torque MAZDA 6 2002 Suplement Service Manual
[x] Cancel search | Manufacturer: MAZDA, Model Year: 2002, Model line: 6, Model: MAZDA 6 2002Pages: 909, PDF Size: 17.16 MB
Page 420 of 909
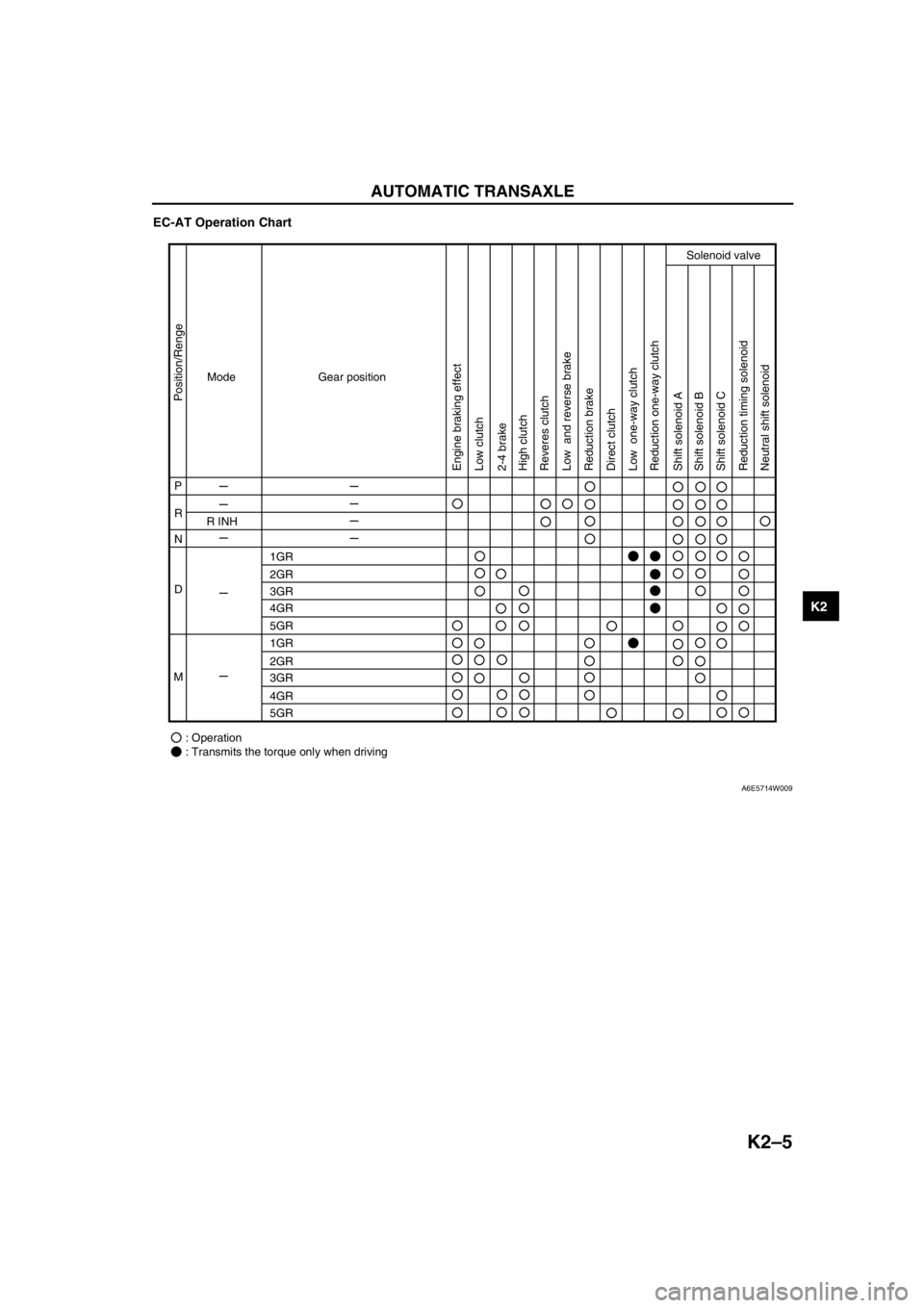
AUTOMATIC TRANSAXLE
K2–5
K2
EC-AT Operation Chart
End Of Sie
Mode
P
R
R INH
1GR
2GR
3GR
4GR
5GR
1GR
2GR
3GR
4GR
5GR
: Operation
: Transmits the torque only when driving N
D
MGear position
Position/Renge
Engine braking effect
Low clutch
Low one-way clutch Low and reverse brake
Reduction brake
Reduction timing solenoid
Neutral shift solenoid Reduction one-way clutch
Shift solenoid A
Shift solenoid B
Shift solenoid C Direct clutch 2-4 brake
Solenoid valve
High clutch
Reveres clutch
A6E5714W009
Page 427 of 909
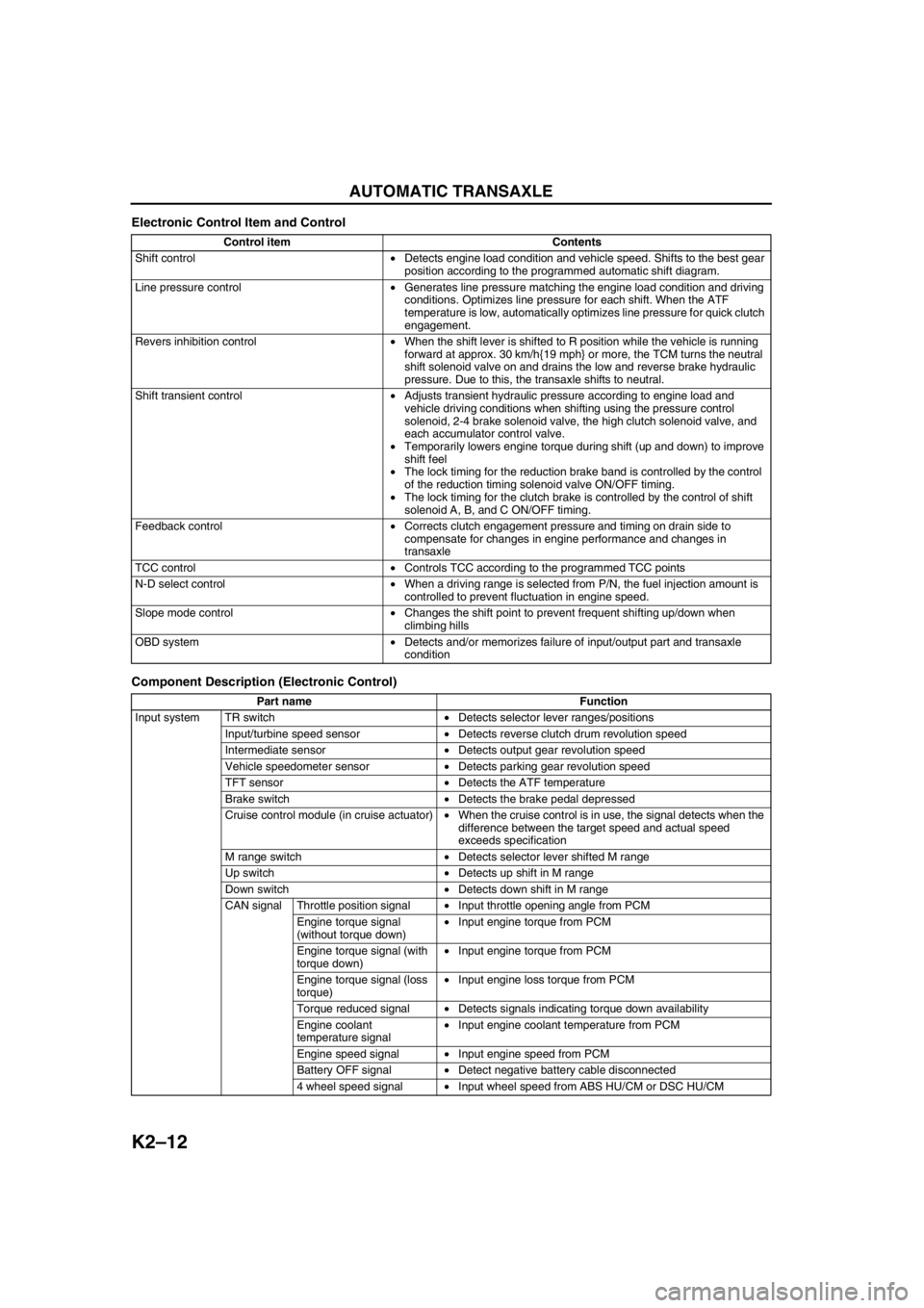
K2–12
AUTOMATIC TRANSAXLE
Electronic Control Item and Control
Component Description (Electronic Control)
Control item Contents
Shift control•Detects engine load condition and vehicle speed. Shifts to the best gear
position according to the programmed automatic shift diagram.
Line pressure control•Generates line pressure matching the engine load condition and driving
conditions. Optimizes line pressure for each shift. When the ATF
temperature is low, automatically optimizes line pressure for quick clutch
engagement.
Revers inhibition control•When the shift lever is shifted to R position while the vehicle is running
forward at approx. 30 km/h{19 mph} or more, the TCM turns the neutral
shift solenoid valve on and drains the low and reverse brake hydraulic
pressure. Due to this, the transaxle shifts to neutral.
Shift transient control•Adjusts transient hydraulic pressure according to engine load and
vehicle driving conditions when shifting using the pressure control
solenoid, 2-4 brake solenoid valve, the high clutch solenoid valve, and
each accumulator control valve.
