LAND ROVER DEFENDER 1996 Workshop Manual
Manufacturer: LAND ROVER, Model Year: 1996, Model line: DEFENDER, Model: LAND ROVER DEFENDER 1996Pages: 455, PDF Size: 6.44 MB
Page 231 of 455
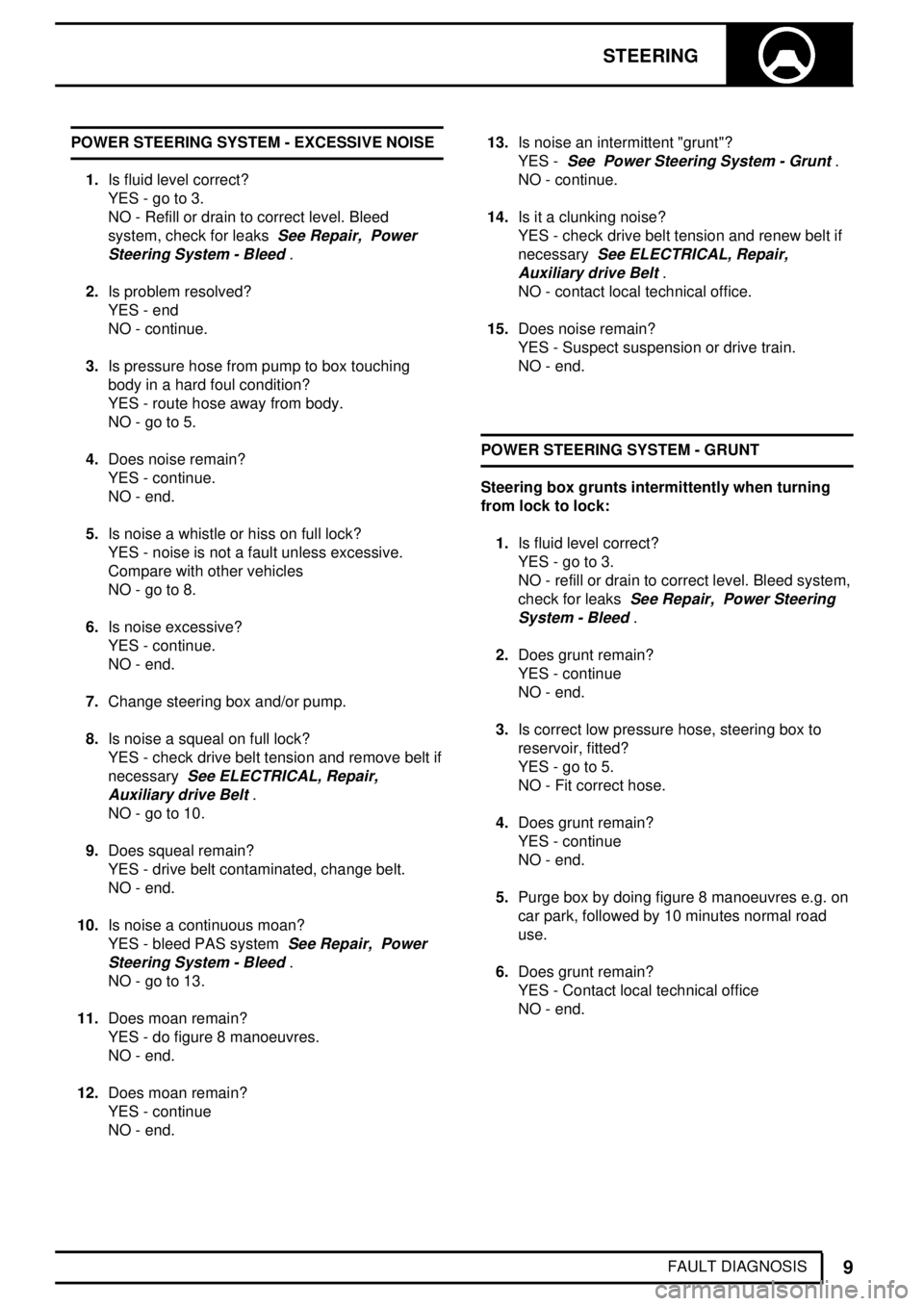
STEERING
9
FAULT DIAGNOSIS POWER STEERING SYSTEM - EXCESSIVE NOISE
1.Is fluid level correct?
YES - go to 3.
NO - Refill or drain to correct level. Bleed
system, check for leaks
See Repair, Power
Steering System - Bleed
.
2.Is problem resolved?
YES - end
NO - continue.
3.Is pressure hose from pump to box touching
body in a hard foul condition?
YES - route hose away from body.
NO - go to 5.
4.Does noise remain?
YES - continue.
NO - end.
5.Is noise a whistle or hiss on full lock?
YES - noise is not a fault unless excessive.
Compare with other vehicles
NO - go to 8.
6.Is noise excessive?
YES - continue.
NO - end.
7.Change steering box and/or pump.
8.Is noise a squeal on full lock?
YES - check drive belt tension and remove belt if
necessary
See ELECTRICAL, Repair,
Auxiliary drive Belt
.
NO - go to 10.
9.Does squeal remain?
YES - drive belt contaminated, change belt.
NO - end.
10.Is noise a continuous moan?
YES - bleed PAS system
See Repair, Power
Steering System - Bleed
.
NO - go to 13.
11.Does moan remain?
YES - do figure 8 manoeuvres.
NO - end.
12.Does moan remain?
YES - continue
NO - end.13.Is noise an intermittent "grunt"?
YES -
See Power Steering System - Grunt.
NO - continue.
14.Is it a clunking noise?
YES - check drive belt tension and renew belt if
necessary
See ELECTRICAL, Repair,
Auxiliary drive Belt
.
NO - contact local technical office.
15.Does noise remain?
YES - Suspect suspension or drive train.
NO - end.
POWER STEERING SYSTEM - GRUNT
Steering box grunts intermittently when turning
from lock to lock:
1.Is fluid level correct?
YES - go to 3.
NO - refill or drain to correct level. Bleed system,
check for leaks
See Repair, Power Steering
System - Bleed
.
2.Does grunt remain?
YES - continue
NO - end.
3.Is correct low pressure hose, steering box to
reservoir, fitted?
YES - go to 5.
NO - Fit correct hose.
4.Does grunt remain?
YES - continue
NO - end.
5.Purge box by doing figure 8 manoeuvres e.g. on
car park, followed by 10 minutes normal road
use.
6.Does grunt remain?
YES - Contact local technical office
NO - end.
