engine MAZDA 6 2002 Suplement Owner's Guide
[x] Cancel search | Manufacturer: MAZDA, Model Year: 2002, Model line: 6, Model: MAZDA 6 2002Pages: 909, PDF Size: 17.16 MB
Page 38 of 909
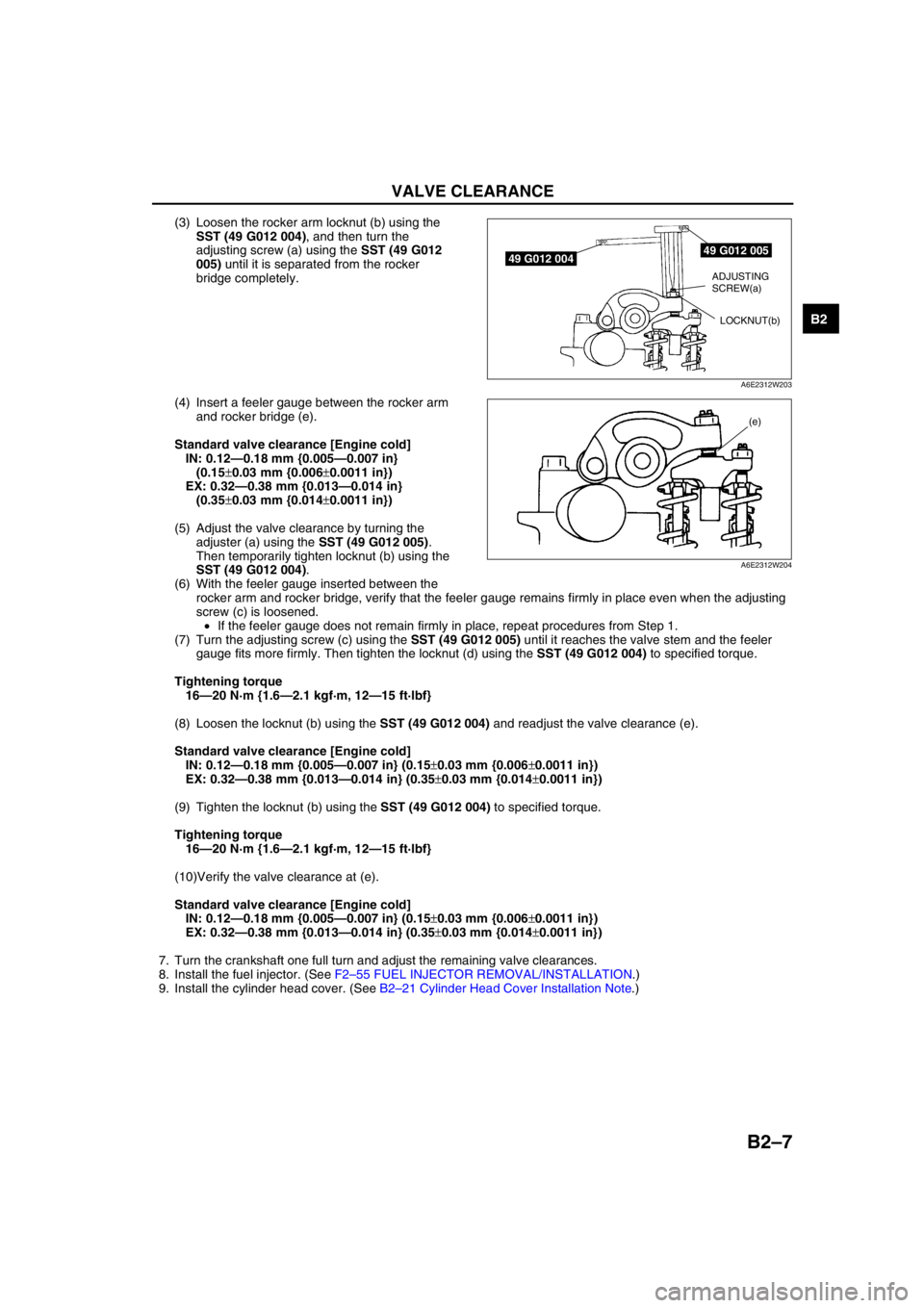
VALVE CLEARANCE
B2–7
B2
(3) Loosen the rocker arm locknut (b) using the
SST (49 G012 004), and then turn the
adjusting screw (a) using the SST (49 G012
005) until it is separated from the rocker
bridge completely.
(4) Insert a feeler gauge between the rocker arm
and rocker bridge (e).
Standard valve clearance [Engine cold]
IN: 0.12—0.18 mm {0.005—0.007 in}
(0.15±0.03 mm {0.006±0.0011 in})
EX: 0.32—0.38 mm {0.013—0.014 in}
(0.35±0.03 mm {0.014±0.0011 in})
(5) Adjust the valve clearance by turning the
adjuster (a) using the SST (49 G012 005).
Then temporarily tighten locknut (b) using the
SST (49 G012 004).
(6) With the feeler gauge inserted between the
rocker arm and rocker bridge, verify that the feeler gauge remains firmly in place even when the adjusting
screw (c) is loosened.
•If the feeler gauge does not remain firmly in place, repeat procedures from Step 1.
(7) Turn the adjusting screw (c) using the SST (49 G012 005) until it reaches the valve stem and the feeler
gauge fits more firmly. Then tighten the locknut (d) using the SST (49 G012 004) to specified torque.
Tightening torque
16—20 N·m {1.6—2.1 kgf·m, 12—15 ft·lbf}
(8) Loosen the locknut (b) using the SST (49 G012 004) and readjust the valve clearance (e).
Standard valve clearance [Engine cold]
IN: 0.12—0.18 mm {0.005—0.007 in} (0.15±0.03 mm {0.006±0.0011 in})
EX: 0.32—0.38 mm {0.013—0.014 in} (0.35±0.03 mm {0.014±0.0011 in})
(9) Tighten the locknut (b) using the SST (49 G012 004) to specified torque.
Tightening torque
16—20 N·m {1.6—2.1 kgf·m, 12—15 ft·lbf}
(10)Verify the valve clearance at (e).
