turn signal MAZDA 6 2002 Suplement Manual Online
[x] Cancel search | Manufacturer: MAZDA, Model Year: 2002, Model line: 6, Model: MAZDA 6 2002Pages: 909, PDF Size: 17.16 MB
Page 646 of 909
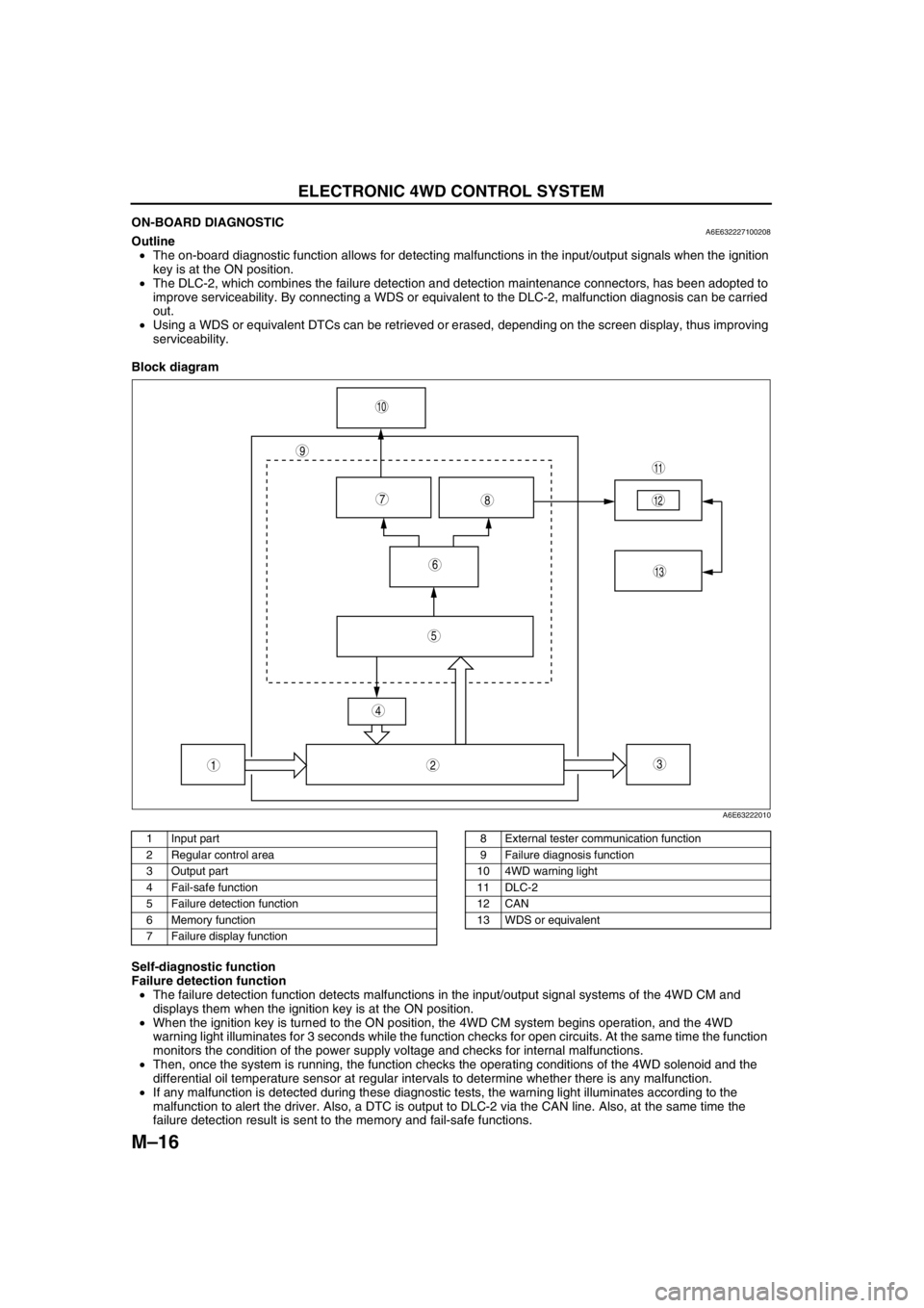
M–16
ELECTRONIC 4WD CONTROL SYSTEM
ON-BOARD DIAGNOSTICA6E632227100208Outline
•The on-board diagnostic function allows for detecting malfunctions in the input/output signals when the ignition
key is at the ON position.
•The DLC-2, which combines the failure detection and detection maintenance connectors, has been adopted to
improve serviceability. By connecting a WDS or equivalent to the DLC-2, malfunction diagnosis can be carried
out.
•Using a WDS or equivalent DTCs can be retrieved or erased, depending on the screen display, thus improving
serviceability.
Block diagram
.
Self-diagnostic function
Failure detection function
•The failure detection function detects malfunctions in the input/output signal systems of the 4WD CM and
displays them when the ignition key is at the ON position.
•When the ignition key is turned to the ON position, the 4WD CM system begins operation, and the 4WD
warning light illuminates for 3 seconds while the function checks for open circuits. At the same time the function
monitors the condition of the power supply voltage and checks for internal malfunctions.
•Then, once the system is running, the function checks the operating conditions of the 4WD solenoid and the
differential oil temperature sensor at regular intervals to determine whether there is any malfunction.
•If any malfunction is detected during these diagnostic tests, the warning light illuminates according to the
malfunction to alert the driver. Also, a DTC is output to DLC-2 via the CAN line. Also, at the same time the
failure detection result is sent to the memory and fail-safe functions.
