ECU LAND ROVER DISCOVERY 2002 Workshop Manual
[x] Cancel search | Manufacturer: LAND ROVER, Model Year: 2002, Model line: DISCOVERY, Model: LAND ROVER DISCOVERY 2002Pages: 1672, PDF Size: 46.1 MB
Page 646 of 1672
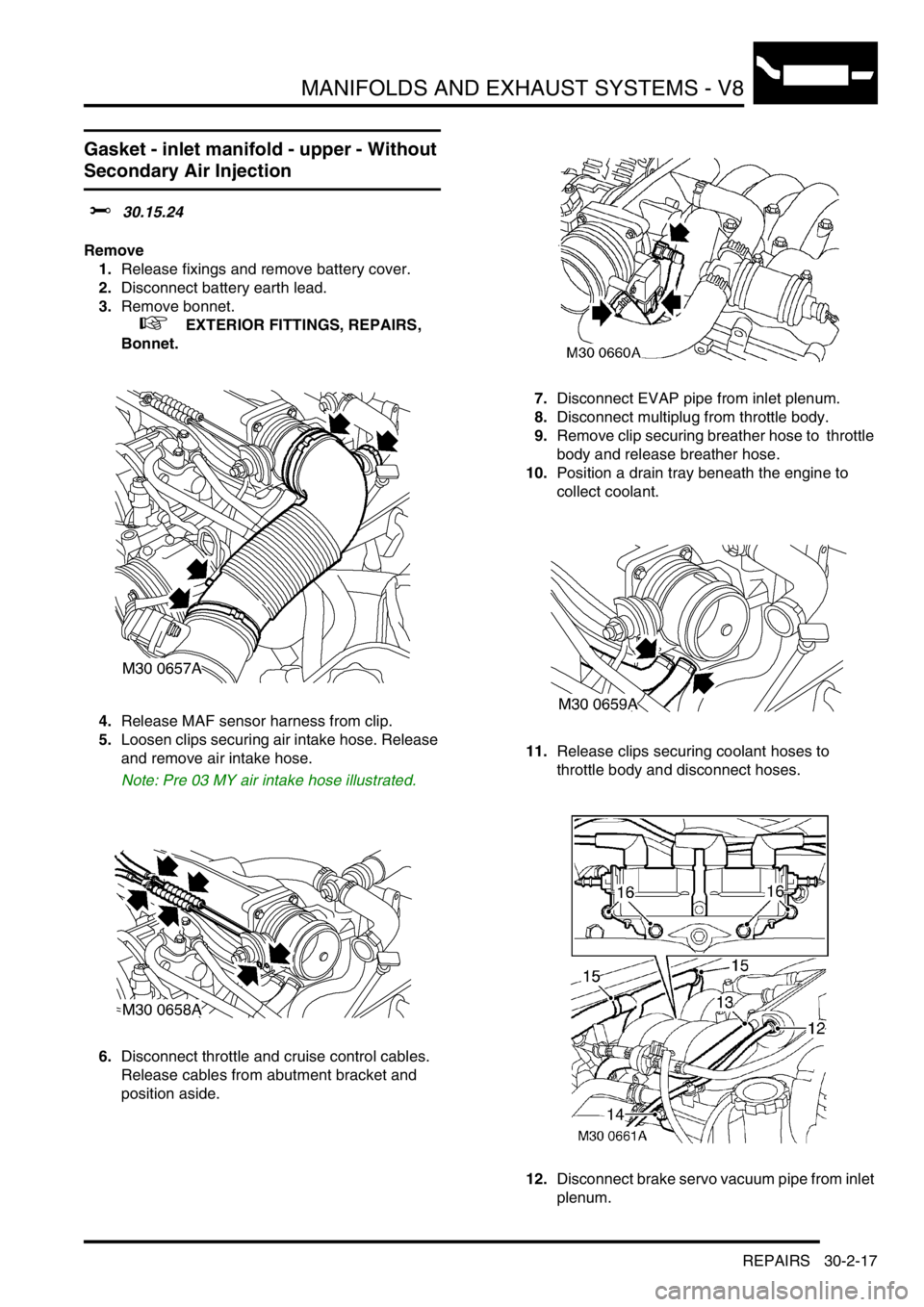
MANIFOLDS AND EXHAUST SYSTEMS - V8
REPAIRS 30-2-17
Gasket - inlet manifold - upper - Without
Secondary Air Injection
$% 30.15.24
Remove
1.Release fixings and remove battery cover.
2.Disconnect battery earth lead.
3.Remove bonnet.
+ EXTERIOR FITTINGS, REPAIRS,
Bonnet.
4.Release MAF sensor harness from clip.
5.Loosen clips securing air intake hose. Release
and remove air intake hose.
Note: Pre 03 MY air intake hose illustrated.
6.Disconnect throttle and cruise control cables.
Release cables from abutment bracket and
position aside. 7.Disconnect EVAP pipe from inlet plenum.
8.Disconnect multiplug from throttle body.
9.Remove clip securing breather hose to throttle
body and release breather hose.
10.Position a drain tray beneath the engine to
collect coolant.
11.Release clips securing coolant hoses to
throttle body and disconnect hoses.
12.Disconnect brake servo vacuum pipe from inlet
plenum.
