MITSUBISHI 380 2005 Workshop Manual
Manufacturer: MITSUBISHI, Model Year: 2005, Model line: 380, Model: MITSUBISHI 380 2005Pages: 1500, PDF Size: 47.87 MB
Page 1181 of 1500
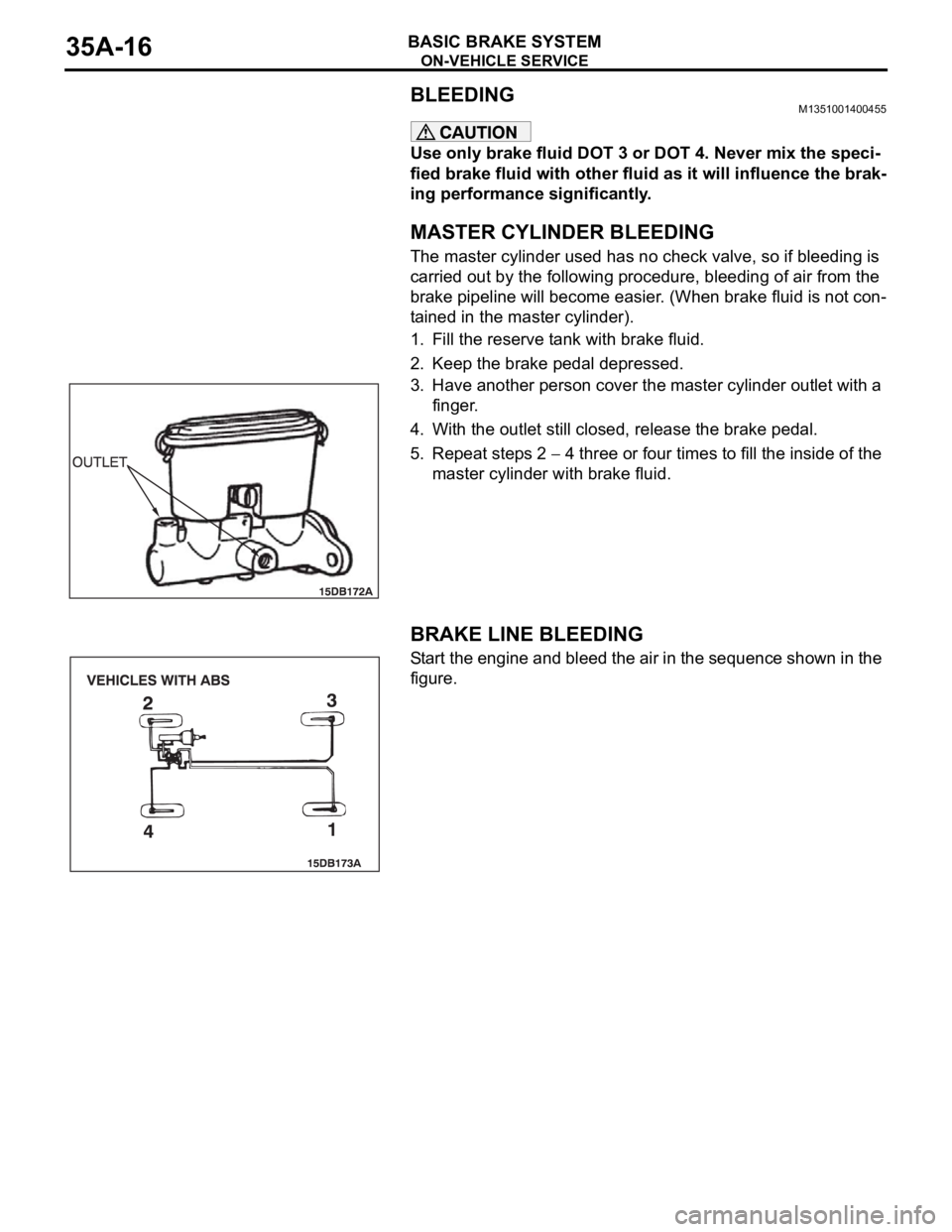
ON-VEHICLE SERVICE
BASIC BRAKE SYSTEM35A-16
BLEEDINGM1351001400455
Use only brake fluid DOT 3 or DOT 4. Never mix the speci-
fied brake fluid with other fluid as it will influence the brak-
ing performance significantly.
.
MASTER CYLINDER BLEEDING
The master cylinder used has no check valve, so if bleeding is
carried out by the following procedure, bleeding of air from the
brake pipeline will become easier. (When brake fluid is not con-
tained in the master cylinder).
1. Fill the reserve tank with brake fluid.
2. Keep the brake pedal depressed.
3. Have another person cover the master cylinder outlet with a
finger.
4. With the outlet still closed, release the brake pedal.
5. Repeat steps 2
4 three or four times to fill the inside of the
master cylinder with brake fluid.
.
BRAKE LINE BLEEDING
Start the engine and bleed the air in the sequence shown in the
figure.