Page 232 of 455
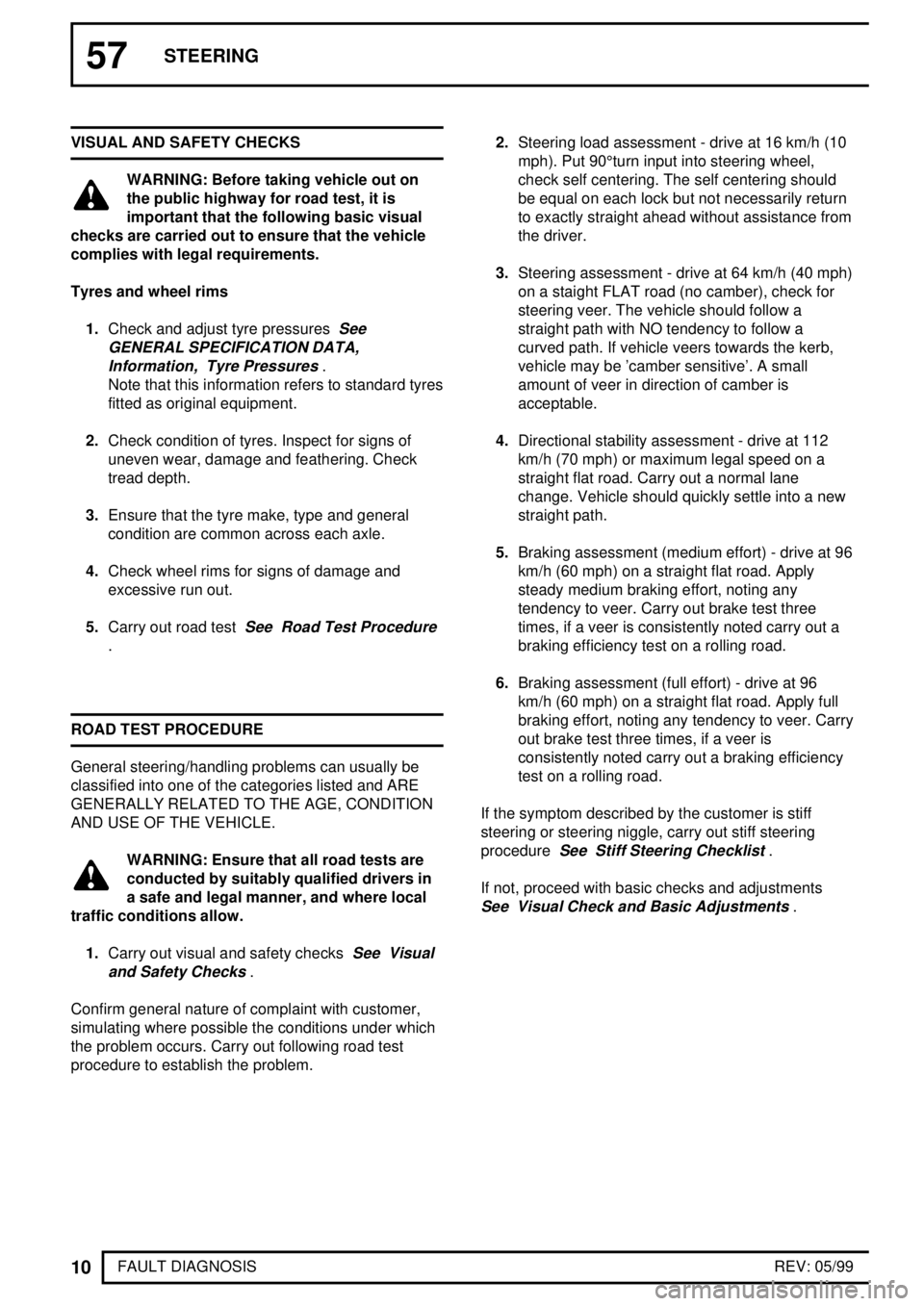
57STEERING
10
FAULT DIAGNOSISREV: 05/99 VISUAL AND SAFETY CHECKS
WARNING: Before taking vehicle out on
the public highway for road test, it is
important that the following basic visual
checks are carried out to ensure that the vehicle
complies with legal requirements.
Tyres and wheel rims
1.Check and adjust tyre pressures
See
GENERAL SPECIFICATION DATA,
Information, Tyre Pressures
.
Note that this information refers to standard tyres
fitted as original equipment.
2.Check condition of tyres. Inspect for signs of
uneven wear, damage and feathering. Check
tread depth.
3.Ensure that the tyre make, type and general
condition are common across each axle.
4.Check wheel rims for signs of damage and
excessive run out.
5.Carry out road test
See Road Test Procedure
.
ROAD TEST PROCEDURE
General steering/handling problems can usually be
classified into one of the categories listed and ARE
GENERALLY RELATED TO THE AGE, CONDITION
AND USE OF THE VEHICLE.
WARNING: Ensure that all road tests are
conducted by suitably qualified drivers in
a safe and legal manner, and where local
traffic conditions allow.
1.Carry out visual and safety checks
See Visual
and Safety Checks
.
Confirm general nature of complaint with customer,
simulating where possible the conditions under which
the problem occurs. Carry out following road test
procedure to establish the problem.2.Steering load assessment - drive at 16 km/h (10
mph). Put 90°turn input into steering wheel,
check self centering. The self centering should
be equal on each lock but not necessarily return
to exactly straight ahead without assistance from
the driver.
3.Steering assessment - drive at 64 km/h (40 mph)
on a staight FLAT road (no camber), check for
steering veer. The vehicle should follow a
straight path with NO tendency to follow a
curved path. If vehicle veers towards the kerb,
vehicle may be 'camber sensitive'. A small
amount of veer in direction of camber is
acceptable.
4.Directional stability assessment - drive at 112
km/h (70 mph) or maximum legal speed on a
straight flat road. Carry out a normal lane
change. Vehicle should quickly settle into a new
straight path.
5.Braking assessment (medium effort) - drive at 96
km/h (60 mph) on a straight flat road. Apply
steady medium braking effort, noting any
tendency to veer. Carry out brake test three
times, if a veer is consistently noted carry out a
braking efficiency test on a rolling road.
6.Braking assessment (full effort) - drive at 96
km/h (60 mph) on a straight flat road. Apply full
braking effort, noting any tendency to veer. Carry
out brake test three times, if a veer is
consistently noted carry out a braking efficiency
test on a rolling road.
If the symptom described by the customer is stiff
steering or steering niggle, carry out stiff steering
procedure
See Stiff Steering Checklist.
If not, proceed with basic checks and adjustments
See Visual Check and Basic Adjustments.
