LAND ROVER DISCOVERY 1995 Workshop Manual
Manufacturer: LAND ROVER, Model Year: 1995, Model line: DISCOVERY, Model: LAND ROVER DISCOVERY 1995Pages: 873, PDF Size: 12.89 MB
Page 381 of 873
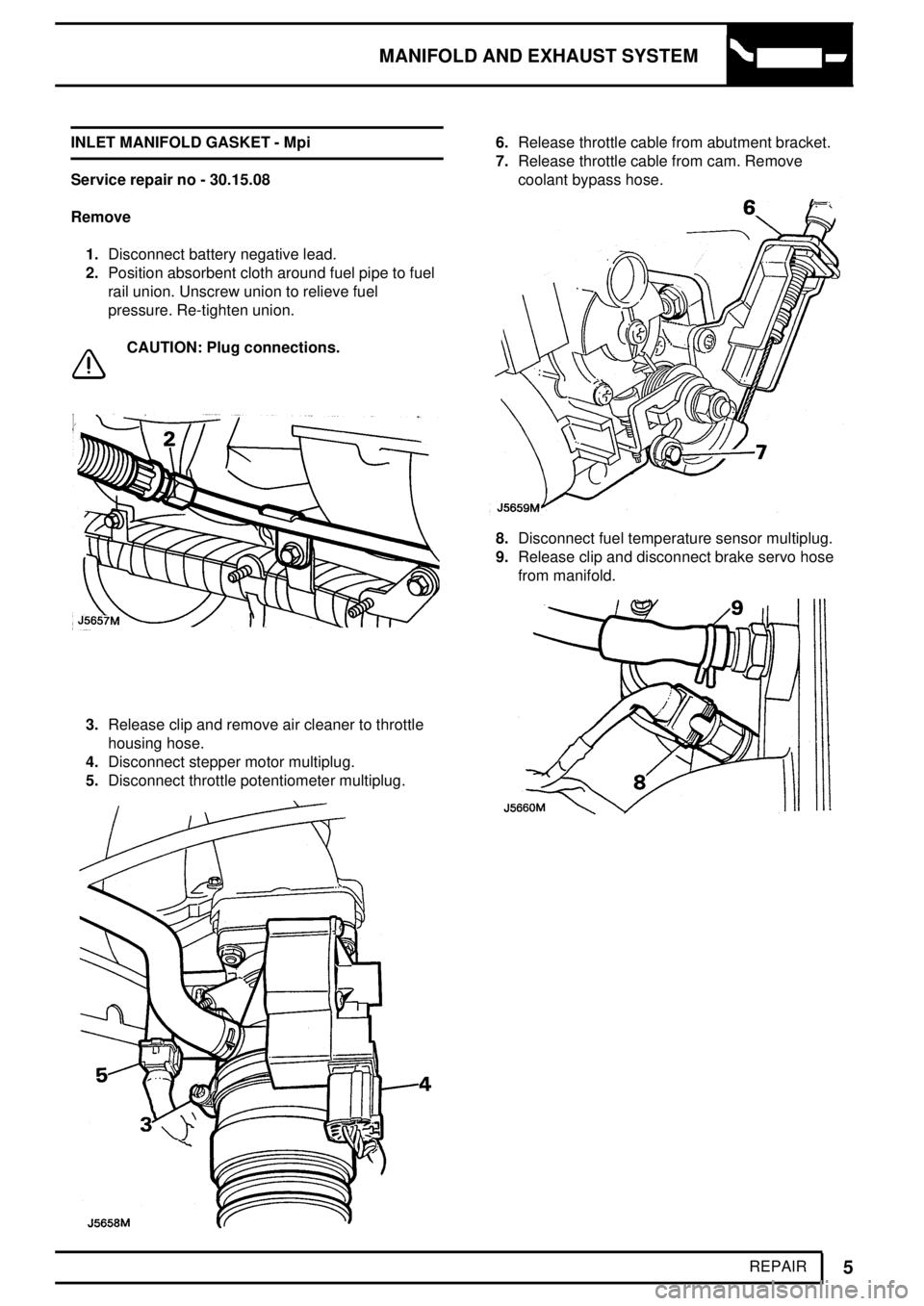
MANIFOLD AND EXHAUST SYSTEM
5
REPAIR INLET MANIFOLD GASKET - Mpi
Service repair no - 30.15.08
Remove
1.Disconnect battery negative lead.
2.Position absorbent cloth around fuel pipe to fuel
rail union. Unscrew union to relieve fuel
pressure. Re-tighten union.
CAUTION: Plug connections.
3.Release clip and remove air cleaner to throttle
housing hose.
4.Disconnect stepper motor multiplug.
5.Disconnect throttle potentiometer multiplug.
6.Release throttle cable from abutment bracket.
7.Release throttle cable from cam. Remove
coolant bypass hose.
8.Disconnect fuel temperature sensor multiplug.
9.Release clip and disconnect brake servo hose
from manifold.
