LAND ROVER DISCOVERY 1995 Workshop Manual
Manufacturer: LAND ROVER, Model Year: 1995, Model line: DISCOVERY, Model: LAND ROVER DISCOVERY 1995Pages: 873, PDF Size: 12.89 MB
Page 191 of 873
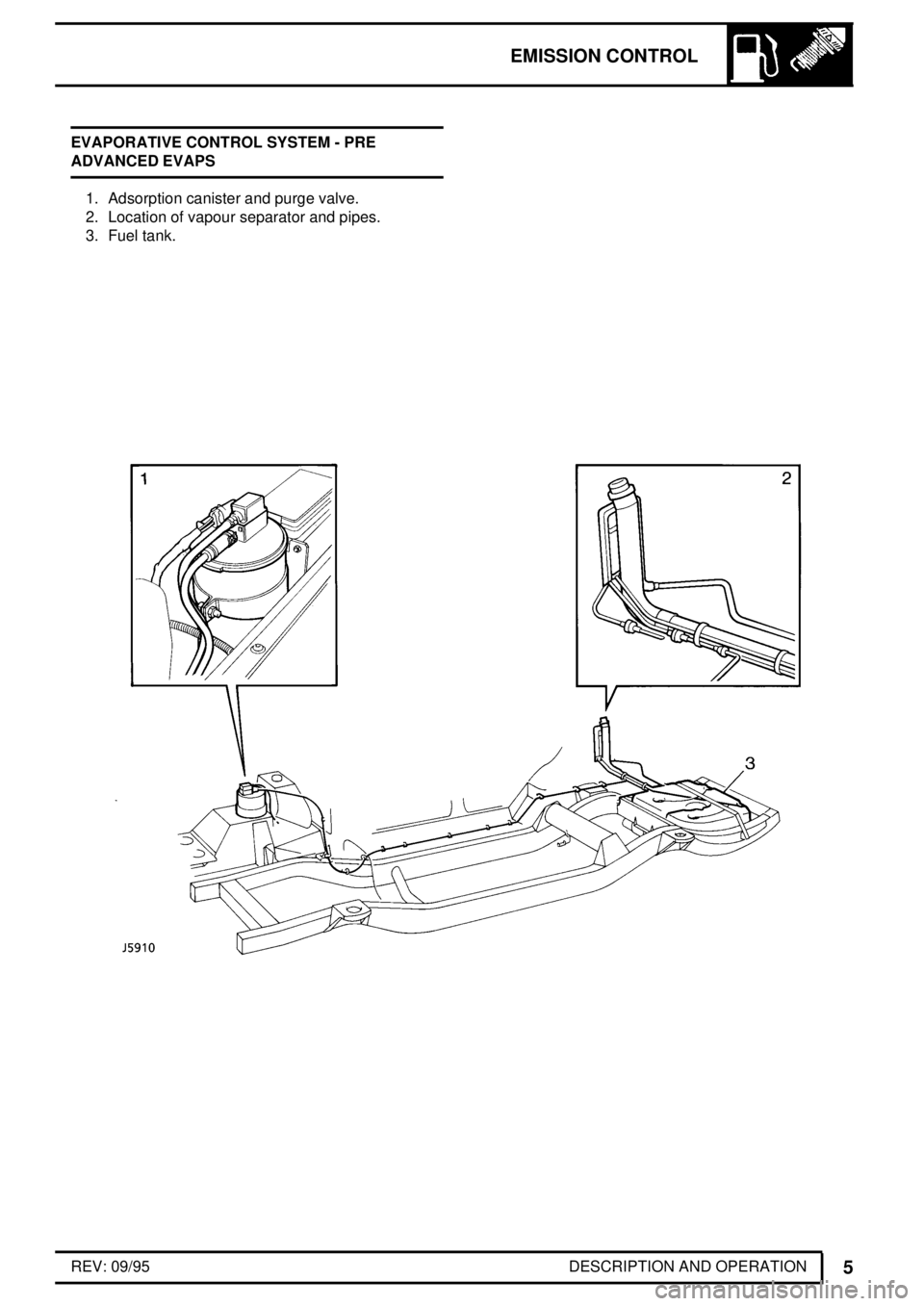
EMISSION CONTROL
5
DESCRIPTION AND OPERATION REV: 09/95 EVAPORATIVE CONTROL SYSTEM - PRE
ADVANCED EVAPS
1. Adsorption canister and purge valve.
2. Location of vapour separator and pipes.
3. Fuel tank.
Page 192 of 873
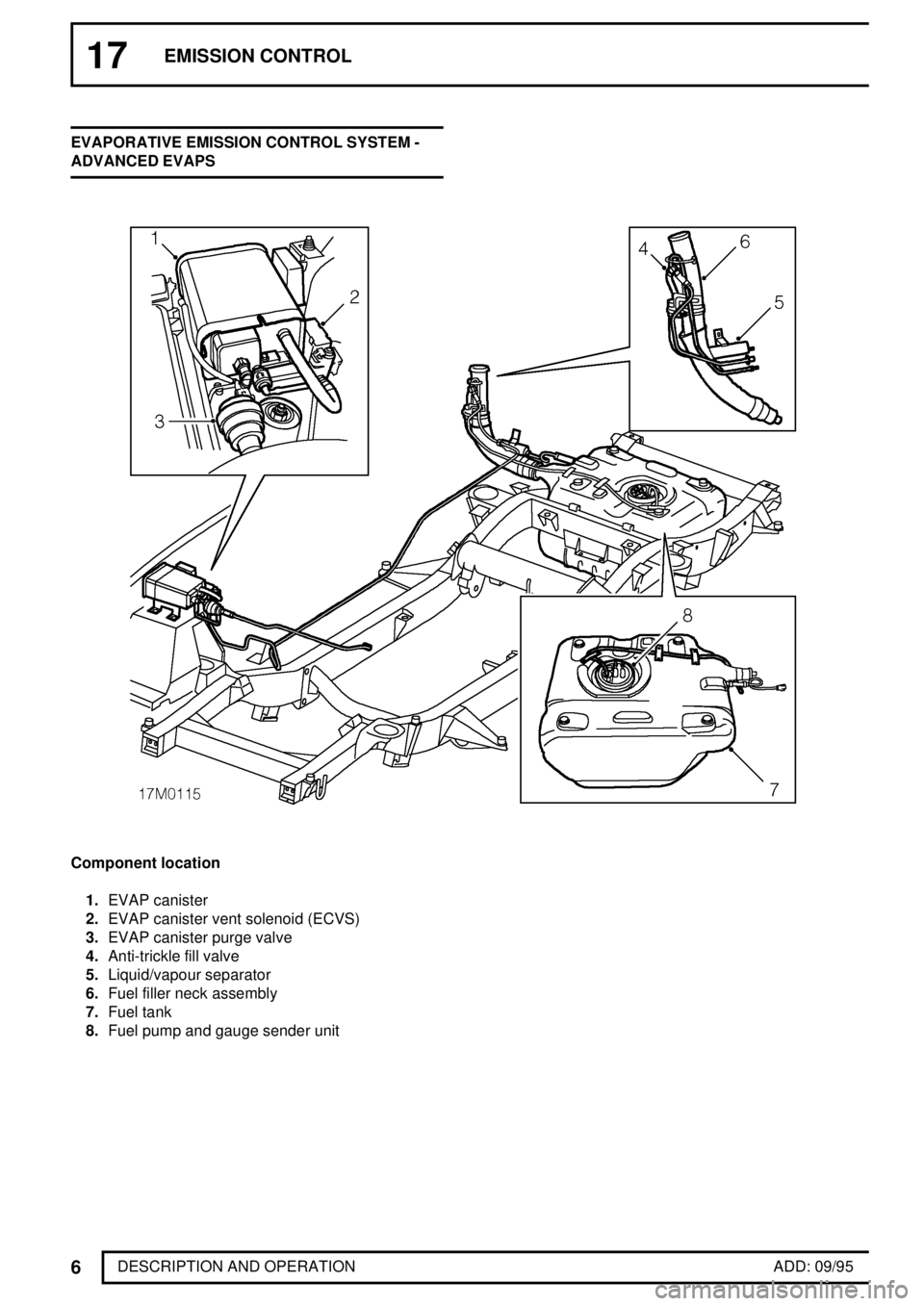
17EMISSION CONTROL
6
DESCRIPTION AND OPERATION ADD: 09/95 EVAPORATIVE EMISSION CONTROL SYSTEM -
ADVANCED EVAPS
Component location
1.EVAP canister
2.EVAP canister vent solenoid (ECVS)
3.EVAP canister purge valve
4.Anti-trickle fill valve
5.Liquid/vapour separator
