ECU LAND ROVER DISCOVERY 2002 User Guide
[x] Cancel search | Manufacturer: LAND ROVER, Model Year: 2002, Model line: DISCOVERY, Model: LAND ROVER DISCOVERY 2002Pages: 1672, PDF Size: 46.1 MB
Page 48 of 1672
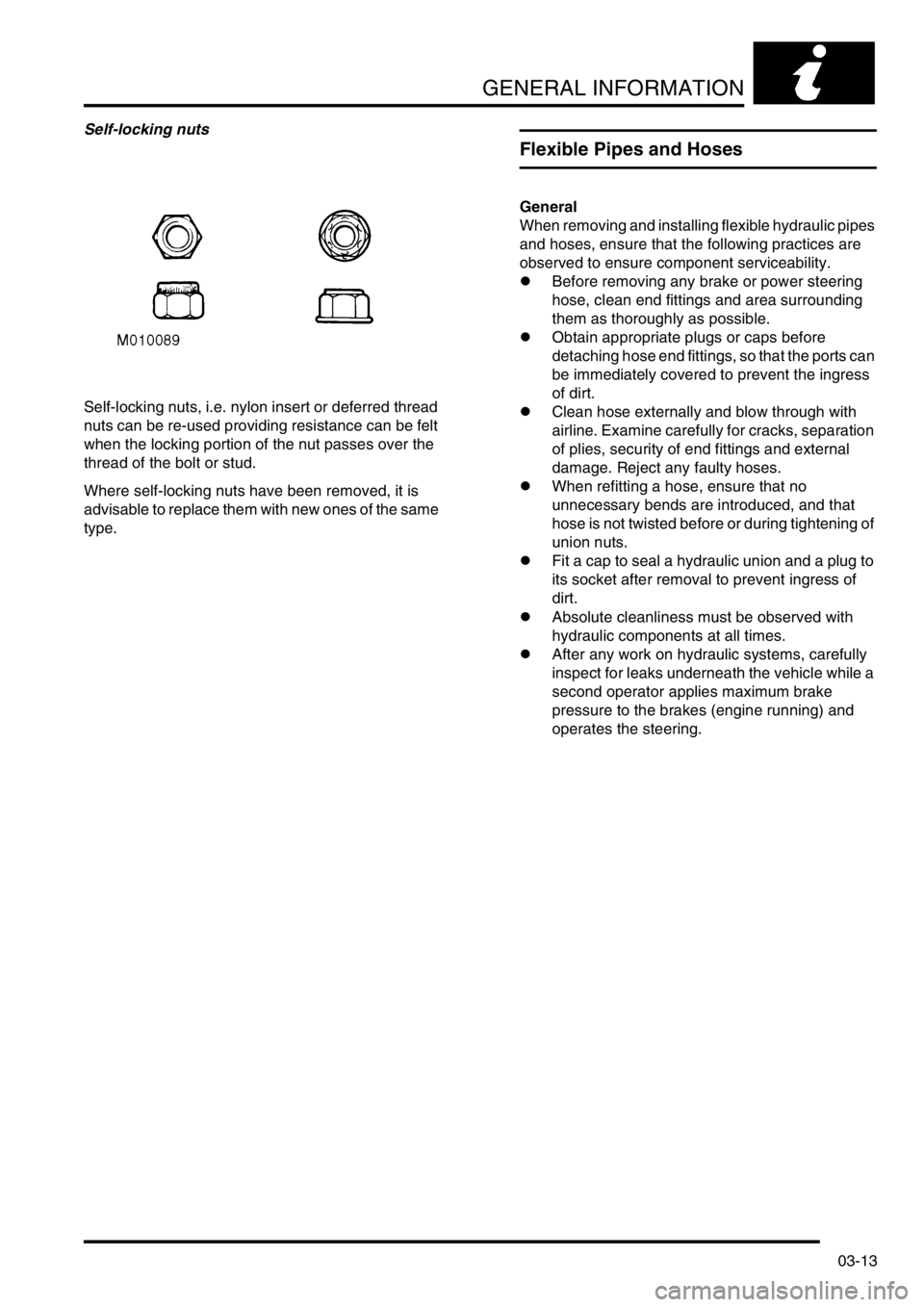
GENERAL INFORMATION
03-13
Self-locking nuts
Self-locking nuts, i.e. nylon insert or deferred thread
nuts can be re-used providing resistance can be felt
when the locking portion of the nut passes over the
thread of the bolt or stud.
Where self-locking nuts have been removed, it is
advisable to replace them with new ones of the same
type.
Flexible Pipes and Hoses
General
When removing and installing flexible hydraulic pipes
and hoses, ensure that the following practices are
observed to ensure component serviceability.
lBefore removing any brake or power steering
hose, clean end fittings and area surrounding
them as thoroughly as possible.
lObtain appropriate plugs or caps before
detaching hose end fittings, so that the ports can
be immediately covered to prevent the ingress
of dirt.
lClean hose externally and blow through with
airline. Examine carefully for cracks, separation
of plies, security of end fittings and external
damage. Reject any faulty hoses.
lWhen refitting a hose, ensure that no
unnecessary bends are introduced, and that
hose is not twisted before or during tightening of
union nuts.
lFit a cap to seal a hydraulic union and a plug to
its socket after removal to prevent ingress of
dirt.
lAbsolute cleanliness must be observed with
hydraulic components at all times.
lAfter any work on hydraulic systems, carefully
inspect for leaks underneath the vehicle while a
second operator applies maximum brake
pressure to the brakes (engine running) and
operates the steering.