Page 233 of 455
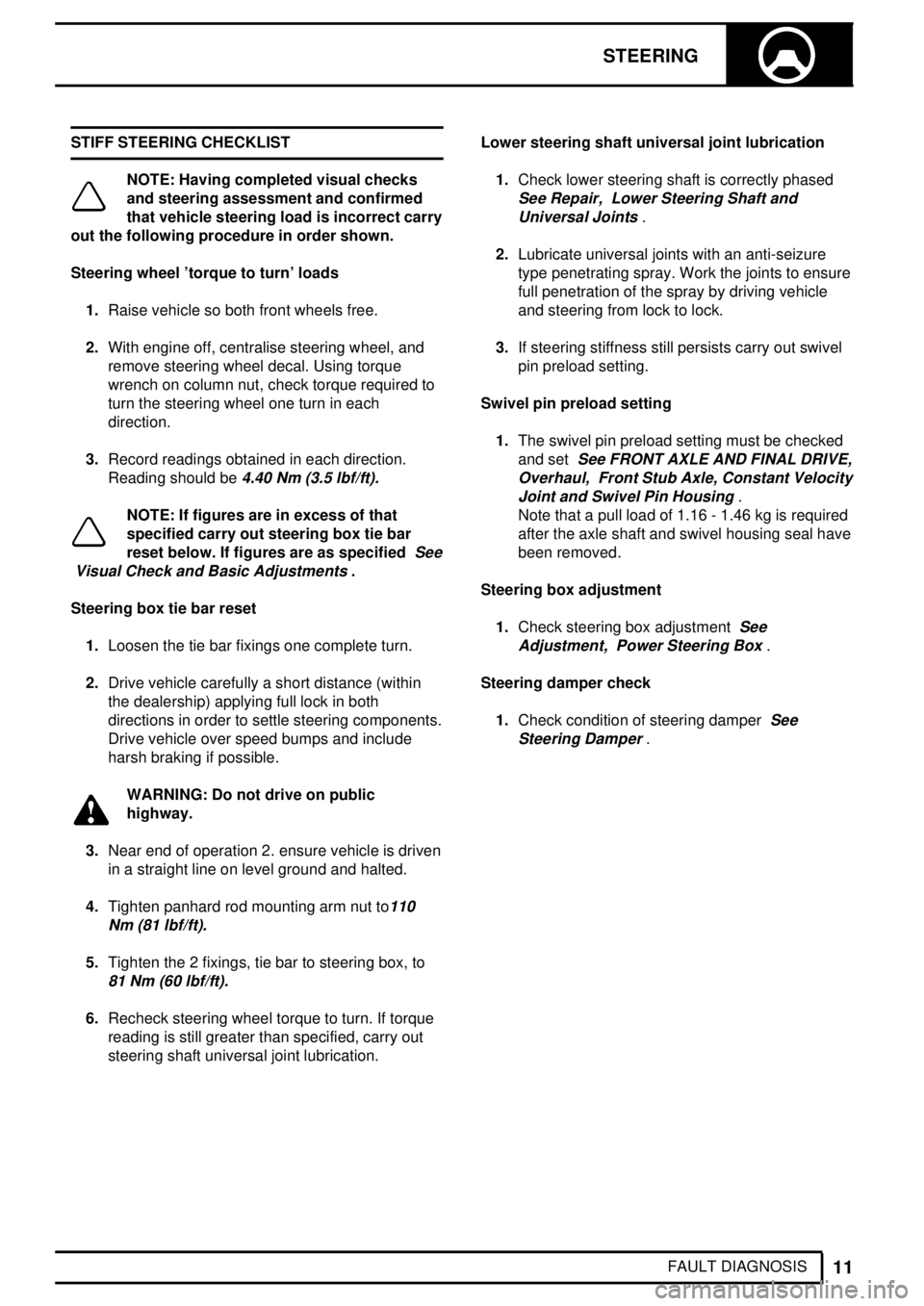
STEERING
11
FAULT DIAGNOSIS STIFF STEERING CHECKLIST
NOTE: Having completed visual checks
and steering assessment and confirmed
that vehicle steering load is incorrect carry
out the following procedure in order shown.
Steering wheel 'torque to turn' loads
1.Raise vehicle so both front wheels free.
2.With engine off, centralise steering wheel, and
remove steering wheel decal. Using torque
wrench on column nut, check torque required to
turn the steering wheel one turn in each
direction.
3.Record readings obtained in each direction.
Reading should be
4.40 Nm (3.5 lbf/ft).
NOTE: If figures are in excess of that
specified carry out steering box tie bar
reset below. If figures are as specified
See
Visual Check and Basic Adjustments
.
Steering box tie bar reset
1.Loosen the tie bar fixings one complete turn.
2.Drive vehicle carefully a short distance (within
the dealership) applying full lock in both
directions in order to settle steering components.
Drive vehicle over speed bumps and include
harsh braking if possible.
WARNING: Do not drive on public
highway.
3.Near end of operation 2. ensure vehicle is driven
in a straight line on level ground and halted.
4.Tighten panhard rod mounting arm nut to
110
Nm (81 lbf/ft).
5.Tighten the 2 fixings, tie bar to steering box, to
81 Nm (60 lbf/ft).
6.Recheck steering wheel torque to turn. If torque
reading is still greater than specified, carry out
steering shaft universal joint lubrication.Lower steering shaft universal joint lubrication
1.Check lower steering shaft is correctly phased
See Repair, Lower Steering Shaft and
Universal Joints
.
2.Lubricate universal joints with an anti-seizure
type penetrating spray. Work the joints to ensure
full penetration of the spray by driving vehicle
and steering from lock to lock.
3.If steering stiffness still persists carry out swivel
pin preload setting.
Swivel pin preload setting
1.The swivel pin preload setting must be checked
and set
See FRONT AXLE AND FINAL DRIVE,
Overhaul, Front Stub Axle, Constant Velocity
Joint and Swivel Pin Housing
.
Note that a pull load of 1.16 - 1.46 kg is required
after the axle shaft and swivel housing seal have
been removed.
Steering box adjustment
1.Check steering box adjustment
See
Adjustment, Power Steering Box
.
Steering damper check
1.Check condition of steering damper
See
Steering Damper
.
Page 234 of 455
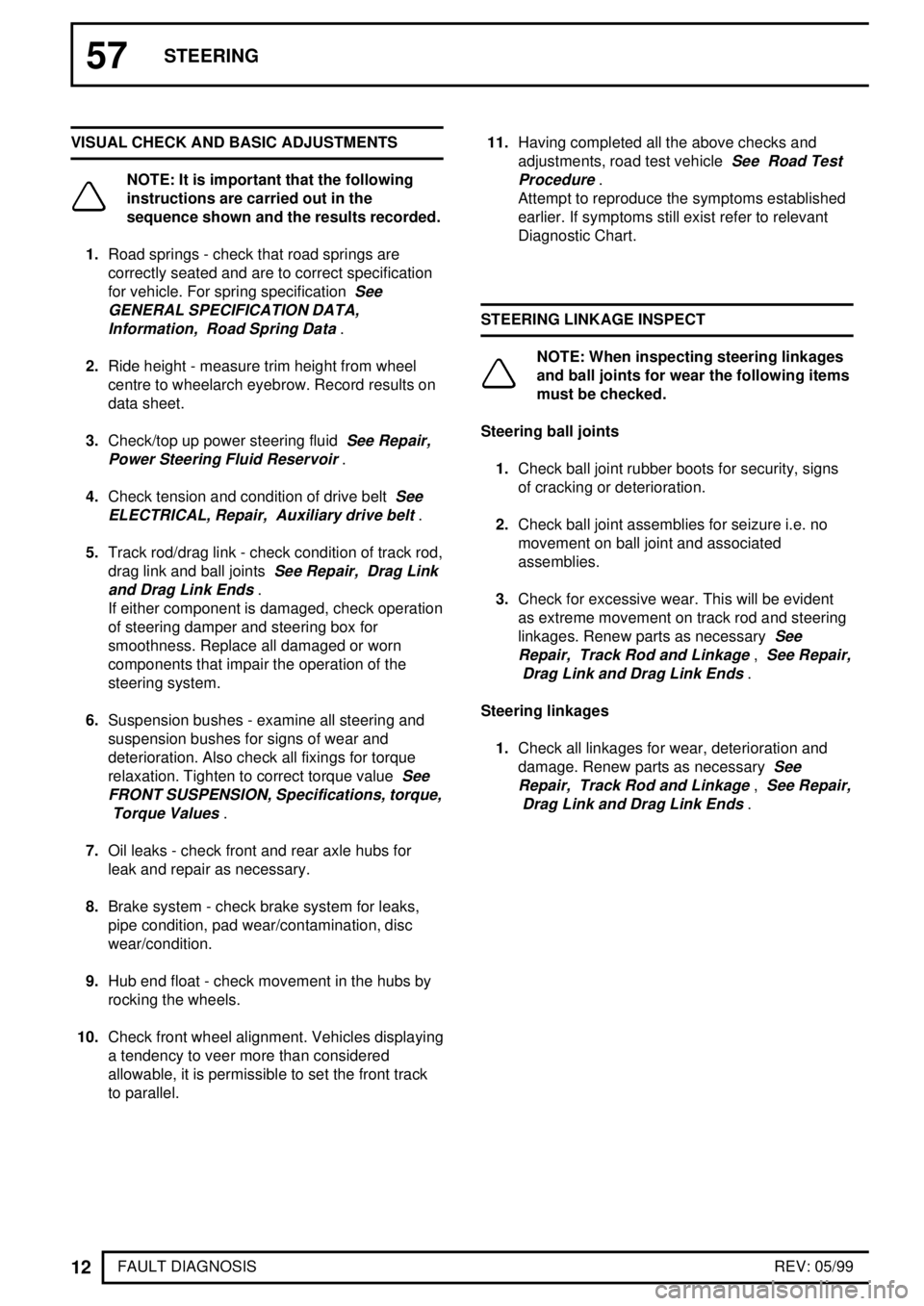
57STEERING
12
FAULT DIAGNOSISREV: 05/99 VISUAL CHECK AND BASIC ADJUSTMENTS
NOTE: It is important that the following
instructions are carried out in the
sequence shown and the results recorded.
