LAND ROVER DISCOVERY 1995 Workshop Manual
Manufacturer: LAND ROVER, Model Year: 1995, Model line: DISCOVERY, Model: LAND ROVER DISCOVERY 1995Pages: 873, PDF Size: 12.89 MB
Page 221 of 873
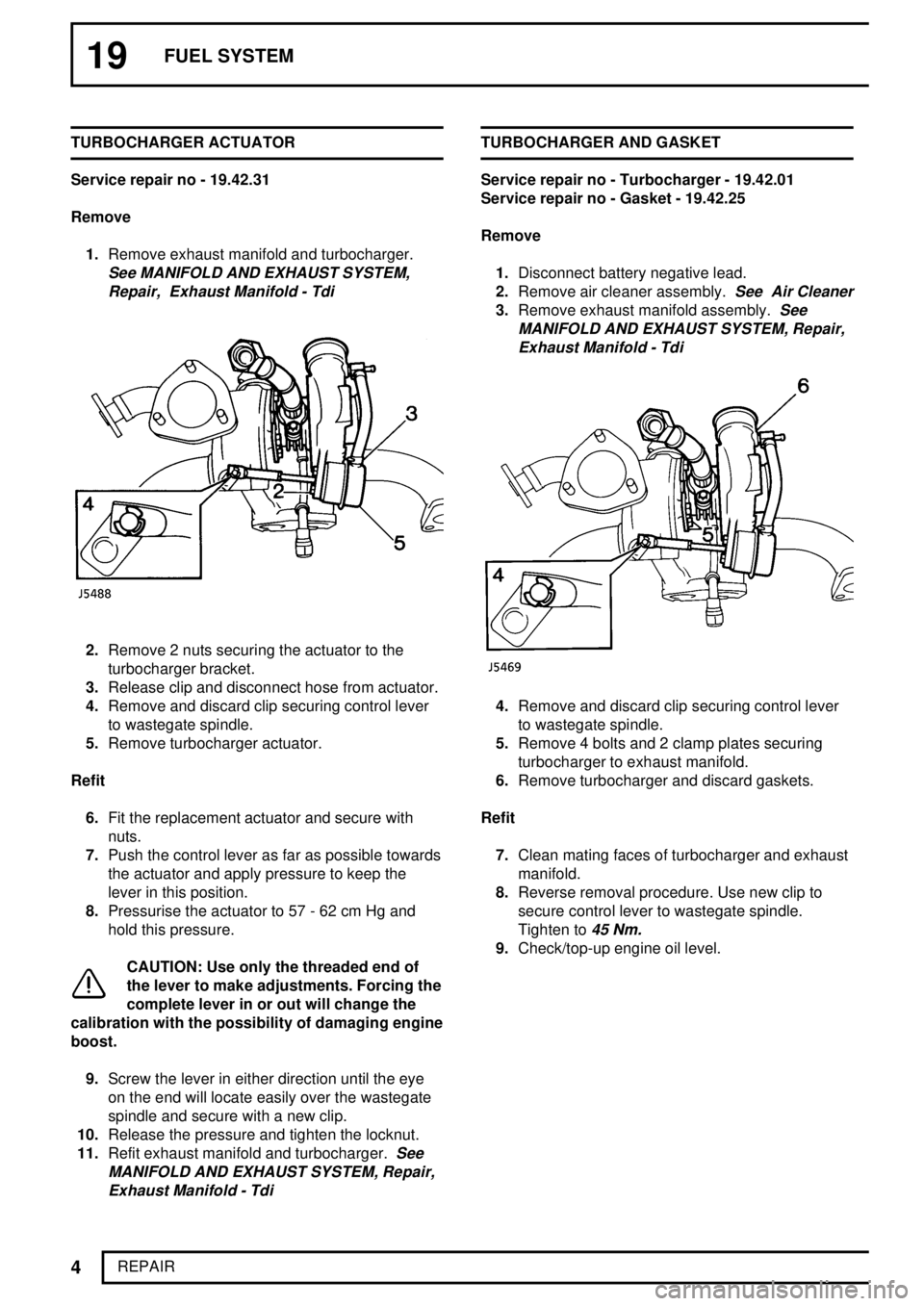
19FUEL SYSTEM
4
REPAIR TURBOCHARGER ACTUATOR
Service repair no - 19.42.31
Remove
1.Remove exhaust manifold and turbocharger.
See MANIFOLD AND EXHAUST SYSTEM,
Repair, Exhaust Manifold - Tdi
2.Remove 2 nuts securing the actuator to the
turbocharger bracket.
3.Release clip and disconnect hose from actuator.
4.Remove and discard clip securing control lever
to wastegate spindle.
5.Remove turbocharger actuator.
Refit
6.Fit the replacement actuator and secure with
nuts.
7.Push the control lever as far as possible towards
the actuator and apply pressure to keep the
lever in this position.
8.Pressurise the actuator to 57 - 62 cm Hg and
hold this pressure.
CAUTION: Use only the threaded end of
the lever to make adjustments. Forcing the
complete lever in or out will change the
calibration with the possibility of damaging engine
boost.
9.Screw the lever in either direction until the eye
on the end will locate easily over the wastegate
spindle and secure with a new clip.
10.Release the pressure and tighten the locknut.
11.Refit exhaust manifold and turbocharger.
See
MANIFOLD AND EXHAUST SYSTEM, Repair,
Exhaust Manifold - Tdi
TURBOCHARGER AND GASKET
Service repair no - Turbocharger - 19.42.01
Service repair no - Gasket - 19.42.25
Remove
1.Disconnect battery negative lead.
2.Remove air cleaner assembly.
See Air Cleaner
3.Remove exhaust manifold assembly.See
MANIFOLD AND EXHAUST SYSTEM, Repair,
Exhaust Manifold - Tdi
4.Remove and discard clip securing control lever
to wastegate spindle.
5.Remove 4 bolts and 2 clamp plates securing
turbocharger to exhaust manifold.
6.Remove turbocharger and discard gaskets.
Refit
7.Clean mating faces of turbocharger and exhaust
manifold.
8.Reverse removal procedure. Use new clip to
secure control lever to wastegate spindle.
Tighten to
45 Nm.
9.Check/top-up engine oil level.