Page 382 of 873
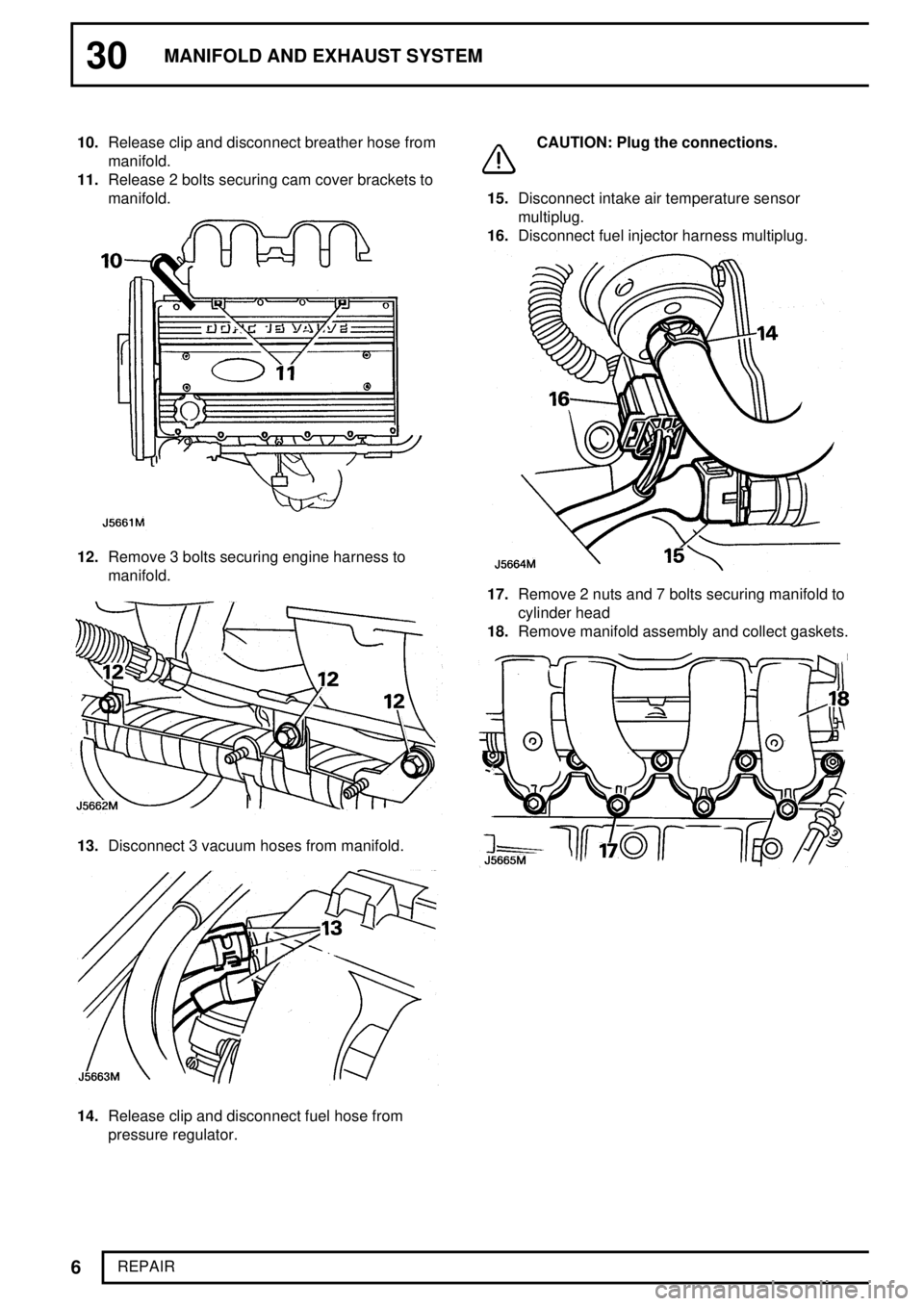
30MANIFOLD AND EXHAUST SYSTEM
6
REPAIR 10.Release clip and disconnect breather hose from
manifold.
11.Release 2 bolts securing cam cover brackets to
manifold.
12.Remove 3 bolts securing engine harness to
manifold.
13.Disconnect 3 vacuum hoses from manifold.
14.Release clip and disconnect fuel hose from
pressure regulator.
CAUTION: Plug the connections.
15.Disconnect intake air temperature sensor
multiplug.
16.Disconnect fuel injector harness multiplug.
17.Remove 2 nuts and 7 bolts securing manifold to
cylinder head
18.Remove manifold assembly and collect gaskets.
Page 383 of 873
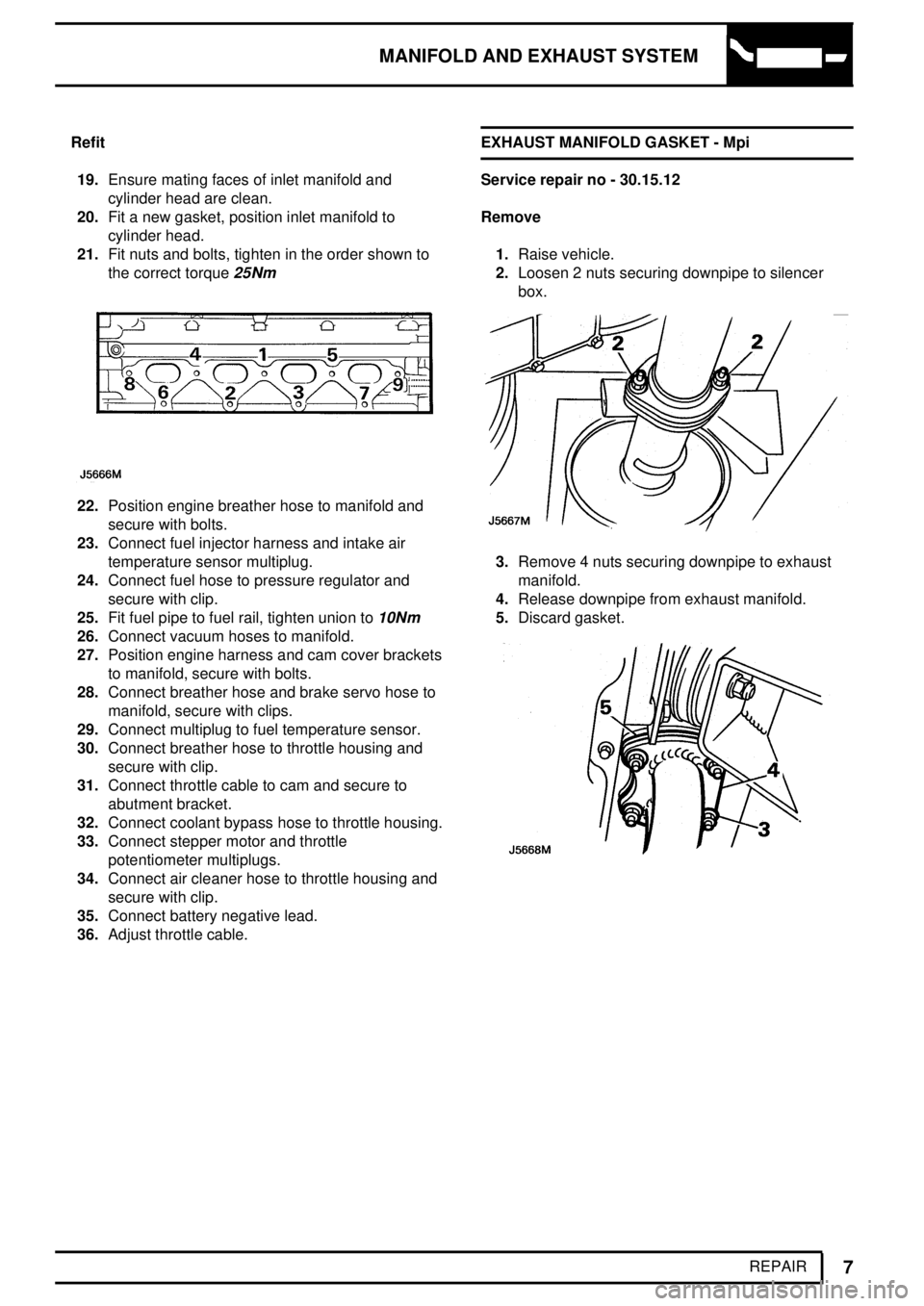
MANIFOLD AND EXHAUST SYSTEM
7
REPAIR Refit
19.Ensure mating faces of inlet manifold and
cylinder head are clean.