Page 50 of 1672
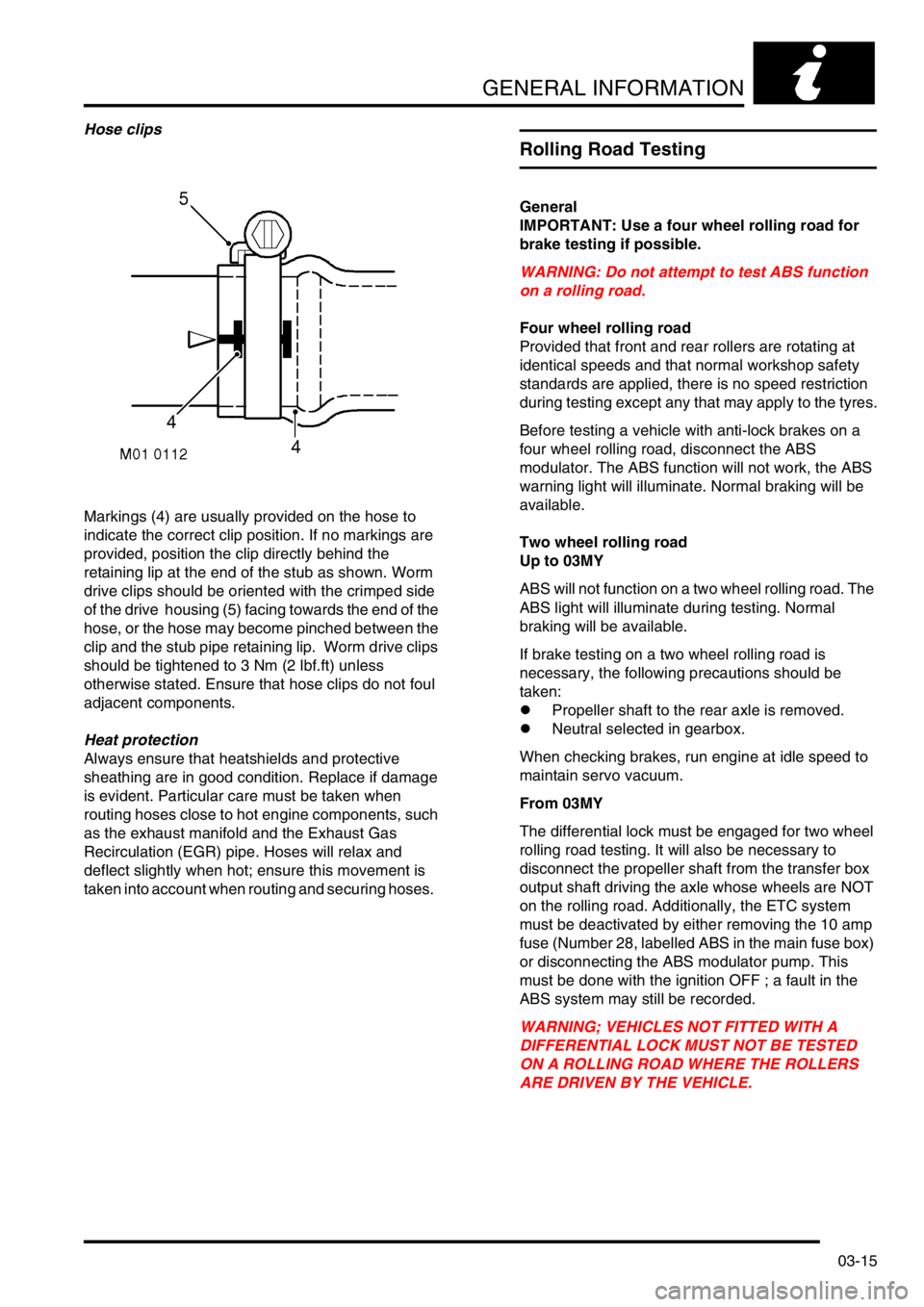
GENERAL INFORMATION
03-15
Hose clips
Markings (4) are usually provided on the hose to
indicate the correct clip position. If no markings are
provided, position the clip directly behind the
retaining lip at the end of the stub as shown. Worm
drive clips should be oriented with the crimped side
of the drive housing (5) facing towards the end of the
hose, or the hose may become pinched between the
clip and the stub pipe retaining lip. Worm drive clips
should be tightened to 3 Nm (2 lbf.ft) unless
otherwise stated. Ensure that hose clips do not foul
adjacent components.
Heat protection
Always ensure that heatshields and protective
sheathing are in good condition. Replace if damage
is evident. Particular care must be taken when
routing hoses close to hot engine components, such
as the exhaust manifold and the Exhaust Gas
Recirculation (EGR) pipe. Hoses will relax and
deflect slightly when hot; ensure this movement is
taken into account when routing and securing hoses.
Rolling Road Testing
General
IMPORTANT: Use a four wheel rolling road for
brake testing if possible.
WARNING: Do not attempt to test ABS function
on a rolling road.
Four wheel rolling road
Provided that front and rear rollers are rotating at
identical speeds and that normal workshop safety
standards are applied, there is no speed restriction
during testing except any that may apply to the tyres.
Before testing a vehicle with anti-lock brakes on a
four wheel rolling road, disconnect the ABS
modulator. The ABS function will not work, the ABS
warning light will illuminate. Normal braking will be
available.
Two wheel rolling road
Up to 03MY
ABS will not function on a two wheel rolling road. The
ABS light will illuminate during testing. Normal
braking will be available.
If brake testing on a two wheel rolling road is
necessary, the following precautions should be
taken:
lPropeller shaft to the rear axle is removed.
lNeutral selected in gearbox.
When checking brakes, run engine at idle speed to
maintain servo vacuum.
From 03MY
The differential lock must be engaged for two wheel
rolling road testing. It will also be necessary to
disconnect the propeller shaft from the transfer box
output shaft driving the axle whose wheels are NOT
on the rolling road. Additionally, the ETC system
must be deactivated by either removing the 10 amp
fuse (Number 28, labelled ABS in the main fuse box)
or disconnecting the ABS modulator pump. This
must be done with the ignition OFF ; a fault in the
ABS system may still be recorded.
WARNING; VEHICLES NOT FITTED WITH A
DIFFERENTIAL LOCK MUST NOT BE TESTED
ON A ROLLING ROAD WHERE THE ROLLERS
ARE DRIVEN BY THE VEHICLE.
Page 51 of 1672

GENERAL INFORMATION
03-16
Fuel Handling Precautions
Fuel vapour is highly flammable and in confined
spaces is also explosive and toxic. The vapour is
heavier than air and will always fall to the lowest
level. The vapour can be easily distributed
throughout a workshop by air currents;
consequently, even a small spillage of fuel is
potentially very dangerous.
The following information provides basic precautions
which must be observed if fuel is to be handled
safely. It also outlines other areas of risk which must
not be ignored. This information is issued for basic
guidance only, if in doubt consult your local Fire
Officer.
General
Always have a fire extinguisher containing FOAM,
CO
2, GAS or POWDER close at hand when handling
or draining fuel or when dismantling fuel systems.
Fire extinguishers should also be located in areas
where fuel containers are stored.
Always disconnect the vehicle battery before
carrying out dismantling or draining work on a fuel
system.
Whenever fuel is being handled, drained or stored, or
when fuel systems are being dismantled, all forms of
ignition must be extinguished or removed; any
leadlamps must be flameproof and kept clear of
spillage.
WARNING: No one should be permitted to repair
components associated with fuel without first
having specialist training.
WARNING: Do not remove fuel system
components while the vehicle is over a pit.
Fuel tank draining
Fuel tank draining should be carried out in
accordance with the procedure outlined in the FUEL
DELIVERY section of this manual and observing the
following precautions.
WARNING: Fuel must not be extracted or drained
from any vehicle while it is over a pit. Extraction
or draining of fuel must be carried out in a well
ventilated area.
The capacity of containers must be more than
adequate for the amount of fuel to be extracted or
drained. The container should be clearly marked
with its contents and placed in a safe storage
area which meets the requirements of local
authority regulations.Fuel tank removal
When the fuel line is secured to the fuel tank outlet by
a spring steel clip, the clip must be released before
the fuel line is disconnected or the fuel tank is
removed. This procedure will avoid the possibility of
fumes in the fuel tank being ignited when the clip is
released.
As an added precaution, fuel tanks should have a
'FUEL VAPOUR' warning label attached to them as
soon as they are removed from the vehicle.
Fuel tank repairs - plastic tank
No attempt should be made to repair a plastic fuel
tank. If the structure of the tank is damaged, a new
tank must be fitted.
Body repairs
Plastic fuel pipes are particularly susceptible to heat,
even at relatively low temperature, and can be
melted by heat conducted from some distance away.
When body repairs involve the use of heat, all fuel
pipes which run in the vicinity of the repair area must
be removed, and the tank outlet plugged.
WARNING: If welding is to be carried out in the
vicinity of the fuel tank, the fuel system must be
drained and the tank removed before welding
commences.
