torque MAZDA 6 2002 Suplement Manual PDF
[x] Cancel search | Manufacturer: MAZDA, Model Year: 2002, Model line: 6, Model: MAZDA 6 2002Pages: 909, PDF Size: 17.16 MB
Page 516 of 909
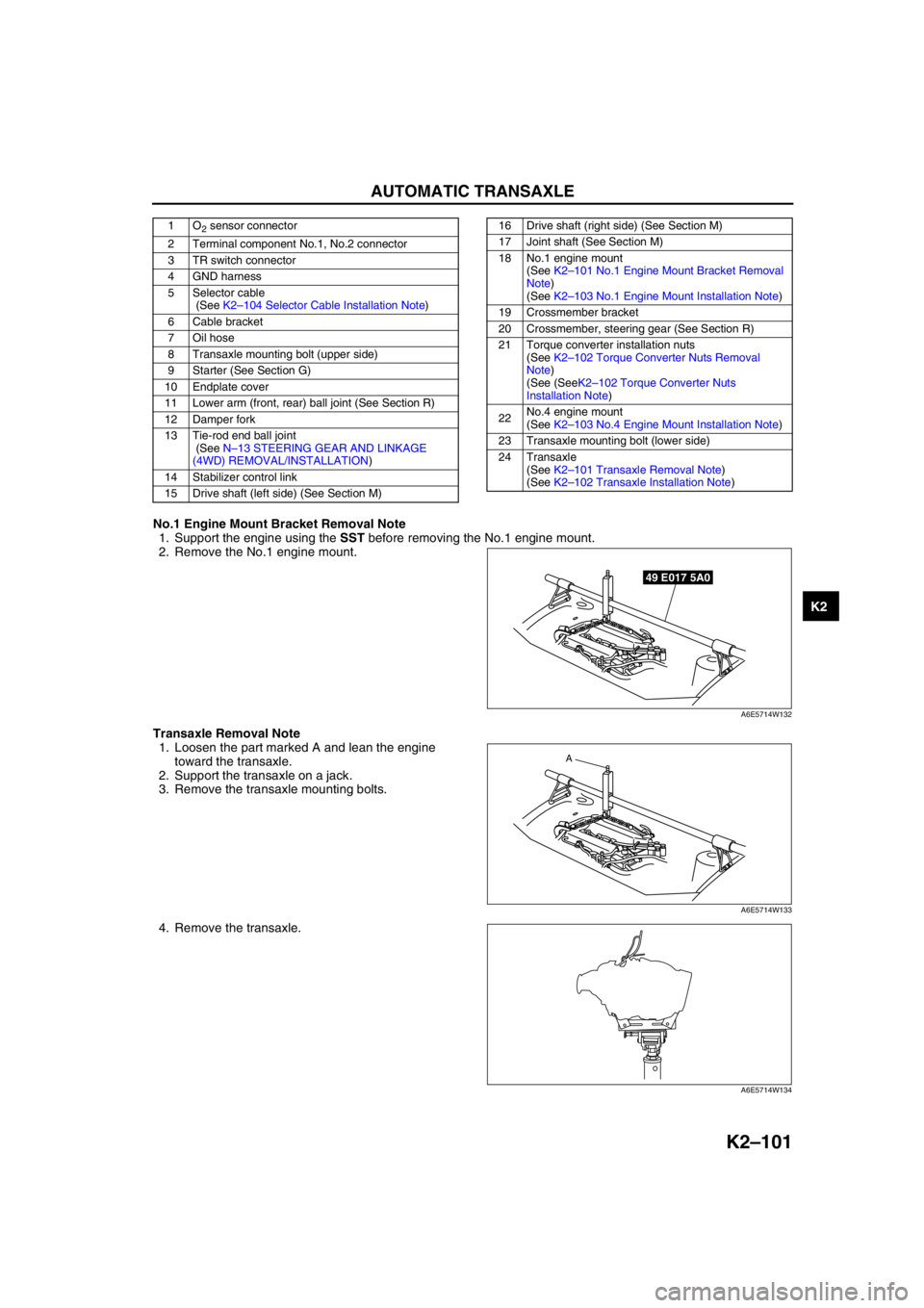
AUTOMATIC TRANSAXLE
K2–101
K2
No.1 Engine Mount Bracket Removal Note
1. Support the engine using the SST before removing the No.1 engine mount.
2. Remove the No.1 engine mount.
Transaxle Removal Note
1. Loosen the part marked A and lean the engine
toward the transaxle.
2. Support the transaxle on a jack.
3. Remove the transaxle mounting bolts.
4. Remove the transaxle.
1O2 sensor connector
2 Terminal component No.1, No.2 connector
3 TR switch connector
4 GND harness
5 Selector cable
(See K2–104 Selector Cable Installation Note)
6 Cable bracket
7 Oil hose
8 Transaxle mounting bolt (upper side)
9 Starter (See Section G)
10 Endplate cover
11 Lower arm (front, rear) ball joint (See Section R)
12 Damper fork
13 Tie-rod end ball joint
(See N–13 STEERING GEAR AND LINKAGE
(4WD) REMOVAL/INSTALLATION)
14 Stabilizer control link
15 Drive shaft (left side) (See Section M)16 Drive shaft (right side) (See Section M)
17 Joint shaft (See Section M)
18 No.1 engine mount
(See K2–101 No.1 Engine Mount Bracket Removal
Note)
(See K2–103 No.1 Engine Mount Installation Note)
19 Crossmember bracket
20 Crossmember, steering gear (See Section R)
21 Torque converter installation nuts