•Temporarily lowers engine torque during shift (up and down) to improve
shift feel
•The lock timing for the reduction brake band is controlled by the control
of the reduction timing solenoid valve ON/OFF timing.
•The lock timing for the clutch brake is controlled by the control of shift
solenoid A, B, and C ON/OFF timing.
Feedback control•Corrects clutch engagement pressure and timing on drain side to
compensate for changes in engine performance and changes in
transaxle
TCC control•Controls TCC according to the programmed TCC points
N-D select control•When a driving range is selected from P/N, the fuel injection amount is
controlled to prevent fluctuation in engine speed.
Slope mode control•Changes the shift point to prevent frequent shifting up/down when
climbing hills
OBD system•Detects and/or memorizes failure of input/output part and transaxle
condition
Part name Function
Input system TR switch•Detects selector lever ranges/positions
Input/turbine speed sensor•Detects reverse clutch drum revolution speed
Intermediate sensor•Detects output gear revolution speed
Vehicle speedometer sensor•Detects parking gear revolution speed
TFT sensor•Detects the ATF temperature
Brake switch•Detects the brake pedal depressed
Cruise control module (in cruise actuator)•When the cruise control is in use, the signal detects when the
difference between the target speed and actual speed
exceeds specification
M range switch•Detects selector lever shifted M range
Up switch•Detects up shift in M range
Down switch•Detects down shift in M range
CAN signal Throttle position signal•Input throttle opening angle from PCM
Engine torque signal
(without torque down)•Input engine torque from PCM
Engine torque signal (with
torque down)•Input engine torque from PCM
Engine torque signal (loss
torque)•Input engine loss torque from PCM
Torque reduced signal•Detects signals indicating torque down availability
