check engine MAZDA 626 1987 Owner's Manual
[x] Cancel search | Manufacturer: MAZDA, Model Year: 1987, Model line: 626, Model: MAZDA 626 1987Pages: 1865, PDF Size: 94.35 MB
Page 139 of 1865
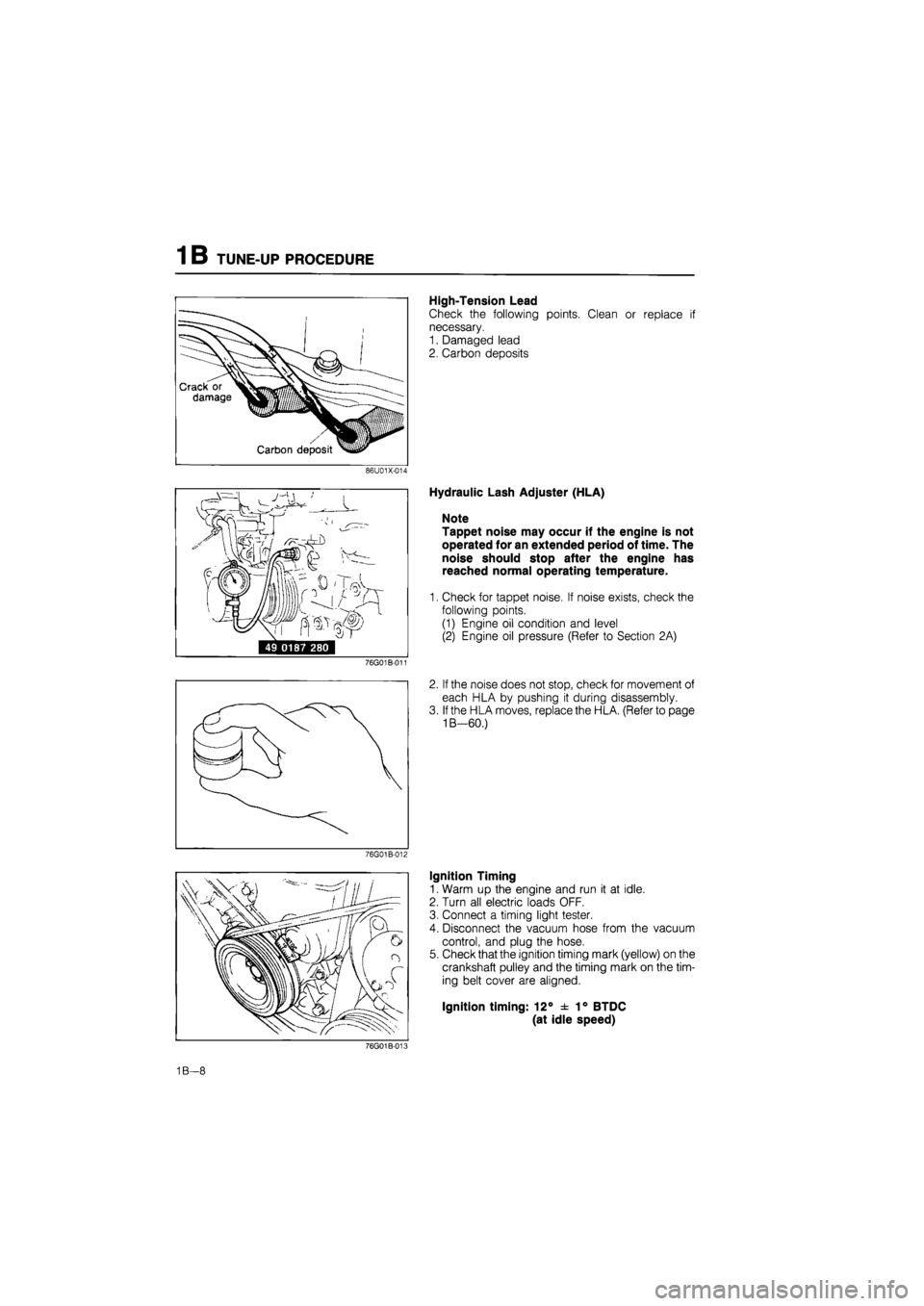
TUNE-UP PROCEDURE 1 B
High-Tension Lead
Check the following points. Clean or replace if
necessary.
1. Damaged lead
2. Carbon deposits
86U01X-014
i^rrr ' /
49 0187 280
76G01B-011
76G01B-012
Hydraulic Lash Adjuster (HLA)
Note
Tappet noise may occur if the engine is not
operated for an extended period of time. The
noise should stop after the engine has
reached normal operating temperature.
1. Check for tappet noise. If noise exists, check the
following points.
(1) Engine oil condition and level
(2) Engine oil pressure (Refer to Section 2A)
2. If the noise does not stop, check for movement of
each HLA by pushing it during disassembly.
3. If the HLA moves, replace the HLA. (Refer to page
1B—60.)
Ignition Timing
1. Warm up the engine and run it at idle.
2. Turn all electric loads OFF.
3. Connect a timing light tester.
4. Disconnect the vacuum hose from the vacuum
control, and plug the hose.
5. Check that the ignition timing mark (yellow) on the
crankshaft pulley and the timing mark on the tim-
ing belt cover are aligned.