Page 1182 of 1500
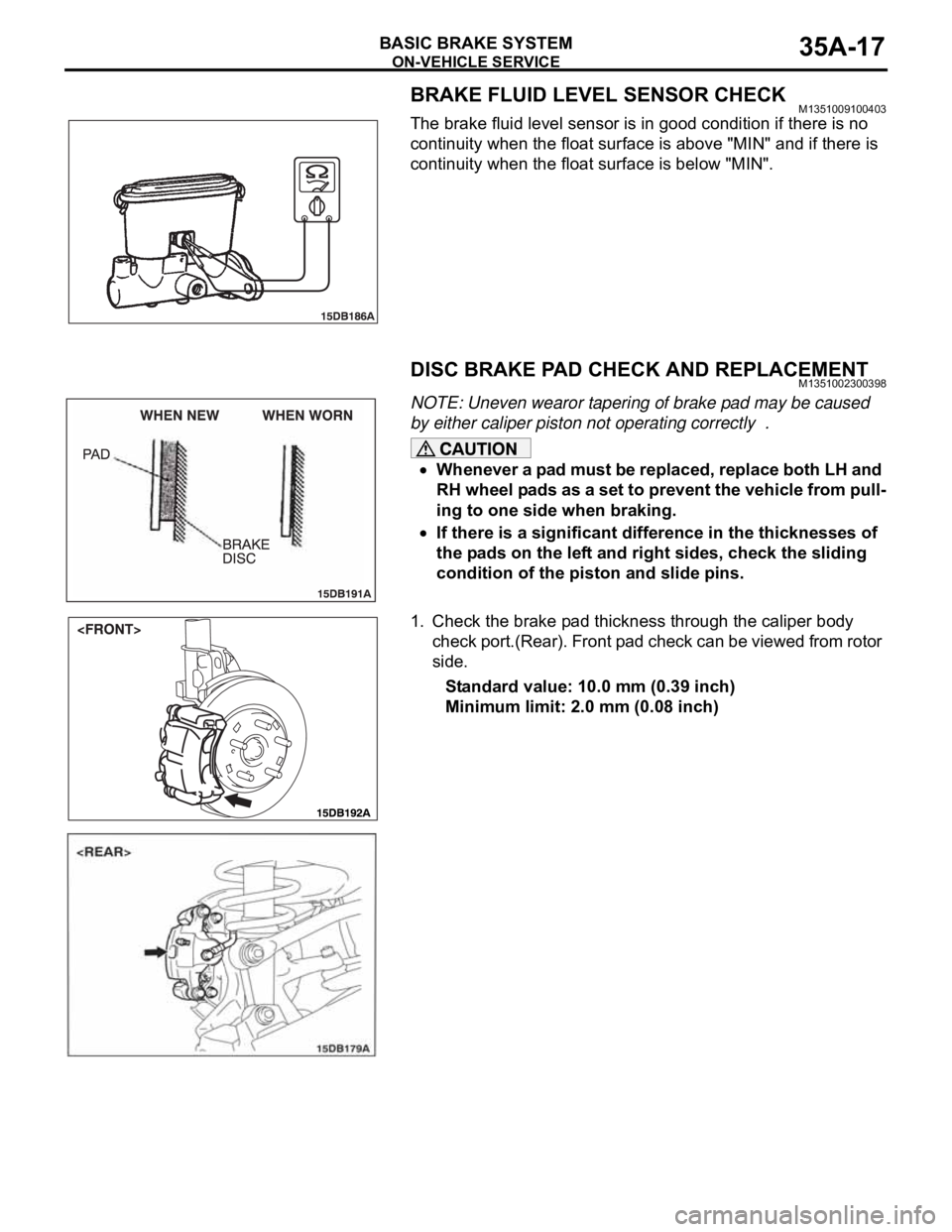
ON-VEHICLE SERVICE
BASIC BRAKE SYSTEM35A-17
BRAKE FLUID LEVEL SENSOR CHECKM1351009100403
The brake fluid level sensor is in good condition if there is no
continuity when the float surface is above "MIN" and if there is
continuity when the float surface is below "MIN".
DISC BRAKE PAD CHECK AND REPLACEMENTM1351002300398
NOTE: Uneven wearor tapering of brake pad may be caused
by either caliper piston not operating correctly .
Whenever a pad must be replaced, replace both LH and
RH wheel pads as a set to prevent the vehicle from pull-
ing to one side when braking.
If there is a significant difference in the thicknesses of
the pads on the left and right sides, check the sliding
condition of the piston and slide pins.
1. Check the brake pad thickness through the caliper body
check port.(Rear). Front pad check can be viewed from rotor
side.
Standard value: 10.0 mm (0.39 inch)
Minimum limit: 2.0 mm (0.08 inch)
Page 1183 of 1500
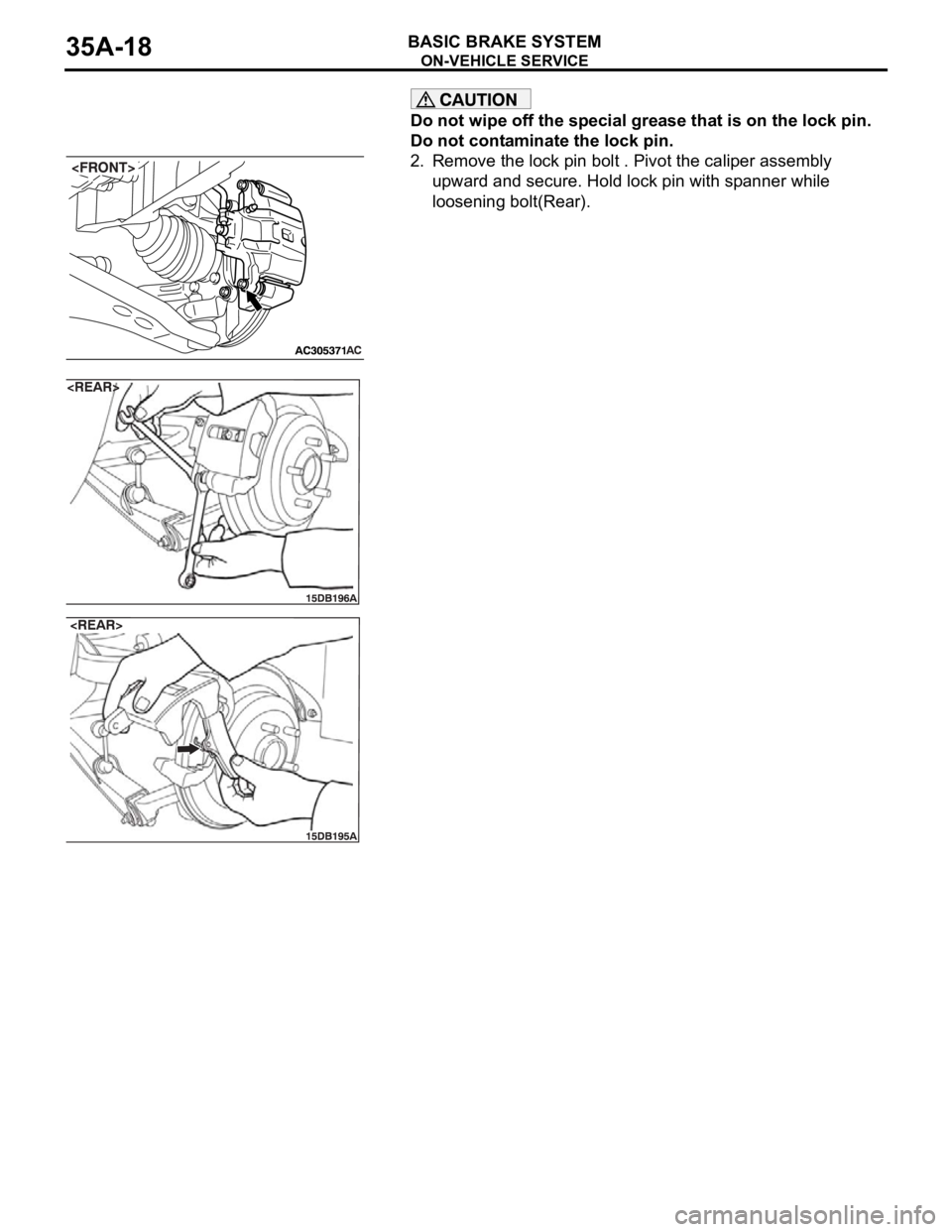
ON-VEHICLE SERVICE
BASIC BRAKE SYSTEM35A-18
Do not wipe off the special grease that is on the lock pin.