Engine coolant
temperature signal•Input engine coolant temperature from PCM
Engine speed signal•Input engine speed from PCM
Battery OFF signal•Detect negative battery cable disconnected
4 wheel speed signal•Input wheel speed from ABS HU/CM or DSC HU/CM
Page 428 of 909
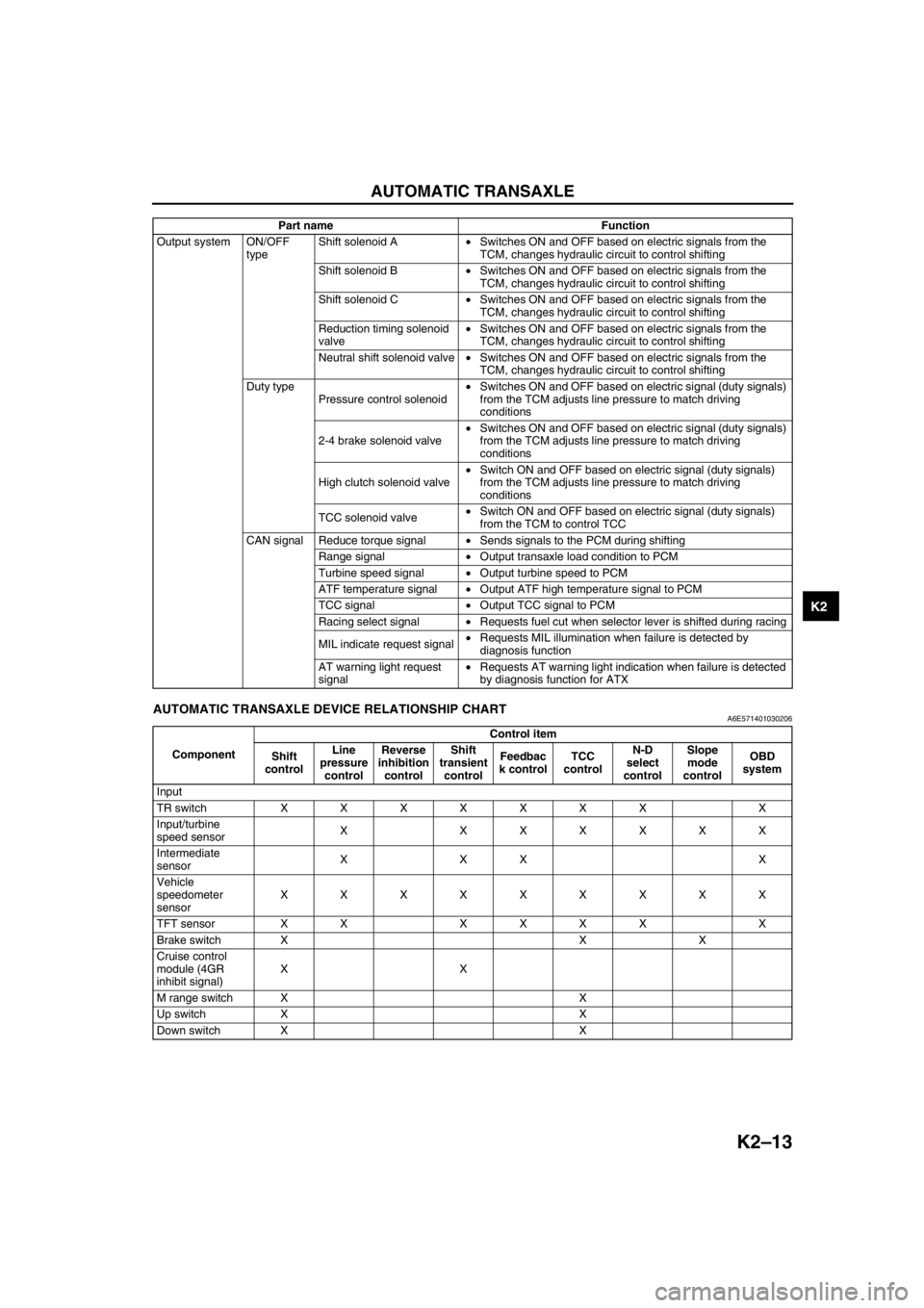
AUTOMATIC TRANSAXLE
K2–13
K2
End Of SieAUTOMATIC TRANSAXLE DEVICE RELATIONSHIP CHARTA6E571401030206
Output system ON/OFF
typeShift solenoid A•Switches ON and OFF based on electric signals from the
TCM, changes hydraulic circuit to control shifting
Shift solenoid B•Switches ON and OFF based on electric signals from the
TCM, changes hydraulic circuit to control shifting
Shift solenoid C•Switches ON and OFF based on electric signals from the
TCM, changes hydraulic circuit to control shifting
Reduction timing solenoid
valve•Switches ON and OFF based on electric signals from the
TCM, changes hydraulic circuit to control shifting
Neutral shift solenoid valve•Switches ON and OFF based on electric signals from the
TCM, changes hydraulic circuit to control shifting
Duty type
Pressure control solenoid•Switches ON and OFF based on electric signal (duty signals)
from the TCM adjusts line pressure to match driving
conditions
2-4 brake solenoid valve•Switches ON and OFF based on electric signal (duty signals)
from the TCM adjusts line pressure to match driving
conditions
High clutch solenoid valve•Switch ON and OFF based on electric signal (duty signals)
from the TCM adjusts line pressure to match driving
conditions
TCC solenoid valve•Switch ON and OFF based on electric signal (duty signals)
from the TCM to control TCC
CAN signal Reduce torque signal•Sends signals to the PCM during shifting
Range signal•Output transaxle load condition to PCM
Turbine speed signal•Output turbine speed to PCM
ATF temperature signal•Output ATF high temperature signal to PCM
