerator pump plunger; re
place if damaged, worn, or hardened. Inspect pump
well
in bowl for wear or scoring.
h.
Check
filter screens for
dirt
or lint.
Clean,
and
if
they remain
clogged,
replace.
i.
If for any reason parts have
become
loose
or
damaged in the cluster assembly, the assembly
must be replaced.
Note:
Use ijew gaskets whenever the carburetor
is disassembled.
E-37.
Throttle Body Assembly
a.
Install
idle mixture adjustment
needles
and
springs in throttle body. Tighten finger-tight, then
unthread
one
turn
as a preliminary adjustment
setting.
Caution:
Do not force idle mixture adjustment
needles
against
seats
or damage may result.
b.
Invert
fuel bowl body and place new throttle
body gasket on bowl. Fasten throttle body to bowl
body with three screws and lockwashers; tighten
securely.
E-38.
Fuel
Bowl Body Assembly
a.
Drop steel discharge check
tall
of accelerator
pump into discharge hole.
Install
pump discharge
spring
and T-shaped retainer. Stake retainer in
place.
Note:
Top of retainer must be flush with flat
surface
of fuel bowl body.
b.
Install
two inserts in main well. Align surface
on lip of insert with flat surface in recess on top
of main well.
Install
venturi cluster with gasket,
and
tighten mounting screws evenly and securely.
Be
certain that center screw is fitted with fiber gasket, and that a special smooth shank screw is
used.
c.
Install
two main metering jets, power valve
gasket and power valve.
d.
Install
small aluminum inlet check
ball
in ac
celerator
pump inlet at
bottom
of pump well. In
sert
pump return spring into well, and center by
pressing spring downward with finger.
e.
Install
pump inlet screen in
bottom
of fuel
bowl.
E-39.
Air
Horn Body
Assembly
a.
Install
choke lever and collar on choke shaft.
Prong
on choke lever must face away from air
horn
body and be on top of choke trip lever.
b.
Install
choke shaft and lever assembly into the
air
horn. Choke rod
hole
in the choke lever must
face fuel inlet side of carburetor.
c.
Install
choke valve plate in choke shaft so that
letters RP
will
face upward in finished carburetor.
Install
two new valve plate attaching screws, but
do not tighten securely until valve plate is centered.
To
center choke valve plate on choke shaft, hold
choke valve tightly closed, then slide choke shaft
inward
to obtain approximately .020" [0,508 mm.]
clearance
between
choke trip lever and choke lever
and
collar assembly. Tighten choke valve screws
securely,
and stake lightly in place. Choke valve
will
be perfectly free in all positions when installed
correctly.
d.
Insert
outer accelerator pump lever and shaft as sembly into air horn body, with lever pointing to
ward
choke shaft.
Install
inner pump arm, with plunger
hole
inward,
and tighten set screw securely.
Position pump plunger assembly on inner pump
arm,
with pump shaft pointing
inward,
and install
retainer.
e.
Install
needle
seat screen on inlet valve seat. In
stall
seat and gasket in air horn body. Tighten seat
securely with a wide-blade screwdriver.
f.
Install
power piston into vacuum cavity.
Lightly
stake piston retainer washer in place. Piston should
travel
freely in cavity.
g.
Install
air horn gasket on air horn body, fitting
gasket over guide pin.
h.
Attach inlet valve
needle
to float.
Carefully
position float and insert float hinge pin. Drop tang
at
rear
of float arm downward toward air horn.
i.
Install
fuel inlet fitting, if removed.
j.
With
air horn assembly inverted, measure the distance from the air horn gasket to top of float
at toe \%£f [27,78 mm.] for standard carburetors
and
\%i [29,36 mm.] for exhaust emission control
equipped carburetors, as shown in Fig. E-23. Use
float level
gauge
J-5127-2. Bend float arm as re
quired
to adjust float level.
k.
With
air horn body held upright, measure dis
tance from gasket to
bottom
of float
pontoon
at outer end. Use a l7/s" [47,625 mm.] float drop
gauge.
Bend float tang, as required, to adjust float
drop.
See Fig. E-24.
I.
Carefully
place air horn body on fuel bowl
body, making certain that the accelerator pump
plunger is properly positioned in the pump well.
Lower
the cover gently, straight down; install air 123
Page 124 of 376
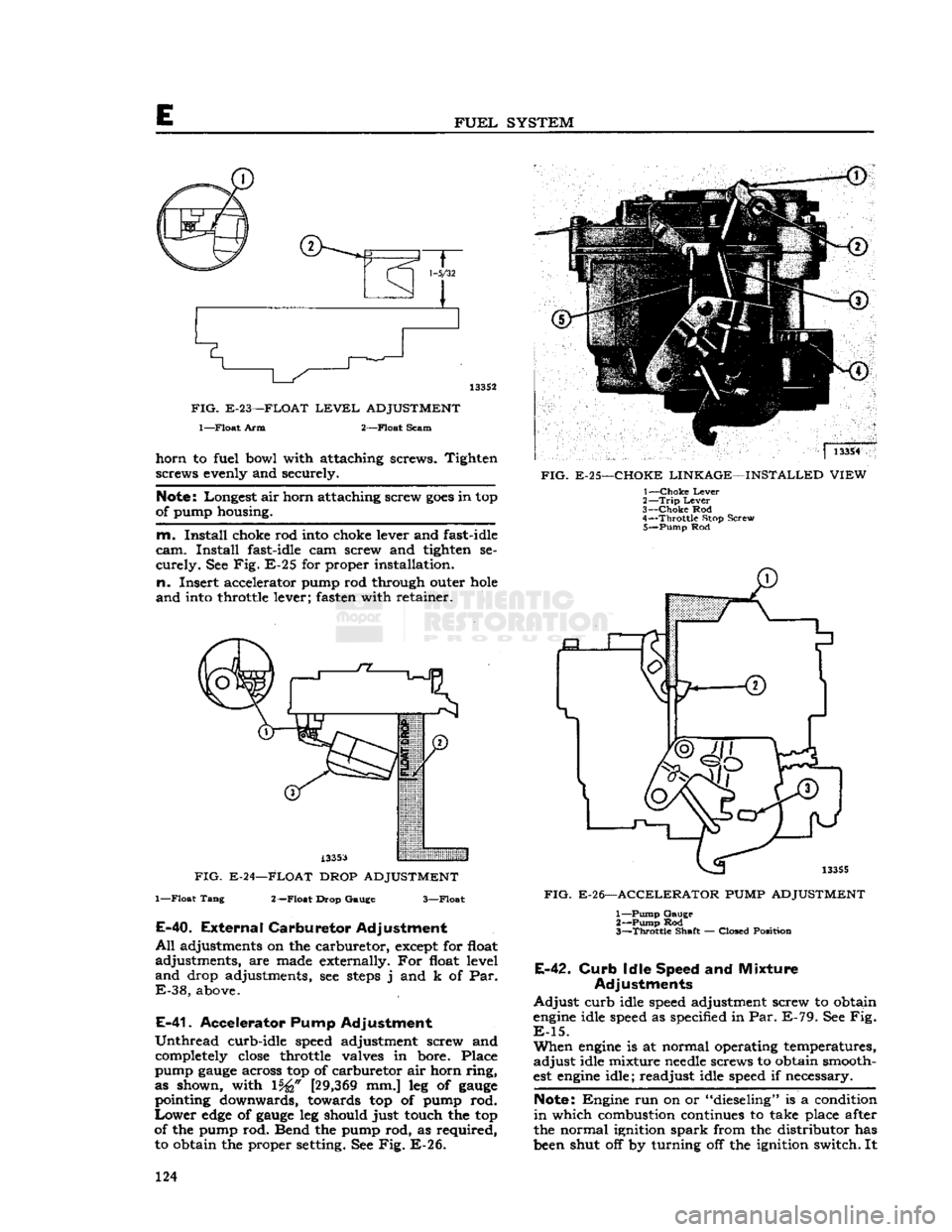
FUEL
SYSTEM
1-5/32
133S2
FIG.