Do not contaminate the lock pin.
2. Remove the lock pin bolt . Pivot the caliper assembly
upward and secure. Hold lock pin with spanner while
loosening bolt(Rear).
Page 1184 of 1500
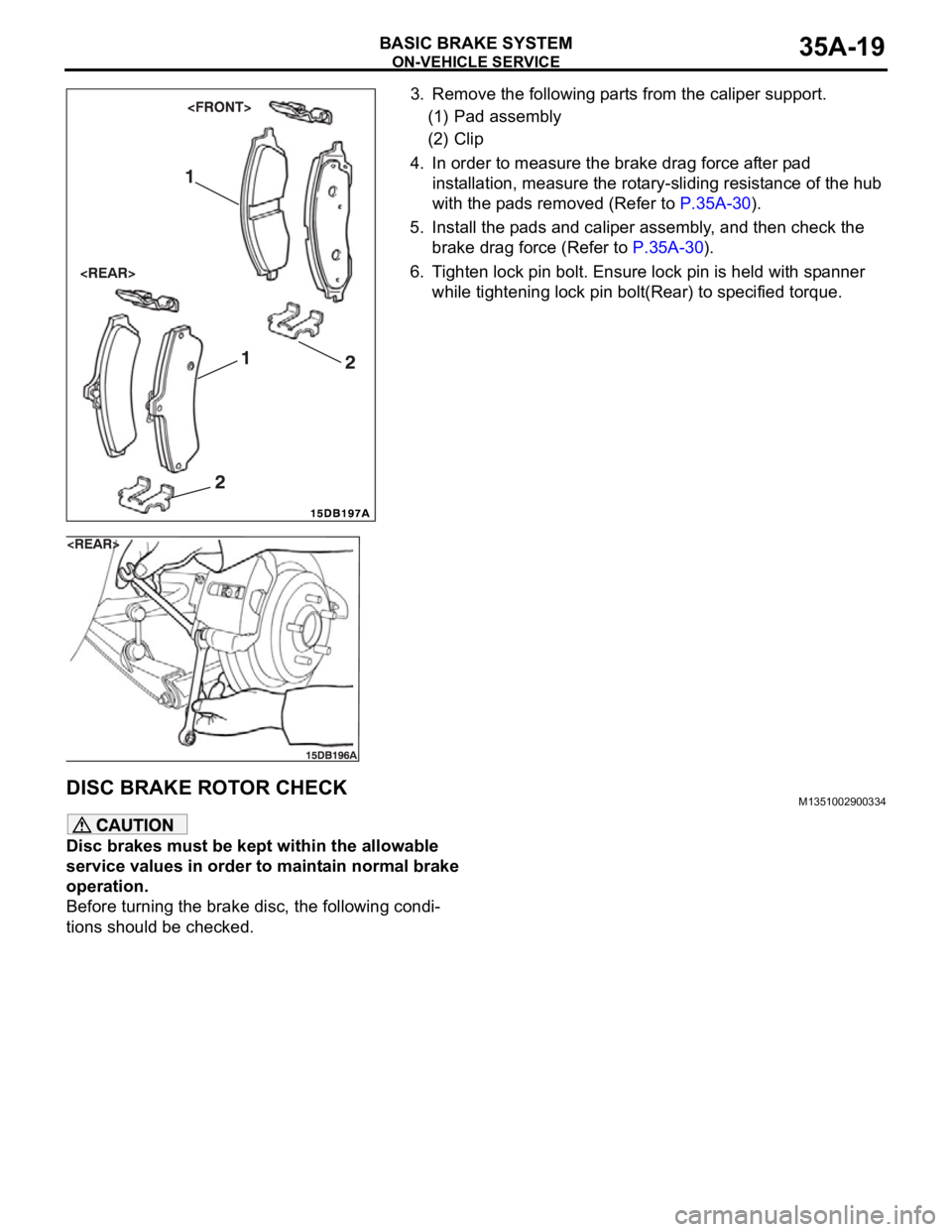
ON-VEHICLE SERVICE
BASIC BRAKE SYSTEM35A-19
3. Remove the following parts from the caliper support.
(1) Pad assembly
(2) Clip
4. In order to measure the brake drag force after pad
installation, measure the rotary-sliding resistance of the hub
with the pads removed (Refer to P.35A-30).