20.Fit a new gasket, position inlet manifold to
cylinder head.
21.Fit nuts and bolts, tighten in the order shown to
the correct torque
25Nm
22.Position engine breather hose to manifold and
secure with bolts.
23.Connect fuel injector harness and intake air
temperature sensor multiplug.
24.Connect fuel hose to pressure regulator and
secure with clip.
25.Fit fuel pipe to fuel rail, tighten union to
10Nm
26.Connect vacuum hoses to manifold.
27.Position engine harness and cam cover brackets
to manifold, secure with bolts.
28.Connect breather hose and brake servo hose to
manifold, secure with clips.
29.Connect multiplug to fuel temperature sensor.
30.Connect breather hose to throttle housing and
secure with clip.
31.Connect throttle cable to cam and secure to
abutment bracket.
32.Connect coolant bypass hose to throttle housing.
33.Connect stepper motor and throttle
potentiometer multiplugs.
34.Connect air cleaner hose to throttle housing and
secure with clip.
35.Connect battery negative lead.
36.Adjust throttle cable.EXHAUST MANIFOLD GASKET - Mpi
Service repair no - 30.15.12
Remove
1.Raise vehicle.
2.Loosen 2 nuts securing downpipe to silencer
box.
3.Remove 4 nuts securing downpipe to exhaust
manifold.
4.Release downpipe from exhaust manifold.
5.Discard gasket.
Page 384 of 873
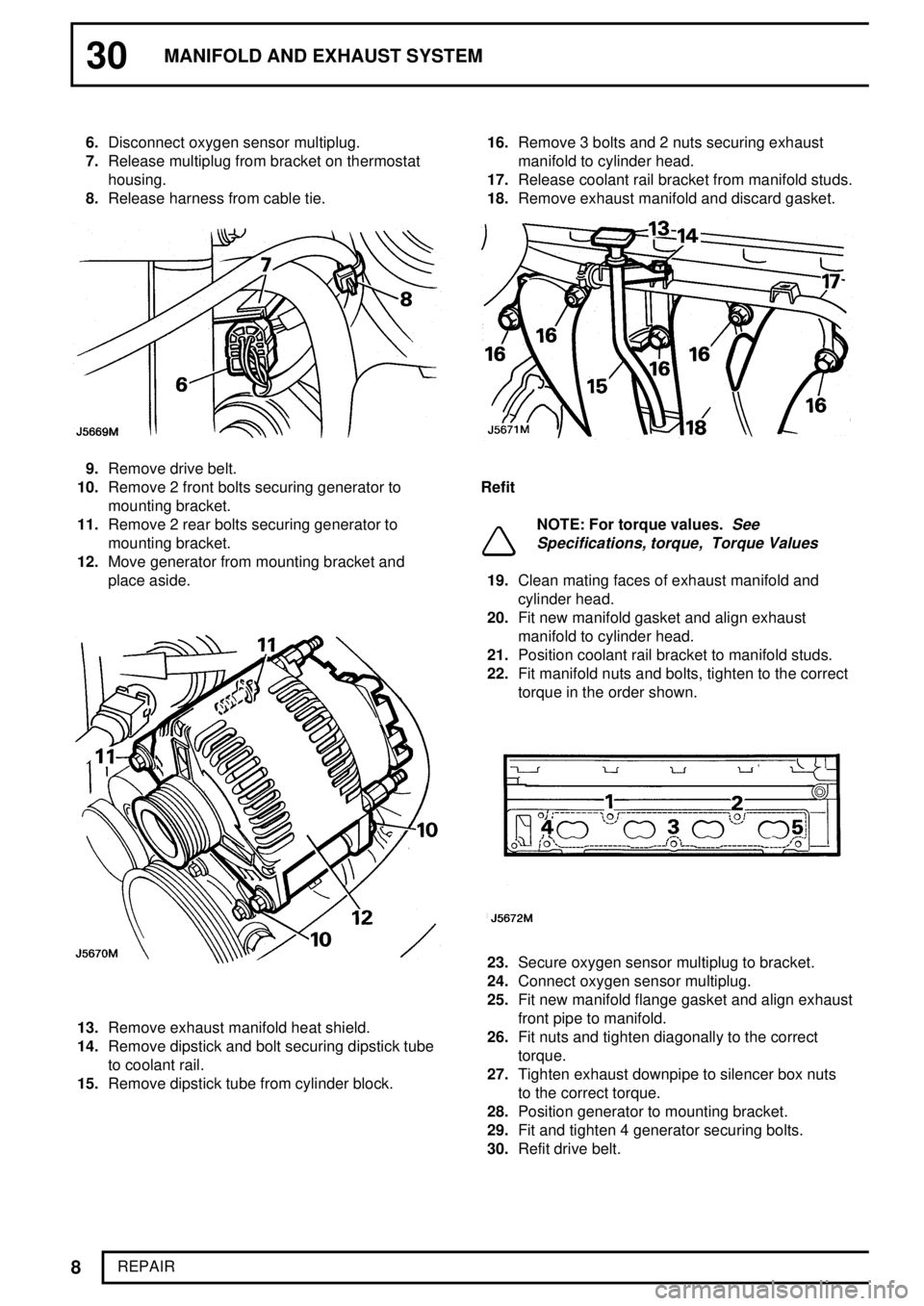
30MANIFOLD AND EXHAUST SYSTEM
8
REPAIR 6.Disconnect oxygen sensor multiplug.
7.Release multiplug from bracket on thermostat
housing.