TCC signal•Output TCC signal to PCM
Racing select signal•Requests fuel cut when selector lever is shifted during racing
MIL indicate request signal•Requests MIL illumination when failure is detected by
diagnosis function
AT warning light request
signal•Requests AT warning light indication when failure is detected
by diagnosis function for ATX Part name Function
ComponentControl item
Shift
controlLine
pressure
controlReverse
inhibition
controlShift
transient
controlFeedbac
k controlTCC
controlN-D
select
controlSlope
mode
controlOBD
system
Input
TR switch XXXXXXX X
Input/turbine
speed sensorX XXXXXX
Intermediate
sensorXXX X
Vehicle
speedometer
sensorXXXXXXXXX
TFT sensor XX XXXX X
Brake switch X X X
Cruise control
module (4GR
inhibit signal)XX
M range switch X X
Up switch X X
Down switch X X
Page 429 of 909
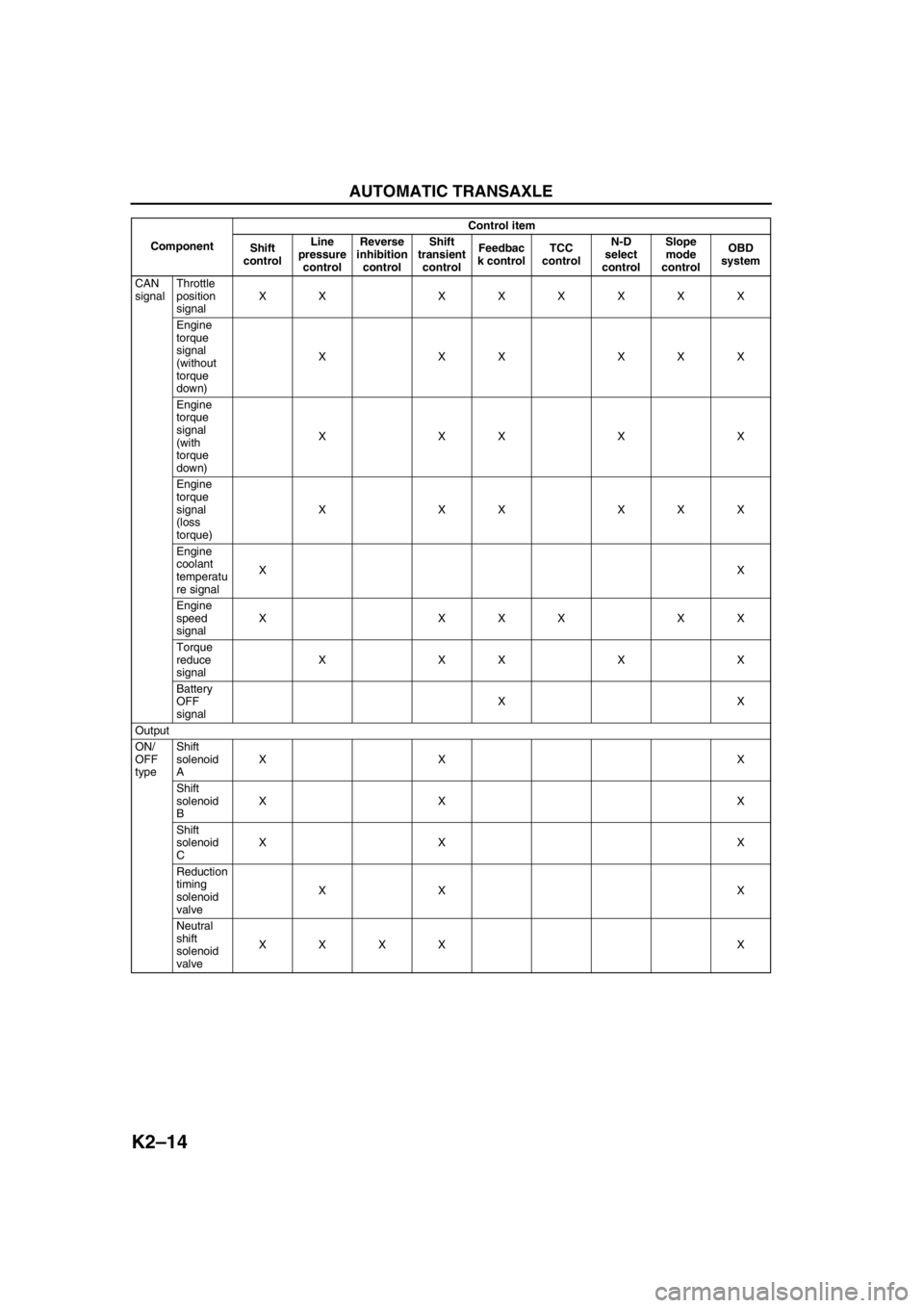
K2–14
AUTOMATIC TRANSAXLE
CAN
signalThrottle
position
signalXX XXXXXX
Engine
torque
signal
(without
torque
down)XXXXXX
Engine
torque
signal
(with
torque
down)XXXXX
Engine
torque
signal
(loss
torque)XXXXXX
Engine
coolant
temperatu
re signalXX
Engine
speed
signalX XXX XX
Torque
reduce
signalXXXXX
Battery
OFF
signalXX
Output
ON/
OFF
typeShift
solenoid
AXX X
Shift
solenoid
BXX X
Shift
solenoid
CXX X
Reduction
timing
solenoid
valveXX X
Neutral
shift
solenoid
valveXXXX X ComponentControl item
Shift
controlLine
pressure
controlReverse
inhibition
controlShift
transient
controlFeedbac
k controlTCC
controlN-D
select
controlSlope
mode
controlOBD
system
Page 430 of 909
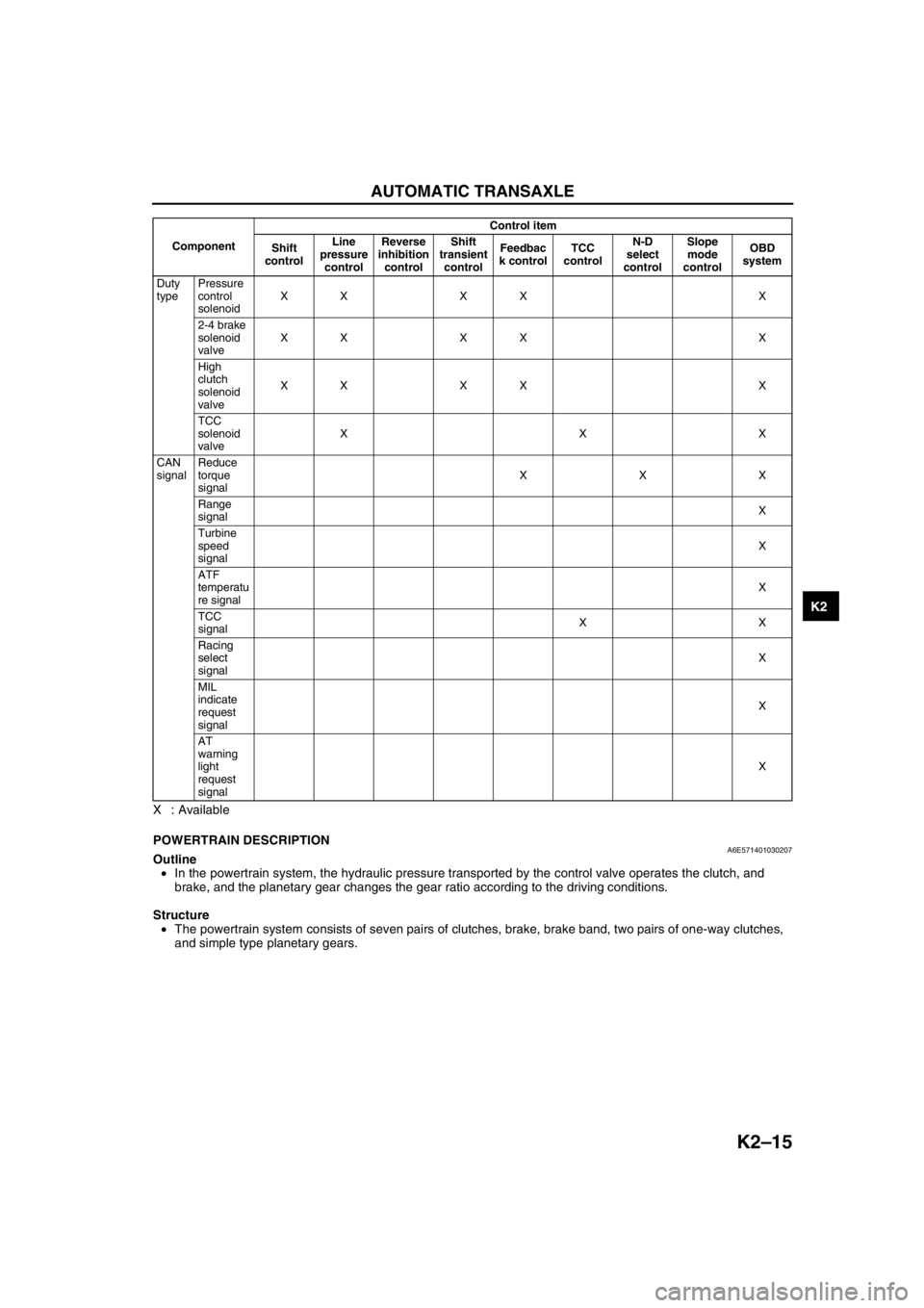
AUTOMATIC TRANSAXLE
K2–15
K2
X : Available
End Of SiePOWERTRAIN DESCRIPTIONA6E571401030207Outline
•In the powertrain system, the hydraulic pressure transported by the control valve operates the clutch, and
brake, and the planetary gear changes the gear ratio according to the driving conditions.