1.Road springs - check that road springs are
correctly seated and are to correct specification
for vehicle. For spring specification
See
GENERAL SPECIFICATION DATA,
Information, Road Spring Data
.
2.Ride height - measure trim height from wheel
centre to wheelarch eyebrow. Record results on
data sheet.
3.Check/top up power steering fluid
See Repair,
Power Steering Fluid Reservoir
.
4.Check tension and condition of drive belt
See
ELECTRICAL, Repair, Auxiliary drive belt
.
5.Track rod/drag link - check condition of track rod,
drag link and ball joints
See Repair, Drag Link
and Drag Link Ends
.
If either component is damaged, check operation
of steering damper and steering box for
smoothness. Replace all damaged or worn
components that impair the operation of the
steering system.
6.Suspension bushes - examine all steering and
suspension bushes for signs of wear and
deterioration. Also check all fixings for torque
relaxation. Tighten to correct torque value
See
FRONT SUSPENSION, Specifications, torque,
Torque Values
.
7.Oil leaks - check front and rear axle hubs for
leak and repair as necessary.
8.Brake system - check brake system for leaks,
pipe condition, pad wear/contamination, disc
wear/condition.
9.Hub end float - check movement in the hubs by
rocking the wheels.
10.Check front wheel alignment. Vehicles displaying
a tendency to veer more than considered
allowable, it is permissible to set the front track
to parallel.11.Having completed all the above checks and
adjustments, road test vehicle
See Road Test
Procedure
.
Attempt to reproduce the symptoms established
earlier. If symptoms still exist refer to relevant
Diagnostic Chart.
STEERING LINKAGE INSPECT
NOTE: When inspecting steering linkages
and ball joints for wear the following items
must be checked.
Steering ball joints
1.Check ball joint rubber boots for security, signs
of cracking or deterioration.
2.Check ball joint assemblies for seizure i.e. no
movement on ball joint and associated
assemblies.
3.Check for excessive wear. This will be evident
as extreme movement on track rod and steering
linkages. Renew parts as necessary
See
Repair, Track Rod and Linkage
,See Repair,
Drag Link and Drag Link Ends
.
Steering linkages
1.Check all linkages for wear, deterioration and
damage. Renew parts as necessary
See
Repair, Track Rod and Linkage
,See Repair,
Drag Link and Drag Link Ends
.
Page 235 of 455
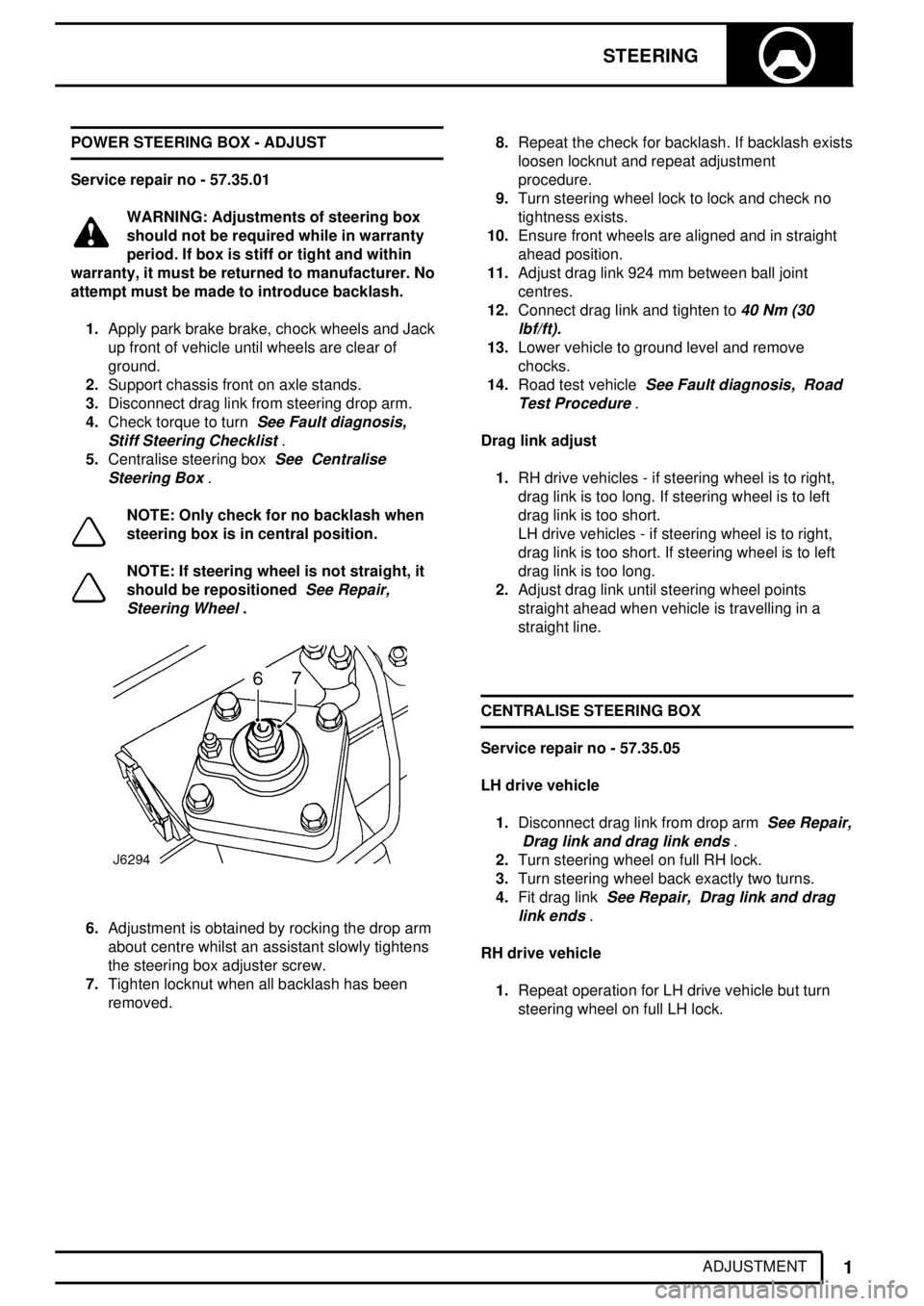
STEERING
1
ADJUSTMENT POWER STEERING BOX - ADJUST
Service repair no - 57.35.01
WARNING: Adjustments of steering box
should not be required while in warranty
period. If box is stiff or tight and within
warranty, it must be returned to manufacturer. No
attempt must be made to introduce backlash.