9
87
5
4
3
10
13
11
12
6
12
A6E63222010
1 Input part
2 Regular control area
3 Output part
4 Fail-safe function
5 Failure detection function
6 Memory function
7 Failure display function8 External tester communication function
9 Failure diagnosis function
10 4WD warning light
11 DLC-2
12 CAN
13 WDS or equivalent
Page 647 of 909
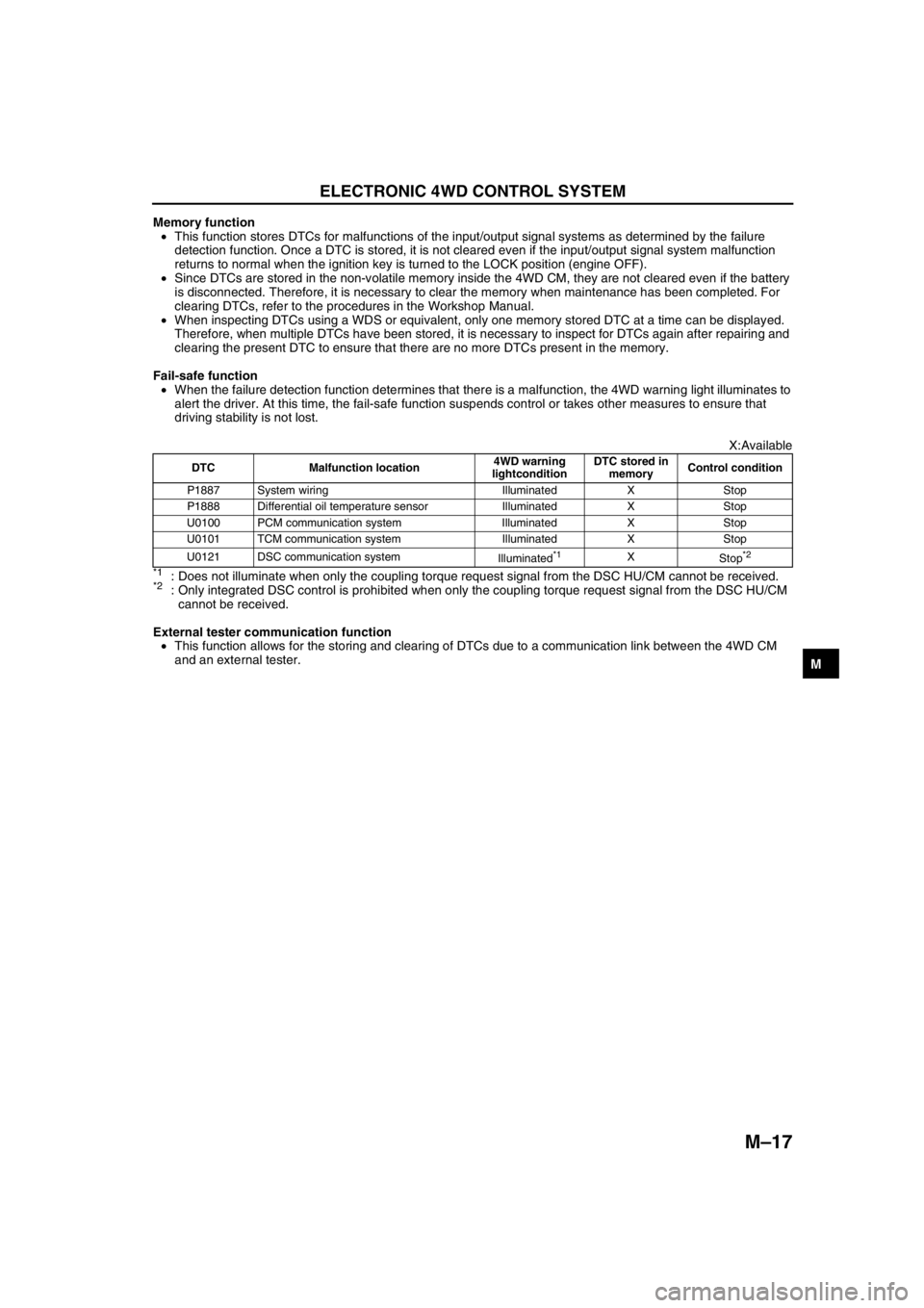
ELECTRONIC 4WD CONTROL SYSTEM
M–17
M
Memory function
•This function stores DTCs for malfunctions of the input/output signal systems as determined by the failure
detection function. Once a DTC is stored, it is not cleared even if the input/output signal system malfunction
returns to normal when the ignition key is turned to the LOCK position (engine OFF).
•Since DTCs are stored in the non-volatile memory inside the 4WD CM, they are not cleared even if the battery
is disconnected. Therefore, it is necessary to clear the memory when maintenance has been completed. For
clearing DTCs, refer to the procedures in the Workshop Manual.
•When inspecting DTCs using a WDS or equivalent, only one memory stored DTC at a time can be displayed.
Therefore, when multiple DTCs have been stored, it is necessary to inspect for DTCs again after repairing and
clearing the present DTC to ensure that there are no more DTCs present in the memory.
Fail-safe function
•When the failure detection function determines that there is a malfunction, the 4WD warning light illuminates to
alert the driver. At this time, the fail-safe function suspends control or takes other measures to ensure that
driving stability is not lost.
X:Available
*1: Does not illuminate when only the coupling torque request signal from the DSC HU/CM cannot be received.*2: Only integrated DSC control is prohibited when only the coupling torque request signal from the DSC HU/CM
cannot be received.
External tester communication function
•This function allows for the storing and clearing of DTCs due to a communication link between the 4WD CM
and an external tester.