E-23—FLOAT
LEVEL
ADJUSTMENT
l—Float
Arm 2—Float Scam
horn
to fuel bowl with attaching screws. Tighten screws evenly and securely.
Note:
Longest air horn attaching screw
goes
in top
of pump housing.
m.
Install
choke rod into choke lever and fast-idle
cam.
Install
fast-idle cam screw and tighten se
curely.
See Fig. E-25 for proper installation,
n.
Insert accelerator pump rod through outer
hole
and
into throttle lever; fasten with retainer.
A33S3
FIG. E-24—FLOAT DROP ADJUSTMENT
1—Float Tang 2—Float Drop Gauge 3—Float
E-40.
External
Carburetor
Adjustment
All
adjustments on the carburetor, except for float
adjustments, are made externally. For float level
and
drop adjustments, see
steps
j and k of Par.
E-38,
above.
E-41.
Accelerator Pump Adjustment
Unthread
curb-idle speed adjustment screw and completely
close
throttle valves in bore. Place
pump
gauge
across top of carburetor air horn ring,
as shown, with 15^" [29,369 mm.] leg of
gauge
pointing downwards, towards top of pump rod.
Lower
edge
of
gauge
leg should just touch the top
of the pump rod. Bend the pump rod, as required, to obtain the proper setting. See Fig. E-26. ]
13354
FIG.
E-25—CHOKE LINKAGE—INSTALLED VIEW 1—
Choke
Lever
2—
Trip
Lever
3—
Choke
Rod
4—
Throttle
Stop Screw 5—
Pump
Rod
13355
FIG.
E-26—ACCELERATOR
PUMP
ADJUSTMENT 1—
Pump
Gauge 2—
Pump
Rod
3—
Throttle
Shaft — Closed Position
E-42.
Curb
Idle Speed and Mixture
Adjustments
Adjust
curb idle speed adjustment screw to obtain
engine
idle speed as specified in Par. E-79. See Fig.
E-15.
When
engine
is at normal operating temperatures,
adjust
idle mixture
needle
screws to obtain smooth
est
engine
idle; readjust idle speed if necessary.
Note:
Engine run on or "dieseling" is a condition
in
which combustion continues to take place after
the normal ignition spark from the distributor has
been shut off by turning off the ignition switch. It 124
Page 125 of 376
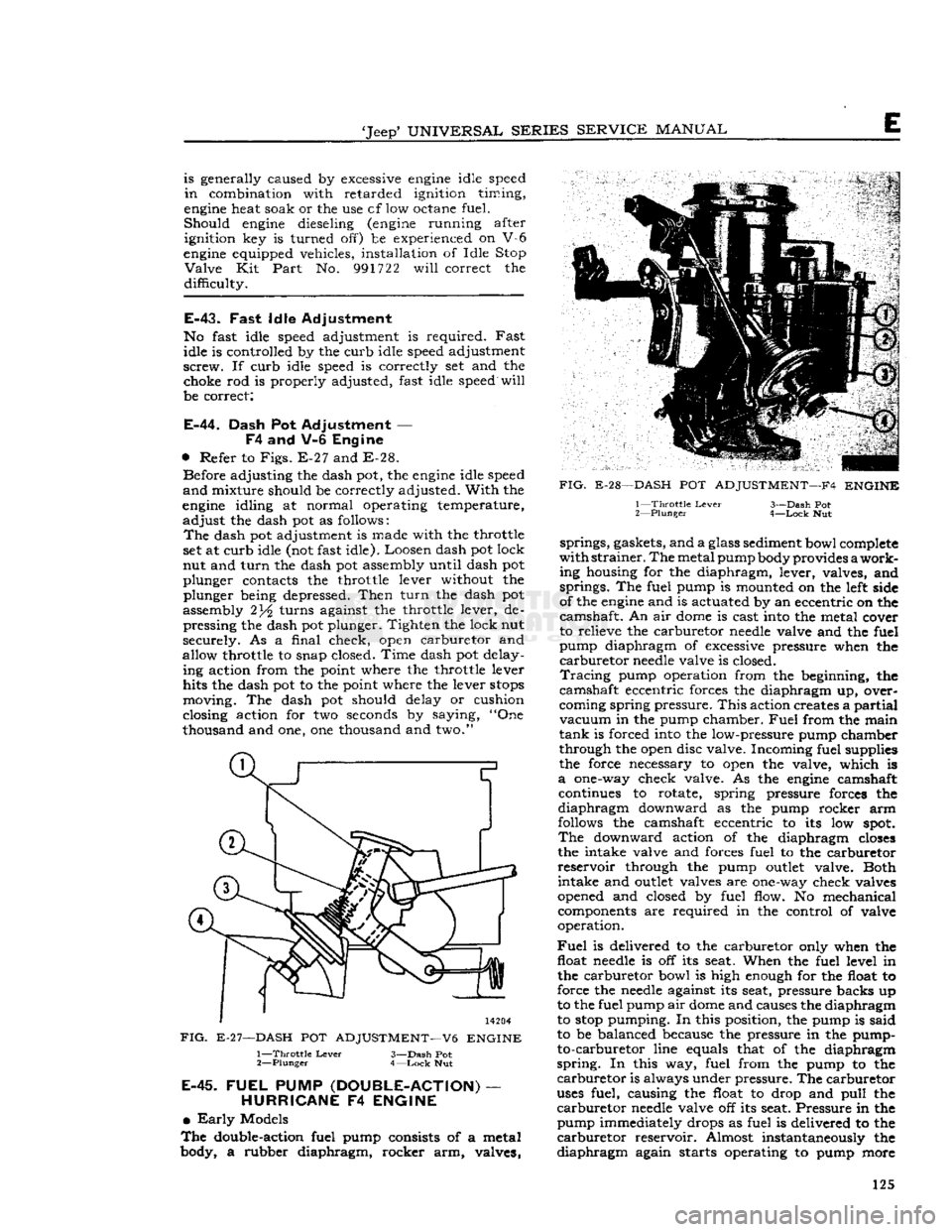
'Jeep'
UNIVERSAL
SERIES
SERVICE
MANUAL
E
is generally caused by excessive
engine
idle speed
in
combination with retarded ignition timing,
engine
heat soak or the use cf low octane fuel.