Ignition timing: 12° ± 1° BTDC
(at idle speed)
76G01B-008
1B—8
Page 140 of 1865
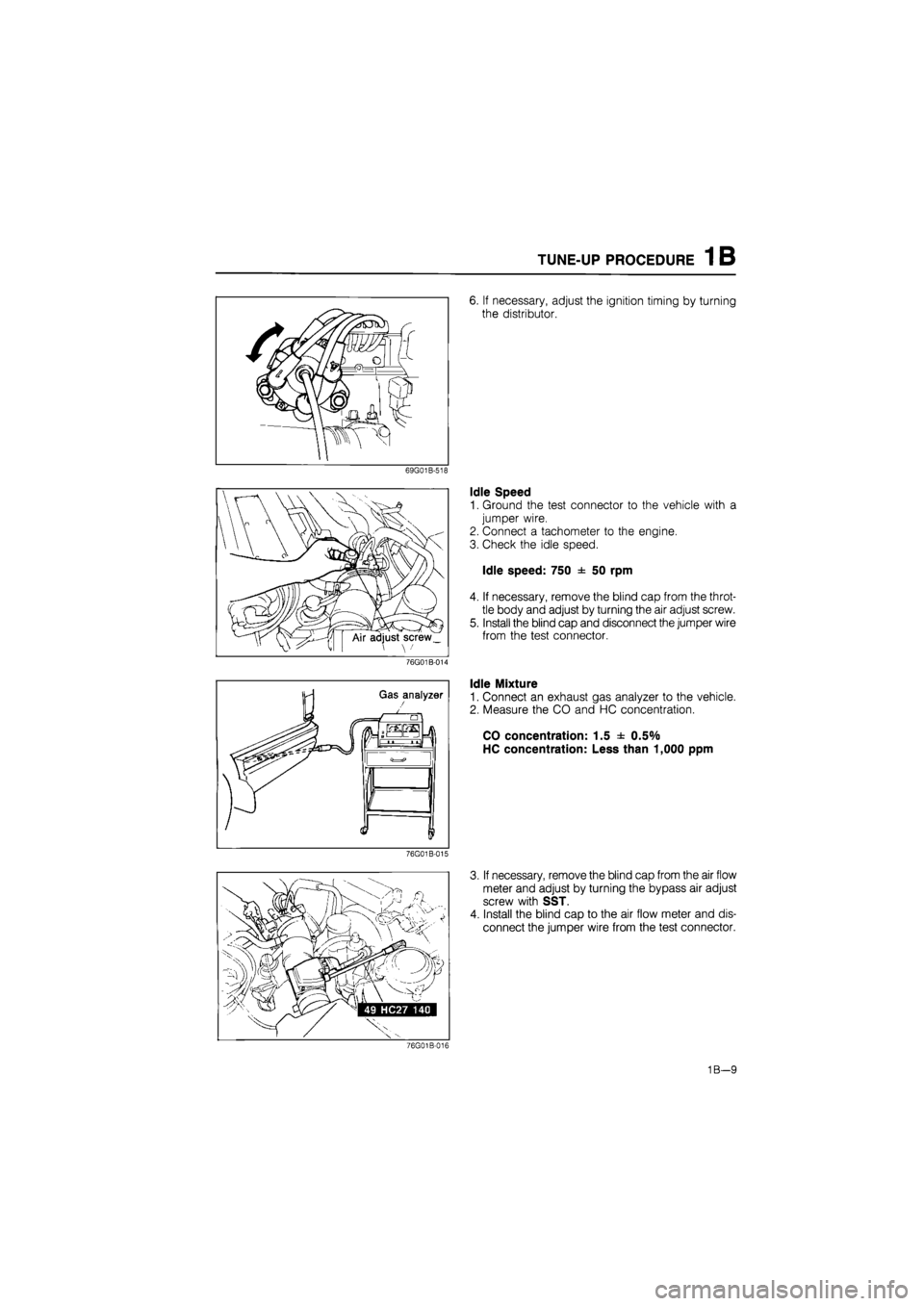
TUNE-UP PROCEDURE 1 B
76G01B-015
6. If necessary, adjust the ignition timing by turning
the distributor.
Idle Speed
1. Ground the test connector to the vehicle with a
jumper wire.
2. Connect a tachometer to the engine.
3. Check the idle speed.
Idle speed: 750 ± 50 rpm
4. If necessary, remove the blind cap from the throt-
tle body and adjust by turning the air adjust screw.
5. Install the blind cap and disconnect the jumper wire
from the test connector.
Idle Mixture
1. Connect an exhaust gas analyzer to the vehicle.
2. Measure the CO and HC concentration.
CO concentration: 1.5 ± 0.5%
HC concentration: Less than 1,000 ppm
3. If necessary, remove the blind cap from the air flow
meter and adjust by turning the bypass air adjust
screw with SST.
4. Install the blind cap to the air flow meter and dis-
connect the jumper wire from the test connector.
76G01B-016
1B—9
Page 141 of 1865
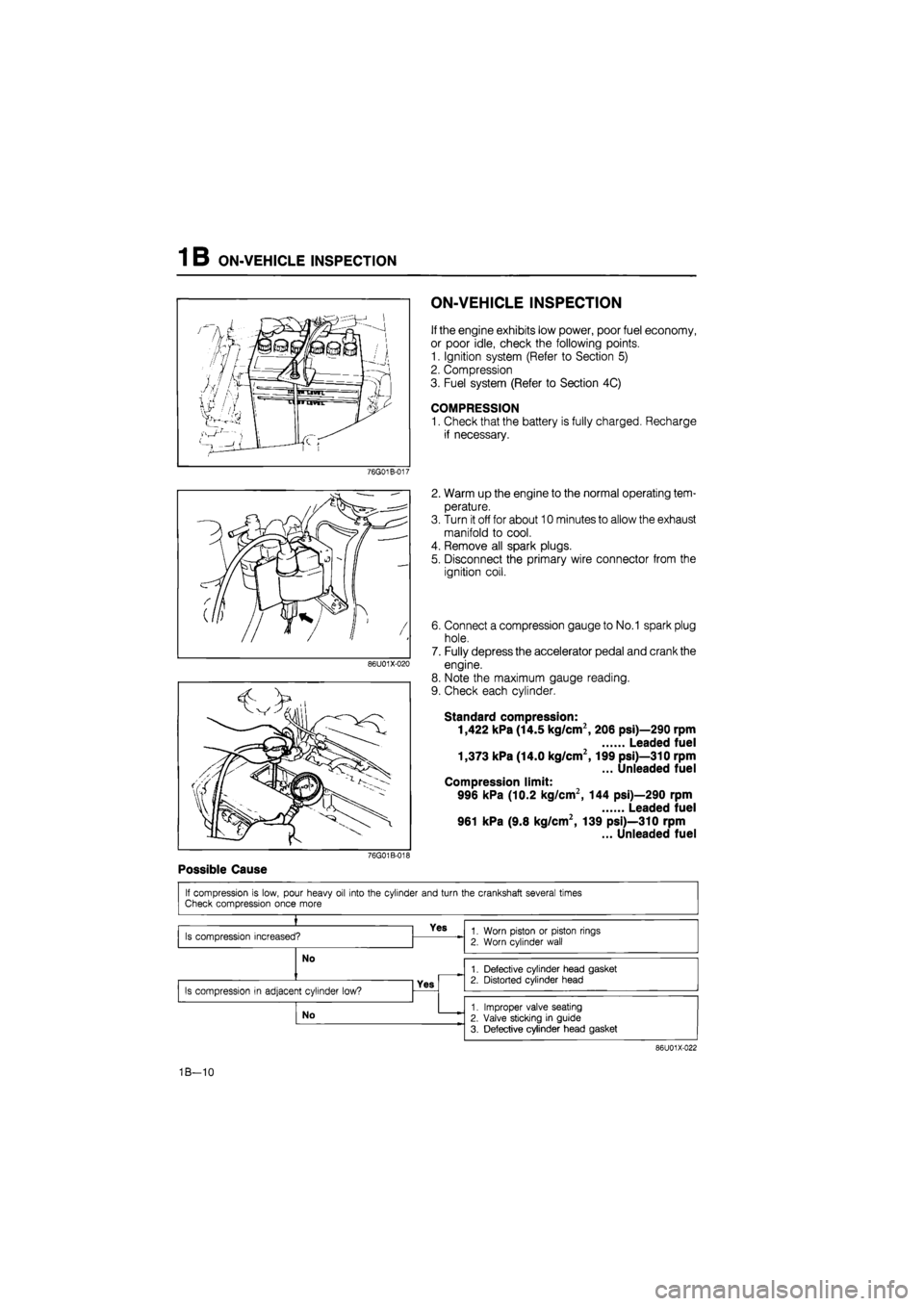
1 B ON-VEHICLE INSPECTION
76G01B-017
86U01X-020
76G01B-018
Possible Cause
ON-VEHICLE INSPECTION
If the engine exhibits low power, poor fuel economy,
or poor idle, check the following points.