(See K2–102 Torque Converter Nuts Removal
Note)
(See (SeeK2–102 Torque Converter Nuts
Installation Note)
22No.4 engine mount
(See K2–103 No.4 Engine Mount Installation Note)
23 Transaxle mounting bolt (lower side)
24 Transaxle
(See K2–101 Transaxle Removal Note)
(See K2–102 Transaxle Installation Note)
49 E017 5A0
A6E5714W132
A
A6E5714W133
A6E5714W134
Page 517 of 909
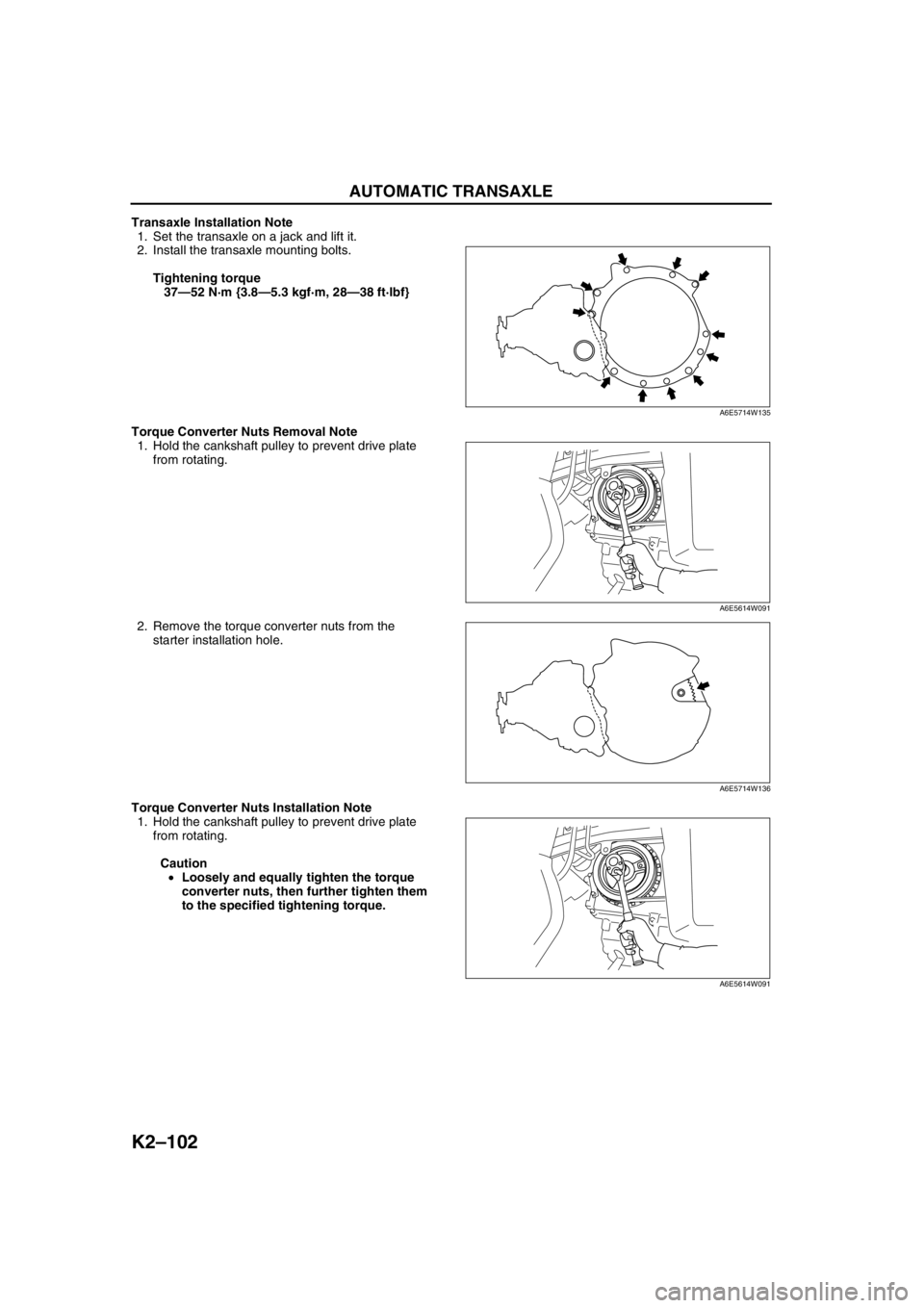
K2–102
AUTOMATIC TRANSAXLE
Transaxle Installation Note
1. Set the transaxle on a jack and lift it.
2. Install the transaxle mounting bolts.
Tightening torque
37—52 N·m {3.8—5.3 kgf·m, 28—38 ft·lbf}
Torque Converter Nuts Removal Note
1. Hold the cankshaft pulley to prevent drive plate
from rotating.
2. Remove the torque converter nuts from the
starter installation hole.
Torque Converter Nuts Installation Note
1. Hold the cankshaft pulley to prevent drive plate
from rotating.
Caution
•Loosely and equally tighten the torque
converter nuts, then further tighten them
to the specified tightening torque.
A6E5714W135
A6E5614W091
A6E5714W136
A6E5614W091
Page 518 of 909
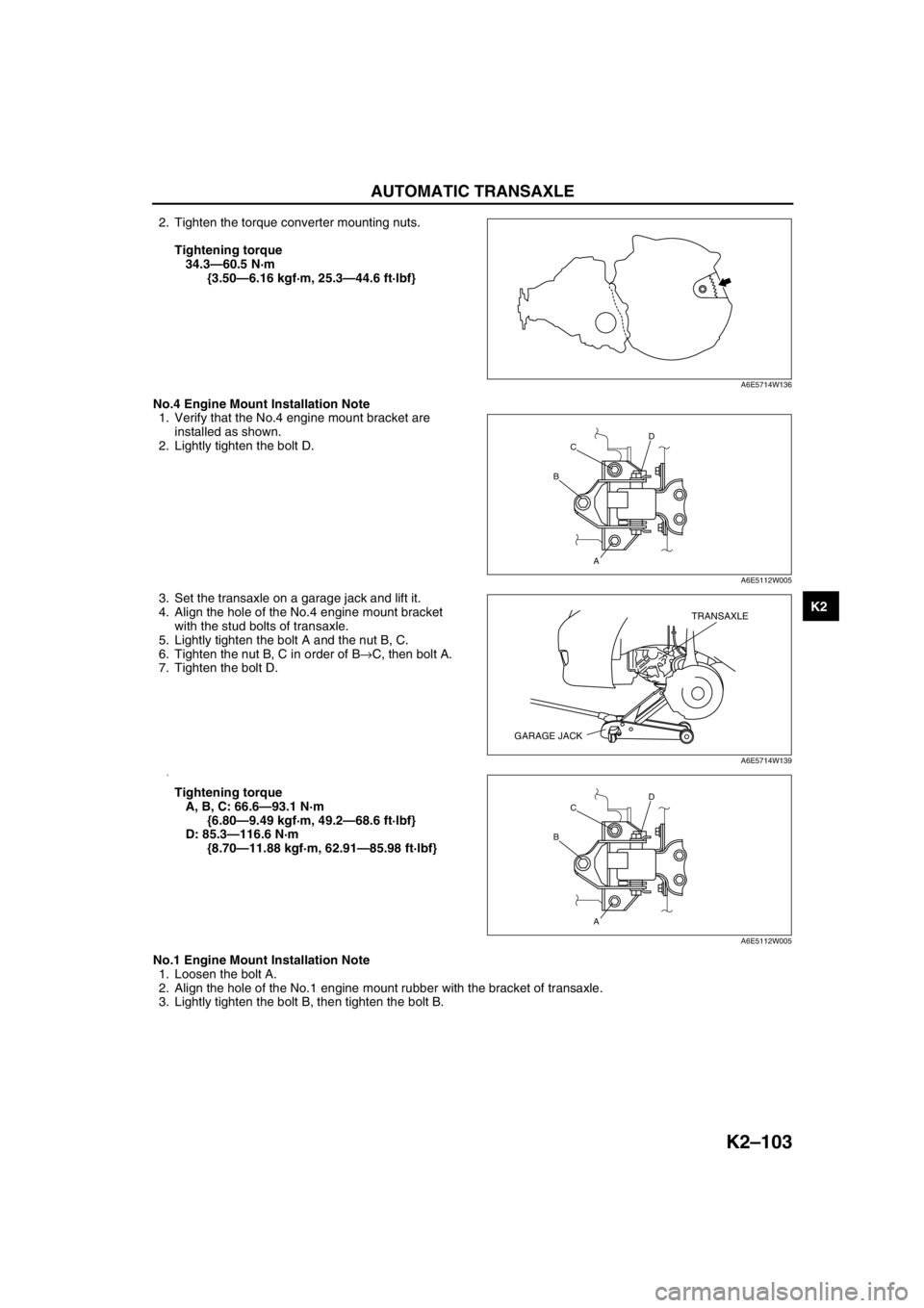
AUTOMATIC TRANSAXLE
K2–103
K2
2. Tighten the torque converter mounting nuts.
Tightening torque
34.3—60.5 N·m
{3.50—6.16 kgf·m, 25.3—44.6 ft·lbf}
No.4 Engine Mount Installation Note
1. Verify that the No.4 engine mount bracket are
installed as shown.