Structure
•The powertrain system consists of seven pairs of clutches, brake, brake band, two pairs of one-way clutches,
and simple type planetary gears.
Duty
typePressure
control
solenoidXX XX X
2-4 brake
solenoid
valveXX XX X
High
clutch
solenoid
valveXX XX X
TCC
solenoid
valveXXX
CAN
signalReduce
torque
signalXXX
Range
signalX
Turbine
speed
signalX
ATF
temperatu
re signalX
TCC
signalXX
Racing
select
signalX
MIL
indicate
request
signalX
AT
warning
light
request
signalX ComponentControl item
Shift
controlLine
pressure
controlReverse
inhibition
controlShift
transient
controlFeedbac
k controlTCC
controlN-D
select
controlSlope
mode
controlOBD
system
Page 455 of 909
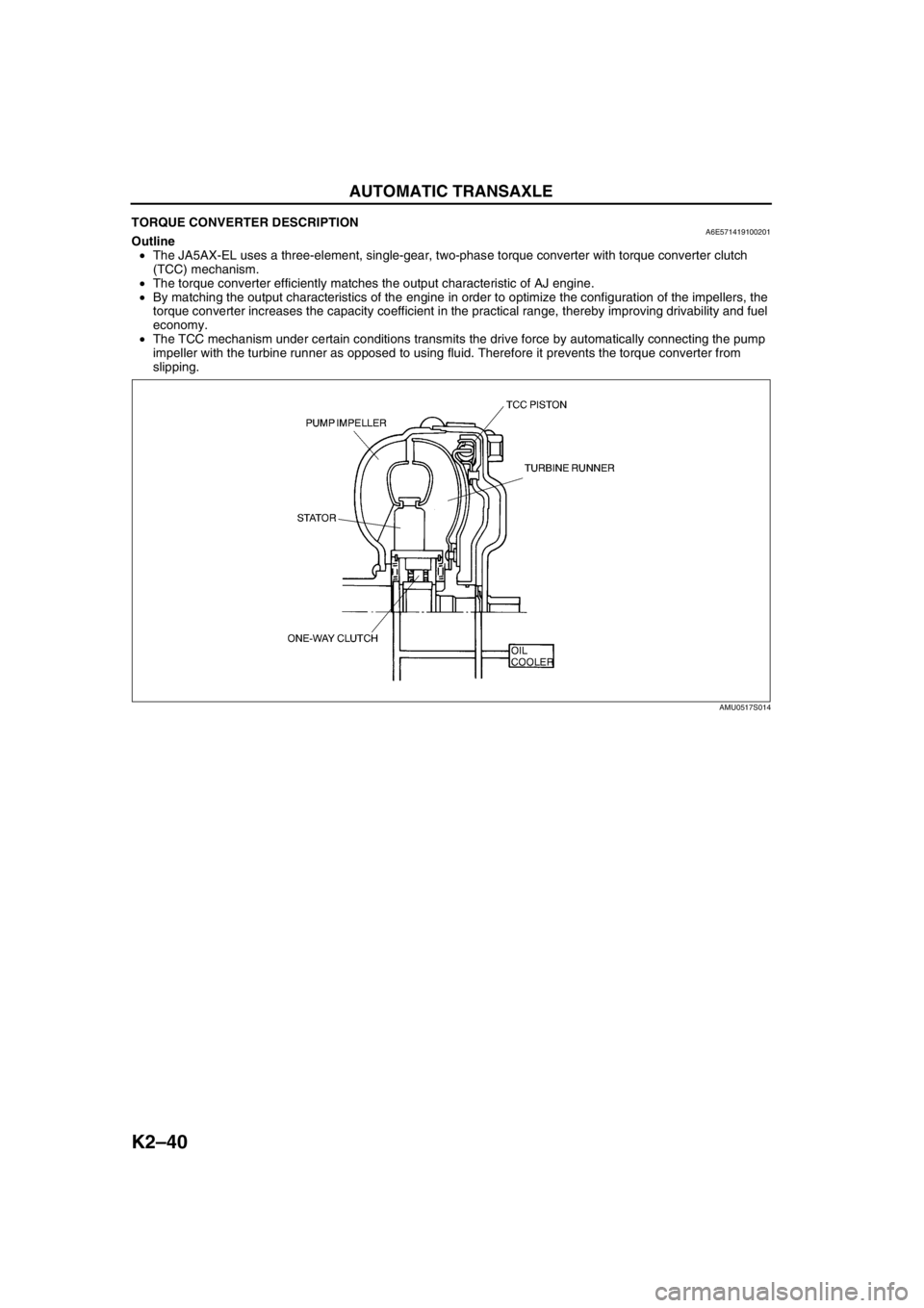
K2–40
AUTOMATIC TRANSAXLE
TORQUE CONVERTER DESCRIPTIONA6E571419100201Outline
•The JA5AX-EL uses a three-element, single-gear, two-phase torque converter with torque converter clutch
(TCC) mechanism.
•The torque converter efficiently matches the output characteristic of AJ engine.
•By matching the output characteristics of the engine in order to optimize the configuration of the impellers, the
torque converter increases the capacity coefficient in the practical range, thereby improving drivability and fuel
economy.
•The TCC mechanism under certain conditions transmits the drive force by automatically connecting the pump
impeller with the turbine runner as opposed to using fluid. Therefore it prevents the torque converter from
slipping.