6.Fuel filler neck assembly
7.Fuel tank
8.Fuel pump and gauge sender unit
Page 193 of 873
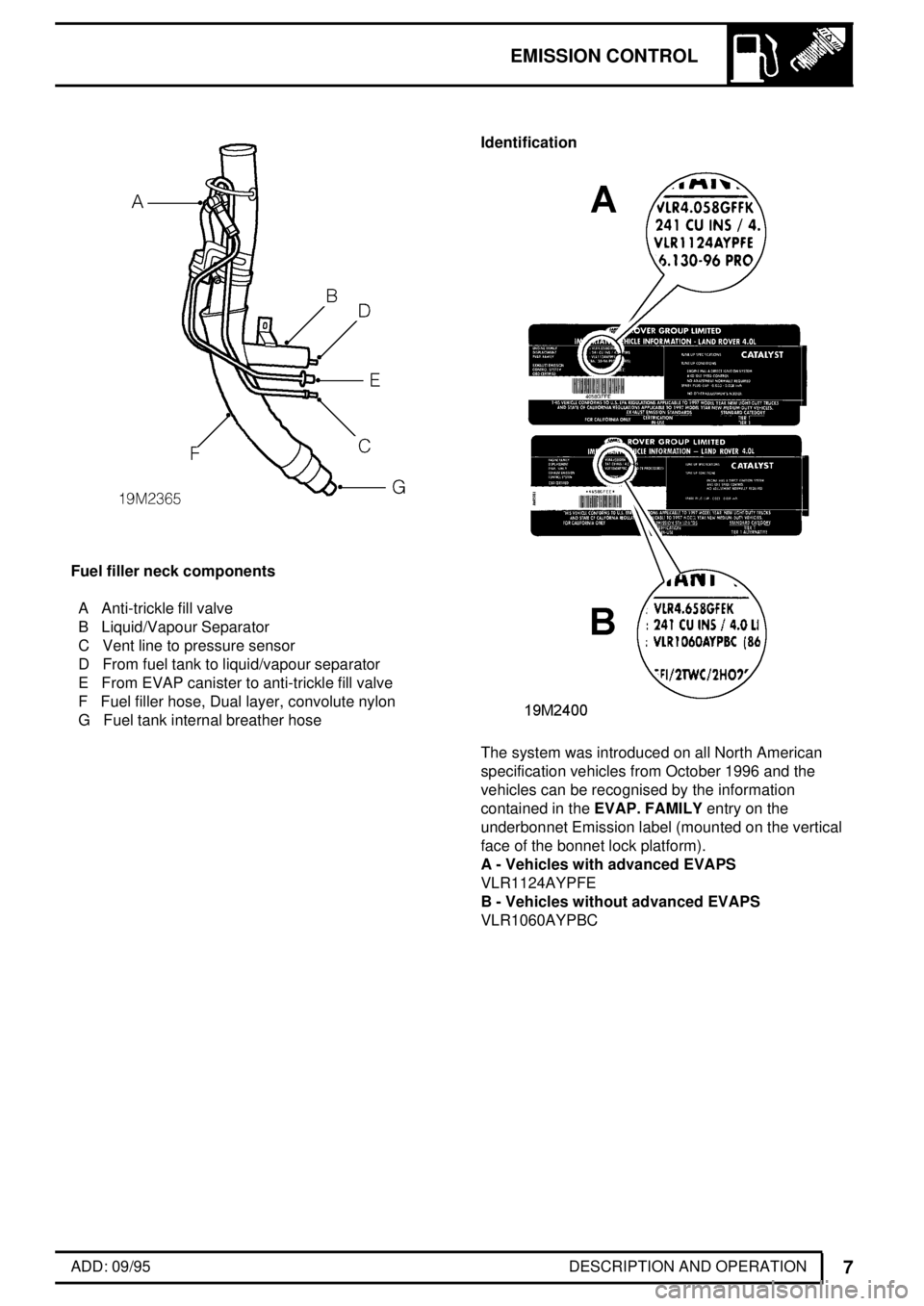
EMISSION CONTROL
7
DESCRIPTION AND OPERATION ADD: 09/95
Fuel filler neck components
A Anti-trickle fill valve
B Liquid/Vapour Separator
C Vent line to pressure sensor
D From fuel tank to liquid/vapour separator
E From EVAP canister to anti-trickle fill valve
F Fuel filler hose, Dual layer, convolute nylon
G Fuel tank internal breather hoseIdentification
The system was introduced on all North American
specification vehicles from October 1996 and the
vehicles can be recognised by the information
contained in theEVAP. FAMILYentry on the
underbonnet Emission label (mounted on the vertical
face of the bonnet lock platform).