2. Lightly tighten the bolt D.
3. Set the transaxle on a garage jack and lift it.
4. Align the hole of the No.4 engine mount bracket
with the stud bolts of transaxle.
5. Lightly tighten the bolt A and the nut B, C.
6. Tighten the nut B, C in order of B→C, then bolt A.
7. Tighten the bolt D.
8.
Tightening torque
A, B, C: 66.6—93.1 N·m
{6.80—9.49 kgf·m, 49.2—68.6 ft·lbf}
D: 85.3—116.6 N·m
{8.70—11.88 kgf·m, 62.91—85.98 ft·lbf}
No.1 Engine Mount Installation Note
1. Loosen the bolt A.
2. Align the hole of the No.1 engine mount rubber with the bracket of transaxle.
3. Lightly tighten the bolt B, then tighten the bolt B.
A6E5714W136
D
A BC
A6E5112W005
TRANSAXLE
GARAGE JACK
A6E5714W139
D
A BC
A6E5112W005
Page 519 of 909
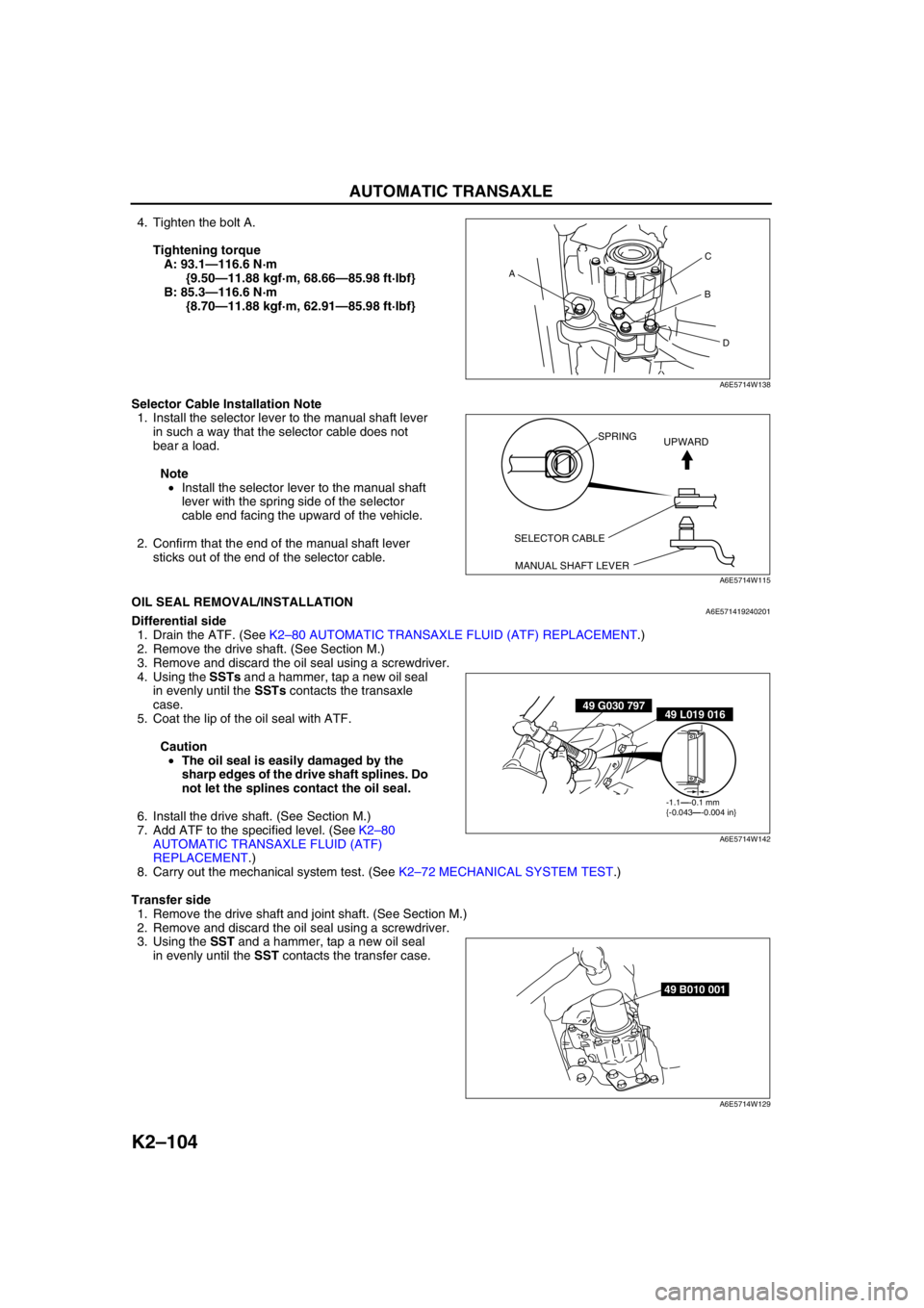
K2–104
AUTOMATIC TRANSAXLE
4. Tighten the bolt A.
Tightening torque
A: 93.1—116.6 N·m
{9.50—11.88 kgf·m, 68.66—85.98 ft·lbf}
B: 85.3—116.6 N·m
{8.70—11.88 kgf·m, 62.91—85.98 ft·lbf}
Selector Cable Installation Note
1. Install the selector lever to the manual shaft lever
in such a way that the selector cable does not
bear a load.
Note
•Install the selector lever to the manual shaft
lever with the spring side of the selector
cable end facing the upward of the vehicle.
2. Confirm that the end of the manual shaft lever
sticks out of the end of the selector cable.
End Of SieOIL SEAL REMOVAL/INSTALLATIONA6E571419240201Differential side
1. Drain the ATF. (See K2–80 AUTOMATIC TRANSAXLE FLUID (ATF) REPLACEMENT.)
2. Remove the drive shaft. (See Section M.)
3. Remove and discard the oil seal using a screwdriver.
4. Using the SSTs and a hammer, tap a new oil seal
in evenly until the SSTs contacts the transaxle
case.
5. Coat the lip of the oil seal with ATF.
Caution
•The oil seal is easily damaged by the
sharp edges of the drive shaft splines. Do
not let the splines contact the oil seal.
6. Install the drive shaft. (See Section M.)
7. Add ATF to the specified level. (See K2–80
AUTOMATIC TRANSAXLE FLUID (ATF)
REPLACEMENT.)
8. Carry out the mechanical system test. (See K2–72 MECHANICAL SYSTEM TEST.)
Transfer side
1. Remove the drive shaft and joint shaft. (See Section M.)
2. Remove and discard the oil seal using a screwdriver.
3. Using the SST and a hammer, tap a new oil seal
in evenly until the SST contacts the transfer case.