Standard valve clearance [Engine cold]
IN: 0.12—0.18 mm {0.005—0.007 in} (0.15±0.03 mm {0.006±0.0011 in})
EX: 0.32—0.38 mm {0.013—0.014 in} (0.35±0.03 mm {0.014±0.0011 in})
7. Turn the crankshaft one full turn and adjust the remaining valve clearances.
8. Install the fuel injector. (See F2–55 FUEL INJECTOR REMOVAL/INSTALLATION.)
9. Install the cylinder head cover. (See B2–21 Cylinder Head Cover Installation Note.)
49 G012 00549 G012 004
LOCKNUT(b) ADJUSTING
SCREW(a)
A6E2312W203
(e)
A6E2312W204
Page 39 of 909
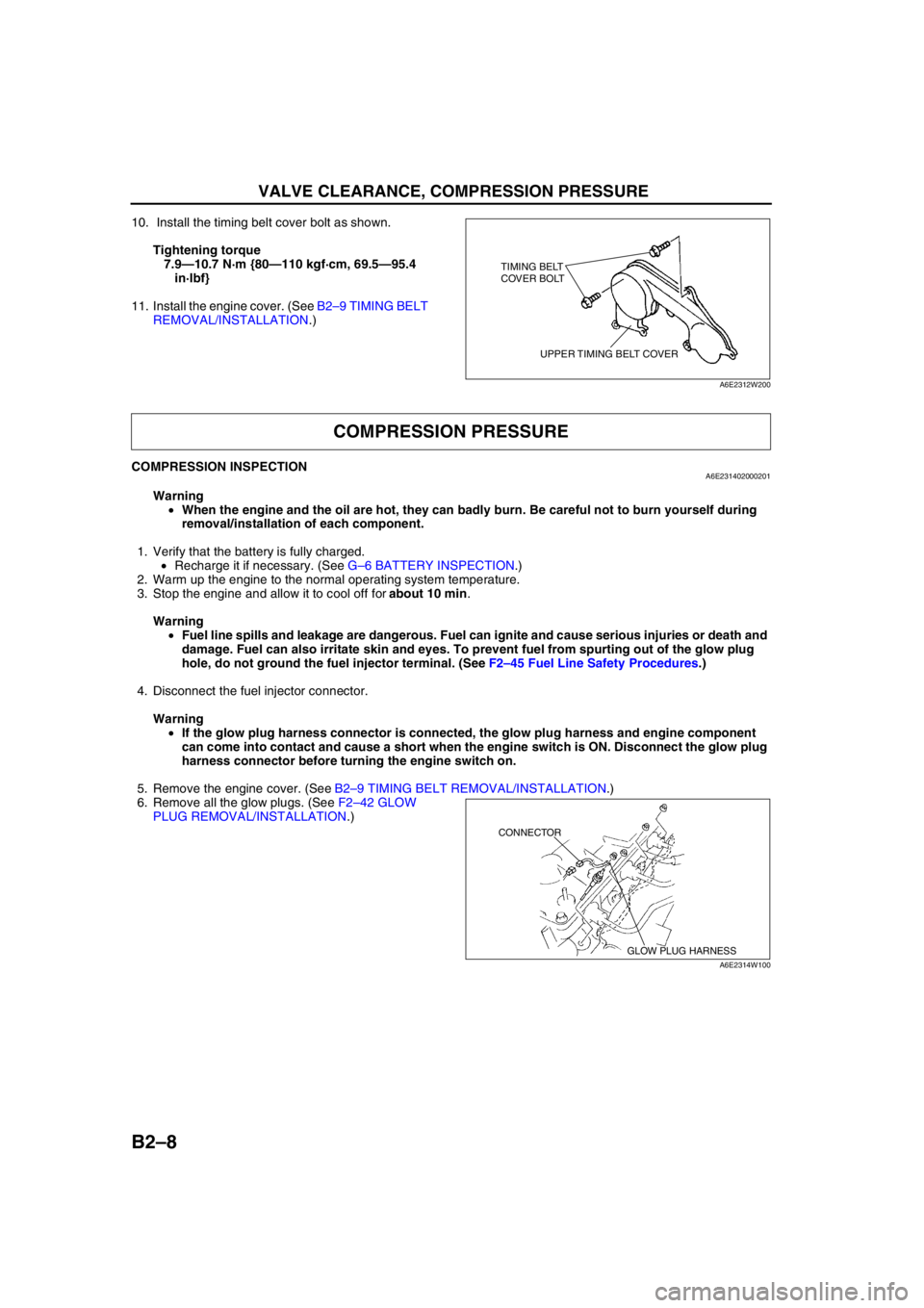
B2–8
VALVE CLEARANCE, COMPRESSION PRESSURE
10. Install the timing belt cover bolt as shown.
Tightening torque
7.9—10.7 N·m {80—110 kgf·cm, 69.5—95.4
in·lbf}
11. Install the engine cover. (See B2–9 TIMING BELT
REMOVAL/INSTALLATION.)
End Of Sie
COMPRESSION INSPECTIONA6E231402000201
Warning
•When the engine and the oil are hot, they can badly burn. Be careful not to burn yourself during
removal/installation of each component.
1. Verify that the battery is fully charged.
•Recharge it if necessary. (See G–6 BATTERY INSPECTION.)
2. Warm up the engine to the normal operating system temperature.
3. Stop the engine and allow it to cool off for about 10 min.
Warning
•Fuel line spills and leakage are dangerous. Fuel can ignite and cause serious injuries or death and
damage. Fuel can also irritate skin and eyes. To prevent fuel from spurting out of the glow plug
hole, do not ground the fuel injector terminal. (See F2–45 Fuel Line Safety Procedures.)
4. Disconnect the fuel injector connector.
Warning
•If the glow plug harness connector is connected, the glow plug harness and engine component
can come into contact and cause a short when the engine switch is ON. Disconnect the glow plug
harness connector before turning the engine switch on.
5. Remove the engine cover. (See B2–9 TIMING BELT REMOVAL/INSTALLATION.)
6. Remove all the glow plugs. (See F2–42 GLOW
PLUG REMOVAL/INSTALLATION.)
