air filter MAZDA PROTEGE 1992 User Guide
[x] Cancel search | Manufacturer: MAZDA, Model Year: 1992, Model line: PROTEGE, Model: MAZDA PROTEGE 1992Pages: 1164, PDF Size: 81.9 MB
Page 283 of 1164
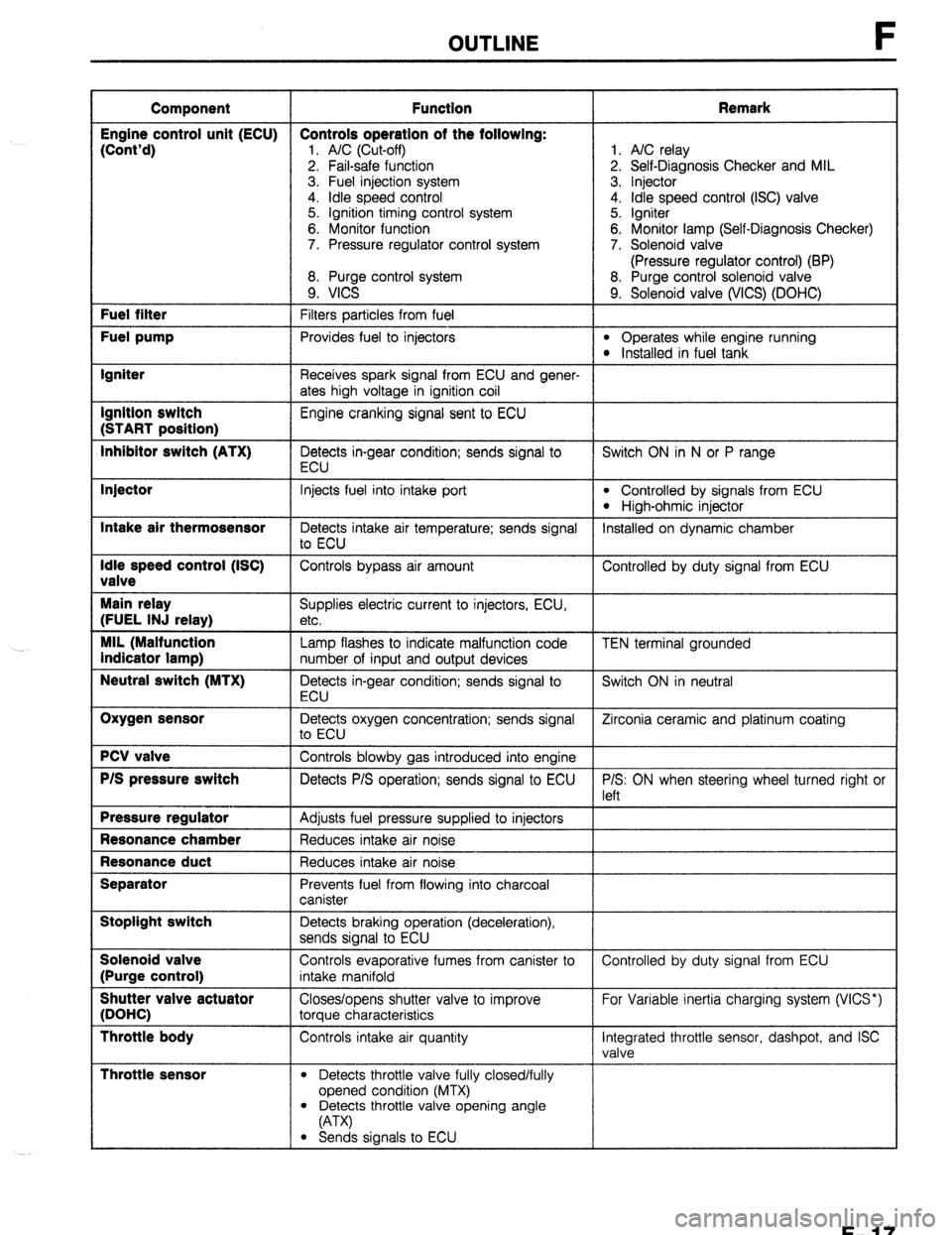
OUTLINE
Component Function Remark
Engine control unit (ECU) Controls operation of the following:
(Cont’d)
1. A/C (Cut-off) 1. A/C relay
2. Fail-safe function 2. Self-Diagnosis Checker and MIL
3. Fuel injection system 3. Injector
4. idle speed control 4. Idle speed control (ISC) valve
5. Ignition timing control system 5. Igniter
6. Monitor function 6. Monitor lamp (Self-Diagnosis Checker)
7. Pressure regulator control system 7. Solenoid valve
(Pressure regulator control) (BP)
8. Purge control system 8. Purge control solenoid valve
9. VICS 9. Solenoid valve (WCS) (DOHC) Fuel filter
Filters particles from fuel Fuel pump
Provides fuel to injectors l Operates while engine running l Installed in fuel tank Igniter
Receives spark signal from ECU and gener-
ates high voltage in ignition coil Ignition switch
Engine cranking signal sent to ECU (START position)
Inhibitor switch (ATX)
Detects in-gear condition; sends signal to Switch ON in N or P range
ECU Injector
Intake air thermosensor
Idle speed control (ISC)
valve
Main relay
(FUEL INJ relay)
MIL (Malfunction
indicator lamp)
Neutral switch (MTX)
Oxygen sensor
PCV valve
P/S pressure switch
Pressure regulator
Resonance chamber
Resonance duct
Separator
Stoplight switch
Solenoid valve
(Purge control)
Shutter valve actuator
(DOHC)
Throttle body
Throttle sensor
Injects fuel into intake port l Controlled by signals from ECU
l High-ohmic injector
Detects intake air temperature; sends signal Installed on dynamic chamber
to ECU
Controls bypass air amount Controlled by duty signal from ECU
Supplies electric current to injectors, ECU,
etc.