Should
engine
dieseling
(engine
running after ignition key is turned off) be experienced on V-6
engine
equipped vehicles, installation of Idle Stop
Valve
Kit
Part
No.
991722
will
correct the
difficulty.
E-43.
Fast
Idle Adjustment
No fast idle speed adjustment is required.
Fast
idle is controlled by the curb idle speed adjustment
screw.
If curb idle speed is correctly set and the choke rod is properly adjusted, fast idle speed
will
be correct;
E-44.
Dash Pot Adjustment —
F4
and V-6 Engine
•
Refer to
Figs.
E-27 and E-28. Before adjusting the dash pot, the
engine
idle speed
and
mixture should be correctly adjusted.
With
the
engine
idling at normal operating temperature,
adjust
the dash pot as follows:
The
dash pot adjustment is made with the throttle
set at curb idle (not fast idle). Loosen dash pot lock
nut and
turn
the dash pot assembly until dash pot
plunger contacts the throttle lever without the plunger being depressed.
Then
turn
the dash pot
assembly 2turns against the throttle lever, de pressing the dash pot plunger. Tighten the lock nut
securely. As a final check, open carburetor and
allow throttle to snap closed. Time dash pot delay ing action from the point where the throttle lever
hits the dash pot to the point where the lever
stops
moving. The dash pot should delay or cushion
closing action for two seconds by saying, "One
thousand and one, one thousand and two."
14204
FIG.
E-27—DASH
POT
ADJUSTMENT—V6
ENGINE
1—
Throttle
Lever
3—Dash Pot
2—
Plunger
4—Lock
Nut
E-45.
FUEL
PUMP
(DOUBLE-ACTION)
—
HURRICANE
F4
ENGINE
•
Early
Models
The
double-action fuel pump consists of a metal
body, a rubber diaphragm, rocker arm, valves,
FIG.
E-28—DASH
POT
ADJUSTMENT—F4
ENGINE
1—
Throttle
Lever
3—Dash Pot
2—
Plunger
4—Lock
Nut springs, gaskets, and a glass sediment bowl complete
with
strainer.
The
metal pump body provides
a
work
ing housing for the diaphragm, lever, valves, and springs. The fuel pump is mounted on the left side
of the
engine
and is actuated by an eccentric on the
camshaft. An air
dome
is cast into the metal cover
to relieve the carburetor
needle
valve and the fuel
pump diaphragm of excessive pressure when the
carburetor
needle
valve is closed.
Tracing
pump operation from the beginning, the
camshaft eccentric forces the diaphragm up, over
coming spring pressure.
This
action creates a
partial
vacuum
in the pump chamber.
Fuel
from the main
tank
is forced into the low-pressure pump chamber
through the open disc valve. Incoming fuel supplies
the force necessary to open the valve, which is
a
one-way check valve. As the
engine
camshaft continues to rotate, spring pressure forces the
diaphragm
downward as the pump rocker arm
follows the camshaft eccentric to its low
spot.
The
downward action of the diaphragm
closes
the intake valve and forces fuel to the carburetor
reservoir
through the pump
outlet
valve. Both intake and
outlet
valves are one-way check valves
opened and closed by fuel flow. No mechanical components are required in the control of valve
operation.
Fuel
is delivered to the carburetor only when the float
needle
is off its seat. When the fuel level in the carburetor bowl is high enough for the float to
force the
needle
against its seat, pressure backs up
to the fuel pump air
dome
and causes the diaphragm
to
stop
pumping. In this position, the pump is said
to be balanced because the pressure in the pump- to-carburetor line equals that of the diaphragm
spring.
In this way, fuel from the pump to the
carburetor
is always under pressure. The carburetor
uses
fuel, causing the float to drop and
pull
the
carburetor
needle
valve off its seat. Pressure in the pump immediately drops as fuel is delivered to the
carburetor
reservoir. Almost instantaneously the
diaphragm
again starts operating to pump more 125
Page 126 of 376
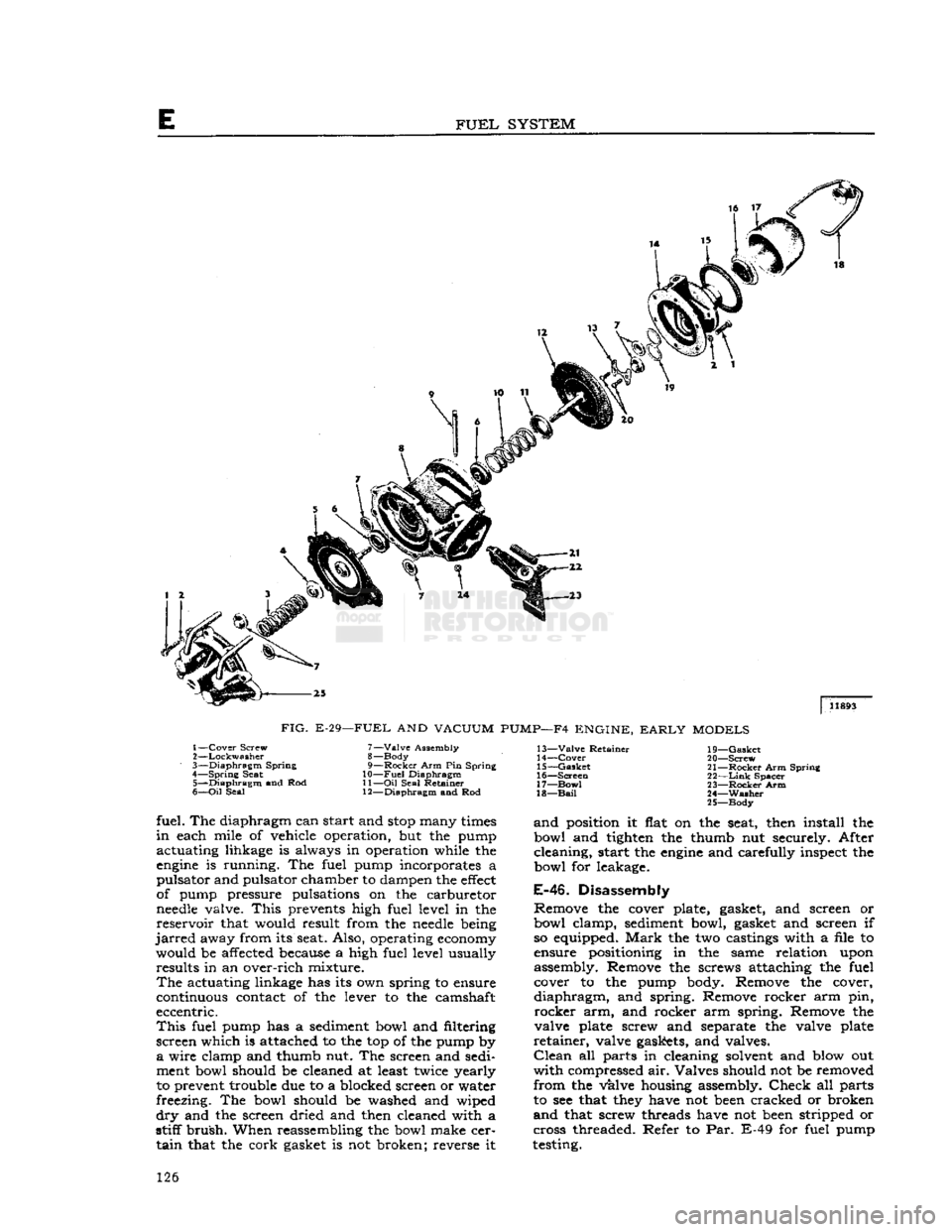
FUEL
SYSTEM
|
11893
FIG.