TIMING BELT
COVER BOLT
UPPER TIMING BELT COVER
A6E2312W200
COMPRESSION PRESSURE
GLOW PLUG HARNESS CONNECTOR
A6E2314W100
Page 40 of 909
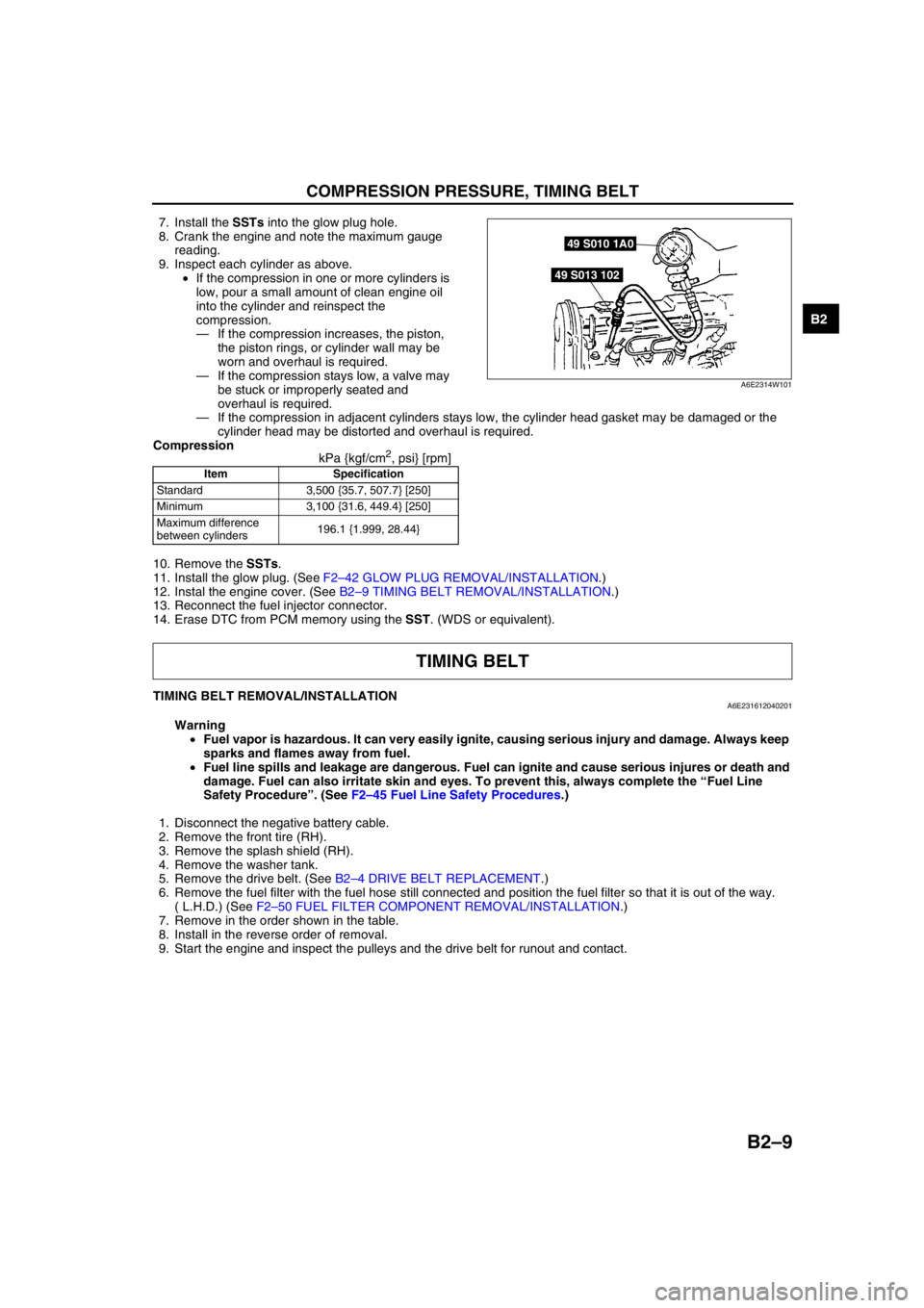
COMPRESSION PRESSURE, TIMING BELT
B2–9
B2
7. Install the SSTs into the glow plug hole.
8. Crank the engine and note the maximum gauge
reading.
9. Inspect each cylinder as above.
•If the compression in one or more cylinders is
low, pour a small amount of clean engine oil
into the cylinder and reinspect the
compression.
—If the compression increases, the piston,
the piston rings, or cylinder wall may be
worn and overhaul is required.
—If the compression stays low, a valve may
be stuck or improperly seated and
overhaul is required.
—If the compression in adjacent cylinders stays low, the cylinder head gasket may be damaged or the
cylinder head may be distorted and overhaul is required.
Compression
kPa {kgf/cm
2, psi} [rpm]
10. Remove the SSTs.
11. Install the glow plug. (See F2–42 GLOW PLUG REMOVAL/INSTALLATION.)
12. Instal the engine cover. (See B2–9 TIMING BELT REMOVAL/INSTALLATION.)
13. Reconnect the fuel injector connector.
14. Erase DTC from PCM memory using the SST. (WDS or equivalent).
End Of Sie
TIMING BELT REMOVAL/INSTALLATIONA6E231612040201
Warning
•Fuel vapor is hazardous. It can very easily ignite, causing serious injury and damage. Always keep
sparks and flames away from fuel.
•Fuel line spills and leakage are dangerous. Fuel can ignite and cause serious injures or death and
damage. Fuel can also irritate skin and eyes. To prevent this, always complete the “Fuel Line
Safety Procedure”. (See F2–45 Fuel Line Safety Procedures.)
1. Disconnect the negative battery cable.
2. Remove the front tire (RH).
3. Remove the splash shield (RH).
4. Remove the washer tank.
5. Remove the drive belt. (See B2–4 DRIVE BELT REPLACEMENT.)
6. Remove the fuel filter with the fuel hose still connected and position the fuel filter so that it is out of the way.
( L.H.D.) (See F2–50 FUEL FILTER COMPONENT REMOVAL/INSTALLATION.)