8.Release harness from cable tie.
9.Remove drive belt.
10.Remove 2 front bolts securing generator to
mounting bracket.
11.Remove 2 rear bolts securing generator to
mounting bracket.
12.Move generator from mounting bracket and
place aside.
13.Remove exhaust manifold heat shield.
14.Remove dipstick and bolt securing dipstick tube
to coolant rail.
15.Remove dipstick tube from cylinder block.16.Remove 3 bolts and 2 nuts securing exhaust
manifold to cylinder head.
17.Release coolant rail bracket from manifold studs.
18.Remove exhaust manifold and discard gasket.
Refit
NOTE: For torque values.See
Specifications, torque, Torque Values
19.Clean mating faces of exhaust manifold and
cylinder head.
20.Fit new manifold gasket and align exhaust
manifold to cylinder head.
21.Position coolant rail bracket to manifold studs.
22.Fit manifold nuts and bolts, tighten to the correct
torque in the order shown.
23.Secure oxygen sensor multiplug to bracket.
24.Connect oxygen sensor multiplug.
25.Fit new manifold flange gasket and align exhaust
front pipe to manifold.
26.Fit nuts and tighten diagonally to the correct
torque.
27.Tighten exhaust downpipe to silencer box nuts
to the correct torque.
28.Position generator to mounting bracket.
29.Fit and tighten 4 generator securing bolts.
30.Refit drive belt.
Page 385 of 873
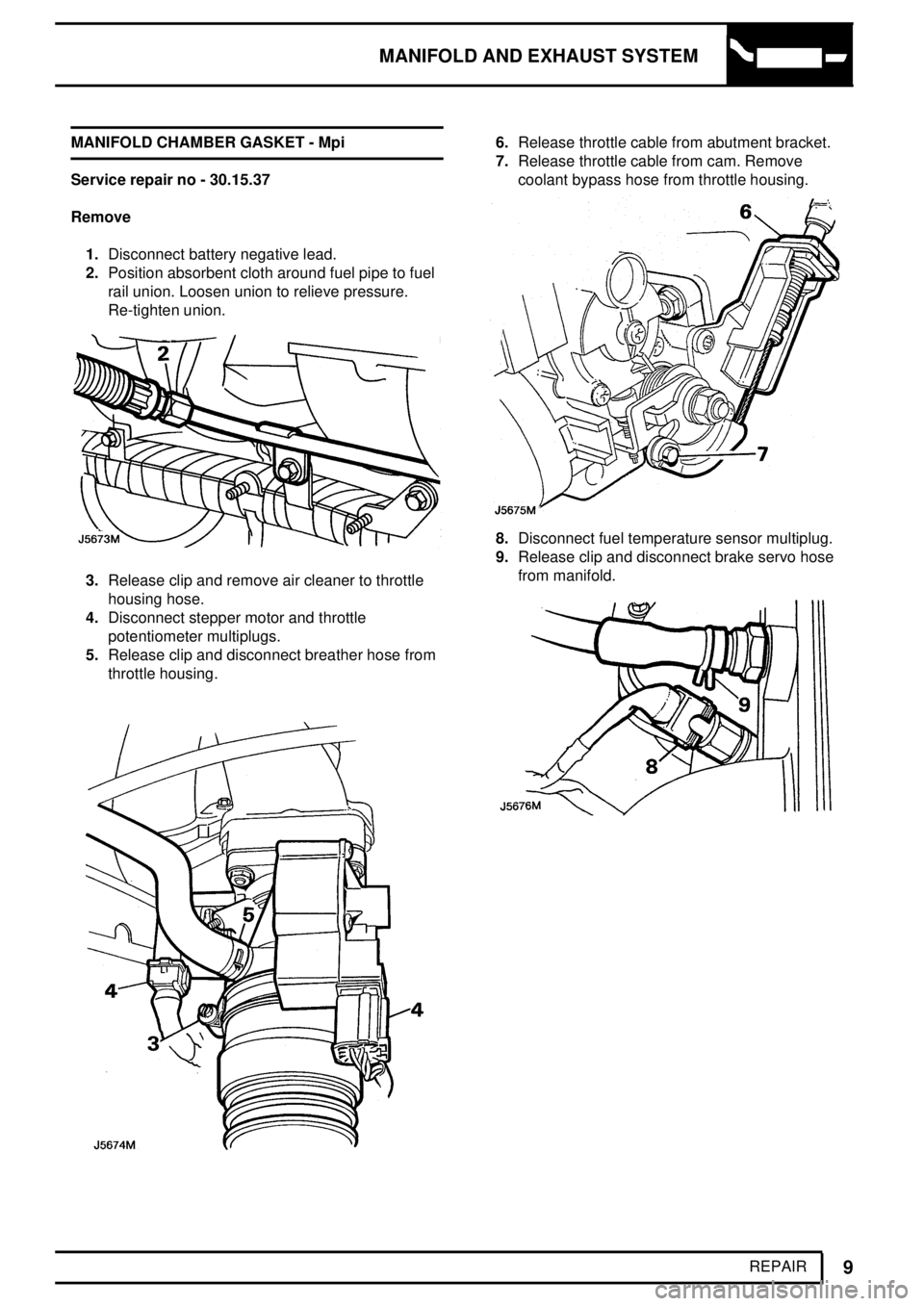
MANIFOLD AND EXHAUST SYSTEM
9
REPAIR MANIFOLD CHAMBER GASKET - Mpi
Service repair no - 30.15.37
Remove
1.Disconnect battery negative lead.
2.Position absorbent cloth around fuel pipe to fuel
rail union. Loosen union to relieve pressure.
Re-tighten union.
3.Release clip and remove air cleaner to throttle
housing hose.
4.Disconnect stepper motor and throttle
potentiometer multiplugs.
5.Release clip and disconnect breather hose from
throttle housing.
6.Release throttle cable from abutment bracket.
7.Release throttle cable from cam. Remove
coolant bypass hose from throttle housing.
8.Disconnect fuel temperature sensor multiplug.
9.Release clip and disconnect brake servo hose
from manifold.