E-29—FUEL
AND
VACUUM
PUMP—F4
ENGINE,
EARLY
MODELS
1—
Cover
Screw
2—
Lockwasher
3—
Diaphragm
Spring
4—
Spring
Seat 5—
Diaphragm
and Rod
6—
Oil
Seal 7—
Valve
Assembly
8— Body
9—
Rocker
Arm Pin Spring
10—
Fuel
Diaphragm
11—
Oil
Seal Retainer
12—
Diaphragm
and Rod 13—
Valve
Retainer
14—
Cover
15—
Gasket
16—
Screen
17—
Bow!
18—
Bail
19—
Gasket
20—
Screw
21—
Rocker
Arm Spring
22—
Link
Spacer
23—
Rocker
Arm
24—
Washer
25—
Body
fuel. The diaphragm can start and
stop
many
times
in
each mile of vehicle operation, but the pump
actuating lihkage is always in operation while the
engine
is running. The fuel pump incorporates a
pulsator and pulsator chamber to dampen the
effect
of pump pressure pulsations on the carburetor
needle
valve.
This
prevents high fuel level in the
reservoir
that would result from the
needle
being
jarred
away from its seat. Also, operating
economy
would be affected because a high fuel level usually results in an over-rich mixture.
The
actuating linkage has its own spring to ensure
continuous contact of the lever to the camshaft
eccentric.
This
fuel pump has a sediment bowl and filtering
screen which is attached to the top of the pump by
a
wire clamp and thumb nut. The screen and sedi
ment bowl should be cleaned at least twice yearly
to prevent trouble due to a blocked screen or water
freezing. The bowl should be washed and wiped
dry
and the screen dried and then cleaned with a
stiff
brush.
When reassembling the bowl make cer
tain
that the cork gasket is not broken; reverse it
and
position it flat on the seat, then install the
bowl and tighten the thumb nut securely. After
cleaning, start the
engine
and carefully inspect the
bowl for leakage.
E-46.
Disassembly
Remove the cover plate, gasket, and screen or
bowl clamp, sediment bowl, gasket and screen if so equipped.
Mark
the two castings with a file to
ensure positioning in the same relation upon
assembly. Remove the screws attaching the fuel cover to the pump body. Remove the cover,
diaphragm,
and spring. Remove rocker arm pin,
rocker
arm, and rocker arm spring. Remove the
valve plate screw and separate the valve plate
retainer,
valve gaskets, and valves.
Clean
all parts in cleaning solvent and blow out
with
compressed air. Valves should not be removed
from
the valve housing assembly.
Check
all parts
to see that
they
have not
been
cracked or broken
and
that screw threads have not
been
stripped or
cross threaded. Refer to Par. E-49 for fuel pump
testing. 126
Page 127 of 376
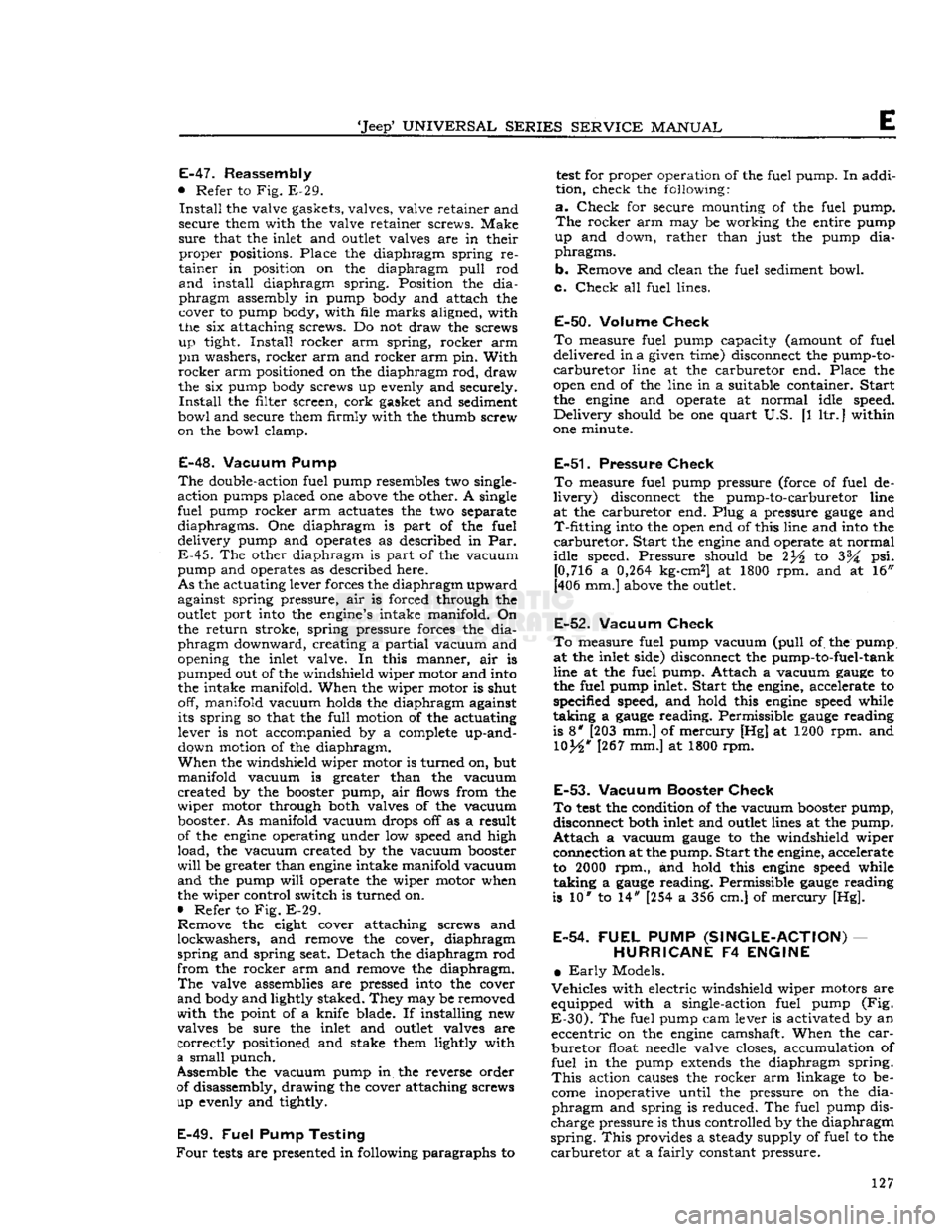
'Jeep'
UNIVERSAL
SERIES
SERVICE
MANUAL
E
E-47.