1. Ignition system (Refer to Section 5)
2. Compression
3. Fuel system (Refer to Section 4C)
COMPRESSION
1. Check that the battery is fully charged. Recharge
if necessary.
2. Warm up the engine to the normal operating tem-
perature.
3. Turn it off for about 10 minutes to allow the exhaust
manifold to cool.
4. Remove all spark plugs.
5. Disconnect the primary wire connector from the
ignition coil.
6. Connect a compression gauge to No.1 spark plug
hole.
7. Fully depress the accelerator pedal and crank the
engine.
8. Note the maximum gauge reading.
9. Check each cylinder.
Standard compression:
1,422 kPa (14.5 kg/cm2, 206 psi)—290 rpm
Leaded fuel
1,373 kPa (14.0 kg/cm2,199 psi)—310 rpm
... Unleaded fuel
Compression limit:
996 kPa (10.2 kg/cm2, 144 psi)—290 rpm
Leaded fuel
961 kPa (9.8 kg/cm2, 139 psi)—310 rpm
... Unleaded fuel
If compression is low, pour heavy oil into the cylinder and turn the crankshaft several times Check compression once more
»
Is compression increased? Yes 1. Worn piston or piston rings
2. Worn cylinder wall
No
1. Worn piston or piston rings
2. Worn cylinder wall
No 1. Defective cylinder head gasket 2. Distorted cylinder head
Is compression in adjacent cylinder low? Yes
1. Defective cylinder head gasket 2. Distorted cylinder head
Is compression in adjacent cylinder low?
No 1. Improper valve seating
2. Valve sticking in guide
3. Defective cylinder head gasket
86U01X-022
1B—10
Page 146 of 1865
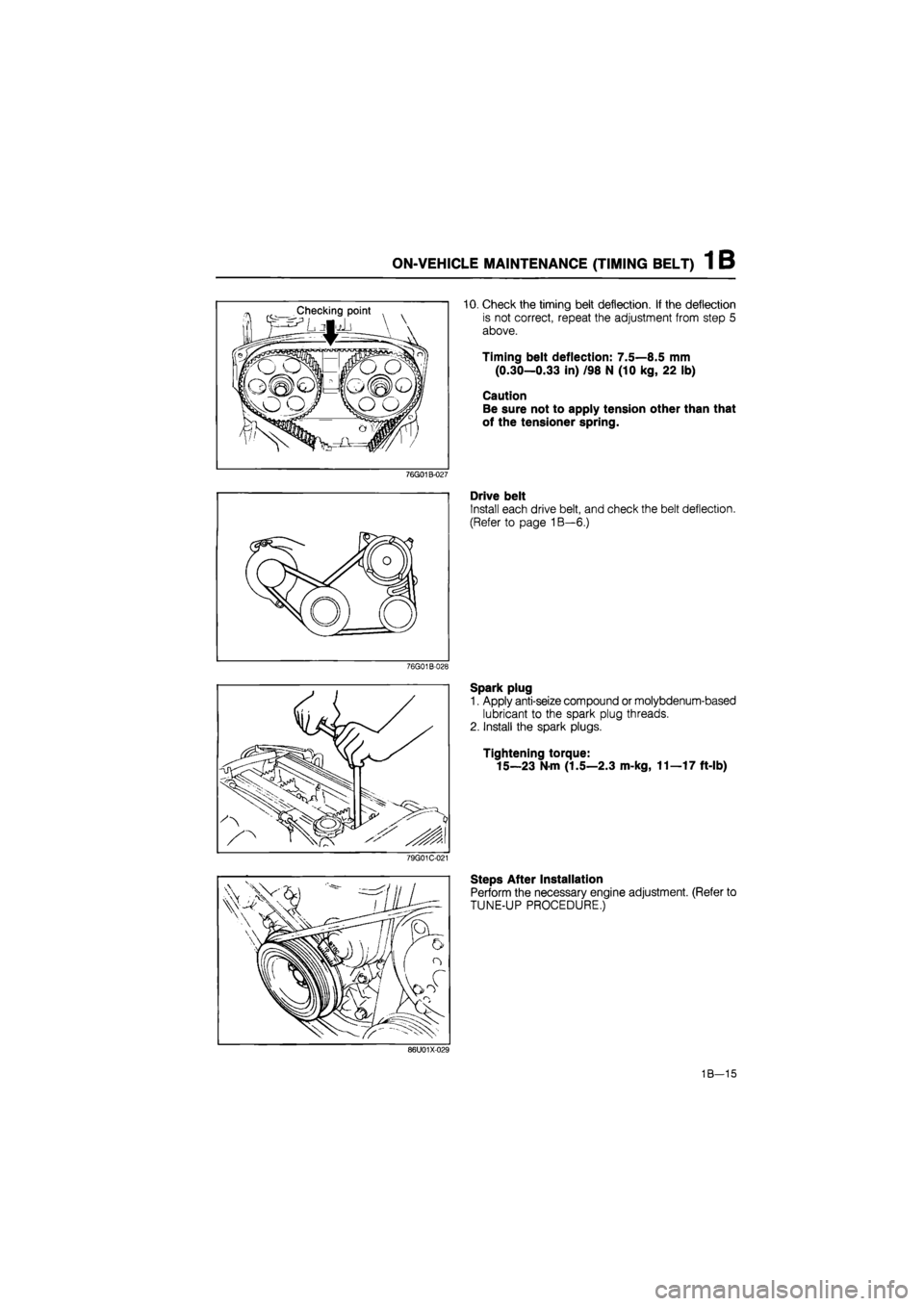
ON-VEHICLE MAINTENANCE (TIMING BELT) 1 B
10. Check the timing belt deflection. If the deflection
is not correct, repeat the adjustment from step 5
above.