Lamp flashes to indicate malfunction code
number of input and output devices
Detects in-gear condition; sends signal to
ECU
Detects oxygen concentration; sends signal
to ECU
Controls blowby gas introduced into engine
Detects P/S operation; sends signal to ECU
Adjusts fuel pressure supplied to injectors
Reduces intake air noise
Reduces intake air noise
Prevents fuel from flowing into charcoal
canister
Detects braking operation (deceleration),
sends signal to ECU
Controls evaporative fumes from canister to
intake manifold
Closes/opens shutter valve to improve
torque characteristics
Controls intake air quantity
l Detects throttle valve fully closed/fully
opened condition (MTX) TEN terminal grounded
Switch ON in neutral
Zirconia ceramic and platinum coating
P/S: ON when steering wheel turned right or
left
Controlled by duty signal from ECU
For Variable inertia charging system (VICS*)
Integrated throttle sensor, dashpot, and ISC
valve
l Detects throttle valve opening angle
(A-W
l Sends signals to ECU
F-l 7
Page 295 of 1164

TROUBLESHOOTING GUIDE F
REAR SEAT C
03UOFX-01
9MUOF2-1;
PRECAUTION
Fuel Pressure Release and Servicing Fuel System
Fuel in the fuel system remains under high pressure even when
the engine is not running.
a) Before disconnecting any fuel line, release the fuel pres-
sure from the fuel system to reduce the possibility of injury
or fire.
1. Start the engine.
2. Push the rear seat cushion buttons and remove the
cushion.
3. Disconnect the fuel pump connector.
4. After the engine stalls, turn off the ignition switch.
5. Reconnect fuel pump connector and install the rear seat
cushion.
b) Use a rag as protection from fuel spray when disconnect-
ing the hoses.
Plug the hoses after removal.
c) When inspecting the fuel system, use a suitable fuel pres-
sure gauge.
Caution
l Install hose clamps to secure the fuel pressure