5. Install the pads and caliper assembly, and then check the
brake drag force (Refer to P.35A-30).
6. Tighten lock pin bolt. Ensure lock pin is held with spanner
while tightening lock pin bolt(Rear) to specified torque.
DISC BRAKE ROTOR CHECKM1351002900334
Disc brakes must be kept within the allowable
service values in order to maintain normal brake
operation.
Before turning the brake disc, the following condi-
tions should be checked.
Page 1185 of 1500
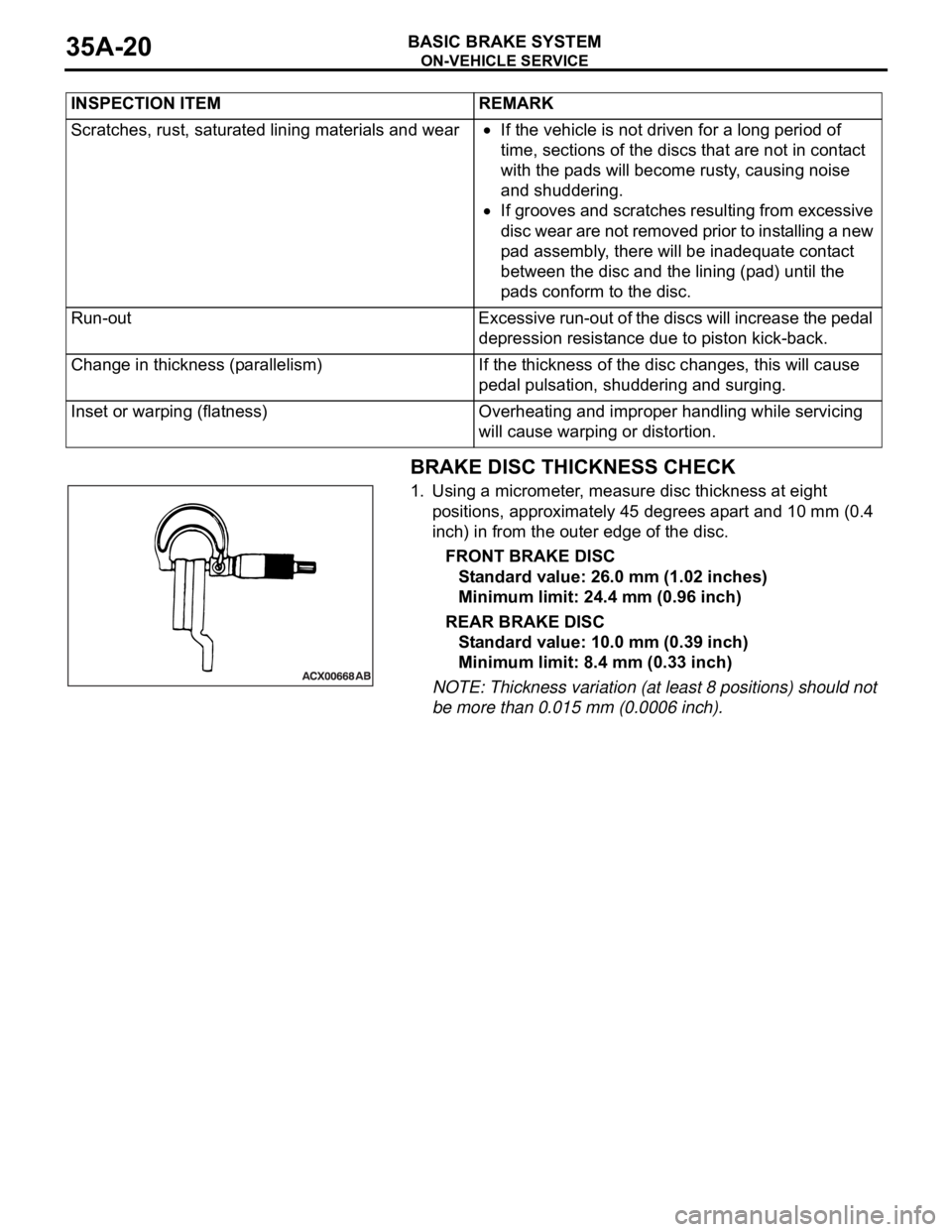
ON-VEHICLE SERVICE
BASIC BRAKE SYSTEM35A-20
.
BRAKE DISC THICKNESS CHECK
1. Using a micrometer, measure disc thickness at eight
positions, approximately 45 degrees apart and 10 mm (0.4
inch) in from the outer edge of the disc.
FRONT BRAKE DISC
Standard value: 26.0 mm (1.02 inches)
Minimum limit: 24.4 mm (0.96 inch)
REAR BRAKE DISC
Standard value: 10.0 mm (0.39 inch)
Minimum limit: 8.4 mm (0.33 inch)
NOTE: Thickness variation (at least 8 positions) should not
be more than 0.015 mm (0.0006 inch). INSPECTION ITEM REMARK
Scratches, rust, saturated lining materials and wear
If the vehicle is not driven for a long period of
time, sections of the discs that are not in contact
with the pads will become rusty, causing noise
and shuddering.
If grooves and scratches resulting from excessive
disc wear are not removed prior to installing a new
pad assembly, there will be inadequate contact
between the disc and the lining (pad) until the
pads conform to the disc.
Run-out Excessive run-out of the discs will increase the pedal
depression resistance due to piston kick-back.
Change in thickness (parallelism) If the thickness of the disc changes, this will cause
pedal pulsation, shuddering and surging.
Inset or warping (flatness) Overheating and improper handling while servicing
will cause warping or distortion.