Page 647 of 1672
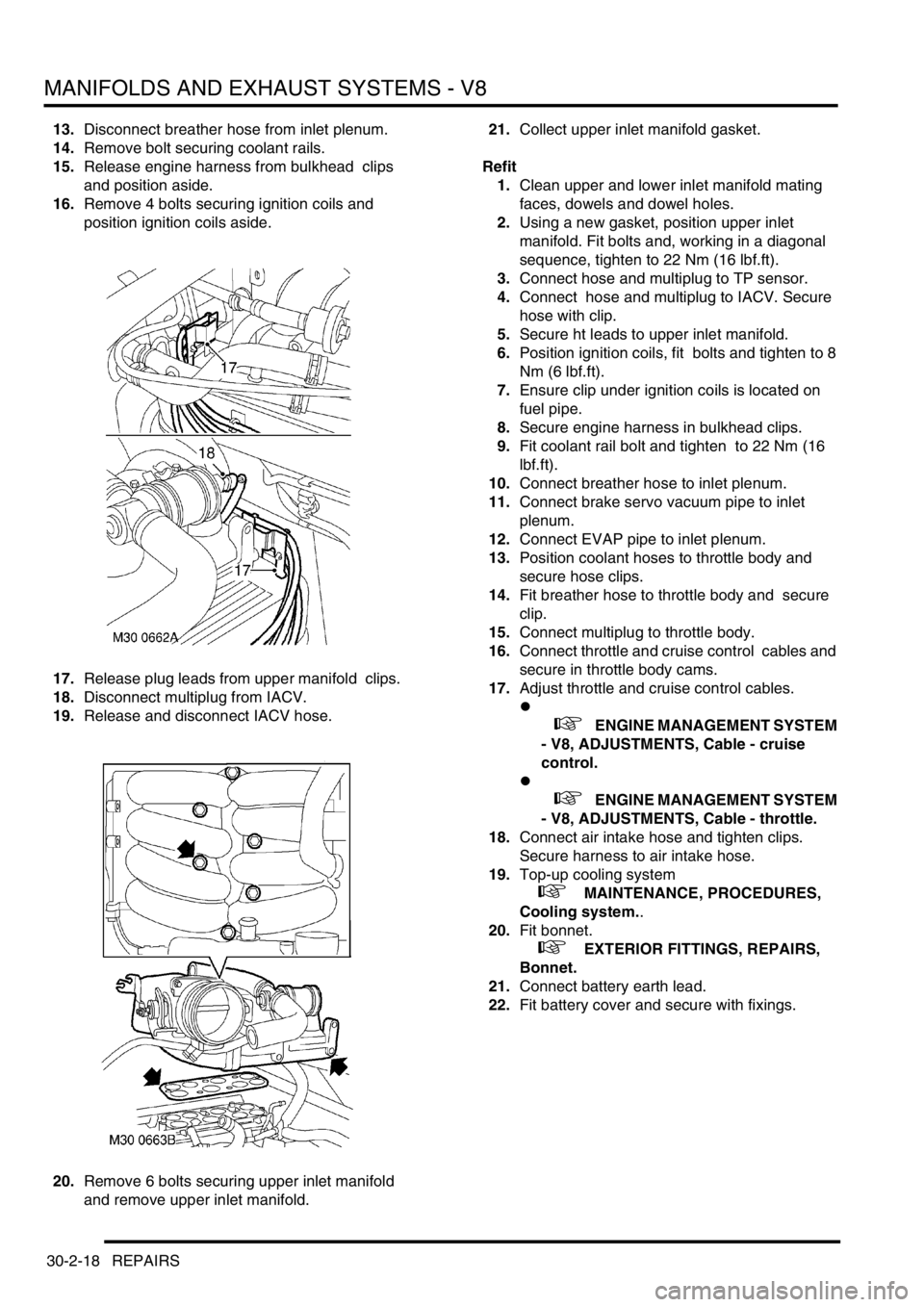
MANIFOLDS AND EXHAUST SYSTEMS - V8
30-2-18 REPAIRS
13.Disconnect breather hose from inlet plenum.
14.Remove bolt securing coolant rails.
15.Release engine harness from bulkhead clips
and position aside.
16.Remove 4 bolts securing ignition coils and
position ignition coils aside.
17.Release plug leads from upper manifold clips.
18.Disconnect multiplug from IACV.
19.Release and disconnect IACV hose.
20.Remove 6 bolts securing upper inlet manifold
and remove upper inlet manifold. 21.Collect upper inlet manifold gasket.
Refit
1.Clean upper and lower inlet manifold mating
faces, dowels and dowel holes.
2.Using a new gasket, position upper inlet
manifold. Fit bolts and, working in a diagonal
sequence, tighten to 22 Nm (16 lbf.ft).
3.Connect hose and multiplug to TP sensor.
4.Connect hose and multiplug to IACV. Secure
hose with clip.
5.Secure ht leads to upper inlet manifold.
6.Position ignition coils, fit bolts and tighten to 8
Nm (6 lbf.ft).
7.Ensure clip under ignition coils is located on
fuel pipe.
8.Secure engine harness in bulkhead clips.
9.Fit coolant rail bolt and tighten to 22 Nm (16
lbf.ft).
10.Connect breather hose to inlet plenum.
11.Connect brake servo vacuum pipe to inlet
plenum.
12.Connect EVAP pipe to inlet plenum.
13.Position coolant hoses to throttle body and
secure hose clips.
14.Fit breather hose to throttle body and secure
clip.
15.Connect multiplug to throttle body.
16.Connect throttle and cruise control cables and
secure in throttle body cams.
17.Adjust throttle and cruise control cables.
l
+ ENGINE MANAGEMENT SYSTEM
- V8, ADJUSTMENTS, Cable - cruise
control.
l
+ ENGINE MANAGEMENT SYSTEM
- V8, ADJUSTMENTS, Cable - throttle.
18.Connect air intake hose and tighten clips.
Secure harness to air intake hose.
19.Top-up cooling system
+ MAINTENANCE, PROCEDURES,
Cooling system..
20.Fit bonnet.
+ EXTERIOR FITTINGS, REPAIRS,
Bonnet.
21.Connect battery earth lead.
22.Fit battery cover and secure with fixings.
Page 648 of 1672
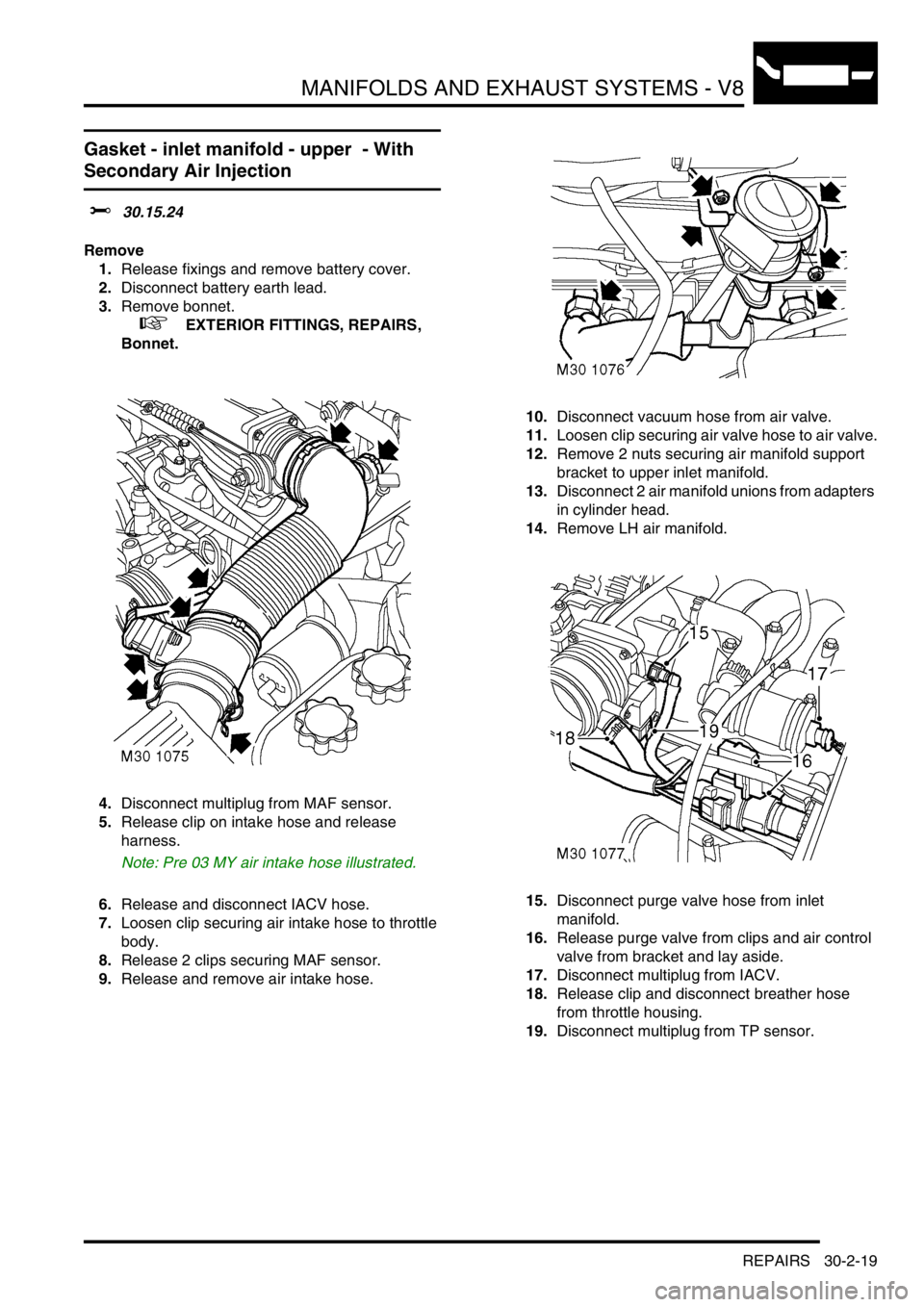
MANIFOLDS AND EXHAUST SYSTEMS - V8
REPAIRS 30-2-19
Gasket - inlet manifold - upper - With
Secondary Air Injection
$% 30.15.24
Remove
1.Release fixings and remove battery cover.