Reassembly
•
Refer to Fig. E-29.
Install
the valve gaskets, valves, valve retainer and
secure them with the valve retainer screws. Make
sure that the inlet and
outlet
valves are in their proper positions. Place the diaphragm spring re
tainer in position on the diaphragm
pull
rod
and
install diaphragm spring. Position the
dia
phragm assembly in pump
body
and attach the
cover to pump body, with file marks aligned, with
the six attaching screws. Do not draw the screws
up tight.
Install
rocker arm spring, rocker arm
pin
washers, rocker arm and rocker arm pin.
With
rocker
arm positioned on the diaphragm rod, draw
the six pump
body
screws up evenly and securely.
Install
the filter screen, cork gasket and sediment
bowl and secure them firmly with the thumb screw
on the bowl clamp.
E-48.
Vacuum
Pump
The
double-action fuel pump resembles two single-
action pumps placed one
above
the other. A single
fuel pump rocker arm actuates the two separate diaphragms. One diaphragm is part of the fuel
delivery pump and operates as described in Par.
E-45.
The other diaphragm is part of the vacuum
pump and operates as described here.
As
the actuating lever forces the diaphragm upward against spring pressure, air is forced through the
outlet
port
into
the
engine's
intake manifold. On
the return stroke, spring pressure forces the
dia
phragm downward, creating a
partial
vacuum and
opening the inlet valve. In this manner, air is pumped out of the windshield wiper motor and
into
the intake manifold. When the wiper motor is shut off, manifold vacuum holds the diaphragm against its spring so that the
full
motion of the actuating
lever is not accompanied by a
complete
up-and-
down motion of the diaphragm.
When
the windshield wiper motor is turned on, but manifold vacuum is greater than the vacuum
created by the
booster
pump, air
flows
from the
wiper motor through both valves of the vacuum
booster.
As manifold vacuum drops off as a result
of the
engine
operating under low
speed
and high load, the vacuum created by the vacuum
booster
will
be greater than
engine
intake manifold vacuum
and
the pump
will
operate the wiper motor when the wiper control switch is turned on.
•
Refer to Fig. E-29. Remove the
eight
cover attaching screws and
lockwashers, and remove the cover, diaphragm
spring
and spring seat. Detach the diaphragm rod
from the rocker arm and remove the diaphragm.
The
valve assemblies are pressed
into
the cover
and
body
and lightly staked. They may be removed
with the point of a knife blade. If installing new valves be sure the inlet and
outlet
valves are
correctly positioned and stake them lightly with
a
small punch.
Assemble the vacuum pump in the reverse order
of disassembly, drawing the cover attaching screws up evenly and tightly.
E-49.
Fuel
Pump
Testing
Four
tests
are presented in following paragraphs to
test
for proper operation of the fuel pump. In addi
tion, check the following:
a.
Check
for secure mounting of the fuel pump.
The
rocker arm may be working the entire pump
up and down, rather than just the pump
dia
phragms.
b. Remove and clean the fuel sediment bowl.
c.
Check
all fuel lines.
E-50.
Volume
Check
To
measure fuel pump capacity (amount of fuel
delivered in a given time) disconnect the pump-to-
carburetor
line at the carburetor end. Place the
open
end of the line in a suitable container.
Start
the
engine
and operate at normal idle speed.
Delivery
should be one quart U.S. [1 ltr.] within
one minute.
E-51.
Pressure
Check
To
measure fuel pump pressure (force of fuel de
livery)
disconnect the pump-to-carburetor line
at the carburetor end. Plug a pressure
gauge
and T-fitting
into
the
open
end of this line and
into
the
carburetor.
Start
the
engine
and operate at normal
idle speed. Pressure should be 2J4 to 3% psi.
[0,716
a
0,264
kg-cm2] at 1800 rpm. and at 16"
[406 mm.]
above
the
outlet.
E-52.
Vacuum
Check
To
measure fuel pump vacuum (pull of. the pump
at the inlet side) disconnect the pump-to-fuel-tank
line at the fuel pump. Attach a vacuum
gauge
to the fuel pump inlet.
Start
the
engine,
accelerate to
specified speed, and hold this
engine
speed
while
taking a
gauge
reading. Permissible
gauge
reading
is 8* [203 mm.] of mercury [Hg] at 1200 rpm. and
10j^'
[267 mm.] at 1800 rpm.
E-53.
Vacuum
Booster
Check
To
test
the condition of the vacuum
booster
pump,
disconnect both inlet and
outlet
lines at the pump.
Attach
a vacuum
gauge
to the windshield wiper
connection at the pump.
Start
the
engine,
accelerate
to
2000
rpm., and hold this
engine
speed
while taking a
gauge
reading. Permissible
gauge
reading
is 10* to 14" [254 a 356 cm.] of mercury [Hg].
E-54.'
FUEL
PUMP
(SINGLE-ACTION)
—
HURRICANE
F4
ENGINE
•
Early
Models.
Vehicles with electric windshield wiper motors are
equipped with a single-action fuel pump (Fig.
E-30).
The fuel pump cam lever is activated by an eccentric on the
engine
camshaft. When the
car
buretor float
needle
valve closes, accumulation of
fuel in the pump
extends
the diaphragm spring.
This
action causes the rocker arm linkage to be
come
inoperative until the pressure on the
dia
phragm and spring is reduced. The fuel pump dis
charge pressure is thus controlled by the diaphragm
spring.