Page 222 of 873
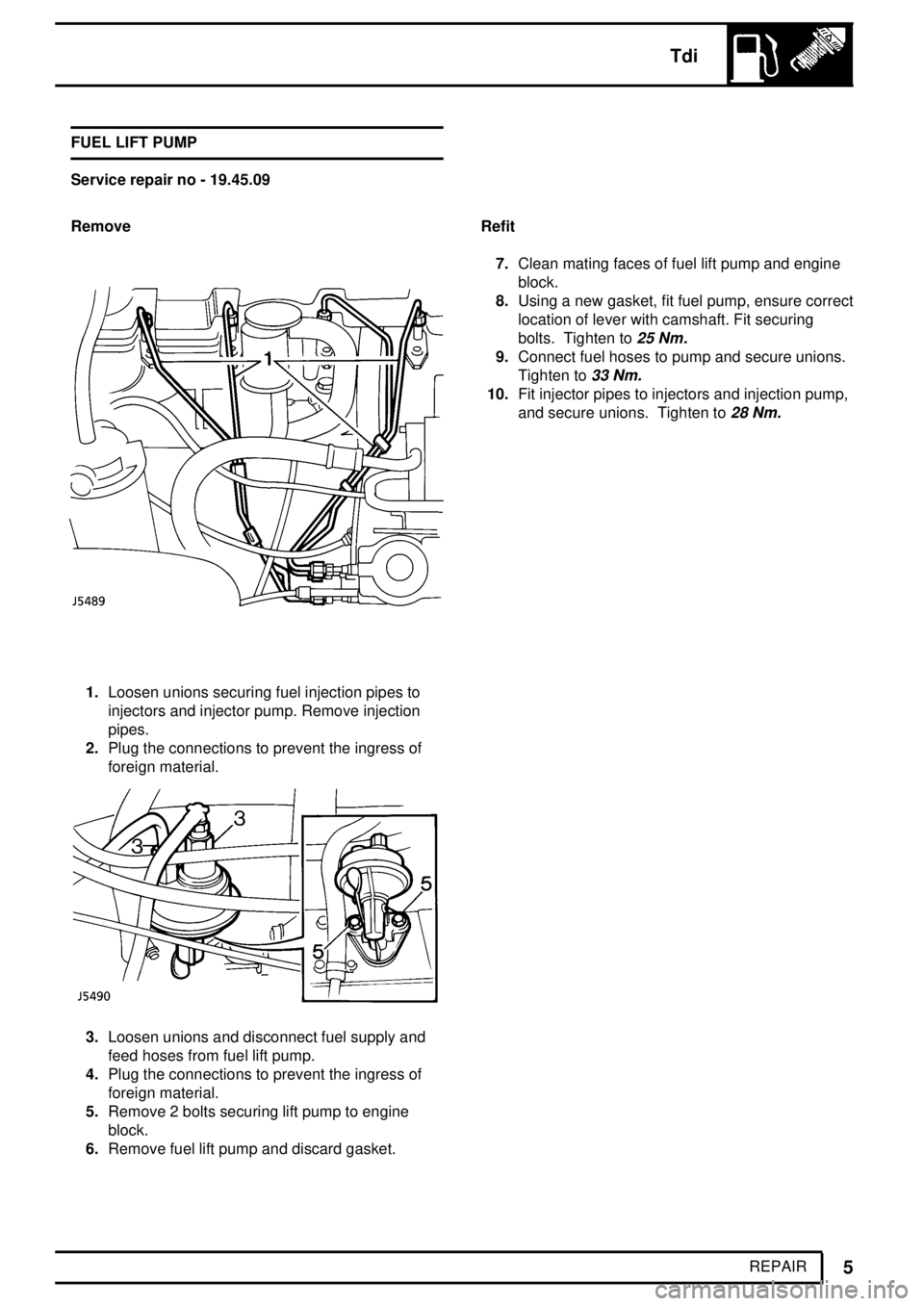
Tdi
5
REPAIR FUEL LIFT PUMP
Service repair no - 19.45.09
Remove
1.Loosen unions securing fuel injection pipes to
injectors and injector pump. Remove injection
pipes.
2.Plug the connections to prevent the ingress of
foreign material.
3.Loosen unions and disconnect fuel supply and
feed hoses from fuel lift pump.
4.Plug the connections to prevent the ingress of
foreign material.
5.Remove 2 bolts securing lift pump to engine
block.
6.Remove fuel lift pump and discard gasket.Refit
7.Clean mating faces of fuel lift pump and engine
block.
8.Using a new gasket, fit fuel pump, ensure correct
location of lever with camshaft. Fit securing
bolts. Tighten to
25 Nm.
9.Connect fuel hoses to pump and secure unions.