2.Disconnect battery earth lead.
3.Remove bonnet.
+ EXTERIOR FITTINGS, REPAIRS,
Bonnet.
4.Disconnect multiplug from MAF sensor.
5.Release clip on intake hose and release
harness.
Note: Pre 03 MY air intake hose illustrated.
6.Release and disconnect IACV hose.
7.Loosen clip securing air intake hose to throttle
body.
8.Release 2 clips securing MAF sensor.
9.Release and remove air intake hose.10.Disconnect vacuum hose from air valve.
11.Loosen clip securing air valve hose to air valve.
12.Remove 2 nuts securing air manifold support
bracket to upper inlet manifold.
13.Disconnect 2 air manifold unions from adapters
in cylinder head.
14.Remove LH air manifold.
15.Disconnect purge valve hose from inlet
manifold.
16.Release purge valve from clips and air control
valve from bracket and lay aside.
17.Disconnect multiplug from IACV.
18.Release clip and disconnect breather hose
from throttle housing.
19.Disconnect multiplug from TP sensor.
Page 649 of 1672
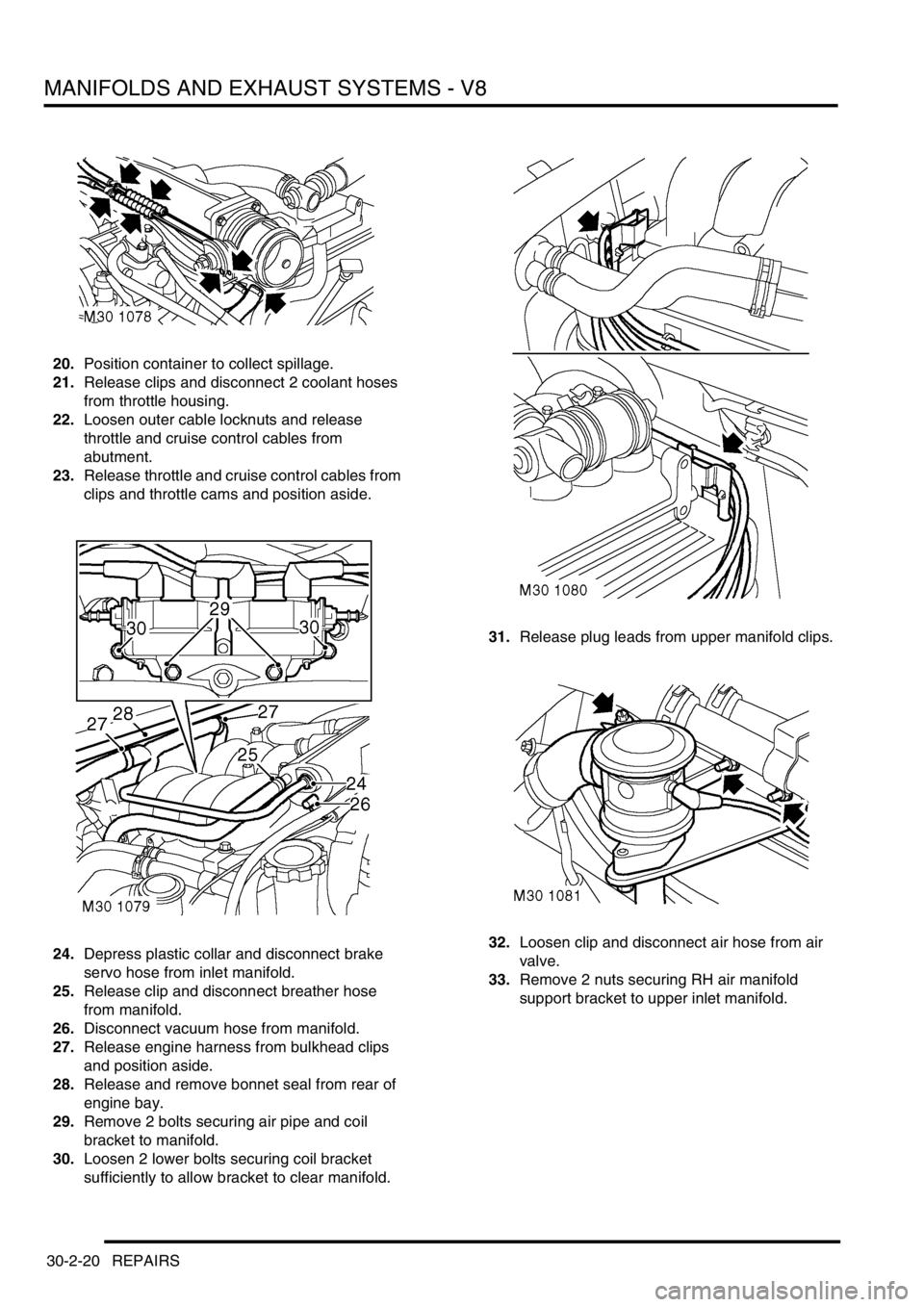
MANIFOLDS AND EXHAUST SYSTEMS - V8
30-2-20 REPAIRS
20.Position container to collect spillage.
21.Release clips and disconnect 2 coolant hoses
from throttle housing.
22.Loosen outer cable locknuts and release
throttle and cruise control cables from
abutment.
23.Release throttle and cruise control cables from
clips and throttle cams and position aside.
24.Depress plastic collar and disconnect brake
servo hose from inlet manifold.
25.Release clip and disconnect breather hose
from manifold.
26.Disconnect vacuum hose from manifold.
27.Release engine harness from bulkhead clips
and position aside.