gauge to the fuel filter and the fuel main hose to pre-
vent fuel leakage.
Pinching Hose
When pinching an air hose or a fuel hose with pliers, wrap
the hose with a rag to prevent damage.
03UOFX-016
F-29
Page 326 of 1164
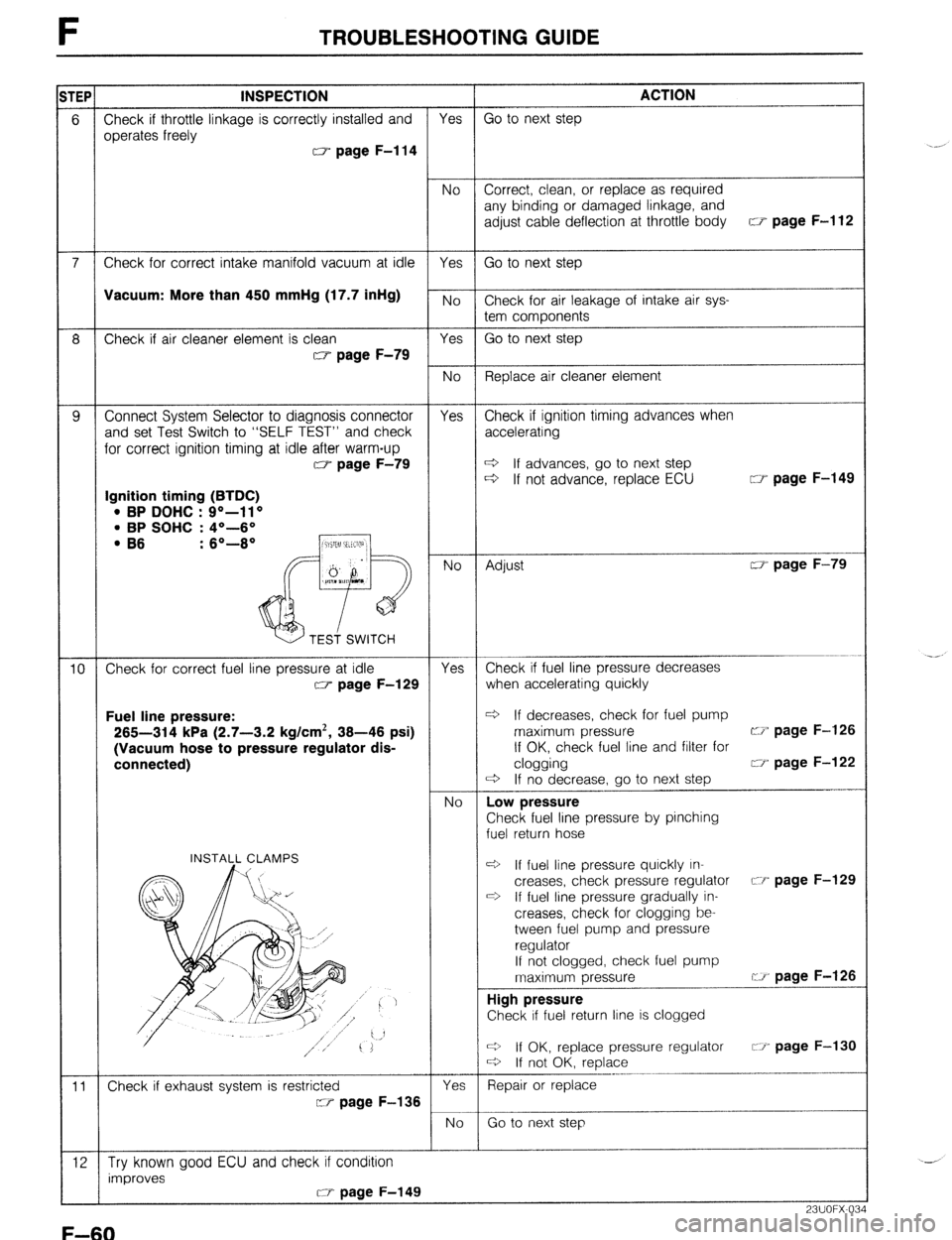
F TROUBLESHOOTING GUIDE
TEP INSPECTION ACTION
6 Check if throttle linkage is correctly installed and Yes Go to next step
operates freely
w page F-l 14
No Correct, clean, or replace as required
any binding or damaged linkage, and
adjust cable deflection at throttle body CT page F-l 12
7 Check for correct intake manifold vacuum at idle Yes Go to next step
Vacuum: More than 450 mmHg (17.7 intig) -
No
Check for air leakage of intake air sys-
tem components
8 Check if air cleaner element is clean Yes Go to next step
w page F-79
No Replace air cleaner element
9 Connect System Selector to diagnosis connector Yes Check if ignition timing advances when
and set Test Switch to “SELF TEST” and check accelerating
for correct ignition timing at idle after warm-up
w page F-79 c3 If advances, go to next step
c3 If not advance, replace ECU [II page F-149
Ignition timing (BTDC)
l BP DOHC : Q”-1 1 o l BP SOHC : 4O-6’
’ B6 : 6O-8O
No Adjust CT+ page F-79
10 Check for correct fuel line pressure at idle Yes Check if fuel line pressure decreases
w page F-129 when accelerating quickly
Fuel line pressure: c3 If decreases, check for fuel pump
265-314 kPa (2.7-3.2 kg/cm*, 38-46 psi) maximum pressure w page F-126
(Vacuum hose to pressure regulator dis- If OK, check fuel line and filter for
connected) clogging CI,’ page F-122
+ If no decrease, go to next step
-
No Low pressure
Check fuel line pressure by pinching
fuel return hose
cti If fuel line pressure quickly In-
creases, check pressure regulator CT page F-129
ti If fuel line pressure gradually in-
creases, check for clogging be-
tween fuel pump and pressure
regulator
If not clogged, check fuel pump