Page 1186 of 1500
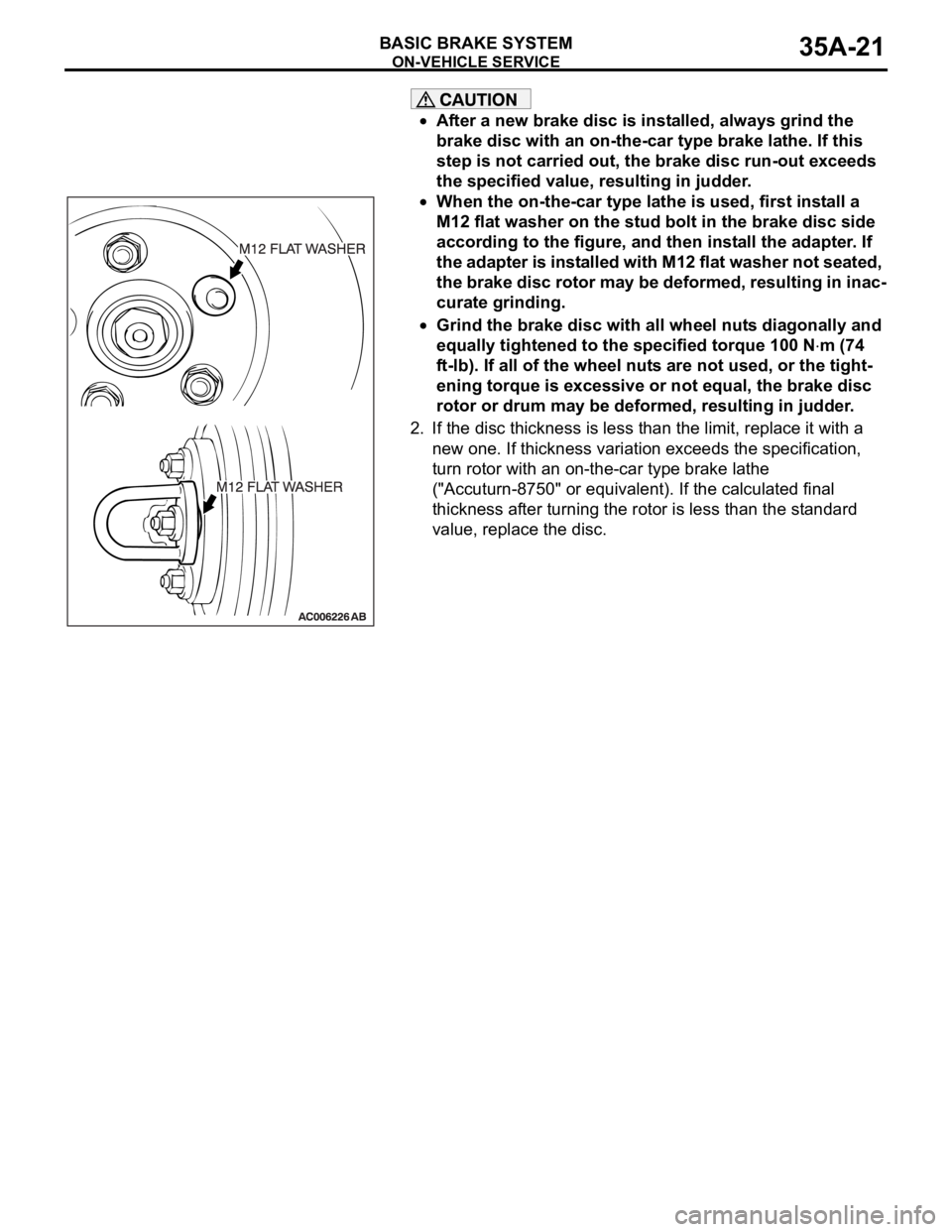
ON-VEHICLE SERVICE
BASIC BRAKE SYSTEM35A-21
After a new brake disc is installed, always grind the
brake disc with an on-the-car type brake lathe. If this
step is not carried out, the brake disc run-out exceeds
the specified value, resulting in judder.
When the on-the-car type lathe is used, first install a
M12 flat washer on the stud bolt in the brake disc side
according to the figure, and then install the adapter. If
the adapter is installed with M12 flat washer not seated,
the brake disc rotor may be deformed, resulting in inac-
curate grinding.
Grind the brake disc with all wheel nuts diagonally and
equally tightened to the specified torque 100 N
m (74
ft-lb). If all of the wheel nuts are not used, or the tight-
ening torque is excessive or not equal, the brake disc
rotor or drum may be deformed, resulting in judder.
2. If the disc thickness is less than the limit, replace it with a
new one. If thickness variation exceeds the specification,
turn rotor with an on-the-car type brake lathe
("Accuturn-8750" or equivalent). If the calculated final
thickness after turning the rotor is less than the standard
value, replace the disc.
.