Timing belt deflection: 7.5—8.5 mm
(0.30—0.33 in) /98 N (10 kg, 22 lb)
Caution
Be sure not to apply tension other than that
of the tensioner spring.
76G01B-027
Drive belt
Install each drive belt, and check the belt deflection.
(Refer to page 1B—6.)
76G01B-028
Spark plug
1. Apply anti-seize compound or molybdenum-based
lubricant to the spark plug threads.
2. Install the spark plugs.
Tightening torque:
15—23
N
m (1.5—2.3 m-kg, 11—17 ft-lb)
79G01C-021
Steps After Installation
Perform the necessary engine adjustment. (Refer to
TUNE-UP PROCEDURE.)
86U01X-029
1B—15
Page 180 of 1865
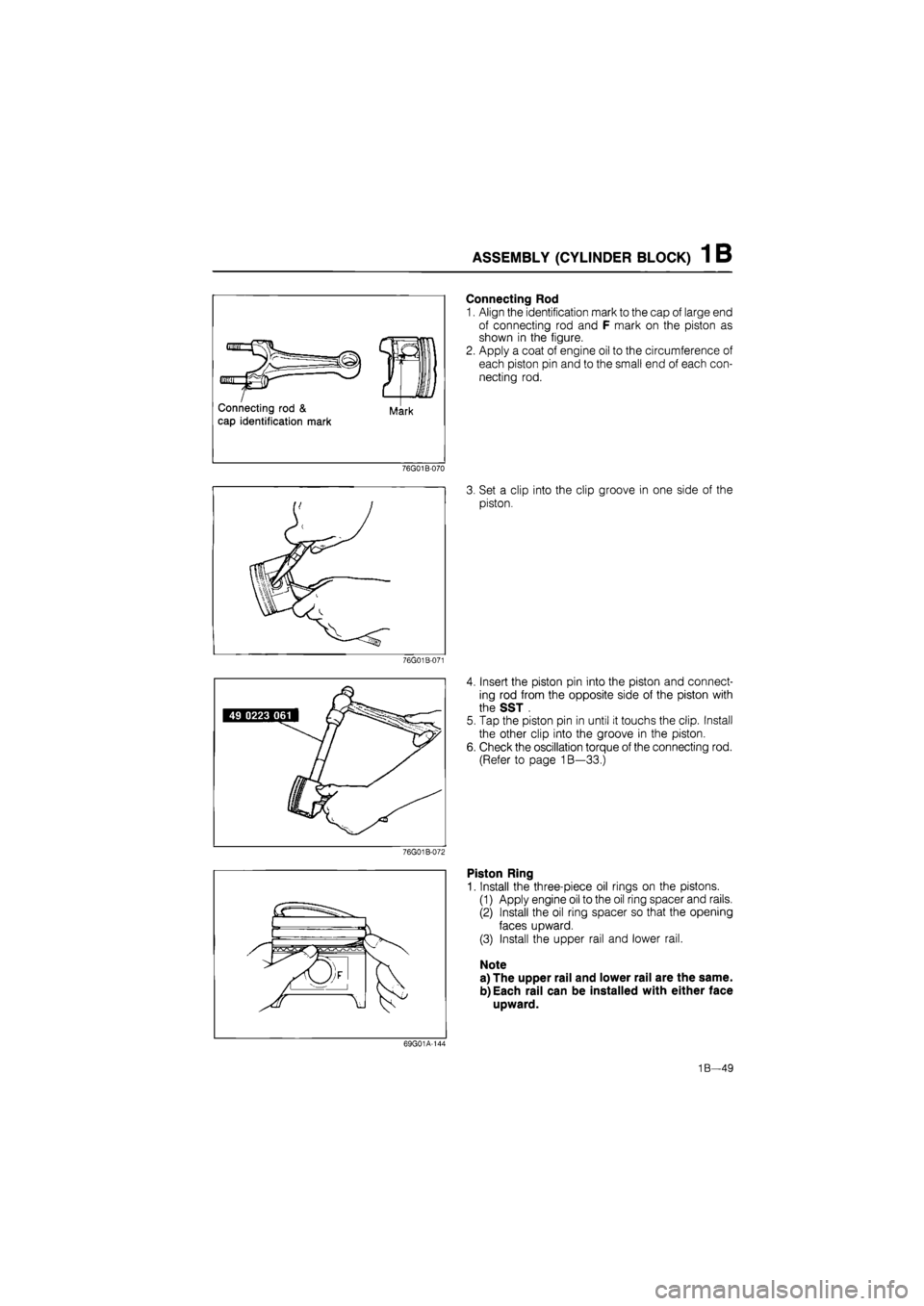
ASSEMBLY (CYLINDER BLOCK) 1 B
76G01B-070
76G01B-071
Connecting Rod
1. Align the identification mark to the cap of large end
of connecting rod and F mark on the piston as
shown in the figure.
2. Apply a coat of engine oil to the circumference of
each piston pin and to the small end of each con-
necting rod.
3. Set a clip into the clip groove in one side of the
piston.
4. Insert the piston pin into the piston and connect-
ing rod from the opposite side of the piston with
the SST .
5. Tap the piston pin in until it touchs the clip. Install
the other clip into the groove in the piston.