End Of Sie
DTC Malfunction location4WD warning
lightconditionDTC stored in
memoryControl condition
P1887 System wiring Illuminated X Stop
P1888 Differential oil temperature sensor Illuminated X Stop
U0100 PCM communication system Illuminated X Stop
U0101 TCM communication system Illuminated X Stop
U0121 DSC communication system
Illuminated
*1X
Stop*2
Page 707 of 909
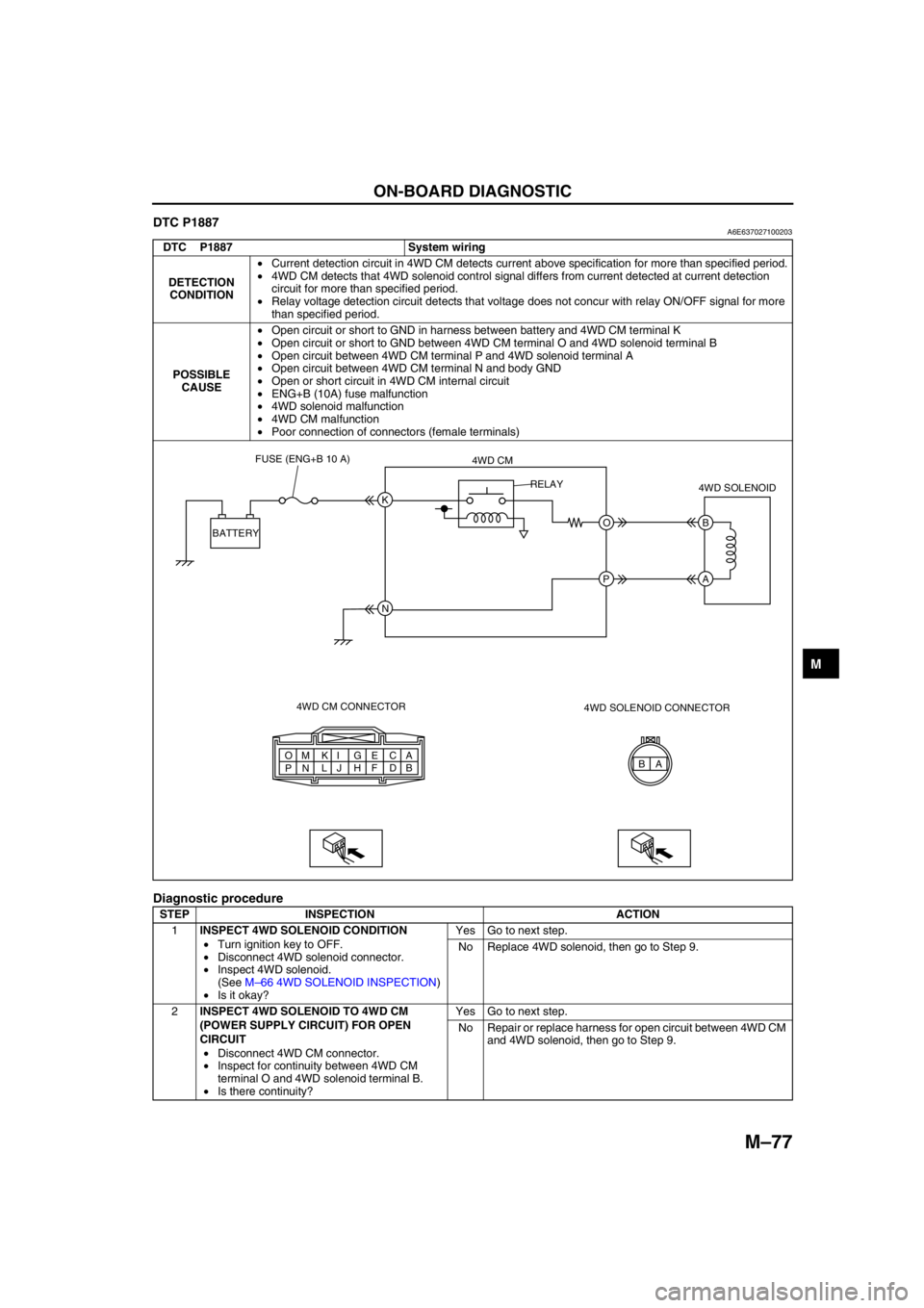
ON-BOARD DIAGNOSTIC
M–77
M
DTC P1887A6E637027100203
Diagnostic procedure
DTC P1887 System wiring
DETECTION
CONDITION•Current detection circuit in 4WD CM detects current above specification for more than specified period.
•4WD CM detects that 4WD solenoid control signal differs from current detected at current detection
circuit for more than specified period.
•Relay voltage detection circuit detects that voltage does not concur with relay ON/OFF signal for more
than specified period.
POSSIBLE
CAUSE•Open circuit or short to GND in harness between battery and 4WD CM terminal K
•Open circuit or short to GND between 4WD CM terminal O and 4WD solenoid terminal B
•Open circuit between 4WD CM terminal P and 4WD solenoid terminal A
•Open circuit between 4WD CM terminal N and body GND
•Open or short circuit in 4WD CM internal circuit
•ENG+B (10A) fuse malfunction
•4WD solenoid malfunction
•4WD CM malfunction
•Poor connection of connectors (female terminals)
STEP INSPECTION ACTION
1INSPECT 4WD SOLENOID CONDITION
•Turn ignition key to OFF.
•Disconnect 4WD solenoid connector.
•Inspect 4WD solenoid.
(See M–66 4WD SOLENOID INSPECTION)
•Is it okay?Yes Go to next step.
No Replace 4WD solenoid, then go to Step 9.
2INSPECT 4WD SOLENOID TO 4WD CM
(POWER SUPPLY CIRCUIT) FOR OPEN
CIRCUIT
•Disconnect 4WD CM connector.
•Inspect for continuity between 4WD CM
terminal O and 4WD solenoid terminal B.
•Is there continuity?Yes Go to next step.
No Repair or replace harness for open circuit between 4WD CM
and 4WD solenoid, then go to Step 9.