A - Vehicles with advanced EVAPS
VLR1124AYPFE
B - Vehicles without advanced EVAPS
VLR1060AYPBC
Page 194 of 873
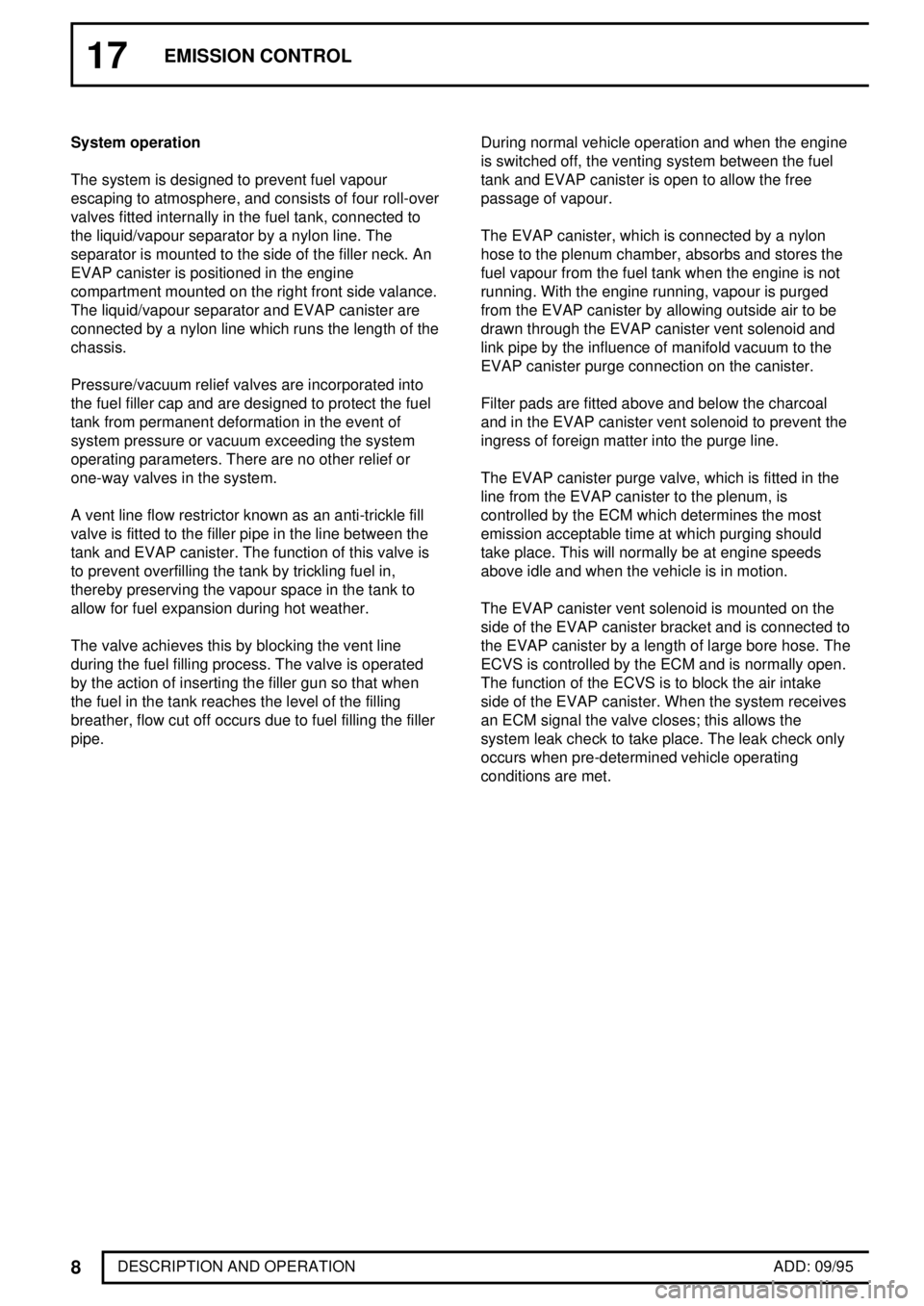
17EMISSION CONTROL
8
DESCRIPTION AND OPERATION ADD: 09/95 System operation
The system is designed to prevent fuel vapour
escaping to atmosphere, and consists of four roll-over
valves fitted internally in the fuel tank, connected to
the liquid/vapour separator by a nylon line. The
separator is mounted to the side of the filler neck. An
EVAP canister is positioned in the engine
compartment mounted on the right front side valance.
The liquid/vapour separator and EVAP canister are
connected by a nylon line which runs the length of the
chassis.
Pressure/vacuum relief valves are incorporated into
the fuel filler cap and are designed to protect the fuel
tank from permanent deformation in the event of
system pressure or vacuum exceeding the system
operating parameters. There are no other relief or
one-way valves in the system.
A vent line flow restrictor known as an anti-trickle fill
valve is fitted to the filler pipe in the line between the
tank and EVAP canister. The function of this valve is
to prevent overfilling the tank by trickling fuel in,
thereby preserving the vapour space in the tank to
allow for fuel expansion during hot weather.
The valve achieves this by blocking the vent line
during the fuel filling process. The valve is operated
by the action of inserting the filler gun so that when
the fuel in the tank reaches the level of the filling
breather, flow cut off occurs due to fuel filling the filler
pipe.During normal vehicle operation and when the engine
is switched off, the venting system between the fuel
tank and EVAP canister is open to allow the free
passage of vapour.
The EVAP canister, which is connected by a nylon
hose to the plenum chamber, absorbs and stores the
fuel vapour from the fuel tank when the engine is not
running. With the engine running, vapour is purged
from the EVAP canister by allowing outside air to be
drawn through the EVAP canister vent solenoid and
link pipe by the influence of manifold vacuum to the
EVAP canister purge connection on the canister.