AC
B
D
A6E5714W138
SELECTOR CABLE
MANUAL SHAFT LEVERSPRING
UPWARD
A6E5714W115
49 G030 79749 L019 016
-1.1—-0.1 mm
{-0.043—-0.004 in}
A6E5714W142
49 B010 001
A6E5714W129
Page 520 of 909
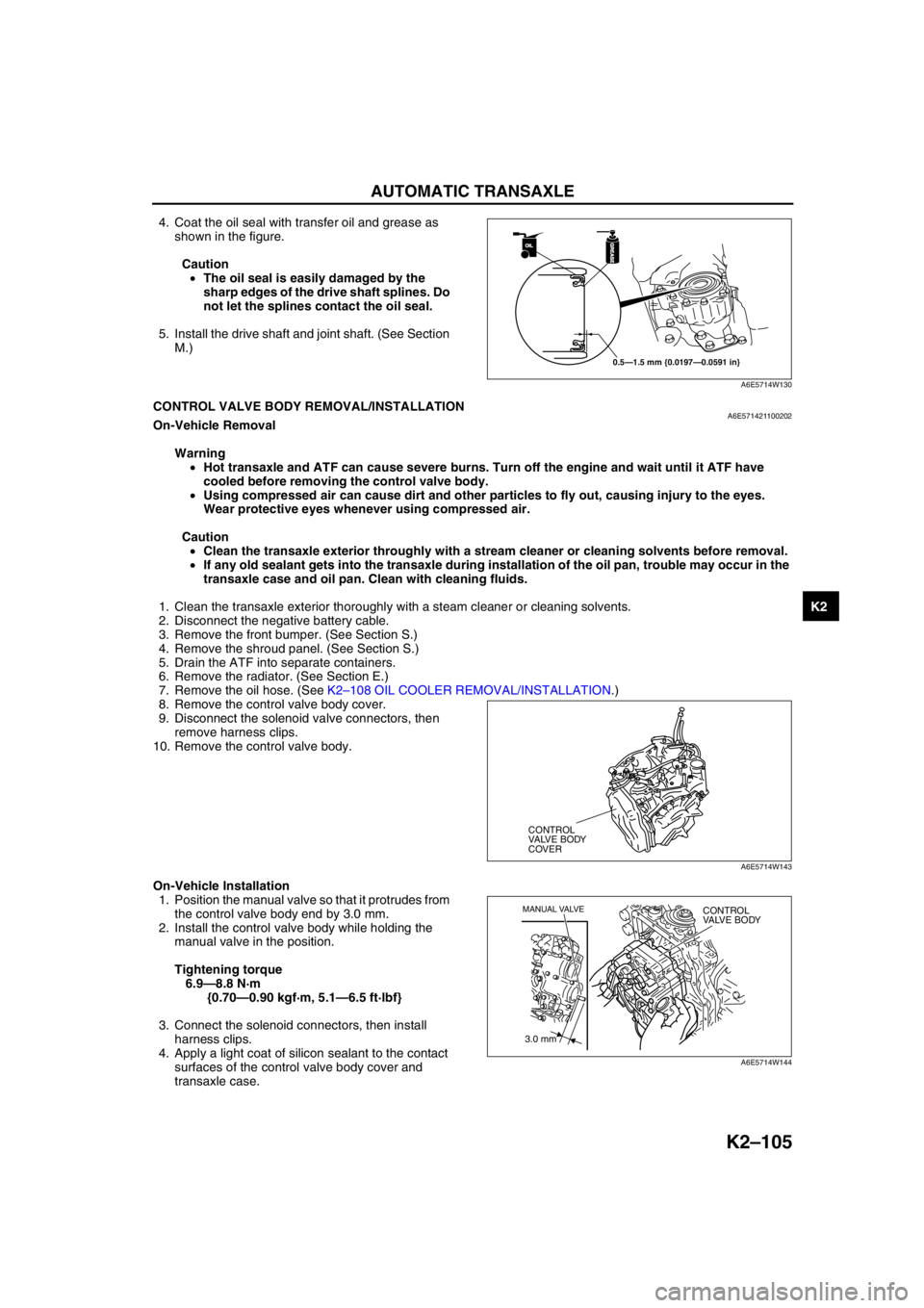
AUTOMATIC TRANSAXLE
K2–105
K2
4. Coat the oil seal with transfer oil and grease as
shown in the figure.
Caution
•The oil seal is easily damaged by the
sharp edges of the drive shaft splines. Do
not let the splines contact the oil seal.
5. Install the drive shaft and joint shaft. (See Section
M.)
End Of SieCONTROL VALVE BODY REMOVAL/INSTALLATIONA6E571421100202On-Vehicle Removal
Warning
•Hot transaxle and ATF can cause severe burns. Turn off the engine and wait until it ATF have
cooled before removing the control valve body.
•Using compressed air can cause dirt and other particles to fly out, causing injury to the eyes.
Wear protective eyes whenever using compressed air.
Caution
•Clean the transaxle exterior throughly with a stream cleaner or cleaning solvents before removal.
•If any old sealant gets into the transaxle during installation of the oil pan, trouble may occur in the
transaxle case and oil pan. Clean with cleaning fluids.
1. Clean the transaxle exterior thoroughly with a steam cleaner or cleaning solvents.
2. Disconnect the negative battery cable.
3. Remove the front bumper. (See Section S.)
4. Remove the shroud panel. (See Section S.)
5. Drain the ATF into separate containers.
6. Remove the radiator. (See Section E.)
7. Remove the oil hose. (See K2–108 OIL COOLER REMOVAL/INSTALLATION.)
8. Remove the control valve body cover.
9. Disconnect the solenoid valve connectors, then
remove harness clips.
10. Remove the control valve body.
On-Vehicle Installation
1. Position the manual valve so that it protrudes from
the control valve body end by 3.0 mm.
2. Install the control valve body while holding the
manual valve in the position.
Tightening torque
6.9—8.8 N·m
{0.70—0.90 kgf·m, 5.1—6.5 ft·lbf}
3. Connect the solenoid connectors, then install
harness clips.
4. Apply a light coat of silicon sealant to the contact
surfaces of the control valve body cover and
transaxle case.