1.Apply park brake brake, chock wheels and Jack
up front of vehicle until wheels are clear of
ground.
2.Support chassis front on axle stands.
3.Disconnect drag link from steering drop arm.
4.Check torque to turn
See Fault diagnosis,
Stiff Steering Checklist
.
5.Centralise steering box
See Centralise
Steering Box
.
NOTE: Only check for no backlash when
steering box is in central position.
NOTE: If steering wheel is not straight, it
should be repositioned
See Repair,
Steering Wheel
.
6.Adjustment is obtained by rocking the drop arm
about centre whilst an assistant slowly tightens
the steering box adjuster screw.
7.Tighten locknut when all backlash has been
removed.8.Repeat the check for backlash. If backlash exists
loosen locknut and repeat adjustment
procedure.
9.Turn steering wheel lock to lock and check no
tightness exists.
10.Ensure front wheels are aligned and in straight
ahead position.
11.Adjust drag link 924 mm between ball joint
centres.
12.Connect drag link and tighten to
40 Nm (30
lbf/ft).
13.Lower vehicle to ground level and remove
chocks.
14.Road test vehicle
See Fault diagnosis, Road
Test Procedure
.
Drag link adjust
1.RH drive vehicles - if steering wheel is to right,
drag link is too long. If steering wheel is to left
drag link is too short.
LH drive vehicles - if steering wheel is to right,
drag link is too short. If steering wheel is to left
drag link is too long.
2.Adjust drag link until steering wheel points
straight ahead when vehicle is travelling in a
straight line.
CENTRALISE STEERING BOX
Service repair no - 57.35.05
LH drive vehicle
1.Disconnect drag link from drop arm
See Repair,
Drag link and drag link ends
.
2.Turn steering wheel on full RH lock.
3.Turn steering wheel back exactly two turns.
4.Fit drag link
See Repair, Drag link and drag
link ends
.
RH drive vehicle
1.Repeat operation for LH drive vehicle but turn
steering wheel on full LH lock.
Page 236 of 455
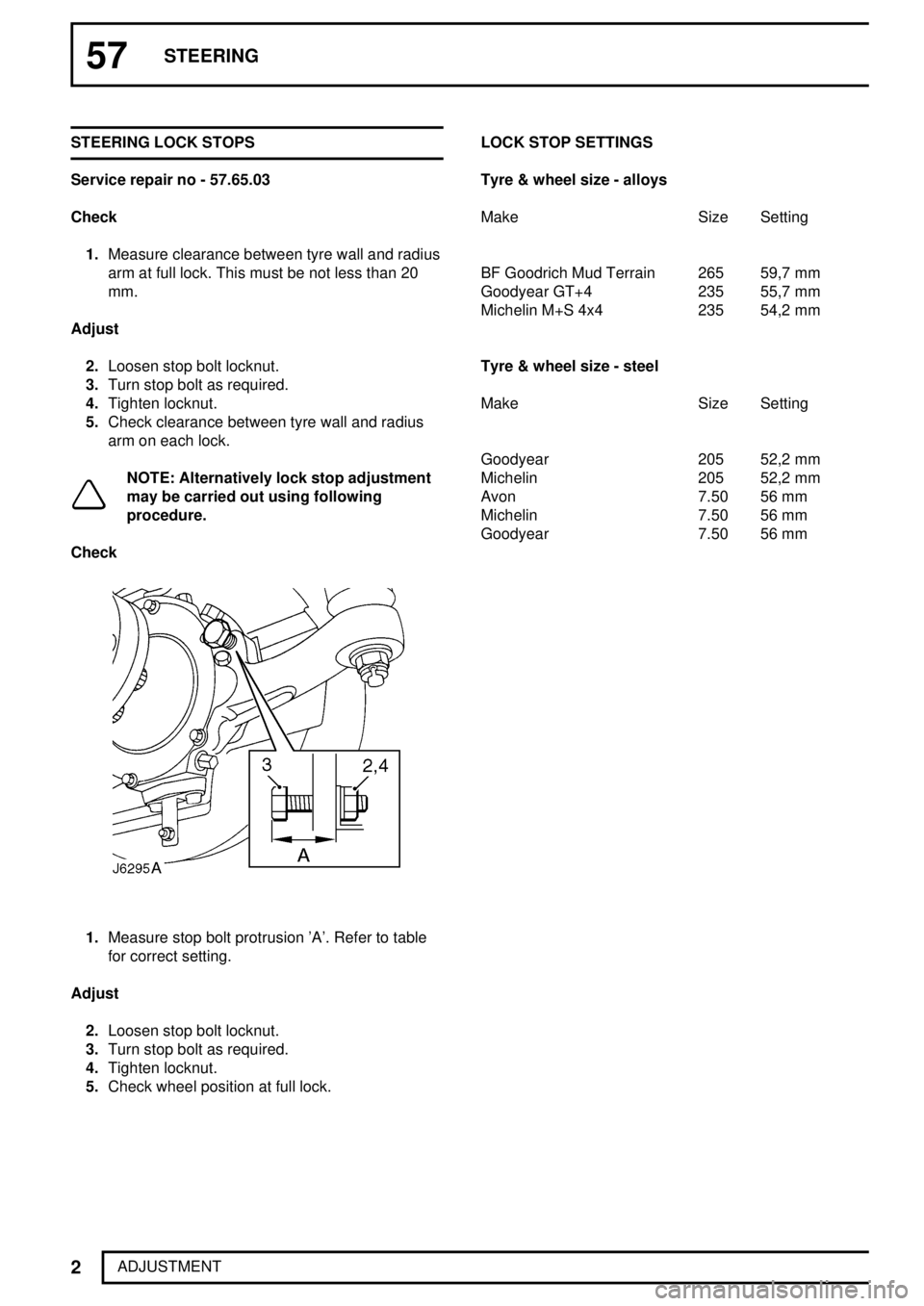
57STEERING
2
ADJUSTMENT STEERING LOCK STOPS
Service repair no - 57.65.03
Check
1.Measure clearance between tyre wall and radius
arm at full lock. This must be not less than 20
mm.
Adjust
2.Loosen stop bolt locknut.
3.Turn stop bolt as required.
4.Tighten locknut.
5.Check clearance between tyre wall and radius
arm on each lock.
NOTE: Alternatively lock stop adjustment
may be carried out using following
procedure.
Check
1.Measure stop bolt protrusion 'A'. Refer to table
for correct setting.
Adjust
2.Loosen stop bolt locknut.
3.Turn stop bolt as required.
4.Tighten locknut.