Tighten to
33 Nm.
10.Fit injector pipes to injectors and injection pump,
and secure unions. Tighten to
28 Nm.
Page 223 of 873
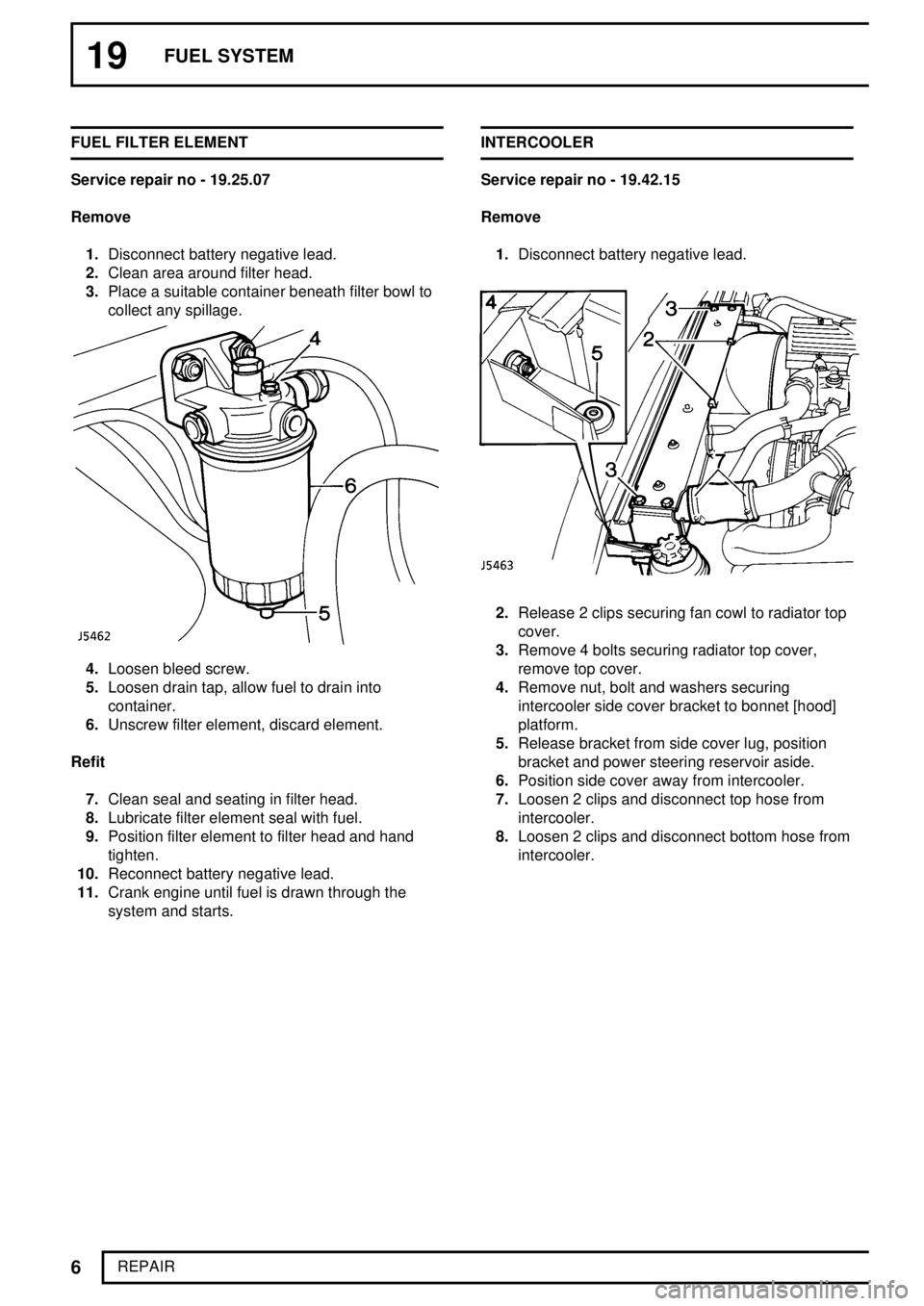
19FUEL SYSTEM
6
REPAIR FUEL FILTER ELEMENT
Service repair no - 19.25.07
Remove
1.Disconnect battery negative lead.
2.Clean area around filter head.
3.Place a suitable container beneath filter bowl to
collect any spillage.
4.Loosen bleed screw.
5.Loosen drain tap, allow fuel to drain into
container.
6.Unscrew filter element, discard element.
Refit
7.Clean seal and seating in filter head.
8.Lubricate filter element seal with fuel.
9.Position filter element to filter head and hand
tighten.
10.Reconnect battery negative lead.
11.Crank engine until fuel is drawn through the
system and starts.INTERCOOLER
Service repair no - 19.42.15
Remove
1.Disconnect battery negative lead.
2.Release 2 clips securing fan cowl to radiator top
cover.
3.Remove 4 bolts securing radiator top cover,
remove top cover.
4.Remove nut, bolt and washers securing
intercooler side cover bracket to bonnet [hood]
platform.
5.Release bracket from side cover lug, position
bracket and power steering reservoir aside.
6.Position side cover away from intercooler.
7.Loosen 2 clips and disconnect top hose from
intercooler.
8.Loosen 2 clips and disconnect bottom hose from
intercooler.
Page 224 of 873
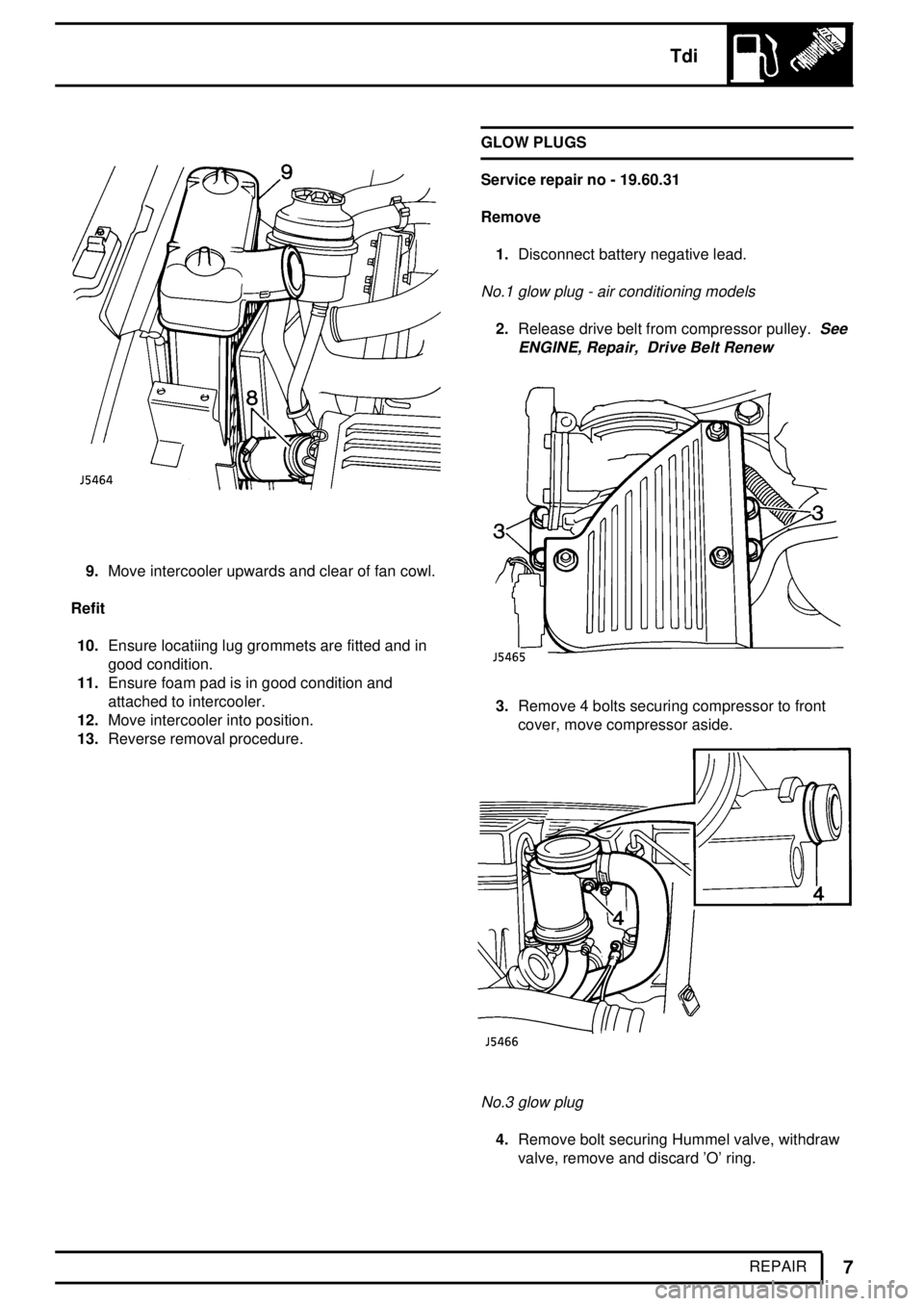
Tdi
7
REPAIR
9.Move intercooler upwards and clear of fan cowl.