28.Release and remove bonnet seal from rear of
engine bay.
29.Remove 2 bolts securing air pipe and coil
bracket to manifold.
30.Loosen 2 lower bolts securing coil bracket
sufficiently to allow bracket to clear manifold.31.Release plug leads from upper manifold clips.
32.Loosen clip and disconnect air hose from air
valve.
33.Remove 2 nuts securing RH air manifold
support bracket to upper inlet manifold.
Page 650 of 1672
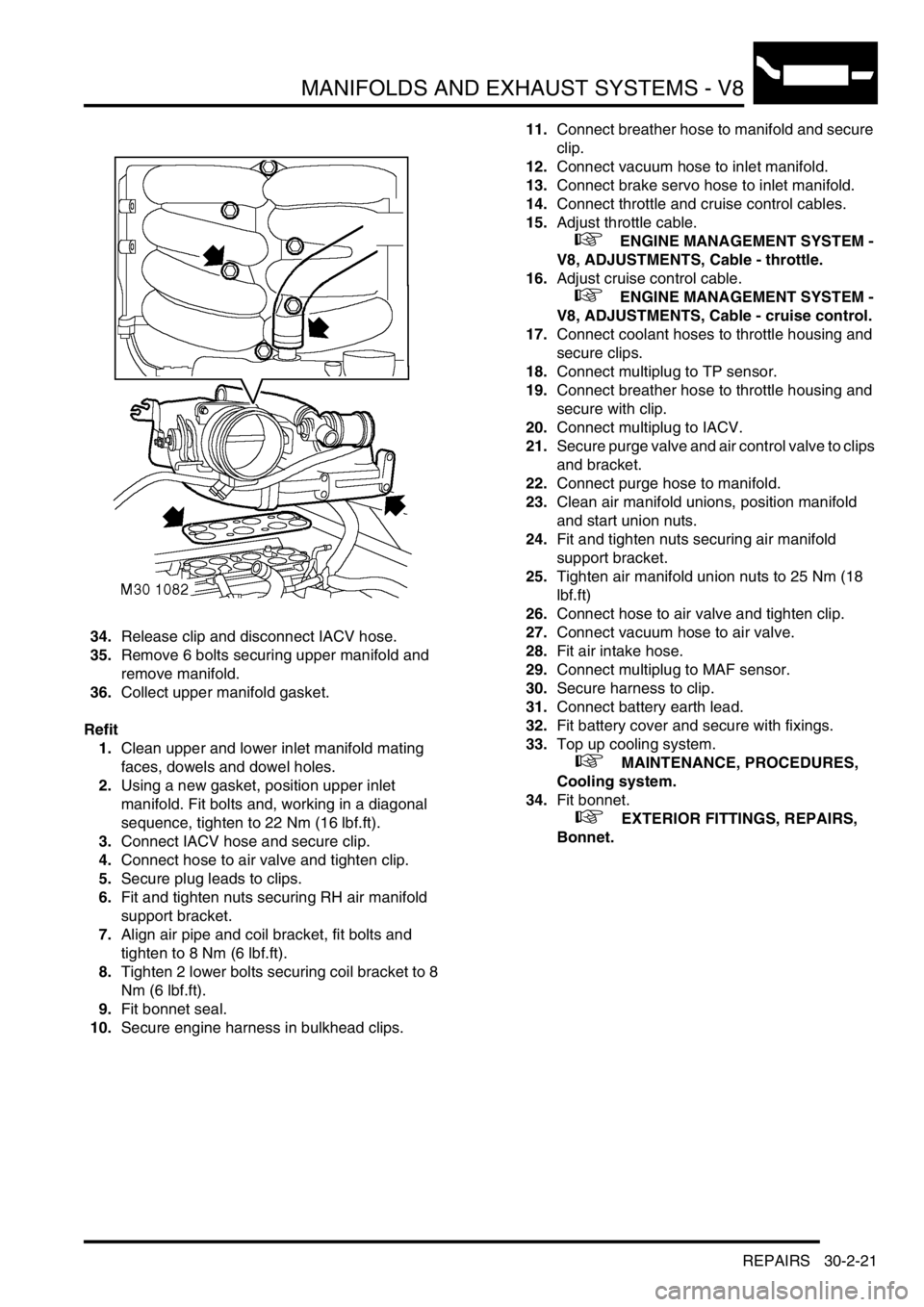
MANIFOLDS AND EXHAUST SYSTEMS - V8
REPAIRS 30-2-21
34.Release clip and disconnect IACV hose.
35.Remove 6 bolts securing upper manifold and
remove manifold.
36.Collect upper manifold gasket.
Refit
1.Clean upper and lower inlet manifold mating
faces, dowels and dowel holes.
2.Using a new gasket, position upper inlet
manifold. Fit bolts and, working in a diagonal
sequence, tighten to 22 Nm (16 lbf.ft).
3.Connect IACV hose and secure clip.
4.Connect hose to air valve and tighten clip.
5.Secure plug leads to clips.
6.Fit and tighten nuts securing RH air manifold
support bracket.
7.Align air pipe and coil bracket, fit bolts and
tighten to 8 Nm (6 lbf.ft).
8.Tighten 2 lower bolts securing coil bracket to 8
Nm (6 lbf.ft).
9.Fit bonnet seal.
10.Secure engine harness in bulkhead clips.11.Connect breather hose to manifold and secure
clip.
12.Connect vacuum hose to inlet manifold.
13.Connect brake servo hose to inlet manifold.
14.Connect throttle and cruise control cables.
15.Adjust throttle cable.
+ ENGINE MANAGEMENT SYSTEM -
V8, ADJUSTMENTS, Cable - throttle.
16.Adjust cruise control cable.
+ ENGINE MANAGEMENT SYSTEM -
V8, ADJUSTMENTS, Cable - cruise control.
17.Connect coolant hoses to throttle housing and
secure clips.
18.Connect multiplug to TP sensor.
19.Connect breather hose to throttle housing and
secure with clip.
20.Connect multiplug to IACV.
21.Secure purge valve and air control valve to clips
and bracket.
22.Connect purge hose to manifold.
23.Clean air manifold unions, position manifold
and start union nuts.
24.Fit and tighten nuts securing air manifold
support bracket.
25.Tighten air manifold union nuts to 25 Nm (18
lbf.ft)
26.Connect hose to air valve and tighten clip.
27.Connect vacuum hose to air valve.
28.Fit air intake hose.
29.Connect multiplug to MAF sensor.
30.Secure harness to clip.
31.Connect battery earth lead.
32.Fit battery cover and secure with fixings.
33.Top up cooling system.
+ MAINTENANCE, PROCEDURES,
Cooling system.
34.Fit bonnet.
+ EXTERIOR FITTINGS, REPAIRS,
Bonnet.