A A
B C
D E
F G
H I
J K
L M
N O
PB K
O B
A
N P BATTERYFUSE (ENG+B 10 A)
4WD CM
4WD CM CONNECTOR4WD SOLENOID
4WD SOLENOID CONNECTOR RELAY
Page 750 of 909
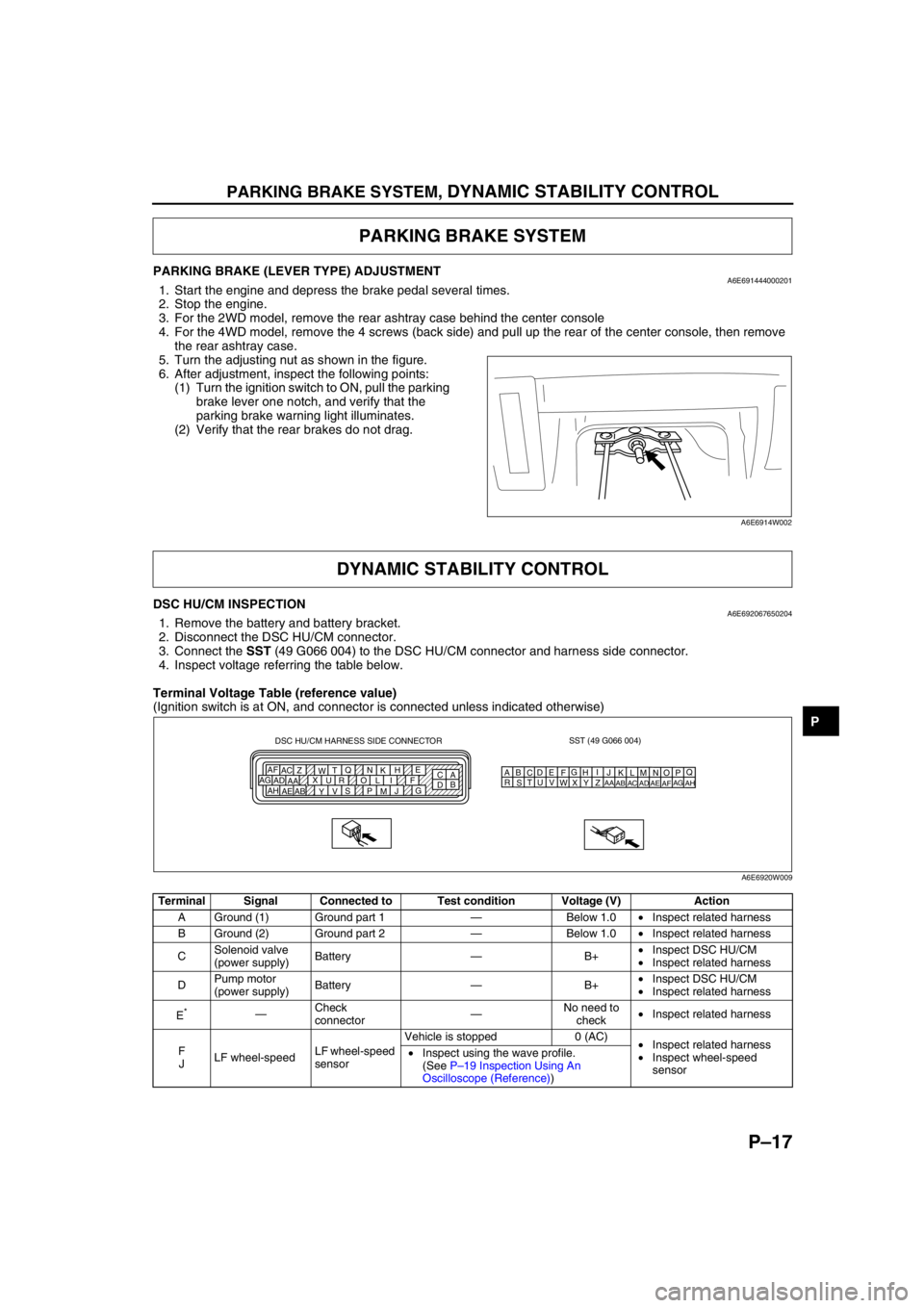
PARKING BRAKE SYSTEM, DYNAMIC STABILITY CONTROL
P–17
P
PARKING BRAKE (LEVER TYPE) ADJUSTMENTA6E6914440002011. Start the engine and depress the brake pedal several times.
2. Stop the engine.
3. For the 2WD model, remove the rear ashtray case behind the center console
4. For the 4WD model, remove the 4 screws (back side) and pull up the rear of the center console, then remove
the rear ashtray case.
5. Turn the adjusting nut as shown in the figure.
6. After adjustment, inspect the following points:
(1) Turn the ignition switch to ON, pull the parking
brake lever one notch, and verify that the
parking brake warning light illuminates.
(2) Verify that the rear brakes do not drag.
End Of Sie
DSC HU/CM INSPECTIONA6E6920676502041. Remove the battery and battery bracket.
2. Disconnect the DSC HU/CM connector.
3. Connect the SST (49 G066 004) to the DSC HU/CM connector and harness side connector.
4. Inspect voltage referring the table below.
Terminal Voltage Table (reference value)
(Ignition switch is at ON, and connector is connected unless indicated otherwise)
PARKING BRAKE SYSTEM
A6E6914W002
DYNAMIC STABILITY CONTROL
Terminal Signal Connected to Test condition Voltage (V) Action
A Ground (1) Ground part 1—Below 1.0•Inspect related harness
B Ground (2) Ground part 2—Below 1.0•Inspect related harness
CSolenoid valve
(power supply)Battery—B+•Inspect DSC HU/CM
•Inspect related harness
DPump motor
(power supply)Battery—B+•Inspect DSC HU/CM
•Inspect related harness
E
*—Check
connector—No need to
check•Inspect related harness
F
JLF wheel-speedLF wheel-speed
sensorVehicle is stopped 0 (AC)
•Inspect related harness
•Inspect wheel-speed
sensor •Inspect using the wave profile.