Refit
10.Ensure locatiing lug grommets are fitted and in
good condition.
11.Ensure foam pad is in good condition and
attached to intercooler.
12.Move intercooler into position.
13.Reverse removal procedure.GLOW PLUGS
Service repair no - 19.60.31
Remove
1.Disconnect battery negative lead.
No.1 glow plug - air conditioning models
2.Release drive belt from compressor pulley.See
ENGINE, Repair, Drive Belt Renew
3.Remove 4 bolts securing compressor to front
cover, move compressor aside.
No.3 glow plug
4.Remove bolt securing Hummel valve, withdraw
valve, remove and discard 'O' ring.
Page 225 of 873
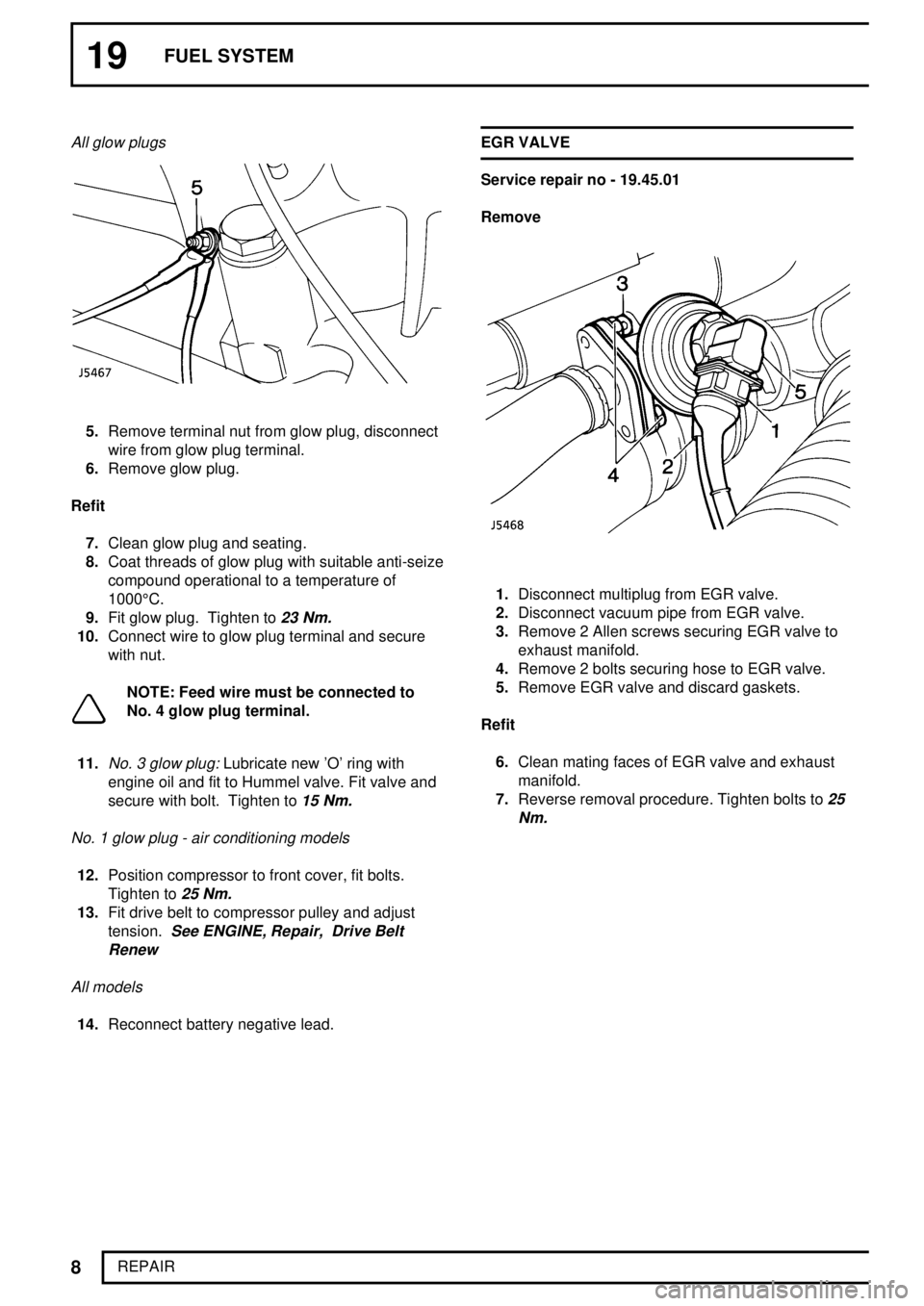
19FUEL SYSTEM
8
REPAIR
All glow plugs
5.Remove terminal nut from glow plug, disconnect
wire from glow plug terminal.
6.Remove glow plug.
Refit
7.Clean glow plug and seating.
8.Coat threads of glow plug with suitable anti-seize
compound operational to a temperature of
1000°C.
9.Fit glow plug. Tighten to
23 Nm.
10.Connect wire to glow plug terminal and secure
with nut.
NOTE: Feed wire must be connected to
No. 4 glow plug terminal.
11.
No. 3 glow plug:Lubricate new 'O' ring with
engine oil and fit to Hummel valve. Fit valve and
secure with bolt. Tighten to
15 Nm.
No. 1 glow plug - air conditioning models
12.Position compressor to front cover, fit bolts.
Tighten to
25 Nm.
13.Fit drive belt to compressor pulley and adjust
tension.
See ENGINE, Repair, Drive Belt
Renew
All models
14.Reconnect battery negative lead.EGR VALVE
Service repair no - 19.45.01
Remove
1.Disconnect multiplug from EGR valve.