Page 386 of 873
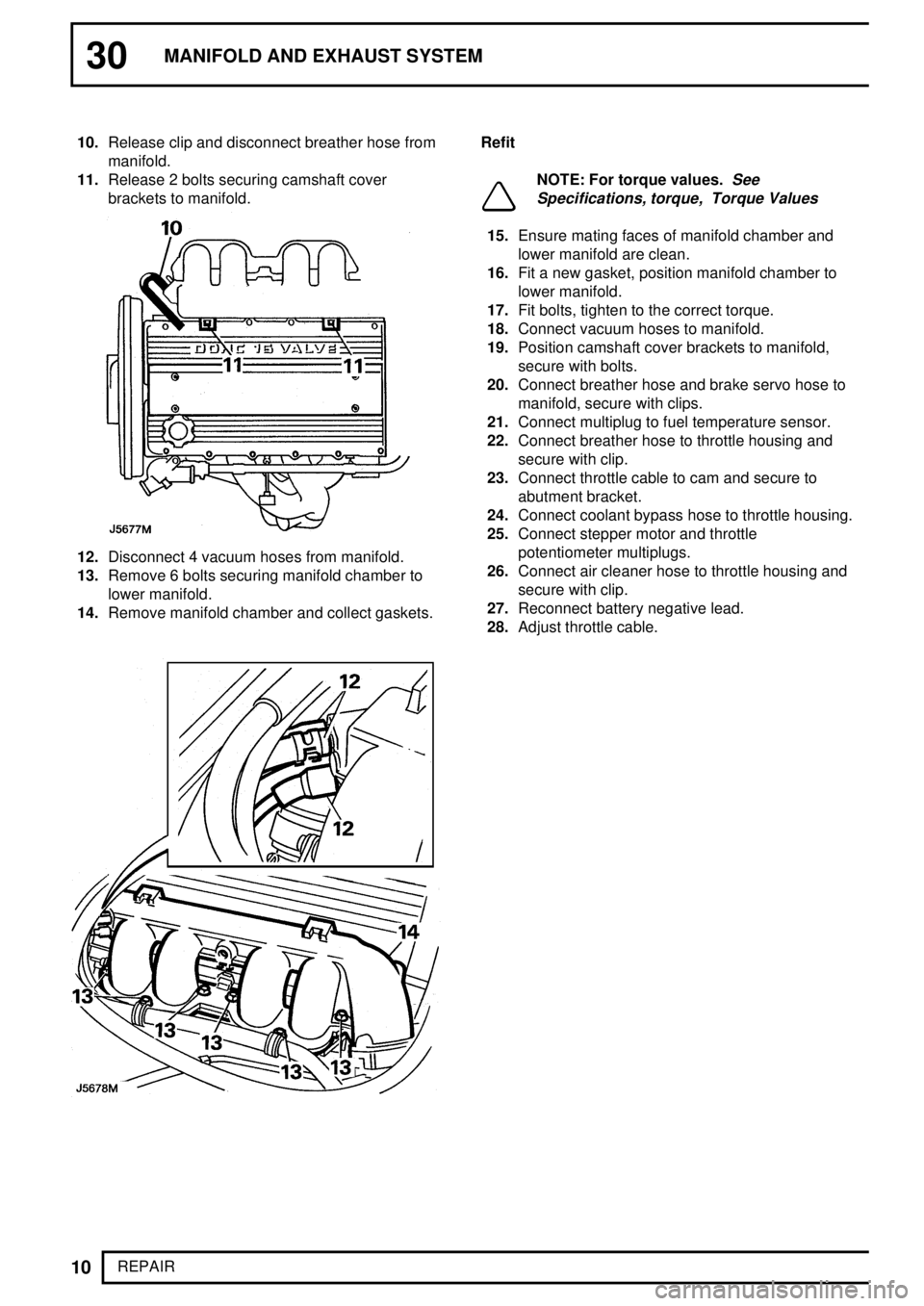
30MANIFOLD AND EXHAUST SYSTEM
10
REPAIR 10.Release clip and disconnect breather hose from
manifold.
11.Release 2 bolts securing camshaft cover
brackets to manifold.
12.Disconnect 4 vacuum hoses from manifold.
13.Remove 6 bolts securing manifold chamber to
lower manifold.
14.Remove manifold chamber and collect gaskets.
Refit
NOTE: For torque values.See
Specifications, torque, Torque Values
15.Ensure mating faces of manifold chamber and
lower manifold are clean.
16.Fit a new gasket, position manifold chamber to
lower manifold.
17.Fit bolts, tighten to the correct torque.
18.Connect vacuum hoses to manifold.
19.Position camshaft cover brackets to manifold,
secure with bolts.
20.Connect breather hose and brake servo hose to
manifold, secure with clips.
21.Connect multiplug to fuel temperature sensor.
22.Connect breather hose to throttle housing and
secure with clip.
23.Connect throttle cable to cam and secure to
abutment bracket.
24.Connect coolant bypass hose to throttle housing.
25.Connect stepper motor and throttle
potentiometer multiplugs.
26.Connect air cleaner hose to throttle housing and
secure with clip.
27.Reconnect battery negative lead.
28.Adjust throttle cable.