OILOIL
0.5—1.5 mm {0.0197—0.0591 in}
GREASEGREASE
A6E5714W130
CONTROL
VALVE BODY
COVER
A6E5714W143
3.0 mm
MANUAL VALVECONTROL
VALVE BODY
A6E5714W144
Page 521 of 909
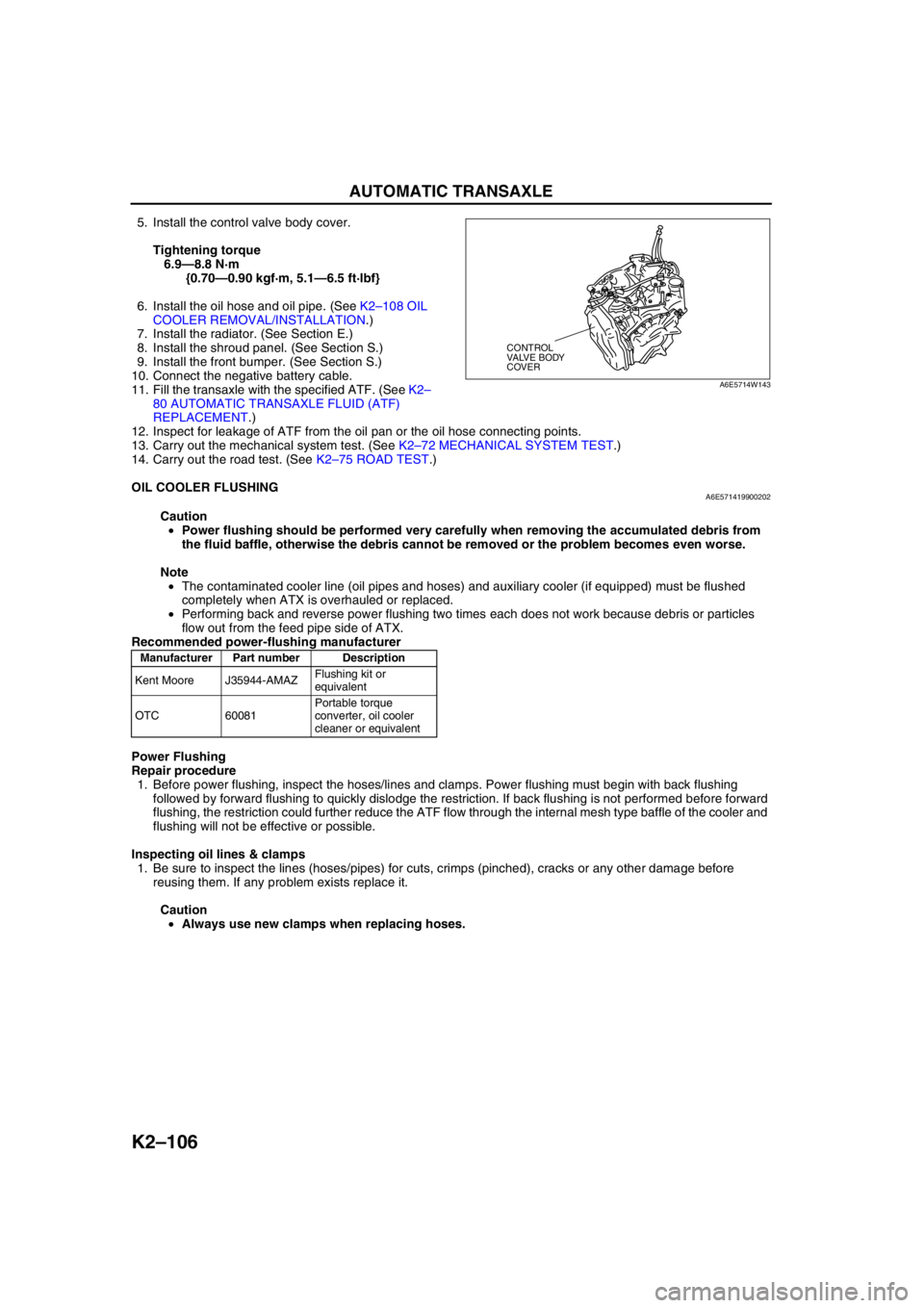
K2–106
AUTOMATIC TRANSAXLE
5. Install the control valve body cover.
Tightening torque
6.9—8.8 N·m
{0.70—0.90 kgf·m, 5.1—6.5 ft·lbf}
6. Install the oil hose and oil pipe. (See K2–108 OIL
COOLER REMOVAL/INSTALLATION.)
7. Install the radiator. (See Section E.)
8. Install the shroud panel. (See Section S.)
9. Install the front bumper. (See Section S.)
10. Connect the negative battery cable.
11. Fill the transaxle with the specified ATF. (See K2–
80 AUTOMATIC TRANSAXLE FLUID (ATF)
REPLACEMENT.)
12. Inspect for leakage of ATF from the oil pan or the oil hose connecting points.
13. Carry out the mechanical system test. (See K2–72 MECHANICAL SYSTEM TEST.)
14. Carry out the road test. (See K2–75 ROAD TEST.)
End Of Sie
OIL COOLER FLUSHINGA6E571419900202
Caution
•Power flushing should be performed very carefully when removing the accumulated debris from
the fluid baffle, otherwise the debris cannot be removed or the problem becomes even worse.
Note
•The contaminated cooler line (oil pipes and hoses) and auxiliary cooler (if equipped) must be flushed
completely when ATX is overhauled or replaced.
•Performing back and reverse power flushing two times each does not work because debris or particles
flow out from the feed pipe side of ATX.
Recommended power-flushing manufacturer
Power Flushing
Repair procedure
1. Before power flushing, inspect the hoses/lines and clamps. Power flushing must begin with back flushing
followed by forward flushing to quickly dislodge the restriction. If back flushing is not performed before forward
flushing, the restriction could further reduce the ATF flow through the internal mesh type baffle of the cooler and
flushing will not be effective or possible.
Inspecting oil lines & clamps
1. Be sure to inspect the lines (hoses/pipes) for cuts, crimps (pinched), cracks or any other damage before
reusing them. If any problem exists replace it.
Caution
•Always use new clamps when replacing hoses.