End Of Sie
AMU0517S014
Page 456 of 909
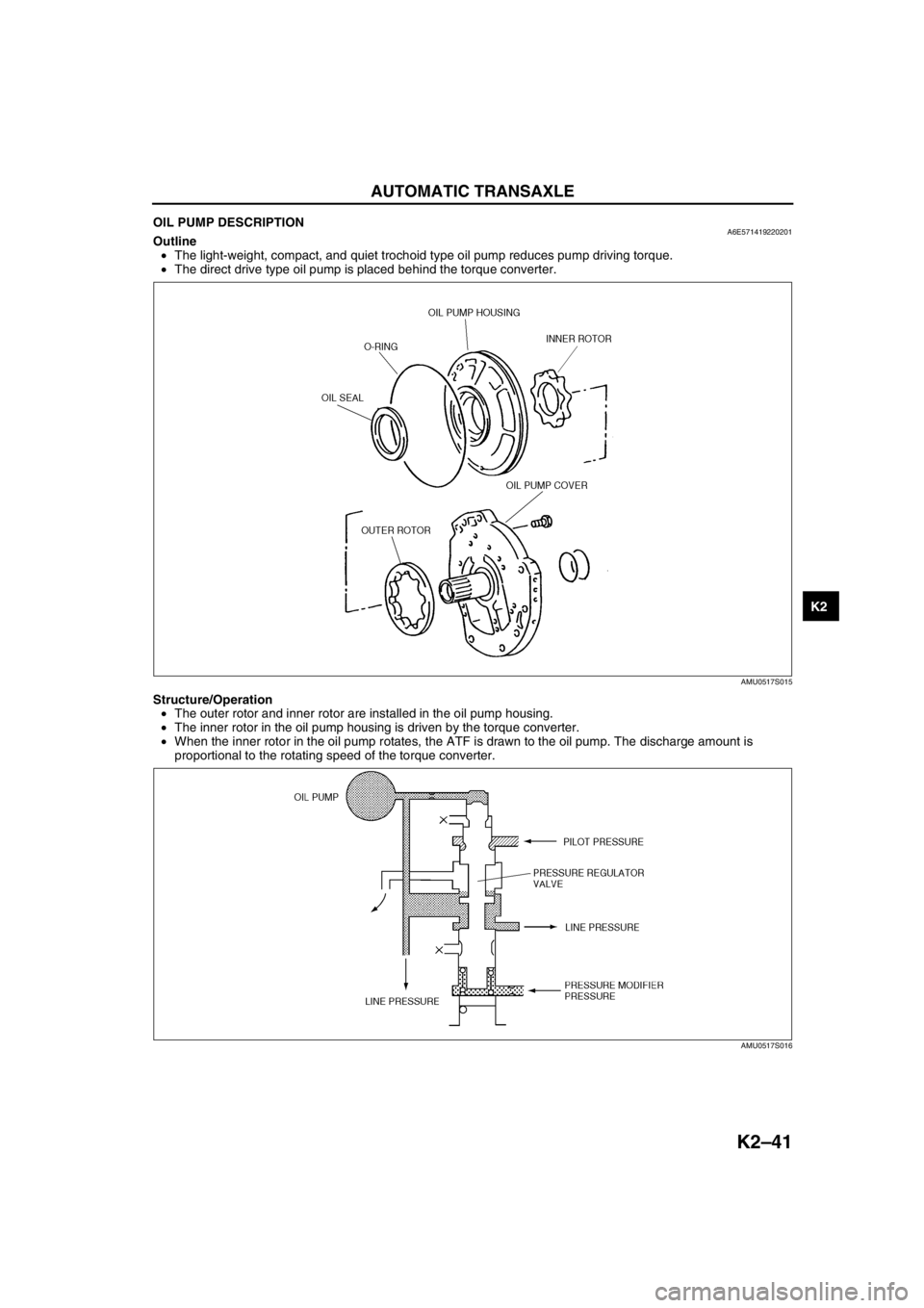
AUTOMATIC TRANSAXLE
K2–41
K2
OIL PUMP DESCRIPTIONA6E571419220201Outline
•The light-weight, compact, and quiet trochoid type oil pump reduces pump driving torque.
•The direct drive type oil pump is placed behind the torque converter.
Structure/Operation
•The outer rotor and inner rotor are installed in the oil pump housing.
•The inner rotor in the oil pump housing is driven by the torque converter.
•When the inner rotor in the oil pump rotates, the ATF is drawn to the oil pump. The discharge amount is
proportional to the rotating speed of the torque converter.
End Of Sie
AMU0517S015
AMU0517S016
Page 460 of 909
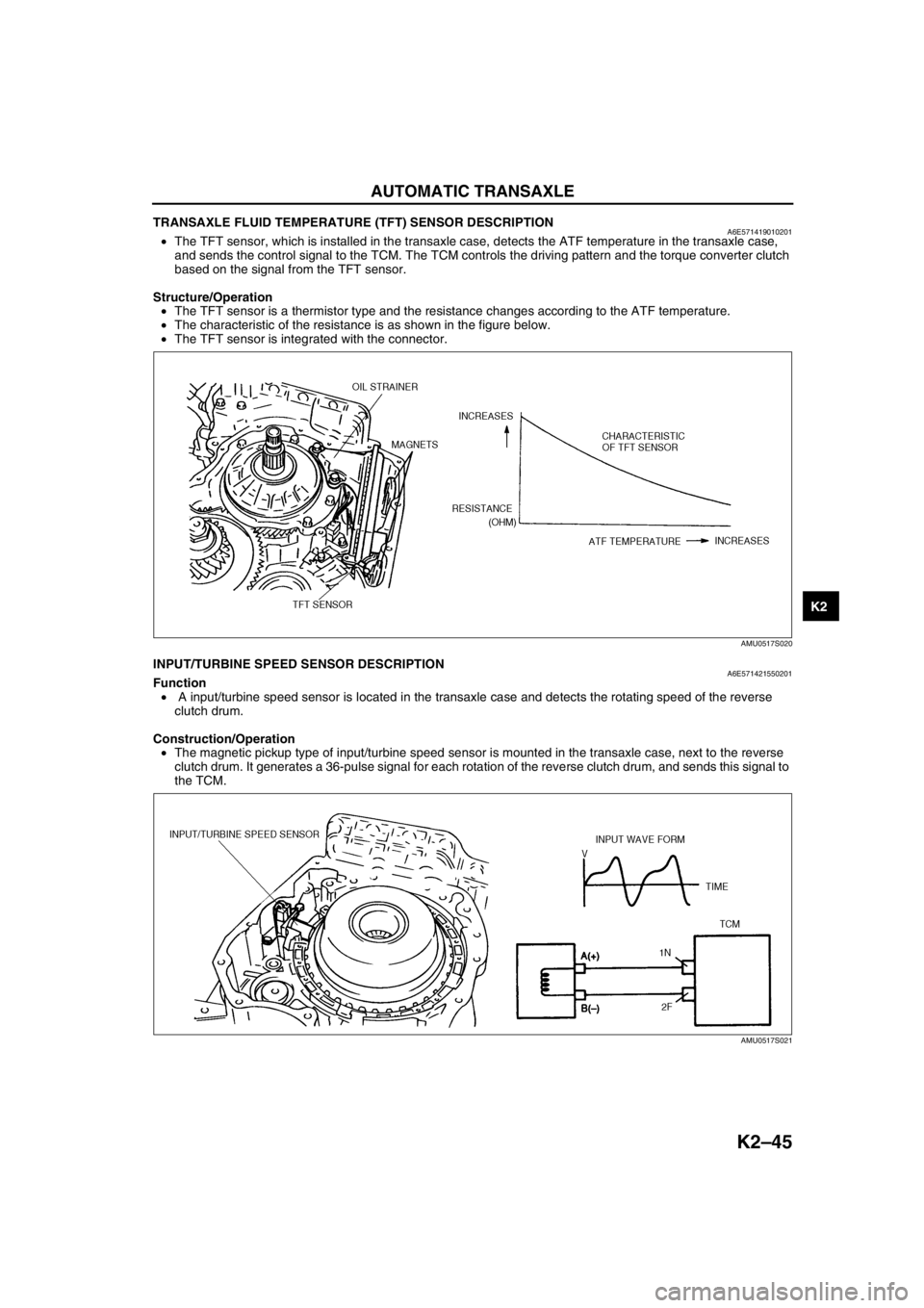
AUTOMATIC TRANSAXLE
K2–45
K2
TRANSAXLE FLUID TEMPERATURE (TFT) SENSOR DESCRIPTIONA6E571419010201•The TFT sensor, which is installed in the transaxle case, detects the ATF temperature in the transaxle case,
and sends the control signal to the TCM. The TCM controls the driving pattern and the torque converter clutch
based on the signal from the TFT sensor.