maximum pressure cr page F-126
-
High pressure
Check if fuel return line is clogged
Q If OK, replace pressure regulator C-Y- page F-130
+ If not OK, replace
--_I. 1”1-~~-~~
11 Check if exhaust system is restricted Yes Repair or replace
C-T- page F-136
No Go to next step
12 Try known good ECU and check if condition
improves
CT page F-149
23UOFX-034
F-60
Page 328 of 1164
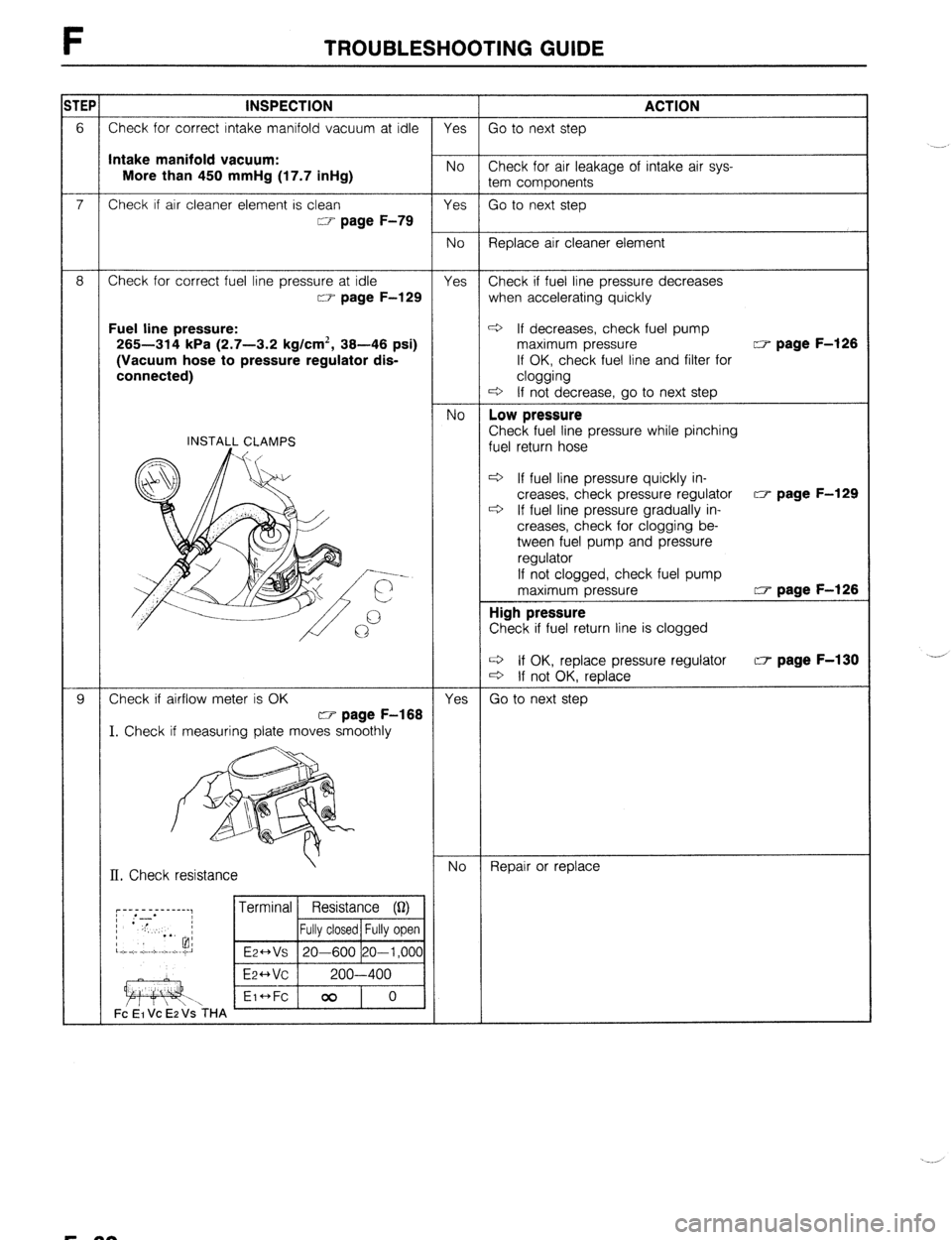
F TROUBLESHOOTING GUIDE
ITEP
INSPECTION ACTION
6 Check for correct intake manifold vacuum at idle Yes Go to next step
Intake manifold vacuum:
More than 450 mmHg (17.7 inHg) No Check for air leakage of intake air sys-
tem components
7 Check if air cleaner element is clean Yes Go to next step
w page F-79
No Replace air cleaner element
8 Check for correct fuel line pressure at idle Yes Check if fuel line pressure decreases
CT= page F-129 when accelerating quickly
Fuel line pressure: c3 If decreases, check fuel pump
265-314 kPa (2.7-3.2 kg/cm’, 38-46 psi) maximum pressure w page F-126
(Vacuum hose to pressure regulator dis- If OK, check fuel line and filter for
connected) clogging
ti If not decrease, go to next step
No Low pressure
INSTALL CLAMPS Check fuel line pressure while pinching
fuel return hose
9 If fuel line pressure quickly in-
creases, check pressure regulator w page F-129
c3 If fuel line pressure gradually in-
creases, check for clogging be-
tween fuel pump and pressure
regulator
If not clogged, check fuel pump
maximum pressure w page F-126
High pressure
Check if fuel return line is clogged
c3 If OK, replace pressure regulator CT page F-130
d If not OK, replace
9 Check if airflow meter is OK
Yes Go to next step
w page F-188
I. Check if measurin late moves smoothly
II. Check resistance No Repair or replace
F-62
Page 332 of 1164
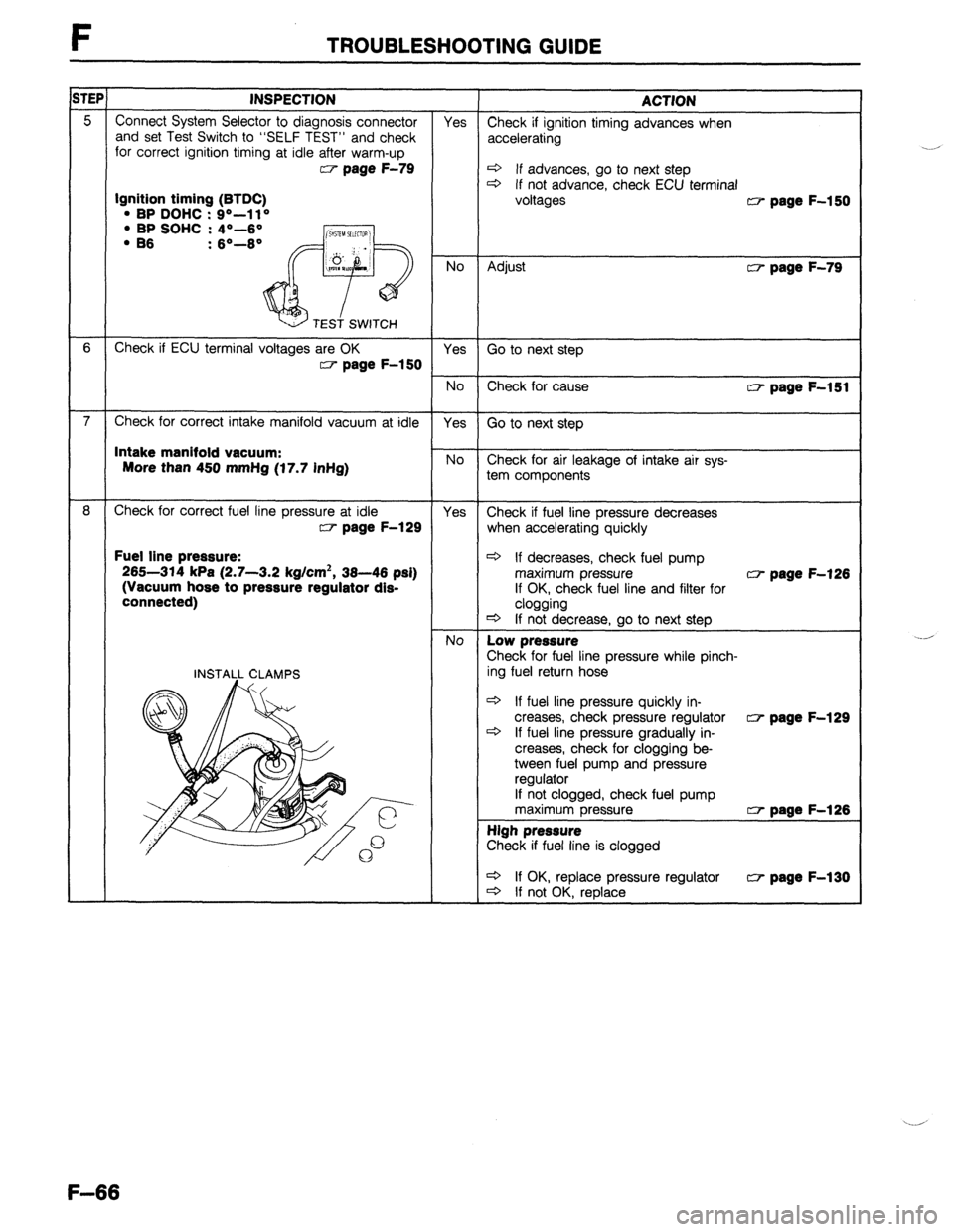
iTEP INSPECTION ACTION
5 Connect System Selector to diagnosis connector Yes