Page 1187 of 1500
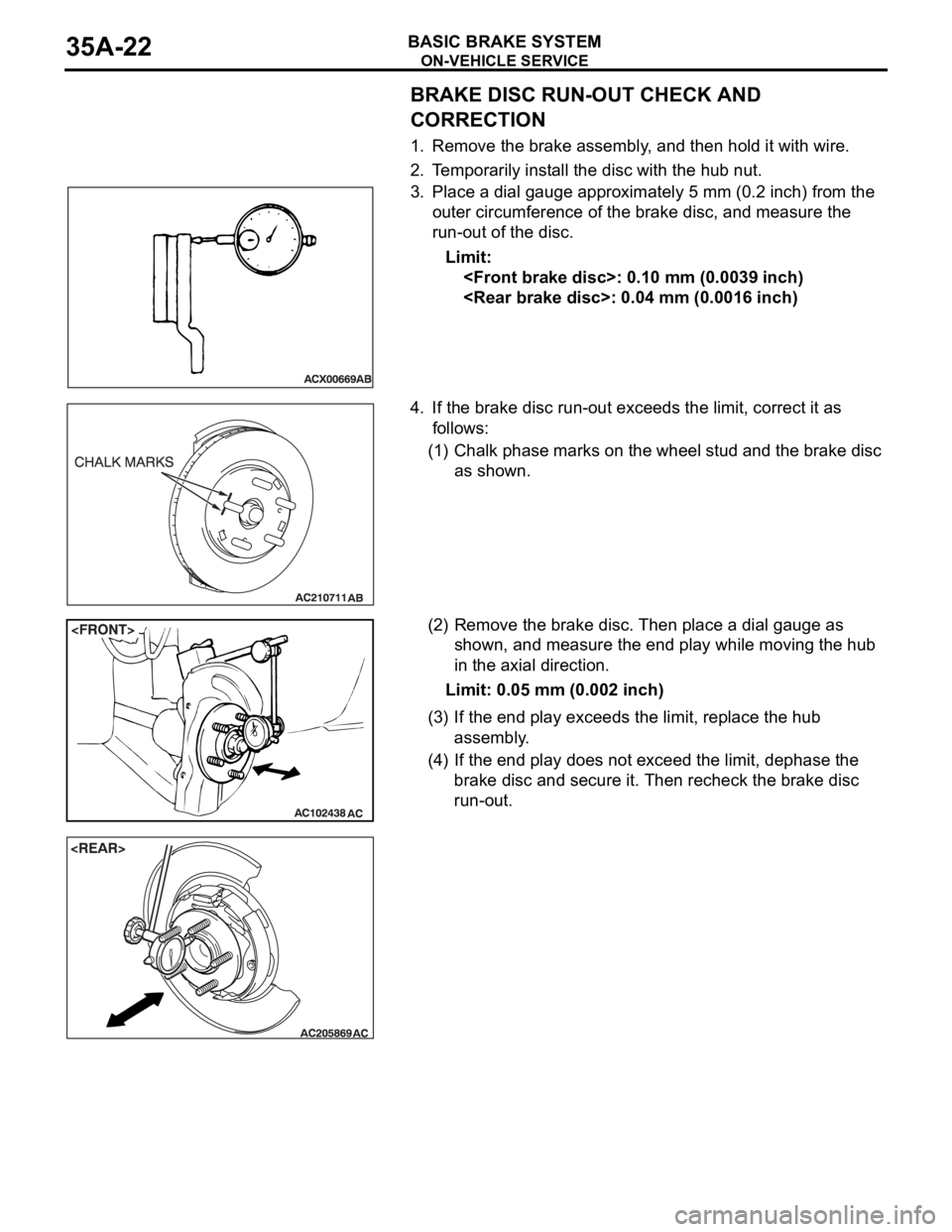
ON-VEHICLE SERVICE
BASIC BRAKE SYSTEM35A-22
BRAKE DISC RUN-OUT CHECK AND
CORRECTION
1. Remove the brake assembly, and then hold it with wire.
2. Temporarily install the disc with the hub nut.
3. Place a dial gauge approximately 5 mm (0.2 inch) from the
outer circumference of the brake disc, and measure the
run-out of the disc.
Limit:
4. If the brake disc run-out exceeds the limit, correct it as
follows:
(1) Chalk phase marks on the wheel stud and the brake disc
as shown.
(2) Remove the brake disc. Then place a dial gauge as
shown, and measure the end play while moving the hub
in the axial direction.
Limit: 0.05 mm (0.002 inch)
(3) If the end play exceeds the limit, replace the hub
assembly.
(4) If the end play does not exceed the limit, dephase the
brake disc and secure it. Then recheck the brake disc
run-out.
Page 1188 of 1500
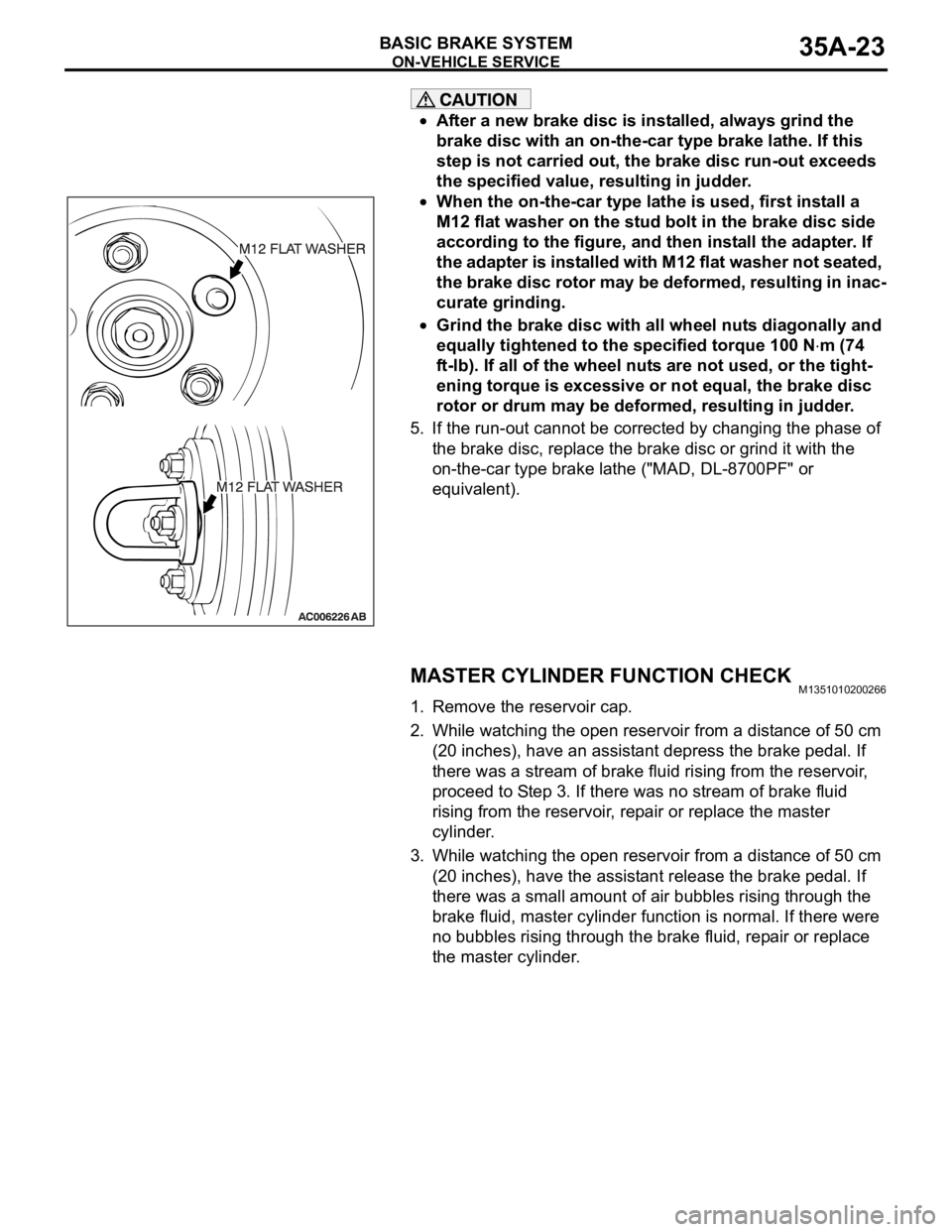
ON-VEHICLE SERVICE
BASIC BRAKE SYSTEM35A-23
After a new brake disc is installed, always grind the
brake disc with an on-the-car type brake lathe. If this
step is not carried out, the brake disc run-out exceeds
the specified value, resulting in judder.