This
provides a steady supply of fuel to the
carburetor
at a fairly constant pressure. 127
Page 128 of 376
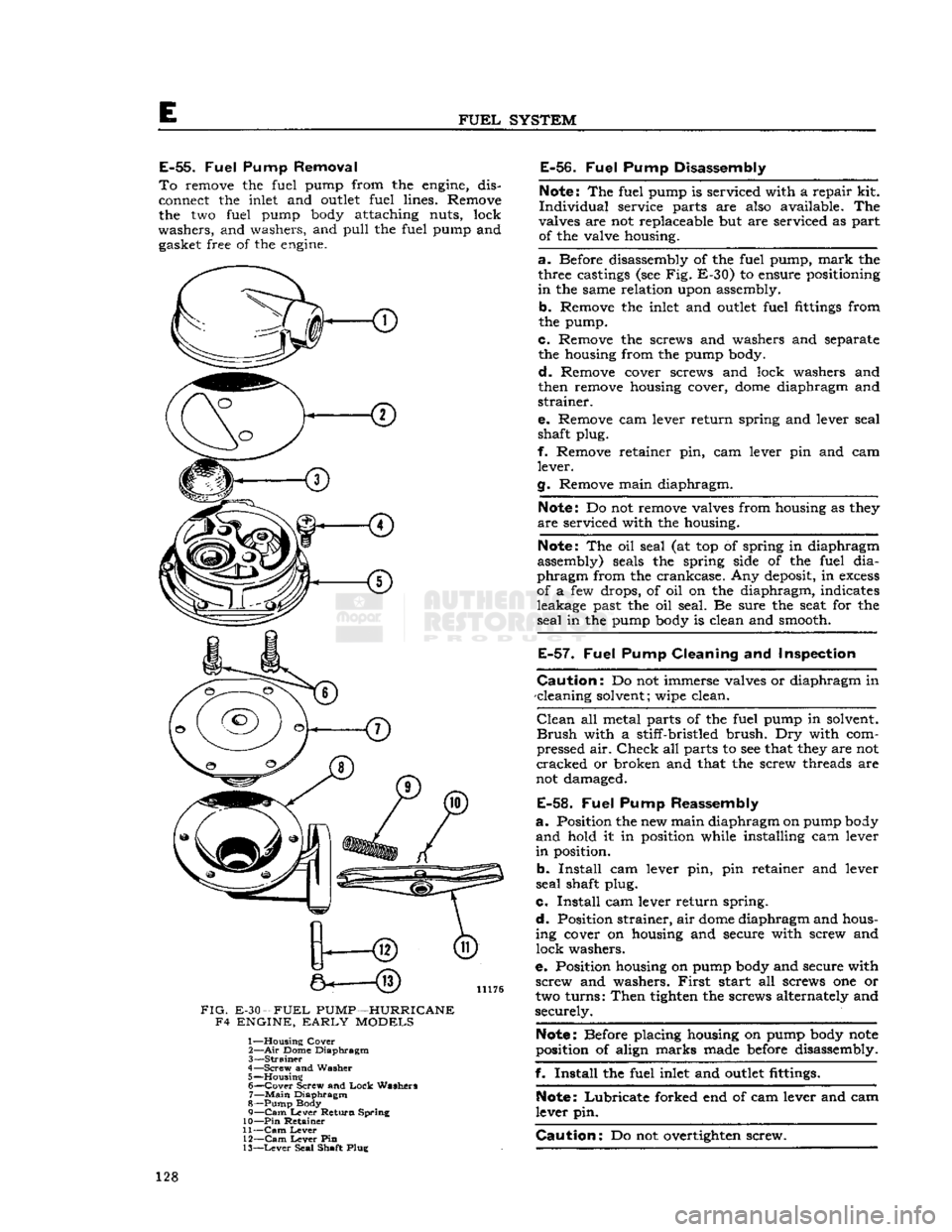
E
FUEL
SYSTEM
E-55.
Fuel
Pump
Removal
To
remove the fuel pump from the engine, dis
connect the inlet and
outlet
fuel lines. Remove the two fuel pump body attaching nuts, lock
washers,
and washers, and pull the fuel pump and gasket free of the engine.
FIG.
E-30
—
FUEL
PUMP—HURRICANE
F4 ENGINE,
EARLY
MODELS
1—
Housing
Cover
2— Air
Dome
Diaphragm
3—
Strainer
4—
Screw
and
Washer
5—
Housing
6—
Cover
Screw
and
Lock
Washers
7—
Main
Diaphragm
8—
Pump
Body
9— Cam
Lever
Return
Spring
10— Pin
Retainer
11— Cam
Lever
12— Cam
Lever
Pin
13—
Lever
Seal
Shaft
Plug
E-56.
Fuel
Pump
Disassembly
Note:
The fuel pump is serviced with a repair kit.
Individual
service parts are also available. The
valves are not replaceable but are serviced as part of the valve housing.
a.
Before disassembly of the fuel pump,
mark
the
three castings (see Fig. E-30) to ensure positioning
in
the same relation upon assembly. b. Remove the inlet and
outlet
fuel fittings from
the pump.
c. Remove the screws and washers and separate the housing from the pump body.
d.
Remove cover screws and lock washers and
then remove housing cover,
dome
diaphragm and
strainer.
e.
Remove cam lever return spring and lever seal
shaft plug.
f. Remove retainer pin, cam lever pin and cam
lever.
g. Remove main diaphragm.
Note:
Do not remove valves from housing as they
are
serviced with the housing.
Note:
The oil seal (at top of spring in diaphragm
assembly) seals the spring side of the fuel
dia
phragm
from the crankcase. Any deposit, in
excess
of a few drops, of oil on the diaphragm, indicates
leakage past the oil seal. Be sure the seat for the
seal
in the pump body is clean and smooth.
E-57.
Fuel
Pump
Cleaning
and
Inspection
Caution:
Do not immerse valves or diaphragm in
-cleaning solvent; wipe clean.
Clean
all metal parts of the fuel pump in solvent.
Brush
with a stiff-bristled brush. Dry with com
pressed air.
Check
all parts to see that they are not
cracked
or broken and that the screw threads are
not damaged.
E-58.
Fuel
Pump
Reassembly
a.
Position the new main diaphragm on pump body
and
hold it in position while installing cam lever
in
position.
b.
Install
cam lever pin, pin retainer and lever
seal
shaft plug.
c.
Install
cam lever return spring.
d.
Position strainer, air
dome
diaphragm and hous
ing cover on housing and secure with screw and
lock
washers.
e.
Position housing on pump body and secure with screw and washers.
First
start all screws one or
two turns:
Then
tighten the screws alternately and
securely.
Note:
Before placing housing on pump body
note
position of align marks made before disassembly.
f.
Install
the fuel inlet and
outlet
fittings.
Note:
Lubricate
forked end of cam lever and cam
lever pin.