and set Test Switch to “SELF TEST” and check Check if ignition timing advances when
for correct ignition timing at idle after warm-up accelerating w page F-79
* If advances, go to next step
r3 If not advance, check ECU terminal Ignition timing (BTDC)
voltages l BP DOHC : go--ll” w page F-150 l BP SOHC : 4O-6O
. B6 : 6O-6O
No
Adjust w page F-79
6
Check if ECU terminal voltages are OK
Yes Go to next step w page F-150
No
Check for cause ~7 page F-151
7
Check for correct intake manifold vacuum at idle
Yes Go to next step Intake manifold vacuum:
More than 450 mmHg (17.7 inHg) No
Check for air leakage of intake air sys-
tem components
8 Check for correct fuel line pressure at idle
Yes Check if fuel line pressure decreases w page F-129
when accelerating quickly Fuel line pressure:
265-314 kPa (2.7-3.2 kg/cm’, 39-46 psi)
(Vacuum hose to pressure regulator dls-
connected)
d If decreases, check fuel pump
maximum pressure (3‘ page F-126
If OK, check fuel line and filter for
clogging
* If not decrease, go to next step
No Low pressure
Check for fuel line pressure while pinch-
ing fuel return hose
c3 If fuel line pressure quickly in-
creases, check pressure regulator w page F-129
+ If fuel line pressure gradually in-
creases, check for clogging be-
tween fuel pump and pressure
regulator
If not clogged, check fuel pump
maximum pressure w page F-126
High pressure
Check if fuel line is clogged
* If OK, replace pressure regulator w page F-130
c3 If not OK, replace
F-66
Page 387 of 1164
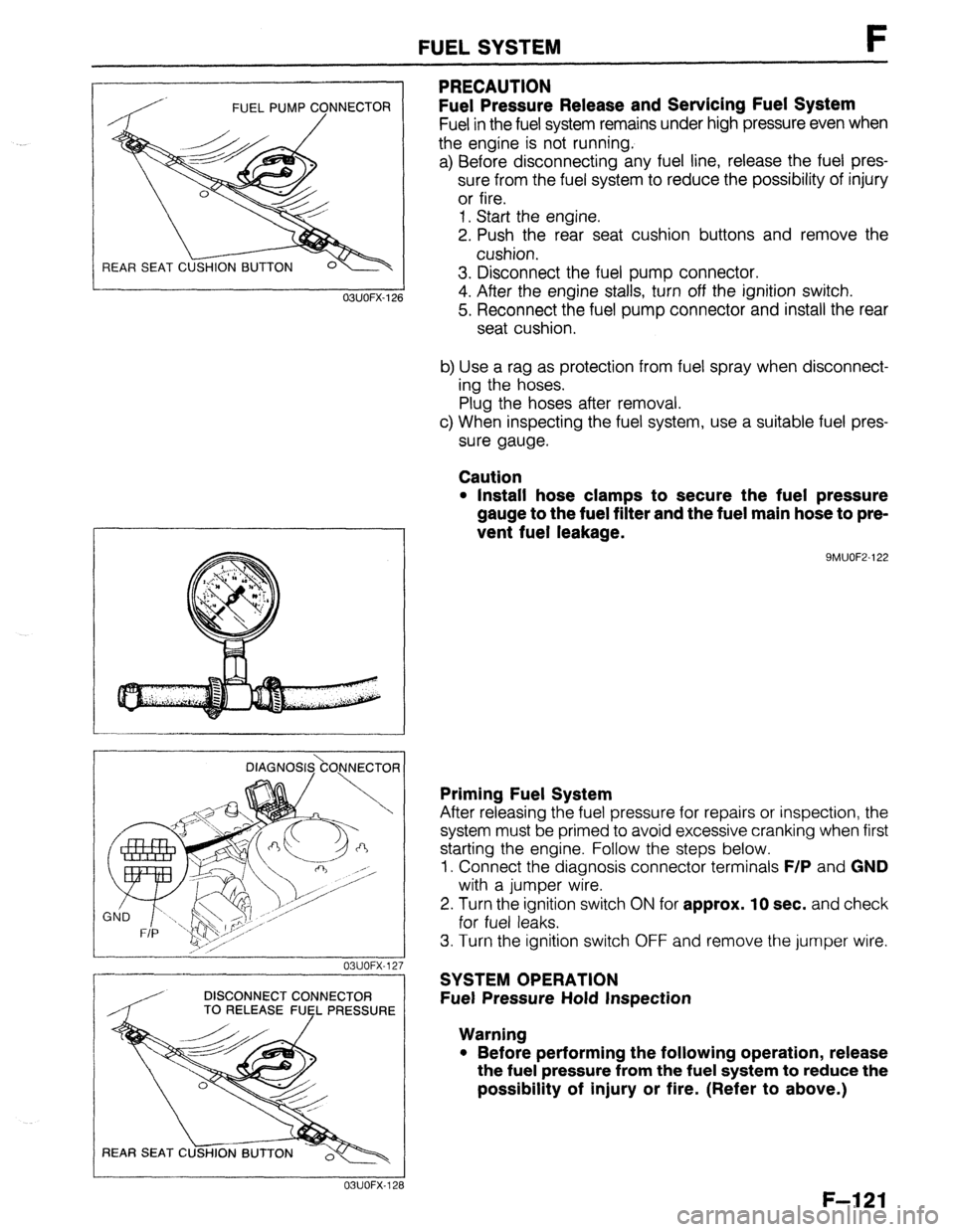
FUEL PUMP CONNECTOR
/
REAR SEAT C
FUEL SYSTEM F
PRECAUTION
Fuel Pressure Release and Servicing Fuel System
Fuel in the fuel system remains under high pressure even when
the engine is not running.
a) Before disconnecting any fuel line, release the fuel pres-
sure from the fuel system to reduce the possibility of injury
or fire.