(See P–19 Inspection Using An
Oscilloscope (Reference))
SST (49 G066 004)
AQ
B
CDE
FG
HI
J DSC HU/CM HARNESS SIDE CONNECTOR
A
C E
H
K N Q
T
W Z AC AF
F I L O R U X
AA AD AG
G
J
M P S
V
Y AB AE AHB
DKN
T
WZ
AC
AFLO
RU
XAA
ADAGMP
SV
YAB
AEAH
A6E6920W009
Page 760 of 909
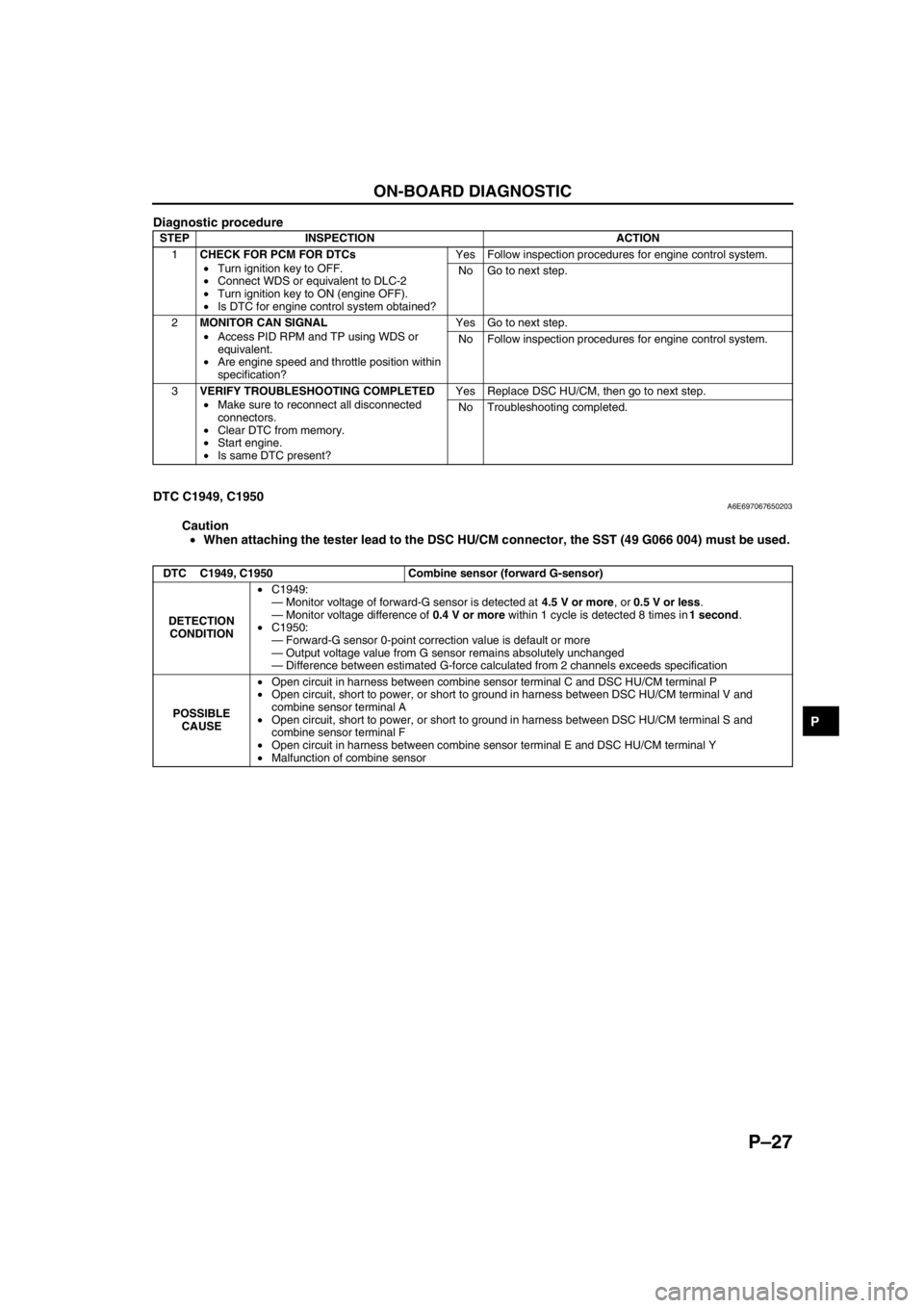
ON-BOARD DIAGNOSTIC
P–27
P
Diagnostic procedure
End Of Sie
DTC C1949, C1950A6E697067650203
Caution
•When attaching the tester lead to the DSC HU/CM connector, the SST (49 G066 004) must be used.
STEP INSPECTION ACTION
1CHECK FOR PCM FOR DTCs
•Turn ignition key to OFF.
•Connect WDS or equivalent to DLC-2
•Turn ignition key to ON (engine OFF).
•Is DTC for engine control system obtained?Yes Follow inspection procedures for engine control system.
No Go to next step.
2MONITOR CAN SIGNAL
•Access PID RPM and TP using WDS or
equivalent.
•Are engine speed and throttle position within
specification?Yes Go to next step.
No Follow inspection procedures for engine control system.
3VERIFY TROUBLESHOOTING COMPLETED
•Make sure to reconnect all disconnected
connectors.
•Clear DTC from memory.
•Start engine.
•Is same DTC present?Yes Replace DSC HU/CM, then go to next step.
No Troubleshooting completed.
DTC C1949, C1950 Combine sensor (forward G-sensor)
DETECTION
CONDITION•C1949:
—Monitor voltage of forward-G sensor is detected at 4.5 V or more, or 0.5 V or less.
—Monitor voltage difference of 0.4 V or more within 1 cycle is detected 8 times in 1 second.