7. Remove in the order shown in the table.
8. Install in the reverse order of removal.
9. Start the engine and inspect the pulleys and the drive belt for runout and contact.
Item Specification
Standard 3,500 {35.7, 507.7} [250]
Minimum 3,100 {31.6, 449.4} [250]
Maximum difference
between cylinders196.1 {1.999, 28.44}
49 S010 1A0
49 S013 102
A6E2314W101
TIMING BELT
Page 41 of 909
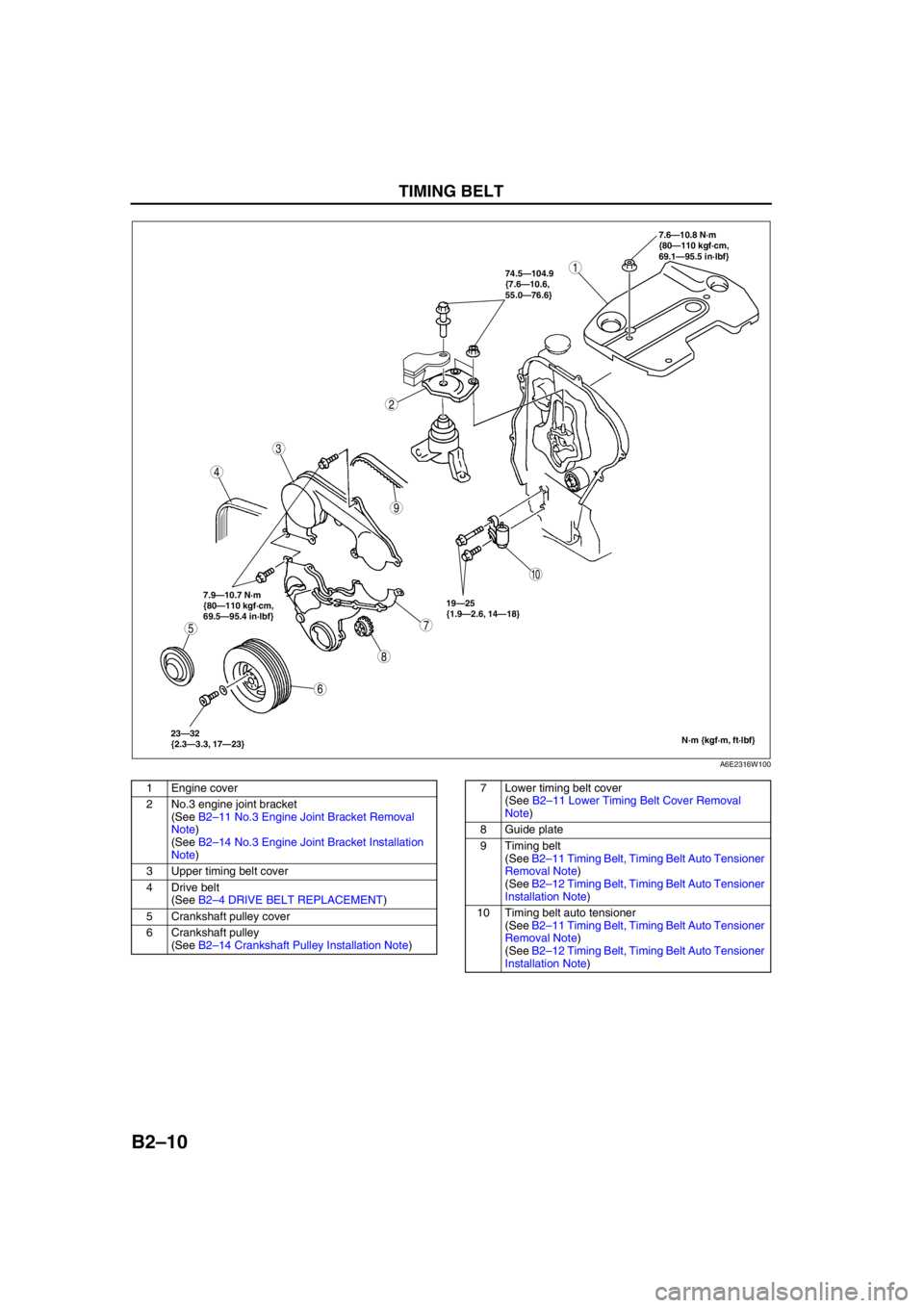
B2–10
TIMING BELT
.
N·m {kgf·m, ft·lbf} 7.6—10.8 N·m
{80—110 kgf·cm,
69.1—95.5 in·lbf}
7.9—10.7 N·m
{80—110 kgf·cm,
69.5—95.4 in·lbf}
23—32
{2.3—3.3, 17—23}19—25
{1.9—2.6, 14—18} 74.5—104.9
{7.6—10.6,
55.0—76.6}
9
8
75
4
3
1
2
10
6
A6E2316W100
1 Engine cover
2 No.3 engine joint bracket
(See B2–11 No.3 Engine Joint Bracket Removal
Note)
(See B2–14 No.3 Engine Joint Bracket Installation
Note)
3 Upper timing belt cover
4Drive belt
(See B2–4 DRIVE BELT REPLACEMENT)
5 Crankshaft pulley cover
6 Crankshaft pulley
(See B2–14 Crankshaft Pulley Installation Note)7 Lower timing belt cover
(See B2–11 Lower Timing Belt Cover Removal
Note)
8 Guide plate
9 Timing belt
(See B2–11 Timing Belt, Timing Belt Auto Tensioner
Removal Note)
(See B2–12 Timing Belt, Timing Belt Auto Tensioner
Installation Note)
10 Timing belt auto tensioner
(See B2–11 Timing Belt, Timing Belt Auto Tensioner
Removal Note)
(See B2–12 Timing Belt, Timing Belt Auto Tensioner
Installation Note)
Page 42 of 909
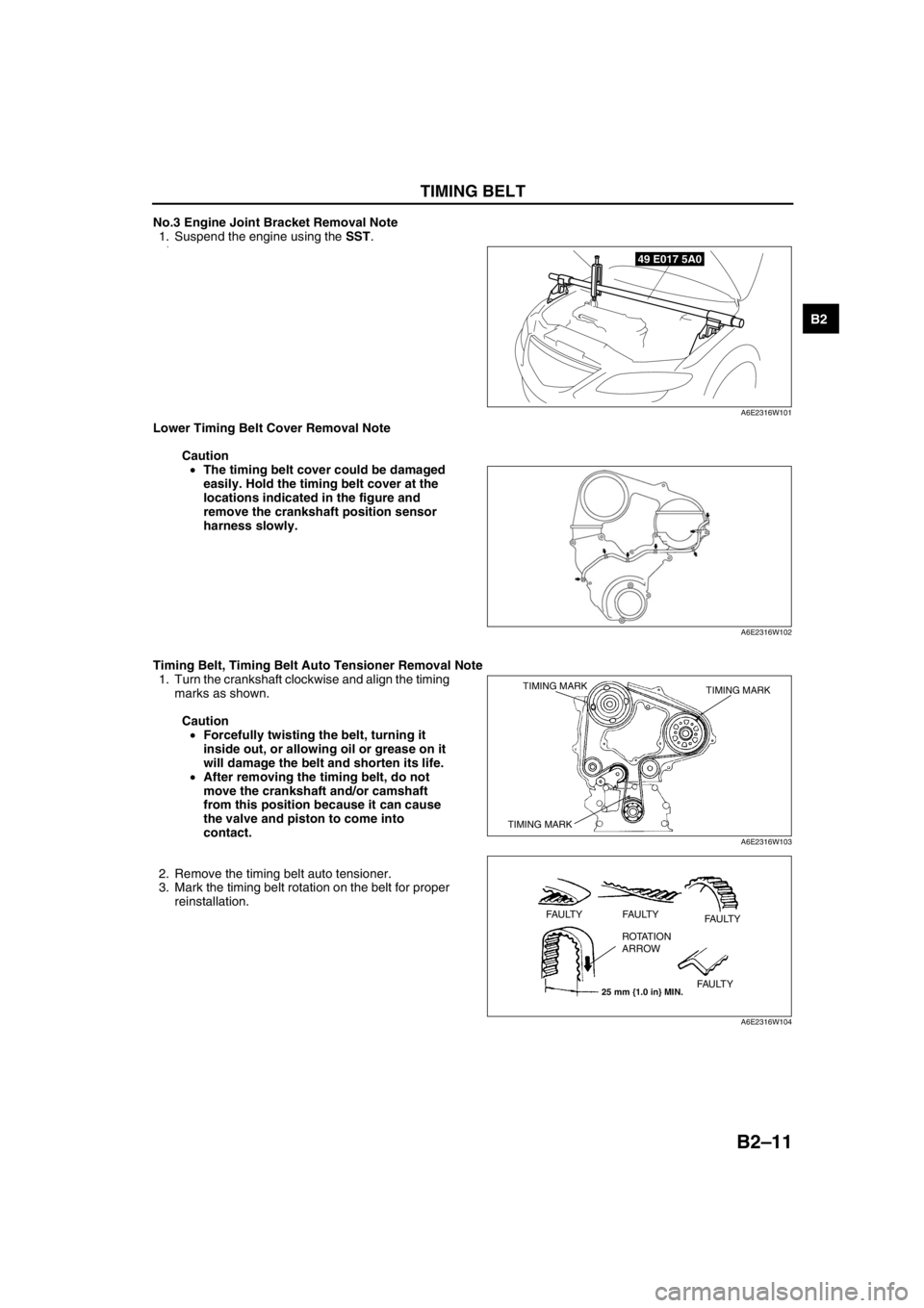
TIMING BELT
B2–11
B2
No.3 Engine Joint Bracket Removal Note
1. Suspend the engine using the SST.
2.