Filter pads are fitted above and below the charcoal
and in the EVAP canister vent solenoid to prevent the
ingress of foreign matter into the purge line.
The EVAP canister purge valve, which is fitted in the
line from the EVAP canister to the plenum, is
controlled by the ECM which determines the most
emission acceptable time at which purging should
take place. This will normally be at engine speeds
above idle and when the vehicle is in motion.
The EVAP canister vent solenoid is mounted on the
side of the EVAP canister bracket and is connected to
the EVAP canister by a length of large bore hose. The
ECVS is controlled by the ECM and is normally open.
The function of the ECVS is to block the air intake
side of the EVAP canister. When the system receives
an ECM signal the valve closes; this allows the
system leak check to take place. The leak check only
occurs when pre-determined vehicle operating
conditions are met.
Page 195 of 873
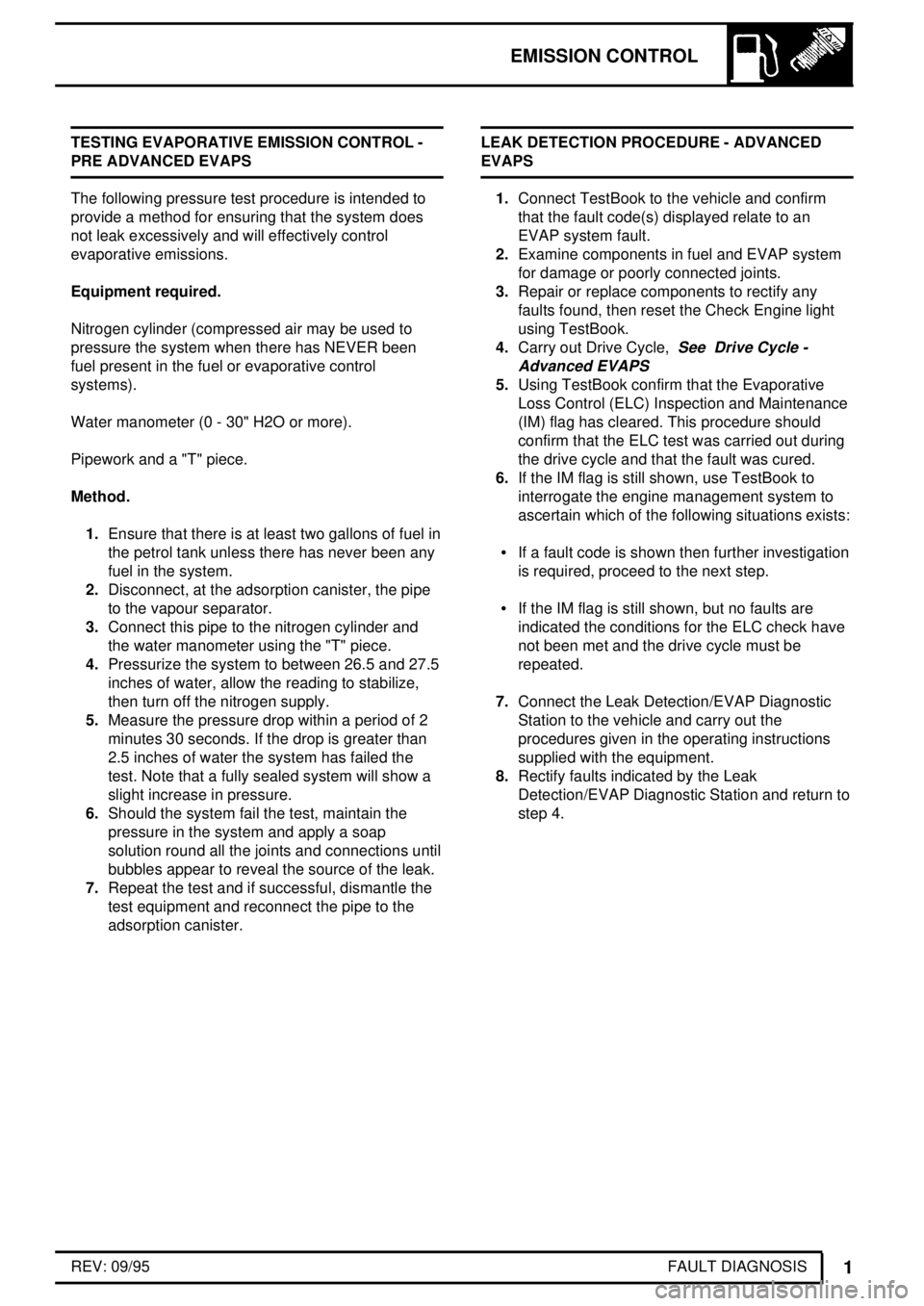
EMISSION CONTROL
1
FAULT DIAGNOSIS REV: 09/95 TESTING EVAPORATIVE EMISSION CONTROL -
PRE ADVANCED EVAPS
The following pressure test procedure is intended to
provide a method for ensuring that the system does
not leak excessively and will effectively control
evaporative emissions.
Equipment required.
Nitrogen cylinder (compressed air may be used to
pressure the system when there has NEVER been
fuel present in the fuel or evaporative control
systems).
Water manometer (0 - 30" H2O or more).
Pipework and a "T" piece.
Method.
1.Ensure that there is at least two gallons of fuel in
the petrol tank unless there has never been any
fuel in the system.
2.Disconnect, at the adsorption canister, the pipe
to the vapour separator.
3.Connect this pipe to the nitrogen cylinder and
the water manometer using the "T" piece.
4.Pressurize the system to between 26.5 and 27.5
inches of water, allow the reading to stabilize,
then turn off the nitrogen supply.
5.Measure the pressure drop within a period of 2
minutes 30 seconds. If the drop is greater than
2.5 inches of water the system has failed the
test. Note that a fully sealed system will show a
slight increase in pressure.
6.Should the system fail the test, maintain the
pressure in the system and apply a soap
solution round all the joints and connections until
bubbles appear to reveal the source of the leak.
7.Repeat the test and if successful, dismantle the
test equipment and reconnect the pipe to the
adsorption canister.LEAK DETECTION PROCEDURE - ADVANCED
EVAPS
1.Connect TestBook to the vehicle and confirm
that the fault code(s) displayed relate to an
EVAP system fault.