6. Check the oscillation torque of the connecting rod.
(Refer to page 1B—33.)
Piston Ring
1. Install the three-piece oil rings on the pistons.
(1) Apply engine oil to the oil ring spacer and rails.
(2) Install the oil ring spacer so that the opening
faces upward.
(3) Install the upper rail and lower rail.
Note
a) The upper rail and lower rail are the same.
b)Each rail can be installed with either face
upward.
69G01A-144
1B—49
Page 181 of 1865
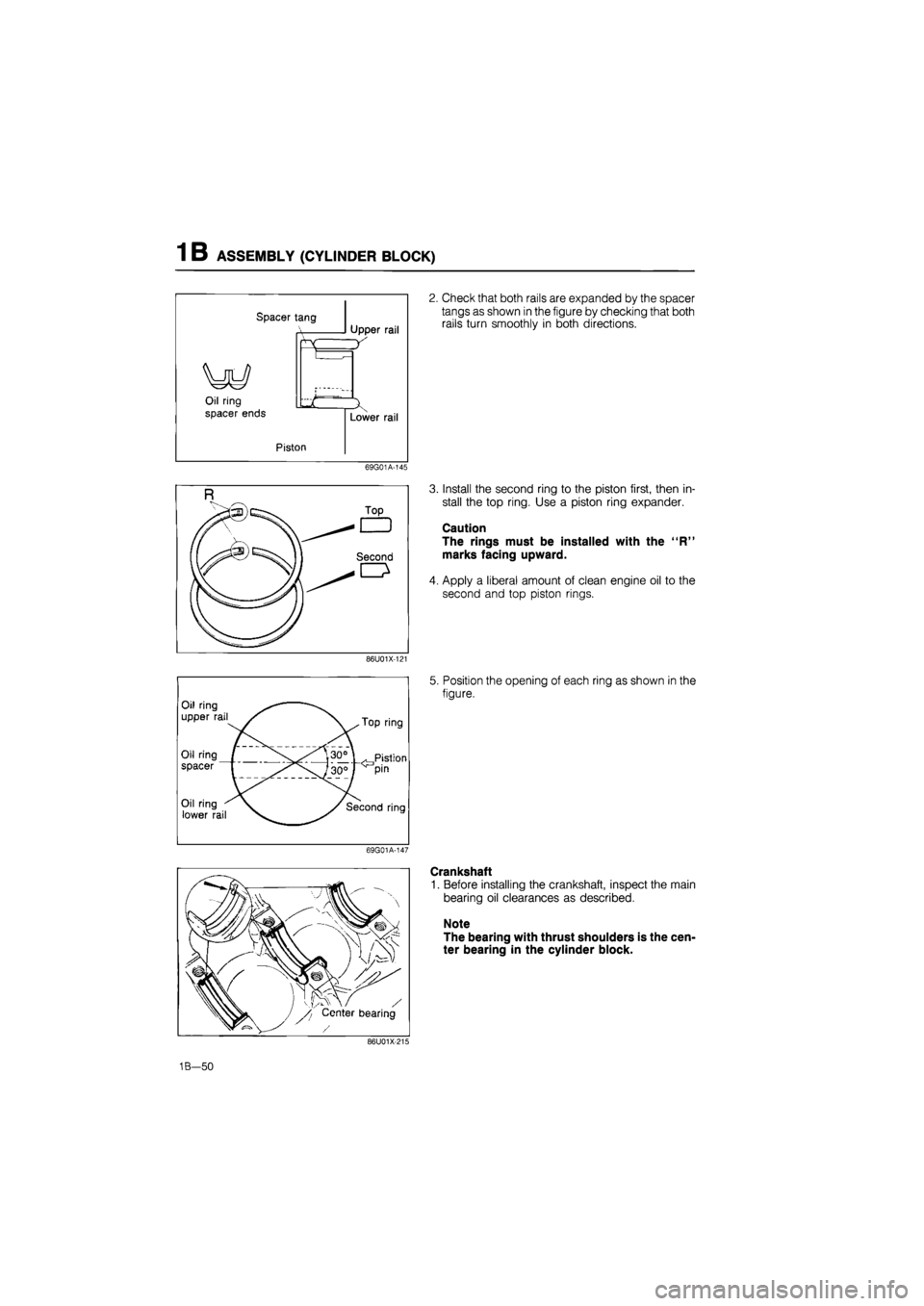
1 B ASSEMBLY (CYLINDER BLOCK)
Spacer tang
Oil ring
spacer ends
Upper rail
Piston
Lower rail
69G01A-145
86U01X-121
Oil ring —
upper rail / N. ^ Top ring
Oil ring I ^_t30° L^Pistion
T Pin spacer I ^_t30° L^Pistion
T Pin
Oil ring
lower rail N. j/ Second ring
69G01A-147
2. Check that both rails are expanded by the spacer
tangs as shown in the figure by checking that both
rails turn smoothly in both directions.
3. Install the second ring to the piston first, then in-
stall the top ring. Use a piston ring expander.
Caution
The rings must be installed with the "R"
marks facing upward.
4. Apply a liberal amount of clean engine oil to the
second and top piston rings.
5. Position the opening of each ring as shown in the
figure.
Crankshaft
1. Before installing the crankshaft, inspect the main
bearing oil clearances as described.
Note
The bearing with thrust shoulders is the cen-
ter bearing in the cylinder block.