Lower Timing Belt Cover Removal Note
Caution
•The timing belt cover could be damaged
easily. Hold the timing belt cover at the
locations indicated in the figure and
remove the crankshaft position sensor
harness slowly.
Timing Belt, Timing Belt Auto Tensioner Removal Note
1. Turn the crankshaft clockwise and align the timing
marks as shown.
Caution
•Forcefully twisting the belt, turning it
inside out, or allowing oil or grease on it
will damage the belt and shorten its life.
•After removing the timing belt, do not
move the crankshaft and/or camshaft
from this position because it can cause
the valve and piston to come into
contact.
2. Remove the timing belt auto tensioner.
3. Mark the timing belt rotation on the belt for proper
reinstallation.
49 E017 5A0
A6E2316W101
A6E2316W102
TIMING MARK TIMING MARK
TIMING MARK
A6E2316W103
25 mm {1.0 in} MIN.
FAULTY FAULTY
FAULTY
FAULTY ROTATION
ARROW
A6E2316W104
Page 45 of 909
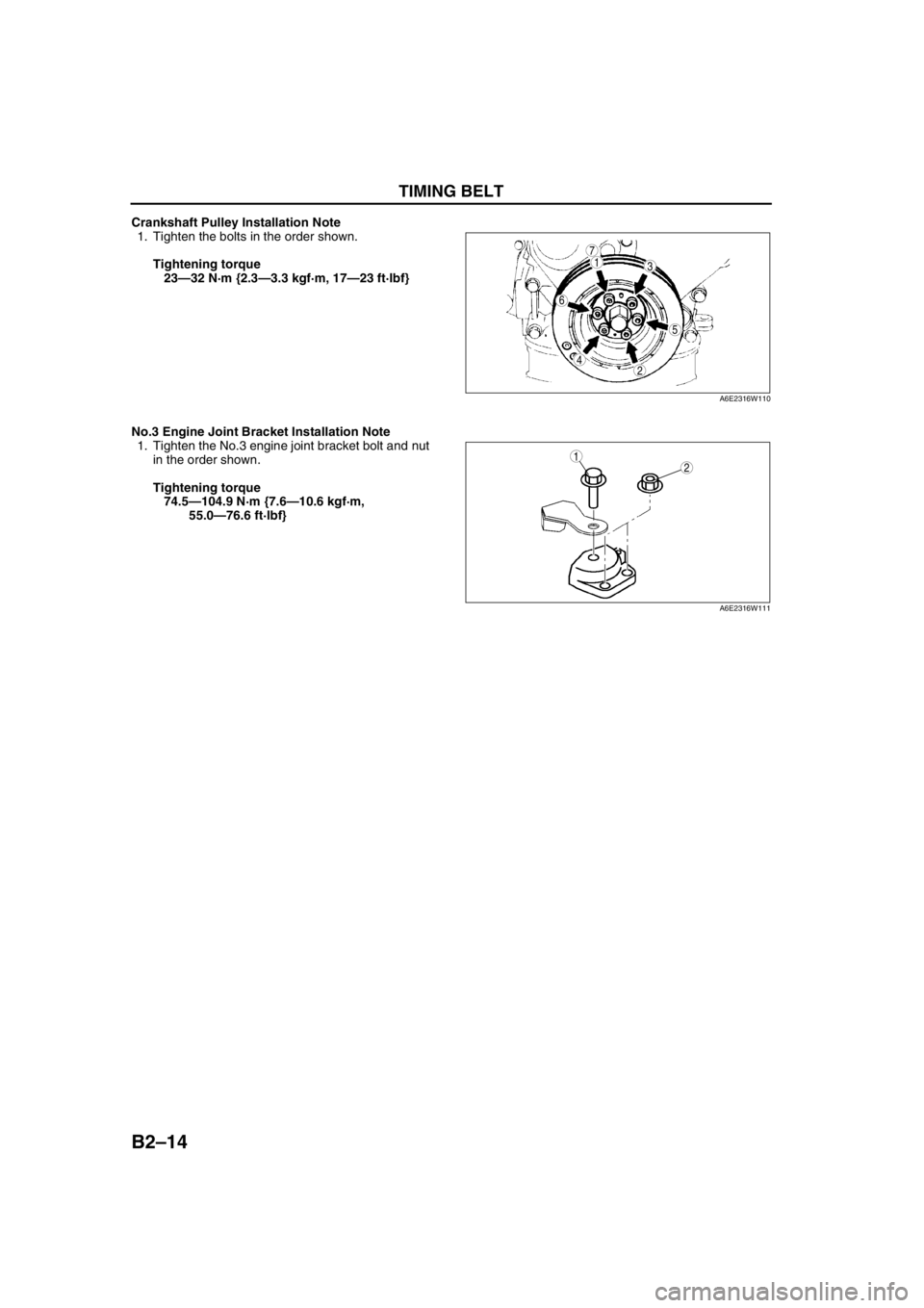
B2–14
TIMING BELT
Crankshaft Pulley Installation Note
1. Tighten the bolts in the order shown.
Tightening torque
23—32 N·m {2.3—3.3 kgf·m, 17—23 ft·lbf}
No.3 Engine Joint Bracket Installation Note
1. Tighten the No.3 engine joint bracket bolt and nut
in the order shown.