Structure/Operation
•The TFT sensor is a thermistor type and the resistance changes according to the ATF temperature.
•The characteristic of the resistance is as shown in the figure below.
•The TFT sensor is integrated with the connector.
End Of SieINPUT/TURBINE SPEED SENSOR DESCRIPTIONA6E571421550201Function
• A input/turbine speed sensor is located in the transaxle case and detects the rotating speed of the reverse
clutch drum.
Construction/Operation
•The magnetic pickup type of input/turbine speed sensor is mounted in the transaxle case, next to the reverse
clutch drum. It generates a 36-pulse signal for each rotation of the reverse clutch drum, and sends this signal to
the TCM.
End Of Sie
AMU0517S020
AMU0517S021
Page 463 of 909
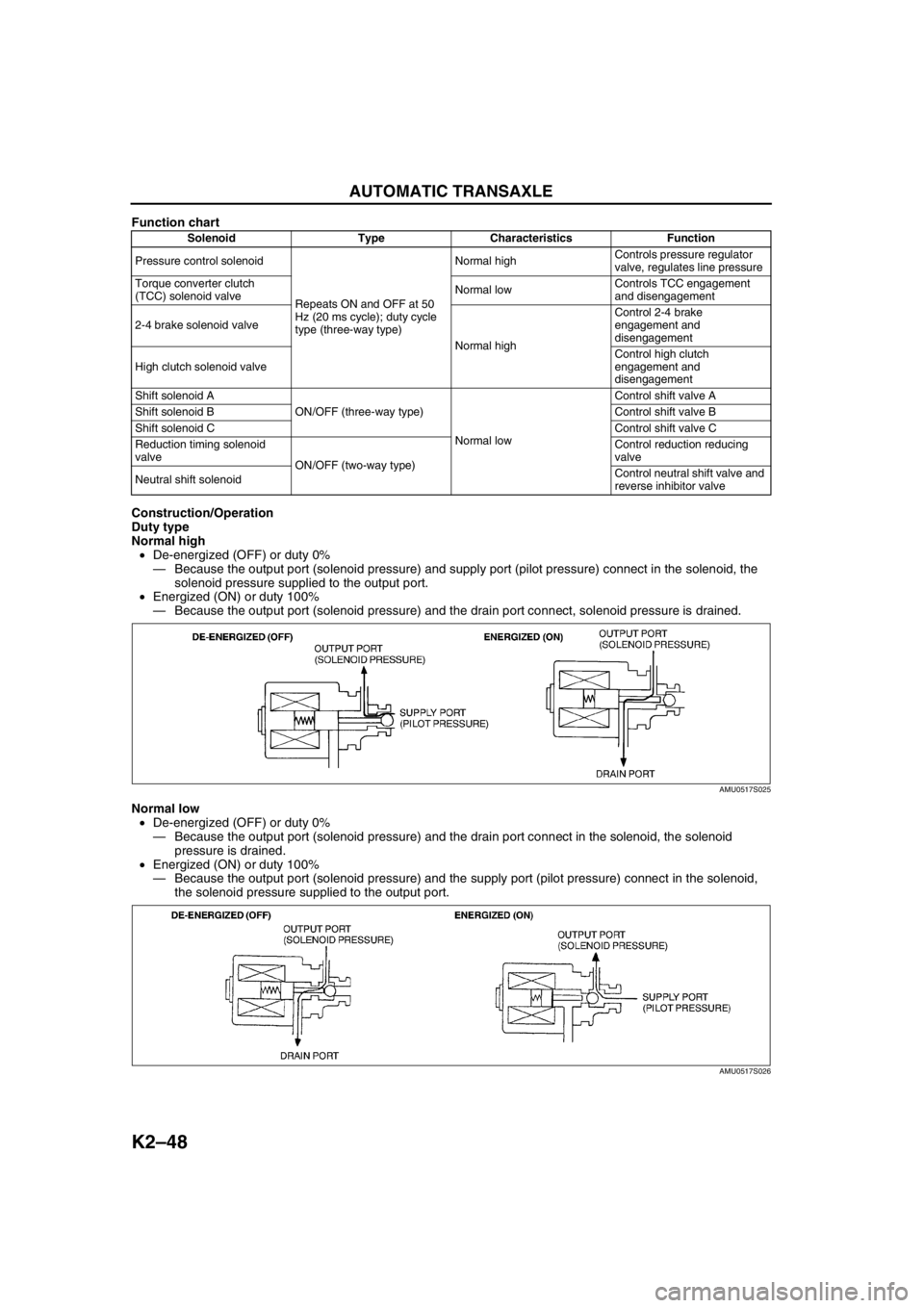
K2–48
AUTOMATIC TRANSAXLE
Function chart
Construction/Operation
Duty type
Normal high
•De-energized (OFF) or duty 0%
—Because the output port (solenoid pressure) and supply port (pilot pressure) connect in the solenoid, the
solenoid pressure supplied to the output port.