5.Check wheel position at full lock.LOCK STOP SETTINGS
Tyre & wheel size - alloys
Make Size Setting
BF Goodrich Mud Terrain 265 59,7 mm
Goodyear GT+4 235 55,7 mm
Michelin M+S 4x4 235 54,2 mm
Tyre & wheel size - steel
Make Size Setting
Goodyear 205 52,2 mm
Michelin 205 52,2 mm
Avon 7.50 56 mm
Michelin 7.50 56 mm
Goodyear 7.50 56 mm
Page 237 of 455
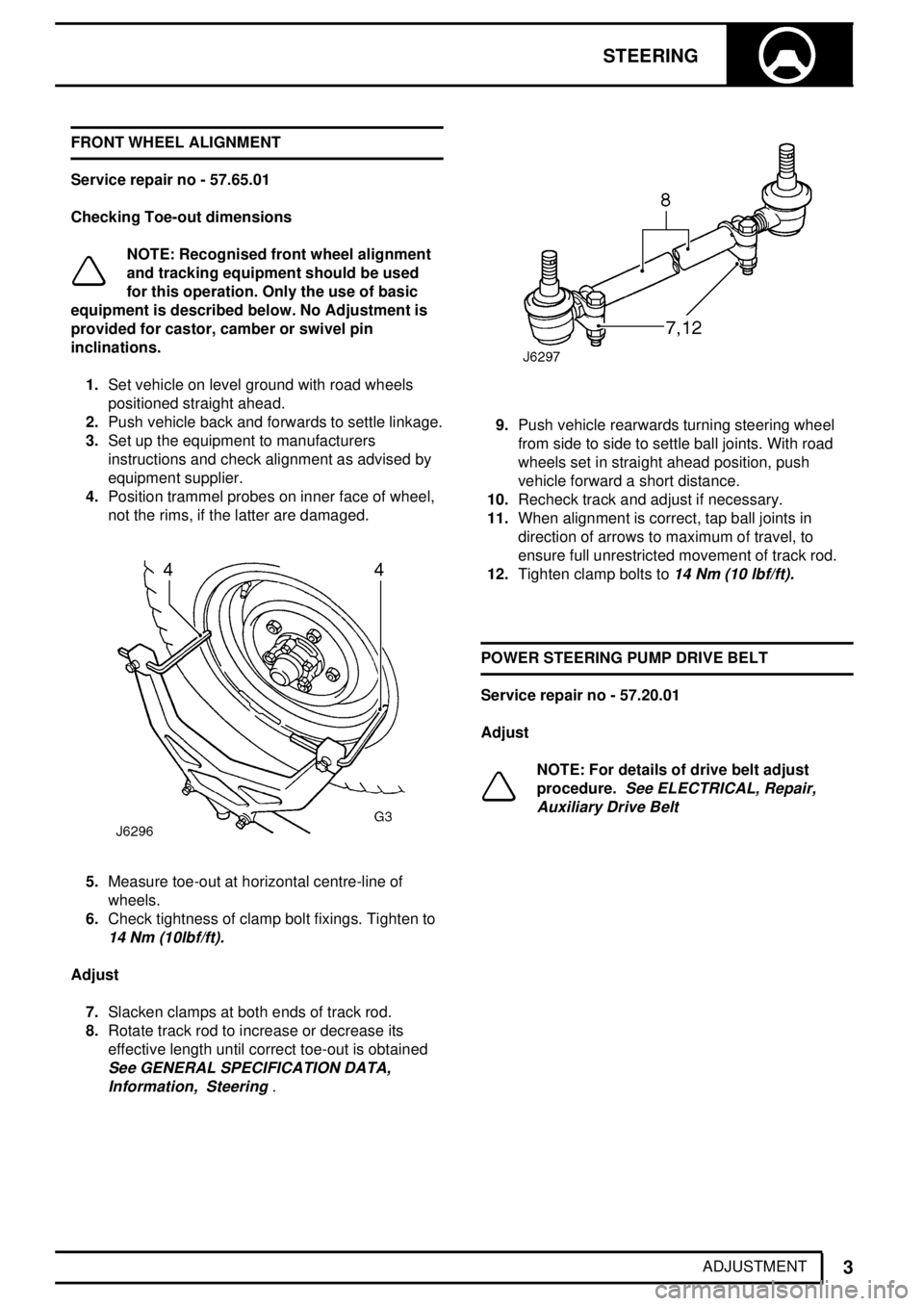
STEERING
3
ADJUSTMENT FRONT WHEEL ALIGNMENT
Service repair no - 57.65.01
Checking Toe-out dimensions
NOTE: Recognised front wheel alignment
and tracking equipment should be used
for this operation. Only the use of basic
equipment is described below. No Adjustment is
provided for castor, camber or swivel pin
inclinations.
1.Set vehicle on level ground with road wheels
positioned straight ahead.
2.Push vehicle back and forwards to settle linkage.
3.Set up the equipment to manufacturers
instructions and check alignment as advised by
equipment supplier.
4.Position trammel probes on inner face of wheel,
not the rims, if the latter are damaged.
5.Measure toe-out at horizontal centre-line of
wheels.
6.Check tightness of clamp bolt fixings. Tighten to
14 Nm (10lbf/ft).
Adjust
7.Slacken clamps at both ends of track rod.
8.Rotate track rod to increase or decrease its
effective length until correct toe-out is obtained
See GENERAL SPECIFICATION DATA,
Information, Steering
.
9.Push vehicle rearwards turning steering wheel
from side to side to settle ball joints. With road
wheels set in straight ahead position, push
vehicle forward a short distance.
10.Recheck track and adjust if necessary.
11.When alignment is correct, tap ball joints in
direction of arrows to maximum of travel, to
ensure full unrestricted movement of track rod.
12.Tighten clamp bolts to
14 Nm (10 lbf/ft).
POWER STEERING PUMP DRIVE BELT
Service repair no - 57.20.01
Adjust
NOTE: For details of drive belt adjust
procedure.