Tightening torque
74.5—104.9 N·m {7.6—10.6 kgf·m,
55.0—76.6 ft·lbf}
7
5
4
3
6
1
2
A6E2316W110
12
A6E2316W111
Page 46 of 909
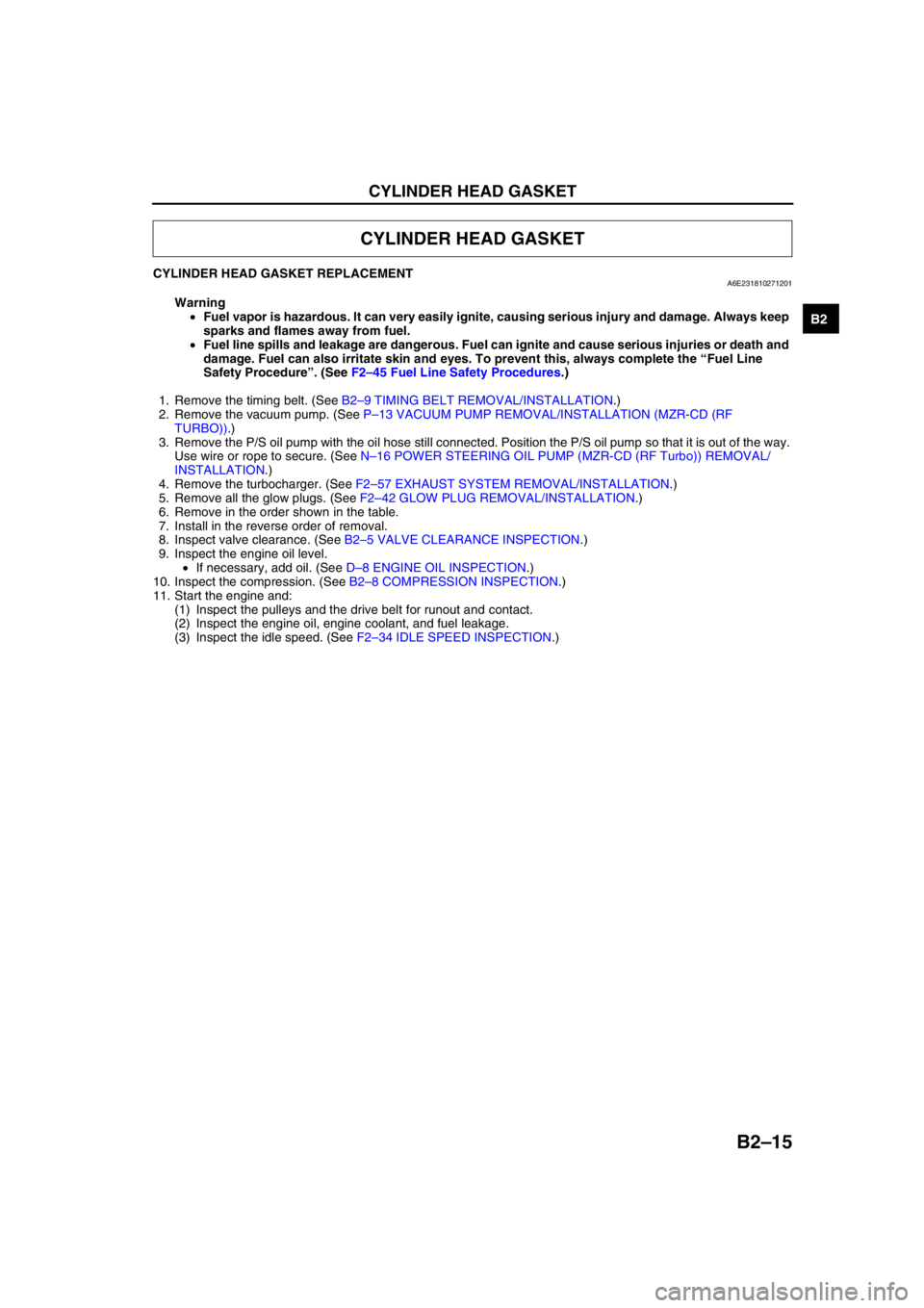
CYLINDER HEAD GASKET
B2–15
B2
End Of Sie
CYLINDER HEAD GASKET REPLACEMENTA6E231810271201
Warning
•Fuel vapor is hazardous. It can very easily ignite, causing serious injury and damage. Always keep
sparks and flames away from fuel.
•Fuel line spills and leakage are dangerous. Fuel can ignite and cause serious injuries or death and
damage. Fuel can also irritate skin and eyes. To prevent this, always complete the “Fuel Line
Safety Procedure”. (See F2–45 Fuel Line Safety Procedures.)
1. Remove the timing belt. (See B2–9 TIMING BELT REMOVAL/INSTALLATION.)
2. Remove the vacuum pump. (See P–13 VACUUM PUMP REMOVAL/INSTALLATION (MZR-CD (RF
TURBO)).)
3. Remove the P/S oil pump with the oil hose still connected. Position the P/S oil pump so that it is out of the way.
Use wire or rope to secure. (See N–16 POWER STEERING OIL PUMP (MZR-CD (RF Turbo)) REMOVAL/
INSTALLATION.)
4. Remove the turbocharger. (See F2–57 EXHAUST SYSTEM REMOVAL/INSTALLATION.)
5. Remove all the glow plugs. (See F2–42 GLOW PLUG REMOVAL/INSTALLATION.)
6. Remove in the order shown in the table.
7. Install in the reverse order of removal.
8. Inspect valve clearance. (See B2–5 VALVE CLEARANCE INSPECTION.)
9. Inspect the engine oil level.
•If necessary, add oil. (See D–8 ENGINE OIL INSPECTION.)
10. Inspect the compression. (See B2–8 COMPRESSION INSPECTION.)
11. Start the engine and:
(1) Inspect the pulleys and the drive belt for runout and contact.
(2) Inspect the engine oil, engine coolant, and fuel leakage.
(3) Inspect the idle speed. (See F2–34 IDLE SPEED INSPECTION.)