Page 657 of 1672
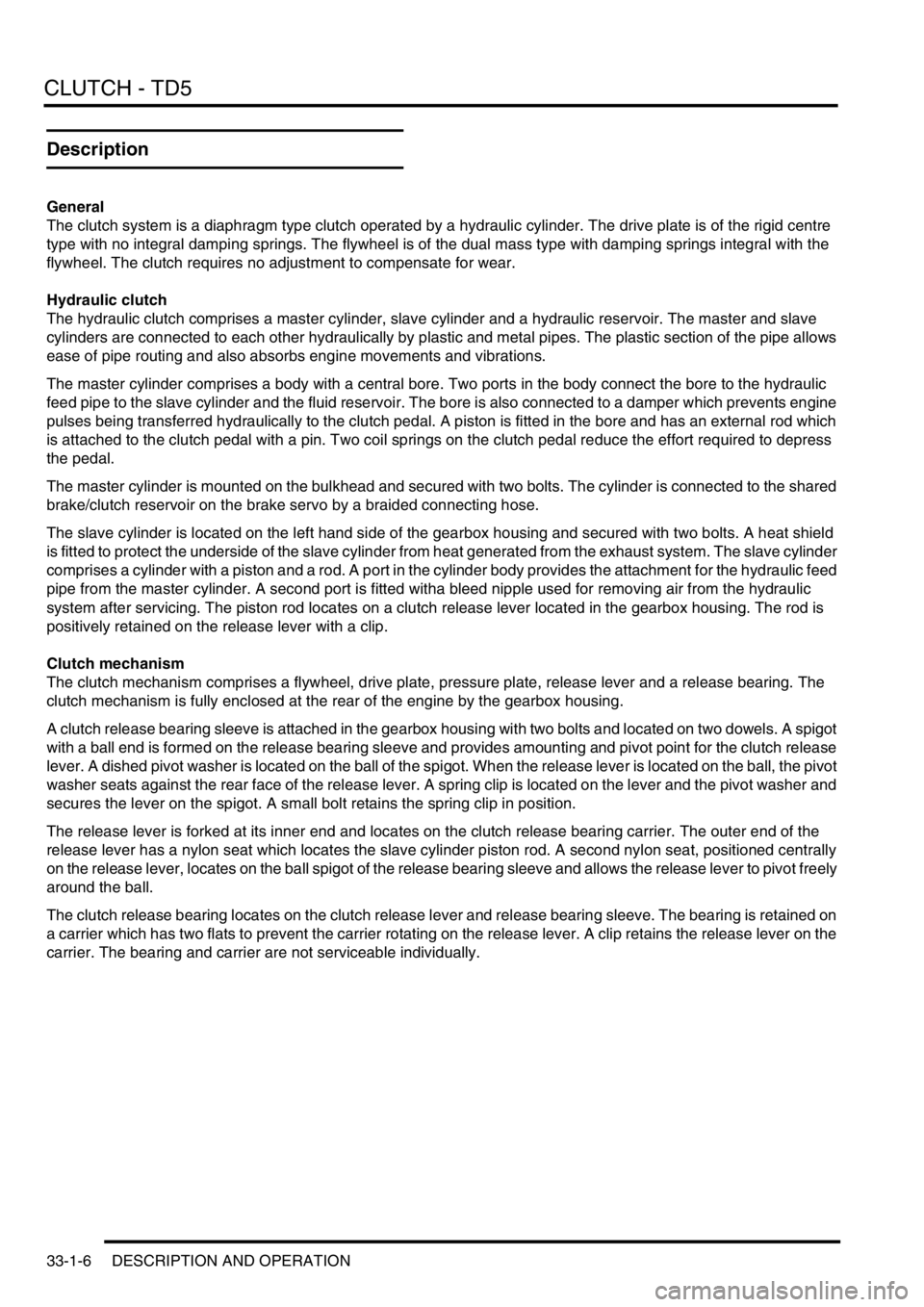
CLUTCH - TD5
33-1-6 DESCRIPTION AND OPERATION
Description
General
The clutch system is a diaphragm type clutch operated by a hydraulic cylinder. The drive plate is of the rigid centre
type with no integral damping springs. The flywheel is of the dual mass type with damping springs integral with the
flywheel. The clutch requires no adjustment to compensate for wear.
Hydraulic clutch
The hydraulic clutch comprises a master cylinder, slave cylinder and a hydraulic reservoir. The master and slave
cylinders are connected to each other hydraulically by plastic and metal pipes. The plastic section of the pipe allows
ease of pipe routing and also absorbs engine movements and vibrations.
The master cylinder comprises a body with a central bore. Two ports in the body connect the bore to the hydraulic
feed pipe to the slave cylinder and the fluid reservoir. The bore is also connected to a damper which prevents engine
pulses being transferred hydraulically to the clutch pedal. A piston is fitted in the bore and has an external rod which
is attached to the clutch pedal with a pin. Two coil springs on the clutch pedal reduce the effort required to depress
the pedal.
The master cylinder is mounted on the bulkhead and secured with two bolts. The cylinder is connected to the shared
brake/clutch reservoir on the brake servo by a braided connecting hose.
The slave cylinder is located on the left hand side of the gearbox housing and secured with two bolts. A heat shield
is fitted to protect the underside of the slave cylinder from heat generated from the exhaust system. The slave cylinder
comprises a cylinder with a piston and a rod. A port in the cylinder body provides the attachment for the hydraulic feed
pipe from the master cylinder. A second port is fitted witha bleed nipple used for removing air from the hydraulic
system after servicing. The piston rod locates on a clutch release lever located in the gearbox housing. The rod is
positively retained on the release lever with a clip.
Clutch mechanism
The clutch mechanism comprises a flywheel, drive plate, pressure plate, release lever and a release bearing. The
clutch mechanism is fully enclosed at the rear of the engine by the gearbox housing.
A clutch release bearing sleeve is attached in the gearbox housing with two bolts and located on two dowels. A spigot
with a ball end is formed on the release bearing sleeve and provides amounting and pivot point for the clutch release
lever. A dished pivot washer is located on the ball of the spigot. When the release lever is located on the ball, the pivot
washer seats against the rear face of the release lever. A spring clip is located on the lever and the pivot washer and
secures the lever on the spigot. A small bolt retains the spring clip in position.
The release lever is forked at its inner end and locates on the clutch release bearing carrier. The outer end of the
release lever has a nylon seat which locates the slave cylinder piston rod. A second nylon seat, positioned centrally
on the release lever, locates on the ball spigot of the release bearing sleeve and allows the release lever to pivot freely
around the ball.
The clutch release bearing locates on the clutch release lever and release bearing sleeve. The bearing is retained on
a carrier which has two flats to prevent the carrier rotating on the release lever. A clip retains the release lever on the
carrier. The bearing and carrier are not serviceable individually.