When the on-the-car type lathe is used, first install a
M12 flat washer on the stud bolt in the brake disc side
according to the figure, and then install the adapter. If
the adapter is installed with M12 flat washer not seated,
the brake disc rotor may be deformed, resulting in inac-
curate grinding.
Grind the brake disc with all wheel nuts diagonally and
equally tightened to the specified torque 100 N
m (74
ft-lb). If all of the wheel nuts are not used, or the tight-
ening torque is excessive or not equal, the brake disc
rotor or drum may be deformed, resulting in judder.
5. If the run-out cannot be corrected by changing the phase of
the brake disc, replace the brake disc or grind it with the
on-the-car type brake lathe ("MAD, DL-8700PF" or
equivalent).
MASTER CYLINDER FUNCTION CHECKM1351010200266
1. Remove the reservoir cap.
2. While watching the open reservoir from a distance of 50 cm
(20 inches), have an assistant depress the brake pedal. If
there was a stream of brake fluid rising from the reservoir,
proceed to Step 3. If there was no stream of brake fluid
rising from the reservoir, repair or replace the master
cylinder.
3. While watching the open reservoir from a distance of 50 cm
(20 inches), have the assistant release the brake pedal. If
there was a small amount of air bubbles rising through the
brake fluid, master cylinder function is normal. If there were
no bubbles rising through the brake fluid, repair or replace
the master cylinder.
Page 1189 of 1500
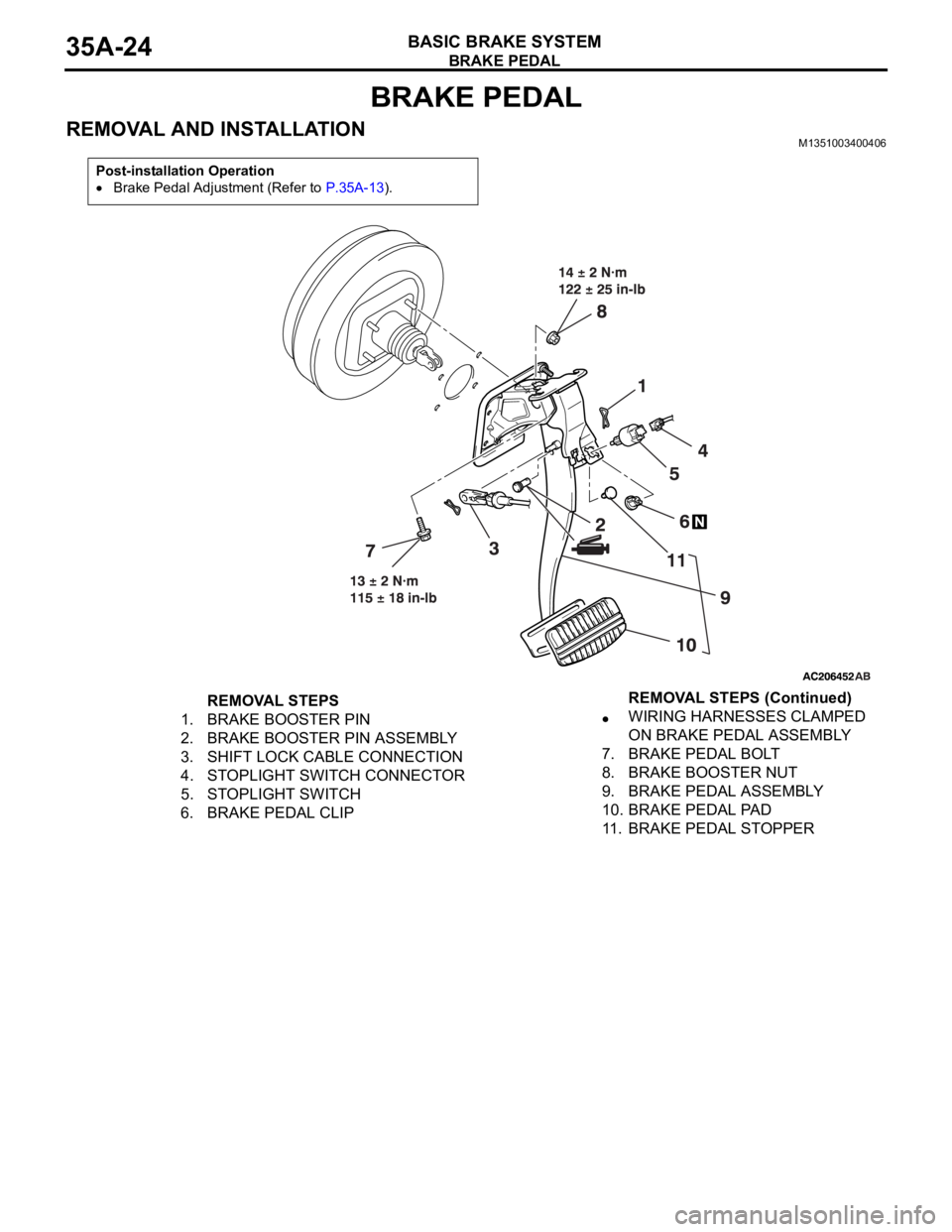
BRAKE PEDAL
BASIC BRAKE SYSTEM35A-24
BRAKE PEDAL
REMOVAL AND INSTALLATIONM1351003400406
Post-installation Operation
Brake Pedal Adjustment (Refer to P.35A-13).