Caution:
Do not overtighten screw. 128
Page 129 of 376
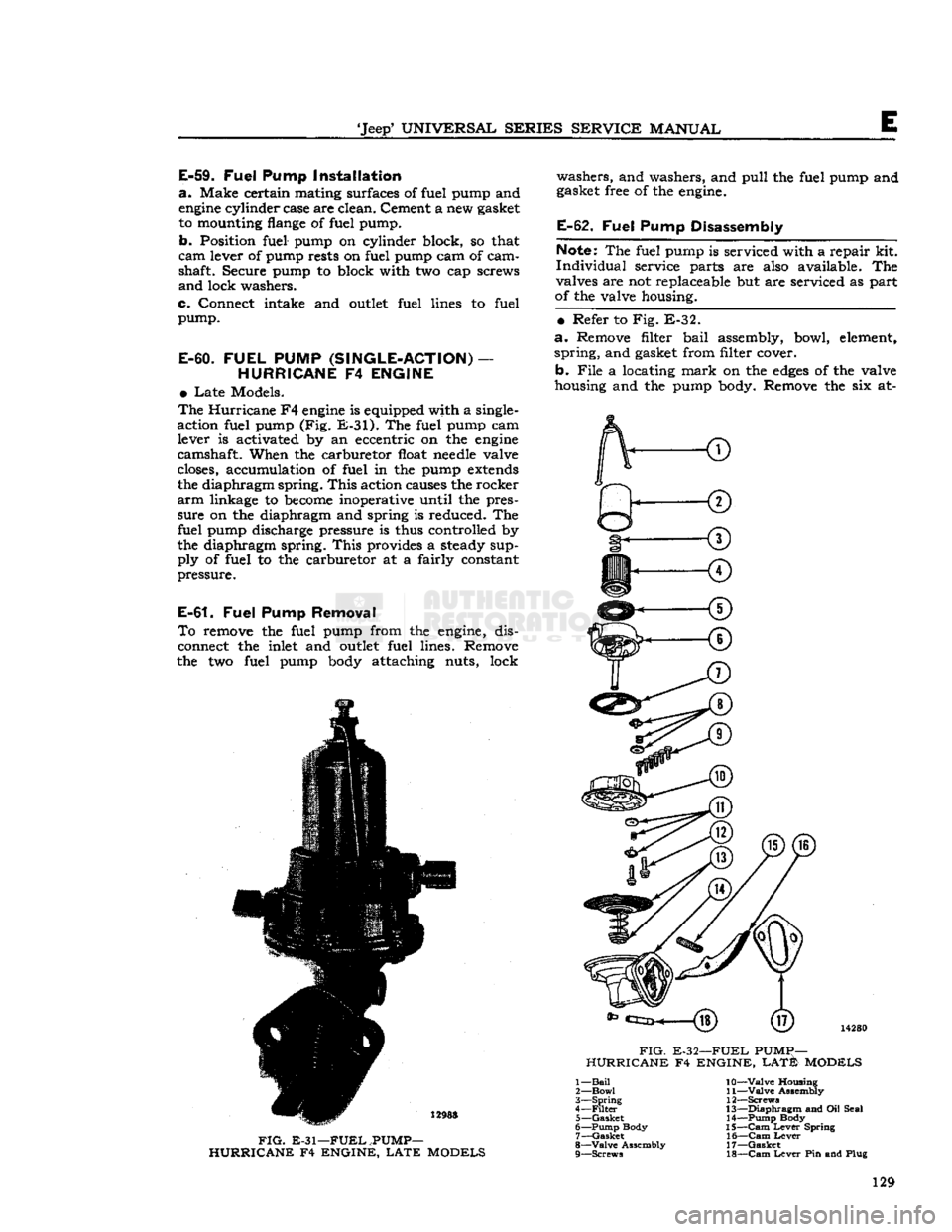
'Jeep9
UNIVERSAL
SERIES
SERVICE
MANUAL
E-59.
Fuel
Pump Installation
a.
Make certain mating surfaces of fuel pump and
engine
cylinder case are clean. Cement a new gasket
to mounting
flange
of fuel pump.
b. Position fuel pump on cylinder block, so that
cam
lever of pump rests on fuel pump cam of cam
shaft. Secure pump to block with two cap screws
and
lock washers.
c. Connect intake and
outlet
fuel lines to fuel
pump.
E-60.
FUEL
PUMP
(SINGLE-ACTION)
—
HURRICANE
F4
ENGINE
•
Late
Models.
The
Hurricane F4
engine
is equipped with a single-
action fuel pump (Fig.
E-31).
The fuel pump cam lever is activated by an eccentric on the
engine
camshaft. When the carburetor float
needle
valve
closes, accumulation of fuel in the pump
extends
the diaphragm spring.
This
action causes the rocker
arm
linkage to
become
inoperative until the pres
sure on the diaphragm and spring is reduced. The fuel pump discharge pressure is thus controlled by
the diaphragm spring.
This
provides a steady sup ply of fuel to the carburetor at a fairly constant
pressure.
E-61.
Fuel
Pump Removal
To
remove the fuel pump from the
engine,
dis
connect the inlet and
outlet
fuel lines. Remove
the two fuel pump
body
attaching nuts, lock washers, and washers, and pull the fuel pump and
gasket free of the
engine.
E-62.
Fuel
Pump Disassembly
Note:
The fuel pump is serviced with a repair kit.
Individual
service parts are also available. The
valves are not replaceable but are serviced as part
of the valve housing.
•
Refer to Fig. E-32.
a.
Remove filter bail assembly, bowl,
element,
spring,
and gasket from filter cover. b.
File
a locating
mark
on the
edges
of the valve
housing and the pump body. Remove the six at-
14280
FIG.
E-32—FUEL
PUMp—
HURRICANE F4 ENGINE,
LATE
MODELS
12988
FIG.