Page 659 of 1672
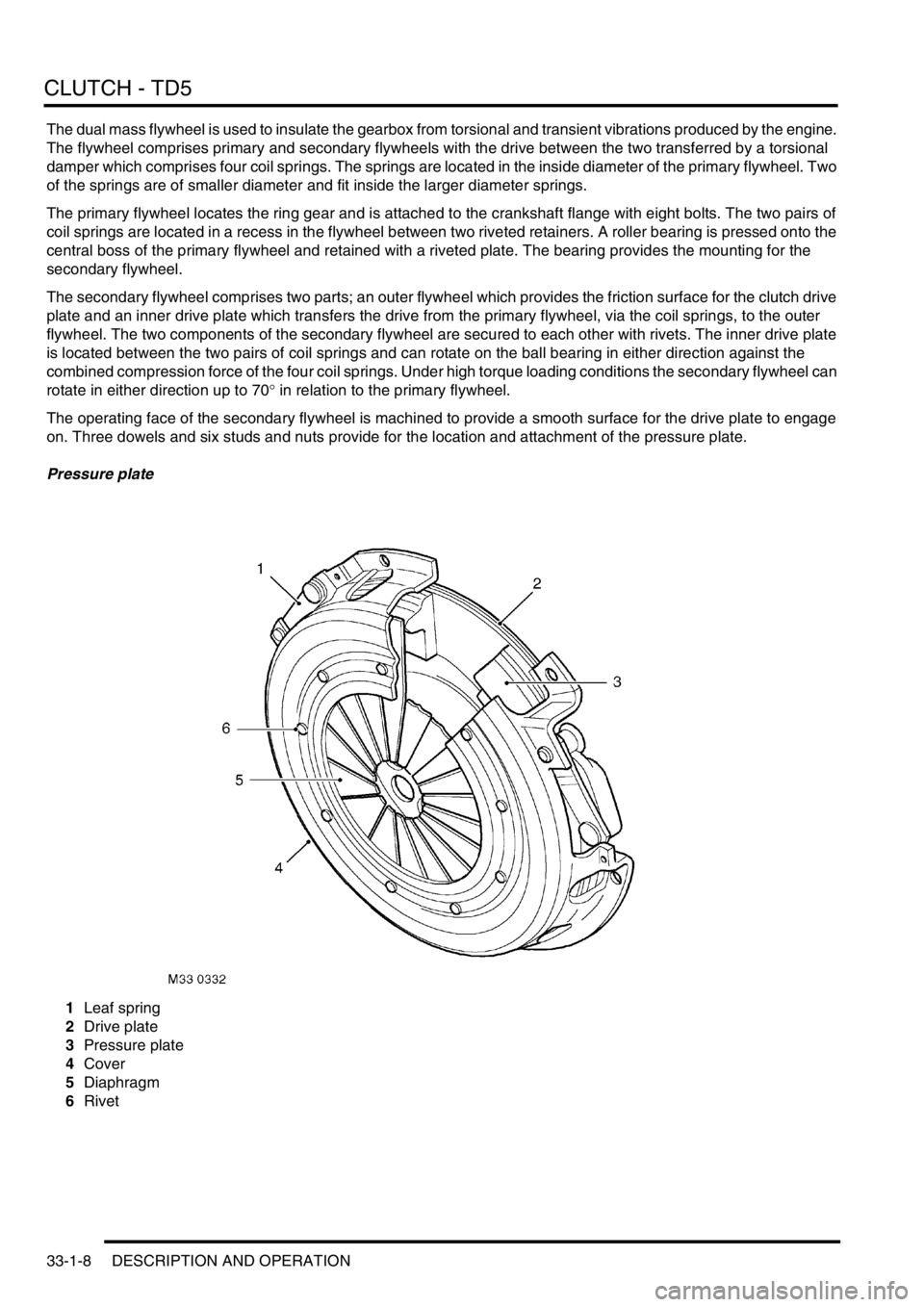
CLUTCH - TD5
33-1-8 DESCRIPTION AND OPERATION
The dual mass flywheel is used to insulate the gearbox from torsional and transient vibrations produced by the engine.
The flywheel comprises primary and secondary flywheels with the drive between the two transferred by a torsional
damper which comprises four coil springs. The springs are located in the inside diameter of the primary flywheel. Two
of the springs are of smaller diameter and fit inside the larger diameter springs.
The primary flywheel locates the ring gear and is attached to the crankshaft flange with eight bolts. The two pairs of
coil springs are located in a recess in the flywheel between two riveted retainers. A roller bearing is pressed onto the
central boss of the primary flywheel and retained with a riveted plate. The bearing provides the mounting for the
secondary flywheel.
The secondary flywheel comprises two parts; an outer flywheel which provides the friction surface for the clutch drive
plate and an inner drive plate which transfers the drive from the primary flywheel, via the coil springs, to the outer
flywheel. The two components of the secondary flywheel are secured to each other with rivets. The inner drive plate
is located between the two pairs of coil springs and can rotate on the ball bearing in either direction against the
combined compression force of the four coil springs. Under high torque loading conditions the secondary flywheel can
rotate in either direction up to 70
° in relation to the primary flywheel.
The operating face of the secondary flywheel is machined to provide a smooth surface for the drive plate to engage
on. Three dowels and six studs and nuts provide for the location and attachment of the pressure plate.
Pressure plate
1Leaf spring
2Drive plate
3Pressure plate
4Cover
5Diaphragm
6Rivet
Page 660 of 1672
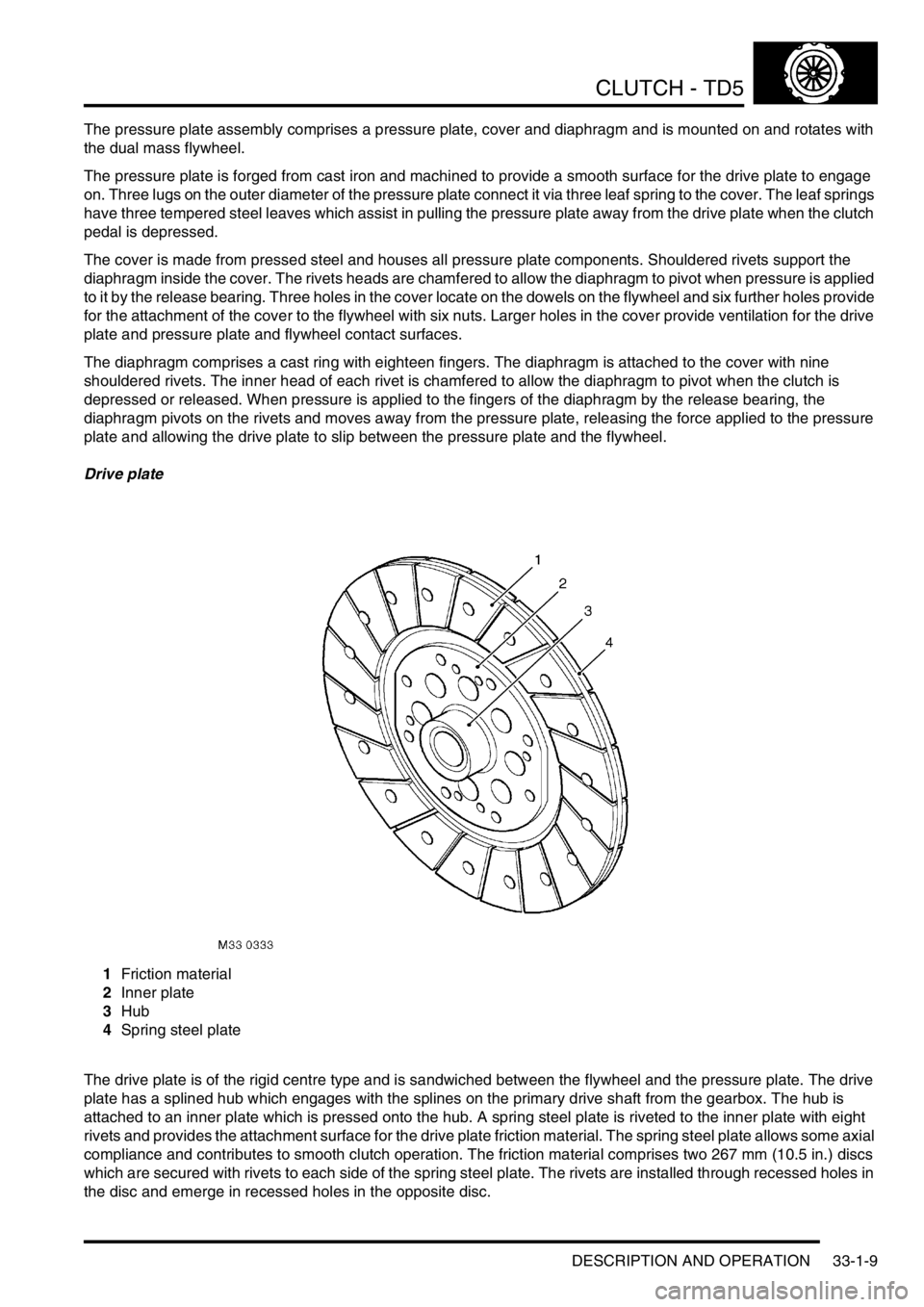
CLUTCH - TD5
DESCRIPTION AND OPERATION 33-1-9
The pressure plate assembly comprises a pressure plate, cover and diaphragm and is mounted on and rotates with
the dual mass flywheel.