•C1950:
—Forward-G sensor 0-point correction value is default or more
—Output voltage value from G sensor remains absolutely unchanged
—Difference between estimated G-force calculated from 2 channels exceeds specification
POSSIBLE
CAUSE•Open circuit in harness between combine sensor terminal C and DSC HU/CM terminal P
•Open circuit, short to power, or short to ground in harness between DSC HU/CM terminal V and
combine sensor terminal A
•Open circuit, short to power, or short to ground in harness between DSC HU/CM terminal S and
combine sensor terminal F
•Open circuit in harness between combine sensor terminal E and DSC HU/CM terminal Y
•Malfunction of combine sensor
Page 762 of 909
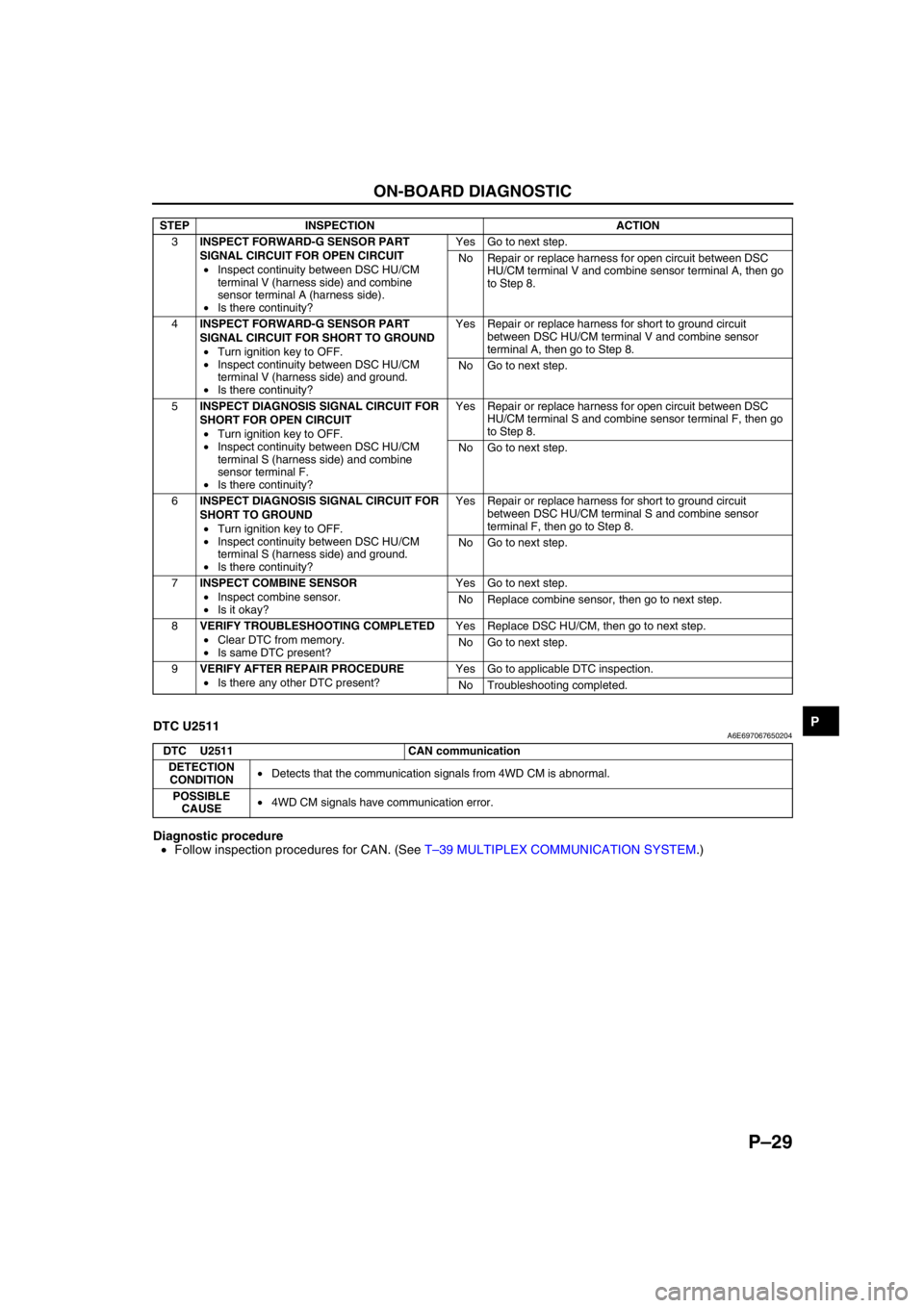
ON-BOARD DIAGNOSTIC
P–29
PEnd Of Sie
DTC U2511A6E697067650204
Diagnostic procedure
•Follow inspection procedures for CAN. (See T–39 MULTIPLEX COMMUNICATION SYSTEM.)
End Of Sie
3INSPECT FORWARD-G SENSOR PART
SIGNAL CIRCUIT FOR OPEN CIRCUIT
•Inspect continuity between DSC HU/CM
terminal V (harness side) and combine
sensor terminal A (harness side).
•Is there continuity?Yes Go to next step.
No Repair or replace harness for open circuit between DSC
HU/CM terminal V and combine sensor terminal A, then go
to Step 8.
4INSPECT FORWARD-G SENSOR PART
SIGNAL CIRCUIT FOR SHORT TO GROUND
•Turn ignition key to OFF.
•Inspect continuity between DSC HU/CM
terminal V (harness side) and ground.
•Is there continuity?Yes Repair or replace harness for short to ground circuit
between DSC HU/CM terminal V and combine sensor
terminal A, then go to Step 8.
No Go to next step.
5INSPECT DIAGNOSIS SIGNAL CIRCUIT FOR
SHORT FOR OPEN CIRCUIT
•Turn ignition key to OFF.
•Inspect continuity between DSC HU/CM
terminal S (harness side) and combine
sensor terminal F.
•Is there continuity?Yes Repair or replace harness for open circuit between DSC
HU/CM terminal S and combine sensor terminal F, then go
to Step 8.
No Go to next step.
6INSPECT DIAGNOSIS SIGNAL CIRCUIT FOR
SHORT TO GROUND
•Turn ignition key to OFF.
•Inspect continuity between DSC HU/CM
terminal S (harness side) and ground.
•Is there continuity?Yes Repair or replace harness for short to ground circuit
between DSC HU/CM terminal S and combine sensor
terminal F, then go to Step 8.
No Go to next step.
7INSPECT COMBINE SENSOR
•Inspect combine sensor.
•Is it okay?Yes Go to next step.
No Replace combine sensor, then go to next step.
8VERIFY TROUBLESHOOTING COMPLETED
•Clear DTC from memory.
•Is same DTC present?Yes Replace DSC HU/CM, then go to next step.
No Go to next step.
9VERIFY AFTER REPAIR PROCEDURE
•Is there any other DTC present?Yes Go to applicable DTC inspection.
No Troubleshooting completed. STEP INSPECTION ACTION
DTC U2511 CAN communication
DETECTION
CONDITION•Detects that the communication signals from 4WD CM is abnormal.
POSSIBLE
CAUSE•4WD CM signals have communication error.