2.Disconnect vacuum pipe from EGR valve.
3.Remove 2 Allen screws securing EGR valve to
exhaust manifold.
4.Remove 2 bolts securing hose to EGR valve.
5.Remove EGR valve and discard gaskets.
Refit
6.Clean mating faces of EGR valve and exhaust
manifold.
7.Reverse removal procedure. Tighten bolts to
25
Nm.
Page 226 of 873
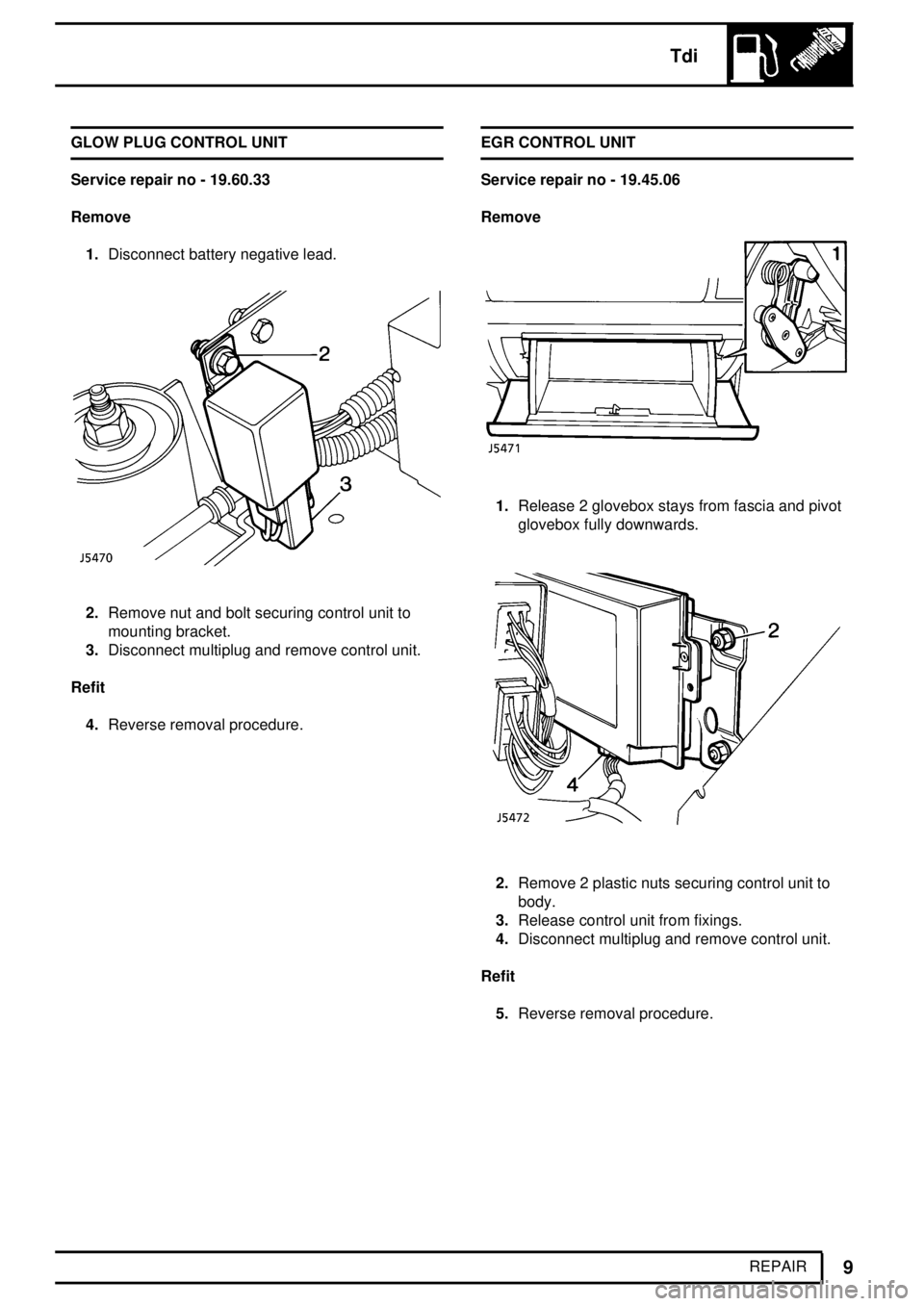
Tdi
9
REPAIR GLOW PLUG CONTROL UNIT
Service repair no - 19.60.33
Remove
1.Disconnect battery negative lead.
2.Remove nut and bolt securing control unit to
mounting bracket.
3.Disconnect multiplug and remove control unit.
Refit
4.Reverse removal procedure.EGR CONTROL UNIT
Service repair no - 19.45.06
Remove
1.Release 2 glovebox stays from fascia and pivot
glovebox fully downwards.
2.Remove 2 plastic nuts securing control unit to
body.
3.Release control unit from fixings.
4.Disconnect multiplug and remove control unit.
Refit
5.Reverse removal procedure.