2.Examine components in fuel and EVAP system
for damage or poorly connected joints.
3.Repair or replace components to rectify any
faults found, then reset the Check Engine light
using TestBook.
4.Carry out Drive Cycle,
See Drive Cycle -
Advanced EVAPS
5.Using TestBook confirm that the Evaporative
Loss Control (ELC) Inspection and Maintenance
(IM) flag has cleared. This procedure should
confirm that the ELC test was carried out during
the drive cycle and that the fault was cured.
6.If the IM flag is still shown, use TestBook to
interrogate the engine management system to
ascertain which of the following situations exists:
·If a fault code is shown then further investigation
is required, proceed to the next step.
·If the IM flag is still shown, but no faults are
indicated the conditions for the ELC check have
not been met and the drive cycle must be
repeated.
7.Connect the Leak Detection/EVAP Diagnostic
Station to the vehicle and carry out the
procedures given in the operating instructions
supplied with the equipment.
8.Rectify faults indicated by the Leak
Detection/EVAP Diagnostic Station and return to
step 4.
Page 196 of 873
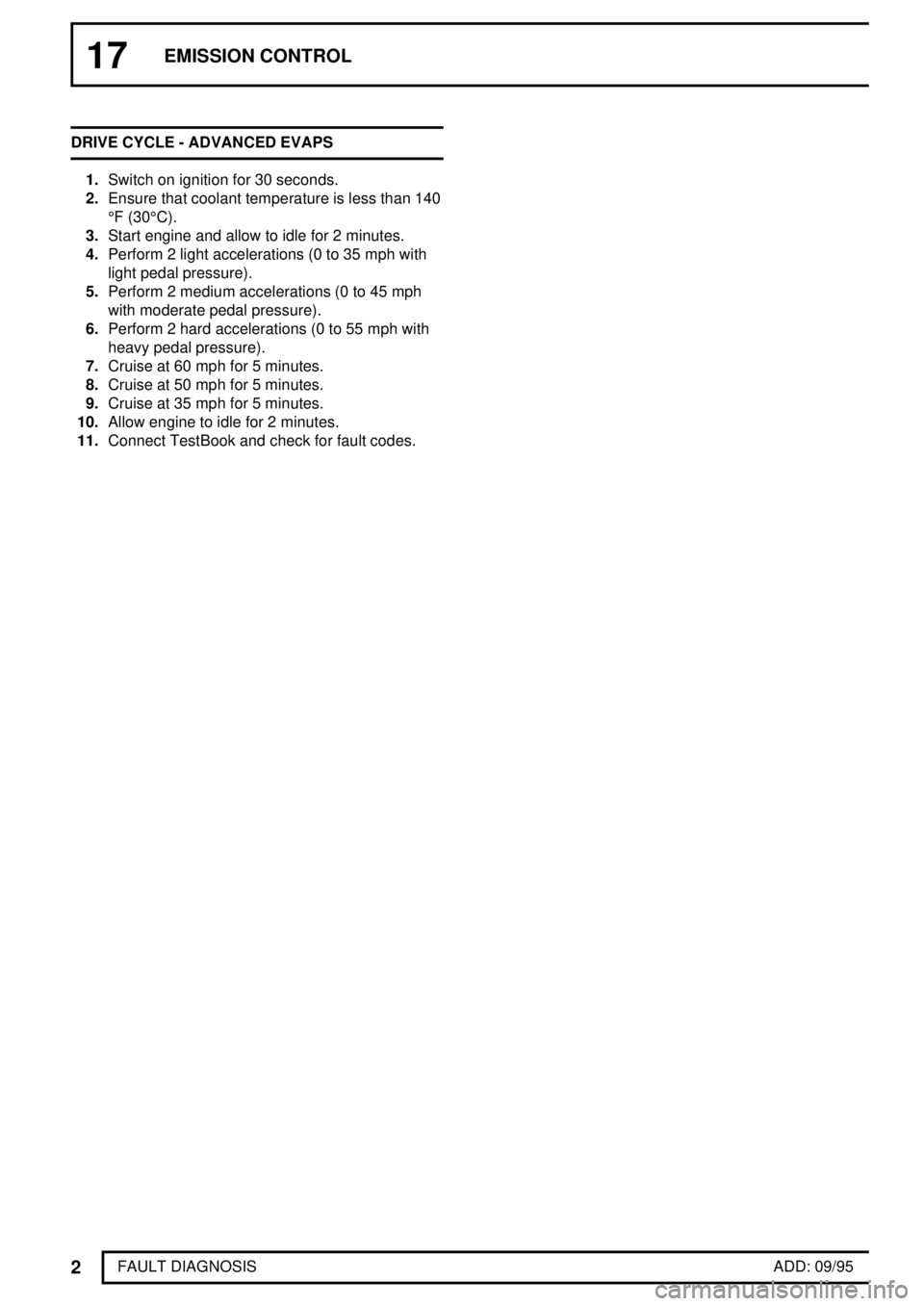
17EMISSION CONTROL
2
FAULT DIAGNOSISADD: 09/95 DRIVE CYCLE - ADVANCED EVAPS
1.Switch on ignition for 30 seconds.
2.Ensure that coolant temperature is less than 140
°F (30°C).
3.Start engine and allow to idle for 2 minutes.
4.Perform 2 light accelerations (0 to 35 mph with
light pedal pressure).
5.Perform 2 medium accelerations (0 to 45 mph
with moderate pedal pressure).
6.Perform 2 hard accelerations (0 to 55 mph with
heavy pedal pressure).
7.Cruise at 60 mph for 5 minutes.
8.Cruise at 50 mph for 5 minutes.
9.Cruise at 35 mph for 5 minutes.
10.Allow engine to idle for 2 minutes.
11.Connect TestBook and check for fault codes.