Page 387 of 873
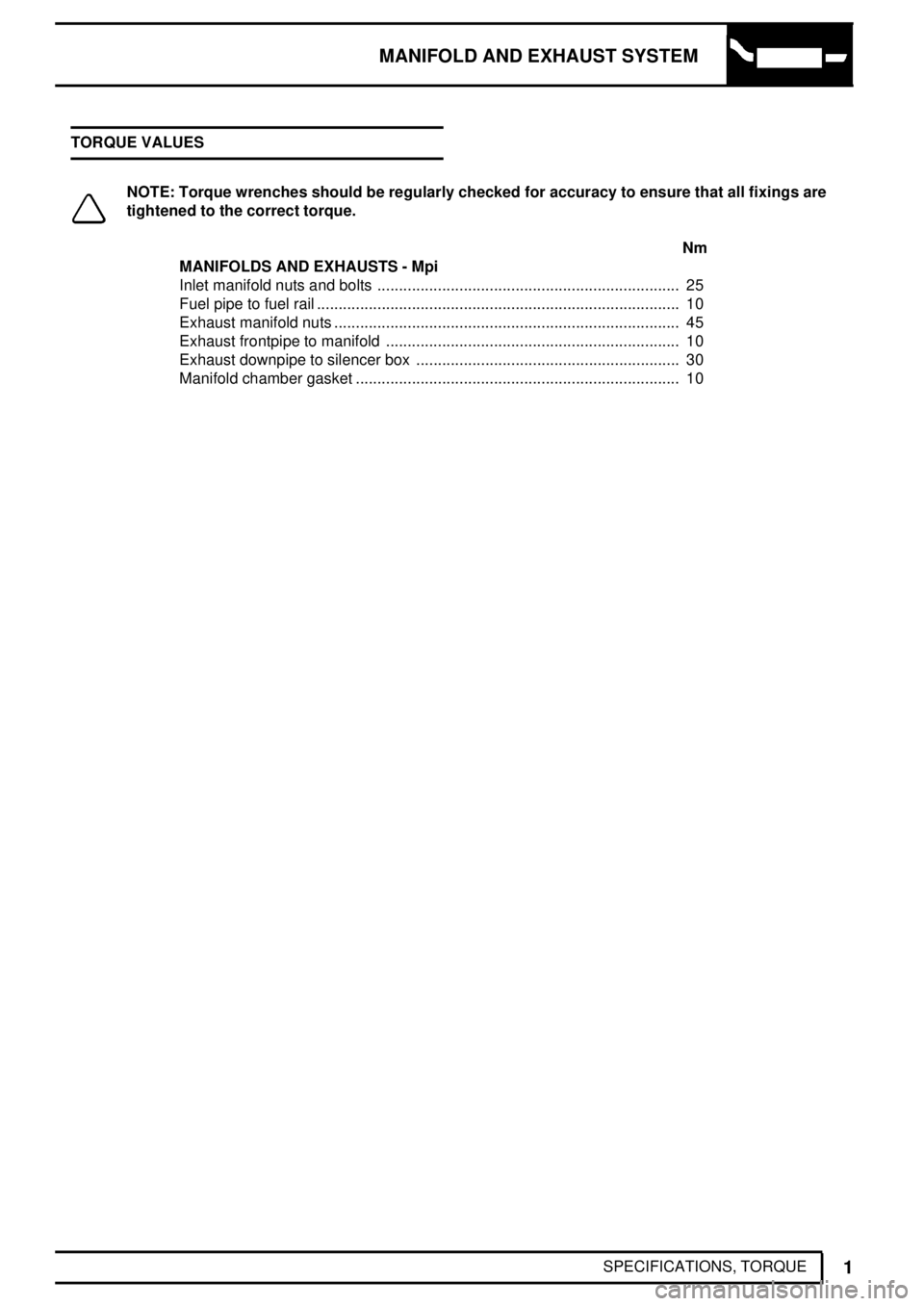
MANIFOLD AND EXHAUST SYSTEM
1
SPECIFICATIONS, TORQUE TORQUE VALUES
NOTE: Torque wrenches should be regularly checked for accuracy to ensure that all fixings are
tightened to the correct torque.
Nm
MANIFOLDS AND EXHAUSTS - Mpi
Inlet manifold nuts and bolts 25......................................................................
Fuel pipe to fuel rail 10....................................................................................
Exhaust manifold nuts 45................................................................................
Exhaust frontpipe to manifold 10....................................................................
Exhaust downpipe to silencer box 30.............................................................
Manifold chamber gasket 10...........................................................................
Page 388 of 873
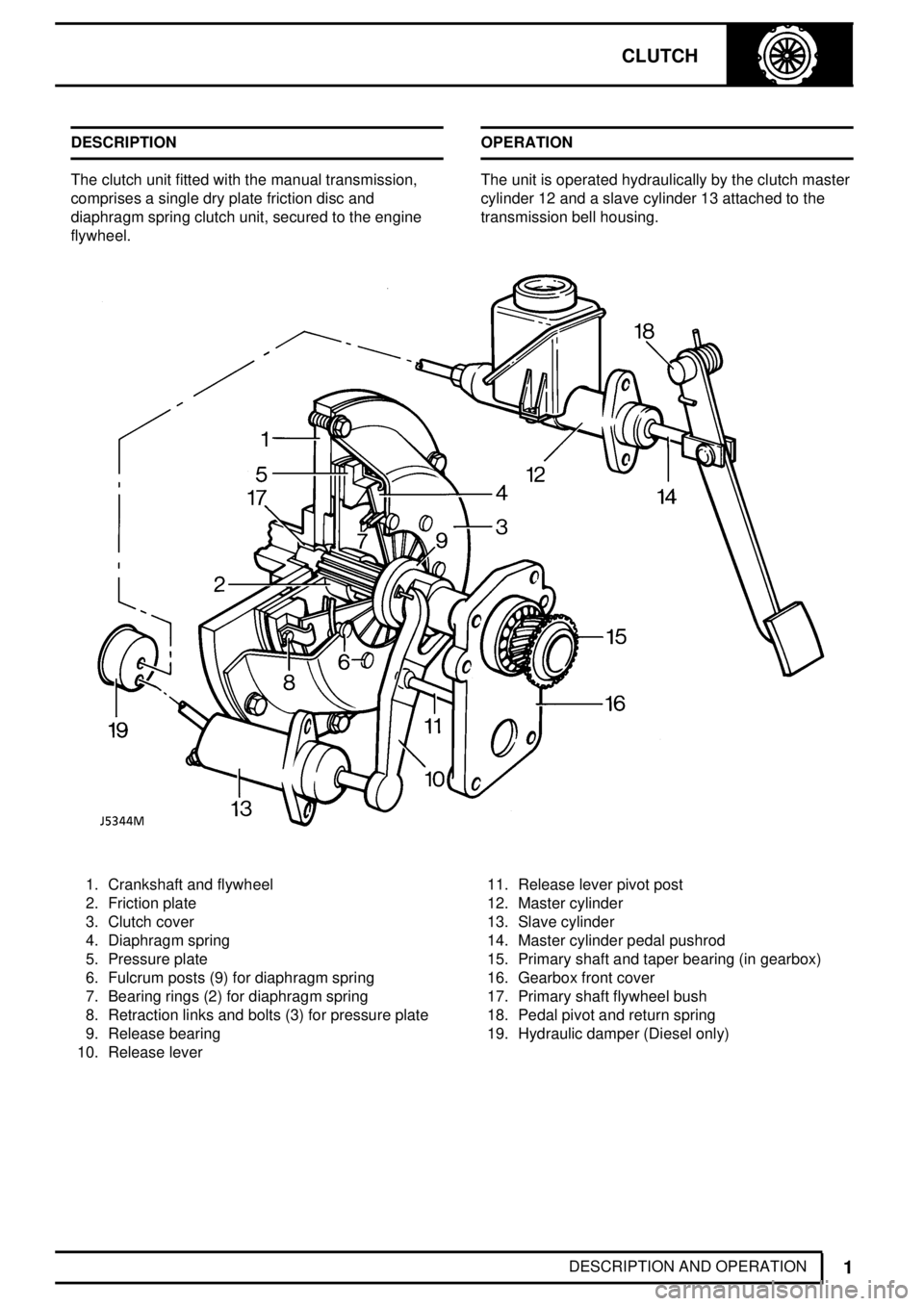
CLUTCH
1
DESCRIPTION AND OPERATION DESCRIPTION
The clutch unit fitted with the manual transmission,
comprises a single dry plate friction disc and
diaphragm spring clutch unit, secured to the engine
flywheel.OPERATION
The unit is operated hydraulically by the clutch master
cylinder 12 and a slave cylinder 13 attached to the
transmission bell housing.