Page 52 of 1672
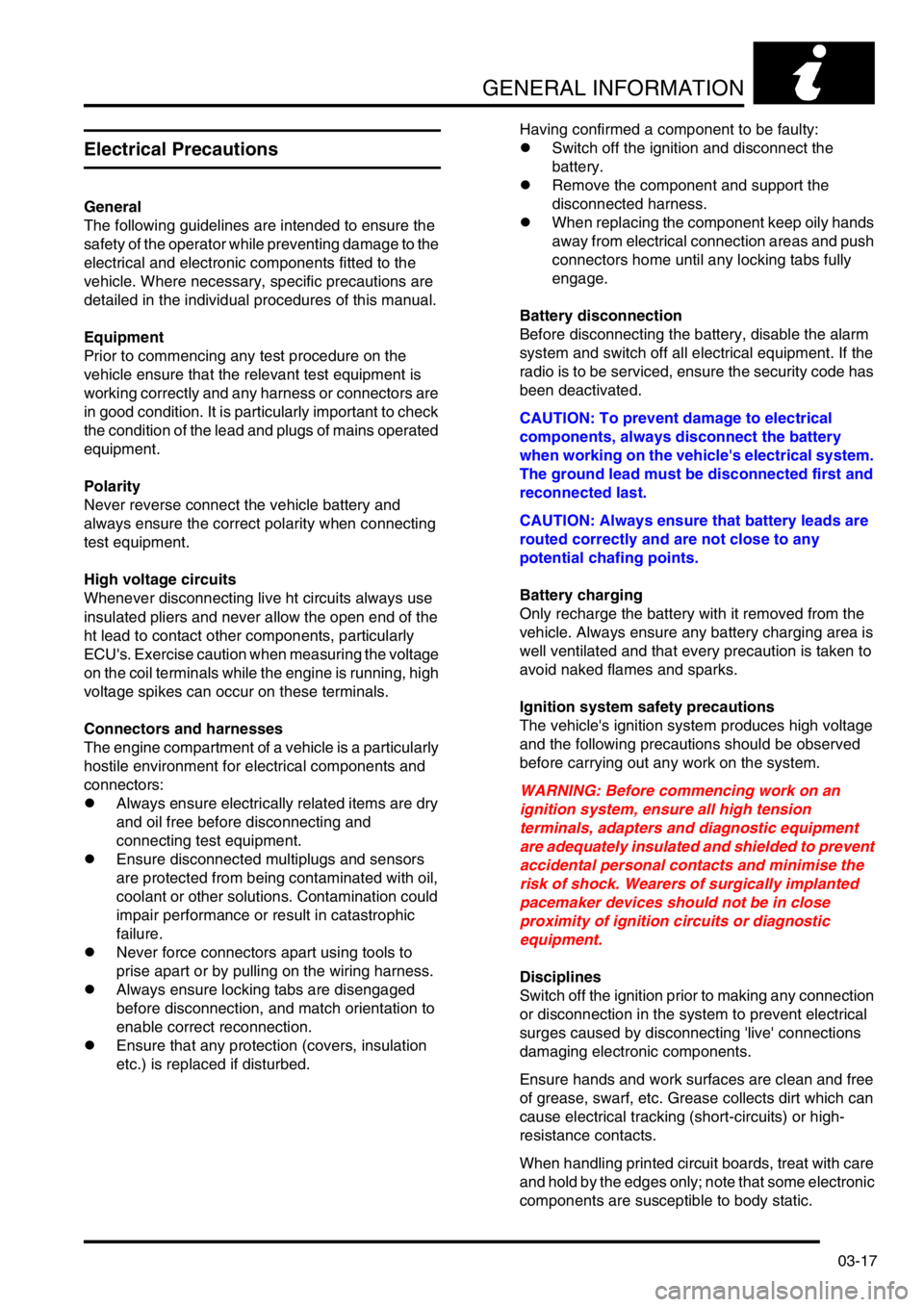
GENERAL INFORMATION
03-17
Electrical Precautions
General
The following guidelines are intended to ensure the
safety of the operator while preventing damage to the
electrical and electronic components fitted to the
vehicle. Where necessary, specific precautions are
detailed in the individual procedures of this manual.
Equipment
Prior to commencing any test procedure on the
vehicle ensure that the relevant test equipment is
working correctly and any harness or connectors are
in good condition. It is particularly important to check
the condition of the lead and plugs of mains operated
equipment.
Polarity
Never reverse connect the vehicle battery and
always ensure the correct polarity when connecting
test equipment.
High voltage circuits
Whenever disconnecting live ht circuits always use
insulated pliers and never allow the open end of the
ht lead to contact other components, particularly
ECU's. Exercise caution when measuring the voltage
on the coil terminals while the engine is running, high
voltage spikes can occur on these terminals.
Connectors and harnesses
The engine compartment of a vehicle is a particularly
hostile environment for electrical components and
connectors:
lAlways ensure electrically related items are dry
and oil free before disconnecting and
connecting test equipment.
lEnsure disconnected multiplugs and sensors
are protected from being contaminated with oil,
coolant or other solutions. Contamination could
impair performance or result in catastrophic
failure.
lNever force connectors apart using tools to
prise apart or by pulling on the wiring harness.
lAlways ensure locking tabs are disengaged
before disconnection, and match orientation to
enable correct reconnection.
lEnsure that any protection (covers, insulation
etc.) is replaced if disturbed.Having confirmed a component to be faulty:
lSwitch off the ignition and disconnect the
battery.
lRemove the component and support the
disconnected harness.
lWhen replacing the component keep oily hands
away from electrical connection areas and push
connectors home until any locking tabs fully
engage.
Battery disconnection
Before disconnecting the battery, disable the alarm
system and switch off all electrical equipment. If the
radio is to be serviced, ensure the security code has
been deactivated.
CAUTION: To prevent damage to electrical
components, always disconnect the battery
when working on the vehicle's electrical system.
The ground lead must be disconnected first and
reconnected last.
CAUTION: Always ensure that battery leads are
routed correctly and are not close to any
potential chafing points.
Battery charging
Only recharge the battery with it removed from the
vehicle. Always ensure any battery charging area is
well ventilated and that every precaution is taken to
avoid naked flames and sparks.
Ignition system safety precautions
The vehicle's ignition system produces high voltage
and the following precautions should be observed
before carrying out any work on the system.
WARNING: Before commencing work on an
ignition system, ensure all high tension
terminals, adapters and diagnostic equipment
are adequately insulated and shielded to prevent
accidental personal contacts and minimise the
risk of shock. Wearers of surgically implanted
pacemaker devices should not be in close
proximity of ignition circuits or diagnostic
equipment.
Disciplines
Switch off the ignition prior to making any connection
or disconnection in the system to prevent electrical
surges caused by disconnecting 'live' connections
damaging electronic components.
Ensure hands and work surfaces are clean and free
of grease, swarf, etc. Grease collects dirt which can
cause electrical tracking (short-circuits) or high-
resistance contacts.
When handling printed circuit boards, treat with care
and hold by the edges only; note that some electronic
components are susceptible to body static.