Page 197 of 873
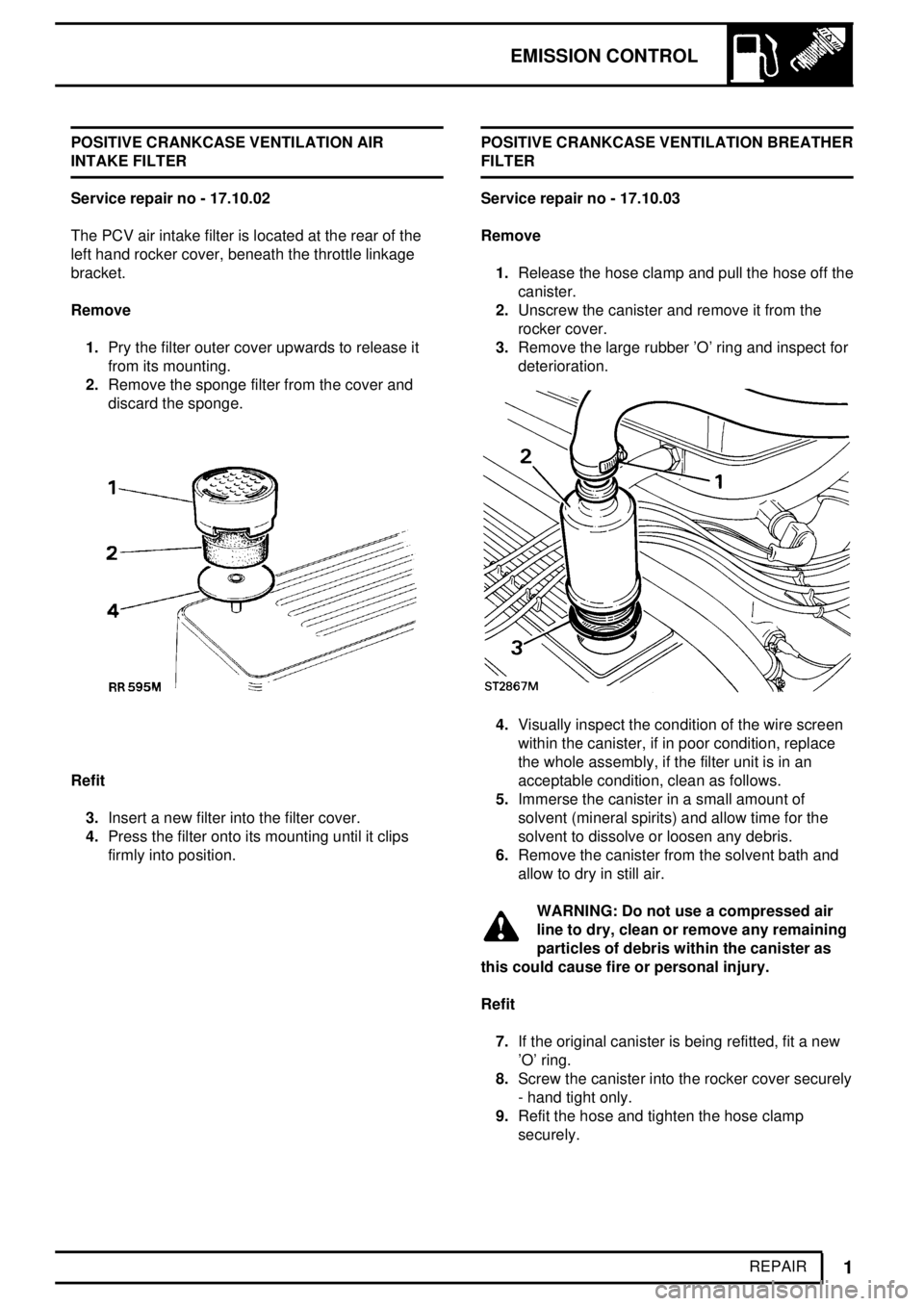
EMISSION CONTROL
1
REPAIR POSITIVE CRANKCASE VENTILATION AIR
INTAKE FILTER
Service repair no - 17.10.02
The PCV air intake filter is located at the rear of the
left hand rocker cover, beneath the throttle linkage
bracket.
Remove
1.Pry the filter outer cover upwards to release it
from its mounting.
2.Remove the sponge filter from the cover and
discard the sponge.
Refit
3.Insert a new filter into the filter cover.
4.Press the filter onto its mounting until it clips
firmly into position.POSITIVE CRANKCASE VENTILATION BREATHER
FILTER
Service repair no - 17.10.03
Remove
1.Release the hose clamp and pull the hose off the
canister.
2.Unscrew the canister and remove it from the
rocker cover.
3.Remove the large rubber 'O' ring and inspect for
deterioration.
4.Visually inspect the condition of the wire screen
within the canister, if in poor condition, replace
the whole assembly, if the filter unit is in an
acceptable condition, clean as follows.
5.Immerse the canister in a small amount of
solvent (mineral spirits) and allow time for the
solvent to dissolve or loosen any debris.
6.Remove the canister from the solvent bath and
allow to dry in still air.
WARNING: Do not use a compressed air
line to dry, clean or remove any remaining
particles of debris within the canister as
this could cause fire or personal injury.
Refit
7.If the original canister is being refitted, fit a new
'O' ring.
8.Screw the canister into the rocker cover securely
- hand tight only.
9.Refit the hose and tighten the hose clamp
securely.