See ELECTRICAL, Repair,
Auxiliary Drive Belt
Page 238 of 455
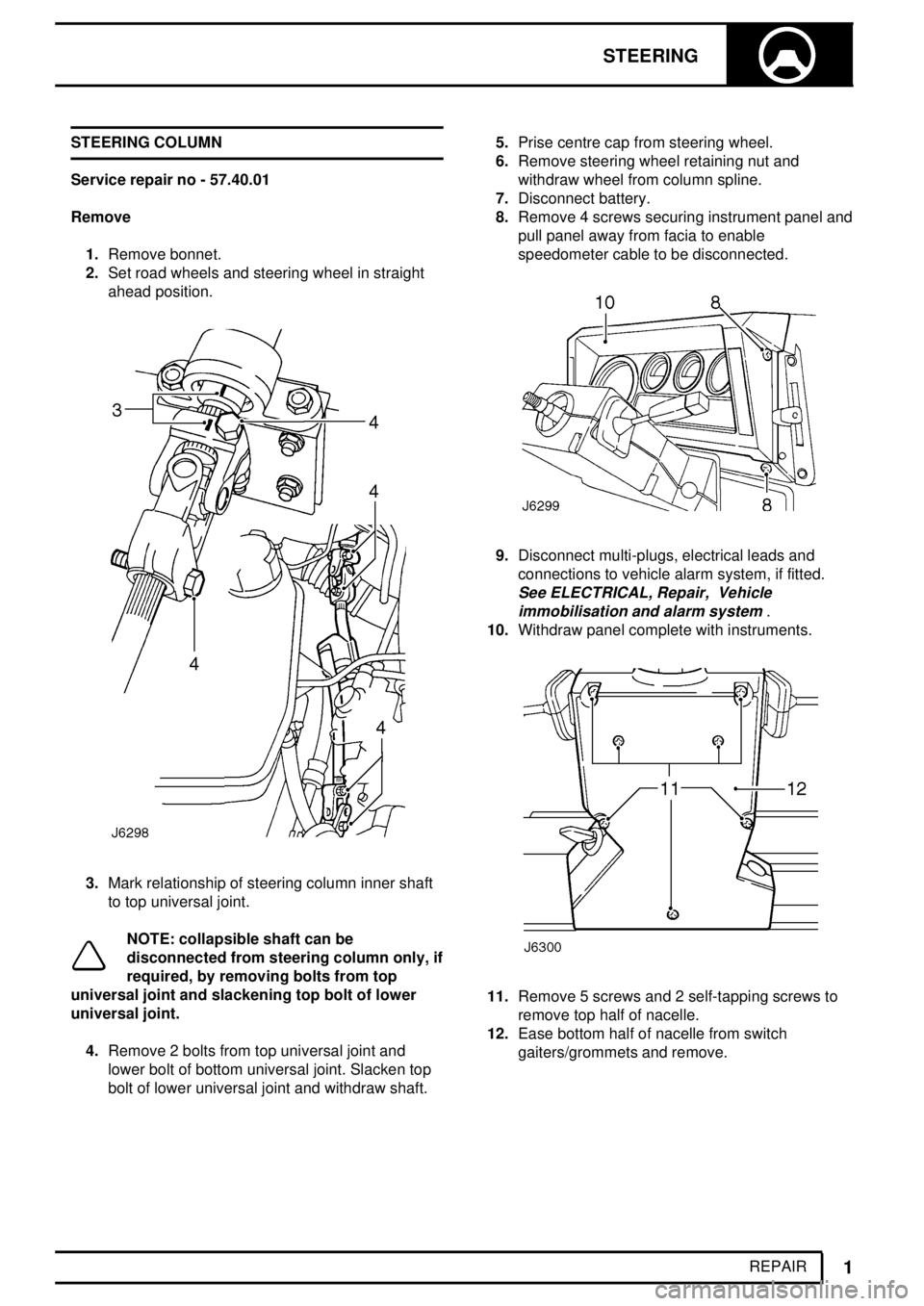
STEERING
1
REPAIR STEERING COLUMN
Service repair no - 57.40.01
Remove
1.Remove bonnet.
2.Set road wheels and steering wheel in straight
ahead position.
3.Mark relationship of steering column inner shaft
to top universal joint.
NOTE: collapsible shaft can be
disconnected from steering column only, if
required, by removing bolts from top
universal joint and slackening top bolt of lower
universal joint.
4.Remove 2 bolts from top universal joint and
lower bolt of bottom universal joint. Slacken top
bolt of lower universal joint and withdraw shaft.5.Prise centre cap from steering wheel.
6.Remove steering wheel retaining nut and
withdraw wheel from column spline.
7.Disconnect battery.
8.Remove 4 screws securing instrument panel and
pull panel away from facia to enable
speedometer cable to be disconnected.
9.Disconnect multi-plugs, electrical leads and
connections to vehicle alarm system, if fitted.
See ELECTRICAL, Repair, Vehicle
immobilisation and alarm system
.
10.Withdraw panel complete with instruments.
11.Remove 5 screws and 2 self-tapping screws to
remove top half of nacelle.
12.Ease bottom half of nacelle from switch
gaiters/grommets and remove.
Page 239 of 455
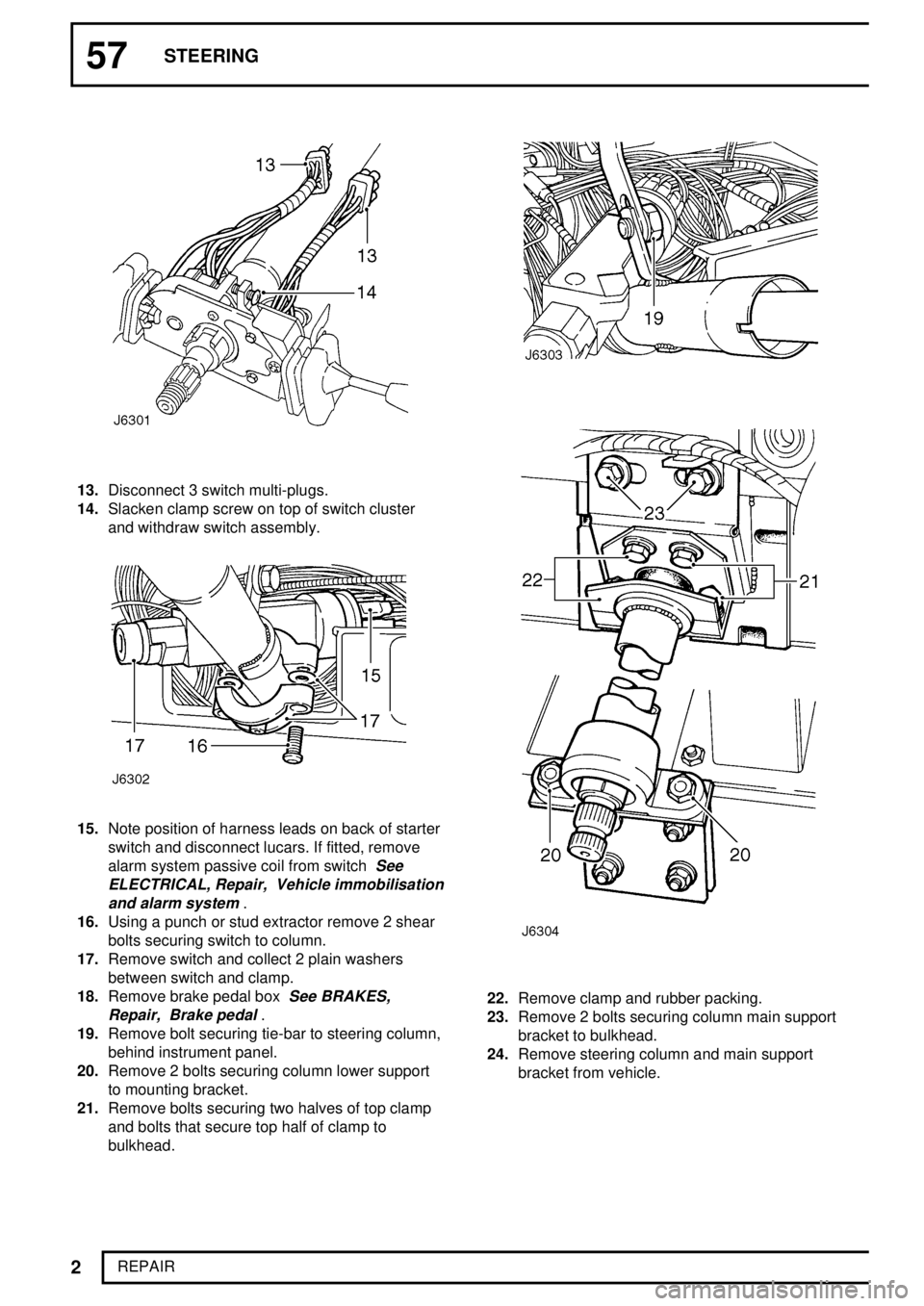
57STEERING
2
REPAIR
13.Disconnect 3 switch multi-plugs.
14.Slacken clamp screw on top of switch cluster
and withdraw switch assembly.
15.Note position of harness leads on back of starter
switch and disconnect lucars. If fitted, remove
alarm system passive coil from switch
See
ELECTRICAL, Repair, Vehicle immobilisation
and alarm system
.