E-31—FUEL
.PUMP-
HURRICANE F4 ENGINE,
LATE
MODELS 1—
Bail
2—
Bowl
3—
Spring
4—
Filter
5—
Gasket
6— Pump Body 7—
Gasket
8—
Valve
Assembly 9— Screws 10—
Valve
Housing
11—
Valve
Assembly
12— Screws
13—
Diaphragm
and Oil Seal 14— Pump Body
15—
Cam
Lever
Spring 16—
Cam
Lever
17—
Gasket
18—
Cam
Lever
Pin and Plug 129
Page 130 of 376
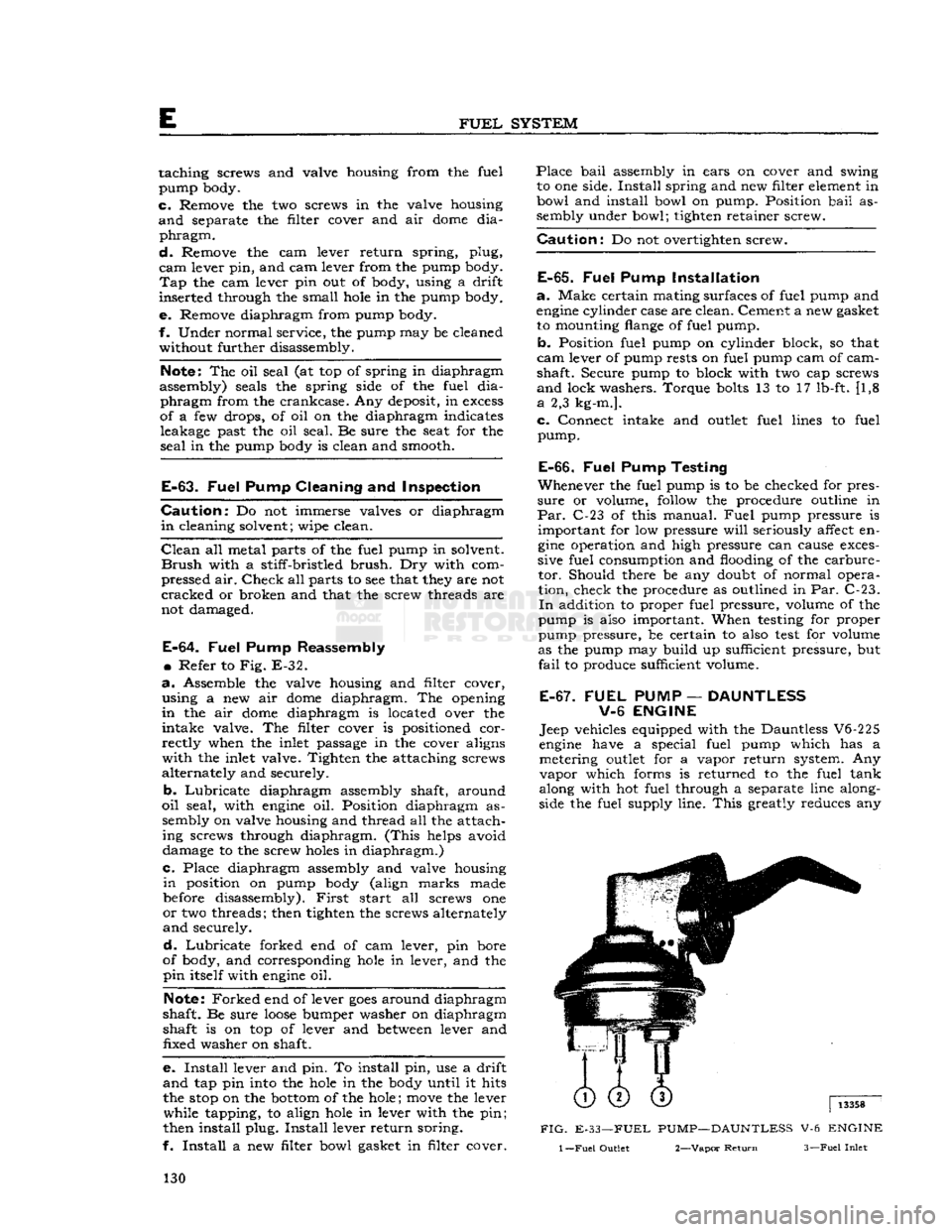
E
FUEL
SYSTEM
taching screws and valve housing from the fuel
pump body.
c.
Remove the two screws in the valve housing
and
separate the filter cover and air
dome
dia
phragm.
d.
Remove the cam lever return spring, plug,
cam
lever pin, and cam lever from the pump body.
Tap
the cam lever pin out of body, using a drift
inserted through the small
hole
in the pump body.
e. Remove diaphragm from pump body.
f. Under normal service, the pump may be cleaned without further disassembly.
Note:
The oil seal (at top of spring in diaphragm
assembly) seals the spring side of the fuel
dia
phragm
from the crankcase. Any deposit, in
excess
of a few drops, of oil on the diaphragm indicates leakage past the oil seal. Be sure the seat for the
seal
in the pump body is clean and smooth.
E-63.
Fuel
Pump Cleaning and Inspection
Caution:
Do not immerse valves or diaphragm
in
cleaning solvent; wipe clean.
Clean
all metal parts of the fuel pump in solvent.
Brush
with a stiff-bristled
brush.
Dry with com
pressed
air.
Check
all parts to see that they are not
cracked
or broken and that the screw threads are
not damaged.
E-64.
Fuel
Pump Reassembly
•
Refer to Fig. E-32.
a.
Assemble the valve housing and filter cover, using a new air
dome
diaphragm. The opening
in
the air
dome
diaphragm is located over the
intake
valve. The filter cover is positioned cor
rectly
when the inlet passage in the cover aligns
with
the inlet valve. Tighten the attaching screws
alternately and securely.
b.
Lubricate
diaphragm assembly shaft, around
oil
seal, with
engine
oil. Position diaphragm as sembly on valve housing and thread all the attach ing screws through diaphragm.
(This
helps avoid
damage to the screw
holes
in diaphragm.)
c.
Place diaphragm assembly and valve housing
in
position on pump body (align marks made
before disassembly).
First
start all screws one
or
two threads; then tighten the screws alternately
and
securely.
d.
Lubricate
forked end of cam lever, pin bore
of body, and corresponding
hole
in lever, and the
pin
itself with
engine
oil.
Note:
Forked
end of lever
goes
around diaphragm
shaft. Be sure
loose
bumper washer on diaphragm shaft is on top of lever and
between
lever and fixed
washer
on shaft.
e.
Install
lever and pin. To install pin, use a drift
and
tap pin into the
hole
in the body until it hits
the
stop
on the
bottom
of the hole;
move
the lever while tapping, to align
hole
in lever with the pin;
then install plug.
Install
lever return spring.
f.
Install
a new filter bowl gasket in filter cover.
Place
bail
assembly in ears on cover and swing
to one side.
Install
spring and new filter element in
bowl and install bowl on pump. Position
bail
as
sembly under bowl; tighten retainer screw.
Caution:
Do not overtighten screw.
E-65.
Fuel
Pump Installation
a.
Make certain mating surfaces of fuel pump and
engine
cylinder case are clean. Cement a new gasket to mounting flange of fuel pump.
b.
Position fuel pump on cylinder block, so that
cam
lever of pump rests on fuel pump cam of cam
shaft. Secure pump to block with two cap screws
and
lock washers. Torque
bolts
13 to 17 lb-ft. [1,8
a
2,3 kg-m.].
c.
Connect intake and
outlet
fuel lines to fuel
pump.
E-66.
Fuel
Pump Testing
Whenever
the fuel pump is to be checked for pres
sure
or volume, follow the procedure outline in
Par.
C-23 of this manual.
Fuel
pump pressure is
important
for low pressure
will
seriously affect en
gine
operation and high pressure can cause exces
sive fuel consumption and flooding of the carbure
tor.
Should there be any doubt of normal opera
tion, check the procedure as outlined in Par. C-23.
In
addition to proper fuel pressure, volume of the
pump is also important. When testing for proper
pump pressure, be certain to also
test
for volume
as the pump may build up sufficient pressure, but
fail
to produce sufficient volume.
E-67. FUEL
PUMP
—
DAUNTLESS
V-6
ENGINE
Jeep vehicles equipped with the Dauntless V6-225
engine
have a special fuel pump which has a metering
outlet
for a vapor return system. Any
vapor
which forms is returned to the fuel tank
along with hot fuel through a separate line along
side the fuel supply line.
This
greatly reduces any
FIG.
E-33—FUEL PUMP—DAUNTLESS V-6 ENGINE
1
—Fuel
Outlet 2—Vapor
Return
3—Fuel
Inlet
130