Page 227 of 873
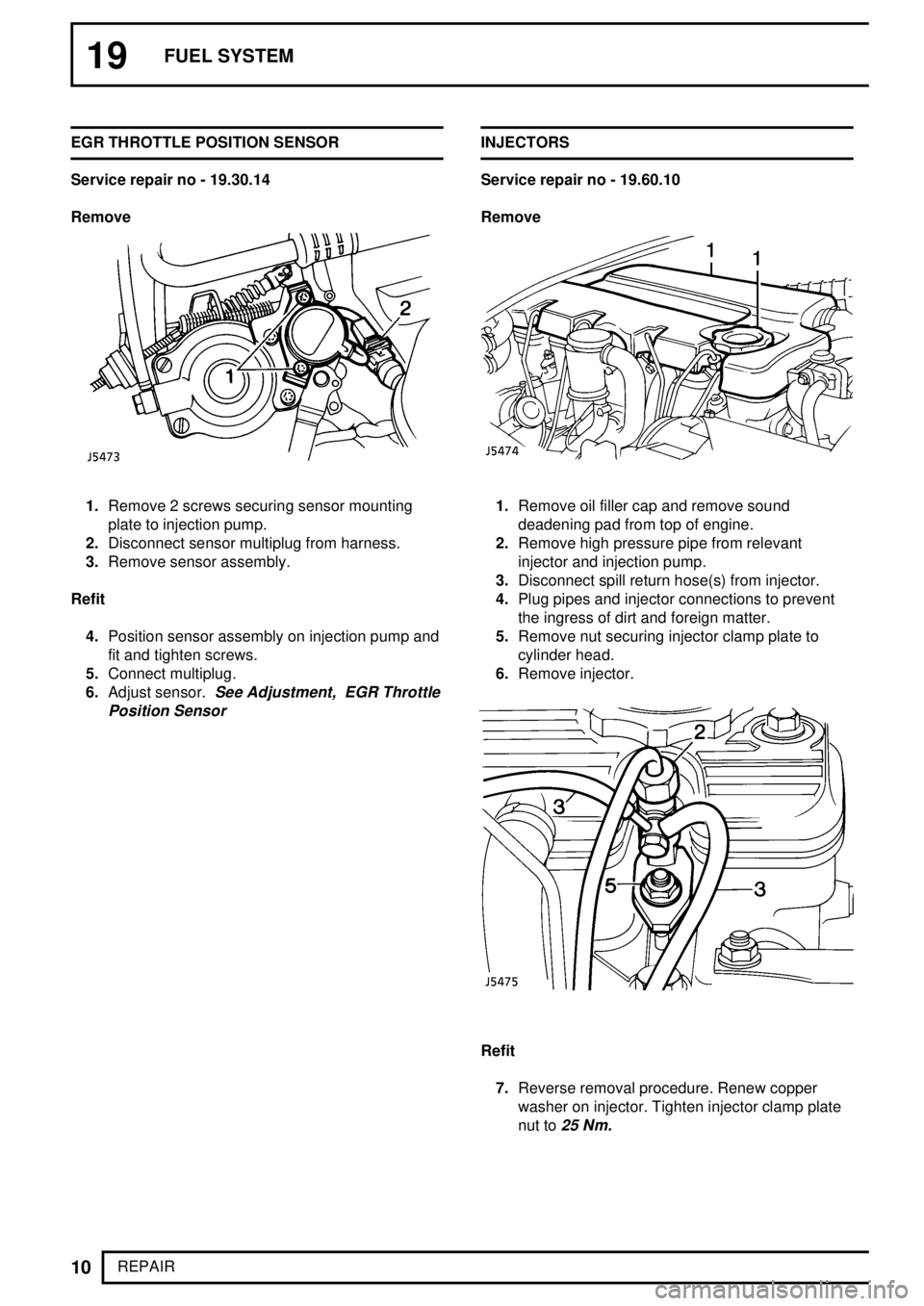
19FUEL SYSTEM
10
REPAIR EGR THROTTLE POSITION SENSOR
Service repair no - 19.30.14
Remove
1.Remove 2 screws securing sensor mounting
plate to injection pump.
2.Disconnect sensor multiplug from harness.
3.Remove sensor assembly.
Refit
4.Position sensor assembly on injection pump and
fit and tighten screws.
5.Connect multiplug.
6.Adjust sensor.
See Adjustment, EGR Throttle
Position Sensor
INJECTORS
Service repair no - 19.60.10
Remove
1.Remove oil filler cap and remove sound
deadening pad from top of engine.
2.Remove high pressure pipe from relevant
injector and injection pump.
3.Disconnect spill return hose(s) from injector.
4.Plug pipes and injector connections to prevent
the ingress of dirt and foreign matter.
5.Remove nut securing injector clamp plate to
cylinder head.
6.Remove injector.
Refit
7.Reverse removal procedure. Renew copper
washer on injector. Tighten injector clamp plate
nut to
25 Nm.
Page 228 of 873
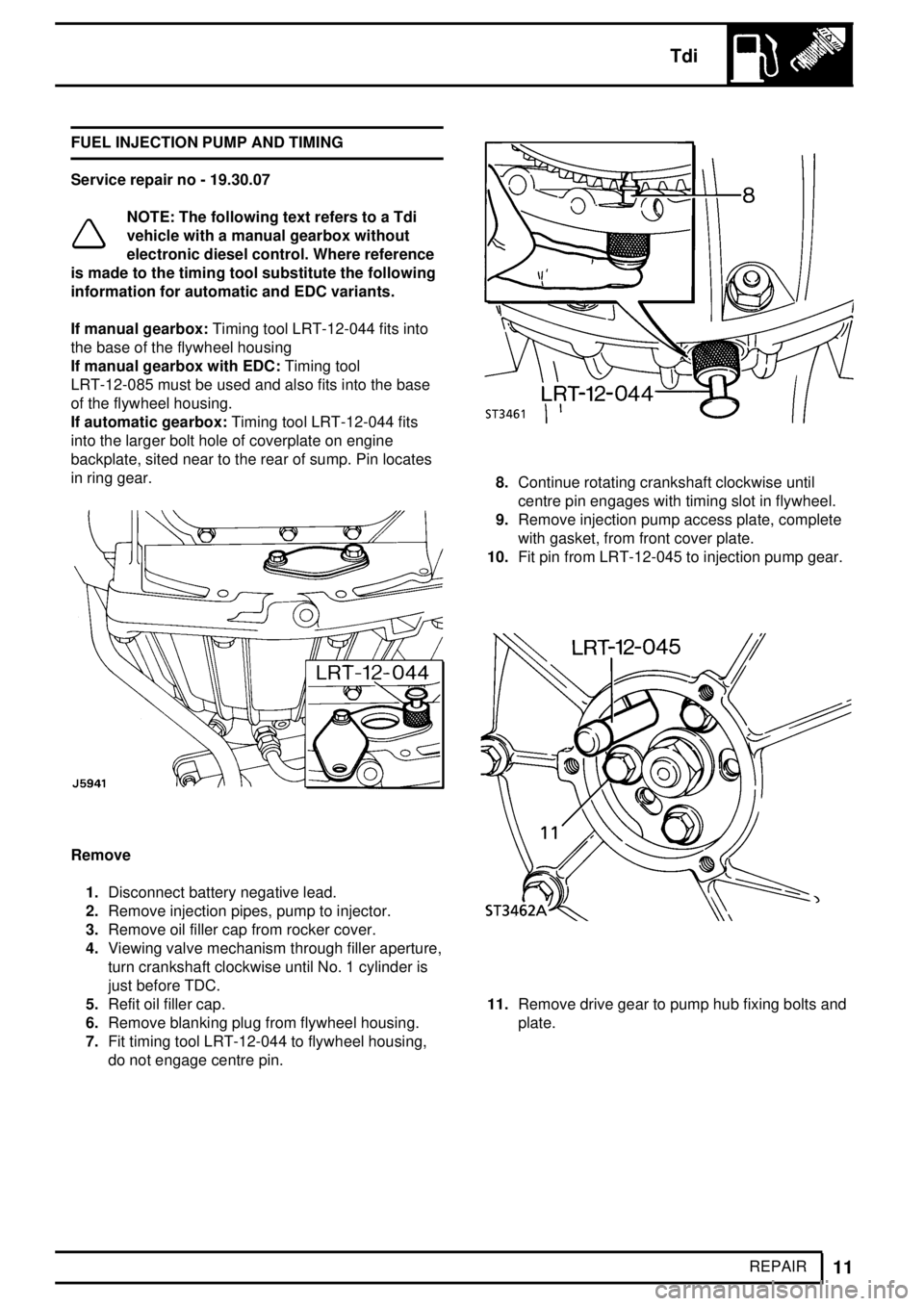
Tdi
11
REPAIR FUEL INJECTION PUMP AND TIMING
Service repair no - 19.30.07
NOTE: The following text refers to a Tdi
vehicle with a manual gearbox without
electronic diesel control. Where reference
is made to the timing tool substitute the following
information for automatic and EDC variants.