1. Start the engine.
2. Push the rear seat cushion buttons and remove the
cushion.
3. Disconnect the fuel pump connector.
4. After the engine stalls, turn off the ignition switch.
5. Reconnect the fuel pump connector and install the rear
seat cushion.
b) Use a rag as protection from fuel spray when disconnect-
ing the hoses.
Plug the hoses after removal.
c) When inspecting the fuel system, use a suitable fuel pres-
sure gauge.
Caution
l Install hose clamps to secure the fuel pressure
gauge to the fuel filter and the fuel main hose to pre-
vent fuel leakage.
9MUOF2-122 OBUOFX-126
DlAGNOS&O,NNECTOR
03UOFX-12.
-
DISCONNECT CONNECTOR
/ TO RELEASE FUEL PRESSURE
03UOFX-12;
Priming Fuel System
After releasing the fuel pressure for repairs or inspection, the
system must be primed to avoid excessive cranking when first
starting the engine. Follow the steps below.
1. Connect the diagnosis connector terminals
F/P and GND
with a jumper wire.
2. Turn the ignition switch
ON for approx. 10 sec. and check
for fuel leaks.
3. Turn the ignition switch OFF and remove the jumper wire.
SYSTEM OPERATION
Fuel Pressure Hold Inspection
Warning
l Before performing the following operation, release
the fuel pressure from the fuel system to reduce the
possibility of injury or fire. (Refer to above.)
F-121
Page 394 of 1164
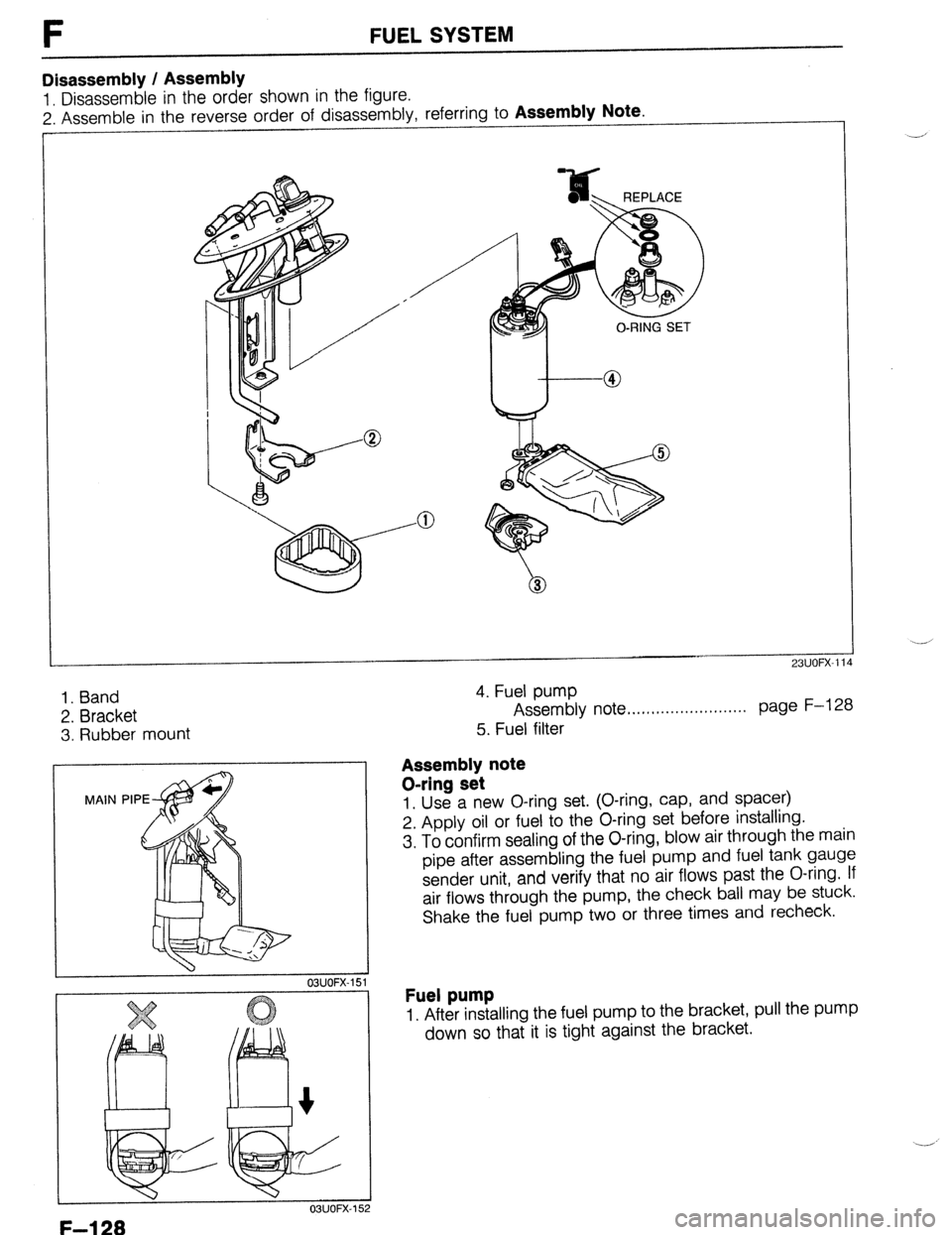
F FUELSYSTEM
Disassembly / Assembly
1. Disassemble in the order shown in the figure.
2. Assemble in the reverse order of disassembly, referring to
Assembly Note
1. Band
2. Bracket
3. Rubber mount
OSUOFX-152
4. Fuel pump
Assembly note ,..........,....,,....,.. page F-l 28
5. Fuel filter
Assembly note
O-ring set
1. Use a new O-ring set. (O-ring, cap, and spacer)
2. Apply oil or fuel to the O-ring set before installing.
3. To confirm sealing of the O-ring, blow air through the main
pipe after assembling the fuel pump and fuel tank gauge
sender unit, and verify that no air flows past the O-ring. If
air flows through the pump, the check ball may be stuck.