The pressure plate is forged from cast iron and machined to provide a smooth surface for the drive plate to engage
on. Three lugs on the outer diameter of the pressure plate connect it via three leaf spring to the cover. The leaf springs
have three tempered steel leaves which assist in pulling the pressure plate away from the drive plate when the clutch
pedal is depressed.
The cover is made from pressed steel and houses all pressure plate components. Shouldered rivets support the
diaphragm inside the cover. The rivets heads are chamfered to allow the diaphragm to pivot when pressure is applied
to it by the release bearing. Three holes in the cover locate on the dowels on the flywheel and six further holes provide
for the attachment of the cover to the flywheel with six nuts. Larger holes in the cover provide ventilation for the drive
plate and pressure plate and flywheel contact surfaces.
The diaphragm comprises a cast ring with eighteen fingers. The diaphragm is attached to the cover with nine
shouldered rivets. The inner head of each rivet is chamfered to allow the diaphragm to pivot when the clutch is
depressed or released. When pressure is applied to the fingers of the diaphragm by the release bearing, the
diaphragm pivots on the rivets and moves away from the pressure plate, releasing the force applied to the pressure
plate and allowing the drive plate to slip between the pressure plate and the flywheel.
Drive plate
1Friction material
2Inner plate
3Hub
4Spring steel plate
The drive plate is of the rigid centre type and is sandwiched between the flywheel and the pressure plate. The drive
plate has a splined hub which engages with the splines on the primary drive shaft from the gearbox. The hub is
attached to an inner plate which is pressed onto the hub. A spring steel plate is riveted to the inner plate with eight
rivets and provides the attachment surface for the drive plate friction material. The spring steel plate allows some axial
compliance and contributes to smooth clutch operation. The friction material comprises two 267 mm (10.5 in.) discs
which are secured with rivets to each side of the spring steel plate. The rivets are installed through recessed holes in
the disc and emerge in recessed holes in the opposite disc.
Page 664 of 1672
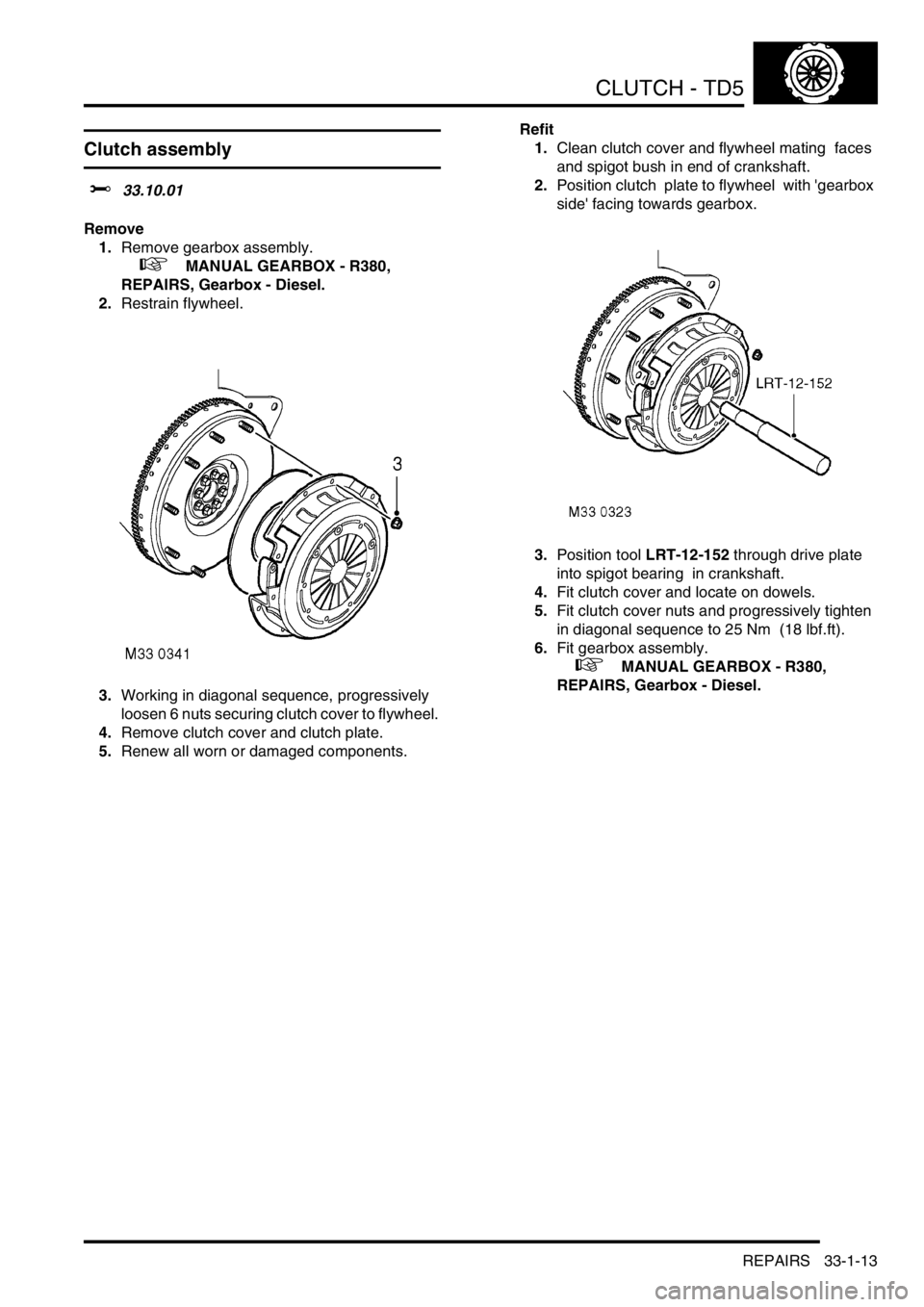
CLUTCH - TD5
REPAIRS 33-1-13
REPAIRS
Clutch assembly
$% 33.10.01
Remove
1.Remove gearbox assembly.