If manual gearbox:Timing tool LRT-12-044 fits into
the base of the flywheel housing
If manual gearbox with EDC:Timing tool
LRT-12-085 must be used and also fits into the base
of the flywheel housing.
If automatic gearbox:Timing tool LRT-12-044 fits
into the larger bolt hole of coverplate on engine
backplate, sited near to the rear of sump. Pin locates
in ring gear.
Remove
1.Disconnect battery negative lead.
2.Remove injection pipes, pump to injector.
3.Remove oil filler cap from rocker cover.
4.Viewing valve mechanism through filler aperture,
turn crankshaft clockwise until No. 1 cylinder is
just before TDC.
5.Refit oil filler cap.
6.Remove blanking plug from flywheel housing.
7.Fit timing tool LRT-12-044 to flywheel housing,
do not engage centre pin.
8.Continue rotating crankshaft clockwise until
centre pin engages with timing slot in flywheel.
9.Remove injection pump access plate, complete
with gasket, from front cover plate.
10.Fit pin from LRT-12-045 to injection pump gear.
11.Remove drive gear to pump hub fixing bolts and
plate.
Page 229 of 873
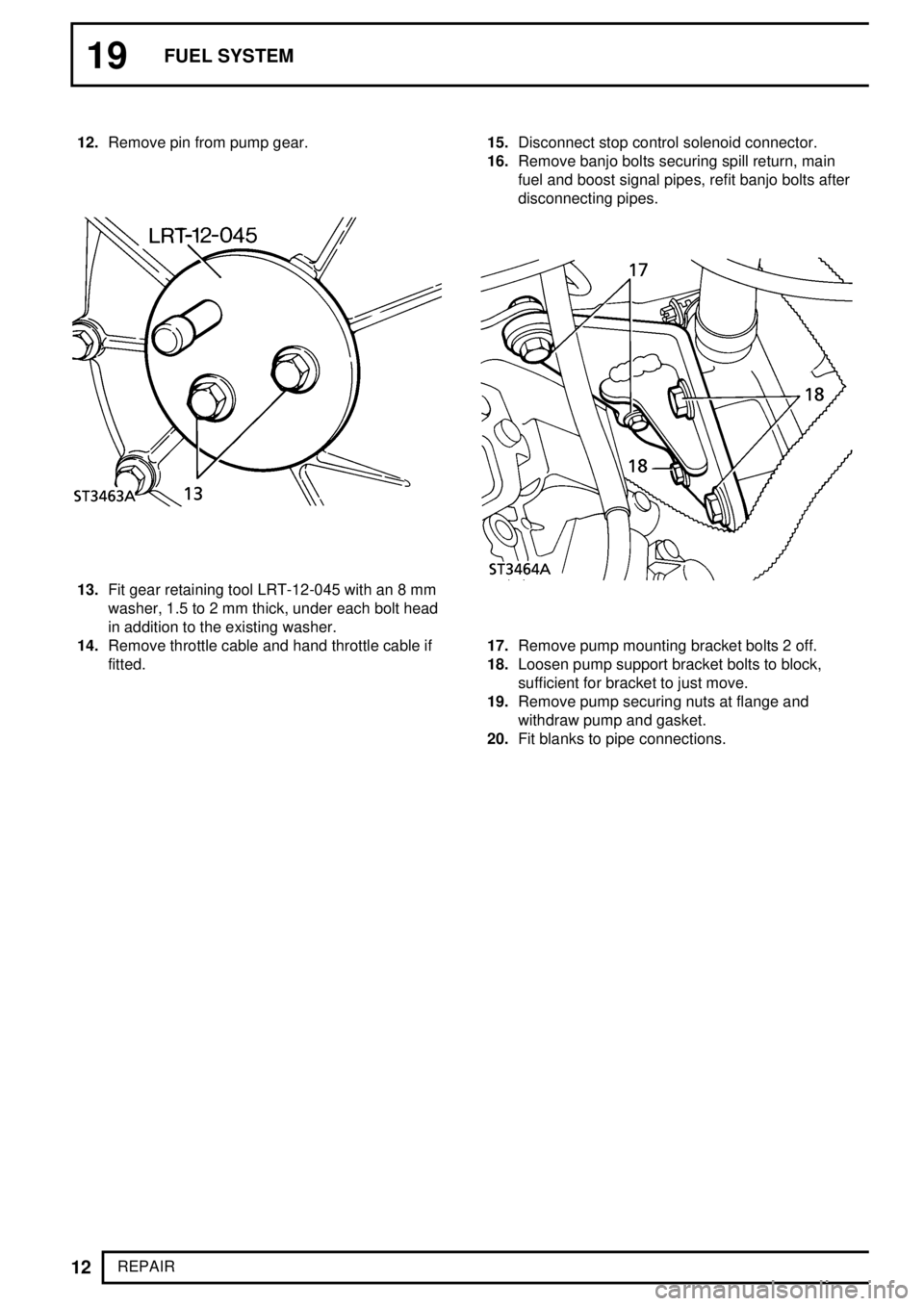
19FUEL SYSTEM
12
REPAIR 12.Remove pin from pump gear.