CONTROL
VALVE BODY
COVER
A6E5714W143
Manufacturer Part number Description
Kent Moore J35944-AMAZFlushing kit or
equivalent
OTC 60081Portable torque
converter, oil cooler
cleaner or equivalent
Page 528 of 909
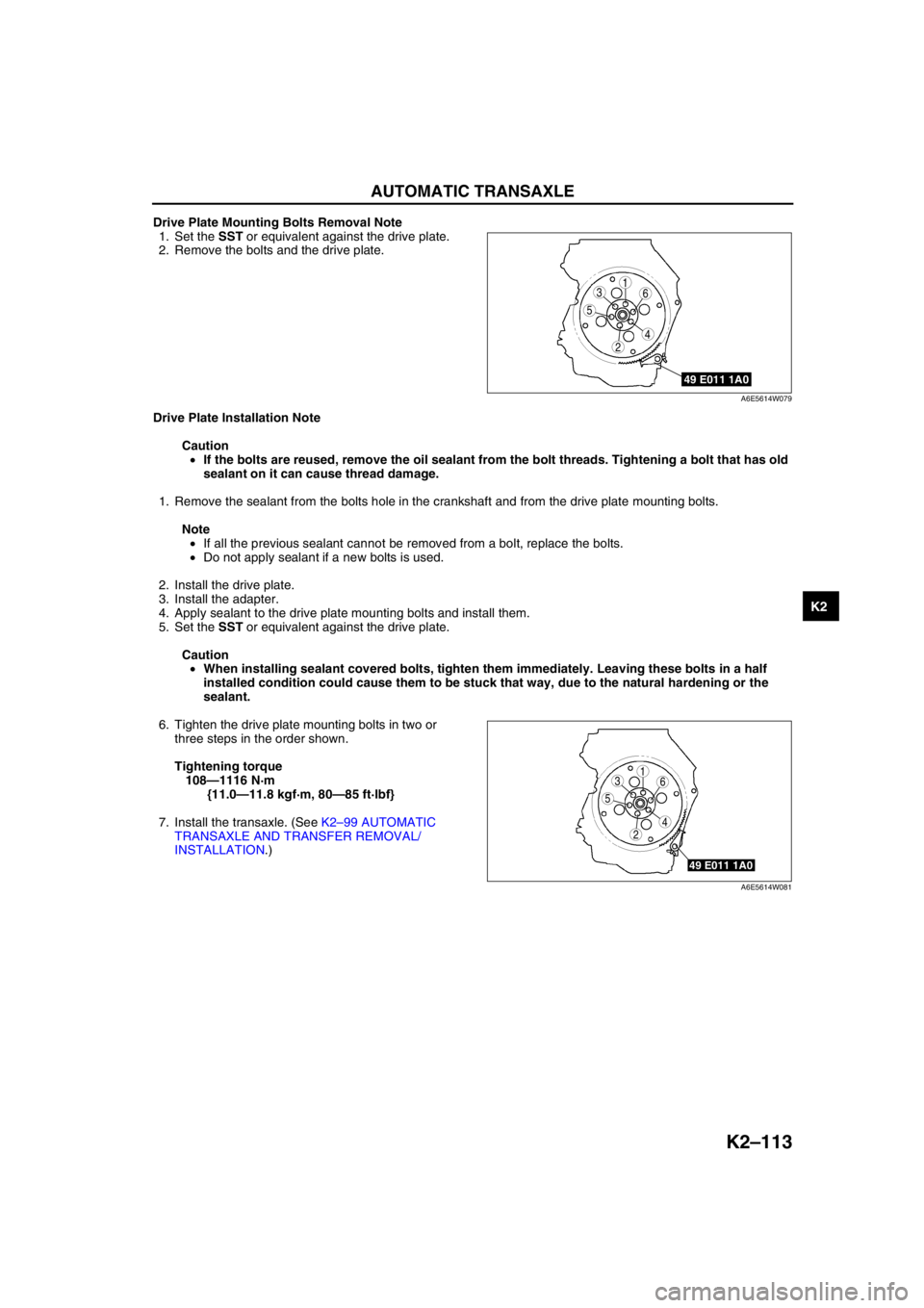
AUTOMATIC TRANSAXLE
K2–113
K2
Drive Plate Mounting Bolts Removal Note
1. Set the SST or equivalent against the drive plate.
2. Remove the bolts and the drive plate.
Drive Plate Installation Note
Caution
•If the bolts are reused, remove the oil sealant from the bolt threads. Tightening a bolt that has old
sealant on it can cause thread damage.
1. Remove the sealant from the bolts hole in the crankshaft and from the drive plate mounting bolts.
Note
•If all the previous sealant cannot be removed from a bolt, replace the bolts.
•Do not apply sealant if a new bolts is used.
2. Install the drive plate.
3. Install the adapter.
4. Apply sealant to the drive plate mounting bolts and install them.
5. Set the SST or equivalent against the drive plate.
Caution
•When installing sealant covered bolts, tighten them immediately. Leaving these bolts in a half
installed condition could cause them to be stuck that way, due to the natural hardening or the
sealant.
6. Tighten the drive plate mounting bolts in two or
three steps in the order shown.
Tightening torque
108—1116 N·m
{11.0—11.8 kgf·m, 80—85 ft·lbf}
7. Install the transaxle. (See K2–99 AUTOMATIC
TRANSAXLE AND TRANSFER REMOVAL/
INSTALLATION.)
End Of Sie
5
4
361
2
49 E011 1A0
A6E5614W079
49 E011 1A0
5
4
361
2
A6E5614W081
Page 529 of 909
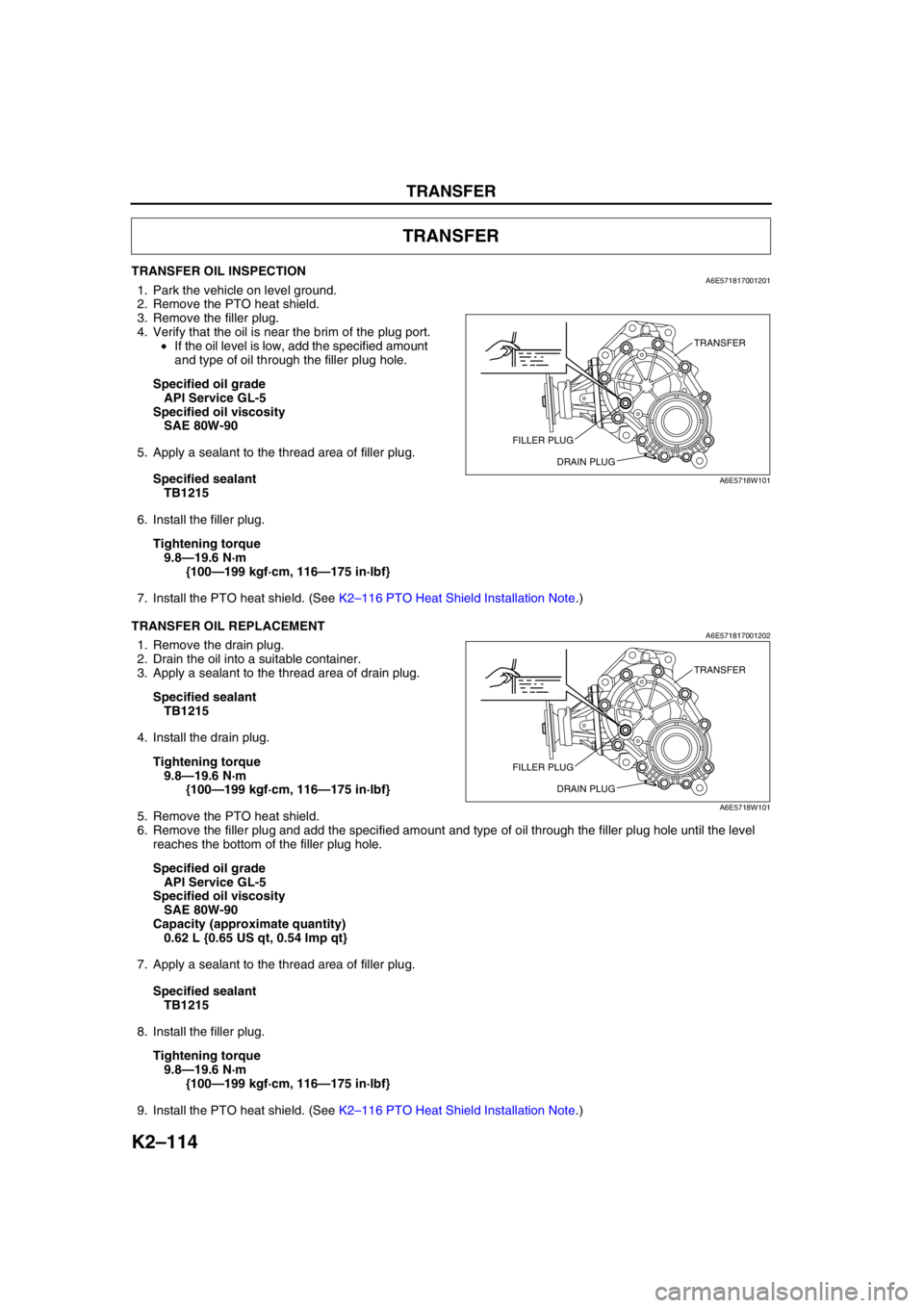
K2–114
TRANSFER
TRANSFER OIL INSPECTIONA6E5718170012011. Park the vehicle on level ground.