Page 55 of 1672
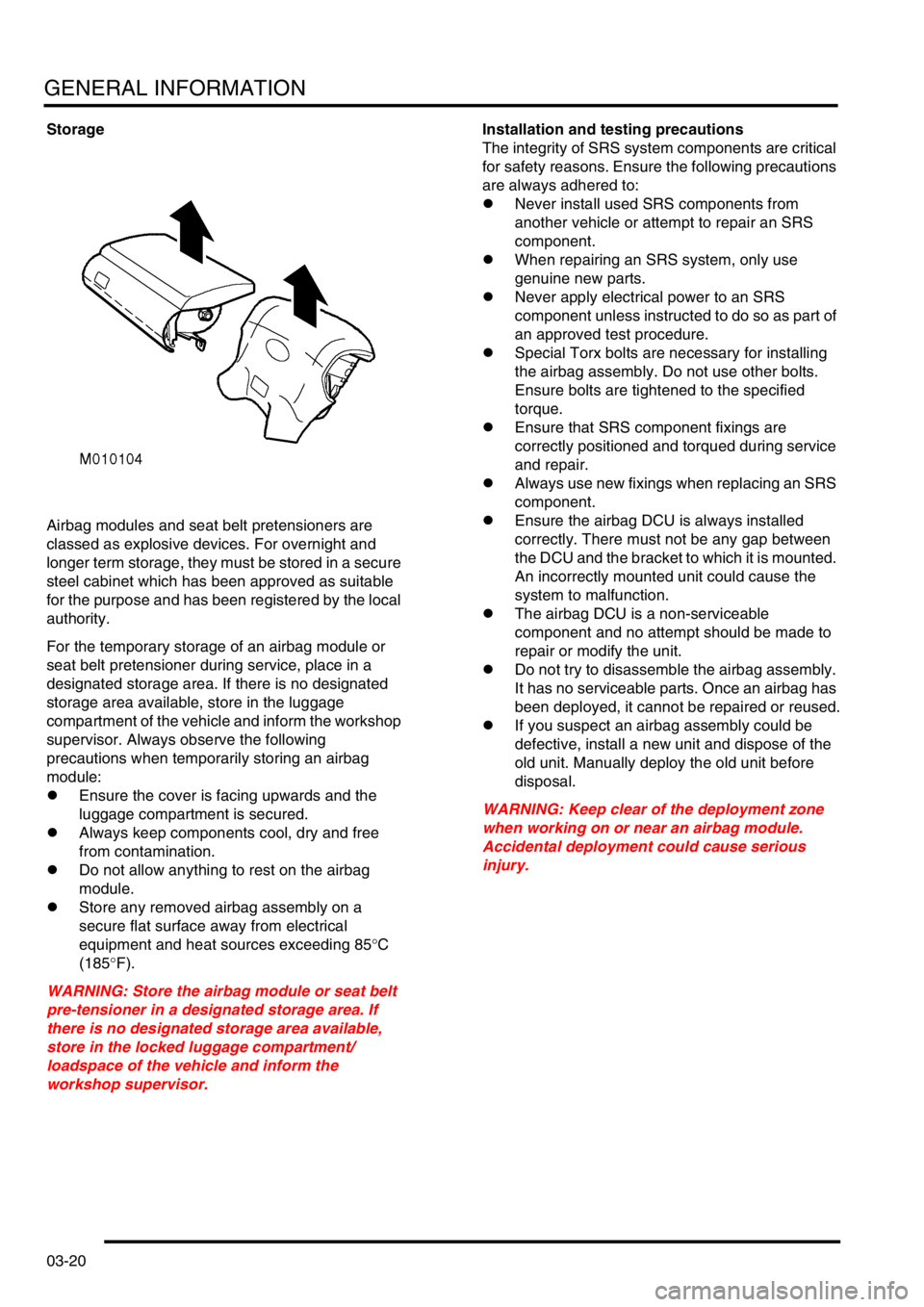
GENERAL INFORMATION
03-20
Storage
Airbag modules and seat belt pretensioners are
classed as explosive devices. For overnight and
longer term storage, they must be stored in a secure
steel cabinet which has been approved as suitable
for the purpose and has been registered by the local
authority.
For the temporary storage of an airbag module or
seat belt pretensioner during service, place in a
designated storage area. If there is no designated
storage area available, store in the luggage
compartment of the vehicle and inform the workshop
supervisor. Always observe the following
precautions when temporarily storing an airbag
module:
lEnsure the cover is facing upwards and the
luggage compartment is secured.
lAlways keep components cool, dry and free
from contamination.
lDo not allow anything to rest on the airbag
module.
lStore any removed airbag assembly on a
secure flat surface away from electrical
equipment and heat sources exceeding 85
°C
(185
°F).
WARNING: Store the airbag module or seat belt
pre-tensioner in a designated storage area. If
there is no designated storage area available,
store in the locked luggage compartment/
loadspace of the vehicle and inform the
workshop supervisor.Installation and testing precautions
The integrity of SRS system components are critical
for safety reasons. Ensure the following precautions
are always adhered to:
lNever install used SRS components from
another vehicle or attempt to repair an SRS
component.
lWhen repairing an SRS system, only use
genuine new parts.
lNever apply electrical power to an SRS
component unless instructed to do so as part of
an approved test procedure.
lSpecial Torx bolts are necessary for installing
the airbag assembly. Do not use other bolts.
Ensure bolts are tightened to the specified
torque.
lEnsure that SRS component fixings are
correctly positioned and torqued during service
and repair.
lAlways use new fixings when replacing an SRS
component.
lEnsure the airbag DCU is always installed
correctly. There must not be any gap between
the DCU and the bracket to which it is mounted.
An incorrectly mounted unit could cause the
system to malfunction.
lThe airbag DCU is a non-serviceable
component and no attempt should be made to
repair or modify the unit.
lDo not try to disassemble the airbag assembly.
It has no serviceable parts. Once an airbag has
been deployed, it cannot be repaired or reused.
lIf you suspect an airbag assembly could be
defective, install a new unit and dispose of the
old unit. Manually deploy the old unit before
disposal.
WARNING: Keep clear of the deployment zone
when working on or near an airbag module.
Accidental deployment could cause serious
injury.