REMOVAL STEPS
1. BRAKE BOOSTER PIN
2. BRAKE BOOSTER PIN ASSEMBLY
3. SHIFT LOCK CABLE CONNECTION
4. STOPLIGHT SWITCH CONNECTOR
5. STOPLIGHT SWITCH
6. BRAKE PEDAL CLIPWIRING HARNESSES CLAMPED
ON BRAKE PEDAL ASSEMBLY
7. BRAKE PEDAL BOLT
8. BRAKE BOOSTER NUT
9. BRAKE PEDAL ASSEMBLY
10. BRAKE PEDAL PAD
11. BRAKE PEDAL STOPPERREMOVAL STEPS (Continued)
Page 1190 of 1500
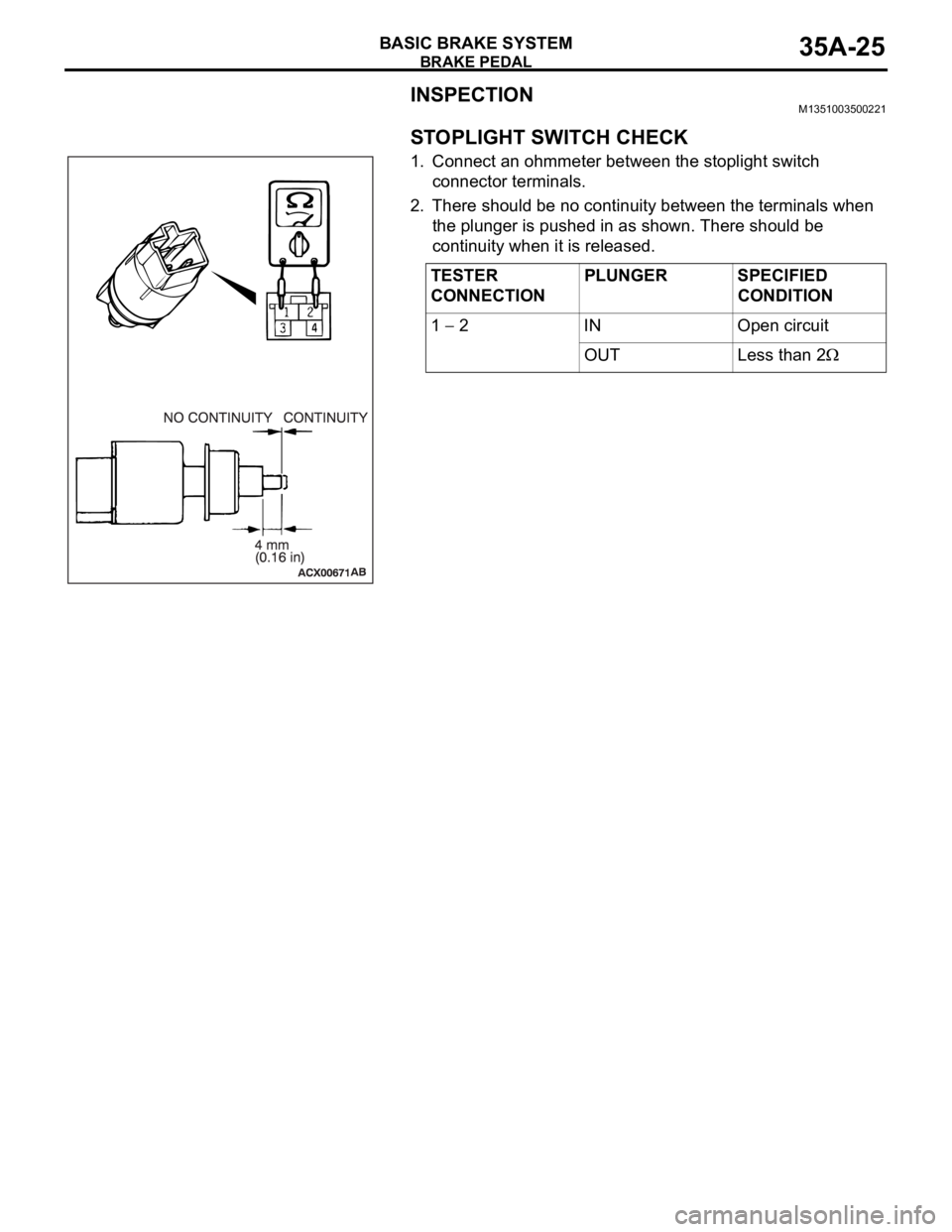
BRAKE PEDAL
BASIC BRAKE SYSTEM35A-25
INSPECTIONM1351003500221.
STOPLIGHT SWITCH CHECK
1. Connect an ohmmeter between the stoplight switch
connector terminals.
2. There should be no continuity between the terminals when
the plunger is pushed in as shown. There should be
continuity when it is released.
TESTER
CONNECTIONPLUNGER SPECIFIED
CONDITION
1
2 IN Open circuit
OUT Less than 2