16.Using a punch or stud extractor remove 2 shear
bolts securing switch to column.
17.Remove switch and collect 2 plain washers
between switch and clamp.
18.Remove brake pedal box
See BRAKES,
Repair, Brake pedal
.
19.Remove bolt securing tie-bar to steering column,
behind instrument panel.
20.Remove 2 bolts securing column lower support
to mounting bracket.
21.Remove bolts securing two halves of top clamp
and bolts that secure top half of clamp to
bulkhead.
22.Remove clamp and rubber packing.
23.Remove 2 bolts securing column main support
bracket to bulkhead.
24.Remove steering column and main support
bracket from vehicle.
Page 240 of 455
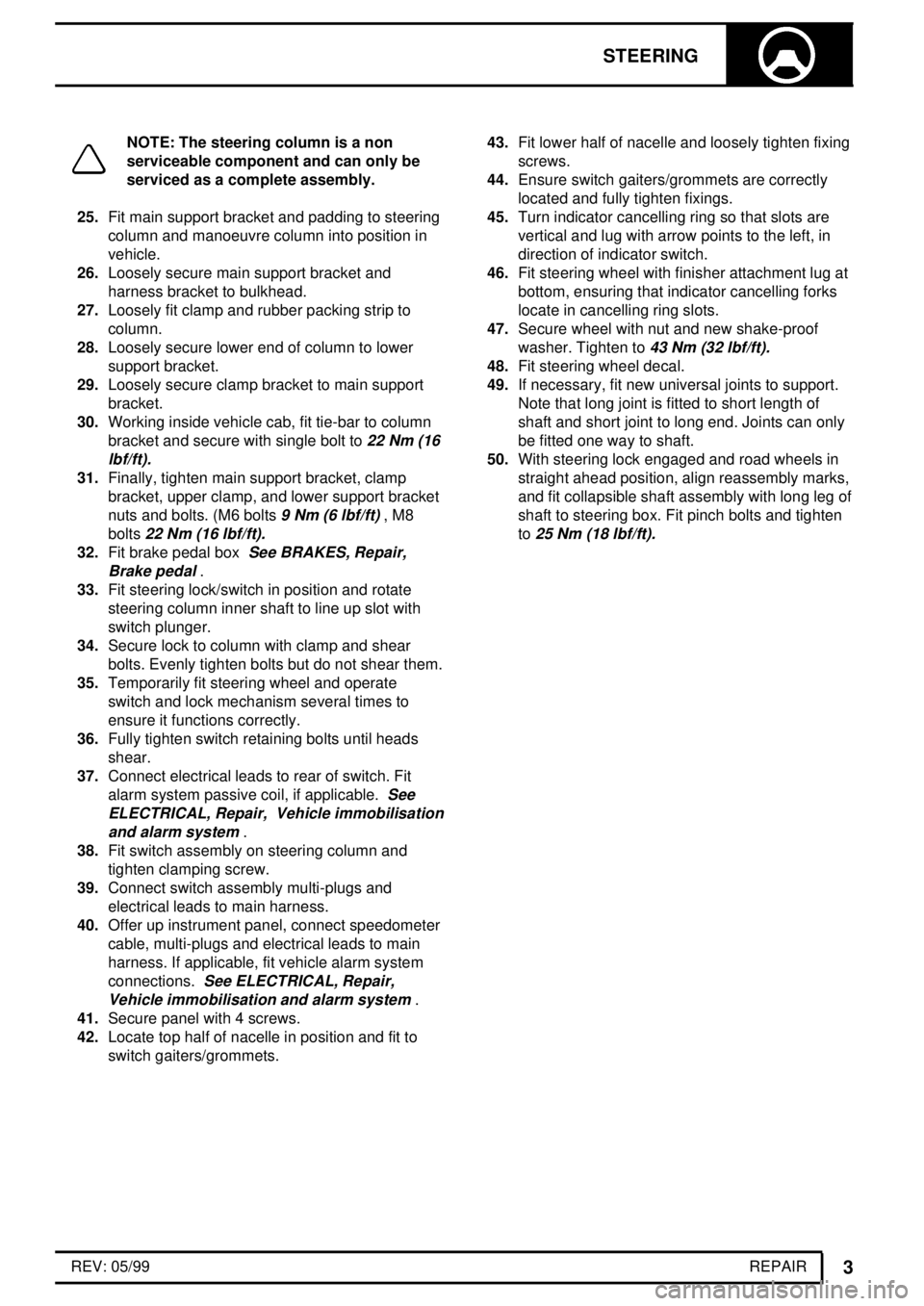
STEERING
3
REPAIR REV: 05/99
NOTE: The steering column is a non
serviceable component and can only be
serviced as a complete assembly.
25.Fit main support bracket and padding to steering
column and manoeuvre column into position in
vehicle.
26.Loosely secure main support bracket and
harness bracket to bulkhead.
27.Loosely fit clamp and rubber packing strip to
column.
28.Loosely secure lower end of column to lower
support bracket.
29.Loosely secure clamp bracket to main support
bracket.
30.Working inside vehicle cab, fit tie-bar to column
bracket and secure with single bolt to
22 Nm (16
lbf/ft).
31.Finally, tighten main support bracket, clamp
bracket, upper clamp, and lower support bracket
nuts and bolts. (M6 bolts
9 Nm (6 lbf/ft),M8
bolts
22 Nm (16 lbf/ft).
32.Fit brake pedal boxSee BRAKES, Repair,
Brake pedal
.
33.Fit steering lock/switch in position and rotate
steering column inner shaft to line up slot with
switch plunger.
34.Secure lock to column with clamp and shear
bolts. Evenly tighten bolts but do not shear them.
35.Temporarily fit steering wheel and operate
switch and lock mechanism several times to
ensure it functions correctly.
36.Fully tighten switch retaining bolts until heads
shear.
37.Connect electrical leads to rear of switch. Fit
alarm system passive coil, if applicable.
See
ELECTRICAL, Repair, Vehicle immobilisation
and alarm system
.
38.Fit switch assembly on steering column and
tighten clamping screw.
39.Connect switch assembly multi-plugs and
electrical leads to main harness.
40.Offer up instrument panel, connect speedometer
cable, multi-plugs and electrical leads to main
harness. If applicable, fit vehicle alarm system
connections.
See ELECTRICAL, Repair,
Vehicle immobilisation and alarm system
.
41.Secure panel with 4 screws.
42.Locate top half of nacelle in position and fit to
switch gaiters/grommets.43.Fit lower half of nacelle and loosely tighten fixing
screws.
44.Ensure switch gaiters/grommets are correctly
located and fully tighten fixings.
45.Turn indicator cancelling ring so that slots are
vertical and lug with arrow points to the left, in
direction of indicator switch.
46.Fit steering wheel with finisher attachment lug at
bottom, ensuring that indicator cancelling forks
locate in cancelling ring slots.
47.Secure wheel with nut and new shake-proof
washer. Tighten to
43 Nm (32 lbf/ft).
48.Fit steering wheel decal.
49.If necessary, fit new universal joints to support.
Note that long joint is fitted to short length of
shaft and short joint to long end. Joints can only
be fitted one way to shaft.
50.With steering lock engaged and road wheels in
straight ahead position, align reassembly marks,
and fit collapsible shaft assembly with long leg of
shaft to steering box. Fit pinch bolts and tighten
to
25 Nm (18 lbf/ft).