Page 56 of 1672
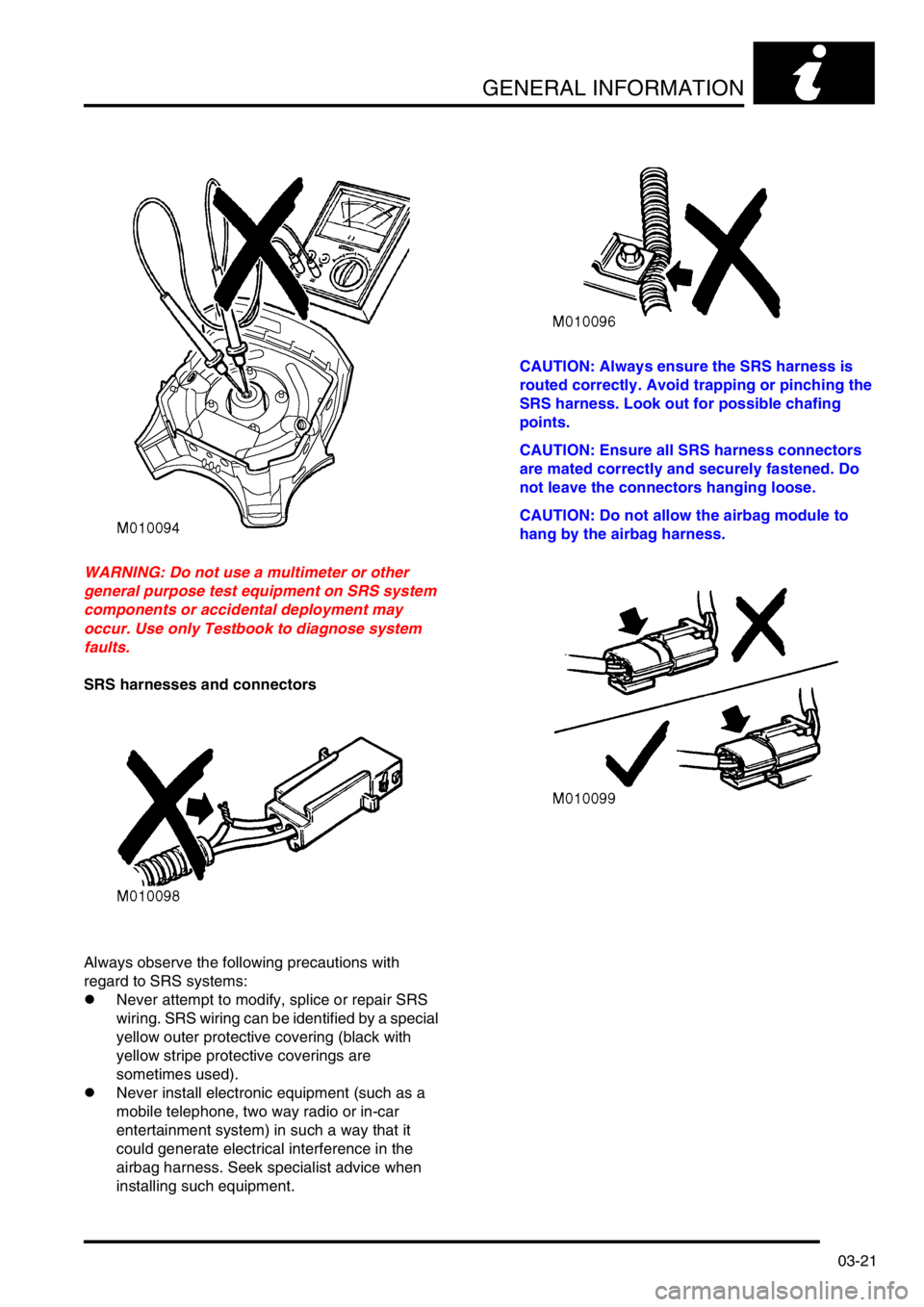
GENERAL INFORMATION
03-21
WARNING: Do not use a multimeter or other
general purpose test equipment on SRS system
components or accidental deployment may
occur. Use only Testbook to diagnose system
faults.
SRS harnesses and connectors
Always observe the following precautions with
regard to SRS systems:
lNever attempt to modify, splice or repair SRS
wiring. SRS wiring can be identified by a special
yellow outer protective covering (black with
yellow stripe protective coverings are
sometimes used).
lNever install electronic equipment (such as a
mobile telephone, two way radio or in-car
entertainment system) in such a way that it
could generate electrical interference in the
airbag harness. Seek specialist advice when
installing such equipment.CAUTION: Always ensure the SRS harness is
routed correctly. Avoid trapping or pinching the
SRS harness. Look out for possible chafing
points.
CAUTION: Ensure all SRS harness connectors
are mated correctly and securely fastened. Do
not leave the connectors hanging loose.
CAUTION: Do not allow the airbag module to
hang by the airbag harness.
Page 57 of 1672
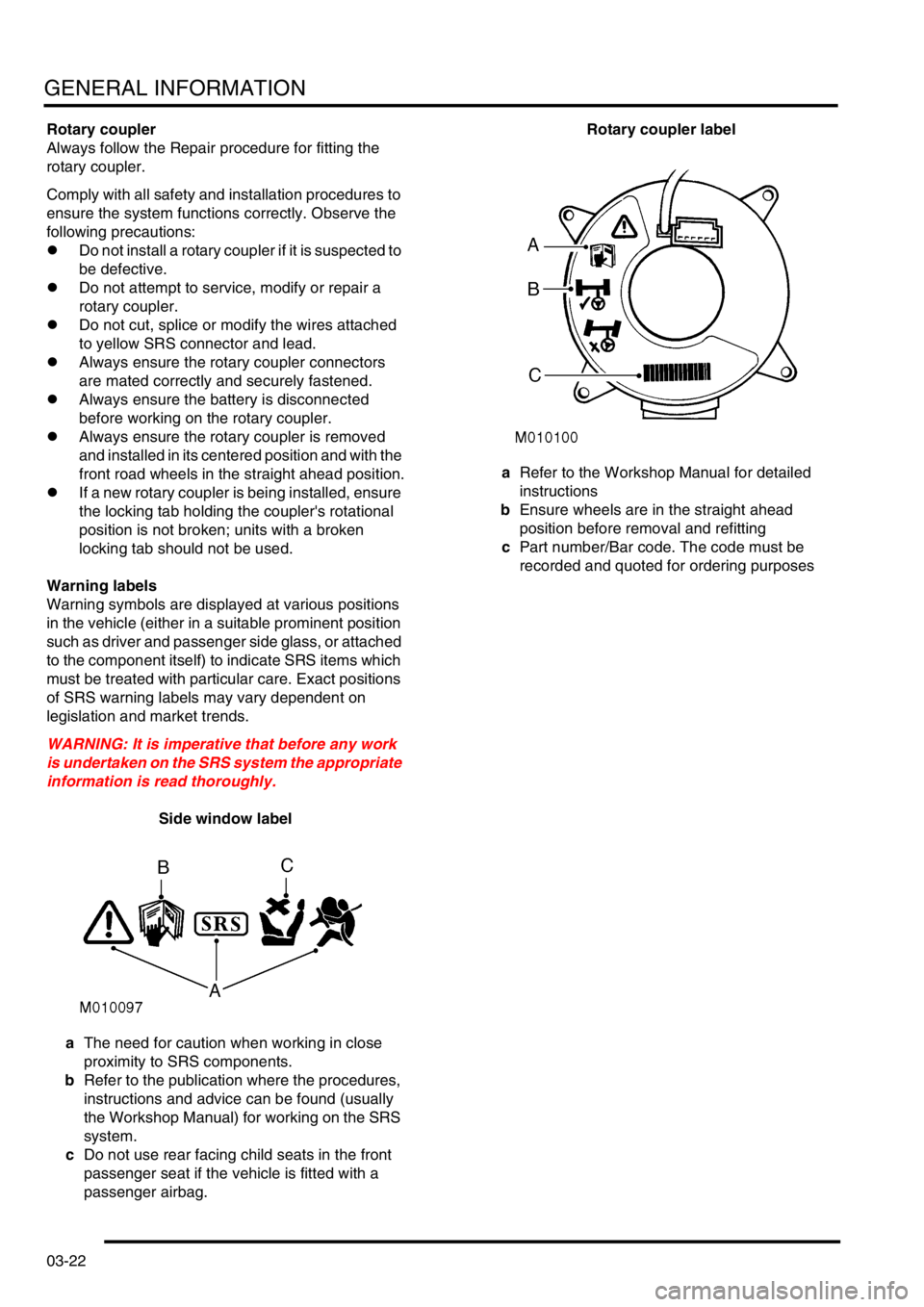
GENERAL INFORMATION
03-22
Rotary coupler
Always follow the Repair procedure for fitting the
rotary coupler.