CYLINDER HEAD GASKET
Page 49 of 909
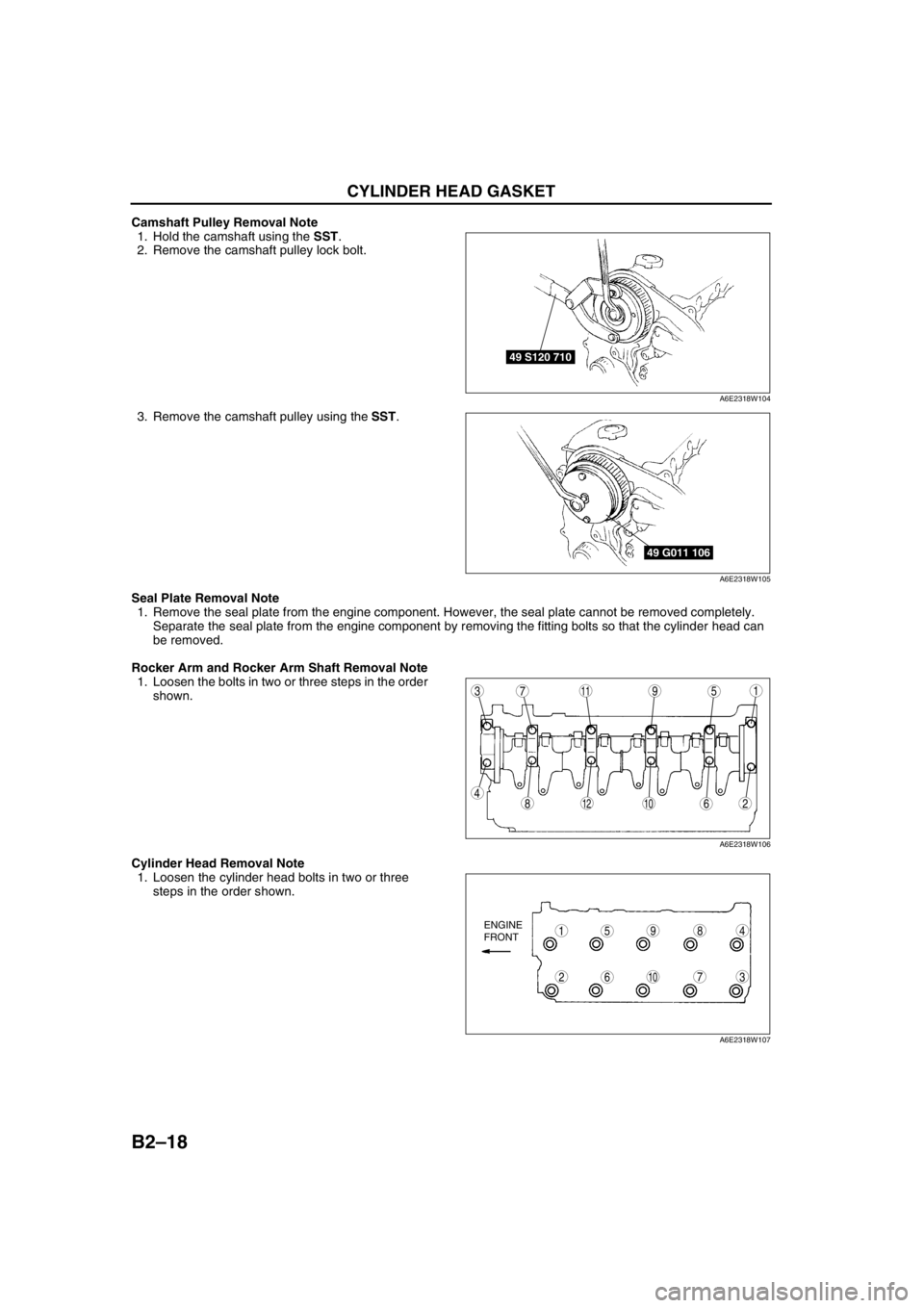
B2–18
CYLINDER HEAD GASKET
Camshaft Pulley Removal Note
1. Hold the camshaft using the SST.
2. Remove the camshaft pulley lock bolt.
3. Remove the camshaft pulley using the SST.
Seal Plate Removal Note
1. Remove the seal plate from the engine component. However, the seal plate cannot be removed completely.
Separate the seal plate from the engine component by removing the fitting bolts so that the cylinder head can
be removed.
Rocker Arm and Rocker Arm Shaft Removal Note
1. Loosen the bolts in two or three steps in the order
shown.
Cylinder Head Removal Note
1. Loosen the cylinder head bolts in two or three
steps in the order shown.
49 S120 710
A6E2318W104
49 G011 106
A6E2318W105
9
8
75
4
3
10
11
1262
1
A6E2318W106
98
7
54
3106
1
2
ENGINE
FRONT
A6E2318W107
Page 50 of 909
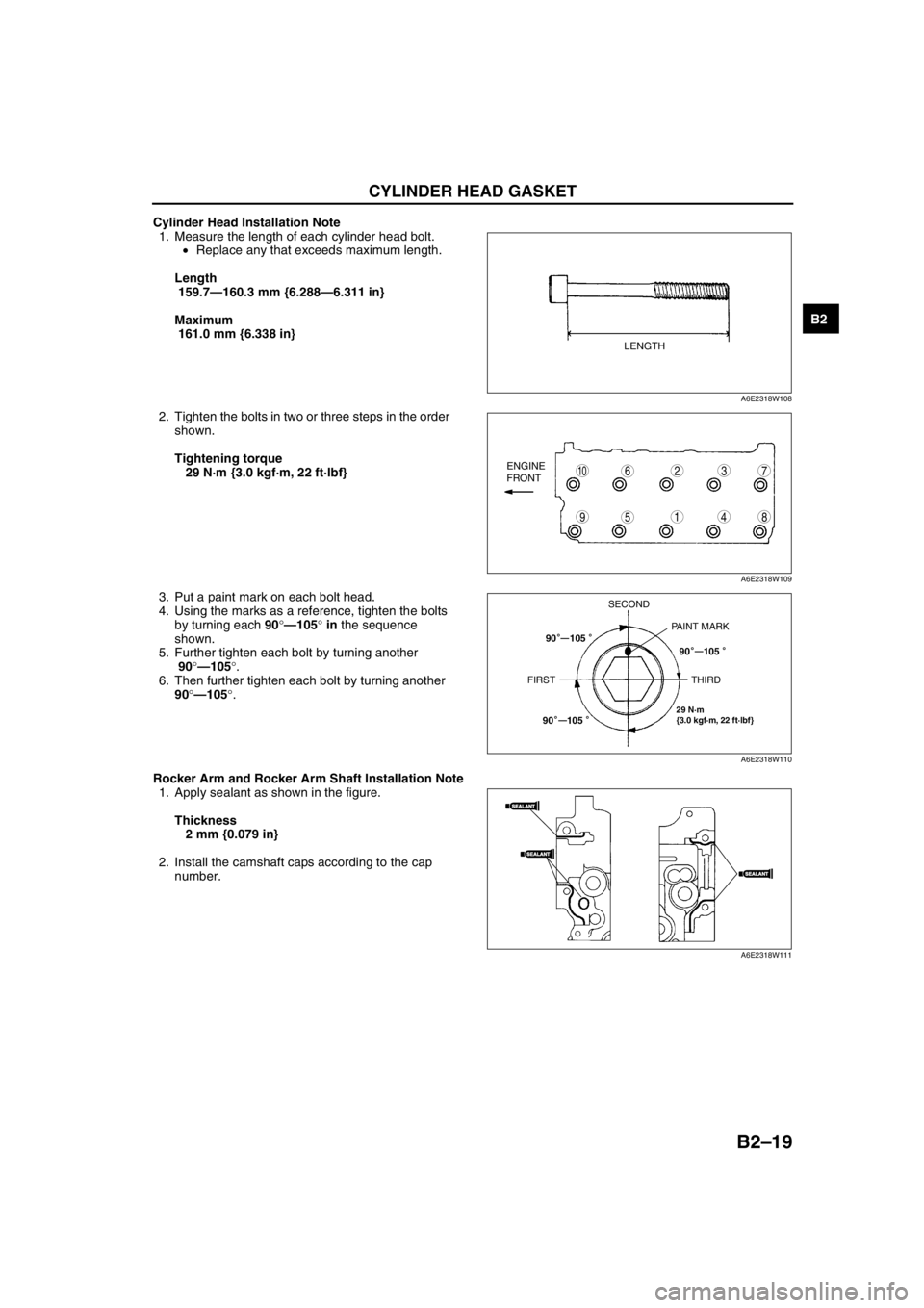
CYLINDER HEAD GASKET
B2–19
B2
Cylinder Head Installation Note
1. Measure the length of each cylinder head bolt.
•Replace any that exceeds maximum length.