Page 844 of 909
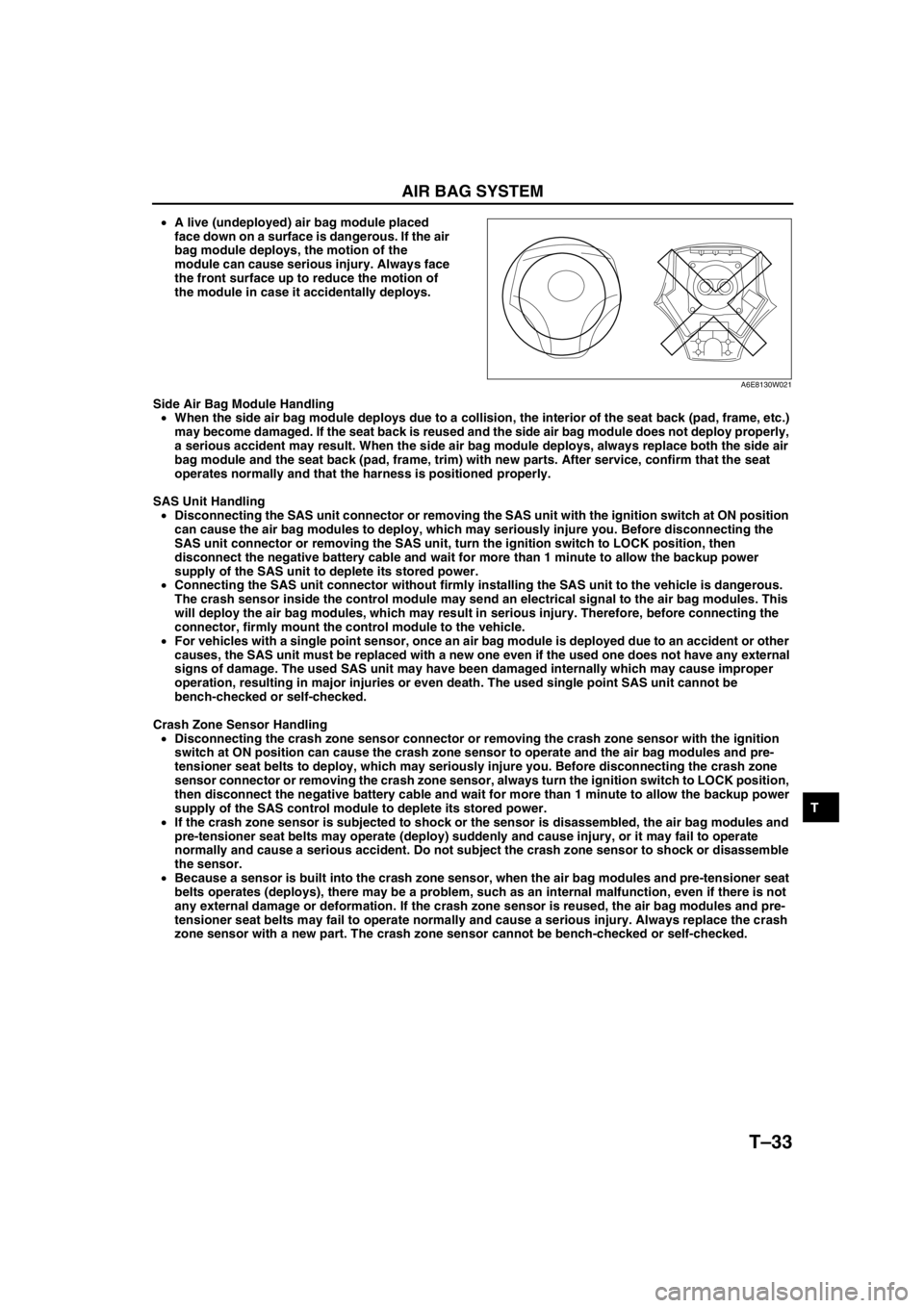
AIR BAG SYSTEM
T–33
T
•A live (undeployed) air bag module placed
face down on a surface is dangerous. If the air
bag module deploys, the motion of the
module can cause serious injury. Always face
the front surface up to reduce the motion of
the module in case it accidentally deploys.
Side Air Bag Module Handling
•When the side air bag module deploys due to a collision, the interior of the seat back (pad, frame, etc.)
may become damaged. If the seat back is reused and the side air bag module does not deploy properly,
a serious accident may result. When the side air bag module deploys, always replace both the side air
bag module and the seat back (pad, frame, trim) with new parts. After service, confirm that the seat
operates normally and that the harness is positioned properly.
SAS Unit Handling
•Disconnecting the SAS unit connector or removing the SAS unit with the ignition switch at ON position
can cause the air bag modules to deploy, which may seriously injure you. Before disconnecting the
SAS unit connector or removing the SAS unit, turn the ignition switch to LOCK position, then
disconnect the negative battery cable and wait for more than 1 minute to allow the backup power
supply of the SAS unit to deplete its stored power.
•Connecting the SAS unit connector without firmly installing the SAS unit to the vehicle is dangerous.
The crash sensor inside the control module may send an electrical signal to the air bag modules. This
will deploy the air bag modules, which may result in serious injury. Therefore, before connecting the
connector, firmly mount the control module to the vehicle.
•For vehicles with a single point sensor, once an air bag module is deployed due to an accident or other
causes, the SAS unit must be replaced with a new one even if the used one does not have any external
signs of damage. The used SAS unit may have been damaged internally which may cause improper
operation, resulting in major injuries or even death. The used single point SAS unit cannot be
bench-checked or self-checked.
Crash Zone Sensor Handling
•Disconnecting the crash zone sensor connector or removing the crash zone sensor with the ignition
switch at ON position can cause the crash zone sensor to operate and the air bag modules and pre-
tensioner seat belts to deploy, which may seriously injure you. Before disconnecting the crash zone
sensor connector or removing the crash zone sensor, always turn the ignition switch to LOCK position,
then disconnect the negative battery cable and wait for more than 1 minute to allow the backup power
supply of the SAS control module to deplete its stored power.
•If the crash zone sensor is subjected to shock or the sensor is disassembled, the air bag modules and
pre-tensioner seat belts may operate (deploy) suddenly and cause injury, or it may fail to operate
normally and cause a serious accident. Do not subject the crash zone sensor to shock or disassemble
the sensor.