86U01X-136
1B—50
Page 183 of 1865
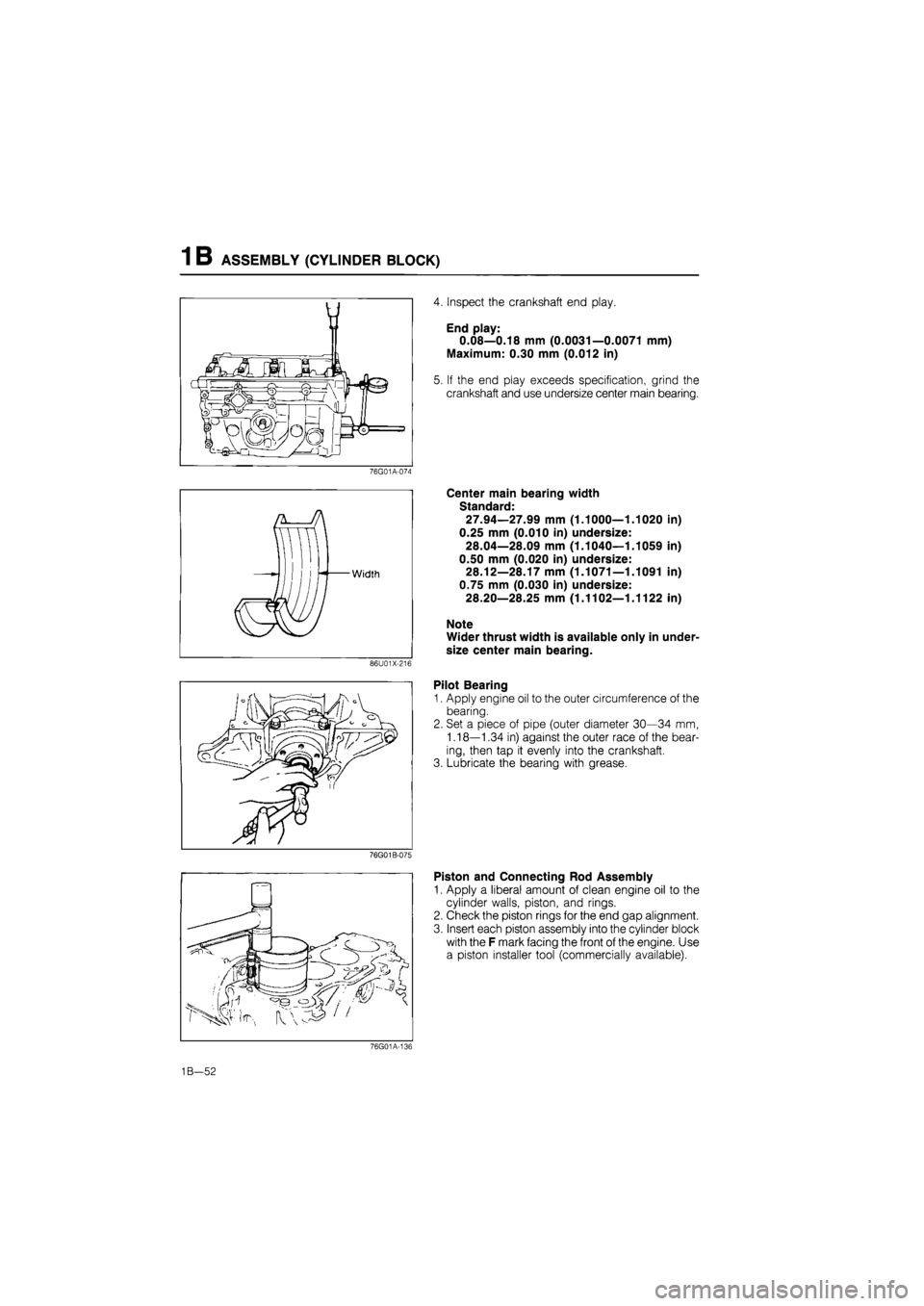
1 B ASSEMBLY (CYLINDER BLOCK)
76G01A-074
86U01X-216
76G01 B-075
4. Inspect the crankshaft end play.
End play:
0.08—0.18 mm (0.0031—0.0071 mm)
Maximum: 0.30 mm (0.012 in)
5. If the end play exceeds specification, grind the
crankshaft and use undersize center main bearing.
Center main bearing width
Standard:
27.94—27.99 mm (1.1000—1.1020 in)
0.25 mm (0.010 in) undersize:
28.04—28.09 mm (1.1040—1.1059 in)
0.50 mm (0.020 in) undersize:
28.12—28.17 mm (1.1071—1.1091 in)
0.75 mm (0.030 in) undersize:
28.20—28.25 mm (1.1102—1.1122 in)
Note
Wider thrust width is available only in under-
size center main bearing.
Pilot Bearing
1. Apply engine oil to the outer circumference of the
bearing.
2. Set a piece of pipe (outer diameter 30—34 mm,
1.18—1.34 in) against the outer race of the bear-
ing, then tap it evenly into the crankshaft.
3. Lubricate the bearing with grease.
Piston and Connecting Rod Assembly
1. Apply a liberal amount of clean engine oil to the
cylinder walls, piston, and rings.
2. Check the piston rings for the end gap alignment.
3. Insert each piston assembly into the cylinder block
with the F mark facing the front of the engine. Use
a piston installer tool (commercially available).