1. Crankshaft and flywheel
2. Friction plate
3. Clutch cover
4. Diaphragm spring
5. Pressure plate
6. Fulcrum posts (9) for diaphragm spring
7. Bearing rings (2) for diaphragm spring
8. Retraction links and bolts (3) for pressure plate
9. Release bearing
10. Release lever11. Release lever pivot post
12. Master cylinder
13. Slave cylinder
14. Master cylinder pedal pushrod
15. Primary shaft and taper bearing (in gearbox)
16. Gearbox front cover
17. Primary shaft flywheel bush
18. Pedal pivot and return spring
19. Hydraulic damper (Diesel only)
Page 389 of 873
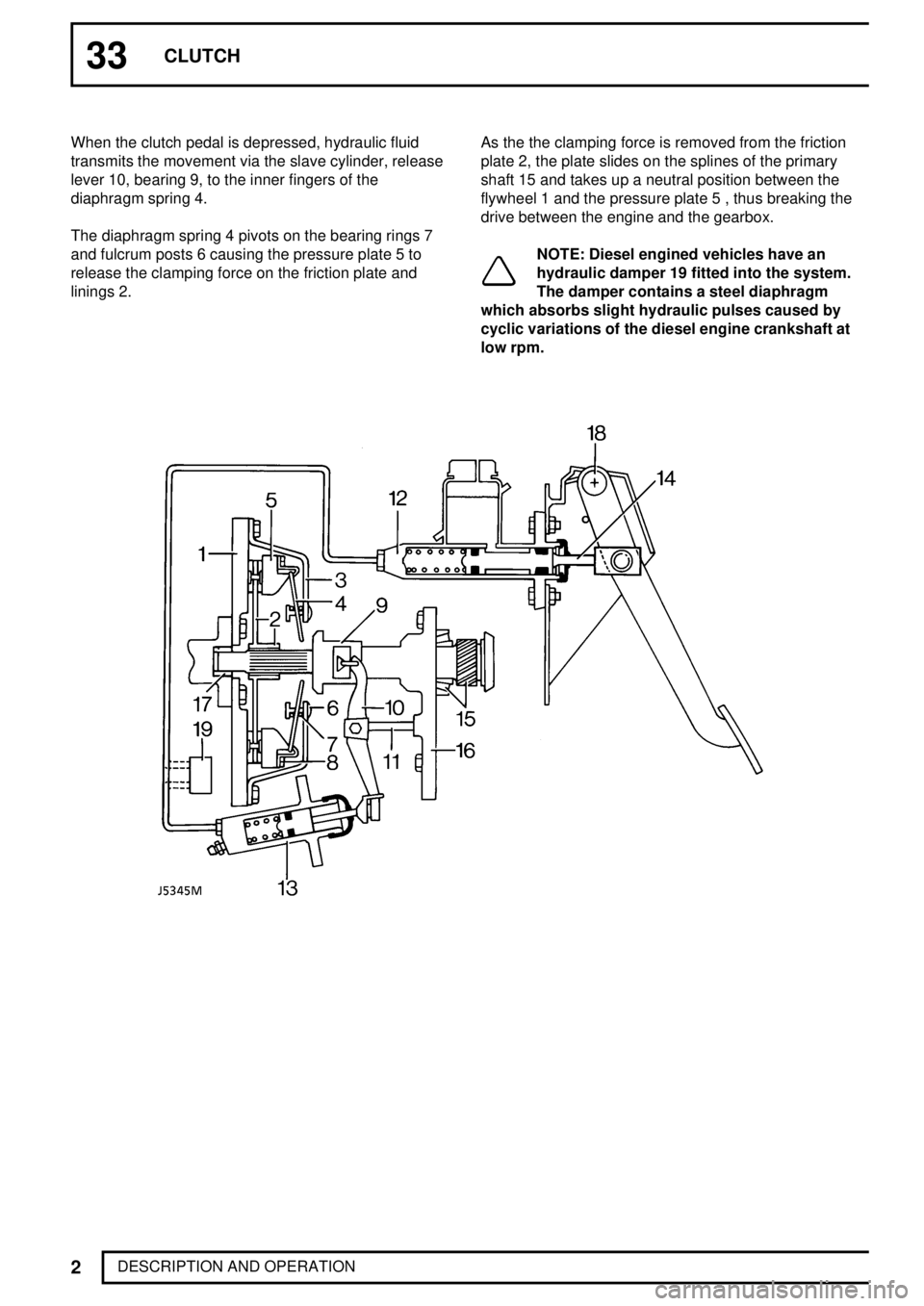
33CLUTCH
2
DESCRIPTION AND OPERATION When the clutch pedal is depressed, hydraulic fluid
transmits the movement via the slave cylinder, release
lever 10, bearing 9, to the inner fingers of the
diaphragm spring 4.
The diaphragm spring 4 pivots on the bearing rings 7
and fulcrum posts 6 causing the pressure plate 5 to
release the clamping force on the friction plate and
linings 2.As the the clamping force is removed from the friction
plate 2, the plate slides on the splines of the primary
shaft 15 and takes up a neutral position between the
flywheel 1 and the pressure plate 5 , thus breaking the
drive between the engine and the gearbox.
NOTE: Diesel engined vehicles have an
hydraulic damper 19 fitted into the system.