•Because a sensor is built into the crash zone sensor, when the air bag modules and pre-tensioner seat
belts operates (deploys), there may be a problem, such as an internal malfunction, even if there is not
any external damage or deformation. If the crash zone sensor is reused, the air bag modules and pre-
tensioner seat belts may fail to operate normally and cause a serious injury. Always replace the crash
zone sensor with a new part. The crash zone sensor cannot be bench-checked or self-checked.
A6E8130W021
Page 879 of 909
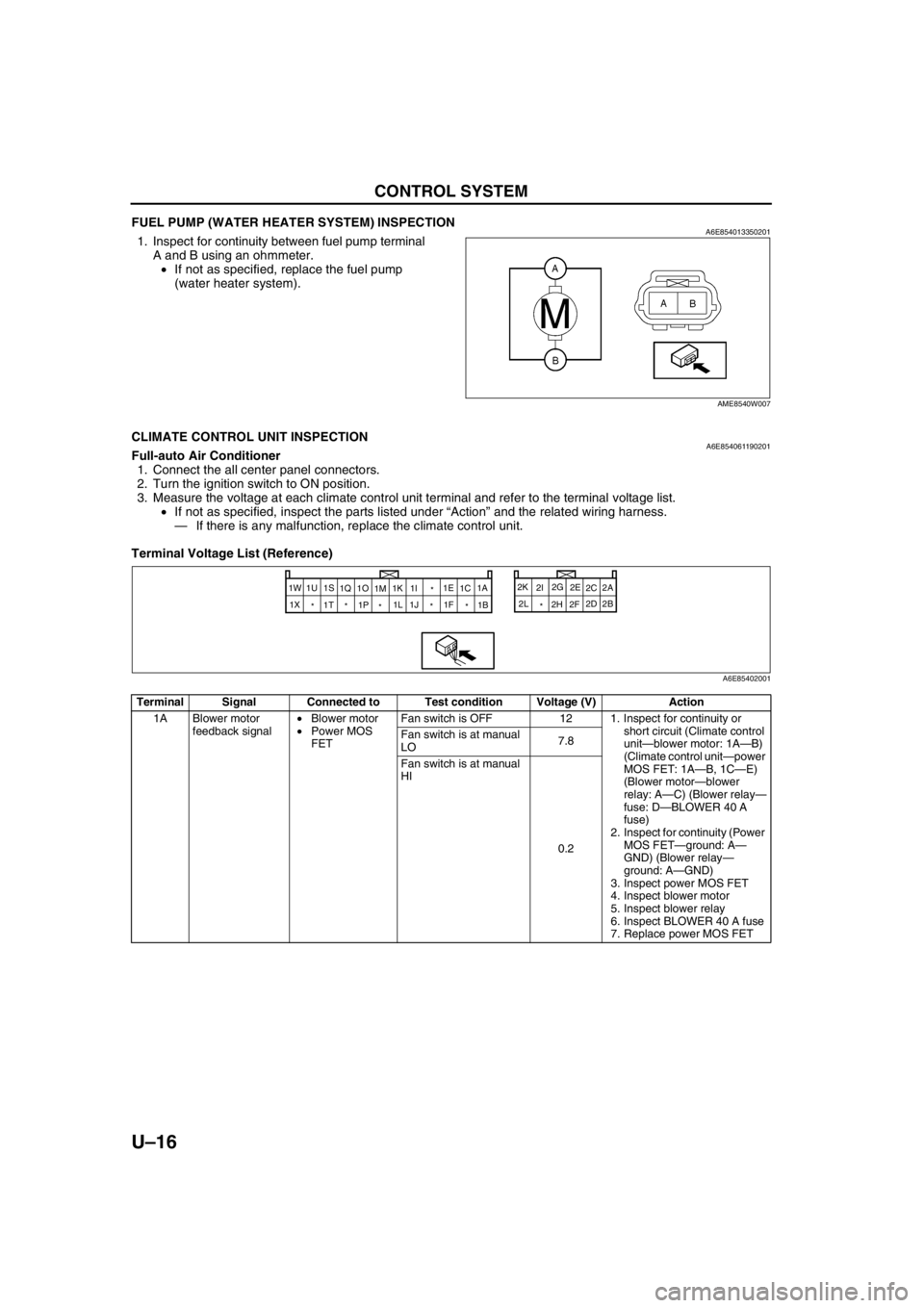
U–16
CONTROL SYSTEM
FUEL PUMP (WATER HEATER SYSTEM) INSPECTIONA6E8540133502011. Inspect for continuity between fuel pump terminal
A and B using an ohmmeter.
•If not as specified, replace the fuel pump
(water heater system).
End Of Sie
CLIMATE CONTROL UNIT INSPECTIONA6E854061190201Full-auto Air Conditioner
1. Connect the all center panel connectors.
2. Turn the ignition switch to ON position.
3. Measure the voltage at each climate control unit terminal and refer to the terminal voltage list.
•If not as specified, inspect the parts listed under “Action” and the related wiring harness.
—If there is any malfunction, replace the climate control unit.
Terminal Voltage List (Reference)
AME8540W007
Terminal Signal Connected to Test condition Voltage (V) Action
1A Blower motor
feedback signal•Blower motor
•Power MOS
FETFan switch is OFF 12 1. Inspect for continuity or
short circuit (Climate control
unit—blower motor: 1A—B)
(Climate control unit—power
MOS FET: 1A—B, 1C—E)
(Blower motor—blower
relay: A—C) (Blower relay—
fuse: D—BLOWER 40 A
fuse)
2. Inspect for continuity (Power
MOS FET—ground: A—
GND) (Blower relay—
ground: A—GND)
3. Inspect power MOS FET
4. Inspect blower motor
5. Inspect blower relay
6. Inspect BLOWER 40 A fuse
7. Replace power MOS FET Fan switch is at manual
LO7.8
Fan switch is at manual
HI
0.2
2A
1W
2B 2C
2D 2E
2F 2G
2H 2I 2K
2L
* 1A
1B
* *
* *
* 1X1C 1E
1F * 1I
1K
1M 1O
1P 1Q 1S
1T 1U
1J 1L
A6E85402001