76G01A-136
1B—52
Page 184 of 1865
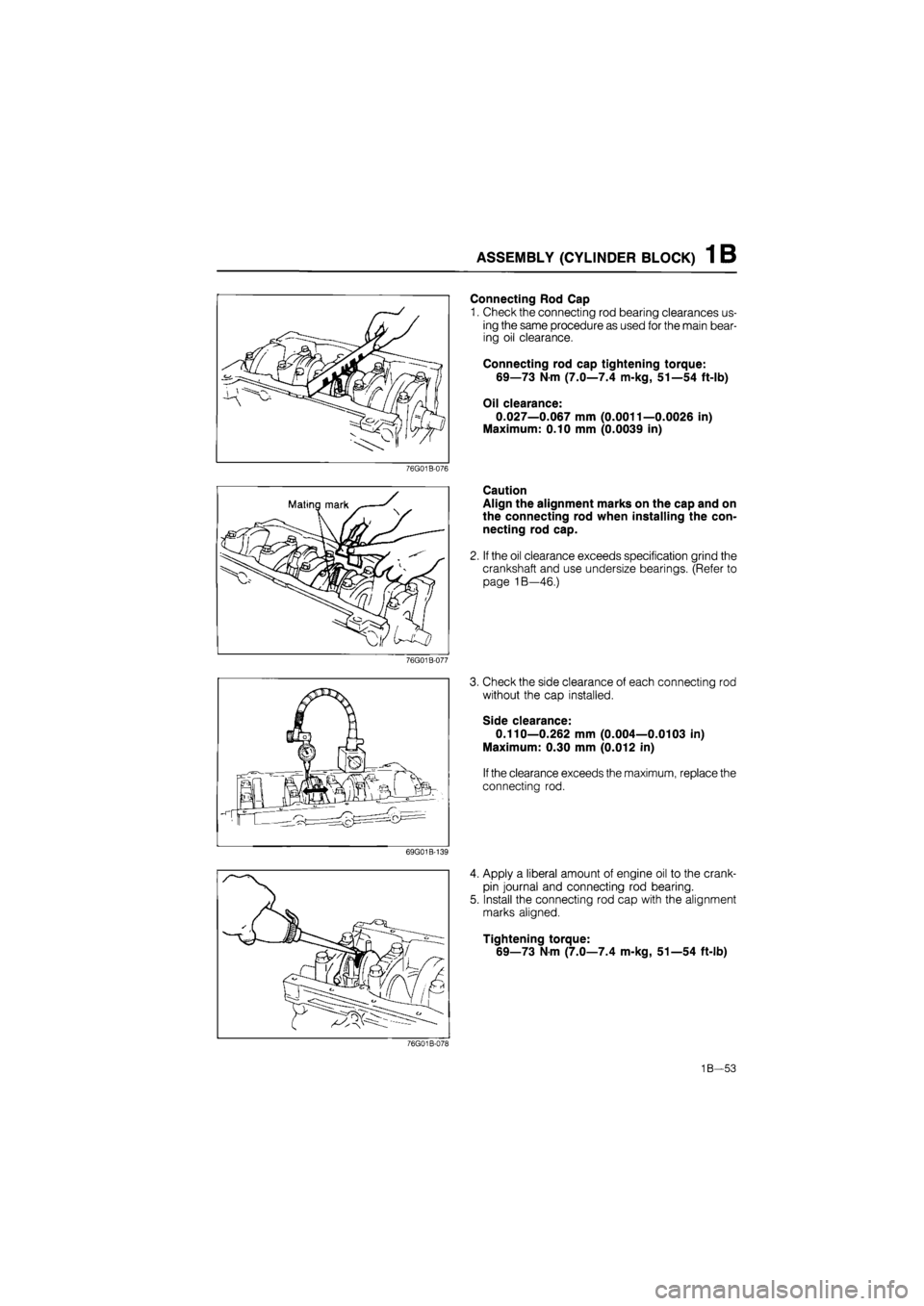
ASSEMBLY (CYLINDER BLOCK) 1 B
Connecting Rod Cap
1. Check the connecting rod bearing clearances us-
ing the same procedure as used for the main bear-
ing oil clearance.
Connecting rod cap tightening torque:
69—73 Nm (7.0—7.4 m-kg, 51—54 ft-lb)
Oil clearance:
0.027—0.067 mm (0.0011—0.0026 in)
Maximum: 0.10 mm (0.0039 in)
76G01B-076
Caution
Align the alignment marks on the cap and on
the connecting rod when installing the con-
necting rod cap.
2. If the oil clearance exceeds specification grind the
crankshaft and use undersize bearings. (Refer to
page 1B—46.)
76G01B-077
3. Check the side clearance of each connecting rod
without the cap installed.
Side clearance:
0.110—0.262 mm (0.004—0.0103 in)
Maximum: 0.30 mm (0.012 in)
If the clearance exceeds the maximum, replace the
connecting rod.
69G01B-139
4. Apply a liberal amount of engine oil to the crank-
pin journal and connecting rod bearing.
5. Install the connecting rod cap with the alignment
marks aligned.
Tightening torque:
69—73 Nm (7.0—7.4 m-kg, 51—54 ft-lb)