Page 198 of 873
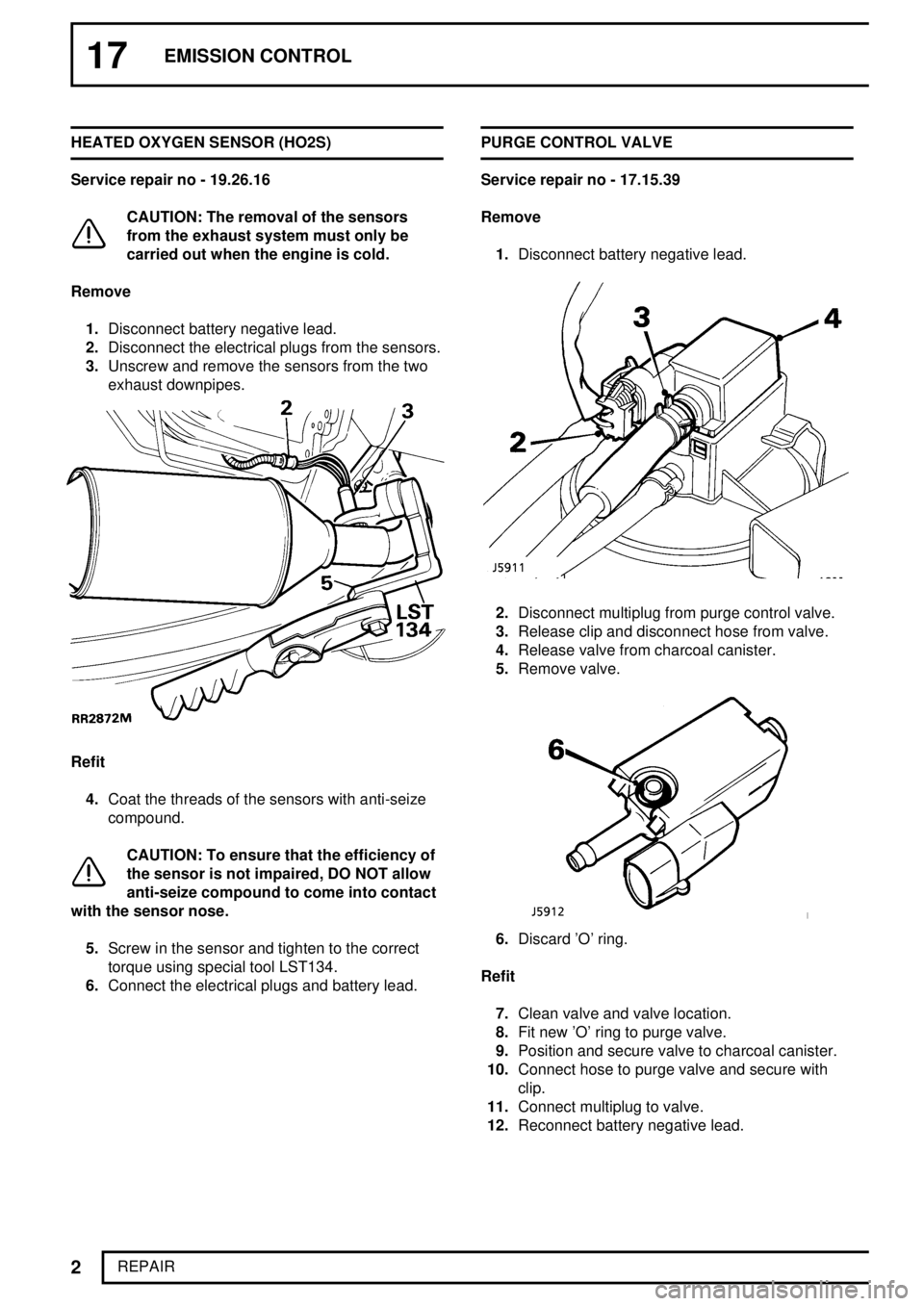
17EMISSION CONTROL
2
REPAIR HEATED OXYGEN SENSOR (HO2S)
Service repair no - 19.26.16
CAUTION: The removal of the sensors
from the exhaust system must only be
carried out when the engine is cold.
Remove
1.Disconnect battery negative lead.
2.Disconnect the electrical plugs from the sensors.
3.Unscrew and remove the sensors from the two
exhaust downpipes.
Refit
4.Coat the threads of the sensors with anti-seize
compound.
CAUTION: To ensure that the efficiency of
the sensor is not impaired, DO NOT allow
anti-seize compound to come into contact
with the sensor nose.
5.Screw in the sensor and tighten to the correct
torque using special tool LST134.
6.Connect the electrical plugs and battery lead.PURGE CONTROL VALVE
Service repair no - 17.15.39
Remove
1.Disconnect battery negative lead.
2.Disconnect multiplug from purge control valve.
3.Release clip and disconnect hose from valve.
4.Release valve from charcoal canister.
5.Remove valve.
6.Discard 'O' ring.
Refit
7.Clean valve and valve location.
8.Fit new 'O' ring to purge valve.
9.Position and secure valve to charcoal canister.
10.Connect hose to purge valve and secure with
clip.
11.Connect multiplug to valve.
12.Reconnect battery negative lead.
Page 199 of 873
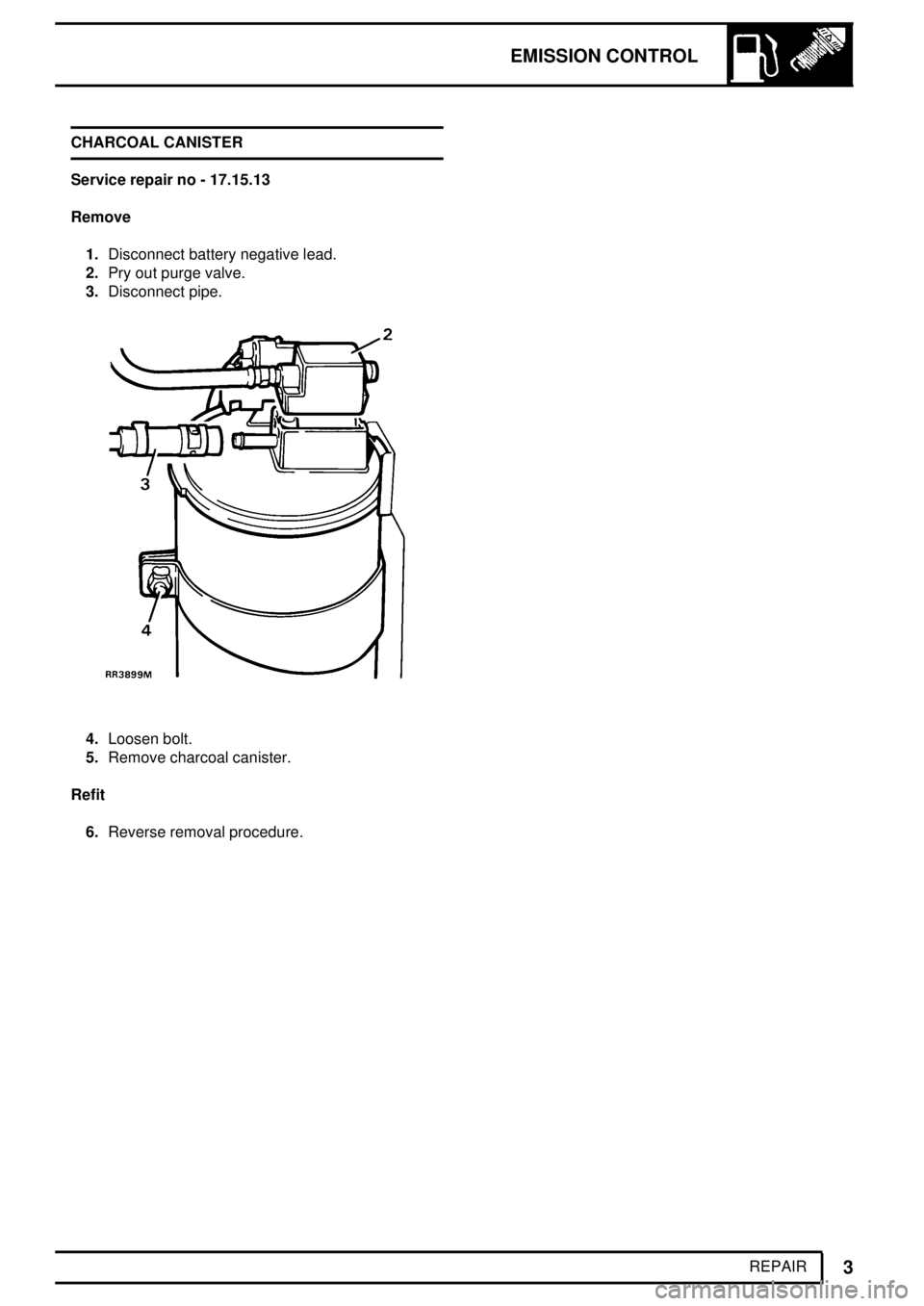
EMISSION CONTROL
3
REPAIR CHARCOAL CANISTER
Service repair no - 17.15.13
Remove
1.Disconnect battery negative lead.