Shake the fuel pump two or three times and recheck.
Fuel pump
1. After installing the fuel pump to the bracket, pull the pump
down so that it is tight against the bracket.
F-l 28
Page 401 of 1164
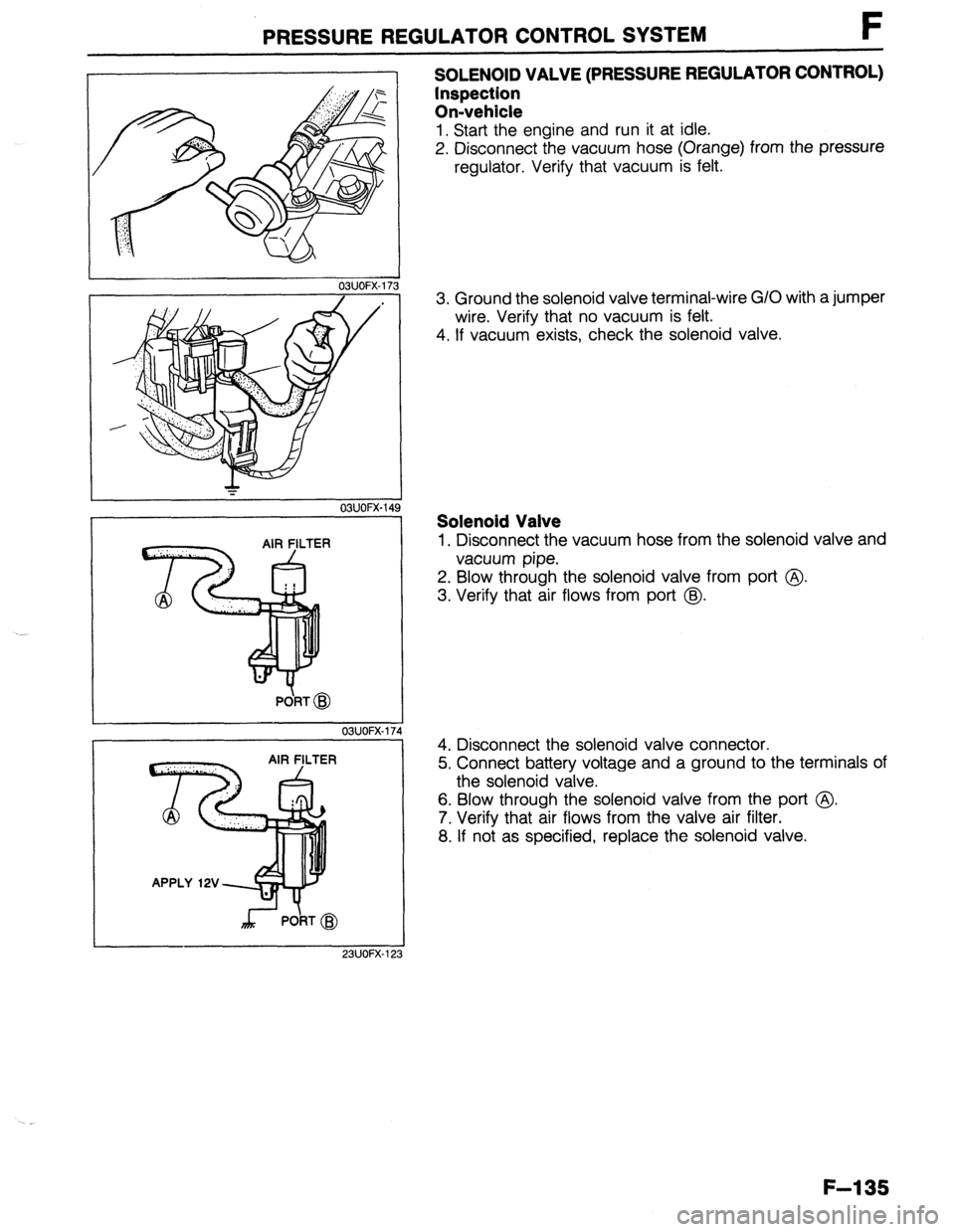
PRESSUREREGULATORCONTROLSYSTEM F
03UOFX-17
*
03UOFX-14!
OSUOFX-17
SOLENOID VALVE (PRESSURE REGULATOR CONTROL)
Inspection
On-vehicle
1. Start the engine and run it at idle.
2. Disconnect the vacuum hose (Orange) from the pressure
regulator. Verify that vacuum is felt.
3. Ground the solenoid valve terminal-wire G/O with a jumper
wire. Verify that no vacuum is felt.
4. If vacuum exists, check the solenoid valve.
Solenoid Valve
1. Disconnect the vacuum hose from the solenoid valve and
vacuum pipe.
2. Blow through the solenoid valve from port @
3. Verify that air flows from port @.
4. Disconnect the solenoid valve connector.
5. Connect battery voltage and a ground to the terminals of
the solenoid valve.