Comply with all safety and installation procedures to
ensure the system functions correctly. Observe the
following precautions:
lDo not install a rotary coupler if it is suspected to
be defective.
lDo not attempt to service, modify or repair a
rotary coupler.
lDo not cut, splice or modify the wires attached
to yellow SRS connector and lead.
lAlways ensure the rotary coupler connectors
are mated correctly and securely fastened.
lAlways ensure the battery is disconnected
before working on the rotary coupler.
lAlways ensure the rotary coupler is removed
and installed in its centered position and with the
front road wheels in the straight ahead position.
lIf a new rotary coupler is being installed, ensure
the locking tab holding the coupler's rotational
position is not broken; units with a broken
locking tab should not be used.
Warning labels
Warning symbols are displayed at various positions
in the vehicle (either in a suitable prominent position
such as driver and passenger side glass, or attached
to the component itself) to indicate SRS items which
must be treated with particular care. Exact positions
of SRS warning labels may vary dependent on
legislation and market trends.
WARNING: It is imperative that before any work
is undertaken on the SRS system the appropriate
information is read thoroughly.
Side window label
aThe need for caution when working in close
proximity to SRS components.
bRefer to the publication where the procedures,
instructions and advice can be found (usually
the Workshop Manual) for working on the SRS
system.
cDo not use rear facing child seats in the front
passenger seat if the vehicle is fitted with a
passenger airbag.Rotary coupler label
aRefer to the Workshop Manual for detailed
instructions
bEnsure wheels are in the straight ahead
position before removal and refitting
cPart number/Bar code. The code must be
recorded and quoted for ordering purposes
Page 58 of 1672
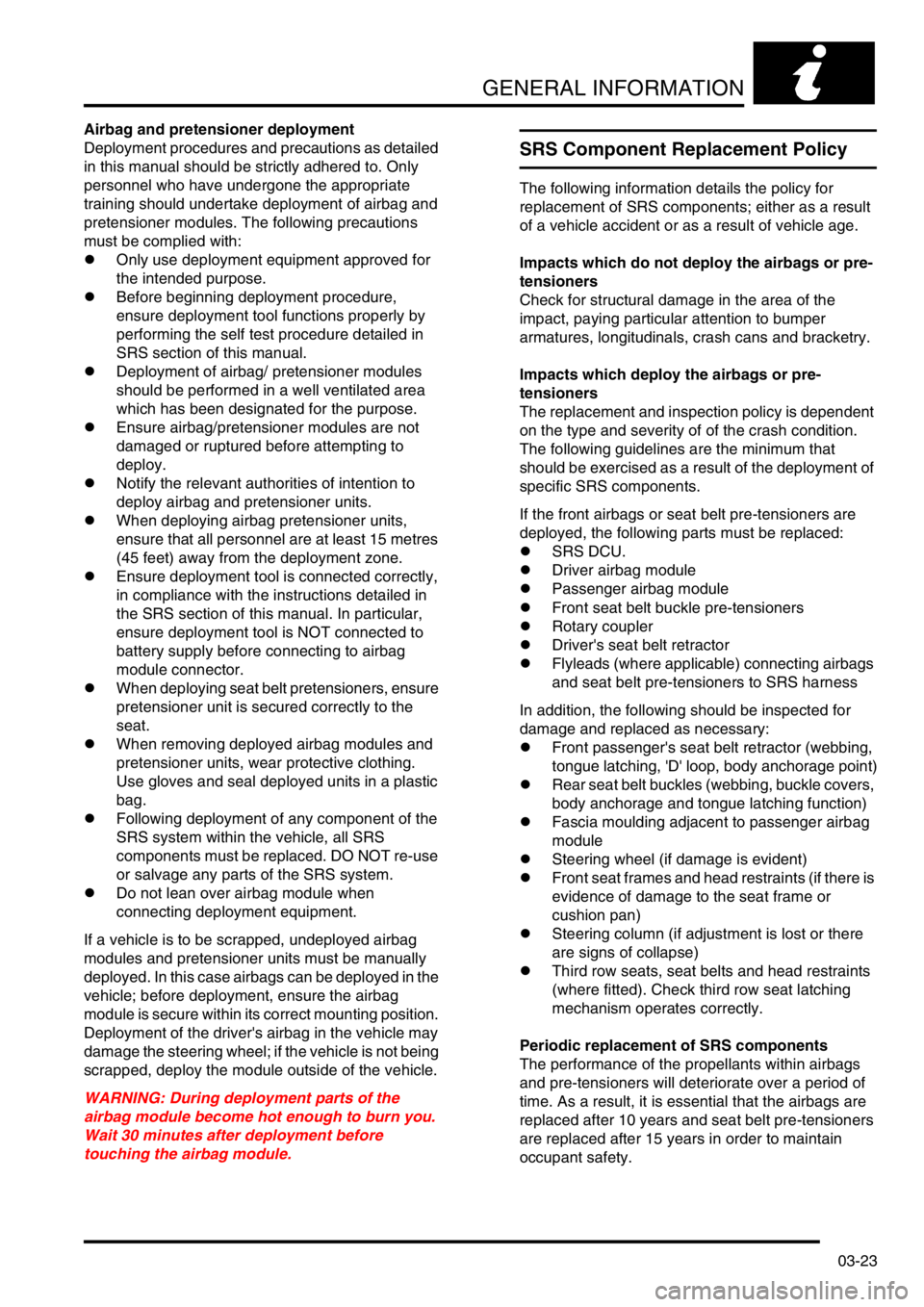
GENERAL INFORMATION
03-23
Airbag and pretensioner deployment
Deployment procedures and precautions as detailed
in this manual should be strictly adhered to. Only
personnel who have undergone the appropriate
training should undertake deployment of airbag and
pretensioner modules. The following precautions
must be complied with:
lOnly use deployment equipment approved for
the intended purpose.
lBefore beginning deployment procedure,
ensure deployment tool functions properly by
performing the self test procedure detailed in
SRS section of this manual.
lDeployment of airbag/ pretensioner modules
should be performed in a well ventilated area
which has been designated for the purpose.
lEnsure airbag/pretensioner modules are not
damaged or ruptured before attempting to
deploy.
lNotify the relevant authorities of intention to
deploy airbag and pretensioner units.
lWhen deploying airbag pretensioner units,
ensure that all personnel are at least 15 metres
(45 feet) away from the deployment zone.
lEnsure deployment tool is connected correctly,
in compliance with the instructions detailed in
the SRS section of this manual. In particular,
ensure deployment tool is NOT connected to
battery supply before connecting to airbag
module connector.
lWhen deploying seat belt pretensioners, ensure
pretensioner unit is secured correctly to the
seat.
lWhen removing deployed airbag modules and
pretensioner units, wear protective clothing.
Use gloves and seal deployed units in a plastic
bag.
lFollowing deployment of any component of the
SRS system within the vehicle, all SRS
components must be replaced. DO NOT re-use
or salvage any parts of the SRS system.
lDo not lean over airbag module when
connecting deployment equipment.
If a vehicle is to be scrapped, undeployed airbag
modules and pretensioner units must be manually
deployed. In this case airbags can be deployed in the
vehicle; before deployment, ensure the airbag
module is secure within its correct mounting position.