76G01B-078
1B—53
Page 191 of 1865
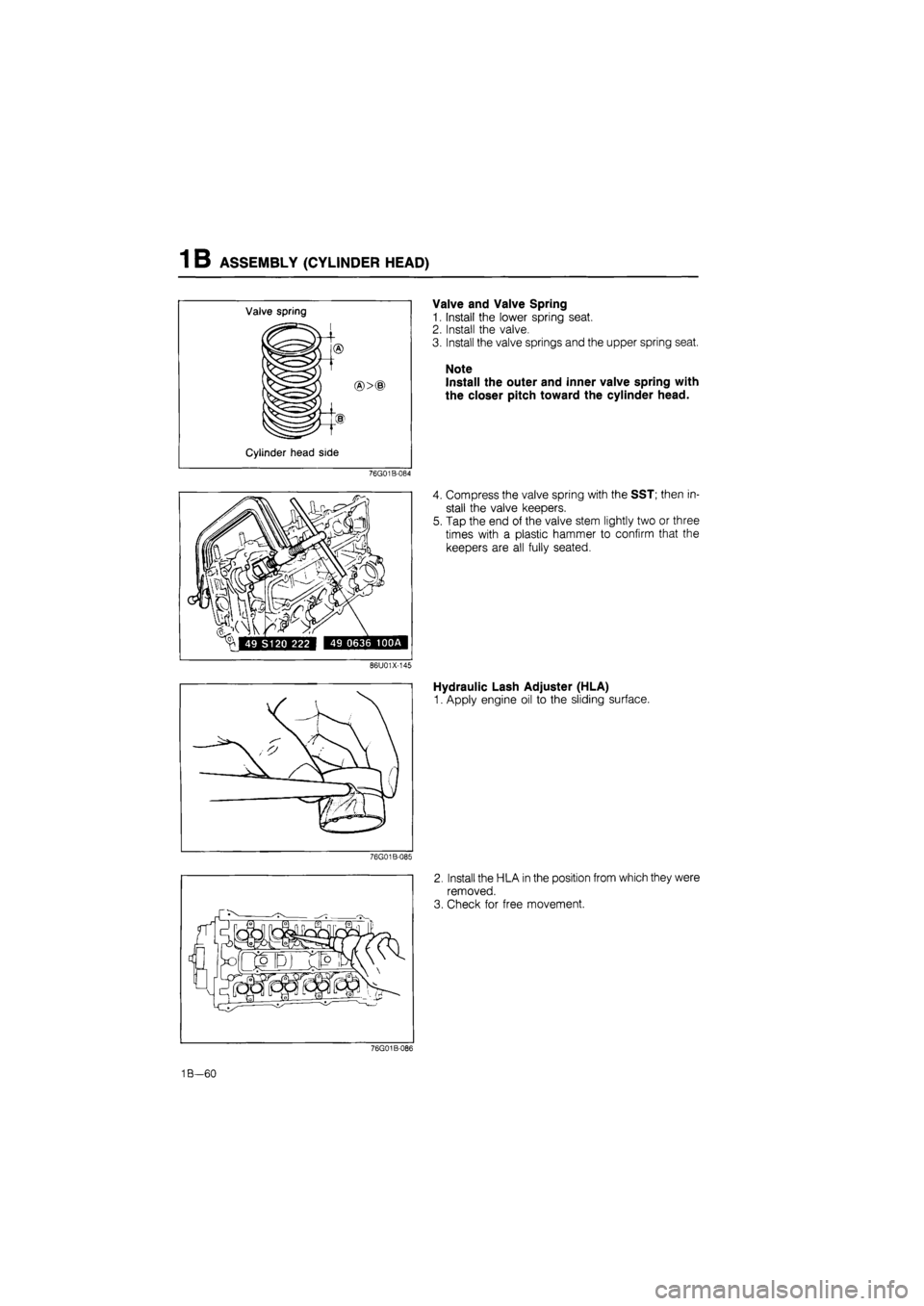
1 B ASSEMBLY (CYLINDER HEAD)
Valve spring
®>®
Cylinder head side
76G01B-084
86U01X-145
76G01B-085
Valve and Valve Spring
1. Install the lower spring seat.
2. Install the valve.
3. Install the valve springs and the upper spring seat.
Note
Install the outer and inner valve spring with
the closer pitch toward the cylinder head.
4. Compress the valve spring with the SST; then in-
stall the valve keepers.
5. Tap the end of the valve stem lightly two or three
times with a plastic hammer to confirm that the
keepers are all fully seated.
Hydraulic Lash Adjuster (HLA)
1. Apply engine oil to the sliding surface.
2. Install the HLA in the position from which they were
removed.
3. Check for free movement.
76G01B-086
1B—60
Page 212 of 1865
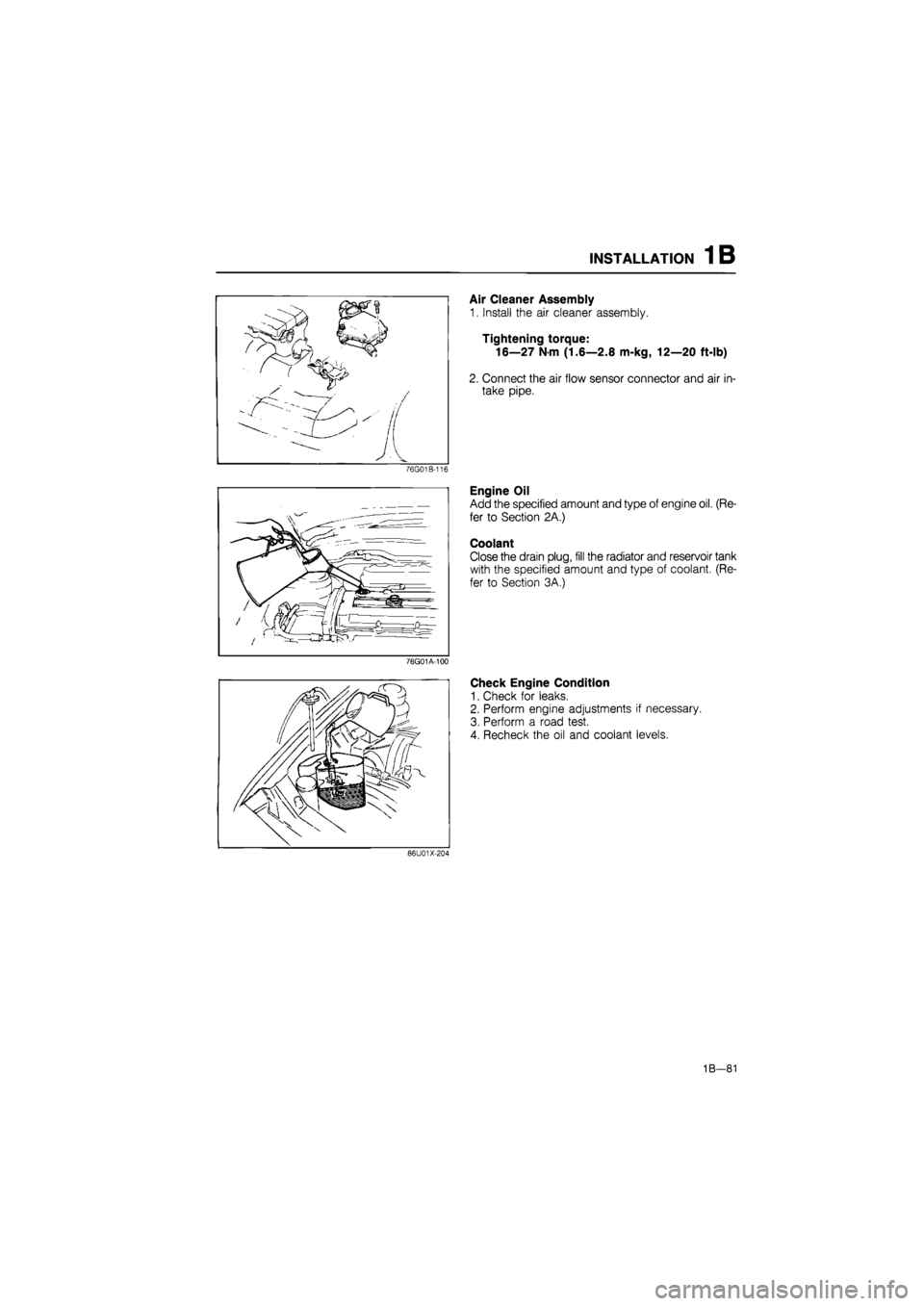
INSTALLATION 1B
76G01A-100
Air Cleaner Assembly
1. Install the air cleaner assembly.
Tightening torque:
16—27
N
m (1.6—2.8 m-kg, 12—20 ft-lb)
2. Connect the air flow sensor connector and air in-
take pipe.
Engine Oil
Add the specified amount and type of engine oil. (Re-
fer to Section 2A.)
Coolant
Close the drain plug, fill the radiator and reservoir tank
with the specified amount and type of coolant. (Re-
fer to Section 3A.)
Check Engine Condition
1. Check for leaks.
2. Perform engine adjustments if necessary.
3. Perform a road test.
4. Recheck the oil and coolant levels.
86U01X-204
1B-81