2. Remove the PTO heat shield.
3. Remove the filler plug.
4. Verify that the oil is near the brim of the plug port.
•If the oil level is low, add the specified amount
and type of oil through the filler plug hole.
Specified oil grade
API Service GL-5
Specified oil viscosity
SAE 80W-90
5. Apply a sealant to the thread area of filler plug.
Specified sealant
TB1215
6. Install the filler plug.
Tightening torque
9.8—19.6 N·m
{100—199 kgf·cm, 116—175 in·lbf}
7. Install the PTO heat shield. (See K2–116 PTO Heat Shield Installation Note.)
End Of Sie
TRANSFER OIL REPLACEMENTA6E5718170012021. Remove the drain plug.
2. Drain the oil into a suitable container.
3. Apply a sealant to the thread area of drain plug.
Specified sealant
TB1215
4. Install the drain plug.
Tightening torque
9.8—19.6 N·m
{100—199 kgf·cm, 116—175 in·lbf}
5. Remove the PTO heat shield.
6. Remove the filler plug and add the specified amount and type of oil through the filler plug hole until the level
reaches the bottom of the filler plug hole.
Specified oil grade
API Service GL-5
Specified oil viscosity
SAE 80W-90
Capacity (approximate quantity)
0.62 L {0.65 US qt, 0.54 lmp qt}
7. Apply a sealant to the thread area of filler plug.
Specified sealant
TB1215
8. Install the filler plug.
Tightening torque
9.8—19.6 N·m
{100—199 kgf·cm, 116—175 in·lbf}
9. Install the PTO heat shield. (See K2–116 PTO Heat Shield Installation Note.)
TRANSFER
TRANSFER
FILLER PLUG
DRAIN PLUG
A6E5718W101
TRANSFER
FILLER PLUG
DRAIN PLUG
A6E5718W101
Page 531 of 909
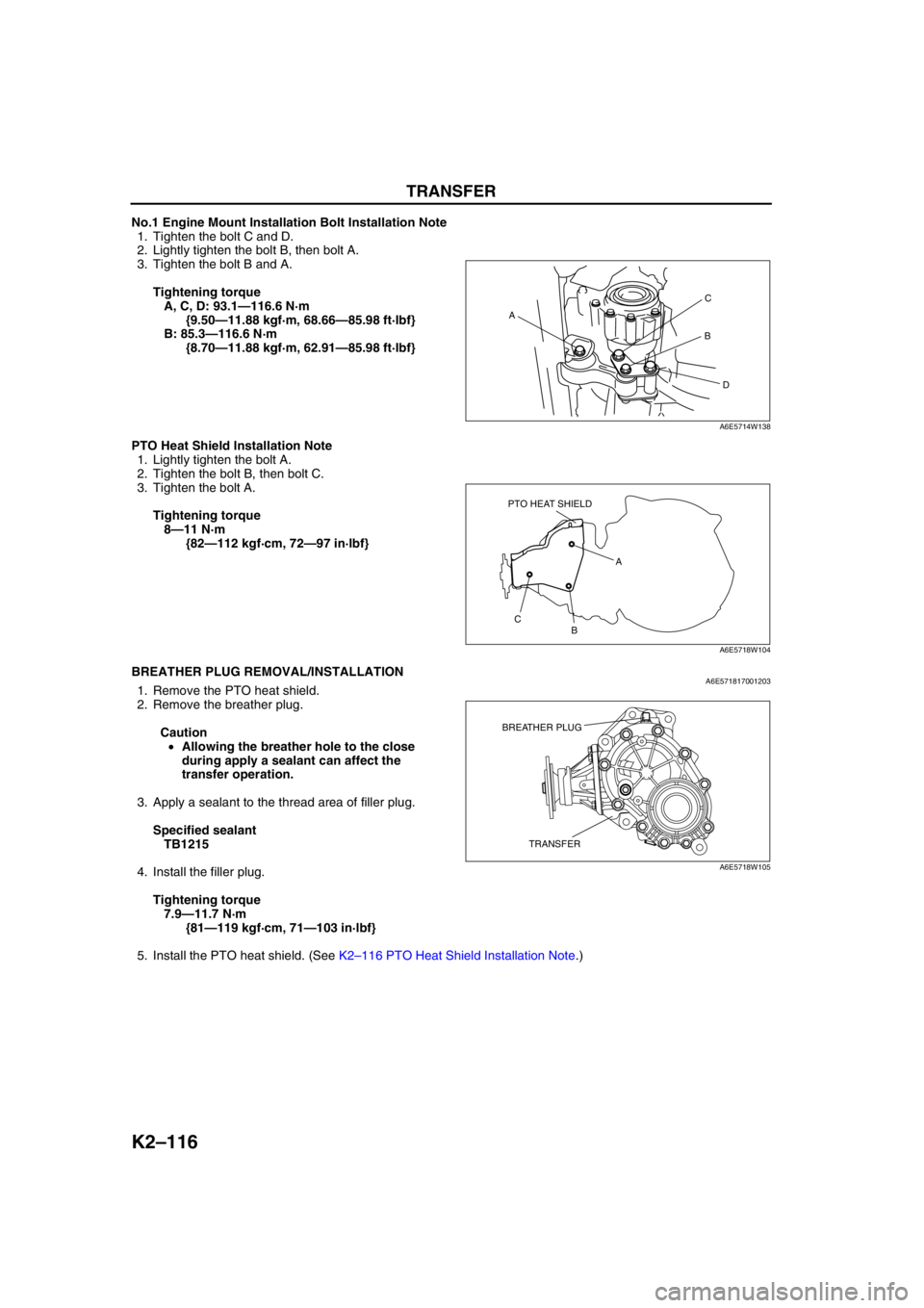
K2–116
TRANSFER
No.1 Engine Mount Installation Bolt Installation Note
1. Tighten the bolt C and D.
2. Lightly tighten the bolt B, then bolt A.
3. Tighten the bolt B and A.
Tightening torque
A, C, D: 93.1—116.6 N·m
{9.50—11.88 kgf·m, 68.66—85.98 ft·lbf}
B: 85.3—116.6 N·m
{8.70—11.88 kgf·m, 62.91—85.98 ft·lbf}
PTO Heat Shield Installation Note
1. Lightly tighten the bolt A.
2. Tighten the bolt B, then bolt C.
3. Tighten the bolt A.
Tightening torque
8—11 N·m
{82—112 kgf·cm, 72—97 in·lbf}
End Of SieBREATHER PLUG REMOVAL/INSTALLATIONA6E5718170012031. Remove the PTO heat shield.
2. Remove the breather plug.
Caution
•Allowing the breather hole to the close
during apply a sealant can affect the
transfer operation.