The damper contains a steel diaphragm
which absorbs slight hydraulic pulses caused by
cyclic variations of the diesel engine crankshaft at
low rpm.
Page 390 of 873
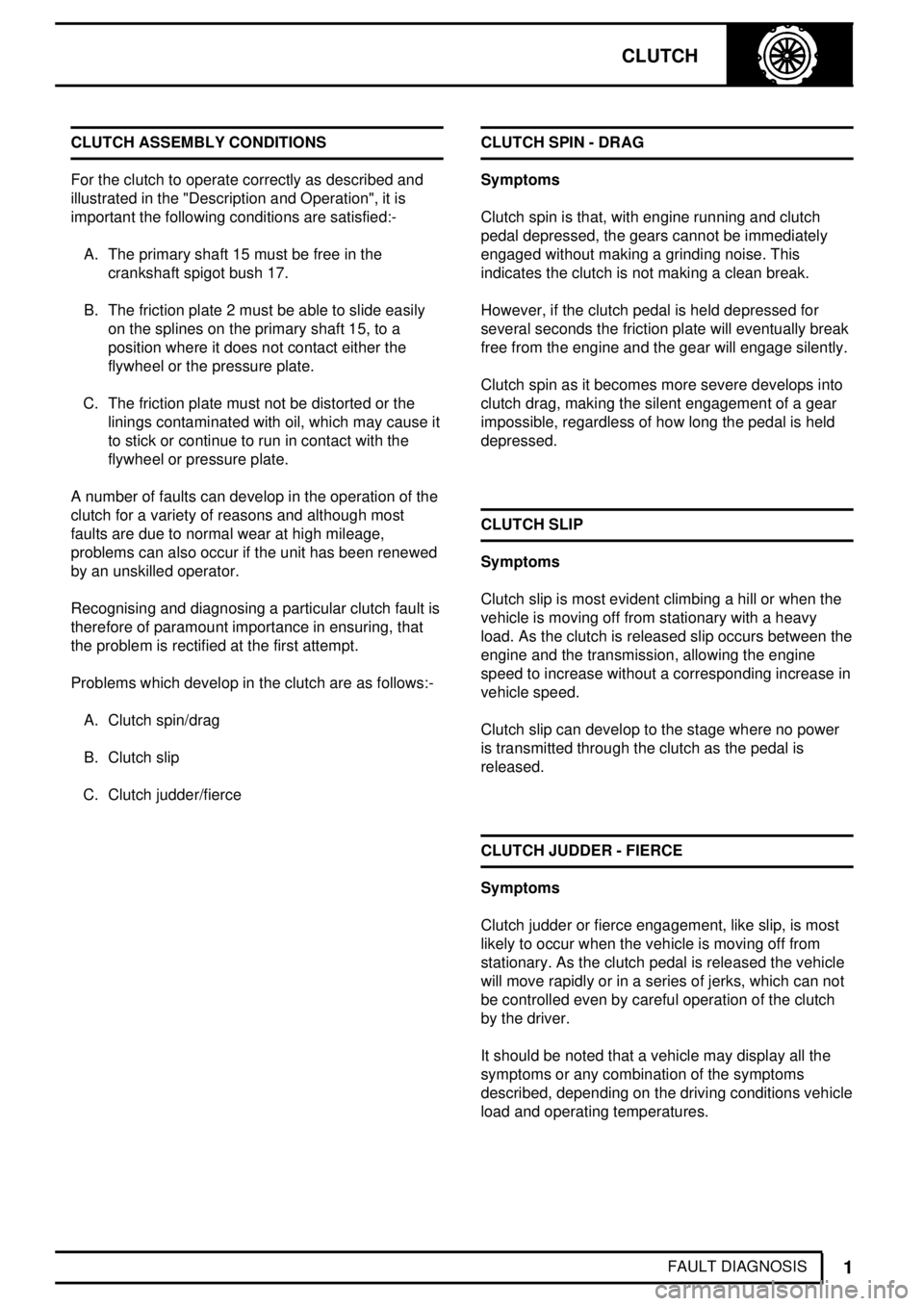
CLUTCH
1
FAULT DIAGNOSIS CLUTCH ASSEMBLY CONDITIONS
For the clutch to operate correctly as described and
illustrated in the "Description and Operation", it is
important the following conditions are satisfied:-
A. The primary shaft 15 must be free in the
crankshaft spigot bush 17.
B. The friction plate 2 must be able to slide easily
on the splines on the primary shaft 15, to a
position where it does not contact either the
flywheel or the pressure plate.
C. The friction plate must not be distorted or the
linings contaminated with oil, which may cause it
to stick or continue to run in contact with the
flywheel or pressure plate.
A number of faults can develop in the operation of the
clutch for a variety of reasons and although most
faults are due to normal wear at high mileage,
problems can also occur if the unit has been renewed
by an unskilled operator.
Recognising and diagnosing a particular clutch fault is
therefore of paramount importance in ensuring, that
the problem is rectified at the first attempt.
Problems which develop in the clutch are as follows:-
A. Clutch spin/drag
B. Clutch slip
C. Clutch judder/fierceCLUTCH SPIN - DRAG
Symptoms
Clutch spin is that, with engine running and clutch
pedal depressed, the gears cannot be immediately
engaged without making a grinding noise. This
indicates the clutch is not making a clean break.
However, if the clutch pedal is held depressed for
several seconds the friction plate will eventually break
free from the engine and the gear will engage silently.
Clutch spin as it becomes more severe develops into
clutch drag, making the silent engagement of a gear
impossible, regardless of how long the pedal is held
depressed.
CLUTCH SLIP
Symptoms
Clutch slip is most evident climbing a hill or when the
vehicle is moving off from stationary with a heavy
load. As the clutch is released slip occurs between the
engine and the transmission, allowing the engine
speed to increase without a corresponding increase in
vehicle speed.
Clutch slip can develop to the stage where no power
is transmitted through the clutch as the pedal is
released.
CLUTCH JUDDER - FIERCE
Symptoms
Clutch judder or fierce engagement, like slip, is most
likely to occur when the vehicle is moving off from
stationary. As the clutch pedal is released the vehicle
will move rapidly or in a series of jerks, which can not
be controlled even by careful operation of the clutch
by the driver.
It should be noted that a vehicle may display all the
symptoms or any combination of the symptoms
described, depending on the driving conditions vehicle
load and operating temperatures.