+ MANUAL GEARBOX - R380,
REPAIRS, Gearbox - Diesel.
2.Restrain flywheel.
3.Working in diagonal sequence, progressively
loosen 6 nuts securing clutch cover to flywheel.
4.Remove clutch cover and clutch plate.
5.Renew all worn or damaged components.Refit
1.Clean clutch cover and flywheel mating faces
and spigot bush in end of crankshaft.
2.Position clutch plate to flywheel with 'gearbox
side' facing towards gearbox.
3.Position tool LRT-12-152 through drive plate
into spigot bearing in crankshaft.
4.Fit clutch cover and locate on dowels.
5.Fit clutch cover nuts and progressively tighten
in diagonal sequence to 25 Nm (18 lbf.ft).
6.Fit gearbox assembly.
+ MANUAL GEARBOX - R380,
REPAIRS, Gearbox - Diesel.
Page 665 of 1672
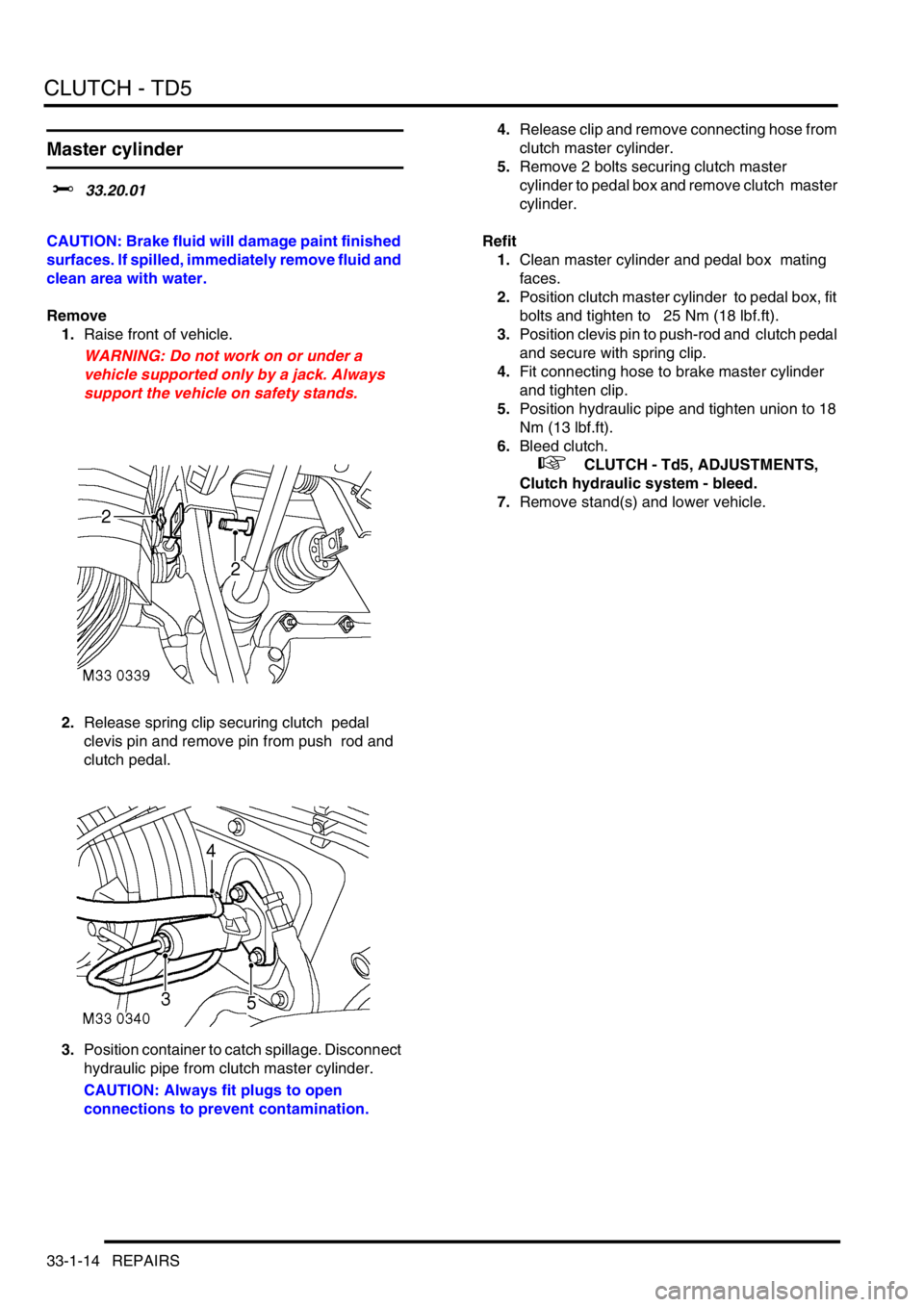
CLUTCH - TD5
33-1-14 REPAIRS
Master cylinder
$% 33.20.01
CAUTION: Brake fluid will damage paint finished
surfaces. If spilled, immediately remove fluid and
clean area with water.
Remove
1.Raise front of vehicle.
WARNING: Do not work on or under a
vehicle supported only by a jack. Always
support the vehicle on safety stands.
2.Release spring clip securing clutch pedal
clevis pin and remove pin from push rod and
clutch pedal.
3.Position container to catch spillage. Disconnect
hydraulic pipe from clutch master cylinder.
CAUTION: Always fit plugs to open
connections to prevent contamination.4.Release clip and remove connecting hose from
clutch master cylinder.
5.Remove 2 bolts securing clutch master
cylinder to pedal box and remove clutch master
cylinder.
Refit
1.Clean master cylinder and pedal box mating
faces.
2.Position clutch master cylinder to pedal box, fit
bolts and tighten to 25 Nm (18 lbf.ft).
3.Position clevis pin to push-rod and clutch pedal
and secure with spring clip.
4.Fit connecting hose to brake master cylinder
and tighten clip.
5.Position hydraulic pipe and tighten union to 18
Nm (13 lbf.ft).
6.Bleed clutch.
+ CLUTCH - Td5, ADJUSTMENTS,
Clutch hydraulic system - bleed.
7.Remove stand(s) and lower vehicle.