13.Fit gear retaining tool LRT-12-045 with an 8 mm
washer, 1.5 to 2 mm thick, under each bolt head
in addition to the existing washer.
14.Remove throttle cable and hand throttle cable if
fitted.15.Disconnect stop control solenoid connector.
16.Remove banjo bolts securing spill return, main
fuel and boost signal pipes, refit banjo bolts after
disconnecting pipes.
17.Remove pump mounting bracket bolts 2 off.
18.Loosen pump support bracket bolts to block,
sufficient for bracket to just move.
19.Remove pump securing nuts at flange and
withdraw pump and gasket.
20.Fit blanks to pipe connections.
Page 230 of 873
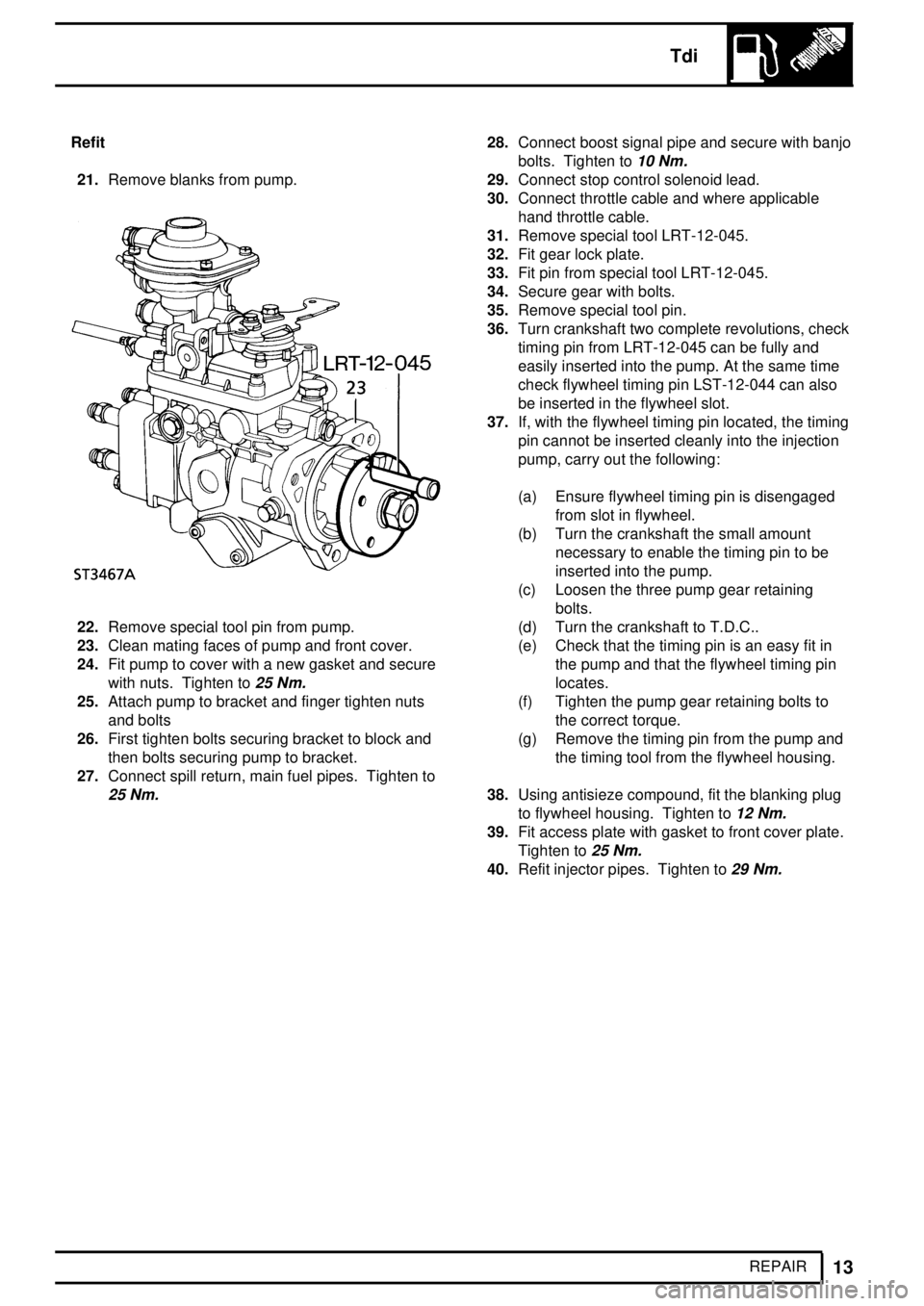
Tdi
13
REPAIR Refit
21.Remove blanks from pump.
22.Remove special tool pin from pump.
23.Clean mating faces of pump and front cover.
24.Fit pump to cover with a new gasket and secure
with nuts. Tighten to
25 Nm.
25.Attach pump to bracket and finger tighten nuts
and bolts
26.First tighten bolts securing bracket to block and
then bolts securing pump to bracket.
27.Connect spill return, main fuel pipes. Tighten to
25 Nm.
28.Connect boost signal pipe and secure with banjo
bolts. Tighten to
10 Nm.
29.Connect stop control solenoid lead.
30.Connect throttle cable and where applicable
hand throttle cable.
31.Remove special tool LRT-12-045.
32.Fit gear lock plate.
33.Fit pin from special tool LRT-12-045.
34.Secure gear with bolts.
35.Remove special tool pin.
36.Turn crankshaft two complete revolutions, check
timing pin from LRT-12-045 can be fully and
easily inserted into the pump. At the same time
check flywheel timing pin LST-12-044 can also
be inserted in the flywheel slot.
37.If, with the flywheel timing pin located, the timing
pin cannot be inserted cleanly into the injection
pump, carry out the following:
(a) Ensure flywheel timing pin is disengaged
from slot in flywheel.
(b) Turn the crankshaft the small amount
necessary to enable the timing pin to be
inserted into the pump.
(c) Loosen the three pump gear retaining
bolts.
(d) Turn the crankshaft to T.D.C..
(e) Check that the timing pin is an easy fit in
the pump and that the flywheel timing pin
locates.
(f) Tighten the pump gear retaining bolts to
the correct torque.
(g) Remove the timing pin from the pump and
the timing tool from the flywheel housing.
38.Using antisieze compound, fit the blanking plug
to flywheel housing. Tighten to
12 Nm.
39.Fit access plate with gasket to front cover plate.
Tighten to
25 Nm.
40.Refit injector pipes. Tighten to29 Nm.