•Energized (ON) or duty 100%
—Because the output port (solenoid pressure) and the drain port connect, solenoid pressure is drained.
Normal low
•De-energized (OFF) or duty 0%
—Because the output port (solenoid pressure) and the drain port connect in the solenoid, the solenoid
pressure is drained.
•Energized (ON) or duty 100%
—Because the output port (solenoid pressure) and the supply port (pilot pressure) connect in the solenoid,
the solenoid pressure supplied to the output port.
Solenoid Type Characteristics Function
Pressure control solenoid
Repeats ON and OFF at 50
Hz (20 ms cycle); duty cycle
type (three-way type)Normal highControls pressure regulator
valve, regulates line pressure
Torque converter clutch
(TCC) solenoid valveNormal lowControls TCC engagement
and disengagement
2-4 brake solenoid valve
Normal highControl 2-4 brake
engagement and
disengagement
High clutch solenoid valveControl high clutch
engagement and
disengagement
Shift solenoid A
ON/OFF (three-way type)
Normal lowControl shift valve A
Shift solenoid BControl shift valve B
Shift solenoid CControl shift valve C
Reduction timing solenoid
valve
ON/OFF (two-way type)Control reduction reducing
valve
Neutral shift solenoidControl neutral shift valve and
reverse inhibitor valve
AMU0517S025
AMU0517S026
Page 465 of 909
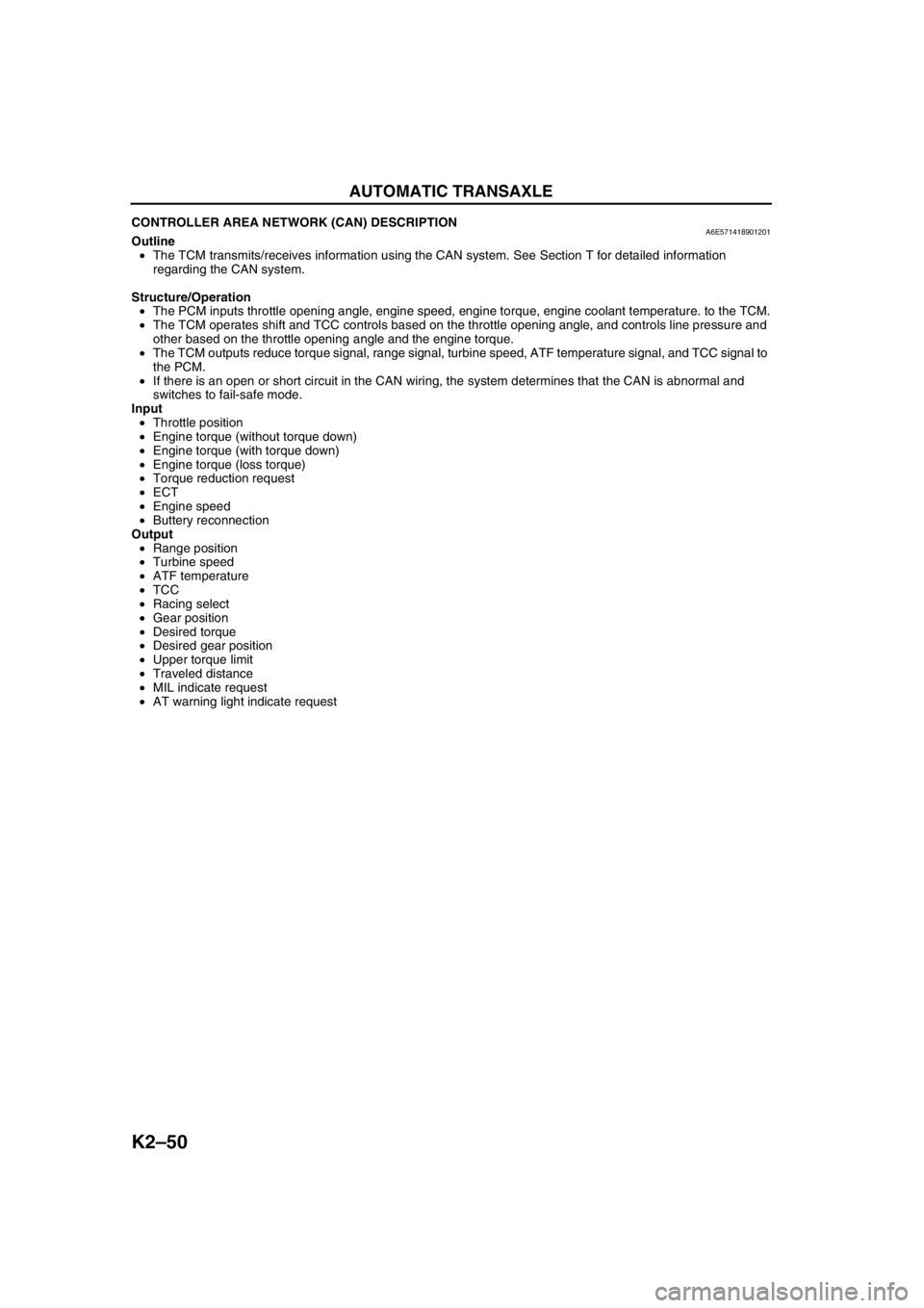
K2–50
AUTOMATIC TRANSAXLE
CONTROLLER AREA NETWORK (CAN) DESCRIPTIONA6E571418901201Outline
•The TCM transmits/receives information using the CAN system. See Section T for detailed information
regarding the CAN system.
Structure/Operation
•The PCM inputs throttle opening angle, engine speed, engine torque, engine coolant temperature. to the TCM.
•The TCM operates shift and TCC controls based on the throttle opening angle, and controls line pressure and
other based on the throttle opening angle and the engine torque.
•The TCM outputs reduce torque signal, range signal, turbine speed, ATF temperature signal, and TCC signal to
the PCM.
•If there is an open or short circuit in the CAN wiring, the system determines that the CAN is abnormal and
switches to fail-safe mode.
Input
•Throttle position
•Engine torque (without torque down)
•Engine torque (with torque down)
•Engine torque (loss torque)
•Torque reduction request
•ECT
•Engine speed
•Buttery reconnection
Output
•Range position
•Turbine speed
•ATF temperature
•TCC
•Racing select
•Gear position
•Desired torque
•Desired gear position
•Upper torque limit
•Traveled distance
•MIL indicate request
•AT warning light indicate request
End Of Sie