2.Pry out purge valve.
3.Disconnect pipe.
4.Loosen bolt.
5.Remove charcoal canister.
Refit
6.Reverse removal procedure.
Page 200 of 873
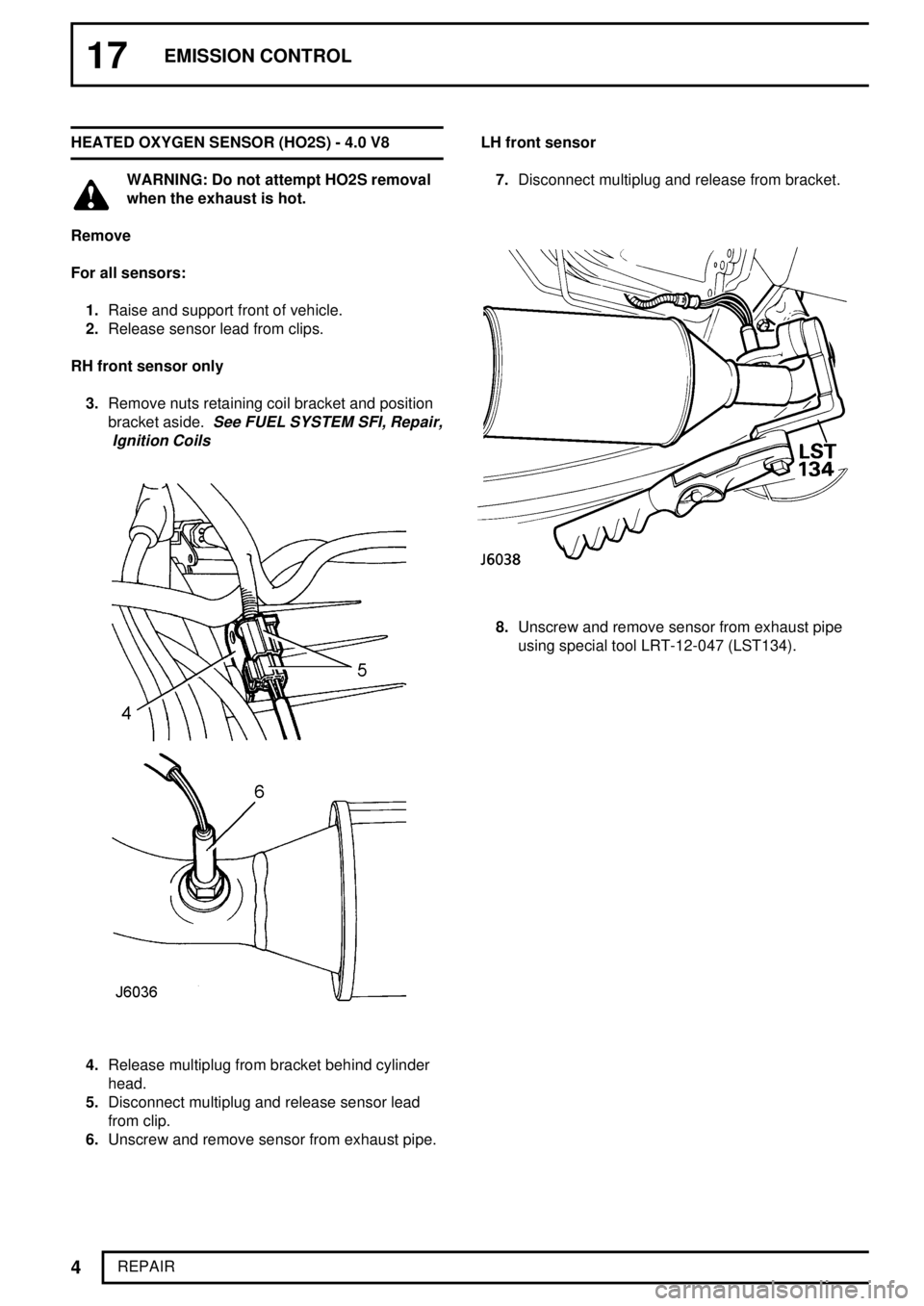
17EMISSION CONTROL
4
REPAIR HEATED OXYGEN SENSOR (HO2S) - 4.0 V8
WARNING: Do not attempt HO2S removal
when the exhaust is hot.
Remove
For all sensors:
1.Raise and support front of vehicle.
2.Release sensor lead from clips.
RH front sensor only
3.Remove nuts retaining coil bracket and position
bracket aside.
See FUEL SYSTEM SFI, Repair,
Ignition Coils
4.Release multiplug from bracket behind cylinder
head.
5.Disconnect multiplug and release sensor lead
from clip.
6.Unscrew and remove sensor from exhaust pipe.LH front sensor
7.Disconnect multiplug and release from bracket.
8.Unscrew and remove sensor from exhaust pipe
using special tool LRT-12-047 (LST134).