Deployment of the driver's airbag in the vehicle may
damage the steering wheel; if the vehicle is not being
scrapped, deploy the module outside of the vehicle.
WARNING: During deployment parts of the
airbag module become hot enough to burn you.
Wait 30 minutes after deployment before
touching the airbag module.
SRS Component Replacement Policy
The following information details the policy for
replacement of SRS components; either as a result
of a vehicle accident or as a result of vehicle age.
Impacts which do not deploy the airbags or pre-
tensioners
Check for structural damage in the area of the
impact, paying particular attention to bumper
armatures, longitudinals, crash cans and bracketry.
Impacts which deploy the airbags or pre-
tensioners
The replacement and inspection policy is dependent
on the type and severity of of the crash condition.
The following guidelines are the minimum that
should be exercised as a result of the deployment of
specific SRS components.
If the front airbags or seat belt pre-tensioners are
deployed, the following parts must be replaced:
lSRS DCU.
lDriver airbag module
lPassenger airbag module
lFront seat belt buckle pre-tensioners
lRotary coupler
lDriver's seat belt retractor
lFlyleads (where applicable) connecting airbags
and seat belt pre-tensioners to SRS harness
In addition, the following should be inspected for
damage and replaced as necessary:
lFront passenger's seat belt retractor (webbing,
tongue latching, 'D' loop, body anchorage point)
lRear seat belt buckles (webbing, buckle covers,
body anchorage and tongue latching function)
lFascia moulding adjacent to passenger airbag
module
lSteering wheel (if damage is evident)
lFront seat frames and head restraints (if there is
evidence of damage to the seat frame or
cushion pan)
lSteering column (if adjustment is lost or there
are signs of collapse)
lThird row seats, seat belts and head restraints
(where fitted). Check third row seat latching
mechanism operates correctly.
Periodic replacement of SRS components
The performance of the propellants within airbags
and pre-tensioners will deteriorate over a period of
time. As a result, it is essential that the airbags are
replaced after 10 years and seat belt pre-tensioners
are replaced after 15 years in order to maintain
occupant safety.
Page 99 of 1672
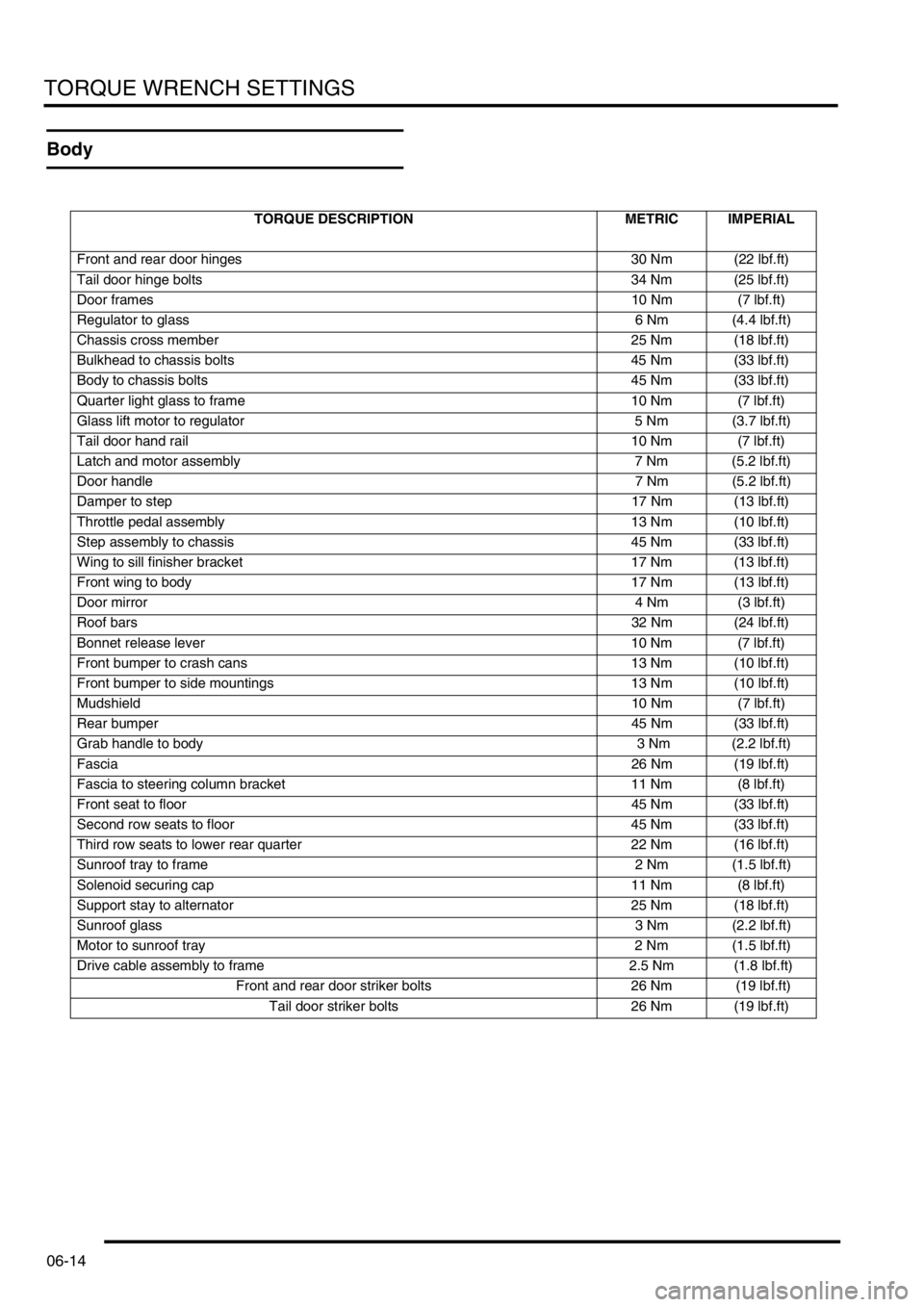
TORQUE WRENCH SETTINGS
06-14
Body
TORQUE DESCRIPTION METRIC IMPERIAL
Front and rear door hinges 30 Nm (22 lbf.ft)
Tail door hinge bolts 34 Nm (25 lbf.ft)
Door frames10 Nm (7 lbf.ft)
Regulator to glass 6 Nm (4.4 lbf.ft)
Chassis cross member 25 Nm (18 lbf.ft)
Bulkhead to chassis bolts 45 Nm (33 lbf.ft)
Body to chassis bolts 45 Nm (33 lbf.ft)
Quarter light glass to frame 10 Nm (7 lbf.ft)
Glass lift motor to regulator 5 Nm (3.7 lbf.ft)
Tail door hand rail 10 Nm (7 lbf.ft)
Latch and motor assembly 7 Nm (5.2 lbf.ft)
Door handle7 Nm (5.2 lbf.ft)
Damper to step17 Nm (13 lbf.ft)
Throttle pedal assembly 13 Nm (10 lbf.ft)
Step assembly to chassis 45 Nm (33 lbf.ft)
Wing to sill finisher bracket 17 Nm (13 lbf.ft)
Front wing to body 17 Nm (13 lbf.ft)