Length
159.7—160.3 mm {6.288—6.311 in}
Maximum
161.0 mm {6.338 in}
2. Tighten the bolts in two or three steps in the order
shown.
Tightening torque
29 N·m {3.0 kgf·m, 22 ft·lbf}
3. Put a paint mark on each bolt head.
4. Using the marks as a reference, tighten the bolts
by turning each 90°—105° in the sequence
shown.
5. Further tighten each bolt by turning another
90°—105°.
6. Then further tighten each bolt by turning another
90°—105°.
Rocker Arm and Rocker Arm Shaft Installation Note
1. Apply sealant as shown in the figure.
Thickness
2 mm {0.079 in}
2. Install the camshaft caps according to the cap
number.
LENGTH
A6E2318W108
98
7
54
3106
1
2ENGINE
FRONT
A6E2318W109
29 N·m
{3.0 kgf·m, 22 ft·lbf}
SECOND
PAINT MARK
FIRST THIRD90 105
90 105
90 105
—
——
A6E2318W110
SEALANTSEALANT
SEALANTSEALANT
SEALANTSEALANT
A6E2318W111
Page 51 of 909
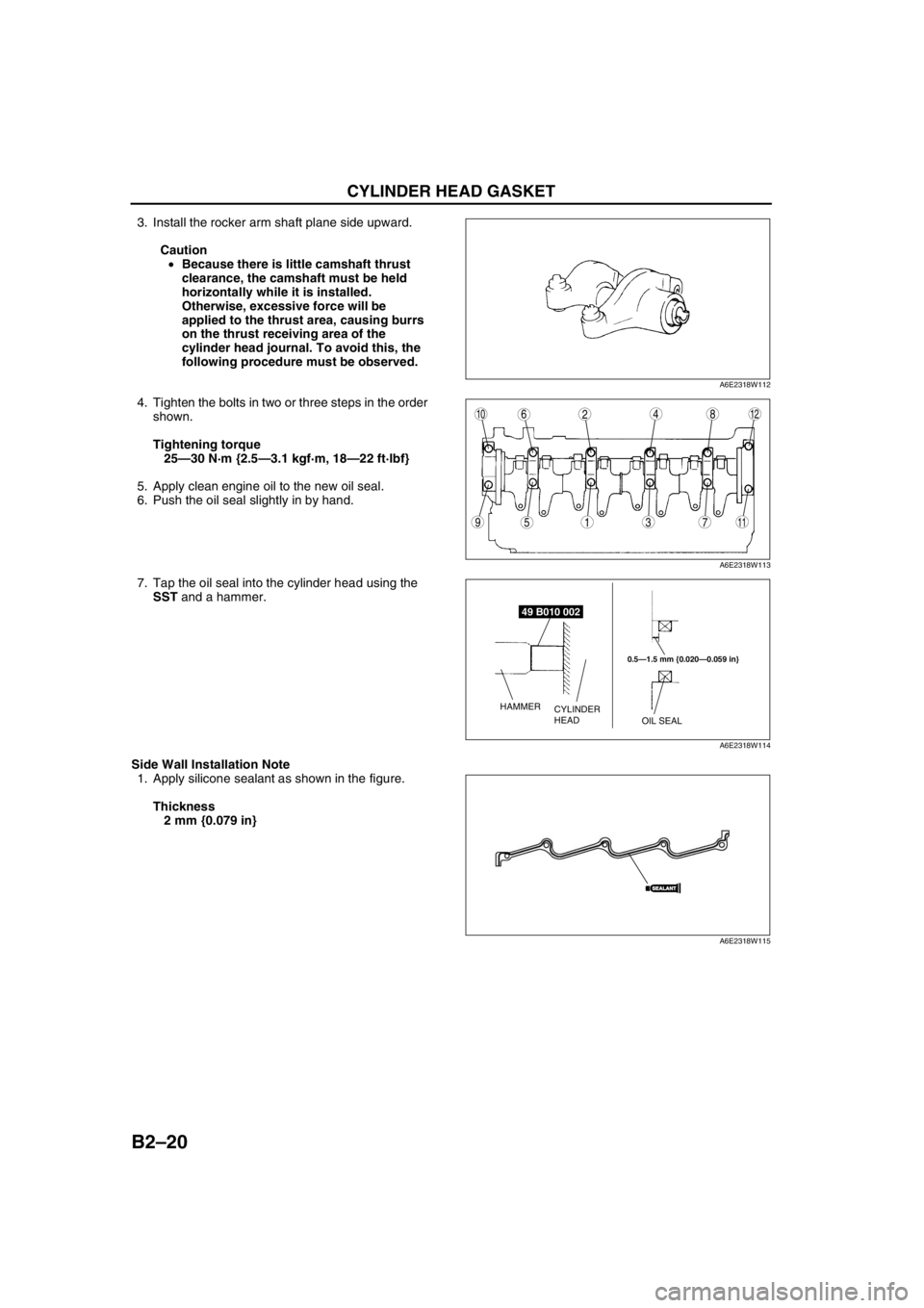
B2–20
CYLINDER HEAD GASKET
3. Install the rocker arm shaft plane side upward.
Caution
•Because there is little camshaft thrust
clearance, the camshaft must be held
horizontally while it is installed.
Otherwise, excessive force will be
applied to the thrust area, causing burrs
on the thrust receiving area of the
cylinder head journal. To avoid this, the
following procedure must be observed.
4. Tighten the bolts in two or three steps in the order
shown.
Tightening torque
25—30 N·m {2.5—3.1 kgf·m, 18—22 ft·lbf}
5. Apply clean engine oil to the new oil seal.
6. Push the oil seal slightly in by hand.
7. Tap the oil seal into the cylinder head using the
SST and a hammer.
Side Wall Installation Note
1. Apply silicone sealant as shown in the figure.
Thickness
2 mm {0.079 in}
A6E2318W112
9
8
75
4
3
10126
1
2
11
A6E2318W113
49 B010 002
0.5—1.5 mm {0.020—0.059 in}
OIL SEAL CYLINDER
HEAD HAMMER
A6E2318W114
SEALANTSEALANT
A6E2318W115