3. Apply a sealant to the thread area of filler plug.
Specified sealant
TB1215
4. Install the filler plug.
Tightening torque
7.9—11.7 N·m
{81—119 kgf·cm, 71—103 in·lbf}
5. Install the PTO heat shield. (See K2–116 PTO Heat Shield Installation Note.)
End Of Sie
AC
B
D
A6E5714W138
PTO HEAT SHIELD
A
B C
A6E5718W104
TRANSFER BREATHER PLUG
A6E5718W105
Page 541 of 909
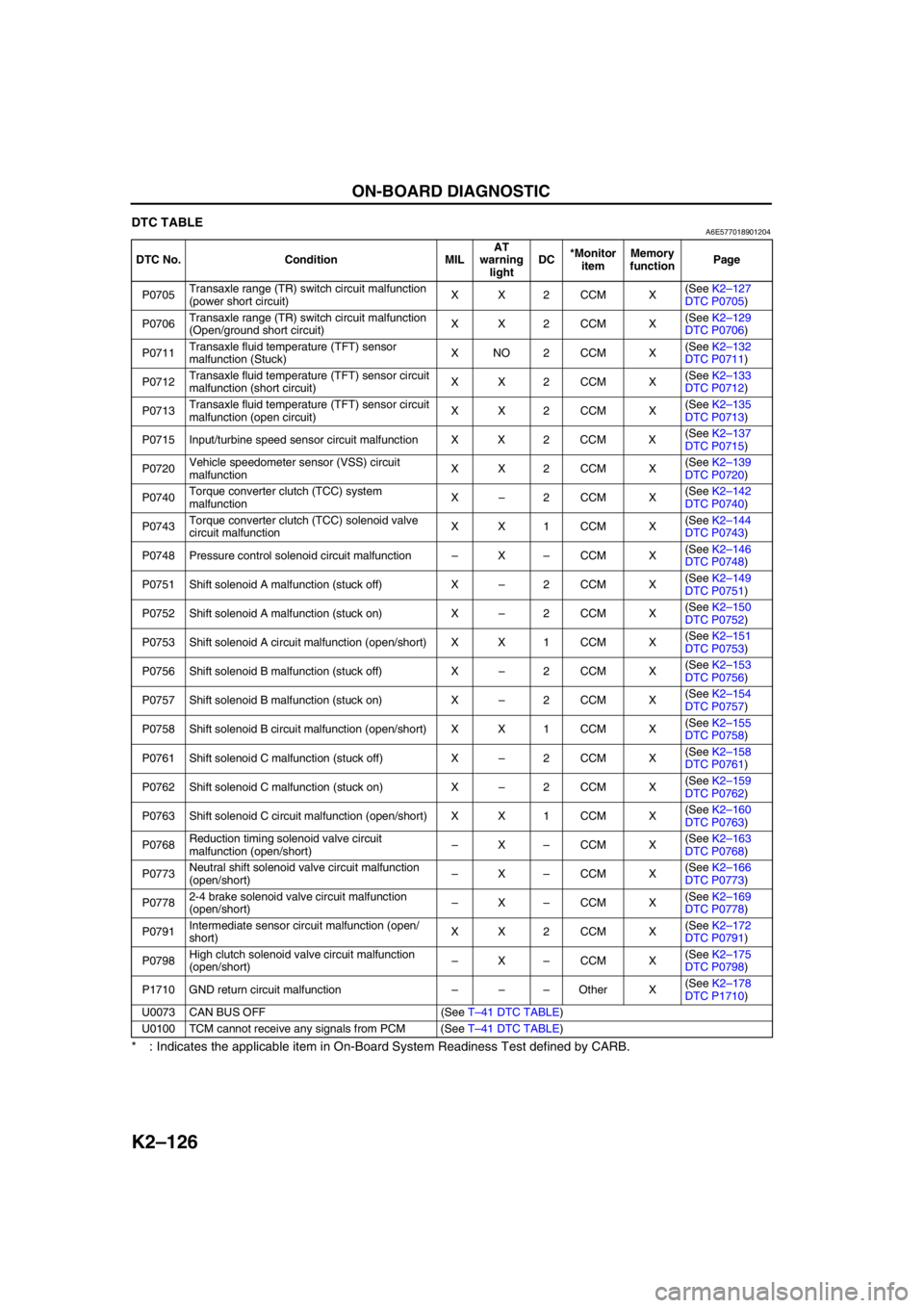
K2–126
ON-BOARD DIAGNOSTIC
DTC TABLEA6E577018901204
* : Indicates the applicable item in On-Board System Readiness Test defined by CARB.
End Of Sie
DTC No. Condition MILAT
warning
lightDC*Monitor
itemMemory
functionPage
P0705Transaxle range (TR) switch circuit malfunction
(power short circuit)XX2CCM X(See K2–127
DTC P0705)
P0706Transaxle range (TR) switch circuit malfunction
(Open/ground short circuit)XX2CCM X(See K2–129
DTC P0706)
P0711Transaxle fluid temperature (TFT) sensor
malfunction (Stuck)XNO2CCM X(See K2–132
DTC P0711)
P0712Transaxle fluid temperature (TFT) sensor circuit
malfunction (short circuit)XX2CCM X(See K2–133
DTC P0712)
P0713Transaxle fluid temperature (TFT) sensor circuit
malfunction (open circuit)XX2CCM X(See K2–135
DTC P0713)
P0715 Input/turbine speed sensor circuit malfunction X X 2 CCM X(See K2–137
DTC P0715)
P0720Vehicle speedometer sensor (VSS) circuit
malfunctionXX2CCM X(See K2–139
DTC P0720)
P0740Torque converter clutch (TCC) system
malfunctionX–2CCM X(See K2–142
DTC P0740)
P0743Torque converter clutch (TCC) solenoid valve
circuit malfunctionXX1CCM X(See K2–144
DTC P0743)
P0748 Pressure control solenoid circuit malfunction–X–CCM X(See K2–146
DTC P0748)
P0751 Shift solenoid A malfunction (stuck off) X–2CCM X(See K2–149
DTC P0751)
P0752 Shift solenoid A malfunction (stuck on) X–2CCM X(See K2–150
DTC P0752)
P0753 Shift solenoid A circuit malfunction (open/short) X X 1 CCM X(See K2–151
DTC P0753)
P0756 Shift solenoid B malfunction (stuck off) X–2CCM X(See K2–153
DTC P0756)
P0757 Shift solenoid B malfunction (stuck on) X–2CCM X(See K2–154
DTC P0757)
P0758 Shift solenoid B circuit malfunction (open/short) X X 1 CCM X(See K2–155
DTC P0758)
P0761 Shift solenoid C malfunction (stuck off) X–2CCM X(See K2–158
DTC P0761)
P0762 Shift solenoid C malfunction (stuck on) X–2CCM X(See K2–159
DTC P0762)
P0763 Shift solenoid C circuit malfunction (open/short) X X 1 CCM X(See K2–160
DTC P0763)
P0768Reduction timing solenoid valve circuit
malfunction (open/short)–X–CCM X(See K2–163
DTC P0768)
P0773Neutral shift solenoid valve circuit malfunction
(open/short)–X–CCM X(See K2–166
DTC P0773)
P07782-4 brake solenoid valve circuit malfunction
(open/short)–X–CCM X(See K2–169
DTC P0778)
P0791Intermediate sensor circuit malfunction (open/
short)XX2CCM X(See K2–172
DTC P0791)
P0798High clutch solenoid valve circuit malfunction
(open/short)–X–CCM X(See K2–175
DTC P0798)
P1710 GND return circuit malfunction–––Other X(See K2–178
DTC P1710)
U0073 CAN BUS OFF (See T–41 DTC TABLE)
U0100 TCM cannot receive any signals from PCM (See T–41 DTC TABLE)