Door mirror4 Nm (3 lbf.ft)
Roof bars32 Nm (24 lbf.ft)
Bonnet release lever 10 Nm (7 lbf.ft)
Front bumper to crash cans 13 Nm (10 lbf.ft)
Front bumper to side mountings 13 Nm (10 lbf.ft)
Mudshield10 Nm (7 lbf.ft)
Rear bumper45 Nm (33 lbf.ft)
Grab handle to body 3 Nm (2.2 lbf.ft)
Fascia26 Nm (19 lbf.ft)
Fascia to steering column bracket 11 Nm (8 lbf.ft)
Front seat to floor 45 Nm (33 lbf.ft)
Second row seats to floor 45 Nm (33 lbf.ft)
Third row seats to lower rear quarter 22 Nm (16 lbf.ft)
Sunroof tray to frame 2 Nm (1.5 lbf.ft)
Solenoid securing cap 11 Nm (8 lbf.ft)
Support stay to alternator 25 Nm (18 lbf.ft)
Sunroof glass3 Nm (2.2 lbf.ft)
Motor to sunroof tray 2 Nm (1.5 lbf.ft)
Drive cable assembly to frame 2.5 Nm (1.8 lbf.ft)
Front and rear door striker bolts 26 Nm (19 lbf.ft)
Tail door striker bolts 26 Nm (19 lbf.ft)
Page 102 of 1672
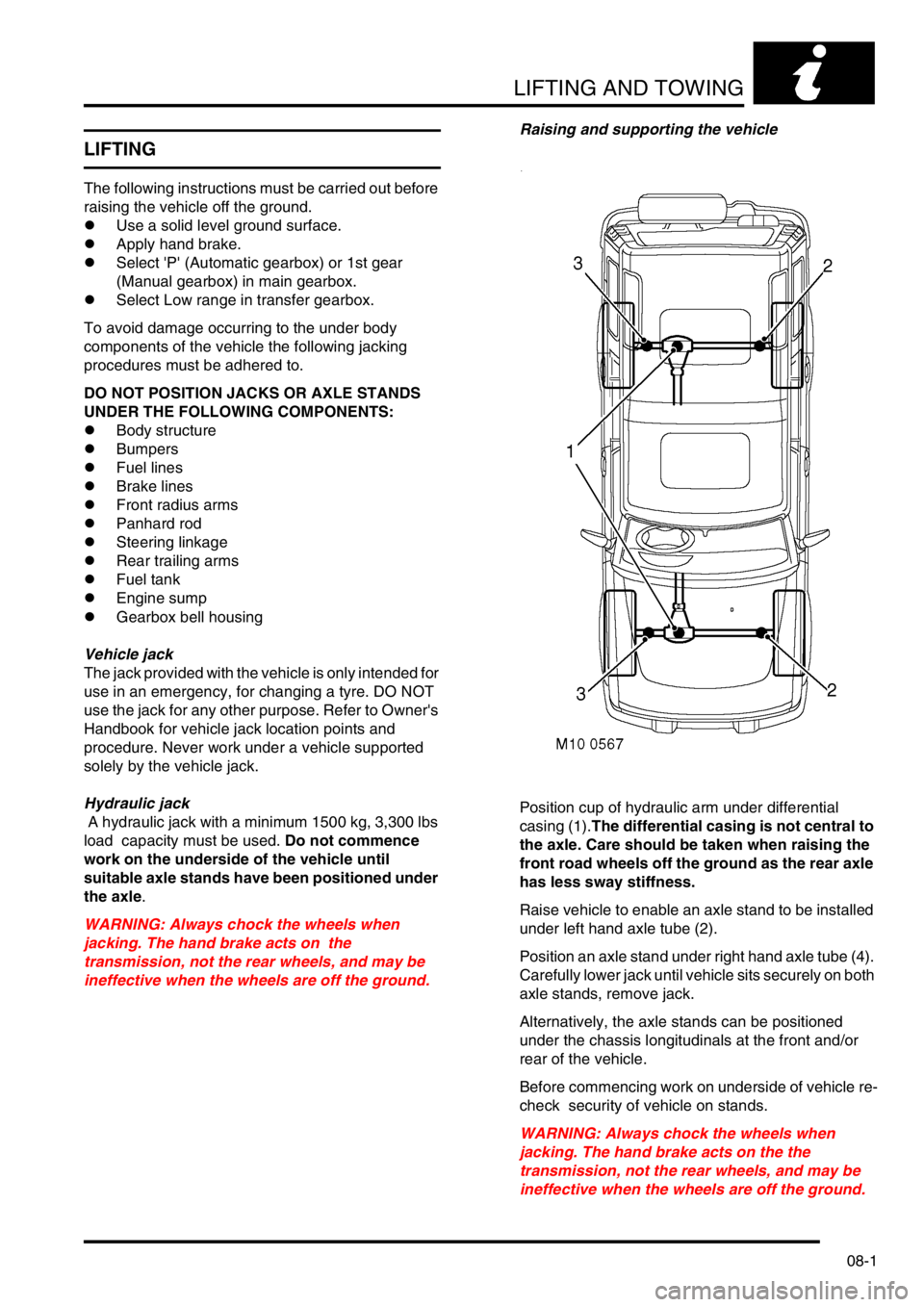
LIFTING AND TOWING
08-1
LIFTING AND TOWING
LIFTING
The following instructions must be carried out before
raising the vehicle off the ground.
lUse a solid level ground surface.
lApply hand brake.
lSelect 'P' (Automatic gearbox) or 1st gear
(Manual gearbox) in main gearbox.
lSelect Low range in transfer gearbox.
To avoid damage occurring to the under body
components of the vehicle the following jacking
procedures must be adhered to.
DO NOT POSITION JACKS OR AXLE STANDS
UNDER THE FOLLOWING COMPONENTS:
lBody structure
lBumpers
lFuel lines
lBrake lines
lFront radius arms
lPanhard rod
lSteering linkage
lRear trailing arms
lFuel tank
lEngine sump
lGearbox bell housing
Vehicle jack
The jack provided with the vehicle is only intended for
use in an emergency, for changing a tyre. DO NOT
use the jack for any other purpose. Refer to Owner's
Handbook for vehicle jack location points and
procedure. Never work under a vehicle supported
solely by the vehicle jack.
Hydraulic jack
A hydraulic jack with a minimum 1500 kg, 3,300 lbs
load capacity must be used. Do not commence
work on the underside of the vehicle until
suitable axle stands have been positioned under
the axle.
WARNING: Always chock the wheels when
jacking. The hand brake acts on the
transmission, not the rear wheels, and may be
ineffective when the wheels are off the ground.Raising and supporting the vehicle
Position cup of hydraulic arm under differential
casing (1).The differential casing is not central to
the axle. Care should be taken when raising the
front road wheels off the ground as the rear axle
has less sway stiffness.
Raise vehicle to enable an axle stand to be installed
under left hand axle tube (2).
Position an axle stand under right hand axle tube (4).
Carefully lower jack until vehicle sits securely on both
axle stands, remove jack.
Alternatively, the axle stands can be positioned
under the chassis longitudinals at the front and/or
rear of the vehicle.
Before commencing work on underside of vehicle re-
check security of vehicle on stands.
WARNING: Always chock the wheels when
jacking. The hand brake acts on the the
transmission, not the rear wheels, and may be
ineffective when the wheels are off the ground.