6. Blow through the solenoid valve from the port @.
7. Verify that air flows from the valve air filter.
8. If not as specified, replace the solenoid valve.
F-l 35
Page 1023 of 1164
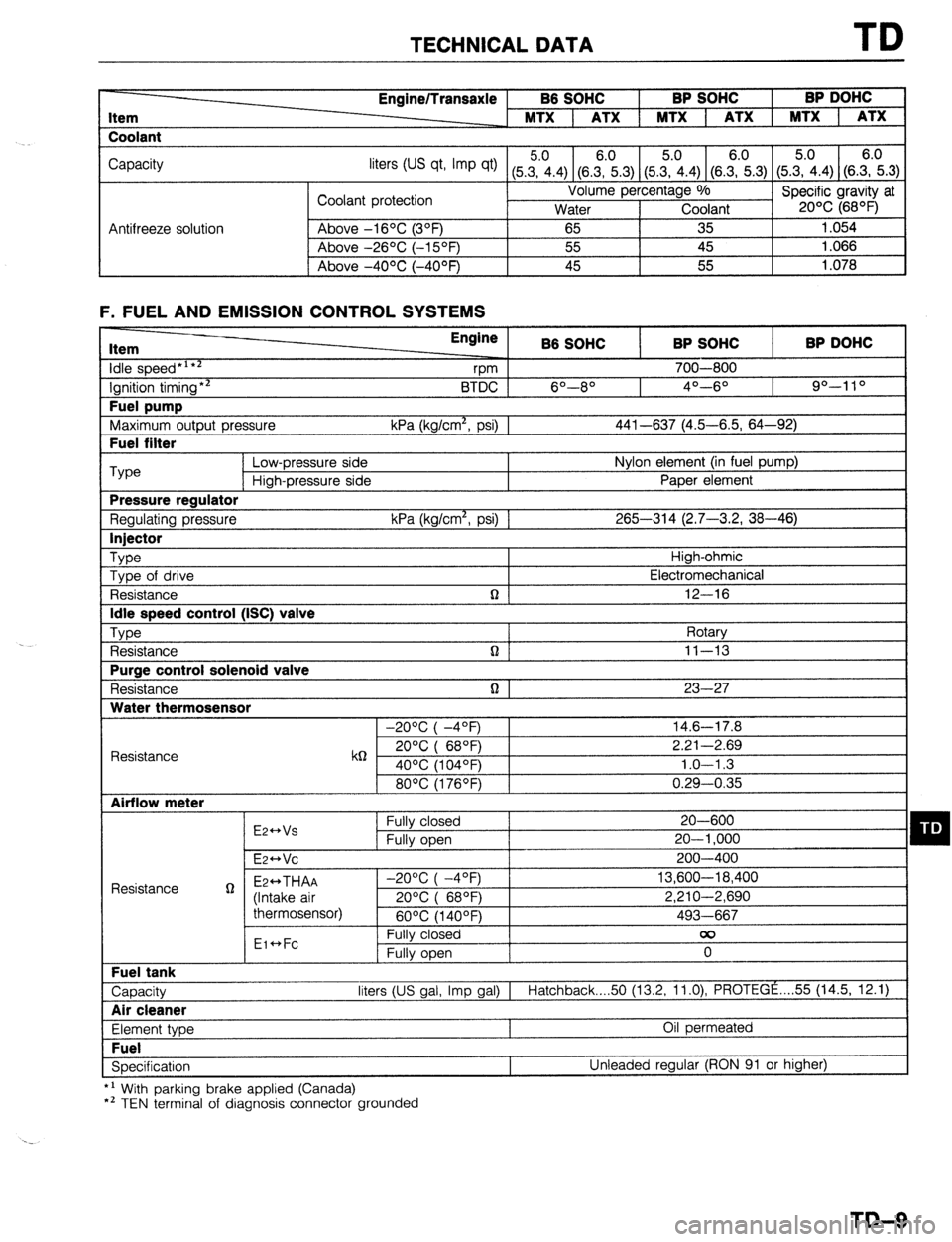
TECHNICAL DATA TD
Item
Coolant Engine/Transaxle B6 SOHC BP SOHC BP DOHC
MTX 1 ATX 1 MTX 1 ATX 1 MTX 1 ATX
Capacity
liters tus qt, Imp qt) (5Z.4) (8.E.3) (5&4) (SE.3) (5.?i.4) (S.E.3)
Coolant protection Volume percentage %
Specific gravity at
Water Coolant 20% (68OF)
Antifreeze solution Above -16OC (3OF)
65 35 1.054
Above -26OC (-15OF) 55 45 1.066
I Above -4OOC (-40°F) 45 55
1.078
F. FUEL AND EMISSION CONTROL SYSTEMS Item
idle speed*‘**
Ignition timing** Fuel pump
Maximum output pressure Fuel filter Engine
B6 SOHC BP SOHC BP DOHC
vm 700-800
BTDC 6O--8O 4O---6O 90-l 10
kPa (kg/cm*, psi) 1 441-637 (4.5-6.5, 64-92) ‘Type
Low-pressure side Nylon element (in fuel pump)
High-pressure side Paper element Pressure regulator
Regulating pressure kPa (kg/cm*, psi) 1 265-314 (2.7-3.2, 38-46) Injector
Type
High-ohmic
Type of drive Electromechanical
Resistance n 12-16 Idle speed control (ISC) valve
Type
Rotary
Resistance n ] 11-13 Purge control solenoid valve
Resistance n 1 23-27 Water thermosensor
-20°C( -4OF) 14.6-17.8
Resistance k6 20°C( 68QF) 2.21-2.69
40% (104OF) 1.0-l .3
80°C(1760F) 0.29-0.35 Airflow meter
E2++Vs Fully closed 20-600 q D Fully open 20-l ,000
E~HVC 200-400
Resistance g Ez++THAA -2O%(-4OF) 13,600-18,400
(Intake air 20%( 68OF) 2,210-2,690
thermosensor)
60°C(1400F) 493-667
Eic*Fc Fully closed 00
Fully open 0 Fuel tank
Capacity liters (US gal, Imp gal) I
Hatchback 50 (13.2, 11.0) PROTEGE . . . . 55 (14.5, 12.1) Air cleaner
Element type Oil permeated Fuel
Specification Unleaded regular (RON 91 or higher)
*’ With parking brake applied (Canada)
*’ TEN terminal of diagnosis connector grounded
TD-9